
CDJ-900NXS
MULTI PLAYER
CDJ-900NXS
THIS MANUAL IS APPLICABLE TO THE FOLLOWING MODEL(S) AND TYPE(S).
Model Type Power Requirement Remarks
CDJ-900NXS UXJCB AC 110 V to 240 V
CDJ-900NXS SYXJ8 AC 110 V to 240 V
CDJ-900NXS FLXJ AC 110 V to 240 V
CDJ-900NXS AXJ5 AC 110 V to 240 V
CDJ-900NXS KXJ5 AC 110 V to 240 V
ORDER NO.
RRV4502
PIONEER CORPORATION 1-1, Shin-ogura, Saiwai-ku, Kawasaki-shi, Kanagawa 212-0031, Japan
PIONEER ELECTRONICS (USA) INC. P.O. Box 1760, Long Beach, CA 90801-1760, U.S.A.
PIONEER EUROPE NV Haven 1087, Keetberglaan 1, 9120 Melsele, Belgium
PIONEER ELECTRONICS ASIACENTRE PTE. LTD. 253 Alexandra Road, #04-01, Singapore 159936
PIONEER CORPORATION
K-MZV DEC.
2013 Printed in Japan

5
6 7 8
CONTENTS
SAFETY INFORMATION.......................................................................................................................................................... 2
1. SERVICE PRECAUTIONS ....................................................................................................................................................4
1.1 NOTES ON SOLDERING............................................................................................................................................... 4
1.2 NOTES ON REPLACING PARTS ................................................................................................................................... 4
1.3 SERVICE NOTICE.......................................................................................................................................................... 5
2. SPECIFICATIONS .................................................................................................................................................................7
3. BASIC ITEMS FOR SERVICE ..............................................................................................................................................8
3.1 CHECK POINTS AFTER SERVICING ........................................................................................................................... 8
3.2 JIGS LIST .......................................................................................................................................................................8
3.3 PCB LOCATIONS ........................................................................................................................................................... 9
4. BLOCK DIAGRAM ..............................................................................................................................................................10
4.1 OVERALL WIRING DIAGRAM .....................................................................................................................................10
4.2 SIGNAL BLOCK DIAGRAM.......................................................................................................................................... 12
4.3 POWER SUPPLY BLOCK DIAGRAM........................................................................................................................... 14
5. DIAGNOSIS ........................................................................................................................................................................ 16
5.1 SEQUENCE..................................................................................................................................................................16
5.2 FAILURE JUDGEMENT OF THE PICKUP ASSY ........................................................................................................ 18
5.3 TROUBLESHOOTING.................................................................................................................................................. 19
5.4 OPERATIONAL WAVEFORMS .................................................................................................................................... 30
5.5 CONNECTION CONFIRMATION WITH THE PC......................................................................................................... 31
6. SERVICE MODE................................................................................................................................................................. 32
6.1 SERVICE MODE .......................................................................................................................................................... 32
6.2 ABOUT THE DEVICE................................................................................................................................................... 46
7. DISASSEMBLY ................................................................................................................................................................... 47
8. EACH SETTING AND ADJUSTMENT................................................................................................................................ 60
8.1 NECESSARY ITEMS TO BE NOTED........................................................................................................................... 60
8.2 FIRMWARE UPDATE / RECOVERY.............................................................................................................................60
8.3 JOG DIAL ROTATION LOAD ADJUSTMENT ............................................................................................................... 61
8.4 ITEMS FOR WHITCH USERS SETTING IS AVAILABLE.............................................................................................62
9. EXPLODED VIEWS AND PARTS LIST...............................................................................................................................64
9.
1 PACKING SECTION ..................................................................................................................................................... 64
9.2 EXTERIOR SECTION .................................................................................................................................................. 66
9.3 CONTROL PANEL SECTION ....................................................................................................................................... 68
9.4 JOG DIAL SECTION .................................................................................................................................................... 70
9.5 SLOT IN MECHA SECTION.........................................................................................................................................72
10. SCHEMATIC DIAGRAM ....................................................................................................................................................74
10.1 SRVB ASSY (1/2) ....................................................................................................................................................... 74
10.2 SRVB (2/2), JINT and SLMB ASSYS ......................................................................................................................... 76
10.3 JACB ASSY ................................................................................................................................................................ 78
10.4 MAIN ASSY (1/6)........................................................................................................................................................80
10.5 MAIN ASSY (2/6)........................................................................................................................................................82
10.6 MAIN ASSY (3/6)........................................................................................................................................................84
10.7 MAIN ASSY (4/6)........................................................................................................................................................86
10.8 MAIN ASSY (5/6)........................................................................................................................................................88
10.9 MAIN ASSY (6/6)........................................................................................................................................................90
10.10 USBB ASSY and DDCB ASSY (1/2) ........................................................................................................................92
10.11 DDCB ASSY (2/2).....................................................................................................................................................94
10.12 LCDB ASSY (1/2) .....................................................................................................................................................96
10.13 LCDB ASSY (2/2) .....................................................................................................................................................98
10.14 PNLB ASSY............................................................................................................................................................100
10.15 KSWB and PSWB ASSYS......................................................................................................................................102
10.16 SLDB and JOGB ASSYS........................................................................................................................................ 103
10.17 JFLB ASSY..................................................................................................................
10.18 POWER SUPPLY and ACIN ASSYS ...................................................................................................................... 106
10.19 WAVEFORMS.........................................................................................................................................................108
11. PCB CONNECTION DIAGRAM......................................................................................................................................110
11.1 SRVB ASSY.............................................................................................................................................................. 110
11.2 JINT, SLMB and JACB ASSYS................................................................................................................................. 114
11.3 MAIN ASSY ..............................................................................................................................................................116
11.4 USBB and DDCB ASSYS.........................................................................................................................................120
11.5 LCDB ASSY..............................................................................................................................................................122
11.6 PNLB ASSY.............................................................................................................................................................. 126
11.7 KSWB, PSWB and SLDB ASSYS ............................................................................................................................ 130
11.8 JOGB and JFLB ASSYS...........................................................................................................................................132
11.9 POWER SUPPLY and ACIN ASSYS ........................................................................................................................136
12. PCB PARTS LIST ............................................................................................................................................................ 138
........................................... 104
A
B
C
D
E
F
CDJ-900NXS
5
6 7 8
3

1
• For environmental protection, lead-free solder is used on the printed circuit boards mounted in this unit.
Be sure to use lead-free solder and a soldering iron that can meet specifications for use with lead-free solders for repairs
accompanied by reworking of soldering.
• Compared with conventional eutectic solders, lead-free solders have higher melting points, by approximately 40 ºC.
Therefore, for lead-free soldering, the tip temperature of a soldering iron must be set to around 373 ºC in general, although
the temperature depends on the heat capacity of the PC board on which reworking is required and the weight of the tip of
the soldering iron.
Do NOT use a soldering iron whose tip temperature cannot be controlled.
Compared with eutectic solders, lead-free solders have higher bond strengths but slower wetting times and higher melting
temperatures (hard to melt/easy to harden).
The following lead-free solders are available as service parts:
• Parts numbers of lead-free solder:
GYP1006 1.0 in dia.
GYP1007 0.6 in dia.
GYP1008 0.3 in dia.
The part listed below is difficult to replace as a discrete component part.
When the part listed in the table is defective, replace whole Assy.
Assy Name
Parts that is Difficult to Replace
Ref No. Function Part No. Remarks
The part listed below is difficult to replace as a discrete component part.
The replaceing method see remarks.
Assy Name
JFLB Assy
JOG FL DEL1058
As the JOG FL is integrated with the FL Holder (DNF1735) with the aid of two
pieces of double-back tape (Z12-016), first remove the integrated JOG FL and
FL Holder, attach a new JOG FL and an FL Holder, using two pieces of
double-back tape, then mount them together. (Note: As the integrated JOG FL
and FL Holder are exactly the same parts as those for the CDJ-2000NXS, you can
handle them in the same manner as with the CDJ-2000NXS.)
V9201
Parts that is Difficult to Replace
Ref No. Function Part No. Remarks
SRVB Assy
12V→USB5V DC/DC converter BD9328EFJ
IC with heat-pad
IC2701
12V→3.3V DC/DC converter BD9328EFJ
IC with heat-pad
IC7302
12V→7.6V DC/DC converter BD9328EFJ
IC with heat-pad
IC7303
DDCB Assy
USB CURRENT LIMIT IC TPS2557DRB
IC with heat-pad
IC2702
LCDB Assy LCD POWER IC R1290K103A
QFN package
IC2001
LCD BACKLIGHT POWER IC BD81A04EFV-M IC with heat-padIC2002
12V→5.2V DC/DC converter
BD9328EFJ IC with heat-padIC2601
12V→3.3V DC/DC converter
BD9328EFJ IC with heat-padIC2602
12V→1.2V DC/DC converter BD9328EFJ IC with heat-padIC705
MAIN Assy
DDR2 K4T1G164QF-BCE7
BGA package
IC1, IC2
MAIN CPU R8A77240D500BG2
BGA package
IC10
AUTHENTICATION CHIP H337S3959 USON package
(UltraSmallOutlineNon-lead)
IC14
DSP D810K013DZKB400 BGA packageIC301
2 3 4
1. SERVICE PRECAUTIONS
1.1 NOTES ON SOLDERING
A
B
C
1.2 NOTES ON REPLACING PARTS
D
E
F
4
1
CDJ-900NXS
2 3 4

5
About the Flash ROM (IC3) in the MAIN Assy
Replacement of the Flash ROM (IC3: DYW1838) in the MAIN Assy is not possible during service, because writing of
the MAC address on the production line is required.
Therefore, the Flash ROM (IC3) is not supplied as a service part. If the Flash ROM is defective, replace the whole MAIN Assy.
About work required after replacement of the Traverse Mechanism Assy (09SD)
After replacement of the traverse mechanism Assy (09SD), enter Service mode then change the drive LD lighting time to "0000".
For details on how to confirm and change the LD lighting time, see "7 Drive LD life manual input" in "[3] Indication of
various information" in "6.1 SERVICE MODE."
About transfer of the accumulated LD lighting time data after replacement of the MAIN Assy
This unit is equipped with self-diagnostic functions for the drives in Service mode. The service-life check for the laser
diode among the self-diagnostic functions uses the accumulated lighting time for judgment. If it is 7,000 hours or less, the laser
diode is judged as OK. The accumulated lighting time of the LD is stored in the Flash ROM (IC3: DYW1838) in the MAIN Assy.
Therefore, after replacement of the MAIN Assy, the accumulated lighting time of the LD is cleared and proper judgment will not
be possible after that. To avoid such a situation, when replacement of the MAIN Assy is required, transfer the LD accumulated
lighting time data.
Before replacement, confirm the drive LD lighting time in Service mode and take note of the time value. After replacement
is finished, enter Service mode then change the drive LD lighting time value to what you noted.
For details on how to confirm and change the LD lighting time, see "7 Drive LD life manual input" in "[3] Indication of
various information" in "6.1 SERVICE MODE."
About the self-diagnostic functions for the drives
This unit has self-diagnostic functions for the drives in Service mode. Use the self-diagnostic functions to check the drives if
the problem symptom pointed out by the customer is a malfunction related to the drives or if a drive-related error is logged in
the error history.
For details on the self-diagnostic functions for the drives, see "[5] Drive Self-Diagnosis" and "[6] Contents of Drive
Self-Diagnosis" in "6.1 SERVICE MODE."
About backup of the UTILITY settings
As this unit is provided with user-settable UTILITY settings (such as the Play mode setting,) it is recommended that you back
up the settings before starting repair. The settings can be stored for backup in a USB memory device.
For details on how to back up and restore data, see "g How to Back Up and Restore the Settings" in "8.4 ITEMS
FOR WHICH USER SETTINGS ARE AVAILABLE ."
Note on detachment of the control panel
The control panel cannot be opened wide, because the 50-pin flexible cable connecting the control panel (CN2004 on the
LCDB Assy) and the main unit (CN2802 on the DDCB Assy) is short.
When the control panel must be detached, such as during diagnosis, be careful not to break the flexible cable or damage the
connectors.
