
CDX-715
SERVICE MANUAL
SPECIFICATIONS
System Compact disc digital audio system
Laser diode properties Material: GaAlAs
Wavelength: 780 nm
Emission Duration: Continuous
Laser out-put Power: Less than 44.6 µW*
* This output is the value measured at a
distance of 200 mm from the objective lens
surface on the Optical Pick-up Block.
Frequency response 10 – 20,000 Hz
Wow and flutter Below the measurable limit
Signal-to-noise ratio 94 dB
Outputs BUS control output (8 pins)
Analog audio output (RCA pin)
US Model
Canadian Model
AEP Model
UK Model
E Model
Model Name Using Similar Mechanism NEW
CD Drive Mechanism Type MG-250B-137
Optical Pick-up Name KSS-521A/J2N
Currnet drain 800 mA (during CD playback)
800 mA (during loading or ejecting a disc)
Operating temperature –10˚C to +55˚C (14˚F to 131˚F)
Dimensions Approx. 262 × 90 × 181.5 mm
(10 3/8 × 3 5/8 × 7 1/4 in.)
(w/h/d)
not incl. projecting parts and controls
Mass Approx. 2.1 kg (4 lb. 10 oz.)
Power requirement 12 V DC car battery (negative ground)
Supplied accessories Disc magazine (1)
Parts for installation and connections (1 set)
Design and specifications subject to change without notice.
MICROFILM
COMPACT DISC CHANGER
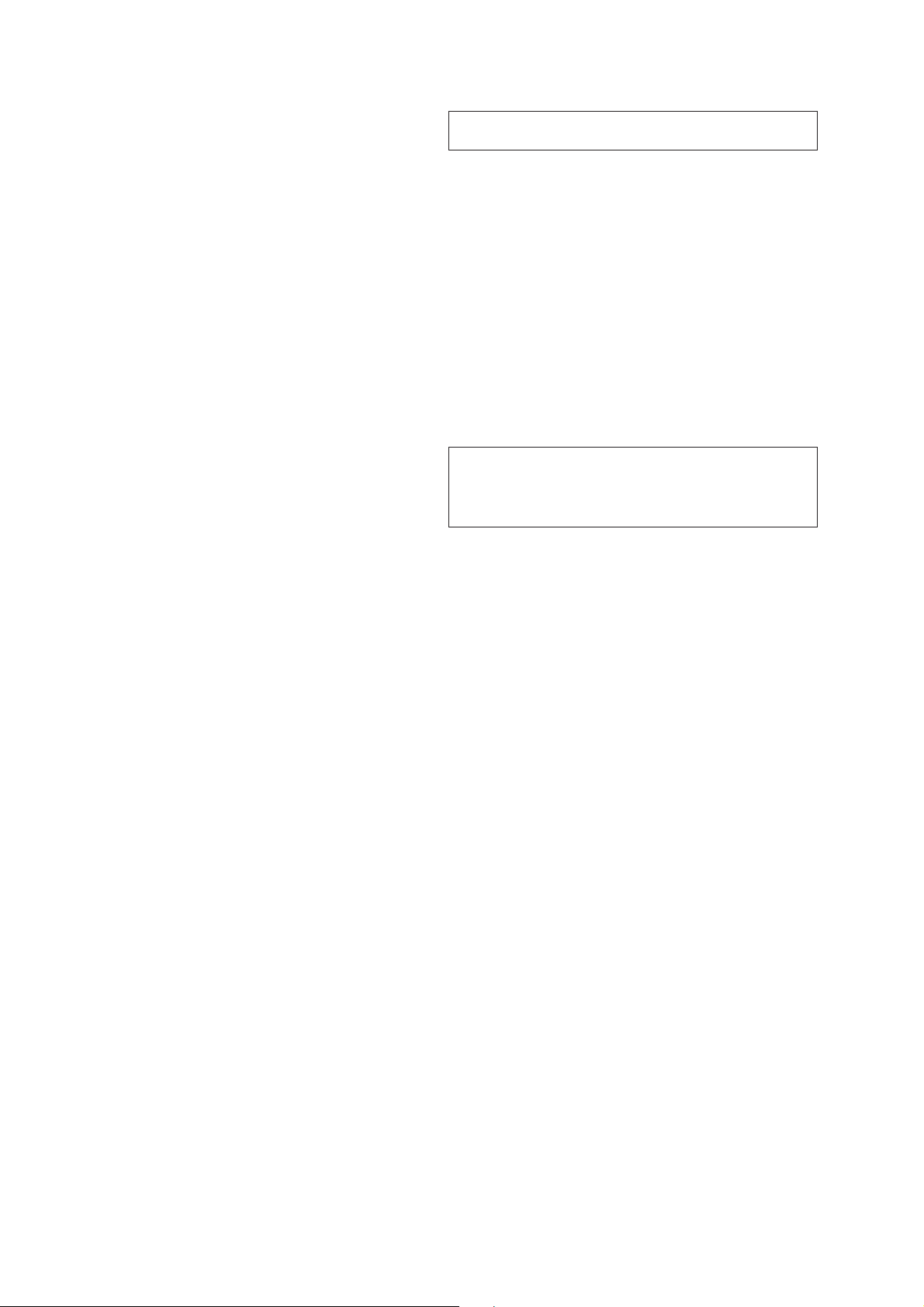
SECTION 1
SERVICE NOTE
TABLE OF CONTENTS
1. SERVICE NOTE ........................................................ 2
2. GENERAL
Installation....................................................................... 5
Connections ..................................................................... 6
3. DISASSEMBLY ......................................................... 8
4. MECHANISMDECK ASSEMBLY...................... 14
5. MECHANICAL ADJUSTMENTS....................... 18
