
Maintenance
Make sure all personnel are standing clear of the unit
before proceeding. The system components will start
when the power is applied.
Fan Belt Adjustment - Belt Drive Units
WARNING
Rotating Components!
The following procedure involves working with rotating
components. Disconnect all electric power, including
remote disconnects before servicing. Follow proper
lockout/tagout procedures to ensure the power can not
be inadvertently energized. Failure to disconnect power
before servicing could result in rotating components
cutting and slashing technician which could result in
death or serious injury.
The fan belts must be inspected periodically to assure
proper unit operation.
Replacement is necessary if the belts appear frayed or
worn. Units with dual belts require a matched set of belts
to ensure equal belt length.
When removing or installing the new belts, do not stretch
them over the sheaves. Loosen the belts using the belt
tension adjustment bolts on the motor mounting base.
Once the new belts are installed, using a Browning or
Gates tension gauge (or equivalent) illustrated in
Figure 29, p. 37; adjust the belt tension as follows;
1. To determine the appropriate belt deflection;
a. Measure the center-to-center shaft distance (in
inches) between the fan and motor sheaves.
b. Divide the distance measured in Step 1a by 64; the
resulting value represents the amount of belt
deflection that corresponds to the proper belt
tension.
2. Set the large O-ring on the belt tension gauge at the
deflection value determined in Step 1b.
3. Set the small O-ring at zero on the force scale of the
gauge plunger.
4. Place the large end of the gauge at the center of the belt
span; then depress the gauge plunger until the large Oring is even with the top of the next belt or even with
a straightedge placed across the fan and motor
sheaves. Refer to Figure 29, p. 37.
5. Remove the belt tension gauge. The small O-ring now
indicates a number other than zero on the plunger’s
force scale. This number represents the force (in
pounds) required to give the needed deflection.
6. Compare the “force” scale reading (Step 5) with the
appropriate “force” value listed in Table 10, p. 37. If the
“force” reading is outside the range, readjust the belt
tension.
Note: Actual belt deflection “force” must not exceed the
maximum “force” value shown in Table 10, p. 37.
Table 10. Belt tension measurement and deflection
ranges
Deflection Force (Lbs.)
Belts
Cross
Section
A
B
Small
P.D
Range
3.0 - 3.6 3 4 1/2 3 7/8 5 1/2 3 1/4 4
3.8 - 4.8 3 1/2 5 4 1/2 6 1/4 3 3/4 4 3/4
5.0 - 7.0 4 5 1/2 5 6 7/8 4 1/4 5 1/4
3.4 - 4.2 4 5 1/2 5 3/4 8 4 1/2 5 1/2
4.4 - 5.6 5 1/8 7 1/8 6 1/2 9 1/8 5 3/4 7 1/4
5.8 - 8.8 6 3/8 8 3/4 7 3/8 10 1/8 7 8 3/4
Super
Gripbelts Gripnotch
Min. Max. Min. Max. Min. Max
Steel Cable
Gripbelts
7. Recheck the belt tension at least twice during the first
2 to 3 days of operation. Belt tension may decrease
until the new belts are “run in”.
Figure 29. Belt tension gauge
Monthly Maintenance
WARNING
Hazardous Voltage!
Disconnect all electric power, including remote
disconnects before servicing. Follow proper lockout/
tagout procedures to ensure the power can not be
inadvertently energized. Failure to disconnect power
before servicing could result in death or serious injury.
Before completing the following checks, turn the unit OFF
and lock the main power disconnect switch open. Failure
to disconnect power before servicing can cause severe
personal injury or death.
