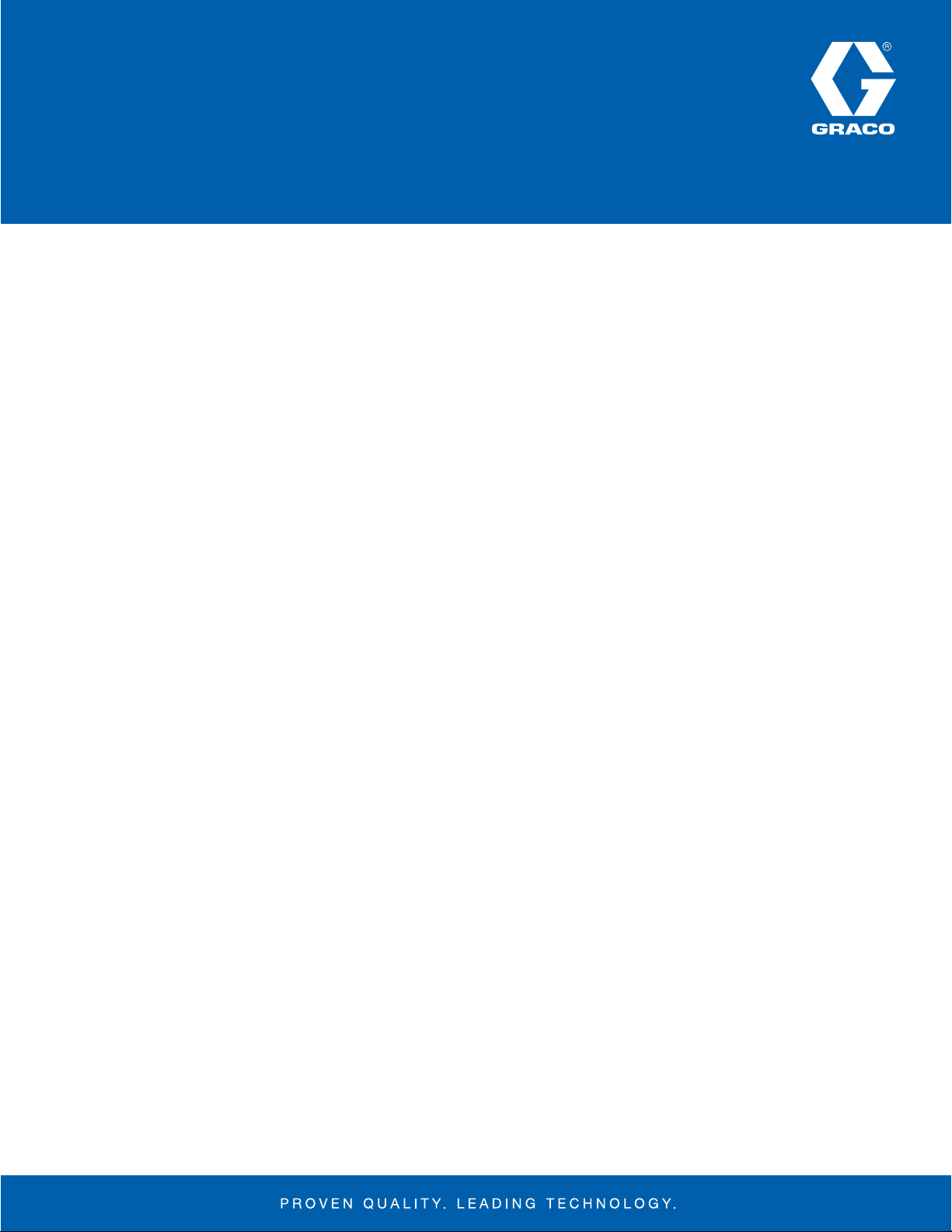
Manzel® Lube Line Alert
OPERATION
The alert can be used with any lubrication system to indicate low,
intermittent or steady flow. Air in any amount cannot be tolerated. For
maximum protection connect the alert in the lubricant line as close to the
terminal point as possible. The alert will detect flow or lack of low up to
and through it, but not beyond it.
One alert per pump will warn of flow stoppage for any reason, including
lack of lubricant in the reservoir, shaft rotation stoppage, broken lubricant
lines, contamination under pump valves or worn plungers.
