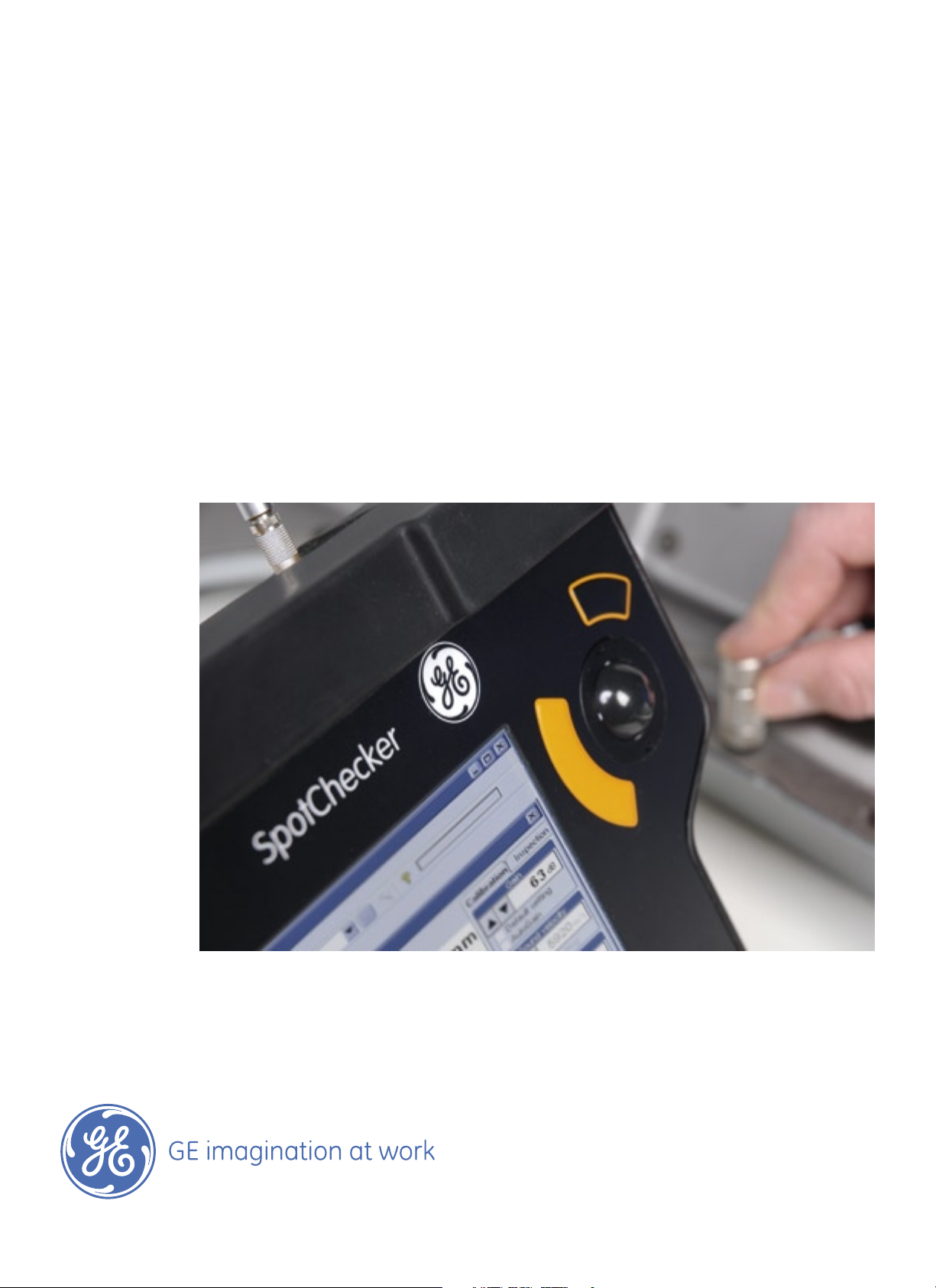
GE
Sensing & Inspection Technologies
SpotChecker
A Truly Mobile Solution for Spot Weld Testing
Offering Significant Gains in Productivity
SpotChecker combines the power of a computerized expert system with easy-to-use portability.
