
B Software description
41
1. Vocabulary explanations
2 Software installation, access into program
2.1 Possible PC configuration
2.2 PC with a hard disk and 1 disk drive
installation, access
3. Explanations for the software
3.1 The differences in the input keyboards
3.2 Important key functions
3.3 Coordinate system
3.4 Screen cursor
3.5 Menu structure - menu summary
3.6 Screen display
3.7 Selection / deselection of the menu points
4. Menu points
4.1 Work piece
4.2 Draw
4.2.1 Cursor
4.2.2 Point
4.2.3 Line
4.2.4 Arc
4.2.5 Visible edges
4.2.6 Mirroring
4.2.7 Cleaning
4.2.8 Erasing the geometric element
4.2.9 Erasing all
4.2.10 Hotkeys - draw
Specimen example 1
Specimen example 2
Specimen example 3
4.3 Program
4.3.1 Moving in the rapid
4.3.2 Moving with feed speed
4.3.3 Cycles
Roughing cycle
Back pocket cycle
Follow contour cycle
Cut-in cycle
Threading cycle
4.3.4
4.3.5
4.3.6
4.3.7
4.3.8
4.3.9
4.310
Machining possibilities: CAD/CAM Edit Tool change
Erase the last movement
Erasing the machining program
Entering the feed values
Change feed unit
Entering the finishing offsets
41
42
42
42
46
46
47
48
49
50
52
52
53
54
55
56
59
61
64
68
68
68
