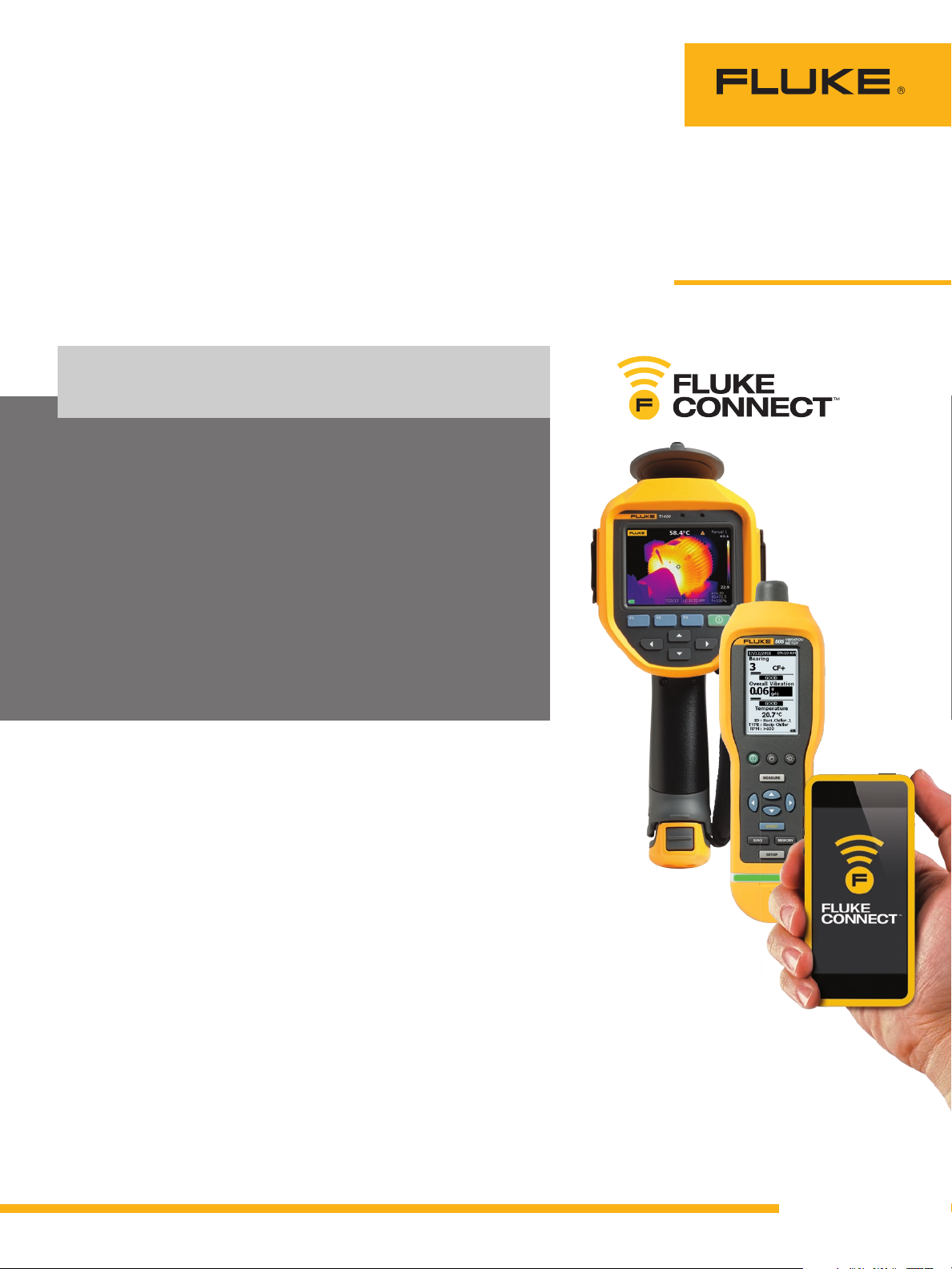
They are better
together—Ti400
Infrared Camera
and Fluke 805
Vibration Meter
If a tree falls in the forest . . . it makes a noise,
whether anybody’s there to hear it or not.
Just like that fabled tree, machines in trouble provide
telltale evidence to warn of impending problems—if
you just know how to look and listen. Two of the most
useful indicators are temperature and vibration. Most
mechanical components emit a certain amount of
heat and vibration in the normal course of operation.
But excessive heat, cold or vibration can tip you off to
underlying problems, so you can fix them before they
lead to breakdown and bring production to a halt.
New test tools such as the Fluke Ti400 Infrared
Camera and Fluke 805 Vibration Meter are available to
help measure heat and vibration and the 805 can help
interpret the data. They tell you what the underlying
problem may be and guide you in making repairs.