Control panel Section
50P flexible cable
LCDB Assy
DDCB Assy
CN2802
CN2004
Main unit
OK NG
6 7 8
1.3 SERVICE NOTICE
A
B
C
D
5
CDJ-900NXS
6 7 8
E
F
5

5
Power requirements....................... AC 110 V to 240 V, 50 Hz/60 Hz
Power consumption..................................................................33 W
Power consumption (standby) ................................................0.4 W
Main unit weight.......................................................... 4.3 kg (9.5 lb)
Max. dimensions....... 320 mm (W) × 105.5 mm (H) × 401.8 mm (D)
(12.6 in. (W) × 4.2 in. (H) × 15.8 in. (D))
Tolerable operating temperature
...............................................+5 °C to +35 °C (+41 °F to +95 °F)
Tolerable operating humidity............5 % to 85 % (no condensation)
Analog audio output (AUDIO OUT L/R)
Output terminals ..........................................................RCA terminal
Output Level .......................................................... 2.0 Vrms (1 kHz)
Frequency response................................................. 4 Hz to 20 kHz
S/N ratio.................................................................................115 dB
Total harmonic distortion .....................................................0.003 %
Digital audio output (DIGITAL OUT)
Output terminals ..........................................................RCA terminal
Output type..................................................Coaxial digital (S/PDIF)
Output level.............................................................. 0.5 Vp-p (75 Ω)
Output format................................................. 44.1 kHz, 24 bit/16 bit
USB downstream section (USB)
Port........................................................................................ Type A
Power supply..........................................................5 V/2.1 A or less
USB upstream section (USB)
Port........................................................................................ Type B
LAN (PRO DJ LINK)
Rating ........................................................................... 100Base-TX
Control output (CONTROL)
Port..................................................................................... Mini-jack
Main display
Display type...............Active matrix TFT liquid crystal display (LCD)
Supported languages ................................................. 18 languages
• CD-ROM (containing rekordbox (Mac/Windows), the driver
software and the operating instructions.
The rekordbox (Mac/Windows)
license key is attached to the CD-ROM.)
(DXX2739)
• Power cord
(UXJCB: ADG7022)
(SYXJ8: ADG1154)
(FLXJ: ADG1154, ADG7097)
(AXJ5: ADG7079)
(KXJ5: ADG7113)
• Audio cable
(XDE3045)
• LAN cable
(DDE1141)
• Disc force eject pin (mounted on bottom of product)
(DEX1023)
• Read Before Use (Important)/Quick Start Guide
(UXJCB: DRH1228)
(SYXJ8: DRH1229)
(FLXJ: DRH1230)
(AXJ5: DRH1231)
(KXJ5: DRH1232)
Accessories
2. SPECIFICATIONS
6 7 8
A
B
C
D
E
F
CDJ-900NXS
5
6 7 8
7

1
Items to be checked after servicing
Distortion
Noise
Volume too low
Volume too high
Volume fluctuating
Sound interrupted
See the table below for the items to be checked regarding audio.
No. Procedure
Item to be checked regarding audio
Check points
To keep the product quality after servicing, confirm recommended check points shown below.
1 Confirm the firmware version on Service mode. The version of the firmware must be latest.
Update firmware to the latest one, if it is not the latest.
2 Confirm whether the customer complain has been solved.
If the customer complain occurs with the specific disc, use it for
the operation check.
The customer complain must not be reappeared.
Audio and operations must be normal.
3 Playback a disc. (track search) Audio, Search and operations must be normal.
5 Check output signals while the Jog dial or TEMPO slider is being
operated.
Audio and operations must be normal.
6 Check the keys on the unit. Check whether a product can be operated properly by buttons
on the product.
7 Check the LCD display.
Check that there is no dirt or dust trapped inside the LCD display.
Audio, Search and operations must be normal.
8
Check the appearance of the product.
No scratches or dirt on its appearance after receiving it for service.
4 Check the connection of each interface.
Playback data contained in the device connected to USB A.
The PC must be linked.
USB B.
The PC must be linked.
LINK.
Lubricants and Glues List
Name Part No. Remarks
Jigs List
Jig Name Part No. Purpose of use / Remarks
CD test disc STD-905 Drive self-diagnosis
iPod cable GGP1201 For use in determining a cause of charging problem for an iPad
DDE1142 (accessory for the CDJ-2000NXS) registered as a jig
* CDJ-900NXS can charge iPad using the cable attached to iPad.
Position to be cleaned Name Remarks
Pickup lens
Cleaning liquied
Refer to "9.5 SLOTIN MECHA SECTION".
Part No.
GEM1004
Cleaning paper GED-008
Lubricating oil GYA1001
Refer to "9.4 JOG DIAL SECTION", "9.5 SLOTIN MECHA SECTION".
Lubricating oil GEM1034 Refer to "9.4 JOG DIAL SECTION".
Dyfree GEM1036 Refer to "9.5 SLOTIN MECHA SECTION".
Cleaning
Before shipping out the product, be sure to clean the following positions by using the prescribed cleaning tools.
2 3 4
3. BASIC ITEMS FOR SERVICE
3.1 CHECK POINTS AFTER SERVICING
A
B
C
3.2 JIGS LIST
D
E
F
8
1
CDJ-900NXS
2 3 4

1
Power on
Pin G4 of MAIN CPU
(IC10) cancels reset
at H.
Program transfer from
FLASH to SDRAM
Canceling DSP reset
from pin A4 of MAIN
CPU. Pin G3 of DSP
(IC301) becomes "H".
Canceling ETHER PHY
reset from pin B14 of MAIN
CPU. Pin 15 of ETHER PHY
(IC704) becomes "H".
Canceling ATAPI reset
from pin M2 of MAIN
CPU. Pin 173 of SODC
(IC7006) becomes "H".
Program transfer to
DSP
Register setting of ETHER PHY
Initialization of the
built-in peripherals
Initialization of the SDRAM
Initialization of the SDRAM
Initialization of the DSP
Initialization of the DAC
Initialization of the peripheral device
Initialization of the MAIN CPU
Pin 12 of PANEL CPU
(IC8003) cancels reset
at H.
Pin 45 of SODC
(IC7006) cancels reset
at H.
Power on
Initialization of the JOG_FL
Initialization of the PANEL CPU
Initialization of the CDC
Power on
Initialization of the
loading mechanism
Initialization of the ATAPI
LED initial lighting
Canceling reset
Apple
authentication
chip
Communication between MAIN CPU and SRVO
Initialization of the SODC
The insertion of the
disk is possible.
The insertion of the
disk is possible.
Built-in peripherals
• USB_A
• USB_B
• ETH_MAC
• ATAPI
• SERIAL
• SSI
Communication between MAIN CPU and PANEL CPU
MAIN CPU PANEL CPU SRVO
POWER ON SEQUENCE
Opening screen display
Device select screen
5. DIAGNOSIS
5.1 SEQUENCE
A
2 3 4
B
C
D
E
F
16
1
2 3 4
CDJ-900NXS
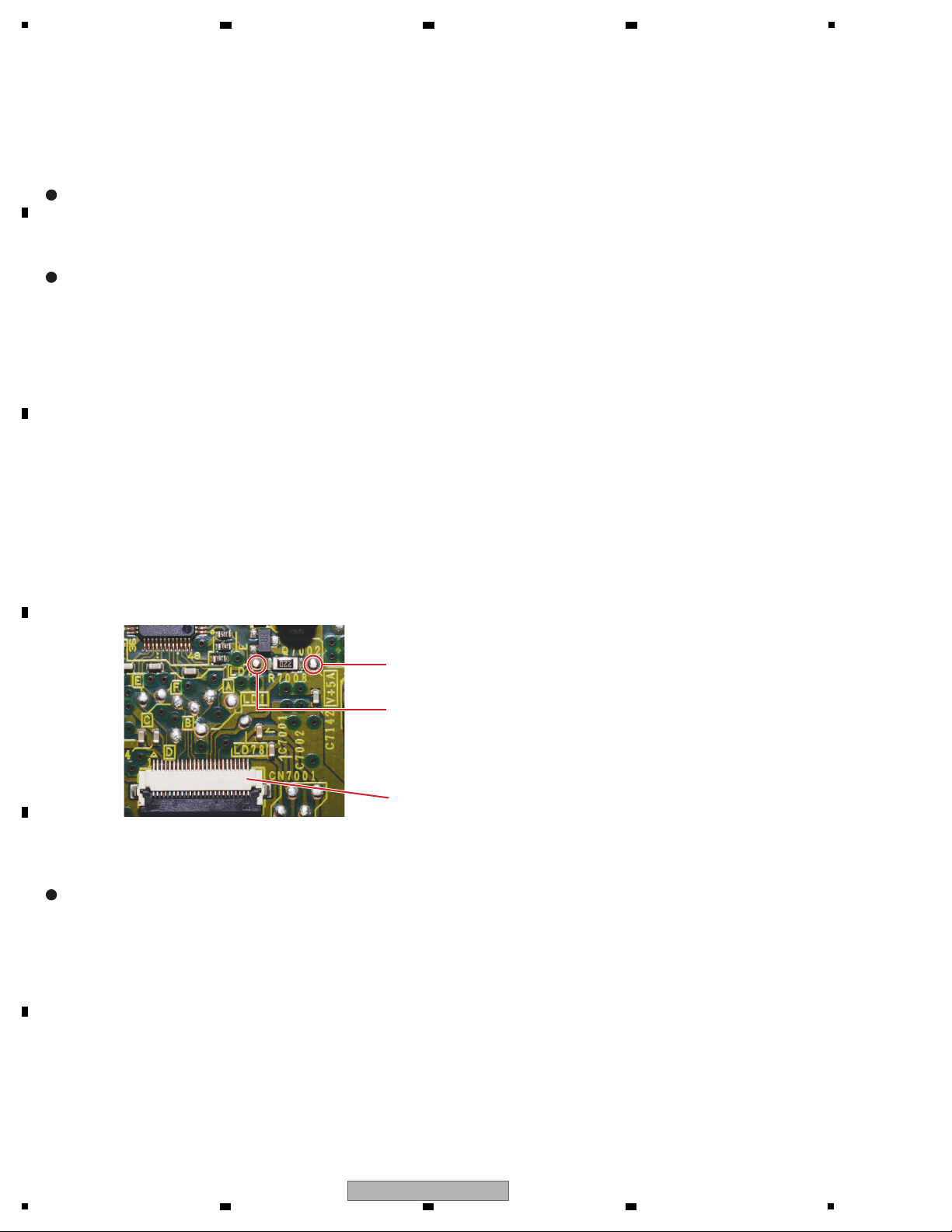
1
Measure the voltage at the probe pad on the SRVB Assy (see the photo below), using a tester.
∗ To check lighting of each LD, follow the procedure indicated in "[7] Checking the servo operations of the drive unit" in
"6.1 SERVICE MODE."
∗ Note that the LD may be degraded if the probes of a tester are applied to or pulled away from the probe pad with the LD ON.
Check method
Directly measure the resistance value of the actuator, using a tester.
* Before measuring, short-circuit the LD short-circuit pads.
Note that the LD may be degraded if connection/disconnection of CN7001 is performed with the LD short-circuit pads open.
• Focus side
Disconnect* the FFC connected to the CN7001 then measure the resistance value between FFC pins 23 and 24.
• Tracking side
Disconnect* the FFC connected to the CN7001 then measure the resistance value between FFC pins 21 and 22.
Check method
1. With the LD OFF, apply the probes of a tester to the reference probe pad (LDI) and V+5A.
2. With the probes kept applied to the above-mentioned pads, turn the LD ON to measure the voltage between them.
3. After measurement, turn the LD OFF (ALL OFF) then pull the probes away.
4. Calculate the current value by dividing the measured voltage value by the resistance value mentioned below.
(R7008 = 22 ohms)
Procedures
If the calculated current value exceeds the maximum value, the LD has been degraded
Failure judgment:
A value out of the range of the specifications is judged as failure.
Failure judgment:
Fig.1 SRVB Assy
LD power after passing through the objective lens [mW]
SPEC: CD 0.210 ± 0.03
Check method: Measure the LD power, using an optical power meter.
Failure judgment: A value out of the range of the specifications is judged as failure.
