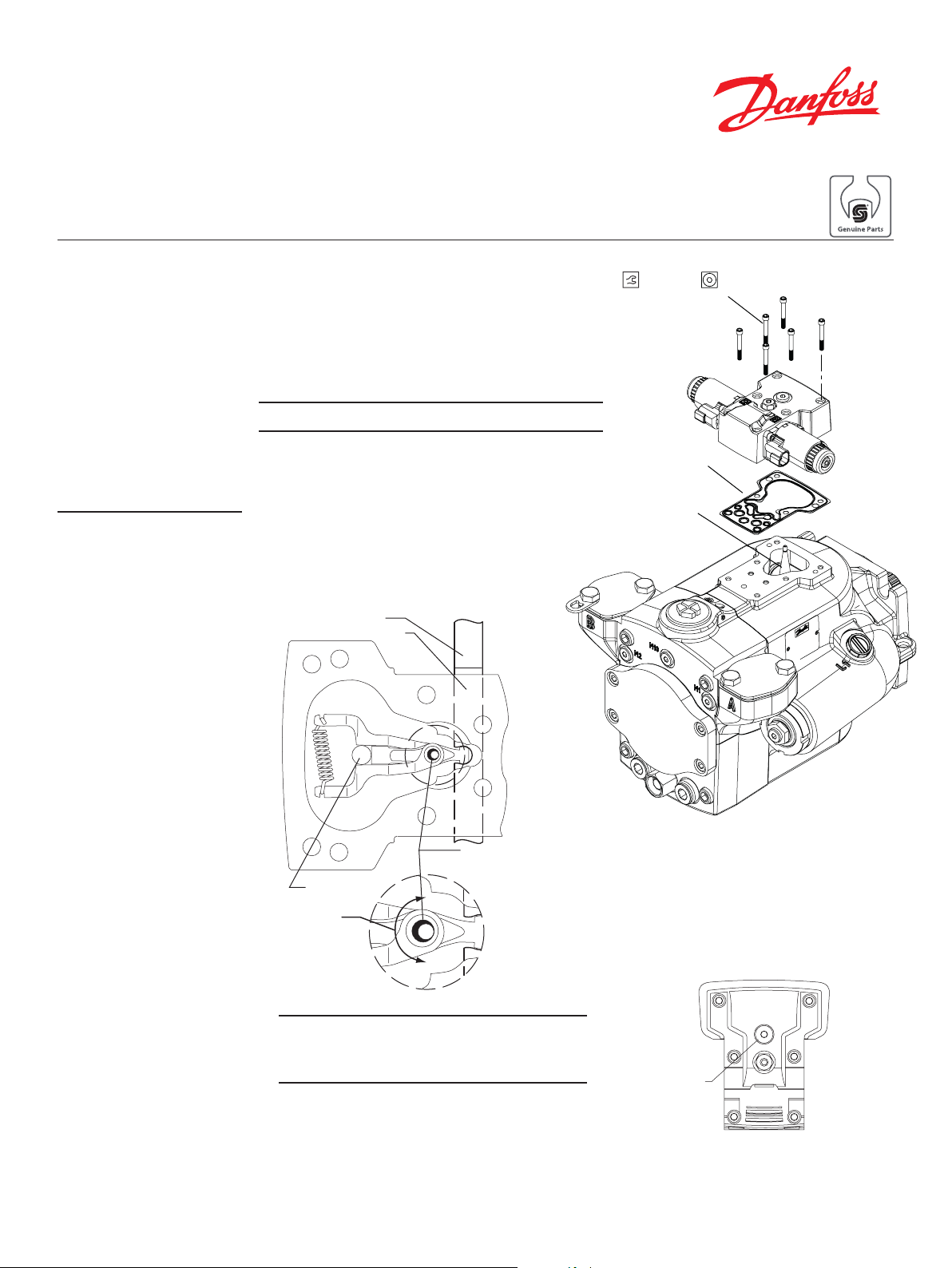
Service Kit Instructions
TMP pump
Electrical displacement control (EDC) replacement procedure
Removal of EDC
Installation of EDC
1. Clean pump externally with clean solvent to
remove debris.
2. Remove control screws (D250) using a 5 mm
internal hex wrench.
3. Remove the control from the pump.
Dowel pins (M140) must remain in pump housing.
4. Remove and discard the control gasket.
1. Install new control gasket (D150).
2. Position control on pump housing. Ensure
that feedback pin on swashplate is positioned
properly in control arm.
Solenoid shaft
Control spool
13.5 N•m
[10 lbf•ft]
D150
Feedback link
D250
5 mm
Adjusting
screw
Feedback pin
Maximum
adjustment
180°
P106 046E
(cam)
4
5
Remove plug (D065) and verify the swashplate
feedback pin is properly positioned between
control feedback arms.
3. Using a 5 mm internal hex wrench, fasten
control to pump with screws (D250). Torque
2
6
1
3
screws to 13.5 N•m [10 lbf•ft] following
torque sequence shown to the right.
