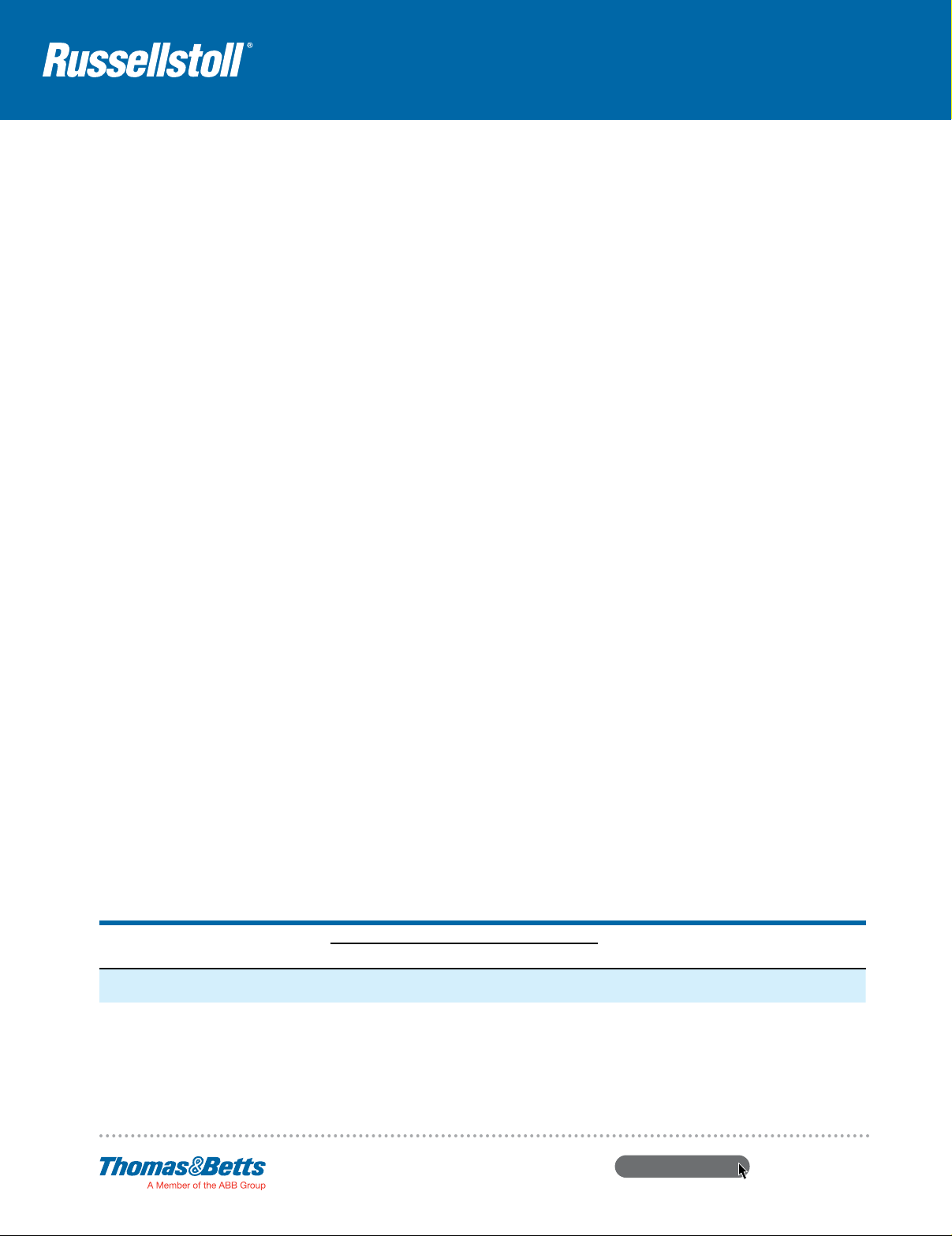
MaxGard® Interconnection Systems
Pin and Sleeve Plugs, Receptacles and Systems
1.0 Scope
1.1 This document covers multi-contact pin and sleeve, industrial grade,
1.2 The devices described shall be Thomas & Betts/Russellstoll
Pin and Sleeve Power Connectors
®
2.0 Product Classifications (Features)
2.1 Gated Deadfront — All receptacles and connectors must have a
Russellstoll
2.2 Delayed Action Arc Containment — All devices upon
2.3 Flap Cover or Screw Cover Option — Flap cover option must
2.4 Polarization — All devices shall be factory polarized for amperage,
2.5 Grounding — The grounding of the device shall be accomplished
arc-quenching, circuit interrupting-rated electrical plugs, motor
plugs, connectors, receptacles, mechanically inter locked receptacles
and assorted accessories. Usable in dry, damp, wet, marine and/or
hazardous locations for electrical power circuits. Devices are to be
rated 30, 60, 100, 200 and/or 400 amperes at 600VAC, 50–400
Hz and 250VDC maximum. Devices are also rated for continuous
use in temperatures from -40° C to +130° C. These devices must
provide internal environmental seals for marine and extreme wet
applications and can be electrically interlocked.
®
®
MaxGard
rotating disk on the face of the interior, which provides live contact
isolation and environmental separation.
disconnect under load shall have provision so the arc is contained
and extinguished within the insulation cavity, making it impossible
to withdraw a live plug.
provide weathertight capability by utilizing a spring actuated selfclosing flap. Watertight capability shall be obtained by using a
gasketed screw cap.
voltage, frequency and phase; thus providing a single voltage rating,
single interface system.
through a separate center ground (earth) make-first and break-last
pole on all devices for complete system grounding.
catalog numbers as specified.