Actuator resistance value [ohms]
Specifications on the focus side: 3.7 ±0.55
Specifications on the tracking side: 4.3 ±0.65
LD current [mA]
SPEC: CD TYP65 MAX75
This unit has self-diagnostic functions for the drives.
For drive-related malfunctions, first perform the self-diagnostics to check the drives in Service mode. If the results indicate any
problem with the drives, check the following items:
CN7001
V+5A
LDI
2 3 4
5.2 FAILURE JUDGEMENT OF THE PICKUP ASSY
A
B
C
D
E
F
18
CDJ-900NXS
1
2 3 4

5
1 ————— ————— Check for the location of a defect in
Service mode.
See the section describing locations of defects in
this manual.
6.1 SERVICE MODE
In this section, causes of failure, diagnostics points, and corrective measures can be searched for according to symptoms.
Before disassembling this unit, it is recommended to infer a failure point by performing a status check and referring to the error
code.
For the relationship of each power-supply and signal system, see “4. BLOCK DIAGRAM,” and “10. SCHEMATIC DIAGRAM.”
If software of the product is updated before performing diagnostics, check that software updating has been performed properly
before proceeding to diagnostics.
If software updating has not been performed properly, update the software, following the instructions in [9] Firmware update of
“6.1 SERVICE MODE.”
Contents
[0] Prior Confirmation
[1] Failure in Startup
[2] Display (JOG FL/LED)
[3] Operations (Button/Volume/Rotary enncoder / Jog dial)
[4] USB (Type A/Type B)
[5] LAN
[6] ATAPI DRIVE
[7] AUDIO OUT
[8] CONTROL
[9] DRIVE Assy
[10] EUP Mode
[11] SERVICE MODE
[12] Error Codes
[0] Prior Confirmation
[0-1] Checking in Service Mode
1 Disconnection,
breakage, or
loose connection
of cables
Cables Check that all the cables are securely
connected.
Check that there is no breakage in the
cables.
Securely connect the cables. If a cable is broken,
replace it.
4.1 OVERALL
WIRING DIAGRAM
10. SCHEMATIC
DIAGRAM
[0-3] Checking Cables
1 ————— Alarm port on
the MAIN Assy
(Fig. 1)
Check the output waveforms from the
alarm port.
If an output waveform is judged to be improper,
see the section describing locations of defects in
this manual.
6.1 SERVICE MODE
_[8] Outputs of the
Alarm Port
[0-2] Checking the Alarm Port
If “[0-1] Checking in Service Mode” is performed, this check is not required.
Fig. 1
MAIN Assy
Alarm port
Waveform example
(at DISC DRIVE ERROR (An ATAPI drive
does not work normally))
No. Cause Diagnostics Point Item to be Checked Corrective Action Reference
No. Cause Diagnostics Point Item to be Checked Corrective Action Reference
No. Cause Diagnostics Point Item to be Checked Corrective Action Reference
[1] Failure in Startup
[1-1] No power
1 The SW power
does not function
properly.
SRVB Assy Check V+12_EUP. If V+12_EUP (CN7302 pin 6) is not output, the
SW power is defective. Replace it.
—————
No. Cause Diagnostics Point Item to be Checked Corrective Action Reference
The waveform numbers confirmation-point numbers (10.19 WAVEFORMS) described in this section correspond to the
numbers on the “10. SCHEMATIC DIAGRAM” and “11. PCB DIAGRAM” .
Be sure to check the failure points, as well as check for failure in their peripheral circuits.
6 7 8
5.3 TROUBLESHOOTING
A
B
C
5
6 7 8
CDJ-900NXS
D
E
F
19

1
[2] Display (JOG FL/LED)
[2-1] The JOG FL does not light.
The JOG FL and the LEDs are controlled by the PANEL CPU (IC8003).
[1-2] Indications on the LCD
Check the indications on the LCD.
Nothing is displayed on the LCD. (Black screen)
2 The SW power
does not function
properly.
PNLB Assy,
LCDB Assy
Check V+3R3_PNL.
The regulator IC (IC2602) may be loosely connected
with its peripheral devices or a part may be defective.
Correct loose connection. If the symptom persists,
replace the defective part.
—————
4 Various power
supply ICs do
not function
properly.
SRVB Assy,
MAIN Assy
Check each power-supply IC.
The power IC and its peripheral devices for each
power supply may be loosely connected or a part
may be defective. Correct loose connection.
If the symptom persists, replace the defective part.
—————
3 The EUP control
unit does not
function properly.
SRVB Assy Check the EUP_CONT signal.
If the signal of XEUP_CONT (CN7302 pin 3) is L, check
the output of the SW power. If V+12 (CN7302 pins 4, 5) is
not output, the SW power is defective. Replace it.
—————
1
Power is not
supplied properly.
JFLB Assy Check the power-supply voltages (V+3R3,
VFDP2R7_F1, VFDP2R7_F2, and V+27)
of the FL (V9201).
Each power-supply may be loosely connected or
may be defective. Correct loose connection. If the
symptom persists, replace the defective part.
—————
3
Defective JOG FL
————— If the symptom persists after the above
corrections,
Replace the JOG FL. —————
2 Defective
control signal
JFLB Assy Check that the FL control line is properly
connected in the JFLB ASSY.
• J_SCLK
• J_BK
• J_LAT
• J_DSO
Check the connection and correct loose
connection.
As the JOG FL is controlled by the PANEL CPU,
if no signal is output, check the PANEL CPU.
10.19 WAVEFORMS
3 (TP9225)
No. Cause Diagnostics Point Item to be Checked Corrective Action Reference
5 Defective
CPU_RST signal
MAIN Assy Check the CPU_RST signal. If CPU_RST is "L" although the V+3R3_CPU is
normal, the RESET IC (IC11) is defective or the
relevant connection is poor.
Correct loose connection. If the symptom
persists, replace the defective part.
—————
6 Defective
SYS_CLK signal
MAIN Assy Check the SYS_CLK (=33.333333 MHz)
signal.
The X2 or Logic IC (IC9) may be loosely connected
with its peripheral devices or a part may be defective.
Correct loose connection. If the symptom persists,
replace the defective part.
10.19 WAVEFORMS
1 (IC9-pin 7)
No. Cause Diagnostics Point Item to be Checked Corrective Action Reference
No. Cause Diagnostics Point Item to be Checked Corrective Action Reference
No. Cause Diagnostics Point Item to be Checked Corrective Action Reference
1 Power for
backlight is not
input properly.
LCDB Assy
Check the connection of the backlight power
connector (CN2003) and the mounting status
of the peripheral parts of the power-supply
circuit for backlighting (IC2002).
Possible causes are poor connection of the backlight
power connector (CN2003) and defective power-supply
circuit for backlighting. Correct loose connection.
If the symptom persists, replace the defective part.
—————
2 Defective
LCD_CLK signal
MAIN Assy Check the LCD_CLK (= approximately
32.0000 MHz) signal.
The X3 may be loosely connected with its peripheral
devices or a part may be defective.
Correct loose connection. If the symptom persists,
replace the defective part.
—————
3
Loose connections
between MAIN CPU
and LCD module
MAIN Assy,
DDCB Assy,
LCDB Assy
LCheck the power source and signals to
the LCD module (CN2001).
• VAVDD (pin 59), VGL (pin 3),
V+3R3LCD (pin 4), VGH (pin 5)
• DCLK (pin 33 = approximately 32 MHz),
DE (pin 32), RSTB (pin 28 ="H"),
STBYB (pin 27 = "H")
Check the signals described in the left adjacent
column at CN706, CN2801, CN2802, and
CN2004 to identify a defective part then correct
connection or replace the defective part with
a new one.
10.19 WAVEFORMS
2 (CN2801-pin 25)
The colors displayed on the LCD are improper.
1
Loose connections
between MAIN CPU
and LCD module
MAIN Assy,
DDCB Assy,
LCDB Assy
LCheck the power source and signals to
the LCD module (CN2001).
• B7 : B2 (pin 34 : 39),
G7 : G2 (pin 42 : 47),
R7 : R2 (pin 50 : 55)
Check the signals described in the left adjacent
column at the MAIN CPU (IC10), CN706,
CN2801, CN2802, and CN2004 to identify
a defective part then correct connection or
replace the defective part with a new one.
—————
A
2 3 4
B
C
D
E
F
20
CDJ-900NXS
1
2 3 4
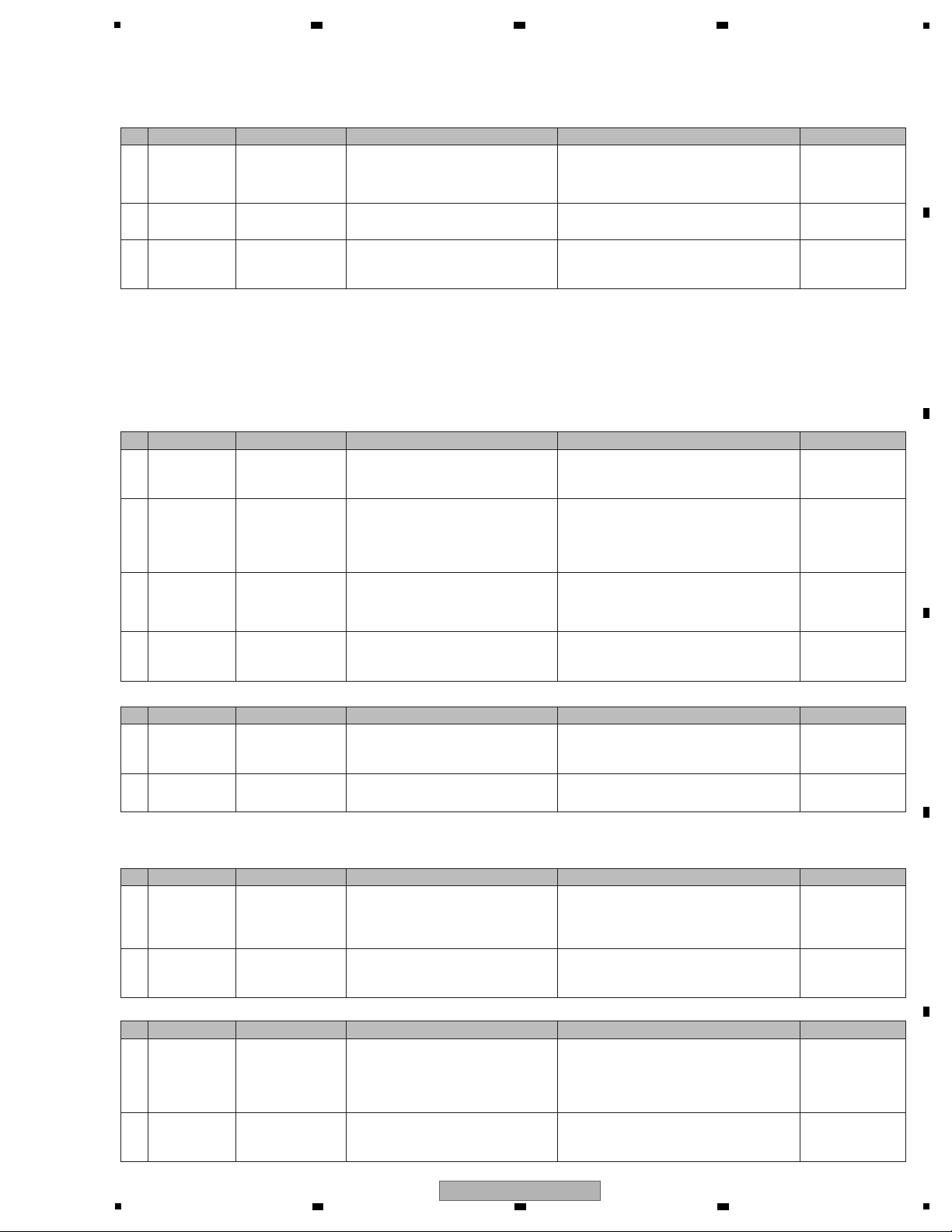
5
[2-2] An LED does not light.
1 Defective SW PNLB Assy Check if there is loose connection on the
signal line from the PANEL CPU (IC8003)
up to the SW.
