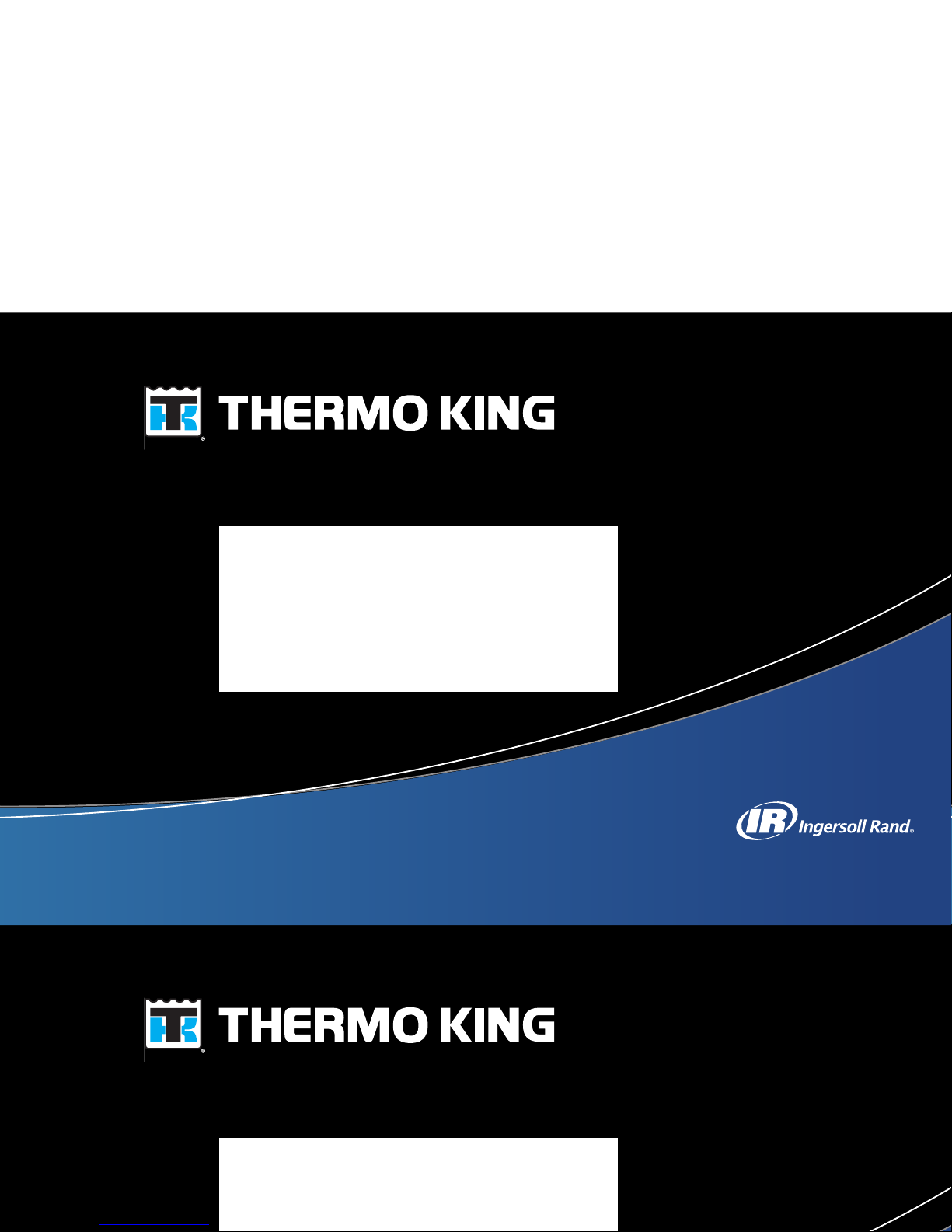
Operator’s Manual
SB-200TG
Operator’s Manual
SB-200TG
TK 53598-2-OP (Rev. 0, 02/07)
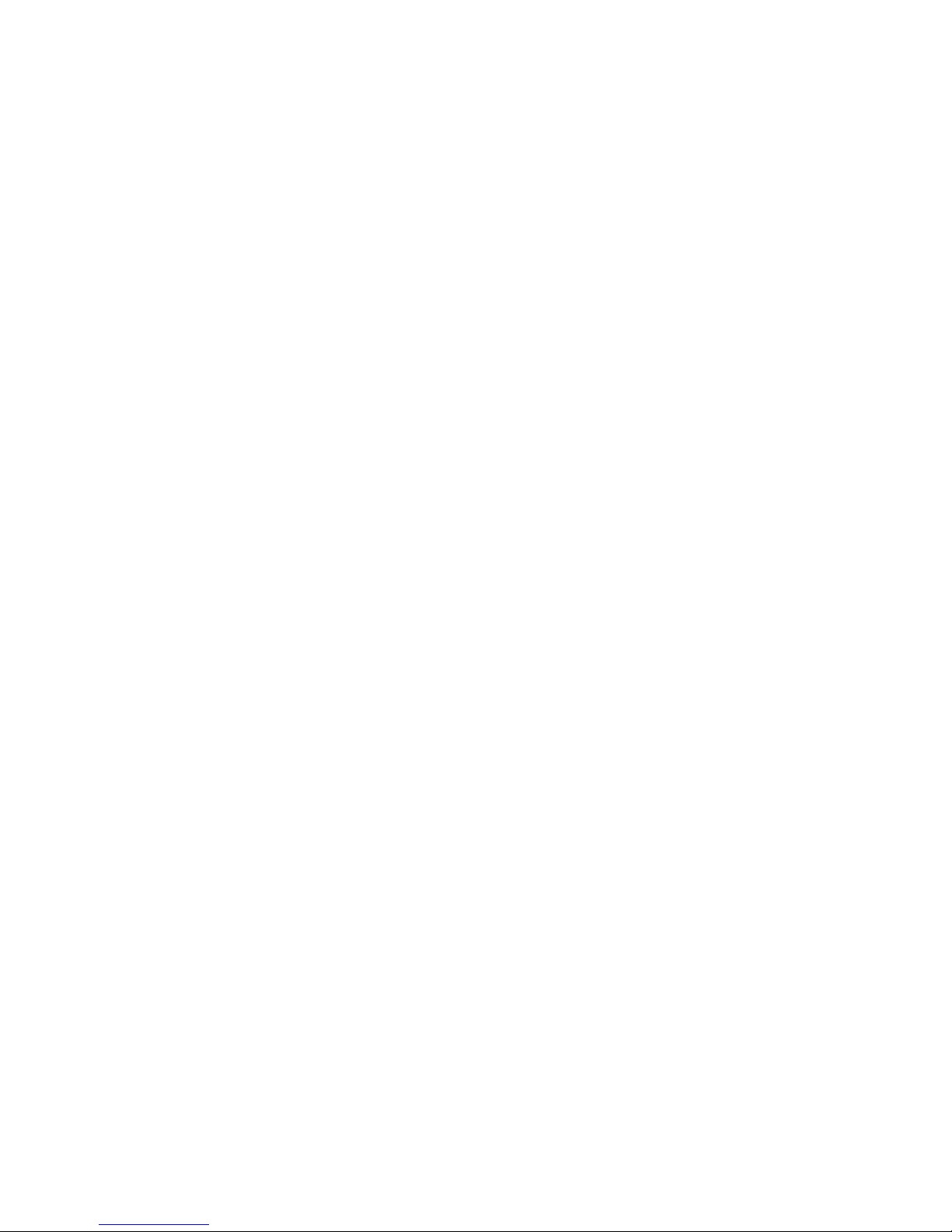
Copyright© 2007 Thermo King Corp., Minneapolis, MN, USA
Printed in USA
SB-200TG
TK 53598-2-OP (Rev. 0, 02/07)
Copyright© 2007 Thermo King Corp., Minneapolis, MN, USA
Printed in USA
SB-200TG
TK 53598-2-OP (Rev. 0, 02/07)
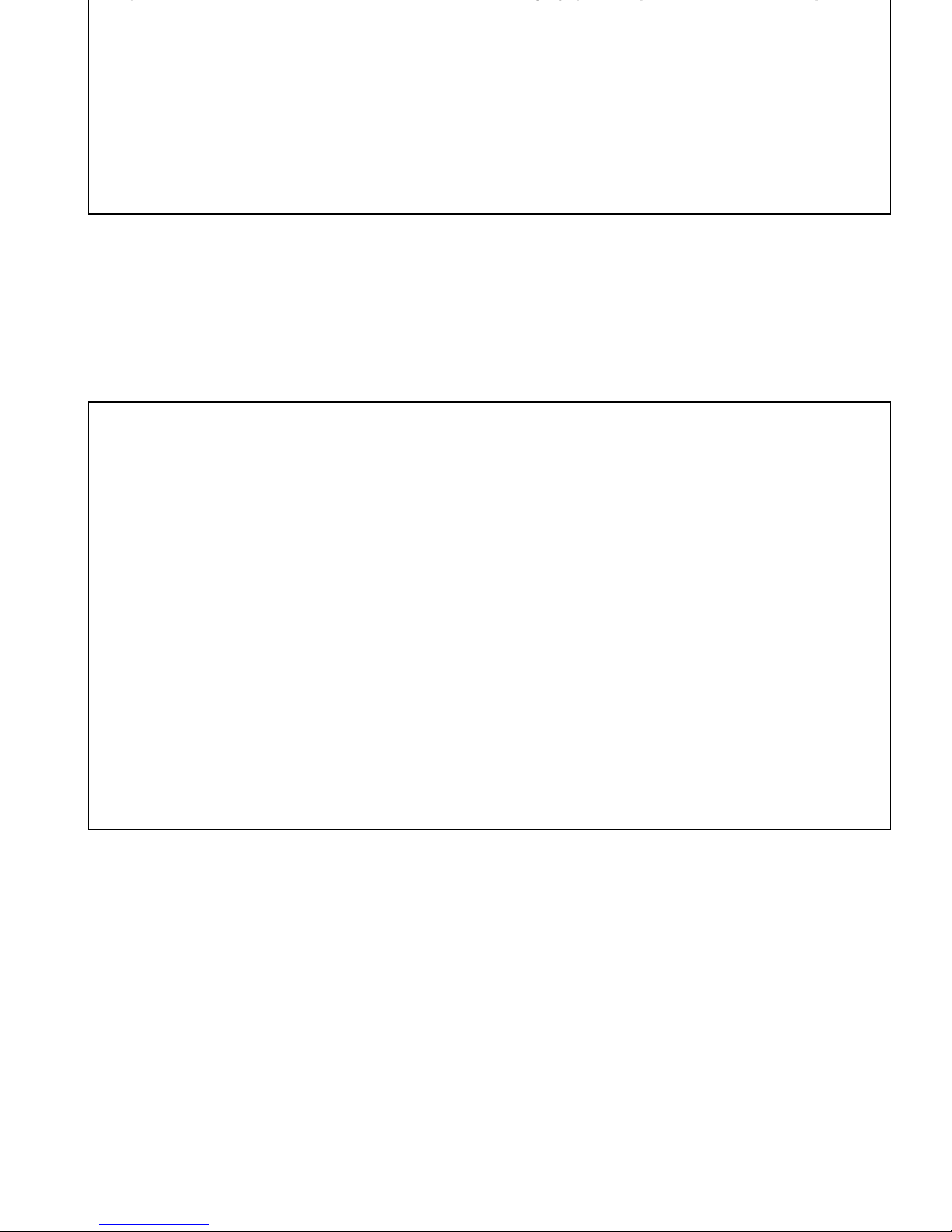
Disclaimer
This manual is published for informational purposes only. Thermo King Corporation makes no
representations or warranties, express or implied, with respect to the information, recommendations and
descriptions contained in this manual and such information, recommendations and descriptions should
not be regarded as all-inclusive or covering all contingencies. If you have questions or require further
information, please contact your local Thermo King dealer.
The procedures described herein should be undertaken only by qualified personnel. Failure to implement
these procedures correctly may cause damage to the Thermo King unit or other property or personal
injury.
Thermo King Corporation and its affiliates shall have no liability in contract or tort (including negligence
and/or strict liability) or otherwise, to any person or entity for any personal injury, property damage or any
other direct, indirect, special or consequential damage or liability whatsoever, arising out of or resulting
from any actions by any person that are contrary to this manual or any of the information,
recommendations or descriptions contained herein or the failure of any person to implement the
procedures described herein correctly or to follow caution and safety decals located on the Thermo King
unit.
Disclaimer
This manual is published for informational purposes only. Thermo King Corporation makes no
representations or warranties, express or implied, with respect to the information, recommendations and
descriptions contained in this manual and such information, recommendations and descriptions should
not be regarded as all-inclusive or covering all contingencies. If you have questions or require further
information, please contact your local Thermo King dealer.
The procedures described herein should be undertaken only by qualified personnel. Failure to implement
these procedures correctly may cause damage to the Thermo King unit or other property or personal
injury.
Thermo King Corporation and its affiliates shall have no liability in contract or tort (including negligence
and/or strict liability) or otherwise, to any person or entity for any personal injury, property damage or any
other direct, indirect, special or consequential damage or liability whatsoever, arising out of or resulting
from any actions by any person that are contrary to this manual or any of the information,
recommendations or descriptions contained herein or the failure of any person to implement the
procedures described herein correctly or to follow caution and safety decals located on the Thermo King
unit.

