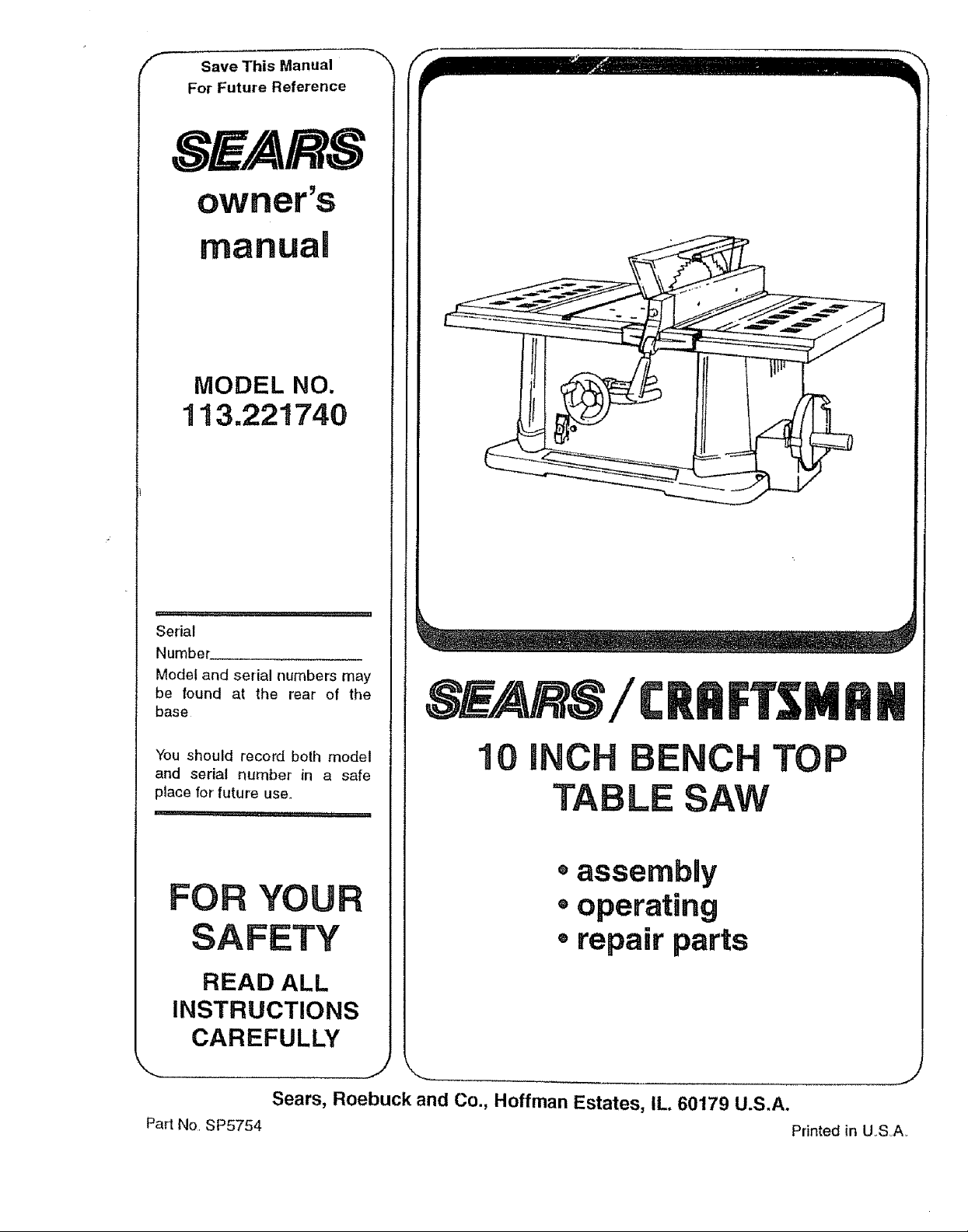
f
Save This Manual
For Future Reference
SEAfR8
ownel"s
manual
MODEL NO.
113=221740
Serial
Number.
Model and serial numbers may
be round at the rear of the
base
You should record botll model
and serial number in a safe
place for future use.
FO YOUR
;AFETY
READ ALL
INSTRUCTIONS
CAREFULLY
\
8 , Rt6/
10 iNCH BENCH TOP
TABLE SAW
®assembly
, operating
. repair parts
J
Pa_ NoSP5754
Sears, Roebuck and Co., Hoffman Estates, IL 60179 U.S.A.
Printed in USoA,
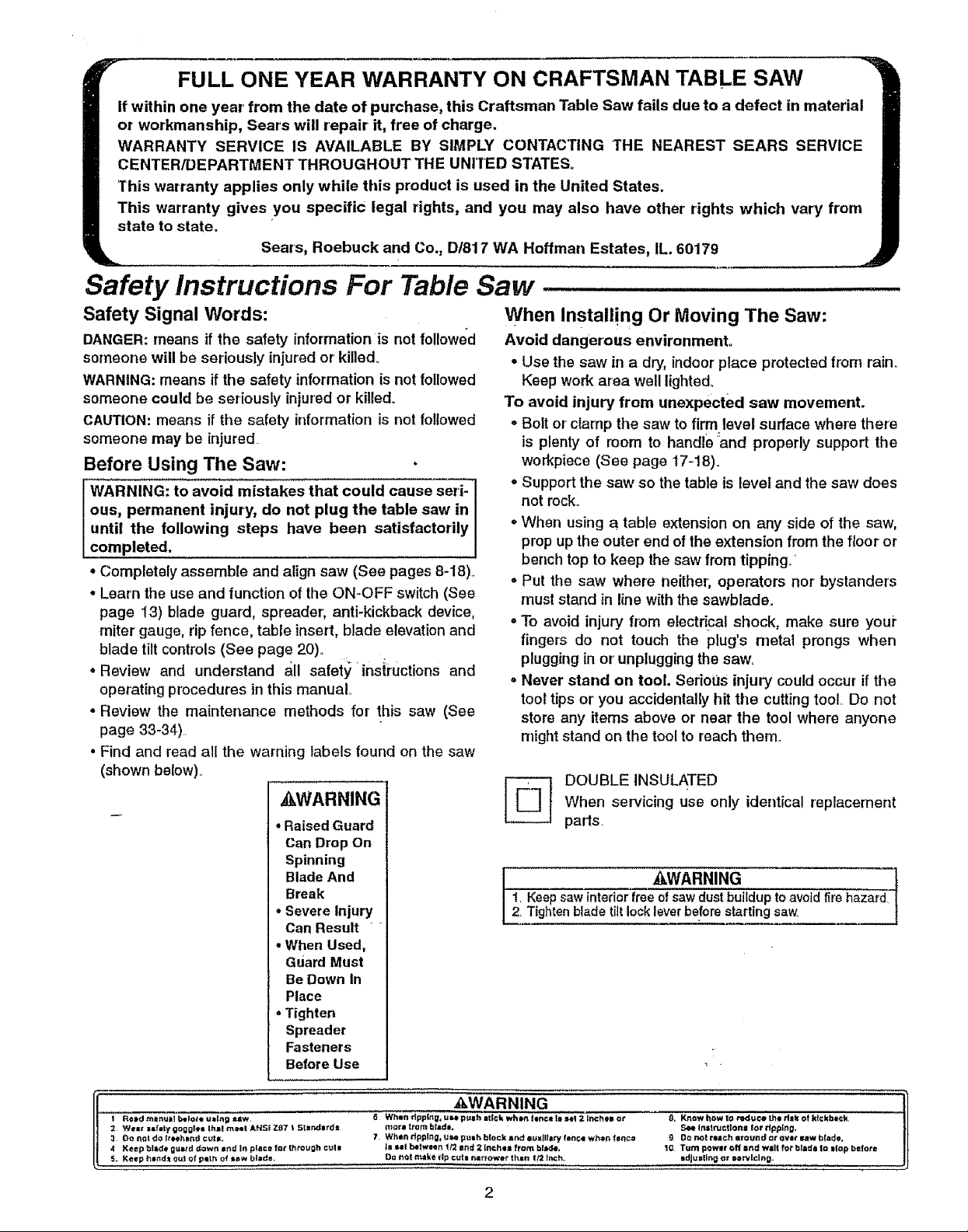
FULL ONE YEAR WARRANTY ON CRAFTSMAN TABLE SAW
If within one year from the date of purchase, this Craftsman Table Saw fails due to a defect in material
or workmanship, Sears will repair it, free of charge.
WARRANTY SERVICE IS AVAILABLE BY SIMPLY CONTACTING THE NEAREST SEARS SERVICE
CENTER/DEPARTMENT THROUGHOUT THE UNITED SIATESo
This warranty applies only while this product is used in the United States,
This warranty gives you specific legal rights, and you may also have other rights which vary from
state to state.
Sears, Roebuck and Co, D1817 WA Hoffman Estates, IL, 60179
Safety Instructions For Table Saw
Safety Signal Words:
DANGER: means if the safety information is not followed
someone will be seriously injured or killed.
WARNING: means ff the safety information is not followed
someone could be seriously injured or killed.
CAUTION: means if the safety information is not followed
someone may be injured
Before Using The Saw:
WARNING: to avoid mistakes that could cause seri-_
ous, permanent injury, do not plug the table saw in I
until the following steps have been satisfactorily I
completed, J
• Completely assemble and align saw (See pages 8-18)
• Learn the use and function of the ON-OFF switch (See
page 13) blade guard, spreader; anti-kickback device,
miter gauge, rip fence, table insert, blade elevation and
blade tilt controls (See page 20)
• Review and understand ill safety insiructions and
operating procedures in this manual
• Review the maintenance methods for this saw (See
page 33-34)
• Find and read all the warning labels found on the saw
(shown beioW)o
When Install!ng Or Moving The Saw:
Avoid dangerous environment,
• Use the saw in a dry, indoorplace protected from rain_
Keep work area well lighted,
To avoid injury from unexpected saw movement,
o Belt or clamp the saw to firm level surface where there
is plenty of room to handle and properly support the
workpiece (See page 17-18).
o Support the saw so the table is level and the saw does
not mck_
oWhen using a table extension on any side of the saw,
prop up the outer end of the extension from the floor or
bench top to keep the saw from tipping/
° Put the saw where neither; operators nor bystanders
must stand in line with the sawblade.
