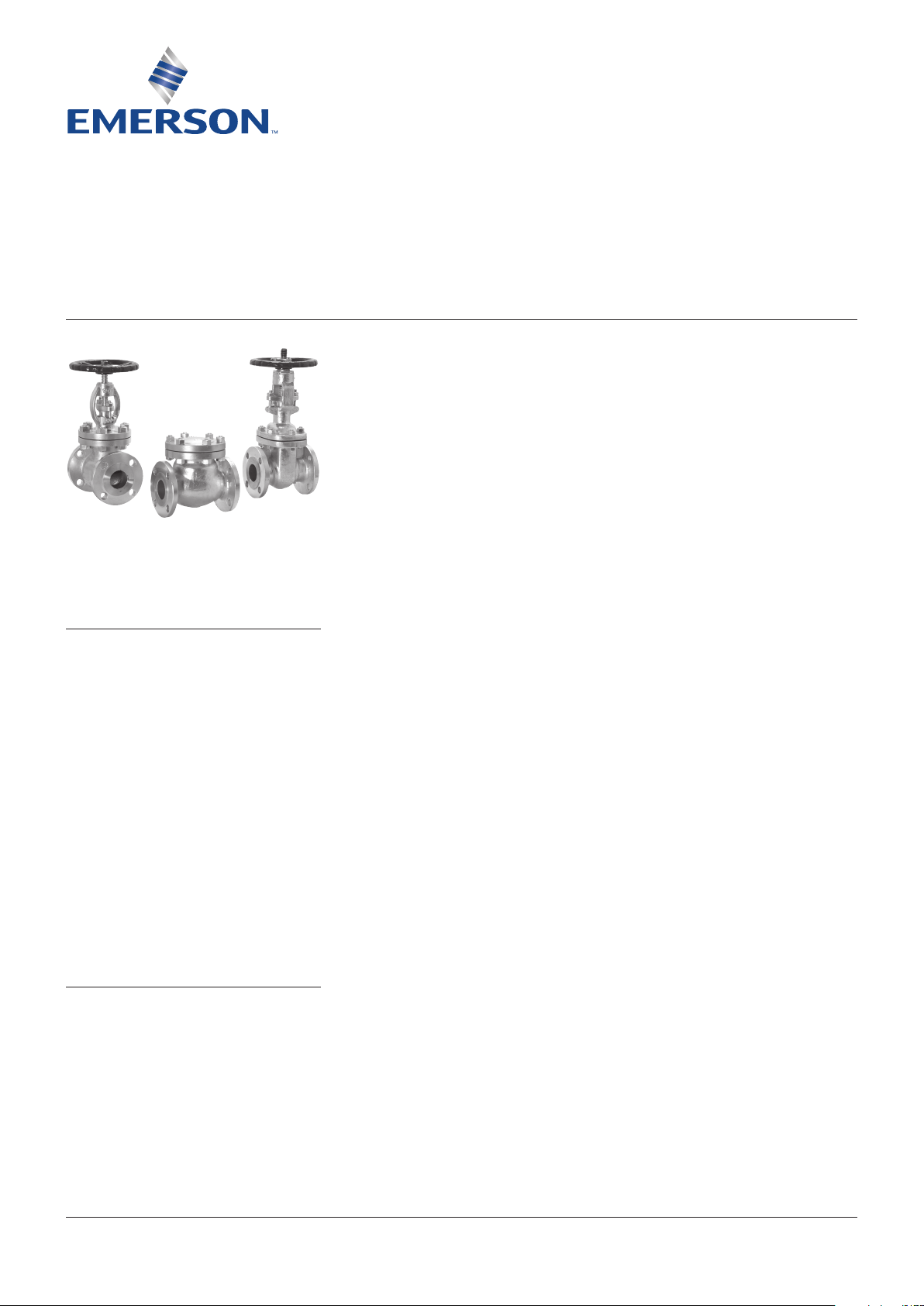
HANCOCK CAST STEEL - GATE, GLOBE AND CHECK VALVES
INSTALLATION, OPERATION AND MAINTENANCE INSTRUCTIONS
Before installation these instructions must be fully read and understood
1.2 Inspection
Before carrying out a valve installation, it is
important to determine whether the valve is in
asatisfactory condition.
The following generally applicable procedure
may be helpful in avoiding subsequent valve
problems and should be observed.
a) Carefully unpack the valve and check tags,
identification plates, direction of rotation
of handwheels etc, against bill of material,
specifications, schematics etc.
b) Make a point of noting any special warning
Instructions for DN 50 - 600 (NPS 2 - 24)
ASMEclass 150, 300 and 600 bolted bonnet
caststeel valves.
