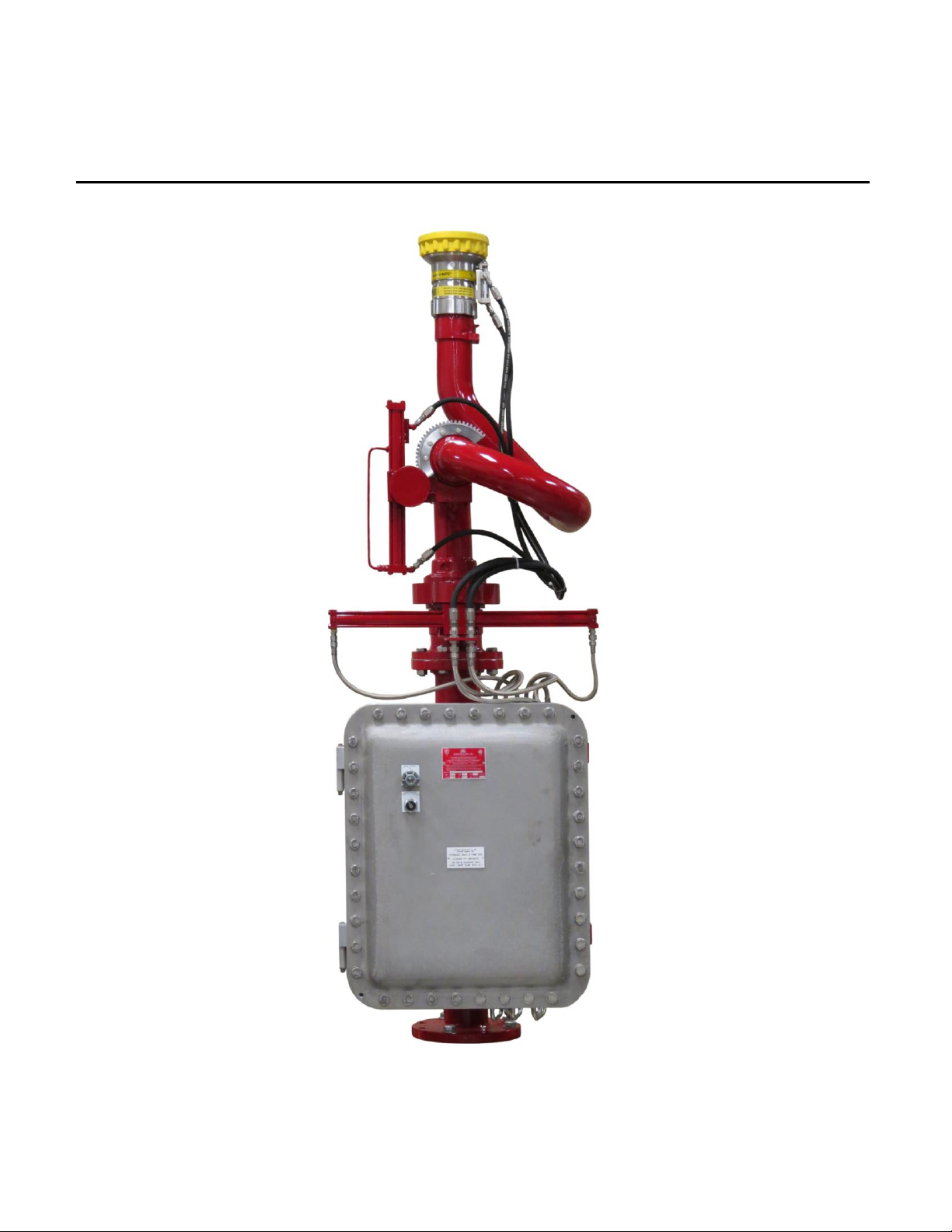
Elkhart Brass Mfg., Co., Inc.