• To avoid injury from electrical shock, make sure your
fingers do not touch the plug's metal prongs when
plugging in or unplugging the saw,
• Never stand on tool. Serious injury could occur if the
tool tips or you accidentally hit the cutting too! Do not
store any items above or near the tool where anyone
might stand on the tool to reach them
kWARNING
• RaisedGuard
[_ DOUBLE INSULATED
When servicing use only identical replacement
parts
Can Drop On
Spinning
BladeAnd
Break
• Severe Injury
1,Keepsawinteriorfreeofsawduetbuilduptoavoidfirehazard
2_Tightenbladeti_tlockleverbeforestarting saw,
_kWARNING 1
Can Result
. When Used,
Guard Must
BeDown In
Place
- Tighten
Spreader
Fasteners
BeforeUse
_WARNING
I F_0td tttmt_tttt _t_lOtl UlIflg ItlW _ Wttltl tfpp_, U_ pU=h =ttCk wh_ tQr_ceIn set 2 [ncttel_ o1 8_ K_w h_W Io ,'edt=ce 1he d_k of k_:kbact<
2 W_l_*laf_tygoQgl_slh=blmNIANSlZ_7_ 5fc=mcho_'d_ morattombl_dm. S_lf|ttt, ltuc_olltJ |or_lp_lng,
3 DO _0! do _tochl_rtd cut_. 7 Whln rlpp_ng_use pu|h blt_ck nnd auxiliary f=no_ wh_ f_n¢_ 9 Do not reach _toull_ a_ ovlt sew hi,do.
4 Keep btld_ g_lt_d _aw_t i_ I_ pflc_ _o( |hro_gh Ct_ _l ea! belw_er_ 1t2 a/_f 2 [ll_h_ from bhK_. 1_ Tutti powlr o/f I_ Wilt for bl#d_ Io i|op befor_
5. Keep httttd_ 0_1 o_ p_ttt of _w btide. D_ _o_ tc_lke t_p ¢u_l rmrrowlr then f/2 _nch. =dJul_ln_ or Ii_l_lng_
2
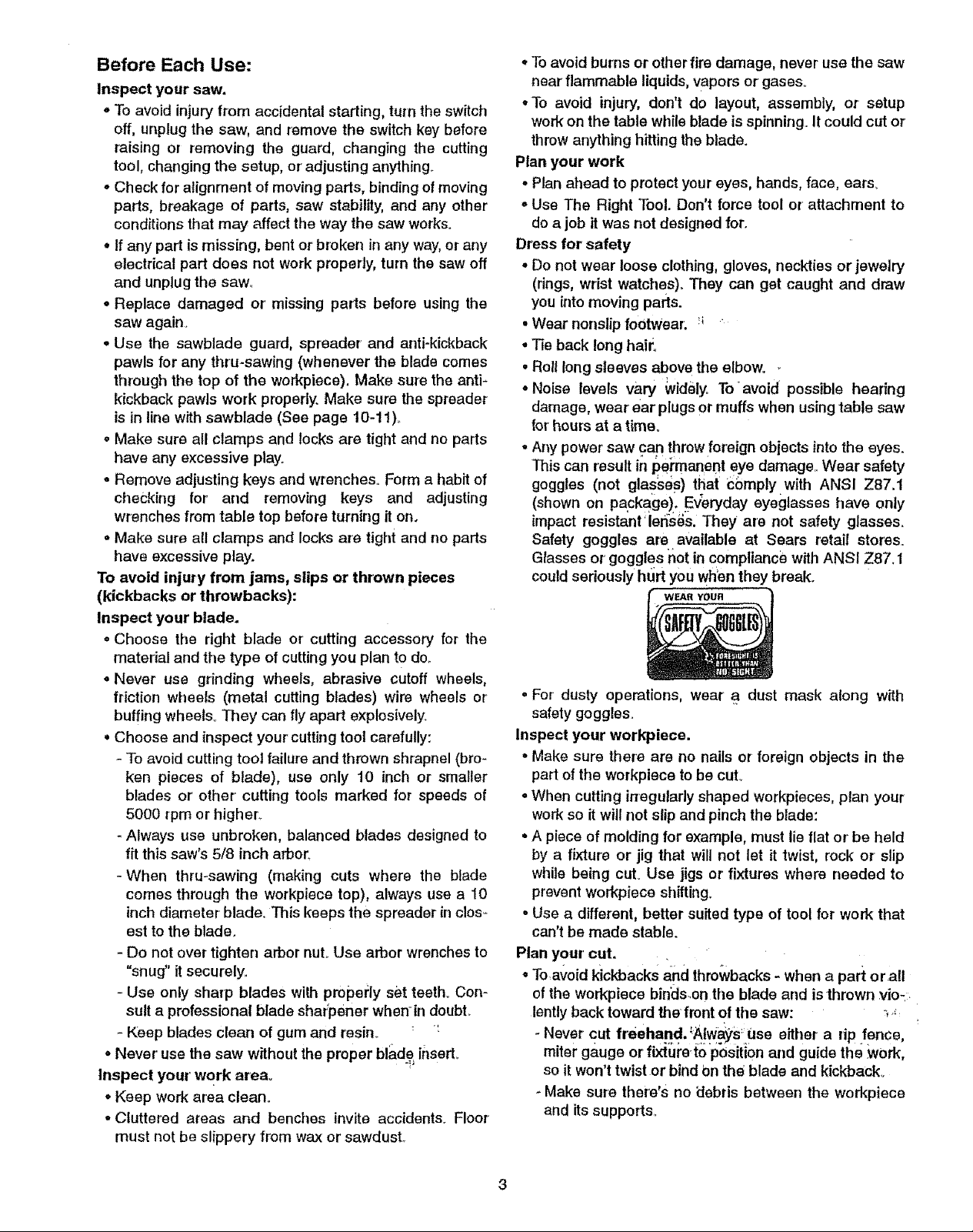
Before Each Use:
inspect your saw.
, To avoid injury from accidental starting, turn the switch
off, unplug the saw, and remove the switch key before
raising or removing the guard, changing the cutting
tool, changing the setup, or' adjusting anything..
* Check for alignment of moving parts, binding of moving
parts, breakage of parts, saw stability, and any other
conditions that may affect the way the saw works°
* If any part is missing, bent or broken in any way, or any
electrical part does not work properly, turn the saw off
and unplug the saw_
=Replace damaged or missing parts before using the
saw again.
oUse the sawblade guard, spreader and anti-kickback
pawls for any thru-sawing (whenever the blade comes
through the top of the workpiece). Make sure the anti-
kickback pawls work properly. Make sure the spreader
is in line with sawblade (See page 10-1!)..
° Make sure all clamps and locks are tight and no parts
have any excessive play.
=Remove adjusting keys and wrenches. Form a habit of
checking for' and removing keys and adjusting
wrenches from table top before turning it on.
° Make sure all clamps and locks are tight and no parts
have excessive play.
To avoid injury from jams, slips or thrown pieces
(kickbacks or throwbacks):
Inspect your blade.
, Choose the right blade or'cutting accessory for the
material and the type of cuttingyou plan to doe
oNever use grinding wheels, abrasive cutoff wheels,
friction wheels (metal cutting blades) wire wheels or
buffing wheels° They can fly apart explosively.
° Choose and inspect your' cutting toot carefully:
- To avoid cutting tool failure and thrown shrapnel (bro-
ken pieces of blade), use only t0 inch or smaller
blades or' other cutting tools marked for speeds of
5000 rpm or higher..
- Always use unbroken, balanced blades designed to
fit this saw's 5/8 inch arbor.
-When thru-sawing (making cuts where the blade
comes through the workpiece top), always use a 10
inch diameter blade. This keeps the spreader in clos-
est to the blade°
- Do not over tighten arbor nu[ Use arbor wrenches to
"snug" it securely.
- Use only sharp blades with pmpedy set teeth. Con-
sult a professional blade shar;pener when-in doubt.
- Keep blades clean of gum and resin.. _ "
o Never' use the saw without the proper blade inserL
inspect your' work area.
o Keep work area clean.
° Cluttered areas and benches invite accidents. Floor
must not be slippery from wax or sawdust..
* Toavoid burns or other fire damage, never usa the saw
near flammable liquids, vapors or gases°
° To avoid injury, don't do layout, assembly, or setup
work on the table while blade is spinning. It could cut or
throw anything hitting the blade.
Plan your work
, Plan ahead to protect your eyes, hands, face, ears.
o Use The Right Tool. Don't force tool or' attachment to
do a job it was not designed for.
Dress for safety
° Do not wear loose clothing, gloves, neckties or jewelry
(rings, wrist watches). They can get caught and draw
you into moving parts.
, Wear nonslip footwear'. _
, Tie back long hair.
oRoll long sleeves above the elbow.
oNoise levels vary _,idelyo To'avoid possible hearing
damage, wear ear plugs or muffs when using table saw
for hours at a time.
oAny power saw can throw foreign objects into the eyes.
This can result in pei'manent eye damage. Wear safety
goggles (not glasses) that cbmply with ANSI Z87.1
(shown on package) .. Ev"eryday eyeglasses have only
impact resistant led_sSs.They are not safety glasses.
Safety goggles are available at Sears retail stores..
Glasses or goggles not in compliance with ANSI Z87.1
could seriously hurt you when they break.
WEAR YOUfl
, For dusty operations, wear a dust mask along with
safety goggles.
inspect your workplace.
, Make sure there are no nails or foreign objects in the
part of the workplace to be cuL
• When cutting in'egularly shaped workpieces, plan your
work so it will not slip and pinch the blade:
• A piece of molding for example, must tie flat or be held
by a fixture or jig that will not let it twist, rock or slip
while being cuL Use jigs or fixtures where needed to
prevent workpiece shifting.
° Use a different, better suited type of tool for work that
can't be made stable.
Plan your cut.
° To avoid kickbacks and throwbacks - when a part orall
of the workplace bin:dls.or_the blade and is thrown vie-..
lently back toward the front of the saw: _
- Never cut freehan d. _!_yS_ Use either a rip fence,
miter gauge or fixtureto position and guide the work,
so it won't twist or bind bn the blade and kickback_
- Make sure there's no _ebris between the workpiece
and its supports.
