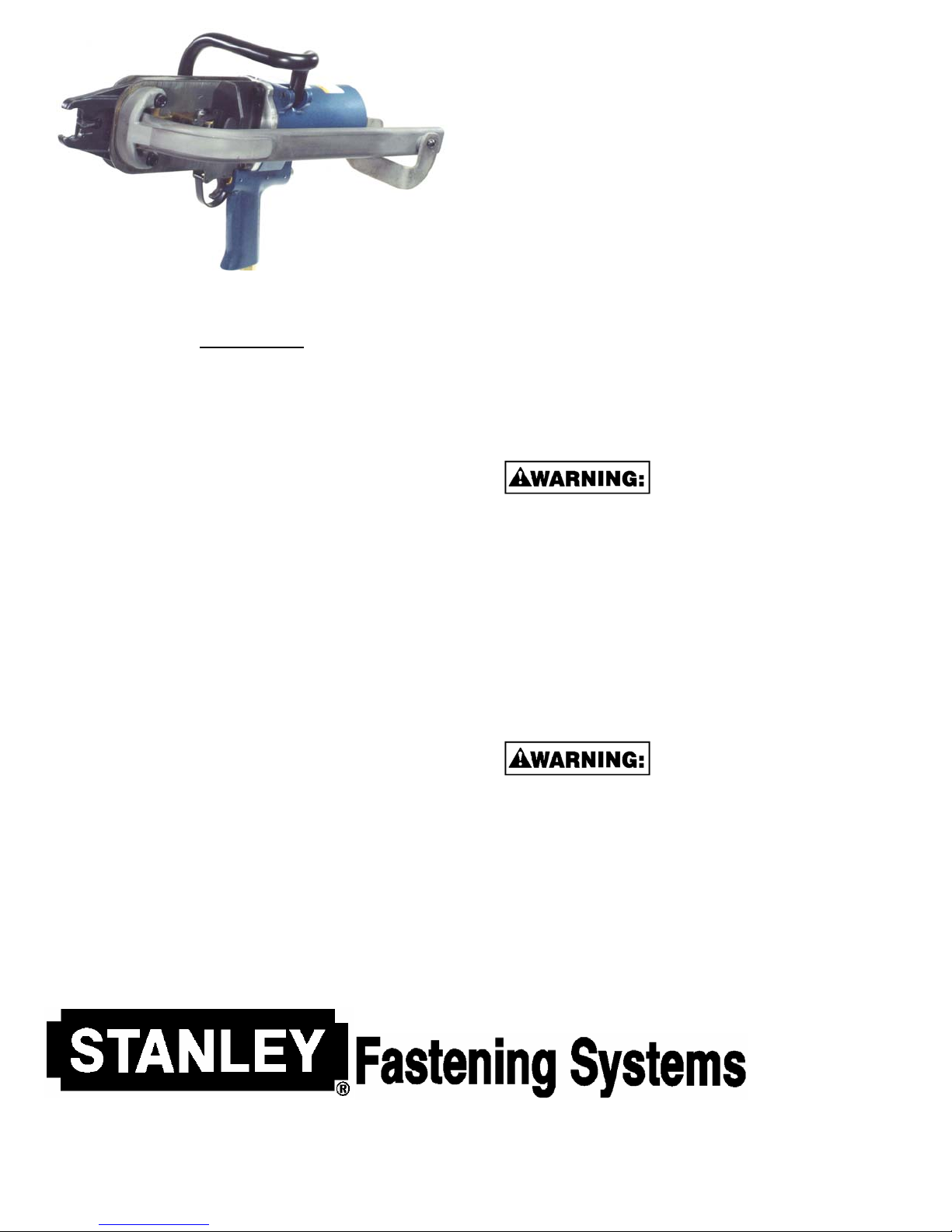
WARNINGS
• Always read tool manual before operating.
• Always wear safety glasses while operating or
while in the vicinity of a tool in operation.
• For testing, always cycle tool away from work
to insure proper ring closure. For safety
reasons, an improperly functioning tool must
not be used. When operating tool, never point
or actuate tool other than into work.