© Danfoss, 2016 AN00000347en-US | 11184963• Rev 0100 • October 2016 1
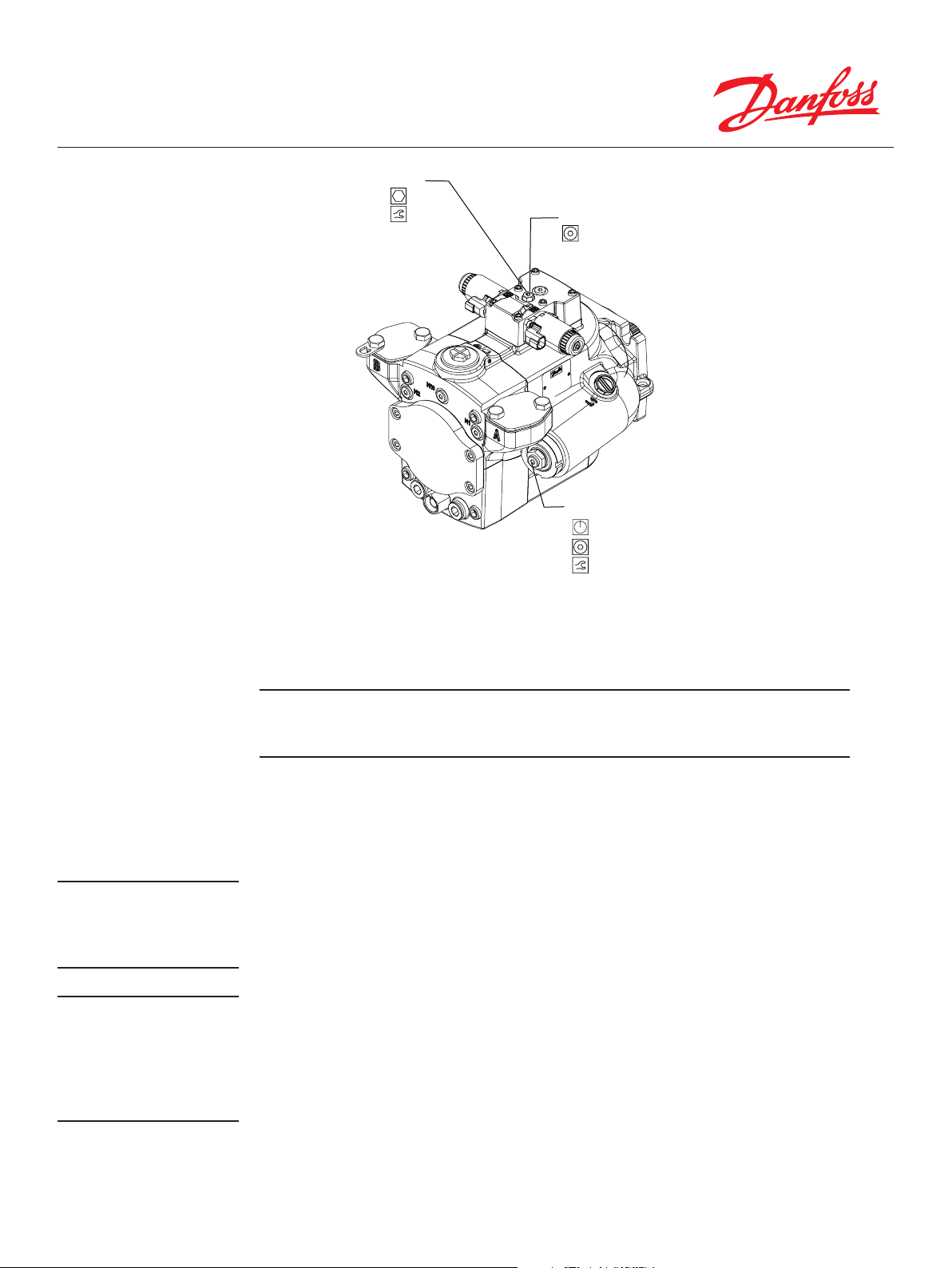
EDC adjustment
D060
13 mm
12 N•m
[8.9 lbf•ft]
D015
4 mm
Servo pressure gauge port
0 - 50 bar [0 - 1000 psi]
M12x1.5
The neutral adjustment is the only adjustment that can be made on electrical displacement controls. All other functions are preset at the factory. The neutral adjustment
must be made with the pump running on a test stand or on the vehicle/machine with
the prime mover operating.
Caution
Adjustment of the EDC is
very sensitive. Be sure to
hold the hex wrench steady
while loosening the lock nut.
A small pressure dierential
is acceptable. Final
adjustment must be within
2 bar dierential. Achieving
zero dierential is not
possible.
Warning
Unintended movement of the machine or mechanism may cause injury to the
technician or bystanders. To protect against unintended movement, secure the
machine or disable/disconnect the mechanism while servicing.
1. Install a 50 bar [1000 psi] pressure gauge in each of the two servo gauge ports (M4 and M5).
Disconnect the external control input (electrical connection) from the control. Start the
prime mover and operate at normal speed.
2. Use a 4 mm internal hex wrench to hold the neutral adjusting screw (D015) stationary while
loosening the lock nut (D060) with a 13 mm wrench.
3. If necessary, turn adjusting screw to reduce any existing pressure dierential.
4. Rotate the neutral adjusting screw (D015) clockwise until the pressure increases in one
of the pressure gauges. Note the angular position of the wrench. Then rotate the neutral
adjusting screw counterclockwise until the pressure increases by an equal amount on the
other gauge. Again note the angular position of the wrench.
5. Rotate the neutral adjusting screw clockwise half the distance between the wrench position
noted above. The gauges should read the same pressure, indicating that the control is in its
neutral position.
6. Hold the neutral adjusting screw stationary. Tighten the lock nut (D060). Torque lock nut to
12 N•m [8.9 lbf•ft]. Do not overtorque the nut.
7. When the neutral position is set, stop the prime mover, remove the gauges, and install the
gauge port plugs. Reconnect the external control input.
© Danfoss, 2016 AN00000347en-US | 11184963• Rev 0100 • October 2016 2