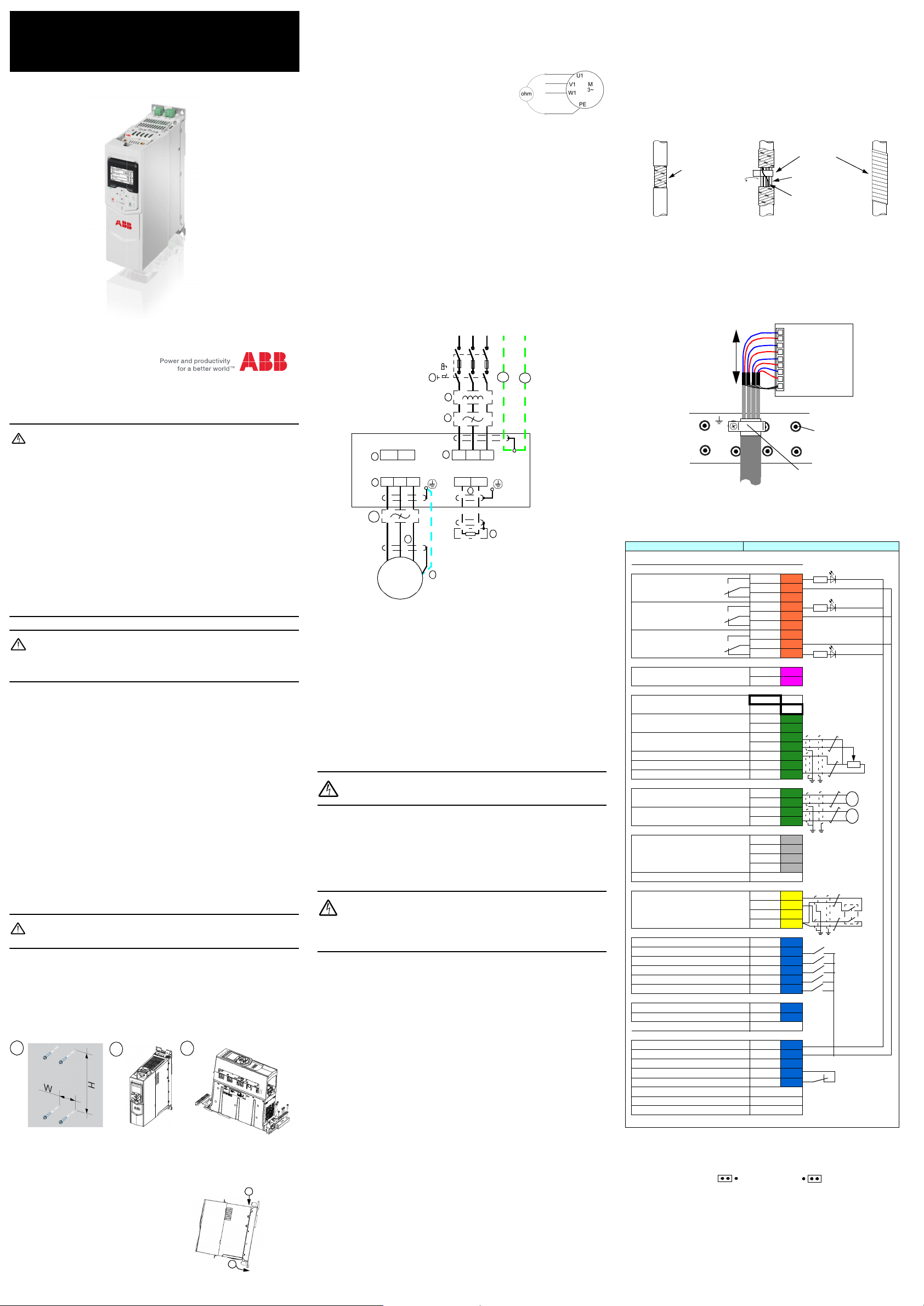
3. Measure the insulation resistance
ABB machinery drives
Quick installation and start-up guide
ACS880-M04 drive
1)
(PE) (PE)
PE
L1 L2 L3
UDC+ UDC–
R– R+
2)
U2 V2 W2
U1 V1 W1
3
~
Motor
V1
W1U1
ACS880-M04
PE
1
3
4
5
6
10
7
7
8
INPUT
OUTPUT
6
9
2a
2b
Cable shield
Shielded twisted pair
Grounding wire
Copper foil
Stripped cable Conductive surface of
the shield exposed
Stripped part covered with
copper foil
2
3
4
1
Keep as sh ort as possi ble
SHIELD*
Where grounding clamps are not available,
twist th e shield st rands into a bundle, crimp a
lug terminal onto it and fasten the lug to the
chas sis. Secu re the ca ble int o place w ith e g.
At th e othe r en d of t he cable,
leave the shield unconnected,
or connect it to ground via a
capacitor w ith a value of a few
*If no dedicated “shield”
connector is provided,
ground the inner cable
Relay outputs XRO1…XRO3
Ready
250 V AC / 30 V DC
2 A
NO
13
COM
12
NC 11
Running
250 V AC / 30 V DC
2 A
NO
23
COM 22
NC
21
Faulted(-1)
250 V AC / 30 V DC
2 A
NO 33
COM 32
NC 31
External power input XPOW
24 V DC, 2 A min. (without optional
modules)
GND 2
+24VI 1
Reference voltage and analog inputs J1, J2, XAI
AI1/AI2 current/voltage selection
AI1: U AI2: U
AI1: I AI2: I
By default not in use.
