
Contents
Section Page
Health and safety 3
Storage 4
Mounting the actuator 4
Setting the actuator stop bolts 5
Cable connections 6
Operating by hand 7
Commissioning 8
Troubleshooting 13
Wiring diagram 14
CHANGE PHOTO
PHOTO CAN BE
DELETED IF TWO
COLUMNS OF
CONTENTS ARE
REQUIRED
This manual contains important
safety information. Please ensure it
is thoroughly read and understood
before installing, operating or
maintaining the equipment.
2
Due to wide variations in the terminal
numbering of actuator products, actual
wiring of this device should follow the
print supplied with the unit.

Health and Safety
This manual is produced to enable a
competent user to install, operate,
adjust and inspect Rotork ROM valve
actuators.
Only persons competent by virtues of their training
or experience should install, maintain and repair
Rotork actuators. Work undertaken must be carried
out in accordance with the instructions in this and
any other relevant manuals.
The user and those persons working on this
equipment should be familiar with their
responsibilities under any statutory provisions
relating to the health and safety of their workplace.
Due considerations of additional hazards should
be taken when using the ROM actuators with
other equipment. Should further information and
guidance relating to the safe use of the ROM be
required, it will be provided on request.
Electrical installation, maintenance and use of these
actuators should be carried out in accordance with
the National Legislation and Statutor y Provisions to
the safe use of this equipment, applicable to the site
of installation.
For the UK: Electricity at Work Regulations 1989
and the guidance given in the applicable edition
if the “IEE Wiring Regulations” should be applied.
Also the user should be fully aware of his/her duties
under the Health and Safety Act 1974.
For the USA: N FPA 70 National Electrical Code is
applicable.
The mechanical installation should be carried out as
outlined in this manual and also in accordance with
relevant standards such as British Standard Codes
of Practice.
Actuator may start and operate without
warning, depending on the remote control
signal status and configuration.
Important Notices
a. Make sure the voltage is correct before wiring.
b. Power off before distribution or for
maintenance purposes.
c. Seal the casing and conduit entries after wiring
to prevent dust or water contamination.
d. Do not install when hazardous or explosive
gases may be present.
e. When more than one electric actuator needs
to operate simultaneously, please connect with
the individual cables.
f. Please connect the ground wire to PE or
inside the electric actuator.
g. The warranty period of our product is one year.
Duty performance
ROM perform Class A for standard type as table
shown according to EN 15714-2:2009(E).
BS EN 15714-2:2009
EN 15714-2:2009(E)
Rated Torque Ranges
Nm
Up to 125 15
126 - 1,000 10
*
One cycle consists of nominal 90o angular travel
in both directions (i.e. 90o to open +90o to close)
based on an average load of at least 30% of the
rated torque, with the ability to transmit 100%
of the rated torque for at least 5% at each end
of travel, with a cumulative operating time not
exceeding 15 minutes in one hour.
Table 6 Part-turn actuator duty performances
According to EN 15714-2:2009(E), duty performance
for ROM is described as follows:
For ROM A and ROM 1, 2: 15 cycles per hour
For ROM 3, 4, 5, 6: 10 cycles per hour
Class A
On-Off
(cycles per hour*)
Redefining Flow Control
3

Storage
Storage
If the actuators are scheduled for installation at a
later date:
a. The actuator should be placed in a clean and
dry place, and protected from the weather and
extreme vibration.
b. If actuator needs to be stored outside, it must
be protected from excess moisture, dust, and
weather.
Rotork cannot accept responsibility for deterioration
caused on-site once the covers are removed.
Every Rotork actuator has been fully tested before
leaving the factory to give years of trouble free
operation providing it is correctly commissioned,
installed and sealed.
Mounting the actuator
The ROM actuator is suitable for quarter turn non
thrust applications. Ensure the valve is secure before
fitting the actuator, as the combination may be top
heavy and therefore unstable.
A suitable mounting flange conforming to ISO5211
or USA Standard MSS SP101 must be fitted to the
valve. Refer to label for conformation of output
flange details.
ROM can be supplied with adaptors to reduce
the size of the output drive square. The square
insert is fitted into the output drive. All ROM
actuators can be supplied with blank drive
bush. This is machined to suit the valve stem as
shown in the picture.
Lubrication
The gear train has been lubricated during assembly
for the life of the actuator.
Installation
a. Before mounting actuator, verify that the
torque requirement is less than the output
torque of the actuator.
Actuator to valve fixing must conform to:
Material Specification ISO Class 8.8, yield strength
628 N/sq mm.
WARNING: Do not lift the actuator and
valve combination via the Actuator. Always lift
the valve/actuator assembly via the valve.
Before engagement, ensure that the actuator and
valve are in the same position (e.g. closed) and the
drive spline matches the stem position. Actuator
position can be determined using the local indicator
and if necessary can be moved using the manual
input drive. Secure the actuator with appropriate
fixing bolts. It may be necessary to adjust the
stop blots to enable sufficient travel. Ensure the
mounting bolts are tight.
