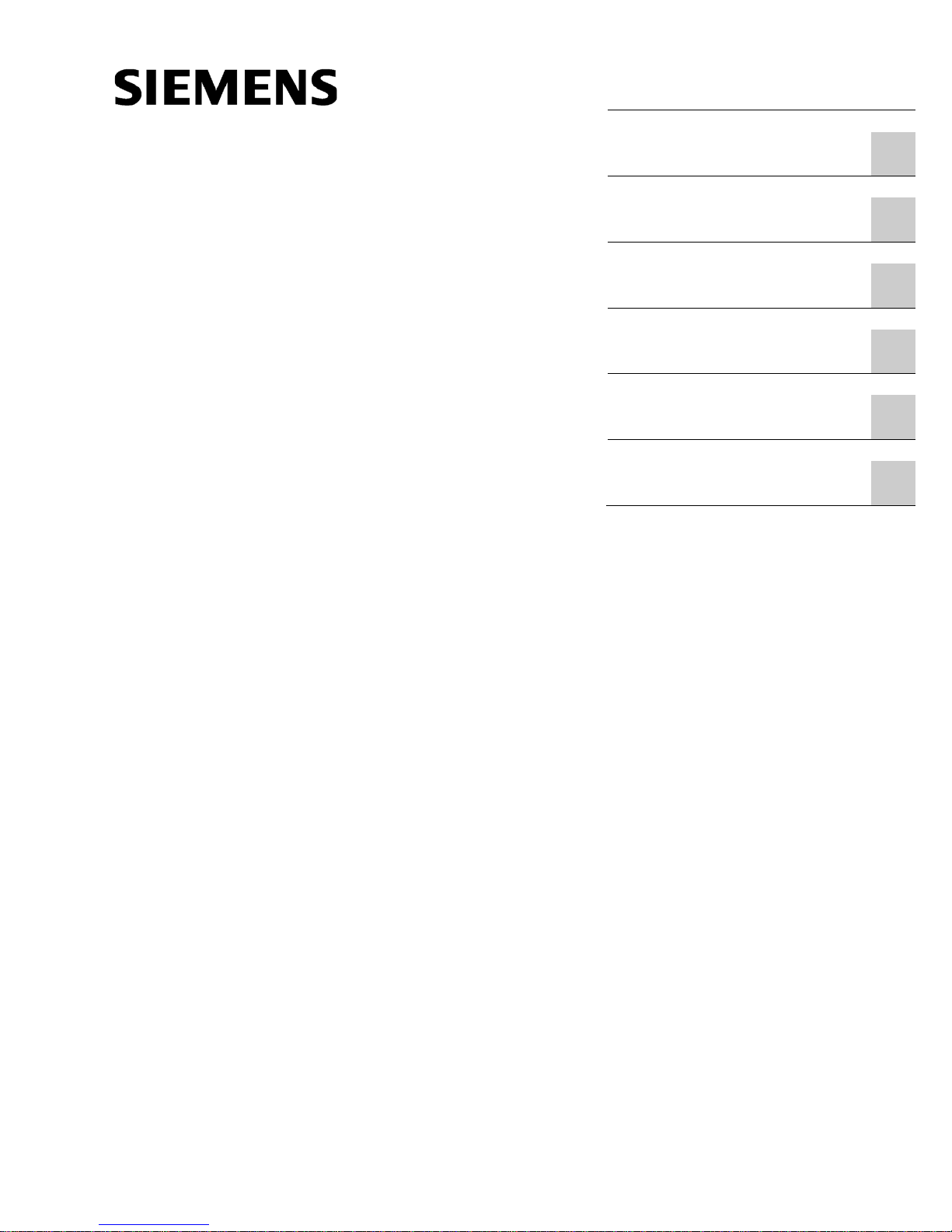
G130, G150, S120 Chassis, S120
Cabinet Modules, S150
Safety Integrated
General information about
SINAMICS Safety Integrated
Description of Safety
Integrated functions
Controlling the safety
functions
Commissioning and
acceptance test
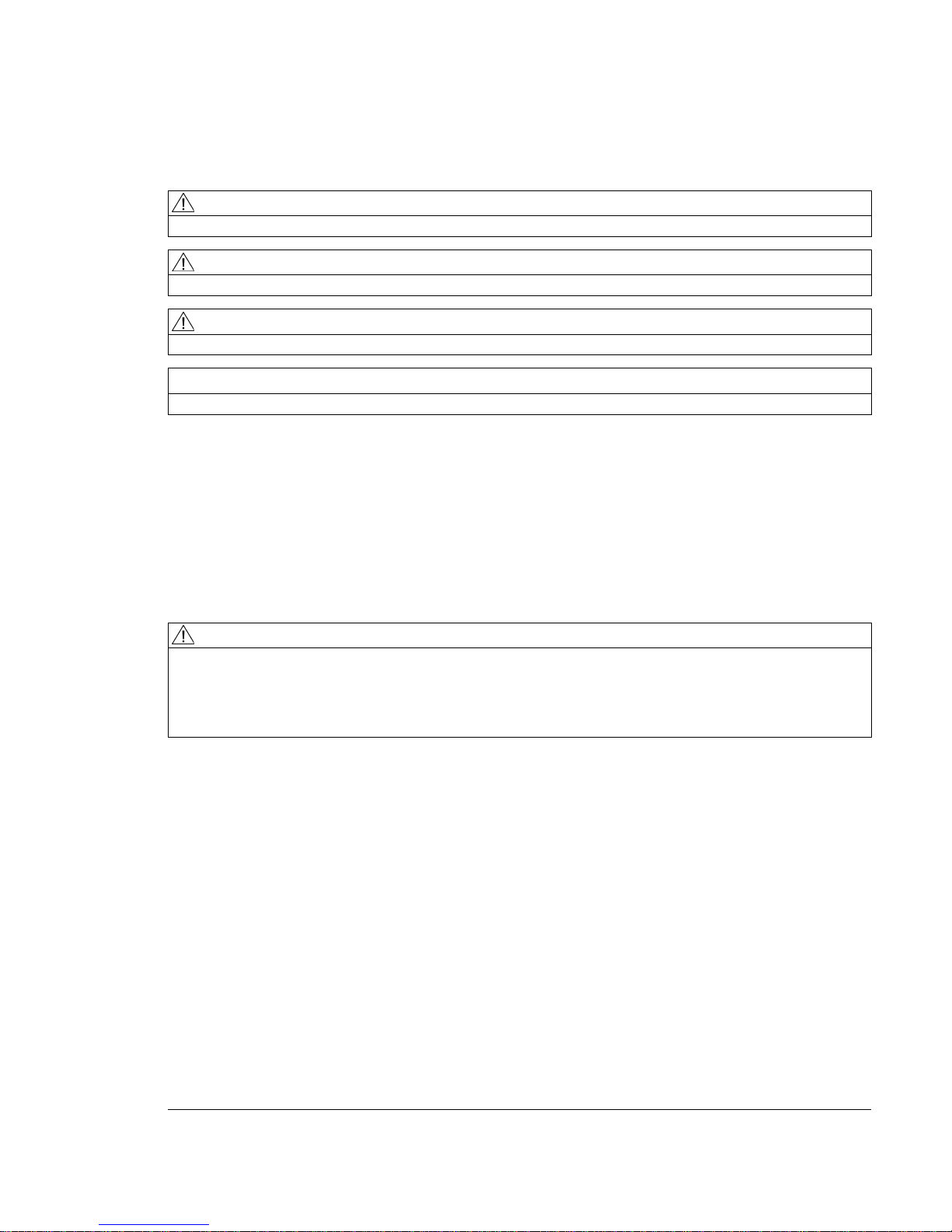
Siemens AG
Division Process Industries and Drives
Postfach 48 48
90026 NÜRNBERG
GERMANY
08/2016 Subject to change
Copyright © Siemens AG 2005 - 2016.
All rights reserved
Legal information
Warning notice system
This manual contains notices you have to observe in order to ensure your personal safety, as well as to prevent
damage to property. The notices referring to your personal safety are highlighted in the manual by a safety alert
symbol, notices referring only to property damage have no safety alert symbol. These notices shown below are
graded according to the degree of danger.
indicates that death or severe personal injury will result if proper precautions are not taken.
indicates that death or severe personal injury may result if proper precautions are not taken.
indicates that minor personal injury can result if proper precautions are not taken.
indicates that property damage can result if proper precautions are not taken.
If more than one degree of danger is present, the warning notice representing the highest degree of danger will
be used. A notice warning of injury to persons with a safety alert symbol may also include a warning relating to
property damage.
The product/system described in this documentation may be operated only by
for the specific
task in accordance with the relevant documentation, in particular its warning notices and safety instructions.
Qualified personnel are those who, based on their training and experience, are capable of identifying risks and
avoiding potential hazards when working with these products/systems.
Proper use of Siemens products
Siemens products may only be used for the applications described in the catalog and in the relevant technical
documentation. If products and components from other manufacturers are used, these must be recommended
or approved by Siemens. Proper transport, storage, installation, assembly, commissioning, operation and
maintenance are required to ensure that the products operate safely and without any problems. The permissible
ambient conditions must be complied with. The information in the relevant documentation must be observed.
All names identified by ® are registered trademarks of Siemens AG. The remaining trademarks in this publication
may be trademarks whose use by third parties for their own purposes could violate the rights of the owner.
We have reviewed the contents of this publication to ensure consistency with the hardware and software
described. Since variance cannot be precluded entirely, we cannot guarantee full consistency. However, the
information in this publication is reviewed regularly and any necessary corrections are included in subsequent
editions.
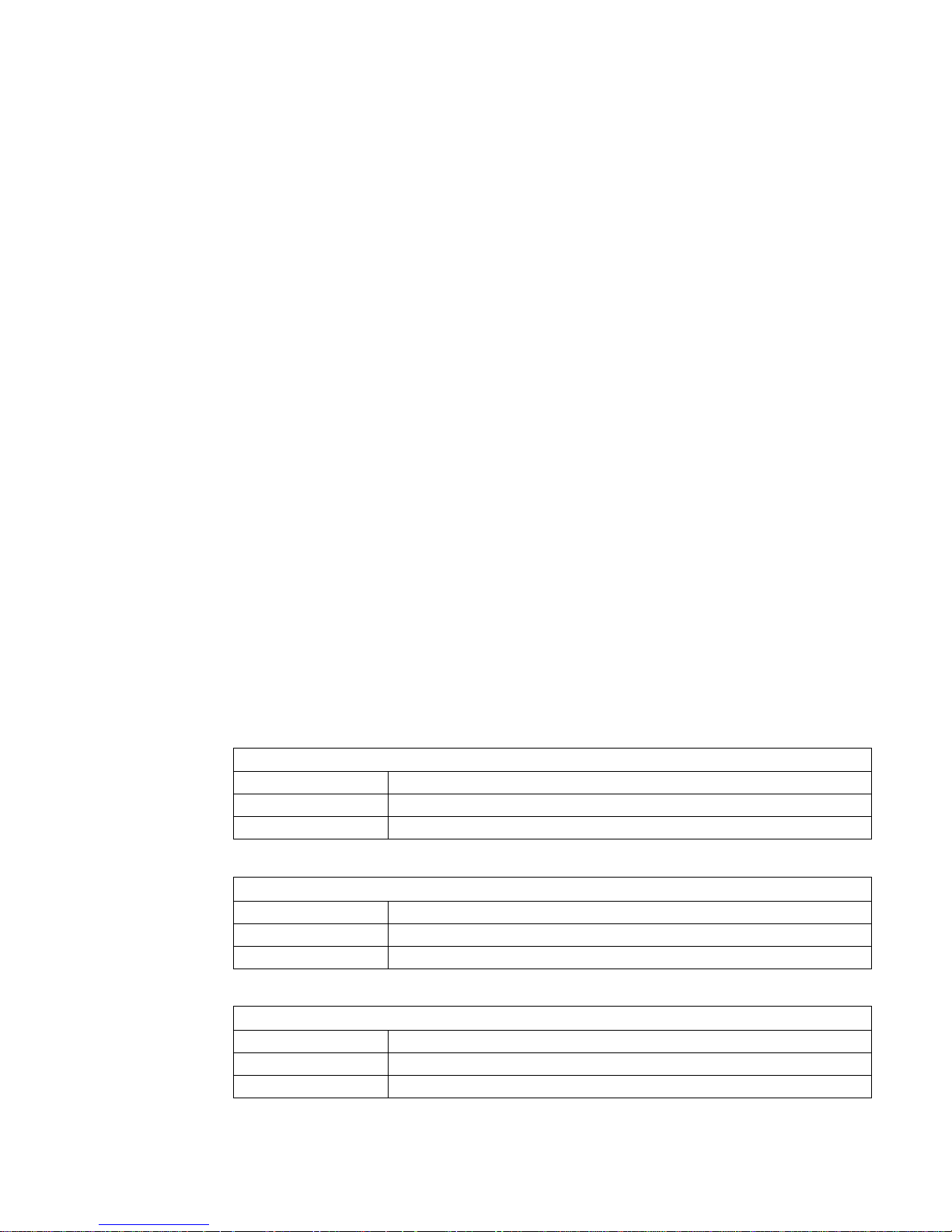
Safety Integrated
Function Manual, 07/2016, A5E03264275A
5
This documentation is intended for machine manufacturers, commissioning engineers, and
service personnel who use the SINAMICS drive system.
The scope of the functionality described in this document can differ from that of the actually
supplied drive system.
● Other functions not described in this documentation might be able to be executed in the
drive system. This does not, however, represent an obligation to supply such functions
with a new controller or when servicing.
● The documentation can also contain descriptions of functions that are not available in a
particular product version of the drive system. The functionalities of the supplied drive
system should only be taken from the ordering documentation.
● Extensions or changes made by the machine manufacturer must be documented by the
machine manufacturer.
For reasons of clarity, this documentation does not contain all of the detailed information on
all of the product types. This documentation cannot take into consideration every
conceivable type of installation, operation and service/maintenance.
