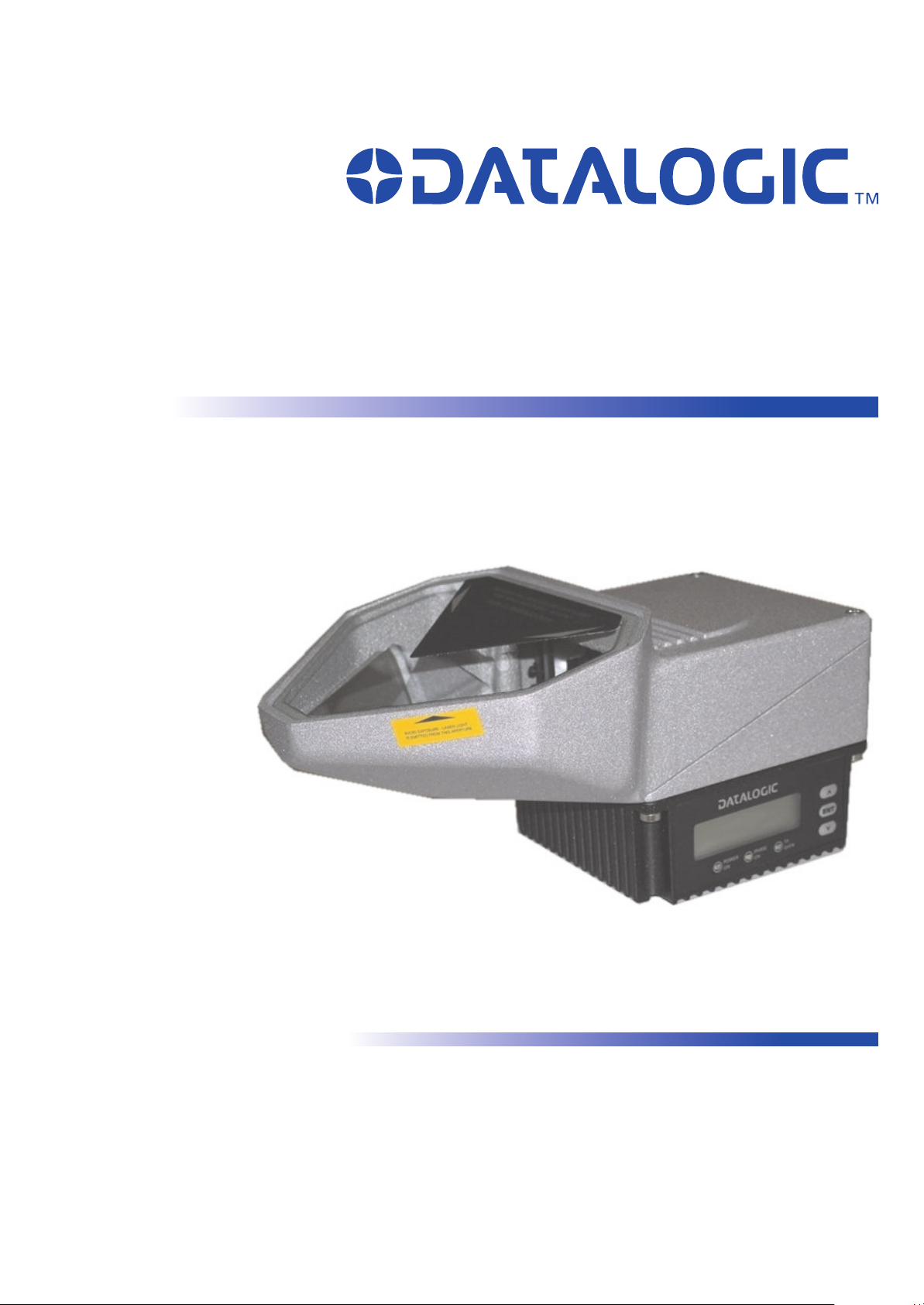
DX6400
Reference Manual
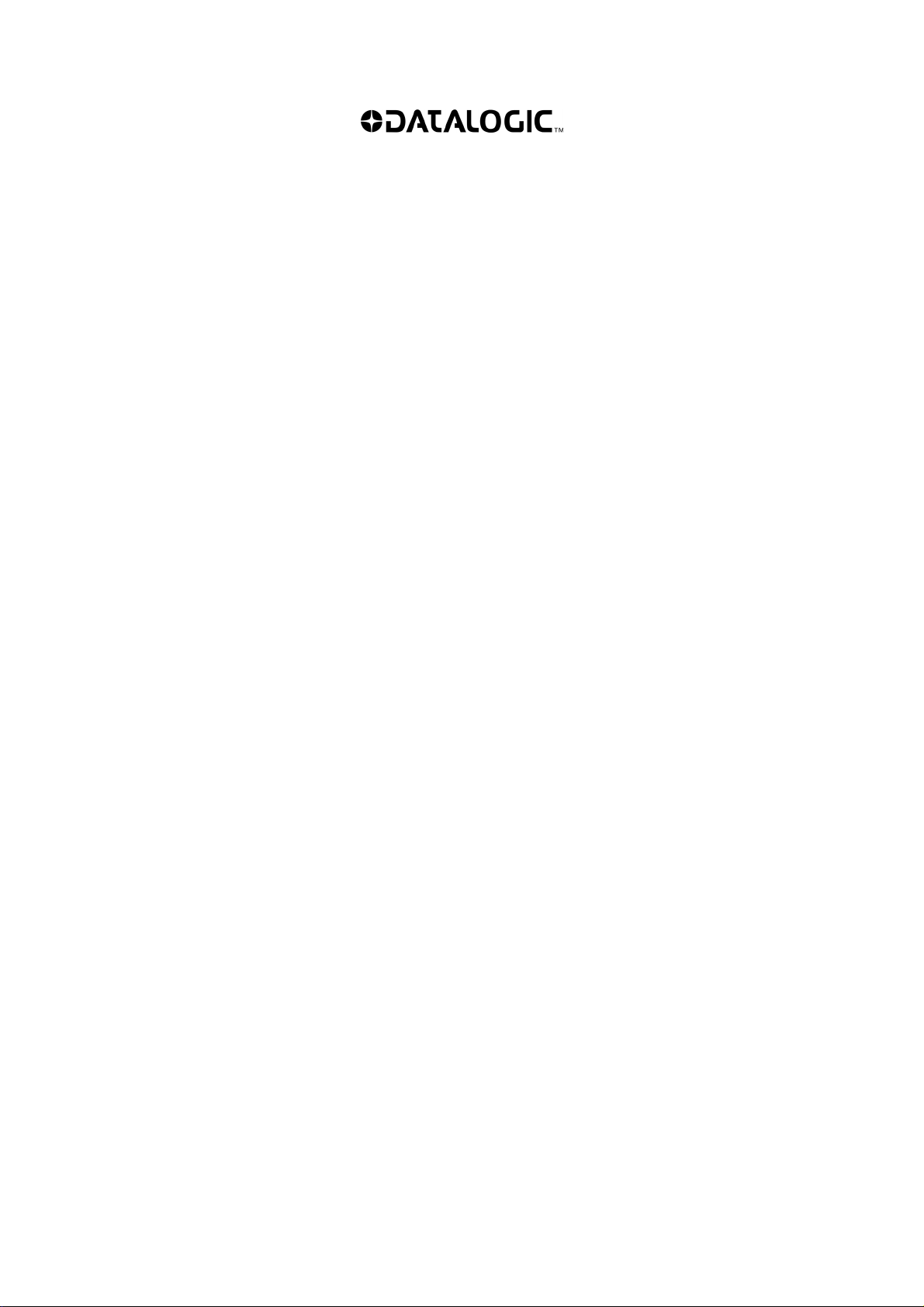
Datalogic Automation S.r.l.
Via S. Vitalino 13
40012 - Lippo di Calderara di Reno
Bologna - Italy
DX6400 Reference Manual
Ed.: 10/2007
ALL RIGHTS RESERVED
Datalogic reserves the right to make modifications or improvements without prior notification.
Datalogic shall not be liable for technical or editorial errors or omissions contained herein, nor for
incidental or consequential damages resulting from the use of this material.
Product names mentioned herein are for identification purposes only and may be trademarks and or
registered trademarks of their respective companies.
© Datalogic Automation S.r.l. 2003 - 2007
02/10/07
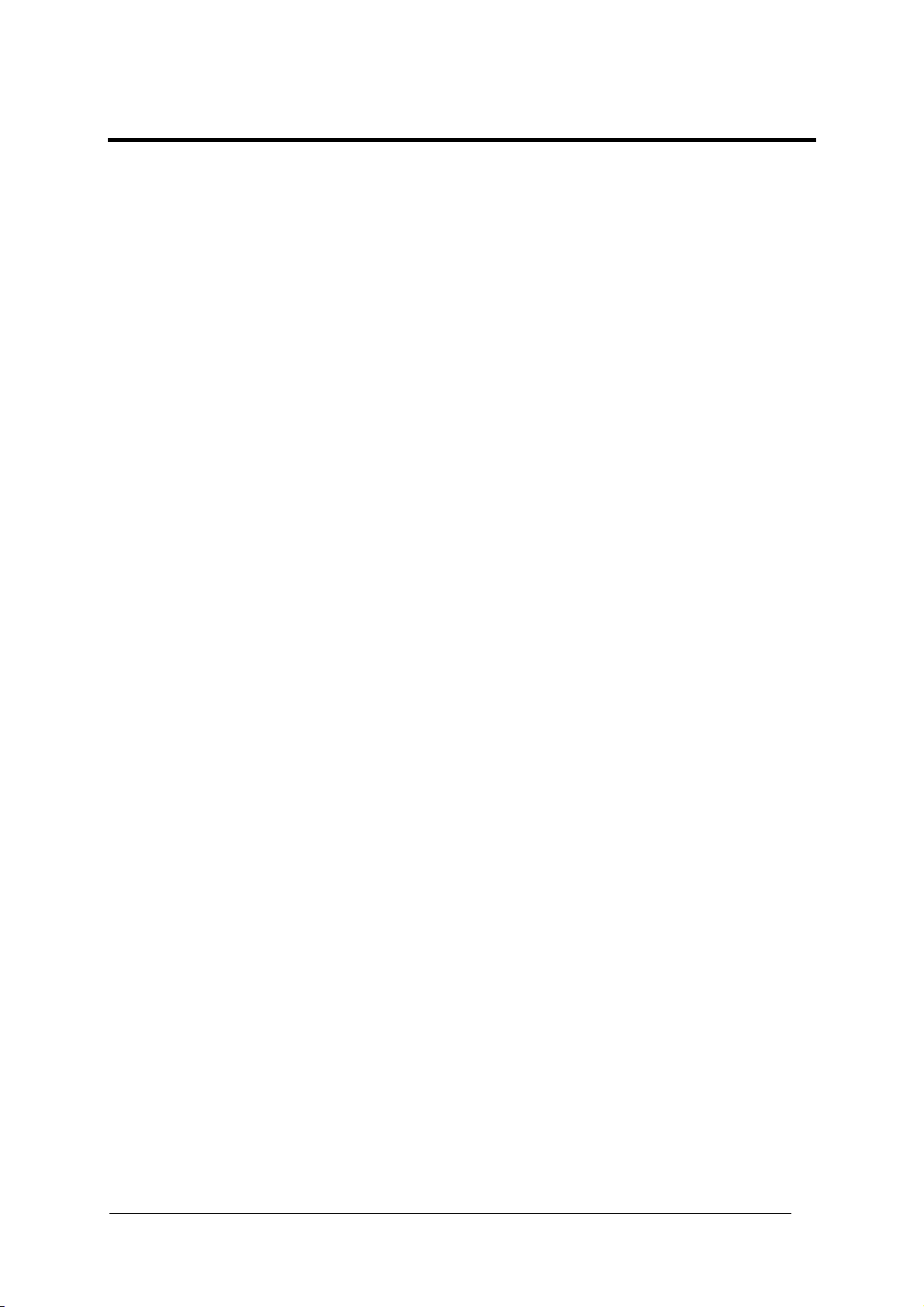
CONTENTS
REFERENCES .............................................................................................................v
Reference Documentation............................................................................................ v
Services and Support ...................................................................................................v
Patents.......................................................................................................................... v
COMPLIANCE.............................................................................................................vi
Electrical Safety........................................................................................................... vi
Laser Safety................................................................................................................. vi
Power Supply...............................................................................................................vii
CE Compliance...........................................................................................................viii
WEEE Compliance .....................................................................................................viii
GENERAL VIEW..........................................................................................................x
GUIDE TO INSTALLATION ....................................................................................... xii
Point-to-Point Installation.............................................................................................xii
Master/Slave Lonworks Installation ............................................................................xiii
1 INTRODUCTION ..........................................................................................................1
1.1 Product Description ......................................................................................................1
1.2 Applications ..................................................................................................................2
1.3 Model Description.........................................................................................................3
1.4 Indicators ......................................................................................................................3
1.5 Accessories ..................................................................................................................4
2 INSTALLATION ...........................................................................................................5
2.1 Package Contents ........................................................................................................5
2.2 Mechanical Mounting....................................................................................................6
2.2.1 Mounting the Scanner...................................................................................................6
2.2.2 Mounting the Scanner with Accessories.......................................................................8
2.3 Electrical Connections ..................................................................................................9
2.3.1 Main/Aux. Serial Interface and I/O Connector ............................................................11
Main Interface.............................................................................................................12
Auxiliary Interface .......................................................................................................14
Inputs..........................................................................................................................15
Outputs .......................................................................................................................17
2.3.2 Lonworks Input/Output Connector..............................................................................20
Network Termination...................................................................................................21
Lonworks Interface .....................................................................................................21
2.3.3 Ethernet Connector.....................................................................................................23
Ethernet Interface .......................................................................................................24
2.3.4 Power Supply..............................................................................................................25
2.4 User Interface .............................................................................................................26
2.5 Typical Layouts...........................................................................................................27
2.5.1 Point-to-Point..............................................................................................................27
2.5.2 Pass Through .............................................................................................................29
2.5.3 RS232 Master/Slave...................................................................................................30
2.5.4 Multiplexer ..................................................................................................................32
2.5.5 Local Lonworks Network.............................................................................................33
Small Synchronized Network......................................................................................34
Large Synchronized Network...................................................................................... 36
iii
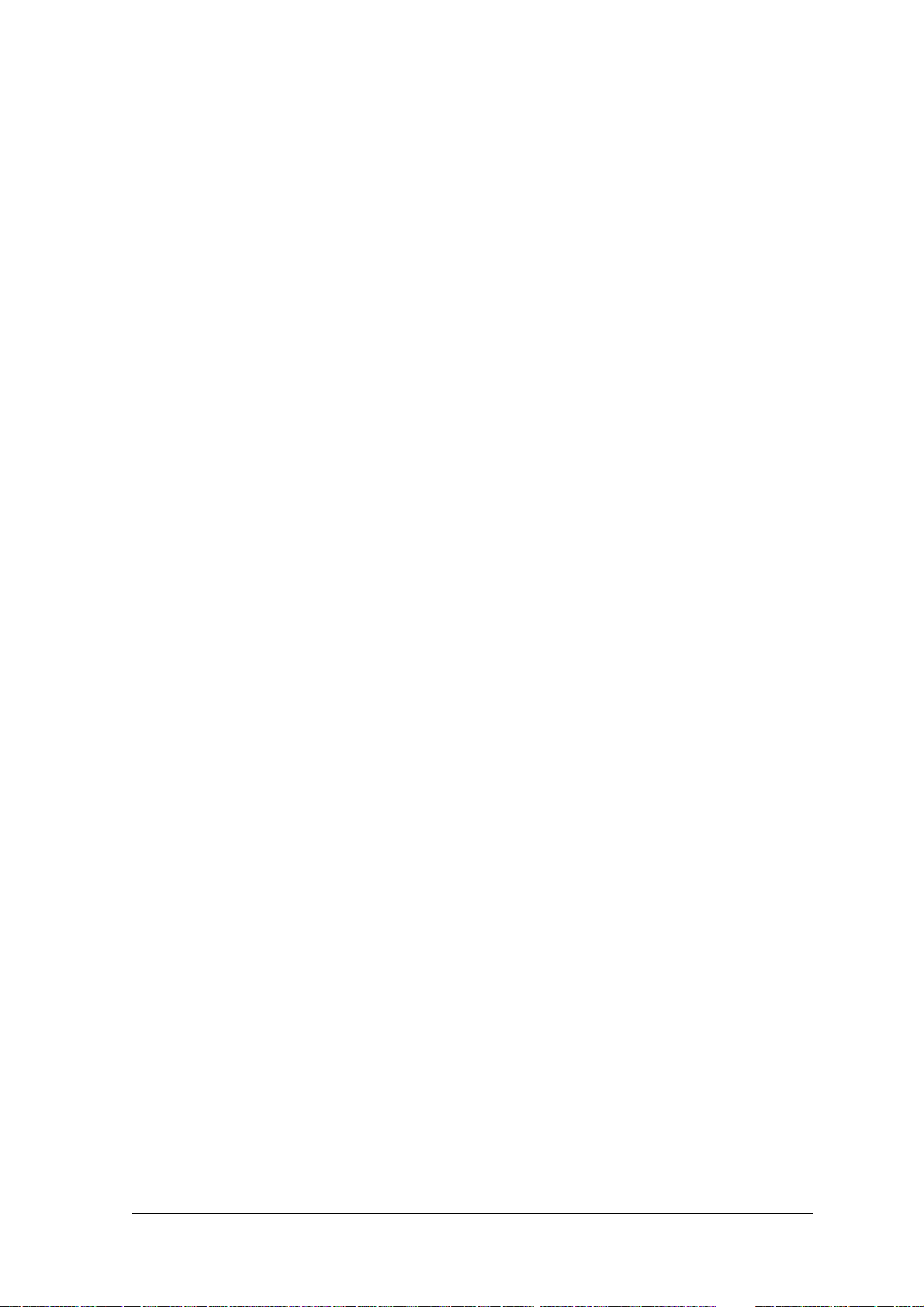
Multidata Network.......................................................................................................37
2.5.6 Fieldbus Network........................................................................................................38
2.6 DX6400 FLASH™ Dynamic Focus.............................................................................39
2.6.1 Fixed Mode.................................................................................................................39
2.6.2 Continuous Mode........................................................................................................ 39
2.6.3 Triggered Mode ..........................................................................................................40
2.6.4 D-FLASH™ Mode.......................................................................................................40
2.7 Keypad and Display....................................................................................................41
2.7.1 Internal Net .................................................................................................................41
2.7.2 Test Mode...................................................................................................................42
3 SOFTWARE CONFIGURATION................................................................................43
3.1 Genius™ Installation...................................................................................................43
3.2 Guide to Rapid Configuration .....................................................................................43
