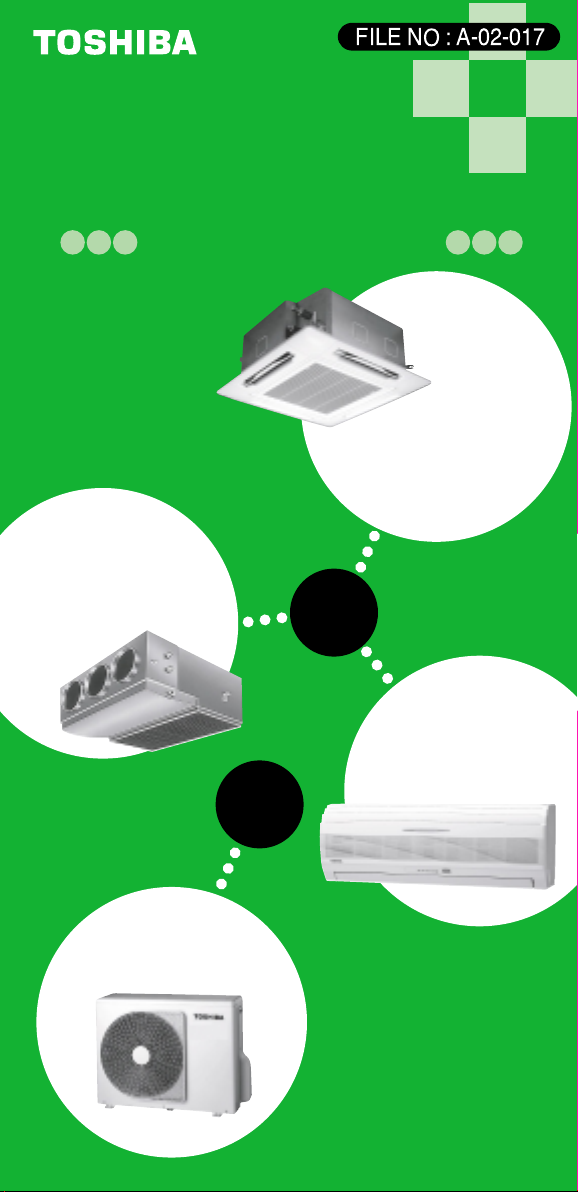
FILE NO : A-02-017
Digital Inverter
Quick reference Card
Air Discharge
Cassette Type
RAV-SM560UT-E
RAV-SM800UT-E
Concealed Duct
Type
RAV-SM560BT-E
RAV-SM800BT-E
Indoor
Units
4-Way
RAV-SM560AT-E
RAV-SM800AT-E
High-Wall Type
RAV-SM560KRT-E
RAV-SM800KRT-E
Outdoor
Units
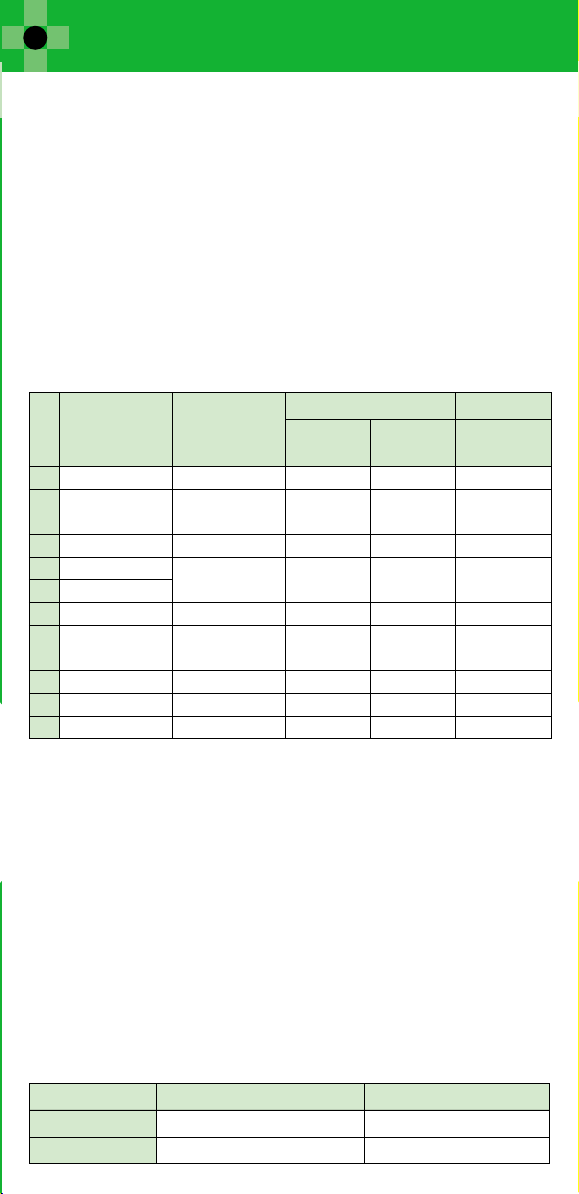
1
1 Refrigerant HFC (R410A)
This air conditioner adopts the new refrigerant HFC (R410A) which
does not damage the ozone layer.
