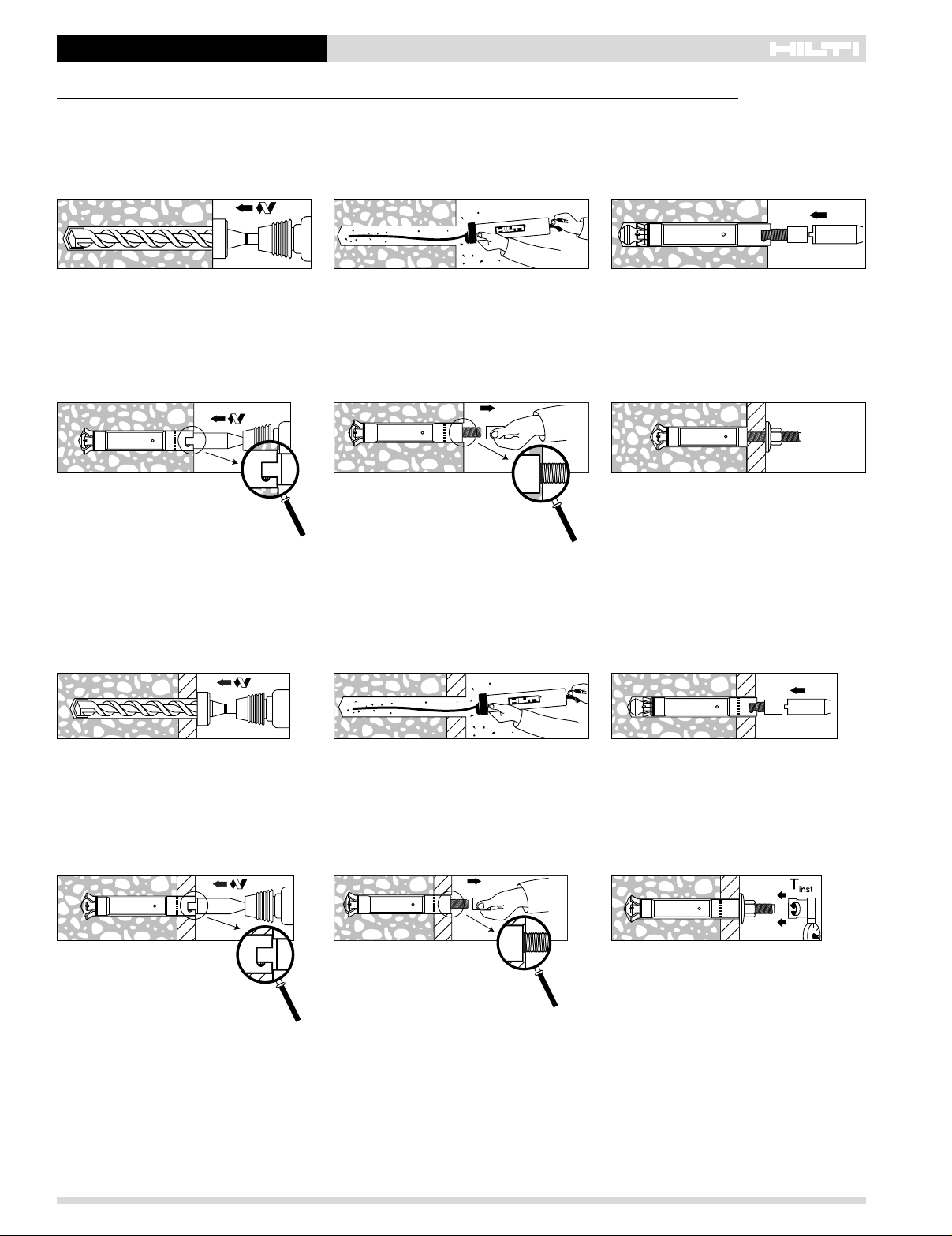
M
echanical Anchoring Systems
4.3.1 HDA Undercut Anchor
4.3.1.4 Installation Instructions
Setting Operation HDA-P/-PR/-PF (Pre-Set Style)
1. Drill a hole to the required depth using a stop drill bit
matched to the anchor,(refer to specification table
2. Clean hole with compressed air or a hand air pump
such that drilling debris is evacuated.
and ordering info.). If rebar is encountered, use a Hilti
metric matched tolerance diamond core bit to drill
through the rebar.Remove the concrete core and
finish drilling the hole with the stop drill bit.
