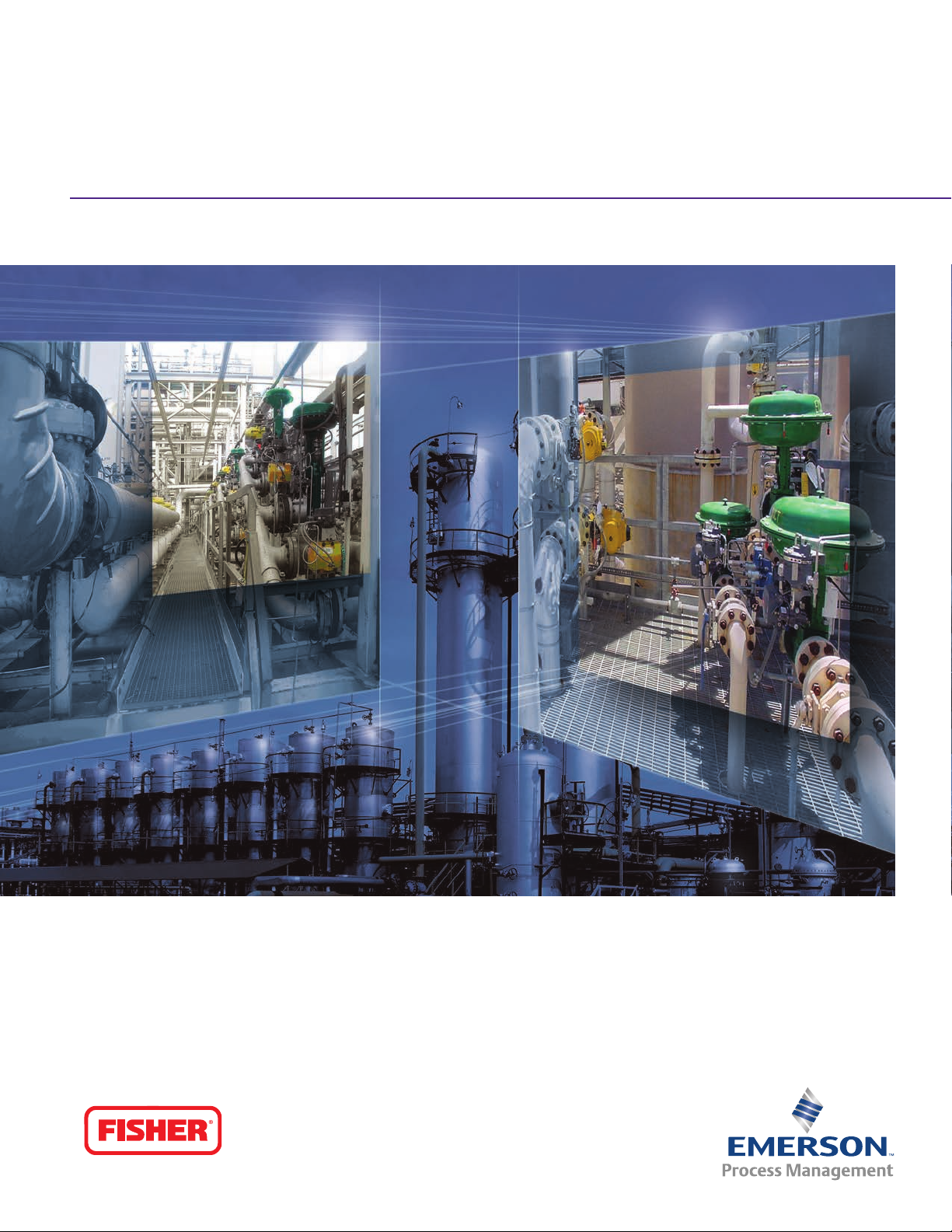
For Nonstop Operation of High-Cycle Applications
Use Fisher Control Valve Assemblies
®
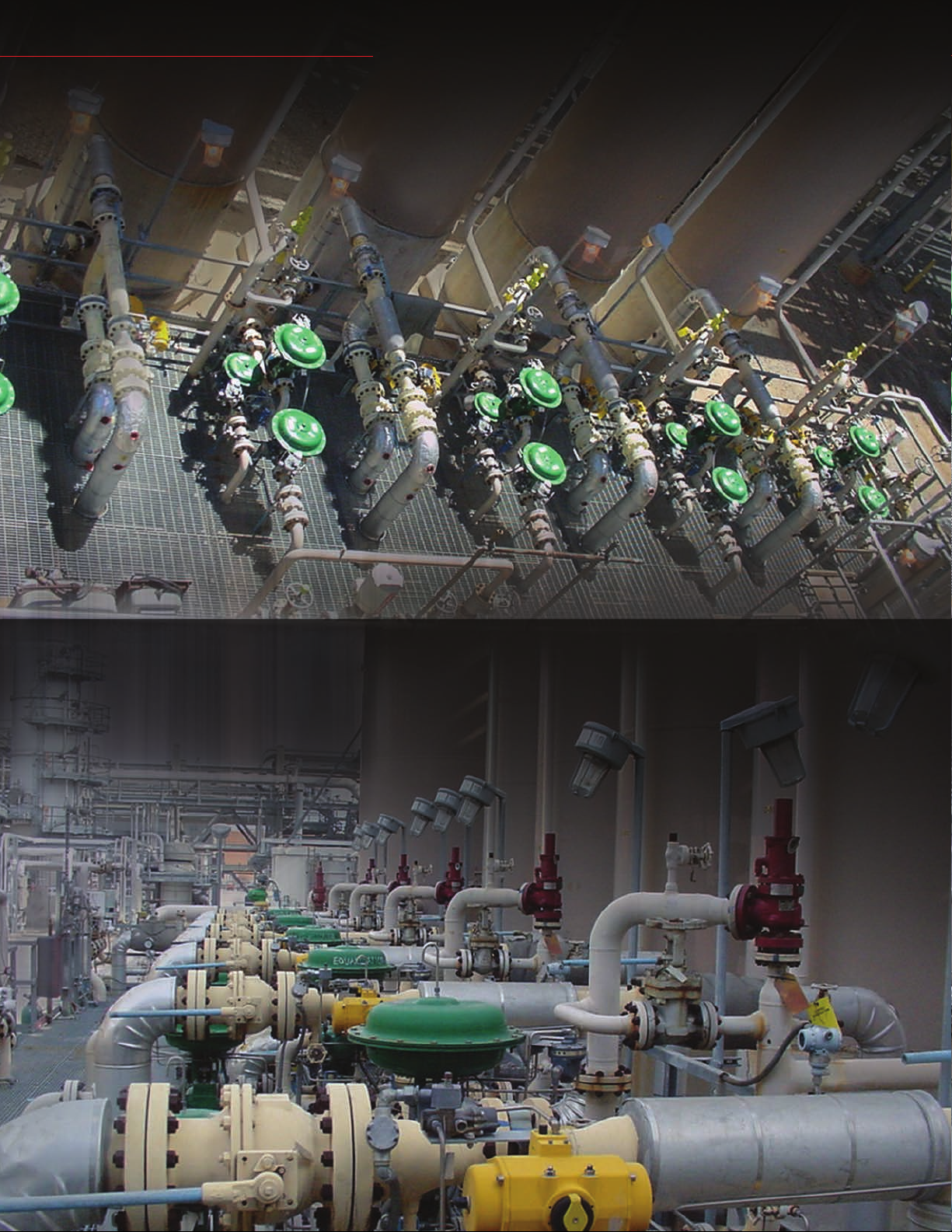
2 | Nonstop High-Cycle Applications