6. ELECTRICAL ADJUSTMENTS......................... 19
7. DIAGRAMS
7-1. Block Diagram
– SERVO Section – ......................................................... 21
– MAIN Section – ........................................................... 23
7-2. Printed Wiring Boards – RF Section – .......................... 25
7-3. Schematic Diagram – RF Section –................................ 27
7-4. Printed Wiring Board
– MAIN Section – MAIN Board (Component side) ...... 29
– MAIN Section – MAIN Board (Conductor side)........ 31
7-5. Schematic Diagram
– MAIN Section – MAIN Board (1/2) ........................... 33
– MAIN Section – MAIN Board (2/2) ........................... 35
7-6. Printed Wiring Board – JACK Section –....................... 37
7-7. Schematic Diagram – JACK Section –........................... 38
7-8. IC Pin Function Description ........................................... 45
8. EXPLODED VIEWS ................................................ 47
9. ELECTRICAL PARTS LIST ............................... 52
NOTES ON HANDLING THE OPTICAL PICK-UP
BLOCK OR BASE UNIT
The laser diode in the optical pick-up block may suffer electrostatic breakdown because of the potential difference generated by
the charged electrostatic load, etc. on clothing and the human body .
During repair, pay attention to electrostatic breakdown and also
use the procedure in the printed matter which is included in the
repair parts.
The flexible board is easily damaged and should be handled with
care.
Laser Diode Properites
• Material: GaAlAs
• Wavelength: 780 nm
• Emission Duration: continuous
• Laser Output Power: less than 44.6 µW*
* This output is the value measured at a distance of 200 mm
