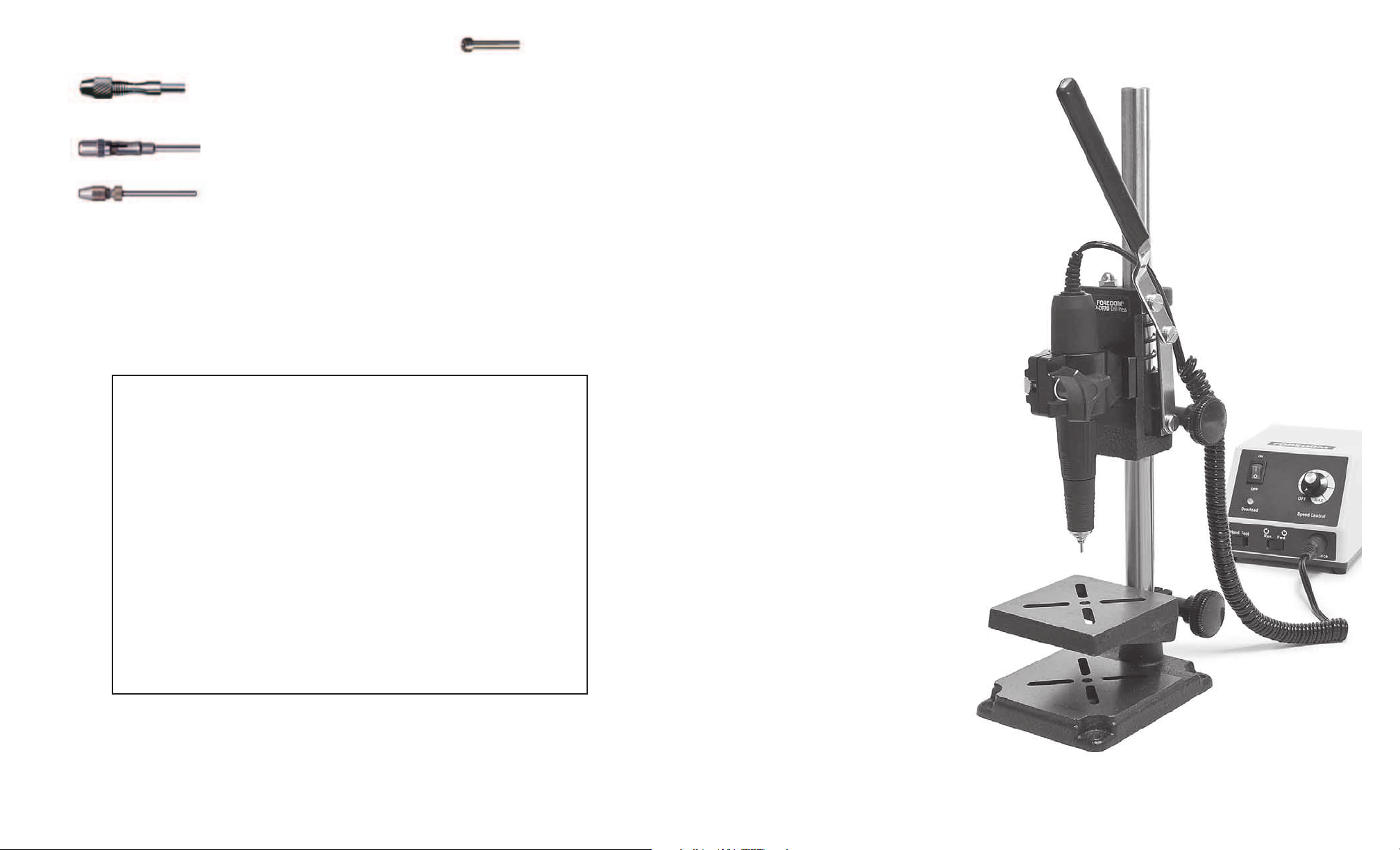
Optional Accessories for the P-DP70 Drill Press:
Micro Chucks –
A-MC2
An accurate, economical adapter chuck, used for 60 to 80
wire gauge drills. The A-MC2 can be held in any 1/8″ collet.
A-M50
for use with drills #70-80
A-M52
Holds 1/16″ shank friction grip burs and has a
3/32″ shank.