The working pressure of the new refrigerant R410A is 1.6 times higher than
conventional refrigerant (R22).
The refrigerating oil is also changed in accordance with change of refrigerant, so
be careful that water, dust, and existing refrigerant or refrigerating oil are not
entered in the refrigerant cycle of the air conditioner using the new refrigerant
during installation work or servicing time.
1. Required Tools
The service port diameter of packed valve of the outdoor unit in the air
conditioner using R410A is changed to prevent mixing of other refrigerant. To
reinforce the pressure-resisting strength, flare processing dimensions and
opposite side dimension of flare nut of the refrigerant piping are lengthened.
Tools exclusive for R410A (The following tools for R410A are required.)
Tools whose specifications are changed for R410A and their interchangeability
Conventional air
conditioner
Whether new
equipment can be
used with conventional
refrigerant
*(Note 1)
R410A air conditioner
installation
No Used tool Usage
1
Flate tool
Copper pipe gauge
for adjusting
2
projection margin
Torque wrench
3
Gauge maniford
4
Charge hose
5
Vacuum pump adapter
6
Electronic balance for
7
refrigerant charging
Refrigerant cylinder
8
Leakage detector
9
Charging cylinder
10
(Note 1)
When flaring is carried out for R410A using the conventional flare tools, adjustment of
projection margin is necessary. For this adjustment, a copper pipe gauge, etc. are necessary.
(Note 2)
Charging cylinder for R410A is being currently developed.
Pipe flaring
Flaring by
conventional flare tool
Connection of flarenut
Evacuating,refrigerant
charge,run check,etc.
Vacuum evacuating
Refrigerant charge
Refrigerant charge
Gas leakage check
Refrigerant charge
Existence of
new equipment
for R410A
Yes
Yes
Yes
Yes
Yes
Yes
Yes
Yes
(Note 2)
Whether
conventional
equipment
can be used
*(Note 1)
*(Note 1)
2. Refrigerant charge
Up to 20m piape length, no need to add refrigerant.
Exceed 20m, add the specified amount of the refrigerant.
Refrigerant adding procedure
1) After vacuuming the pipe, charge the refrigerant with the valve close.
2) When the specified amount of the refrigerant cannot be charged, add the
remained refrigerant from charging port of the valve at gas side with cooling
operation.
Record the added amount of the refrigerant in the site.
(Note)
Charge the refrigerant as liquid state. Otherwise the component of the refrigerant varies and
the normal operation is disabled.