3
Table of Contents
List of Figures . . . . . . . . . . . . . . . . . . . . . . . . . . . . . . . 7
Introduction . . . . . . . . . . . . . . . . . . . . . . . . . . . . . . . . . 9
Safety Precautions . . . . . . . . . . . . . . . . . . . . . . . . . . 11
General Safety Practices . . . . . . . . . . . . . . . . . . . . . . 11
Automatic Start/Stop Operation . . . . . . . . . . . . . . . . . 12
Electrical Hazard . . . . . . . . . . . . . . . . . . . . . . . . . . . . . 12
Refrigerant . . . . . . . . . . . . . . . . . . . . . . . . . . . . . . . . . 12
Refrigerant Oil . . . . . . . . . . . . . . . . . . . . . . . . . . . . . . . 13
First Aid . . . . . . . . . . . . . . . . . . . . . . . . . . . . . . . . . . . . 13
First Aid–Refrigerant . . . . . . . . . . . . . . . . . . . . . . . 13
First Aid–Refrigerant Oil . . . . . . . . . . . . . . . . . . . . 13
Safety Decals And Locations . . . . . . . . . . . . . . . . . . . 14
EPA Emission Control System
Warranty Statement . . . . . . . . . . . . . . . . . . . . . . . . . .17
Responsibilities . . . . . . . . . . . . . . . . . . . . . . . . . . . . . .18
Thermo King Corporation Responsibilities . . . . . .18
Owner Responsibilities . . . . . . . . . . . . . . . . . . . . .19
Limitations . . . . . . . . . . . . . . . . . . . . . . . . . . . . . . . . . .19
Unit Description . . . . . . . . . . . . . . . . . . . . . . . . . . . . .21
Unit Overview . . . . . . . . . . . . . . . . . . . . . . . . . . . . . . . .21
Design Features . . . . . . . . . . . . . . . . . . . . . . . . . . . . . .22
Diesel Engine . . . . . . . . . . . . . . . . . . . . . . . . . . . . . . . .23
ELC (Extended Life Coolant) . . . . . . . . . . . . . . . . . . . .23
EMI 3000 . . . . . . . . . . . . . . . . . . . . . . . . . . . . . . . . . . .24
Thermo King X430L Compressor . . . . . . . . . . . . . . . .24
3
Table of Contents
List of Figures . . . . . . . . . . . . . . . . . . . . . . . . . . . . . . . 7
Introduction . . . . . . . . . . . . . . . . . . . . . . . . . . . . . . . . . 9
Safety Precautions . . . . . . . . . . . . . . . . . . . . . . . . . . 11
General Safety Practices . . . . . . . . . . . . . . . . . . . . . . 11
Automatic Start/Stop Operation . . . . . . . . . . . . . . . . . 12
Electrical Hazard . . . . . . . . . . . . . . . . . . . . . . . . . . . . . 12
Refrigerant . . . . . . . . . . . . . . . . . . . . . . . . . . . . . . . . . 12
Refrigerant Oil . . . . . . . . . . . . . . . . . . . . . . . . . . . . . . . 13
First Aid . . . . . . . . . . . . . . . . . . . . . . . . . . . . . . . . . . . . 13
First Aid–Refrigerant . . . . . . . . . . . . . . . . . . . . . . . 13
First Aid–Refrigerant Oil . . . . . . . . . . . . . . . . . . . . 13
Safety Decals And Locations . . . . . . . . . . . . . . . . . . . 14
EPA Emission Control System
Warranty Statement . . . . . . . . . . . . . . . . . . . . . . . . . .17
Responsibilities . . . . . . . . . . . . . . . . . . . . . . . . . . . . . .18
Thermo King Corporation Responsibilities . . . . . .18
Owner Responsibilities . . . . . . . . . . . . . . . . . . . . .19
Limitations . . . . . . . . . . . . . . . . . . . . . . . . . . . . . . . . . .19
Unit Description . . . . . . . . . . . . . . . . . . . . . . . . . . . . .21
Unit Overview . . . . . . . . . . . . . . . . . . . . . . . . . . . . . . . .21
Design Features . . . . . . . . . . . . . . . . . . . . . . . . . . . . . .22
Diesel Engine . . . . . . . . . . . . . . . . . . . . . . . . . . . . . . . .23
ELC (Extended Life Coolant) . . . . . . . . . . . . . . . . . . . .23
EMI 3000 . . . . . . . . . . . . . . . . . . . . . . . . . . . . . . . . . . .24
Thermo King X430L Compressor . . . . . . . . . . . . . . . .24
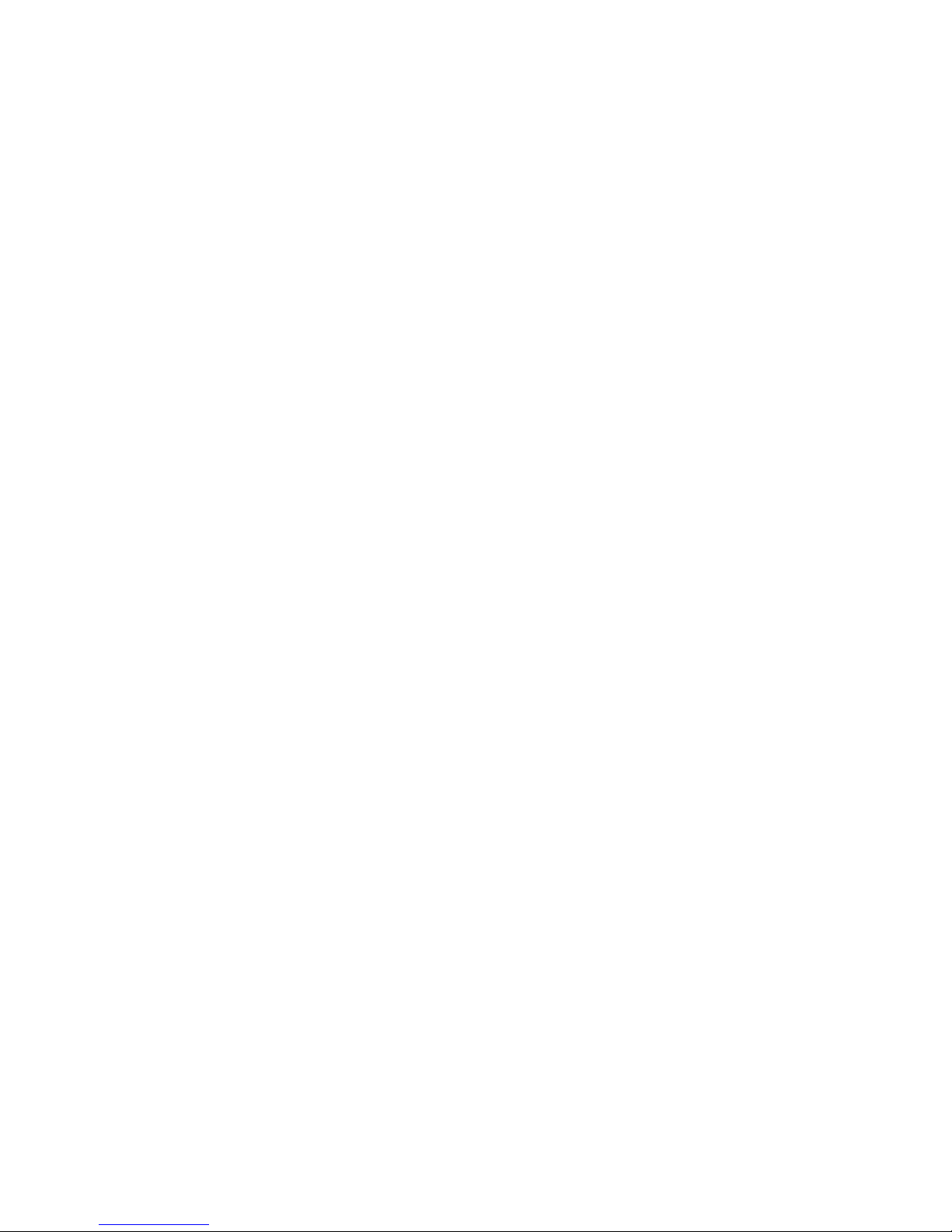
Table of Contents
4
TG-VI Microprocessor Controller . . . . . . . . . . . . . . . . .25
CYCLE-SENTRY Start-Stop Controls . . . . . . . . . . 27
Defrost . . . . . . . . . . . . . . . . . . . . . . . . . . . . . . . . . 27
DAS (Optional) . . . . . . . . . . . . . . . . . . . . . . . . . . . . . .28
Opening the Front Doors . . . . . . . . . . . . . . . . . . . . . . . 29
Opening the Secondary Door Latch . . . . . . . . . . . 29
Closing the Front Doors . . . . . . . . . . . . . . . . . . . . . . . .30
Engine Compartment Components . . . . . . . . . . . . . . . 31
Unit Protection Devices . . . . . . . . . . . . . . . . . . . . . . . .32
TG-VI Controller Description . . . . . . . . . . . . . . . . . . 35
TG-VI Overview . . . . . . . . . . . . . . . . . . . . . . . . . . . . . . 35
Display Screen . . . . . . . . . . . . . . . . . . . . . . . . . . . . . .36
Upper and Lower Display . . . . . . . . . . . . . . . . . . . 37
Display Icons . . . . . . . . . . . . . . . . . . . . . . . . . . . . . 38
Standard Display . . . . . . . . . . . . . . . . . . . . . . . . . . 39
Keypad . . . . . . . . . . . . . . . . . . . . . . . . . . . . . . . . . . . .40
Remote Status Light (Optional) . . . . . . . . . . . . . . . . 43
Manual Pretrip Inspection
(Before Starting the Unit) . . . . . . . . . . . . . . . . . . . . .45
Unit Operation with TG-VI Controller . . . . . . . . . . . 47
Control Panel . . . . . . . . . . . . . . . . . . . . . . . . . . . . . . . 48
On/Off Switch . . . . . . . . . . . . . . . . . . . . . . . . . . . . 48
Starting the Diesel Engine . . . . . . . . . . . . . . . . . . . . . 49
Starting the Unit with a Unit Self Check Test . . . . . . . 50
Displaying Operating Data During Normal Operation 52
Changing the Setpoint . . . . . . . . . . . . . . . . . . . . . . . . 53
Selection of Operating Modes . . . . . . . . . . . . . . . . . . 54
Selecting CYCLE-SENTRY or Continuous Mode . . . 55
Initiating a Manual Defrost Cycle . . . . . . . . . . . . . . . . 56
Checking Software Revision . . . . . . . . . . . . . . . . . . . 57
Printing a Trip Report . . . . . . . . . . . . . . . . . . . . . . . . . 58
Initiating a Start of Trip . . . . . . . . . . . . . . . . . . . . . . . . 60
Displaying and Clearing Alarm Codes . . . . . . . . . . . . 61
Alarm Codes . . . . . . . . . . . . . . . . . . . . . . . . . . . . . . . 63
Introduction . . . . . . . . . . . . . . . . . . . . . . . . . . . . . . . . . 63
Repair . . . . . . . . . . . . . . . . . . . . . . . . . . . . . . . . . . . . . 63
Alarm Types . . . . . . . . . . . . . . . . . . . . . . . . . . . . . . . . 64
Corrective Action . . . . . . . . . . . . . . . . . . . . . . . . . . . . 64
Alarm Code 84 (Restart Null) . . . . . . . . . . . . . . . . . . . 65
Alarm Code 85 (Forced Unit Operation) . . . . . . . . . . . 65
Table of Alarm Codes . . . . . . . . . . . . . . . . . . . . . . . . . 66
Table of Contents
4
TG-VI Microprocessor Controller . . . . . . . . . . . . . . . . .25
CYCLE-SENTRY Start-Stop Controls . . . . . . . . . . 27
Defrost . . . . . . . . . . . . . . . . . . . . . . . . . . . . . . . . . 27
DAS (Optional) . . . . . . . . . . . . . . . . . . . . . . . . . . . . . .28
Opening the Front Doors . . . . . . . . . . . . . . . . . . . . . . . 29
Opening the Secondary Door Latch . . . . . . . . . . . 29
Closing the Front Doors . . . . . . . . . . . . . . . . . . . . . . . .30
Engine Compartment Components . . . . . . . . . . . . . . . 31
Unit Protection Devices . . . . . . . . . . . . . . . . . . . . . . . .32
TG-VI Controller Description . . . . . . . . . . . . . . . . . . 35
TG-VI Overview . . . . . . . . . . . . . . . . . . . . . . . . . . . . . . 35
Display Screen . . . . . . . . . . . . . . . . . . . . . . . . . . . . . .36
Upper and Lower Display . . . . . . . . . . . . . . . . . . . 37
Display Icons . . . . . . . . . . . . . . . . . . . . . . . . . . . . . 38
Standard Display . . . . . . . . . . . . . . . . . . . . . . . . . . 39
Keypad . . . . . . . . . . . . . . . . . . . . . . . . . . . . . . . . . . . .40
Remote Status Light (Optional) . . . . . . . . . . . . . . . . 43
Manual Pretrip Inspection
(Before Starting the Unit) . . . . . . . . . . . . . . . . . . . . .45
Unit Operation with TG-VI Controller . . . . . . . . . . . 47
Control Panel . . . . . . . . . . . . . . . . . . . . . . . . . . . . . . . 48
On/Off Switch . . . . . . . . . . . . . . . . . . . . . . . . . . . . 48
Starting the Diesel Engine . . . . . . . . . . . . . . . . . . . . . 49
Starting the Unit with a Unit Self Check Test . . . . . . . 50
Displaying Operating Data During Normal Operation 52
Changing the Setpoint . . . . . . . . . . . . . . . . . . . . . . . . 53
Selection of Operating Modes . . . . . . . . . . . . . . . . . . 54
Selecting CYCLE-SENTRY or Continuous Mode . . . 55
Initiating a Manual Defrost Cycle . . . . . . . . . . . . . . . . 56
Checking Software Revision . . . . . . . . . . . . . . . . . . . 57
Printing a Trip Report . . . . . . . . . . . . . . . . . . . . . . . . . 58
Initiating a Start of Trip . . . . . . . . . . . . . . . . . . . . . . . . 60
Displaying and Clearing Alarm Codes . . . . . . . . . . . . 61
Alarm Codes . . . . . . . . . . . . . . . . . . . . . . . . . . . . . . . 63
Introduction . . . . . . . . . . . . . . . . . . . . . . . . . . . . . . . . . 63
Repair . . . . . . . . . . . . . . . . . . . . . . . . . . . . . . . . . . . . . 63