4. The anchor is set with the hammer
drill in hammer drill mode. During
the setting procedure, both drilling and
impact energy are transferred to the sleeve
by the setting tool, causing the sleeve to slide
over the conical end of the anchor bolt while
forming the undercut in the base material. On the
setting tool, the red ring indicates the progress
of the setting operation.
5. The mark on the anchor rod
provides the indicator for correct
setting. The anchor is set and the undercut
is fully formed when the red marking on the
anchor bolt is visible above the top edge of the
sleeve. If anchor setting time exceeds 40 seconds for
M10 or M12 anchors or 60 seconds for M16 or M20
anchors, remove the anchor (see HDA removal tool
Instructions). Install a new HDA anchor.
Setting Operation HDA-T/-TR/-TF (Through-Set Style)
3. The anchor is inserted in the hole, so that the cone
sits on the bottom of the drilled hole. Do not remove
the plastic cap which protects the threaded rod.
Using the assigned setting tool and Hilti Hammer Drill
(Refer to spec. Table and Ordering Info.), the setting
tool is guided over the anchor rod and engages the
grooves in the sleeve. It is critical to use the
specified Hilti hammer drills.
6. Remove the plastic thread protector cap. Secure the
part to be fastened by using the conical spring washer and nut provided. Apply a torque not to exceed the
maximum values given in the Specification Table.
Torque is not required to set the anchor.
1. Drill a hole to the required depth using a stop drill bit
matched to the anchor,(refer to specification table
and ordering info.). If rebar is encountered, use a Hilti
metric matched tolerance diamond core bit to drill
through the rebar.Remove the concrete core and finish drilling the hole with the stop drill bit.
4. The anchor is set with the hammer
drill in hammer drill mode. During
the setting procedure, both drilling
and impact energy are transferred to the
sleeve by the setting tool, causing the sleeve
to slide over the conical end of the anchor bolt
while forming the undercut in the base material. On
the setting tool, the red ring indicates the progress of
the setting operation. When this marking is flush with
the connected part, check the anchor for proper
setting (refer to step 5).
192 Hilti, Inc. (US) 1-800-879-8000 | www
.us.hilti.com
2. Clean hole with compressed air or a hand air pump
such that drilling debris is evacuated.
3. The anchor is inserted in the hole, so that the cone
sits on the bottom of the drilled hole. Do not remove
the plastic cap which protects the threaded rod.
Using the assigned setting tool and Hilti Hammer Drill
(Refer to spec. Table and Ordering Info.), the setting
tool is guided over the anchor rod and engages the
grooves in the sleeve.
specified Hilti hammer drills.
5. The mark on the anchor rod
provides the indicator for correct
setting. The anchor is set and the
undercut is fully formed when the red
marking on the anchor bolt is visible above
6. Remove the plastic thread protector cap. Secure the
part to be fastened by using the conical spring washer and nut provided. Apply a torque not to exceed the
maximum values given in the Specification Table.
Torque is not required to set the anchor.
the top edge of the sleeve.If anchor setting time
exceeds 40 seconds for M10 or M12 anchors or 60
seconds for M16 or M20 anchors, remove the anchor
(see HDA Removal Tool instructions). Install a new
HDA anchor.
I en español 1-800-879-5000 I Hilti (Canada) Corp. 1-800-363-4458 I www
.ca.hilti.com
It is critical to use the
echnical Guide 2006
oduct T
I Pr