Additional charging amount
Capacity rank Additional charging amount Max. Pipe Length
56 type
80 type
20g/m
40g/m
30 m
50 m
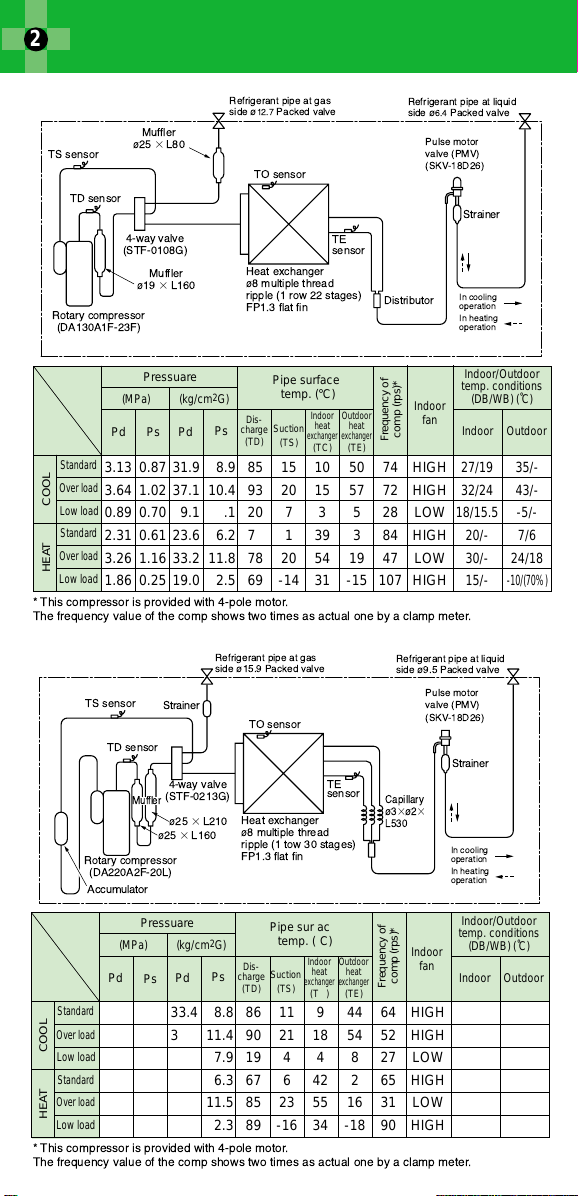
2
Systematic Diagram of Refrigerating Cycle
RAV-SM560AT-E
Muffler
¿25
4-way valve
(STF-0108G)
¿19
Pressuare
(MPa)
Pd
Ps
0.87
1.02
0.70
0.61
1.16
0.25
L80
Muffler
TS sensor
TD sensor
Rotary compressor
(DA130A1F-23F)
Standard
3.13
Over load
3.64
COOLHEAT
Low load
0.89
Standard
2.31
Over load
3.26
Low load
1.86
* This compressor is provided with 4-pole motor.
The frequency value of the comp shows two times as actual one by a clamp meter.
RAV-SM800AT-E
TS sensor
Rotary compressor
(DA220A2F-20L)
Accumulator
Standard
3.28
Over load
3.71
COOLHEAT
Low load
0.98
Standard
2.53
Over load
3.40
Low load
1.99
* This compressor is provided with 4-pole motor.
The frequency value of the comp shows two times as actual one by a clamp meter.
TD sensor
Muffler
Pressuare
(MPa)
Pd
0.86
1.12
0.77
0.62
1.13
0.23
Strainer
(STF-0213G)
¿25
Ps
4-way valve
¿25
L160
(kg/cm2G)
Ps
Pd
8.9
31.9
10.4
37.1
7.1
9.1
6.2
23.6
11.8
33.2
2.5
19.0
Refrigerant pipe at gas
side ¿15.9 Packed valve
L210
L160
(kg/cm2G)
Ps
Pd
8.8
33.4
11.4
37.8
7.9
10.0
6.3
25.8
11.5
34.7
2.3
20.3
Refrigerant pipe at gas
12.7 Packed valve
side ¿
TO sensor
Heat exchanger
¿
8 multiple thread
ripple (1 row 22 stages)
FP1.3 flat fin