Alarm Types . . . . . . . . . . . . . . . . . . . . . . . . . . . . . . . . 64
Corrective Action . . . . . . . . . . . . . . . . . . . . . . . . . . . . 64
Alarm Code 84 (Restart Null) . . . . . . . . . . . . . . . . . . . 65
Alarm Code 85 (Forced Unit Operation) . . . . . . . . . . . 65
Table of Alarm Codes . . . . . . . . . . . . . . . . . . . . . . . . . 66
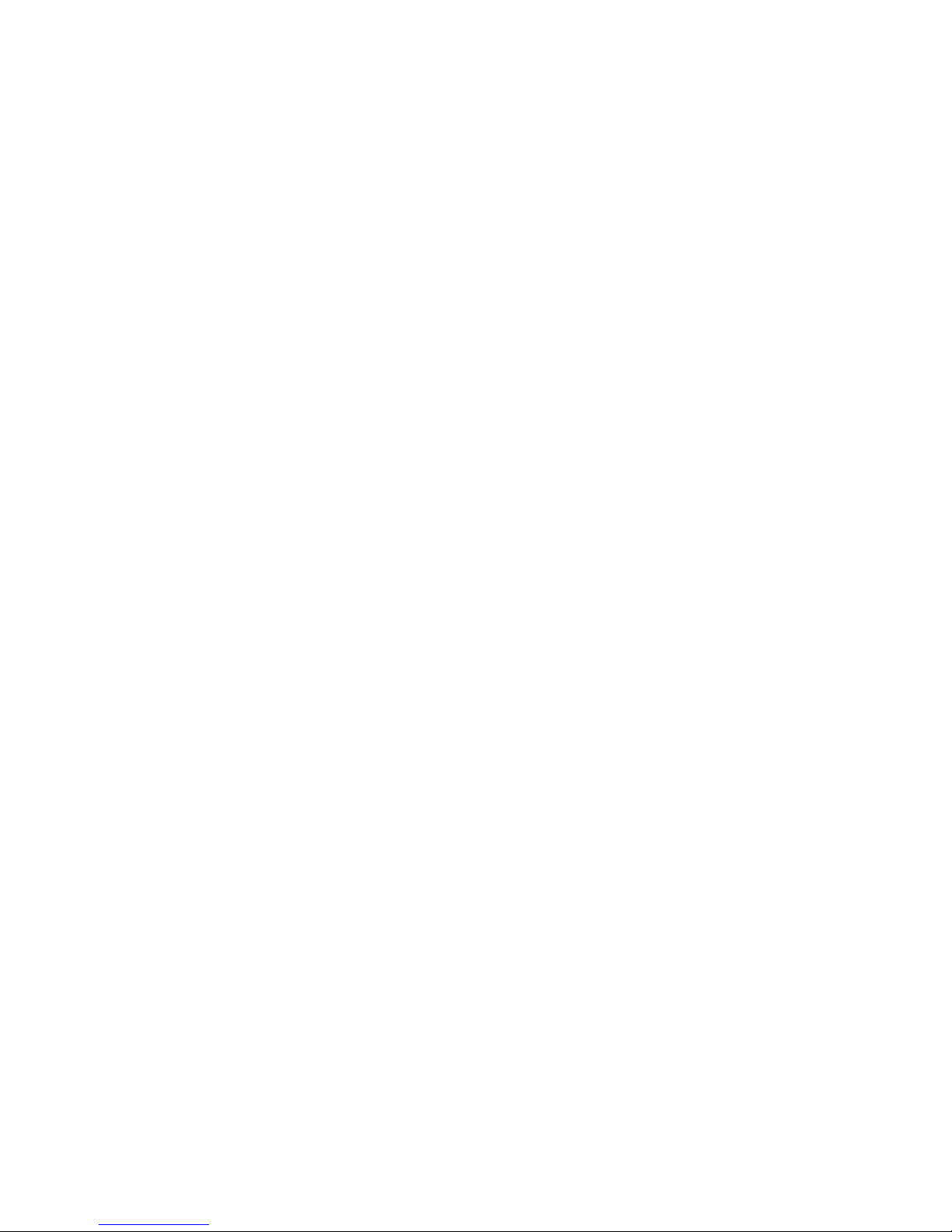
Table of Contents
5
Loading and Enroute Inspections . . . . . . . . . . . . . . 83
Pre-Loading Inspection . . . . . . . . . . . . . . . . . . . . . . . . 83
Post-Loading Inspection . . . . . . . . . . . . . . . . . . . . . . . 85
Enroute Inspections . . . . . . . . . . . . . . . . . . . . . . . 86
Jump Starting . . . . . . . . . . . . . . . . . . . . . . . . . . . . . . 89
Specifications . . . . . . . . . . . . . . . . . . . . . . . . . . . . . . 93
Engine . . . . . . . . . . . . . . . . . . . . . . . . . . . . . . . . . . . . . 93
Belt Tension . . . . . . . . . . . . . . . . . . . . . . . . . . . . . . . . 95
Electrical Control System . . . . . . . . . . . . . . . . . . . . . . 95
Refrigeration System . . . . . . . . . . . . . . . . . . . . . . . . . 96
Maintenance Inspection Schedule . . . . . . . . . . . . . 97
Warranty . . . . . . . . . . . . . . . . . . . . . . . . . . . . . . . . . .101
Glossary . . . . . . . . . . . . . . . . . . . . . . . . . . . . . . . . . .103
Index . . . . . . . . . . . . . . . . . . . . . . . . . . . . . . . . . . . . .109
Serial Number Locations . . . . . . . . . . . . . . . . . . . . .113
Emergency Cold Line . . . . . . . . . . . . . . . . . . . . . . .117
Recover Refrigerant . . . . . . . . . . . . . . . . . . . . . . . . .118
California Proposition 65 Warning . . . . . . . . . . . . .119
Table of Contents
5
Loading and Enroute Inspections . . . . . . . . . . . . . . 83
Pre-Loading Inspection . . . . . . . . . . . . . . . . . . . . . . . . 83
Post-Loading Inspection . . . . . . . . . . . . . . . . . . . . . . . 85
Enroute Inspections . . . . . . . . . . . . . . . . . . . . . . . 86
Jump Starting . . . . . . . . . . . . . . . . . . . . . . . . . . . . . . 89
Specifications . . . . . . . . . . . . . . . . . . . . . . . . . . . . . . 93
Engine . . . . . . . . . . . . . . . . . . . . . . . . . . . . . . . . . . . . . 93
Belt Tension . . . . . . . . . . . . . . . . . . . . . . . . . . . . . . . . 95
Electrical Control System . . . . . . . . . . . . . . . . . . . . . . 95
Refrigeration System . . . . . . . . . . . . . . . . . . . . . . . . . 96
Maintenance Inspection Schedule . . . . . . . . . . . . . 97
Warranty . . . . . . . . . . . . . . . . . . . . . . . . . . . . . . . . . .101
Glossary . . . . . . . . . . . . . . . . . . . . . . . . . . . . . . . . . .103
Index . . . . . . . . . . . . . . . . . . . . . . . . . . . . . . . . . . . . .109
Serial Number Locations . . . . . . . . . . . . . . . . . . . . .113
Emergency Cold Line . . . . . . . . . . . . . . . . . . . . . . .117
Recover Refrigerant . . . . . . . . . . . . . . . . . . . . . . . . .118
California Proposition 65 Warning . . . . . . . . . . . . .119
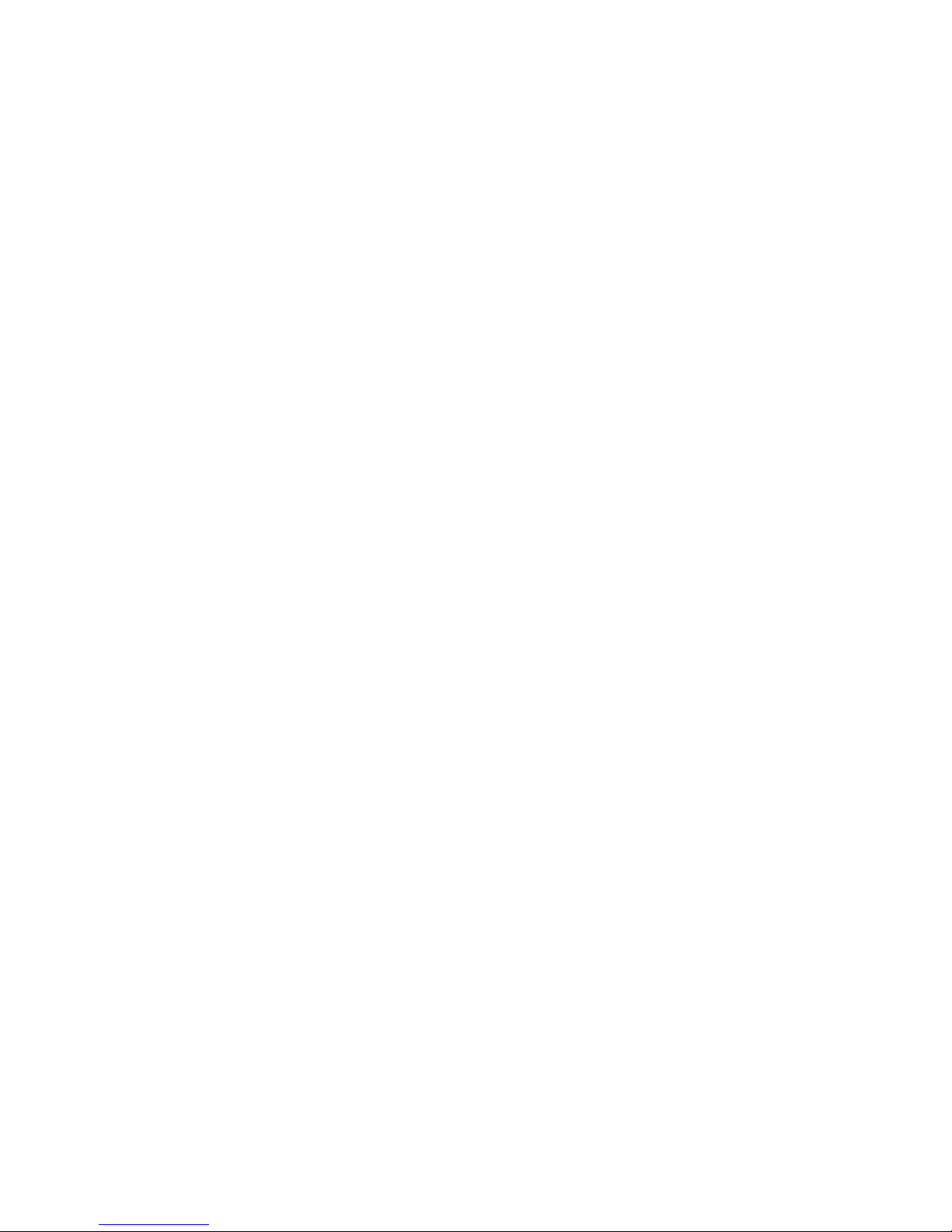
7
List of Figures
Figure 1:Belt Warning
(Located on condenser housing) . . . . . . . . . . . . . . . . 14
Figure 2:Belt Replacement Caution
(Located on condenser housing) . . . . . . . . . . . . . . . . 14
Figure 3:Automatic Start Caution. . . . . . . . . . . . . . . . . 15
Figure 4:Fan Caution . . . . . . . . . . . . . . . . . . . . . . . . . . 15
Figure 5:Door Latch Warning
(Located on curbside door) . . . . . . . . . . . . . . . . . . . . . 16
Figure 6:Front View . . . . . . . . . . . . . . . . . . . . . . . . . . . 21
Figure 7:TK486V (Tier 2) . . . . . . . . . . . . . . . . . . . . . . 23
Figure 8:Control and Switch Panels . . . . . . . . . . . . . . 25
Figure 9:Door Latch Location . . . . . . . . . . . . . . . . . . . 29
Figure 10:Opening Secondary Door Latch . . . . . . . . . 29
Figure 11:Engine Compartment . . . . . . . . . . . . . . . . . 31
Figure 12:Relay Board . . . . . . . . . . . . . . . . . . . . . . . . 34
Figure 13:TG-VI Control Panel With all Possible
Icons and Characters Displayed . . . . . . . . . . . . . . . . . 35
Figure 14:Display Screen With all Possible Icons and
Characters Displayed . . . . . . . . . . . . . . . . . . . . . . . . . .36
Figure 15:Upper and Lower Displays . . . . . . . . . . . . . .37
Figure 16:Standard Display . . . . . . . . . . . . . . . . . . . . .39
Figure 17:Keypad . . . . . . . . . . . . . . . . . . . . . . . . . . . .40
Figure 18:Remote Status Light . . . . . . . . . . . . . . . . . .43
Figure 19:TG-VI Microprocessor Controller . . . . . . . . .47
Figure 20:Control and Switch Panels . . . . . . . . . . . . . .48
Figure 21:Unit Self Check . . . . . . . . . . . . . . . . . . . . . .50
Figure 22:Standard Display . . . . . . . . . . . . . . . . . . . . .52
Figure 23:Changing the Setpoint . . . . . . . . . . . . . . . . .53
Figure 24:Selecting CYCLE-SENTRY
or Continuous Mode . . . . . . . . . . . . . . . . . . . . . . . . . . .55
Figure 25:Initiating a Manual Defrost Cycle . . . . . . . . .56
Figure 26:Checking Software Revision . . . . . . . . . . . .57
Figure 27:Printing a Trip Report . . . . . . . . . . . . . . . . . .58
Figure 28:Initiating a Start of Trip . . . . . . . . . . . . . . . . .60
7
List of Figures
Figure 1:Belt Warning
(Located on condenser housing) . . . . . . . . . . . . . . . . 14
Figure 2:Belt Replacement Caution
(Located on condenser housing) . . . . . . . . . . . . . . . . 14
Figure 3:Automatic Start Caution. . . . . . . . . . . . . . . . . 15
Figure 4:Fan Caution . . . . . . . . . . . . . . . . . . . . . . . . . . 15
Figure 5:Door Latch Warning
(Located on curbside door) . . . . . . . . . . . . . . . . . . . . . 16
Figure 6:Front View . . . . . . . . . . . . . . . . . . . . . . . . . . . 21
Figure 7:TK486V (Tier 2) . . . . . . . . . . . . . . . . . . . . . . 23
Figure 8:Control and Switch Panels . . . . . . . . . . . . . . 25
Figure 9:Door Latch Location . . . . . . . . . . . . . . . . . . . 29
Figure 10:Opening Secondary Door Latch . . . . . . . . . 29
Figure 11:Engine Compartment . . . . . . . . . . . . . . . . . 31
Figure 12:Relay Board . . . . . . . . . . . . . . . . . . . . . . . . 34
Figure 13:TG-VI Control Panel With all Possible
Icons and Characters Displayed . . . . . . . . . . . . . . . . . 35
Figure 14:Display Screen With all Possible Icons and
Characters Displayed . . . . . . . . . . . . . . . . . . . . . . . . . .36
Figure 15:Upper and Lower Displays . . . . . . . . . . . . . .37
Figure 16:Standard Display . . . . . . . . . . . . . . . . . . . . .39
Figure 17:Keypad . . . . . . . . . . . . . . . . . . . . . . . . . . . .40
Figure 18:Remote Status Light . . . . . . . . . . . . . . . . . .43
Figure 19:TG-VI Microprocessor Controller . . . . . . . . .47
Figure 20:Control and Switch Panels . . . . . . . . . . . . . .48
Figure 21:Unit Self Check . . . . . . . . . . . . . . . . . . . . . .50
Figure 22:Standard Display . . . . . . . . . . . . . . . . . . . . .52
Figure 23:Changing the Setpoint . . . . . . . . . . . . . . . . .53
Figure 24:Selecting CYCLE-SENTRY
or Continuous Mode . . . . . . . . . . . . . . . . . . . . . . . . . . .55
Figure 25:Initiating a Manual Defrost Cycle . . . . . . . . .56
Figure 26:Checking Software Revision . . . . . . . . . . . .57
Figure 27:Printing a Trip Report . . . . . . . . . . . . . . . . . .58
Figure 28:Initiating a Start of Trip . . . . . . . . . . . . . . . . .60
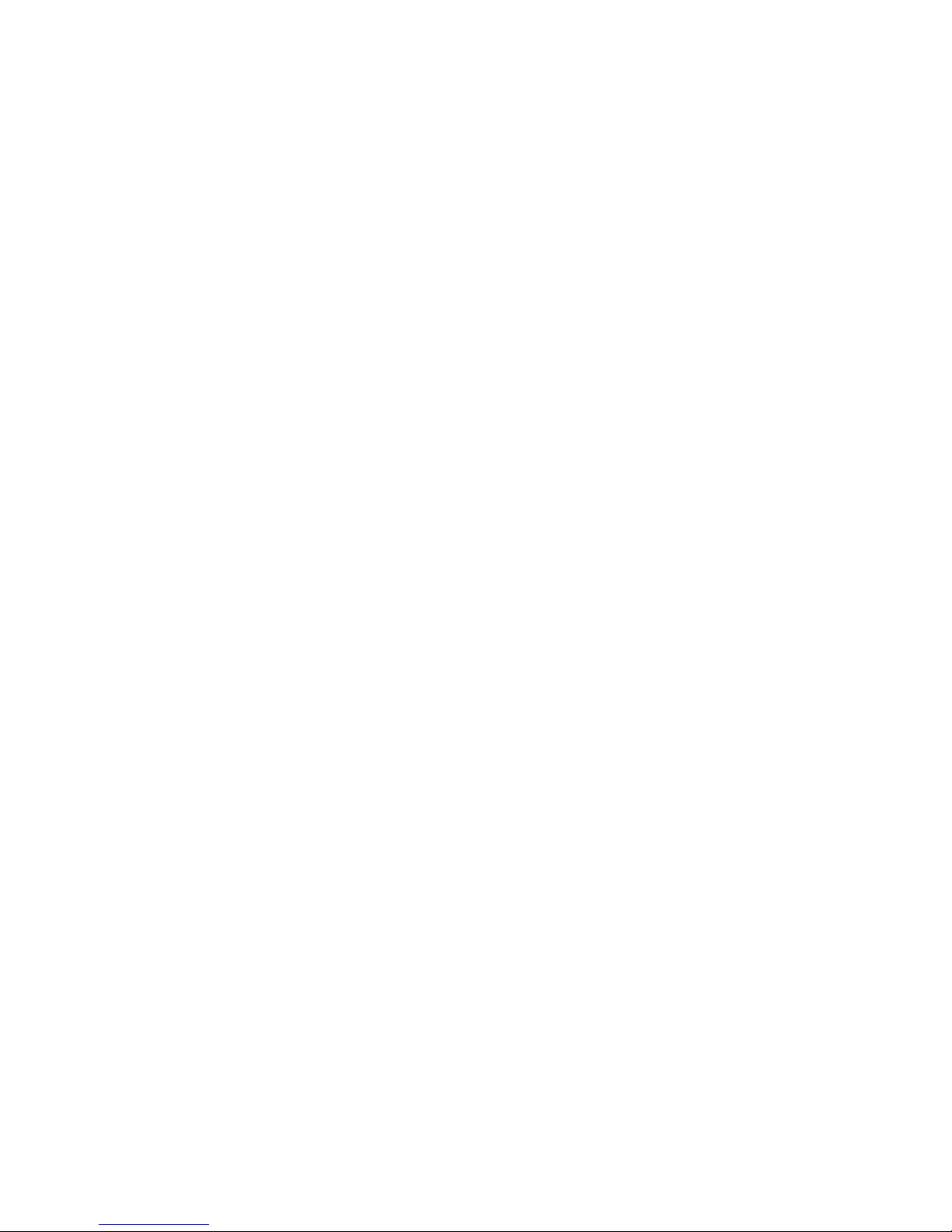
List of Figures
8
Figure 29:Alarm Symbol Location . . . . . . . . . . . . . . . .61
Figure 30:Loading Considerations . . . . . . . . . . . . . . . . 84
Figure 31:Unit Battery . . . . . . . . . . . . . . . . . . . . . . . . .90
Figure 32:Sequence for Connecting Jumper Cables . . 90
Figure 33:Unit Engine . . . . . . . . . . . . . . . . . . . . . . . . .91
Figure 34:Sequence for Disconnecting
Jumper Cables . . . . . . . . . . . . . . . . . . . . . . . . . . . . . .92
Figure 35:Compressor Serial Number Location . . . . 113
Figure 36:Engine Serial Number Location . . . . . . . . 114
Figure 37:Unit Serial Number Plate Locations . . . . . 114
Figure 38:Unit Serial Number Plate . . . . . . . . . . . . . 115
List of Figures
8
Figure 29:Alarm Symbol Location . . . . . . . . . . . . . . . .61
Figure 30:Loading Considerations . . . . . . . . . . . . . . . . 84
Figure 31:Unit Battery . . . . . . . . . . . . . . . . . . . . . . . . .90
Figure 32:Sequence for Connecting Jumper Cables . . 90
Figure 33:Unit Engine . . . . . . . . . . . . . . . . . . . . . . . . .91
Figure 34:Sequence for Disconnecting
Jumper Cables . . . . . . . . . . . . . . . . . . . . . . . . . . . . . .92
Figure 35:Compressor Serial Number Location . . . . 113
Figure 36:Engine Serial Number Location . . . . . . . . 114
Figure 37:Unit Serial Number Plate Locations . . . . . 114
Figure 38:Unit Serial Number Plate . . . . . . . . . . . . . 115
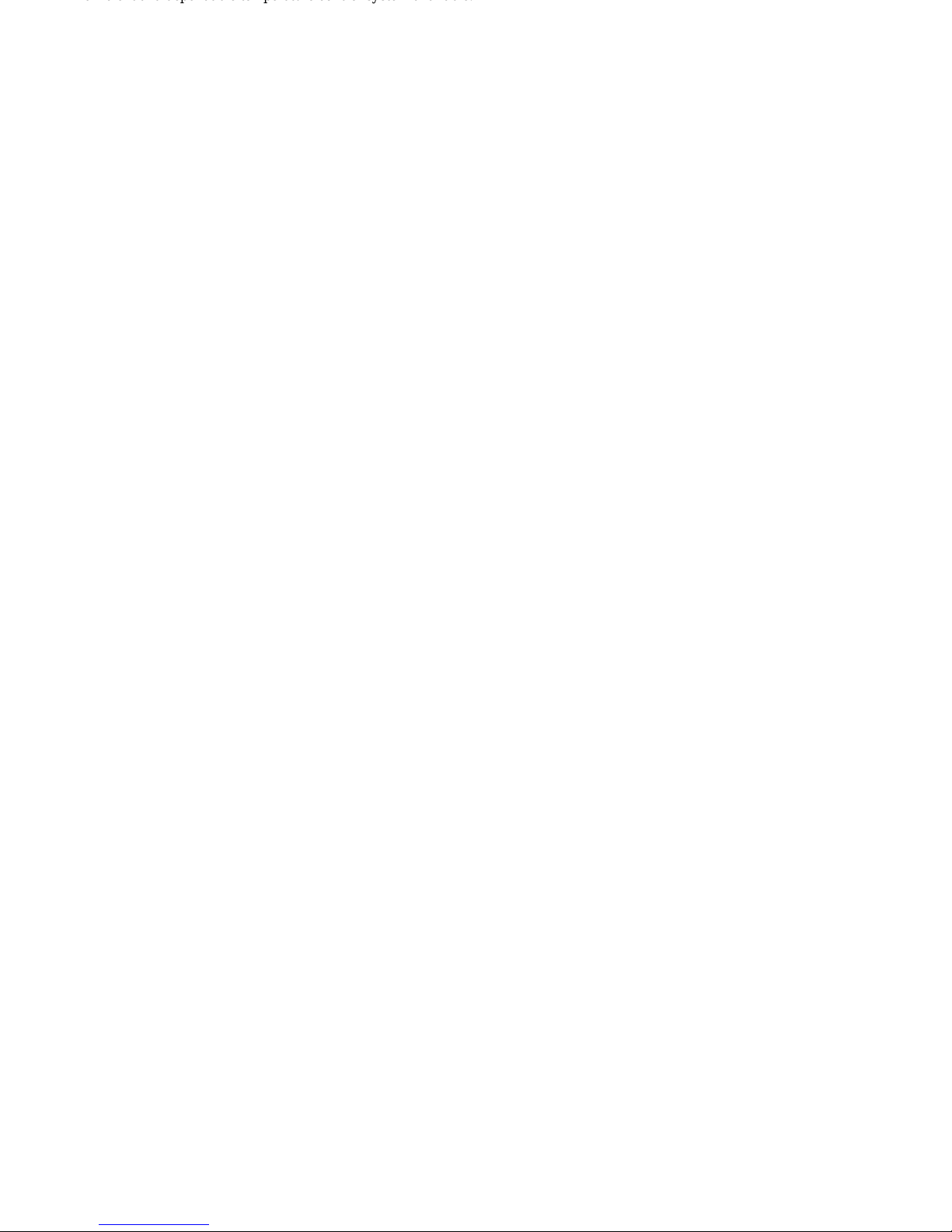
9
Introduction
There is nothing complicated about operating and maintaining
your Thermo King unit, but a few minutes studying this
manual will be time well spent.
