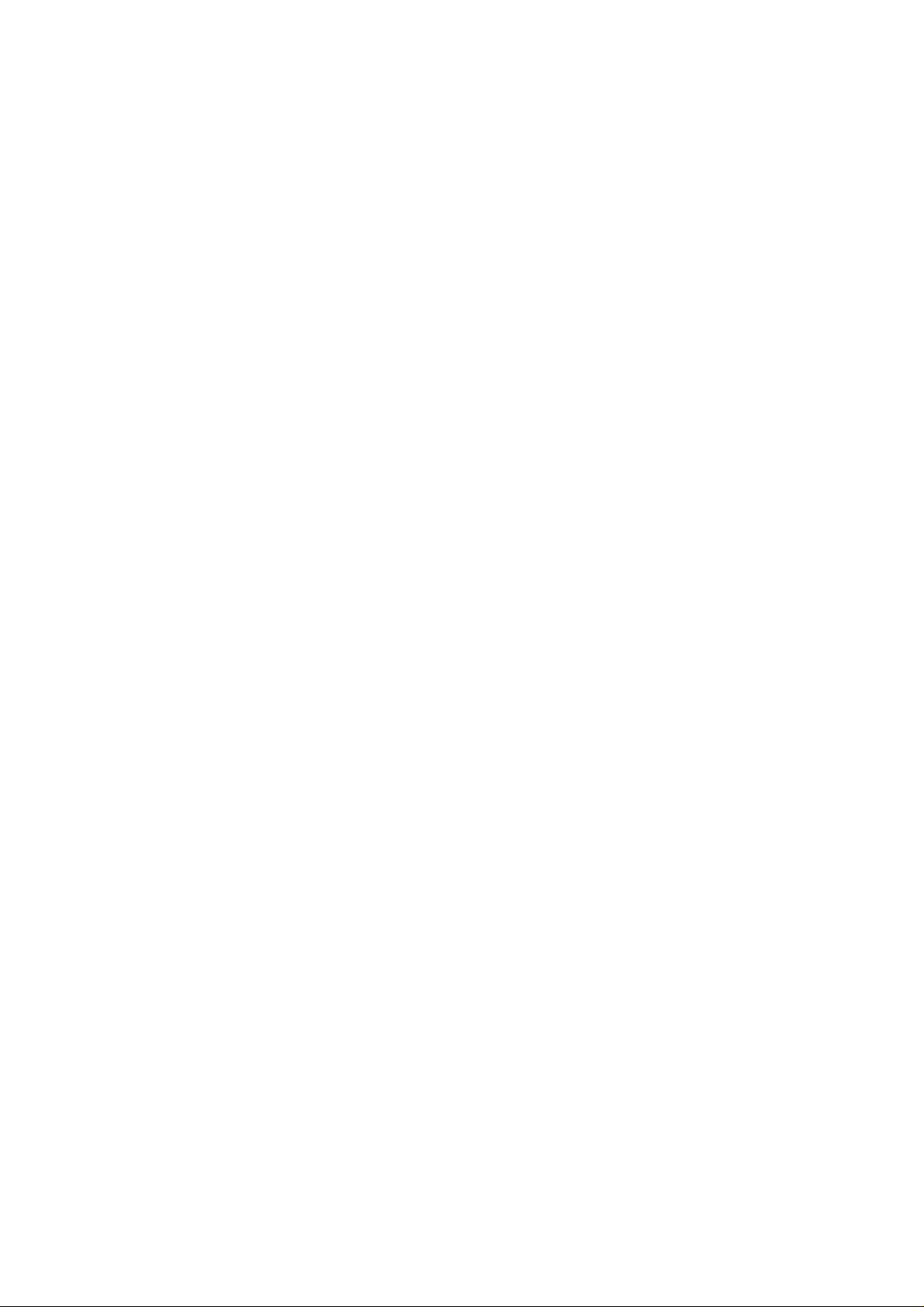
2
B029
Page No.