Application Note
Trouble heats up
An abnormally hot or cold spot
or an unusual thermal pattern
on process equipment often indicates an emerging problem. This
makes thermal cameras, which
capture two-dimensional images
of the apparent surface temperatures of objects, useful tools for
regular predictive maintenance
of mechanical, electrical and
other equipment. With thermal
imaging you can discover and
diagnose various issues including high-resistance electrical
connections that impede airflow,
bearing issues on motors and
tank levels, and many other
mechanical problems.
In a major Florida brewery,
scanning with a Fluke infrared
camera revealed that the gearbox of a bottle labeling machine
was running hotter than normal
– nearly boiling hot. A physical
inspection showed the box was
filled with water, not lubricant.
A damaged seal had allowed the
water in. A breakdown could
have shut down the bottling
line.
One way to prioritize infrared
scanning is to begin with the
critical assets whose failure
would threaten people, property or product. Then determine
what conditions add stress and
monitor those assets more frequently. For example, the sludge
and particulates found in many
processes put extra stress on
motors affecting bearings, windings and insulation. This stress
can show up as heat detectable by a thermal imager. Such
motors should be scanned for
fre q uently.
What to look for
Use your thermal imager to look
for hot and cold spots, as well
as other anomalies. Be especially aware of similar kinds
of equipment operating under
similar conditions, but at different apparent temperatures.
Such deviations might signal
a problem. A good approach is
From the Fluke Digital Library @ www.fluke.com/library
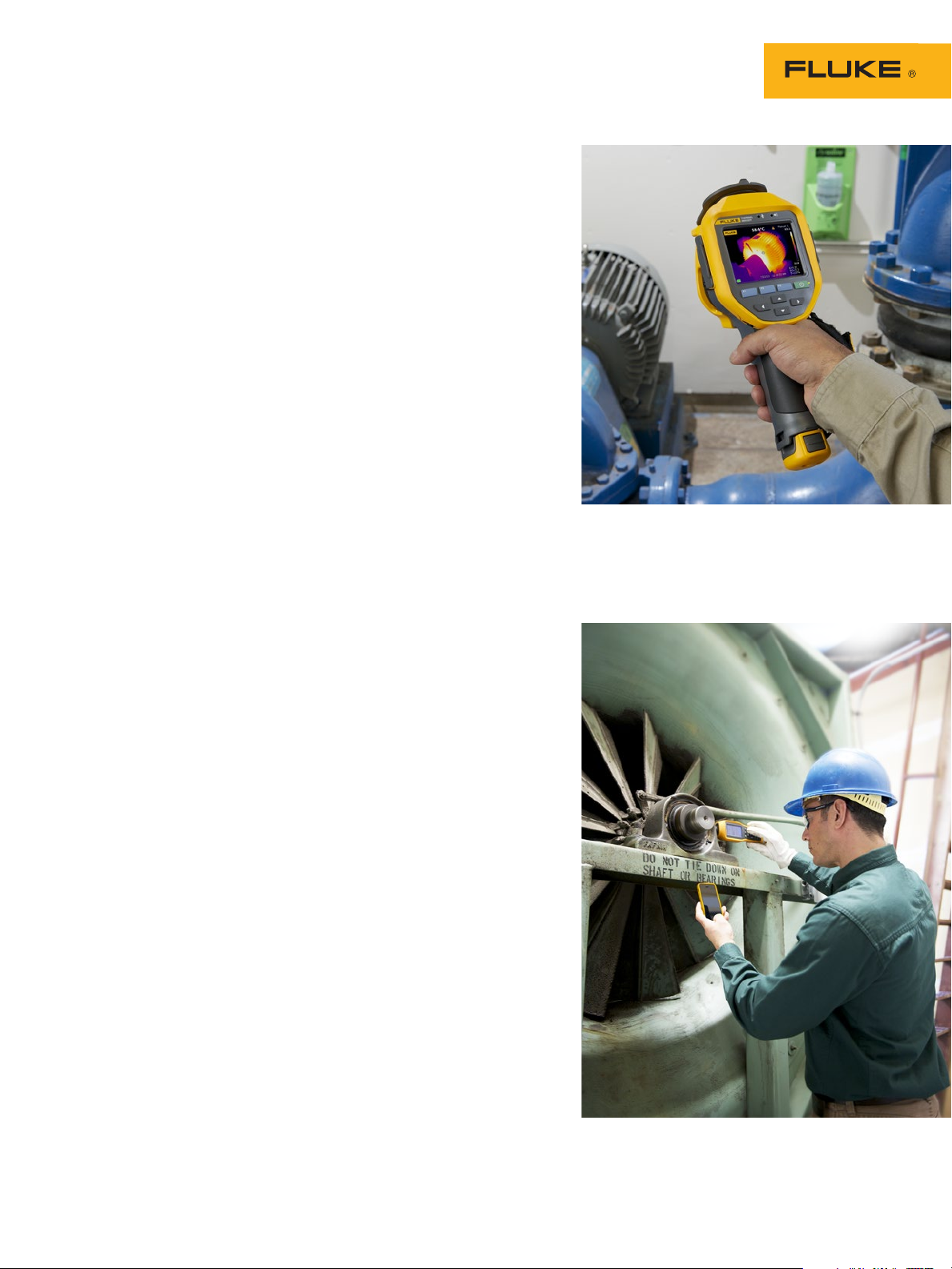
to create inspection routes that
include all critical assets using
Fluke Connect™ EquipmentLog™
history.