Pipe surface
temp. (°C)
Dis-
charge
(TD)
85
93
20
71
78
69
TO sensor
Heat exchanger
¿
8 multiple thread
ripple (1 tow 30 stages)
FP1.3 flat fin
Dis-
charge
(TD)
86
90
19
67
85
89
Indoor
heat
Suction
exchanger
(TS)
(TC)
10
15
15
20
7
39
1
54
20
31
-14
Pipe surface
temp. (°C)
Indoor
heat
Suction
exchanger
(TS)
(TC)
9
11
18
21
4
4
42
6
55
23
34
-16
3
TE
sensor
TE
sensor
Outdoor
heat
exchanger
(TE)
50
57
5
3
19
-15
Outdoor
heat
exchanger
(TE)
44
54
8
2
16
-18
Refrigerant pipe at liquid
6.4 Packed valve
side ¿
Pulse motor
valve (PMV)
(SKV-18D26)
Distributor
Indoor
fan
comp (rps)*
Frequency of
HIGH
74
HIGH
72
LOW
28
HIGH
84
LOW
47
HIGH
107
Refrigerant pipe at liquid
side ¿9.5 Packed valve
Pulse motor
valve (PMV)
(SKV-18D26)
Capillary
¿3¿2
L530
Indoor
fan
comp (rps)*
Frequency of
HIGH
64
HIGH
52
LOW
27
HIGH
65
LOW
31
HIGH
90
Strainer
In cooling
operation
In heating
operation
Indoor/Outdoor
temp. conditions
(DB/WB) (˚C)
Outdoor
Indoor
35/-
27/19
43/-
32/24
-5/-
18/15.5
7/6
20/-
24/18
30/-
-10/(70%)
15/-
Strainer
In cooling
operation
In heating
operation
Indoor/Outdoor
temp. conditions
(DB/WB) (˚C)
Outdoor
Indoor
27/19
35/-
32/24
43/-
18/15.5
-5/-
20/-
7/6
30/-
24/18
-10/(70%)
15/-
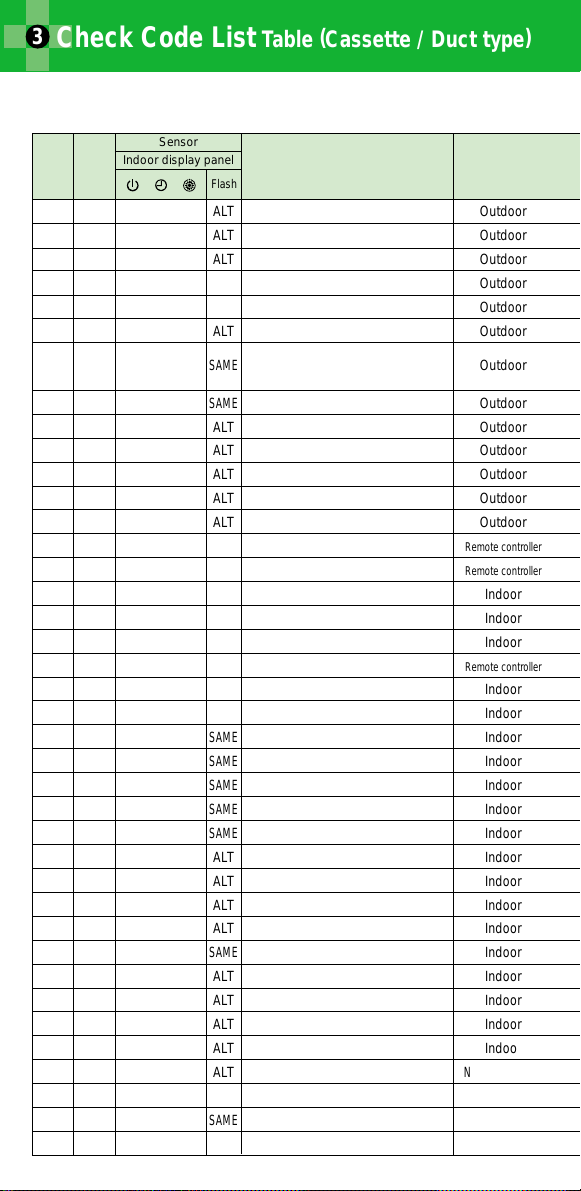
3
Check Code List Table
: Go on ◎ : Flash 䊉 : Go off
䊊
ALT : Two LED flash alternately. SAME : Two LED flash at the same time.