Performing pre-trip checks and enroute inspections on a
regular basis will m ini mi ze on -t he-r oad o perat ing problems. A
regular maintenance program will also help to keep your unit
in top operating condition. If factory reco mmended p rocedures
are followed, you will find that you have purchased the most
efficient and dependable temperature control system available.
All service requirements, major and minor, should be handled
by a Thermo King dealer for four very important reasons:
• They are equipped with the factory recommended tools to
perform all service functions
• They have factory trained and certified technicians
• They have genuine Thermo King replacement parts
• The warranty on your new unit is valid only when the
repair and replacement of component parts is performed
by an authorized Thermo King dealer.
IMPORTANT: This manual is published for informational
purposes only and the information furnished herein should
not be considered as all-inclusive or meant to cover all
contingencies. If more information is re qu ired, consult your
Thermo King Service Directory for the location and
telephone number of the local dealer.
9
Introduction
There is nothing complicated about operating and maintaining
your Thermo King unit, but a few minutes studying this
manual will be time well spent.
Performing pre-trip checks and enroute inspections on a
regular basis will m ini mi ze on -t he-r oad o perat ing problems. A
regular maintenance program will also help to keep your unit
in top operating condition. If factory reco mmended p rocedures
are followed, you will find that you have purchased the most
efficient and dependable temperature control system available.
All service requirements, major and minor, should be handled
by a Thermo King dealer for four very important reasons:
• They are equipped with the factory recommended tools to
perform all service functions
• They have factory trained and certified technicians
• They have genuine Thermo King replacement parts
• The warranty on your new unit is valid only when the
repair and replacement of component parts is performed
by an authorized Thermo King dealer.
IMPORTANT: This manual is published for informational
purposes only and the information furnished herein should
not be considered as all-inclusive or meant to cover all
contingencies. If more information is re qu ired, consult your
Thermo King Service Directory for the location and
telephone number of the local dealer.
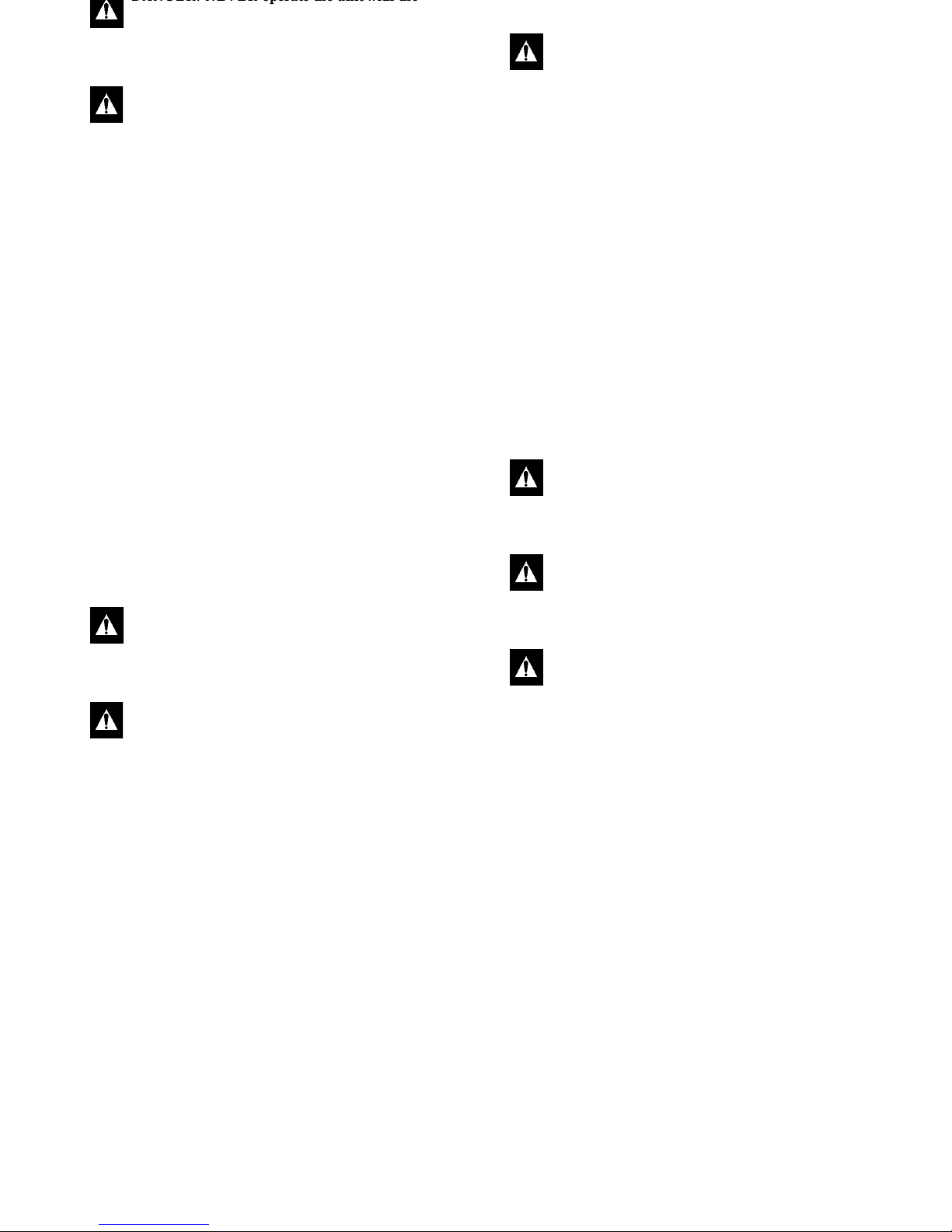
11
Safety Precautions
Thermo King recommends t hat servicing be done only by a
Thermo King dealer. However, you should be aware of several
safety practices. This chapter gives basic safety precautions for
working with Thermo King units and describes the safety
stickers on your unit that you should be familiar with.
General Safety Practices
DANGER: NEVER operate the unit with the
compressor discharge valve closed. Doing so could
cause the compressor to explode, causing death or
serious injury.
WARNING: Always wear goggles or safety glasses
when working with or around the refrigeration system
or battery. Refrigerant or battery acid can cause
permanent damage if it comes in contact with your
eyes.
WARNING: Keep hands and loose clothing clear of
fans and belts at all times when the unit is operating
or when opening or closing compressor service
valves.
WARNING: Exposed coil fins can cause painful
lacerations. Service work on the evaporator or
condenser coils should be done by a certified Thermo
King technician.
WARNING: Do not apply heat to a closed cooling
system. Before applying heat to a cooling system,
drain it. Then flush it with water an d dr ai n t h e wa ter.
Antifreeze contains water and ethylene glycol. The
ethylene glycol is flammable and can ignite if the
antifreeze is heated enough to boil off the water.
11
Safety Precautions
Thermo King recommends t hat servicing be done only by a
Thermo King dealer. However, you should be aware of several
safety practices. This chapter gives basic safety precautions for
working with Thermo King units and describes the safety
stickers on your unit that you should be familiar with.
General Safety Practices
DANGER: NEVER operate the unit with the
compressor discharge valve closed. Doing so could
cause the compressor to explode, causing death or
serious injury.
WARNING: Always wear goggles or safety glasses
when working with or around the refrigeration system
or battery. Refrigerant or battery acid can cause
permanent damage if it comes in contact with your
eyes.
WARNING: Keep hands and loose clothing clear of
fans and belts at all times when the unit is operating
or when opening or closing compressor service
valves.
WARNING: Exposed coil fins can cause painful
lacerations. Service work on the evaporator or
condenser coils should be done by a certified Thermo
King technician.
WARNING: Do not apply heat to a closed cooling
system. Before applying heat to a cooling system,
drain it. Then flush it with water an d dr ai n t h e wa ter.
Antifreeze contains water and ethylene glycol. The
ethylene glycol is flammable and can ignite if the
antifreeze is heated enough to boil off the water.
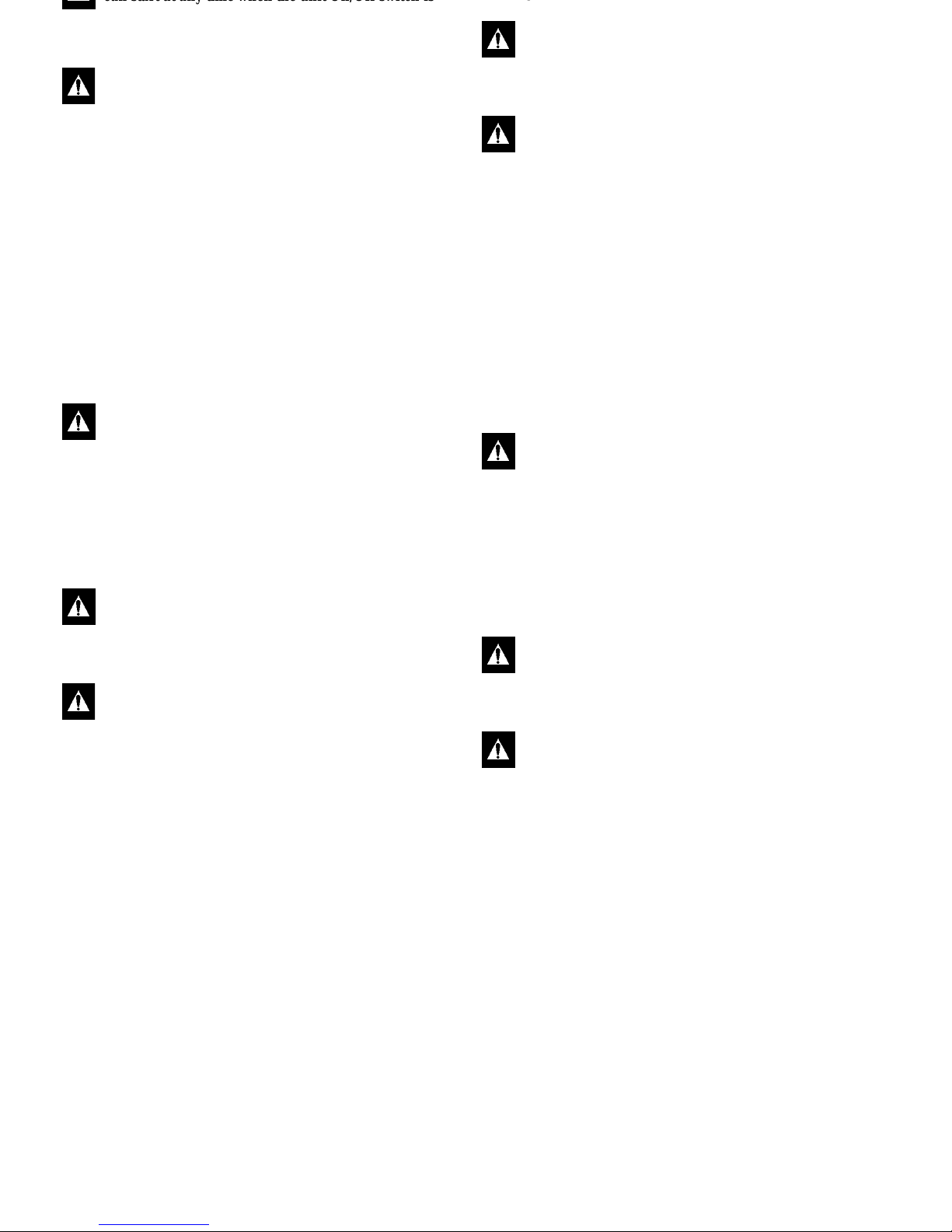
Safety Precautions
12
Automatic Start/Stop Operation
This unit is capable of automatic operation and could start at
any time without warning.
Electrical Hazard
Refrigerant
Although fluorocarbon refrigerants are classified as safe, use
caution when working with refrigerants or in areas where they
are being used.
CAUTION: Use extreme caution when drilling holes
in the unit. Drilling into electrical wiring or
refrigerant lines could cause a fire. Do not drill into
structural components.
WARNING: CYCLE-SENTRY Operation. The unit
can start at any time when the unit On/Off switch is
in the on position and the unit is operating in
CYCLE-SENTRY.
WARNING: Turn the unit On/Off switch to the Off
position before inspecting any part of the unit.
CAUTION: Turn off the high voltage power supply
and disconnect the electric cable before working on
the unit. Units with electric standby present a
potential electrical hazard.
DANGER: Fluorocarbon refrigerants can produce
toxic gases. In the presence of an open flame or
electrical short, these gases are severe respiratory
irritants CAPABLE OF CAUSING DEATH.
DANGER: Fluorocarbon refrigerants tend to
displace air and can cause oxygen depletion which
could result in DEATH BY SUFFOCA TION. Provide
adequate ventilation in enclosed or confined areas.
Safety Precautions
12
Automatic Start/Stop Operation
This unit is capable of automatic operation and could start at
any time without warning.
Electrical Hazard
Refrigerant
Although fluorocarbon refrigerants are classified as safe, use
caution when working with refrigerants or in areas where they
are being used.
CAUTION: Use extreme caution when drilling holes
in the unit. Drilling into electrical wiring or
refrigerant lines could cause a fire. Do not drill into
structural components.
WARNING: CYCLE-SENTRY Operation. The unit
can start at any time when the unit On/Off switch is
in the on position and the unit is operating in
CYCLE-SENTRY.
WARNING: Turn the unit On/Off switch to the Off
position before inspecting any part of the unit.
CAUTION: Turn off the high voltage power supply
and disconnect the electric cable before working on
the unit. Units with electric standby present a
potential electrical hazard.
DANGER: Fluorocarbon refrigerants can produce
toxic gases. In the presence of an open flame or
electrical short, these gases are severe respiratory
irritants CAPABLE OF CAUSING DEATH.
DANGER: Fluorocarbon refrigerants tend to
displace air and can cause oxygen depletion which
could result in DEATH BY SUFFOCA TION. Provide
adequate ventilation in enclosed or confined areas.