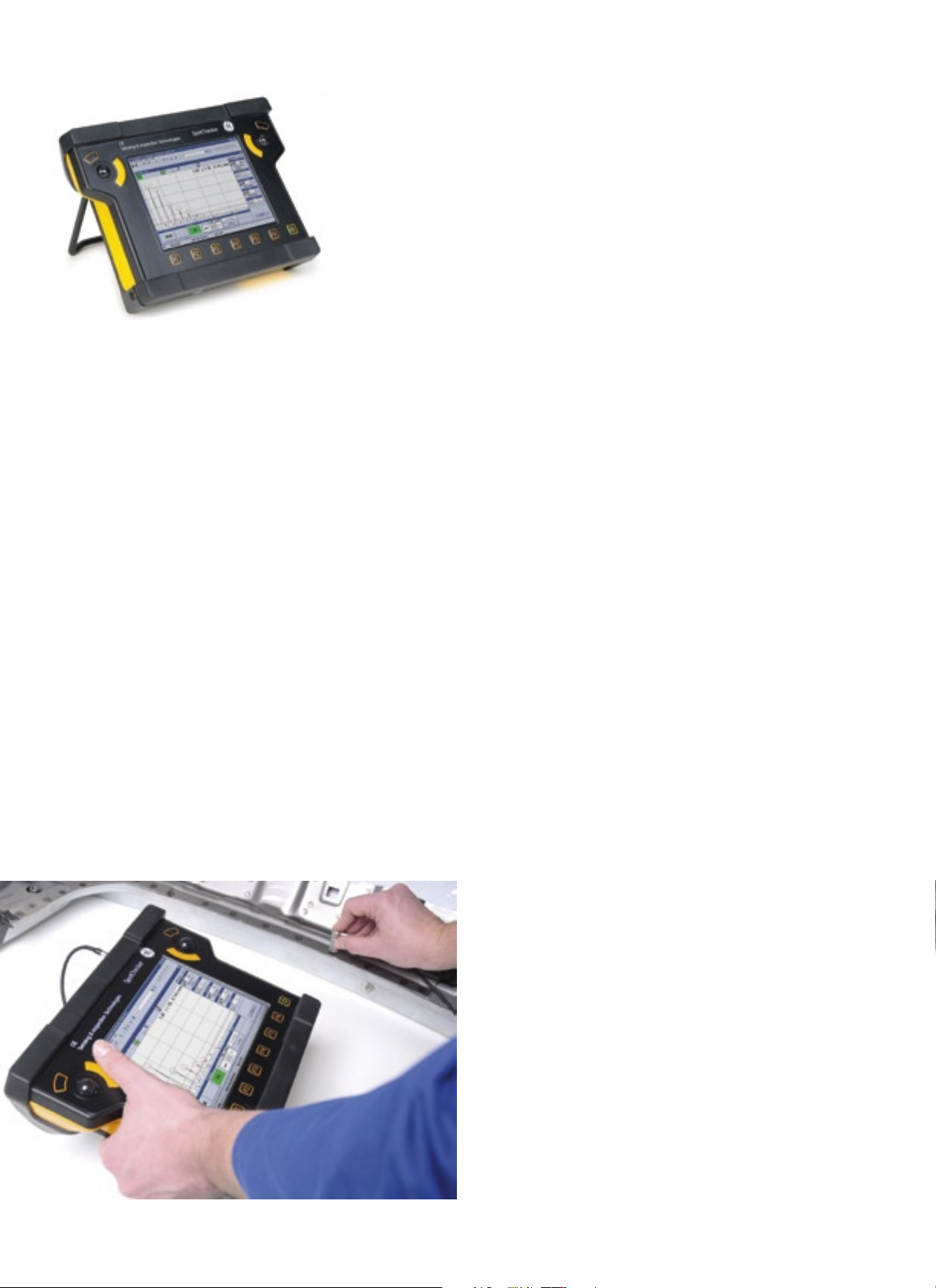
The SpotChecker :
A Hand-Held Flaw Detector
for Testing Spot Welds in
Situ on the Production Line
The range of joining methods used in automotive body
assembly lines has significantly increased in the last few
years. While formerly, resistance-welding and MIG/MAG
welds were the preferred joining methods, techniques such
as laser welding/soldering, bonding, etc, are also in common
use today. Since all of these processes can be used singly
and sometimes all together, this complexity places new
demands on test engineering. In addition to destructive
testing of spot welds, i.e. with a hammer and chisel, nondestructive testing with ultrasound has become routinely
applied in recent years. The increased acceptance of this
procedure is due in no small part to the decisive
advancements contributed by GE Sensing & Inspection
Technologies, working in close cooperation with the
automotive sector. Today ultrasonic spot weld checking is
a technique employed by major car manufacturers.
The SpotChecker allows to take spot weld checking right
onto the production line, saving time – and money.
Portable and Robust
SpotChecker weighs just 3.2 kg (7.05 lb), is battery operated and is
sealed to IP65. It features hot swap battery exchange to ensure
continuous operation. Battery charging can be done with batteries
inside or outside of the instrument, using an external charger.
Portability allows inspection to be carried out at the place of
welding or on the production line, with no need to transport
components to designated inspection stations. As a result, more
inspections can be carried out within the same time frame, which
means increased productivity.
Easy-to-Use
SpotChecker does not require intensive training but offers the
advantage of an “expert” system for people less qualified in weld
inspection. Its ergonomically designed operator interface features
an 8.4” LCD touch screen, six programmable function keys and twin
track balls, so that it can be operated simply and efficiently in the
most restricted of testing locations.
Connectivity
The flaw detector can be connected to external periphery devices
such as mouse, keyboard and printer by USB. The instrument can
also be connected to a PC wirelessly by WLAN or Bluetooth for data
up-and down-load.
A non-directional, user-friendly remote control, equipped with
programmable functions, provides extended flexibility. Intelligent
dialog probes, whose data is automatically recognized and loaded,
ensure 100-percent documentation accuracy and increased test
reliability in spot weld inspection.
Can be Integrated within
Quality Control Loops
By transmitting test results immediately and wirelessly to a suitable
database, it is possible to achieve accurate and reliable feedback to
adjust welding parameters and correct welding faults and eliminate
spotweld defects.