• Operate tool in an unobstructed work area.
• Disconnect air supply prior to servicing,
maintenance/repairs and when tool is not in use.
• Use clean dry air to maximize efficiency. Do
Not Exceed 105 P.S.I. (7.2 bars)
• Do not use bottled gases such as oxygen,
hydrogen, carbon dioxide, acetylene, etc.
• Tools shall be operated with a fitting or hose
coupling on or near the tool in such a manner
that all compressed air in the tool is discharged
at the time the fitting or hose coupling is
disconnected. Use ¼-18 NPT or equivalent
fitting when connecting to the tool.
PNEUMATIC C-RING TOOL
SC50T
SAFETY INSTRUCTIONS
WARNING:
The employer and/or user must ensure that proper eye
protection is worn. Eye protection equipment must
conform to the requirements of the American National
Standard Institute, ANSI Z87.1-1989 and provide
frontal and side protection. Eye protection shall be
worn by the operator and others in the work area when
loading, operating, or servicing this tool. Eye
protection is required to guard against possible flying
particles and/or debris, which could cause severe eye
injury.
NOTE: Non-side shielded prescription glasses and
faceshields alone do not provide adequate protection.
OPERATION
Always handle tool with care:
• Never engage in horseplay.
• Never pull the trigger unless nose of tool is
directed toward the work.
• Keep others at a safe distance from the tool while
the tool is in operation as actuation occurs,
possibly causing injury. Keep hands and body
away from the jaw mechanism of the tool.
LOADING TOOL
When loading tool:
• Never place a hand or any part of body in jaw
mechanism area of tool.
• Never point tool at anyone.
• Never actuate tool when loading, accidental injury
may occur.
AIR CONSUMPTION
SC50T Tool require 10.4 cubic feet per minute (.293
cubic meters per minute) of free air to operate at a rate
of 100 cycles per minute, at 100 P.S.I. (6.9 bars).
1 of 6 01/03
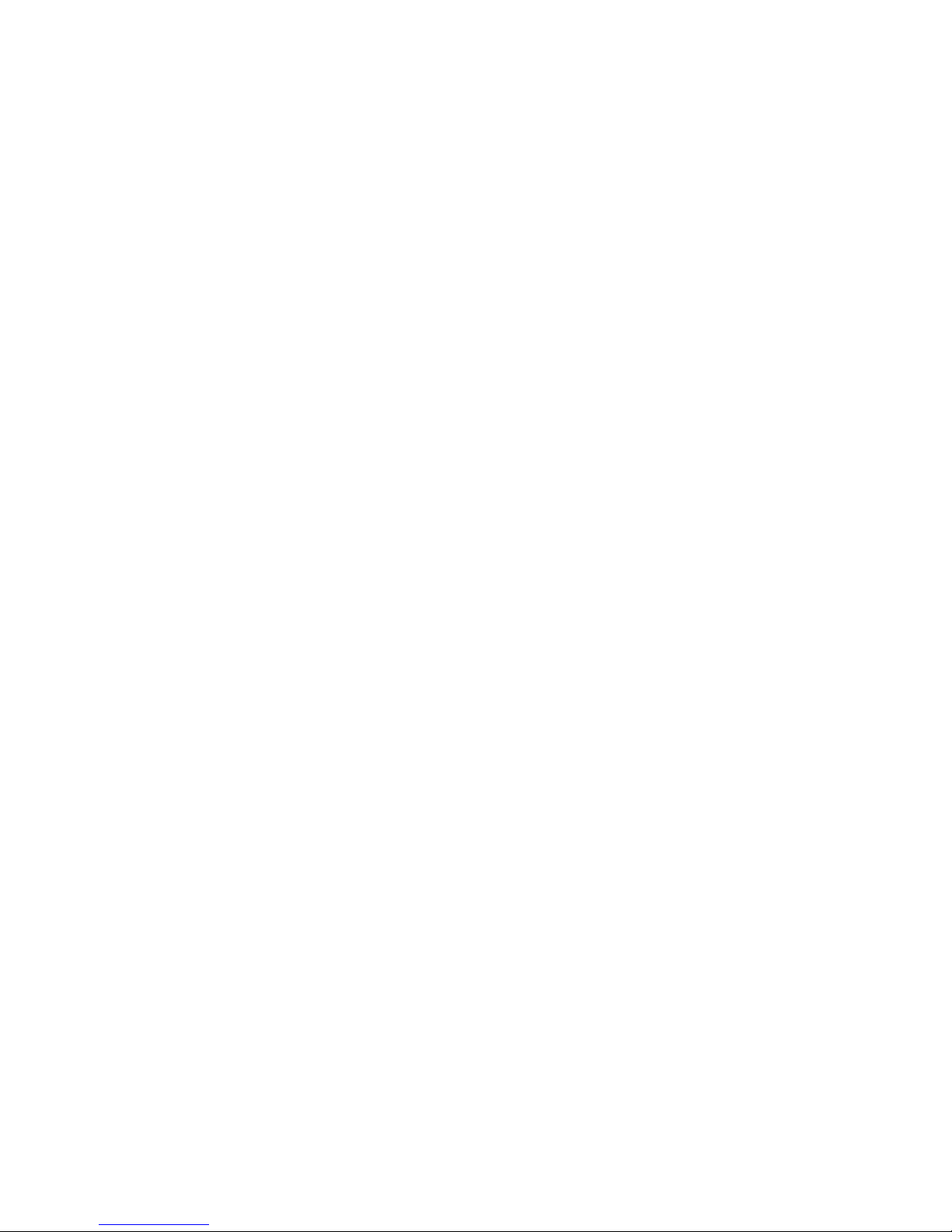