1. SERVICING INSTRUCTIONS
1.1 Replacement of Parts 3
1.2 To Gain General Access
- Removing the Front Panel 3
- Removing the Side Panels 4
- To Lower the Control Panel 4
1.3 Access to the Combustion Chamber
- Removing the Sealed Combustion Chamber 5
- Removing the Burner and Injectors 5
- Removing the Electrodes 6
- Removing the Main Heat Exchanger 7
- Removing the Air Pressure Switch 7
- Removing the Venturi Device 8
- Removing the Fan 8
1.4 Servicing and Removal of the Gas Valve
- Setting Gas Pressure 9
- Removing the Spark Ignitor 11
- Removing the Gas Valve 12
1.5 Access to the Hydraulic Circuit
- Removing the D.H.W. (Secondary) Exchanger 12
- Removing the Safety Valve 13
- Removing the Automatic Air Vent 13
- Removing the Main Flow Circuit Switch 13
- Removing the Pump 14
- Removing the Pressure Gauge 14
- Removing the Expansion Vessel 15
- Removing the Overheat Ther mostat 15
- Removing the Heating Temperature Sensor (N.T.C.) 15
1.6 Access to the Control System
- Checking the Fuses 16
- Removing the Time Clock 16
- Removing the P.C.B.s 17
2. FAULT FINDING
2.1 Fault Finding Guide (Flow-chart) 18
2.2 Fault Finding Using the Total Check System 23
3. ELECTRICAL DIAGRAMS
3.1 Electrical Connection 24
3.2 Functional Flow Connection 25
4. SHORT SPARE PARTS LIST
26
TABLE OF CONTENTS
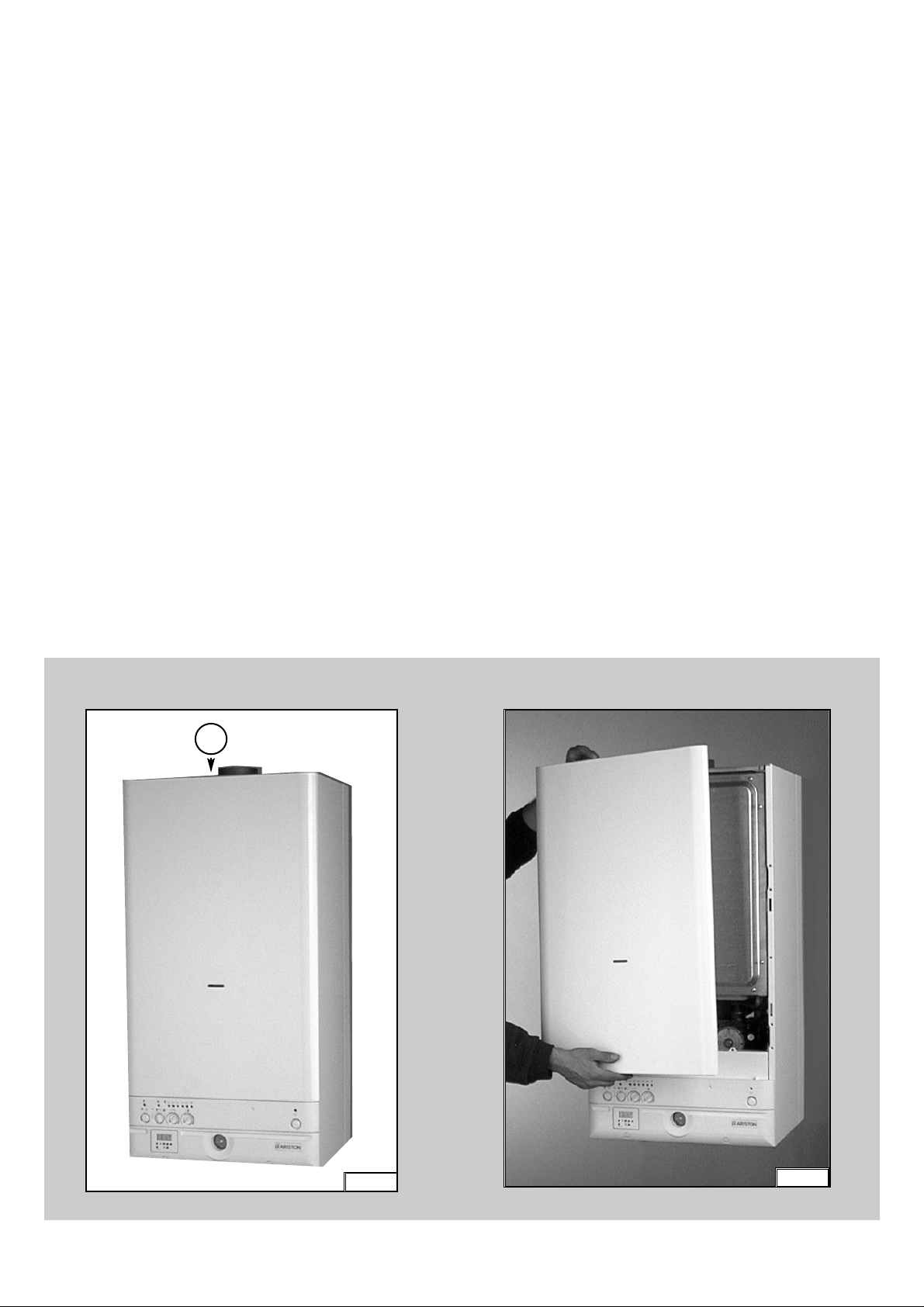
3
B029
1. SERVICING
INSTRUCTIONS
The life of individual components vary and they will need servicing or
replacing as and when faults develop.
The fault finding sequence chart in chapter 2 will help to locate which
component is the cause of any malfunction, and instructions for removal,
inspection and replacement of the individual parts are given in the following
pages.
1.1 Replacement
of Parts
1.2 To Gain General
Access
All testing and maintenance operations on the boiler require the control panel
to be lowered.This will also require the removal of the casing.
To dismantle the front part of the casing, proceed as follows:
1.
Remove screw “A”
(see fig. 1.1)
;
2.
Lift the front panel up and forward
(see fig. 1.2)
.
A
Fig. 1.2
Fig. 1.1
To ensure efficient safe operation, it is recommended that the boiler is
serviced annually by a competent person.
Before starting any servicing work, ensure both the gas and electrical
supplies to the boiler are isolated and the boiler is cool.
Before and after servicing, a combustion analysis should be made via the flue
sampling point (please refer to the Installation Manual for further details).
After servicing, preliminary electr ical system checks must be carried out to
ensure electrical safety (i.e. polar ity, earth continuity, resistance to earth and
short circuit).