A single lube line alert per lubricator compartment on an active pump will
warn of lack of lubricant in the reservoir, or shaft rotation stoppage. It
will warn of a broken lubricant line, contamination under the pump check
valve, or a worn plunger on the individual pump on which the alert is
mounted.
A single lube line alert per lubricator compartment on a special spare
pump having a shortened pump suction tube and returns the flow directly
to the reservoir, will warn of shaft rotation stoppage or low lubricant level
in the reservoir before the active pumps are out of oil. Note: Cannot be
used with Manzel Model 25 Lubricator.
INSTALLATION
Cut the lubricant line as close to the point of lubrication as practical.
Extreme care is needed to eliminate all dirt and lint. Install the alert using
caution to get proper flow direction, as shown on the name plate.
CHECK VALVES
Check valves should be used if the alert is going to be connected:
Directly down stream** of a lubricator pumping unit.•
Directly up stream* of a terminal check valve of lubrication point •
feeding a pulsating pressure source.
When a rupture relief or vent is directly up stream of the alert. •
That is, there is no check valve or divider valve between the alert
and the relief or vent.
Any system where the alert could be subjected to a sudden •
pressure or flow reversal.
Check valves are not necessarily required if the alert is in a lubrication
system:
Between the lube meter and divider valve.•
Between sets of divider valves.•
Between a pump manifold which has inlet check valves and no •
rupture relief and a lube meter or set of divider valves.
7/16-20 NF straight thread O-ring check valves and tube fittings are
available for various tubing and pipe thread sizes. See specification sheet
bulletin No. 54000 for connection.
ELECTRIC CIRCUITRY
The alert should not be mounted near strong magnetic fields, such as
large motors, since they may adversely affect the permanent magnet or
the magnetically actuated switch. The lead wires from the switch are
readily available through the 1/2" NPT conduit connection for wiring into
a suitable alarm or other circuit to handle electrical loads up to the rated
switch capacity.
For the normally open (NO) switch position, multiple alerts should
be wired in series or through separate circuits to provide fail-safe
circuitry. Note: The loose cover must be assembled over the exposed
machined face of the alert hydraulic body for proper Underwriters
Laboratory listing. For normally closed (NC) switch position, multiple
alerts should be wired in parallel or through separate circuits. Note:
Automatic start-up and shutdown circuits will require the use of a time
delay relay to lock out the alert circuit during start-up. A start-up delay
time of approximately sixty (60) seconds or longer is required on some
installations.
Caution: To reduce the risk of ignition of hazardous atmospheres
conduit runs must have a sealing fitting connected with 18 inches of the
enclosure.
ALERT ADJUSTMENT
Check the actual installation by operating the system. If the alert fails to
energize the circuit or continuously cuts in and out, see Troubleshooting.
If, when the system is shut down, the delay time (time from flow failure
to indication) is too long, the delay time can be reduced by adjusting
the switch housing body towards outlet. Adjustment should be made in
small increments, about 1/32" at a time. The final adjustment should
be checked out several times, since the total time delay is dependent
on the physical location of the inner parts of the alert at the time of the
flow stoppage. Excessive adjustment of the alert can result in failure to
energize the circuit.
If a longer or shorter time delay is needed than can be obtained with the
switch body adjustment, see Troubleshooting.
CONTAMINATION CONTROL
Alerts must be cleaned periodically. The frequency depends on the
cleanliness of the installation. Remove the hydraulic body from the
lubricant line, remove the inlet plug and tap the O-ring, bushing, plunger
magnet, and spring out through the inlet connection. Flush and blow out
all the passages. Wipe the magnet free of any iron dust.
Do not place the magnet on or near iron or steel. This may cause some
demagnetization, and affect the operation of the switch on reassembly.
Make sure the plunger is oriented in the bushing the same as in the
original assembly.
Note: The plungers and bushing are tested in matched sets at the
factory. DO NOT INTERCHANGE WITH OTHER PLUNGERS AND
BUSHINGS.
*Up Stream - toward the pump or supply source.
