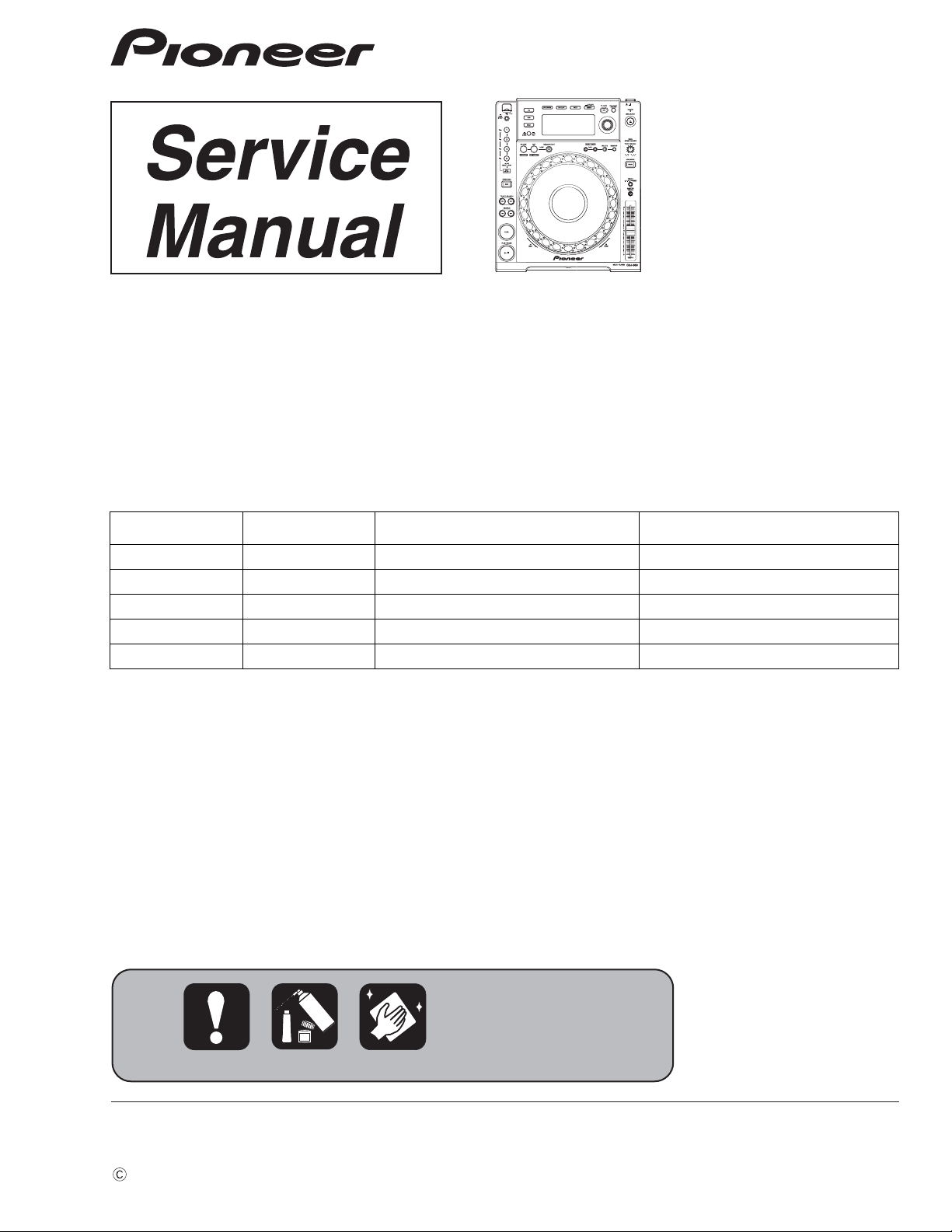
CDJ-850
For details, refer to "Important Check Points for good servicing".
MULTI PLAYER
CDJ-850
THIS MANUAL IS APPLICABLE TO THE FOLLOWING MODEL(S) AND TYPE(S).
Model Type Power Requirement Remarks
CDJ-850 SYXJ8 AC 220 V to 240 V
CDJ-850 CUXJ AC 120 V
CDJ-850 FLXJ AC 110 V to 240 V
CDJ-850 KXJ5 AC 220 V
CDJ-850 AXJ5 AC 220 V to 240 V
ORDER NO.
RRV4128
PIONEER CORPORATION 1-1, Shin-ogura, Saiwai-ku, Kawasaki-shi, Kanagawa 212-0031, Japan
PIONEER ELECTRONICS (USA) INC. P.O. Box 1760, Long Beach, CA 90801-1760, U.S.A.
PIONEER EUROPE NV Haven 1087, Keetberglaan 1, 9120 Melsele, Belgium
PIONEER ELECTRONICS ASIACENTRE PTE. LTD. 253 Alexandra Road, #04-01, Singapore 159936
PIONEER CORPORATION
K-IZV JULY
2010 Printed in Japan
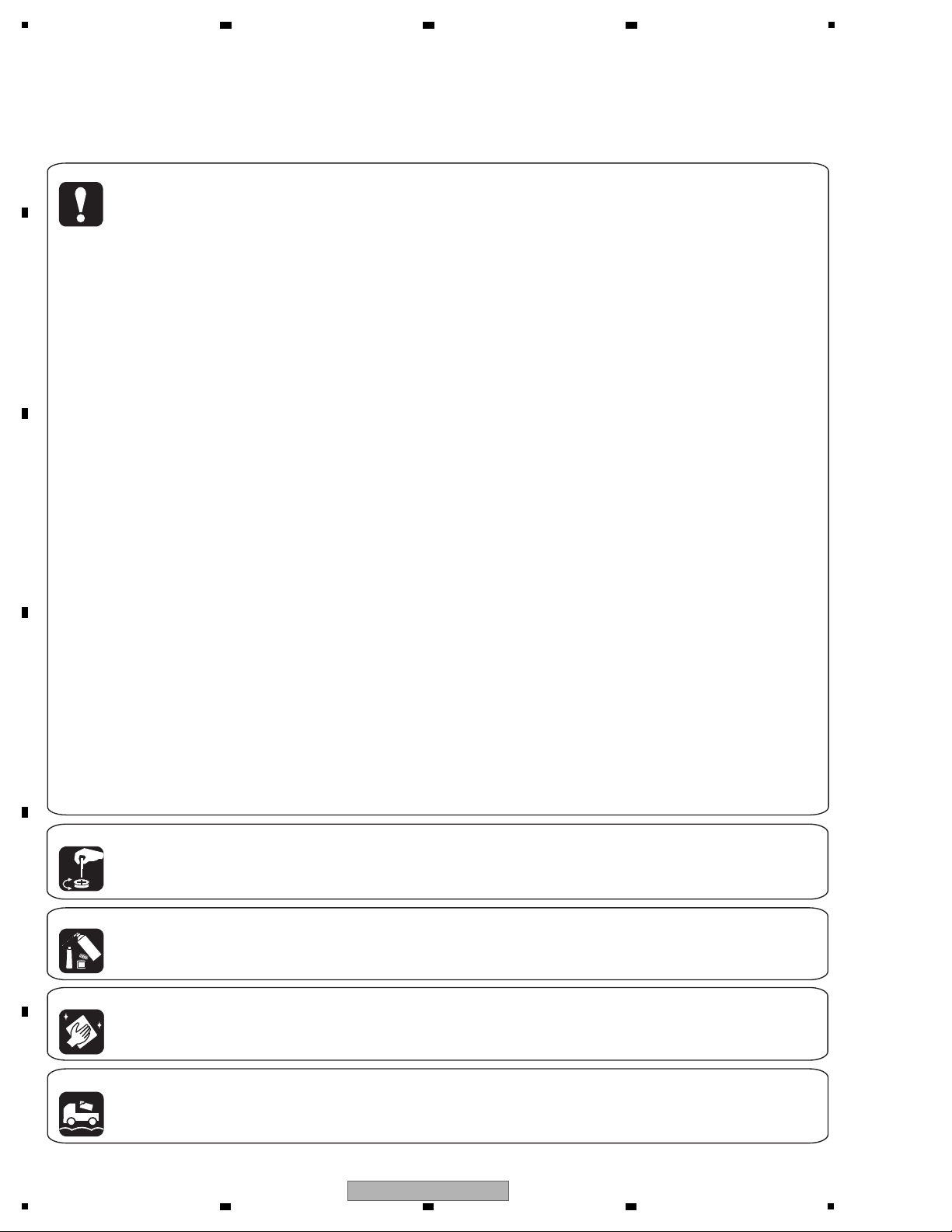
1
[Important Check Points for Good Servicing]
In this manual, procedures that must be performed during repairs are marked with the below symbol.
Please be sure to confirm and follow these procedures.
1. Product safety
Please conform to product regulations (such as safety and radiation regulations), and maintain a safe servicing environment by
following the safety instructions described in this manual.
1 Use specified parts for repair.
Use genuine parts. Be sure to use important parts for safety.
2 Do not perform modifications without proper instructions.
Please follow the specified safety methods when modification(addition/change of parts) is required due to interferences such as
radio/TV interference and foreign noise.
3 Make sure the soldering of repaired locations is properly performed.
When you solder while repairing, please be sure that there are no cold solder and other debris.
Soldering should be finished with the proper quantity. (Refer to the example)
4 Make sure the screws are tightly fastened.
Please be sure that all screws are fastened, and that there are no loose screws.
5 Make sure each connectors are correctly inserted.
Please be sure that all connectors are inserted, and that there are no imperfect insertion.
6 Make sure the wiring cables are set to their original state.
Please replace the wiring and cables to the original state after repairs.
In addition, be sure that there are no pinched wires, etc.
7 Make sure screws and soldering scraps do not remain inside the product.
Please check that neither solder debris nor screws remain inside the product.
8 There should be no semi-broken wires, scratches, melting, etc. on the coating of the power cord.
Damaged power cords may lead to fire accidents, so please be sure that there are no damages.
If you find a damaged power cord, please exchange it with a suitable one.
9 There should be no spark traces or similar marks on the power plug.
When spark traces or similar marks are found on the power supply plug, please check the connection and advise on secure
connections and suitable usage. Please exchange the power cord if necessary.
a Safe environment should be secured during servicing.
When you perform repairs, please pay attention to static electricity, furniture, household articles, etc. in order to prevent injuries.
Please pay attention to your surroundings and repair safely.
2. Adjustments
To keep the original performance of the products, optimum adjustments and confirmation of characteristics within specification.
Adjustments should be performed in accordance with the procedures/instructions described in this manual.
4. Cleaning
For parts that require cleaning, such as optical pickups, tape deck heads, lenses and mirrors used in projection monitors, proper
cleaning should be performed to restore their performances.
3. Lubricants, Glues, and Replacement parts
Use grease and adhesives that are equal to the specified substance.
Make sure the proper amount is applied.