3.2.1 Wizard for Quick Reader Setup..................................................................................43
Test Operating Mode..................................................................................................44
On Line Operating Mode ............................................................................................45
Automatic Operating Mode.........................................................................................45
3.2.2 Genius™ Network Setup Through Master..................................................................46
Net-Autoset.................................................................................................................48
Express Network Setup ..............................................................................................48
Network Wizard ..........................................................................................................49
3.2.3 Alternative Slave Address Assignment.......................................................................51
3.3 Advanced Genius™ Configuration .............................................................................51
3.4 Parameter Default Values...........................................................................................52
4 READING FEATURES...............................................................................................56
4.1 Advanced Code Reconstruction (ACR™ 4)................................................................ 56
4.1.1 Tilt Angle for Advanced Code Reconstruction............................................................56
4.2 PackTrack™ ...............................................................................................................57
4.2.1 PackTrack™ Calibration for DX6400..........................................................................59
Scanner Direction .......................................................................................................60
4.2.2 Overwriting PackTrack™ Calibration for DX6400....................................................... 62
4.3 Performance ...............................................................................................................63
4.4 Reading Conditions ....................................................................................................64
4.5 Reading Diagrams......................................................................................................65
5 MAINTENANCE .........................................................................................................67
5.1 Cleaning......................................................................................................................67
5.2 Automatic Scanner Replacement ...............................................................................67
5.2.1 ASR Network Configuration........................................................................................67
5.2.2 Scanner Replacement Procedure............................................................................... 68
6 TROUBLESHOOTING ...............................................................................................69
7 TECHNICAL FEATURES........................................................................................... 72
GLOSSARY................................................................................................................ 74
INDEX.........................................................................................................................77
iv
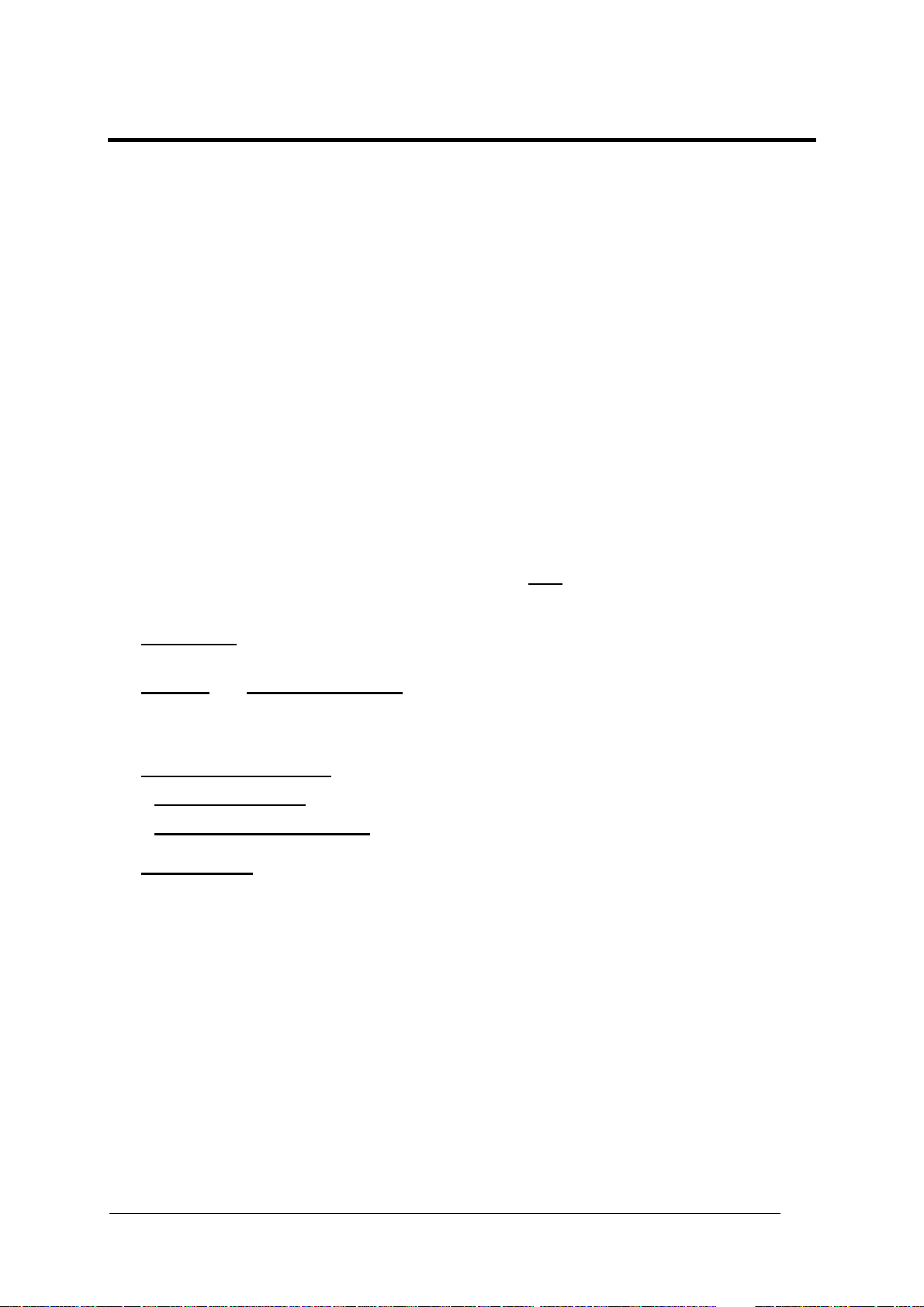
REFERENCES
REFERENCE DOCUMENTATION
The documentation related to the DX6400 management is listed below:
• C-BOX 100 Installation Manual
• INT-30 20 mA Current Loop Interface Board for C-BOX 100
• PWR series power supply unit Installation Manuals
• PWO power supply unit Installation Manual
• SC6000 Controller Reference Manual
• Document about the Ethernet connectivity
• Help On-Line in PDF format
SERVICES AND SUPPORT
Datalogic provides several services as well as technical support through its website. Log on
to www.automation.datalogic.com and click on the
links indicated for further information
including:
•
PRODUCTS
Search through the links to arrive at your product page where you can download specific
Manuals and Software & Utilities including:
- Genius™ a utility program, which allows device configuration using a PC. It provides
RS232 interface configuration.
•
SERVICES & SUPPORT
-
Datalogic Services – Warranty Extensions and Maintenance Agreements
-
Authorised Repair Centres
•
CONTACT US
E-mail form and listing of Datalogic Subsidiaries
PATENTS
This product is covered by one or more of the following patents:
U.S. patents: 5,483,051; Re. 36,251; 6,049,406; 5,992,740; 6,347,740B1; 6,629,639B2;
6,394,352B1; 6,742,710B2; 7,161,685B1; 6,688,524B1; 6,443,360 B1; 7,195,162B2.
European patents: 652,530B1; 786,734B1; 789,315B1; 851,376B1; 1,363,228B1;
959,426B9; 1,300,798B1.
Additional patents pending.
v
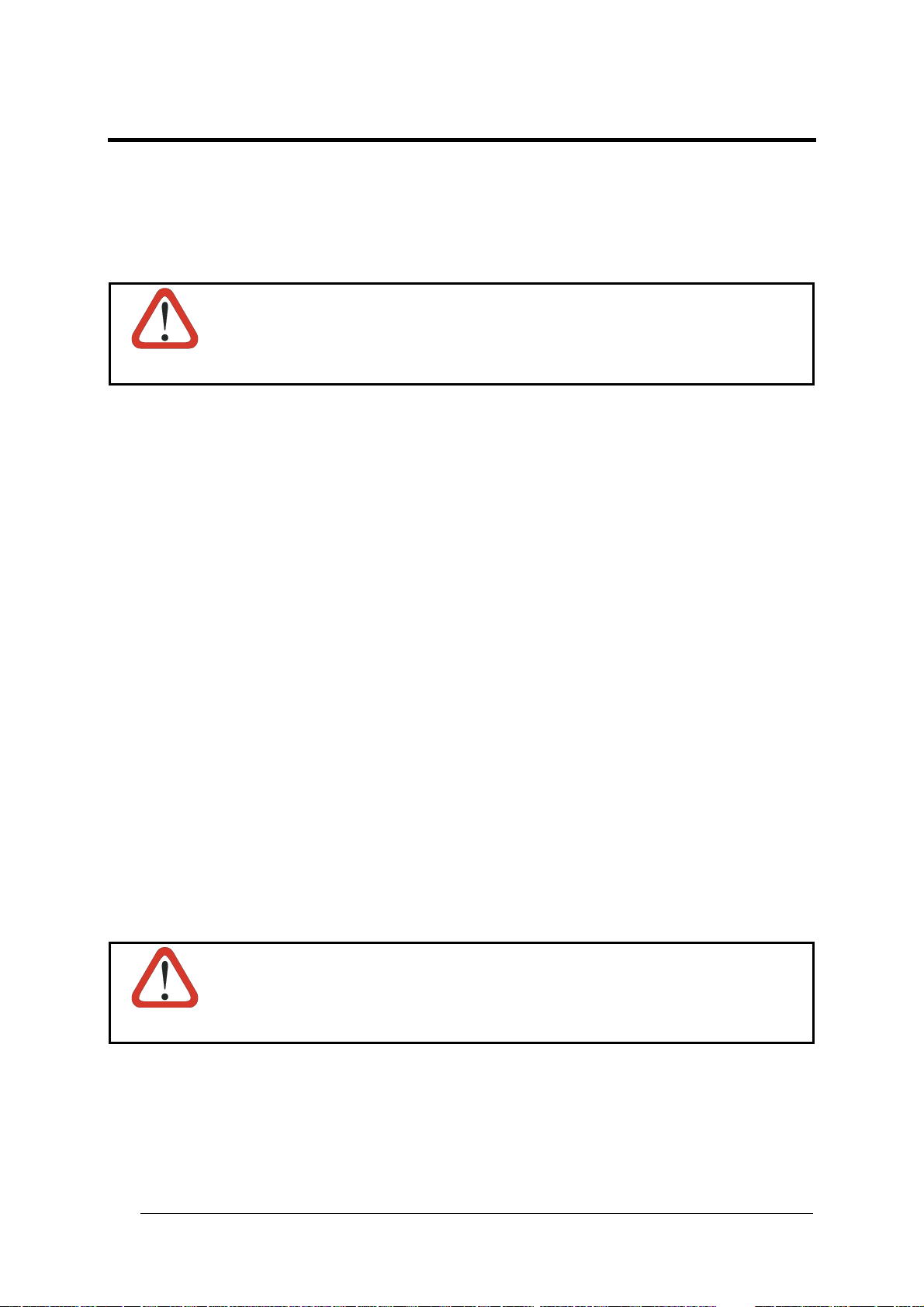
COMPLIANCE
ELECTRICAL SAFETY
This product conforms to the applicable requirements contained in the European Standard for
electrical safety EN-60950-1 at the date of manufacture.
WARNING
This symbol refers to operations that must be performed by qualified
personnel only. Example: opening the device.
LASER SAFETY
The following information is provided to comply with the rules imposed by international
authorities and refers to the correct use of the DX6400 readers.
Standard Regulations
This scanner utilizes up to 2 low-power laser diodes. Although staring directly at the laser
beam momentarily causes no known biological damage, avoid staring at the beam as one
would with any very strong light source, such as the sun.
Avoid that the laser beam hits the eye of an observer, even through reflective surfaces such
as mirrors, etc.
This product conforms to the applicable requirements of both EN60825-1 and
CDRH 21 CFR1040 at the date of manufacture. The reader is classified as a Class 2 laser
product according to EN60825-1 regulations and as a Class II laser product according to
CDRH regulations.
Disconnect the power supply when opening the device during maintenance or installation to
avoid exposure to hazardous laser light.
There is a safety device, which allows the laser to be switched on only if the motor is rotating
above the threshold for its correct scanning speed.
WARNING
Use of controls or adjustments or performance of procedures other than those
specified herein may result in exposure to hazardous visible laser light.
The laser light is visible to the human eye and is emitted from the window on the head of the
reader (Figure A, 7).
vi
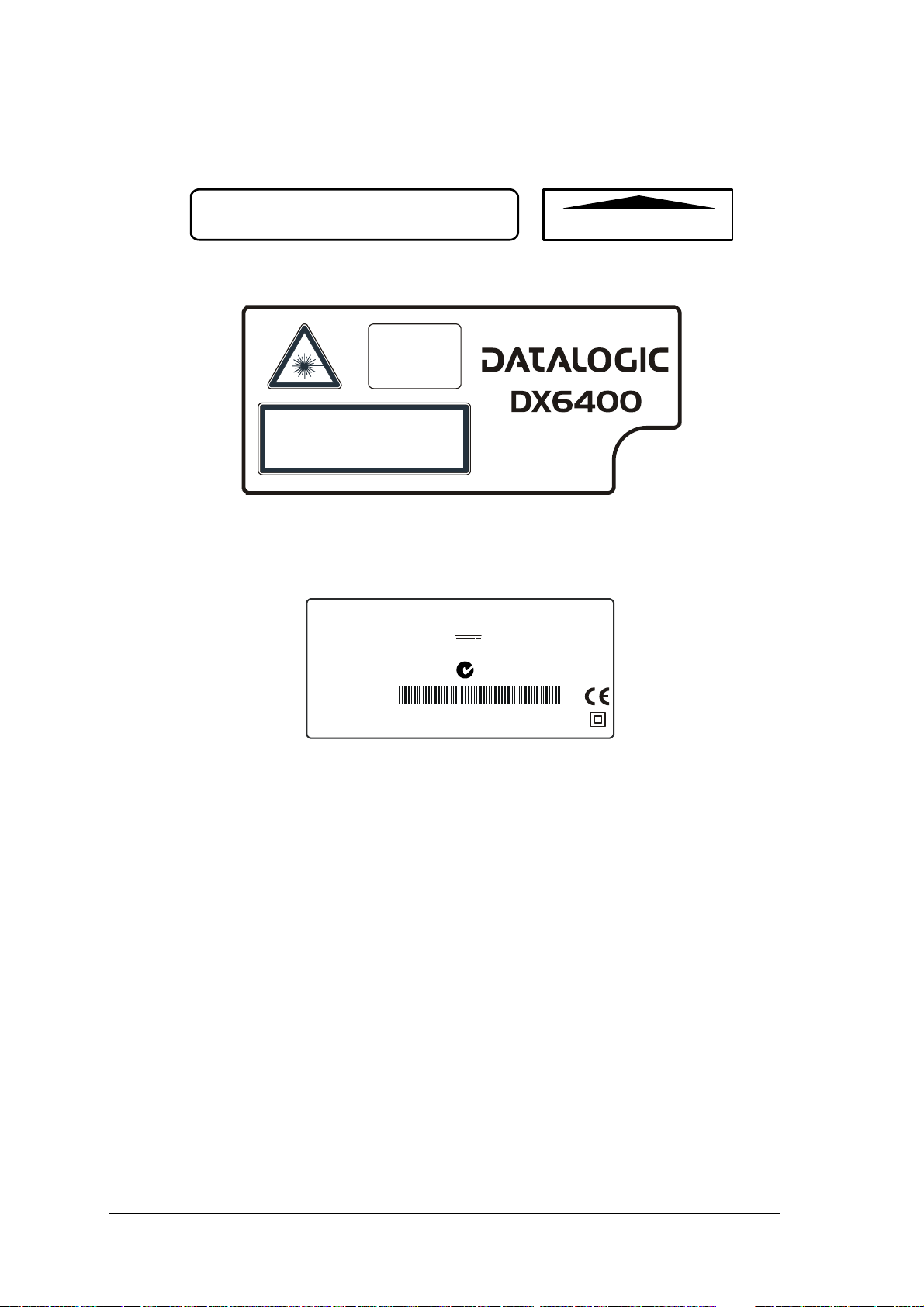
Warning labels indicating exposure to laser light and the device classification are applied
onto the head of the reader (Figure A, 1 & 3):
AVOID EXPOSURE
LASER RADIATION IS EMITTED FROM THIS APERTURE
AVOID EXPOSURE – LASER LIGHT
IS EMITTED FROM THIS APERTURE
Laser Safety Label for Oscillating Mirror and Standard Models
CAUTION-CLASS 3B
LASER LIGHT
WHEN OPEN
AVOID EXPOSURE
TO BEAM
LASER LIGHT – DO NOT STARE INTO BEAM
CLASS 2 LASER PRODUCT
MAX. OUTPUT RADIATION 1 mW
EMITTED WAVE LENGTH 630 ~ 680 nm
EN60825-1:2001
Warning and Device Class Label
The identification label is applied onto the bottom part of the scanner (Figure A, 2):
N2468
DATALOGIC S.p.A. Via Candini, 2
40012 LIPPO DI CALDERARA DI RENO (BO) ITALY
MANUFACTURED VOLT Amp.
JANUARY 2002 15-30 DC 1.2-0.6
MODEL No.
SERIAL No.
This product conforms to the applicable requirements
of 21CFR 1040 at the date of manufacture.
Device Identification Label
The laser diode used in this device is classified as a Class 3B laser product according to
EN60825-1 regulations and as a Class IIIb laser product according to CDRH regulations. Any
violation of the optic parts in particular can cause radiation up to the maximum level of the
laser diode (35 mW at 630~680 nm).
POWER SUPPLY
- This product is intended to be installed by Qualified Personnel only.
- All DX6400 Models:
This device is intended to be supplied by a UL Listed Power Unit marked “Class 2” or LPS
power source, which supplies power directly to the scanner via the 25/26-pin connector.
