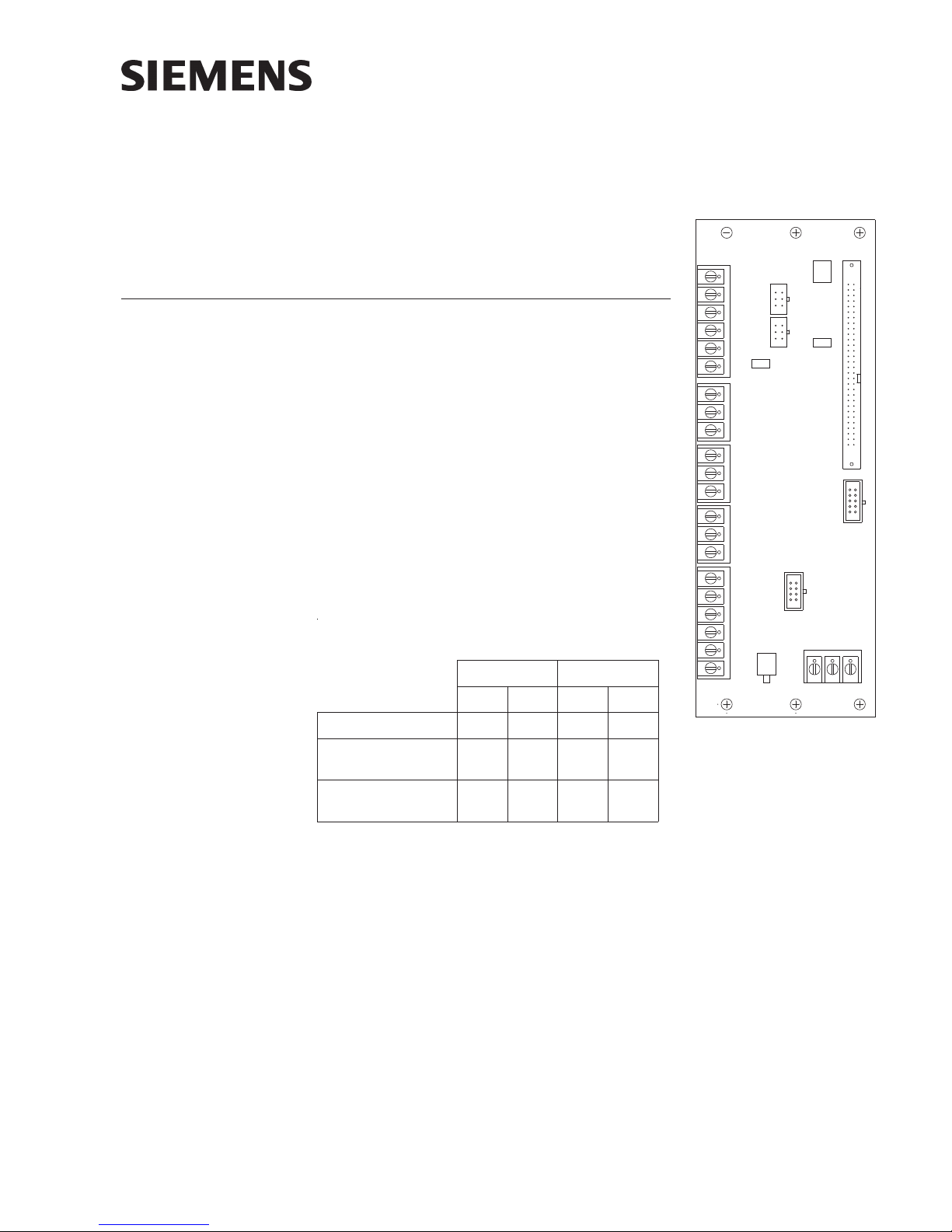
Installation Instruct ions
Model RNI
Remote Network Interface
INTRODUCTION The Model RNI from Siemens Industry, Inc., allows for
the remote installation of the PMI/PMI-2/PMI-3, Global
PMI/PMI-2/PMI-3 (on XNET), SSD-C-REM (on HNET),
and the LVM/LCM-8/SCM-8/FCM-6/SIM-16/OCM-16
(on CAN) modules. When used in a REMBOX4, the
FMT and LVM are also supported.
The HNET/XNET can be wired either Style 4 or Style
7. The RNI must be placed in between two NIC-Cs
when used in a Style 7 Network with the Global PMI/
PMI-2/PMI-3 (on XNET) or the SSD-C-REM (HNET).
When using the PMI/PMI-2/PMI-3, the RNI may be
located in the middle or at the end of the HNET. Refer
to the table below for the allowable locations of
modules at the end of a HNET or XNET.