from the objective lens surface on the Optical Pick-up Block.
CAUTION
Use of controls or adjustments or performance of procedures
other than those specified herein may result in hazardous radiation exposure.
Flexible Circuit Board Repairing
• Keep the temperature of the soldering iron around 270 ˚C during repairing.
• Do not touch the soldering iron on the same conductor of the
circuit board (within 3 times).
• Be careful not to apply force on the conductor when soldering
or unsoldering.
Notes on chip component replacement
• Never reuse a disconnected chip component.
• Notice that the minus side of a tantalum capacitor may be damaged by heat.
– 2 –
SAFETY-RELATED COMPONENT WARNING!!
COMPONENTS IDENTIFIED BY MARK ! OR DOTTED
LINE WITH MARK ! ON THE SCHEMATIC DIAGRAMS
AND IN THE PARTS LIST ARE CRITICAL TO SAFE
OPERATION. REPLACE THESE COMPONENTS WITH
SONY PARTS WHOSE PART NUMBERS APPEAR AS
SHOWN IN THIS MANUAL OR IN SUPPLEMENTS PUBLISHED BY SONY.
ATTENTION AU COMPOSANT AYANT RAPPORT
À LA SÉCURITÉ!
LES COMPOSANTS IDENTIFIÉS P AR UNE MARQUE !
SUR LES DIAGRAMMES SCHÉMATIQUES ET LA LISTE
DES PIÈCES SONT CRITIQUES POUR LA SÉCURITÉ
DE FONCTIONNEMENT. NE REMPLACER CES COMPOSANTS QUE PAR DES PIÈCES SONY DONT LES
NUMÉROS SONT DONNÉS DANS CE MANUEL OU
DANS LES SUPPLÉMENTS PUBLIÉS PAR SONY.
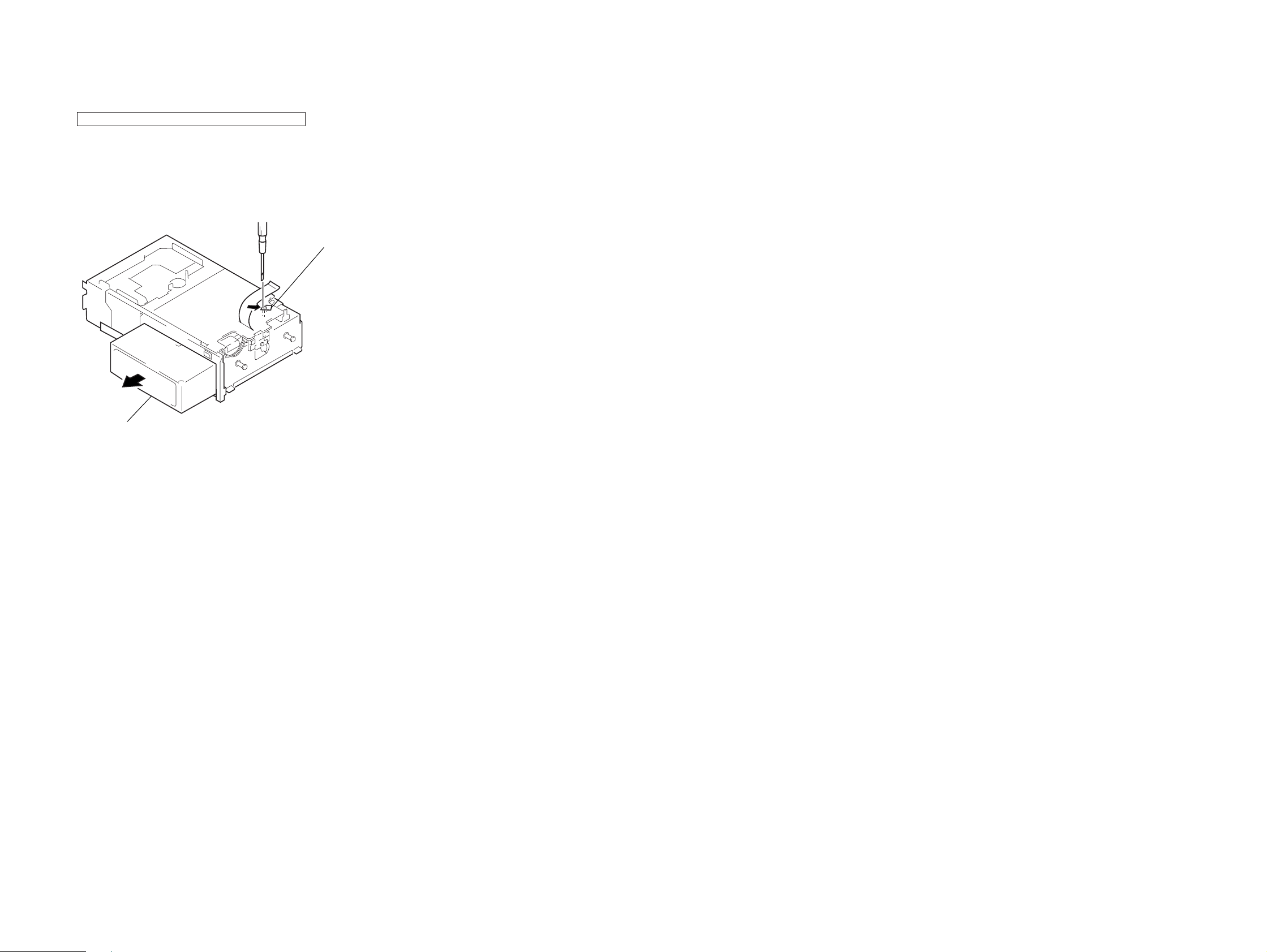
DISC MAGAZINE GETTING OUT PROCEDURE ON
Lever (stop) ass’y
Magazine ass’y
THE POWER SUPPLY IS OFF
Remove the CASE (LOWER) assembly beforehand
1) Press the lever (stop) ass’y to arrow direction.
2) Removal the magazine ass’y.
Note: Take out the magazine only when the tray is completely within the
magazine. If the disc or tray is sticking out, turn on the power and
eject the magazine.
– 3 – – 4 –