5. Shipping mode and Shipping screws
To protect products from damages or failures during transit, the shipping mode should be set or the shipping screws should be
installed before shipment. Please be sure to follow this method especially if it is specified in this manual.
A
2 3 4
B
C
D
E
F
4
1
CDJ-850
2 3 4
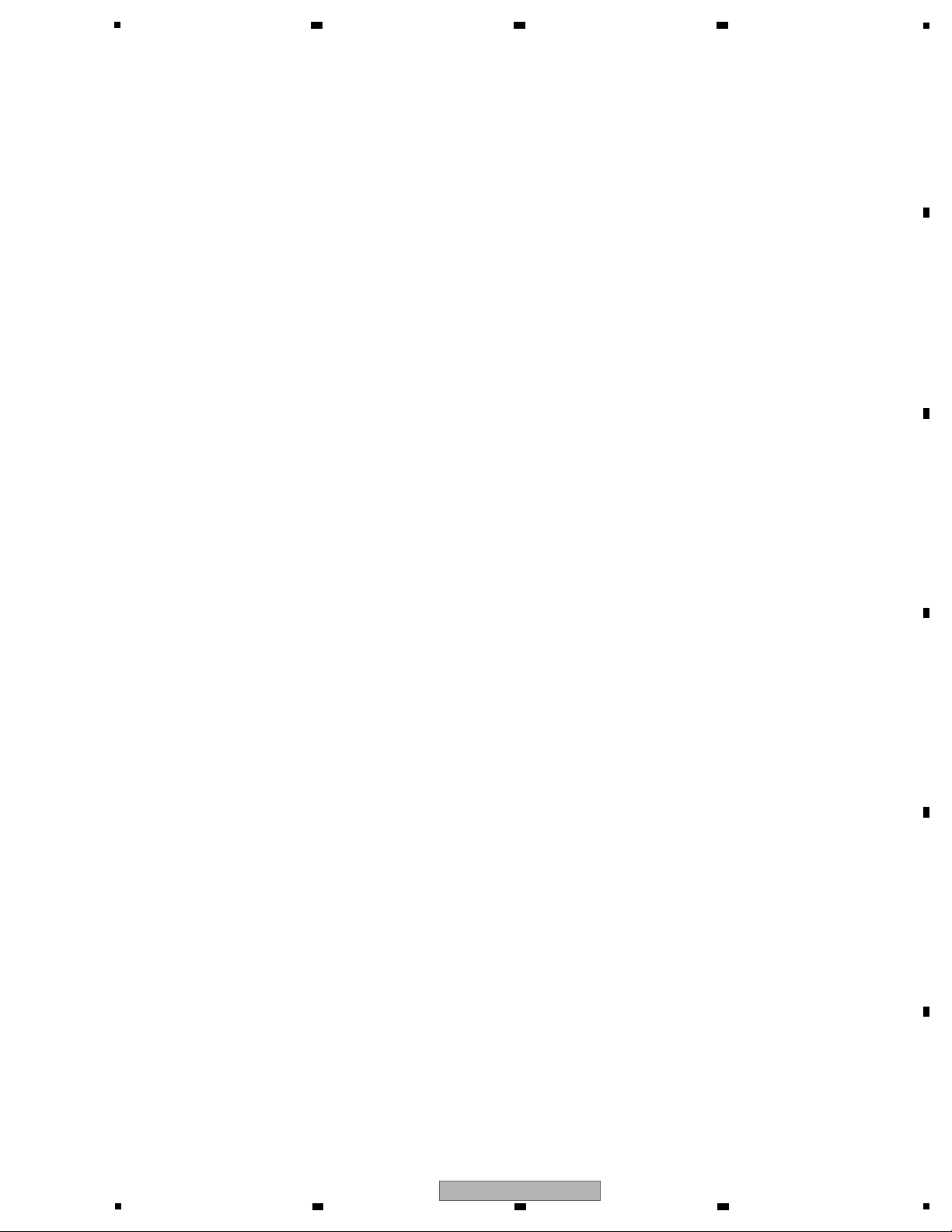
5
6 7 8
CONTENTS
SAFETY INFORMATION.......................................................................................................................................................... 2
1. SERVICE PRECAUTIONS ....................................................................................................................................................6
1.1 NOTES ON SOLDERING............................................................................................................................................... 6
1.2 ABOUT POWER SUPPLY MONITORING...................................................................................................................... 6
2. SPECIFICATIONS .................................................................................................................................................................7
2.1 SPECIFICATIONS .......................................................................................................................................................... 7
2.2 USABLE DISCS AND USB DEVICES............................................................................................................................ 8
2.3 PANEL FACILITIES....................................................................................................................................................... 10
3. BASIC ITEMS FOR SERVICE ............................................................................................................................................13
3.1 CHECK POINTS AFTER SERVICING .........................................................................................................................13
3.2 JIGS LIST .....................................................................................................................................................................13
3.3 PCB LOCATIONS ......................................................................................................................................................... 14
4. BLOCK DIAGRAM ..............................................................................................................................................................16
4.1 OVERALL WIRING DIAGRAM .....................................................................................................................................16
4.2 SIGNAL BLOCK DIAGRAM.......................................................................................................................................... 18
4.3 POWER SUPPLY BLOCK DIAGRAM........................................................................................................................... 20
5. DIAGNOSIS ........................................................................................................................................................................ 22
5.1 POWER ON SEQUENCE.............................................................................................................................................22
5.2 TROUBLESHOOTING.................................................................................................................................................. 23
5.3 DIAGNOSIS OF THE PICKUP ASSY........................................................................................................................... 32
5.4 CONNECTION CHECK WITH THE PC........................................................................................................................ 33
5.5 ABOUT POWER SUPPLY MONITORING.................................................................................................................... 34
5.6 ABOUT THE PROTECTORS........................................................................................................................................ 34
6. SERVICE MODE................................................................................................................................................................. 35
6.1 SERVICE MODE ................................................................................................................
6.2 ABOUT THE DEVICE OF CDJ-850..............................................................................................................................35
6.3 DETAILS ON SERVICE MODE .................................................................................................................................... 36
7. DISASSEMBLY ................................................................................................................................................................... 42
8. EACH SETTING AND ADJUSTMENT................................................................................................................................ 52
8.1 NECESSARY ITEMS TO BE NOTED...........................................................................................................................52
8.2 USER SETABLE ITEMS ............................................................................................................................................... 52
8.3 UPDATING OF THE FIRMWARE ................................................................................................................................. 53
8.4 JOG DIAL ROTATION LOAD ADJUSTMENT ............................................................................................................... 55
9. EXPLODED VIEWS AND PARTS LIST...............................................................................................................................56
9.1 PACKING SECTION ..................................................................................................................................................... 56
9.2 EXTERIOR SECION.....................................................................................................................................................58
9.3 CONTROL PANEL SECTION ....................................................................................................................................... 60
9.4 JOG DIAL SECTION .................................................................................................................................................... 62
9.5 SLOTIN MECHA SECTION.......................................................................................................................................... 64
10. SCHEMATIC DIAGRAM .................................................................................................................................................... 66
10.1 CNCT, SLMB and JINT ASSYS .................................................................................................................................. 66
10.2 MAIN ASSY (1/4)........................................................................................................................................................68
10.3 MAIN ASSY (2/4)........................................................................................................................................................70
10.4 MAIN ASSY (3/4)........................................................................................................................................................72
10.5 MAIN ASSY (4/4)........................................................................................................................................................74
10.6 CMPX (1/2) and USBA ASSYS .................................................................................................................................. 76
10.7 CMPX ASSY (2/2) ......................................................................................................................................................78
10.8 DFLB ASSY .....................................................................................................................
SW1 and KSW2 ASSYS .......................................................................................................................................... 82
10.9 K
10.10 JFLB and JOGB ASSYS...........................................................................................................................................84
10.11 SLD1, PSWB and SLD2 ASSYS ..............................................................................................................................86
10.12 POWER SUPPLY and ACIN ASSYS ........................................................................................................................ 88
10.13 VOLTAGES ............................................................................................................................................................... 90
10.14 WAVEFORMS...........................................................................................................................................................91
10.15 EACH SIGNAL LEVEL.............................................................................................................................................. 93
11. PCB CONNECTION DIAGRAM........................................................................................................................................94
11.1 CNCT, SLMB and JINT ASSYS .................................................................................................................................. 94
11.2 MAIN ASSY ................................................................................................................................................................ 98
11.3 CMPX and USBA ASSYS.........................................................................................................................................102
11.4 DFLB ASSY .............................................................................................................................................................. 106
SW1 and KSW2 ASSYS ........................................................................................................................................ 110
11.5 K
11.6 JFLB and JOGB ASSYS...........................................................................................................................................112
11.7 SLD1, PSWB and SLD2 ASSYS ..............................................................................................................................114
11.8 POWER SUPPLY and ACIN ASSYS ........................................................................................................................116
12. PCB PARTS LIST ............................................................................................................................................................ 118
.......................................... 35
........................................... 80
A
B
C
D
E
F
CDJ-850
5
6 7 8
5
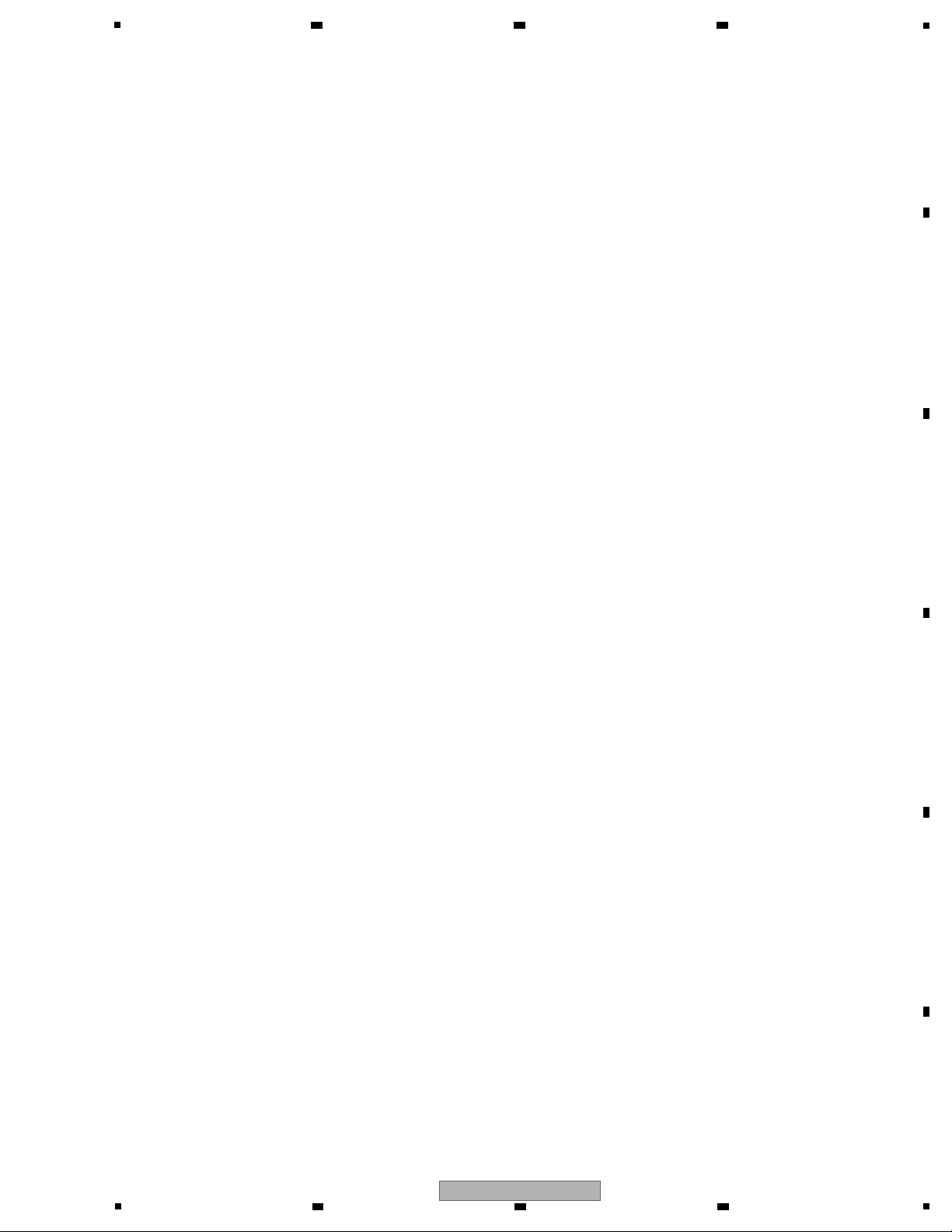
5
Power requirements........ AC 220 V to 240 V, 50 Hz/ 60 Hz (SYXJ8)
AC 120 V, 60 Hz (CUXJ)
AC 110 V to 240 V, 50 Hz/ 60 Hz (FLXJ)
AC 220 V, 60 Hz (KXJ5)
AC 220 V to 240 V, 50 Hz/ 60 Hz (AXJ5)
Power consumption................................................................... 21 W
Power consumption (standby).................................................. 0.4 W
Main unit weight....................................................................... 2.3 kg
Max. dimensions........ 305 mm (W) × 105.5 mm (H) × 364.4 mm (D)
(12 in. (W) × 4.2 in. (H) × 14.3 in. (D))
Tolerable operating temperature.............................. +5 °C to +35 °C
(+41 °F to +95 °F)
Tolerable operating humidity.............5 % to 85 % (no condensation)
Analog audio output (AUDIO OUT L/ R)
Output terminal.............................................................RCA terminal
Output Level........................................................... 2.0 Vrms (1 kHz)
Frequency response.................................................. 4 Hz to 20 kHz
S/ N ratio.................................................................................115 dB
Total harmonic distortion.......................................................0.003 %
USB downstream section (USB)
Port..........................................................................................Type A
Power supply.......................................................5 V/ 500 mA or less
USB upstream section (USB)
Port..........................................................................................Type B
Control output (CONTROL)
Port...................................................................................... Mini-jack
• The specifications and design of this product are subject to
change without notice.
