
Intermittent duty
(ops/h)
140
120
100
80
60
40
Switching frequency
20
0
0 20 40 60 80 100(%)
ta = 0.5s
ta = 1s
ta = 1.5s
ta = 3s
ta = 3.5s
Closing time
Switching frequency
in relation to load factor.
ta: motor starting time
Technical data
for Overload relays
Technical
TA25DU – TA110DU
Switching frequency
To avoid nuisance tripping, TA and T thermal O/L relays have been designed to withstand roughly 15
switching operations per hour with an approximately equal distribution between working and rest cycles.
In these conditions, the motor starting time must not exceed 1 second and the starting current must
be lower than or equal to 6 times the motor In.
For intermittent operations, the diagram opposite specifies relay operating limits.
Example: Motor starting time: .................1 sec.
Tripping limits at ambient temperatures varying by + 20°C
Load factor: .............................40 %
Switching frequency: ............... 60 ops./h according to diagram
1.5
1.4
1.3
1.2
1.1
1.0
0.9
ultiple of the setting current
M
-20 -10 0 10 20 30 40 50
Ambient temperature
compensation limits
according to IEC 947-4-1
No tripping
Ambient temperature
Tripping
Ambient temperature compensation
Thermal O/L relays are compensated against ambient
temperature variations by a compensation bimetal which
is sensitive to the ambient temperature.
Thermal O/L relays are designed to operate between –5
°C and +40 °C in compliance with standard IEC947-4-1.
For a wider range of –25° C to +55 °C consult the graph
opposite.
Example: tripping at –25 °C. Tripping takes place before
1.5 times the setting current.
Resetting: TA25DU – TA110DU thermal O/L relays have
convertible manual/automatic resetting.
Delivery: in manual resetting mode.
data
OVERLOAD RELAYS: General info: 3.1 – 3.2 Selection: 3.3 – 3.4 Accessories: 3.5 – 3.6 Technical data: 3.7 – 3.10 Dimensions: 3.11 – 3.12
AC 1030 – 6/98
ABB Control Inc. 3.7
Overload relays
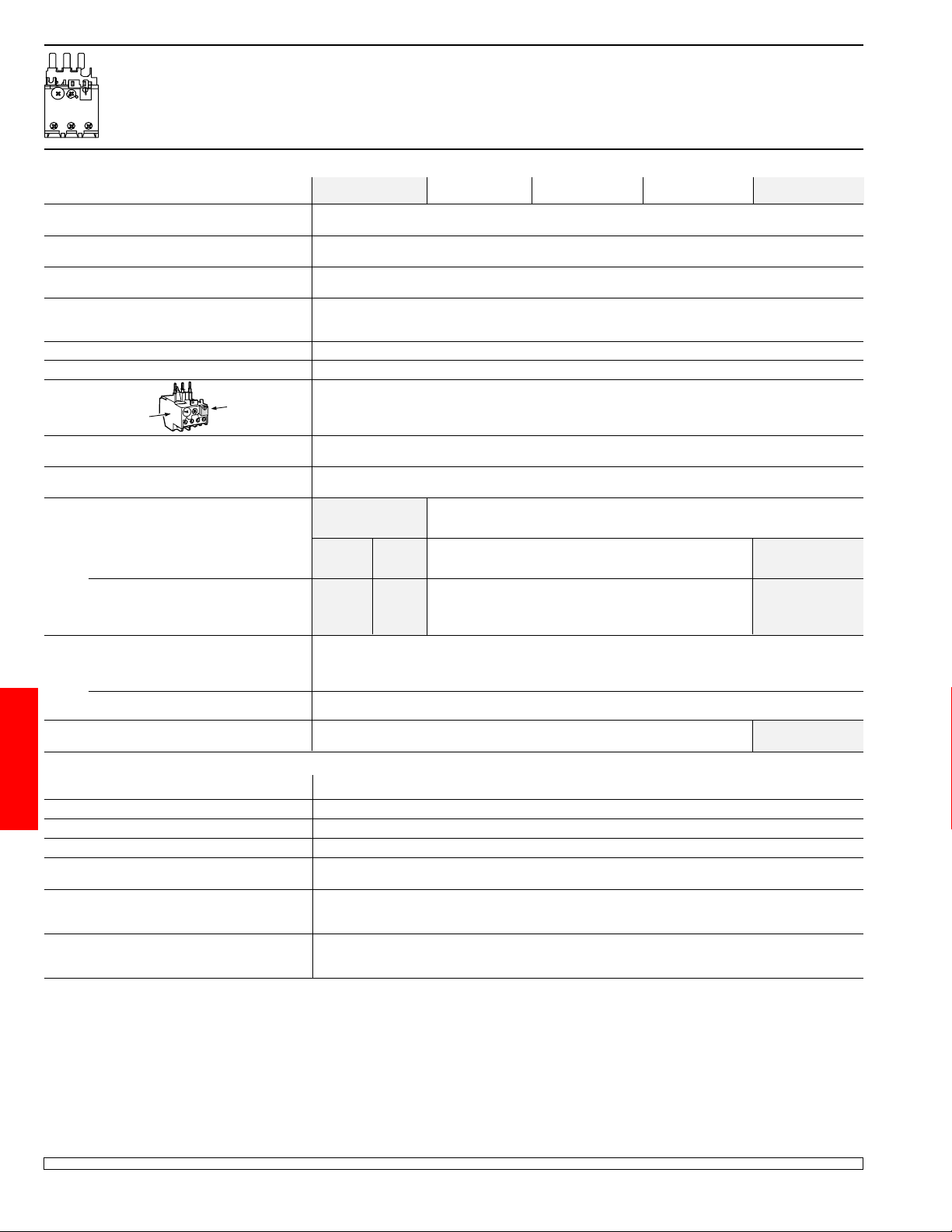
Technical data
Technical
data
General technical data
Types TA25DU TA42DU TA75DU TA80DU TA110DU
Standards: (main standards:
international, European and national)
Rated insulation voltage U
according to IEC947–4–1
Rated impulse withstand voltage U
according to IEC947–4–1
Permissible ambient temperature
Climatic withstand DIN 50017 Humidity in alternate climate KFW, 30 cycles
Mounting positions 1
Shock withstand shock duration ms 15
at nominal I
Critical direction
of shocks A1, A2 multiples of g 12
Resistance to vibrations
(±1 mm, 50 Hz) multiples of g 8