69
69
70
71
72
73
74
74
74
74
75
77
79
81
83
90
91
91
91
91
91
91
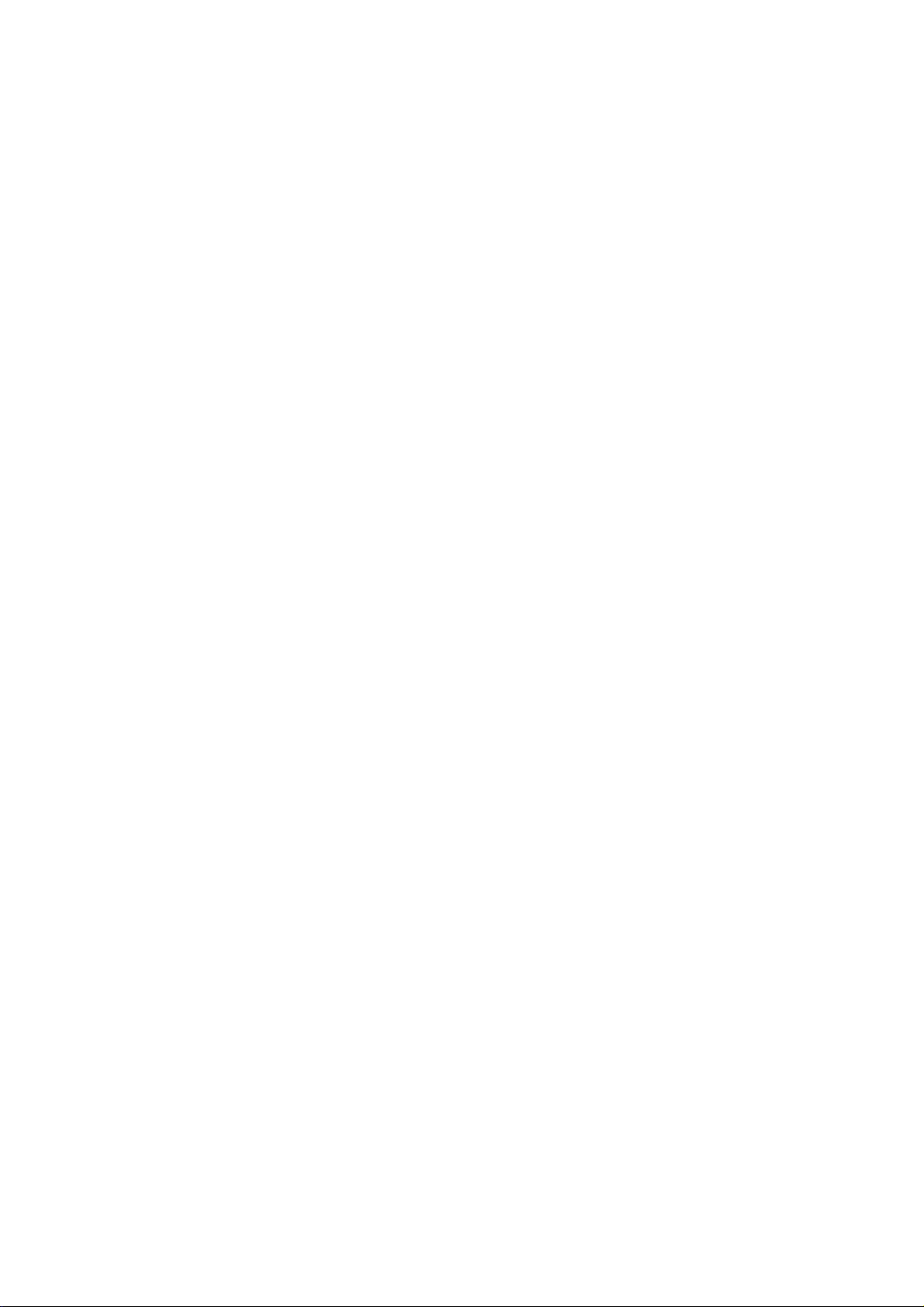
4.4.1 Zoom all
Menu summary, hotkeys (for
4.4.2 Zoom window
4.4.3 Zoom work piece
4.4.4 Removing, inserting the head stock
4.4.5 Removing, inserting the work piece
4.4.6 Removing, inserting the tool
4.4.7 Removing, inserting the tool path
4.4.8 Inserting, removing the tail stock
4.4.9 Changing the simulation display
4.4.10 Shift Geometry
Set up 0,0
4.5
Manual
4.6
Machine
4.7
4.7.1 Automatic
4.7.2 Single Step
4.7.3 Fast run (Rapid)
4.7.4 Empty cut step
4.7.5 Repeating the program
4.7.6 Moving the tool to the cursor
4.7.7 Shifting the program
4.7.8 Altering the scale program
4.8 Archive
4.8.1 Storing the program
4.8.2 loading the program
4.8.3 Storing the geometry
4.8.4 loading the geometry
4.9 Print
4.10 End
92
92
92
93
93
93
93
94
94
94
95
96
97
98
98
98
98
98
99
99
99
99
100
100
100
101
101
101
101
5.Specimen examples
6. Edit
7.Notes for the software compilation
Work sheets:
taking out)
102
109
130
133
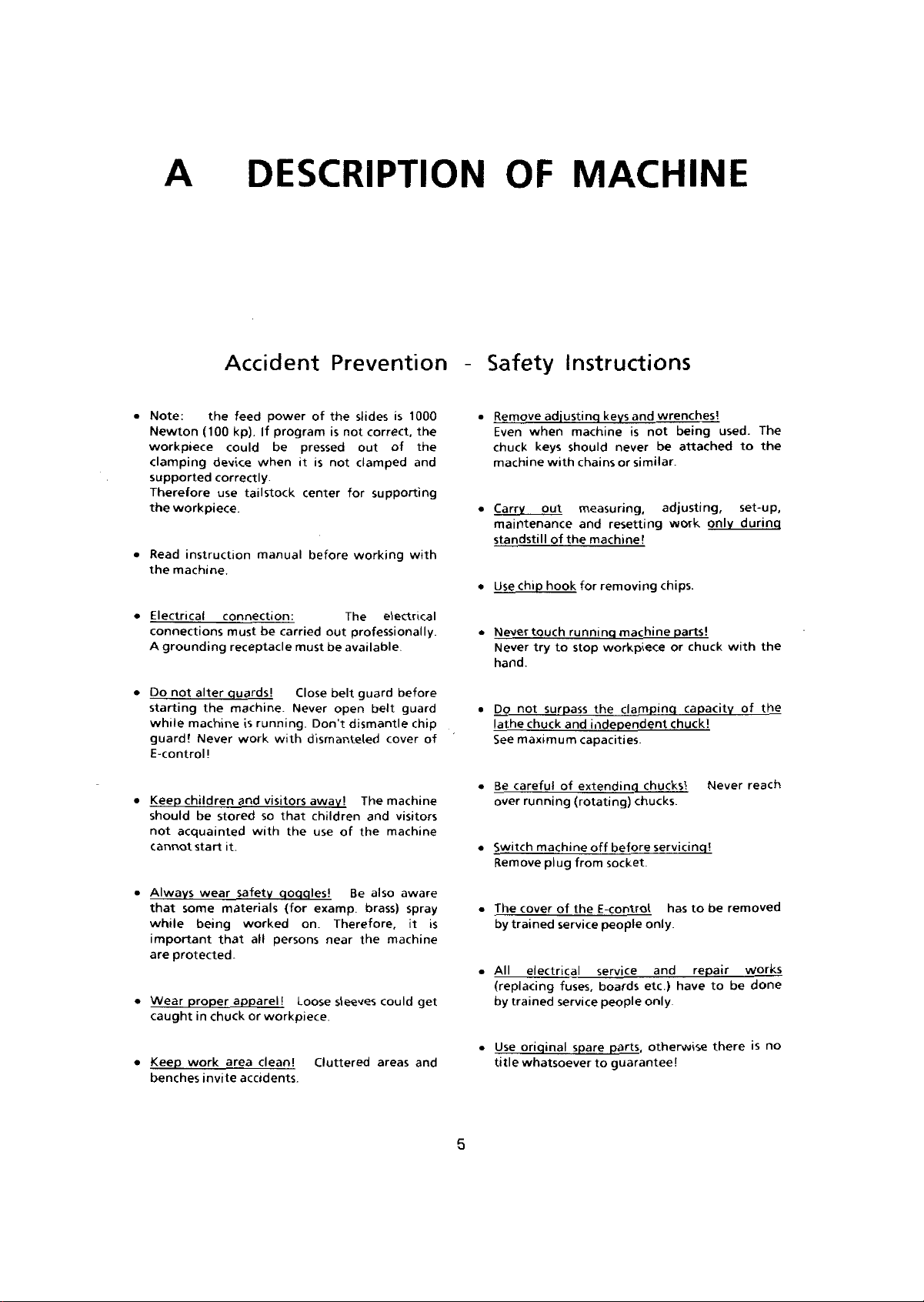
A
DESCRIPTION
OF
MACHINE
Note:
•
Newton
workpiece
clamping
supported
Therefore
workpiece