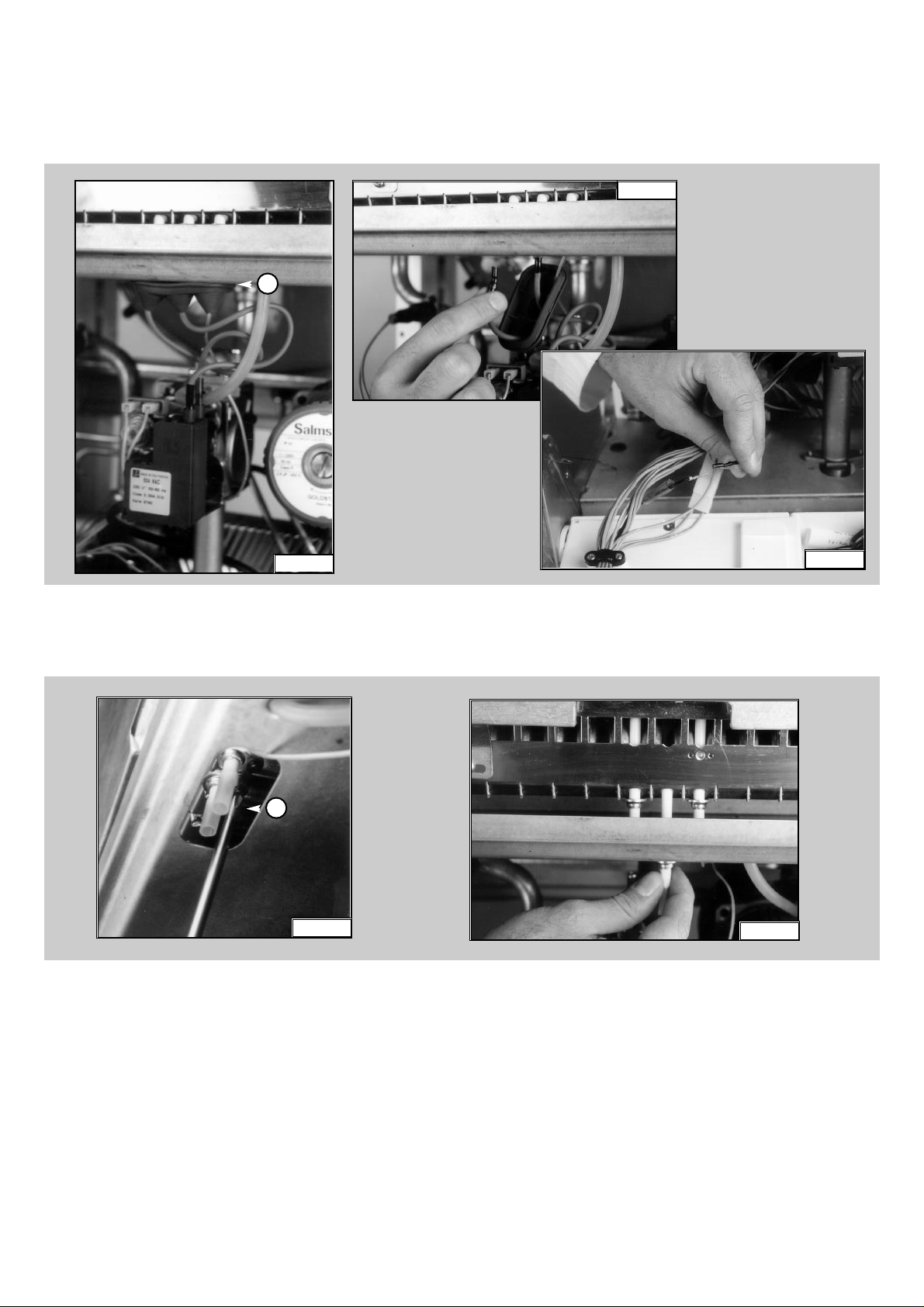
6
B029
Removing the electrodes 1.
Remove rubber gasket “G”
(see fig. 1.13)
;
2.
Disconnect ignition leads by pulling downward
(see fig. 1.14)
;
3.
To remove the flame sensor, disconnect the cable at its only connection
point close to the P.C.B.
(see fig. 1.15)
;
5.
Remove screw “H” using a Philips No.2 star tip screwdriver
(see fig. 1.16)
;
6.
Slide the electrode gently downward
(see fig. 1.17).
To replace, repeat the steps in reverse order , pa ying particular attention to the
following:
a
-Centre the electrode in the positioning hole carefully, otherwise the
electrode may break;
b
-Check that the cables have been connected correctly;
c
-Check that the rubber gasket covers the cable/electrode connection
point completely.