This scanner must be supplied by a Class II Power Supply Unit conforming to the
EN 60950 safety regulation.
vii
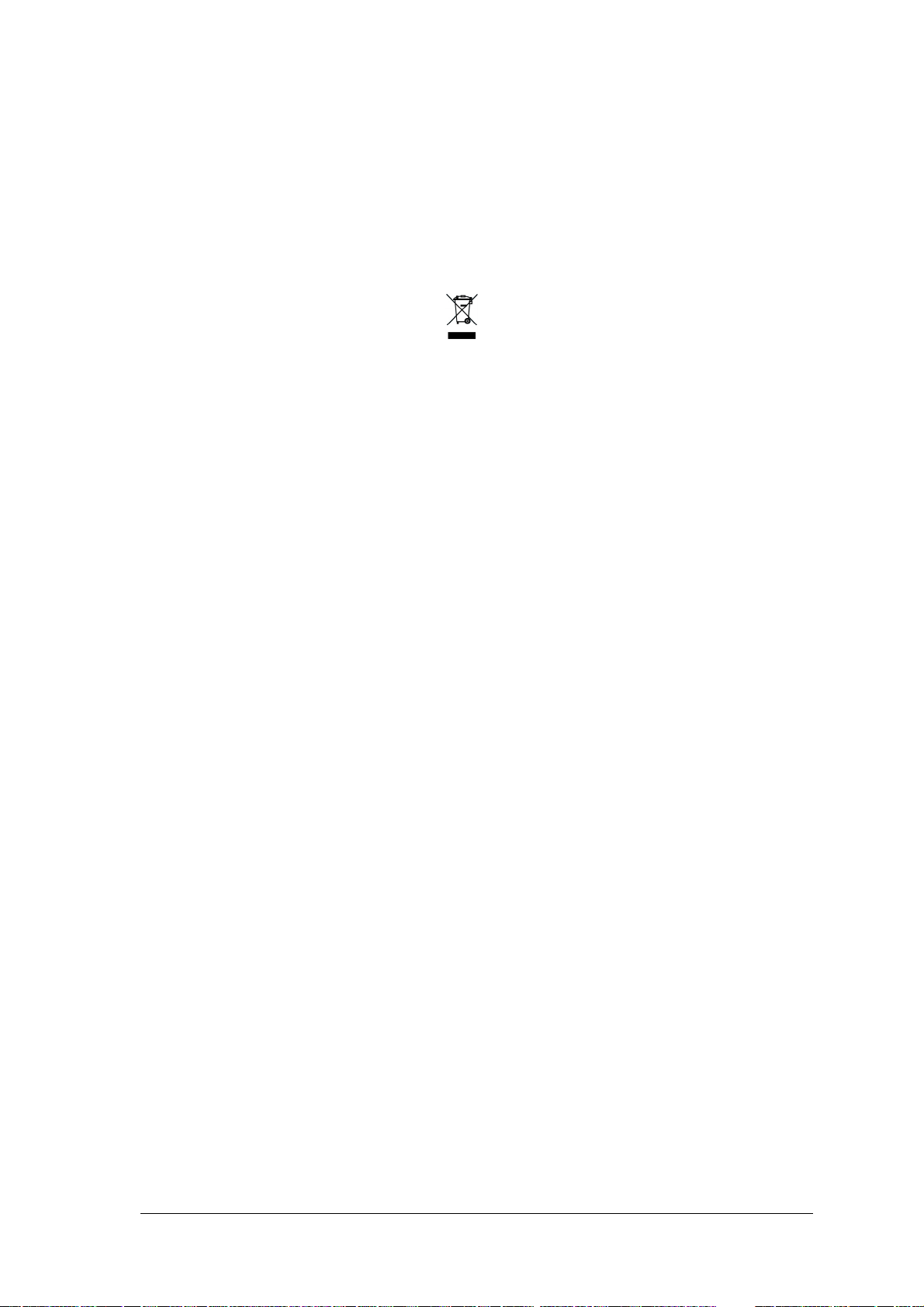
CE COMPLIANCE
Warning:
This is a Class A product. In a domestic environment this product may cause radio
interference in which case the user may be required to take adequate measures.
WEEE COMPLIANCE
ENGLISH
Information for the user in accordance with the European Commission Directive 2002/96/EC
At the end of its useful life, the product marked with the crossed out wheeled wastebin must be disposed of
separately from urban waste.
Disposing of the product according to this Directive:
• avoids potentially negative consequences to the environment and human health which otherwise could
be caused by incorrect disposal
• enables the recovery of materials to obtain a significant savings of energy and resources.
For more detailed information about disposal, contact the supplier that provided you with the product in question
or consult the dedicated section at the website www.automation.datalogic.com.
ITALIANO
Informazione degli utenti ai sensi della Direttiva Europea 2002/96/EC
L’apparecchiatura che riporta il simbolo del bidone barrato deve essere smaltita, alla fine della sua vita utile,
separatamente dai rifiuti urbani.
Smaltire l’apparecchiatura in conformità alla presente Direttiva consente di:
• evitare possibili conseguenze negative per l’ambiente e per la salute umana che potrebbero invece
essere causati dall’errato smaltimento dello stesso;
• recuperare materiali di cui è composto al fine di ottenere un importante risparmio di energia e di risorse.
Per maggiori dettagli sulle modalità di smaltimento, contattare il Fornitore dal quale è stata acquistata
l’apparecchiatura o consultare la sezione dedicata sul sito www.automation.datalogic.com.
DEUTSCH
Benutzerinformation bezüglich Richtlinie 2002/96/EC der europäischen Kommission
Am Ende des Gerätelebenszyklus darf das Produkt nicht über den städtischen Hausmüll entsorgt werden. Eine
entsprechende Mülltrennung ist erforderlich.
Beseitigung des Produkts entsprechend der Richtlinie:
• verhindert negative Auswirkungen für die Umwelt und die Gesundheit der Menschen
• ermöglicht die Wiederverwendung der Materialien und spart somit Energie und Resourcen
Weitere Informationen zu dieser Richtlinie erhalten Sie von Ihrem Lieferanten, über den Sie das Produkt
erworben haben, oder besuchen Sie unsere Homepage unter www.automation.datalogic.com.
viii
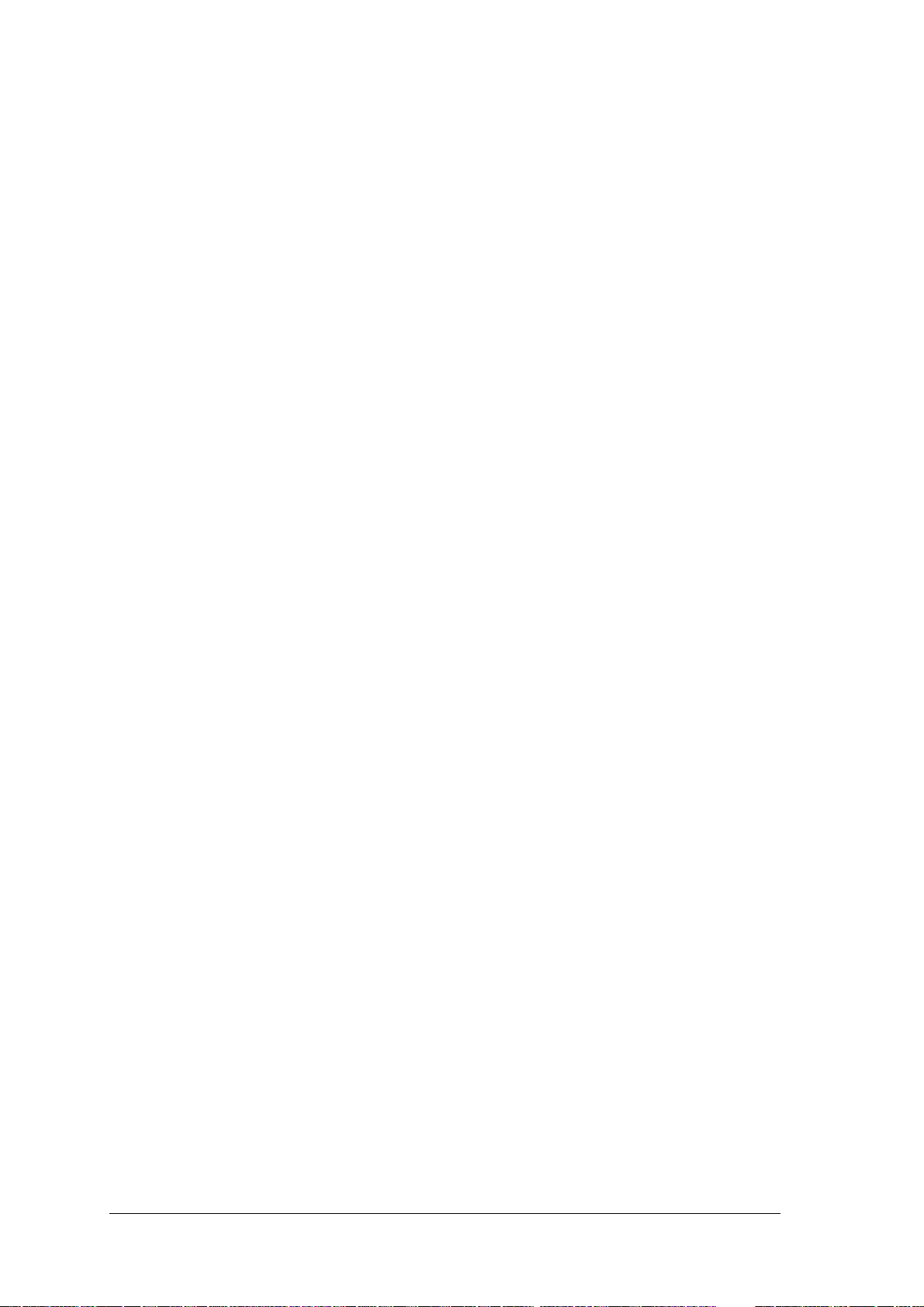
FRANÇAIS
Information aux utilisateurs concernant la Directive Européenne 2002/96/EC
Au terme de sa vie utile, le produit qui porte le symbole d'un caisson à ordures barré ne doit pas être éliminé avec
les déchets urbains.
Éliminer ce produit selon cette Directive permet de:
• éviter les retombées négatives pour l'environnement et la santé dérivant d'une élimination incorrecte
• récupérer les matériaux dans le but d'une économie importante en termes d'énergie et de ressources
Pour obtenir des informations complémentaires concernant l'élimination, veuillez contacter le fournisseur auprès
duquel vous avez acheté le produit ou consulter la section consacrée au site Web
www.automation.datalogic.com.
ESPAÑOL
Información para el usuario de accuerdo con la Directiva Europea 2002/96/CE
Al final de su vida útil, el producto marcado con un simbolo de contenedor de bassura móvil tachado no debe
eliminarse junto a los desechos urbanos.
Eliminar este producto de accuerdo con la Directiva permite de:
• evitar posibles consecuencias negativas para el medio ambiente y la salud derivadas de una eliminación
inadecuada
• recuperar los materiales obteniendo así un ahorro importante de energía y recursos
Para obtener una información más detallada sobre la eliminación, por favor, póngase en contacto con el
proveedor donde lo compró o consultar la sección dedicada en el Web site www.automation.datalogic.com.
ix
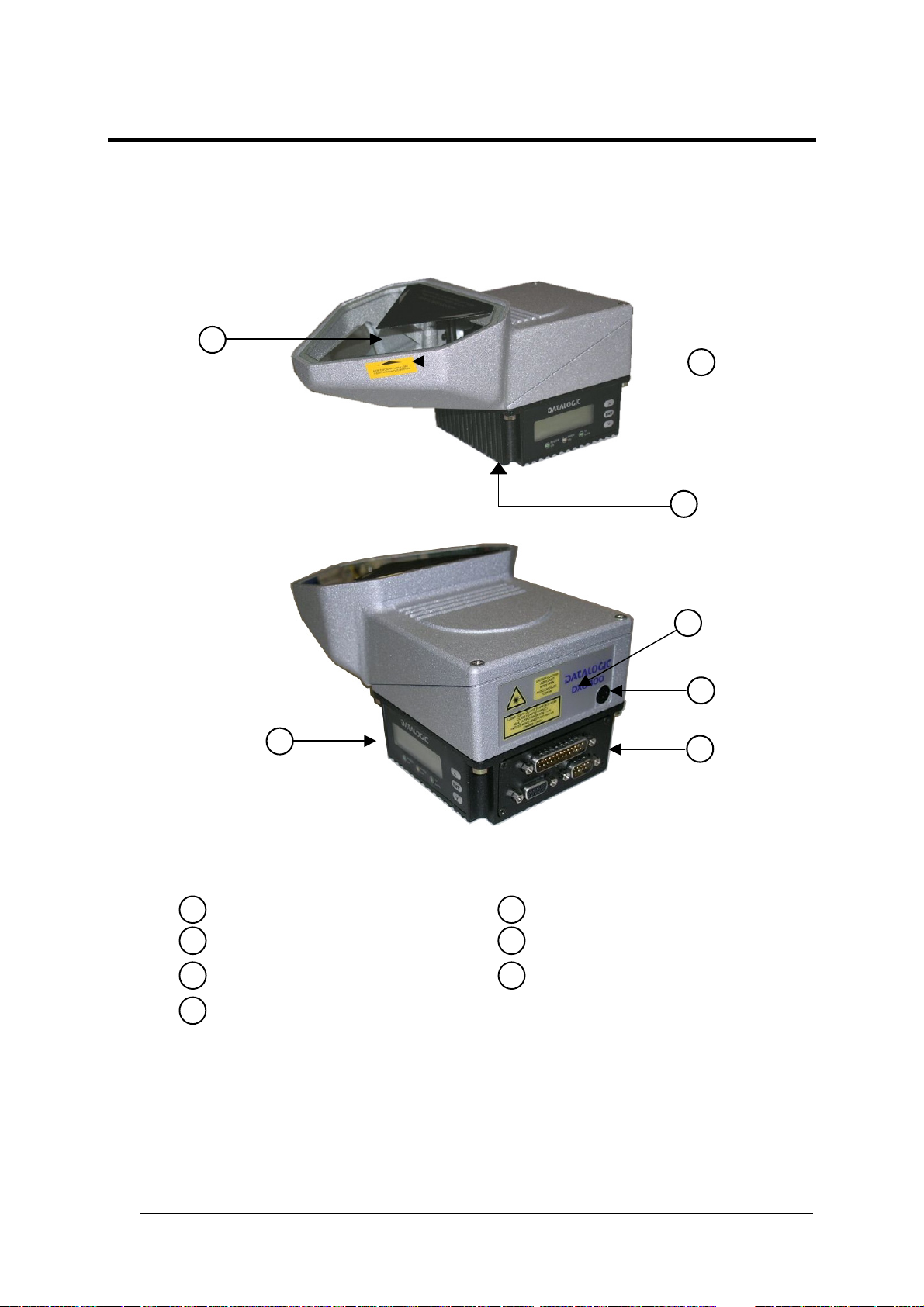
GENERAL VIEW
DX6400
5
2
1
3
4
6
7
Figure A – DX6400
Laser Safety Label
Warning and Device Class Label
Identification Label
Connector Panel
Display and Keypad Panel
Laser Beam Output Window
1
3
7
6
5
2
Service Cap
4
x
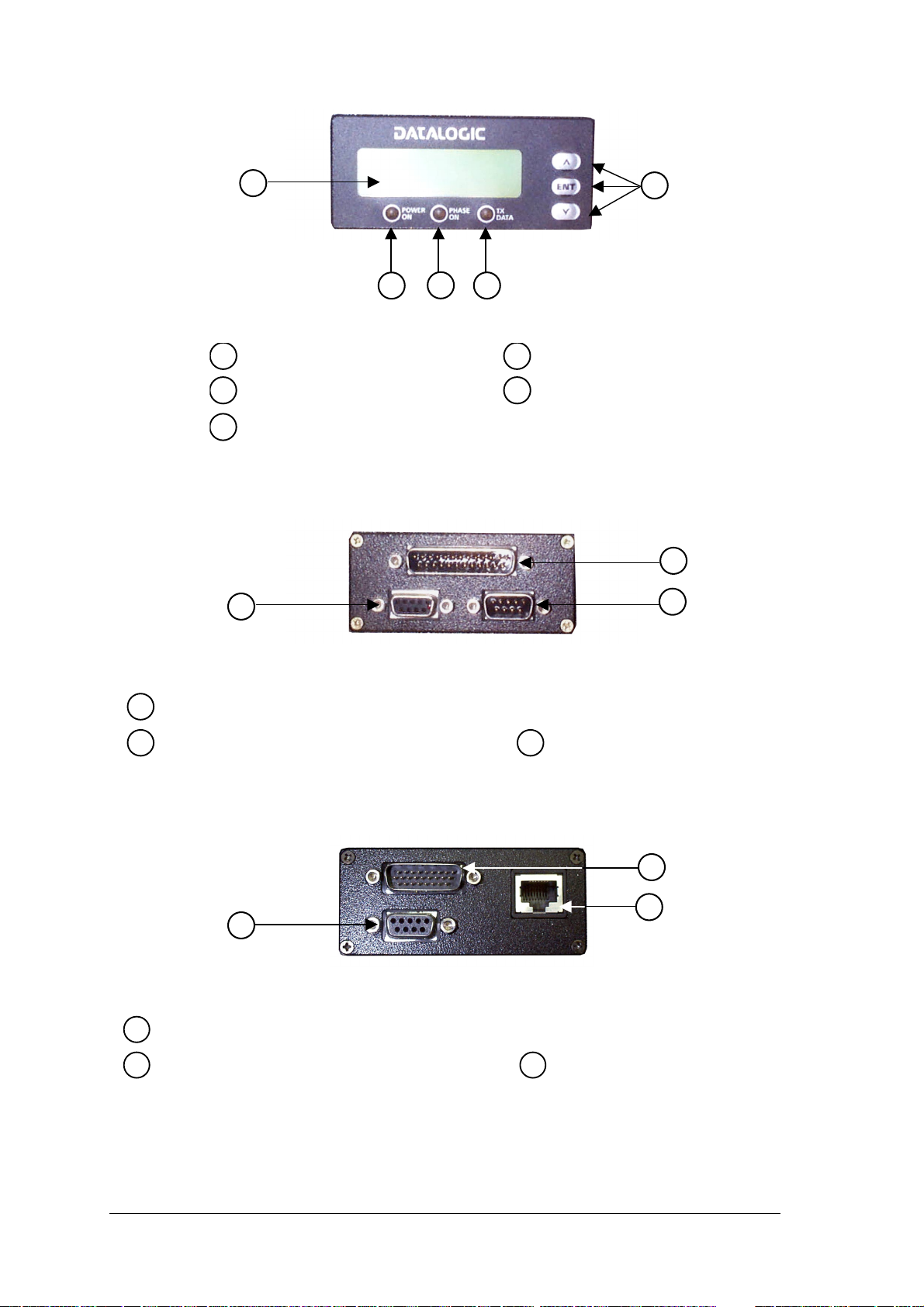
Figure B – Display and Keypad Panel
Programming Keypad
Phase On LED
TX Data LED
Power On LED
LCD Display
1
2
3
5
4
Figure C – Connector Panel for Master/Slave Models
Main/Aux. Interface 25-pin D-Sub male connector
1
Lonworks 9-pin male connector
2
Lonworks 9-pin female connector
3
Figure D – Connector Panel for Ethernet Models
Main/Aux. Interface 26-pin D-Sub male connector
1
RJ45 modular connector for Ethernet Interface
2
Lonworks 9-pin female connector
3
4
3
2
5
1
2
1
3
2
1
3
xi
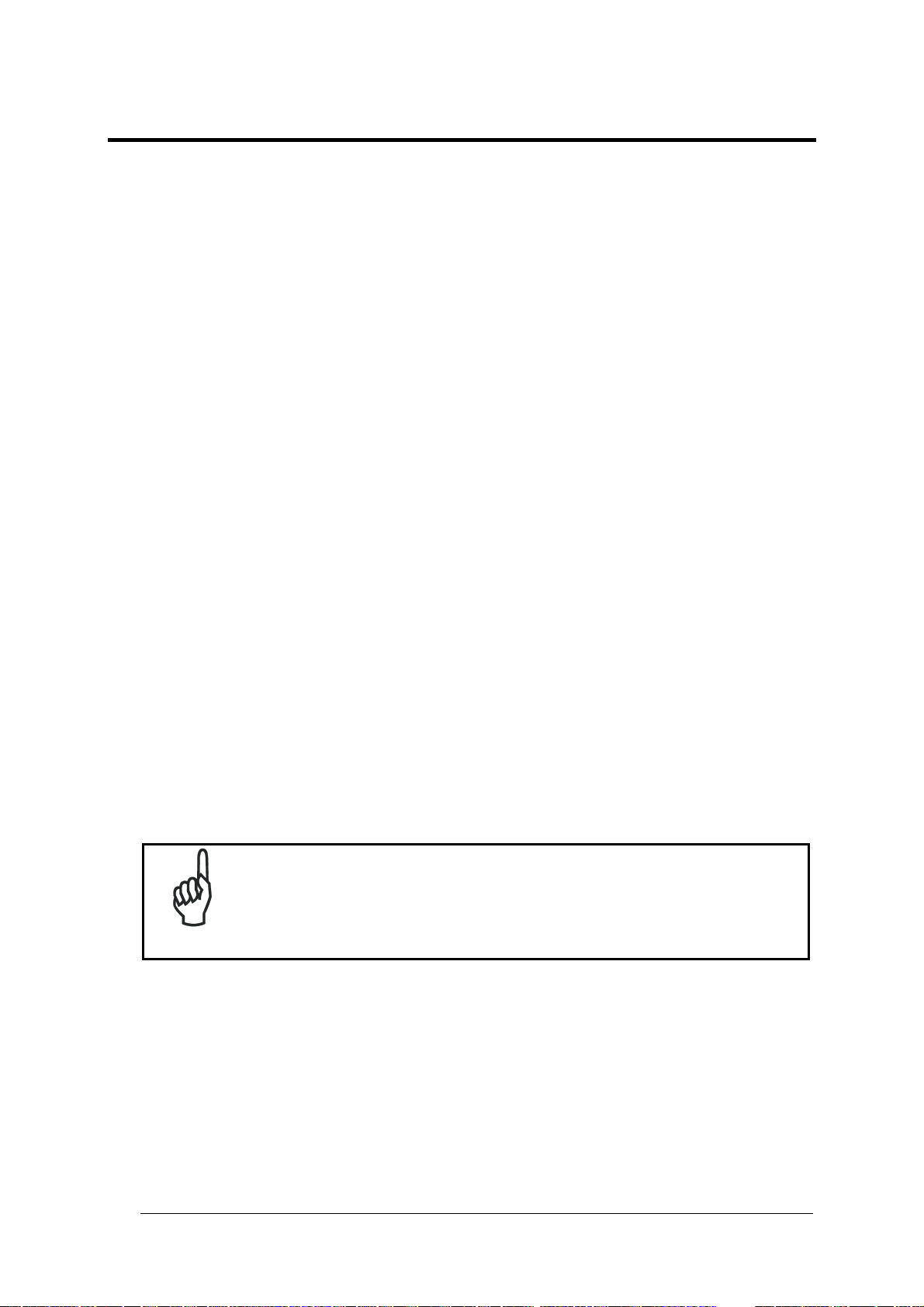
GUIDE TO INSTALLATION
POINT-TO-POINT INSTALLATION
The following can be used as a checklist to verify all the steps necessary to complete
installation of the DX6400 scanner.