the
Read
•
machine
the
Electrical
•
connections
A
grounding
Do
not
•
starting
while
guard!
E-control!
Keep
•
should
not
cannot
Accident
the
(100
could
device
correctly.
use
instruction
connection:
must
alter
the
machine
Never
children
be
storedsothat
acquainted
start
it.
power
feed
kp).
If
when
tailstock
manual
be
receptacle
guards!
machine.
is
running.
work
visitors
and
with
program
be
pressed
it
center
before
carried
must
Close
Never
with
dismanteled
the
Prevention
slides
the
of
is
Don't
away!
children
use
correct,
is
not
out
not
clamped
for
working
The
professionally
out
be
available
guard
belt
open
dismantle
The
and
of
the
supporting
electrical
belt
cover
machine
machine
1000
is
of
and
with
before
guard
chip
visitors
the
the
Safety
Remove
•
Even
chuck
machine
Carry
•
maintenance
standstillofthe
chip
Use
•
Never
•
Never
Instructions
adjusting
when
machine
keys
should
with
chains
measuring,
out
and
machine!
removing
for
hook
running
touch
try
to
stop
keys
and
is
not
never
similar
or
resetting
machine
workpiece
wrenches!
being
attached
be
adjusting,
work
chips.
parts!
chuck
or
only
used.
with
The
the
to
set-up,
during
the
hand.