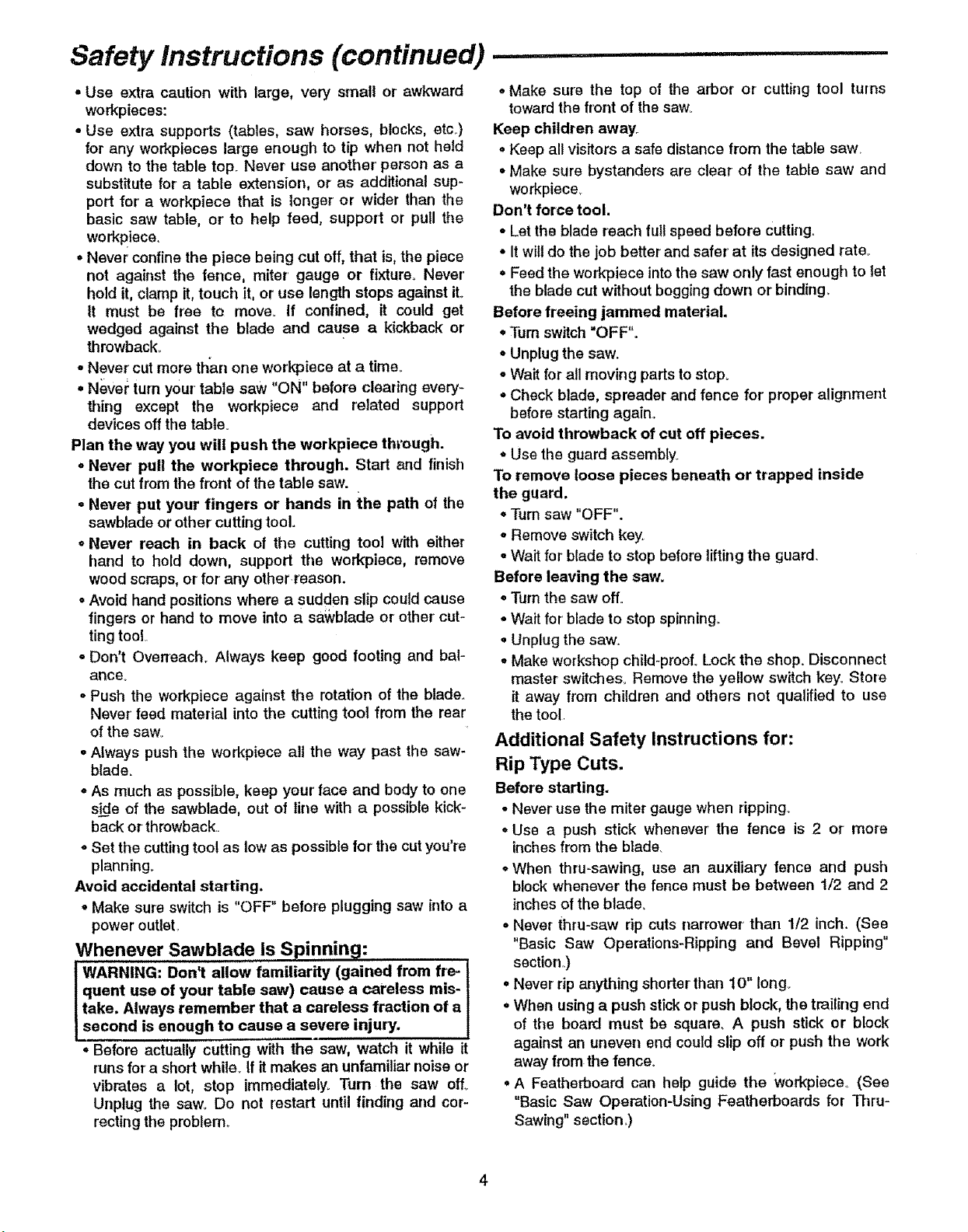
Safety Instructions (continued)
ii ,i ,, ii,
• Use extra caution with large, very small or awkward
workpieces:
• Use extra supports (tables, saw horses, blocks, etc.)
for any workpieces large enough to tip when not held
down to the table top. Never use another' person as a
substitute for a table extension, or as additional sup-
port for' a workpiece that is longer or wider than the
basic saw table, or to help feed, support or pull the
workpiece,
• Never confine the piece being cut off, that is, the piece
not against the fence, miter' gauge or fixture. Never'
hold it, clamp it, touch it, or use length stops against iL
It must be free to move. If confined, it could get
wedged against the blade and cause a kickback or
throwback°
• Never' cut more than one workpiece at a time°
• Never turn your' table saw "ON" before clearing every-
thing except the workpiece and related support
devices off the table°
Plan the way you will push the workpiece tht'ough.
. Never' pull the workpiece through. Start and finish
the cut from the front of the table saw.
° Never put your fingers or hands in the path of the
sawblade or other cutting tool.
• Never reach in back of tile cutting tool with either
hand to hold down, support the workpiece, remove
wood scraps, or for any other.reason.
oAvoid hand positions where a sudden slip could cause
fingers or hand to move into a sawbtade or other' cut-
ting tool.
- Don't Oveneach._ Always keep good footing and bal-
ance.
oPush the workpiece against the rotation of the blade.,
Never' feed material into the cutting toot from the rear
of the saw.
oAlways push the workpiece all the way past the saw-
blade,
o As much as possible, keep your face and body to one
sLde of the sawblade, out of line with a possible kick-
back or throwback..
° Set the cutting too! as low as possible for the cut you're
planning_
Avoid accidental starting.
° Make sure switch is "OFF" before plugging saw into a
power outlet,
Whenever Sawblade Is Spinning:
l WARNING: Don't allow familiarity (gained from fre-
quent use of your table saw) cause a careless mis-
take. Always remember that a careless fraction of a
second is enough to cause a severe injury,
• Before actually cutting with the saw, watch it while it
runs for a short while. If it makes an unfamiliar noise or
vibrates a lot, stop immediately. Turn the saw off.
Unplug the saw° Do not restart until finding and cor-
recting the problem,
, Make sure the top of the arbor or cutting tool turns
toward the front of the saw.
Keep children away
, Keep all visitors a safe distance from the table saw
° Make sure bystanders are clear' of the table saw and
workpiece.
Don't force tool.
• Let the blade reach full speed before Cutting.
° Itwilldo the job better and safer at its designed rate°
, Feed the workpiece intothe saw only fast enough to let
the blade cut without bogging down or binding_
Before freeing jammed material.
° Turn switch "OFF"°
• Unplug the saw.
oWait for all moving parts tostop_
° Check blade, spreader and fence for' proper alignment
before starting again..
To avoid throwback of cut off pieces.
• Use the guard assemblyv
To remove loose pieces beneath or trapped inside
the guard.
° Turn saw "OFF".
° Remove switch key
- Wait for blade to stop before lifting the guard.
Before leaving the saw,
• Turn the saw off.
• Wait for blade to stop spinning°
, Unplug the saw.
• Make workshop child-proofo Lock the shop.. Disconnect
master switches_ Remove the yellow switch key. Store
it away from children and others not qualified to use
the tool
Additional Safety Instructions for:
Rip Type Cuts.
Before starting.
• Never use the miter gauge when ripping.
• Use a push stick whenever' the fence is 2 or more
inches from the blade.
oWhen thru-sawing, use an auxiliary fence and push
block whenever the fence must be between 1/2 and 2
inches of the blade,
° Never {hru-saw dp cuts narrower than 1/2 inch. (See
"Basic Saw Operations-Ripping and Bevel Ripping"
section o)
, Never rip anything shorter than 10" long..
° When using a push stick or push block, the trailing end
of the board must be square, A push stick or block
against an uneven end could slip off or push the work
away from the fence.
° A Featherboard can help guide the Workpiece._(See
"Basic Saw Operation-Using Featherboards for Thru-
Sawing" section..)

* Always use featherboards for any non thru rip type
cuts+
IJI
24'
_,, i _*_=.,_-.=. J==-...=o-
!
FEATHERBOARDS
• To avoid kickbacks and slips into the. blade, make sure
the rip fence is parallel to the sawblade.
° Before thru-sawing, check the anti-kickback pawls.
(See Basic _.aw Ope_t!o_l :,rU+slr!g3_ne,Rip Fence?'
- The pawls must stop a kickback_once it has started°
Replace or sharpen anti-kickback pawls when points
become dullo ++
° Plastic and composition (like hardboard) materials may
be cut on your saw+ However, since these are usually
quite hard and slippery, the anti-kickback pawls may
not stop a kickback. Therefore, be especially careful in
your setup and cutting procedures.
While thru-sawing.
. To avoid kickbacks and slips into the blade, always
push forward on the section of the workpiece between
the sawblade and the rip fence. Never push forward on
the piece being cut off.+
Additional Safety Instructions For:
Crosscut Type Cuts.
Before starting.
• Never use the ripfence whan crosscutting.
oAn auxiliary wood facing attached to the miter gauge can
help prevent work'piecetwisting and throwbacks.Attach it
to the holes provided. Make the facing long enough and
big enough to support your work,, Make sure, however, it
will not interferewith the sawblade guard.
oUse jigs or fixtures to help hold any piece too small to
extend across the full length of the miter gauge face
during the cut. This lets you properly hold the miter
gauge and workpiece and helps keep your hands away
from the blade.
While cutting.
° Toavoidblade contact,always ho_ the mitergauge as shown
in "BasicSaw Operations- Using The Miter Gauge".
Glossary of Terms for Woodworking ......................
Anti=Kickback Pawls (AKP i
Device which when properly maintained is designed to
stop the workp_ece from being kicked back at the opera-
tor during ripping operation.
Arbor
The shaft on which a cuttingtool is mounted+
Bevel Cut : +
An angle cutting operation made through the face of the
workpiece.
Compound Cut
A simultaneous bevel and miter crosscutting operation..
Crosscut
A cutting operation made across the width of the work-
piece°
Dado
A non thru cut which produces a square sided notch or
trough in the workpiece.
Featherboard
A device which can help guide workpieces during rip type
operation. .,
Freehand
Performing a cut without the use Of fence (guide), miter'
gauge, fixture, hold downior 0the! p+roper device to pre-
vent the workpiece from twisting during the cutting opera-
tion. Twisting of the wo_piece can cause _tto be thrown.
Gum , .... ., :
A sticky, sap based residue from wood products,,
Heel ,.
Misa+ignment of the sawblade such that the blade is not
parallel to the miter gauge groove..
. • +'. ,t + ,, , !+._,.....