SAFETY NOTICE
It is essential that a safe system of work
should be adopted before any maintenance
work is done on a valve. The following safety
considerations should be taken in to account
when preparing maintenance instructions.
Before removing valves from a pipework
system or dismantling a valve to carry out
maintenance, it will be necessary to open,
or partially open, the valves and to flush the
system to remove all traces of dangerous
fluidsand pressures.
It is important to recognize the danger
associated with the removal of the stem
packing gland with pressure in the pipework
system and the use of the backseat should not
be regarded as a device permitting repacking
of the stem packing gland whilst the valve
is under pressure as this is recognized as
dangerous practise.
tags or plates attached to or accompanying
the valve, and take any appropriate action.
c) Check the valve for any marking indicating
flow direction. If the flow direction is
indicated, appropriate care should be
exercised to install the valve for proper
flowdirection.
d) As far as is practicable, inspect the valve
interior through the end ports to determine
whether it is reasonably clean, free from
foreign matter and harmful corrosion.
Remove any special packing materials,
such as blocks used to prevent disk
movement during transport and handling,
and anti-corrosion packs. Wipe clean from
preservation coatings, particularly seatings.
e) If practicable, cycle the valve through open
and close. Check guides or seat faces, etc.
f) Immediately prior to valve installation,
check the pipework to which the valve is
tobe fastened for cleanliness and freedom
from foreign materials.
1 GENERAL INSTALLATION INSTRUCTIONS
1.1 General
The installation procedure is a critical stage in
the life of a valve and care should be taken to
avoid damaging the valve.
© 2017 Emerson. All Rights Reserved.Emerson.com/FinalControl VCIOM-02504-EN 19/04
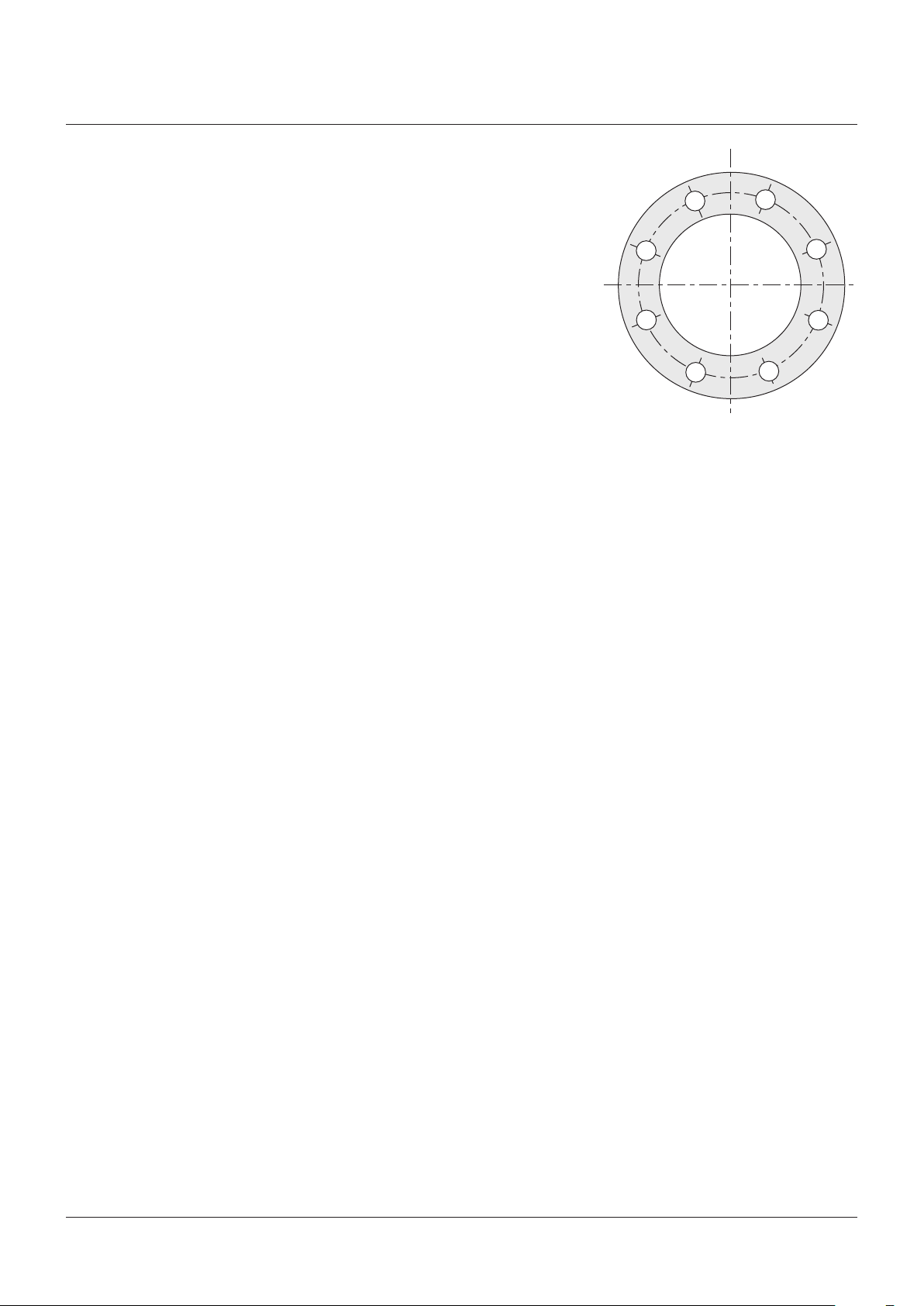
HANCOCK CAST STEEL - GATE, GLOBE AND CHECK VALVES
INSTALLATION, OPERATION AND MAINTENANCE INSTRUCTIONS
1.3 Flanged joint assembly
Pipe flanged joints depend on compressive
deformation of gasket material between the
facing flange surfaces for tight sealing.
In order to obtain satisfactory flange joints,
thefollowing points should be observed.
a) Check the mating flange facings (both valve
and pipework flanges) for correct gasket
contact face, surface finish and condition.
b) Check the bolting for proper size, length
and material. A carbon steel bolt on a high
temperature flange joint can result in early
joint failure.
c) Check the gasket material. For flange joints
using low strength bolting, such as may be
provided for iron flanges, metal gaskets
(flat, grooved, jacketed, corrugated or spiral
wound) should not be used.
d) Check the gaskets for freedom from defects
or damage.
e) Take care to provide good alignment of
the flanges being assembled. Use suitable
lubricants on bolt threads. In assembly,