This section is extracted from
instruction manual.
SECTION 2
GENERAL
– 5 – – 6 –
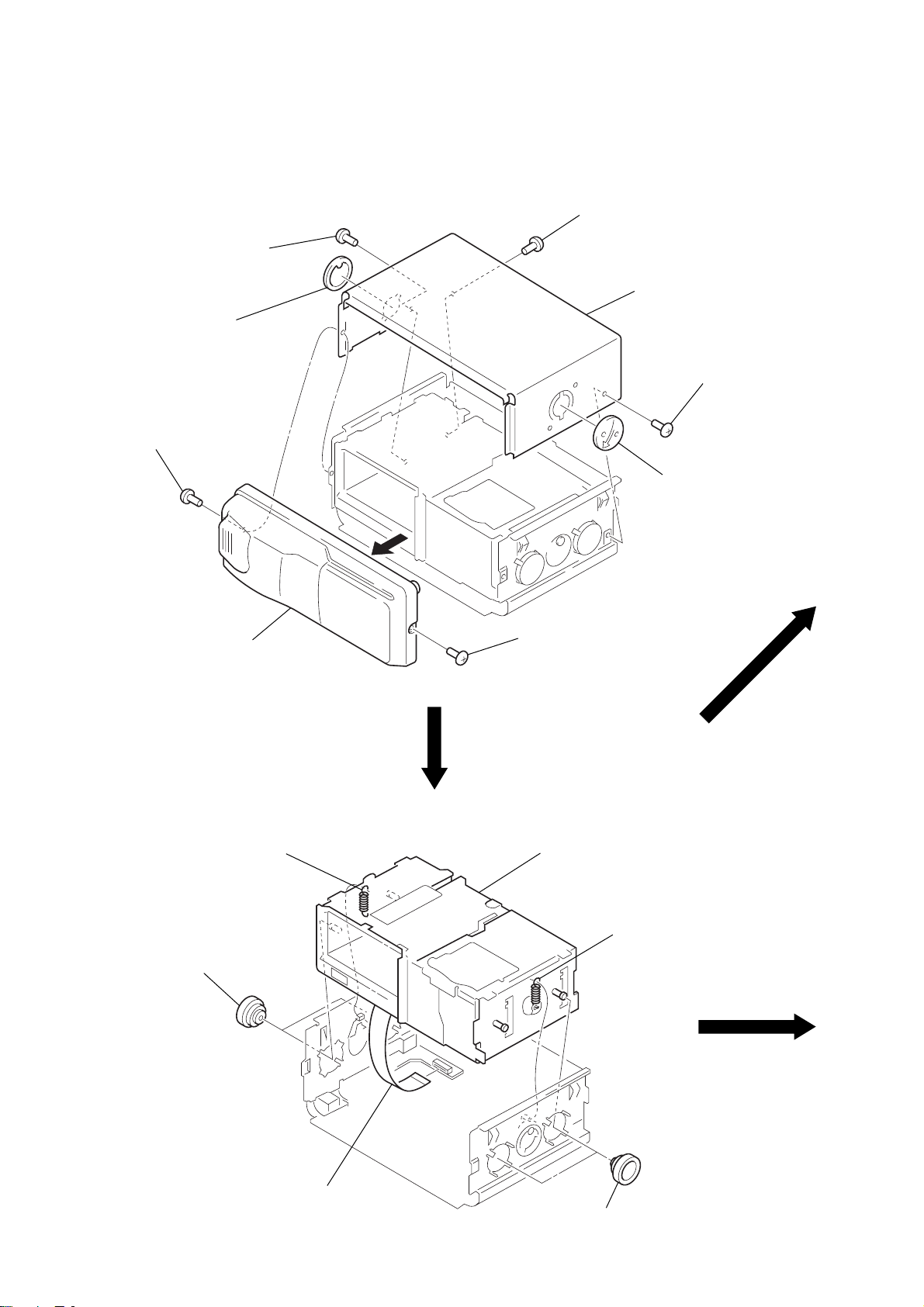
SECTION 3
DISASSEMBLY
Note: Follow the disassembly procedure in the numerical order given.
COVER (UPPER), FRONT PANEL ASS’Y
1
screw
(PTT2.6 × 6)
3
lever (FL)
1
screw
(PTT2.6 × 6)
1
screw
(PTT2.6 × 6)
2
case (upper)
3
1
screw
(PTT2.6 × 6)
lever (FL)
4
front panel ass’y
MECHANISM DECK (MG-250B-137)
2
spring (FL)
1
two dampers (250)
1
screw
(PTT2.6 × 6)
4
mechanism deck (MG-250B-137
2
spring (FL)
3
jack flexible board
(CN901)
– 8 –
1
two dampers (250)