Fig. 1.13
G
Fig. 1.14
Fig. 1.15
Fig. 1.16
Fig. 1.17
H
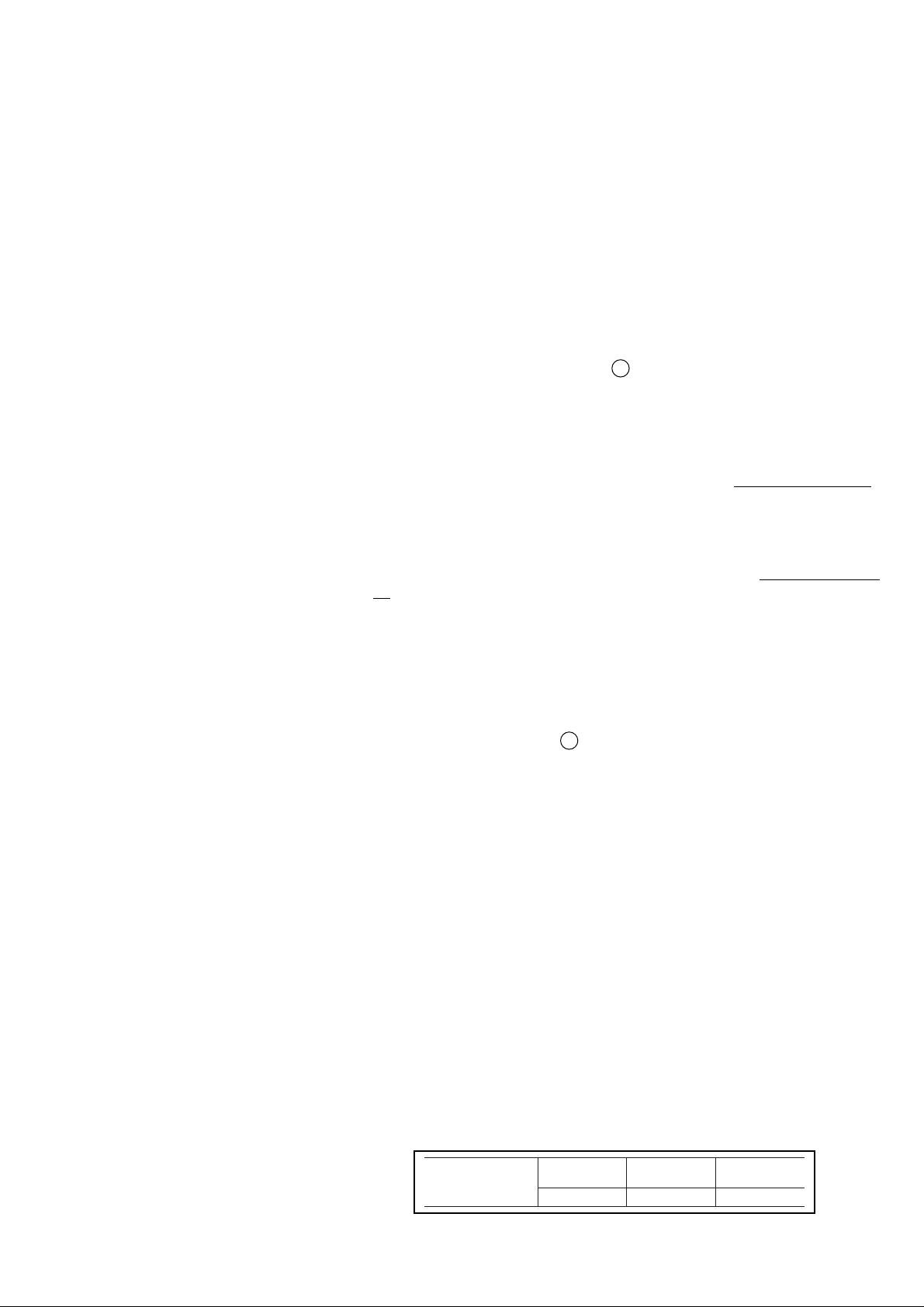
10
B029
Setting the minimum and the maximum power of the boiler
1. Check that the supply pressure to the gas valve is a minimum of 20 mbar
for natural gas.
2. To do this, remove the screw “A”.
Fit the pipe of the pressure gauge to the pressure connection of the gas
valve “B”.
When you have completed this operation, replace the screw “A” securely
into its housing to seal off the gas.
3. To check the pressure supplied by the gas valve to the burner, remove the
screw “C”. Fit the pipe of the pressure gauge to the pressure outlet of the
gas valve “D”.
Disconnect the compensation pipe either from the gas valve or from the
sealed chamber.
4. Set the On/Off button to position < I > and the "summer/winter" switch to
the winter position.
To set the maximum power, turn on the hot water tap and allow the hot
water tap to run at a rate of about 8 litres/minute so that the main burner
lights.
Adjust nut “E” on the modureg to set the gas pressure (displayed on the
pressure gauge) corresponding to the maximum power (see table “A”page 11).
5. T o set the minim um pow er, disconnect a supply terminal from the modureg
and adjust screw “F”.
Turn the screw clockwise to increase the pressure and counter-clockwise to decrease the pressure (displayed on the
pressure gauge) corresponding to the minimum power (see table “A” page
11).
6. When you have completed the above operations, turn off the
hot water tap, re-connect the supply terminal to the modureg
on the gas valve and replace the cap on the screw of the
modureg.
Setting the maximum heating circuit power
7. To set the maximum heating circuit power, place the
On/Off button to position < I > and the "summer/winter" switch to winter
position.
Turn the knob of the heating ther mostat clockwise to maximum;
8. Remove the left hand inspection panel of the P.C.B. and fit a small
cross-head screwdriver in to the right hand potentiometer.Turn clockwise
to increase the pressure or counter-clockwise to reduce the pressure.
Adjust the setting to the required heating pressure value (displayed on the
pressure gauge), as indicated in the diagrams shown in page 11.
9. Turn off the boiler by placing the main switch to the "Off" position.
Setting pressure for soft ignition.
Disconnect the detection electrode connection from the P.C.B. (see fig.
1.13).
Start the boiler and during the ignition sequence adjust the centre
potentiometer until the gas pressure reads the required gas pressure as
per the table below.
Once the gas pressure is set turn off the boiler and reconnect the
connection to the P.C.B.
NB.:It may be necessary to reset the flame failure reset a number of times
during this operation.
Recommended pressure for
slow ignition
NATURAL GAS (G20) BUTANE GAS (G30) PROPANE GAS (G31)
5 mbar - 1.95 in w.g.
18 mbar - 7.0 in w.g. 19 mbar - 7.4 in w.g.