Check
code
(Central)
19
18
1b
1F
1d
17
1C
46
1E
21
1A
14
16
97
—
97
04
96
99
CF
97,99
96
99
99
46
b6
08
0F
0d
0C
12
11
0b
11
47
b7
97
98
99
Check
code
(Individual)
F04
F06
F08
H01
H02
H03
L29
L31
P03
P04
P22
P26
P29
E01
E02
E03
E04
E08
E09
E10
E18
L08
L07
L08
L09
L30
P19
F01
F02
F10
F29
P01
P10
P12
P31
—
—
L20
—
Sensor
Indoor display panel
Flash
◎◎
䊊
ALT
◎◎
䊊
ALT
◎◎
䊊
ALT
◎
䊉
䊉
◎
䊉
䊉
◎
䊉
䊉
◎䊊◎
◎
◎
◎
◎
◎
◎
◎
◎
◎
䊉䊉
◎
◎
◎
◎
◎
◎
◎
◎
◎
◎
◎◎
◎◎
◎◎
◎◎
䊉
䊉
䊉
◎
Up to the unit type
◎
◎
䊊
◎
䊉
◎
䊉
◎
䊉
◎
䊉
◎
䊉
䊉䊉
䊉䊉
䊉䊉
◎
䊉䊉
䊉䊉
䊉䊉
䊉䊉
◎
䊉
◎
䊉
◎
䊉
◎
䊉
◎
䊊
◎
䊉
䊉
䊉
䊉
䊉
◎◎
◎◎
◎◎
◎
䊉
—
◎
䊊
—
ALT
SAME
SAME
ALT
ALT
ALT
ALT
ALT
SAME
SAME
SAME
SAME
SAME
ALT
ALT
ALT
ALT
SAME
ALT
ALT
ALT
ALT
ALT
SAME
Outdoor, TD sensor error
Outdoor, TE, TS sensor error
Outdoor, TO sensor error
Compressor breakdown
Compressor lock
Outdoor, curr ent detection err or
Other outdoor error
Phase order error, etc
Outdoor, discharge gas temp error
Outdoor, high-pressure error
Outdoor, outdoor FM error
Outdoor, inverter ldc operation
Outdoor, position detect error
Remote controller No master or No communication
Remote controller signal sending erro
Indoor /remote controller communication error
Indoor/Outdoor serial communication error
Duplicated indoor addresses*
Duplicated master remote controllers
Communication error between CPU
Master/Sub Indoor communication error
Duplicated master indoor units*
Group wiring in individual indoor unit
Unset indoor group address
Unset indoor capacity
Abnormal input to indoor unit
4-way valve error
Indoor TCJ sensor error
Indoor TC sensor error
Indoor TA sensor error
Indoor, other indoor P.C. board error
Indoor, indoor FM error
Indoor, overflow detected
Indoor, indoor FM error
Other indoor unit error
Indoor Error among group
LAN communication error
LAN communication error
Adapter Duplicated error
*Group organization when the power supply is turned on.
(
Cassette / Duct type
Failed position Detection
r
)
Outdoor
Outdoor
Outdoor
Outdoor
Outdoor
Outdoor
Outdoor
Outdoor
Outdoor
Outdoor
Outdoor
Outdoor
Outdoor
Remote controller
Remote controller
Indoor
Indoor
Indoor
Remote controller
Indoor
Indoor
Indoor
Indoor
Indoor
Indoor
Indoor
Indoor
Indoor
Indoor
Indoor
Indoor
Indoor
Indoor
Indoor
Indoor
Network adapter
Network adapter,
central
Network adapter,
central
Network adapter
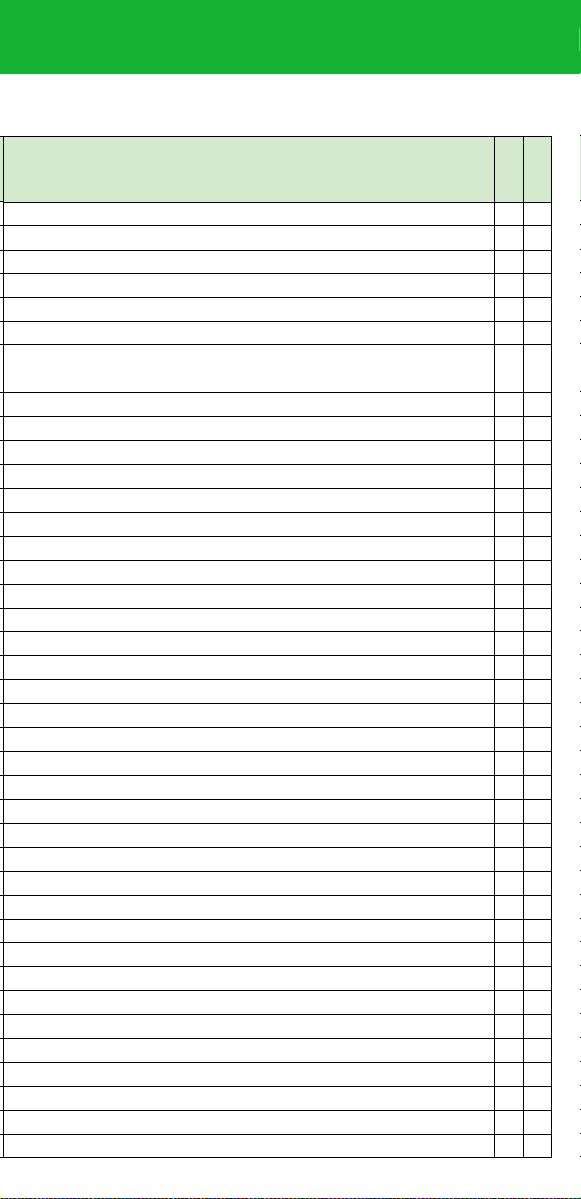
Description
Open or short of TD sensor was detected.