2.6 Pole Capabilities — All devices shall accom modate up to four
power pins plus a separate center ground pin and they shall be
integral with the connector bodies (five pins total).
2.7 Interior Type — Interiors must be male (pin type) or female
(sleeve type). Pins and sleeves shall also be self-aligning and
self-wiping/self-cleaning.
2.8 Control Contacts — All devices must have an option for two
control contacts, which shall be make-last and break-first for use
in electrical interlocks and/or control circuits. See table below.
2.9 Conductor Terminals — Pin and sleeve connections shall employ
solderless pressure-type screw terminals and be sized to accept
stranded or solid copper conductors in AWG sizes (max. O.D.s as
noted). The screw terminals shall also have socket heads to ensure
proper torquing of wires.
2.10 Environmental Seals — Each device must have an environmental
seal or O-ring around all interiors and around each pin and sleeve
to prevent water and contaminants from entering the wiring
compartment. This provides waterproof capability, even when
not mated.
2.11 Hazardous Location — All standard plugs 30, 60 and 100
amp shall be UL
Division 1, Groups C and D; Class II Division 1, Groups F and G.
A hazardous location circuit breaker-pro tected interlock shall also
be applicable to the same environments and possess all the same
product features as outlined above. Enclosures shall meet NEMA 8
hazardous outdoor-duty classifications and shall meet shipboard use
above deck in accordance with the Department of Transportation
(USCG “Green Water”).
2.12 Lockout Devices — Plug connection lockout is achieved
by a padlock through plug sleeve housing hole provided for
this purpose. On Hazardous Location/Explosion Proof Interlock
Receptacles, lockout shall additionally be achieved by separate
lockout accessory available from the factory. On standard
Interlocks, lockout accessory/construction is available from
the factory.
