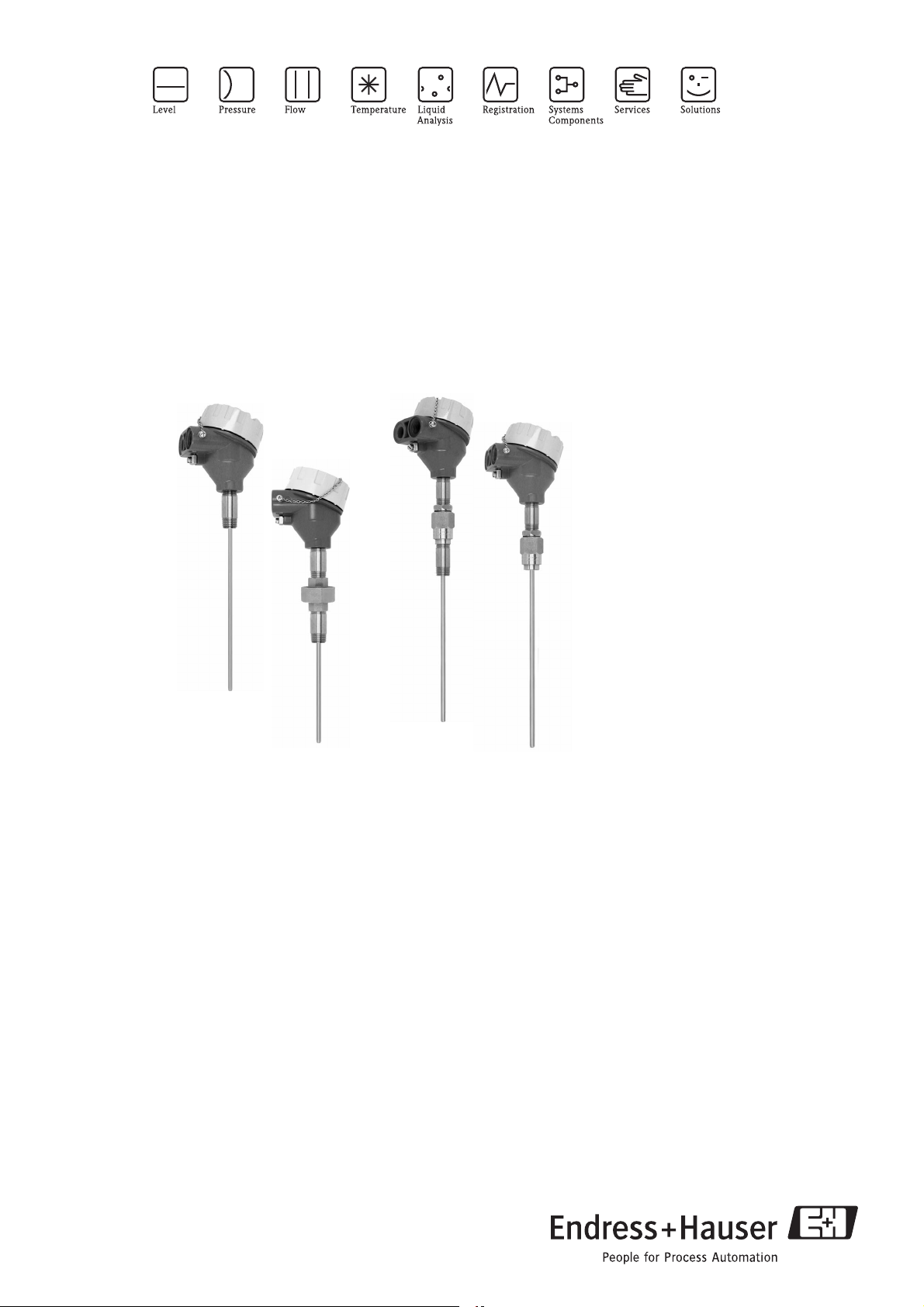
Technical Information
Omnigrad S -TC62
Thermocouple thermometer EEx-d certified, replaceable inset , complete
from nipple and union to thermowell connection.
PCP (4...20 mA), HART® or PROFIBUS-PA® electronics
Range of uses
The Omnigrad S TC62 is an industrial thermometer (thermocouple TC: K or J) with a replaceable inset and a neck without
thermowell.
It is developed for heavy duty and/or generic industrial applications, assembled with a thermowell from bar stock or pipe.
In compliance to EN 50014/18/20 (ATEX certification) it is
therefore particularly suitable also for hazardous areas.
When required, it’s also available with a transmitter
(PCP, HART® or PROFIBUS-PA®) into the housing.
The TC62 is available in several standard versions and different
configurations, can also be configured with specific dimensions
and characteristics depending on process requirements.