Kerr
The amount: of material removed by the blade in a
through cut. Also the slot produced by the blade in a non-
through or partial cut+
Kickback
An uncontrolled grabbing and throwing of the workpiece
back toward the front of the saw.
Leading End
The end of the workpiece which, during a rip type opera-
tion, is pushed intothe cutting tool first..
Miter Cut
An angle cutting operation made across the width of tile
workpiece.
Molding
A non through cut which produces a special shape in tile
workpiece used for joining or'decoration+
Push Stick
A device used to feed the workpiece through the saw dur-
ing narrow ripping type operations,. The push stick helps
keep tile operator's hands well away from the blade..
Push Block .+
A device used for' ripping type operations too narrow to
allow use of a push st!ck_ .
Rabbet
A notch inthe edge of a workpiece+
Resin
A sticky,sap based substance that has hardened.
Revolutions Per Minute (RPM)
The number' of turns completed by a spinning object in
one minute+
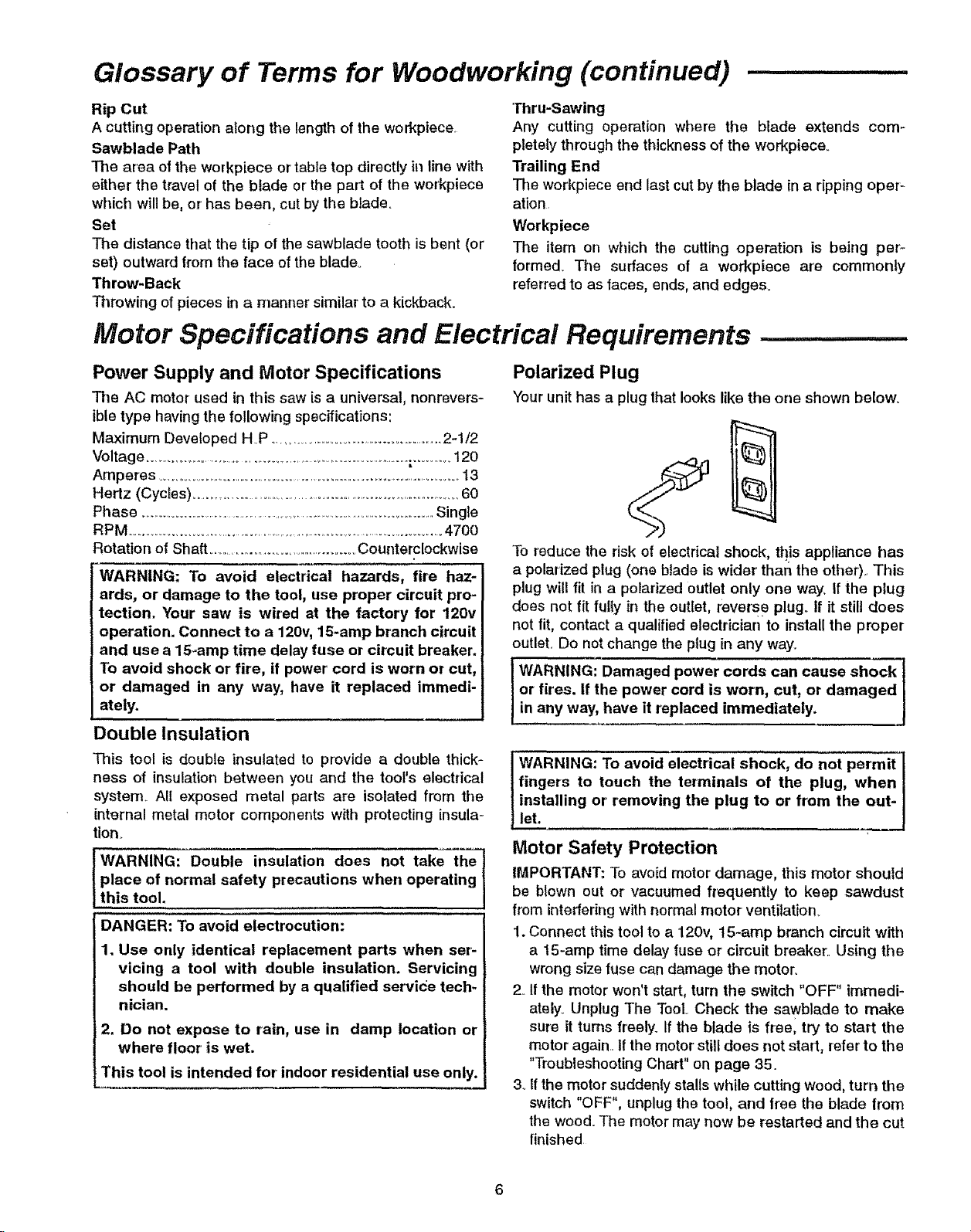
Glossary of Terms for Woodworking (continued) ............................
Rip Cut
A cutting operation along the length of the workpiece.
Sawblade Path
The area of the workpJece or table top directly in line with
either the travel of the blade or the part of the workpiece
which will be, or has been, cut by the blade..
Set
The distance that the tip of the sawblade tooth is bent (or
set) outward from the face of the blade.
Throw-Back
Throwing ofpieces in a manner similar to a kickback.
Thru-Sawing
Any cutting operation where the blade extends com-
pletely through the thickness of the workpiece.
Trailing End
The workpiece end last cut by the blade in a ripping oper-
ation
Workpiece
The item on which the cutting operation is being per-
formed_ The surfaces of a workpiece are commonly
referred to as faces, ends, and edges_
Motor Specifications and Electrical Requirements
Power Supply and Motor Specifications
Tile AC motor used in this saw is a universal, nonrevers-
ibletype having the following specifications:
Maximum Developed HP ....................................................2-1/2
Voltage ........................................................................................;.............120
Amperes ..................................................................................................13
Hertz (Cycles) .........................................................................................60
Phase .................................................................................................Single
RPM .........................................................................................................4700
Rotation of Shaft ...............................................Countemlockwise
WARNING: To avoid electrical hazards, fire haz-
ards, or damage to the tool, use proper circuit pro-
tection. Your saw is wired at the factory for 120v
operation. Connect to a 120v, 15-amp branch circu it
and use a 15oamp time delay fuse or circuit breaker.
To avoid shock or' fire, if power cord is worn or cut,
or damaged in any way, have it replaced immedi-
ately.
Double Insulation
Polarized Plug
Your unit has a plug that looks like the one shown below.
To reduce the risk of electrical shock, tt_is appliance has
a polarized plug (one blade is wider than the other).. This
plug will fit in a polarized outlet only one way, If the plug
does not fit fulfy in the outlet, reverse plugo If it still does
not fit, contact a qualified electrician to install the proper
outlet.. Do not change the plug in any way.
or fires. If the power cord is worn, cut, or damaged
in any way, have it replaced immediately.
This tool is double insulated to provide a double thick_
ness of insulation between you and the tool's electrical
systern_ All exposed metal parts are isolated from the
internal metal motor components wifh protecting insula-
tion..
WARNING: Double insulation does not take the
place of normal safety precautions when operating
this tool.
DANGER: To avoid electrocution:
1. Use only identical replacement parts when ser-
vicing a tool with double insulation. Servicing
should be performed by a qualified service tech-
nician.
2. Do not expose to rain, use in damp location or
where floor is wet.
This tool is intended for indoor residential use only.
fingers to touch the terminals of the plug, when
installing or removing the plug to or from the out-
i WARNING: To avoid electrical shock, do not permit
let.
Motor Safety Protection
IMPORTANT: To avoid motor damage, this motor should
be blown out or vacuumed frequently to keep sawdust
from interfering with normal motor' ventilation.
1. Connect this tool to a 120v, 15-amp branch circuit with
a 15-amp time delay fuse or circuit breaker. Using the
wrong size fuse can damage the motor°
2. If the motor won't start, turn the switch "OFF" immedi-
ately_ Unplug The Tool Check the sawblade to make
sure it turns freely. If the blade is freel try to start the
motor again.. If the motor still does not start, refer to the
"Troubleshooting Chart" on page 35.
3. If the motor suddenly stalls while cutting wood, turn the
switch "OFF", unplug the tool, and free the blade from
the wood° The motor may now be restarted and the cut
finished
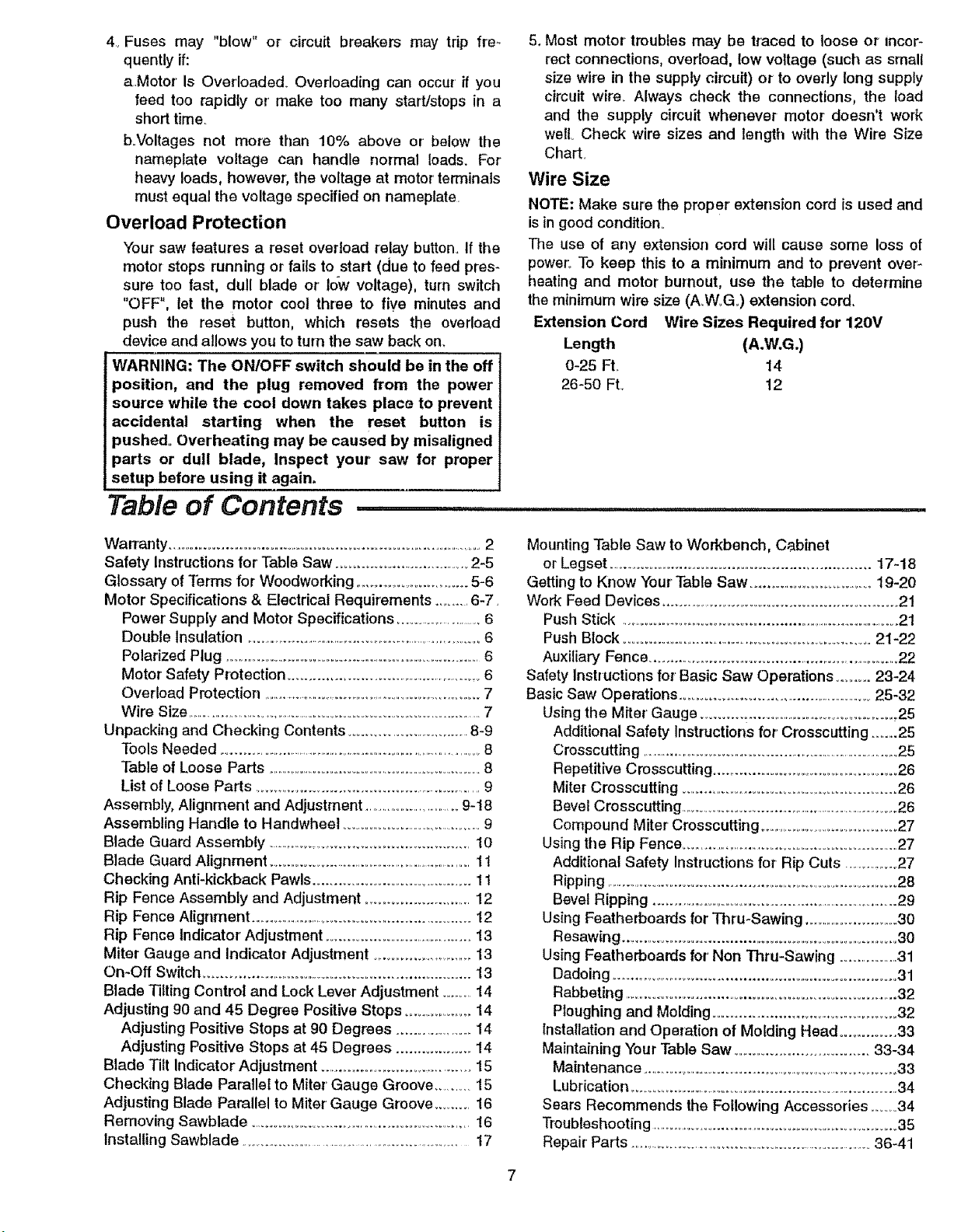
4._Fusesmay "blow"or circuitbreakersmaytrip fre_
quentlyif:
aMotor Is Overloaded. Ovedoading can occur' if you
feed too rapidly or' make too many start/stops in a
short time.