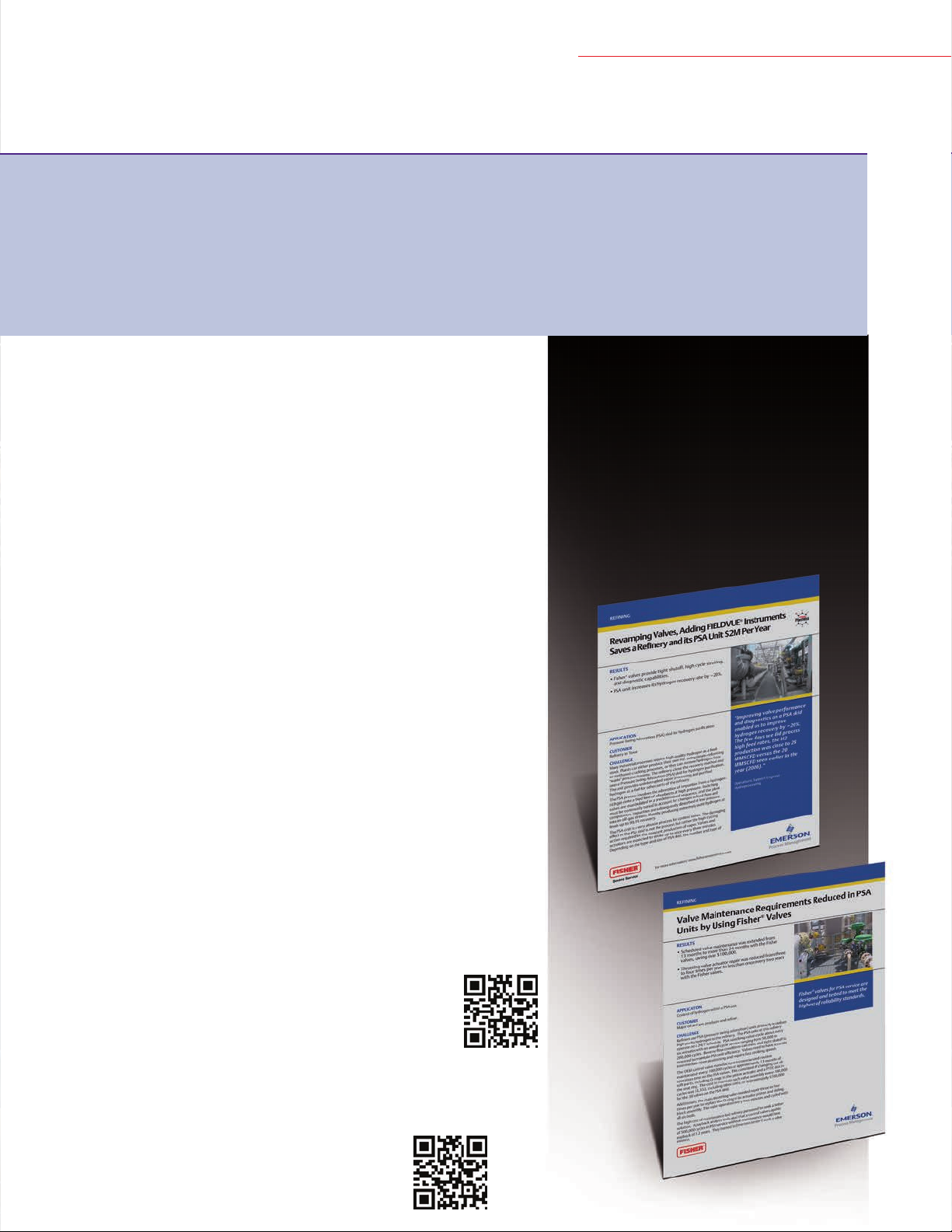
For Nonstop Operation of High-Cycle Operations,
Use Fisher Control Valve Assemblies
Nonstop High-Cycle Applications | 3
igh-cycle applications such as pressure swing adsorption
H
and molecular sieve adsorption are very abusive on control
valve assemblies. Stroking frequency exceeds 60,000 cycles
per year and tight shutoff to Class V or Class VI is required to
maintain industrial gas purity and efficiency.
