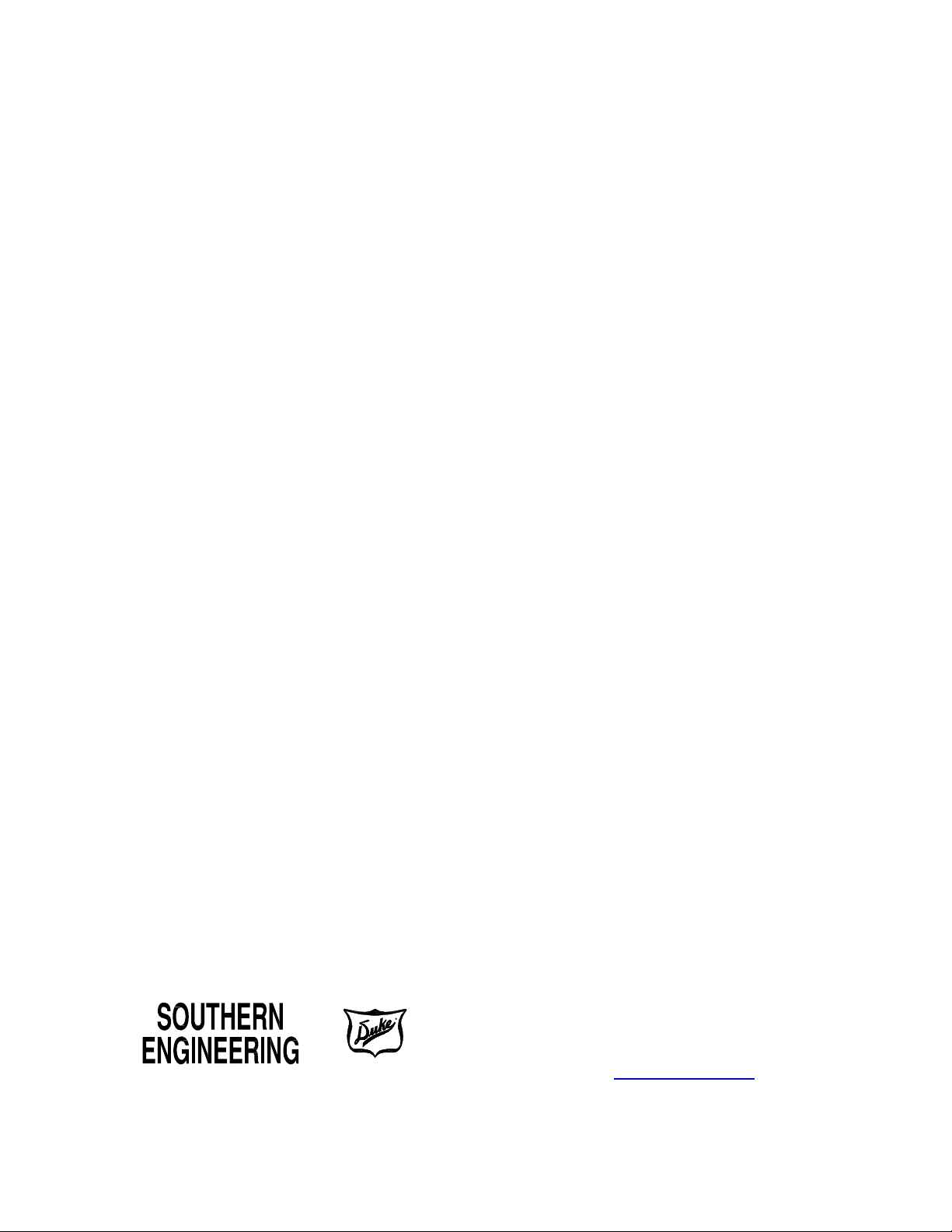
SUGGESTED SPECIFICATIONS FOR VENTILATOR MODEL
HVXSTFM
Exhaust Ventilator to be SOUTHERN ENGINEERING SYSTEMS by Duke Mfg Co., model
HVXSTFM, Type I, UL listed, hood assembly for commercial cooking appliances and be in compliance
with NFPA Bulletin No. 96 Ventilator shall be high velocity, low volume, cartridge type and have a
nominal 95% grease extraction efficiency certified by an independent testing laboratory.
Canopy, constructed of 18-gauge stainless steel (where exposed) with bottom perimeter edges gutterless.
Weld extraction chamber, plenum, and external seams and joints to form a liquid tight construction.
Polish stainless steel to a #3 finish.
Exhaust plenum Extraction Chamber to be same material as canopy, full length of section at the back.
Furnish welded stainless steel self-draining cartridge inserts, installed horizontally. Cartridge housing to
form a high velocity slot. Inserts to lift out using tool provided exposing access to plenum chamber for
easy cleaning. Bottom of exhaust plenum to be formed into a pitched gutter to accept gravity flow
residue and drain to a covered stainless steel container.
Grease Container constructed of 18-gauge stainless steel having a maximum capacity of one gallon.
Fabricate container so as to be easily removable for daily cleaning. Removal of container exposes 1-1/2”
ID stainless steel tube to allow capture of cleaning solution when hood and duct system are cleaned.
Furnish Duct Collar, fully welded, in top of canopy within exhaust plenum area. Duct collar size based
on an average 1800 F.P.M. air velocity.
Optional automatic Fire Damper constructed of 12-gauge steel within exhaust duct collar. Damper
operated by an externally mounted spring-loaded mechanism and controlled by a fusible link.