Regulating the heating power for
natural gas (G20)
Regulating the heating power for
butane gas (G30)
Regulating the heating power for
propane gas (G31)
model 23
model 27
model 23
model 27
GAS REQUIREMENTS
Gas rate
Gas rate
Inlet pressure
Burner pressure
Burner pressure
Burner injectors
40
38
36
34
model 23
model 27
NATURAL GAS (G20) BUTANE GAS (G30) PROPANE GAS (G31)
max
min
3
/h
3.0 m 106.0 ft
3
/h 42.3 ft
1.2 m
3
3
/h
20 mbar 7.8 in w.g.
max 12.3 mbar 4.8 in w.g.
min
2.0 mbar 0.8 in w.g.
13 x 1.25
/h
3
0.88 m 31.1 ft
/h
3
0.35 m
/h 12.3 ft
28 mbar 10.9 in w.g.
28 mbar 10.9 in w.g.
5.1 mbar 2.0 in w.g.
13 x 0.72
3
/h
1.15 m3/h 40.6 ft3/h
3
/h
0.46 m3/h 16.2 ft3/h
37 mbar
37 mbar 14.4 in w .g.
7.0 mbar 2.7 in w.g.
13 x 0.72
14.4 in w .g.

12
B029
10. Remove the pipe from the pressure gauge and connect screw “C” to the
pressure outlet in order to seal off the gas.
11.Carefully check the pressure outlets for gas leaks (valve inlet
and outlet).
IMPORTANT!
Whenever you disassemble and reassemble the gas connections, always
check for leaks using a soap and water solution.
Setting the anti-cycling device
This appliance is equipped with a potentiometer which delays the ignition of
the heating control and is situated on the P.C.B .(see the electrical diagrams).
By adjusting the potentiometer, it is possible to change the time interval
between the burner shutting down and its next ignition.
It is preset at 1 minute and can be adjusted from 0 to 2 minutes.
Use this control in particular situations where continuous shutting down and
ignition of the main burner occurs.
40 50 60 70 80
Anti-cycling
Device
Soft-light
Adjustment
Max. Heating
Adjustment
Removing the spark generator (SIT Sigma gas valve)
1.
Disconnect ignition leads “Q” by pulling upwards
(see fig. 1.27)
;
2.
Remove the screws “R”
(see fig. 1.28)
with a Pozidrive
No.2 star tip screwdriver;
3.
Remove the spark generator.
Fig. 1.27
Fig. 1.28 Fig. 1.29
Q
R
C C

14
B029
1.5
Access to the
Hydraulic Circuits
Fig. 1.37
U
U
Removing the D.H.W. (secondary)
exchanger
1.
Remove the screw “U”
(see fig. 1.37)
;
2.
Push the exchanger towards the rear of the
boiler, lift upwards and remove out of the
front of the boiler;
3.
Before replacing the exchanger ensure that
the O-rings are in good condition and
replace if necessary.
Important!
Before any component is removed, the boiler
must be drained of all water.
Removing the gas valve
1.
Disconnect all the cables from the solenoid and
modureg;
2.
Remove the spark generator;
3.
Release the top nut “S” using a 30 mm open ended
spanner
(see fig. 1.31)
;
4.
Remove the screws “T” from the bottom of the gas
valve pipe
(see fig. 1.32)
.
Attention!!
The gas valve is connected with the two pipes
(as shown) with an O-ring connection.
Fig. 1.33
Fig. 1.34
Fig. 1.35
S
T
T
Fig. 1.36

19
B029
Removing the P.C.B.s
1.
Isolate electricity;
2.
Remove the front cover of the boiler;
3.
Remove the inspection panel
(see fig. 1.6-1.7
);
5.
Remove the mounting screws “A6’
(see fig. 1.53)
;
6.
Disconnect the connection cable”A7”
(see fig. 1.54)
;
7.
To remove the 24V P.C.B.: remove the electrical plug
connectors and screws “A8”
(see fig. 1.55)
;
8.
To remove the 240V P.C.B.: remove the electrical plug
connectors and screws “A9”
(see fig. 1.56)
;
9.
Replace either P.C.B. in reverse order.
Fig. 1.53
Fig. 1.54
Fig. 1.55
Fig. 1.56
A6
A6
A6
A6
A7
A7
A8
A8
A9
A9
N.B.
It is possible to by-pass the time clock in the event of failure by simply
unplugging the electrical connection from the P.C.B.
(see fig. 1.48
). This will
revert control of the central heating to the room stat connection on the rev erse
of the control panel.

It is possible to detect and correct any defect by using the standard fault
finding diagrams described in this chapter.
2.1
Fault Finding Guide
(Flow-chart)
Preliminary Checks
Makesure that:
1) Thereis sufficient
water i nthesys tem
2) Thegas is turned on
3) Theelectr icitytothe
boiler is on
Press the
On /Off Button
HAS
THE LIGHT fOR
THE POWER SUPPLY
COME ON?
YES
NO
1)Checkthefuses
2)Check thepower
supply cord, plug and
outlet
3)Check/replacethepower
supply PCB
NO
SUMMER
ISHOT
WATERBEING
DEMANDED?
NO
FOR BOILERS
EQUIPPED WITHAN
ELEC T R ONICANT -FREEZE
SYST EM :HASTHESAFETYBEEN
TRIGGERED TO ACTIVATE
TH EDEVIC E?
(Tsensor <5°C)
SETTING
FOR THE OPERATING
MODE
FUME DISCHARGE TEST
YES
YES
A
YES
WIN TER
YES
ISHOT
WATERBEING
DEMANDED?