Hydraulic operated remote controlled fire monitor system
Installation, Operating, & Maintenance Instructions
Models: 294-11XBHC-N4X, 294-11XBHC-N7/4, 299-20XHC-N4X, & 299-20XHC-N7/4
Revised 8/20/2010 1 EB98175000_Rev. B
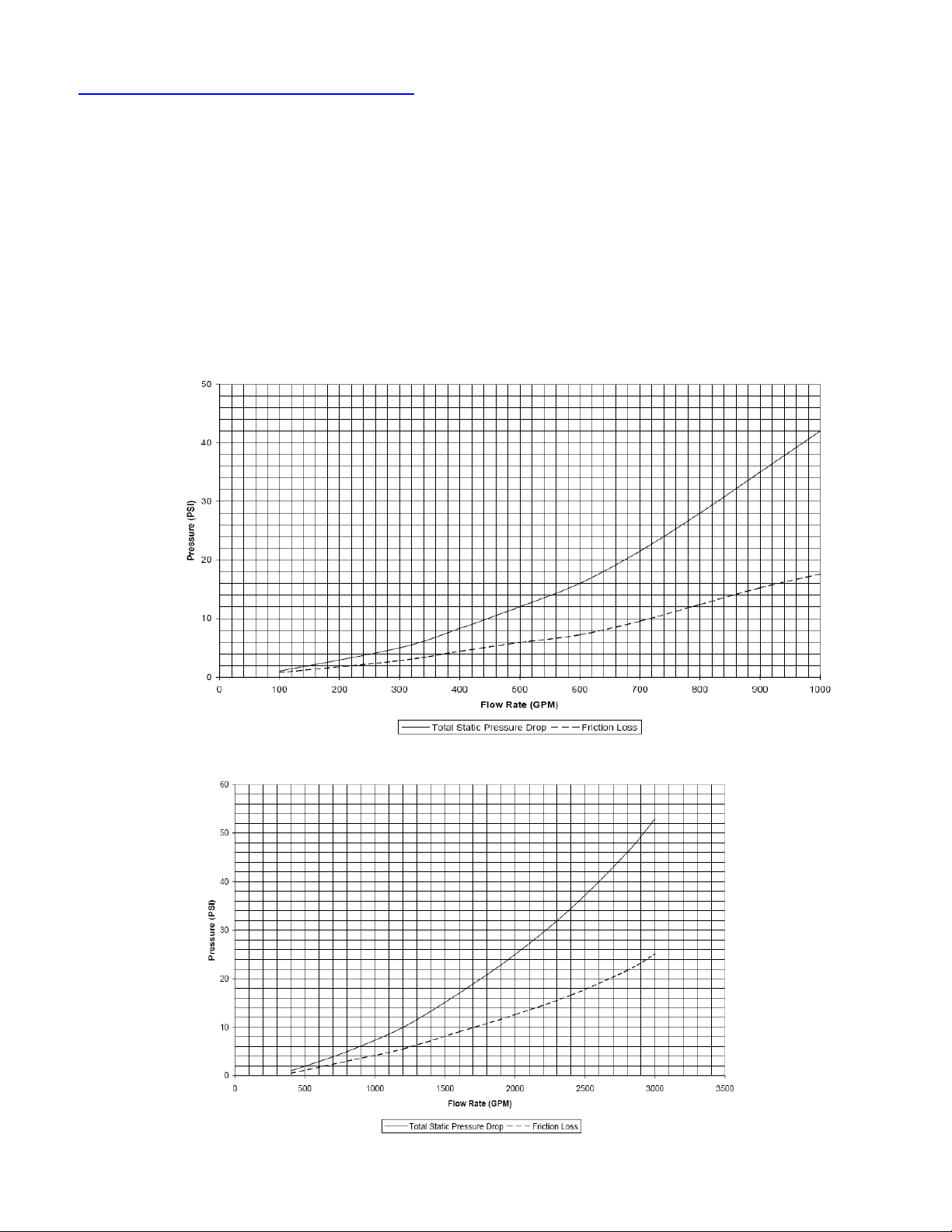
INSTALLATION INSTRUCTIONS
1.0 Installing Monitor and Nozzle:
1.1 Bolt the monitor to standpipe, terminated with 4" - 150# Flat Face ASA flange base.
1.2 Standpipe must be structurally strong enough to withstand reaction force of nozzle when
discharging a straight stream at 90º of the standpipe or tower. The formula for calculating
nozzle reaction is: REACTION FORCE = 0.0505 x G.P.M. x √¯P.S.I.