In case of questions, please contact us through the following hotline:
Time zone Europe / Africa
https://support.industry.siemens.com/sc/ww/en/sc/2090
techsupport.sea@siemens.com
support.asia.automation@siemens.com
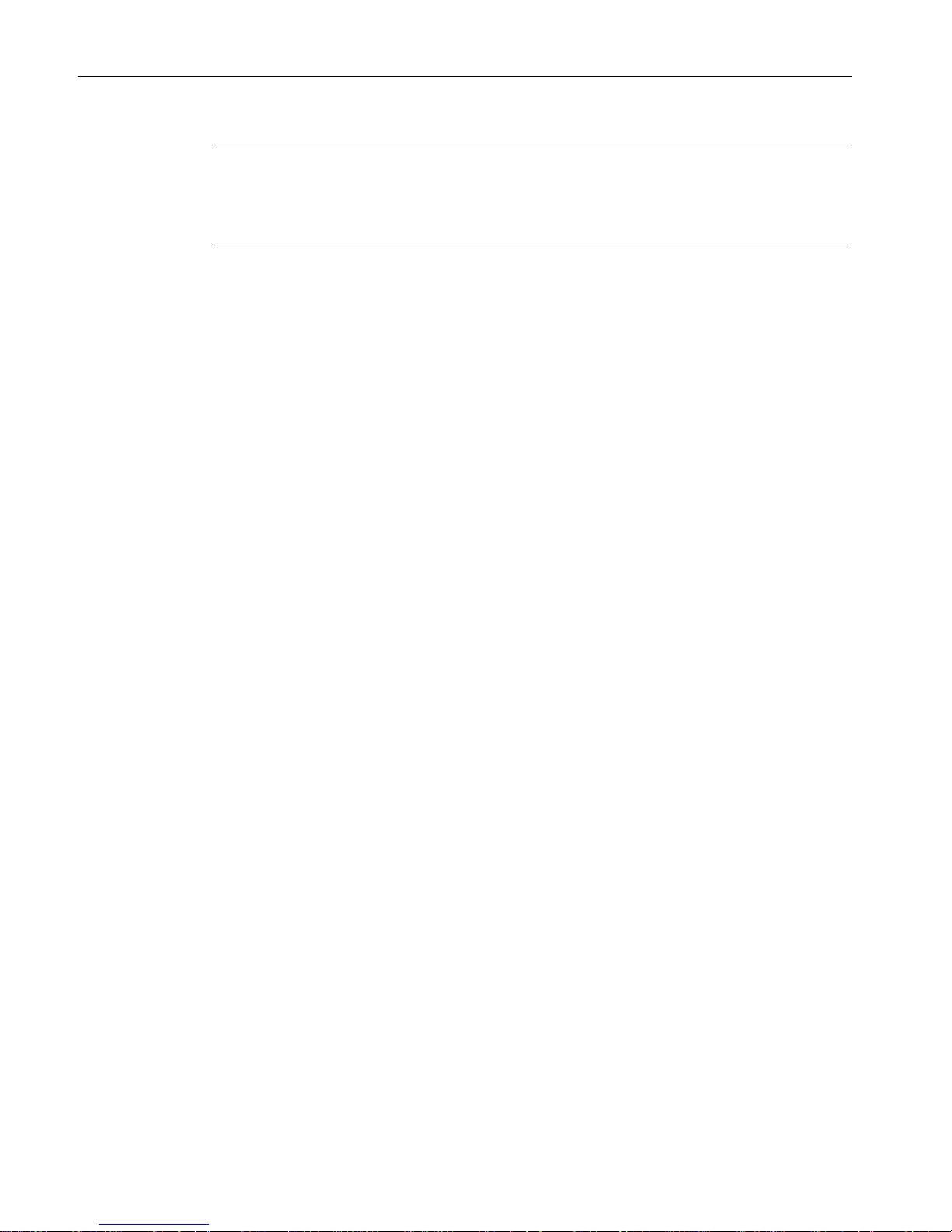
Preface
Safety Integrated
6 Function Manual, 07/2016, A5E03264275A
-specific telephone numbers for technical support are provided under the following
https://www.automation.siemens.com/aspa_app
You can find spare parts on the Internet at:
https://support.industry.siemens.com/sc/de/en/sc/2110
Internet address for SINAMICS
http://www.siemens.com/sinamics.
Internet address for Safety Integrated
http://www.siemens.com/safety
This address contains detailed application examples for Safety Integrated.
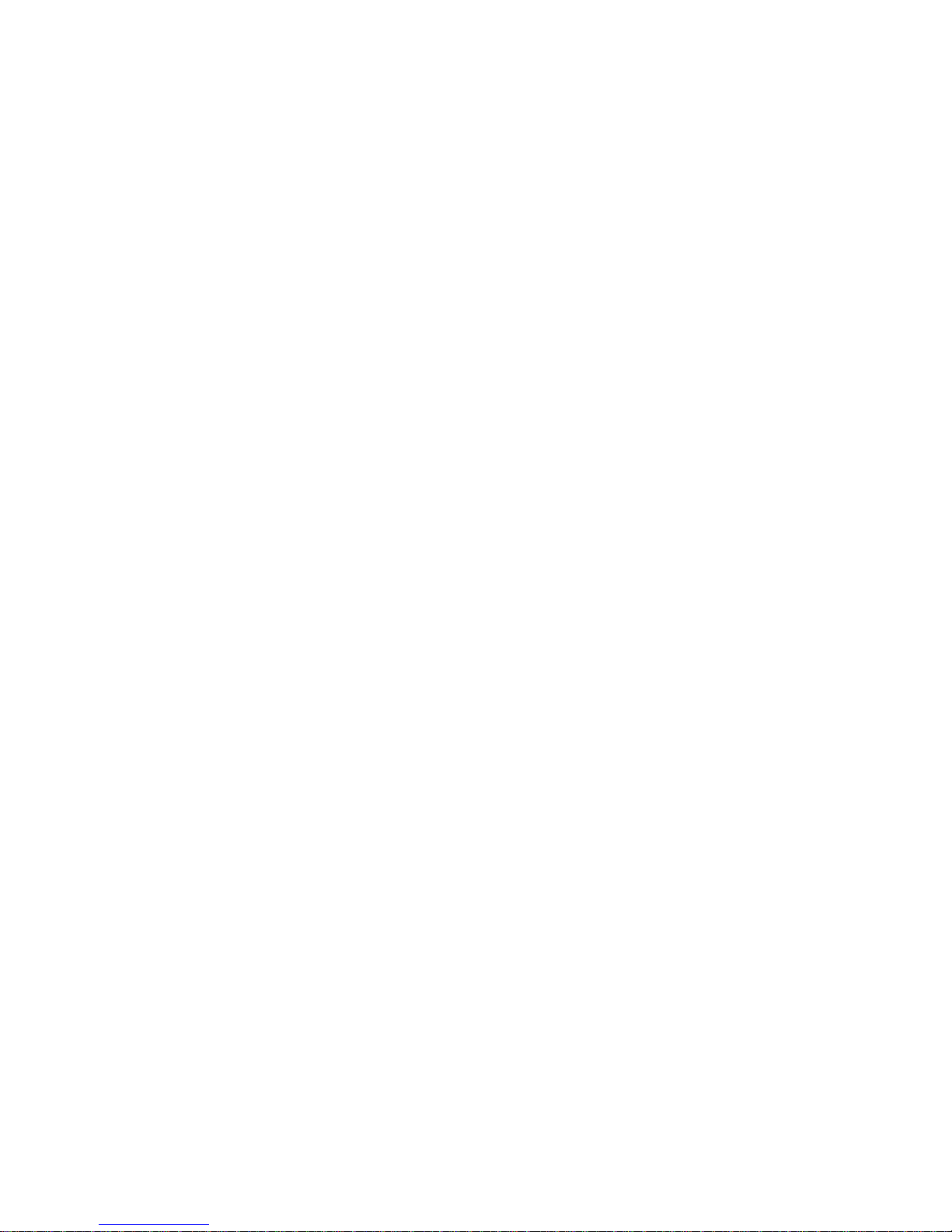
Safety Integrated
Function Manual, 07/2016, A5E03264275A
7
Preface ................................................................................................................................................... 5
1 Safety information ................................................................................................................................... 9
1.1 Industrial security .................................................................................................................... 10
2 Introduction ........................................................................................................................................... 13
3 General information about SINAMICS Safety Integrated ........................................................................ 15
3.1 Supported functions ................................................................................................................ 15
3.1.1 SINAMICS G130 ..................................................................................................................... 18
3.1.1.1 Basic functions ........................................................................................................................ 18
3.1.1.2 Extended Functions ................................................................................................................ 18
3.1.2 SINAMICS G150 ..................................................................................................................... 20
3.1.2.1 Basic functions ........................................................................................................................ 20
3.1.2.2 Extended Functions ................................................................................................................ 20
3.1.3 SINAMICS S120 chassis ........................................................................................................ 22
3.1.3.1 Basic functions ........................................................................................................................ 22
3.1.3.2 Extended Functions ................................................................................................................ 22
3.1.4 SINAMICS S120 Cabinet Modules, booksize format ............................................................. 24
3.1.4.1 Basic functions ........................................................................................................................ 24
3.1.4.2 Extended Functions ................................................................................................................ 24
3.1.5 SINAMICS S120 Cabinet Modules, chassis format ................................................................ 26
3.1.5.1 Basic functions ........................................................................................................................ 26
3.1.5.2 Extended Functions ................................................................................................................ 26
3.1.6 SINAMICS S150 ..................................................................................................................... 28
3.1.6.1 Basic functions ........................................................................................................................ 28
3.1.6.2 Extended Functions ................................................................................................................ 28
3.2 Drive monitoring with or without encoder................................................................................ 29
4 Description of Safety Integrated functions ............................................................................................. 31
4.1 Preconditions for Safety Integrated Basic Functions .............................................................. 31
4.2 Preconditions for Safety Integrated Extended Functions ....................................................... 32
5 Controlling the safety functions.............................................................................................................. 33
5.1 Control possibilities ................................................................................................................. 33
5.2 Control of "STO" and "SS1" via terminal module for option K82 ............................................ 34
5.2.1 Terminal module for control of "STO" and "SS1" for SINAMICS G150 .................................. 34
5.2.2 Terminal module for control of "STO" and "SS1" for SINAMICS S120 Cabinet Modules ...... 39
5.2.2.1 General information ................................................................................................................ 39
5.2.2.2 Use of the K82 option with Control Unit CU320-2 .................................................................. 43
5.2.2.3 Use of the K82 option with Control Unit CU320-2 .................................................................. 44
5.2.2.4 Wiring ...................................................................................................................................... 44
5.2.3 Terminal module for control of "STO" and "SS1" for SINAMICS S150 .................................. 44
5.3 Control of "STO" and "SS1" via terminals on the Control Unit and the Motor/Power
Module .................................................................................................................................... 50