4
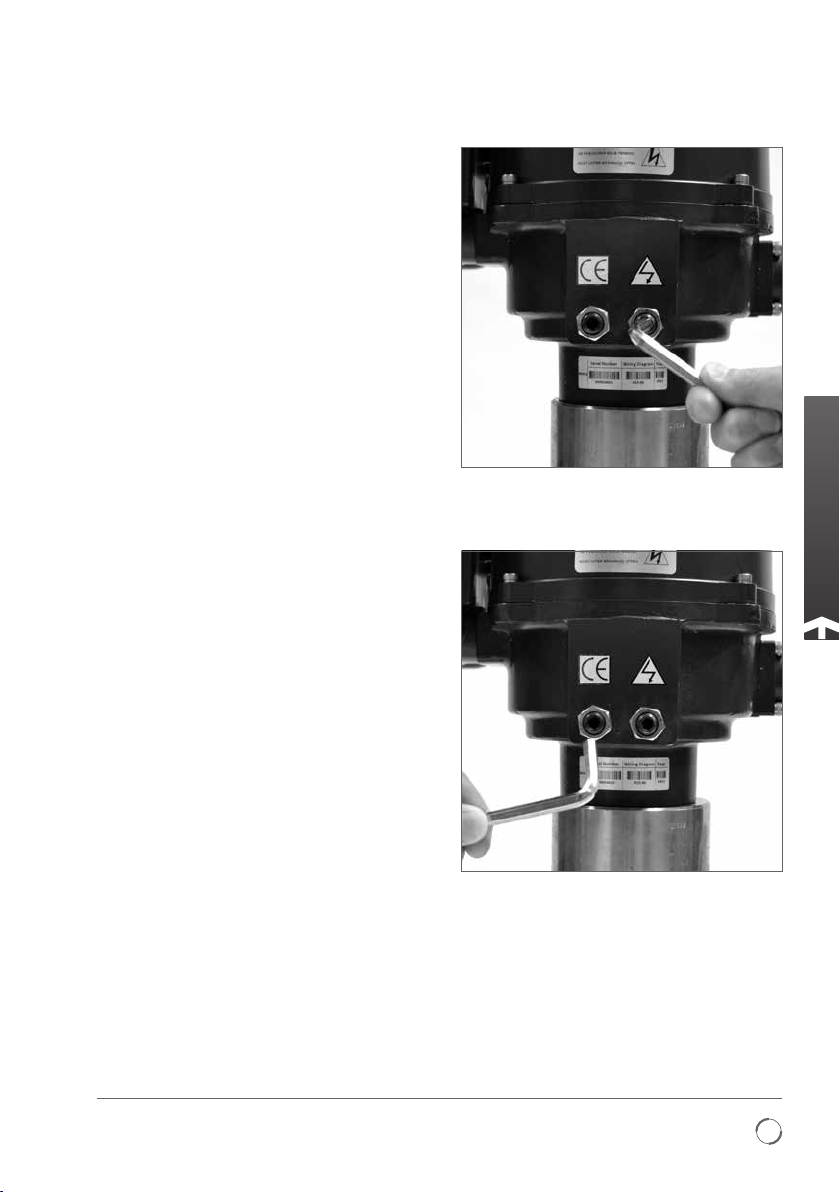
Setting the actuator stop bolts
Stop Bolts
There are no stop bolts fitted in the ROM 1,A.
Adjusting the stop bolts in and out will increase or
decrease the valve travel. It is recommended that
stop bolt adjustment be carried out by the valve
maker/supplier before the valve is fitted into the
pipe work. Once installed, the valve maker/supplier
should be consulted before stop bolt re-adjustment
is carried out. After resetting the stop bolts the limit
switches must be reset. The stop bolts are factory
set to give a nominal 90º travel. If fitted the stop
bolts are located near the gearbox base. Stop bolt
adjustment allows variation at each end position.
Screwing the bolt in reduces movement, out
increases movement.
For clockwise closing valves the right hand stop
bolt is the closed stop. The left is the open stop as
shown in the picture.
Adjustment for non-seating valve types
For closed and open stop position adjustments.
Undo stop bolt lock-nut. Move actuator and valve to
the required stopping position (it may be necessary
to unscrew stop bolt to allow more travel). Screw
stop bolt in until a stop is felt. Tighten stop bolt
lock nut.
Adjustment for seating valve types
For closed and open stop position adjustments.
Undo stop bolt lock-nut. Move actuator and valve
to the required seating position of the valve (it may
be necessary to unscrew stop bolt to allow more
travel). Screw stop bolt in until a stop is felt then
back off by two turns. Tighten stop bolt lock nut
Setting clockwise to close stop bolt
Setting anti-clock to close stop bolt
Redefining Flow Control
5