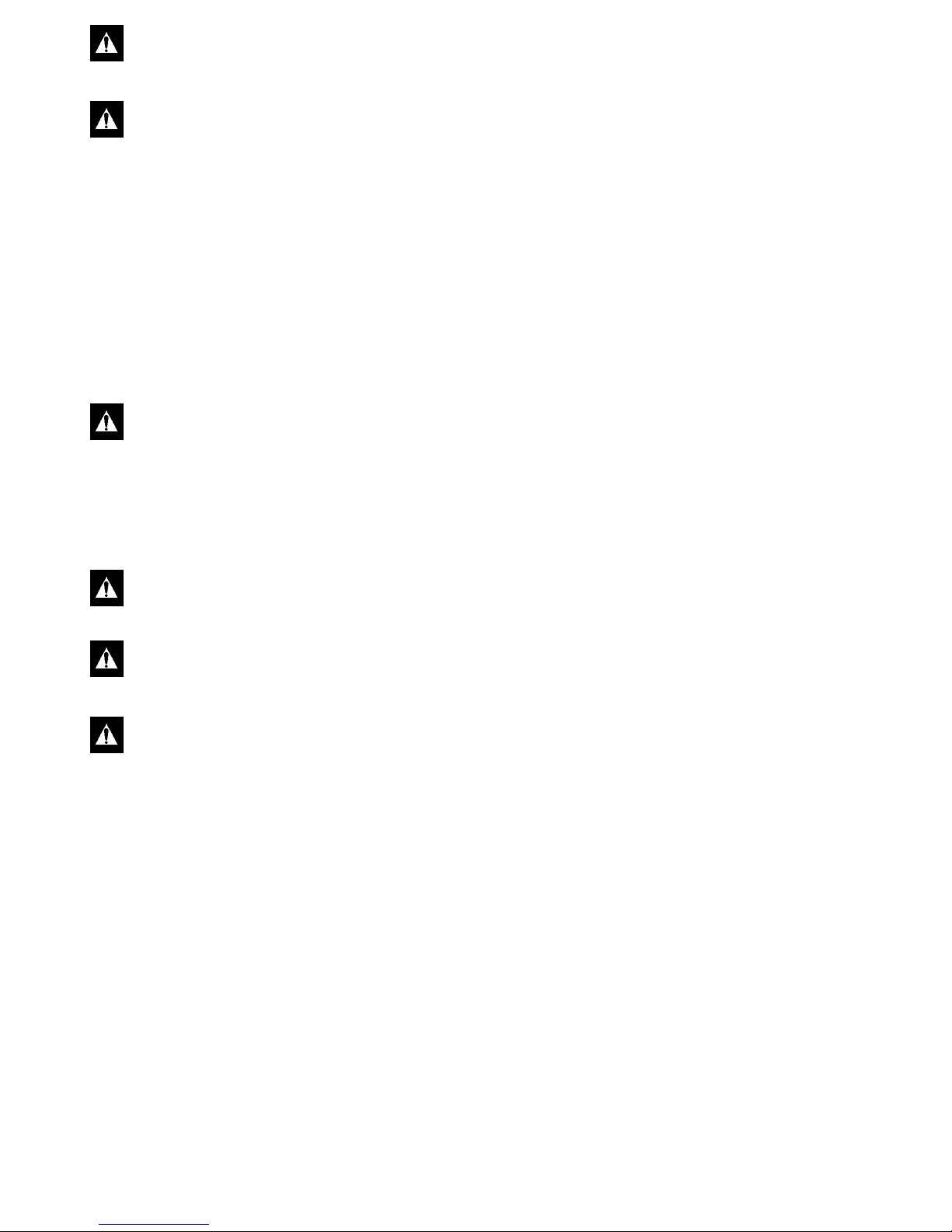
Safety Precautions
13
Refrigerant Oil
Observe the following precautions when working with or
around refrigerant oil:
First Aid
First Aid–Refrigerant
Eyes: For contact with liquid, immediately flush eyes with
large amounts of water. Get prompt medical attention.
Skin: Flush areas with large amounts of warm water. Do not
ap
ply heat. Wrap burns with dry, sterile, bulky dressing to
protect from infection or injury. Get prompt medical attention.
Inhalation: Move victim to fresh air and restore breathing if
ne
cessary. Stay with victim until emergency personnel arrive.
First Aid–Refrigerant Oil
Eyes: Immediately flush eyes with large amounts of water for
at least 15 minutes while holding the eyelids open. Get prompt
medical attention.
Skin: Remove contaminated clothing. Wash thoroughly with
so
ap and water. Get medical attention if irritation persists.
Inhalation:
Move victim to fresh air and restore breathing if
necessary. Stay with victim until emergency personnel arrive.
WARNING: Fluorocarbon refrigerants evaporate
rapidly, freezing anything they contact if accidentally
released into the atmosphere from the liquid state.
W AR N ING : Al wa ys wear goggles or safety glasses to
protect eyes from refrigerant oil contact.
WARNING: Protect skin and clothing from
prolonged or repeated contact with refrigerant oil.
Rubber gloves are recommended.
WARNING: Wash thoroughly immediately after
handling refrigerant oil to prevent irritation.
Safety Precautions
13
Refrigerant Oil
Observe the following precautions when working with or
around refrigerant oil:
First Aid
First Aid–Refrigerant
Eyes: For contact with liquid, immediately flush eyes with
large amounts of water. Get prompt medical attention.
Skin: Flush areas with large amounts of warm water. Do not
ap
ply heat. Wrap burns with dry, sterile, bulky dressing to
protect from infection or injury. Get prompt medical attention.
Inhalation: Move victim to fresh air and restore breathing if
ne
cessary. Stay with victim until emergency personnel arrive.
First Aid–Refrigerant Oil
Eyes: Immediately flush eyes with large amounts of water for
at least 15 minutes while holding the eyelids open. Get prompt
medical attention.
Skin: Remove contaminated clothing. Wash thoroughly with
so
ap and water. Get medical attention if irritation persists.
Inhalation:
Move victim to fresh air and restore breathing if
necessary. Stay with victim until emergency personnel arrive.
WARNING: Fluorocarbon refrigerants evaporate
rapidly, freezing anything they contact if accidentally
released into the atmosphere from the liquid state.
W AR N ING : Al wa ys wear goggles or safety glasses to
protect eyes from refrigerant oil contact.
WARNING: Protect skin and clothing from
prolonged or repeated contact with refrigerant oil.
Rubber gloves are recommended.
WARNING: Wash thoroughly immediately after
handling refrigerant oil to prevent irritation.

Safety Precautions
14
Ingestion: Do not induce vomiting. Immediately contact
local poison control center or physician.
Safety Decals And Locations
Figure 1: Belt Warning
(Located on condenser housing)
Figure 2: Belt Replacement Caution
(Located on condenser housing)
AKB65
AKB66
Safety Precautions
14
Ingestion: Do not induce vomiting. Immediately contact
local poison control center or physician.
Safety Decals And Locations
Figure 1: Belt Warning
(Located on condenser housing)
Figure 2: Belt Replacement Caution
(Located on condenser housing)
AKB65
AKB66

Safety Precautions
15
Figure 3: Automatic Start Cauti on
(Locations vary depending on model. Decals are
located near areas that contain moving parts which
can cause severe injuries if hands or clothing become
tangled when unit automatically starts.)
Figure 4: Fan Caution
(Locations vary depending on model. Decals are
located near areas that contain fans which can cause
severe injuries when unit automatically starts.)
AKB67 AKB68
Safety Precautions
15
Figure 3: Automatic Start Cauti on
(Locations vary depending on model. Decals are
located near areas that contain moving parts which
can cause severe injuries if hands or clothing become
tangled when unit automatically starts.)
Figure 4: Fan Caution
(Locations vary depending on model. Decals are
located near areas that contain fans which can cause
severe injuries when unit automatically starts.)
AKB67 AKB68
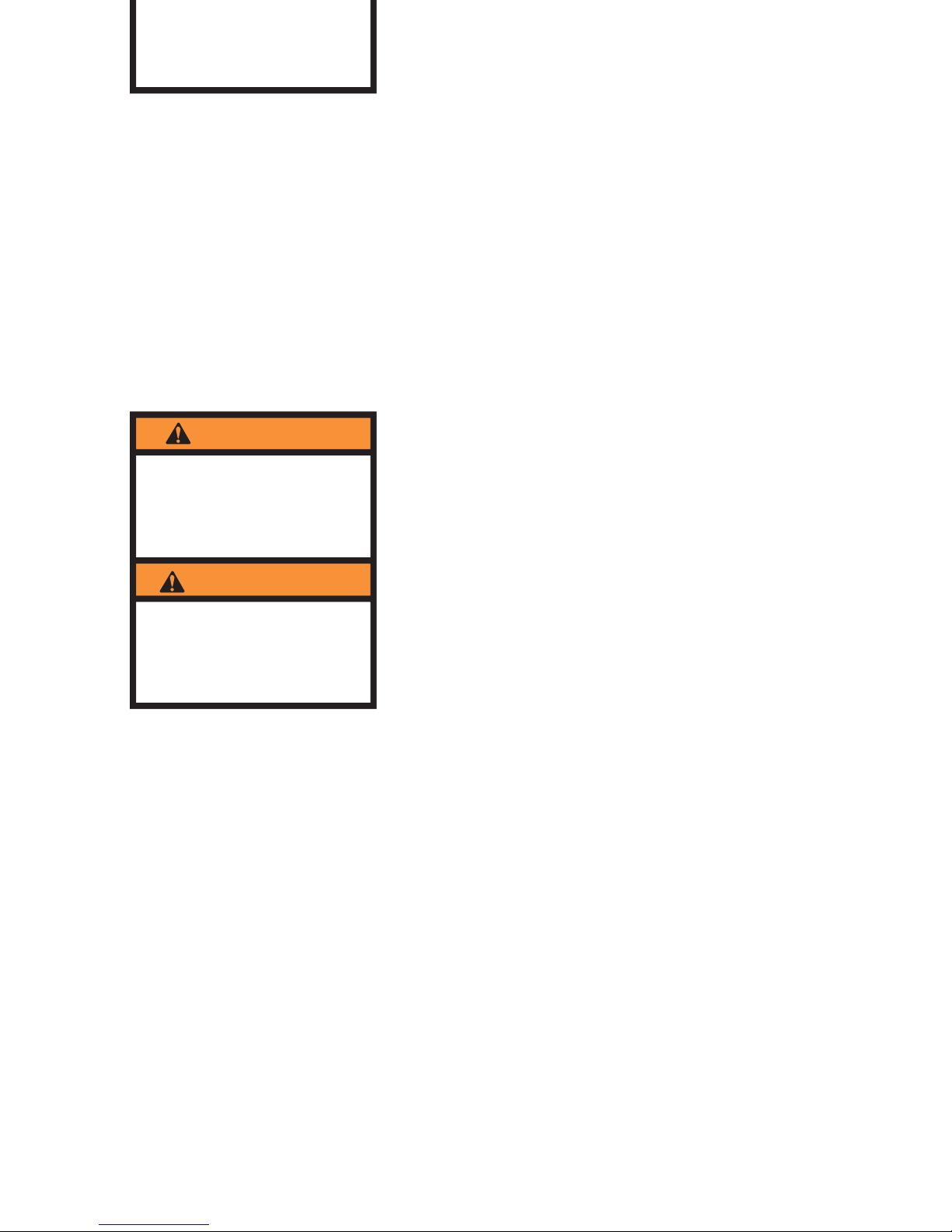
Safety Precautions
16
Figure 5: Door Latch Warning
(Located on curbside door)
WARNING
ATENCIÓN
NEW DOOR LATCH DESIGN
REQUIRES DOOR TO BE SLAMMED
SHUT BEFORE MOVING TRAILER.
FAILURE TO CLOSE DOOR FIRMLY
CAN ALLOW WIND TO TEAR DOOR
FROM REFRIGERATION UNIT AND
CAUSE INJURY TO OTHERS.
NUEVO DESEÑO DE CERRADURA
REQUIERE ASOTAR LA PUERTA ANTES
DE CONDUCIR EL TRAILER.
AL NO CERRAR LA PUERTA CON
FIRMEZA EL VIENTO PODRÍA
DESPRENDER LA PUERTA DE LA
UNIDAD DE REFRIGERACIÓN Y
CAUSAR DAÑOS A OTROS.
AEA2422
Safety Precautions
16
Figure 5: Door Latch Warning
(Located on curbside door)
WARNING
ATENCIÓN
NEW DOOR LATCH DESIGN
REQUIRES DOOR TO BE SLAMMED
SHUT BEFORE MOVING TRAILER.
FAILURE TO CLOSE DOOR FIRMLY
CAN ALLOW WIND TO TEAR DOOR
FROM REFRIGERATION UNIT AND
CAUSE INJURY TO OTHERS.
NUEVO DESEÑO DE CERRADURA
REQUIERE ASOTAR LA PUERTA ANTES
DE CONDUCIR EL TRAILER.
AL NO CERRAR LA PUERTA CON
FIRMEZA EL VIENTO PODRÍA
DESPRENDER LA PUERTA DE LA
UNIDAD DE REFRIGERACIÓN Y
CAUSAR DAÑOS A OTROS.
AEA2422

17
EPA Emission Control System Warranty
Statement
Thermo King warrants to the initial owner and each subsequent
owner that the certified, non-road diesel engine in your unit is:
1. Designed, built and equipped so as to conform, at the time
of sale, with all applicable regulations adopted by the
United States Environmental Protection Agency (EPA).
2. Free from defects in materials and workmanship in
specific emission related parts for a period of five years or
3,000 hours of operation, whi chever comes first, after date
of delivery to the initial owner.
If an emission-related part or component fails during the
warranty period, it will be repaired or replaced. Any such part
or component repaired or replaced under warranty is warranted
for the warranty period.
During the term of this warranty, Thermo King will provide,
through a Thermo King authorized service dealer or other
establishment authorized by Thermo King, repair or
replacement of any warranted part at no char ge to the no n-road
engine owner.
In emergency, repairs may be performed at any service
establishment, or by the owner, using any replacement part.
Thermo King will reimburse the owner for their expenses,
including diagnostic charges for such emergency repair. These
expenses shall not exceed Thermo King’ s suggested retail price
for all warranted parts replaced, and labor changes based on
Thermo King’s reco mmend ed time allowance for the warranty
repair and the geographically appropriate hourly labor rate.
17
EPA Emission Control System Warranty
Statement
Thermo King warrants to the initial owner and each subsequent
owner that the certified, non-road diesel engine in your unit is:
1. Designed, built and equipped so as to conform, at the time
of sale, with all applicable regulations adopted by the
United States Environmental Protection Agency (EPA).
2. Free from defects in materials and workmanship in
specific emission related parts for a period of five years or
3,000 hours of operation, whi chever comes first, after date
of delivery to the initial owner.
If an emission-related part or component fails during the
warranty period, it will be repaired or replaced. Any such part
or component repaired or replaced under warranty is warranted
for the warranty period.
During the term of this warranty, Thermo King will provide,
through a Thermo King authorized service dealer or other
establishment authorized by Thermo King, repair or
replacement of any warranted part at no char ge to the no n-road
engine owner.
In emergency, repairs may be performed at any service
establishment, or by the owner, using any replacement part.
Thermo King will reimburse the owner for their expenses,
including diagnostic charges for such emergency repair. These
expenses shall not exceed Thermo King’ s suggested retail price
for all warranted parts replaced, and labor changes based on
Thermo King’s reco mmend ed time allowance for the warranty
repair and the geographically appropriate hourly labor rate.
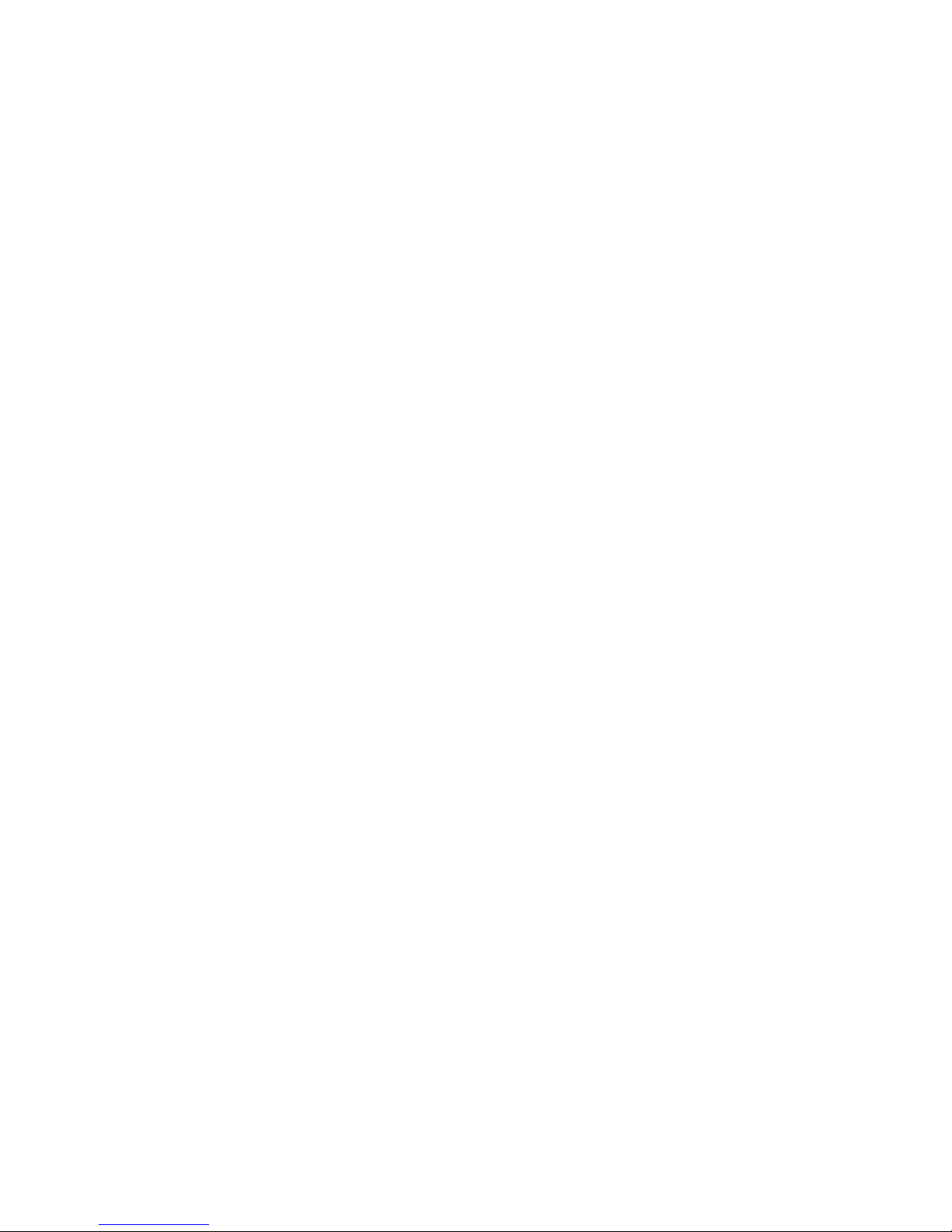
EPA Emission Control System Warranty Statement
18
Any replacement part can be used for maintenance or repairs.