2. SPECIFICATIONS
2.1 SPECIFICATIONS
6 7 8
A
B
C
D
E
F
CDJ-850
5
6 7 8
7
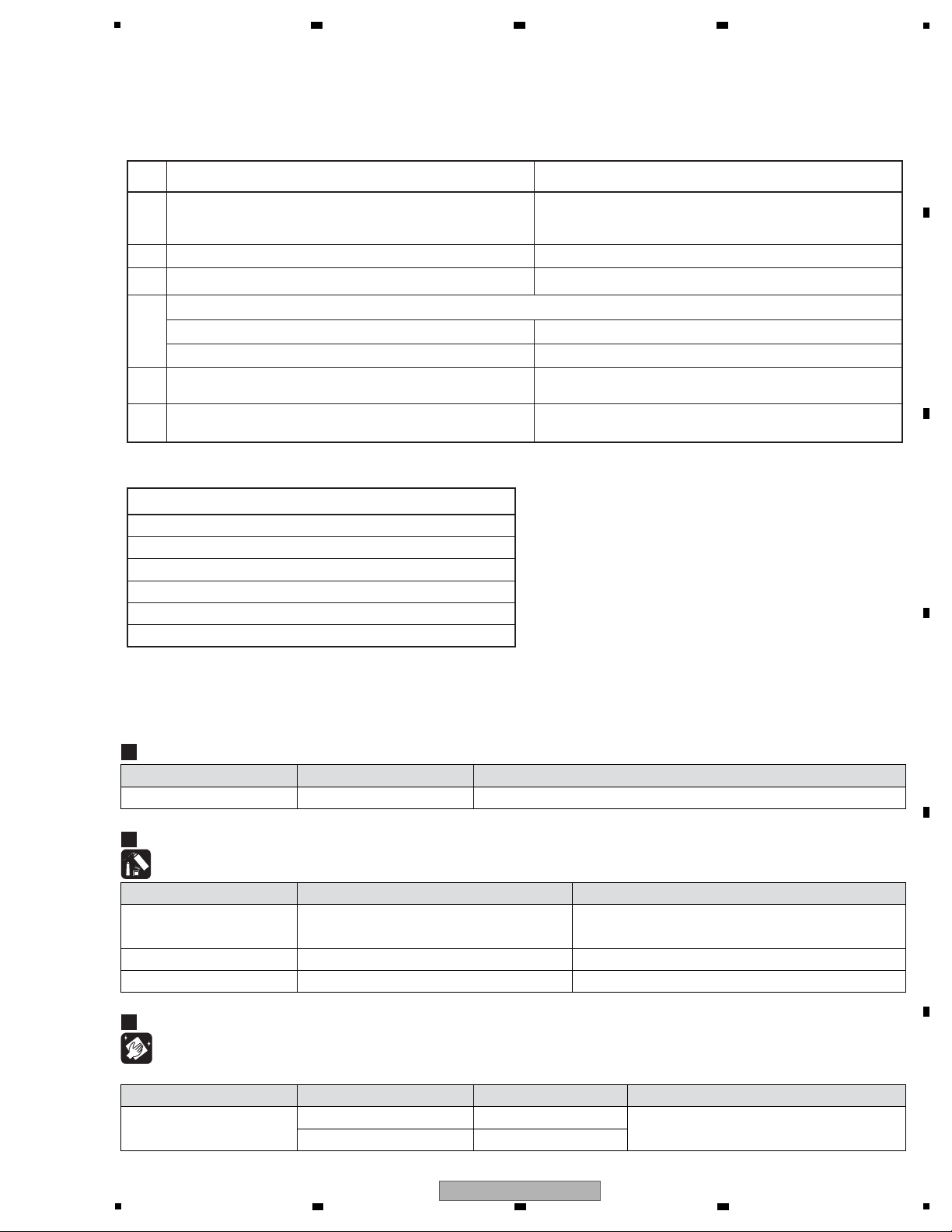
5
Items to be checked after servicing / CDJ
To keep the product quality after servicing, confirm recommended check points shown below.
No.
Procedures Check points
1
3
4
5
6
Confirm whether the customer complain has been solved.
If the customer complain occurs with the specific disc, use it for
the operation check.
The customer complain must not be reappeared.
Audio and operations must be normal.
Play back a CD. (track search) Audio, Search and operations must be normal.
2 Check output analog audio. Audio and operations must be normal.
Check the connection of each interface.
Play back data contained in the device connected to USB A. Audio, Search and operations must be normal.
USB B The device must be recognized by the PC.
Check output signals while the JOG dial or TEMPO slider is
being operated.
Audio and operations must be normal.
Check the appearance of the product.
No scratches or dirt on its appearance after receiving it for
service.
Item to be checked regarding audio
Distortion
Noise
Volume too low
Volume too high
Volume fluctuating
Sound interrupted
See the table below for the items to be checked regarding video and audio.
Cleaning
Name Part No. Remarks
Cleaning paper GED-008
Cleaning liquied GEM1004 Refer to
"9.5 SLOTIN MECHA SECTION".
Position to be cleaned
Pickup lenses
Jigs List
Jig Name Part No. Purpose of use / Remarks
CD test disc STD-905 CD playback diagnosis
Before shipping out the product, be sure to clean the following positions by using the prescribed cleaning tools.
Lubricants and Glues List
Name Part No. Remarks
Lubricating oil ZLB-HFD1600 Refer to “9.4 JOG DIAL SECTION”.
Dyfree GEM1036 Refer to “9.5 SLOTIN MECHA SECTION”.
Lubricating oil GYA1001
Refer to “9.4 JOG DIAL SECTION”,
“9.5 SLOTIN MECHA SECTION”.
6 7 8
3. BASIC ITEMS FOR SERVICE
3.1 CHECK POINTS AFTER SERVICING
A
B
3.2 JIGS LIST
5
6 7 8
CDJ-850
C
D
E
F
13

1
ADG7022 (For CUXJ)
ADG7097, ADG1154 (For FLXJ)
XDG3054 (For KXJ5)
ADG1154 (For SYXJ8)
ADG7079 (For AXJ5)
ACIN ASSY
(DWX3173: CUXJ)
(DWX3158: OTHERS)
P
DKP3891: CUXJ
DKP3889: OTHERS
I
H
KSW2
(DWS
KSW1 A
(DWS1
B
C
SLMB ASSY
(DWS1425)
O
POWER SUPPLY
ASSY
(DWR1463)
JINT ASSY
(DWX3157)
A
CNCT ASSY
(DWX3151)
CMPX ASSY
(DWX3153)
E
E E
1/2, 2/2
MAIN ASSY
(DWX3174)
D
D D
1/4- 4/4
!
!