Do
•
of
lathe
See
Be
•
over
Switch
•
Remove
surpass
not
chuck
maximum
careful
running
machine
plug
and
of
(rotating)
the
independent
capacities
extending
off
before
from
socket
damping
chucks.
chuck!
chucks!
servicing!
capacity
Never
of
reach
the
Always
•
that
while
important
are
Wear
•
caught
Keep
•
benches
wear
some
being
protected.
proper
in
chuck
work
invite
safety
materials
worked
all
that
apparel!
or
area
accidents.
goggles!
(for
persons
Loose
workpiece.
clean!
examp.
on.
near
Cluttered
also
Be
brass)
Therefore,
the
sleeves
could
areas
aware
spray
it
machine
get
and
removed
be
has
cover
The
•
is
by
All
•
(replacing
by
Use
•
title
trained
electrical
trained
original
whatsoever
of
the
service
fuses,
service
spare
E-control
people
service
boards
people
parts,
guarantee!
to
only.
etc.)
only
to
repair
and
have
otherwise
to
there
be
works
done
no
is
5
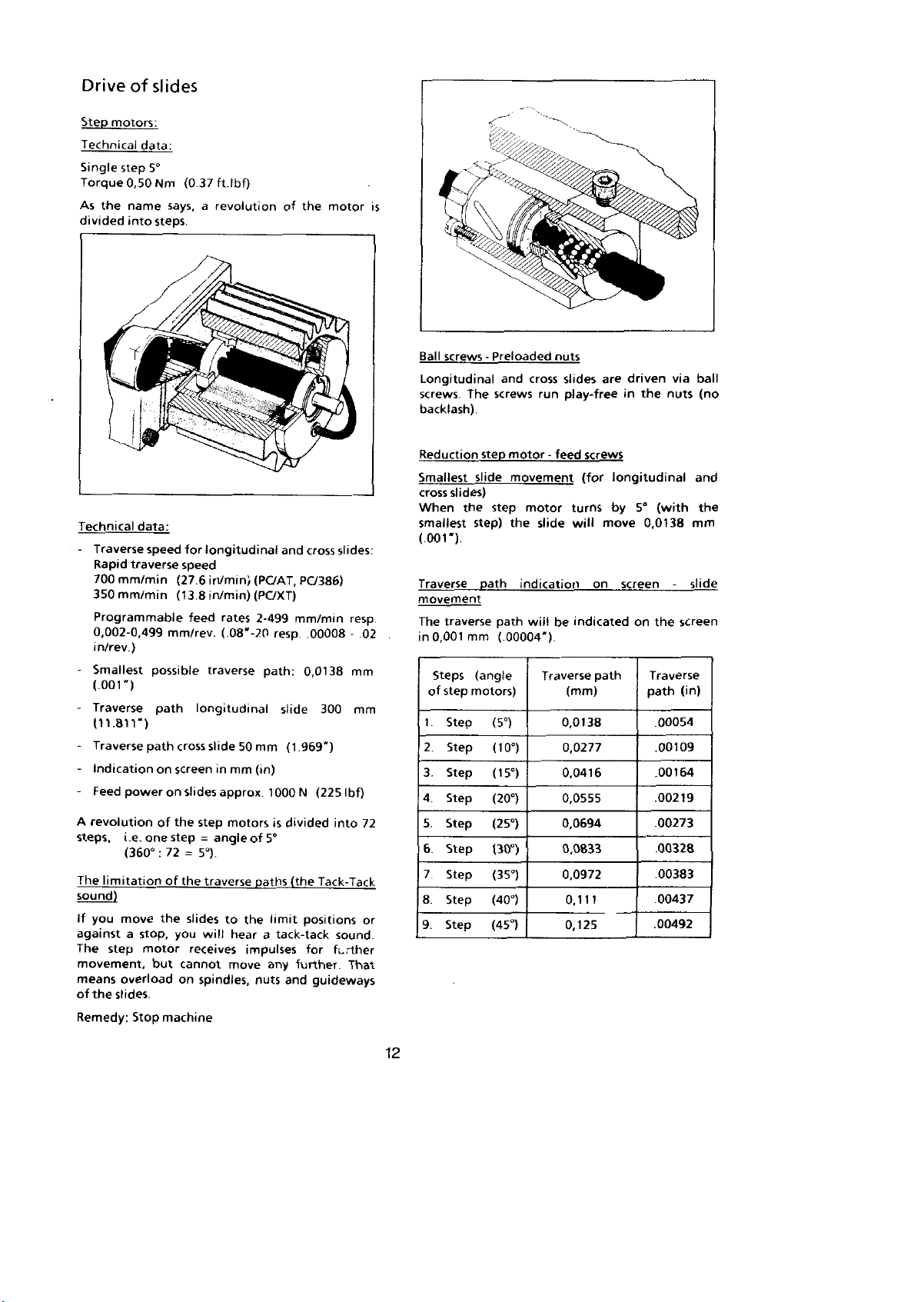
Drive
Step
motors:
Technical
Single
Torque
the
As
divided
of
step
0,50
name
into
slides
data:
5°
Nm
steps
(0
says,
ft.lbf)
37
a
revolution
'M
of
the
motor
is
v
gg
A
ii
Technical
data:
Traverse
Rapid
700
350
Programmable
0,002-0,499
in/rev.)