The owner should ensure that such parts are equivalent in
design and durability to genuine Thermo King parts. However,
Thermo King is not liable for parts that are not genuine
Thermo King parts.
A part not being available within 30 days or repair not being
completed within 30 days constitutes an emergency.
As a condition of reimbursement, replaced parts and received
invoices must be presented at a place of business of a Thermo
King authorized service dealer or other establi shment
authorized by Thermo King.
This warranty covers the following emission-related parts and
components:
• Fuel Injection System
• Intake Manifold
•Exhaust Manifold
• Miscellaneous hoses, clamps, connectors and sealing
devices used in the above systems.
If failure of one of these parts or components results in failure
of another part or component, both will be covered by this
warranty.
Responsibilities
This warranty is subject to the following:
Thermo King Corporation
Responsibilities
During the emission warranty period, if a defect in material or
workmanship of a warranted part or component is found,
Thermo King will provide:
• New, remanufactured, or repaired parts or components
required to correct the defect.
NOTE: Items replaced under this warranty become the
property of Thermo King.
• Labor, dur ing normal working h ours, req uired to make t he
warranty repair. This includes diagnosis and labor to
remove and install the engine, if necessary.
EPA Emission Control System Warranty Statement
18
Any replacement part can be used for maintenance or repairs.
The owner should ensure that such parts are equivalent in
design and durability to genuine Thermo King parts. However,
Thermo King is not liable for parts that are not genuine
Thermo King parts.
A part not being available within 30 days or repair not being
completed within 30 days constitutes an emergency.
As a condition of reimbursement, replaced parts and received
invoices must be presented at a place of business of a Thermo
King authorized service dealer or other establi shment
authorized by Thermo King.
This warranty covers the following emission-related parts and
components:
• Fuel Injection System
• Intake Manifold
•Exhaust Manifold
• Miscellaneous hoses, clamps, connectors and sealing
devices used in the above systems.
If failure of one of these parts or components results in failure
of another part or component, both will be covered by this
warranty.
Responsibilities
This warranty is subject to the following:
Thermo King Corporation
Responsibilities
During the emission warranty period, if a defect in material or
workmanship of a warranted part or component is found,
Thermo King will provide:
• New, remanufactured, or repaired parts or components
required to correct the defect.
NOTE: Items replaced under this warranty become the
property of Thermo King.
• Labor, dur ing normal working h ours, req uired to make t he
warranty repair. This includes diagnosis and labor to
remove and install the engine, if necessary.
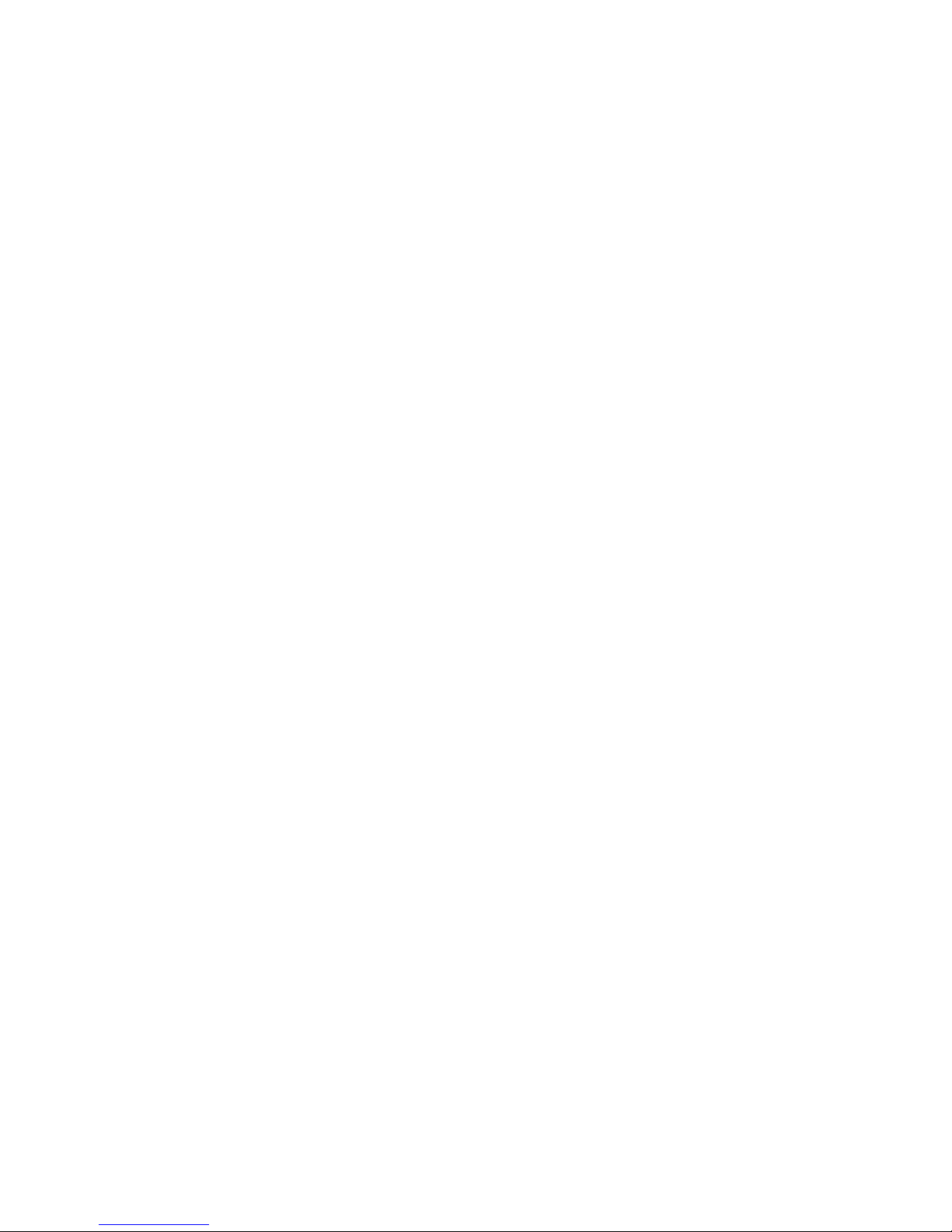
EPA Emission Control System Warranty Statement
19
Owner Responsibilities
During the emission warranty period, the owner is responsible
for:
• The performance of all required maintenance. A warranty
claim will not be denied because the scheduled
maintenance was not performed. However, if the lack of
required maintenance was the reason for the repair, then
the claim will be denied.
• Premium of overtime cost.
• Cost to investigate complaints that are not caused by
defects in Thermo King material or workmanship.
• Providing timely notice of a warrantable failure and
promptly making the product available for re pair.
Limitations
Thermo King is not responsible for resultant damages to an
emission-related part or component resulting from:
• Any application or installation Thermo King deems
improper as explained in this Operator’s Manual, or any
other manuals provided for the unit.
• Attachments, accessory items, or parts not authorized for
use by Thermo King.
• Improper off-road engine maintenance, repair or abuse.
• Owner’s unreasonable delay in making the product
available after being notified of a potential product
problem.
This warranty is in addition to Thermo King’s standard
warranty applicable to the off-road engine product involved.
Remedies under this warranty are limited to the provision of
material and services as specified herein. Thermo King is not
responsible for incidental or consequential damages such as
downtime or loss of engi ne powered equipment .
EPA Emission Control System Warranty Statement
19
Owner Responsibilities
During the emission warranty period, the owner is responsible
for:
• The performance of all required maintenance. A warranty
claim will not be denied because the scheduled
maintenance was not performed. However, if the lack of
required maintenance was the reason for the repair, then
the claim will be denied.
• Premium of overtime cost.
• Cost to investigate complaints that are not caused by
defects in Thermo King material or workmanship.
• Providing timely notice of a warrantable failure and
promptly making the product available for re pair.
Limitations
Thermo King is not responsible for resultant damages to an
emission-related part or component resulting from:
• Any application or installation Thermo King deems
improper as explained in this Operator’s Manual, or any
other manuals provided for the unit.
• Attachments, accessory items, or parts not authorized for
use by Thermo King.
• Improper off-road engine maintenance, repair or abuse.
• Owner’s unreasonable delay in making the product
available after being notified of a potential product
problem.
This warranty is in addition to Thermo King’s standard
warranty applicable to the off-road engine product involved.
Remedies under this warranty are limited to the provision of
material and services as specified herein. Thermo King is not
responsible for incidental or consequential damages such as
downtime or loss of engi ne powered equipment .
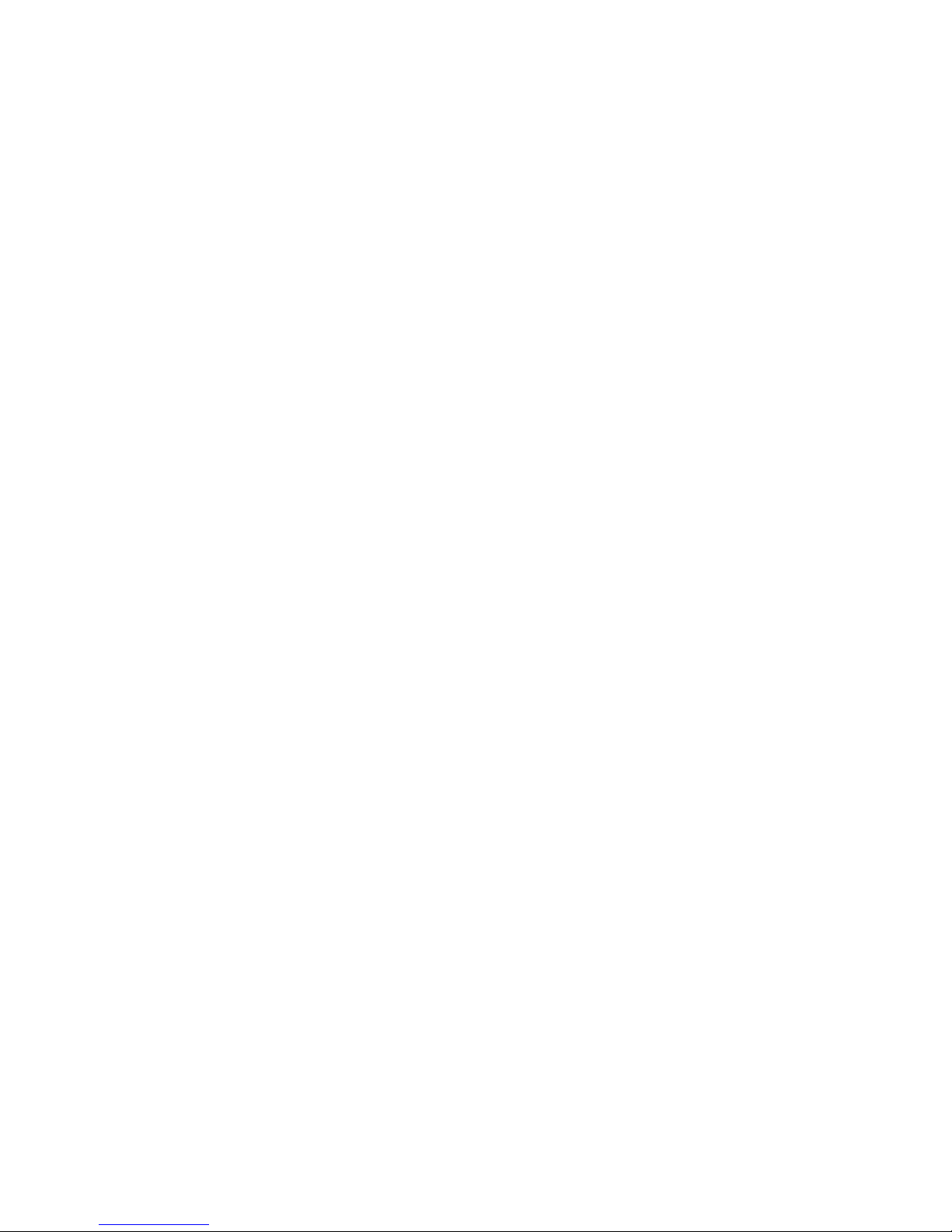
EPA Emission Control System Warranty Statement
20
EPA Emission Control System Warranty Statement
20

21
Unit Description
Unit Overview
The Thermo King SB-200TG is a one piece, self-contained,
diesel powered, air cooling/heating unit operating under the
control of a TG-VI programmable microprocessor controller.
The unit mounts on the front of the trailer with the evaporator
extending through an opening in the front wall.
The unit is available as a Model 30 and features cooling and
heating using a quiet running Thermo King TK486V engine .
Figure 6: Front View
21
Unit Description
Unit Overview
The Thermo King SB-200TG is a one piece, self-contained,
diesel powered, air cooling/heating unit operating under the
control of a TG-VI programmable microprocessor controller.
The unit mounts on the front of the trailer with the evaporator
extending through an opening in the front wall.
The unit is available as a Model 30 and features cooling and
heating using a quiet running Thermo King TK486V engine .
Figure 6: Front View
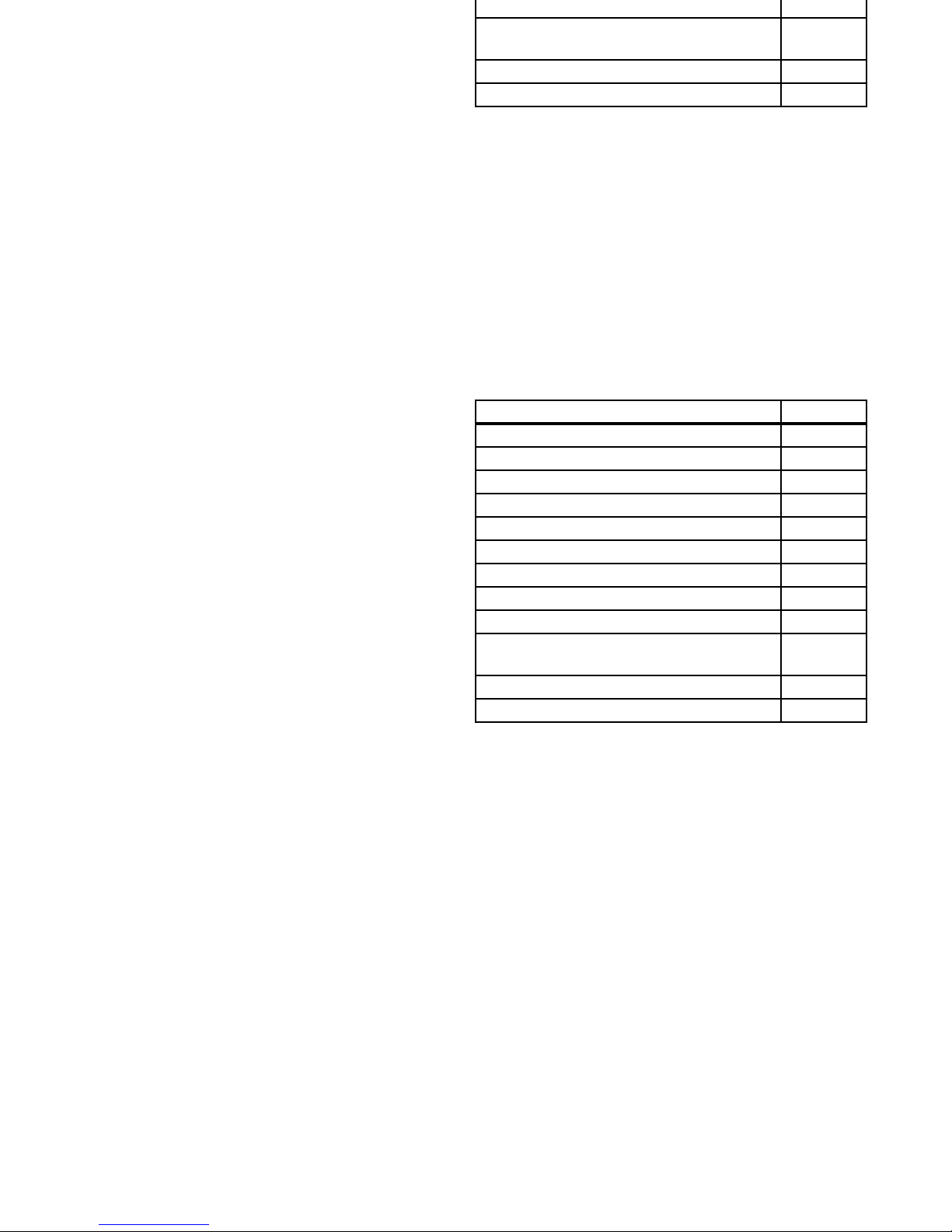
Unit Description
22
Design Features
The following chart lists key design features and options.