NO
DO THE
PROGRAMMING
TIMERAND/OREXTERNAL
TH ERM OS T ATNEED
TO BE ACTIVATED
NO
FOR BOILERS
EQUIPPED WITHAN
ELEC T R ONICANT -FREEZE
SYST EM :HASTHESAFETYBEEN
TRIGGERED TO ACTIVATE
TH EDEVIC E?
(Tsensor <5°C)

A
DOES THE
CIRCULATIONPUMP
COME ON?
YES
NO
1)Checkfor air in the
system
2)Checkthepressureswitch
foractivatingpump
3)Check/replace water
gaug eandre fill the
thesyste mproperly
1)Turn the boiler off
and thenbackon
again (safe tyreset)
YES
DOES THE
INS UFFICI ENT WATER
INDIC ATORLIG H TCOME
ON?(wi thi n
40sec.)
NO
B
POWER TO
THE PUMP ?
YES
1)Check to see if pump is
stuck
2)Replacecirculationpump
NO
1) Check
wiring
2) Check/replace
wire toP CB
3) Replace
power supply
PCB
4) Replace control
PCB
5) Check microswitch when hot
water isrequested.

B
DOESTHE FAN
COME ON?
YES
C
NO
BOILER
SHUT D OWN ?
NO
PUMP
SAFETYDEVICE
ACTIVATED?
NO
INTERNAL
SAFETYDEVICE
FOR PCB
ACTIVATED?
NO
ISTHEREPOWER
TO THE FAN?
YES
YES
YES
YES
NO
1)Reset the boiler
1)Check/replacediffere ntial
pressureswitch for pump
2)Check/replace wiring
3)Check/replacePCB wire
4)Check/replace power
supply P CB
5)Check/replace control
PCB
1)
Check/replaceair
pressureswitch/wiring
2)Check whether reset
button isstuck
3)
Check/replace flame
dete cti onele ctrod e
1)
Check/replace wiring
2)
Check/replacePCB wire
3)Check/replacepower
supply PCB
4)
Check/replace control
PCB
5)
Check/replace air
pressureswitch
1)Replacefan

C
IS
THEAIR PRESSURE
SWITCH ACTIVATED?
YES
ARETHE
FUMES DISCHARGED
CORRECTLY?
YES
DOESTHE
BURN ERLIGH T ?
YES
SAFETY
SHUT D OWNOFTHE
BOILER ACTIVATED?
NO
NO
NO
NO
YES
1) Check flue discharge
2) Check venturi & small pipes
3) Check wire for air press.switch
4) Check/replace air press. switch
5) Check/replace PCB wire
6) Check/replace power PCB
7) Check/replace control PCB
1)Check/replaceigniterplugs
2)Check wiring
3)Check starter
4)Check small wire
5)Check power supply PCB
6)Checkcontrol P C B
1)Checksupplyofgasto gas
valve
2)Check power supply PCB
3)Checkcontrol P C B
4)Checkfunct i o na lityofthe
valve
1)Check whether flame
dete cti onele ctrodeis
hitbythefla me
2)Check theelectrode
3)Check thepowerPCB
4)Checkthecontrol PCB
D
NO
WASTHE
RESET SWITCH
PRESSED?
YES
Shutdown LEDoff
Res tartofthefan

D
THERE STILL A
IS
PROBLEM?
YES
NO
FUNCTIONS
NORMALLY
LISTOFMALF UNCT ION S
De live ryofhot wate rfordomes ti cuse :
De live ryofhot wate rfordomes ti cuse :
1
whenthetapisturnedon,theburnergoe sout.
whenthetapisturnedon,theburnergoe sout.
2
De live ryofhot wate rfordomes ti cuse :
De live ryofhot wate rfordomes ti cuse :
theradia tore sareheatedin summe rmode.
theradia tore sareheatedin summe rmode.
De live ryofhot wate rfordomes ti cuse :
De live ryofhot wate rfordomes ti cuse :
3
watertempe ra tureisnot satis f actory .
watertempe ra tureisnot satis f actory .
4
De live ryofhot wate rfordomes ti cuse :
De live ryofhot wate rfordomes ti cuse :
noisyopera tion.
noisyopera tion.
POSSIBLE CAUSES
- Airinthese c ondaryexchange r
- Airinthese c ondaryexchange r
- Hot water pressureswitch isdefective
- Hot water pressureswitch isdefective
- 3-way valve isdefective
- 3-way valve isdefective
- 3-way valve isdefective
- 3-way valve isdefective
- Checkhe a t i ngsensor s
- Checkhe a t i ngsensor s
- Checkgasset t i ngsandregula t ion
- Checkgasset t i ngsandregula t ion
- Checkwaterflowra t e
- Checkwaterflowra t e
- Check exchanger for domes tichot water
- Check exchanger for domes tichot water
- Primaryexchanger isdefective
- Primaryexchanger isdefective
- Low waterpressurein heatingsys tem
- Low waterpressurein heatingsys tem
- Checkgasset t i ngsandregula t ion
- Checkgasset t i ngsandregula t ion
5
Drop/increasein pre ss urein primarycircuit.
Drop/increasein pre ss urein primarycircuit.
6
Repeatedshutdowns.
Repeatedshutdowns.
7
Safe ty therm os ta tistrigge re drepe a te d ly.
Safe ty therm os ta tistrigge re drepe a te d ly.
8
Whenthecold watertapisturne doff,the
Whenthecold watertapisturne doff,the
boiler comeson.
boiler comeson.