0(4)…20 mA, Rin= 100 ohm
1)
AI2- 7
AI2+
6
Speed reference
0(2)…10 V, R
in
>200kohm
2)
AI1- 5
AI1+ 4
Ground AGND 3
-10 V DC, RL 1…10 kohm -VREF 2
10 V DC, RL 1…10 kohm +VREF 1
Analog outputs XAO
Motor current 0…20 mA, RL < 500 ohm
AGND 4
AO2
3
Motor speed rpm 0…20 mA,
RL< 500 ohm
AGND 2
AO1 1
Drive-to-drive link
XD2D
Drive-to-drive link
3)
Shield 4
BGND 3
A 2
B 1
Drive-to-drive link termination
3)
J3
Safe torque off XSTO
Safe torque off. Both circuits must be
closed for the drive to start.
4)
IN2 4
IN1 3
SGND 2
OUT 1
Digital inputs XDI
By default not in use. DI6 6
Constant speed 1 select (1 = on) 5)DI5 5
Acceleration & deceleration select 6)DI4 4
Reset DI3 3
Forward (0) / Reverse (1) DI2 2
Stop (0) / Start (1) DI1 1
Digital input/outputs
XDIO
Output: Running DIO2 2
Output: Ready DIO1 1
Ground selection
7)
J6
Auxiliary voltage output, digital interlock
8)
XD24
Digital input/output ground DIOGND 5
+24 V DC 200 mA
9)
+24VD 4
Digital input ground DICOM 3
+24 V DC 200 mA
9)
+24VD 2
Run enable
8)
DIIL 1
Safety functions module connection X12
Control panel connection X13
Memory unit connection X205
Fault
Drive: Do not do voltage tolerance or insulation resistance tests on the drive, because
this can cause damage to the drive.
Input power cable: Before you connect the input power cable, me asure the
insulation of the input cable. Obey the local regulations.
Motor and motor cable:
1. Make sure the mo tor cable is connected to the
motor and disconnected from the dri ve output
terminals T1/U, T2/V and T3/W.
2. Use a voltage of 1000 V DC to measure the
insulation resistance between each phase
conductor and the protective earth conductor.
The insulation resistance of ABB mot or must be more than 100 Mohm (at 25 °C/
77 °F). For the insulation resistance of other motors, see the manufacturer’s
documentation.
Note: Moisture in the motor decreases the insulation resistance. If you think that
there is moisture in the motor, dry the motor and do the measurement again.
4. Select the cables
Input power cable: For the best EMC performance, use a symmetrical shielded
cable and two grounding conductors.
Motor cable: Use a symmetrical shielded cable.
Control cable: Use a double-shielded twisted-pair cable for analog signals. Use a
single-shielded cable for digital, relay and I/O signals. Use separate cables for analog
and relay signals.
Control panel cable: Use a CAT 5e unshielded or shielded twisted pair cable for
connecting the control panel to the drive. Use a USB type a (PC) - type B (control
panel) cable for connecting the Drive compose PC tool to the drive through the USB
port of the control panel.
5. Connect the power cables
Connection diagram
6. Connect the control cables
Connection procedure
1. In the cabinet, remove shrouding wherever necessary to allow access to the
cable entries and any trunking inside the cubicle.
2. Connect the control cables into the cubicle. If possible, arrange for a 360°
grounding of the cable shield at the cable entry.
If the outer surface of the shield is non-conductive, turn the shield inside out as
shown below and wrap a copper foil around the cable to keep the shielding
continuous. Do not cut the grounding wire (if present).
3. Connect the cables to the control unit of the drive (or other connection point)
using cable trunking wherever possible.
4. When connecting the cable to drive, remove the outer sheathing of the cable of
one of the clamps on the plate. Tighten the clamp on to the bare cable shield.
5. Cut the cables to suitable length.
6. Strip the cable ends and conductors. When conne cting to the drive I/O, also
remove the shield along with the outer sheathing, and use electrical tape or
shrink tubing to contain the strands. Otherwise, twist the outer shield strands into
a bundle, crimp a lug onto it and conne ct it to the nearest chassis groundi ng
point.
Safety instructions
Read the full safety instructions in the ACS880-M04 drive Hardware manual
(3AXD50000028613 [English]).
WARNING! Follow these safety instructions. If you ignore them, injury or death,
or damage to the equipment can occur.
• When you install the drive, make sure that dust does not go into the drive.
• When the drive or connected equipment is energized, do not do work on the drive,
motor cable, motor, control cables or control circuits.
• After you disconnect the drive, always wait for 5 minutes to let the intermediate
circuit capacitors discharge before you continue.
• Disconnect any external power sources from the control circuit before you do work
on the control cables.
• Measure that the installation is de-energi zed:
• Use a multimeter with an impedance of at least 1 Mohm.