b.Voltages not more than 10% above or below the
nameplate voltage can handle normal loads. For
heavy loads, however, the voltage at motor terminals
must equal the voltage specified on nameplate.
Overload Protection
Your saw features a reset overload relay button. If the
motor stops running or fails to start (due to feed pres-
sure too fast, dull blade or' low voltage), turn switch
"OFF", let the motor cool three to five minutes and
push the reset button, which resets the overload
device and allows you to turn the saw back on.
WARNING: The ON/OFF switch should be in the off
position, and the plug removed from the power
source while the cool down takes place to prevent
accidental starting when the reset button is
pushed. Overheating may be caused by misaligned
parts or dull blade, Inspect your saw for proper
setup before using it again.
5, Most motor tmubtes may be traced to loose or incor-
rect connections, overload, low voltage (such as small
size wire in the supply circuit) or to overly long supply
circuit wire.. Always check the connections, the load
and the supply circuit whenever motor' doesn't work
well Check wire sizes and lengttl with the Wire Size
Chart.
Wire Size
NOTE: Make sure the proper extension cord is used and
is in good condition°
The use of any extension cord will cause some loss of
power, To keep this to a minimum and to prevent over'-
heating and motor burnout, use the table to determine
the minimum wire size (A_W,G,.)extension cord.
Extension Cord Wire Sizes Required for 120V
Length (A.W.G.)
0-25 FL 14
26-50 FL 12
Table of Contents
Warranty ..........................................................................................2
Safety Instructions for' Table Saw ....................................2-5
Glossary of Terms for Woodworking ...................................5-6
Motor Specifications & Electrical Requirements ............6-7.
Power Supply and Motor Specifications ..............................6
Double Insulation .................................................................................6
Polarized Plug .........................................................................6
Motor Safety Protection ....................................................6
Overload Protection .......................................................................7
Wire Size ...........................................................................................7
Unpacking and Checking Contents ...................................8-9
Tools Needed ..........................................................................................8
Table of Loose Parts ....................................................................8
List of Loose Parts .................................................................9
Assembly, Alignment and Adjustment ............................9-18
Assembling Handle to Handwheel ........................................9
Blade Guard Assembly ......................................................10
Blade Guard Alignment ................................................................1t
Checking Anti-kickback Pawls ..........................................11
Rip Fence Assembly and Adjustment ............................12
Rip Fence Alignment ...................................................................... 12
Rip Fence Indicator' Adjustment ..........................................13
Miter Gauge and Indicator Adjustment ...............................13
On-Off Switch ........................................................................13
Blade Tilting Control and Lock Lever Adjustment ...........14
Adjusting 90 and 45 Degree Positive Stops ......................14
Adjusting Positive Stops at 90 Degrees ................... 14
Adjusting Positive Stops at 45 Degrees ................... 14
Blade Tilt Indicator Adjustment ............................................15
Checking Blade Parallel to Miter' Gauge Groove ...........15
Adjusting Blade Parallel to Miter Gauge Groove ........ 16
Removing Sawbiade .............................................................16
Installing Sawblade .................................................................17
Mounting Table Saw to Workbench, Cabinet
or Legset ......................................................................17-18
Getting to Know Your Table Saw ......................................19-20
Work Feed Devices .............................................................21
Push Stick .......................................................................................21
Push Block .......................................................................21-22
Auxiliary Fence ..........................................................................22
Safety Instructions for Basic Saw Operations ........ 23-24
Basic Saw Operations .........................................................25-32
Using the Miter' Gauge .......... :.............................................25
Additional Safety Instructions for Crosscutting .........25
Crosscutting ....................................................................................25
Repetitive Crosscutting .................................................26
Miter Crosscutting ........................................................26
Bevel Crosscutting ..........................................................................26
Compound Miter Crosscutting ......................................27
Using tile Rip Fence ........................................................27
Additional Safety Instructions for Rip Cuts ..................27
Ripping ...............................................................................28
Bevel Ripping ......................................................................29
Using Featherboards for Thru-Sawing ......................................30
Resawing ............................................................................30
Using Featherboards for' Non Thru-Sawing ..................31
Dadoing ...........................................................................31
Rabbeting .................................................................... 32
Ploughing and Molding ....................................................32
Installation and Operation of Molding Head .............. 33
Maintaining Your Table Saw ............................... 33-34
Maintenance .......................................................................33
Lubrication .................................................................................... 34
Sears Recommends the Following Accessories ........34
Troubleshooting ......................................................................35
Repair Parts .....................................................................36-41
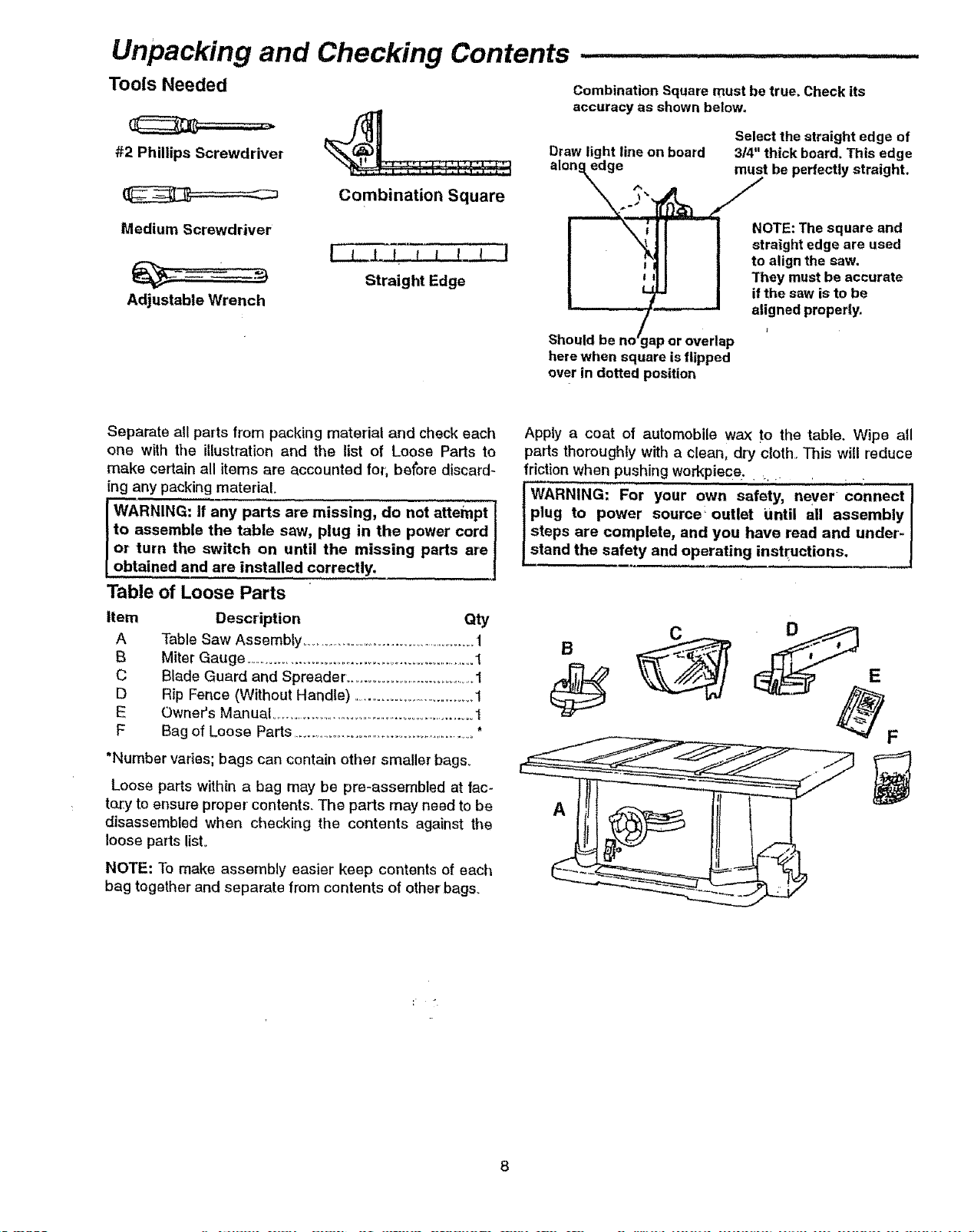
Unpacking and Checking Contents
Tools Needed
#2 Phillips Screwdriver
Combination Square
Medium Screwdriver
[_L_.L! r _ I._.Lj
__-_ii, ----L _.--__
Adjustable Wrench
Separate all parts from packing material and check each
one with the illustration and the list of Loose Parts to
make certain all items are accounted for, before discard-
ing any packing material.