RT-SVX33G-EN 37
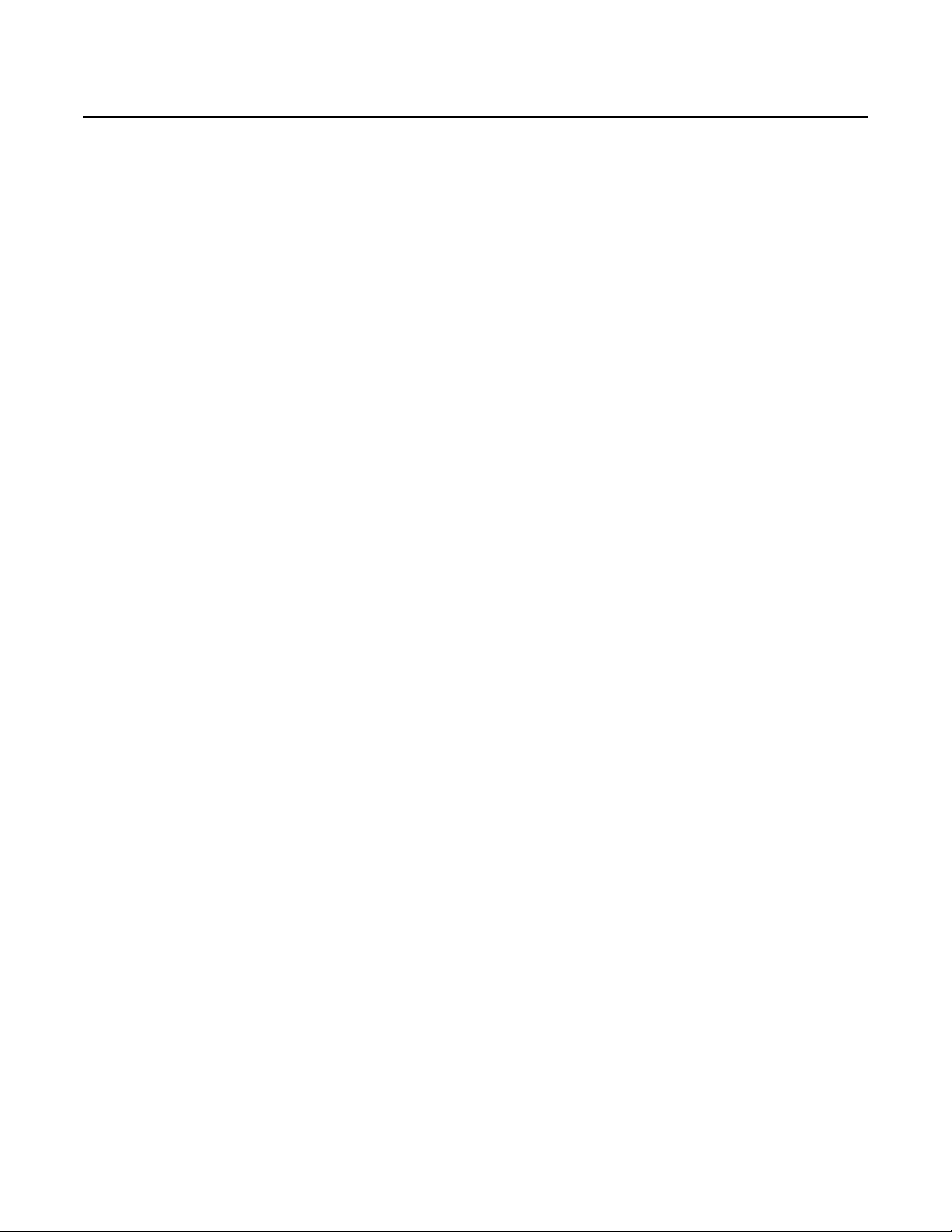
Maintenance
Filters
Inspect the return air filters. Clean or replace them if
necessary. Refer to the unit Service Facts for filter
information.
Condensate Overflow Switch
During maintenance, the switch float (black ring) must be
checked to ensure free movement up and down.
Return Air Smoke Detector Maintenance
Airflow through the unit is affected by the amount of dirt
and debris accumulated on the indoor coil and filters. To
insure that airflow through the unit is adequate for proper
sampling by the return air smoke detector, complete
adherence to the maintenance procedures, including
recommended intervals between filter changes, and coil
cleaning is required.
Periodic checks and maintenance procedures must be
performed on the smoke detector to insure that it will
function properly. For detailed instructions concerning
these checks and procedures, refer to the appropriate
section(s) of the smoke detector Installation and
Maintenance Instructions provided with the literature
package for this unit.
Cooling Season
• Check the unit’s drain pans and condensate piping to
ensure that there are no blockages.
• Inspect the evaporator and condenser coils for dirt,
bent fins, etc. If the coils appear dirty, clean them
according to the instructions described in “Coil
Cleaning” later in this section.
• Manually rotate the condenser fan(s) to ensure free
movement and check motor bearings for wear. Verify
that all of the fan mounting hardware is tight.
• Inspect the F/A-R/A damper hinges and pins to ensure
that all moving parts are securely mounted. Keep the
blades clean as necessary.
• Verify that all damper linkages move freely; lubricate
with white grease, if necessary.
• Check supply fan motor bearings; repair or replace the
motor as necessary.