Smallest
(.001-)
speed
traverse
mm/min
mm/min
possible
Traverse
(11.811*)
Traverse
path
Indication
power
Feed
A
revolutionofthe
i
(360°
limitation
you
move
step
overload
the
slides.
.e.
a
Stop
one
stop,
motor
steps,
The
sound)
If
against
The
movement,
means
of
Remedy:
speed
(27.6
(13.8
mm/rev.
path
cross
on
screen
on
step
:
72
of
the
the
you
but
cannot
on
machine
longitudinal
for
in/min)
in/min)
feed
rates
(
traverse
longitudinal
slide
in
slides
approx.
step
angle
=
5°).
=
traverse
slides
to
will
receives
spindles,
08'-20
50
mm
motors
the
hear
impulses
move
(PC/AT,
(PC/XT)
2-499
resp
path:
mm
(in)
1000N
is
of
5°
paths
limit
a
tack-tack
any
nuts
and
PC/386)
mm/min
0,0138
slide
(1
969")
divided
(the
positions
further.
and
slides:
cross
resp
-
00008
mm
300
(225Ibf)
into
Tack-Tack
sound
for
further
That
guideways
02
mm
72
or
Ball
screws
Longitudinal
screws
backlash).
The
Reduction
slides)
traverse
0,001
Steps
step
Step
Step
Step
Step
Step
Step
Step
Step
Step
slide
the
step)
mm
(angle
motors)
Smallest
cross
When
smallest
(.001').
Traverse
movement
The
in
of
1.
2
3
4.
5.
6.
7
8.
9
-
Preloaded
and
screws
step
motor
movement
step
the
path
path
(.00004')
(5°)
(10“)
(15°)
(20°)
(25°)
(30°)
(35°)
(40°)
(45°)
nuts
cross
run
-
feed
motor
slide
indication
will
be
Traverse
0,0138
0,0277
0,0416
0,0555
0,0694
0,0833
0,0972
slides
play-free
screws
(for
turns
will
on
indicated
path
(mm)
0,111
0,125
driven
are
in
the
longitudinal
by
5°
0,0138
move
screen
on
via
nuts
(with
screen
the
Traverse
(in)
path
.00054
.00109
.00164
.00219
.00273
00328
00383
00437
.00492
ball
(no
and
the
mm
slide
12

P
11
14
15
16
17
18
19
2o
21
22
23
24
25
26
27
28
29
3o
31
32
33
34
35
36
37
lo
12
13
OS
B5,3
DIN9o21
M5xl2
DIN84-4.8
18x1,2
PS12x
9
DIN6799
24x1.2
DIN471
M5xl2
DIN84-4.8
6oo6-2Z
6oo6/2K
SS45x55x3
B55x2
DIN472
6x335
6x45o
DIN933-5.6
M6xl2
M8
DIN934-6
A8,4
DIN9o21
B5,3
DIN9o21
M5xl2
DIN6912-6.9
NM8
DIN98o-8
PS
12x18x0,3
TS
231-20Y
H231-11Y
ZV1
0IN7991-8.8
M4x25
A4
DIN127-A2E
DIN
DIN7981
220
115
100
Riemenscheibe
Motorriemenscheibe
Scheibe
Zyl
inderschraube
Vorgelegeriemenscheibe
Stiitzscheibe
Sicherungsscheibe