• Make sure that the voltage between the drive input power terminals (L1, L2,
L3) and the grounding (PE) busbar is 0 V
• Make sure that the voltage between the drive DC terminals (UDC+ and UDC-)
and the grounding terminal (PE) is close to 0 V.
• If you have connected safety circuits to the drive (for example, emergency stop and
Safe torque off), validate th em at the start up.
• Do not work on a drive when a rotating permanent magnet motor is connected to it.
A rotating permanent magnet motor energizes the drive including its input power
terminals.
WARNING! The installation, start-up and operation of the drive requires detailed
installations. Refer to this quick guide and the hardware and firmware manuals
intended for use with this product. Retain the guides with the drive at all times. You
can download these manuals from the A BB website or order hard copies of drive
manuals with the delivery.
1. Examine the installation site
The drive has an ingress protection classification of IP20 for cabinet installation.
Make sure that in the installation area:
• There is sufficient cooling and prevent hot air recirculation.
• The ambient conditions obey the technical specifications. See Ambient conditions.
• The mounting surface is non-flammable and can hold the weight of the drive. Se e
Dimensions and weights.
• Materials near the drive are non-flammable.
• There is sufficient space above and below the d rive for cooling and to do
maintenance work. See Free space requirements.
For more details, see ACS880-M04 drive Hardware manual (3AXD50000028613
[English]).
2. Install the drive
You can install the drive with screws or to a DIN installation rail (with integrated lock).
Installation requirements:
• Make sure the space around the drive obeys the Free space requirements at the
top and bottom of the drive for cooling air.
• You can install the drive vertically alone or several drives side by side.
• You can install the drive horizontally alon e or several drives side by side (front or
back).
WARNING! Do not install the drive upside down or with the top of the drive
top) is always above the cooling air inlet (at the bottom).
To install the drive with screws
1. Mark the locations for the four holes an d fix the screws or bo lts to the marked
2. Install the drive onto t he mounting screws.
above the bottom of th e drive. Make sure that the cooling air exhaust (at the
locations. See the dimension drawings in ACS880-M04 drive Hardware manual
(3AXD50000028613 [English]).
Note: Lift the drive only by its chassis.
3. Tighten the mounting screws.
To install the drive to a DIN installation rail with integrated
lock – frames R1 and R2 only
1. Position the drive to the rail. To detach the
drive, press the release lever on top of the
drive.
2. Fasten the lower edge of the drive to the
mounting base through the two fastening
points.
1
Hand-operated input disconnecting device.
2a,
Two grounding conductors, PE cable (2a) and Cable with grounding conductor (2b).
2b
Use separate cables if shielded cables are used and the conductivity of the shield is less than 50%
of the conductivity of the phase conductor.
3
External mains choke (optional with frames R1 and R2).
With frame R3 and R4, the drive has an internal mains choke.
4
External EMC filter (optional with frames R1 and R2).
With frames R3 and R4, the drive has an internal filter.
5
Terminals for common DC configurations.
6
Pane for input and output power cables.
7
Cabinet entry with 360-degree grounding (recommended).
8
Separate grounding cable. Use this cable if the conductivity of the cable shield is less than 50% of
the conductivity of the phase conductor and there is no symmetrically constructed grounding
conductor in the cable.
9
Brake resistor (optional).
10
du/dt filt er (optional).
Connection procedure
WARNING! Follow the safety instructions in the ACS880-M04 Hardware
manual (3AXD50000028613 [English]). If you ignore them, injury or death, or
damage to the equipment can occur.
1. If you are using a drive of frame size R3 or R4, remove the plastic connector
covers on top and bottom of the drive. Each cover is fastened with screws.
2. On IT (ungrounded) systems and corner grounded TN systems, disconnect the
internal varistors and EMC filters (option +E200) by removing the screws
connected to the VAR, VAR1, VAR2 and EMC terminals.
In frames R1 and R2, the VAR terminal is located cl ose to the supply terminal.
In frames R3 and R4, the EMC, VAR1 and VAR2 terminals are located on the
front of the power unit.
WARNING! If a drive whose varistors/filters are not disconnected is installed
on an IT system (an ungrounded power system or a h igh resistance grounded
[over 30 ohms] po wer system), the system connects to the ground potential
through these varistors/filters of the drive.
If a drive whose varistors/filters are not connected is installed on a corner grounded
TN system, the d rive will be damaged.
3. Fasten the cable clamp plates to the top and bottom of the drive. The clamp
plates are ident ical.
4. Strip the power cables so that the shields are bare at the cable clamps.
5. Twist the ends of the cable shield wires into pigtails.
6. Strip the ends of the phase conductors.
7. Connect the ph ase conductors of supply cable to U1, V1 and W1 terminals of the
drive.
8. Connect the phase conductors of moto r cable to U2, V2 and W2 terminals.
9. Connect the resi stor cable conductors (if present) to the R+ and R- terminal s.
In frame sizes R3 and R4, attach the screw terminal lugs included with the
conductors. It is recommended to use crimp lugs instead of screw lugs.
10. Tighten the cable clamps onto the bare cable shields.
11. Crimp a cable lug onto each shield pigtail. Fasten the lugs to ground terminals.
Note: Try to work out a compromise betwe en the length of the pigtail and the
length of unshielded phase conductors as both should ideally be as short as
possib le.