TO DISASSEMBLE
Jaws, magazine and pusher assembly
1. Remove flexloc nuts, washers, support plate, latch spring
and jaw bolts (#35, #34, #68, #37 and #61).
2. Remove buttom head socket cap screw (#67) and lock
washer (#66) from feeder arm (#65).
3. Magazine assembly (#62) and spring bracket assembly
(#58) may now be removed.
4. Drive out jaw bushings (#32) and remove jaws (#31 and
#41).
5. Remove (2) flexlock nuts (#72) from studs (#16) at rear of
tool and remove feeder arm bracket (#65).
Feeder blade, rollers, piston rod
1. Remove button head screw and washer (#51 and #50) from
trigger guard and (4) cap screws with lock washers (#30 and
#29) in front end assembly (with piston) from cylinder
housing.
2. Remove piston (#24), o-ring (#22), flexlock nut (#23)
piston stop spacer assembly (#26), piston rod assembly with
piston rod (#43), feeder blade (#40), (2) roller pins (#42)
and (4) rollers (#39) from the front end assembly.
Throttle
1. Loosen set screws (#19) on both ends. Do not loosen
center set screw #19.
2. Do not remove throttle valve bushing (#15), location is
pre-set at Spenax.
3. Remove air deflector parts (#1, #2, #3 and #4).
4. Remove rear valve seat (#5).
5. Remove throttle spring and locator parts (#7 and #8).
6. Remove front valve seat (#48) and throttle stem (#47) using
a 3/16” wrench.
7. Using two 9/64” Allen wrenches, unscrew throttle valve
screws (#9) to remove valve units. Hint: Hold tool so that
the valve is vertical to help prevent loosing parts.
8. One valve screw will remain with other valve parts on
spacer (#14), and can be disassembled after removal from
housing.
TO RE-ASSEMBLE
1. Assemble one side of the o-ring support assembly (#9, #10,
#11, #12, #13, #12, and #11) on spacer (#14). The chamfer
on both washers (#10) should be installed, with chamfer
side against cap screw head (#9).
2. Hold tool vertically and install o-ring support assembly with
spacer into bushing from the top.