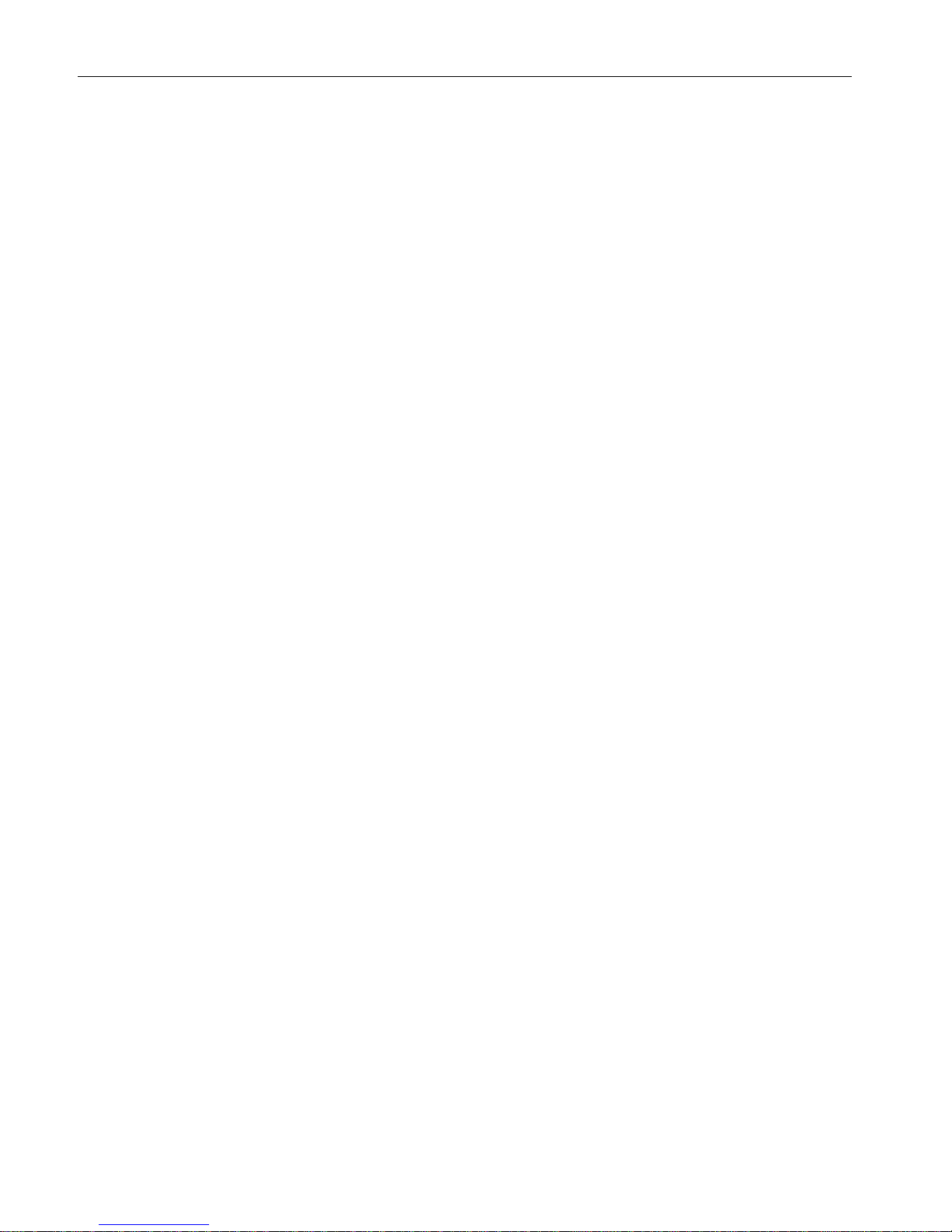
Table of contents
Safety Integrated
8 Function Manual, 07/2016, A5E03264275A
5.3.1 Simultaneity and tolerance time of the two monitoring channels ........................................... 53
5.3.2 Bit pattern test ........................................................................................................................ 55
5.3.3 Control of "STO" and "SS1" for SINAMICS G130 ................................................................. 56
5.3.4 Control of "STO" and "SS1" for SINAMICS G150 ................................................................. 62
5.3.5 Control of "STO" and "SS1" for SINAMICS S120 Chassis .................................................... 68
5.3.6 Control of "STO" and "SS1" for SINAMICS S120 Cabinet Modules ...................................... 74
5.3.7 Control of "STO" and "SS1" for SINAMICS S150 .................................................................. 80
5.4 Activating "SBC" via the Safe Brake Adapter ........................................................................ 86
5.4.1 Activating "SBC" via the Safe Brake Adapter for option K88 (230 V AC) .............................. 86
5.4.2 Safe Brake Adapter SBA 230 V AC for SINAMICS G130/SINAMICS S120 Chassis ........... 90
5.5 Control by way of PROFIsafe ................................................................................................ 95
5.6 Control via TM54F.................................................................................................................. 96
5.6.1 Control via TM54F for SINAMICS G130, S120 Chassis ....................................................... 96
5.6.2 Control via option K87 for SINAMICS S120 Cabinet Modules .............................................. 96
5.6.3 Control via K87 for SINAMICS S150 ..................................................................................... 96
5.7 Motion monitoring without selection ....................................................................................... 97
6 Commissioning and acceptance test ..................................................................................................... 99
Index ................................................................................................................................................... 101
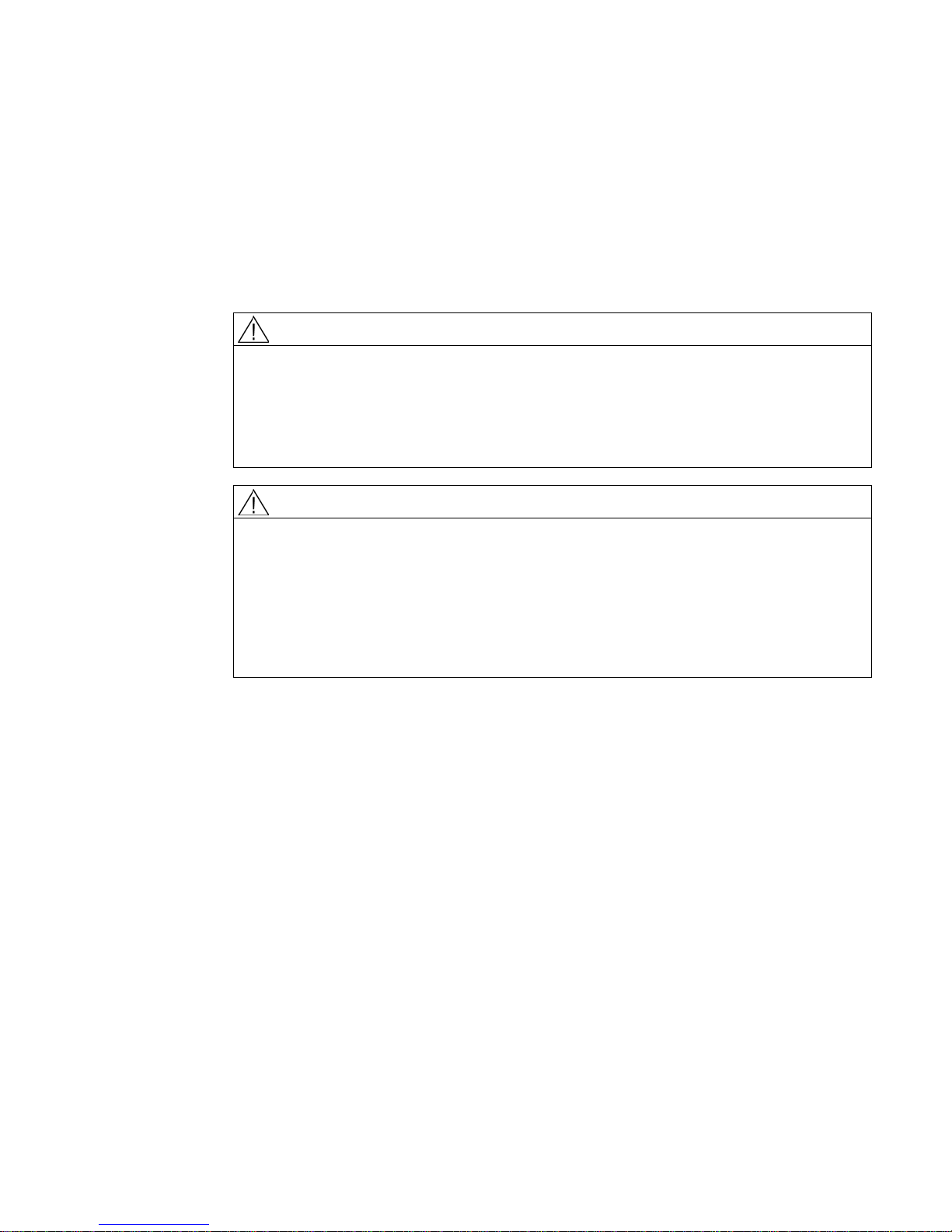
Safety Integrated
Function Manual, 07/2016, A5E03264275A
9
Risk of death if the safety instructions and remaining risks are not carefully observed
If the safety instructions and residual risks are not observed in the associated
documentation, accidents involving severe injuries or death can occur.
• Observe the safety instructions given in the associated documentation.
• When assessing the risk, take into account residual risks.
Danger to life or malfunctions of the machine as a result of incorrect or changed parameter
assignment
Machines can malfunction as a result of incorrect or changed parameter assignment, which
in turn can lead to injuries or death.
• Protect the parameterization (parameter assignments) against unauthorized access.
• Respond to possible malfunctions by applying suitable measures (e.g. EMERGENCY
STOP or EMERGENCY OFF).
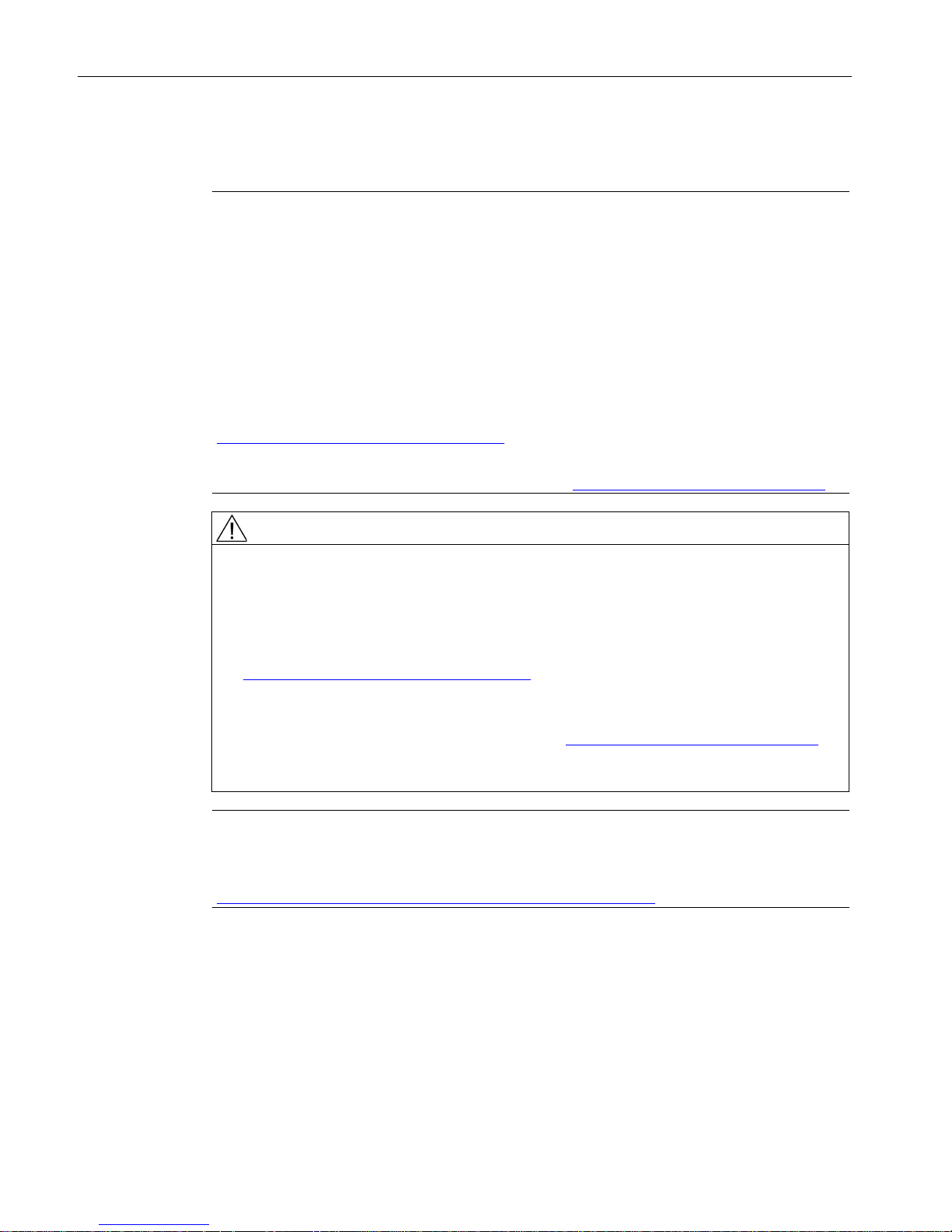
Safety information
1.1 Industrial security
Safety Integrated
10 Function Manual, 07/2016, A5E03264275A
Note
Industrial security
Siemens provides products and solutions with industrial security functions that support the
secure operation of plants, solutions, machines, devices, and/or networks. They are
important compon
ents in a holistic industrial security concept. With this in mind, Siemens
products and solutions undergo continuous development. Siemens recommends strongly
that you regularly check for product updates.
For the secure operation of Siemens products and sol
utions, it is necessary to take suitable
preventive action (e.g. cell protection concept) and integrate each component into a holistic,
state
-of-the-art industrial security concept. Any third-party products that may be in use must
also be taken into accoun
t. For more information about industrial security, visit Hotspot-Text
http://www.siemens.com/industrialsecurity).
To receive information about product updates on a regular basis, register for ou
newsletter. For more information, visit Hotspot
-Text (https://support.industry.siemens.com).
Danger due to unsafe operating states caused by software manipulation
Software manipulations (e.g. viruses, trojans, malware, worms) can cause unsafe operating
states in your system that may lead to death, serious injury, and property damage.
• Update your software regularly.
You will find relevant information and newsletters at this address
(http://www.siemens.com/industrialsecurity).
• Integrate the automation and drive components into a holistic, state-of-the-art industrial
security concept for the plant or machine.
You will find further information at this address (https://support.industry.siemens.com).
• Make sure that you include all installed products into the holistic industrial security
concept.
Note
Industrial Security Configuration Manual
You can
find a Configuration Manual on the topic of Industrial Security at this address
https://support.industry.siemens.com/cs/ww/en/view/108862708).

Safety information
1.1 Industrial security
Safety Integrated
Function Manual, 07/2016, A5E03264275A
11
Note
Malfunctions as a result of withdrawing and inserting components
Malfunctions can occur by withdrawing and inserting components that are used for Safety
Integrated without having to exit the fail
-safe state. For example, PROFIsafe communication
is not reestablished after this
Withdrawing and inserting components used for Safety Integrated (power units, Sensor
Modules, TM54F) in operation
in the deactivated state is
permissible. Activating
the components always requires a POWER ON.
Note
Approval of option K82
Only circuits that have been manufactured by the OEM or by certified factories or that have
been installed by the authorized service for option K82, possess an approval. Possible plant
side reproductions by non
-certified manufacturers do not possess this approval!