• Check the fan shaft bearings for wear. Replace the
bearings as necessary.
• Check the supply fan belt. If the belt is frayed or worn,
replace it. Refer to the “Fan Belt Adjustment” section
for belt replacement and adjustments.
• Verify that all wire terminal connections are tight.
• Remove any corrosion present on the exterior surfaces
of the unit and repaint these areas.
• Generally inspect the unit for unusual conditions (e.g.,
loose access panels, leaking piping connections, etc.)
• Make sure that all retaining screws are reinstalled in
the unit access panels once these checks are complete.
• With the unit running, check and record the: ambient
temperature; compressor suction and discharge
pressures (each circuit); superheat (each circuit);
Record this data on an “operator’s maintenance log” like
the one shown in Table 11, p. 39. If the operating pressures
indicate a refrigerant shortage, measure the system
superheat. For guidelines, refer to the “Compressor StartUp” section.
Note: Do not release refrigerant to the atmosphere! If
adding or removing refrigerant is required, the
service technician must comply with all federal,
state and local laws.
Heating Season
• Inspect the unit’s air filters. If necessary, clean or
replace them.
• Check supply fan motor bearings; repair or replace the
motor as necessary.
• Inspect both the main unit control panel and heat
section control box for loose electrical components
and terminal connections, as well as damaged wire
insulation. Make any necessary repairs.
• Verify that the electric heat system operates properly.
Coil Cleaning
Regular coil maintenance, including annual cleaning,
enhances the unit’s operating efficiency by minimizing:
compressor head pressure and amperage draw;
evaporator water carryover; fan brake horsepower, due to
increase static pressure losses; airflow reduction.
At least once each year, or more often if the unit is located
in a “dirty” environment, clean the evaporator and
condenser coils using the instructions outlined below. Be
sure to follow these instructions as closely as possible to
avoid damaging the coils.
To clean refrigerant coils, use a soft brush and a sprayer
(either a garden pump-up type or a high-pressure sprayer).
A high-quality detergent is also required; suggested
brands include “SPREX A.C.”, “OAKITE 161”, “OAKITE 166”
and “COILOX”. If the detergent selected is strongly alkaline
(ph value exceeds 8.5), add an inhibitor.
1. Remove enough panels from the unit to gain access to
the coil. Remove the access panel from the roof located
next to the rear condenser fan.
2. Protect all electrical devices such as motors and
controllers from any over spray.
3. Straighten any bent coil fins with a fin comb.
4. Mix the detergent with water according to the