Sicherungsring
Teil
Zyl
inderschraube
Hiilse
Rillenkugel
Ausgleichscheibe
Stiitzscheibe
Sicherungsring
Hauptspindel
Kei
lriemen
Kei
Iriemen
Frontschi
Sechskantschraube
Sechskantmutter
Scheibe
Lagerbol
Tragerplatte
Spindels
Schei
Zyl
inderschraube
Sicherungsmutter
Lichtschranke
Blechschraube
Abstimmblech
Pa(3scheibe
Motor
V
Motor
V
Motor
V
Endschal
Ischwenkhebel
Rol
Senkschraube
Federring
Benennung
scheibe
lager
Id
zen
tockabdeckung
b.e
ter
loo
Description
Pulley
pulley
Motor
Washer
Flat
head
Countershaft
Supporting
Retaining
Retaining
Dividing
Flat
washer
head
Spacer
bearing
Ball
Compensating
Supporting
Retaining
spindle
Main
V-belt
V-belt
plate
Front
Hexagon
Hexagonal
head
nut
Washer
Bearing
Carrier
Headstock
Washer
Socket
Securing
Light
Sheet
Compensating
Shim
Motor
Motor
Motor
limit
Control
Flat
Split
shaft
plate
cover
head
nut
barrier
metal
ring
switch
lever
head
washer
screw
pulley
ring
washer
ring
screw
washer
ring
ring
screw
screw
screw
sheet
screw
loo
Poul
Poul
Rondel
Vis
Poul
Rondel
Poulie
Anneau
Disque
Vis
Douille
Roulement
Rondel!
Rondel
Anneau
Broche
Courroie
Courroie
Plaque
Vis
Ecrou
Rondel
Axe
Plaque
Couvercle
Rondel
Vis
Ecrou
Barriere
Vis
Tole
Rondelle
Moteur
Moteur
Moteur
Ref.
No.
1
A6A
ooo
o2o
A5A
2
3
4
5
A5A
6
ZSB
7
ZSB
8
9
A6A
ZSR
A6A
ZLG
ZSB
ZSB
ZRG
A5A
ZRM
ZRM
A60
ZSR
ZMU
ZSB
A5A
A5A
A6A
ZSB
ZSR
ZMU
A6A
ZSR
A6A
ZSB
ZMO
ZMO
ZMO
ZEL
ZEE
ZSR
ZRG
ZSB
ZSR
ZRG
ooo
22
64
060
lo
99
71
ooo
84
ooo
6o
o2
lo
72
ooo
4o
4o
ooo
33
34
21
ooo
13o
o3o
22
11
8o
lo8
S3
ooo
12
17
19
17
21
47
79
26
o3o
o53o
o512
ooo
2181
o9oo
2412
Ho
o512
24o
o6o2
6006
5553
552o
olo
6335
645o
17o
0612
0800
o84o
loo
OOO
ooo
o53o
0512
0800
ool
3513B3.5x13
28o
12o3
1224
1114
1104
2034
0010
0425
0040
ie
ie
le
a
tete
ie
le
tete
a
le
hexagonal
6
le
palier
le
6
a
de
en
de
Interrupteur
levier
tete
h
Vis
Rondel
le-ressort
Designation
de
moteur
cylindrique
retenue
de
retenue
de
diviseur
cylindrique
d'ecartement
billes
a
compensation
e
de
de
retenue
principale
trapezoidale
trapezoidale
frontale
e
pans
pans
surete
de
seule
la
creux
support
lumineux
tole
compensation
de
fin
de
commande
conique
loo
poupee
fixe
27

Pos.