-to-date list of authorized factories is available on request from your local Siemens
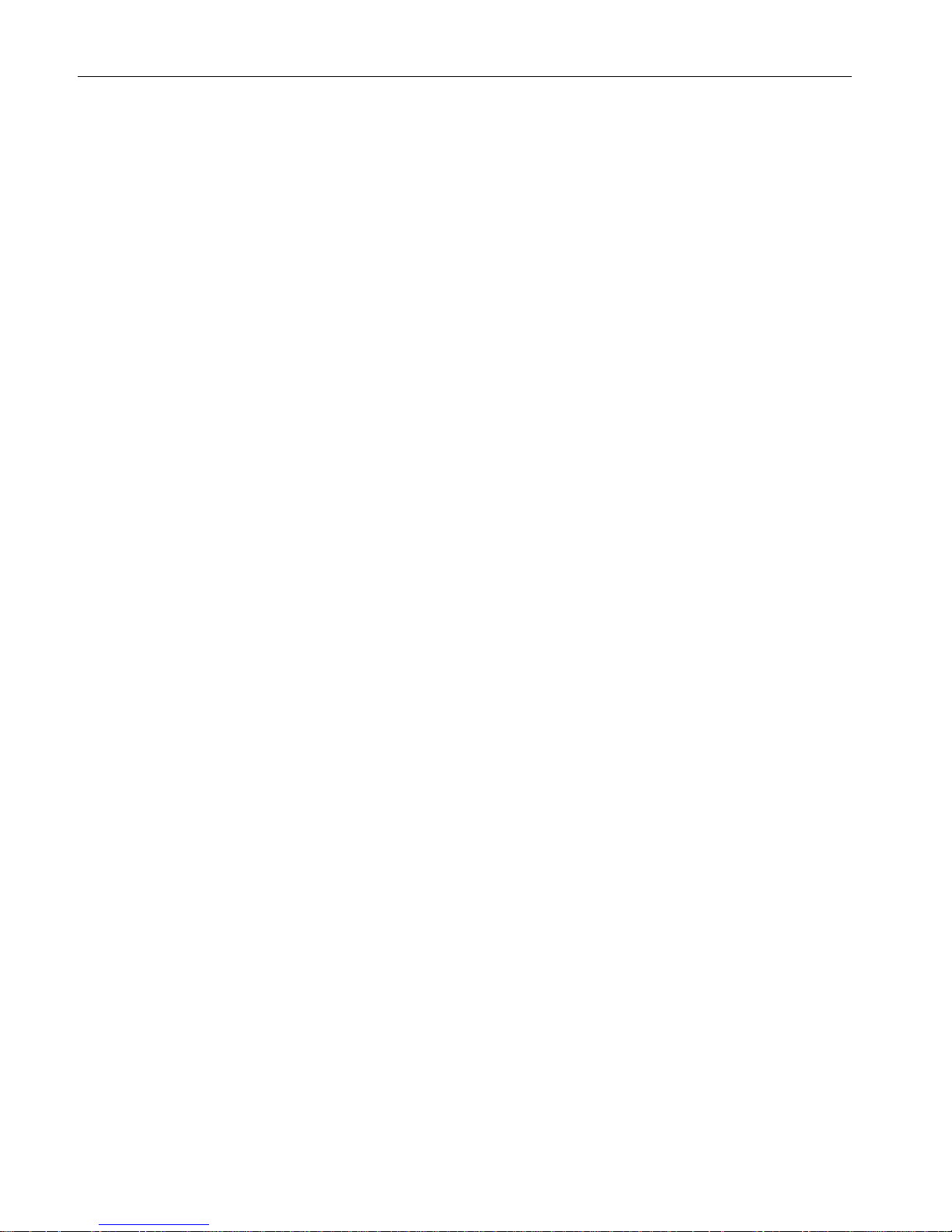
Safety information
1.1 Industrial security
Safety Integrated
12 Function Manual, 07/2016, A5E03264275A
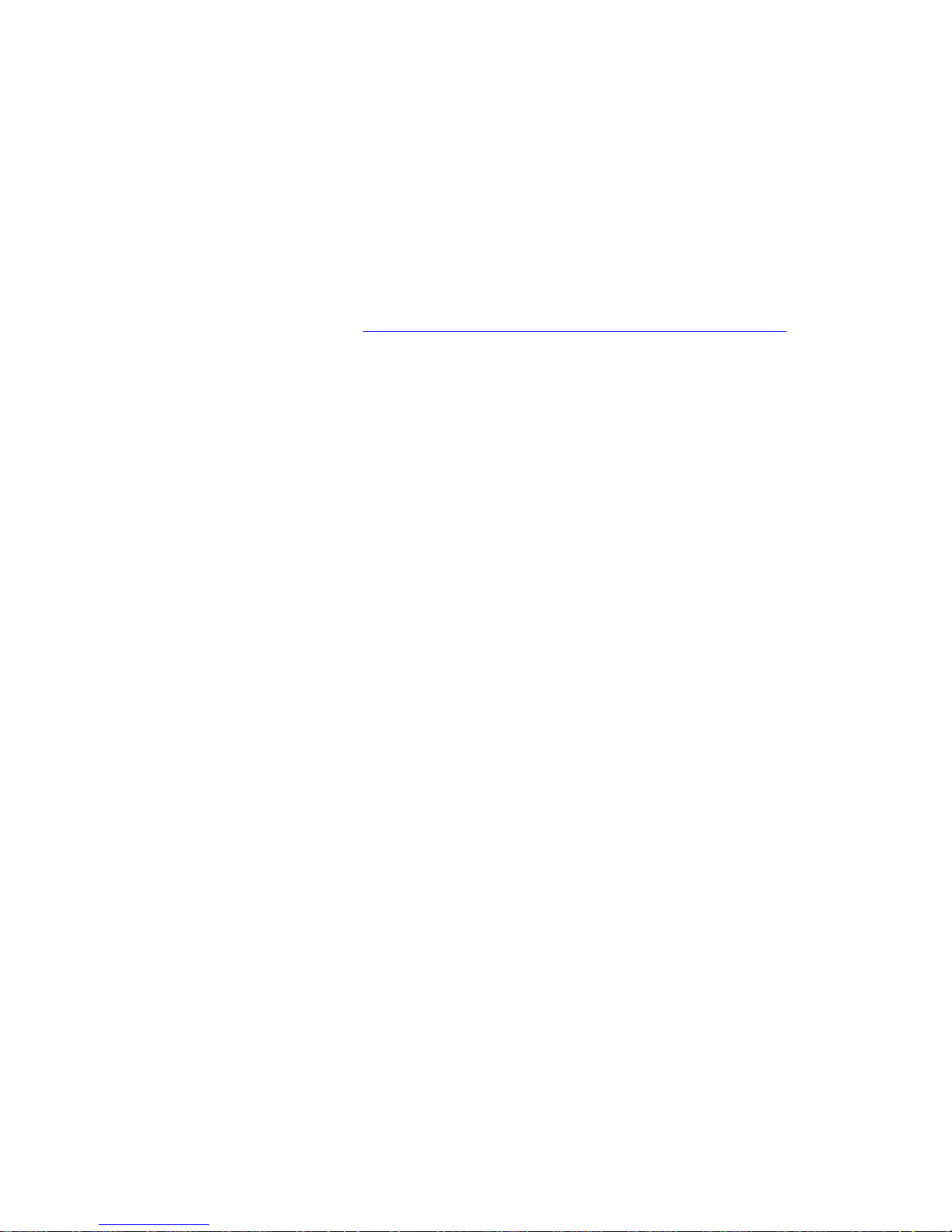
Safety Integrated
Function Manual, 07/2016, A5E03264275A
13
This document is a supplement to the "SINAMICS S120 Safety Integrated Function Manual"
which serves as the basis for the functional scope of the Safety Integrated functions.
The "SINAMICS S120 Safety Integrated Function Manual" is available on the Internet at the
following address (https://support.industry.siemens.com/cs/ww/en/ps/13231/man).
This document contains additional information on the use of the Safety Integrated functions
with the following SINAMICS converters:
● SINAMICS G130
● SINAMICS G150
● SINAMICS S120 Chassis
● SINAMICS S120 Cabinet Modules
● SINAMICS S150

Introduction
Safety Integrated
14 Function Manual, 07/2016, A5E03264275A
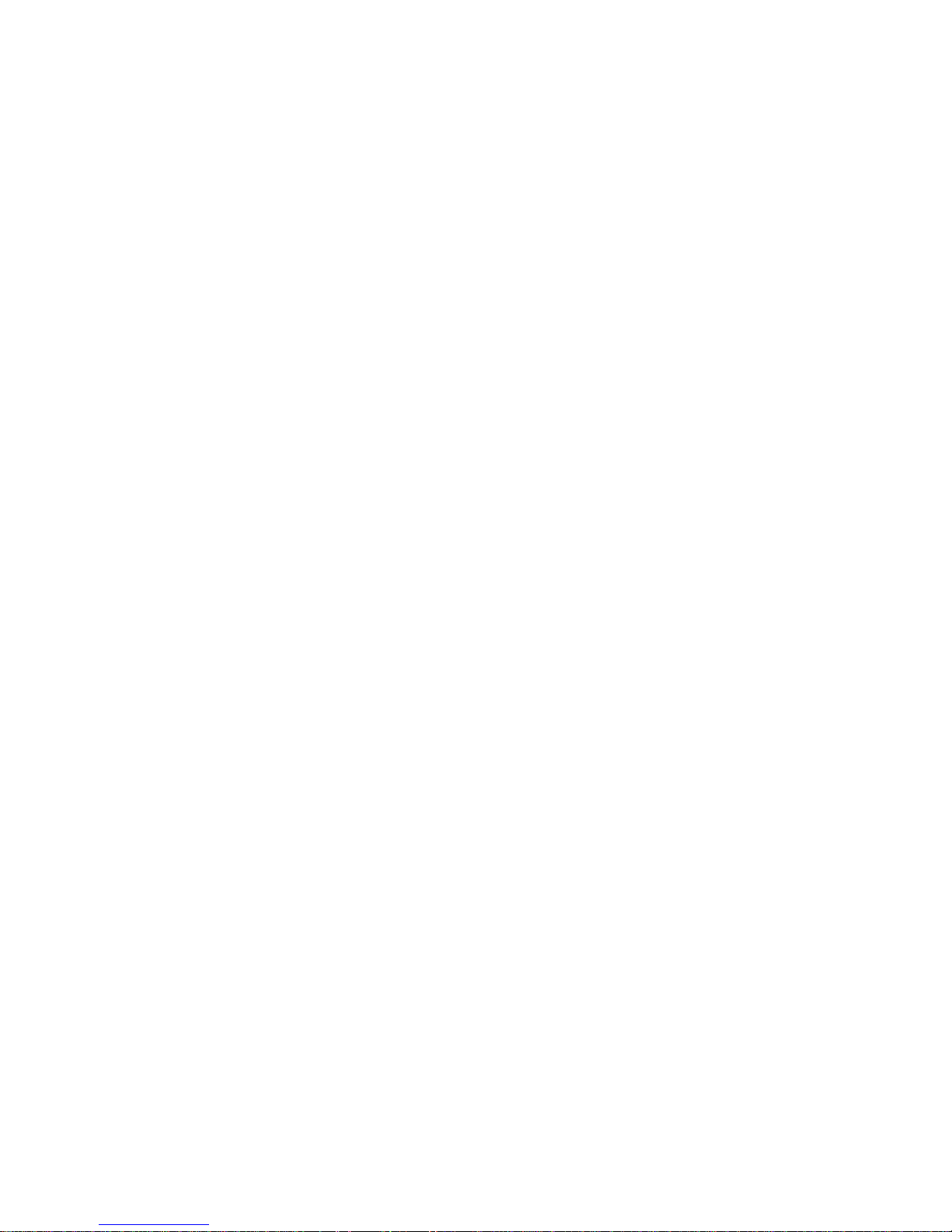
Safety Integrated
Function Manual, 07/2016, A5E03264275A
15
All of the Safety Integrated functions available under SINAMICS are listed in this section.
SINAMICS makes a distinction between Safety Integrated Basic Functions and Safety
Integrated Extended Functions.
The safety functions listed here are in conformance with:
● Safety Integrity Level (SIL) 2 according to IEC 61508
● Category 3 according to DIN EN ISO 13849-1
● Performance Level (PL) d according to DIN EN ISO 13849-1
The safety functions correspond to the functions according to DIN EN 61800-5-2 (under the
assumption that they are defined there).
The following Safety Integrated functions (SI functions) are available:
●
Safety Integrated Basic Functions
These functions are part of the standard scope of the drive and can be used without
requiring an additional license. These functions are always available, and do not require
an encoder and/or do not place any special requirements on the encoder used.
– Safe Torque Off (STO)
Safe Torque Off is a safety function to avoid unexpected startup in accordance with
EN 60204-1. STO prevents the supply of energy to the motor which can generate a
torque and corresponds to Stop Category 0.
– Safe Stop 1 (SS1, time-controlled)
Safe Stop 1 is based on the "Safe Torque Off" function. This means that a Category 1
stop according to EN 60204-1 can be implemented.
– Safe Brake Control (SBC)
Safe Brake Control safely controls a holding brake.
1)
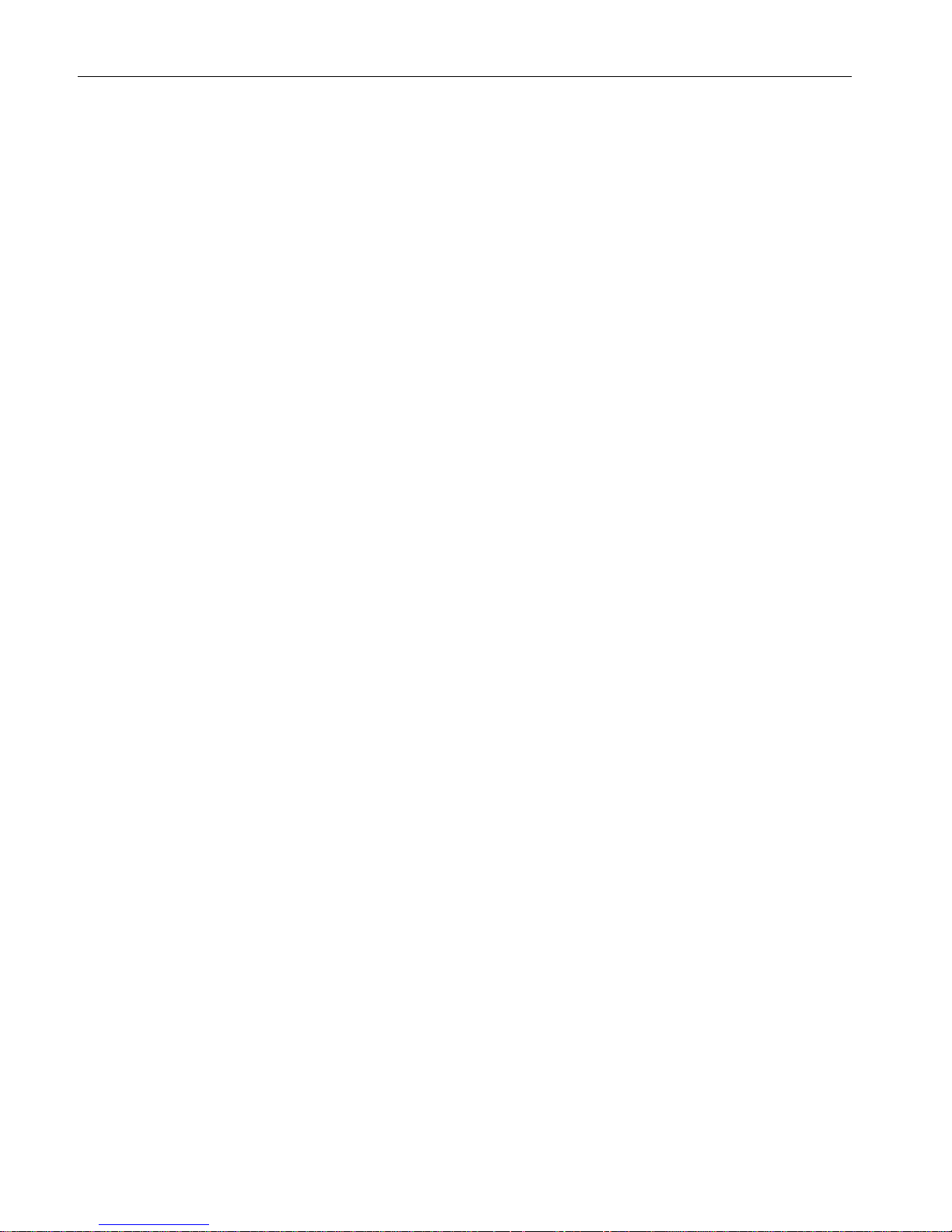
General information about SINAMICS Safety Integrated
3.1 Supported functions
Safety Integrated
16 Function Manual, 07/2016, A5E03264275A
●
Safety Integrated Extended Functions
These functions require an additional safety license. Extended Functions with encoder
require an encoder with safety capability.
– Safe Torque Off (STO)
Safe Torque Off is a safety function that prevents the drive from restarting
unexpectedly according to EN- 60204-1.
– Safe Stop 1 (SS1, time- and acceleration-controlled)
Safe Stop 1 is based on the "Safe Torque Off" function. This means that a Category 1
stop according to EN 60204-1 can be implemented.
– Safe Brake Control (SBC)
Safe Brake Control safely controls a holding brake.
1)
– Safe Operating Stop (SOS)
Safe Operating Stop protects against unintentional movement. The drive is in closedloop control mode and is not disconnected from the power supply.
– Safe Stop 2 (SS2)
Safe Stop 2 safely brakes the motor with a subsequent transition into the "Safe
Operating Stop" state (SOS). This means that a Category 2 stop according to EN
60204-1 can be implemented.
– Safely-Limited Speed (SLS)
Safely Limited Speed monitors that the drive does not exceed a preset speed/velocity
limit.
– Safe Speed Monitor (SSM)
Safe Speed Monitor safely identifies when a speed limit is undershot in both directions
of motion, e.g. to identify zero speed. A fail-safe output signal is available for further
processing.
– Safe Direction (SDI)
Safe Direction is used to safely monitor the direction of motion.