WARNING: If any parts are missing, do not attempt
to assemble the table saw, plug in the power cord
or turn the switch on until the missing parts are
obtained and are installed correctly _
Table of Loose Parts
Straight Edge
Combination Square must be true. Check its
accuracy as shown below.
Select the straight edge of
Draw light line on board
alon edge
Should be no gap or overlap
here when square is flipped
over in dotted position
Apply a coat of automobile wax to the table. Wipe all
parts thoroughly with a clean, dry cloth, This will reduce
friction when pushing workpiece.. ....
l WARNiNG: "F'or your own safety, never connect
_plug to power source _outlet iantil all assembly
j steps are complete, and you have read and under-
[ stand the safety and operating instructions,
l
314" thick board, This edge
must be perfectly straight,
NOTE: The square and
straight edge are used
to align the saw,
They must be accurate
if the saw is to be
aligned properly.
Item Description Qty
A Table Saw Assembly .....................................................1
B Miter Gauge ......................................................................1
C Blade Guard and Spreader ......................................1
D Rip Fence (Without Handle) .................................1
E Owner's Manual ................................................................t
F Bag of Loose Parts ........................................................*
*Number varies; bags can contain other smaller bags..
Loose parts within a bag may be pro-assembled at fac-
tory to ensure proper contents, The parts may need to be
disassembled when checking the contents against the
loose parts lisL
NOTE: To make assembly easier keep contents of each
bag together and separate from contents of other bags.
B
A
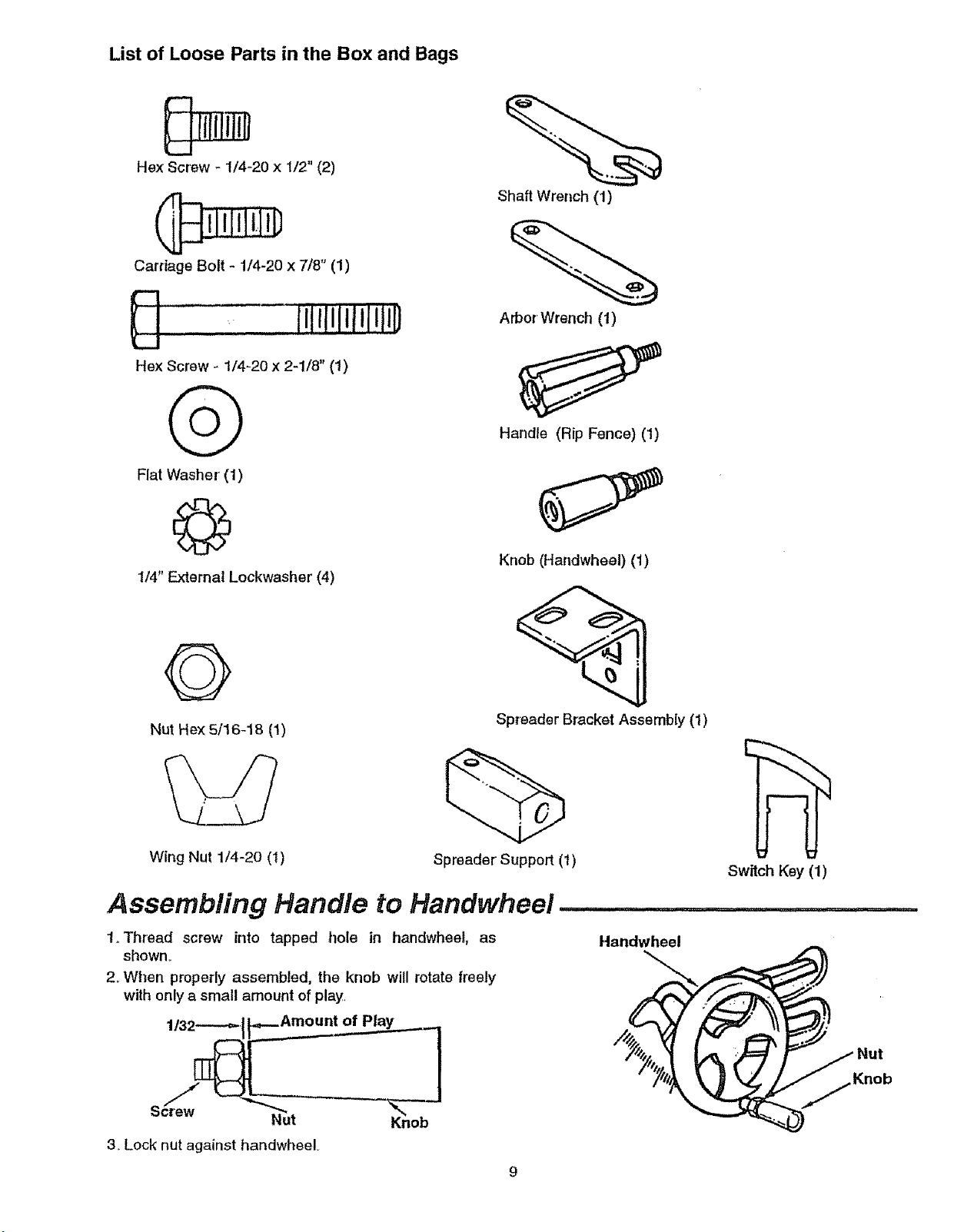
List of Loose Parts in the Box and Bags
He)( Screw - 1/4-20 x I/2" (2)
Carriage Bolt - 1/4-20 x 7/8" (1)
Shaft Wrench (1)
..... , Ii,[,!lllllJl ilt;
He× Screw _ 1/4-20 x 2-1/8" (1)
Flat Washer' (1)
©
114" External kockwasher (4)
Nut Hex 5/16-18 (!)
Arbor' Wrench (1)
Handle (Rip Fence) (1)
Knob (Handwheel) (1)
Spreader Bracket Assembly (1)
Wing Nut 1/4-20 (I)
Spreader Support (1)
Assembling Handle to Handwheel .......................
1.Thread screw into tapped hole in handwheel, as
shown.
2oWhen properly assembled, the knob will rotate freely
with only a small amount of play.
3. Lock nut against handwheel
Handwheel
Switch Key (1)
Nut
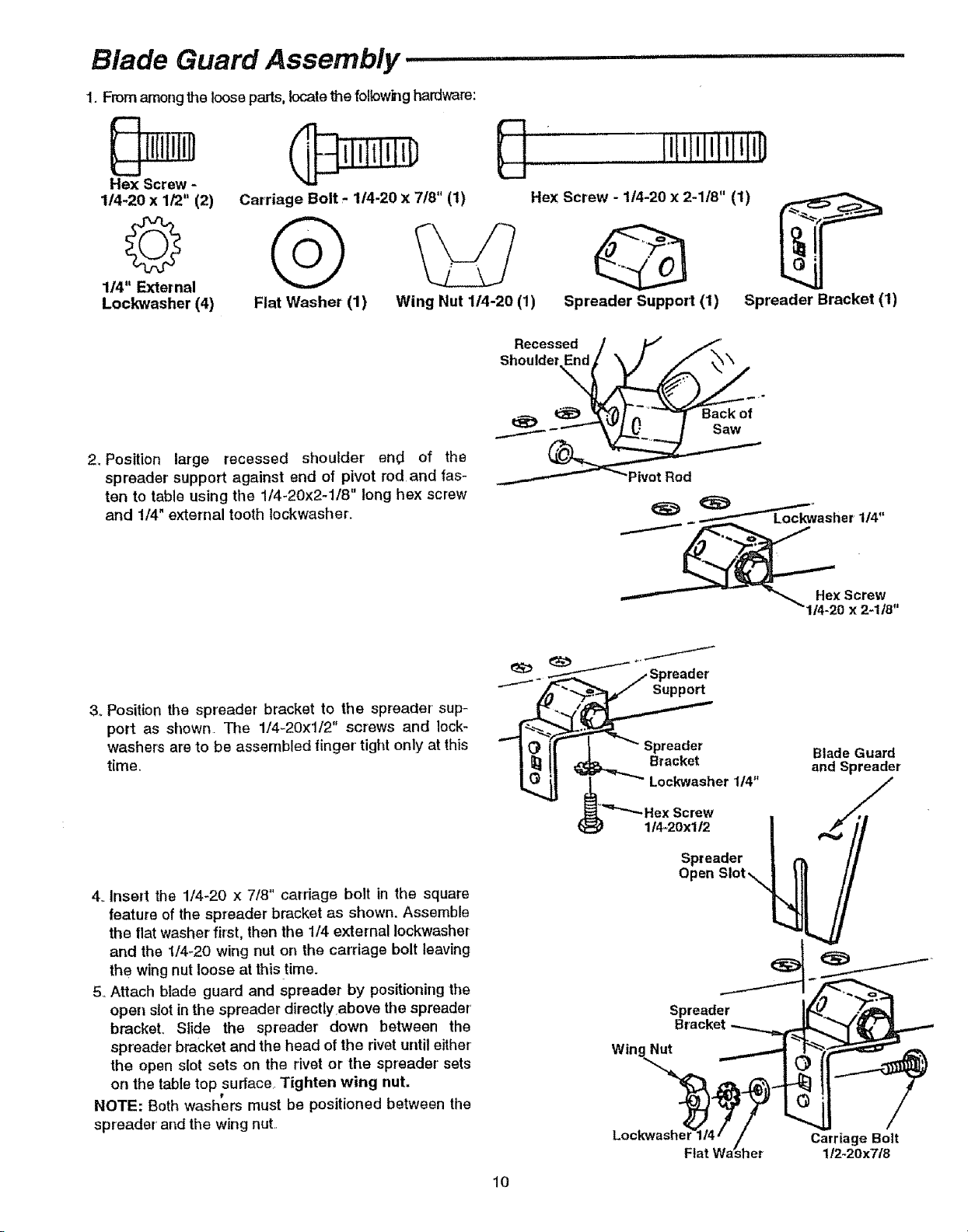
Blade Guard Assembly .......... '......
1. Frornamongthe loose parts, locate the folk_wirlghardware:
Hex Screw -
114-20 x 1/2" (2)
©
1/4" External
Lockwasher (4)
2. Position large recessed shoulder end of the
spreader support against end of pivot rod and fas-
ten to table using the 1/4-20x2-1/8" long hex screw
and 1/4" external tooth Iockwasher.