If there is no loose connection and if the signal
does not become L when the SW is pressed,
that SW is defective. Replace it.
—————
2 Defective PANEL
CPU
PNLB Assy If the symptom persists after the above
corrections.
Check the connection of the PANEL CPU
(IC8003). If the connection is OK, the port may
be damaged. Replace it.
—————
2 Defective PANEL
CPU
PNLB Assy If the symptom persists after the above
corrections.
Check the connection of the PANEL CPU
(IC8003). If the connection is OK, the port may
be damaged. Replace it.
—————
2 Defective
MAIN CPU
MAIN Assy If the symptom persists after the above
corrections.
The MAIN CPU (IC10) is defective.
Replace the MAIN Assy.
—————
1 Defective SW PNLB Assy,
MAIN Assy
Check if there is loose connection on the
signal line from the MAIN CPU (IC10)
up to the SW.
If there is no loose connection and if the signal
does not become L when the SW is pressed,
that SW is defective. Replace it.
—————
1 Defective
TEMPOslider
SLDB Assy,
PNLB Assy
Check the waveform of signals on the
signal line (ADCT, ADIN).
If the voltage on the signal line (ADIN) fluctuates
within the range of 0–3.3 V, with 1.65 V at the
center, go to Step 2. If it does not, the TEMPO
slider (VR8701) is defective. Replace it.
—————
2 Defective PANEL
CPU
PNLB Assy If the symptom persists after the above
corrections.
Check the connection of the PANEL CPU
(IC8003). If the connection is OK, the port may
be damaged. Replace it.
—————
1 Defective VOL PNLB Assy Check the connections of and waveforms
of signals on the signal line (TCH/RELS).
If the voltage on the signal line (TCH/RELS)
fluctuates within the range of 0–3.3 V, go to
Step 2. If it does not, the TOUCH/RELEASE
(VR8001) are loosely connected or defective.
Connect them properly or replace them.
—————
1 Defective LEDs PNLB Assy
Check that soldering at the LED in question
is properly made. If it is OK, check that the
forward voltage (2.2 - 2.7 V) is present at
both ends of the LED.
Correct any defective soldering.
If the forward voltage is present, then the LED
itself is defective. Replace it.
—————
2 Defective drive
circuit
Transistor in
question
Check that the control signal for the LED in
question is output from the PANEL CPU (IC8003).
If the LED does not light even if the control signal is
output properly, then the transistor is defective. Replace it.
—————
3 Defective PANEL
CPU
PNLB Assy If the symptom persists after the above
corrections.
Check the connection between the PANEL CPU
(IC8003) and the LED in question. If the connection
is OK, the port may be damaged. Replace it.
—————
[3] Operations (Button / Volume / Rotary encoder / Jog dial)
[3-1] No key functions.
[3-2] Variable volumes not controllable
As operations of all buttons, variable volumes, rotary encoder and Jog dial can be checked in Service mode, it is recommended to check
operations of those controls in Service mode before proceeding to the subsequent checks.(For details, refer to 6. SERVICE MODE.)
The USB STOP button does not function. (The signal from the USB STOP button is input to the MAIN CPU.)
No key functions. (except USB STOP button)
TEMPO slider not controllable
VINYL SPEED ADJUST TOUCH/RELEASE control not controllable
No. Cause Diagnostics Point Item to be Checked Corrective Action Reference
No. Cause Diagnostics Point Item to be Checked Corrective Action Reference
No. Cause Diagnostics Point Item to be Checked Corrective Action Reference
No. Cause Diagnostics Point Item to be Checked Corrective Action Reference
No. Cause Diagnostics Point Item to be Checked Corrective Action Reference
2 Defective
RST signal of
PA NEL CPU
PNLB Assy Check the RST signal of the PANEL CPU
(IC8003 pin 12).
If Pin 12 of IC8003 is "L" although the V+3R3E is
normal, the RESET IC (IC8001) or Q8026 is
defective or the relevant connection is poor.
Correct connection or replace the defective part
with a new one.
—————
3 Defective
CLK signal of
PA NEL CPU
PNLB Assy Check the CLK signal of the PANEL CPU
(IC8003 pin 13 = 15.975 MHz).
The X8001 may be loosely connected with its
peripheral devices or a part may be defective.
Correct loose connection. If the symptom persists,
replace the defective part.
10.19 WAVEFORMS
4 (TP8096)
6 7 8
A
B
C
D
5
CDJ-900NXS
6 7 8
E
F
21
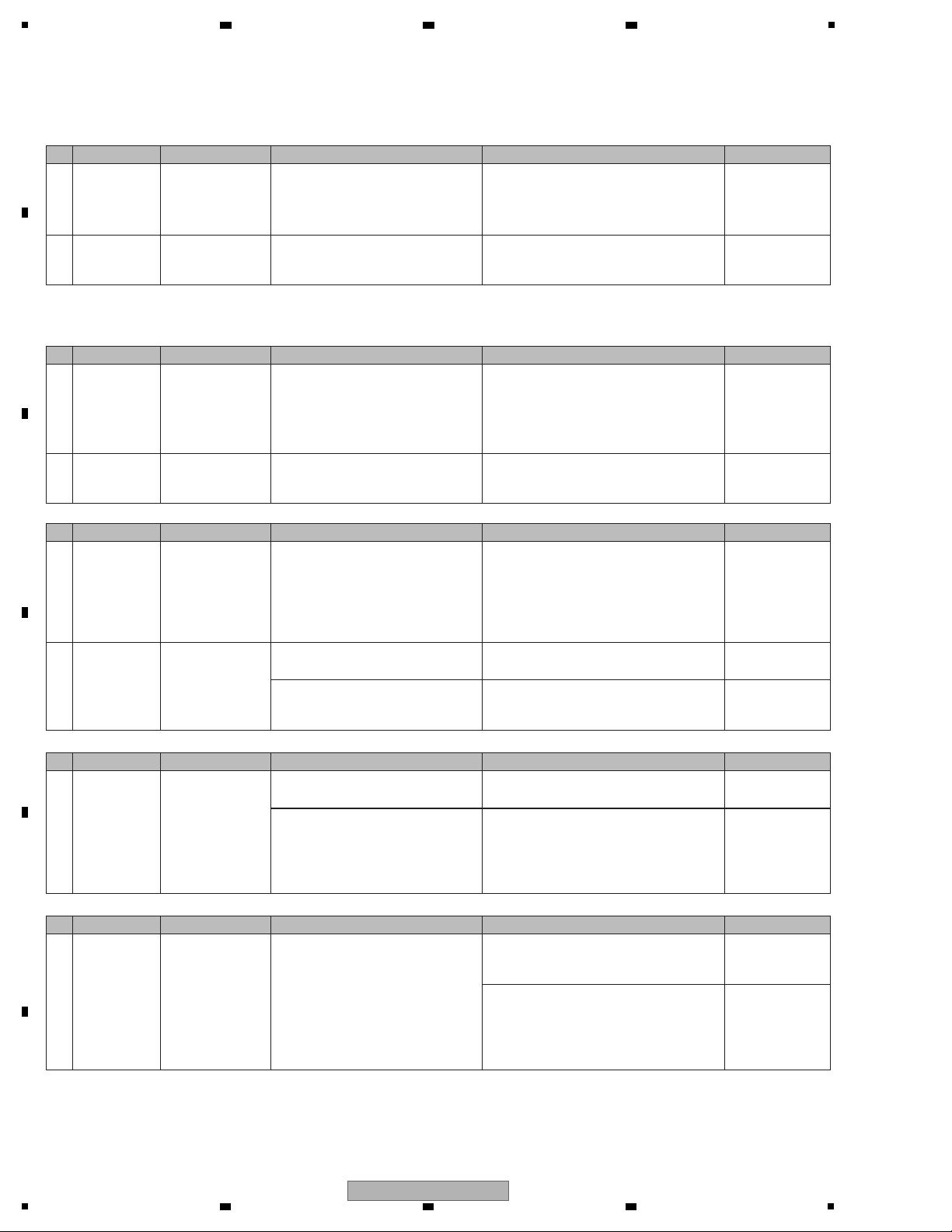
1
1 Defective photo
interrupter or
PA NEL CPU
JOGB Assy,
JFLB Assy,
PNLB Assy
Check the waveforms of the signal lines
(JOG1/JOG2).
If no waveform can be confirmed, the photo interrupter
(PC9301) may be defective. Replace it.
If a waveform can be confirmed, the signal line may be
loosely connected or the PANEL CPU (IC8003) may
be defective. Reconnect the signal line.
If the symptom persists, replace it.
10.19 WAVEFORMS
56
(CN9301-pin 2 (JOG1))
(CN9301-pin 1 (JOG2))
2 Defective
encoder plate
JOG Assy Check if the encoder plate has come off
Gear A or is dirty.
If it has come off, adhere it at its original position.
If it is dirty, replace it with a new one.
—————
2 Defective
SW ring
and
Holder/JOG
Jog dial Section Check if there is any foreign object
between the SW ring and Holder/JOG.
Remove any foreign object, if present. —————
Check if the cushions that are adhered to
the Holder/JOG and SW ring have worn
out.
Replace the SW cushion with a new one. —————
[3-4] Abnormalities regarding the Jog dial
Turning of the Jog dial is not detected
1 Defective
Sheet SW
or
PA NEL CPU
Sheet SW,
JFLB Assy,
PNLB Assy
Check the waveform of the signal on the
signal line (JOG_SW) when the Jog dial
is pressed.
If the signal on the signal line (JOG_SW) is not set to
L when the Jog dial is pressed, the Sheet SW
may be defective. Replace it.
If the signal line is set to L, the signal line may be
loosely connected or the PANEL CPU (IC8003) may
be defective. Reconnect the signal line.
If the symptom persists, replace it.
—————
Pressing on the Jog dial cannot be detected.
1 Defective
JFLB Assy
or
gears
Jog dial Section Check if the JOG FL of the JFLB has
been shifted upward from the holder.
The JOG FL may interfere with Jog dial A.
Replace the JFLB Assy.
—————
There may be any scratches on the 3
gears or some foreign object between
the gears.
If there are any scratches, replace the scratched
gear with a new one. If there is any foreign object,
remove it then replace the gears with new ones.
After that, check that the Jog adjustment value is
within the reference range, referring to “8.3 JOG
DIAL ROTATION LOAD ADJUSTMENT.”
—————
Noise is heard when the Jog dial is turned.
No. Cause Diagnostics Point Item to be Checked Corrective Action Reference
No. Cause Diagnostics Point Item to be Checked Corrective Action Reference
No. Cause Diagnostics Point Item to be Checked Corrective Action Reference
No. Cause Diagnostics Point Item to be Checked Corrective Action Reference
1 Improper adjust-
ment
or assembly
of the Jog dial
Jog dial Section Check that the load value for the Jog dial
is within the specified range, referring to
“Measuring method” in “8.3 JOG DIAL
ROTATION LOAD ADJUSTMENT.”
If it is outside the specified range, adjust the position
of the Adjust plate to change the load value for the
Jog dial, referring to “How to Adjust” in “8.3 JOG DIAL
ROTATION LOAD ADJUSTMENT.”
—————
During the above adjustment, if the upper-limit
adjustment position of the Adjust plate is reached,
oil mayhave been spattered on the Adjust Plate.
Replace the washer, gear, and smoother with new
ones, then reassemble. After replacement, adjust
the position of the Adjust Plate to change the load
value for the Jog dial.
—————
The Jog dial turns too freely. (The load value for the Jog dial is outside the specified range.)
No. Cause Diagnostics Point Item to be Checked Corrective Action Reference
1
Loose connections
in the signal line
or defective SW
LCDB Assy,
PNLB Assy
Check the connections of the signal lines for
ENC_SW, ENC1, and ENC2. When the SW is
pressed, the ENC_SW signal must become L,
and when it is turned, the waveforms of the
signal lines for ENC1 and ENC2 must change.
The PANEL CPU (IC8003) and SW may be
loosely connected or they may be defective.
Reconnect them securely.
If the symptom persists, replace them.
—————
[3-3] The Rotary encoder does not work.