12. Cover the visible bare shield and pigtail with an insulating tape.
13. If you are using a drive of frame size R3 or R4, cut suitable slots on the edges of
the connector covers to accommodate the supply and motor cables. Install the
covers again. Torque the terminals to 3 N.m [25 lbf.in].
14. Mechanically secure th e cables outside the u nit.
15. Ground the other end o f the supply cable shield or PE conductor(s) at the
distribution board.
If a mains choke and/or an EMC filter is installed, make sure the PE conductor is
continuous from the distribution bo ard to the drive.
7. Connect the conductors to appropriate te rminals.
8. Refit any shrouds removed earlier.
Default I/O connection diagram
Descriptions Term inal s
Note: The wire size accepted by all screw terminals (for both stranded and solid wire) is
0.5 … 2.5 mm
1) Current [0(4)…20 mA, R
2) Current [0(4)…20 mA, R
3) Settings: Termination enabled . Termination disabled
4) Se e Safe torque off function in AC S880 -M04 d rive HW man ual.
5) Constant speed 1 is defined by parameter 22.26.
6) 0 = Acc eleration/ decelerat ion ra mps defin ed by para meters 2 3.12/ 23.13 in use.
7) Jumper/switch J6. Determines whether DICOM is separated from DIOGND (ie. common reference
8) DIIL input used for connecting safety circuits. By default, the input is parameterized to stop the unit
9) Total load capacity of these outputs is 4.8 W (200 mA at 24 V) minus the power taken by DIO1 and
2
(24…12 AWG). The torque is 0.5 N·m (5 lbf·in).
jumper J2. Change of setting requires reboot of control unit
jumper J1. Change of setting requires reboot of control unit.
1 = A ccele ratio n/deceler ation ramp s defined by param eters 23.14/23. 15 in use.
for digi tal inp uts flo ats; in practice, se lects w hether the digital inputs are used in c urrent sink ing or
sourcing mode). See the Ground isolation diagram (ZCU) in ACS880-M04 drive Hardware manual
(3AXD50000028613 [English]).
when the input sign al is lost.
DIO2.
= 100 ohm] or voltage [0(2)…10 V, Rin> 200 kohm ] inp ut selecte d by
in
= 100 ohm] or voltage [0(2)…10 V, Rin> 200 kohm ] inp ut selecte d by
in
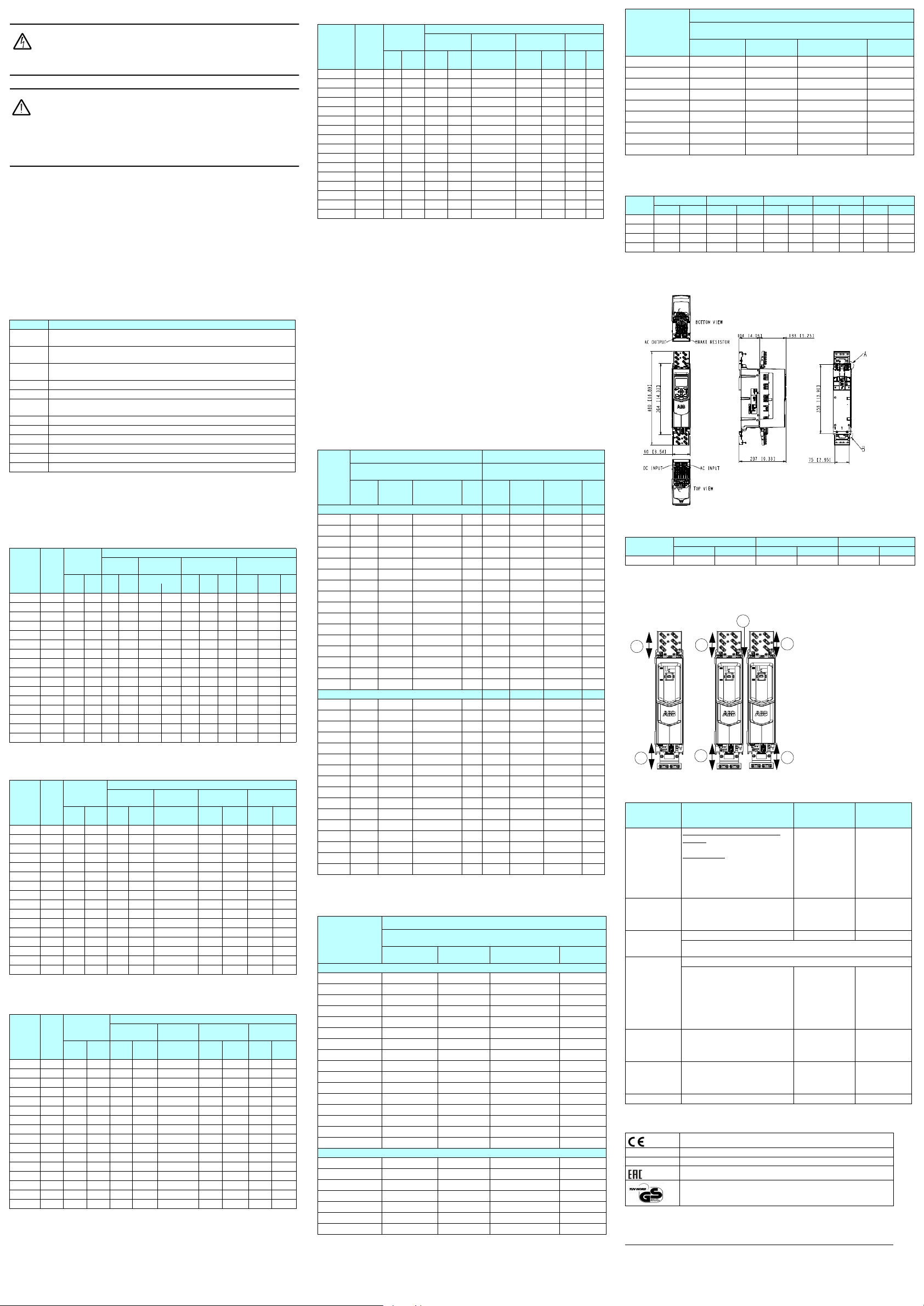
7. Start up the drive
H1
H2
W
D
H1 – Heigh t without cable cla mp plate
H2 – Height with cable clamp plate
W – Width
D – Depth (with c ontrol panel)
a
b
a
a
b
b
c
= 0
a – Above
b – Below
c – On the sides
WARNING! Follow all safety instructions of the drive. Only qua lified
electricians are allowed to start up the drive.