● Standard Features
❍ Option/Factory installed
❏ Option/Dealer Installed
Key Features & Options SB-200TG
EMI-3000
●
High-Capacity Condenser Coil ●
Easy-Access D oor Design ●
Composite Exterior Panels ●
Long-Life Coolant/Silicone Hoses ●
Standard Unit Color White ●
Standard Grille Color Black ●
Directional Air Delivery ●
Vibration Isolation System ●
Aluminum Undermount Fuel Tank 50 Gal.
(186 Liter)
●
DAS Data Logger ❍ / ❏
Remote Status Light ❏
Unit Description
22
Design Features
The following chart lists key design features and options.
● Standard Features
❍ Option/Factory installed
❏ Option/Dealer Installed
Key Features & Options SB-200TG
EMI-3000
●
High-Capacity Condenser Coil ●
Easy-Access D oor Design ●
Composite Exterior Panels ●
Long-Life Coolant/Silicone Hoses ●
Standard Unit Color White ●
Standard Grille Color Black ●
Directional Air Delivery ●
Vibration Isolation System ●
Aluminum Undermount Fuel Tank 50 Gal.
(186 Liter)
●
DAS Data Logger ❍ / ❏
Remote Status Light ❏
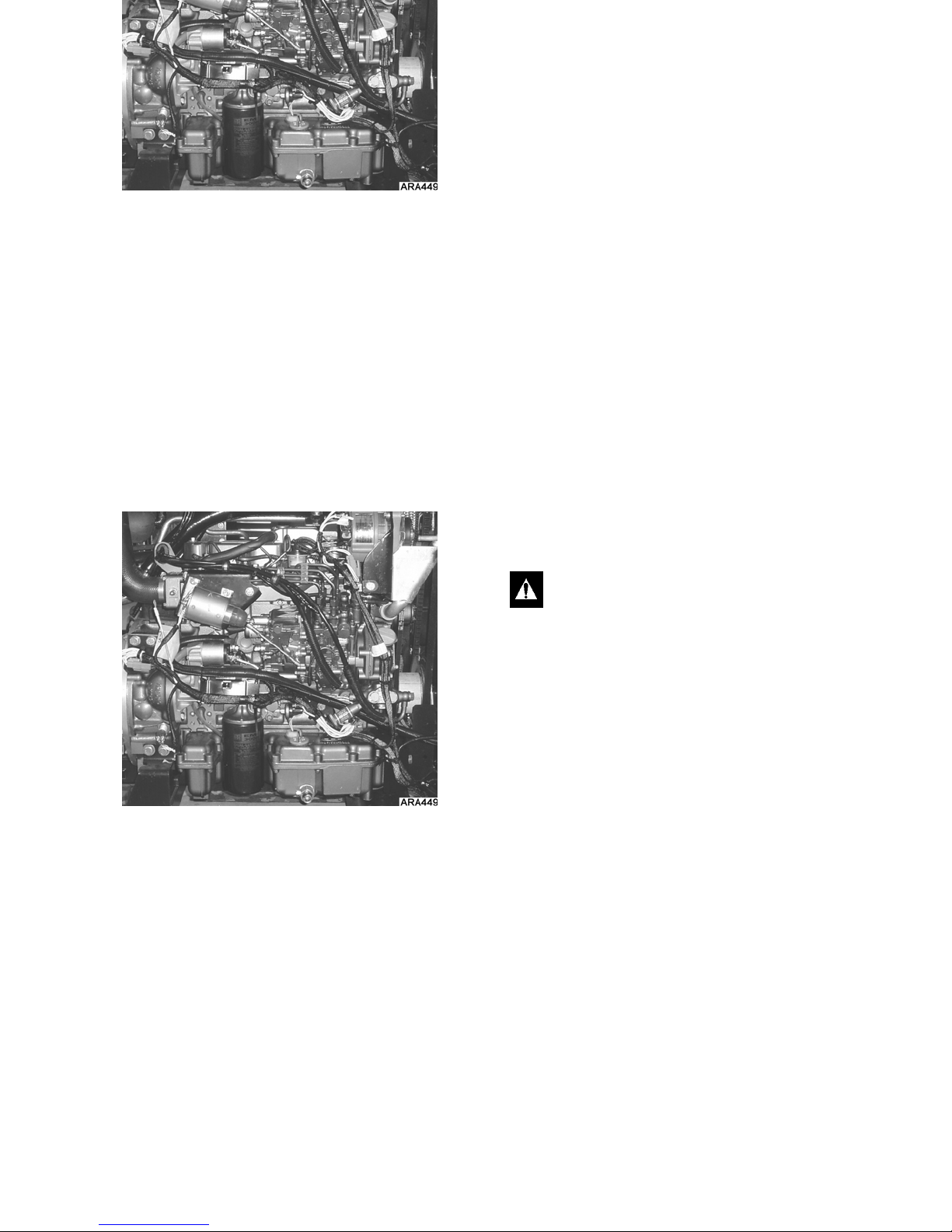
Unit Description
23
Diesel Engine
The unit uses a quiet running TK486V (Tier 2), which is a
4-cylinder, water cooled, direct injection diesel engine. The
engine is coupled directly to the compressor. Belts transmit
power to the unit fans, alternator and water pump.
Figure 7: T K486 V (Tier 2)
ELC (Extended Life Coolant)
ELC (Extended Life Coolant) is standard equipment. The
maintenance interval for ELC is five years or 12,000 hours. A
nameplate on the coolant expansion tank identifies units with
ELC (see “Safety Decals and Locations”). The new engine
coolant, Chevron Extended Life Coolant, is RED in color
instead of the previous GREEN or BLUE-GREEN colored
conventional coolants.
NOTE: The use of 50/50% pre-mixed ELC is recommended
to assure that de-ionized water is being used. If 100% full
strength concentrate is used, de-ionized or distilled water is
recommended instead of tap water to insure the integrity of
the cooling system is maintained.
CAUTION: Do not add “GREEN” or
“BLUE-GREEN” conventional coolant to cooling
systems using “RED” Extended Life Coolant, except
in an emergency. If conventional coolant is added to
Extended Life Coolant, the coolant must be changed
after 2 years instead of 5 years.
Unit Description
23
Diesel Engine
The unit uses a quiet running TK486V (Tier 2), which is a
4-cylinder, water cooled, direct injection diesel engine. The
engine is coupled directly to the compressor. Belts transmit
power to the unit fans, alternator and water pump.
Figure 7: T K486 V (Tier 2)
ELC (Extended Life Coolant)
ELC (Extended Life Coolant) is standard equipment. The
maintenance interval for ELC is five years or 12,000 hours. A
nameplate on the coolant expansion tank identifies units with
ELC (see “Safety Decals and Locations”). The new engine
coolant, Chevron Extended Life Coolant, is RED in color
instead of the previous GREEN or BLUE-GREEN colored
conventional coolants.
NOTE: The use of 50/50% pre-mixed ELC is recommended
to assure that de-ionized water is being used. If 100% full
strength concentrate is used, de-ionized or distilled water is
recommended instead of tap water to insure the integrity of
the cooling system is maintained.
CAUTION: Do not add “GREEN” or
“BLUE-GREEN” conventional coolant to cooling
systems using “RED” Extended Life Coolant, except
in an emergency. If conventional coolant is added to
Extended Life Coolant, the coolant must be changed
after 2 years instead of 5 years.
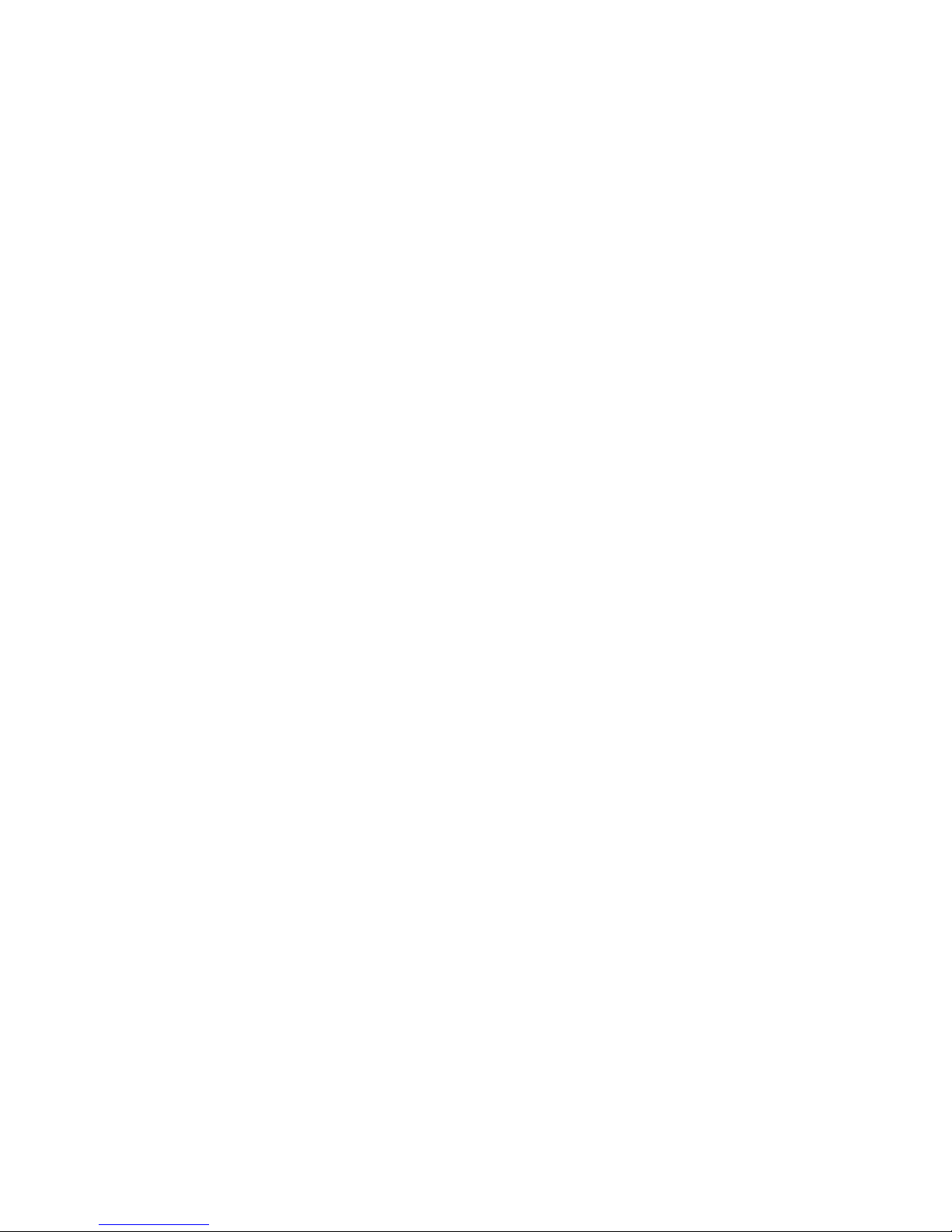
Unit Description
24
EMI 3000
EMI 3000 is an extended maintenance interval package. It is
standard equipment. The EMI 3000 package consists of the
following key components:
• New EMI 3000-Hour Cyclonic Air Cleaner Assembly an d
Air Cleaner Element
• New EMI 3000-Hour Fuel Filter (black with gold
lettering)
• New EMI 3000-Hour Dual Element Oil Filter (black with
gold lettering)
• API Rating CI-4 Mineral Oil
• Five Year or 12,000 Hour ELC (Extended Life Coolant)
The EMI package allows standard maintenance intervals to be
extended to 3,000 hours, or 2 years, whichever occurs first.
NOTE: Units equipped with the EMI 3000 package do
require regular inspection in accordance with Thermo King's
maintenance recommendations.
NOTE: The new EMI 3000 oil filters and new EMI 3000 air
cleaners are NOT interchangeable with the older style oil
filters and air cl eaners.
Thermo King X430L Compressor
The unit is equipped with a Ther mo King X430L, four -cylinder
compressor with 30 cu. in. (492 cm
3
) displacement. The unit is
also equipped with a compressor oil filter.
Unit Description
24
EMI 3000
EMI 3000 is an extended maintenance interval package. It is
standard equipment. The EMI 3000 package consists of the
following key components:
• New EMI 3000-Hour Cyclonic Air Cleaner Assembly an d
Air Cleaner Element
• New EMI 3000-Hour Fuel Filter (black with gold
lettering)
• New EMI 3000-Hour Dual Element Oil Filter (black with
gold lettering)
• API Rating CI-4 Mineral Oil
• Five Year or 12,000 Hour ELC (Extended Life Coolant)
The EMI package allows standard maintenance intervals to be
extended to 3,000 hours, or 2 years, whichever occurs first.
NOTE: Units equipped with the EMI 3000 package do
require regular inspection in accordance with Thermo King's
maintenance recommendations.
NOTE: The new EMI 3000 oil filters and new EMI 3000 air
cleaners are NOT interchangeable with the older style oil
filters and air cl eaners.
Thermo King X430L Compressor
The unit is equipped with a Ther mo King X430L, four -cylinder
compressor with 30 cu. in. (492 cm
3
) displacement. The unit is
also equipped with a compressor oil filter.

Unit Description
25
TG-VI Microprocessor Controller
Thermo King has applied the newest technological advances to
develop a programmable microprocessor controller that
controls unit functioning and displays operating information
quickly and accurately .
Features include:
Thermometer: Displays return air temperature with 0.1
degree accuracy.
Thermostat: Provides temperature control from -20 to 80 F
(- 28 to 27 C) in 1.0 degree increments.
Defrost Control: The controller is programmed to
automatically initiate timed or demand defrost cycles. The
operator can also manually initiate a defrost cycle. See
“Defrost” on page 27.
Alarm: Can detect and display alarm conditions. Refer to the
Operating and Alarm Codes Sections later in this manual.
1. Control Panel 4. Computer Port (Optional)
2. Display 5. Printer Port (Optional)
3. Keypad 6. On/Off Switch
Figure 8: Control and Switch Panels
ANA03
AJA1070
4
1
2
3
5
6
COMPUTER PRINTER
Unit Description
25
TG-VI Microprocessor Controller
Thermo King has applied the newest technological advances to
develop a programmable microprocessor controller that
controls unit functioning and displays operating information
quickly and accurately .
Features include:
Thermometer: Displays return air temperature with 0.1
degree accuracy.
Thermostat: Provides temperature control from -20 to 80 F
(- 28 to 27 C) in 1.0 degree increments.
Defrost Control: The controller is programmed to
automatically initiate timed or demand defrost cycles. The
operator can also manually initiate a defrost cycle. See
“Defrost” on page 27.
Alarm: Can detect and display alarm conditions. Refer to the
Operating and Alarm Codes Sections later in this manual.
1. Control Panel 4. Computer Port (Optional)
2. Display 5. Printer Port (Optional)
3. Keypad 6. On/Off Switch
Figure 8: Control and Switch Panels
ANA03
AJA1070
4
1
2
3
5
6
COMPUTER PRINTER

Unit Description
26
Depending on the air temperature in the trailer sensed by the
TG-VI Microprocessor Controller, the unit will operate in one
of the following modes:
In Continuous Run Operation Mode:
• High Speed Co ol
• Low Speed Cool
• Low Speed Heat
• High Speed Heat
•Defrost.
In CYCLE-SENTRY Operation Mode:
• High Speed Cool
• Low Speed Cool
• Null (Engine Off)
• Low Speed Heat
• High Speed Heat
•Defrost.
Generally, the unit will operate in low speed switching back
and forth from cooling to heating as necessary, thus controlling
the temperature in the trailer.
On very hot days, with the setpoint at a low temperature, the
unit may cycle between high speed cool and low speed cool
without switching into a heating cycle.
On very cold days, the unit may cycle between high speed heat
and low speed heat. The unit may switch into cooling for short
periods of time.
CAUTION: Firmly close the controller access door
after operating the microprocessor controller or
before starting a trip. The control panel might be
damaged in transit if the door is not firmly closed.
Unit Description
26
Depending on the air temperature in the trailer sensed by the
TG-VI Microprocessor Controller, the unit will operate in one
of the following modes:
In Continuous Run Operation Mode:
• High Speed Co ol
• Low Speed Cool
• Low Speed Heat
• High Speed Heat
•Defrost.
In CYCLE-SENTRY Operation Mode:
• High Speed Cool
• Low Speed Cool
• Null (Engine Off)
• Low Speed Heat
• High Speed Heat
•Defrost.
Generally, the unit will operate in low speed switching back
and forth from cooling to heating as necessary, thus controlling
the temperature in the trailer.
On very hot days, with the setpoint at a low temperature, the
unit may cycle between high speed cool and low speed cool
without switching into a heating cycle.
On very cold days, the unit may cycle between high speed heat
and low speed heat. The unit may switch into cooling for short
periods of time.