– Safely-Limited Position (SLP)
Safely-Limited Position ensures that a freely definable traversing range is not left.
– Transferring safe position values (SP)
The "Transfer safe position values (SP)" function enables you to transfer a safe
position to a higher-level controller via PROFIsafe.
– Safe gearbox stage switchover
The "Safe gearbox stage switchover" function facilitates reliable switching between
different gearbox stages. The switchover is only possible via PROFIsafe.
– Safe Brake Test (SBT)
The diagnostic function "Safe Brake Test" function (SBT) checks the required holding
torque of a brake (operating or holding brake).
1)
Note on Power/Motor Modules with chassis format:
For chassis format, SBC is only supported by Power/Motor Modules with article number
...3 or higher. A Safe Brake Adapter is also required for this design.
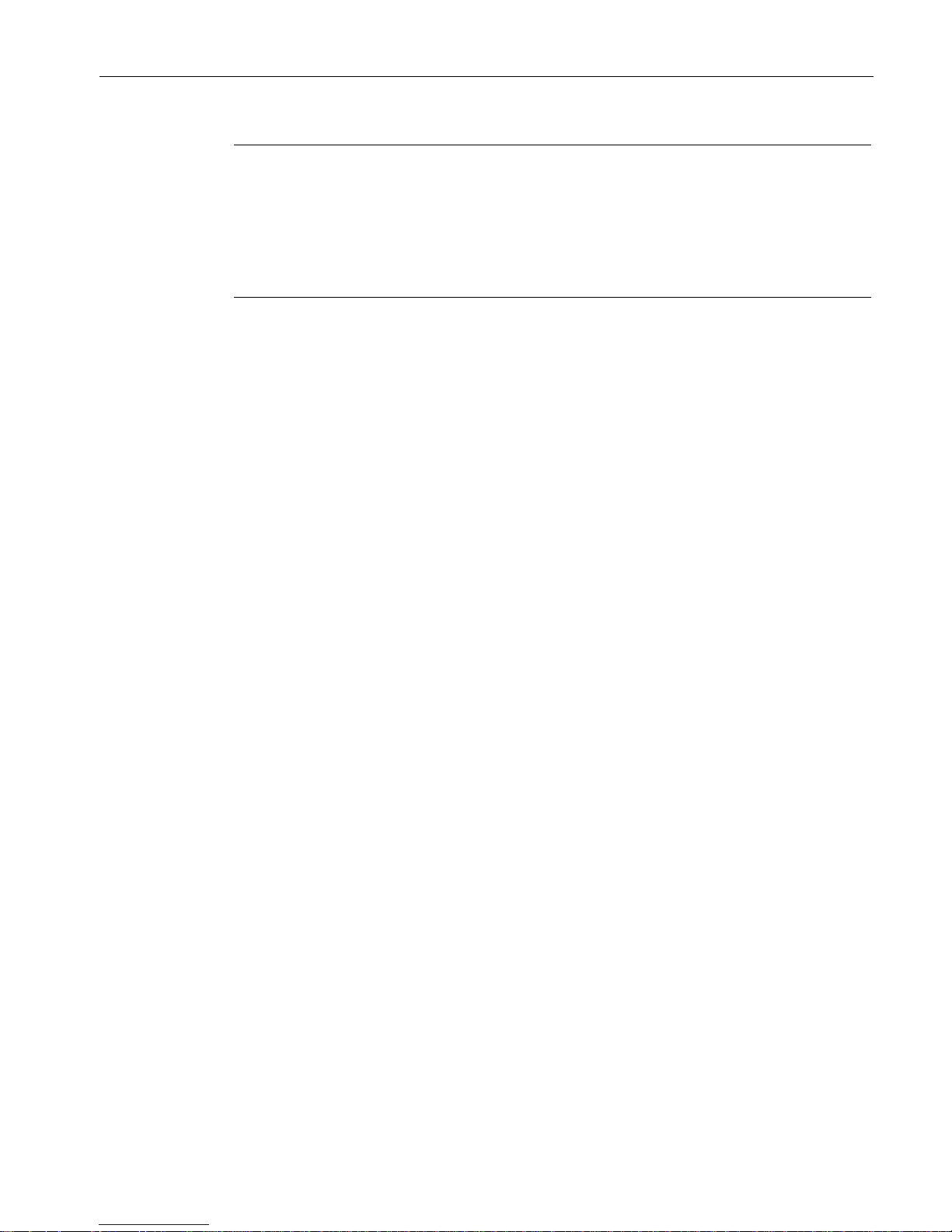
General information about SINAMICS Safety Integrated
3.1 Supported functions
Safety Integrated
Function Manual, 07/2016, A5E03264275A
17
Note
Parallel use of Safety Integrated Functions
All Safety Integrated Functions can be used simultaneously.
If SOS and SLS are activated simultaneously, SOS has higher priority and overrides the SLS
reaction.
Invalid operating modes for Safety Integrated Extended Functions "without encoder"
● Current controller clock cycles 31.25 µs and 62.5 μs (for Double Motor Modules with two
configured safety drives) are not permissible.
● For the independent setting of current controller clock cycle and pulse frequency in
conjunction with Safety Integrated "without encoder", the following system clock cycles
are not permissible:
– Double Motor Modules <125 μs
– All other components: <62.5 μs
– p9589 must be set = 3300 to allow the current controller clock cycle and pulse
frequency to be independently set.
● For chassis format devices, the following also applies:
– For chassis format devices, operation without encoder is only permissible for induction
motors, however
for synchronous motors.
– No operation involving parallel connections
– Optimized pulse patterns cannot be selected for SIMOTICS FD
– Only using parameter p1810 = factory setting, this includes:
- No wobbling
- No fine setting of the pulse frequency
● No "shaft generator" functionality
● Induction motors up to a maximum of 1000 kW; for extremely large machines, it is
necessary to adapt parameter p9585
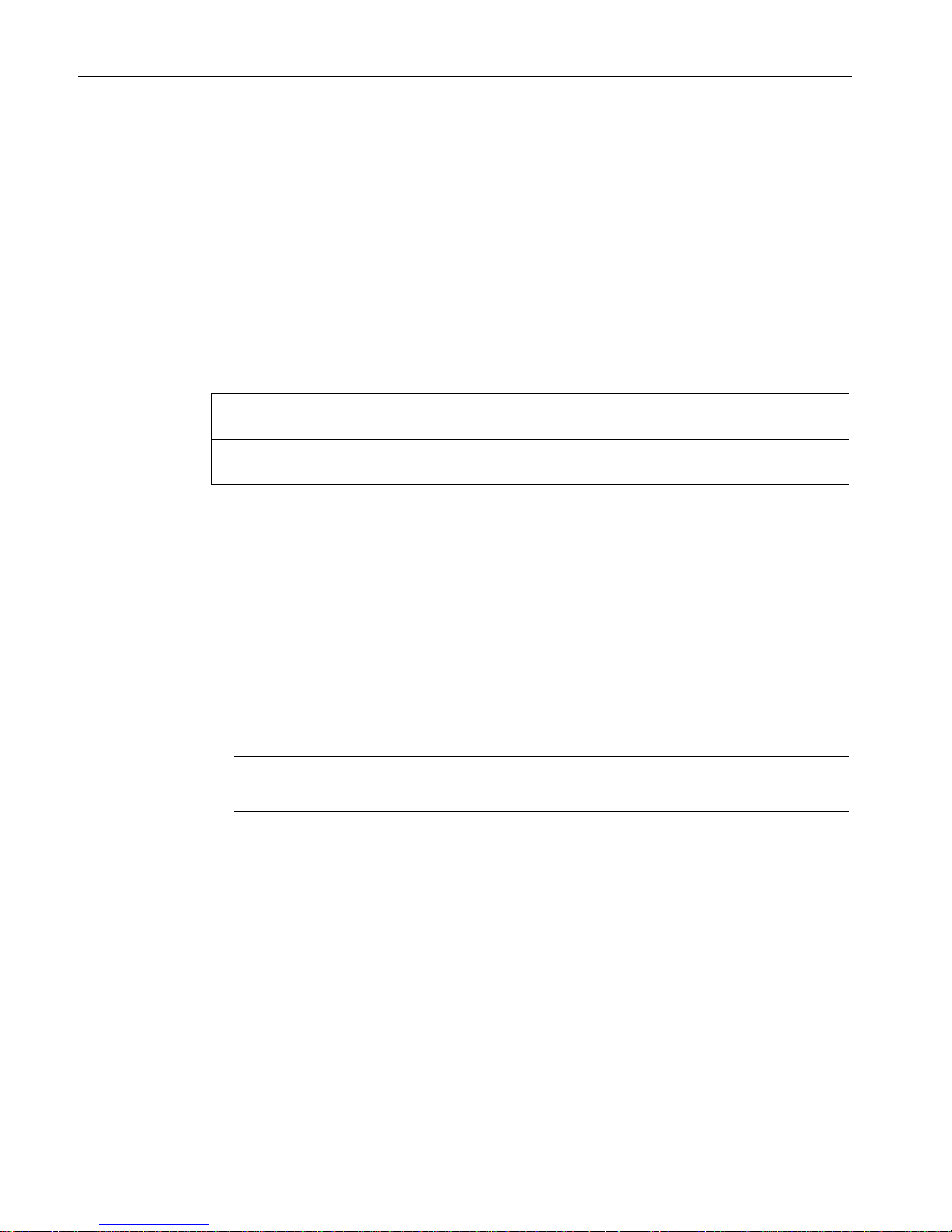
General information about SINAMICS Safety Integrated
3.1 Supported functions
Safety Integrated
18 Function Manual, 07/2016, A5E03264275A
Basic functions
Requirements
The Safety Integrated Basic Functions are part of the standard scope of the drive and can be
used without an additional license.
Supported Safety Integrated Basic Functions
● Control Unit and terminal (on the power unit)
● PROFIsafe and terminal (on the power unit)
Extended Functions
Requirements
: Safety license for one axis
Note
The term "axes" should also be interpreted
● For Extended Functions with encoder:
Two SMC30 Sensor Modules (HTL/TTL encoders)
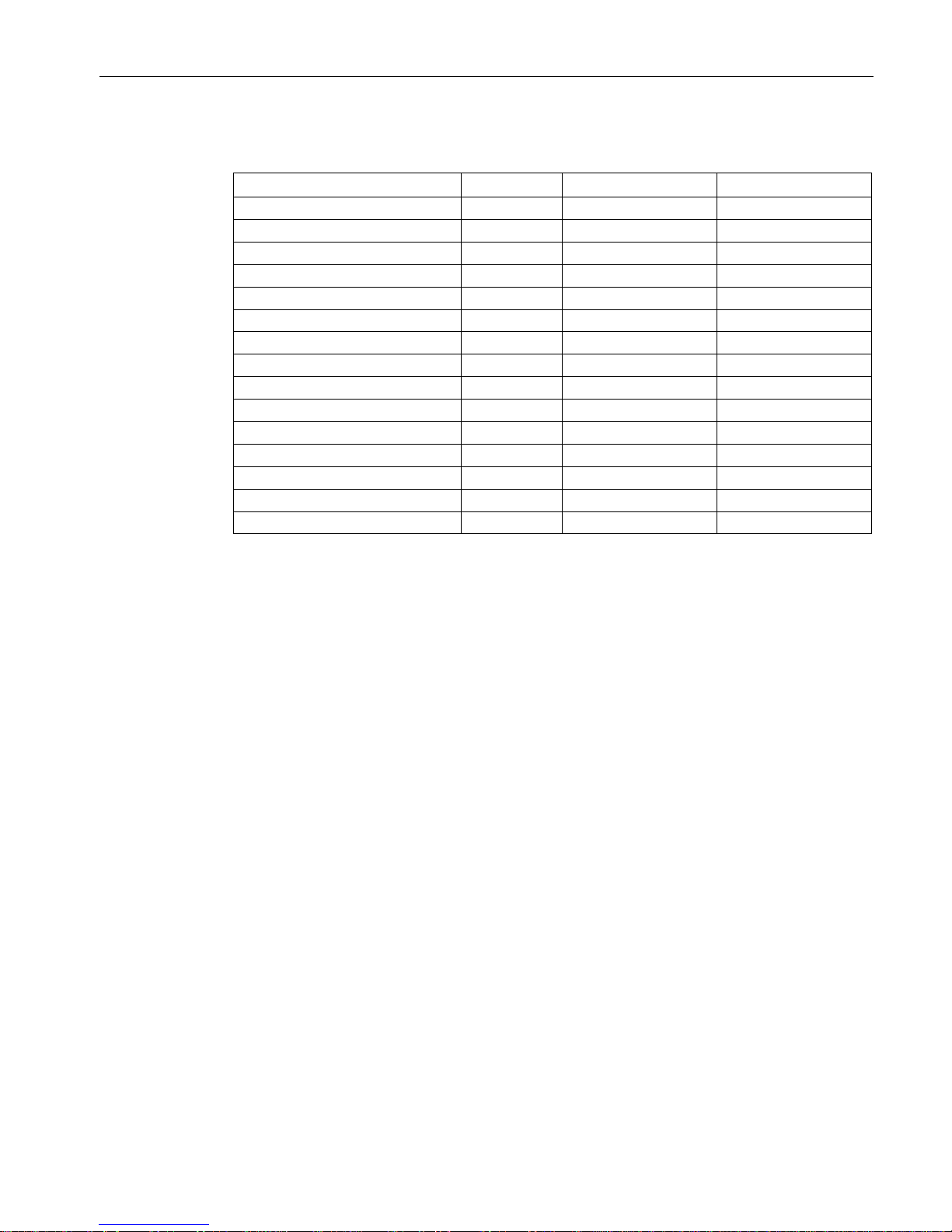
General information about SINAMICS Safety Integrated
3.1 Supported functions
Safety Integrated
Function Manual, 07/2016, A5E03264275A
19
Supported Safety Integrated Extended Functions
Transferring safe position values
Safe Acceleration Monitor
Safe gearbox stage switchover
Two SMC30 Sensor Modules (HTL/TTL encoders)
The use of this safety function without an encoder is permitted only for induction motors.
3)
Using Safe Brake Adapter.