3. Holding cap screw with an Allen wrench, bring second oring support assembly (mounted on screw (#9)) in from the
opposite side and complete valve assembly. The valve
should have free motion of travel of about 3/32”
[.09”(2.3mm)].
4. Insert valve spring locator and spring (#8 and #7) into the
rear of the valve.
5. Screw rear valve seat with lubricated o-ring (#5 and #6) into
rear of the valve port.
6. Insert throttle stem (#47) into front valve seat (#48) and
slowly screw front valve seat with lubricated o-ring (#6)
into front of the valve port. (See Throttle Valve
Adjustment).
7. Assemble piston stop spacer assembly (#26), piston (#24),
piston rod (#43) and nylock nut (#23) together. Be careful
not to damage o-ring (#21) when pushing stop spacer onto
piston rod, use lubrication. Place piston so that the
extended neck is opposite the nylock nut. Nylock nut at rear
of piston must be Loctited into place (Loctite #242 or
equivalent). Place o-ring (#22) onto piston.
8. Mount feeder blade (#40) and two roller pins (#42) on
piston rod (#43).
9. Place (4) rollers (#39) on the (2) roller pins (#42).
Lubrication will hold the rollers in place while assembling
the rest of the tool.
10. Mount latch (#38) onto side plate (#28R) with latch pin clip
(#36).
11. Assemble trigger, (2) spacers and trigger guard (#44, #33
and #49) to the side plates with (3) roll pins (#45).
12. Mount side plate assembly (#28R, #28L, #44, #33 and #49)
over stop spacer assembly.
13. Place cylinder gasket (#25) between the stop spacer and the
housing.
14. Insert front end assembly into the cylinder housing. Be
careful not to damage o-ring (#22) when pushing piston into
the cylinder bore, use lubrication.
15. Secure front end assembly with (4) lock washers and cap
screws (#29 and #30).
16. Leave trigger guard loose for adjusting the valve. See
throttle valve adjustment procedure for proper valve
adjustment instructions.
17. Mount feeder arm (#65) onto the studs at rear of the
cylinder housing with two nylock nuts (#72).
18. Place spring bracket assembly (#58) between magazine
assembly (#62) and side plate (#28L). If unassembled see
Pusher Spring Installation Procedure.
19. Attach the magazine assembly (#62) to the feeder arm (#65)
with lock washer and button head cap screw (#66 and #67).
But do not tighten completely.
20. Place jaws (#31 and #41) between the side plates (#28R and
#28L).
21. Install (2) jaw bushings (#32) through side plate, jaws and
side plate (#28R, #31, #41 and #28L). Lubricate both jaws
and bushings before installing them.
22. Place (1) .030” magazine shim (#60A) and (1) .010”
magazine shim (#60C) under the foot of magazine (#62),
between magazine and side plate. Other shims may be
added or subtracted to get the proper drop in the magazine
shoe (See Installation Procedure/Adjustments).
23. Insert (2) jaw bolts (#61) through magazine, shims, spring
spool bracket, side plate, jaw bushing, side plate, latch
spring (#37), support plate (#68) and (2) washers (#34).
Secure jaw bolts with (2) nylock nuts (#35). Do not over
tighten jaw bolts, jaws must still pivot freely.
24. Tighten button head cap screw (#67)
25. After all adjustments to the tool are made, the trigger guard
is secured with button head screw and washer (#51 and
#50).
INSTALLATION PROCEDURE / ADJUSTMENTS
Magazine
1. Before tightening jaw bolts (#61), insert approximately
.040” of shims.
2. Tighten bolts and check shoe (#70) for proper fit. Shoe
should have approximately .020”(.50mm) float up and
down.
3. When shimmed correctly, and with the feeder blade in the
forward position, the shoe will be approximately in the
center of the available amount of travel.
4. Cycle tool and check for proper closure of ring. If feeder
blade hits rear of shoe, add another shim. Shims (#60A &
B) are available in two thickness’ of .030”(.762mm) and
.010”(.25mm).
5. When the tool is completely re-assembled, check to insure
that magazine (#62) is parallel to housing (#17).
4 of 6 01/03