Mounting — on contactor Latching below the contactor, screw fixing on main terminals
Terminals and cross-sectional areas
for main conductors (motor side)
Terminals and cross-sectional area
for auxiliary conductors
Overload relays
Degree of protection according to IEC144, IEC529
DIN 40 050, NFC20-010 and VDE110/Part. 106
— for storage
— with compensation °C
e
— separate with DB - kit Using screws: 2 x M4 or 35 mm EN50022
• screw terminal to 18-25 A
— with cable clamp M4 —
— via tunnel connector — M5 M6 M6 M6 HC, M8
— flat type for lug or busbar — — — — — —
• conductor cross-sectional area AWG 16 – 8 16 – 8 8 – 1 8 – 1 8 – 1 6 – 1
— rigid solid or rigid stranded mm22 x 1.5 – 6 1 x 10 1 x 2.5 – 35 or 2 x 2.5 x 16 16 – 35
— flexible with cable end mm
— recommended busbars mm — — — — — 12 x 3
• screw terminal (screw size)
— with cable clamp M 3.5
• conductor cross sectional area
— rigid solid or rigid stranded AWG 2 x 18 – 24
i
A1
for Overload relays
TA25DU – TA110DU
V
imp
A2
kV
°C
TA25DU setting ranges: TA25DU setting ranges:
from 0.1-0.16A
2
2 x 1.5 – 4
UL, CSA, IEC947–4–1, VDE0660, NFC63 650, BS4941, EN60947-4-1
600V (UL); 690V (IEC)
6
–25 to +55 (maximum values: see page 3.7)
2 x 0.75 – 6
–40 to +70
24-32 A
1 x 2.5 – 25 or 2 x 2.5 x 10 16 – 35
2 3
Pole characteristics
Number of poles 3
Setting ranges see page 3.4
Tripping class according to IEC947–4 10A
Operating frequency Hz 0 – 400
Tripping frequency Up to 15 ops./h or 60 ops./h with 40 % load factor when neither
without untimely tripping the starting current of 6 x In nor the starting time 1s are exceeded.
Resistance per phase in mΩ
and heat dissipation in W see page 3.9
at the maximum current setting
Protection fuses
co-ordination with short circuit protection To be sized per NEC Article 430-152
devices
1 On a support at an angle of ±30° in relation to the vertical plane (standard position). Other positions possible except mounting on a horizontal plane (in this case the tripping mechanism
would be located above the bimetals).
2 All the terminals are protected against direct contact according to VDE0106/Part. 100. (without additional terminal shrouds).
3 All the terminals are protected against direct contact according to VDE0106/Part. 100. (with additional terminal shrouds).
OVERLOAD RELAYS: General info: 3.1 – 3.2 Selection: 3.3 – 3.4 Accessories: 3.5 – 3.6 Technical data: 3.7 – 3.10 Dimensions: 3.11 – 3.12
3.8 ABB Control Inc.
AC 1030 – 6/98

Technical data
for Overload relays
TA25DU – TA110DU
Auxiliary contacts Normally Closed N.C. Normally Open N.O.