Never work on the drive, the brake chopper circuit, the motor cable or the
motor when power is applied to the drive. Always make sure by measuring that no
voltage is actually present.
WARNING! Make sure that the machinery into which the drive with brake
control function is integrated fulfills the p ersonnel safety regulations.
Note that the frequency converter (a Comp lete Drive Module or a Basic Drive
Module, as defined in IEC 61800-2), is not considered as a safety device mentioned
in the European Machinery Directive and related harmonized standards. Thus, the
personnel safety of the complete machinery must not be based on a specific
frequency converter feature (such as the brake control function), but it has to be
implemented as defined in the application specific regulations.
1. Check the mechanical and electrical installations of the d rive before start-up. See
the installation checklist in ACS880-M04 drive Hardware manual
(3AXD50000028613 [English]).
2. Make sure the moto r and drive equipment are ready to start.
3. Perform the start-up tasks as instructed by the cabinet installer of the drive
module.
4. Switch On the power.
5. Configure the drive parameters. See start-up instructions in ACS880-M04 drive
Firmware manual (3AXD50000030629 [English]).
6. Validate the Safe torque off function. See the STO function acceptance test
procedure in ACS880-M04 drive Hardware manual (3AXD50000028613
[English]).
Fault messages generated by the drive
Code Warning/f ault
A2A1/2281 Warning: Current calibration is done at the next start.
A2B1/2310 Overcurrent. The output current is more than the internal limit. This can result from
A2B3/2330 Earth leakage. A load unbalance that is typically caused by an earth fault in the
A2B4/2340 Short circuit. There is a short circuit in the motor or the motor cable.
3130 Input phase loss. The intermediate DC circuit voltage oscillates.
3181 Wiring or earth fault. The input power and motor cable connections are incorrect or
A3A1/3210 DC link overvoltage. There is an overvoltage in the intermediate DC circuit.
A3A2/3220 DC link undervoltage. There is an undervoltage in the intermediate DC circuit.
3381 Output phase loss. All three phases are not connected to the motor.
A5A0/5091 Safe torque off. The Safe torque off (STO) function is on.
FA81 Safe torque off 1 loss. The Safe torque off circuit 1 is broken.
FA82 Safe torque off 2 loss. The Safe torque off circuit 2 is broken.
For more details, see ACS880-M04 drive Firmware manual (3AXD50000030629 [English]).
Fault: Output phase current measurement fault.
an earth fault or phase loss.
motor or the motor cable.
there is a load unbalance due to earth fault in motor or motor cable.
Ratings
See symbol definitions at the end of the ratings tables.