Carriage Bolt - 1/4-20 x 7/8" (1)
Q
Flat Washer (1)
Wing Nut 114-20 (1)
Hex Screw - 1/4-20 x 2-1/8" (1)
G
Spreader Support/1) Spreader Bracket (1)
Recessed / /.'f /
/ 2 8ackof
"'Pivot Rod
_ _asher 1/4"
Screw ,,
1/4-20x 2-1/8
3_ Position the spreader bracket to the spreader sup-
port as shown The 1/4-20xl/2" screws and lock-
washers are to be assembled finger' tight only at this
time.
4_ Insert the 1/4-20 x 7/8" carriage bolt in the square
feature of the spreader bracket as shown. Assemble
the fiat washer first, then the 1/4 external Iockwasher
and the 1/4-20 wing nut on the carriage bolt leaving
the wing nut loose at this time.
5, Attach bIade guard and spreader by positioning the
open slot in the spreader directly above the spreader'
brackeL Slide the spreader down between the
spreader bracket and the head of the rivet until either
the open slot sets on the rivet or the spreader sets
on the table top sudace. Tighten wing nut.
NOTE: Both wash'ers must be positioned between the
spreader' and the wing nut,,
Spreader
Win Nut
Carriage Belt
1/2-20x7/8
10
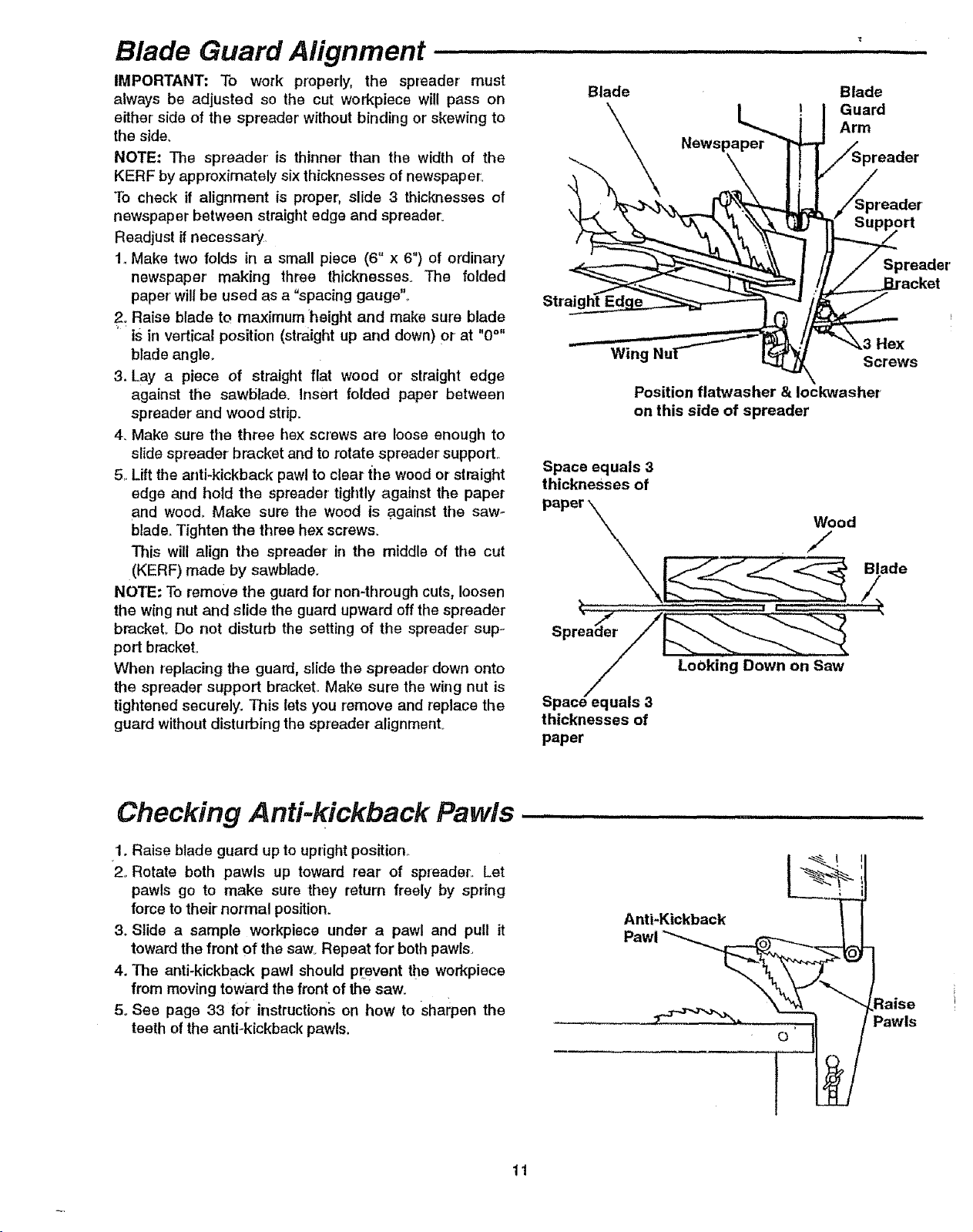
Blade Guard Alignment
IMPORTANT: To work properly, the spreader must
always be adjusted so the cut workpiece will pass on
either'side of the spreader without binding or'skewing to
the side.
NOTE: The spreader' is thinner than the width of the
KERF by approximately six thicknesses of newspaper,
To check if alignment is proper, slide 3 thicknesses of
newspaper between straight edge and spreader:
Readjust ifnecessary,
1,,Make two folds in a small piece (6" x 6") of ordinary
newspaper' making three thicknesses. The folded
paper'will be used as a "spacing gauge'S
2. Raise blade to maximum height and make sure blade
"is in vertical position (straight up and down) Or at "0°"
blade angle.
3. Lay a piece of straight flat wood or straight edge
against the sawblade,, Insert folded paper between
spreader and wood strip.
4. Make sure the three hex screws are loose enough to
slide spreader bracket and to rotate spreader' support,.
5, Lift the anti-kickback pawl to clear the wood or straight
edge and hold the spreader tightly against the paper
and wood,, Make sure the wood is ,against the saw-
blade,,Tighten the three hex screws.
This will align the spreader in the middle of the cut
(KERF) made by sawblade.
NOTE: To remove the guard for non-through cuts, loosen
the wing nut and slide the guard upward off the spreader
bracket,. Do not disturb the setting of the spreader' sup-
portbracket.
When replacing the guard, slide the spreader' down onto
the spreader support bracket.. Make sure the wing nut is
tightened securely.. This lets you remove and replace the
guard without disturbing the spreader alignment.
Blade Blade
Strai!
Wing
Position flatwasher & Iockwasher
on this side of spreader
Space equals 3
thicknesses of
/ Looking Down on Saw
/
S
pace equals 3-
thicknesses of
paper
ii IIII,Mlll ,,I,I
Guard
Arm
Spreader'
,tex
Screws
Checking Anti-kickback Pawls,
1. Raise blade guard up to upright position..
2. Rotate both pawls up toward rear of spreader° Let
pawls go to make sure they return freely by spring
force to their normal position.
3. Slide a sample workpiece under a pawl and pull it
toward the front of the saw_Repeat for both pawls.
4. The anti-kickback pawl should pr+eventthe workpiece
from moving toward the front of the saw.
5oSee page 33 foi+instructions on how to sharpen the
teeth of the anti-kickback pawls.
"a'j"+"+°°" T
:laise
Pawls
11
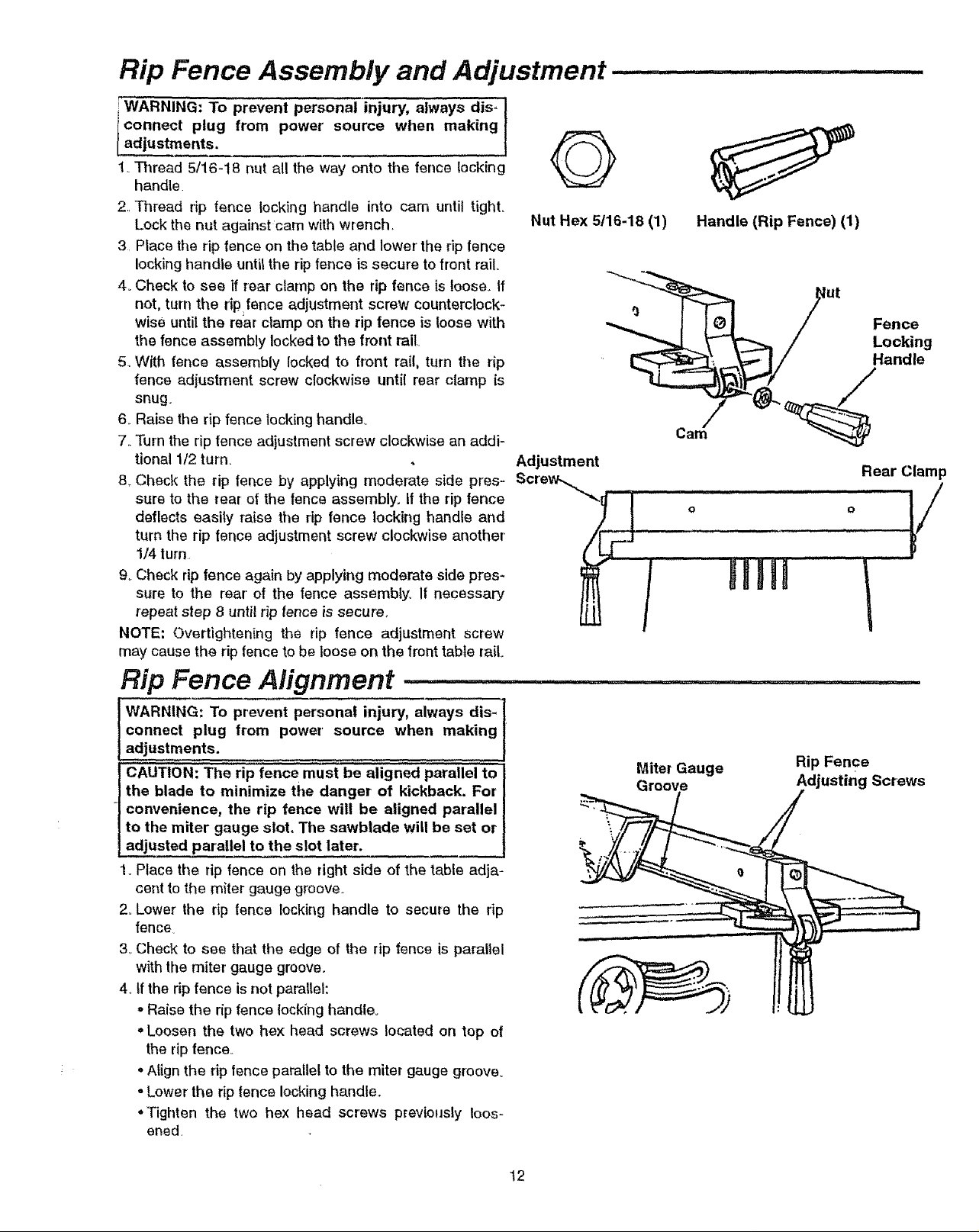
Rip Fence Assembly and Adjustment ...........................
i WARNING: To prevent personal injury, always dis- i
l connect plug from power source when making I
adjustments.