TB6
TB5
TB4
TB3
P6
P4
P3
X
H
OFF
P7
P5
ON
JP1
P1
RNI
P2
afodnEehttatnemecalPeludoM
krowteNTENXroTENH
TENHTENX
TB2
24 V
S1
TB1
4elytS7elytS4elytS7elytS
MER-C-DSSYN**
3-IMP/2-IMP/IMP
)TENH(
)TENX(3-IMP/2
YY* *
-IMP/IMPLABOLG
**YN
krowtensihtnodewollatoN*,dewollA=Y,dewollatoN=N
Figure 1
RNI Remote Network
Interface
The CAN network may only be wired Style 4. The RNI may be located at the end or in
the middle of a CAN network. A 24VDC input is also required. This can be obtained
from the PSC-12 power limited output (TB3) or any 24 VDC UL/ULC regulated, power
limited power supply listed for fire protective signaling use. Audio signals for the LVM
and FMT are connected to TB1 of the PSC-12.
The RNI mounts in the rear of either the REMBOX2 or REMBOX4 enclosures. It can
also be installed in a CAB1, CAB2, or CAB3 using the mounting plate RNI-CAB-BRKT.
The RNI provides terminal blocks for all field wiring connections. Internal connections
are made to plug in connectors specifically provided for each of the installed modules.
The HNET/XNET and the CAN networks can be used simultaneously.
P/N 315-033420-13
Building Building
Building
Building Building
Siemens Siemens
Siemens
Siemens Siemens
TT
ecec
hnologies Dihnologies Di
T
ec
hnologies Di
TT
ecec
hnologies Dihnologies Di
IndustryIndustry
Industry
IndustryIndustry
visionvision
vision
visionvision
,,
Inc. Inc.
,
Inc.
,,
Inc. Inc.
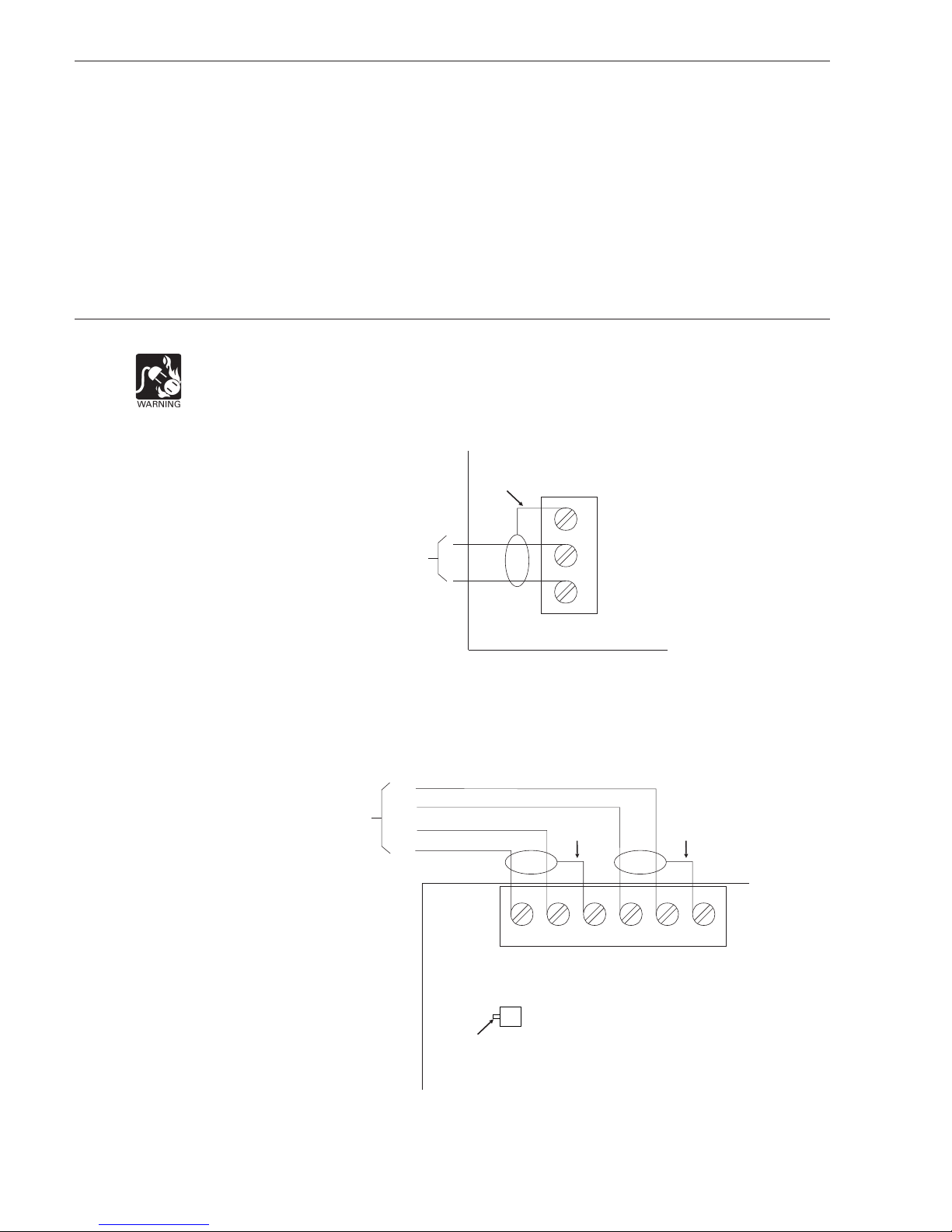
PRE-INSTALLATION P7 enables or disables an audible device similar to the CSB. This audible sounds
whenever a switch is pressed on either the LVM, SCM-8 or the FCM-6. If this is not
desired the audible can be silenced by changing the jumper installed on P7 to
positions 2 and 3. P7 is configured in the factory (positions 1 and 2) to have the
audible active.