The installation on the plants, require separately order of the
thermowell (form pipe or from bar-stock).
Application areas
• Chemicals industry
• Energy industry
• Gas Processing industry
• Petrochemical industry
• General industrial services
TI286T/02/en
Features and benefits
• Customized immersion length
• Aluminium housing, with protection grade from IP66 to IP68
• Thermocouple with hot junction grounded or ungrounded in
mineral oxide cable (MgO cable) diameter: 3 or 6 mm
• PCP, HART® and PROFIBUS-PA®,
(4...20 mA 2-wire transmitters)
• The accuracy of the thermocouple TC (K (NiCr-Ni)
and J (Fe-CuNi)) are:
Cl. 1 - 2 (EN 60584) or Cl. Special - Standard (ANSI MC96.1)
• The thermocouple TC (K or J) are available in single or double
element
• ATEX II 2 GD EEx-d IIC certification
4 0
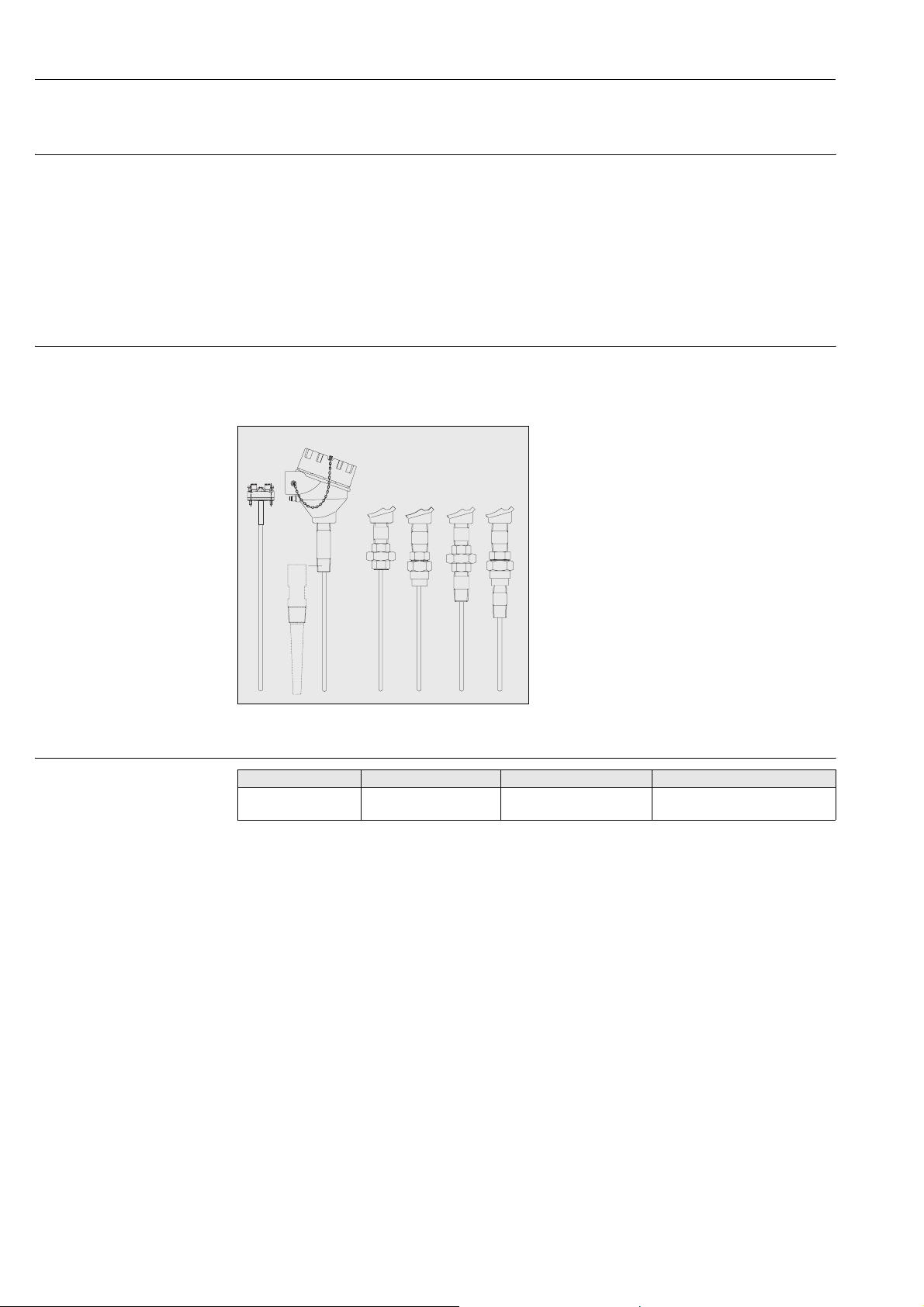
Omnigrad S TC62
Function and system design
Measuring principle The thermocouple (TC) thermometer’s sensing element consists of two metal wires that are homogeneous but
different one from the other and insulated along their entire length. The two wires are welded together at one
end, known as the “measurement or hot junction”. The other end, where the wires are free, is known as the
“cold or reference junction” and is connected to a electromotive force measurement circuit where the force is
generated by the different thermoelectric power of each of the thermocouple’s wires if there is a temperature
difference between the hot joint (T1) and the cold joint (Seebeck effect). The cold junction has to be “compensated” with reference to the temperature of 0°C (T0). The function that links the electromotive force to the
temperatures T1 and T0 is a curve whose characteristics depend on the materials used in the construction of
the thermocouple. Some thermocouples curves, and particularly those most reliable for the purposes of industrial readings, are those compliant with standards EN 60584 and ANSI MC96.1.