Micro Chucks must be used at lower speeds:
A-MC2 10,000 RPM maximum speed
A-M50 10,000 RPM maximum speed
A-M52 20,000 RPM maximum speed
Drills - visit www.foredom.net to learn more about our
broad selection of diamond, steel and cobalt drills.
Collet Adapters –
This is not a collet. It is a ‘step down’ adapter that fits inside
a collet and allows the use of smaller shank size accessories
without having to actually change the collet. Use in H.MH-
170 micromotor handpiece (also for exible shaft collet
style handpieces):
HPL4-3233 3/32″ to 1/16″
HPL4-3234 1/8″ to 1/16″
HPL4-3235 3.0mm to 3/32″
HPL4-3236 1/8″ to 3/32″
HPL4-3237 3.0mm to 1.6mm
For More Information:
For more information on Foredom® equipment and accessories, contact your local dealer. When no local dealer is
available, visit on line: www.foredom.net
®
FOREDOM
P-DP70
Owner’s
Manual
LIMITED WARRANTY
Foredom Electric Company warrants the P-DP70 Drill Press to be free of defects in material or
workmanship for a period of one year after purchase. During the warranty period, the defective
product will be repaired or replaced without charge or, at our option, the purchase price will be
refunded. This warranty does not cover damage caused in transit or by accident, misuse, or
ordinary wear.
ALL IMPLIED WARRANTIES, INCLUDING BUT NOT LIMITED TO WARRANTIES OF FITNESS
AND MERCHANTABILITY, ARE HEREBY LIMITED IN DURATION TO A PERIOD ENDING ONE
YEAR FROM DATE OF PURCHASE, AND WE WILL NOT BE LIABLE OR RESPONSIBLE FOR
ANY SPECIAL OR CONSEQUENTIAL DAMAGES.
Repair or replacement will be made at our option if the product is returned post-paid to:
Foredom Electric Company
16 Stony Hill Road
Bethel, CT USA 06801
All warranty repairs must be done at the factory at the above address. We will not pay any
shipping or transportation charges. This warranty only covers the original purchaser of the
product. Some states do not allow limitations on how long an implied warranty lasts, so the
above limitations may not apply to you. This warranty gives you specific legal rights, and you
may also have other rights which vary from state to state.