S1 is used to terminate the HNET/XNET. If the RNI is installed at the end of an HNET
network, S1 must be set to the ON position. If the RNI is in the middle of the HNET/
XNET, set S1 to the OFF position.
P5 must be set to the HNET (H) position to select HNET or the XNET (X) position to
select XNET. Only one network, either HNET or XNET, can be used.
INSTALLATION
Remove all system power before installation, first battery then AC. (To power up,
connect the AC first, then the battery.)
RNI
SHIELD
NOTES:
1. 14-18 AWG.
2. 2A max. input current.
3. Supervised
4. Refer to PSC-12/PSX-12
Installation Instructions,
P/N 315-033060 for
connection to TB3 and
ground fault detection
impedance.
NOTES:
1. No EOLR required.
2. 18 AWG min., 14 AWG max.
3. 2000 feet max. per pair.
4. Use twisted pair (Style 4/7)
or twisted shielded pair
(Style 4 only).
5. Power limited to NFPA 70
per NEC 760.
6. Refer to NIC-C Installation
Instructions, P/N 315033240 for connection of
A and B pairs and ground
fault detection impedance.
7. Omit B pair for Style 4.
8. All wiring supervised.
TO PSC-12 TB3
OR ANY UL/ULC
REGULATED,
POWER LIMITED
POWER SUPPLY
LISTED FOR FIRE
PROTECTIVE
SIGNALING USE
S3
24 V
–
2
1
+
TB1
Figure 2
Connecting The 24VDC Input
B+
FROM
NIC-C
B–
A+
A–
SHIELD
SHIELD
TB2
5
B+
6
S
PRESS
DOWN
1
A–
S1
2
A+
SET TO ON
4
3
B–
S
RNI
Figure 3
Connecting HNET/XNET At The End Of The Network (Style 4 and Style 7)
(HNET PMI/PMI-2/PMI-3 Only For Style 7)
Siemens Industry, Inc.
Building Technologies Division
P/N 315-033420-132