Nominal ratings with 230 V AC supply
ACS880-
Frame
M04
-03A0-2 R1 2.1 3.5 3.0 4.4 0.37 0.5 2.8 0.37 0.5 2.5 0.37 0.5
-03A6-2 R1 2.9 5.2 3.6 5.3 0.55 0.75 3.4 0.55 0.75 3.0 0.37 0.5
-04A8-2 R1 3.7 6.3 4.8 7.0 0.75 1 4.5 0.75 1 4.0 0.55 0.75
-06A0-2 R1 5.2 8.9 6.0 8.8 1.1 1.5 5.5 1.1 1.5 5.0 0.75 1
-08A0-2 R1 6.3 10.7 8.0 10.5 1.5 2 7.6 1.5 2 6.0 1.1 1.5
-010A-2 R2 8.3 13 10.5 13.5 2.2 3 9.7 2.2 3 9.0 1.5 2
-014A-2 R2 11 17 14 16.5 3 3 13.0 3 3 11.0 2.2 3
-018A-2 R2 15 21 18 21 4 5 16.8 4 5 14.0 3 3
-025A-2 R3 19 – 25 33 5.5 7.5 23 5.5 7.5 19.0 4 5
-030A-2 R3 26 – 30 36 7.5 10 28 7.5 10 24 5.5 7.5
-035A-2 R3 30 – 35 44 7.5 10 32 7.5 10 29 7.5 10
-044A-2 R3 35 – 44 53 11 15 41 11 15 35 7.5 10
-050A-2 R3 42 – 50 66 11 15 46 11 15 44 11 15
-061A-2 R4 54 – 61 78 15 20 57 15 20 52 11 15
-078A-2 R4 64 – 78 100 18.5 25 74 18.5 25 69 15 20
-094A-2 R4 81 – 94 124 22 30 90 22 30 75 18.5 25
Input
size
ratings
I1N*I1NI2NI
A A A A kW hp A kW hp A kW hp
Nominal No-overload
use
MaxPN
Output ratings
Light-ove rload
use
ILdPLdPLdIHdPHdP
Heavy-duty use
3AXD10000434191
Hd
Nominal ratings with 400 V AC supply
ACS880-
Frame
M04
-03A0-5 R1 2.3 3.8 3.0 4.4 1.1 2.8 1.1 2.5 0.75
-03A6-5 R1 3.1 5.6 3.6 5.3 1.5 3.4 1.5 3.0 1.1
-04A8-5 R1 4.0 6.8 4.8 7.0 2.2 4.5 1.5 4.0 1.5
-06A0-5 R1 5.5 9.4 6.0 8.8 2.2 5.5 2.2 5.0 2.2
-08A0-5 R1 6.6 11.2 8.0 10.5 3.0 7.6 3.0 6.0 2.2
-010A-5 R2 8.7 13 10.5 13.5 4.0 9.7 4.0 9.0 4.0
-014A-5 R2 12 18 14 16.5 5.5 13.0 5.5 11.0 5.5
-018A-5 R2 16 23 18 21 7.5 16.8 7.5 14.0 7.5
-025A-5 R3 20 – 25 33 11.0 23 11 19.0 7.5
-030A-5 R3 26 – 30 36 15.0 28 15 24 11.0
-035 A-5 R3 30 – 35 44 18.5 32 15 2 9 15.0
-044A-5 R3 36 – 44 53 22 41 22 35 18.5
-050A-5 R3 42 – 50 66 22 46 22 44 22
-061A-5 R4 55 – 61 78 30 57 30 52 22
-078A-5 R4 65 – 78 104 37 74 37 66 37
-094A-5 R4 82 – 94 124 45 90 45 75 37
Input rating s Output ratings
size
I1N*I1NI2NI
A A A A kW A kW A kW
Nominal No-overload
use
MaxPN
Light-ove rload
use
I
LdPLdIHdPHd
Heavy-duty
use
3AXD10000434191
Nominal ratings with 460 V AC supply
ACS880-
Frame
M04
-03A0-5 R1 2.3 3.8 3.0 4.4 1.5 2.8 1.0 2.5 1.0
-03A6-5 R1 3.1 5.6 3.6 5.3 2.0 3.4 2.0 3.0 1.5
-04A8-5 R1 4.0 6.8 4.8 7.0 3.0 4.5 2.0 4.0 2.0
-06A0-5 R1 5.5 9.4 6.0 8.8 3.0 5.5 3.0 5.0 3.0
-08A0-5 R1 6.6 11.2 8.0 10.5 5.0 7.6 5.0 6.0 3.0
-010A-5 R2 8.7 13 10.5 13.5 5.0 9.7 5.0 9.0 5.0
-014A-5 R2 12 18 14 16.5 7.5 13.0 7.5 11.0 7.5
-018A-5R216231821 10 16.810 14.010
-025A-5 R3 20 – 25 33 15 23 15 19.0 10
-030A-5 R3 26 – 30 36 20 28 20 24 15
-035A-5 R3 30 – 35 44 25 32 20 29 20
-044A-5 R3 36 – 44 53 30 41 30 35 25
-050A-5 R3 42 – 50 66 30 46 30 44 30
-061A-5 R4 55 – 61 78 40 57 40 52 40
-078A-5R465– 7810450 7450 6650
-094A-5R482– 9412460 9060 7550
Input ratings Output rating s
size
I1N*I1NI2NI
A A A A hp A hp A hp
Nominal No-overload
use
MaxPN
Light-overload
use
ILdPLdI
Heavy-duty
use
HdPHd
3AXD 100004341 91
Nominal ratings with 500 V AC supply
ACS880M04
-03A0-5 R1 2.3 3.8 3.0 4.4 1.5 2.8 1.1 2.5 1.1
-03A6-5 R1 3.1 5.6 3.6 5.3 1.5 3.4 1.5 3.0 1.5
-04A8-5 R1 4.0 6.8 4.8 7.0 2.2 4.5 2.2 4.0 2.2
-06A0-5 R1 5.5 9.4 6.0 8.8 3.0 5.5 3.0 5.0 2.2
-08A0-5 R1 6.6 11.2 8.0 10.5 4.0 7.6 4.0 6.0 3.0
-010A-5 R2 8.7 13 10.5 13.5 5.5 9.7 5.5 9.0 4.0
-014A-5 R2 12 18 14 16.5 7.5 13.0 7.5 11.0 5.5
-018A-5 R2 16 23 18 21 11.0 16.8 7.5 14.0 7.5
-025A-5 R3 20 – 25 33 15.0 23 11.0 19.0 11.0
-030A-5 R3 26 – 30 36 18.5 28 15.0 24 15.0
-035A-5 R3 30 – 35 44 22 32 18.5 29 18.5
-044A-5 R3 36 – 44 53 30 41 22 35 22
-050A-5 R3 42 – 50 66 30 46 30 44 30
-061A-5 R4 55 – 61 78 37 57 37 52 30
-078A-5 R4 65 – 78 104 45 74 45 66 45
-094A-5 R4 82 – 94 124 55 90 55 75 45
Frame
Input
size
ratings
I1N*I1NI2NI
A A A A kW A kW A kW
Output ratings
Nominal No-overload
use
MaxPN
Light-overl oad
use
I
Ld
Heavy-duty
use
PLdIHdP
3AXD10000434191
Hd
Definitions
I1NNominal input current (rms) at 40 °C (104 °F).