1) Read all information in the section “Safety Precautions” at the beginning of this manual.
2) Correctly mount the scanner according to the information in par. 2.2 and position the
reader at the correct reading distance according to the reading diagrams in par. 4.5.
3) Make electrical connections to your DX6400 scanner by:
a) Connecting the DX6400 scanner to the C-BOX 100 by means of one of the cables
provided as accessory (see par. 1.5).
b) Providing correct and complete system cabling through the C-BOX 100 according to
the signals (trigger, inputs, outputs) necessary for the layout of your application.
• Layout: Point-to-Point, RS232 Master/Slave, Lonworks, Fieldbus. See sub-
paragraphs under 2.5 for reference.
• Cabling: Power, Main Serial Interface – RS232, RS485 Half Duplex, RS485 Full
Duplex, 20 mA Current Loop, Auxiliary Interface, Inputs, Outputs, etc -. For further
details, see all sub-paragraphs under par. 2.3.
4) Configure the DX6400 scanner by installing and running the Genius™ configuration
program from the CD-ROM provided. The main steps are:
• Select the codes to be read
• Set-up the communication parameters
• When PackTrack™ is required, set the PS Offset and Position parameters
• Define data formatting parameters
NOTE
Fine tuning of the scanner position for barcode reading can be
accomplished by performing a test through the SPY configuration tool
in Genius™.
5) Exit the configuration program and run your application.
The installation is now complete.
xii
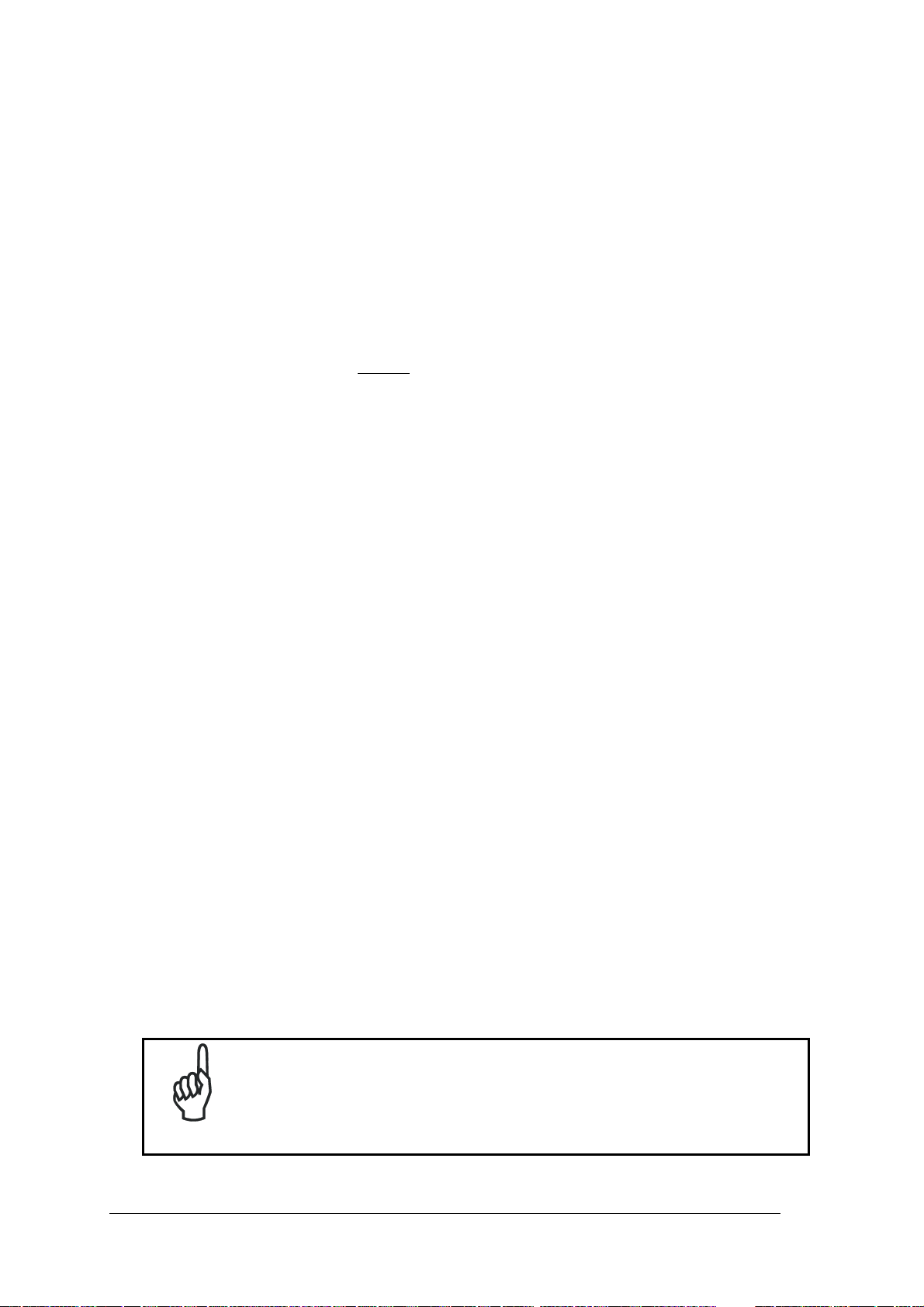
MASTER/SLAVE LONWORKS INSTALLATION
The following can be used as a checklist to verify all the steps necessary to complete
installation of the DX6400 scanner in a Master/Slave Lonworks network.
1) Read all information in the section “Safety Regulations” at the beginning of this manual.
2) Correctly mount the scanner according to the information in par. 2.2 and position it at the
correct reading distance as shown in par. 4.5.
3) Make electrical connections to your DX6400 scanner by:
a) Connecting the DX6400 Master scanner to the C-BOX 100 by means of one of the
cables provided as accessory (see par. 1.5).
b) Correctly inserting the BTK-6000 terminator in the DX6400 Master reader according
to the information given under “Local Lonworks Network” in par. 2.3.2 and par. 2.5.5.
c) Completing the system wiring adding as many slave scanners as required by your
system layout (refer to par. 2.5.5).
d) Correctly inserting the BTK-6000 terminator in the last DX6400 Slave reader of the
network according to the information given under “Local Lonworks Network” in par.
2.3.2 and par. 2.5.5.
4) Install and run the Genius™ configuration program from the CD-ROM provided.
Configure the Local Lonworks Network using one of the procedures given below:
a) Configure the entire network through the Master as described in par. 3.2.2.
b) Configure the Master as described in par. 3.2.2 and locally define each slave scanner
address as described in par. 3.2.3.
c) Define each scanner, master and slaves (with their addresses), by using the scanner
keypad according to the information given in par. 2.7.1.
5) Configure the Master scanner through the Genius™ program. The main steps are:
• Select the codes to be read
• Set-up the communication parameters
• When PackTrack™ is required, perform PackTrack™ calibration, see par. 4.2.1.
• Define data formatting parameters
6) Configure each Slave scanner through the Master scanner using Genius™. The main
steps are:
• Select the codes to be read
• When PackTrack™ is required, perform PackTrack™ calibration, see par. 4.2.1.
NOTE
Fine tuning of the scanner position for barcode reading can be
accomplished by performing a test through the SPY configuration tool
in Genius™.
xiii
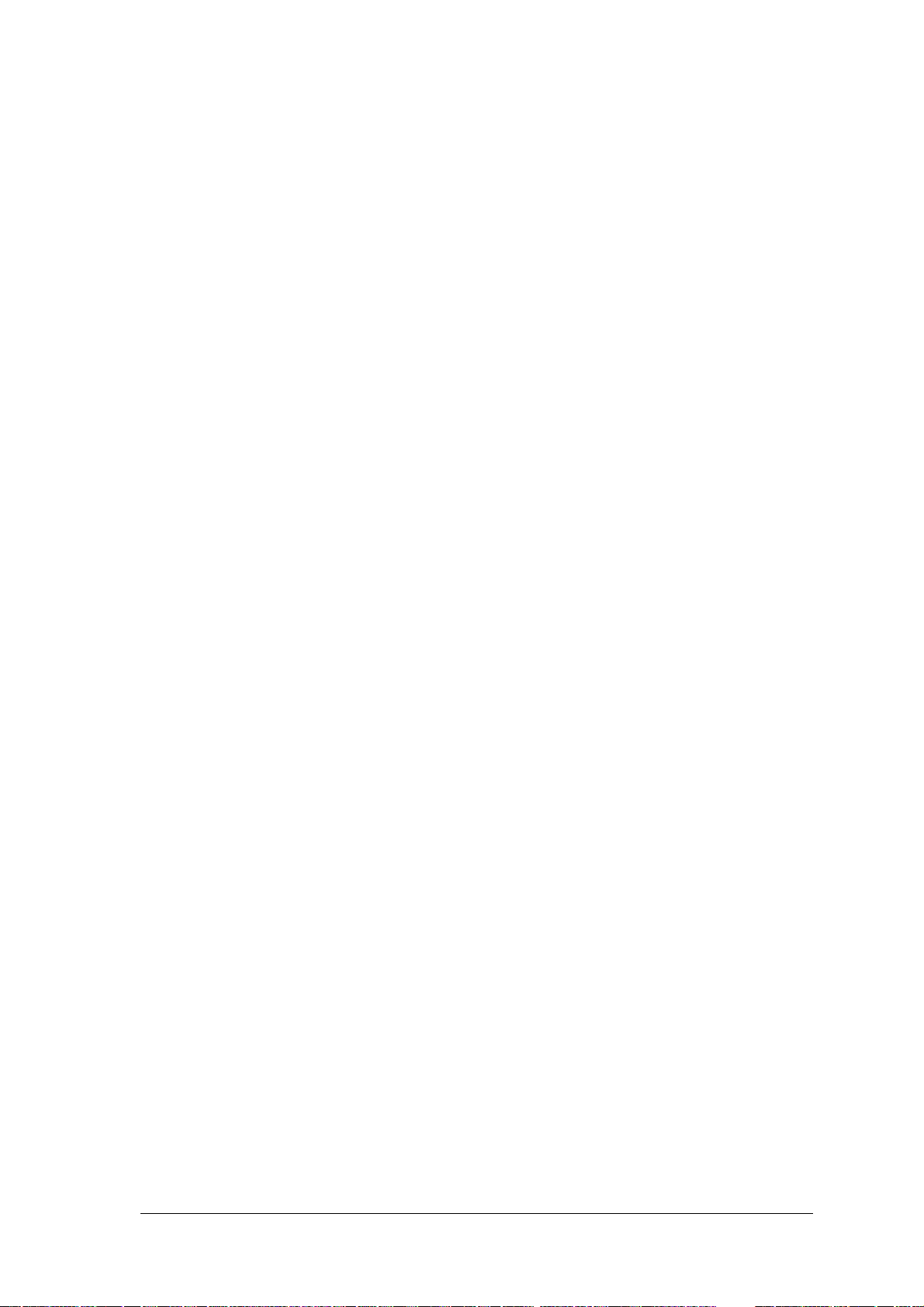
7) Send the configuration to the Master.
8) Optionally, perform the ASR Network Configuration procedure for system backup
purposes (see par. 5.2.1).
9) Exit the configuration program and run your application.
The installation is now complete.
xiv
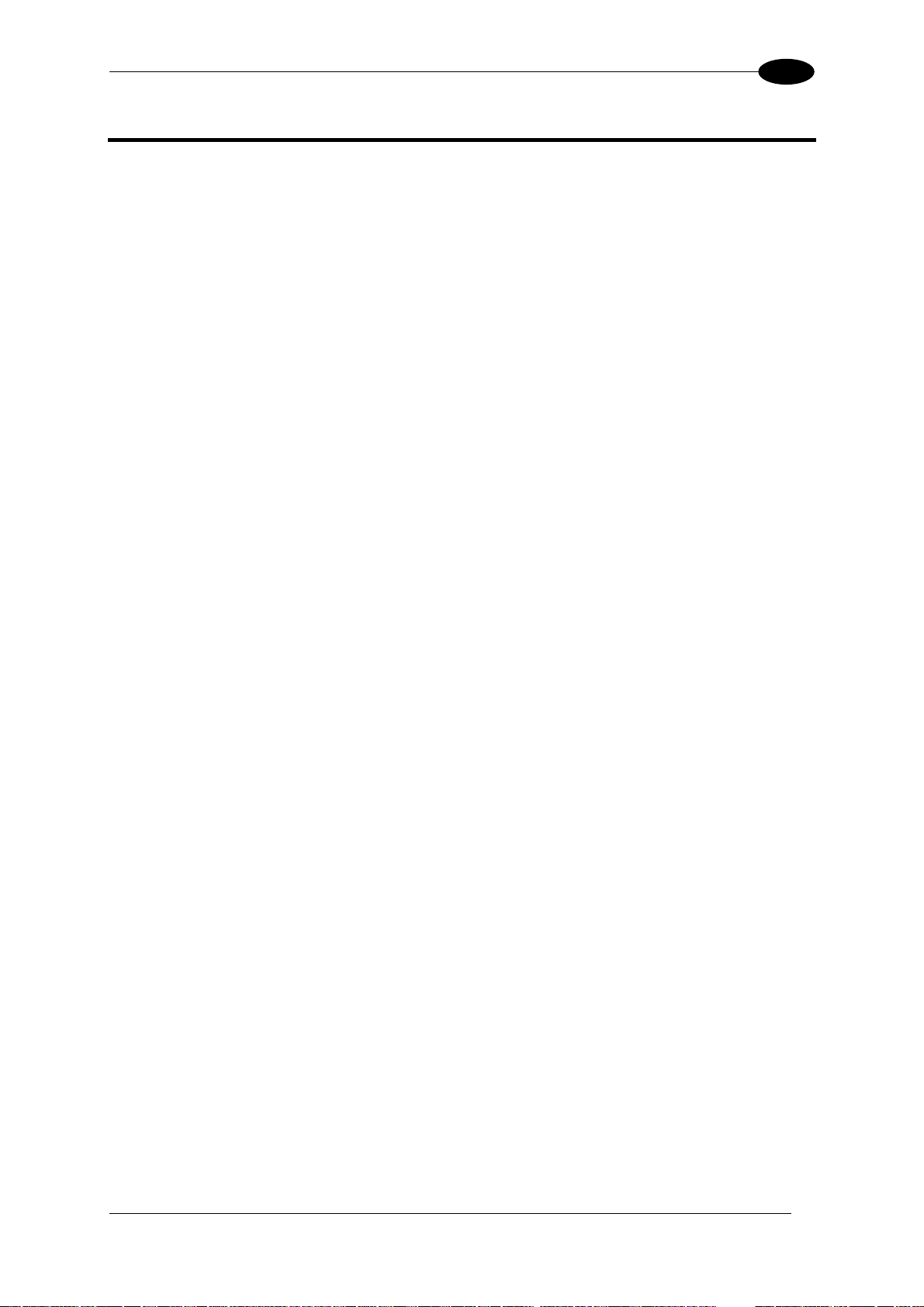
INTRODUCTION
1
1 INTRODUCTION
1.1 PRODUCT DESCRIPTION
The DX6400 is a high performance laser scanner in a complete range of industrial bar code
readers offering an innovative and modular solution in terms of reading performance,
connectivity and maintenance, in addition to a completely new hardware and software
platform.