®
FOREDOM
Foredom Electric Company
16 Stony Hill Road, Bethel, CT 06801
Tel.: 203-792-8622 • Fax: 203-796-7861
Form 1240 bh Printed in USA
www.foredom.net
For Your Own Safety:
Always wear eye protection.
Read this Owner’s Manual
before operating your
Foredom tool.
Micromotor not included
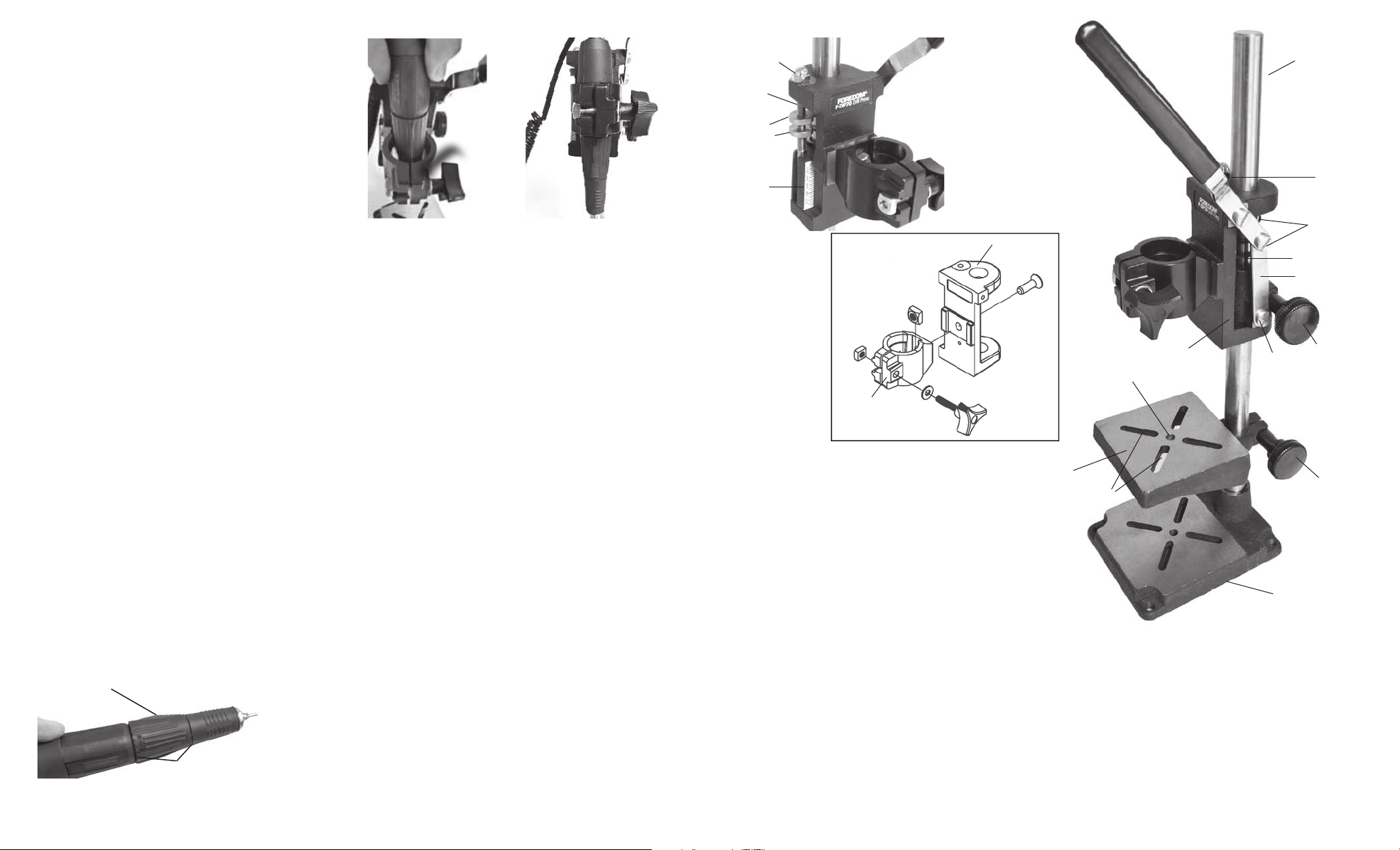
General Information
Foredom’s P-DP70 Drill Press is designed for use our High
Speed, Rotary Micromotor Handpiece– H.MH-170. It securely holds the handpiece in a vertical position for drilling
straight, accurate holes to specifi ed depths. It is also ideal
for modeling, spot-facing, countersinking and reaming in
wood, wax, plastic, metal, glass and gemstone.
Follow these Important
Safety Instructions:
Always wear safety glasses to protect eyes from fl ying
debris and chips.
Never continue to use a drill or accessory which appears to
be wobbling, out of round, vibrating or not running true.
Always use drills and accessories rated for 38,000 RPM or
higher.
Never wear loose clothing, dangling jewelry or other apparel
which may become caught in the equipment.
Always keep hands, fi ngers and hair well away from the drill
or other accessories.
Always bolt down the Drill Press for extra stability.
Set-Up and Operation
As you unpack the Drill Press, make sure that you have the
complete assembly (see photo). Loosen the Adjusting Knob
and move the Head Assembly up the Post to the desired
height. Tighten the Knob securely. Be sure that the head,
table and base are aligned and centered.
Foredom recommends bolting the drill press to the workbench or platform for extra stability. Insert suitable length
bolts through the four holes provided in the Base Plate.
Fasten to the workbench or to a piece of plywood approximately 2‘ x 2‘ x 3⁄4″.
Arm Adjustment
Test the downstroke action of the handle. This has been
preadjusted at the factory, but may have rattled loose during
shipping. It should feel smooth and free. If it feels too loose,
adjust the Shoulder Screws in the handle arm assembly.
These screws should be tightened snugly.