No response when the Rotary selector is operated
2 Defective PANEL
CPU
PNLB Assy If the symptom persists after the above
corrections.
Check the connection of the PANEL CPU
(IC8003). If the connection is OK, the port may
be damaged. Replace it.
—————
A
2 3 4
B
C
D
E
F
22
CDJ-900NXS
1
2 3 4

5
1
Loose connections
in the communication line.
Between USBB Assy
and MAIN Assy
Check the connection of the USB
communication line.
If connection is improper, resolder it.
If connection is proper, go to 2.
—————
5 Defective
MAIN CPU
MAIN Assy If the symptom persists after the above
corrections.
The MAIN CPU (IC10) is defective.
Replace the MAIN Assy.
—————
5 Defective
MAIN CPU
MAIN Assy If the symptom persists after the above
corrections.
The MAIN CPU (IC10) is defective.
Replace the MAIN Assy.
—————
3
The USB
POWER SW IC
or its control
signal is defective.
DDCB Assy,
MAIN Assy
Check the CPU_USB_HSTPWREN and
HSSW_PWRFL signals from the
USB POWER SW IC (IC2702).
If the CPU_USB_HSTPWREN signal does not become H,
check the connection. If the connection is OK, then the
MAIN CPU (IC10) is defective. Replace the MAIN Assy.
If the HSSW_PWRFL signal does not become H, the
USB POWER SW IC (IC2702) is in a state of shutdown
caused by abnormally high temperature. Check the
connection. If the connection is OK, then the port may be
damaged. Replace it.
—————
2 V+5_USB
is defective.
DDCB Assy Check V+5_USB of the USB power supply. If V+5_USB cannot be confirmed, go to 3.
If V+5_USB can be confirmed, go to 4.
—————
[4] USB (Type A/Type B)
[4-1] No communication via the USB connector (Type A)
Check the following, with a USB device connected to the USB A connector.
1
Loose connections
in the communication line.
DDCB Assy,
MAIN Assy
Check the USB communication line. If connection is improper, resolder it.
If connection is proper, go to 2.
—————
3
Loose connections
in the USB signal.
MAIN Assy Check the connections of the
communication line (USB_D+, USB_D-).
The communication line may be loosely
connected. Correct it if it is.
If connection is proper, go to 4.
—————
[4-2] No communication via the USB connector (Type B)
Check the following, with a USB device connected to the USB B connector.
No. Cause Diagnostics Point Item to be Checked Corrective Action Reference
No. Cause Diagnostics Point Item to be Checked Corrective Action Reference
4 Defective
USB_CLK signal
MAIN Assy Check the USB_CLK (= 48.000 MHz)
signal.
The X1 or logic IC (IC4) may be loosely connected
with its peripheral devices or a part may be defective.
Correct loose connection. If the symptom persists,
replace the defective part.
10.19 WAVEFORMS
7 (TP34)
2 Defective
CPU_VBUS1
signal
MAIN Assy Check the CPU_VBUS1 signal. If the CPU_VBUS1 signal cannot be found,
something is wrong in the line from the USBB to
MAIN Assys via the DDCB Assy. Identify the
defective site and correct it.
If the CPU_VBUS1 signal is found, go to 3.
—————
4 Defective
USB_CLK signal
MAIN Assy Check the USB_CLK (= 48.000 MHz)
signal.
The X1 or logic IC (IC4) may be loosely connected
with its peripheral devices or a part may be defective.
Correct loose connection. If the symptom persists,
replace the defective part.
10.19 WAVEFORMS
7 (TP34)
1
Loose connections
in the communication line.
MAIN Assy Check the connection of the periphery
circuit of ETHER PHY (IC704).
If connection is improper, resolder it. —————
2 Defective
ETHER PHY
or
MAIN CPU
MAIN Assy If the symptom persists after the above
corrections.
The ETHER PHY (IC704) may be defective.
Replace it.
If the symptom persists, the MAIN CPU (IC10)
may be defective. Replace the MAIN Assy.
—————
[5] LAN
[5-1] No LAN communication
Check the following, with a peripheral device connected to the LINK terminal.
No. Cause Diagnostics Point Item to be Checked Corrective Action Reference
1 Improper adjust-
ment of the JOG
dial or defective
washer, gear, or
cam plate
Jog dial Section Check that the load value for the Jog dial
is within the specified range, referring to
“Measuring method” in “8.3 JOG DIAL
ROTATION LOAD ADJUSTMENT.”
If it is outside the specified range, adjust the position
of the Adjust plate to change the load value for the
Jog dial, referring to “How to Adjust” in “8.3 JOG DIAL
ROTATION LOAD ADJUSTMENT.”
—————
During the above adjustment, if the lower-limit
adjustment position of the Adjust plate is reached,
shavings from the worn-out washer may have
increased the friction. Replace the washer, gear,
and smoother with new ones, then reassemble.
After replacement, adjust the position of the Adjust
plate to change the load value for the Jog dial.
—————
Resistance to turning the Jog dial is too strong. (The load value for the Jog dial is outside the specified range.)
No. Cause Diagnostics Point Item to be Checked Corrective Action Reference
6 7 8
A
B
C
D
E
5
CDJ-900NXS
6 7 8
F
23

1
3 Defective
MAIN CPU
MAIN Assy Check the periphery circuit of the MAIN
CPU.
Check the periphery of the MAIN CPU (IC10).
If no problem is found, the MAIN CPU may be
defective. Replace the MAIN Assy.
—————
2
Loose connections
in the communication line.
SRVB Assy,
MAIN Assy
Check the connection of the ATAPI lines. Check the connection between the MAIN CPU
(IC10) and SODC (IC7006). If no problem is
found, see “[9] DRIVE ASSY.” If the symptom
persists after those corrections, go to Step 3.
—————
1 Improper
RESET signal
SRVB Assy,
MAIN Assy
Check the ATA_RESET signal
(CN7001 pin 40).
Communication will not start while the ATA_RESET signal
is L. Check the connection between the MAIN CPU (IC10)
and SODC (IC7006). If the connection is not properly
made, correct it. If connection is proper, go to Step2.
—————
1
Power is not
supplied properly.
MAIN Assy,
JACB Assy
Check the power voltages (V+12A, V-12A,
V+5, V+5_DAC) for audio.
Each power-supply may be loosely connected or
may be defective. Correct loose connection.
If the symptom persists, replace the defective part.
—————
2 Defective
MUTE signal
MAIN Assy Check the MUTE signal (CN9401 pin 5).
While you usually playback, MUTE is
canceled, and consist with around -6 V.
The connection, transistor, or DSP may be
defective. Correct loose connection. If the
symptom persists, replace the defective part.
—————
3
Loose connections
in the signal line.
MAIN Assy,
JACB Assy
Check the connection of the audio signal
lines (ROUT, LOUT).
If connection is improper, resolder it.
If connection is proper, go to 4.
—————
1
Loose connections
in the signal line.
MAIN Assy,
JACB Assy
Check the digital audio signal (SPDIF)
and its connection.
If connection is improper, resolder it. If the SPDIF
signal cannot be recognized, go to Step 3.
—————
3 Defective
MAIN DSP
MAIN Assy If the symptom persists after the above
corrections.
Replace the MAIN Assy. —————
2 Defective
transistor
MAIN Assy Check the digital audio signal
(SPDIF_OUT) and its connection.
If the SPDIF_OUT signal can be recognized, then the
transistor (Q906) may be defective. Check the connection.
If no problem is found, replace the transistor. If the
SPDIF_OUT signal cannot be recognized, check the
connection. If soldering is improper, resolder it.
—————
[6] ATAPI DRIVE
[6-1] No disc playback (Although loading and disc rotation can be performed properly, no track data are output.)
[7] AUDIO OUT
[7-1] No sound
The analog audio signal is not output.
The digital audio signal is not output.
No. Cause Diagnostics Point Item to be Checked Corrective Action Reference
No. Cause Diagnostics Point Item to be Checked Corrective Action Reference
No. Cause Diagnostics Point Item to be Checked Corrective Action Reference
5
DAC or DSP
is defective.
MAIN Assy,
JACB Assy
Check the digital inputs (IC901 pin 1, 2,
3, 4 ) on DAC (IC901) and digital outputs
(IC901 pin 8, 11).
If the analog signal is not output although the
digital signal is input, DAC (IC901) or one of its
peripheral parts may be defective. If the digital
signal is not input, DSP (IC301) or one of its
peripheral parts may be defective.
Correct loose connection. If the symptom
persists, replace the defective part.
—————
4 Defective
DAC_MCLK
signal
MAIN Assy Check the DAC_MCLK
(IC901 pin 4 = 16.9344 MHz) signal.
The X501 or logic IC (IC506) may be loosely
connected with its peripheral devices or a part may
be defective. Correct loose connection. If the
symptom persists, replace the defective part.
10.19 WAVEFORMS
8 (IC901-pin 4)
1
Loose connections
in the signal line.
JACB Assy
Check the waveforms of the control signals
(CONT1, CONT2) from the CN9401 on the
JACB Assy.
If the signal cannot be recognized, the JACB Assy
may be defective. Check the soldering at the JACB
Assy then resolder it, if necessary.
If the signal can be recognized, go to Step 2.
—————
2 Defective
MAIN CPU
MAIN Assy
Check the waveforms of the control signals
(CONT01, CONT02) from the MAIN Assy.
If the input signal can be recognized, then the MAIN CPU
(IC10) may be defective. Replace the MAIN Assy. If the
input signal cannot be recognized, the communication
line or the peripheral devices may be loosely connected.
Resolder the terminals.
—————
[8] CONTROL
[8-1] Improper fader operation after fader start
No. Cause Diagnostics Point Item to be Checked Corrective Action Reference
A
2 3 4
B
C
D
E
F
24
1
CDJ-900NXS
2 3 4
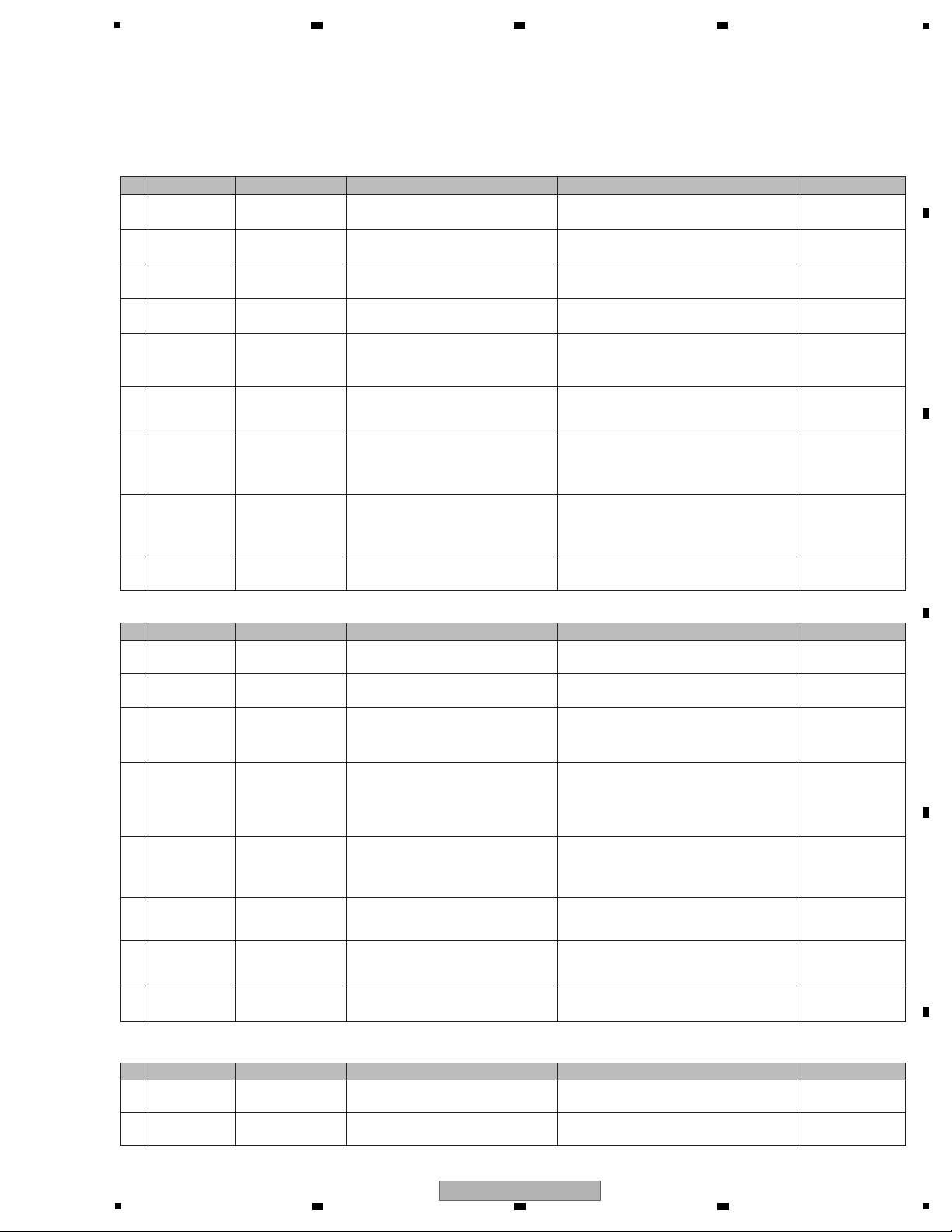
5
1 Missing or
defective part
Loading mecha Check that there is no part missing or
defective.