®
and CSA listed for hazardous location Class I
38
Rating for Pilot/Control Contacts
Contact Rating Code Designation A-600, Table 119.1 — UL 508 Heavy Pilot Duty Load (720 VA/600VAC) Maximum
THERMAL
CONTINUOUS
CURRENT AMPS 120V
Make Break Make Break Make Break Make Break Make Break
10 (#12 AWG) 60 6 30 3 15 1.5 12 1.2 7200 720
United States
Tel: 901.252.8000
800.816.7809
Fax: 901.252.1354
MAXIMUM CURRENT AMPERE
Technical Services
Tel: 888.862.3289
600V MAX. VOLT AMPERE240V 480V
www.tnb.com
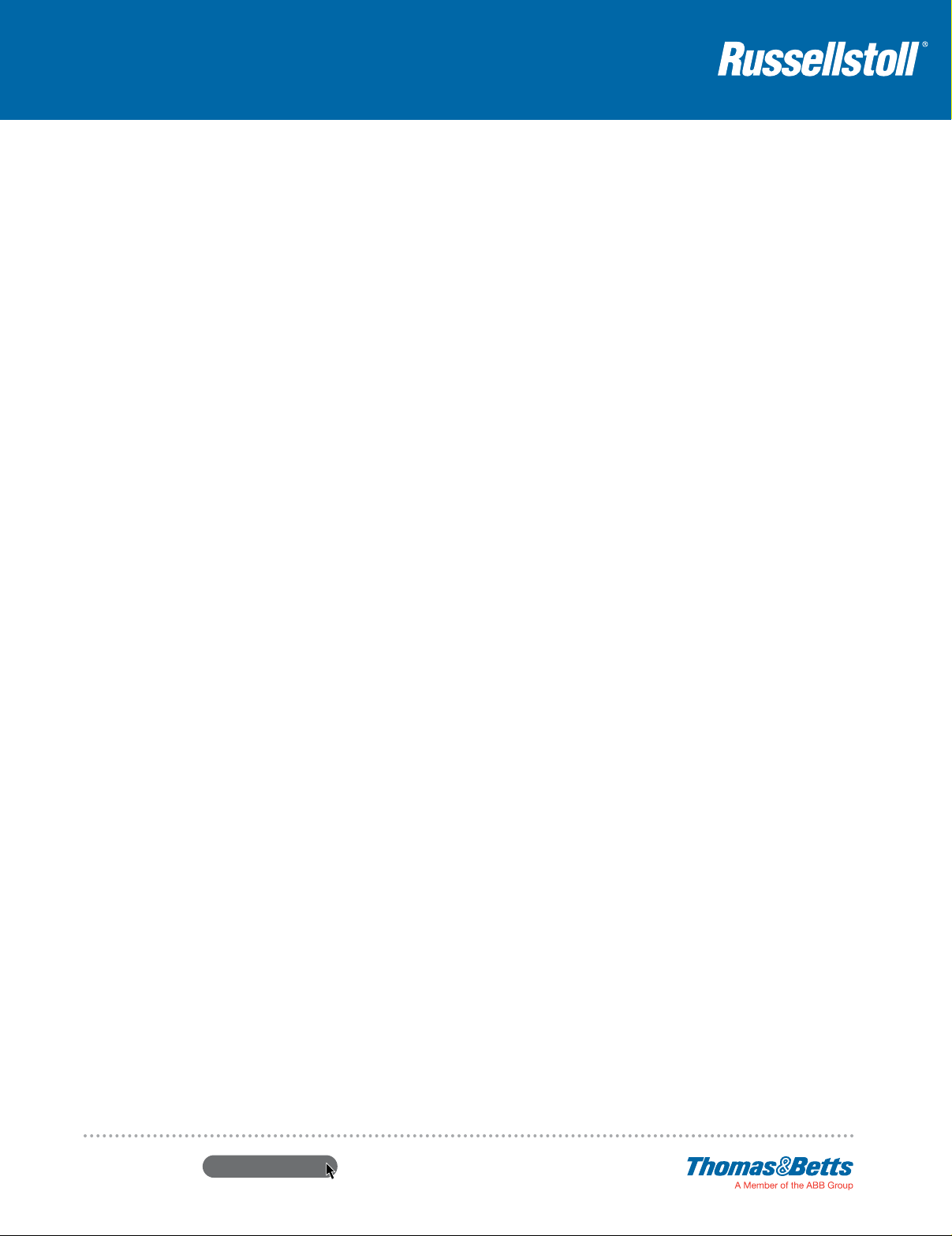
MaxGard® Interconnection Systems
3.0 Materials Requirements
3.1 Housings — Plug, motor plug,
receptacles, connectors and interlock
housings, associated covers and caps,
screw collars, and clamp holders shall
be made of copper-free cast aluminum
(max. .004% copper).