The DX6400 has been specifically designed for simple installation, easy use and flexibility.
An innovative mechanical design together with the Datalogic patent pending
Step-a-Head
TM
feature make it possible to rotate the reader head and the decoder base
independently from each other. Step-a-Head
TM
enables the DX6400 to always be installed in
the ideal position, by modifying the orientation of the connector panel while leaving the laser
window in the desired position. The need for space is minimized and installation is easier.
The DX6400 has an innovative linear motor designed to control the focus position of the
scanner via software. This dynamic system, called FLASH
TM
,
is able to move the focus
position rail to rail, from the minimum position to the maximum position, in less than 10 msec.
In typical applications, where a DOF <1 meter is required, the focus position is adjusted in 4
msec.
The DX6400 can read all most popular barcodes even in the most difficult conditions, thanks
to a new generation decoder with Intel XScale CPU and code reconstruction technology
(ACR™ 4).
Great attention has been given to built-in connectivity for market standards. Lonworks, and
Ethernet bus have been integrated in dedicated versions of the decoder base.
Some of the main features of DX6400 are listed below:
• scanning speed up to 750 scans/sec per scan line (total 1500 scans/sec);
• 2 serial communication interfaces
• reading all popular codes;
• supply voltage from 15 to 30 Vdc;
• electrical connection through connectors;
• high speed Lonworks connectivity for Master/Slave layout;
• built-in connectivity for Ethernet;
• programmable in 5 different operating modes to suit the most various barcode reading
system requirements;
• light source: solid state laser diode; the light emitted has a wavelength between
630~680nm.
• IP64 protection class of the enclosure (for Master/Slave models).
1
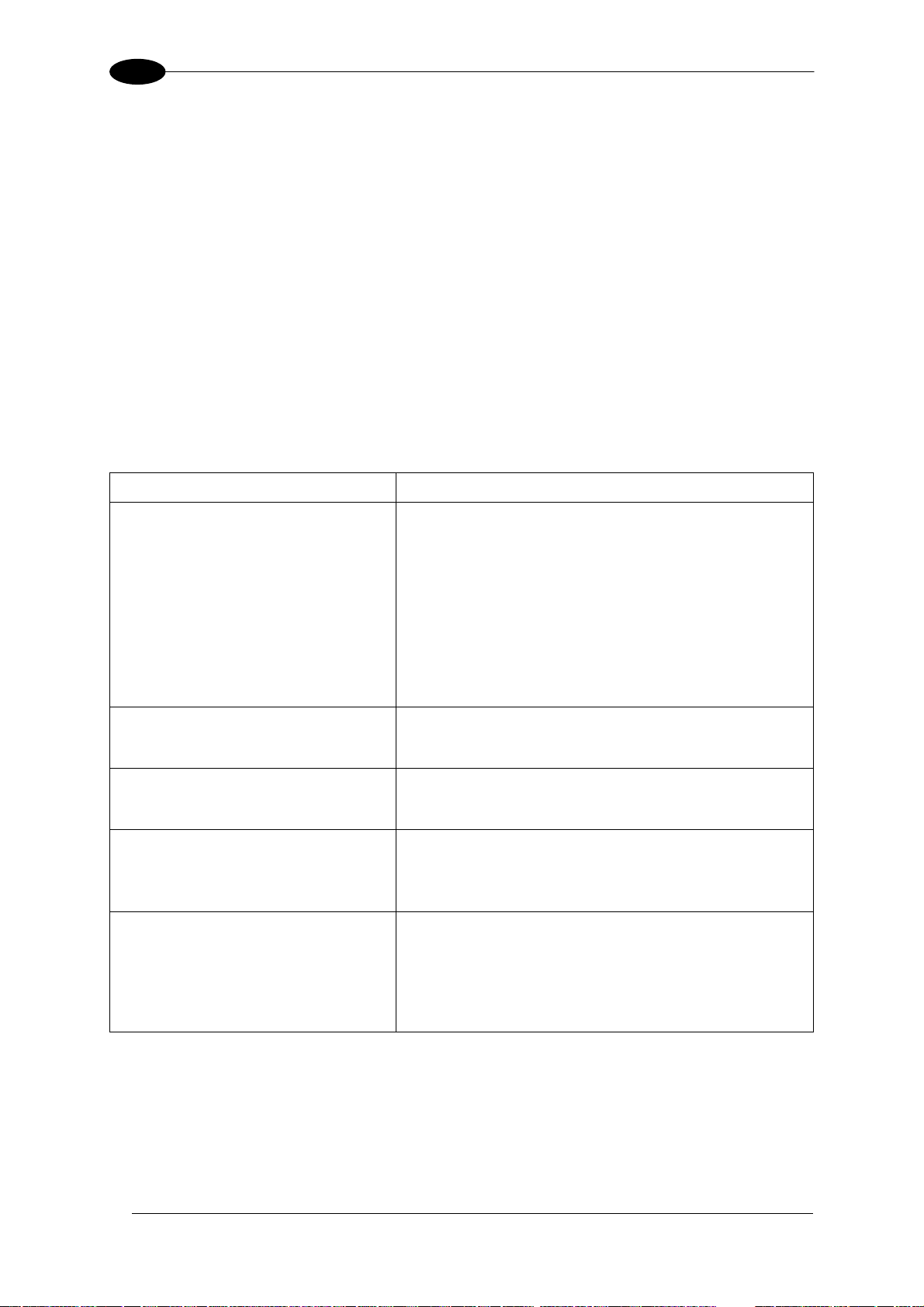
DX6400
1
1.2 APPLICATIONS
The DX6400 barcode reader is specifically designed for industrial applications and for all
cases requiring high reading performance such as:
• omni-directional reading
• code reconstruction
• reading of codes covered by plastic film
• reading of codes with a wide depth of field
• reading of high resolution codes positioned at medium distances from the reader
• code reading on fast moving objects
DX6400 is designed for both single-reader layouts and multi-reader layouts. For typical
layouts see paragraph 2.5.
Feature
Benefit
Modular solution with separated
head and base and
Step-a-Head
TM
feature
• Possibility to select the combination of head and
base that best fits the needs of the application.
• Great scalability of the offer.
• Down time cost reduction, since the decoder base
works even if the head has been removed.
• Easy maintenance. In case of replacement of the
head, all the configuration parameters are stored
in the base, and the scanner is automatically
configured.
• Easy installation with the minimum room needed.
Reading on pallets or big objects
where a large reading distance /
wide reading field are needed
• DX6400 with FLASH
TM
dynamic focusing system.
Reading parcels on conveyors • DX6400 implements the Packtrack
TM
functionality,
which leads to an increase of the plant production
as a result of the augmented system throughput.
Master working as a multiplexer
on a high speed Lonworks bus
• Great competitiveness of the offer, since the cost
of an external multiplexer is saved.
• High data transfer on a industrial, reliable bus
running at 1,2 Mbit/sec.
Genius™ Configurator SW • Reduced learning time, with an easy wizard
approach.
• Multilanguage platform.
• All the configuration parameters stored into the
scanner.
• Not dependent on the Physical interface.
2
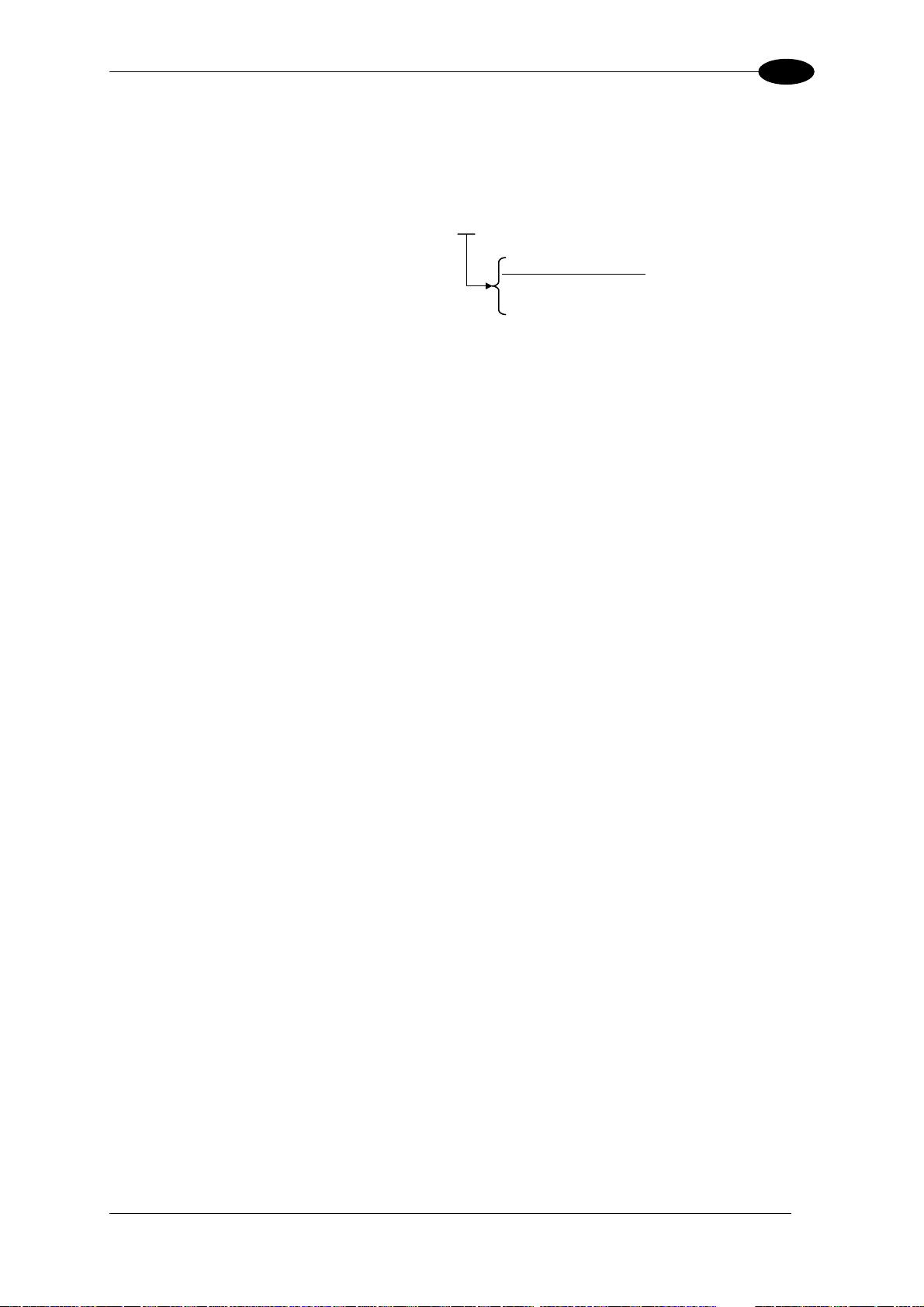
INTRODUCTION
1
1.3 MODEL DESCRIPTION
The DX6400 scanner is available in versions that differ in regard to the Decoder Model
(Base):
Decoder Model (Base)
10 = Master/Slave
12 = Ethernet
DX6400 - 100 - 0YY
1.4 INDICATORS
The DX6400 decoder base provides an LCD display for system messages and configuration
menus. The three keys present on the side of the display allow configuration menu
navigation (Figure B, 1). See par. 2.7 for details. The three LED indicators have the following
functions:
POWER ON
(red) Indicates the reader is turned on (Figure B, 4).
PHASE ON
(yellow) Indicates the external presence sensor is active (Figure B, 3).
TX DATA
(green) Indicates the main serial interface is operating correctly during
data transmission (Figure B, 2).
3
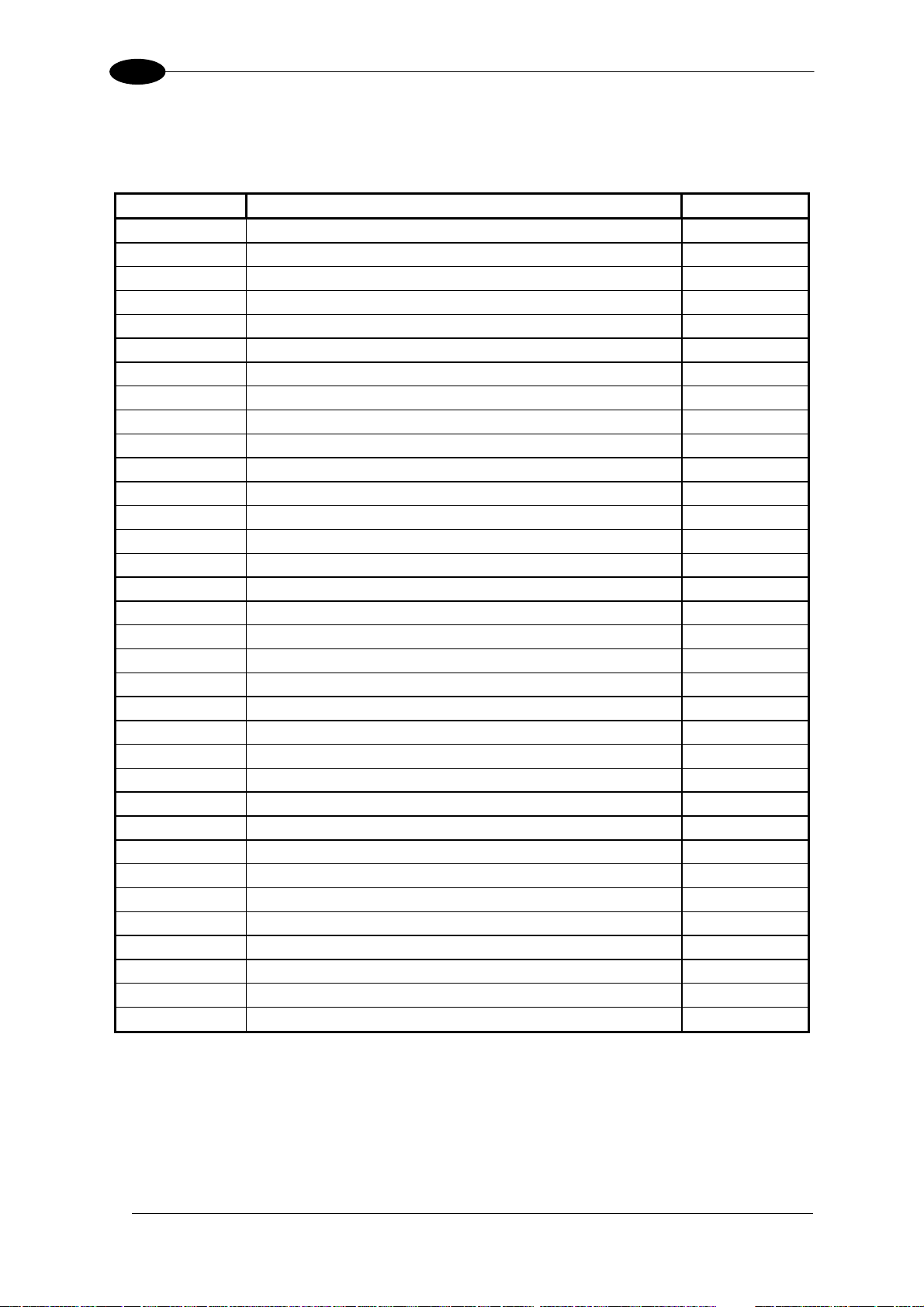
DX6400
1
1.5 ACCESSORIES
The following accessories are available on request for DX6400:
Name Description Part Number
BTK-6000
Bus terminator kit (5 pcs) 93ACC1710
CAB-6001 25-pin scanner to C-BOX100 cable 1 m 93A051190
CAB-6002 25-pin scanner to C-BOX100 cable 2 m 93A051200
CAB-6005 25-pin scanner to C-BOX100 cable 5 m 93A051210
CAB-6010 25-pin scanner to C-BOX100 cable 10 m 93A051271
CAB-6011 26-pin scanner to C-BOX100 cable 1 m (Ethernet version) 93A051221
CAB-6012 26-pin scanner to C-BOX100 cable 2 m (Ethernet version) 93A051222
CAB-6015 26-pin scanner to C-BOX100 cable 5 m (Ethernet version) 93A051223
CAB-6101
9-pin scanner/scanner connection cable 1 m
93A051220
CAB-6102 9-pin scanner/scanner connection cable 2 m
93A051230
CAB-6105 9-pin scanner/scanner connection cable 5 m 93A051240
CAB-6112 9-pin scanner to scanner no power cable 2 m 93A051224
CAB-6115 9-pin scanner to scanner no power cable 5 m 93A051225
CAB-6305 25-pin power cable Fam 6k 5 m 93ACC1768
CAB-6310 25-pin power cable Fam 6k 10 m 93ACC1752
CAB-6502 Fam 6K-8K cross cable 2.5 m 93A051288
CAB-6505 Fam 6K-8K cross cable 5 m 93A051289
C-BOX 100
Passive connection box 93ACC1510
C-BOX 300
Profibus-DP connection box 93A301000
C-BOX 310
Profibus-DP connection box with display 93A301030
C-BOX 400
Devicenet connection box 93A301010
C-BOX 410
Devicenet connection box with display 93A301040
FBK-6000 Fast bracket kit (2 pcs) 93ACC1721
INT-30 20 m.A. C.L. interface board for C-BOX 100 93A151022
PH-1 Photocell kit – PNP 93ACC1791
MEP-543 Photocell kit – NPN 93ACC1728
PG6002
Single unit power supply (US) 93ACC1718
PG6001
Single unit power supply (UK) 93ACC1719
PG6000 Single unit power supply (EU) 93ACC1720
PWR-120
J-box power unit 110/230 VAC 24 V 120 W
93ACC1530
PWR-240
J-box power unit 110/230 VAC 24 V 240 W
93ACC1070
PWR-480
J-box power unit 110/230 VAC 24 V 480 W
93ACC1080
OEK-2
Optical encoder (10 m cable + spring)
93ACC1770
OEK-1
Optical encoder kit + 10 m
93ACC1600
4
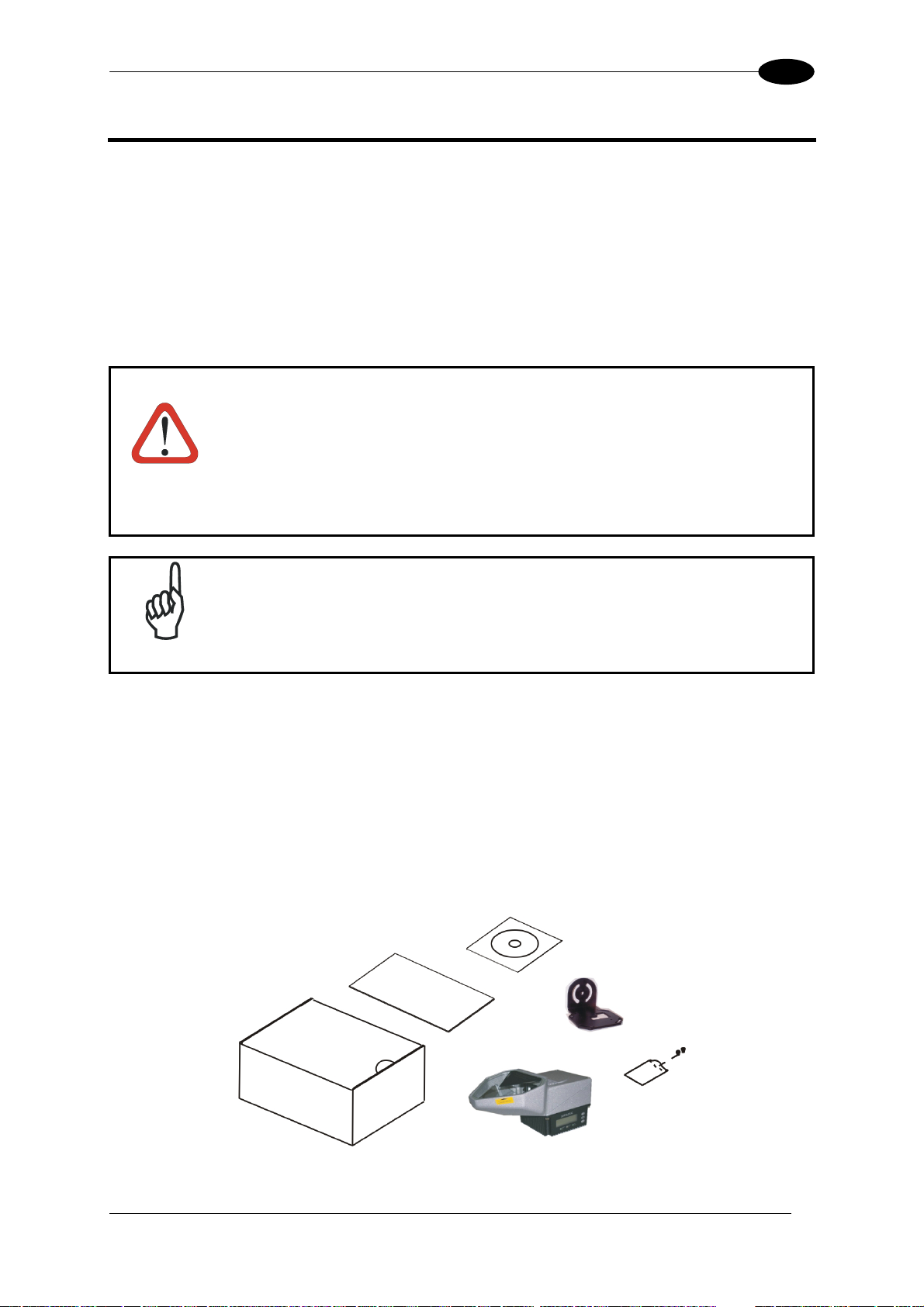
INSTALLATION
2
2 INSTALLATION
To install the system follow the given procedure:
1. Select the mounting location for DX6400;
2. Mount the DX6400 scanner;
3. Position the scanner with respect to the barcode;
4. Proceed with system electrical connection;
5. Install the Genius™ program on the PC and configure the scanner;
6. Set the Flash™ dynamic focus by means of the Genius™ software tool.
WARNING
When installing several scanners, take care to position them correctly so that
no laser beam enters the reading window perpendicularly and at the same
level of the output beam of the other scanners. This condition could occur
more frequently for side mounted applications. If these precautions are not
followed, it may occur that the laser of the blinded scanner starts blinking due
to an internal circuit which temporarily turns the laser off when detecting a
power anomaly. To resolve this problem, it is sufficient to slightly change the
inclination and position of one of the two scanners involved.
NOTE
Refer to the Reference Documentation for details on connecting your
DX6400 reader to other devices in the system (i.e. C-BOX 100 etc.).
2.1 PACKAGE CONTENTS
Verify that the DX6400 reader and all the parts supplied with the equipment are present and
intact when opening the packaging; the list of parts includes:
• DX6400 reader
• Installation Quick Reference + barcode test chart
• DX6400 configuration CD-ROM
• Mounting bracket and screws
Figure 1 – DX6400 Package Contents
5
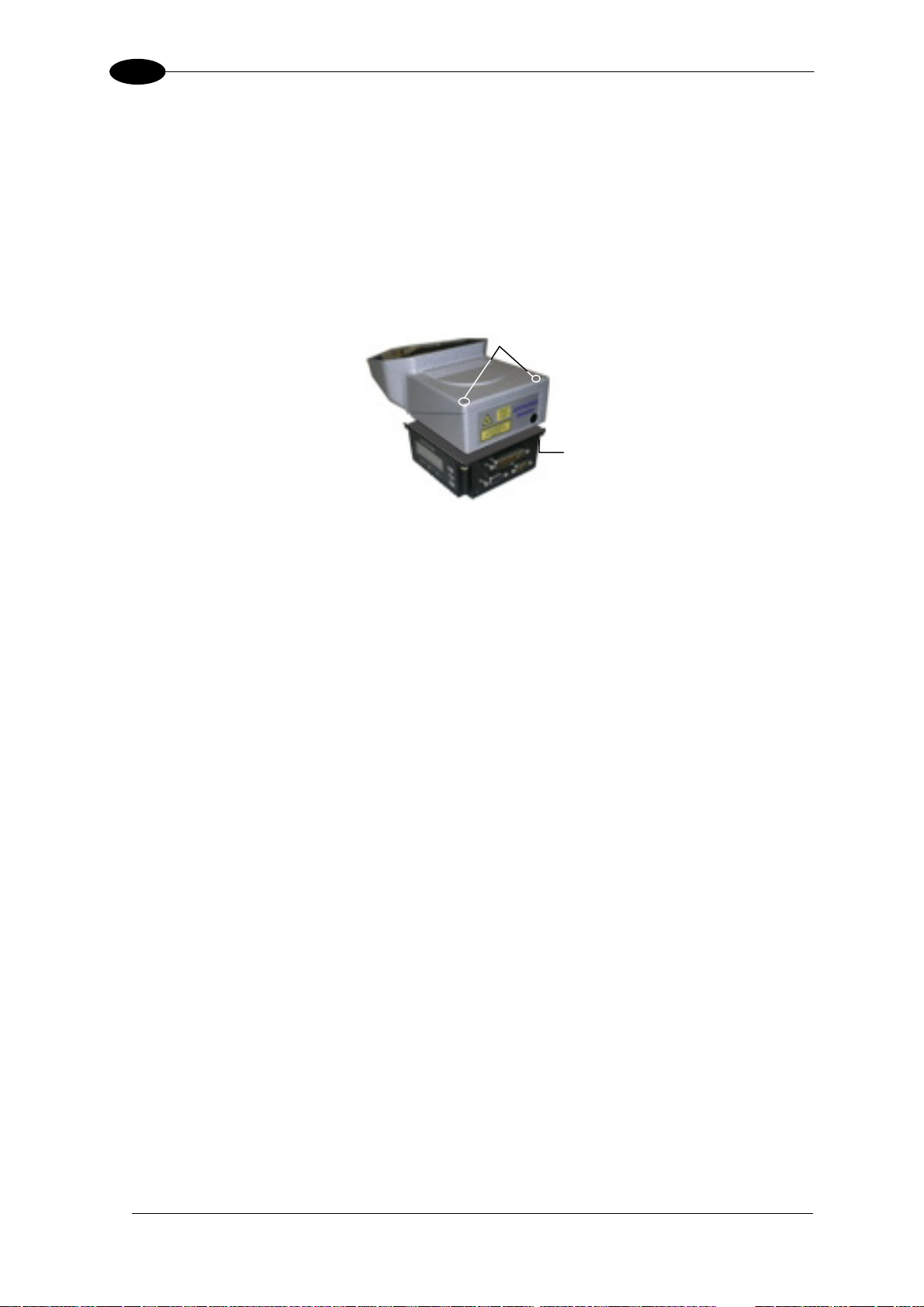
DX6400
2
2.2 MECHANICAL MOUNTING
2.2.1 Mounting the Scanner
The DX6400 reader can be positioned and installed in the best way possible as a result of
the Step-a-Head™ feature. Thanks to the separation between Head and Base, you can
modify the orientation of the decoder base, and therefore display-keypad and connector
panels, while keeping the optic head in the correct reading position. The reading head and
the decoder base can be rotated independently from each other allowing the installation even
in the most critical locations.
Head Screws
Fixing S
(4)
cre
Figure 2 - Step-A-Head™ Feature
To rotate the head follow the given procedure:
1. detach the head from the base by unscrewing the four fixing screws;
2. rotate the head in the desired position;
3. loosen but don't remove the two screws on top of the head;
4. affix the head onto the base carefully aligning the four fixing screws and progressively
tightening them about half-way;
5. completely tighten the two screws on top of the head;
6. completely tighten the four fixing screws.
6
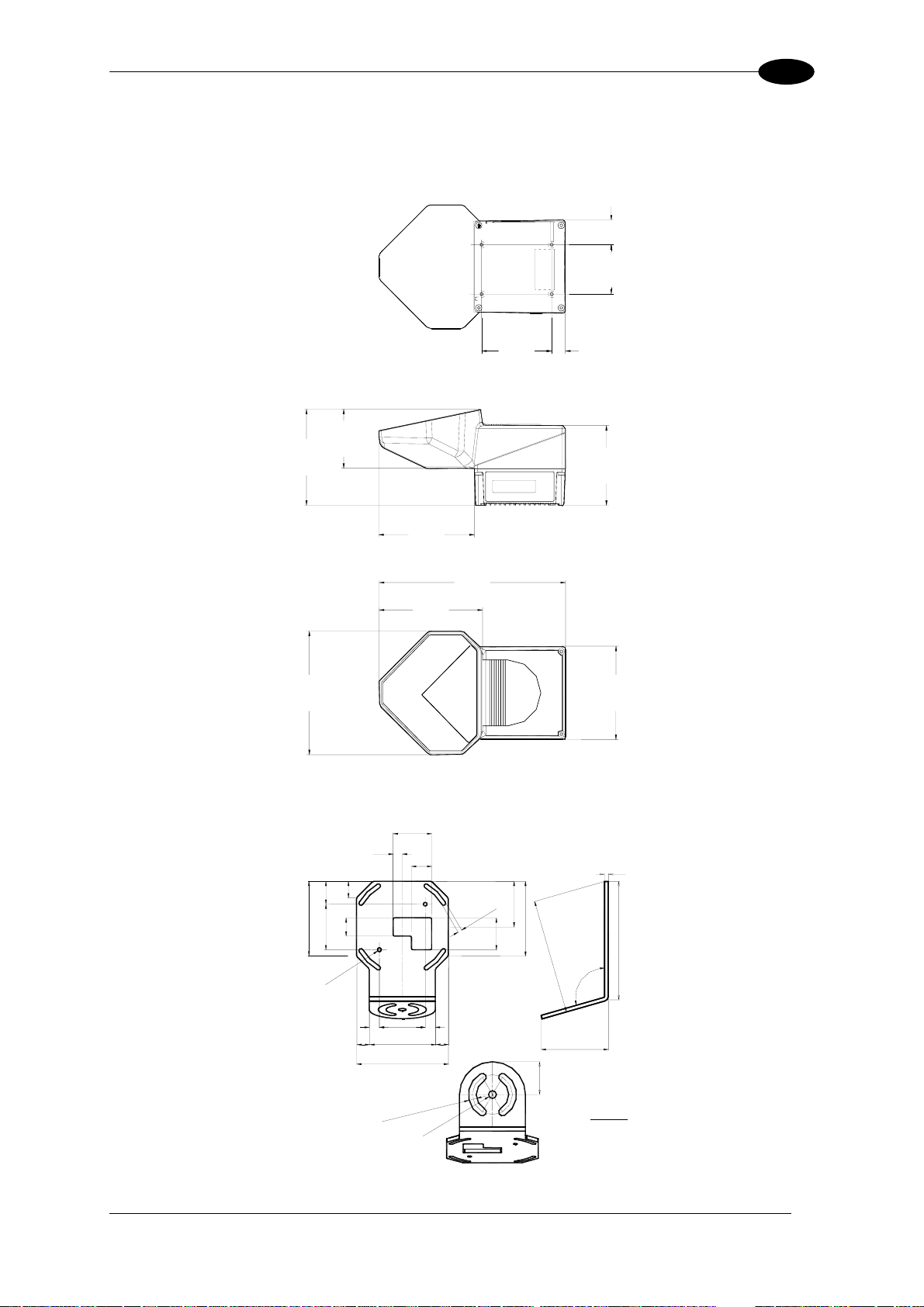
INSTALLATION
2
The following diagrams give the overall dimensions of the reader and mounting brackets.
They may be used for their installation.
85
[3.35]
60
[2.36]
16.5
[0.65]
29.9
[1.18]
116.8
[4.60]
71.8
[2.83]
115.9
[4.56]
96.9
[3.82]
225.9
[8.89]
149.8
[5.90]
125.3
[4.93]
113.1
[4.45]
Figure 3 - DX6400 Overall Dimensions
==
==
82
3.22
20
0.78
50
1.96
18
0.71 N°2
25
0.98
10
0.4
22
0.86
42
1.65
Ø
4
.
1
N
°
2
Ø
0
.
1
6
N
°
2
4
.
5
N
°
4
S
L
O
T
S
0
.
1
8
N
°
4
S
L
O
T
S
82
3.22
50
1.96
35
1.37
50
1.96
72
2.83
100
3.93
4
0.1
130
5.12
1
2
6
4
.
9
6
106°
73.2
2.88
36
1.41
8
.
5
N
°
2
S
L
O
T
S
0
.
3
3
N
°
2
S
L
O
T
S
Ø
8
.
5
Ø
0
.
3
3
mm
inch
Figure 4 – ST-237 Mounting Bracket Overall Dimensions
7
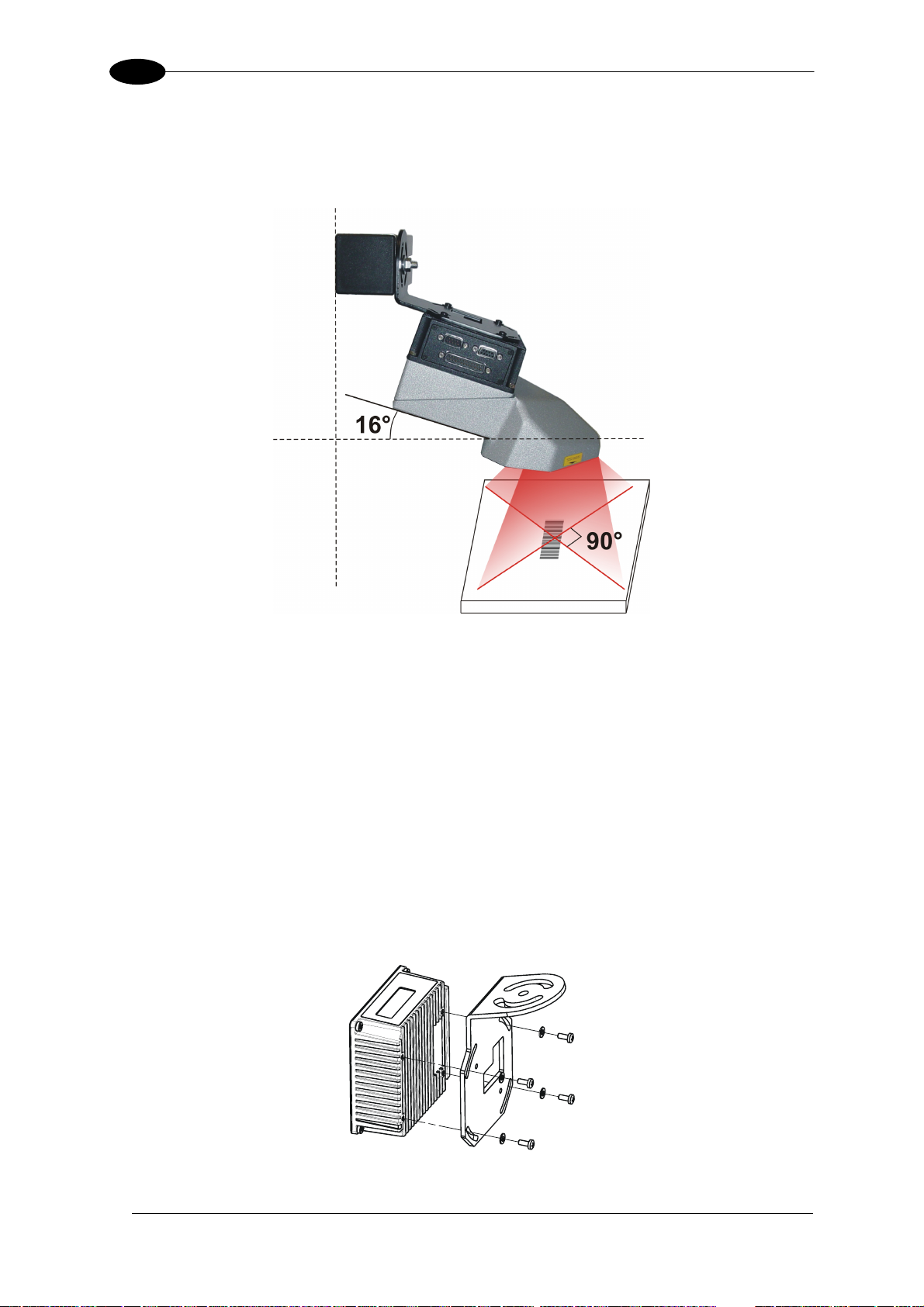
DX6400
2
Mount the scanner using the ST-237 mounting bracket which assures an angle of 16°, as
indicated in the figure below, in order to obtain an angle of 90° between the two scan lines.
This guarantees an omni directional reading of the barcode, if the code label satisfies the
ACR™ 4 conditions (see par. 4.4 for details).
Figure 5 – Mounting Position
Refer to par. 4.5 for correct positioning of the scanner with respect to the reading zone and
scanner orientation. See par. "Scanner Direction" for scanner direction relative to the
conveyor.
2.2.2 Mounting the Scanner with Accessories
The following accessories allow installing the DX6400 reader in the most suitable position for
your network layout:
- ST-237 mounting bracket;
- FBK-6000 fast bracket.