9
Tempe rature of radiatorsnot s atisfactory.
Tempe rature of radiatorsnot s atisfactory.
- Checkfor leaksin heatingcircuit
- Checkfor leaksin heatingcircuit
- Defe ctivewater supplyinlet valve
- Defe ctivewater supplyinlet valve
- Secondary exchanger isdefective
- Secondary exchanger isdefective
- Expansion vessal is empty
- Expansion vessal is empty
- Detection electrodes are defective
- Detection electrodes are defective
- Checkgasset t i ngsandregula t ion
- Checkgasset t i ngsandregula t ion
- Checkelectrical circuit for f lamedetection
- Checkelectrical circuit for f lamedetection
- F a ulty(contacts)ntcheating sensors-
- F a ulty(contacts)ntcheating sensors-
- Defective (poorlycalibrated)safety thermostat
- Defective (poorlycalibrated)safety thermostat
- Pres e nceofair in theprimary watercircuit
- Pres e nceofair in theprimary watercircuit
- Dropin pre ss urein thewater mains,resulting
- Dropin pre ss urein thewater mains,resulting
in waterhammering
in waterhammering
- Checkntcheati ng s ensor
- Checkntcheati ng s ensor
- Check by-pass
- Check by-pass
- Checkgasset t i ngsandregula t ion
- Checkgasset t i ngsandregula t ion

25
B029
Signalling
Boiler Off
Auto diagnostic state
Spark ignition state
Boiler functioning normally
Lockout
Boiler thermostat satisfied
Room thermostat/clock no demand or
selector in summer setting
Malfunction
Faulty ventilation system
Air pressure switch stuck in N.O. position
Faulty reset switch
Faulty main circuit flow switch
Faulty flame detection
Faulty overheat ther mostat
Faulty exhaust fumes sensor
Faulty heating sensor (N.T.C.)
Faulty D.H.W.sensor (N.T.C.)
A
b
C
d
E
F
G
I
m
1
2
3
4
5
6
2.2
Fault Finding Using the
Total Check System
Pump fed
Main flow switch closed
Air pressure switch N.O.
Flame detected
Water at required temperature
Room thermostat/clock no demand or
selector in summer setting
Auto diagnostics faulty
Heating temperature control
D.H.W. temperature control
Heating circuit efficiency control
D.H.W.exchanger efficiency control

573294
573520
997206
573224
569236
573340
573528
573727
573172
571649
997208
953730
952981
952610
572989
572990
573343
573314
571651
571652
570717
564254
569387
571449
571646
573295
573825
571807
573521
997150
997151
571965
574279
574232
574233
573441
569390
569560
569561
572271
572277
572343
572372
572749
572835
571993
571444
997029
571443
571442
571447
571446
571547
571772
571771
571770
573138
569281
569282
Key
no.
G.C. part
no.
ARISTON
Part No.
Description
1
11
14
17
18
19
23
24
25
28
32
45
46
47
57AB
57CD
58
61
72AB
72CD
75
84
85
87
89AB
89CD
90
92
96
98AB
98CD
100
101
102
108
112
116
118
119
120A
120B
120C
120D
121AB
121CD
301
311
321
361
362
363
364
371
372
373
374
375
381
382
379816
164 225
164 338
164 229
378 814
E03 818
E02 071
379 079
164 230
164 282
379 981
164 261
379 979
379 980
E02 026
E02 078
164 311
Expansion vessel
Gasket 3/4"
Overheat thermostat
Main flow Switch
Temp probe (C.H.W.)
Microswitch for 3-way/main flow group
Gasket 1/2"
Manual vent cock
Safety valve 3 bar 1/2"
Pressure gauge
Time clock
P.C.B. EX C-MI/FFI
P.C.B. EI A-MFFI
P.C.B. cable
Fan
Fan
Fan inlet gasket
Venturi (exhaust manifold/header)
Air pressure switch
Air pressure switch
Fastening spring
Automatic air release valve
Gasket 1"
O-ring
Secondary exchanger (plate-type) exchanger 23kW
Secondary exchanger (plate-type) exchanger 27kW
O-ring (secondary exchanger)
20-18 O-ring
Gasket 3/8"
Pump
Pump
O-ring (13)
Gasket
Gas valve (SIT Sigma)
Spark generator
Detection electrode
Gasket 1/4"
Ignition electrode (R.H.)
Ignition electrode (L.H.)
Main burner
Main burner
Main burner
Main burner
Main exchanger
Main exchanger
Front panel runner kit
D.H.W. actuator kit
SIT Sigma gas valve operator coils
Heating by-pass kit
D.H.W. pressure switch kit
3-way spring kit
D.H.W. diaphram valve
Main flow switch diaphram
Main flow switch magnet
Main flow switch spring
Main flow switch top cap
Main flow switch reed system
Burner jet 1.25 full kit (Natural gas)
Burner jet 0.72 full kit (LPG)
1
1
1
1
1
1
1
1
1
1
1
1
1
1
1
1
1
1
1
1
1
1
1
1
1
1
1
1
1
1
1
1
1
1
1
1
1
A/23 MFFI - A/27 MFFI (SIT Sigma Gas Valve)

A/23 MFFI - A/27 MFFI (SIT Tandem Gas Valve)
Key
no.