3.2 Finish — All external surfaces
except those that provide means
of grounding shall be epoxy powder
coated to resist corrosion.
3.3 Hardware — All hardware, external
and springs, shall be stainless steel.
Cable clamps shall be stainless steel
or epoxy powder coated, copper-free
cast aluminum.
3.4 Insulators — All device body insulators
shall be molded from glass-reinforced
high-strength thermoset polyester,
minimum of UL
3.5 Contacts — Contacts base material
shall be made of a conductive copper
alloy (brass CDA485) to prevent
dezincification. Accessory material
of the contacts shall be made of a
compatible corrosion resistant material.
3.6 Environmental Seals — Environmental
gaskets and O-rings shall be made of
Neoprene material.
®
94-V0 flammability rated.
4.0 Design and Construction
Requirements
4.1 Circuit Interrupting Rating — All
devices 30, 60, 100 and 200 amperes
shall be tested to be interrupted at 150%
of rated current. Additionally, all devices
shall be designed and tested to interrupt
100% of rated current.
4.2 Wiring — All devices shall be wired
from the rear requiring no disassembly
of the pins and/or sleeves from the
insulated body.
5.0 Applicable Documents (Compliances)
5.1 Underwriters Laboratories (UL) —
The devices specified herein shall be
listed in applicable sections of UL
Standards 1010, 231, 1682 and
1686, File Nos. E2630, E57324,
E68085, E123752.
5.2 Canadian Standard Association (CSA)
— The devices specified shall be listed
in the applicable sections of CSA C22.2-
182.1, File Number LR14096.
5.3 International Electro-Technical
Commission (IEC) — The 30-, 60- and
100-ampere devices specified shall have
been tested and comply with IEC 309-1.
5.4 Federal Department of Transportation
— Refrigerated National Shipboard
location devices shall meet and comply
with Federal Register volume 47, number
68, subpart 111.79.
5.5 Standards — The devices specified
shall comply with Military Standards
MIL-STD-105 and 1344; ASTM Standards
D570 and D2565: NEMA Standard
PR4-1983; and OSHA regulations when
installed in accordance with the National
Electrical Code
®
(NEC®).
5.6 NEMA 250 Enclosures
Standard
NEMA 1 — General Purpose for indoor
use; guards against contact with equipment.
NEMA 3R — Outdoor use primarily to
protect against rain, sleet, wind-blown dust
and damage from external ice formation.
NEMA 4 — Indoor or outdoor use to
protect against windblown dust and rain;
splashing and hose-directed water.
NEMA 4X — Watertight, dust-tight
corrosion-resistant for indoor or
outdoor applications.
NEMA 6 — Watertight, casual/
temporary immersion.
NEMA 7 — Class I (Hazardous) for indoor
use in Class I areas, per NEC
NEMA 8 — Class I (Hazardous) for indoor
use in Class I, oil-immersed equipment.
NEMA 9 — Class II (Hazardous) for indoor
use in Class II areas, per NEC
NEMA 12 — Industrial use, dust-tight for
indoor use to protect against dust, falling
dirt and dripping non-corrosive liquids.
NEC and National Electrical Code are
registered trademarks of the National
Fire Protection Association, Inc.
®
.
®
.
Russellstoll
®
Pin and Sleeve Power Connectors
www.tnb.com
United States
Tel: 901.252.8000
800.816.7809
Fax: 901.252.1354
Technical Services
Tel: 888.862.3289
39