AKM1299-A
CN401
1
V+7R6_M2GNDM
3
GNDD4GNDD5GNDD
6
V+7R6_D7V+7R6_D
8
GNDD
9
V+12
10
GNDD
11
V-10_A
12
GNDA
13
V+10_A
B6B-XH-A
1
GNDM
2
GNDD
3
PWR_XON
4
V+12
5
V+12
6
V+12_EUP
B2P3-VH
1
LIVE(PURPLE)
2
NEUTRAL(BLUE)
1V+6R6
2GNDD
3CUE_LED
4CUE_SW
5PLAY_LED
1
ST1-
2
ST1+
3
ST2+
4
ST2-
1
FR
2
FD
3
TR
4
TD
5
NC
6
GNDS
7
LD650
8
PD
9
LD780
10
GNDS
11
VR780
12
VRCOM
13
VR650
14
A
15
B
16
VRF
17
SW1_DVD/CD
18
C
19
D
20
E
21
Vcc
22
VREF
23
F
24
GNDS
DKN1445-A
CN2302
GNDS
1
V+5P
2
F
3
VREF
4
E
5
D
6
C
7
GNDS
8
GNDS
9
B
10
A
11
GNDS
12
GNDS
13
VR780PD
14
GNDS
15
GNDS
16
GNDS
17
GNDS
18
LD780
19
GNDS
20
TD
21
TR
22
FD
23
FR
24
DKN1312-A
CN2301
1
INSW
2
W
3
V
4
U
5
HB
6
W-
7
W+
8
V-
9
V+
10
U-
11
U+
12
VCC
CN2304
DKN1288-A
ST1-
1
ST1+
2
ST2+
3
ST2-
4
DKN1445-A
CN2501
FR
1
FD
2
TR
3
TD
4
NC
5
GNDS
6
LD650
7
PD
8
LD780
9
GNDS
10
VR780
11
VRCOM
12
VR650
13
A
14
B
15
VRF
16
SW1_DVD/CD
17
C
18
D
19
E
20
Vcc
21
VREF
22
F
23
GNDS
24
DKN1445-A
CN2502
1
GNDS
2
V+5P
3
F
4
VREF
5
E
6
D
7
C
8
GNDS
9
GNDS
10
B
11
A
12
GNDS
13
GNDS
14
VR780PD
15
GNDS
16
GNDS
17
GNDS
18
GNDS
19
LD780
20
GNDS
21
TD
22
TR
23
FD
24
FR
CN1701
VKN 1265-A
LPS21
LPS12
GNDD3
LO+4
LO-5
RKN1058-A
CN403
1
GNDD
2
GNDD
3
VBUS_B
4
GNDD
5
USB_D_P
6
USB_D_N
7
GNDD
8
CONT2
9
GNDD
10
CONT1
11
GNDD
12
GNDD
13
GNDA
14
LOUT
15
GNDA
16
ROUT
17
GNDA
RKN1068-A
CN402
1
USBA_D_P
2
USBA_D_N
3
GNDD
4
USB_CODETFLG
5
GNDD
6
USB_VBUSON
7
GNDD
8
PWR_ON
9
GNDD
10
VDET
11
GNDD
12
MAIN_XMUTE
13
GNDD
14
MAIN_XRST
15
TSI
16
MAIN_XBUSY
17
TSO
18
PNL_XBUSY
19
GNDD
20
TSCK
21
GNDD
22
V+5R6
23
V+5R6
24
GNDD
25
GNDD
26
V+12_EUP
27
GNDD
KM200NA13
CN2004
1
V+7R6_M
2
GNDM
3
GNDD
4
GNDD
5
GNDD
6
V+7R6_D
7
V+7R6_D
8
GNDD
9
V+12
10
GNDD
11
V-10_A
12
GNDA
13
V+10_A
B6B-XH-A
CN2001
1
GNDM
2GNDD
3PWR_XON
4V+12
5V+12
6V+12_EUP
VKN1252-A
CN2003
1
TSO
2
PNL_XBUSY
3
TSI
4
GNDD
5
TSCK
6
GNDD
7
PNL_CNVSS
8
GNDD
9
PNL_XRST
10
MAIN_XBUSY
11
USB_STOP
12
MAIN_XRST
13
PWR_ON
14
PNL_XMUTE
15
VDET
16
GNDD
17
V+12
18
V+12
19
GNDD
20
V+12_EUP
21
GNDD
VKN 1258-A
CN2002
CN1
CN2
1
GNDD
2
V+12_EUP
3
GNDD
4
GNDD
5
V+5R6
6
V+5R6
7
GNDD
8
TSCK
9
GNDD
10 PNL_XBUSY
11 TSO
12
MAIN_XBUSY
13 TSI
14
MAIN_XRST
15
GNDD
16
MAIN_XMUTE
17
GNDD
18
VDET
19
GNDD
20 PWR_ON
21
GNDD
22
USB_VBUSON
23
GNDD
24 USB_CODETFLG
25
GNDD
26 USBA_D_N
27 USBA_D_P
VKN1248-A
CN2006
1
GNDA
2
ROUT
3
GNDA
4
LOUT
5
GNDA
6
GNDD
7
GNDD
8
CONT1
9
GNDD
10
CONT2
11
GNDD
12
USB_D_N
13
USB_D_P
14
GNDD
15
VBUS_B
16
GNDD
17
GNDD
CN2005
52147-0510
1
V+5_USB
2
USBA_D_N
3
USBA_D_P
4
GNDD
5
GNDD
51048-0500
JH2201
1
V+5_USB
2
USBA_D_N
3
USBA_D_P
4
GNDD
5
GNDD
JA2401
1
2
DKN1407-A
CN2305
1
INSW
2
W
3
W
4
V
5
V
6
U
7
U
8
GNDD
9
HW-
10
HW+
11
HV-
12
HV+
13
HU-
14
HU+
15
V+5M
16
GNDD
17
FR
18
FD
19
TR
20
TD
21
GNDS
22
LD780
23
GNDS
24
PD
25
A_A
26
A_B
27
A_C
28
A_D
29
A_S1
30
VREF
31
A_S2
32
V+5P
33
GNDS
34
GNDS
35
GNDS
36
LPS1
37
LPS2
38
GNDS
39
LO-
40
LO-
41
LO+
42
LO+
43
ST2+
44
ST2+
45
ST2-
46
ST2-
47
ST1+
48
ST1+
49
ST1-
50
ST1-
DKN1404-A
CN201
1
ST1-
2
ST1-
3
ST1+
4
ST1+
5
ST2-
6
ST2-
7
ST2+
8
ST2+
9
LO+
10
LO+
11
LO-
12
LO-
13
GNDS
14
LPS2
15
LPS1
16
GNDS
17
GNDS
18
GNDS
19
V+5P
20
A_S2
21
VREF
22
A_S1
23
A_D
24
A_C
25
A_B
26
A_A
27
PD
28
GNDS
29
LD780
30
GNDS
31
TD
32
TR
33
FD
34
FR
35
GNDD
36
V+5M
37
HU+
38
HU-
39
HV+
40
HV-
41
HW+
42
HW-
43
GNDD
44
U
45
U
46
V
47
V
48
W
49
W
50
INSW
CN2303
VKN 1374-A
1
LPS2
2
LPS1
3
GNDD
4
LO+
5
LO-
1
INSW
2
W
3
V
4
U
5
HB
6
W-
7
W+
8
V-
9
V+
10
U-
11
U+
12
VCC
NEUTRAL
LIVE
SPINDLE MOTOR
09SD PICK UP ASSY
DDD1527Pitch=1.0mm
Length=180mm
Same Face
FFC
DDD1491Pitch=0.5mm
Length=175mm
Reverse Face FFC
ZWNN1007G28-9-06A
Length=60mm
White Single Wire
ZWNN1007G28-8-06A
Length=60mm
Gray Single Wire
LO-
LO-
LO+
LO+
LOADING MOTOR
ASSY-S
(DXX2615)
Pitch=1.0mm
Reverce Face
FFC
DDD1536-(Gold)
Pitch=0.5mm
Length=66mm
Reverse Face FFC
PF13PP-S07
Pitch=2.0mm
Length=75mm
Connector Ass'y
DDD1524Pitch=1.0mm
Length=70mm
Same Face
FFC
DDD1523Pitch=1.0mm
Length=70mm
Same Face
FFC
D20PDY07
Pitch=2.0m
Length=20
Parallel Ju
DDD1522Pitch=1.0mm
Length=170mm
Same Face
FFC
D20PDY0510E
Pitch=2.0mm
Length=100mm
Parallel Jumper
Wire
DE010VE0
Length=100mm
Earth Lead Cable
Horizontal
Contact Side Down
Vertical
Horizontal
AC POWER CORD
Vertical
Contact Side
Vertical
Contact Side
Vertical
Vertical
VH
Soldered
DKP3869Pitch=2.5mm
Length=100mm
Connector Assy
DKP3870Pitch=3.96mm
Length=100mm
Connector Ass'y
US
Pitch=1.0mm
Same Face
FPC
STEPPING
MOTOR
Horizontal
Contact Side Up
Vertical
Contact Side
Horizontal
Contact Side Up
Horizontal
Contact Side Down
Horizontal
Contact Side Down
Horizontal
Contact Side Down
Horizontal
Contact Side Down
Horizontal
Contact Side Down
Horizontal
Contact Side Up
Horizontal
Contact Side Up
Boardin
Vertical
Vertical
Vertical
Verti
Vertical
Contact Side
Soldered
DDD1535Pitch=0.5mm
Length=80mm
Reverse Face FFC
SLOTIN MECHA ASSY
(DXA2206)
TM ASSY-S (DXX2616)
4. BLOCK DIAGRAM
4.1 OVERALL WIRING DIAGRAM
A
16
1
B
C
D
E
F
2 3 4
2 3 4
CDJ-850
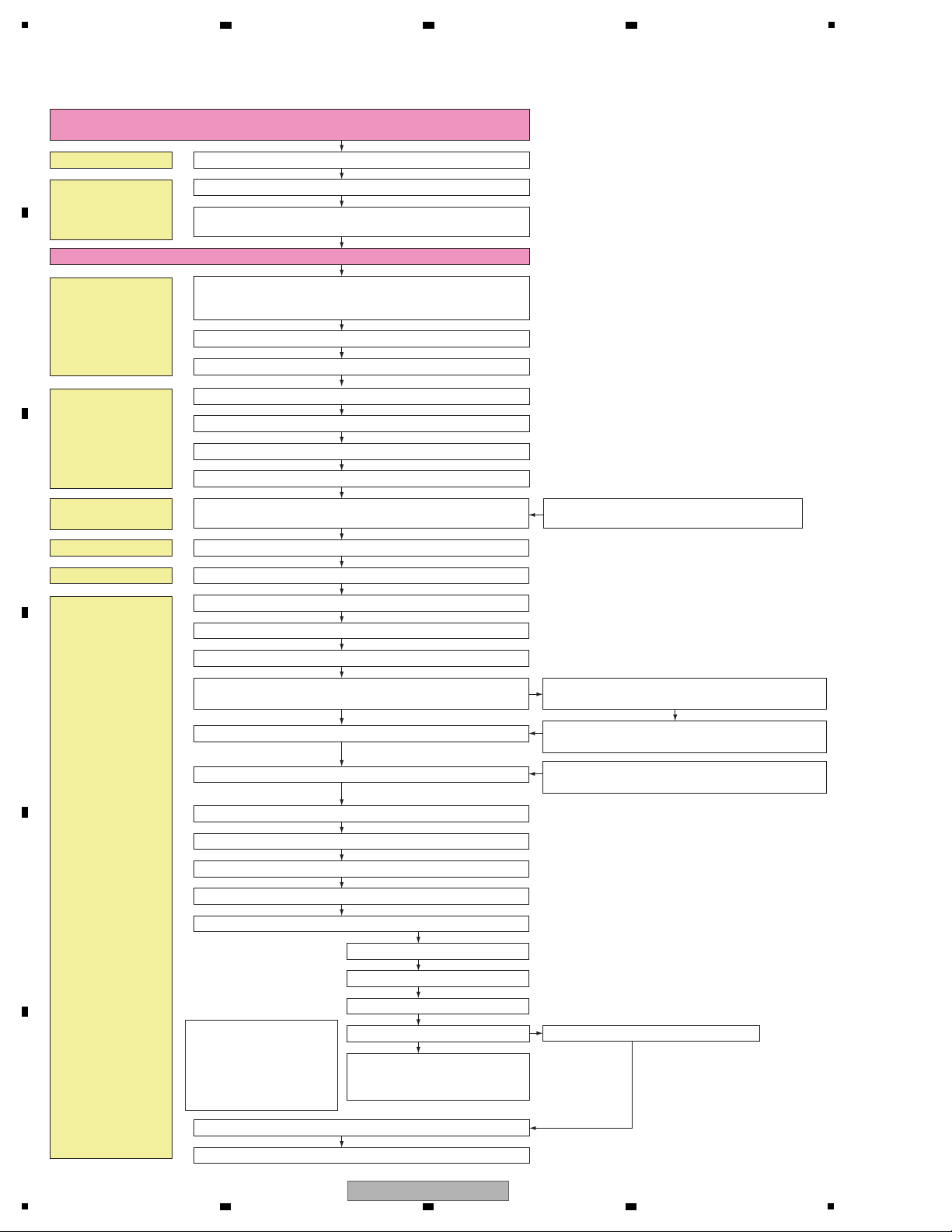
1
If the level of the S-shaped waveform is 0.88 Vp-p or less,
focusing is turned ON with RF gain increased.