● Terminal Module TM54F
● PROFIsafe
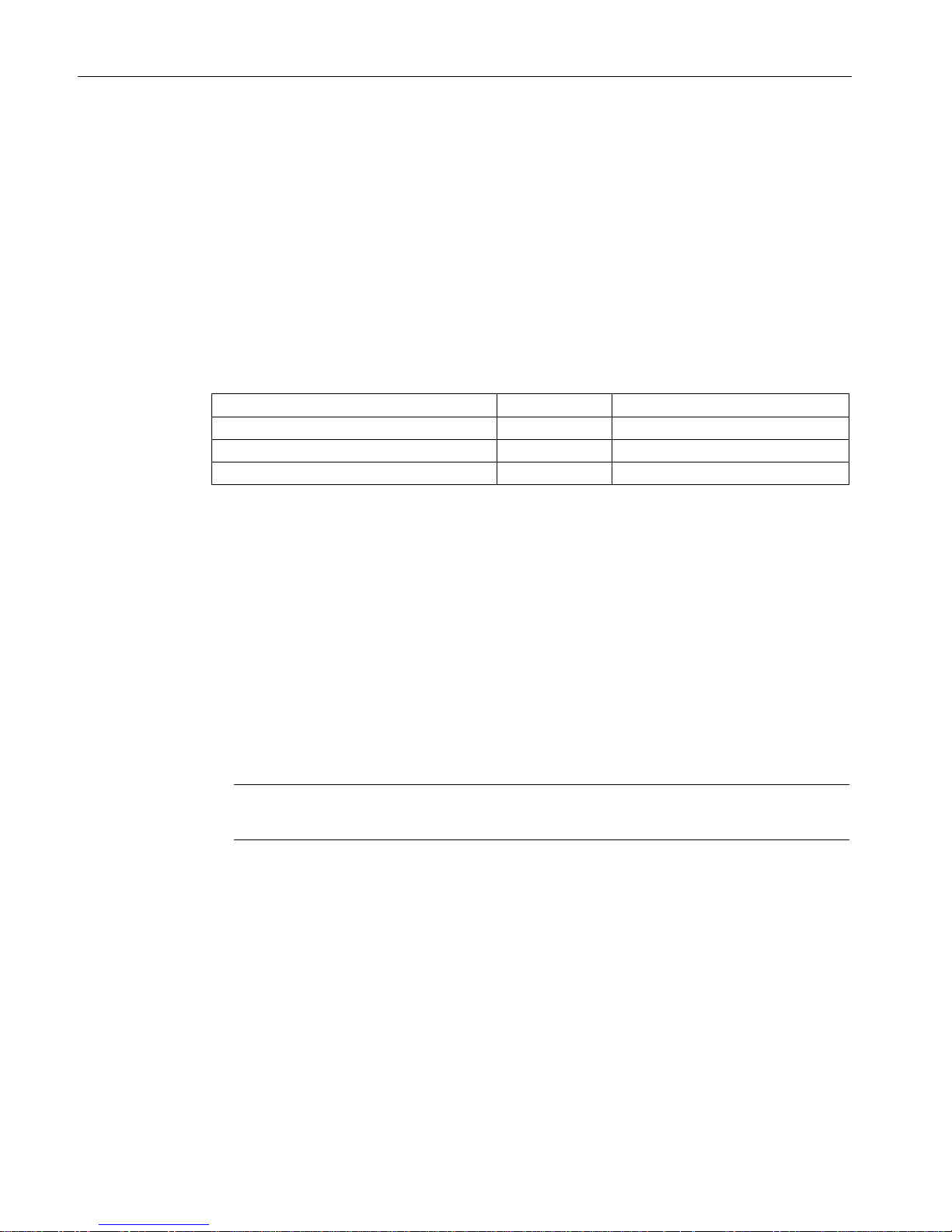
General information about SINAMICS Safety Integrated
3.1 Supported functions
Safety Integrated
20 Function Manual, 07/2016, A5E03264275A
Basic functions
Requirements
The Safety Integrated Basic Functions are part of the standard scope of the drive and can be
used without an additional license.
Supported Safety Integrated Basic Functions
: Terminal Module for controlling safety functions "STO" and "SS1"
● Control Unit and terminal (on the power unit)
● PROFIsafe and terminal (on the power unit)
Extended Functions
Requirements
: Safety license for one axis
Note
The term "axes" should also be interpreted as "drives".
● For Extended Functions with encoder:
Options
: Two SMC30 Sensor Modules (HTL/TTL encoders)
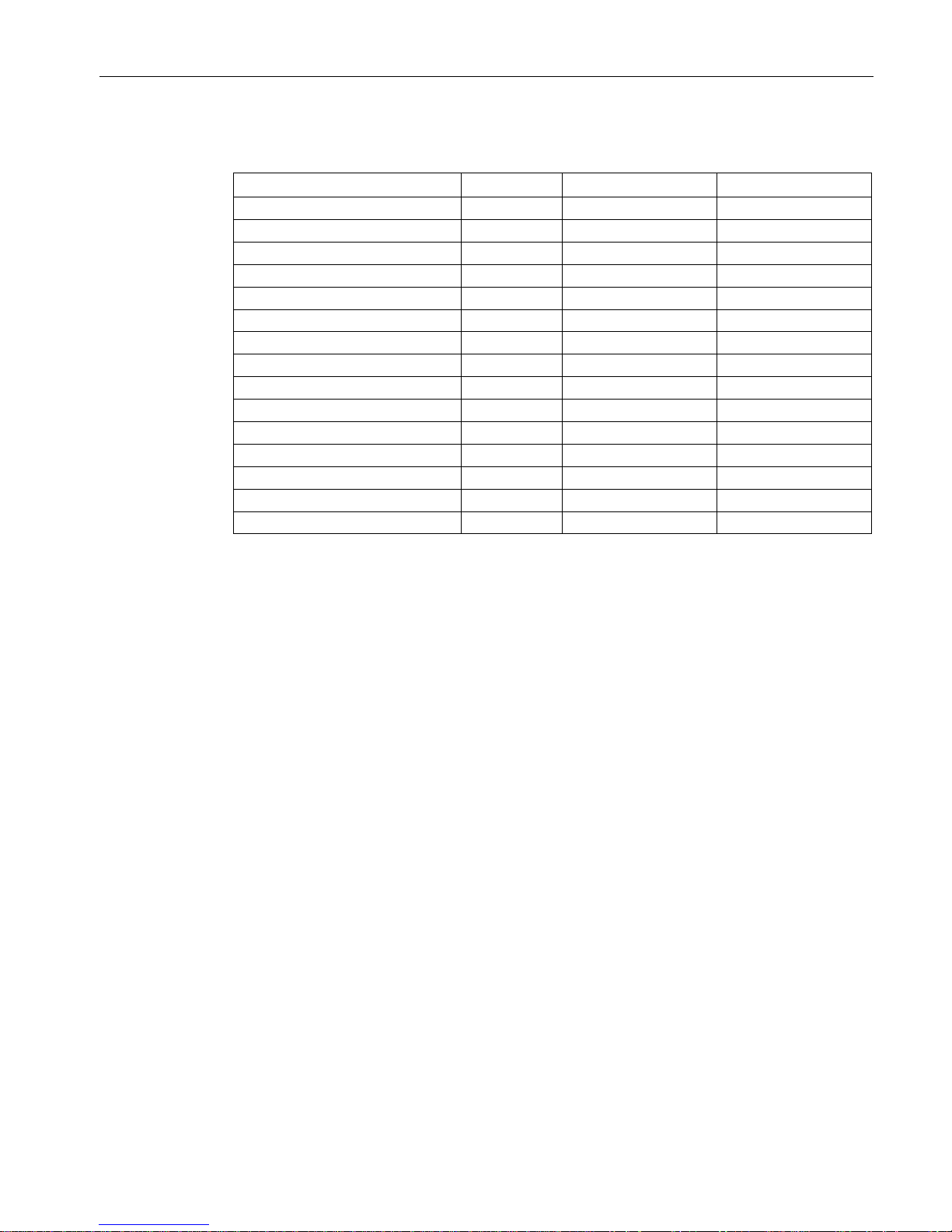
General information about SINAMICS Safety Integrated
3.1 Supported functions
Safety Integrated
Function Manual, 07/2016, A5E03264275A
21
Supported Safety Integrated Extended Functions
Transferring safe position values
Safe Acceleration Monitor
Safe gearbox stage switchover
: Two SMC30 Sensor Modules (HTL/TTL encoders)
The use of this safety function without an encoder is permitted only for induction motors.
3)
Using Safe Brake Adapter (option K88).
: Terminal Module TM54F
● PROFIsafe
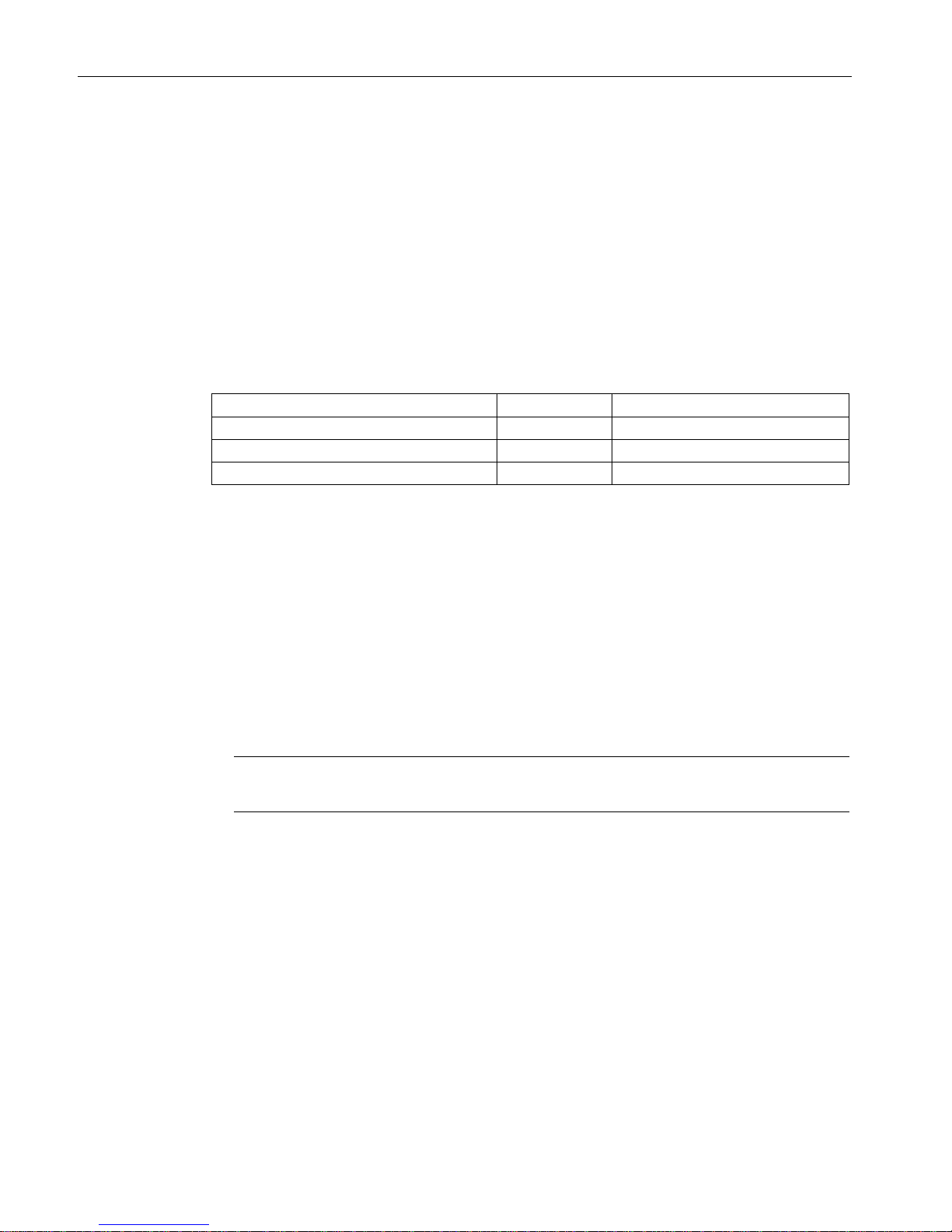
General information about SINAMICS Safety Integrated
3.1 Supported functions
Safety Integrated
22 Function Manual, 07/2016, A5E03264275A
SINAMICS S120 chassis
3.1.3.1
Basic functions
Requirements
The Safety Integrated Basic Functions are part of the standard scope of the drive and can be
used without an additional license.
Supported Safety Integrated Basic Functions
● Control Unit and terminal (on the power unit)
● PROFIsafe and terminal (on the power unit)
Extended Functions
Requirements
: Safety license for one to five axes
Note
The term "axes" should also be interpreted as "drives".
● For Extended Functions with encoder:
– Sin/cos sensor evaluation (SMC20, SME20/25/120/125, SMI20 Sensor Modules) or
– Two SMC30 Sensor Modules (HTL/TTL encoders)
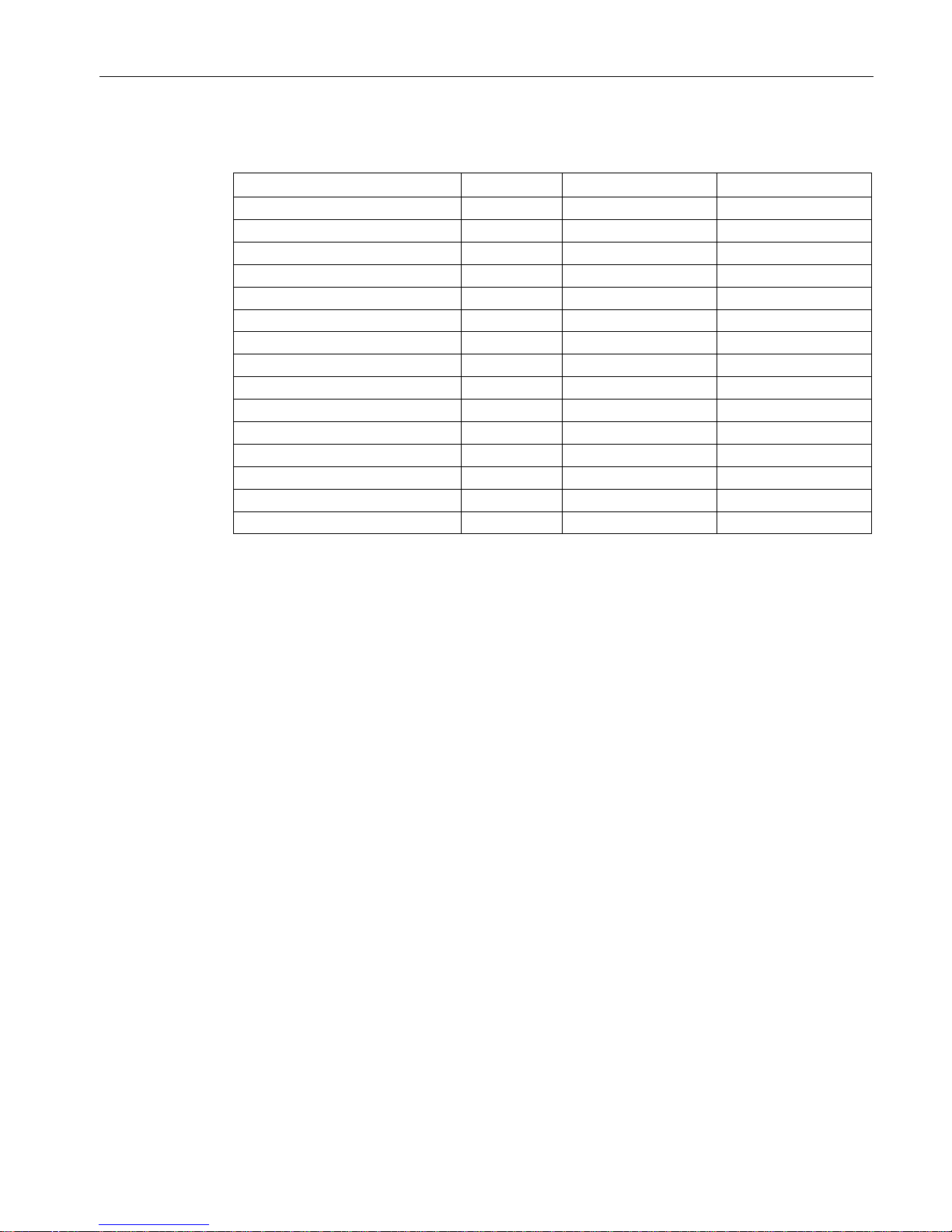
General information about SINAMICS Safety Integrated
3.1 Supported functions
Safety Integrated
Function Manual, 07/2016, A5E03264275A
23
Supported Safety Integrated Extended Functions
Transferring safe position values
Safe Acceleration Monitor
Safe gearbox stage switchover
Sin/cos sensor evaluation or 2 SMC30 Sensor Modules (HTL/TTL encoders)
The use of this safety function without an encoder is permitted only for induction motors.