manufacturer’s instructions. If desired, heat the
solution to 150° F maximum to improve its cleansing
capability.
38 RT-SVX33G-EN
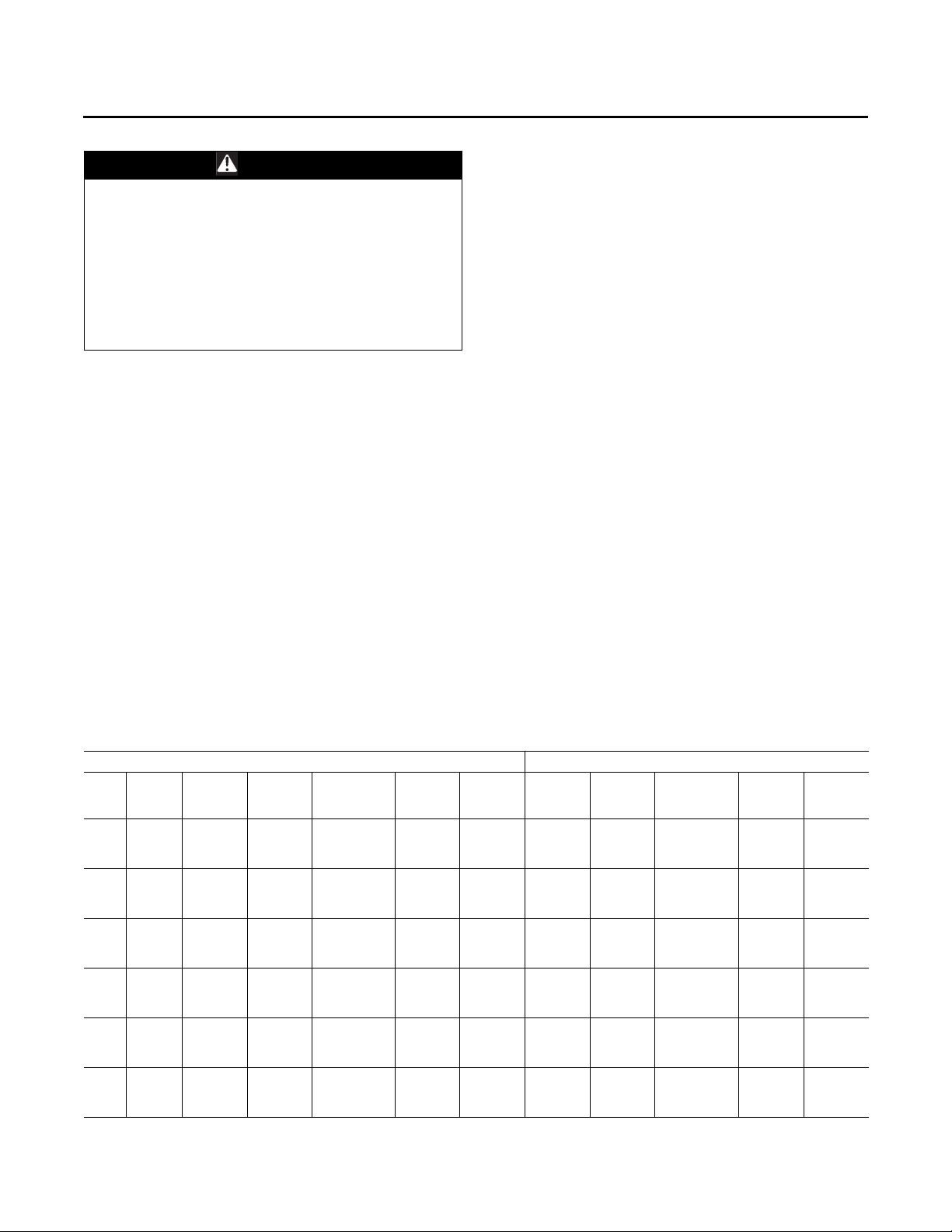
WARN IN G
Hazardous Pressures!
If a heat source is required to raise the tank pressure
during removal of refrigerant from cylinders, use only
warm water or heat blankets to raise the tank
temperature. Do not exceed a temperature of 150°F. Do
not, under any circumstances apply direct flame to any
portion of the cylinder. Failure to follow these safety
precautions could result in a sudden rise of pressure
possibly resulting in a violent explosion which could
result in death or serious injury.
Do not heat the detergent-and-water solution above 150°F.
Hot liquids sprayed on the exterior of the coil will raise the
coil’s internal pressure and may cause it to burst. Failure to
follow proper procedures can result in personal illness or
injury or severe equipment damage.
5. Pour the cleaning solution into the sprayer. If a highpressure sprayer is used:
a. do not allow sprayer pressure to exceed 600 psi.
b. the minimum nozzle spray angle is 15 degrees.
c. maintain a minimum clearance of 6" between the
sprayer nozzle and the coil.
d. spray the solution perpendicular (at 90 degrees) to
the coil face.
6. Spray the leaving-airflow side of the coil first; then
spray the opposite side of the coil. Allow the cleaning
solution to stand on the coil for five minutes.
7. Rinse both sides of the coil with cool, clean water.
Maintenance
8. Inspect both sides of the coil; if it still appears to be
dirty, repeat Steps 6 and 7.
9. Reinstall all of the components and panels removed in
Step 1 and any protective covers installed in step 2.
10. Restore the unit to it’s operational status and check
system operation.
Final Process
For future reference, you may find it helpful to record the
unit data requested below in the blanks provided.
(1) Complete Unit Model Number:
_____________________________________________________
__________________
(2) Unit Serial Number:
_____________________________________________________
__________________
(3) Wiring Diagram Numbers (from unit control panel):
— schematic(s)
_____________________________________________________
__________________
_____________________________________________________
__________________
— connection(s)
_____________________________________________________
__________________
_____________________________________________________
__________________
Table 11. Sample maintenance log
Refrigerant Circuit #1 Refrigerant Circuit #2
Current
Date
Ambient
temp F/C
RT-SVX33G-EN 39
Compr. Oil
Level
Suction
Pressure
Psig/kPa
Dischcharge
Pressure
Psig/kpa
Super heat
F/C
Sub cool
F/C
Compr. Oil
Level
Suction
Pressure
Psig/kPa
Dischcharge
Pressure
Psig/kpa
Super heat
F/C
Sub cool
F/C