If checking fails three times, “EJECT” will be
displayed on the FL display.
The first track is searched for.
After TOC reading is completed
Waiting 300 ms
Tracking balance adjustment (Tracking open)
Tracking close
GFS (RF lock) check
Main CPU (IC103)
Panel CPU (IC1007)
Adjustment of tracking and focus offset
Spindle kick, focus sweep, and focus ON
Checking if focus is OK
Audio DSP (IC301)
Servo DSP (IC201)
CD drive
Playback (Muting OFF)
Focus gain adjustment
AC IN (Plugging of the AC power cord)
Power supply (V+12_EUP, V+3R3R_EUP) to the Panel CPU starts.
Reset IC (IC1004)
TOC reading
Depending on the accuracy
of the stepper, the TOC
position memory will be
located after the unit is
turned ON.
Tracking gain adjustment
RF gain adjustment
If the pickup is reading the
program area, it will jump
to the TOC area.
The program is downloaded to IC301 (Audio DSP).
IC103 (Pin 158): The Reset signal is sent to the Audio DSP (IC301).
IC301 (Pin 47): Receives the Reset signal.
IC1007 (Pin 12): Receives the Reset signal.
IC1004 (Pin 4): The Reset signal is sent to the Panel CPU (IC1007).
POWER ON (Turn on the POWER switch.)
Main CPU
(IC103)
STANDBY mode is entered.
*FL display: Unlit.
Panel CPU
(IC1007)
Panel CPU
(IC1007)
IC1007 (Pin 45): Power supply to the Main CPU (IC103) starts.
IC1007 (Pin 40): The Reset signal is sent to the Main CPU (IC103).
IC103 (Pin 69): The Reset signal is sent to the Servo DSP (IC201).
If communication fails, “E–8709” will be
displayed on the FL display.
STANDBY mode is shifted to POWER_ON mode.
“POWER ON” is displayed on the FL display.
Focus balance adjustment
IC103 (Pin 59): Receives the Reset signal.
Communication between the Main CPU (IC103) and
Panel CPU (IC1007) starts.
IC201 (Pin 90): Receives the Reset signal.
Checking the inside SW
LD (Laser Diode) ON
Acceleration of spindle (200 ms)
CLV servo ON
If the first check fails, measure the level of the S-shaped
waveform while the pickup lens is descending.
5. DIAGNOSIS
5.1 POWER ON SEQUENCE
A
2 3 4
B
C
D
E
F
22
1
CDJ-850
2 3 4
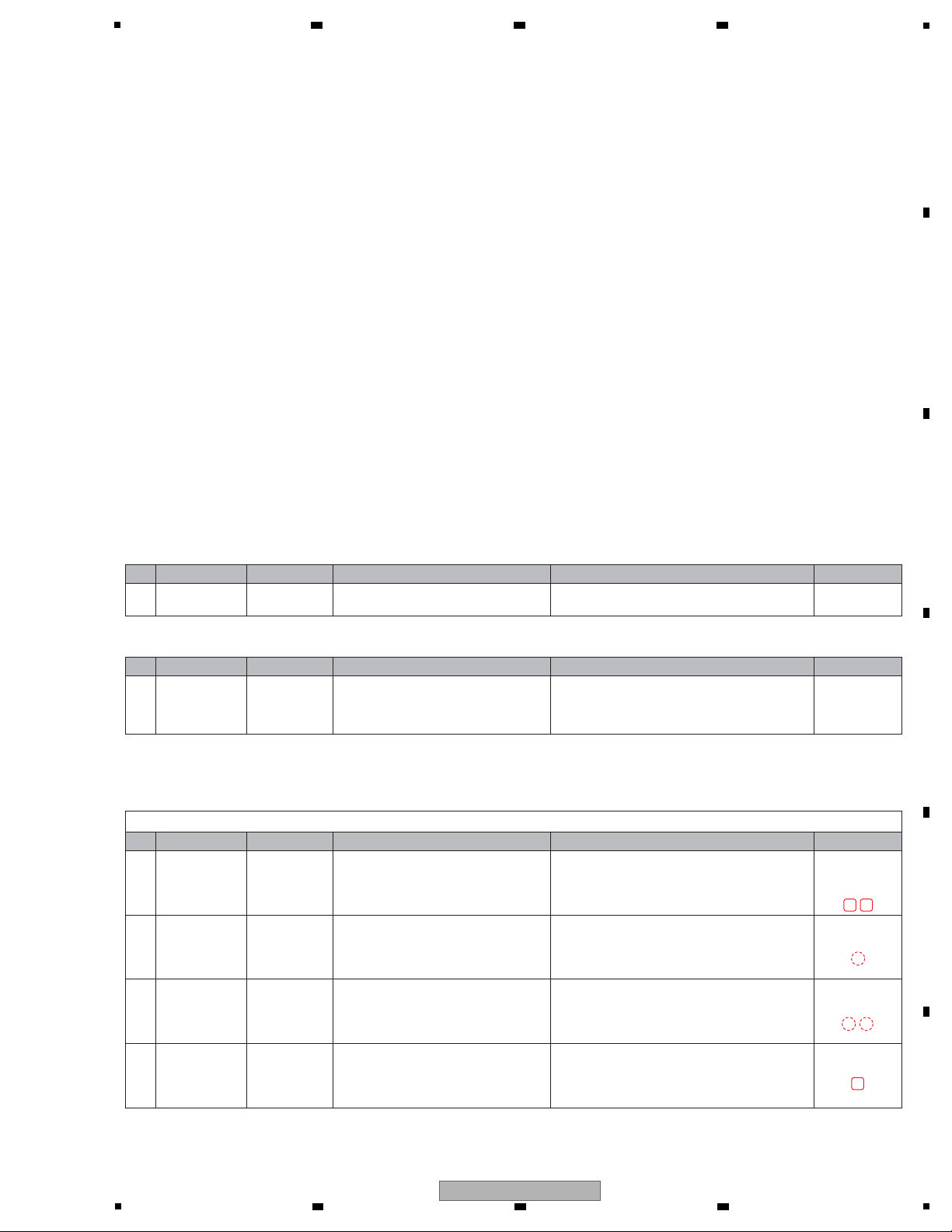
5
In this section, causes of failure, diagnostics points, and corrective measures can be searched for according to symptoms.
Before disassembling this unit, it is recommended to infer a failure point by referring to the error code.
For the relationship of each power-supply and signal system, see “4.3 POWER SUPPLY BLOCK DIAGRAM.”
If software of the product is updated before performing diagnostics, check that software updating has been performed properly
before proceeding to diagnostics.
If software updating has not been performed properly, update the software, following the instructions in “8.3 UPDATING OF
THE FIRMWARE.”
Contents
[0] Prior Confirmation
[1] Failure in Startup
[2] Display (DATA FL/JOG FL/LED)
[3] Operations (SW/Volume/JOG)
[4] USB (USB-Type A), PC (USB-Type B)
[5] AUDIO OUT
[6] CONTROL
[7] DRIVE Assy
[8] SERVICE MODE
[9] Error Codes
[10] Basic Operation Check of CPU/DSP
The waveform numbers described in this section correspond to the “10.14 WAVEFORMS.”
[0] Prior Confirmation
[0-1] Checking in Service Mode
[0-2] Checking Cables
[1] Failure in Startup
[1-1] No power
No. Cause
Diagnostics Point
Item to be Checked Corrective Action Reference
No. Cause
Diagnostics Point
Item to be Checked Corrective Action Reference
No. Cause
Diagnostics Point
Item to be Checked Corrective Action Reference
1 — Check the failure points.
See the section describing locations of defects in
this manual.
6. SERVICE
MODE
1 Cables
Service mode
Disconnection,
breakage, or
loose connection
of cables
Check that all the cables are securely
connected.
Check that there is no breakage in the
cables.
Securely connect the cables. If a cable is broken,
replace it.
4.1 OVERALL
CONNECTION
DIAGRAM
4.3 POWER SUPPLY
BLOCK DIAGRAM
10.13 VOLTAGES
Plug the AC power cord in and even if turn the power on, the product does not startup.
1
Standby power
failure
CMPX Assy
DFLB Assy
POWER
SUPPLY Assy
Check the voltages of V+12_EUP and
V+3R3_EUP.
If the V+12_EUP voltage is not output, the POWER
SUPPLY Assy may be defective.
If the V+12_EUP voltage is output, the DFLB Assy
may be defective.
10.15 EACH
SIGNAL LEVEL
2
Path failure of
the power switch
DFLB Assy
SLD1 Assy
PSWB Assy
Check if there is loose connection on the
signal line from the Power switch (S1601)
to PANEL CPU (IC1007).
If the connection up to the Power switch is properly
made and if the PWR_SW signal is not set to "L"
when the Power switch is pressed, the Power switch
may be defective.
10.15 EACH
SIGNAL LEVEL
3
Path failure of
the power on
DFLB Assy
CMPX Assy
Check the level of PWR_ON (IC1007-pin
45) and PWR_XON (CN2001-pin 3) signals.
If the PWR_ON is "L", PANEL CPU(IC1007) may be
defective.
If the PWR_XON is "H", poor connection or Q2021
may be defective.
10.13 VOLTAGES
4 Power failure
CMPX Assy
POWER
SUPPLY Assy
Check the V+12 voltage of CN2001-pins
4 and 5.
If the voltage is not output, POWER SUPPLY Assy
may be defective.