1.3 Inlet pressure at base of monitor must be high enough to allow for pressure Lose through
monitor. To accomplish this, use friction loss for G.P.M. flowing, from friction loss chart and
add to nozzle pressure. (See chart below).
1.4 After Modular Monitor is installed on standpipe, open Valve & Pump Box door and remove
yellow cap from pump reservoir. Remove rubber disc from inside of cap and replace it with
breather filter supplied in zip-loc bag attached to hydraulic pump. Replace cap on reservoir.
294-11XBHC Monitor (4” Inlet and 2.5” Outlet)
299-20XHC Monitor (4” Inlet and 3.5” Outlet)
Revised 8/20/2010 2 EB98175000_Rev. B
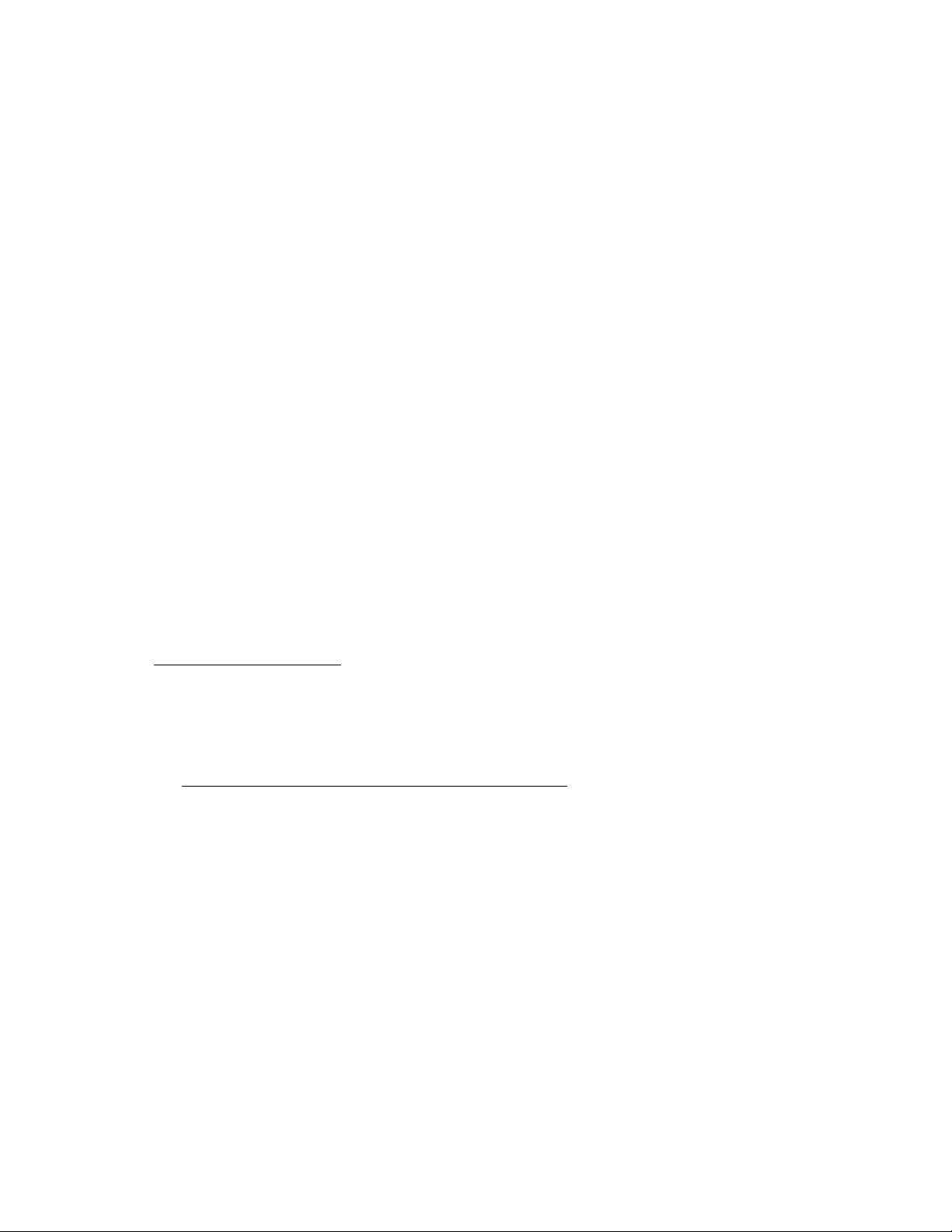
2.0 Electrical control system installation:
2.1 Install control boxes at designated locations and cut out holes in box to attach conduit. All
cable entry knockouts on all NEMA #4X enclosures are provided by others. All NEMA
#7/4 enclosures have N.P.T. female threaded entries provided.
2.2 Install conduit and pull electrical conductors between control boxes and Valve & Pump Box.
Main power source to be connected at Valve & Pump Box, supplied by others. Primary power
source required is: 85-265 VAC, 47-264 Hz., single-phase power. When power is connected,
ACDC power supplies will automatically set at voltage and cycles within range required. All
operating voltages for control system and hydraulic pump is 24-VDC powered through power
supply located in Valve & Pump Box. 15 conductors are required from each valve & pump box
to control box, see electrical drawings for connections.
2.3 Conductor size is determined by length of wire needed between control boxes. Recommended
conductor size is as follows:
0 – 300 foot length use #22 AWG wire (voltage drop = 0.48 maximum)