Open or short of TE.TS sensor was detected.
Open or short of TO sensor was detected.
After current control , short-circuit current (ldc) was detected
Locked compressor was detected.
Abnormal current in AC-CT or phase missing was detected.
Other outdoor unit error 1) MCU Communication error between IPDU and CDB.
2)
Abnormal temperature was detected in temp sensor of IGBT heat sink.
Phase order error of 3-phase power supply and others.
Abnormal TD temp. was detected.
High-pressure switch IOL worked. Abnormal TE temp was detected.
Over-current, lock, etc. was detected on drive circuit of outdoor FM.
Short-circuit protection of G-Tr, IGBT worked.
Position detection error of compressor.
No Signal from indoor (No master)
Signal could not send to indoor.
No signal from remote controller or network adapter.
Indoor/Outdoor serial communication error.
The same address with the one was detected.
Both 2 remote controller were set as master in 2 controllers. Master unit stop.
Communication error between main and motor control MCU.
No communication between Master and Sub Indoor unit in the Gr.
Multiple master units in a group.
Group wiring is connected to the individual indoor units.
Indoor address group was unset.
Indoor unit capacity was unset.
CN80 abnormal input and unit stop.
In heating temp down of indoor heat exchanger.
Open/short of TCJ sensor was detected. (TC)
Open/short of TCJ sensor was detected. (TC)
Open/short of TA sensor was detected.
EEPROM error (Other error may be detected. Otherwise AUTO address is repeated.)
Indoor AC FM error was detected. (Fan motor thermal relay worked)
Float switch worked.
Indoor DC FM error (over-current, lock, etc.) was detected.
Another indoor unit in the group alert. (E03/L07/L03/L08 alarm)
Indoor error found in the Group of central remote controller.
Communication error of the central control system. *No displayed on the remote controller.
Indoor addresses duplicated in the central control system .
Multiple adapters in the wiring of the remote controller.
Operation ON
Auto Restart
⫻
⫻
⫻
⫻
䊊
䊊
⫻
⫻
⫻
⫻
⫻
⫻
⫻
⫻
䉭
⫻
⫻
⫻
⫻
⫻
⫻
⫻
⫻
⫻
⫻
⫻
⫺
⫺
⫺
⫺
⫻
䊊
⫻
䊊
⫻
䊊
䉭
⫻
⫻
䊊
⫻
䊊
⫻
⫻
⫻
⫻
⫻
⫻
⫻
⫻
⫻
⫻
⫻
䊊
⫻
䊊
⫻
䊊
⫻
䊊
⫻
⫻
⫻
⫻
⫻
⫻
⫻
⫻
⫻
䊊
⫺
⫺
䊊
䊊
⫻
䊊
䊊
䊊
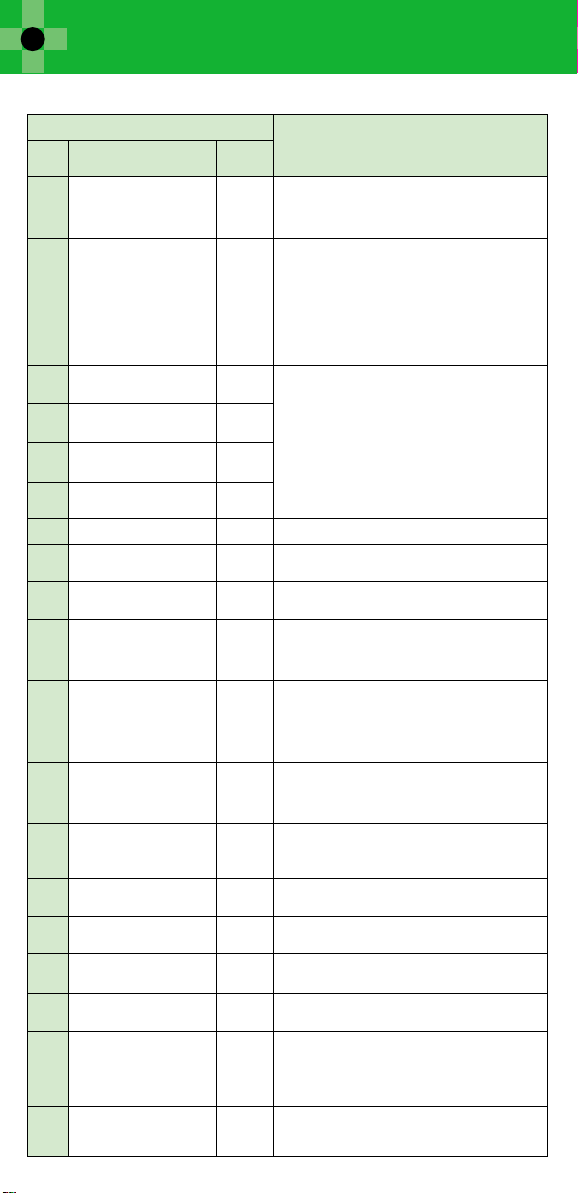
4
Check Code List : Indoor Unit Detect (Cassette/Duct Type)
Error to be detected by indoor unit
Operation of diagnostic function
Check
code
E03
E04
E08
L03
L07
L08
L09
L30
P01
P10
P12
P19
P31
F01
F02
F10
F29
E10
E18
Cause
No communication from
remote controller (including wireless ) and communication adapter.
No serial signal from