The ST-237 is a 106° mounting bracket to be mounted on the reader as displayed in the
image below:
Figure 6 – Mounting the ST-237 Mounting Bracket
8
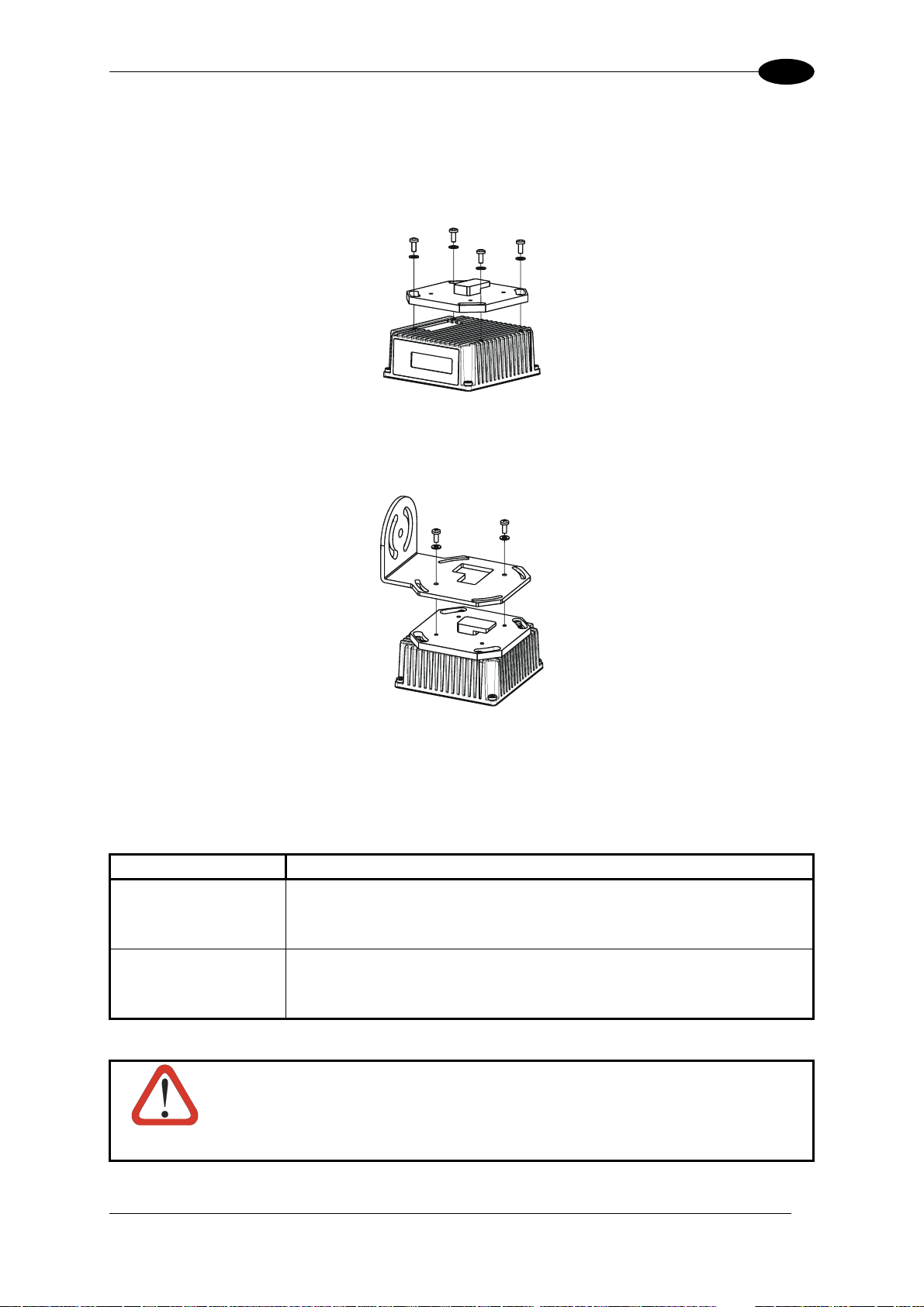
INSTALLATION
2
The FBK-6000 is a fast bracket kit allowing a quick and easy mounting of the scanner on the
ST-237 bracket.
First, it is necessary to fix the FBK-6000 to the DX6400 scanner by means of the mounting
screws:
Figure 7 – Mounting the FBK-6000 on the Scanner
Then, attach the assembly to the mounting bracket by slipping the hook into the bracket hole.
Finally, fix it by means of the 2 fixing screws:
Figure 8 – Mounting the Assembly on the Bracket
2.3 ELECTRICAL CONNECTIONS
All the connectors available for each scanner model are the following:
Scanner Model Connectors
Master/Slave 25-pin male serial interface and I/O connector
9-pin male Lonworks connector*
9-pin female Lonworks connector
Ethernet 26-pin male serial interface and I/O connector
9-pin female Lonworks connector
RJ45 modular connector
CAUTION
* Do not connect an RS232 port to the 9-pin Lonworks Connector. This may
damage your Laptop PC.
9
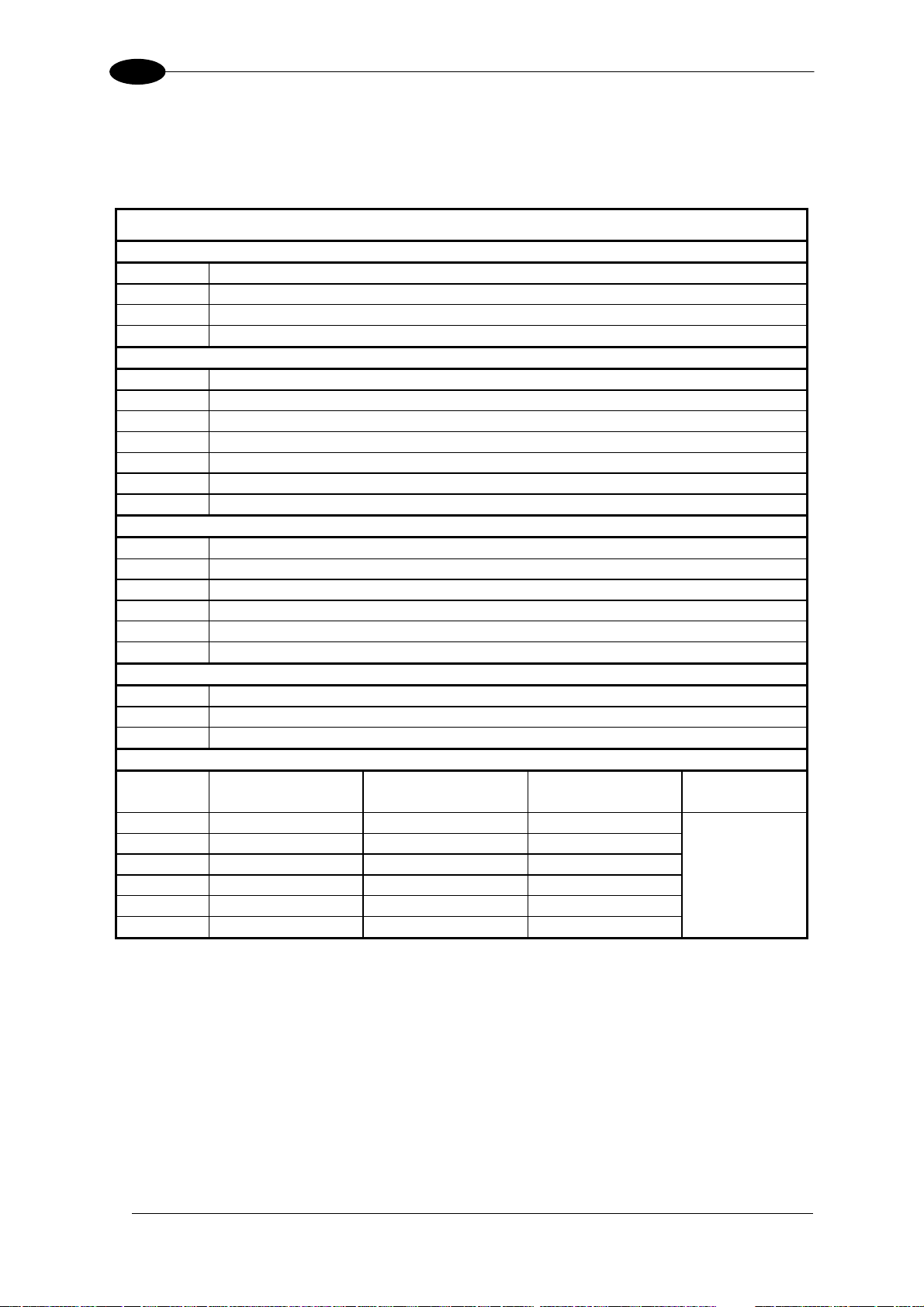
DX6400
2
The table below gives the pinout of the C-BOX 100 terminal block connectors. Use this
pinout when the DX6400 reader is connected in a network by means of the
C-BOX 100:
C-BOX 100 Terminal Block Connectors
Power
1, 3, 5 VS
2, 4, 6 GND
7, 8 EARTH GROUND
20, 40 Reserved
Inputs
27 EXT TRIG/PS A (polarity insensitive) for PS
28 EXT TRIG/PS B (polarity insensitive) for PS
29 IN 2/ENC A (polarity insensitive) for Encoder
30 IN 2/ENC B (polarity insensitive) for Encoder
31, 33 IN 3A (polarity insensitive)
32, 34 IN 4A (polarity insensitive)
36 IN 3B/IN 4B Reference (polarity insensitive)
Outputs
21 OUT 1+
22 OUT 1-
23 OUT 2+
24 OUT 2-
25 OUT 3A (polarity insensitive)
26 OUT 3B (polarity insensitive)
Auxiliary Interface
35 TX AUX
37 RX AUX
38, 39 GND
Main Interface
RS232
RS485
Full-Duplex
RS485
Half-Duplex
20 mA C.L.
(with INT-30 only)
11, 15 TX232 TX485+ RTX485+
12, 16 RTS232 TX485- RTX485-
17 RX232 * RX485+
18 CTS232 * RX485-
10, 14, 19
SGND Main Isolated SGND Main Isolated SGND Main Isolated
9, 13
RS485 Cable Shield RS485 Cable Shield
see INT-30
instructions
* Do not leave floating, see par. "RS485 Full-Duplex Interface" for connection details.
10
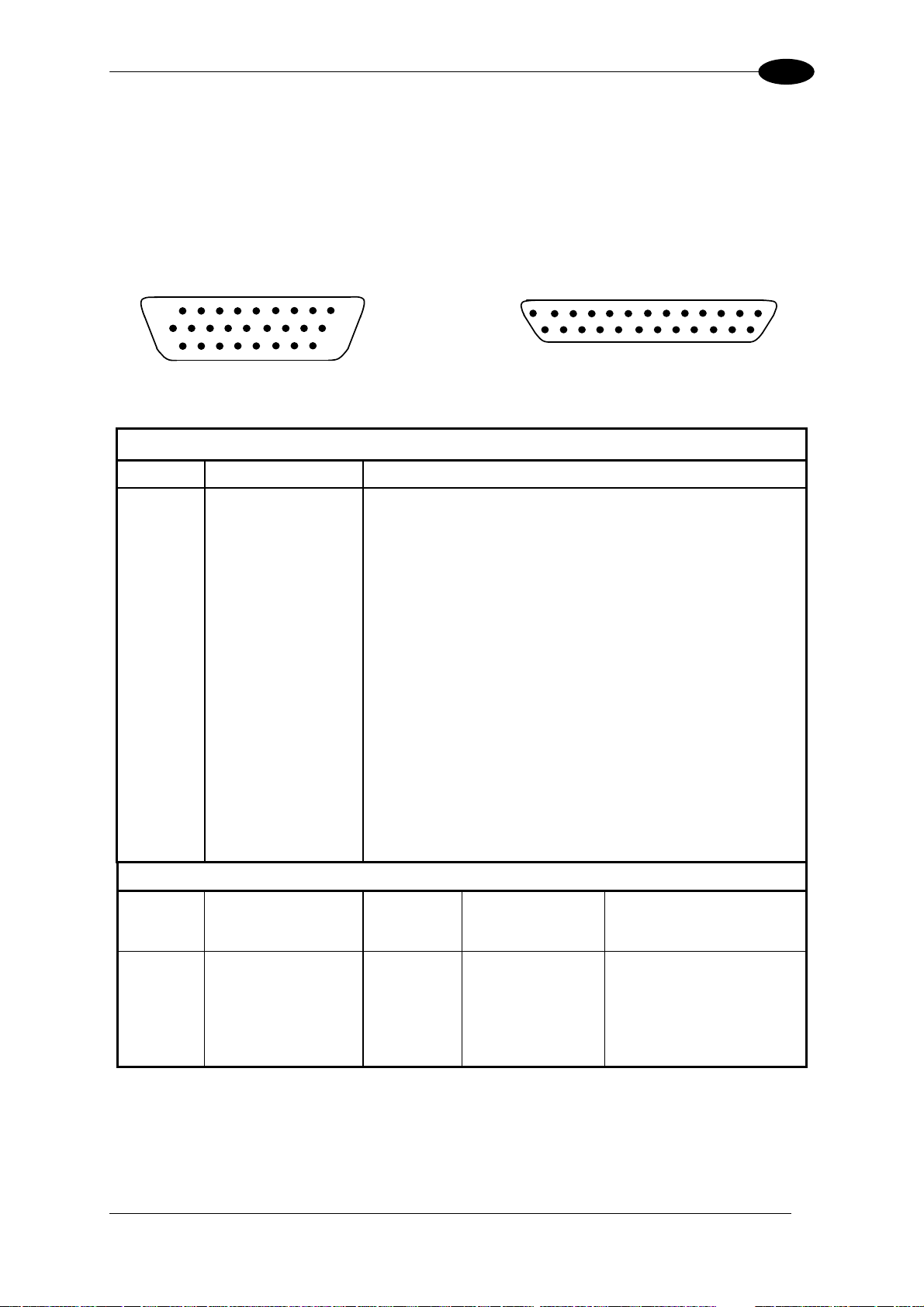
INSTALLATION
2
2.3.1 Main/Aux. Serial Interface and I/O Connector
The DX6400 master/slave model is equipped with a 25-pin male D-sub connector for
connection to the host computer, power supply and input/output signals.
The DX6400 Ethernet models adopt a 26-pin male connector instead of the 25-pin one.
The details of the connector pins are indicated in the following table:
10
19
1
18
9
26
14
1
25
13
Figure 9 - 26-pin Connector Figure 10 - 25-pin Connector
DX6400 25-pin/26-pin D-sub connector pinout
Pin Name Function
Chassis - internally connected to GND
1 CHASSIS
Cable connected to chassis
20 RXAUX Receive data of auxiliary RS232 (referred to GND)
21 TXAUX Transmit data of auxiliary RS232 (referred to GND)
8 OUT 1+ Configurable digital output 1 - positive pin
22 OUT 1- Configurable digital output 1 - negative pin
11 OUT 2+ Configurable digital output 2 - positive pin
12 OUT 2- Configurable digital output 2 - negative pin
16 OUT 3A Configurable digital output 3 - polarity insensitive
17 OUT 3B Configurable digital output 3 - polarity insensitive
18 EXT_TRIG/PS A External trigger (polarity insensitive) for PS
19 EXT_TRIG/PS B External trigger (polarity insensitive) for PS
6 IN 2/ENC A Input signal 2 (polarity insensitive) for Encoder
10 IN 2/ENC B Input signal 2 (polarity insensitive) for Encoder
14 IN 3A Input signal 3 (polarity insensitive)
15 IN 4A Input signal 4 (polarity insensitive)
24 IN_REF Common reference of IN3 and IN4 (polarity insensitive)
9,13 VS Supply voltage - positive pin
23,25,26 GND Supply voltage - negative pin
Main Interface Connector Pinout
Pin
RS232
RS485
Full
Duplex
RS485
Half Duplex
20 mA C.L.
(INT-30 with C-BOX 100 only)
2 TX TX485 + RTX485 +
3 RX * RX485 +
4 RTS TX485 - RTX485 -
5 CTS * RX485 -
7 GND_ISO GND_ISO GND_ISO
see INT-30 instructions
Pin 26 is only available for Ethernet models.
* Do not leave floating, see par. "RS485 Full-Duplex Interface" for connection details.
11
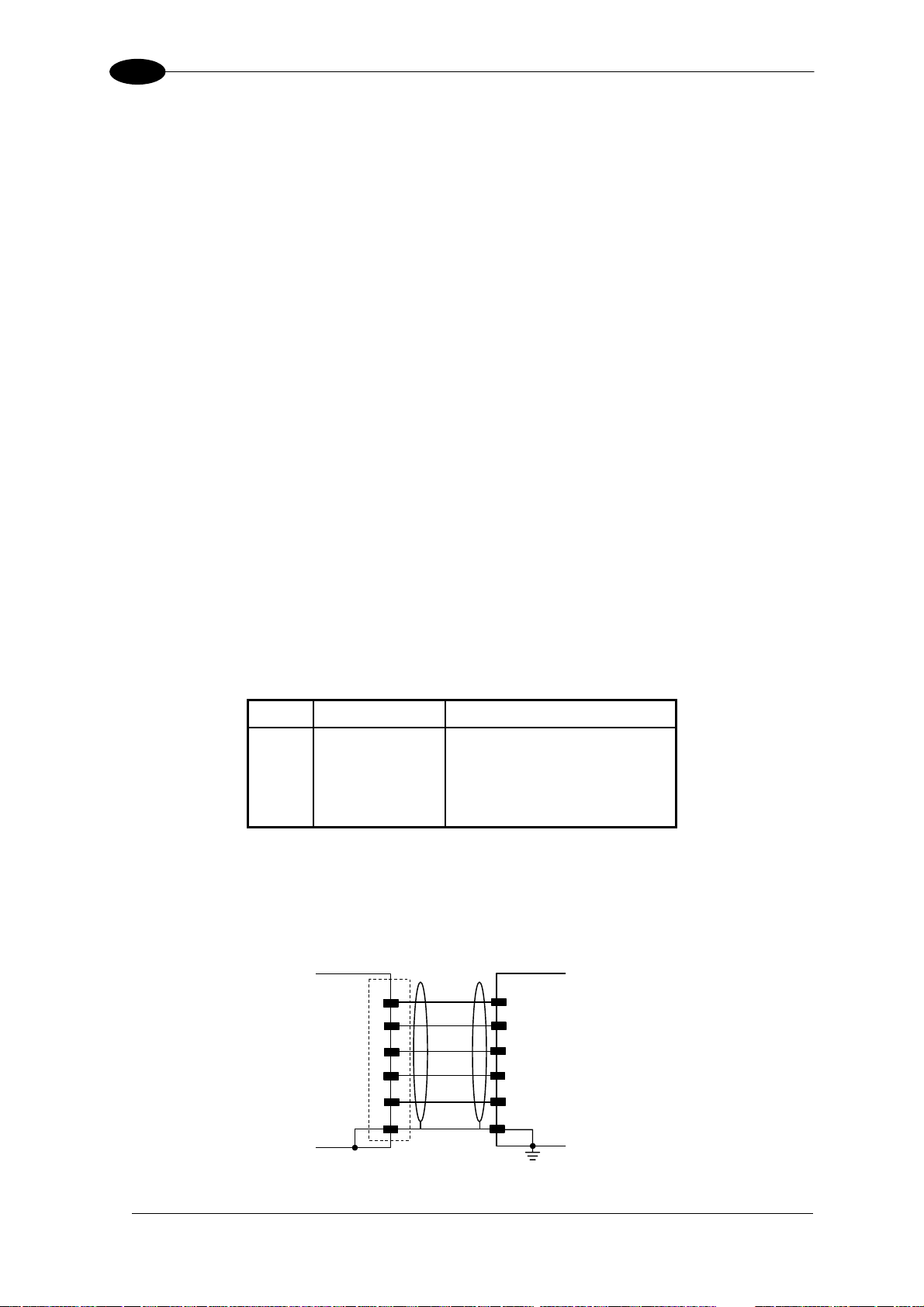
DX6400
2
Main Interface
The main serial interface is compatible with the following electrical standards:
RS232
RS485 full-duplex
RS485 half-duplex
(20 mA current loop)
The 20 mA Current Loop interface is available by using the C-BOX 100 with the optional
INT-30 accessory installed in it. The scanner communicates to the C-BOX 100 through the
RS232 interface and the INT-30 converts the signals.