Inserting the Handpiece
2 knurled ‘wings’ on opposite
sides of the Locking Ring
H.MH-170
Locking Ring
The Locking Ring on the handpiece turns to Release or Secure
accessories in the collet. The ‘wings’ on the Locking Ring
Gap
Ï
should align vertically with the gap at the front and back of
the Handpiece Holder when inserting the H.MH-170
Micromotor handpiece. Loosen the mounting knob on the
holder and gently slide the handpiece into the handpiece
holder all the way until it is snug. The handpiece should fi t
so far down that the Locking Ring is below the Handpiece
Holder and can twist to open and close positions for changing
out accessories. Re-tighten the knob until the handpiece is
fi rmly held in place. Take care not to tighten and damage the
handpiece. You can now open the collet and insert the bur or
drill bit and close the collet to begin work.
Table Adjustment
Determine the desired table height for the thickness of the
material to be worked. When using a drill, make sure that
the drill tip is aligned with the center of the Table Drill Hole
by moving the drill gently through the hole while the motor
is still off.
Removing Adjustable Table
If you need to remove the adjustable table, the Head Assembly must be removed fi rst. Loosen the Head Adjusting Knob
and slide the Head Assembly up and off the Post.
Note: Make sure that you have a fi rm grip on the Head
Assembly before loosening the knob. It could be damaged
if allowed to drop. Place the head on the work surface,
handle side up. Repeat procedure with the Adjustable Table.
Replace the Handpiece Head Assembly onto the post and
tighten the Adjusting Knob, aligning head and base plate.
Drill Stroke Adjustment
Adjust the drill stroke depth from 0–1-1⁄4″ with Lock Nuts.
Move the Depth Stroke Indicator to the desired measurement on the Scale by pressing down on the handle. Hold at
desired setting and move Lock Nuts until the depth indicator
is stopped.
Securing the Workpiece
Slots are provided in the Adjustable Table and Base Plate for
use with clamps, jigs, and other holding devices. Make sure
the workpiece is securely fastened before beginning work.
Acorn Nut
DP10617
Threaded
Rod
DP10613
Depth
Lock Nut
DP10614
Scale
DP10605
Depth
Stroke
Indicator
Handpiece Holder
Assembly
Nut
UA10780
Handpiece
Holder
UA10786
Drill Press Head
Assembly
Nut
UA10781
Flat Washer
UA10421
Drill Press Head
DP10603MM
Screw
UA10782
Knob with
threaded stud
UA10776
Drilling
For drilling, generally high-speed steel, cobalt and diamond
drills are most often used. Whatever accessory you use,
let the speed of the tool do the work. Too much feeding
pressure can damage or break your drill, and may cause
loss of control. Twist drills are often used for drilling holes
in metals, woods, and plastics. On work items with rounded
surfaces such as rods, it is a good idea to centerpunch a
starting hole to keep the tip of the drill from “walking” or
wandering from the desired starting point.
When drilling, lift the drill up and down frequently to clear
away dust and chips.
Speed
Always use drills and accessories rated for 38,000 RPM or
higher. Generally, work speed is determined by experience
and varies with the type of material being drilled, the type of
drill or accessory, the thickness of the material, and the type
of work being done. Follow recommendations of the drill or
accessory manufacturer. Usually, higher speeds are used
on soft materials and lower speeds on harder materials. It is
always a good idea to experiment on a scrap piece of mate-
rial before beginning the fi nal work operation.
Coolants
Coolants are sometimes needed to help keep the accessory
Post
UA11030
Shoulder
Screws
DP10607
Spring
DP10612
Link
DP10606
Adjustable
Table
DP10602
Table Drill
Hole
Slots
Head Assembly
DP10603
Shoulder
Screws
DP10607
Base Plate
DP10618
cool and to keep the workpiece clean of debris. Which type
to use is determined by the material and the accessory and
will vary with operator preference. Wetting agents with rust
inhibitors, waxes, oils and water are often used when drill-
ing very hard materials such as metals, gems and stones.
Coolent must not be allowed to enter the handpiece.
Lubrication
All unpainted surfaces are sprayed with a rust inhibitor
when shipped. Be sure to clean away all debris after use.
Respray with rust inhibitor when necessary, especially during storage. The Spring and two Shoulder Screws should be
lubricated periodically with a light coat of oil.
Handle
DP10608
Adjusting
Knob
with spacer
UA11021/
UA11022
Adjusting
Knob
with spacer
UA11021/
UA11022