If there is, install the missing part or replace the
defective part.
—————
2
Loose connections
in the signal line.
Loading mecha Check that the LP switch has been
mounted.
If soldering is improper, resolder it. —————
3 Improper
assembling
Loading mecha Check that the lever is engaged with the
LP switch.
Engage the lever with the LP switch. —————
4 Improper
soldering
Loading mecha Check that the wires from the loading
motor have been properly soldered.
If they are not soldered, solder them. —————
5 Power supply
error
SRVB Assy Check the power voltages (12 V, 7.6 V, 5 V,
3.3 V, and 1.5 V).
Check the connection of the parts at the periphery of
the power-supply IC that does not output the voltage.
If the symptom persists after a corrective action, the
power supply block is defective. Replace it.
—————
7 MUTE1 and
MUTE2 signal
errors
SRVB Assy Check the waveforms of the MUTE1 and
MUTE2 signals. (During loading, the
MUTE1 signal is L and the MUTE2 signal
is H.)
DRIVER IC (IC7001) and SODC (IC7006) may
be improperly soldered or defective.
Resolder them, if necessary. If the symptom
persists, replace SODC (IC7006).
—————
9 Defective SRVB
Assy
————— If the symptom persists after the above
corrections.
Replace the SRVB Assy or Loading mecha Assy. —————
6 LPS1 and LPS2
signal errors
SRVB Assy
Check the waveforms of the LPS1 and LPS2
signal lines. (The LPS1 and LPS2 signals
becomes L when the SW is set to ON.)
The loading detection SWs (S9001 and S9002) may
be improperly soldered or defective. Resolder them,
if necessary. If the symptom persists, replace them.
5.4 OPERATIONAL
WAVEFORMS
2
8 LOAD signal
error
SRVB Assy,
SLMB Assy,
JINT Assy
Check the waveforms of the LOAD signal,
LO+ and LO– signals.
DRIVER IC (IC7001) and SODC (IC7006) may
be improperly soldered or defective.
Resolder them, if necessary. If the symptom
persists, replace SODC (IC7006) or IC7001.
5.4 OPERATIONAL
WAVEFORMS
2
1
The main unit is
positioned inclined.
Main unit
Check if the main unit is positioned inclined.
Place it on a level surface. —————
2
Improper assembling
Traverse mecha
Check if there is a missing or defective part at the
section where the main axis and stepper contact.
If there is, install the missing part or replace the
defective part.
—————
3 Power supply
error
SRVB Assy Check the power voltages (12 V, 7.6 V, 5 V,
3.3 V, 1.5 V, VREF1, VREF2 and VHALF).
Check the connection of the parts at the periphery of
the power-supply IC that does not output the voltage.
If the symptom persists after a corrective action, the
power supply block is defective. Replace it.
—————
4INSW signal
error
SRVB Assy
Check the INSW signal.
(The INSW signal is switched to ON [L]
when a disc is loaded for the first time after
the unit is powered up then will immediately
be switched to OFF [H].)
The FFC cables that connect the traverse mechanism,
JINT, and SRVB are loosely connected, or the INSW
is defective. Reconnect them securely.
If the symptom persists, replace the INSW.
—————
5 MU1 signal error SRVB Assy Check that the MU1 signal becomes H
after loading is completed.
DRIVER IC (IC7001) and SODC (IC7006) may
be improperly soldered or defective.
Resolder them, if necessary. If the symptom
persists, replace SODC (IC7006).
—————
6
Improper assembling
Cables
Check that the FPC cable that connects the
traverse mecha and the SRVB Assy is
securely connected.
If it does not, securely connect it. If it is broken,
replace the traverse mecha.
—————
[9] DRIVE ASSY
[9-1] Improper operation of the loading mechanism
[9-2] The stepper does not work.
No loading
When it is thought abnormally, the drive section execute drive self-diagnose beforehand.
No. Cause Diagnostics Point Item to be Checked Corrective Action Reference
No. Cause Diagnostics Point Item to be Checked Corrective Action Reference
7 Signal error SRVB Assy Check that a sine-wave signal is input to
Pins 29 and 30 of IC7001.
The IC7001 may be loosely connected or defective.
Resolder them, if necessary. If the symptom persists,
replace SODC (IC7006).
5.4 OPERATIONAL
WAVEFORMS
5 7 8
8 Defective
traverse mecha
————— If the symptom persists after the above
corrections.
Replace the parts in the order of (1) DRIVER IC
(IC7001), (2) SRVB Assy, then (3) traverse mecha.
—————
[9-3] No playback
1 Short-circuit pad Traverse mecha Check if the LD short-circuit pad is
short-circuited.
If it is, open it. —————
2 LD current SRVB Assy Check that the LD current is within the
specified range.
If there is any error, replace the traverse mecha.
5.2 Failure Judgment
of the Pickup Assy
No. Cause Diagnostics Point Item to be Checked Corrective Action Reference
6 7 8
A
B
C
5
CDJ-900NXS
6 7 8
D
E
F
25

1
4INSW signal
error
SRVB Assy
Check the INSW signal. (The INSW signal is
switched to ON [L] when a disc is loaded for
the first time after the unit is powered up then
will immediately be switched to OFF [H].)
If the signal waveform is not proper, replace the
INSW.
—————
5 MUTE1 signal
error
SRVB Assy Check that the MUTE1 signal becomes H
after loading is completed.
DRIVER IC (IC7001) and SODC (IC7006) may
be improperly soldered or defective.
Resolder them, if necessary. If the symptom
persists, replace SODC (IC7006).
—————
6 Improper
assembling
Traverse mecha Check if the objective lens is dirty. Clean the lens. —————
9 ————— ————— If the symptom persists after the above
corrections.
Replace the parts in the order of
(1) DRIVER IC (IC7001), (2) FEP (IC7002),
(3) SODC (IC7006), (4) SRVB Assy, then
(5) traverse mecha.
—————
7 A–F signal error SRVB Assy Check the A–F signals (CN7001).
Check that the signals fluctuate with 2.2 V at the center.
If a DC signal is not output, check the VREF1. If a DC
signal is not output from it, replace the FEP (IC7002).
If an AC signal is not output, check the soldering at the
CN7001–IC7002 of the pickup. If soldering is improper,
resolder it. If soldering is OK, replace the parts in the
order of (1) FEP (IC7002), (2) DRIVER IC (IC7001),
(3) SODC (IC7006), (4) SRVB Assy, then (5) traverse
mecha.
—————
8 RF signal error SRVB Assy Check the RF signal (CN7001).
Compare the waveform with the operational waveform
to check if its quality is low. Check if the disc is dirty or
scratched. When it is normal, Check the connections
between pickup and CN7001 and IC7002. If soldering is
improper, resolder it. If soldering is OK, replace the parts
in the order of
(1) FEP (IC7002), (2) DRIVER IC (IC7001), (3) SODC
(IC7006), (4) SRVB Assy, then (5) traverse mecha.
5.4 OPERATIONAL
WAVEFORMS
1
No. Cause Diagnostics Point Item to be Checked Corrective Action Reference
1 Defective
PA NEL CPU
PNLB Assy Check that the signal from pin 29 of the
PA NEL CPU (IC8003) changes from H to
L during mode shift.
The PANEL CPU (IC8003) may be defective.
Check the soldering of the PANEL CPU and its
periphery. If the soldering is OK, then replace it.
—————
2
Disconnection,
breakage, or
loose connection
of cables
SRVB Assy Check the XEUP_CONT signal
(CN7302 pin 3) changes from L to H
during mode shift.
The signal line cable may be defective.
If it is loosely connected, securely connect it.
If it is broken, replace it.
—————
3 Defective SW
power
————— ————— The SW power is defective. Replace it. —————
3
Disconnection,
breakage, or
loose connection
of cables
SRVB Assy Check the XEUP_CONT signal
(CN7302 pin 3) changes from H to L
during mode shift.
The signal line cable may be defective.
If it is loosely connected, securely connect it.
If it is broken, replace it.
—————
4 Defective SW
power
————— ————— The SW power is defective. Replace it. —————
[10] EUP Mode
Shifting to EUP mode is not possible.
1 Defective key or
loose connection
of the signal line
PNLB Assy
its periphery
Check the connection of the
nonresponding key.
Check the connection of the signal line for the
nonresponding key. If the connection is proper,
replace the connected SW.
—————
2 Defective
PA NEL CPU
PNLB Assy Check that the signal from pin 29 of the
PA NEL CPU (IC8003) changes from L to
H during mode shift.
The PANEL CPU (IC8003) may be defective.
Check the soldering of the PANEL CPU and its
periphery. If the soldering is OK, then replace it.
—————
EUP mode cannot be exited.
No. Cause Diagnostics Point Item to be Checked Corrective Action Reference
No. Cause Diagnostics Point Item to be Checked Corrective Action Reference
Normal mode EUP mode
XEUP_CONT (CN7302 pin3) L H or open
PA NEL CPU (IC8003) pin 29 H L
Reference: Signal logic during EUP mode
3 Power supply
error
SRVB Assy Check the power voltages (12 V, 7.6 V, 5 V,
3.3 V, 1.5 V, VREF1, VREF2 and VHALF).
Check the connection of the parts at the periphery of
the power-supply IC that does not output the voltage.
If the symptom persists after a corrective action, the
power supply block is defective. Replace it.