2
1 18
B J
A
6 7 8
5.2 TROUBLESHOOTING
A
B
C
D
E
F
CDJ-850
5
6 7 8
23
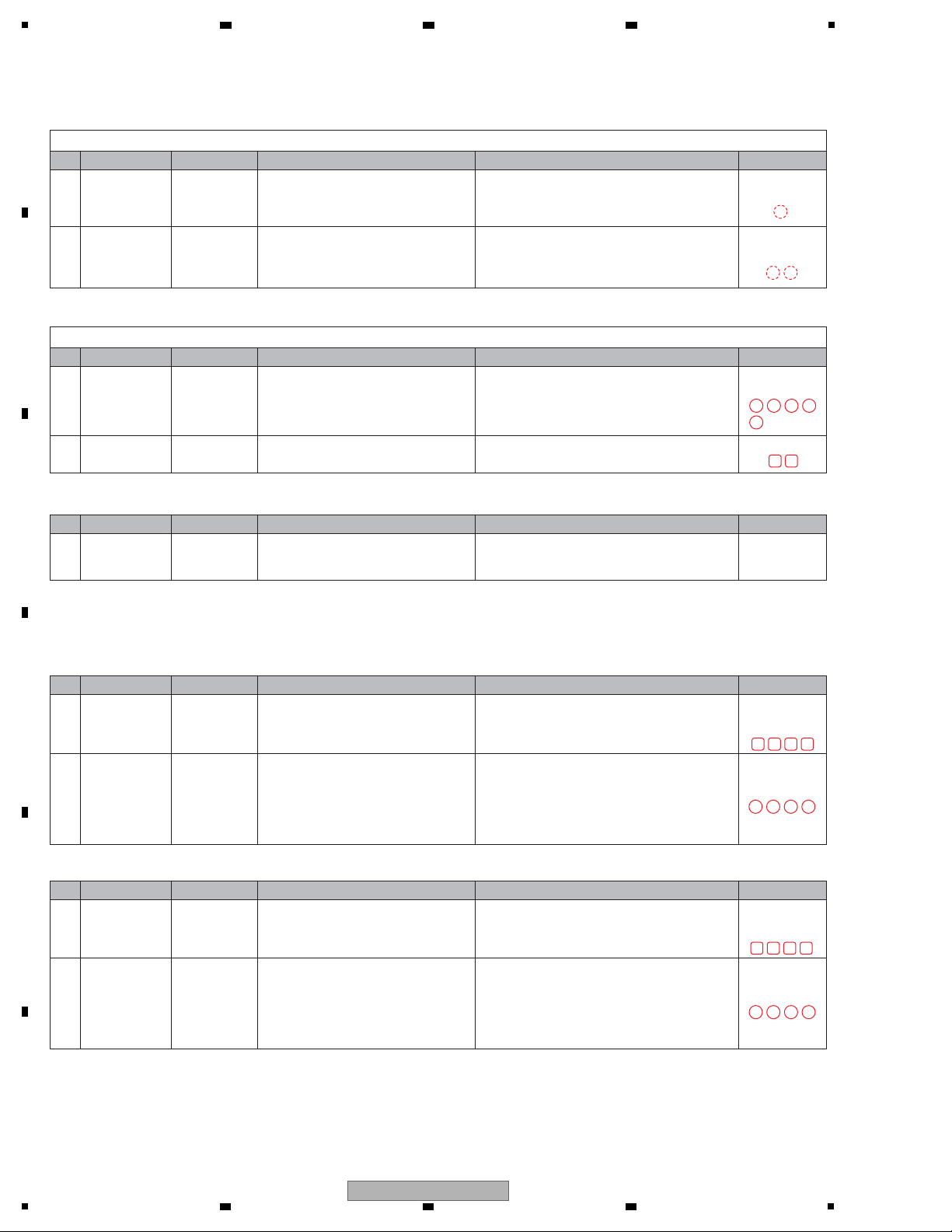
1
[1-2] Mode shift error in Standby mode
[2-1] The DATA FL does not light.
[2-2] The JOG FL does not light.
[2] Display (DATA FL/JOG FL/LED)
[1-3] “E-8709” is displayed on the DATA FL display after startup.
[1-4] The Standby LED flashes in red.
Shifting to the STANDBY mode cannot be performed even if turn the power off.
1
Path failure of
the power switch
DFLB Assy
SLD1 Assy
PSWB Assy
Check if there is loose connection on the
signal line from the Power switch (S1601)
to PANEL CPU (IC1007).
If the connection up to the Power switch is properly
made and if the PWR_SW signal is not set to "H"
when the Power switch is turned off, the Power switch
may be defective.
2
Path failure of
the power on
DFLB Assy
CMPX Assy
Check the level of PWR_ON (IC1007-pin
45) and PWR_XON (CN2001-pin 3) signals.
If the PWR_ON is "H", PANEL CPU(IC1007) may be
defective.
If the PWR_XON is "L", poor connection or Q2021
may be defective.
10.14
WAVEFORMS
1 Power failure DFLB Assy
Check the power-supply voltages
(V+6R6,F±, V+38, V+3R3_SW) of the FL.
If the presence of power is not confirmed, check the
mounting statuses of the regulator IC and its
peripheral parts for each power supply. If they are
properly mounted, then the parts may be defective.
4.3 POWER SUPPLY
BLOCK DIAGRAM
10.13 VOLTAGES
2 Signal errors DFLB Assy
Check the waveforms and connection of
communication line of FL in the DFLB Assy.
• D_SCLK
• D_SO
• D_LAT
• D_BK
If no signal is output, the PANEL CPU (IC1007) may
be defective.
If output signal is no problem, DATA FL (V1001) may
be defective.
10.14
WAVEFORMS
1 Power failure JFLB Assy
Check the power-supply voltages
(VFDP2R7_F1, VFDP2R7_F2, V+27,
V+3R3_SW) of the FL.
If the presence of power is not confirmed, check the
mounting statuses of the regulator IC and its
peripheral parts for each power supply. If they are
properly mounted, then the parts may be defective.
4.3 POWER SUPPLY
BLOCK DIAGRAM
10.13 VOLTAGES
2 Signal errors JFLB Assy
Check the waveforms and connection of
communication line of FL in the JFLB Assy.
• J_SCLK
• J_SO
• J_LAT
• J_BK
If no signal is output, the PANEL CPU (IC1007) may
be defective.
If output signal is no problem, JOG FL (V1801) may
be defective.
10.13 VOLTAGES
5.5 ABOUT POWER
SUPPLY MONITORING
10.13 VOLTAGES
10.14
WAVEFORMS
Communication between the Main CPU and Panel CPU has not been established.
1
Communication
failure between
the microcomputer
DFLB Assy
MAIN Assy
Check the TSCK, TSI, PNL_BUSY, TSO and
MAIN_BUSY waveforms.
If no signal is output, the possible causes are poor
connection, failure in the PANEL CPU (IC1007) or
MAIN CPU (IC103), and startup failure of the
MAIN CPU caused by defective FLASH ROM
(IC101) or SDRAM (IC102).
1
A voltage error
was generated.
— Check the level of the VDET signal.
If the signal level is "L", a voltage error was
generated.
2 Power failure MAIN Assy
Check the V+3R3 and V+1R2 power
voltages.
If power is not output, a part of the power supply
section may be defective.
10.15 EACH
SIGNAL LEVEL
10.15 EACH
SIGNAL LEVEL
No. Cause
Diagnostics Point
Item to be Checked Corrective Action Reference
No. Cause
Diagnostics Point
Item to be Checked Corrective Action Reference
No. Cause
Diagnostics Point
Item to be Checked Corrective Action Reference
No. Cause
Diagnostics Point
Item to be Checked Corrective Action Reference
No. Cause
Diagnostics Point
Item to be Checked Corrective Action Reference
20 21 23 19
24 25 22 19
9 10
B J
A
849 7 10
1 4 3 2
1 4 3 2
A
2 3 4
B
C
D
E
F
24
CDJ-850
1
2 3 4
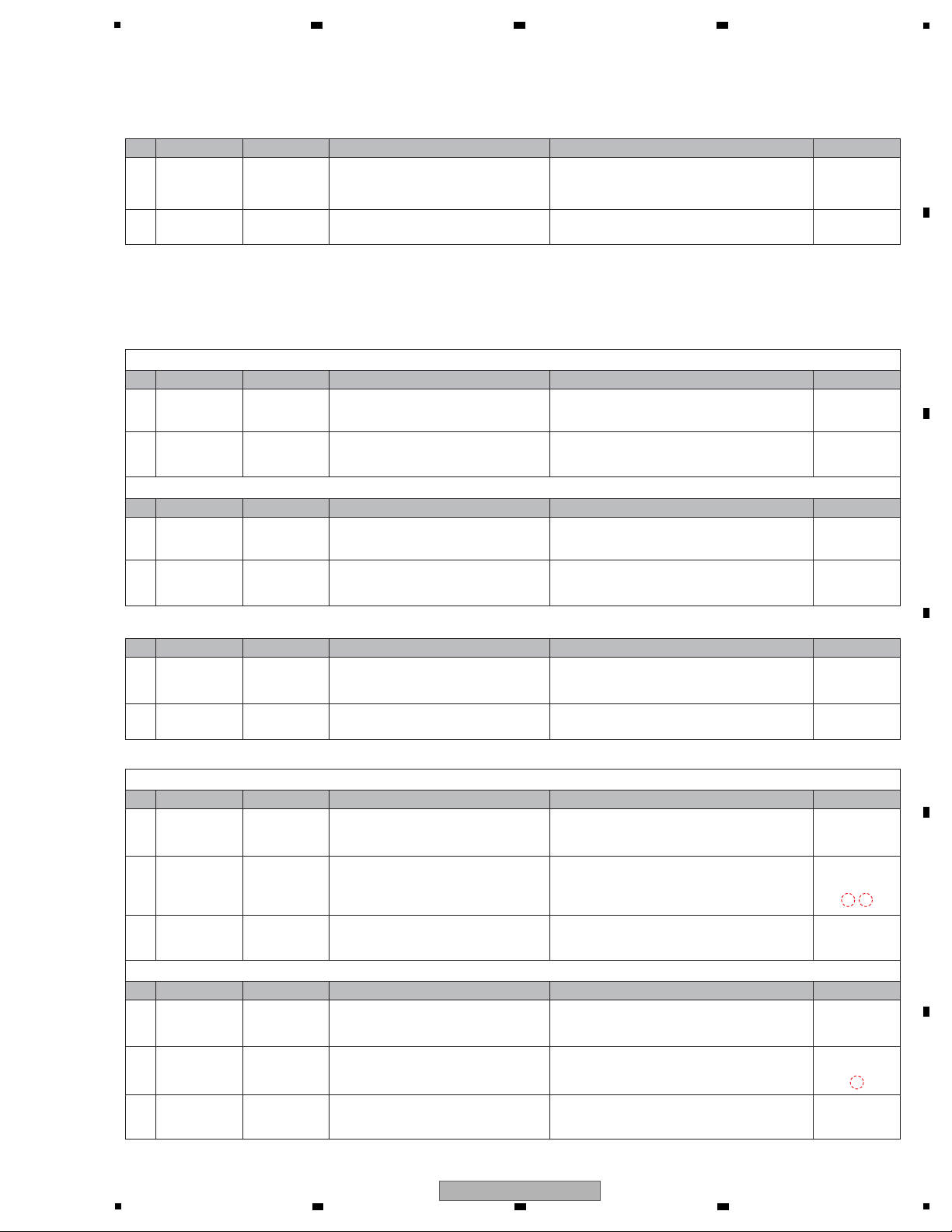
5
[2-3] The LED does not light.