Equipment architecture The construction of the TC62 temperature sensor is based on the following standards:
• EN 50014/18 (housing)
• Neck (Nipple and 3 elements)
• EN 60584 (insert).
The housing is in painted aluminium alloy; it is suitable
to contain a transmitter and/or the ceramic block of
the inset; the “Ingress Protection” is from IP66 to
IP68.
The neck composed by one or two nipple and one "3
union", standard or EEx- execution, it is the extension
between the head and the thermowell on the process.
The replaceable insert is placed inside the thermowell;
the insert is spring loaded to its base in order to
improve heat transfer.
The hot junction of the thermocouple (type K or J) are
positioned close to the tip of the probe. The thermocouple is available in two versions: grounded or
ungrounded hot junction. The electrical structure of
the thermocouple always complies with EN
60584/61515 or ANSI MC96.1/ASTM E585 standard rules.
Fig. 1: TC62 with the various types of thermowell connections and end parts of the probe
Material & Weight
Housing Insert Extension neck Weight
aluminium epoxy
coated
sheath in SS 316L/1.4404
Inconel®600/2.4816
SS 316/1.4401 or A105 From 0.5 to 1.0 kg for standard
options
2 Endress+ Hauser
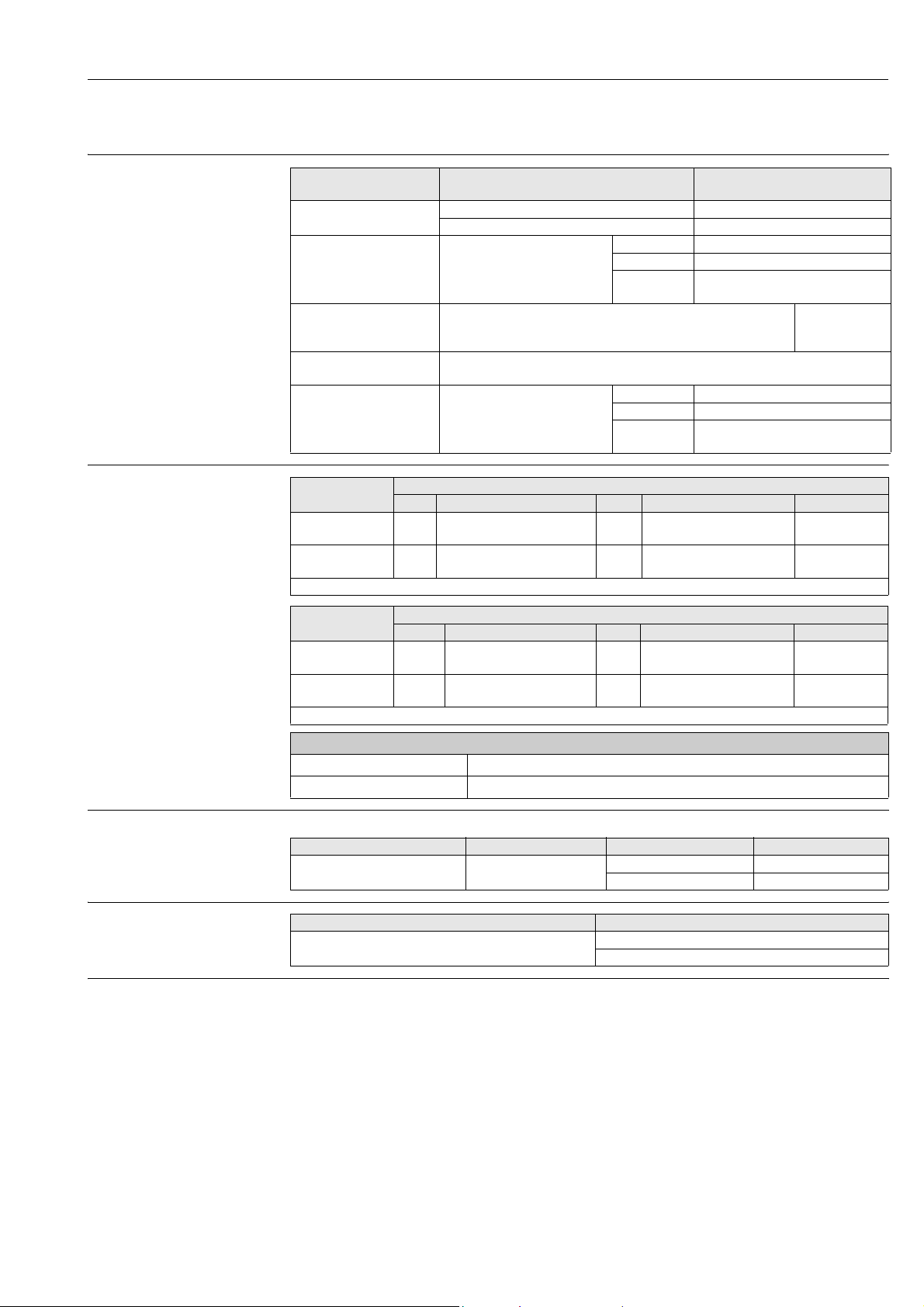
Performance
Omnigrad S -TC62
Operating conditions
Accuracy
Operating condition or
test
Ambient temperature housing (without head-mounted transmitter -40÷130°C
Process temperature It is restricted by the thermowell
Process pressure
(Maximum)
Maximum flow velocity The highest flow velocity, (of the stream or of the fluid), tolerated by the thermowell,
Shock and vibration resistance test
Thermocouple
and range °C
J (Fe-CuNi)
-40° ... 750°C
K (NiCr-Ni)
-40 ... 1200°C
Thermocouple
and range °C
J (Fe-CuNi)
0 ...750°C
K (NiCr-Ni)
0...1250°C
Product type or rules Value or data of test
housing (with head-mounted transmitter) -40÷85°C
< 600°C SS 316L/1.4404