**Down stream - toward the outlet or terminal point.
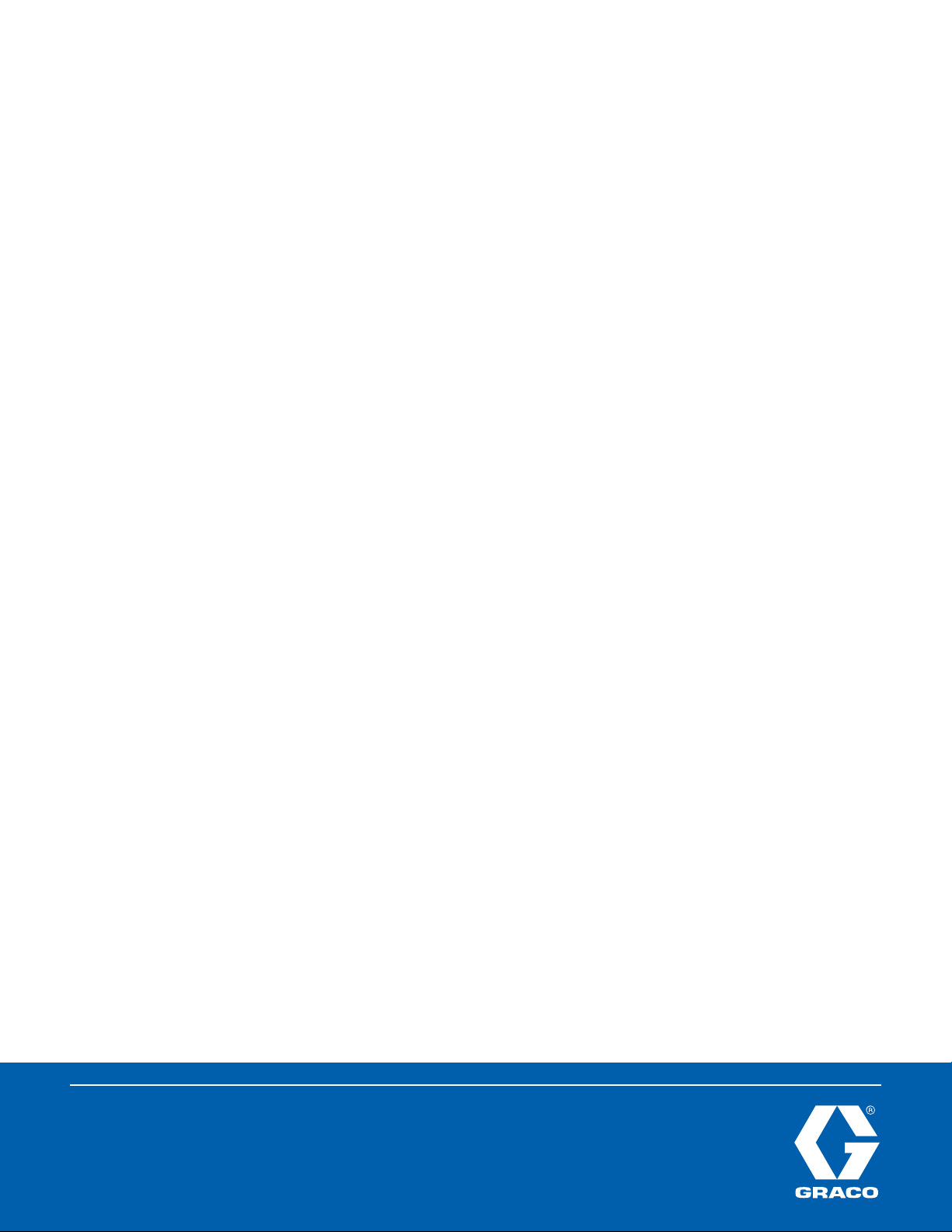
TROUBLESHOOTING
When contacting the Distributor, please specify delay code, oil viscosity,
operating temperature (ambient and maximum differential), flow rate (cc/
minute or drops/minute), pumping frequency, operating pressure, and
type of difficulty such as listed in II, III or IV following.
Delay CodeI.
Delay Code numbers are stamped in the left hand blue area of 1.
the name plate, above model number stamping space.
The numbers are the time delays in seconds (time from flow 2.
failure to signal). The top number is for NO circuit and the
bottom number of the NC circuit. This time delay in seconds
is the delay time this unit had during its production test.