JACK BOARD
Remove the JACK board of
the arrow.
1
ground point screw
(+PTT2.6 × 6)
2
JACK board
MAIN BOARD
5
screw
(P1.4
×
3.0)
1
main flexible board
(CNJ12)
6
three screws
7
MAIN board
2
connector
(CNP301)
3
screw
(BVTT2
×
4)
5
screw
(P1.7
×
2.5)
– 9 –
4
heat sink

ELEVATOR MOTOR ASS’Y (M104)
1
screw
(P2 × 2.2)
2
bracket (ELV motor)
3
elevator motor ass’y
ESCUTCHEON
2
Remove the claw
of the arrow
4
Remove the ditch
of the arrow
5
Remove the escutcheon
of the arrow
A
B
C
3
two claws
.
A
.
.
B
4
C
ditch
1
screw
(M2
– 10 –
×
3)

CASE (UPPER) ASS’Y
4
three screws
(B2 × 3)
7
Remove the case
(upper) ass’y of
the arrow B.
4
screw
(B2 × 3)
3
spring (stopper. upper)
4
two screws
(B2 × 3)
6
Remove the edge
of the arrow A.
2
bracket (stopper upper)
1
screw
(P2 × 2.2)
5
A
B
CHASSIS ASS’Y
5
chassis ass’y
4
4
3
polyethylene washe
1
stop ring 2.0
(E type)
2
washer
– 11 –
6
spring (stopper. lower)

RF BOARD
5
connector
(CNP52)
2
two screws
(PS2
1
×
4)
OP flexible board
(CNJ11)
3
two screws
(PS2
×
4)
4
RF board
SLED MOTOR ASS’Y (M102), OPTICAL PICK-UP (KSS-512A/J2N)
1
4
Turn at the direction of the
arrow, then remove
shaft (sled) ass’y
two screws
(P2 × 3)
2
sled motor ass’y
(M102)
5
two connectors
(CNP11, 503)
3
optical pick-up
(KSS-521A/J2N
– 12 –

SW BOARD, SPINDLE MOTOR ASS’Y (M101)
8
two screws
(P1.7
×
2.2)
1
screw
×
2.2)
(P2
2
SW board
7
3
spring (chucking)
6
retainer (disc)
4
screw
×
(P2
5
bracket (CP)
9
Remove the spindle motor ass’y (M101)
of the arrow.
2.2)
CHUCKING MOTOR ASS’Y (M103)
3
bracket
(load motor)
2
two screws (P2 × 2.5)
1
connector
(CNP51)
4
chucking motor ass’y
(M103)
– 13 –

SECTION 4
MECHANISMDECK ASSEMBLY
Note: Follow the assembly procedure in the numerical order given.
OPTICAL PICK-UP COMPLETE ASS’Y
1
Move the lever (LOCK 3) in direction A, and return it a little in
direction
to the lower limit.
chuck plate
B
from the position where the chuck plate is moved down
B
shaft (A)
A
3
4
stop ring 2.0 (E type)
5
tension spring (DH)
2
polyethylene washer
optical pick-up complete ass’y
Note: Insert the shaft (A) first.
GEAR (LOMINI) / (LOAD 1) ASS’Y
gear (LOAD 2)
gear (LOMINI)
marking
Fig. A.
3
Attach the gear (LOAD 1) ass’y
with its facing inside.
chuck plate
slit
2
Attach the gear (LOMINI) at the position
shown in Fig. A.
shaft (rotary prevention C)
1
B
4
stop ring 1.5 (E type)
Move the lever (LOCK 3)
fully in direction B to
move the chuck plate up.
– 14 –

OPERATION CHECK
1
Confirm that the slider moves in direction C to move down the
chuck plate if the gear (LOAD 1) is rotated in direction A or the
chuck plate moves up and the slider mo ves in direction D if the
gear is rotated in direction B.
chuck plate
slider
D
C
A
gear (LOAD 1) ass’y
B
– 15 –

SLIDER (L)
1
Move the lever (STOP) ass’y in direction
until it gets stopped.
3
washer
A
2
slider (L)
SLIDER (R)
3
washer
4
polyethyelene slider
1
slider (R)
5
polyethyelene washer
case (lower) ass’y
2
Engage the slots of slider (R)
with the shafts.
slider (R)
– 16 –