1
2
J
4
5
6
7
8
9
lo
11
12
13
14
15
16
17
13
19
2o
21
22
23
24
25
26
27
28
29
3o
31
32
33
A6A
A6A
A6A
A6A
f\6f\
ZSR
ZSR
ZSR
A6A
ZST
ZMU
/T5A
A6A
ZSR
ZSR
A6A
A6A
ZSR
A6A
A6A
A5A
A6A
ZSB
ZSR
A6A
ZSR
ZSR
A6A
ZMO
ZRM
ZSR
A6A
A6A
A6A
Ref.
o2o
o2o
o2o
o2o
o2o
103
78
021
12
12
84
13
34
ISO
o4o
12
12
ooo
ooo
84
ooo
ooo
ooo
ooo
25
12
ooo
33
33
73
12
ooo
ooo
ooo
No.
olo
o2o
060
o7o
ooo
o5o8
o51o
o5o6
080
c6o6
o4oo
Ooo
ooo
o4o8
0516
22o
2oo
o3o8
23o
21o
13o
o5o
o53o
0512
o7o
o51o
o4o8
001
0010
48o5
o535
080
14o
26o
M5x8
M5xlo
M5x6
M6x6
DIN934-5
M4
M4x8
M5xl6
M3x8
B5
,3
M5xl2
M5xlo
M4x8
M5x35
DIN
DIN912-6
DIN
DIN913-45H
DIN912-6.9
DIN84-4
DIN
DIN933-5.6
.9
912-6.9
DIN
84-4.8
DIN912-6
.8
125
DIN912-6
DIN933-5.6
DIN912-6.
broche
6
6
6
pointeau
pointeau
vis
de
6
6
a
6
hexagonal
hexagonale
Moteur
Moteur
sans
sans
6
Support
Designation
transversal
e
transversal
pans
creux
creux
pans
creux
pans
pans
6
-mere
racleur
pans
creux
pans
creux
feutre
en
de
cylindrique
tete
en
feutre
de
de
chariot
de
chariot
e
1
creux
pans
de
moteur
pas
a
a
pas
cable
refroidi
crantee
pans
creux
de
moteur
de
tourelle
posterieur
racleur
racleur
1
e
pas
pas
sseur
2
post.
post.
court
long
X,Z
X,Z
e
post.l
post.
1
1
2
Benennung
Schlitten
tten
Querschl
Abdeckbl
i
ech
Einstelleiste
Querspindel
Gruppe
Zylinderschraube
Zylinderschraube
Zyl
inderschraube
Gewi
ndestift
ndestift
Gewi
Sechskantmutter
Langsspindel
Gruppe
Abstreifblech
Zyl
inderschraube
Zyl
.9
inderschraube
Abstreiffilz
Abstreifblech
Zyl
inderschraube
Abstreiffilz
Abstreifblech
Bettleiste
Bettleiste
1
1
2
2
kurz
lang
Scheibe
Zyl
.9
inderschraube
Motorplatte
1
Sechskantschraube
Sechskantschraube
S:hrit.tmctor
Schrittmotor
Kabel
ohne
KLihlkorper
ohne
X,Z
X,Z
Zahnflachriemen
9
Zylinderschraube
Motorplatte
2
Anschlag
hal
teraufl
Stahl
age
Description
Slide
Cross
Cover
Gib
Cross
Socket
Socket
Socket
screw
Set
screw
Set
Hexagonal
screw
Lead
Wiper
Socket
Socket
wi
Fel
t
Wiper
Flat
head
Fel
t
wi
Wiper
plate
Keep
Keep
plate
Washer
Socket
Motor
Hexagon
Hexagon
Step
motor
Step
motor
without
without
Timing
Socket
Motor
Stop
post
Tool
slide
sheet
slide
head
head
head
sheet
head
head
per
plate
per
plate
head
plate
head
head
cable
dissipator
belt
head
plate
support
spindle
screw
screw
screw
nut
complete
screw
screw
1
1
screw
2
2
short
long
screw
1
screw
screw
X,Z
X,Z
screw
2
Chariot
Chariot
Couvercl
Lardon
c
Ens.
Vis
Vis
Vis
Vis
Vis
Ecrou
Ens.
Tole
Vis
Vis
Racleur
Plaquette
Vis
Racleur
Plaquette
Lardon
Lardon
Rondel
Vis
Plaque
Vis
Vis
Courroie
Vis
Plaque
Butee
29
y>