*Without mains choke.
Nominal input current (rms) at 40 °C (104 °F), without mains choke.
*I
1N
Nominal output current.
I
2N
I
Maximum output current. Available for at least 10 seconds at start, otherwise as long as allowed by
Max
drive temperature.
Typical motor power for no-overload use.
P
N
I
Continuous rms output current. 10% overload is allowed for 1 minute every 5 minutes.
Ld
P
Typical motor power for light-overload use.
Ld
Continuous rms output current. 50% overload is allowed for 1 minute every 5 minutes.
I
Hd
P
Typical motor power for heavy-duty use.
Hd
Note:
• To achieve the rated motor power given in the table, the rated current of the drive must be higher
than or equal to the rated motor current.
• The DriveSize dimensioning tool available from ABB is recommended for selecting the drive,
motor and gear combination.
• The maximum allowed motor shaft power is limited to 1.5 · P
value is the greatest). If the limit is exceeded, motor torque and current are automatically
restricted. The function protects the input bridge of the drive against overload.
, 1.1 · PN or P
Hd
cont.max
(whichever
Fuses
gG and gR fuses
ACS880M04
Voltage rating: 500 V
Manufacturer: ABB
Input
current
(A)
1-phase UN = 230 V
03A0-2 6 110 OFAF000H6 000 20 70 170M2693 00
03A6-2 6 110 OFAF000H6 000 20 70 170M2693 00
04A8-2 10 360 OFAF000H10 000 20 70 170M2693 00
06A0-2 10 360 OFAF000H10 000 20 70 170M2693 00
08A0-2 16 750 OFAF000H16 000 20 70 170M2693 00
010A-2 16 750 OFAF000H16 000 20 70 170M2693 00
014A-2 20 1500 OFAF000H20 000 25 125 170M2694 00
018A-2 25 2550 OFAF000H25 000 32 275 170M2695 00
025A-2 25 2550 OFAF000H25 000 32 275 170M2695 00
030A-2 32 4500 OFAF000H35 000 32 275 170M2695 00
035A-2 40 7800 OFAF000H40 000 50 1000 170M2697 00
044A-2 50 16000 OFAF000H50 000 50 1000 170M2697 00
050A-2 50 16000 OFAF000H50 000 63 1800 170M2698 00
061A-2 63 20000 OFAF000H63 000 80 3600 170M2699 00
078A-2 80 37000 OFAF000H80 000 100 6650 170M2700 00
094A-2 100 65000 OFAF000H100 000 125 12000 170M2701 00
3-phase UN = 400 V
03A0-5 6 110 OFAF000H6 000 25 125 170M2694 00
03A6-5 6 110 OFAF000H6 000 25 125 170M2694 00
04A8-5 10 360 OFAF000H10 000 25 125 170M2694 00
06A0-5 10 360 OFAF000H10 000 25 125 170M2694 00
08A0-5 16 750 OFAF000H16 000 25 125 170M2694 00
010A-5 16 750 OFAF000H16 000 25 125 170M2694 00
014A-5 20 1500 OFAF000H20 000 40 490 170M2696 00
018A-5 25 2550 OFAF000H25 000 40 490 170M2696 00
025A-5 25 2550 OFAF000H25 000 40 490 170M2696 00
030A-5 32 4500 OFAF000H35 000 40 490 170M2696 00
035A-5 40 7800 OFAF000H40 000 63 1800 170M2698 00
044A-5 50 16000 OFAF000H50 000 63 1800 170M2698 00
050A-5 50 16000 OFAF000H50 000 63 1800 170M2698 00
061A-5 63 20000 OFAF000H63 000 80 3600 170M2699 00
078A-5 80 37000 OFAF000H80 000 100 6650 170M2700 00
094A-5 100 65000 OFAF000H100 000 125 12000 170M2701 00
gG fuses gR fuses
Voltag e rating: 690 V
A2s
(@500 V)
ABB type Fuse
Manufacturer: Bussmann
Input
size
current
DIN
(A)
A2s
(@600 V)
ABB type F use
3AXD10000299801.xls
size
DIN
aR fuses
Typ e
ACS880-M04
1-phase UN = 230 V
03A0-2 25 130 170M1561 000
03A6-2 25 130 170M1561 000
04A8-2 25 130 170M1561 000
06A0-2 25 130 170M1561 000
08A0-2 25 130 170M1561 000
010A-2 25 130 170M1561 000
014A-2 40 270 170M1563 000
018A-2 40 270 170M1563 000
025A-2 40 270 170M1563 000
030A-2 40 270 170M1563 000
035A-2 63 1450 170M1565 000
044A-2 63 1450 170M1565 000
050A-2 80 2550 170M1566 000
061A-2 100 4650 170M1567 000