The main serial interface type and its relative parameters (baud rate, data bits, etc.) are
selected via software using the Genius™ utility program. For more details refer to the
section "Main Serial Port" in the Genius™ Help On Line.
Details regarding the connections and use of the main interface selection are given in the
next paragraphs.
RS232 Interface
The main serial interface is used for communication with the Host computer and allows both
transmission of code data and configuring the reader. The overall maximum cable length
should not exceed 15 m (50 ft).
The following pins of the 25-pin and 26-pin connector are used for RS232 interface
connection depending on the reader model:
Pin Name Function
2 TX Transmit
3 RX Receive
4 RTS Request to send
5 CTS Clear to send
7 GND_ISO Main signal ground
The RTS and CTS signals control data transmission and synchronize the connected devices.
If the RTS/CTS hardware protocol is enabled, the DX6400 activates the RTS output to
indicate a message can be transmitted. The receiving unit must activate the CTS input to
enable the transmission.
DX6400
7
GND_ISO
SGND Main Isolated
USER INTERFACE
RTS
4
CTS
5
RX
3
RXD
TX
2
TXD
1
Earth
Ground
CHASSIS
Figure 11 - RS232 Connections
12
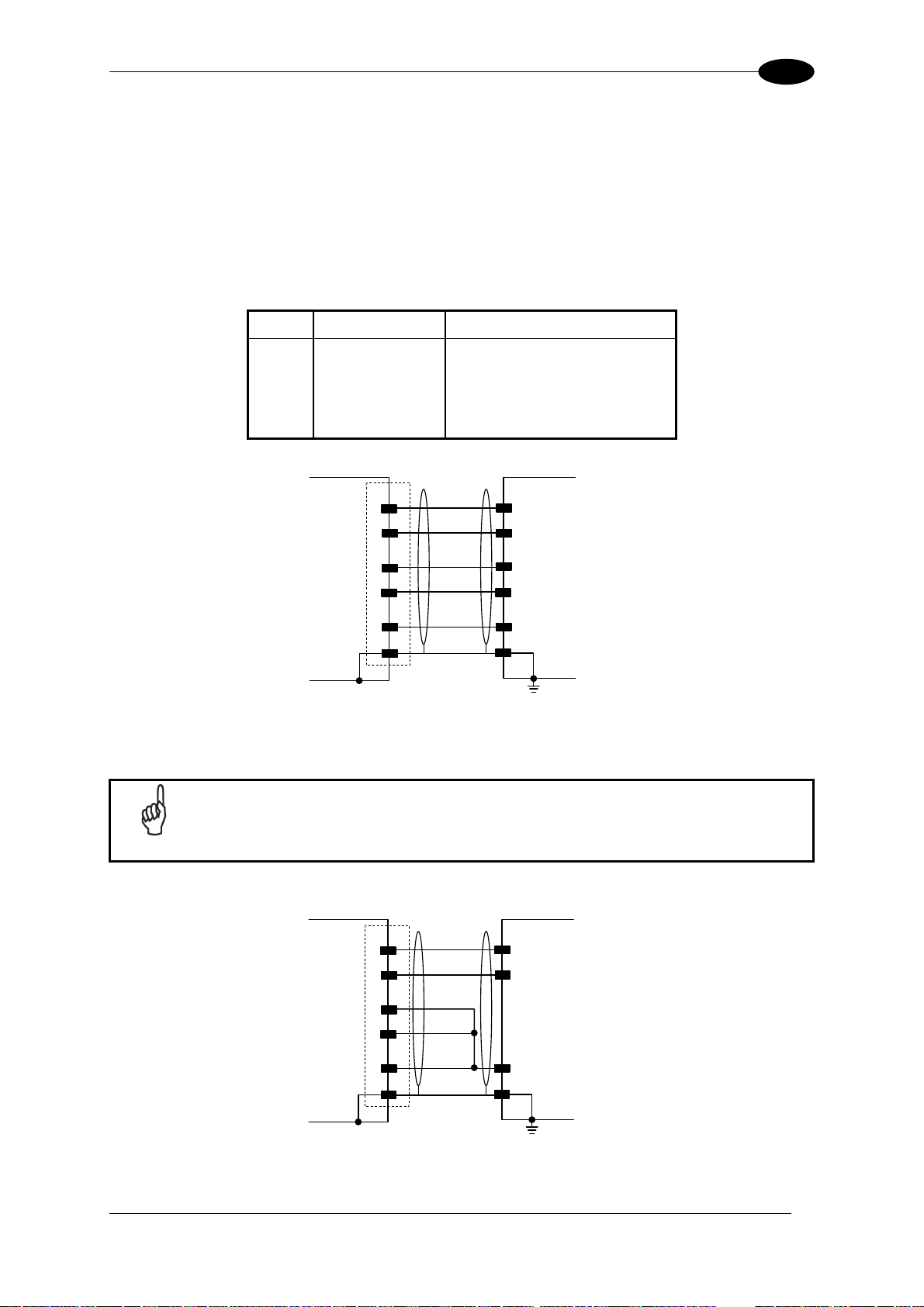
INSTALLATION
2
RS485 Full-Duplex Interface
The RS485 full-duplex interface is used for non-polled communication protocols in
point-to-point connections over longer distances than those acceptable for RS232
communications or in electrically noisy environments. The overall maximum cable length
should not exceed 1200 m (3937 ft).
The following pins of the 25-pin and 26-pin connector are used for RS485 full-duplex
interface connection:
Pin Name Function
2 TX485 + RS485 output (+)
3 RX485 + RS485 input (+)
4 TX485 - RS485 output (-)
5 RX485 - RS485 input (-)
7 GND_ISO Main signal ground
DX6400
7
GND_ISO
TX485+
2
RX485+
3
TX485-
4
RX485-
5
TX485+
TX485-
SGND Main Isolate
USER INTERFACE
RX485-
RX485+
1
Earth
Ground
CHASSIS
Figure 12 - RS485 Full-Duplex Interface Connections
NOTE
For applications that do not use RX485 signals, do not leave these lines
floating but connect them to GND_ISO as shown below.
DX6400
7
GND_ISO
TX485+
2
TX485-
4
RX485+
3
RX485-
5
SGND Main Isolated
USER INTERFACE
RX485-
RX485+
1
Earth
Ground
CHASSIS
Figure 13 - RS485 Full-Duplex Interface Connections Using Only TX Signals
13
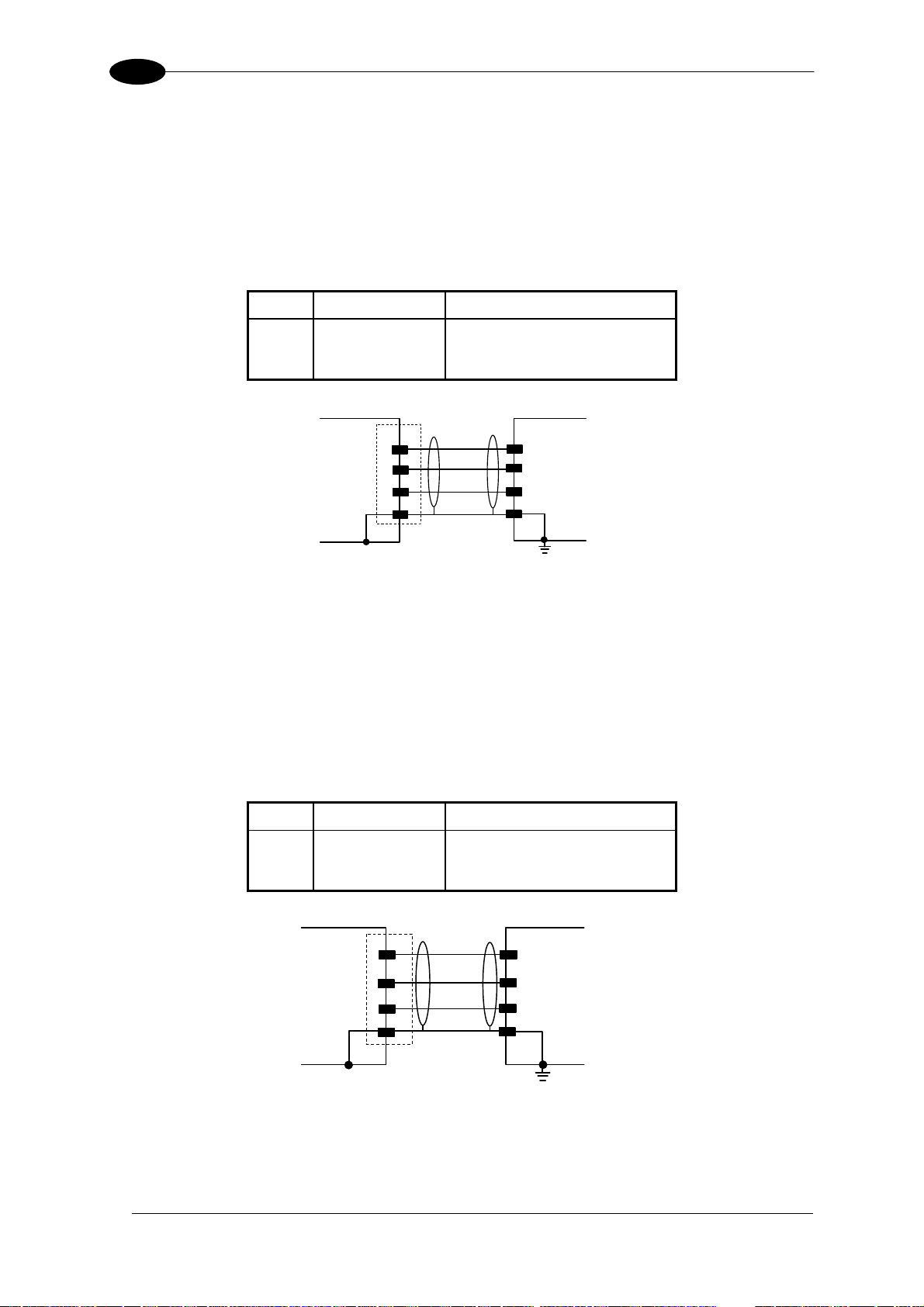
DX6400
2
RS485 Half-Duplex Interface
The RS485 half-duplex interface can be used for multidrop connections with a Datalogic
multiplexer or it can also be used for a master/slave layout. The overall maximum cable
length should not exceed 1200 m (3937 ft).
The following pins of the 25-pin and 26-pin connector are used for RS485 half-duplex
interface connection:
Pin Name Function
2 RTX485 + RS485 input/output (+)
4 RTX485 - RS485 input/output (-)
7 GND_ISO Main signal ground
DX6400
7
GND_ISO
RTX485+
2
RTX485-
4
RS485REF
MULTIPLEXER
RTX485-
RTX485+
1
Earth
Ground
CHASSIS
Figure 14 – RS485 Half-Duplex Interface Connections
Auxiliary Interface
The auxiliary serial interface is equipped with RS232 full-duplex interface connections. The
interface type is exclusive and is selectable through the Genius™ configuration program. The
overall maximum cable length should not exceed 15 m (50 ft).
The following pins of the 25-pin and 26-pin connector are used for RS232 full-duplex
interface connection:
Pin Name Function
20 RXAUX Receive data
21 TXAUX Transmit data
23 SGND AUX Auxiliary signal ground
DX6400
USER INTERFACE
23
GNDAUX
GND
TXD
RXAUX
20
RXD
TXAUX
21
1
Earth
Ground
CHASSIS
Figure 15 - RS232 Auxiliary Interface Connections
14
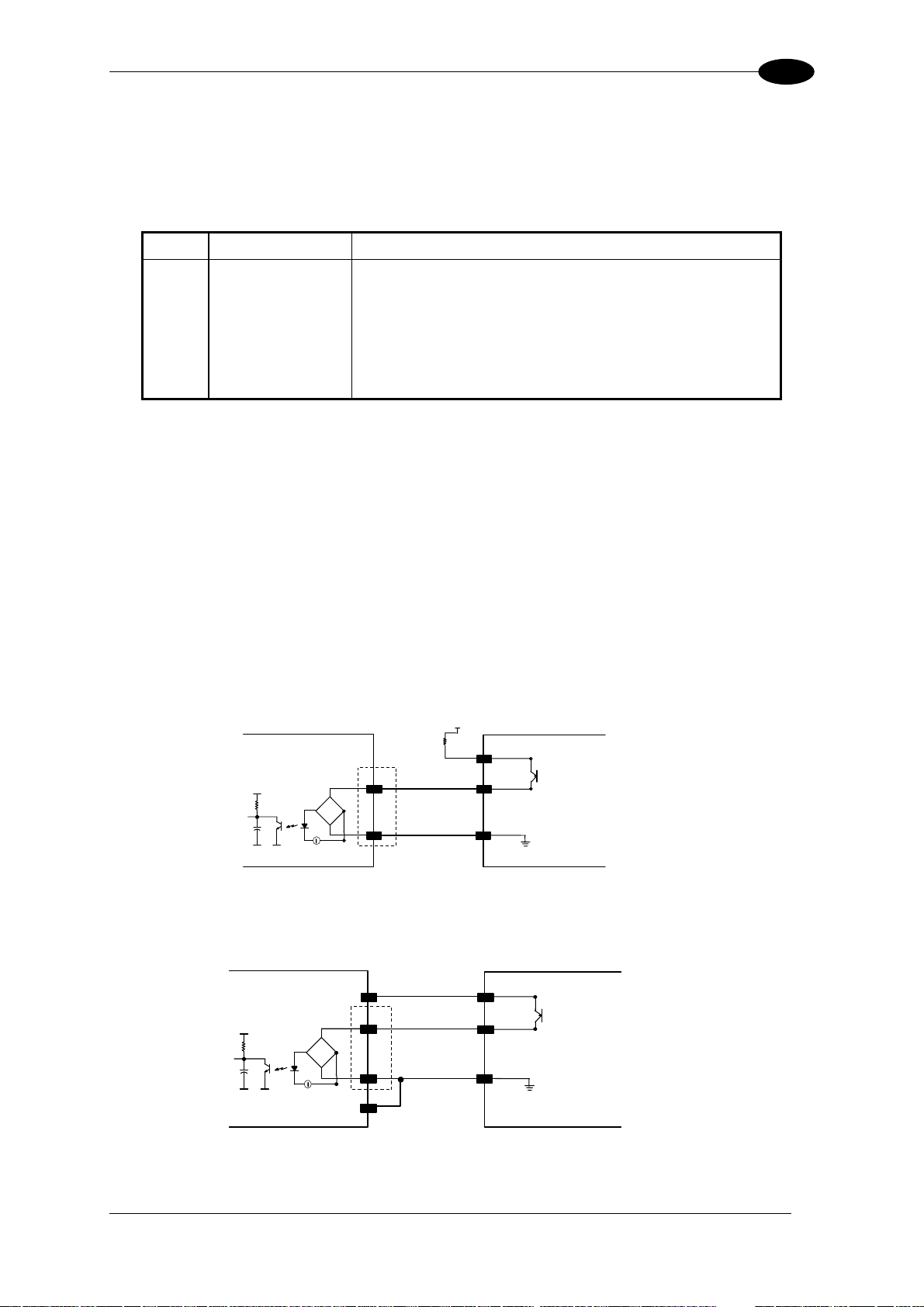
INSTALLATION
2
Inputs
The inputs of the reader are on the 25-pin and 26-pin connector of the DX6400.
These inputs are called EXT_TRIG/PS, IN2/ENC, IN3 and IN4.
Pin Name Function
18 EXT_TRIG/PS A External trigger (polarity insensitive) for PS
19 EXT_TRIG/PS B External trigger (polarity insensitive) for PS
6 IN2/ENC A Input signal 2 (polarity insensitive) for Encoder
10 IN2/ENC B Input signal 2 (polarity insensitive) for Encoder
14 IN3A Input signal 3 (polarity insensitive)
15 IN4A Input signal 4 (polarity insensitive)
24 IN_REF Common reference of IN3 and IN4 (polarity insensitive)
IN2/ENC is normally used for the Encoder input. In PackTrack™ mode, it detects the
conveyor speed. The maximum Encoder frequency is 2 KHz.
EXT_TRIG/PS is the main presence sensor. When active, this input tells the scanner to scan
for a code and that decoding can take place. The yellow LED (Figure C,3) indicates the
EXT_TRIG/PS is active.
IN3 and IN4 can be used as the stop signal for the reading phase.
All inputs are optocoupled, polarity insensitive, and driven by a constant current generator;
the command signal is filtered through an anti-disturbance circuit which generates a delay
which can be set to 5 ms or 500 µs. In particular, EXT_TRIG/PS, IN3 and IN4 share the
same value which usually corresponds to 5 ms when using a photoelectric sensor, while
IN2/ENC has a different value which is set to 500 µs when this input is used for the Encoder.
EXTERNAL TRIGGER/ENCODER
DX6400
+ 5V
A/B
Vext
B/A
V
~
~
+
-
Ground
Figure 16 – PNP Command Input Connection using External Power
EXTERNAL TRIGGER/ENCODER
DX6400
+ 5V
A/B
B/A
GND
V
~
~
+
-
VS
Ground
Figure 17 - PNP Command Input Connection using Scanner Power
15