—
[3] Operations (Keys/variable controls/JOG)
As operations of all keys, variable controls, and JOG dial can be checked in Service mode.
[3-1] No key functions
PLAY, CUE, AUTO BEAT LOOP 1-4, BEAT SELECT, REV, LOOP IN/OUT, RELOOP, or USB STOP key does not function.
1
Loose connection
/Defective SW
Related point
Check if there is loose connection on the
signal line from the PANEL CPU (IC1007)
up to the SW.
If there is no loose connection and if the signal does
not become "L" when the SW is pressed, that SW is
defective.
2
Defective PANEL
CPU (IC1007)
DFLB Assy
If the symptom persists after the above
corrections,
Check a mounting state of PANEL CPU (IC1007).
If the mounting is OK, the IC1007 may be defective.
The signals from other keys are analog and connected to multiple switches.
1
Loose connection
/Defective SW
Related point
Check if there is loose connection on the
signal line from the PANEL CPU (IC1007)
up to the SW.
If the SWs connected to the signal line function
properly and if the connections are properly made,
the SWs may be defective.
2
Defective PANEL
CPU (IC1007)
DFLB Assy
If the symptom persists after the above
corrections,
Check a mounting state of PANEL CPU (IC1007).
If the mounting is OK, the IC1007 may be defective.
[3-2] Rotary selector not controllable
1
Defective rotary
selector
DFLB Assy
Check if the signals from the RENC_1, RENC
_2, and RENC_SW signal lines are normal
when the rotary selector is turned or pressed.
If the signals are not normal, check the connections of
the signal lines. If the connections are properly made,
the Rotary selector (S1018) may be defective. Replace it.
2
Defective PANEL
CPU (IC1007)
DFLB Assy
If the symptom persists after the above
corrections,
Check a mounting state of PANEL CPU (IC1007).
If the mounting is OK, the IC1007 may be defective.
[3-3] Variable controls not controllable
Tempo slider not controllable
1
Loose
connection
DFLB Assy
SLD1 Assy
SLD2 Assy
Check if there is loose connection on the
signal line from the PANEL CPU (IC1007)
to the tempo slider (VR1501).
If the connections of signal line are improper,
resolder it.
2
Defective tempo
slider
DFLB Assy
SLD2 Assy
Check the ADCT and ADIN signals level.
If the voltage of the ADCT signal (IC1007-pin 1) is not
1.65 V, or the voltage of the ADIN signal (IC1007-pin 2)
does not change between 3.3 V and 0 V, the Tempo
slider (VR1501) may be defective.
3
Defective PANEL
CPU (IC1007)
DFLB Assy
If the symptom persists after the above
corrections,
Check a mounting state of PANEL CPU (IC1007).
If the mounting is OK, the IC1007 may be defective.
1 Signal errors DFLB Assy
Check that the control signal for the LED
is output from the PANEL CPU (IC1007).
If no signal is output, check a mounting state of
PA NEL CPU(IC1007). If the mounting is OK, the
IC1007 may be defective.
[10] Basic operation
check of CPU/DSP
[10] Basic operation
check of CPU/DSP
—
—
[10] Basic operation
check of CPU/DSP
[10] Basic operation
check of CPU/DSP
[10] Basic operation
check of CPU/DSP
2 Defective parts DFLB Assy
Check that the voltage (2.2 V) is present
at both ends of the LED.
If the voltage is abnormal, the LED, transistor or
peripheral resistors may be defective.
10.15 EACH
SIGNAL LEVEL
10.15 EACH
SIGNAL LEVEL
10.15 EACH
SIGNAL LEVEL
VINYL SPEED ADJUST not controllable
1
Loose
connection
DFLB Assy
SLD1 Assy
Check if there is loose connection on the
signal line from the PANEL CPU (IC1007) to
the VINYL SPEED ADJUST VR (VR1301).
If the connections of signal line are improper,
resolder it.
2
Defective
variable
controls
DFLB Assy
SLD1 Assy
Check the TCH/REL signal level.
If the voltage of the TCH/REL signal line (IC1007-pin 88)
does not change between 3.3 V and 0 V, the VINYL
SPEED ADJUST VR (VR1301) may be defective.
3
Defective PANEL
CPU (IC1007)
DFLB Assy
If the symptom persists after the above
corrections,
Check a mounting state of PANEL CPU (IC1007).
If the mounting is OK, the IC1007 may be defective.
—
[10] Basic operation
check of CPU/DSP
10.15 EACH
SIGNAL LEVEL
No. Cause
Diagnostics Point
Item to be Checked Corrective Action Reference
No. Cause
Diagnostics Point
Item to be Checked Corrective Action Reference
No. Cause
Diagnostics Point
Item to be Checked Corrective Action Reference
No. Cause
Diagnostics Point
Item to be Checked Corrective Action Reference
No. Cause
Diagnostics Point
Item to be Checked Corrective Action Reference
No. Cause
Diagnostics Point
Item to be Checked Corrective Action Reference
E
C D
6 7 8
A
B
C
D
E
5
6 7 8
CDJ-850
F
25
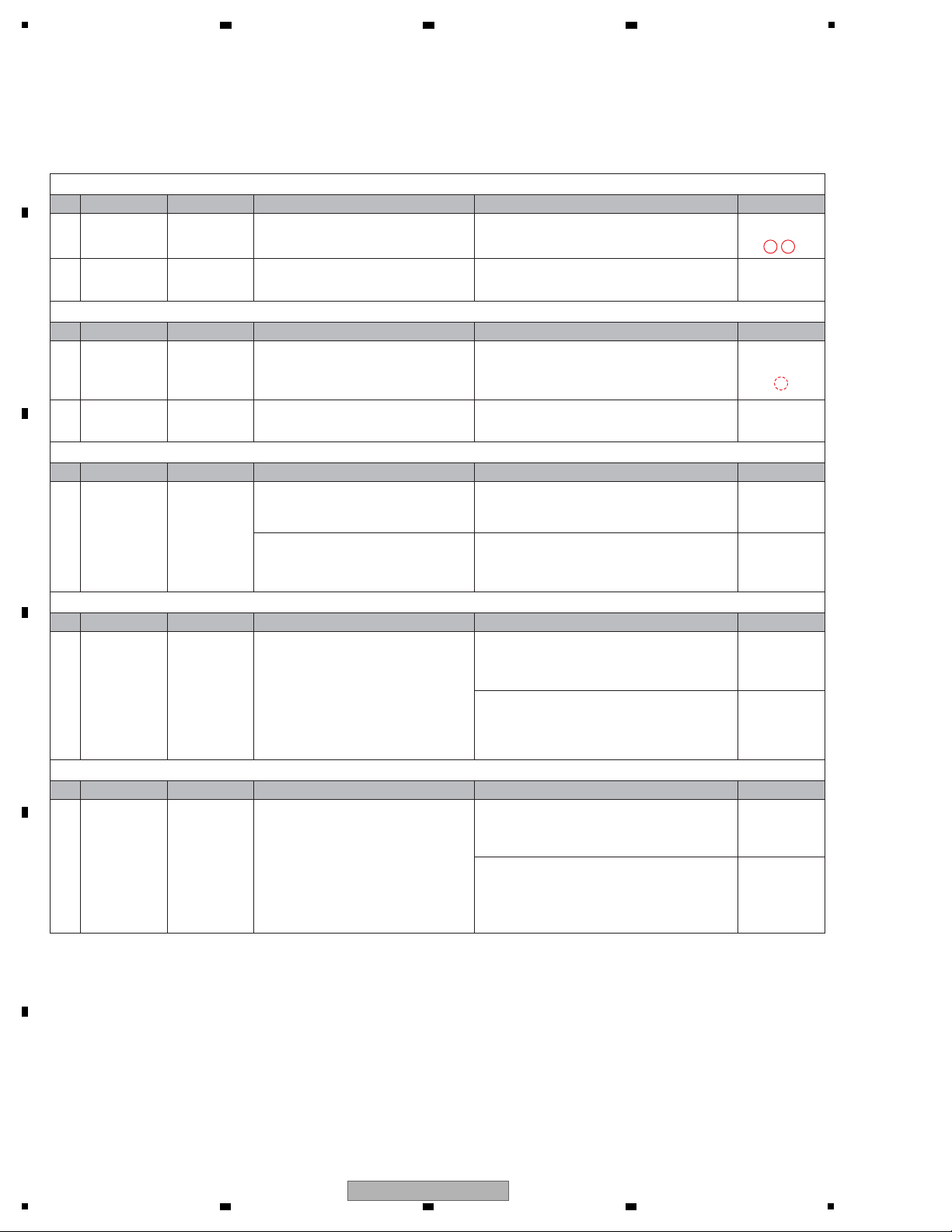
1
—
—
—
[10] Basic operation
check of CPU/DSP
[3-4] Abnormalities regarding the JOG dial
After the JOG Assy is disassembled then reassembled, be sure to check that the load value for the JOG dial is within the
specified range. (Refer to the "8.4 JOG DIAL ROTATION LOAD ADJUSTMENT".)
Turning of the JOG dial is not detected
1
Defective part of
photo interrupter
DFLB Assy
JFLB Assy
JOGB Assy
Check the waveforms of signal lines.
JOG1_C (IC1007-pin 26)
JOG2_C (IC1007-pin 25)
If no waveform can be confirmed, the photo
interrupter (PC1901) may be defective.
10.14
WAVEFORMS
2
Defective PANEL
CPU (IC1007)
DFLB Assy
If the symptom persists after the above
corrections,
Check a mounting state of PANEL CPU (IC1007).
If the mounting is OK, the IC1007 may be defective.
Pressing on the JOG dial cannot be detected.
1
Defective part
DFLB Assy
JFLB Assy
Check the level of JOG_SW signal (IC1007
-pin 27) when the JOG dial is pressed.
If the JOG_SW signal (IC1007-pin 27) is not set to
"L" when the JOG dial is pressed and it is not set to
"H" when the JOG dial is not pressed, the SHEET
SW(DSX1078) may be defective.
2
Defective PANEL
CPU (IC1007)
DFLB Assy
If the symptom persists after the above
corrections,
Check a mounting state of PANEL CPU (IC1007).
If the mounting is OK, the IC1007 may be defective.