3)
Using Safe Brake Adapter.
● Terminal (TM54F)
● PROFIsafe
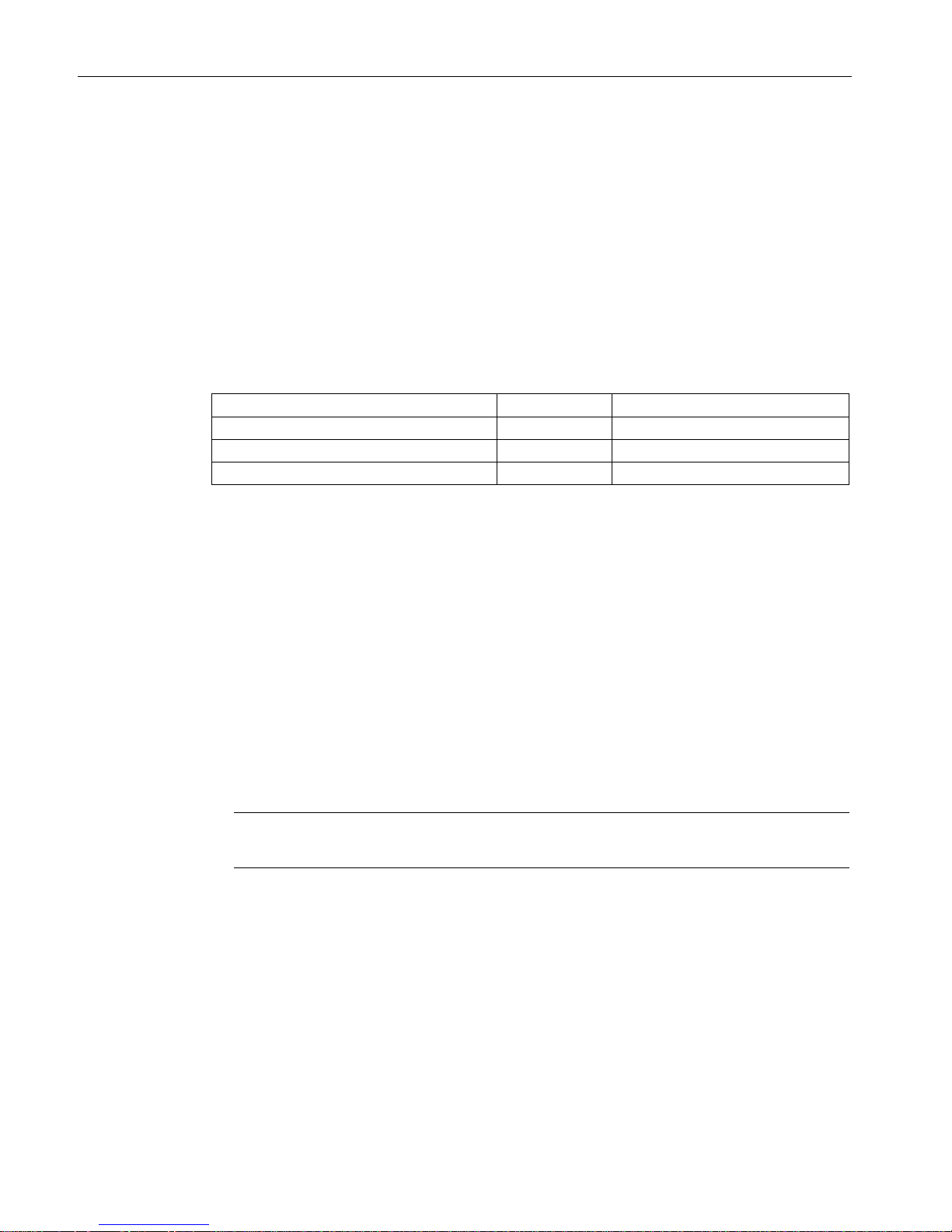
General information about SINAMICS Safety Integrated
3.1 Supported functions
Safety Integrated
24 Function Manual, 07/2016, A5E03264275A
SINAMICS S120 Cabinet Modules, booksize format
3.1.4.1
Basic functions
Requirements
The Safety Integrated Basic Functions are part of the standard scope of the drive and can be
used without an additional license.
Supported Safety Integrated Basic Functions
: Terminal Module for controlling safety functions "STO" and "SS1"
● Control Unit and terminal (on the power unit)
● PROFIsafe and terminal (on the power unit)
Extended Functions
Requirements
: Safety license for one to five axes
Note
The term "axes" should also be interpreted as "drives".
● For Extended Functions with encoder
– Option
: SMC20 Sensor Module (sin/cos encoder) or
– Options
: Two SMC30 Sensor Modules (HTL/TTL encoders)
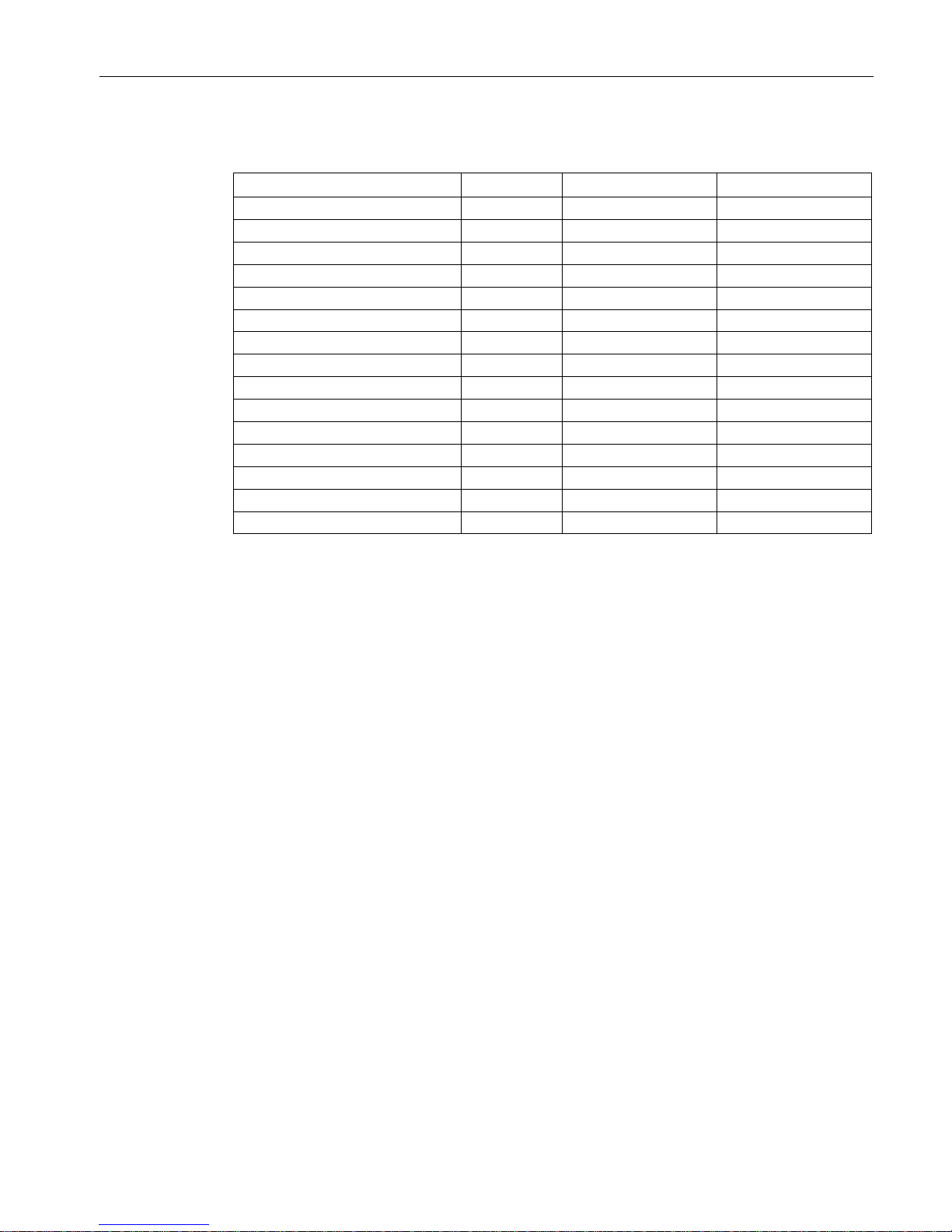
General information about SINAMICS Safety Integrated
3.1 Supported functions
Safety Integrated
Function Manual, 07/2016, A5E03264275A
25
Supported Safety Integrated Extended Functions
Transferring safe position values
Safe Acceleration Monitor
Safe gearbox stage switchover
: SMC20 Sensor Module (sin/cos encoder) or
options
: Two SMC30 Sensor Modules (HTL/TTL encoders)
The use of this safety function without encoder is permitted only for induction motors or synchro-
nous motors of the SIEMOSYN series.
: Terminal Module TM54F
● PROFIsafe

General information about SINAMICS Safety Integrated
3.1 Supported functions
Safety Integrated
26 Function Manual, 07/2016, A5E03264275A
SINAMICS S120 Cabinet Modules, chassis format
3.1.5.1
Basic functions
Requirements
The Safety Integrated Basic Functions are part of the standard scope of the drive and can be
used without an additional license.
Supported Safety Integrated Basic Functions
: Terminal Module for controlling safety functions "STO" and "SS1"
● Control Unit and terminal (on the power unit)
● PROFIsafe and terminal (on the power unit)
Extended Functions
Requirements
: Safety license for one to five axes
Note
The term "axes" should also be interpreted as "drives".
● For Extended Functions with encoder:
– Option
: SMC20 Sensor Module (sin/cos encoder) or
– Options
: Two SMC30 Sensor Modules (HTL/TTL encoders)
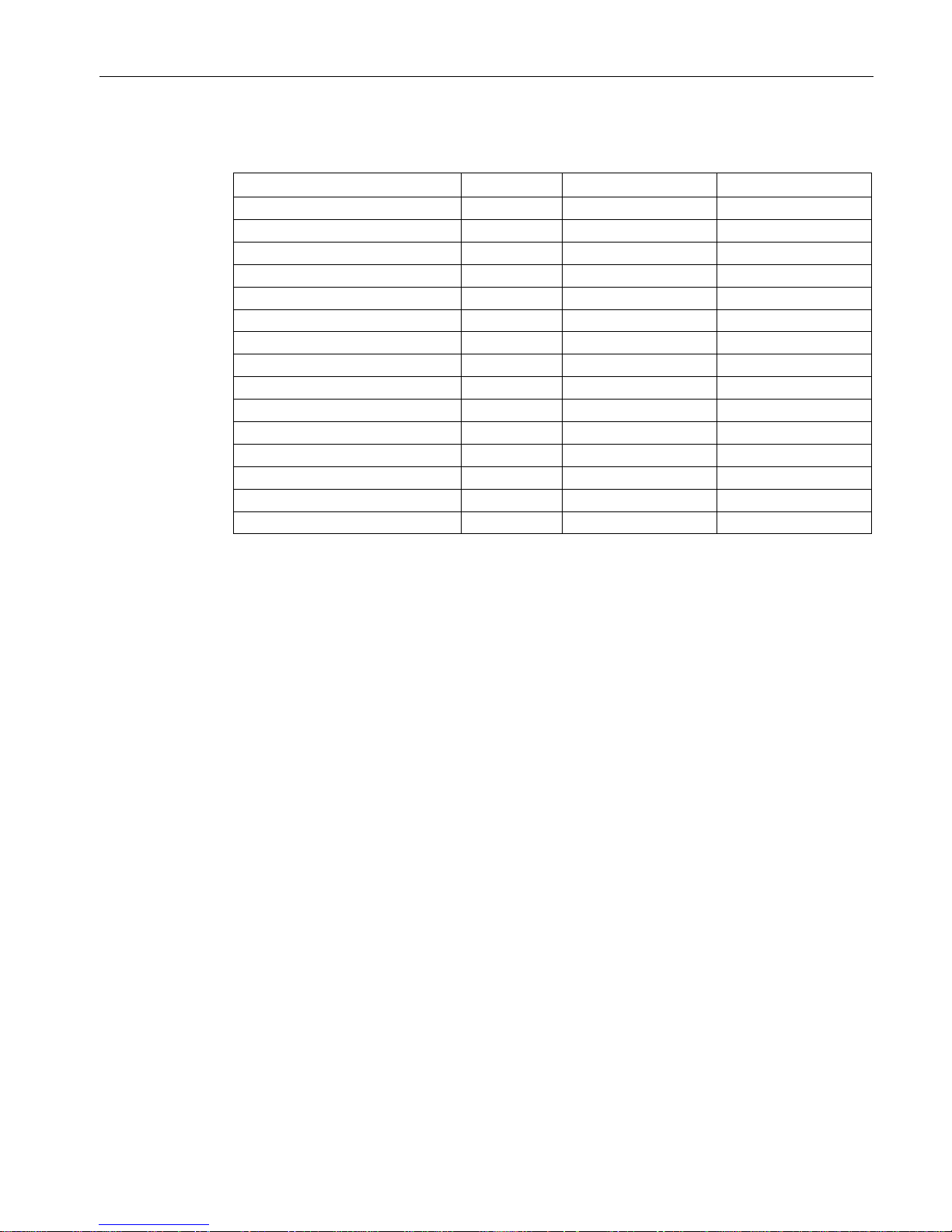
General information about SINAMICS Safety Integrated
3.1 Supported functions
Safety Integrated
Function Manual, 07/2016, A5E03264275A
27
Supported Safety Integrated Extended Functions
Transferring safe position values
Safe Acceleration Monitor
Safe gearbox stage switchover
: SMC20 Sensor Module (sin/cos encoder) or
options
: Two SMC30 Sensor Modules (HTL/TTL encoders)
The use of this safety function without an encoder is permitted only for induction motors.