1
11
14
17
18
19
23
24
25
28
31
44
46
47
57AB
57CD
58
61
72AB
72CD
75
84
85
87
89AB
89CD
90
92
96
98AB
98CD
101
103
106
114
118
120
121
122A
122B
122C
122D
123AB
123CD
311
321
322
323
361
362
363
364
371
372
373
374
375
381
382
G.C. part
no.
379816
164 225
164 338
164 229
378 814
E03 818
E02 071
379 079
164 230
164 282
379 976
379 981
164 261
379 979
379 980
E02 026
E02 078
378 978
378 815
164 303
164 311
Description
Expansion vessel
Gasket 3/4"
Overheat thermostat
Main flow Switch
Temp probe (C.H.W.)
Microswitch for 3-way/main flow group
Gasket 1/2"
Manual vent cock
Safety valve 3 bar 1/2"
Pressure gauge
Time clock
P.C.B. EX C-MI/FFI
P.C.B. EI A-MFFI
P.C.B. cable
Fan
Fan
Fan inlet gasket
Venturi (exhaust manifold/header)
Air pressure switch
Air pressure switch
Fastening spring
Automatic air release valve
Gasket 1"
O-ring
Secondary exchanger (plate-type) exchanger 23kW
Secondary exchanger (plate-type) exchanger 27kW
O-ring (secondary exchanger)
O-ring (20-18)
Gasket 3/8"
Pump
Pump
Gas valve (SIT Tandem)
Spark generator
O-ring (13)
Detection electrode
Gasket 1/4"
Ignition electrode (R.H.)
Ignition electrode (L.H.)
Main burner
Main burner
Main burner
Main burner
Main exchanger
Main exchanger
D.H.W. actuator kit
SIT Tandem gas valve operator coils
SIT Tandem modureg coil
Gas modulator cartridge
Heating by-pass kit
D.H.W. pressure switch kit
3-way spring kit
D.H.W. diaphram valve
Main flow switch diaphram
Main flow switch magnet
Main flow switch spring
Main flow switch top cap
Main flow switch reed system
Burner jet 1.25 full kit (Natural gas)
Burner jet 0.72 full kit (LPG)
ARISTON
Part No.
1
1
1
1
1
1
1
1
1
1
1
1
1
1
1
1
1
1
1
1
1
1
1
1
1
1
1
1
1
1
1
1
1
1
1
1
1
573294
573520
997206
573224
569236
573340
573528
573727
573172
571649
997207
953730
952981
952610
572989
572990
573343
573314
571651
571652
570717
564254
569387
571449
571646
573295
573825
571807
573521
997150
997151
570732
573023
571965
573441
569390
569560
569561
572271
572277
572343
572372
572749
572835
571444
570712
573740
573745
571443
571442
571447
571446
571547
571772
571771
571770
573138
569281
569282

573294
573520
997206
573224
569236
573340
573528
573727
573172
571649
997207
953730
952981
952610
572989
572990
573343
573314
571651
571652
570717
564254
569387
571449
571646
573295
573825
571807
573521
997150
997151
570732
573023
571965
573441
569390
569560
569561
572271
572277
572343
572372
572749
572835
571444
570712
573740
573745
571443
571442
571447
571446
571547
571772
571771
571770
573138
569281
569282
Key
no.
G.C. part
no.
ARISTON
Part No.
Description
1
11
14
17
18
19
23
24
25
28
31
44
46
47
57AB
57CD
58
61
72AB
72CD
75
84
85
87
89AB
89CD
90
92
96
98AB
98CD
101
106
114
118
120
121
122A
122B
122C
122D
123AB
123CD
311
321
322
323
361
362
363
364
371
372
373
374
375
381
382
379816
164 225
164 338
164 229
378 814
E03 818
E02 071
379 079
164 230
164 282
379 976
379 981
164 261
379 979
379 980
E02 026
E02 078
378 978
378 815
164 303
164 311
Expansion vessel
Gasket 3/4"
Overheat thermostat
Main flow Switch
Temp probe (C.H.W.)
Microswitch for 3-way/main flow group
Gasket 1/2"
Manual vent cock
Safety valve 3 bar 1/2"
Pressure gauge
Time clock
P.C.B. EX C-MI/FFI
P.C.B. EI A-MFFI
P.C.B. cable
Fan
Fan
Fan inlet gasket
Venturi (exhaust manifold/header)
Air pressure switch
Air pressure switch
Fastening spring
Automatic air release valve
Gasket 1"
O-ring
Secondary exchanger (plate-type) exchanger 23kW
Secondary exchanger (plate-type) exchanger 27kW
O-ring (secondary exchanger)
O-ring (20-18)
Gasket 3/8"
Pump
Pump
Gas valve (SIT Tandem)
Spark generator
O-ring (13)
Detection electrode
Gasket 1/4"
Ignition electrode (R.H.)
Ignition electrode (L.H.)
Main burner
Main burner
Main burner
Main burner
Main exchanger
Main exchanger
D.H.W. actuator kit
SIT Tandem gas valve operator coils
SIT Tandem modureg coil
Gas modulator cartridge
Heating by-pass kit
D.H.W. pressure switch kit
3-way spring kit
D.H.W. diaphram valve
Main flow switch diaphram
Main flow switch magnet
Main flow switch spring
Main flow switch top cap
Main flow switch reed system
Burner jet 1.25 full kit (Natural gas)
Burner jet 0.72 full kit (LPG)
1
1
1
1
1
1
1
1
1
1
1
1
1
1
1
1
1
1
1
1
1
1
1
1
1
1
1
1
1
1
1
1
1
1
1
1
1
103
A 23/27 MFFI (SIT Tandem Gas Valve)