Using the EquipmentLog™
history feature you can create
a folder for each critical equipment asset with a description
of the asset and the location
in the Fluke Cloud™ storage.
Each time you inspect a piece
of equipment you or any other
team member who has been
given access, saves a thermal
image or measurement data to
that equipment folder, allowing
you and your team to track and
monitor the equipment condition
over time and getting instant
access to historical data – all
from one location. Now maintenance technicians can easily
do a side-by-side comparison
from previous inspections to
help determine whether a hot
spot or cool spot is unusual and
if any planned maintenance is
required. This keeps your equipment running longer, saving you
time and money and reduces the
risk of unplanned downtime.
When vibration shows
a problem
Vibration can be normal in
machine operation—or it can be
a sign of trouble. Most industrial devices are engineered to
operate smoothly and AVOID
vibration, not produce it. In electric motors, rotary pumps and
compressors, fans, and blowers,
low vibration is the ideal. In
these machines, vibration can
indicate problems or deterioration in the equipment.
But how can the plant
maintenance professional tell
acceptable, normal vibration
from the kind of vibration that
requires immediate attention,
to service or replace troubled
equipment?
Use vibration to screen
machine health
Unchecked machine wear
can quickly damage equipment, cause safety problems,
and degrade plant working
conditions. In the worst cases,
machine faults can knock equipment out of service and halt
plant production that cuts into
the bottom line.
When machines are screened,
vibration can be used in a
preventive maintenance program as an indicator of machine
condition, and you can target
remedial action before disaster
strikes. This gives maintenance
staff time to schedule repairs
and acquire needed parts.
Increased maintenance intervals
mean machine life is extended
and maintenance can be scheduled by need. Peace of mind
builds confidence in maintenance schedules, budgeting and
productivity estimates.
The hand-held Fluke 805
Vibration meter with Fluke
Connect ShareLive™ not only
measures machine vibration,
bearing impacting, and bearing temperature, but compares
the readings to 37 specific
machine categories—all while
letting you stay in direct contact with your team. This gives
the maintenance technician
critical information about the
machine health and warning
of bearing failures in a wide
variety of mechanical equipment, including motors, pumps,
fans, blowers, compressors and
more. You can reduce equipment downtime and costs with
the EquipmentLog™ history
function of the Fluke Connect™
app. With EquipmentLog™ you
can create unique folders for
individual machines, storing
historical inspection data that
can be accessed later by your
team. This allows side-by-side
comparisons of previous measurements so any accelerated
trends of degradation can be
identified to help determine how
quickly a repair is needed or if
it can be delayed to a more convenient time. Trending vibration
2 Fluke Corporation They are better together–Ti400 Infrared Camera and Fluke 805 Vibration Meter

readings over time will help you
to know which machines need
to be scheduled for repair before
a simple bearing failure leads to
the loss of the shaft, loss of the
machine, or loss of production.
Instead of complicated vibration analyzers that require an
experienced vibration expert to
analyze complex waveform data,
the vibration meter is a tool that
a maintenance technician with
no formal vibration analysis
training can use to screen the
many machines in the plant.
The Fluke 805 quickly screens
vibration in order to let the
user know which machines are
healthy and which ones need
repairs and with the Fluke Connect ShareLive video call feature
you can get questions answered
or work authorized in an instant
without even leaving the field.
3 Fluke Corporation They are better together–Ti400 Infrared Camera and Fluke 805 Vibration Meter
Fluke. Keeping your world
up and running.
Fluke Corporation
PO Box 9090, Everett, WA 98206 U.S.A.
Fluke Europe B.V.
PO Box 1186, 5602 BD
Eindhoven, The Netherlands
For more information call:
In the U.S.A. (800) 443-5853 or
Fax (425) 446-5116
In Europe/M-East/Africa +31 (0) 40 2675 200 or
Fax +31 (0) 40 2675 222
In Canada (800)-36-FLUKE or
Fax (905) 890-6866
From other countries +1 (425) 446-5500 or
Fax +1 (425) 446-5116
Web access: http://www.fluke.com
©2014 Fluke Corporation.
Specifications subject to change without notice.
Printed in U.S.A. 4/2014 6002682A_EN
Modification of this document is not permitted
without written permission from Fluke Corporation.
®