sequence bolt tightening to make the initial
contact of flanges and gaskets as flat and
parallel as possible. Tighten gradually and
uniformly to avoid the tendency to twist one
flange relative to other.
f) Parallel alignment of flanges is especially
important in the case of the assembly of a
valve in to an existing system. It should be
recognized in such instances that, if the
flanges are not parallel, it will be necessary
to introduce bending to make the flange
joint tight. Simply, forcing the flanges
together with the bolting may bend the pipe,
or it may bend the valve.
g) All bolts shall be tightened in a star
pattern as shown below to ensure uniform
gasketloading.
1.4 Butt weld joint assembly
All welding should comply with the appropriate
pipe system or application code. Welded
joints, properly made, provide a structural
andmetallurgical continuity between the
pipeand the valve body.
Butt welds require full penetration and
thickness at least equal to that of the pipes.
If a pipe of high strength alloy is welded to a
valve with body material of lower mechanical
strength, the weld should taper to a
compensating greater thickness at the valve
end, or the valve should have a matching high
strength welded-on extension.
Particular care is necessary when welding
valves into the line. Considerable distortion,
resulting in line strains, may occur if valves
are not welded into the line with care, where
required, the weld properly stress relieved,
but it is necessary to ensure that such stress
relieving does not result in valve components,
particularly the seatings being subjected to
unacceptable temperatures.
It is recommended that the valves are not
installed in the pipework at points of high
bending moments, as this can adversely
affectthe seating performances.
1.5 Testing and adjustment
Following installation, all valves should
be operated to check that they still
functioncorrectly.
On new pipework systems, system pressure
testing and commissioning follow after
installation when various checks are made.
Valves are usually supplied in the lubricated
condition, but it is recommended that checks
are made to ensure that this is still intact,
particularly after the application of heat
(e.g.welding operation).
A first observation can be made by actuating
the valve through an open-close or
close-opencycle.
It is common practice, after installation of
pipework systems, to clean the system by
blowing with a gas or steam or flushing with
a liquid to remove debris and / or internal
protective films and coatings. It should be
recognized that valve cavities may form a
natural trap in a pipework system and material
not dissolved in or carried out by the flushing
fluid may settle in such cavities and adversely
affect valve operation. Also, abrasive material
carried by a high velocity fluid stream may
cause serious damage to seating surfaces.
Do not subject the valve to pressures/
temperature testing in excess of its
statedlimits.
1
8
4
6
BOLT TORQUING SEQUENCE
1-2-3-4-5-6-7-8
5
3
7
2
2