material:
The pressure values to which the thermowell can be subjected at the
various temperatures. Example: for 9 mm diameter pipes, with a limited flow velocity, the maximum tolerated pressures are the following:
diminishes with increasing lengths, of the thermowell/probe exposed.
TC Inset in according to the rule
IEC 60751:
Class Max deviation Class Max deviation Cable colors
2 +/-2.5°C (-40...333°C)
+/-0.0075 |t| (333...750°C)
2 +/-2.5°C (-40...333°C)
+/-0.0075 |t| (333...1200°C)
ItI = absolute temperature value in °C
Class Max deviation Class Max deviation Cable colors
Stand-
ard
Stand-
ard
+/-2.2°C (0...293°C)
+/-0.75%o(293...750°C)
+/-2.2°C (0...293°C)
+/-0.75%o(293...1250°C)
ItI = absolute temperature value in °C
< 800°C SS 316Ti/1.4571
< 1100°C Hast.® C276/2.4819 -
Inc.600®/2.4816
50 bar to 20°C
33 bar to 250°C
24 bar to 400°C
Acceleration 3 g of peak
Frequency from 10Hz to 500Hz and back
Time of the
test
EN 60584
1 +/-1.5°C (-40...375°C)
1 +/-1.5°C (-40...375°C)
+/-0.004 |t| (375...1000°C)
ANSI MC96.1
Special +/-1.1°C (0...275°C)
Special +/-1.1°C (0...275°C)
10 hours
+/-0.004 |t| (375...750°C)
+/-0.4%o(275...750°C)
+/-0.4%o(275...1250°C)
+ black
- white
+ green
- white
+ black
- red
+ yellow
- red
Others errors
Transmitter maximum error See the corresponding documentation (codes at the end of the document)
Display maximum error 0.1% FSR + 1 digit (FSR = Full Scale Range)
Response time Tests, with the TC insert, in water at 0.4 m/s (according to IEC 60751) from 23 to 33°C:
Stem diameter of the insert Sensing element type Temperature of test Response time
Insulation
SS 316 - d. 6 mm K (NiCr-Ni), J (Fe-CuNi) t
Measurement Insulation type Result
Insulation resistance between terminals and probe sheath
according to EN 60584, test voltage 500 V
50
t
90
> 1GΩ at 25°C
> 5 MΩ at 500°C
2,5 s
7,0 s
Self heating Negligible when the E+H iTEMP® transmitters are employed.
Endress+Hauser 3