3)
Using Safe Brake Adapter (option K88).
: TM54F Terminal Module
● PROFIsafe
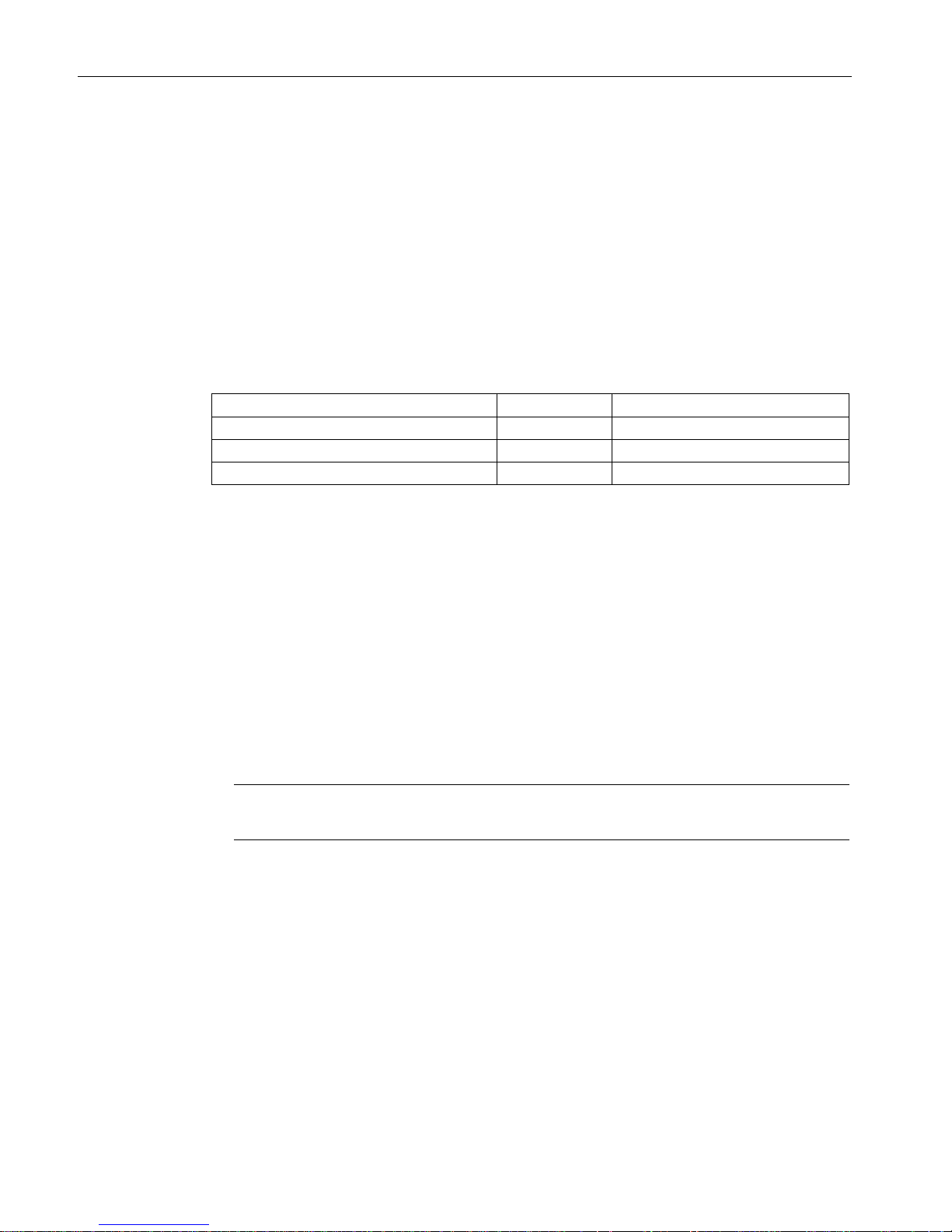
General information about SINAMICS Safety Integrated
3.1 Supported functions
Safety Integrated
28 Function Manual, 07/2016, A5E03264275A
Basic functions
Requirements
The Safety Integrated Basic Functions are part of the standard scope of the drive and can be
used without an additional license.
Supported Safety Integrated Basic Functions
: Terminal Module for controlling safety functions "STO" and "SS1"
● Control Unit and terminal (on the power unit)
● PROFIsafe and terminal (on the power unit)
Extended Functions
Requirements
: Safety license for one axis
ould also be interpreted as "drives".
● For Extended Functions with encoder:
– Option
: SMC20 Sensor Module (sin/cos encoder) or
– Options
: Two SMC30 Sensor Modules (HTL/TTL encoders)
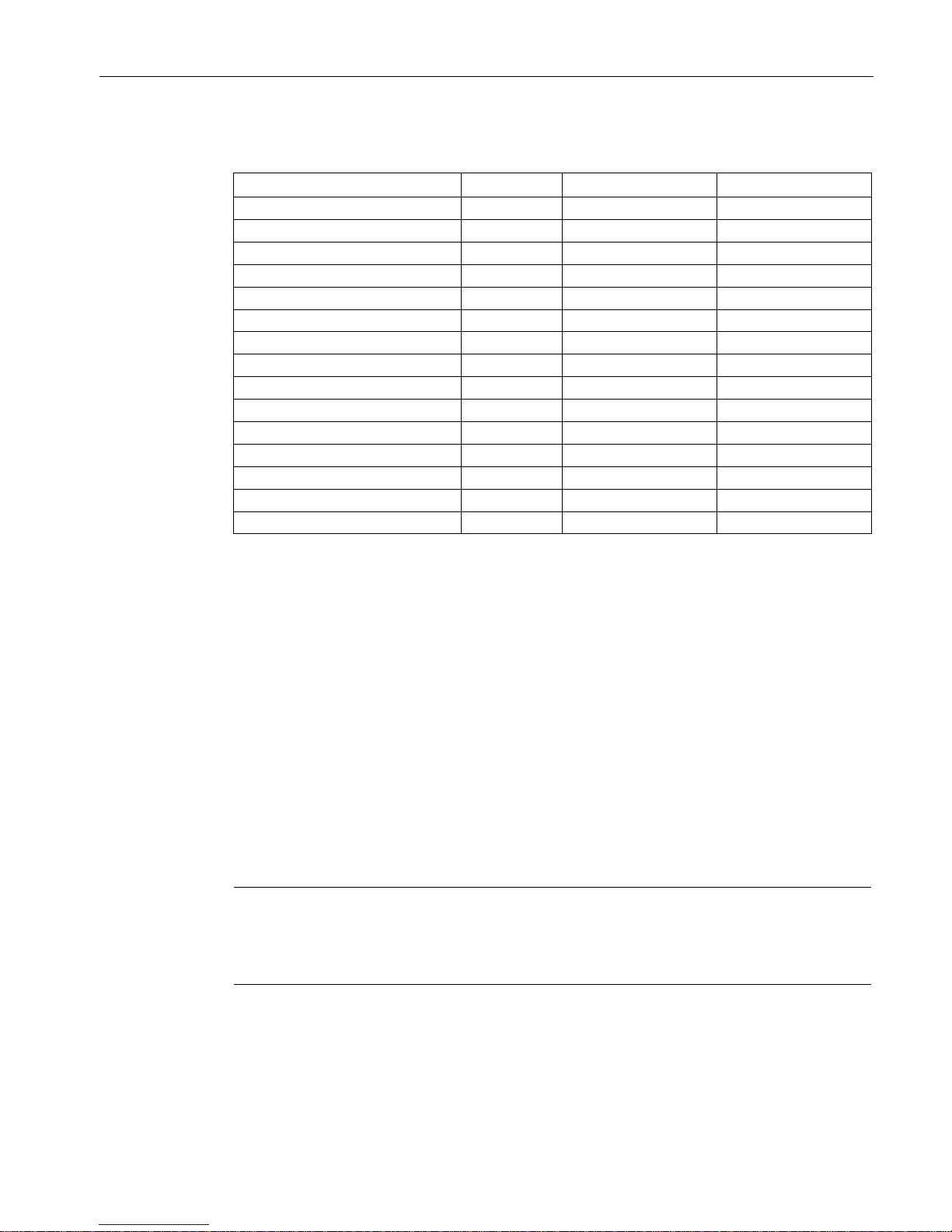
General information about SINAMICS Safety Integrated
3.2 Drive monitoring with or without encoder
Safety Integrated
Function Manual, 07/2016, A5E03264275A
29
Supported Safety Integrated Extended Functions
Transferring safe position values
Safe Acceleration Monitor
Safe gearbox stage switchover
: SMC20 Sensor Module (sin/cos encoder) or
options
: Two SMC30 Sensor Modules (HTL/TTL encoders)
The use of this safety function without an encoder is permitted only for induction motors.
3)
Using Safe Brake Adapter (option K88).
: TM54F Terminal Module
● PROFIsafe
Drive monitoring with or without encoder
If motors without a (safety-capable) encoder are being used, not all Safety Integrated
functions are available.
Note
Definition: "Without encoder"
When "without encoder" is used in this manual, then this always means that either no
encoder or no safety
-capable encoder is being used.
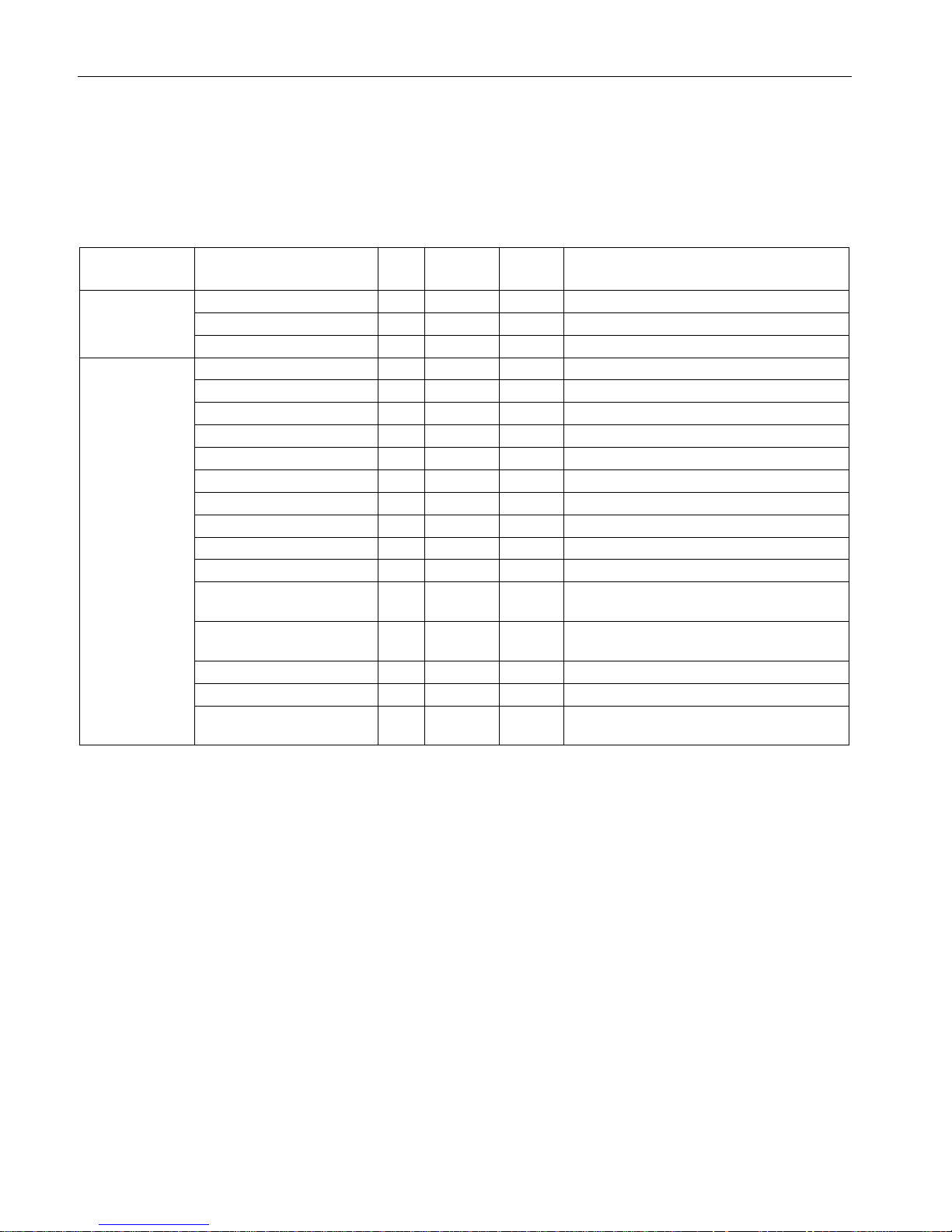
General information about SINAMICS Safety Integrated
3.2 Drive monitoring with or without encoder
Safety Integrated
30 Function Manual, 07/2016, A5E03264275A
In operation without encoder, the actual speed values are calculated from the measured
electrical actual values. Therefore, speed monitoring is also possible during operation
without encoder.
Table 3- 1 Overview of Safety Integrated functions
Safe Stop 1 SS1 Yes Yes Safe stop according to stop category 1
Safe stop according to stop category 1
Safe monitoring of the standstill position
Safe stop according to stop category 2
Safe monitoring of the maximum speed
Safe monitoring of the minimum speed
Safe monitoring of the direction of motion
Transferring safe position
SP Yes Yes1) Transferring safe position values
Safe Brake Test SBT Yes No Safe test of the required holding torque of a
Safe Acceleration Monitor
Safe monitoring of drive acceleration
Safe gearbox stage switch-
The use of this safety function without encoder is permitted only for induction motors or synchronous motors of the
The configuration of the Safety Integrated functions and the selection of monitoring with or
without encoder is realized in the Safety screens of the STARTER or SCOUT tools.