Proper selection of control valve assemblies is imperative.
®
control valve assemblies typically consist of the control
Fisher
valve, an actuator, and a digital valve controller.
Incorporating Fisher control valve assemblies from Emerson into
your high-cycle applications can have significant benefits.
Improve Reliability – End users have increased turnaround
schedules to five years using Fisher control valve assemblies.
Their long-term reliability is demonstrated by rigorous testing to
more than 1,000,000 cycles and they are licensor accepted.
Improve Uptime – When you use Fisher control valve
assemblies you can expect to see improvements in uptime,
as they are engineered to meet high-cycle application
requirements. The durability of their mechanical moving parts
and soft parts is the key to long periods of operation.
Read how Emerson’s Fisher
control valve assemblies have
helped customers with their
high-cycle applications.
These proven results flyers
provide solid, quantifiable
results from real customers.
Improve Purity – Higher quantities of on-specification industrial
gas can be produced using Fisher control valve assemblies that
maintain tight shutoff throughout their lifetime.
In addition to providing top quality, expertly engineered
control valve assemblies, Emerson offers application assistance,
responsive replacement parts service, and training.
Revamping Control Valves and
Adding FIELDVUE Instruments
Saved a Refinery and its PSA
Unit $2,000,000 Per Year
Control Valve Maintenance
Requirements Reduced in PSA
Units by Using Fisher Valves
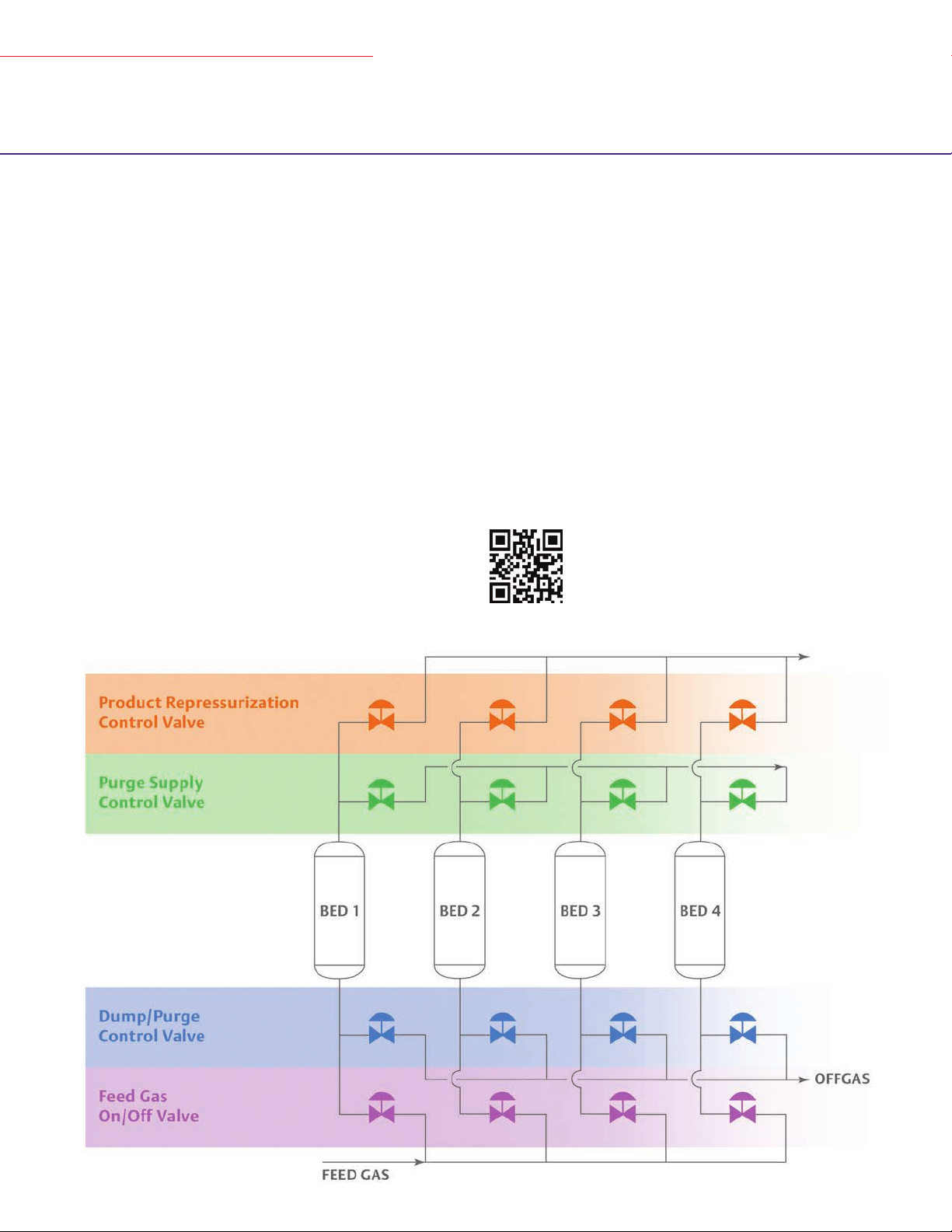
4 | Nonstop High-Cycle Applications
Applications Discussion
Pressure Swing Adsorption (PSA)
PSA is a process that involves separating impurities from
a feedgas mixture to produce a single product gas such as
