
Technical Information
Thermal Processing
Thermal Staking Design
Guidelines
In manufacturing products
with thermoplastic components,
it is often necessary to join a
thermoplastic to a part of
dissimilar material, whether
it be metal, a dissimilar plastic,
or other material. This technical
information sheet provides
design guidelines, configurations, and techniques for successful thermal (heat) staking.
GENERAL DESCRIPTION:
Thermal staking is an assembly
method that uses the controlled
melting and reforming of a
plastic stud or boss to capture
or lock another plastic or metal
component of an assembly
in place.
The plastic stud protrudes
through a hole in the component
to be locked in place. The heated
thermal tip contacts the top of
the stud, which melts and fills
the volume of the tip cavity to
produce a head, locking the component in place. The progressive
melting of plastic under continuous pressure forms the head.
When staking, the right combination of heat and pressure for the
application is critical.
ADVANTAGES:
• Simplification of machinery
• Reduced cost of machinery
• Multiple fastening points
• Allows higher density of welds
compared to hot air cold form
or ultrasonic welding
• Many different size or shaped
heads can be formed
Following are descriptions and
specifications for the various
staking profiles.
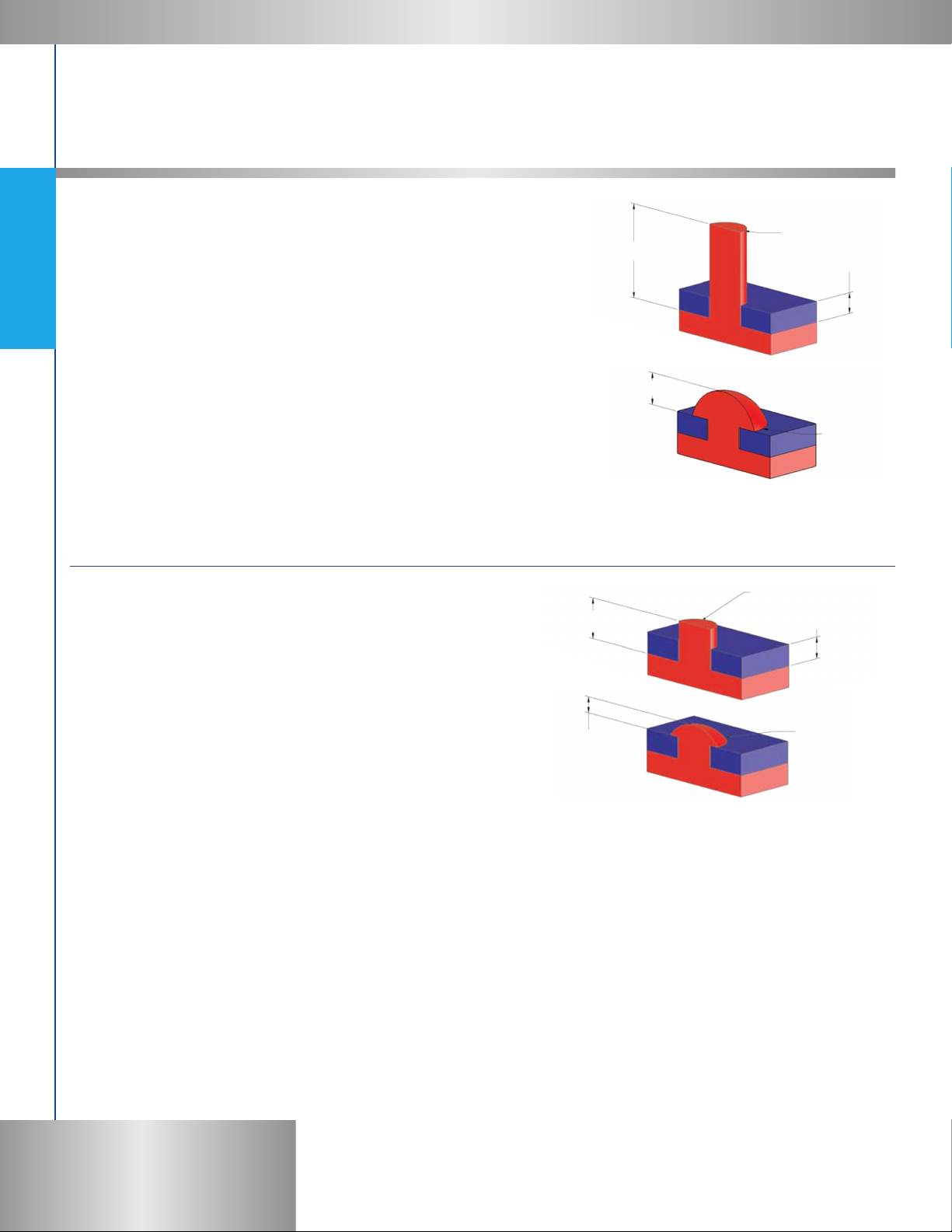
DOME STAKE - HIGH PROFILE:
• To obtain optimal results use with a boss of 0.250”
or less O.D.
• Smaller head means faster weld times
• Under normal conditions this method will create a perfectly
symmetrical weld
• Recommended for crystalline plastics with highly defined
melting points such as 33% G.F.
• Works well with plastics with abrasive fillers and for materials
that easily degrade
• Dome stakes come in two basic silhouettes: high and low
Total Boss Height =
CMT + 1.75 X
Finished Height
= 0.750 X
Boss Dia = X
CMT = Captured
Material Thickness
Finished
Diameter
= 2 X
• Counter bored holes can improve the appearance of these welds
• Stronger weld but slower weld time than a low profile
DOME STAKE - LOW PROFILE:
• To obtain optimal results use with a boss of 0.250” or less O.D.
• Smaller head means faster weld times
• Under normal conditions this method will create a perfectly
symmetrical weld
• Recommended for crystalline plastics with highly defined melting
points such as 33% G.F.
• Works well with plastics with abrasive fillers and for materials
that easily degrade
• Dome stakes come in two basic silhouettes: high and low
• Counter bored holes can improve the appearance of these welds
Total Boss Height
= CMT + 0.45 X
Finished Height
= 0.375 X
Figure 1. Dome stake, high profile.
Boss Dia = X
CMT = Captured
Material Thickness
Figure 2. Dome stake, low profile.
Finished
Diameter
= 1.5 X