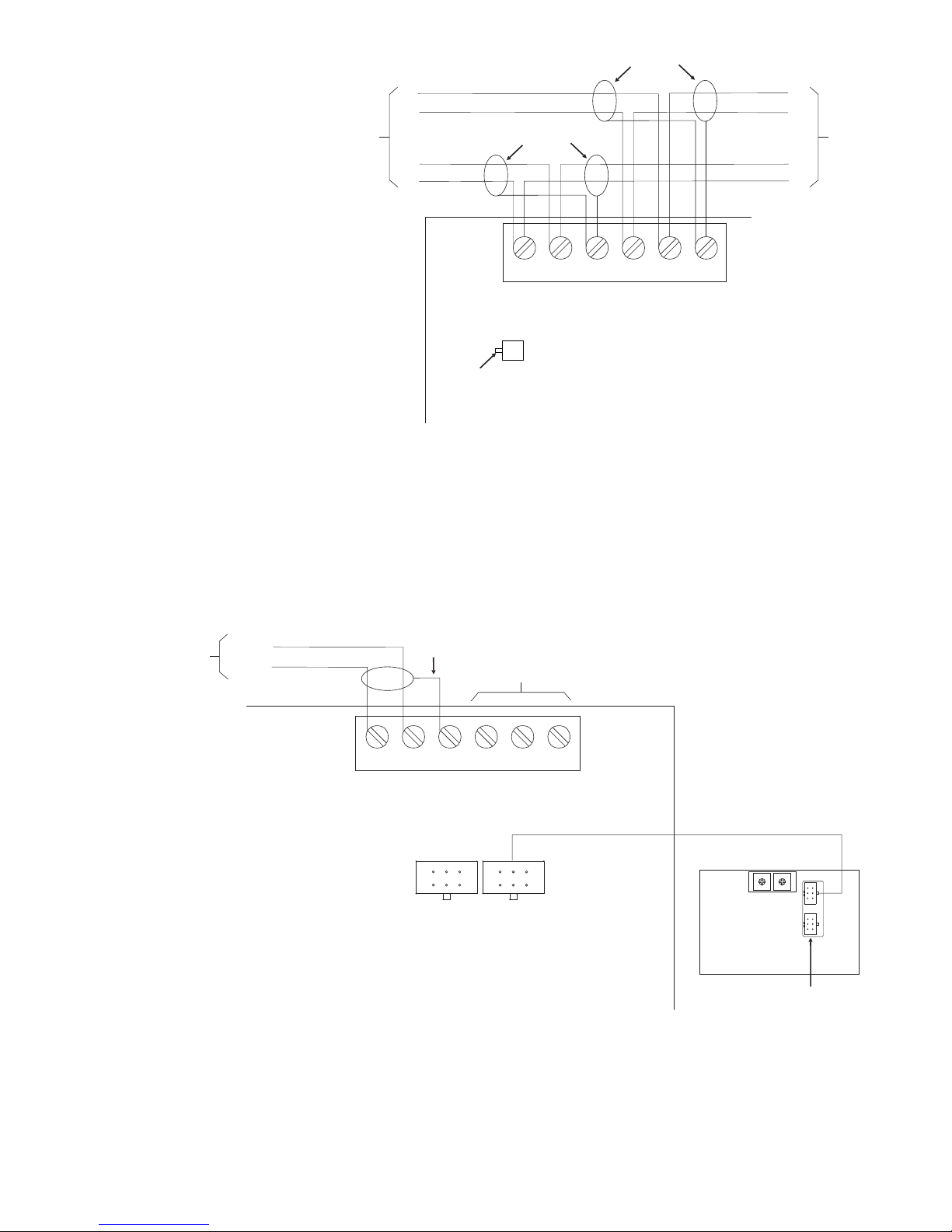
SHIELD
1
4
3
6
4
1
3
6
P3 P4
CAN +
CAN –
SHIELD
FROM
PSC-12
TB1
1
C+
2
C–
CCL (SUPPLIED WITH THE RNI)
3
S
4
C+
5
C–
6
S
RNI
TB6
DO NOT
USE
DO NOT
USE
1
2
3
4
5
6
7
8
9
0
1
2
3
4
5
6
7
8
9
0
LCM-8
OR
SCM-8
INSTALL
CAN TERMINATOR
P/N 110-134215
(SHIPPED WITH NIC-C)
MOUNT TO ID-MP
ON INNER DOOR
OF REMBOX2/4
†
†
NOTES:
1. No EOLR required.
2. 18 AWG min., 14 AWG max.
3. 2000 feet max. per pair
between NIC-Cs.
4. Use twisted pair (Style 4/7)
or twisted shielded pair
(Style 4 only).
5. Power limited to NFPA 70
per NEC 760.
6. Refer to NIC-C Installation
Instructions, P/N 315033240 for connection of
A and B pairs and ground
fault detection impedance.
7. Omit B pair for Style 4.
8. All wiring supervised.
B+
B–
A+
A–
FROM
NIC-C
OR RNI
B+
B–
SHIELD
A+
A–
TB2
5
B+
RNI
6
S
PUSH
UP
1
A–
S1
2
A+
SET TO OFF
4
3
B–
S
Figure 4
Connecting HNET/XNET In The Middle Of The Network (Style 4 and Style 7)
TO NEXT
NIC-C
OR RNI
NOTES:
1. 18 AWG min., 14 AWG max.
2. 15 ohms max. for CAN
network.
3. Use twisted pair or twisted
shielded pair.
4. Power limited to NFPA 70
per NEC 760.
5. Refer to NIC-C Installation
Instructions, P/N 315033240 for connection of
CAN–, CAN+.
6. Only 1 SCM-8 shown. SCM8, LCM-8, FCM-6, OCM-16,
SIM-16 all allowed.
7. All field wiring supervised.
8. Refer to PSC-12 Installation
Instructions, P/N 315033060 for ground fault
detection impedance.
Siemens Industry, Inc.
Building Te chnologies Division
Figure 5
Connecting CAN At The End Of The Network
P/N 315-033420-133