This production test is done under strict specifications, i.e.,
oil viscosity held at a specific temperature, flow rate, pump
strokes per minute, etc.
The numbers are stamped on the assemblies to be used as 3.
a base reference point only. They are not the time delays
(time from flow failure to signal) that customers will get
on their actual installations. Operating conditions will
vary widely from those of the specific production test
specifications.
Failure to Actuate CircuitII.
Check flow from the lubricant line beyond the alert. If no flow 1.
occurs, check the lubricator pump unit and lubricant line for
trouble. If there is the required flow -
Check the switch body adjustment on the hydraulic body. The 2.
NC or NO mark on the hydraulic should be opposite the “0”
mark on the switch body. The “0” is the point at which this
switch activated based testing at the time of manufacture and
is a reference point only for this switch. Actual oil viscosity,
flow rates and oil temperature will cause shutdown time to
vary within a range of 60 to 180 seconds. It may be necessary
to move the switch body up or down to obtain the desired
shutdown time based on actual operating parameters.
If the above two check out and the circuit still does not 3.
actuate, check the dimension of the adjustment screw from
the outlet end of the alert. As shipped from the factory, this
dimension should be 17/32". To increase the delay time (time
from flow failure to signal), back the screw out not more than
1/4 turn at a time. This screw has a 20 pitch thread, so each
full turn backs the screw out .050 inches.
If the alert does not actuate with the required flow rate, or if 4.
it flashes and cannot be adjusted as above, remove the outlet
fitting and spring adjusting screw. Replace the original spring
with the lighter spring, and reset the screw to 17/32".
If the above procedures fail to correct the difficulty, check the 5.
delay code:
If the delay code is low (example: 65), replace the unit a.
with one having a higher delay code (example: 120).
If the delay code is high (example: 120), and the delay b.
time (time from flow failure to signal) is too long, replace
the unit with one having a lower delay code (example:
70-90).
Flashing or Sporadic Actuation of CircuitIII.
This can be caused by the flow rate being too low, the 1.
frequency between pump cycles being too long, or the fluid
viscosity being too low (normally due to high temperature). To
overcome the above, see Section II. C or II. D.
Switch or Circuit FailuresIV.
If this trouble is suspected;1.
Remove the four switch body bolts.a.
Slide the switch body back and forth across the face of b.
the hydraulic body. This should cause the test light or
circuit to go on or off.
If the test light or circuit does not flash on or off, check c.
the circuitry.
If the circuit is satisfactory, replace the switch body. The 2.
switch contacts are probably welded closed due to overload.
The new switch body will not have the "O" line. This can be
established by:
Oil flow to the alert must be stopped, and the alert a.
magnet and plunger must be at a no flow position.
With the circuit or test light energized, place the switch b.
body part way on the lower portion of the hydraulic body.
Slide the switch body along the hydraulic face until the c.
test light goes on.
Move the switch body 3/64" beyond the point where the d.
light goes on. Mark the "O" Line opposite the NC line.
The end of the switch housing must be flush or slightly
above the end of the hydraulic body. If necessary, turn
the switch body end over end to accomplish this.
After checking the NC - "O" position to orient the switch e.
body correctly, slide the switch body along the hydraulic
body until the test light goes out.
Move the switch body 3/64" beyond the point where the f.
light goes off.
The "O" line on the switch body should be opposite the g.
NO line. If they do not line up, but the NO line is within
1/64" above the "O" line, it can be used as the NO- "O"
line. If it is more than the 1/64" above the "O" line, then
the original NO line must be blocked out and a new NO
line established on the hydraulic body opposite the "O"
line on the switch housing.
Operate the system several times with the new setting to h.
double check the delay time and proper switch action.
All written and visual data contained in this document are based on the latest product information available at the time of publication. Graco reserves the right to make changes at any time without notice.
Contact us today!
To receive product information or talk with a Graco representative,
call 800-533-9655 or visit us online at www.graco.com.
©2006-2009 Graco Inc. Form No. L45370 Rev. B 3/09 Printed in U.S.A. All other brand names or marks are used for identification purposes and are trademarks of their respective owners. All written and
visual data contained in this document are based on the latest product information available at the time of publication. Graco reserves the right to make changes at any time without notice.