—————
A
2 3 4
B
C
D
E
F
26
CDJ-900NXS
1
2 3 4
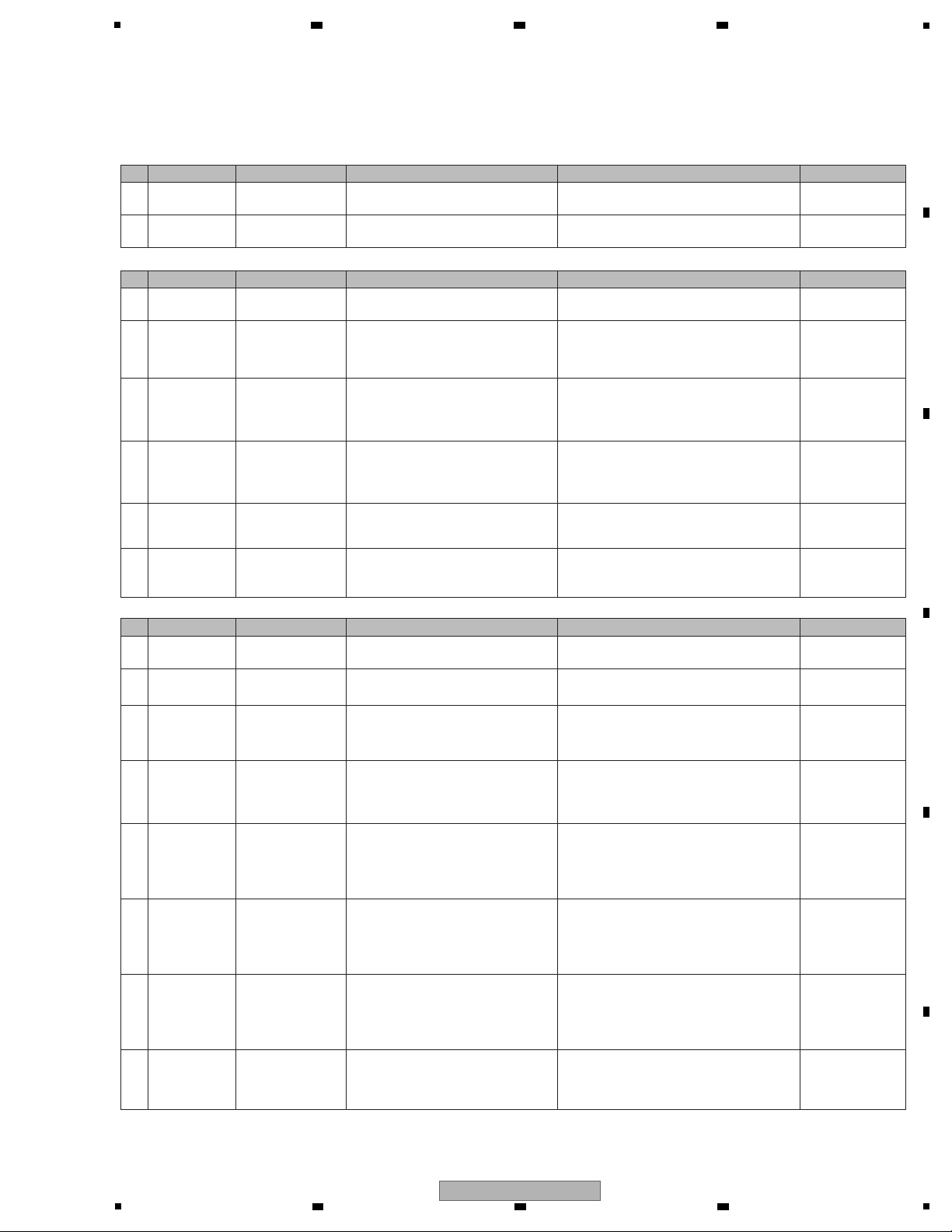
5
1 Short-circuit pad Traverse mecha Check if the LD short-circuit pad is
short-circuited.
If it is, open it. —————
1 Missing or
defective part
Loading mecha Check that there is no part missing or
defective.
If there is, install the missing part or replace the
defective part.
—————
2 Power supply
error
SRVB Assy
Check the power voltages (12 V, 7.6 V, 5 V,
3.3 V, 1.5 V, VREF1, VREF2 and VHALF).
Check the connection of the parts at the periphery of
the power-supply IC that does not output the voltage.
If the symptom persists after a corrective action, the
power supply block is defective. Replace it.
—————
3 Power supply
error
SRVB Assy
Check the power voltages (12 V, 7.6 v, 5 V,
3.3 V, 1.5 V, VREF1, VREF2 and VHALF).
Check the connection of the parts at the periphery of
the power-supply IC that does not output the voltage.
If the symptom persists after a corrective action, the
power supply block is defective. Replace it.
—————
3 MUTE1 signal
error
SRVB Assy Check that the MUTE1 signal becomes H
after loading is completed.
DRIVER IC (IC7001) and SODC (IC7006) may
be improperly soldered or defective.
Resolder them, if necessary. If the symptom
persists, replace SODC (IC7006).
—————
4 MUTE1 signal
error
SRVB Assy Check that the MUTE1 signal becomes H
after loading is completed.
DRIVER IC (IC7001) and SODC (IC7006) may
be improperly soldered or defective.
Resolder them, if necessary. If the symptom
persists, replace SODC (IC7006).
—————
4 SPDLEC signal
error
SRVB Assy Check that the SPDLEC signal is a PWM
signal with 1.65 V at the center.
DRIVER IC (IC7001) and SODC (IC7006) may
be improperly soldered or defective.
Resolder them, if necessary. If the symptom
persists, replace SODC (IC7006).
5.4 OPERATIONAL
WAVEFORMS
4 9
5 SPDLFG signal
error
SRVB Assy Check the SPDLFG signal.
SPDLFG signal may be improperly solded and
SODC (IC7006) may be defective.
Resolder them, if necessary. If the symptom
persists, replace SODC (IC7006). If the symptom
persists, replace DRIVER IC (IC7001).
5.4 OPERATIONAL
WAVEFORMS
4 9
6 FEDRV signal
error
SRVB Assy Check that the FEDRV signal fluctuates
with 1.65 V at the center.
FEDRV signal may be improperly solded and
SODC (IC7006) may be defective.
Resolder them, if necessary. If the symptom
persists, replace SODC (IC7006). If the symptom
persists, replace FEP (IC7002).
5.4 OPERATIONAL
WAVEFORMS
3 4 9
7 FE signal error SRVB Assy Check that an S-shaped signal is output
when a waveform of the FE (FEDRV)
signal is rising after it drops down from
1.65 V.
FE signal may be improperly solded and SODC
(IC7006) may be defective.
Resolder them, if necessary. If the symptom
persists, replace SODC (IC7006). If the symptom
persists, replace FEP (IC7002).
5.4 OPERATIONAL
WAVEFORMS
3 4 5 9
5 SPIN1 signal
error
SRVB Assy
Check that the SPIN1 signal to pin 26 of IC7001
is 3.3 V when disc rotation is at full speed soon
after inserted a disc.
If the signal is not input, check the soldering.
If the soldering is improper, resolder it.
5.4 OPERATIONAL
WAVEFORMS
4
6 ————— ————— If the symptom persists after the above
corrections.
Replace the parts in the order of
(1) DRIVER IC (IC7001), (2) SODC (IC7006),
(3) SRVB Assy, then (4) traverse mecha.
—————
8 ————— ————— If the symptom persists after the above
corrections.
Replace the parts in the order of
(1) FEP (IC7002), (2) SODC (IC7006),
(3) DRIVER IC (IC7001), (4) SRVB Assy,
then (5) traverse mecha.
—————
[11] SERVICE MODE
[11-1] The drive does not work during Test Operation mode.
The LD does not emit light.
1 Short-circuit pad Traverse mecha Check if the LD short-circuit pad is
short-circuited.
If it is, open it. —————
In-focus not possible
The spindle motor does not rotate.
2 LD current SRVB Assy Check that the LD current is within the
specified range.
If there is any error, replace the traverse mecha.
5.2 Failure Judgment
of the Pickup Assy
2 LD current SRVB Assy Check that the LD current is within the
specified range.
If there is any error, replace the traverse mecha.
5.2 Failure Judgment
of the Pickup Assy
No. Cause Diagnostics Point Item to be Checked Corrective Action Reference
No. Cause Diagnostics Point Item to be Checked Corrective Action Reference
No. Cause Diagnostics Point Item to be Checked Corrective Action Reference
6 7 8
A
B
C
D
E
F
CDJ-900NXS
5
6 7 8
27

1
1 ————— Traverse mecha Check that focusing is in. (If focusing is
out, tracking close is not possible.)
See “In-focus not possible” above. —————
1 ————— ————— ————— If it is judged as NG, the ATAPI drive does not
work properly. If the track data are not output
although loading and rotating are properly
performed, see [6] ATAPI DRIVE. In other cases,
see [9] DRIVE ASSY.
—————
1 ————— ————— ————— If it is judged as NG, the DSP (IC301) or SDRAM
(IC302)does not work properly or communication
between the MAIN CPU (IC10) and DSP is not
established. Proceed as follows:
—————
2
Power is not
supplied properly.
MAIN Assy Check the power voltages (V+3R3_DSP
and V+1R2_DSP).
The DSP requires two power supply systems.
Check the connections of the power supply lines.
If soldering is improper, resolder it.
—————
3 The clock is not
properly input.
MAIN Assy Check that the frequency at pin 38 (DSP_
CLK) of SDRAM (IC302) is
approx. 129 MHz.
Check the connection of the logic ICs
(IC501, IC506).
If soldering is improper, resolder it.
10.19 WAVEFORMS
9 (IC302-pin 38)
4 The RESET
signal is not
properly input.
MAIN Assy Check that the signals of the DSP_RST
line are H.
Check the connection of the logic IC (IC8).
If soldering is improper, resolder it.
If the signal of the DSP_RST line is L, check the
connection of the logic IC (IC8) and its periphery.
—————
5
Loose connection
between the MAIN
CPU and DSP
MAIN Assy Check the connection between the
MAIN CPU and DSP.
Check the connections between MAIN CPU
(IC10) and DSP (IC301).
If soldering is improper, resolder it.
—————
6
Loose connection
between the MAIN
DSP and SDRAM
MAIN Assy Check the connection between the
DSP and SDRAM.
Check the connections between DSP (IC301)
and SDRAM (IC302).
If soldering is improper, resolder it.
—————
No tracking close
2 Signal error SRVB Assy Check that the E and F signals fluctuate
with 2.2 V at the center.
Check that the signals fluctuate with 2.2 V at the center.
If a DC signal is not output, check the VREF1. If a DC
signal is not output from it, replace the FEP (IC7002).
If an AC signal is not output, check the soldering at the
CN7001–IC7002 of the pickup. If soldering is improper,
resolder it. If soldering is OK, replace the traverse
mecha.
5.4 OPERATIONAL
WAVEFORMS
3 TE signal error SRVB Assy Check that the TE signal fluctuates
with 1.65 V at the center.
Check the connection of the parts at the periphery of
the FEP (IC7002). If soldering is improper, resolder it.
If soldering is OK, replace the FEP (IC7002).
5.4 OPERATIONAL
WAVEFORMS
4 5 6 7 8
4 TEDRV signal
error
SRVB Assy Check that the TEDRV signal fluctuates
with 1.65 V at the center, and that a
pulselike signal is output during tracking
close.
If the output signal waveform is not proper, the connection
of the SODC (IC7006) and its periphery may be
loose or the parts may be defective. If the connection is
loose, reconnect securely. If the connection is OK,
replace the SODC (IC7006).
5.4 OPERATIONAL
WAVEFORMS
6 7 8
[12] Error Codes
[12-1] E-7001: DISC DRIVE ERROR
How to respond when an error code is displayed on the CONTROLLER DISPLAY (LCD) is described below.
The ATAPI drive does not work properly.
[12-2] E-7010: DSP DEVICE ERROR
The DSP (IC301) does not work properly. Downloading of programs is not possible.
5 ————— ————— If the symptom persists after the above
corrections.
Replace the parts in the order of (1) FEP (IC7002),
(2) SODC (IC7006), (3) DRIVER IC (IC7001),
(4) SRVB Assy, then (5) traverse mecha.
—————
7 ————— ————— If the symptom persists after the above
corrections.