078A-2 125 8500 170M1568 000
094A-2 160 16000 170M1569 000
3-phase UN = 400 V
03A0-5 25 130 170M1561 000
03A6-5 25 130 170M1561 000
04A8-5 25 130 170M1561 000
06A0-5 25 130 170M1561 000
08A0-5 25 130 170M1561 000
010A-5 25 130 170M1561 000
014A-5 40 270 170M1563 000
Voltag e rating: 690 V
Manufacturer: bussmann
Input current
(A)
A2s
(@500 V)
aR fuses
ABB type Fuse size
DIN
Typ e
ACS880-M04
018A-5 40 270 170M1563 000
025A-5 40 270 170M1563 000
030A-5 40 270 170M1563 000
035A-5 63 1450 170M1565 000
044A-5 63 1450 170M1565 000
050A-5 80 2550 170M1566 000
061A-5 100 4650 170M1567 000
078A-5 125 8500 170M1568 000
094A-5 160 16000 170M1569 000
Voltage rating: 690 V
Manufacturer: bussmann
Input current
(A)
A2s
(@500 V)
aR fuses
ABB type Fuse size
DIN
3AXD1 000029980 1.xls
Dimensions and weights
Frame
size
R1 364 14.33 480 18.89 90 3.54 237 9.33 3.2 7.1
R2 380 14.97 480 18.89 100 3.94 315 12.40 5.4 11.9
R3 467 18.37 558 21.96 168 6.60 316 12.44 15.6 34.4
R4 467 18.37 644 25.34 223 8.76 316 12.44 21.3 47.0
See the dimensions of frame R1 below. For other frame dimensions, see ACS880-M04 drive
Hardware manual (3AXD50000028613 [English]).
H1 H2 W D Weight
mm in mm in mm in mm in kg lbs
Dimension drawing – frame R1
Free space requirements
Frame
size
R1...R4 200 7.9 300 12 0 0
See below an example of vertical mounting. For other mounting types, see ACS880-M04 drive Hardware
manual (3AXD50000028613 [English])
a b c
mm in mm in mm in
3AXD10000299801.xls
Drive vertical mounting: alone or side by side
Ambient conditions
Operation
installed for stationary use
Installation site
altitude
Air temperature -10 to +55°C (14 to 131°F). No frost
Relative
humidity
Contamination
levels
(IEC 60721-3-3,
IEC 60721-3-2,
IEC 60721-3-1)
Sinusoidal
vibration
(IEC 60721-3-3)
Shock
(IEC 60068-2-27,
ISTA 1A)
Free fall Not allowed 76 cm (30”) 76 cm (30”)
Non-corner grounded TN and TT
systems: 0 to 4000 m (13123 ft)
above sea level.
Other systems: 0 to 2000 m (6561 ft)
above sea level.
Above 1000 m (3281 ft), see se ction
Altitude derating in ACS880-M04 drive
Hardware manual (3AXD50000028613
[English]).
allowed. see section Derating in
ACS880-M04 drive Hardware manual
(3AXD50000028613 [English]).
0 to 95% Max. 95% Max. 95%
No condensation allowed. Maximum allowed relative humidity is 60% in the
presence of corrosive gases.
No conductive d ust al lowed.
According to IEC 60721-3-3:
Chemical gases: Class 3C2
Solid particles: Class 3S2
The drive must be installed in clean
air according to enclosure
classification. Cooling air must be
clean, free from corrosive materials
and electrically conductive dust.
Tested according to IEC 60721-3-3,
mechanical conditions: Class 3M4
2…9 Hz: 3.0 mm (0.12”)
9…200 Hz : 10 m /s2 (33 ft/s2)
– According to ISTA
Compliance markings
CE marking
UL UL marking
RCM RCM marking
EAC marking
TüV Nord certification
Related manuals
Drive manuals and guides Code (English)
ACS880-M04 drive hardware manual 3AXD50000028613
ACS880-M04 drive firmware manual 3AXD50000030629
Storag e
in the protective
package
--
-40...+70 °C
(-40...158 °F)
According to IEC
60721-3-1:
Chemic al case s:
Class 1C2
Solid particles:
Class 1S2
––
1A.
Max. 100 m/s2
(330 ft/s2), 11 ms
Transportation
in the protective
package
-40...+70 °C
(-40...158 °F)
According to IEC
60721-3-2:
Chemical cases:
Class 2C2
Solid partic les:
Class 2S2
According to ISTA
1A.
Max. 100 m/s2
(330 ft/s2), 11 ms
3AXD50000032345 Rev A EN 2016-04-11