300 – 500 foot length use #20 AWG wire (voltage drop = 0.52 maximum)
501 – 800 foot length use #18 AWG wire (voltage drop = 0.52 maximum)
801 – 1200 foot length use #16 AWG wire (voltage drop = 0.51 maximum)
1201 – 1800 foot length use #14 AWG wire (voltage drop=0.49 maximum)
1801 – 3000 foot length use #12 AWG wire (voltage drop = 0.51 maximum)
3.0 Energize and adjusting hydraulic system:
(This procedure has been done at factory and should not have to be repeated unless hydraulic system is
opened.)
3.1 Fill reservoir with hydraulic fluid. For best results use automatic transmission fluid ( Dexron III).
Check reservoir fluid after each function is bleed out.
WARNING!! Do not operate hydraulic pump without hydraulic fluid.
3.2 Priming hydraulic pump:
3.2.1 Remove electrical plug from valve solenoid V1B and hydraulic pressure tube between
pump & solenoid valve manifold.
3.2.2 Jog “UP” switch on control panel until hydraulic fluid flows out pressure port of pump.
3.2.3 Reconnect pressure hydraulic tube and valve solenoid electrical plug.
3.3 Bleed air out of system by using the following procedure:
3.3.2 Set pump relief valve pressure to 50 P.S.I., which is as low as possible. Lower monitor
vertical movement to maximum down position and disconnect hydraulic hoses from
vertical actuator ports V1A & VIB. Open port controls at both ends of rotary actuator;
turn screws counterclockwise until it stops. (See illustration 1 for location of port control
valve adjusting screws).
3.3.3 Insert open end of V1B hydraulic hose into clean container, and activate “UP” mode
switch at control box. Hold switch until hydraulic fluid is discharging from hose and
is free of air. Reconnect hydraulic hose to port V1B, increase pump pressure then,
activate “UP” switch until monitor rises to maximum elevation.