outdoor unit .
· Wrong wiring
· Serial sending circuit
error on outdoor P.C.
board
· Serial receiving circuit
error on indoor P.C.
board
Duplicated indoor unit
addresses
Duplicated master
indoor unit
Group line in individual
indoor units
Unset indoor group
address
Unset indoor capacity
Abnormal input of out-
side interlock
Fan motor thermal
protection
Float switch operation
· Disconnection/coming off of float circuit,
switch contact error
Indoor DC FM error
4-way valve failure
Alarm other indoor
unit, own unit stops.
Coming-off, disconnection
or short of TCJ sensor
Coming-off, disconnection
or short of TC sensor
Coming-off, disconnection
or short of TA sensor
Indoor EEPROM error
EEPROM access error
· Communication error
between indoor MCU
· Communication error
Between FM driving
MCU and main MCU
· Communication error
between master and
sub indoor units
Unit
status
1. Check wiring of remote controller and
All off
(Automatic
· Disconnection : controller display off
restart )
· [97] check code of central remote controller
1. Outdoor unit no operate
· wiring check, case thermo operation
· Outdoor P.C. board check
All off
2. Outdoor unit normally operate.
(Automatic
P.C. board (Indoor receiving/Outdoor sending)
restart )
1. Check connection change after power on
All off
All off
All off
All off
All off
1. Set the indoor capacity. (DN = 11)
1. Outside devices check
All off
2. Indoor P.C. board check
1. Thermal relay check of fan motor
All off
2. Indoor P.C. board check
1. Defective drain pump
2. Stagnation of drain water
All off
3. Float switch check
4. Indoor P.C. board check
1. Position detection error
2. Over-current protective circuit of indoor fan
All off
3. Indoor FM lock
4. Indoor P.C. board check
1. 4-way valve check
All off
2. TC/TCJ sensor check
(Automatic
3. Indoor P.C. board check
restart )
1. Sub units judg while master unit is in [E03],
All off
(Sub)
(Automatic
2. Indoor P.C. board check
restart )
All off
1. Check for indoor TCJ sensor
(Automatic
2. Indoor P.C. board check
restart )
1. Check for indoor TC sensor
All off
(Automatic
2. Indoor P.C. board check
restart )
All off
1. Check for indoor temp sensor (TA)
(Automatic
2. Indoor P.C. board check
restart )
All off
1.
(Automatic
restart )
All off
(Automatic
restart )
All off
(Automatic
restart )
Check Indoor EEPROM (including socket insertion)
2. Indoor P.C. board check
1. Indoor P.C. board check
1. Remote controller wiring check
2. Indoor power wiring check
3. Indoor P.C. board check
Judgment and Action
communication adapter.
check
firstly.
drive unit works.
[L03], [L07] or [L08].