hydrogen, oxygen, or nitrogen.
Feedgas cycles through fixed-bed adsorbers, which are
surrounded by control valves that use forward and reverse
flow to rapidly switch gases between parallel vessels. Within
the fixed-bed adsorber, impurities are removed from the
product gas at high pressure and then rejected as the
system pressure “swings” to a lower pressure. The ability to
completely adsorb impurities allows the production of high
purity (99.99%) end product.
PSA Unit
The PSA unit is a severe service application for control
valve assemblies. High cycling action and tight shutoff
is required. Annual cycle service exceeds 60,000 cycles
for four-bed units like the one shown below.
The challenge of PSA is that control valve assemblies are
expected to cycle as often as every thirty seconds and provide
tight, bi-directional shutoff. Common failures of control valve
assemblies in PSA units include:
•
Stem or shaft breakage due to deficient pinning design
•
Poor valve-actuator-positioner linkages leading to multiple
mechanical failures in a high-cycle environment
•
Loss of shutoff
Your PSA units can achieve longer lifecycles with Fisher control
valve assemblies. Fisher control valve assemblies for PSA
applications are tested to one million cycles to meet Emerson’s
high-cycle quality standard.
The high-performance, linkage-less feedback system in
FIELDVUE
™
digital valve controllers has no wearing parts
so cycle life is maximized. The feedback system eliminates
physical contact between the valve stem and the digital valve
controller. It is completely non-contact and
does not rely on linkages, eliminating the most
common control valve failure mode. Scan the
QR code to learn more about the linkage-less
feedback system in the DVC6200 instrument.