3.3.4 Close port controls valves at V1A & V1B actuator ports, turn screws clockwise until
it stops, and then open both screws one complete revolution.
3.3.5 Insert open end of V1A hydraulic hose into clean container, and activate “DOWN”
mode switch at control box. Hold switch until hydraulic fluid is discharging from
hose and is free of air. Reconnect hydraulic hose to port V1A, then activate “DOWN”
switch until monitor is lowered to minimum elevation.
Revised 8/20/2010 3 EB98175000_Rev. B
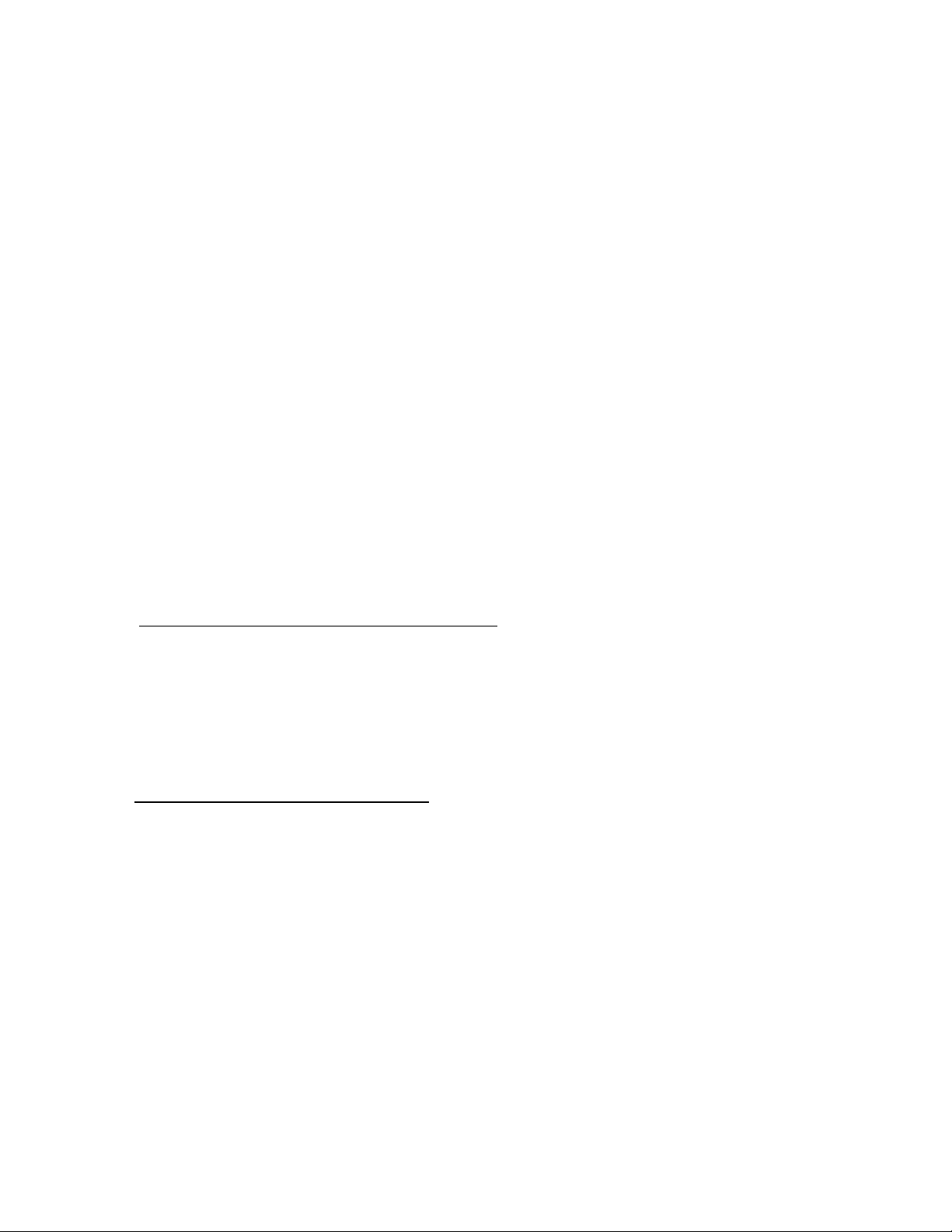
3.3.6 Disconnect hydraulic lines from horizontal actuator ports V2A & V2B. Open port
control valves at both ends of rotary actuator, turn screws counterclockwise until they
stop. (See illustrations 1 & 4 for location). Manually turn monitor to maximum
horizontal clockwise position.