Integral Make-Up Air furnished at front of ventilator shall be SOUTHERN ENGINEERING
SYSTEMS proprietary “Lazy Air” design. Outside shell constructed of 18-gauge stainless steel integrated
with canopy. Front face of canopy fitted with full height by full width 18-gauge stainless steel perforated
panels. Panels to be designed to distribute make-up air outward at a low velocity. Front panels shall be
hinged at top to allow easy access to interior of make-up chamber. Make-up air chamber fitted with an
interior diffuser baffle designed to provide even air distribution across the perforated surface. Top of
chamber to be fitted with properly sized rectangular duct collar. Make-up air duct collar sized to permit
up to 85% supply air.
Canopy shall be UL and NSF listed. All equipment built in an ISO 9001:2000 approved manufacturing
facility
2305 N. Broadway
St. Louis, MO 63012
BY
"Your Solut ions Par tner"
Ph 314-231-1130
Fax 314-231-5074
www.dukemfg.com
6/07
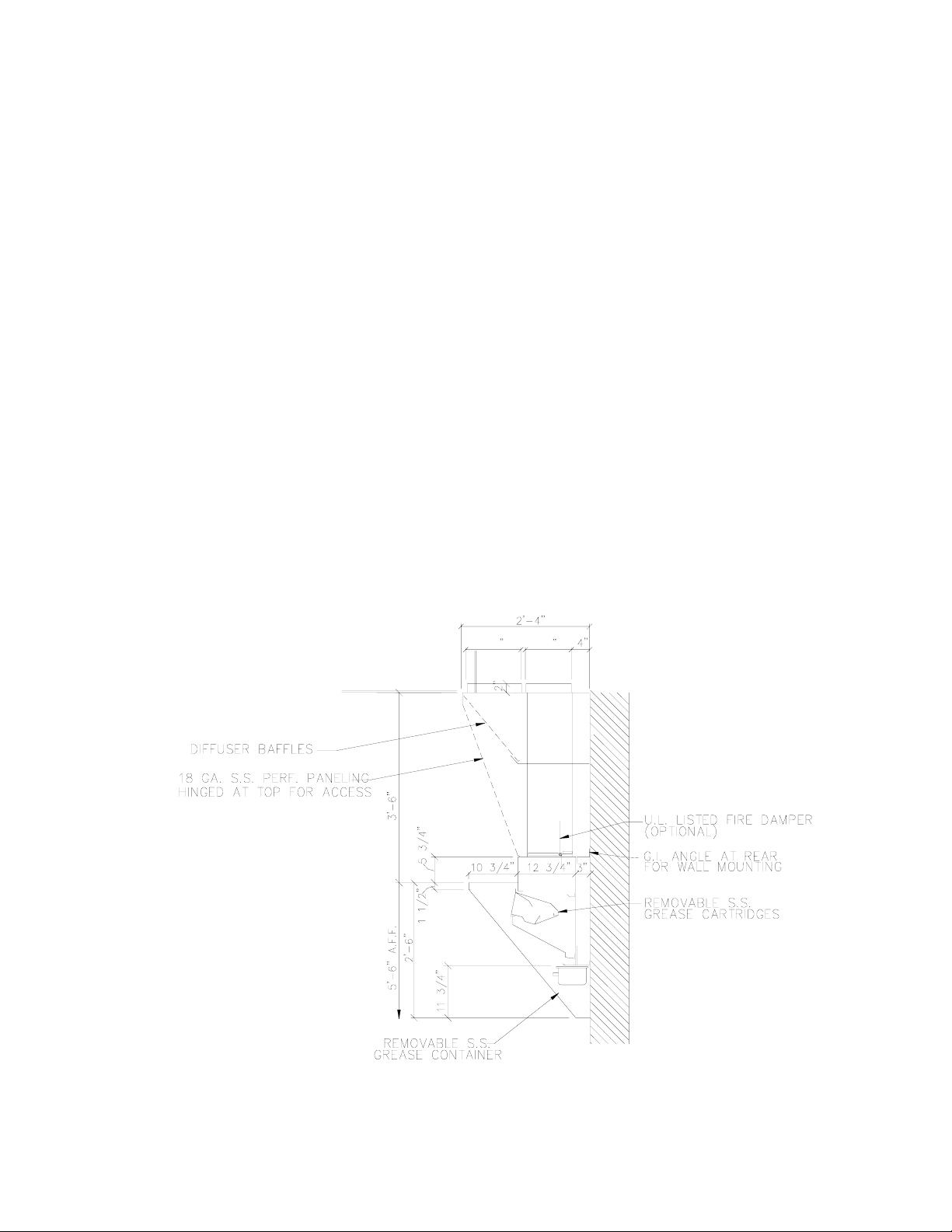
Exhaust Requirements Make-up Air Requirements
CFM ________________ SP (“w.g.) _____________ CFM ________________ SP (“w.g.) ________
Duct Collar ________ “x ______________” Duct Collar ________ “x __________”
Fire Protection Lighting Fixtures
(Submit cooking equipment plan showing make (Not Available)
and model on equipment.)
Ansul Wet #R-102
Other ___________________________________ Enclosure paneling
Internal Piping Only (Finished ceiling higher than 9’0”)
Complete System Fan switch
By Others Loose duct collars
NOTE: Fuel shut-off devices by others (unless specified UL Exhaust Fire Damper
otherwise).
Optional Accessories
Shipping Wt. 100 lbs./Linear Ft.
COMMENTS/NOTES ____________________________________________