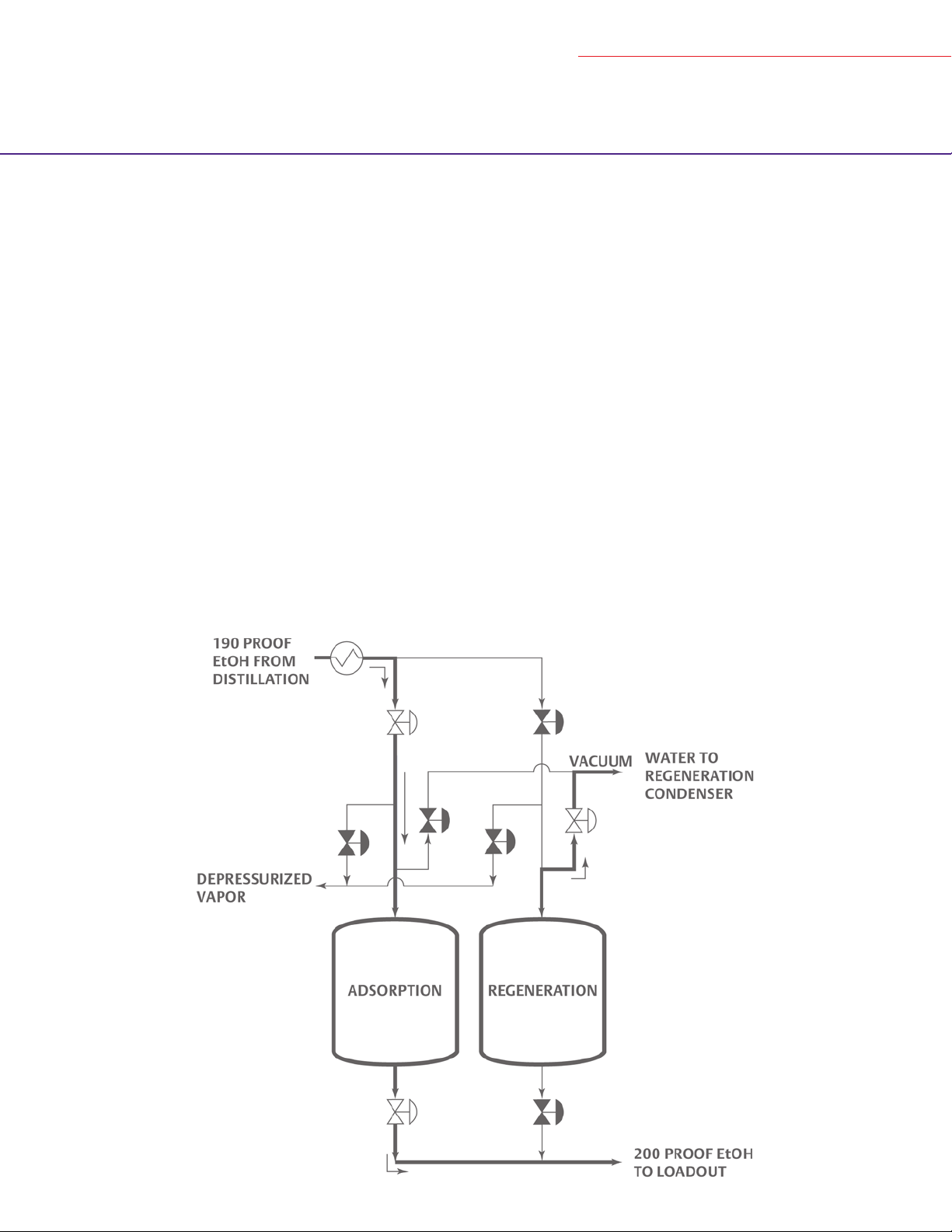
Nonstop High-Cycle Applications | 5
Molecular Sieve Adsorption
With the competitive environment in the ethanol industry
constantly increasing, now is the time to focus on improving
overall plant efficiency and reliability. Regardless of plant
scale, the molecular sieve adsorption application presents a
significant opportunity for such improvements.
In surveying ethanol producers from around the world, some
of the most commonly reported maintenance problems
related to the molecular sieve adsorption unit include:
•
Selection of oversized butterfly valves leading to poor
control and reduced cycle life
•
Accelerated bearing wear, often seen after only a few months
•
Poor valve-actuator-positioner linkages leading to multiple
mechanical failures in a high-cycle environment
•
Poor performance from low-quality valve positioners in both
the adsorption and regeneration cycles
Continued enhancement of this essential component of
the ethanol process is critical to achieving plant output and
revenue targets. Fisher control valve assemblies for molecular
sieve adsorption applications are tested to one million cycles
to meet Emerson’s high-cycle quality standard.
Molecular Sieve Adsorption
Improper selection of control valve
assemblies can lead to unscheduled
downtime. During this downtime,
a typical 50 million gallon-per-year
ethanol facility can suffer over
$10,000 USD per hour in lost revenue.