Replace the MAIN Assy. —————
No. Cause Diagnostics Point Item to be Checked Corrective Action Reference
No. Cause Diagnostics Point Item to be Checked Corrective Action Reference
No. Cause Diagnostics Point Item to be Checked Corrective Action Reference
A
2 3 4
B
C
D
E
F
28
CDJ-900NXS
1
2 3 4
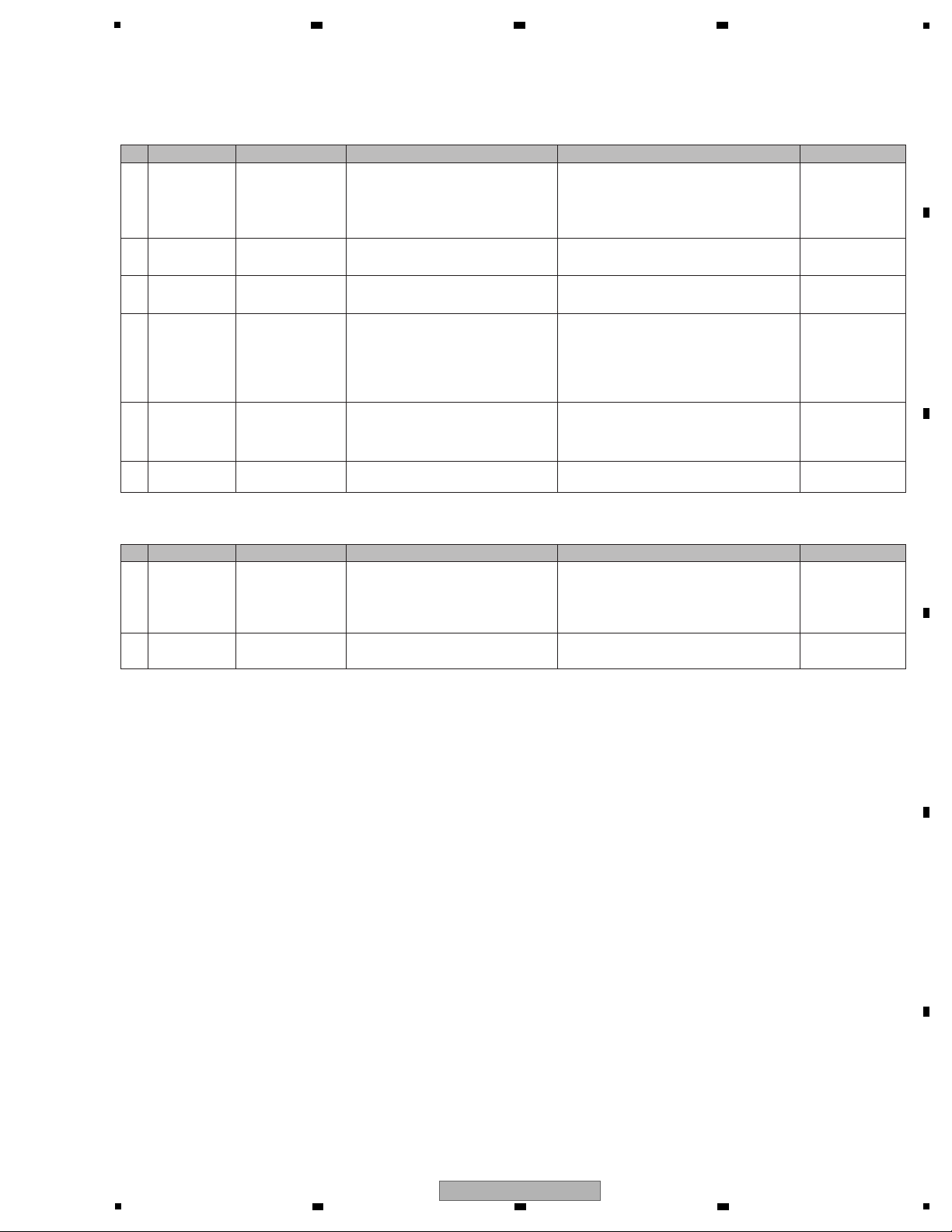
5
2 Power is not
supplied properly.
MAIN Assy Check the power voltages of V+3R3_ETH
and V+3R3A_ETHR) lines.
Check the connections of the power supply lines.
If soldering is improper, resolder it.
—————
3 The clock is not
properly input.
MAIN Assy Check that the frequency at Pin 5 (CLK) of
ETHER PHY (IC704) is 25 MHz.
Check the connections between X701 and
ETHER PHY. If soldering is improper, resolder it.
10.19 WAVEFORMS
a (IC704-pin 5)
4 The RESET
signal is not
properly input.
MAIN Assy Check that the signals of the ETHER_RST
and CPU_ETHER_RST lines are H.
Check the connection of the logic IC (IC8).
If soldering is improper, resolder it.
If the signal of the CPU_ETHER_RST line is L,
the port on the MAIN CPU may be damaged.
If the signal of the ETHER_RST line is L, check the
connection of the logic IC (IC8) and its periphery.
—————
5
Loose connection
between the
MAIN CPU and
ETHER PHY
MAIN Assy
Check the connections of communication
line
between the MAIN CPU and
ETHER PHY.
Check the connections between MAIN CPU
(IC10) and ETHER PHY (IC704).
If soldering is improper, resolder it.
—————
1 ————— ————— ————— If it is judged as NG, the ETHER PHY (IC704)
does not work properly or communication
between the MAIN CPU (IC10) and ETHER PHY
is not established. Proceed as follows: See also
“[5-1] No LAN communication.”
—————
[12-3] E-7021: PHY CHIP ERROR
The ETHER PHY (IC704) does not work properly.
6 ————— ————— If the symptom persists after the above
corrections.
Replace the ETHER PHY (IC704). —————
2 ————— ————— If the symptom persists after the above
corrections.
Replace the MAIN Assy. —————
No. Cause Diagnostics Point Item to be Checked Corrective Action Reference
No. Cause Diagnostics Point Item to be Checked Corrective Action Reference
[12-4] E-7026: AUTH CHIP ERROR
The Apple authentication chip (IC14) does not work properly.
1
Loose connection
between the
MAIN CPU and
AUTHENTICATION
CHIP
MAIN Assy
Check the connections of communication
line between the MAIN CPU and
AUTHENTICATION CHIP
.
Check the connections between MAIN CPU
(IC10) and AUTHENTICATION CHIP (IC14).
If soldering is improper, resolder it.
—————
6 7 8
A
B
C
D
E
F
CDJ-900NXS
5
6 7 8
29
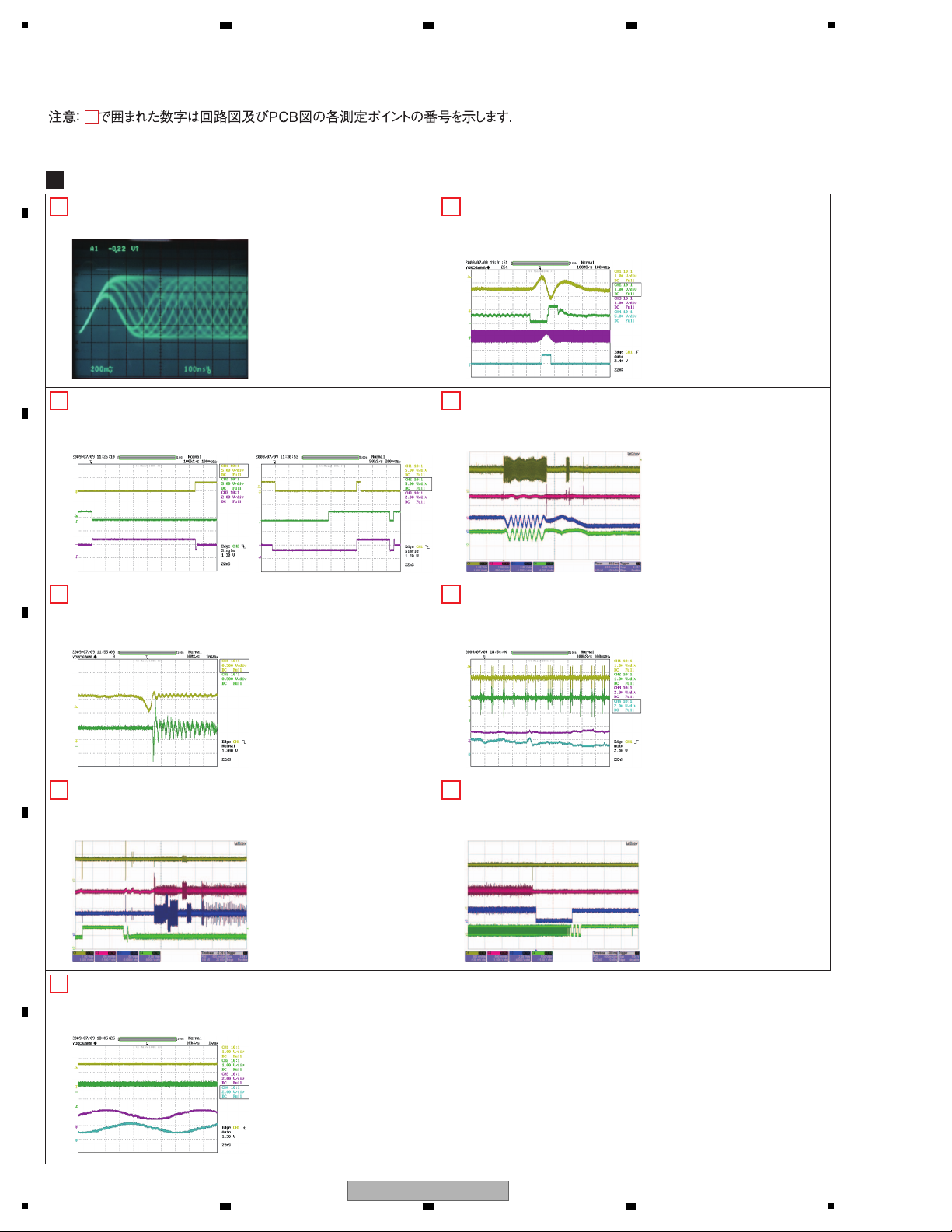
1
RF (CD: STD-905)
V: 200 mV/div. H: 100 nsec/div.
1
Pause (CD) 1-ch TE, 2-ch TEDRV, 3-ch RF, 4-ch OFTR
(CH1) V: 1 V/div. H: 100 μsec/div.
(CH2) V: 1 V/div. H: 100 μsec/div.
(CH3) V: 1 V/div. H: 100 μsec/div.
(CH4) V: 5 V/div. H: 100 μsec/div.
6
Loading in
(1-ch LPS1, 2-ch LPS2, 3-ch LOAD)
(CH1) V: 5 V/div. H: 100 msec/div.
(CH2) V: 5 V/div. H: 100 msec/div.
(CH3) V: 2 V/div. H: 100 msec/div.
Loading out
(1-ch LPS1, 2-ch LPS2, 3-ch LOAD)
(CH1) V: 5 V/div. H: 200 msec/div.
(CH2) V: 5 V/div. H: 200 msec/div.
(CH3) V: 2 V/div. H: 200 msec/div.
2
Track search (CD) 1-ch TE, 2-ch TEDRV, 3-ch SLIN1, 4-ch SLIN2
(CH1) V: 1 V/div. H: 200 msec/div.
(CH2) V: 1 V/div. H: 200 msec/div.
(CH3) V: 2 V/div. H: 200 msec/div.
(CH4) V: 2 V/div. H: 200 msec/div.
7
In-focus (CD) 1-ch FE, 2-ch FEDRV
(CH1) V: 0.5 V/div. H: 1 msec/div.
(CH2) V: 0.5 V/div. H: 1 msec/div.
3
Search (CD-DA) 1-ch TE, 2-ch TEDRV, 3-ch SLIN1, 4-ch SLIN2
(CH1) V: 1 V/div. H: 100 msec/div.
(CH2) V: 1 V/div. H: 100 msec/div.
(CH3) V: 2 V/div. H: 100 msec/div.
(CH4) V: 2 V/div. H: 100 msec/div.
8
Setup (CD) 1-ch FE, 2-ch FEDRV, 3-ch TE, 4-ch SPIN
(CH1) V: 1 V/div. H: 500 msec/div.
(CH2) V: 500 mV/div. H: 500 msec/div.
(CH3) V: 1 V/div. H: 500 msec/div.
(CH4) V: 2 V/div. H: 500 msec/div.
4
Playback (CD) 1-ch FE, 2-ch TE, 3-ch SLIN1, 4-ch SLIN2
(CH1) V: 1 V/div. H: 1 sec/div.
(CH2) V: 1 V/div. H: 1 sec/div.
(CH3) V: 2 V/div. H: 1 sec/div.
(CH4) V: 2 V/div. H: 1 sec/div.
5
Stop (CD) 1-ch FE, 2-ch FEDRV, 3-ch SPIN, 4-ch SPDLFG
(CH1) V: 500 mV/div. H: 500 msec/div.
(CH2) V: 500 mV/div. H: 500 msec/div.
(CH3) V: 2 V/div. H: 500 msec/div.
(CH4) V: 5 V/div. H: 500 msec/div.
9
NOTE: The squared numbers denote measuring point in the schematic diagram and PCB diagram.
A
SRVB ASSY
2 3 4
5.4 OPERATIONAL WAVEFORMS
A
B
C
D
E
F
30
1
CDJ-900NXS
2 3 4