1. Thread 5/16-18 nut all the way onto the fence locking
handle
2, Thread rip fence locking handle into cam until tight,,
Lock the nut against cam with wrench,
3 Place the rip fence on the table and lower' the rip fence
locking handle until the rip fence is secure to front rail.
4. Check to see if rear' clamp on the rip fence is loose,. If
not, turn the rip fence adjustment screw counterclock-
wise until the rear clamp on the rip fence is loose with
the fence assembly locked to the front rail,
5, With fence assembly locked to front rail, turn the rip
fence adjustment screw clockwise until rear clamp is
snug.
6, Raise the rip fence lockinghandle.
7,.Turn the rip fence adjustment screw clockwise an addi-
tional 1/2 turn.
8. Check the rip fence by applying moderate side pres-
sure to the rear ef the fence assembly, If the rip fence
deflects easily raise the rip fence locking handle and
turn the rip fence adjustment screw clockwise another
1/4 turn.
9. Check rip fence again by applying moderate side pres-
sure to the rear of the fence assembly. If necessary
repeat step 8 until rip fence is secure.
NOTE: Overtightening the rip fence adjustment screw
may cause the rip fence to be loose on the front table rail.
Q
Nut Hex 5/16-18 (1)
Adjustment
Handle (Rip Fence) (1)
/
ut Fence
/ Locking
Rear Clamp
o
Rip Fence Alignment ..................
connect plug from power' source when making
j WARNING: To prevent personal injury, always dis- I
adjustments.
i CAUTION: The rip fence must be aligned parallel to
'1the blade to minimize the danger of kickback. For }
} convenience, the rip fence will be aligned parallel
I to the miter gauge slot. The sawblade will be set or I
1adjus!ed parallel to the slot later. !
1,.Place the rip fence on the right side of the table adja-
cent to the miter gauge groove,.
2. Lower the rip fence locking handle to secure the rip
fence.
3. Check to see that the edge of the rip fence is parallel
with the miter gauge groove.
4. If the rip fence is not parallel:
oRaise the rip fence locking handle.
• Loosen the two hex head screws located on top of
the rip fence,.
oAlign the ripfence parallel to the miter gauge groove.
oLower the rip fence locking handle,,
•Tighten the two hex head screws previously loos-
ened,
m
I
Miter Gauge
Rip Fence
Adjusting Screws
!2
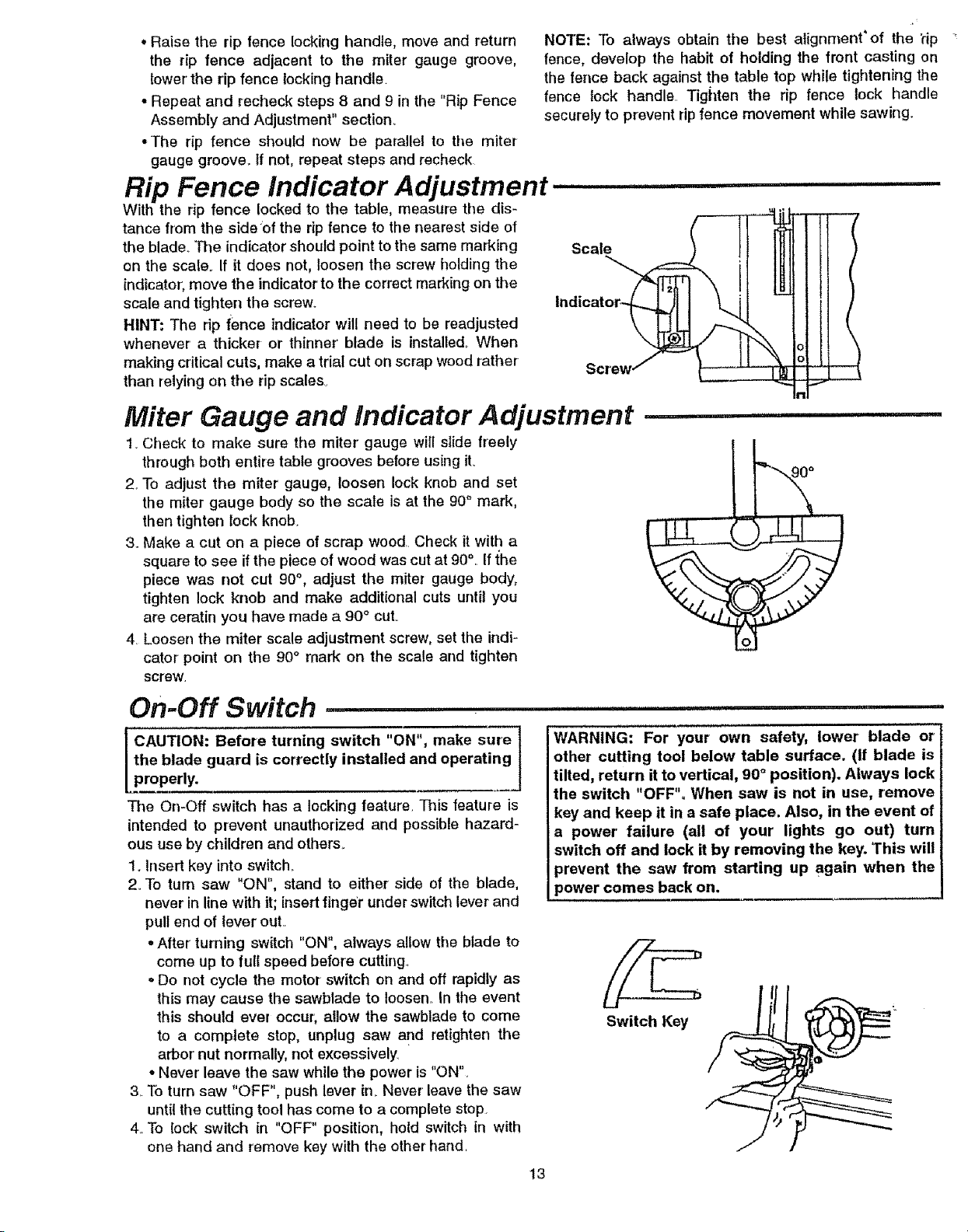
°Raisethe ripfencelockinghandle,moveandreturn
thenipfenceadjacentto the mitergaugegroove,
lower'theripfencelockinghandle.
•Repeatandrechecksteps8 and9inthe"RipFence
Assemblyand Adjustment" sectien_
•The rip fence should now be parallel to the miter
gauge groove.. If not, repeat steps and recheck
NOTE: To always obtain tile best atignment'of the 'rip
fence, develop the habit of holding the front casting on
the fence back against the table top while tightening the
fence tock handle Tigilten the rip fence lock handle
securely to prevent rip fence movement while sawing.
Rip Fence Indicator Adjustment .......
With the rip fence locked to the table, measure the dis-
tance from the side'of the rip fence to the nearest side of
the blade.. The indicator should point to the same marking
on the scale. If it does not, loosen the screw holding the
indicator; move the indicator to the correct marking on the
scale and tighten the screw.
HINT; The dp fence indicator will need to be readjusted
whenever a thicker or thinner' blade is installed. When
making critical cuts, make a trial cut on scrap wood rather
than relying on tile rip scales.
Scal_
screw (
Miter Gauge and Indicator Adjustment
1. Check to make sure the miter' gauge will slide freely
through both entire table grooves before using it.
2. To adjust the miter gauge, loosen lock knob and set
the miter gauge body so the scale is at the 90° mark,
then tighten lock knob.
3. Make a cut on a piece of scrap wood.. Check it with a
square to see if the piece of wood was cut at 90% If the
piece was not cut 90°, adjust the miter gauge body,
tighten lock knob and make additional cuts until you
are ceratin you have made a 90° cut..
4. Loosen the miter scale adjustment screw, set the indi-
cator point on the 90° mark on the scale and tighten
screw.
lUUlU,ii
90°
On-Off Switch
WARNING: For your own safety, lower blade or
the blade guard is correctly installed and operating
lc.° io.;oo,o.o,um,°0ow.c.o.., o.ol
properly.
The On-Off switch has a locking feature. This feature is
intended to prevent unauthorized and possible hazard-
ous use by children and others..
1. Insert key into switch.
2. To turn saw "ON", stand to either side of the blade,
never in line with it; insert finger under switch lever and
pull end of lever out..
oAfter' turning switch "ON", always allow the blade to
come up to full speed before cutting
oDo not cycle the motor switch on and oft rapidly as
this may cause the sawblade to loosen. In the event
this should ever occur, allow the sawblade to come
to a complete stop, unplug saw and retighten the
arbor' nut normally, not excessively "
° Never leave the saw while the power is "ON".
3_To turn saw "OFF", push lever in. Never leave the saw
until the cutting tool has come to a complete stop.
4..To lock switch in "OFF" position, hold switch in with
one hand and remove key with the other hand
other cutting tool below table surface. (If blade is
tilted, return it to vertical, 90 ° position). Always lock
the switch "OFF". When saw is not in use, remove
key and keep it in a safe place. Also, in the event of
a power' failure (all of your lights go out) turn
switch off and lock it by removing the key. 'This will
13
_revent the saw from starting up again when the
}ower comes back on.
Switch Key