Terminal marking 95 – 96 97 – 97
Rated insulation voltage U
Conventional thermal current (in free air) I
Rated operation current Ie' AC-15
Rated operational current I
Protection against short circuits
gG (gl) fuses (according to IEC269 A 10 6
S271/S 281 circuit breaker A k3 k1
Maximum potential difference VAC 500 500
between N.C. and N.O. auxiliary contacts VDC 440 440
up to 240V A 3.0 1.5
up to 440V A 1.9 0.95
up to 500V A 1.0 0.75
up to 250V A 0.12 0.04
i
DC-13
e
Resistance and Joule Loss per phase
TA25DU Thermal O/L relay
Setting range Resistance Joule loss
from – to current
A A mΩ W
0.1 – 0.16 85850.0 2.2
0.16 – 0.25 85150.0 2.2
0.25 – 0.4 13750.0 2.2
0.4 – 0.63 5370.0 2.2
0.63 – 1.0 2190.0 2.2
1.0 – 1.4 1120.0 2.2
1.3 – 1.8 670.0 2.2
1.7 – 2.4 383.0 2.2
2.2 – 3.1 229.0 2.2
2.8 – 4.0 137.0 2.2
3.5 – 5.0 87.5 2.2
4.5 – 6.5 61.0 2.2
6.0 – 8.5 30.4 2.2
7.5 – 11 18.2 2.2
10 – 14 11.2 2.2
13 – 19 6.3 2.3
18 – 25 4.7 2.9
24 – 32 3.2 3.3
per phase per phase at
VAC 500 500
A 10 6
th
TA42DU Thermal O/L relay
max. setting
Setting range Resistance Joule loss
A–A mΩ W
18 – 25 5.5 3.43
22 – 32 2.89 2.91
29 – 42 1.84 3.24
per phase per phase
TA75DU Thermal O/L relay
18 – 25 5.5 3.43
22 – 32 2.89 2.91
29 – 42 1.84 3.24
36 – 52 1.3 3.51
45 – 63 0.936 3.72
60 – 80 0.615 3.94
TA80DU Thermal O/L relay
29 – 42 1.84 3.24
36 – 52 1.3 3.51
45 – 63 0.936 3.72
60 – 80 0.615 3.94
TA110DU Thermal O/L relay
80 – 100 0.378 3.78
Technical
data
Overload relays
OVERLOAD RELAYS: General info: 3.1 – 3.2 Selection: 3.3 – 3.4 Accessories: 3.5 – 3.6 Technical data: 3.7 – 3.10 Dimensions: 3.11 – 3.12
AC 1030 – 6/98
ABB Control Inc. 3.9

T ripping curves
Technical
data
for Overload relays
TA25DU – TA110DU
TA25DU TA42DU TA75DU TA80DU TA110DU
TA-DU and T-DU thermal O/L relays are 3 pole with manual or automatic resetting mode selection. The reset button can also be used for
stopping.
Built in auxiliary contacts are physically separate and, consequently, can be used in different circuits (control circuit/indication circuit).
Each relay is temperature compensated and ensures phase failure protection.
Protective relays up to size TA75DU are protected against direct contact from the front face.
The connecting terminals are delivered in open position with (+,-) posidrive screws and screwdriver guidance. It is advisable to tighten unused
terminal screws.
Thermal O/L relay tripping curves
TA25DU, T25DU TA42DU, TA75DU and TA80DU TA110DU
(tripping class 10A) (tripping class 10A) (tripping class 10A)
120
100
80
60
40
20
10
8
Minutes
Tripping time
Seconds
4
2
1
40
20
10
2 Phases
868
6
4
3 Phases
2
from warm state
1
0.8 1 2 3 4 5 6 7 8 9 101.2 1.5
Tripping current
in multiples of the setting current
Overload relays
from cold state
2 Phases
3 Phases
Minutes
Tripping time
Seconds
120
100
80
60
40
20
10
8
4
2
1
40
20
2 Phases
10
3 Phases
868
6
4
2
1
from warm state
0.8 1 2 3 4 5 6 7 8 9 101.2 1.5
Tripping current
in multiples of the setting current
from cold state
2 Phases
3 Phases
Minutes
Tripping time
Seconds
120
100
80
60
40
20
10
8
4
2
1
40
20
3 Phases
10
868
6
4
2 Phases
2
from warm state
1
0.8 1 2 3 4 5 6 7 8 9 101.2 1.5
Tripping current
in multiples of the setting current
from cold state
2 Phases
3 Phases
OVERLOAD RELAYS: General info: 3.1 – 3.2 Selection: 3.3 – 3.4 Accessories: 3.5 – 3.6 Technical data: 3.7 – 3.10 Dimensions: 3.11 – 3.12
3.10 ABB Control Inc.
AC 1030 – 6/98