3.3.7 Insert open end of V2A hydraulic hose into clean container, and activate “LEFT”
mode switch at control box. Hold switch until hydraulic fluid is discharging from
hose and is free of air. Reconnect hydraulic hose to actuator port V2A, then activate
“LEFT” switch until monitor reaches maximum counterclockwise position.
3.3.8 Insert open end of V2B hydraulic hose into clean container, and activate “RIGHT”
mode switch at control box. Hold switch until hydraulic fluid is discharging from
hose and is free of air. Reconnect hydraulic hose to actuator port V2B, then activate
“RIGHT” switch until monitor is moved to maximum clockwise position.
3.3.9 Reposition monitor so nozzle hydraulic line connections are easily accessible.
Disconnect hydraulic lines V3A & V3B from nozzle ports. Open needle valve on
nozzle (see illustration 2) to full counterclockwise position. Then manually push
nozzle tip to full fog position Insert open end of V3A hydraulic hose into clean
container and activate “STRT” switch at control box. Hold switch until fluid is
discharging from hose and is free of air. Reconnect hydraulic hose to nozzle port V3A
and activate “STRT” switch until nozzle reaches the straight stream position.
3.3.10 Insert open end of V3B hydraulic hose into clean container and activate “FOG”
switch at control box. Hold switch until fluid is discharging from hose and is free of
air. Reconnect hydraulic hose to nozzle port V3B and activate “FOG” switch until
nozzle reaches the maximum fog position. Lower monitor to approximately 45º
below horizontal and move from fog to straight stream positions several times
allowing about one minute idle time at each end of stroke, this will remove any
remaining air bubbles in nozzle cylinder.
3.4 Hydraulic pump pressure adjustment procedure:
3.4.1 Check hydraulic fluid levels in reservoir, if low add fluid.
3.4.2 Activate and hold “FOG” function switch, this will start hydraulic pump and move tip
to fog position. Hold switch in fog position and check pressure on gauge located in
valve & pump box.
3.4.3 Open adjustable relief valve until pressure reads 1000 PSI, and then tighten down lock
nut on relief valve screw. Turn relief valve screw clockwise to increase pressure and
c’clockwise to decrease pressure.
3.5 Adjusting speed of monitor and nozzle:
3.5.1 Port control valves are located at each end of the monitor rotary actuators and needle
valve is plumbed into hydraulic line of piston on nozzle. (See illustrations on page 5).
3.5.2 Horizontal movement should operate at proper speed with port control valves at full
open (c’clockwise) position.
3.5.3 To adjust vertical speed of monitor, open port control valves completely at both ends of
actuator. Turn screw counterclockwise.
3.5.4 Raise nozzle to full up vertical position. With nozzle in fully up position close port
control valve, turning in clockwise direction slowly until desired speed in downward
movement is reached and nozzle lowers at a steady rate. Turn port control valve screw in
c’clockwise direction to increase speed.
3.5.5 If monitor starts to jerk when moving downward, raise nozzle to the full vertical
position. While lowering nozzle, turn port control screw for down movement (see
Illustration 3) clockwise slowly until nozzle lowers smoothly. By doing this removes
backpressure on pilot check valve and allows valve to stay open while monitor is
moving to the down position.
Revised 8/20/2010 4 EB98175000_Rev. B