CAUTION: Firmly close the controller access door
after operating the microprocessor controller or
before starting a trip. The control panel might be
damaged in transit if the door is not firmly closed.
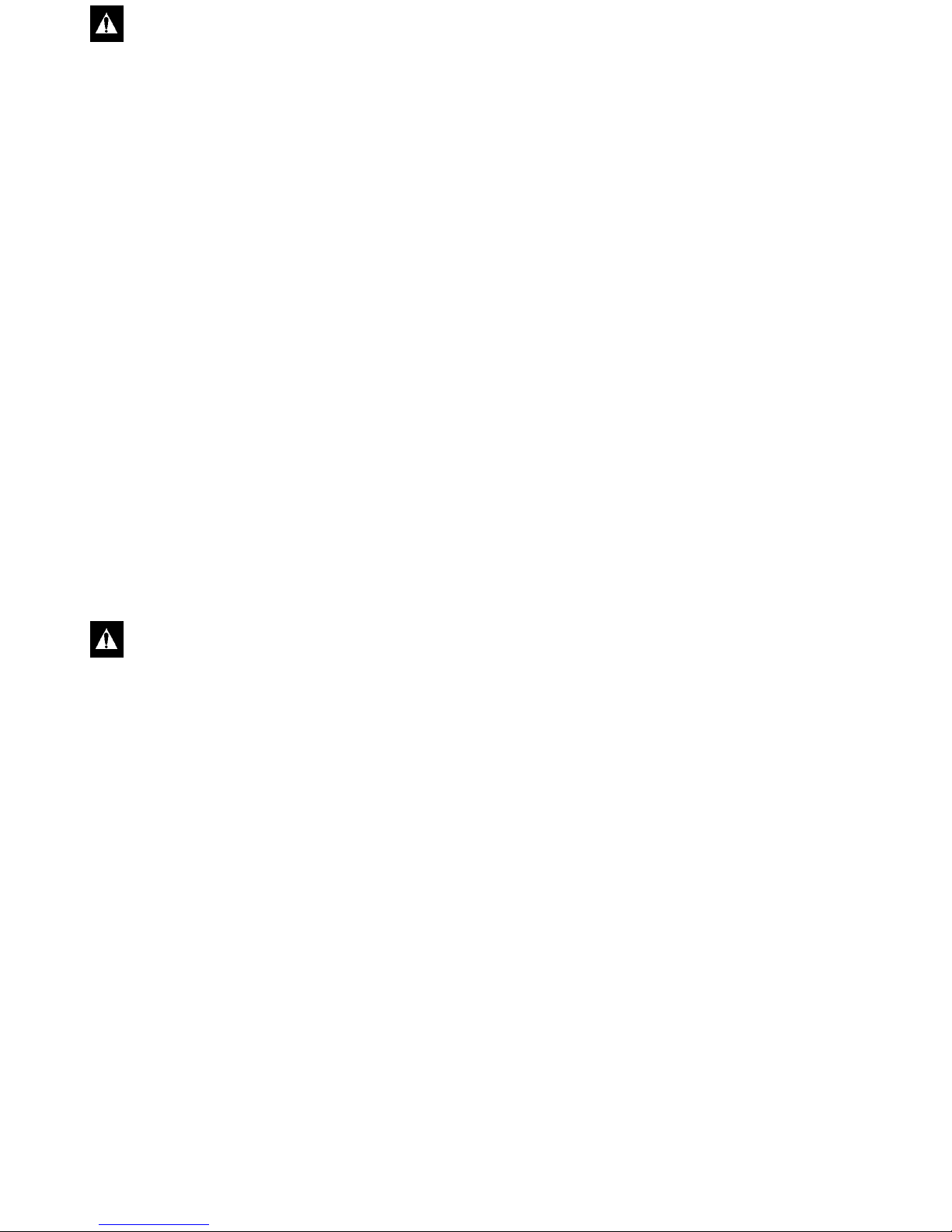
Unit Description
27
CYCLE-SENTRY Start-Stop Controls
The CYCLE-SENTRY Start-Stop fuel saving system provides
optimum operating economy.
CYCLE-SENTRY automatically starts the unit on
microprocessor demand, and shuts down the unit when all
demands are satisfied.
The system automatically monitors and maintains
compartment temperatures, the engine block temperature and
battery charge levels at a point where quick, easy starts are
possible.
Defrost
Frost gradually builds-up on evaporator coils as a result o f
normal operation. The unit uses hot refrigerant to defrost the
evaporator coils. Hot refrigerant gas passes through the
evaporator coil and melts the frost. The water flows through
collection drain tubes onto the ground. The methods of defrost
initiation are Manual and Automatic.
Automatic Defrost: The controller is programmed to
automatically initiate timed or demand defrost cycles. Defrost
intervals are set at the factory at 2, 4 6, 8, 10, or 12 hours. The
unit can enter a demand defrost cycle as often as every 30
minutes if required.
Manual Defrost: The operator manually initiates a defrost
cycle.
NOTE: The unit will not perform a Manual Defrost cycle
unless the O
N/OFF switch is set to ON, the unit is running in
Continuous or CYCLE -SENTRY mode, (or shut down in
CYCLE-SENTRY Null mode), and the coil temperature is
below 45 F (7.2 C).
WARNING: Set the unit ON/OFF switch to OFF
before opening doors or inspecting any part of the
unit. With the unit O
N/OFF switch in the ON position,
the unit may start at any time without warnin g.
Unit Description
27
CYCLE-SENTRY Start-Stop Controls
The CYCLE-SENTRY Start-Stop fuel saving system provides
optimum operating economy.
CYCLE-SENTRY automatically starts the unit on
microprocessor demand, and shuts down the unit when all
demands are satisfied.
The system automatically monitors and maintains
compartment temperatures, the engine block temperature and
battery charge levels at a point where quick, easy starts are
possible.
Defrost
Frost gradually builds-up on evaporator coils as a result o f
normal operation. The unit uses hot refrigerant to defrost the
evaporator coils. Hot refrigerant gas passes through the
evaporator coil and melts the frost. The water flows through
collection drain tubes onto the ground. The methods of defrost
initiation are Manual and Automatic.
Automatic Defrost: The controller is programmed to
automatically initiate timed or demand defrost cycles. Defrost
intervals are set at the factory at 2, 4 6, 8, 10, or 12 hours. The
unit can enter a demand defrost cycle as often as every 30
minutes if required.
Manual Defrost: The operator manually initiates a defrost
cycle.
NOTE: The unit will not perform a Manual Defrost cycle
unless the O
N/OFF switch is set to ON, the unit is running in
Continuous or CYCLE -SENTRY mode, (or shut down in
CYCLE-SENTRY Null mode), and the coil temperature is
below 45 F (7.2 C).
WARNING: Set the unit ON/OFF switch to OFF
before opening doors or inspecting any part of the
unit. With the unit O
N/OFF switch in the ON position,
the unit may start at any time without warnin g.
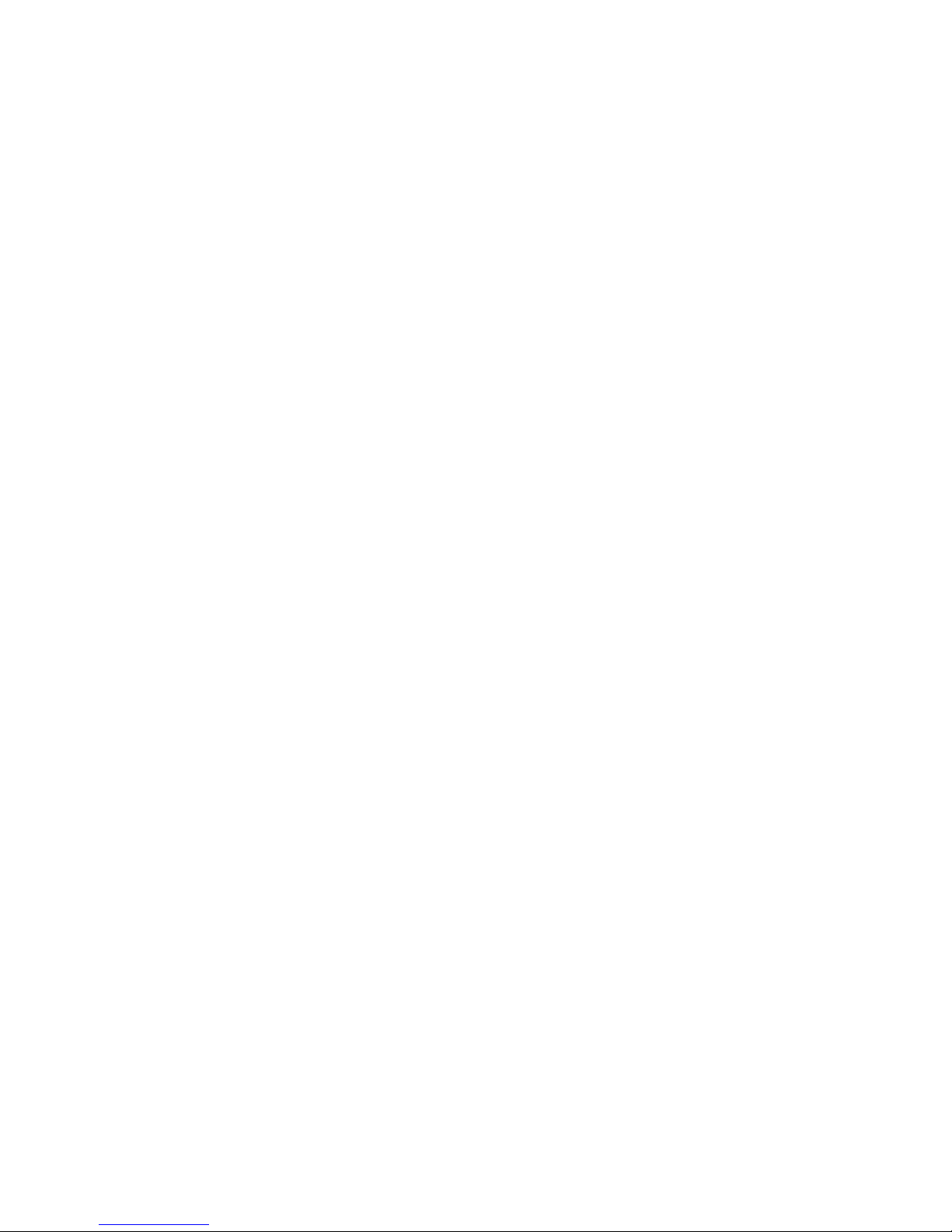
Unit Description
28
DAS (Optional)
The DAS (Data Acquisition System) is an independent data
logger that logs information from dedicated external DAS
sensors and inputs. The DAS features (up to six) directly
connected sensors. The DAS is also connected through a serial
port to the unit microprocessor. Sensor readings can be viewed
on the microprocessor keyboard panel using the S
ELECT key.
See “Figure 8: Control and Switch Panels,” on page 25. The
DAS allows unit operating information, operating events,
alarm codes and compartment temperatures to be logged as
well. The data can be retrieved using an IBM
®
PC compatible
laptop or desktop comp uter and Thermo King WinTrac 4.1 (or
higher) software. The computer is connected to the computer
port on the front of t he control box . See “Figur e 8: Control and
Switch Panels,” on pag e 25. Detaile d graph or ta ble trip repo rts
can then be created.
A hand-held printer can be connected to the printe r por t on th e
front of the control box to print out the DAS sensor readings.
Refer to the DAS Data Acquisition System Manual TK 50565
for more information.
Unit Description
28
DAS (Optional)
The DAS (Data Acquisition System) is an independent data
logger that logs information from dedicated external DAS
sensors and inputs. The DAS features (up to six) directly
connected sensors. The DAS is also connected through a serial
port to the unit microprocessor. Sensor readings can be viewed
on the microprocessor keyboard panel using the S
ELECT key.
See “Figure 8: Control and Switch Panels,” on page 25. The
DAS allows unit operating information, operating events,
alarm codes and compartment temperatures to be logged as
well. The data can be retrieved using an IBM
®
PC compatible
laptop or desktop comp uter and Thermo King WinTrac 4.1 (or
higher) software. The computer is connected to the computer
port on the front of t he control box . See “Figur e 8: Control and
Switch Panels,” on pag e 25. Detaile d graph or ta ble trip repo rts
can then be created.
A hand-held printer can be connected to the printe r por t on th e
front of the control box to print out the DAS sensor readings.
Refer to the DAS Data Acquisition System Manual TK 50565
for more information.
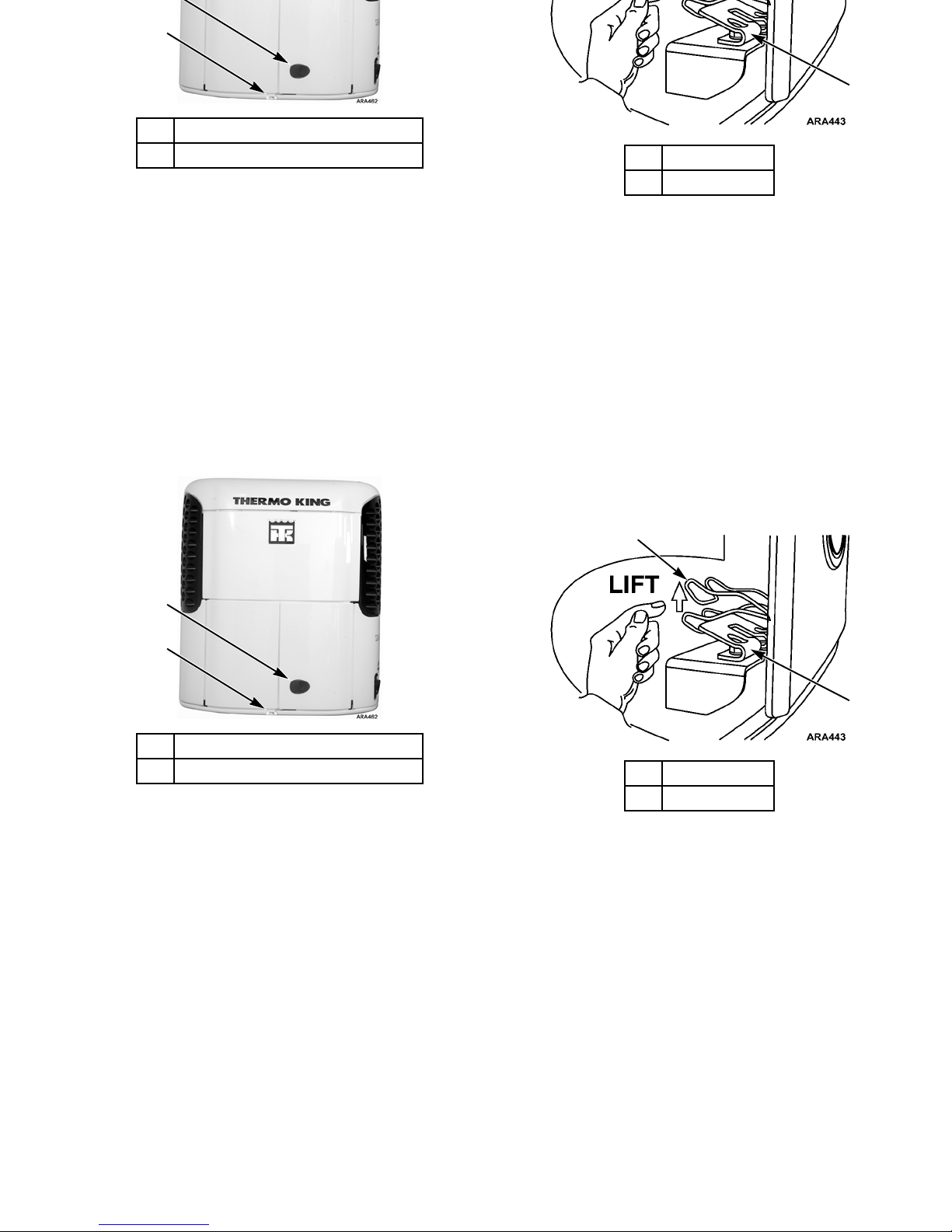
Unit Description
29
Opening the Front Doors
Pull the door latch handle to open the door and access the
engine compartment.
Opening the Secondary Door Latch
These units are also equipped with a secondary door latch. A
secondary door latch nameplate is located below the front
doors. After opening the door latch, reach between the front
doors and lift the spring latch over the spring catch while
opening the door.
1. Door Latch
2. Secondary Door Latch Nameplate
Figure 9: Door Latch Location
1
2
1. Spring Latch
2. Spring Catch
Figure 10: Opening Secondary Door Latch
Unit Description
29
Opening the Front Doors
Pull the door latch handle to open the door and access the
engine compartment.
Opening the Secondary Door Latch
These units are also equipped with a secondary door latch. A
secondary door latch nameplate is located below the front
doors. After opening the door latch, reach between the front
doors and lift the spring latch over the spring catch while
opening the door.
1. Door Latch
2. Secondary Door Latch Nameplate
Figure 9: Door Latch Location
1
2
1. Spring Latch
2. Spring Catch
Figure 10: Opening Secondary Door Latch