Noise is heard when the JOG dial is turned.
1
Defective
attachment of
the JOG FL.
Defective gear
or JOG DIAL B.
JFLB Assy
JOGB Assy
Check if the JOG FL of the JFLB Assy has been
shifted upward from the holder.
Also check the JOGB Assy is attached normally.
The JOG FL may interfere with JOG A.
There may be any scratches on the 3
gears or some foreign object between
the gears.
If there are any scratches, replace the scratched gear
with a new one. If there is any foreign object, remove
it then replace the gears with new ones.
Gears to be replaced: Load gear, Gear A, Gear B
The JOG dial turns too freely. (The load value for the JOG dial is outside the specified range.)
1
Improper adjustment or assembly
of the JOG dial
JOG Assy
Check that the load value for the JOG dial
is within the specified range, referring to
“Measuring method” in “8.4 JOG Dial
Rotation Load Adjustment.”
If it is outside the specified range, adjust the position
of the Adjust Plate to change the load value for the
JOG dial, referring to “Load adjustment method” in
“8.4 JOG Dial Rotation Load Adjustment.”
8.4 JOG Dial
Rotation Load
Adjustment.
8.4 JOG Dial
Rotation Load
Adjustment.
During the above adjustment, if the upper-limit adjustment position of the Adjust Plate is reached, oil may
have been spattered on the Cam Plate.
Replace the washer, load gear, and cam plate with
new ones, then reassemble.
Resistance to turning the JOG dial is too strong. (The load value for the JOG dial is outside the specified range.)
1
Improper adjustment of the JOG
dial or defective
washer, gear, or
cam plate
JOG Assy
Check that the load value for the JOG dial
is within the specified range, referring to
“Measuring method” in “8.4 JOG Dial
Rotation Load Adjustment.”
If it is outside the specified range, adjust the position
of the Adjust Plate to change the load value for the
JOG dial, referring to “Load adjustment method” in
“8.4 JOG Dial Rotation Load Adjustment.”
8.4 JOG Dial
Rotation Load
Adjustment.
8.4 JOG Dial
Rotation Load
Adjustment.
During the above adjustment, if the lower-limit adjustment position of the
Adjust
Plate is reached, shavings
from the worn-out washer may have increased the
friction. Replace the washer, load gear, and cam plate
with new ones, then reassemble.
10.15 EACH
SIGNAL LEVEL
No. Cause
Diagnostics Point
Item to be Checked Corrective Action Reference
No. Cause
Diagnostics Point
Item to be Checked Corrective Action Reference
No. Cause
Diagnostics Point
Item to be Checked Corrective Action Reference
No. Cause
Diagnostics Point
Item to be Checked Corrective Action Reference
No. Cause
Diagnostics Point
Item to be Checked Corrective Action Reference
F
5 6
A
2 3 4
B
C
D
E
F
26
1
2 3 4
CDJ-850
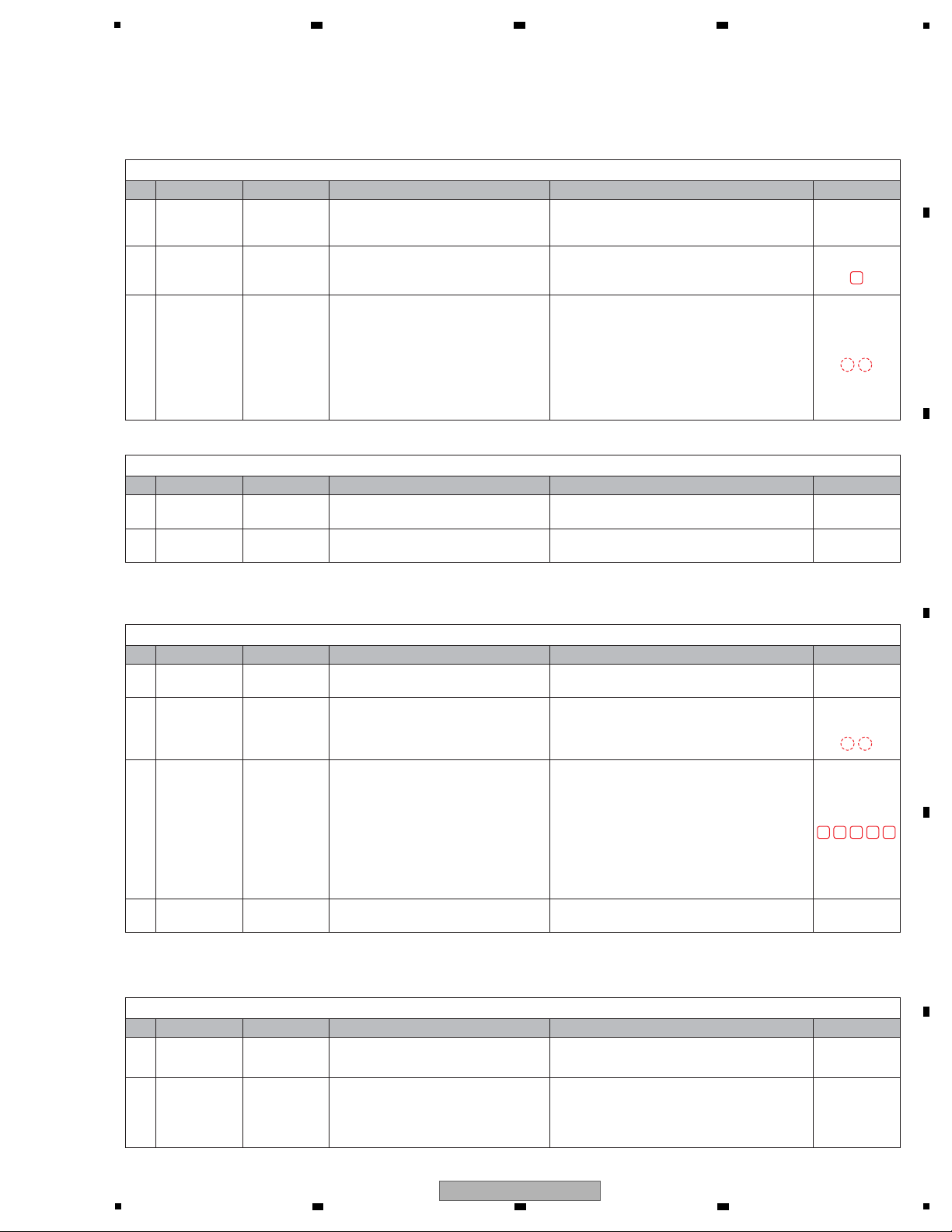
5
[5] AUDIO OUT
The analog audio signal is not output.
Improper fader operation after fader start.
3 Power failure MAIN Assy
Check the voltages for audio (V+10_A,
V-AUDIO(V-10_A), V+5_A, V+3R3_A,
V+1R25).
Check also if the protector (P2003) is
broken.
• If the V+10_A voltage level is abnormal, Q2028
and its peripheral parts may be defective.
• If the V-AUDIO(V-10_A) voltage level is abnormal,
Q2031 and its peripheral parts may be defective.
• If the V-5_A voltage level is abnormal, IC406
and its peripheral parts may be defective.
• If the V+3R3_A voltage level is abnormal, IC402
and its peripheral parts may be defective.
• If the V+1R25 voltage level is abnormal, IC403
and its peripheral parts may be defective.
1
Loose
connections
MAIN Assy
CMPX Assy
Check the connection of the audio signal
lines (ROUT/LOUT).
If connection is improper, resolder it.
2
MUTE signal
error
MAIN Assy
DFLB Assy
CMPX Assy
Check the AMUTE signal.
"L" (release mute) at normal playback.
Check the MAIN_XMUTE signal.
"H" (release mute) at normal playback.
If the signal is abnormal, loose connection and mute
circuit may be defective.
—
—
—
—
4
Signal error
Defective part
MAIN Assy
Check the AUDIO DSP (IC301) and AUDIO
DAC (IC302).
AUDIO DSP (IC301), AUDIO DAC (IC302) and its
peripheral parts may be defective.
[6] CONTROL
1
Loose
connections
MAIN Assy
CMPX Assy
Check the connection of the control signal
lines (CONT1/CONT2).
If connection is improper, resolder it.
2
Signal error
Defective part
MAIN Assy
Check the waveform of the control signal
lines (CONT1/CONT2).
If the input signal cannot be recognized at input pin
of MAIN CPU (IC101), the signal line or the
peripheral devices may be defective.
If the input signal can be recognized, the MAIN
CPU (IC103) may be defective.
10.14
WAVEFORMS
—
[10] Basic operation
check of CPU/DSP
[10] Basic operation
check of CPU/DSP
10.15 EACH
SIGNAL LEVEL
10.13 VOLTAGES
10.13 VOLTAGES
[4] USB (USB-Type A), PC (USB-Type B)
[4-1] USB (USB-Type A)
Check the following, with a USB device connected to the USB-Type A connector.
1
Loose
connections
USBA Assy
CMPX Assy
MAIN Assy
Check the connections of the USBA_D_P/N
communication line, USB_VBUSON and
USB_CODETFLG signal lines.
If connection is improper, resolder it.
2
USB VBUS is
defective.
USBA Assy
CMPX Assy
Check the voltage level of V+5_USB
(JA2201-pin 1 and IC2002-pin 3) of USB
power supply.
If the voltage of IC2002-pin 3 is abnormal, IC2002
may be defective.
If the voltage of JA2201-pin 1 is abnormal, go to [3].
3 Defective part CMPX Assy
Check the signal level of USB_CODETFLG
(IC2003-pin 5) and USB_VBUSON(IC504pin 4).
• If the USB_VBUSON(IC504-pin 4) is not "H", MAIN
CPU(IC103) may be defective.
• If the USB_VBUSON(IC504-pin 4) and USB_
CODETFLG(IC2003-pin 5) are "H", IC2003 may be
defective.
• If the USB_VBUSON(IC504-pin 4) is "H" and USB_
CODETFLG(IC2003-pin 5) is "L", USB power
supply may be short-circuited in the ground or
IC2003 may be defective.
Defective part
[4-2] PC (USB-Type B) does not work
Check the following, with a USB device connected to the USB-Type B connector.
1
Loose
connections
Check the connections of the USBB_D_P/N
communication line and VBUS_B signal line.
If connection is improper, resolder it.
2
If the symptom persists after the above
corrections,
The MAIN CPU (IC103) may be defective.
10.15 EACH
SIGNAL LEVEL
10.15 EACH
SIGNAL LEVEL
No. Cause
Diagnostics Point
Item to be Checked Corrective Action Reference
No. Cause
Diagnostics Point
Item to be Checked Corrective Action Reference
No. Cause
Diagnostics Point
Item to be Checked Corrective Action Reference
No. Cause
Diagnostics Point
Item to be Checked Corrective Action Reference
5 6 16
11 12
7
L K
H I
6 7 8
A
B
C
D
E
5
6 7 8
CDJ-850
F
27
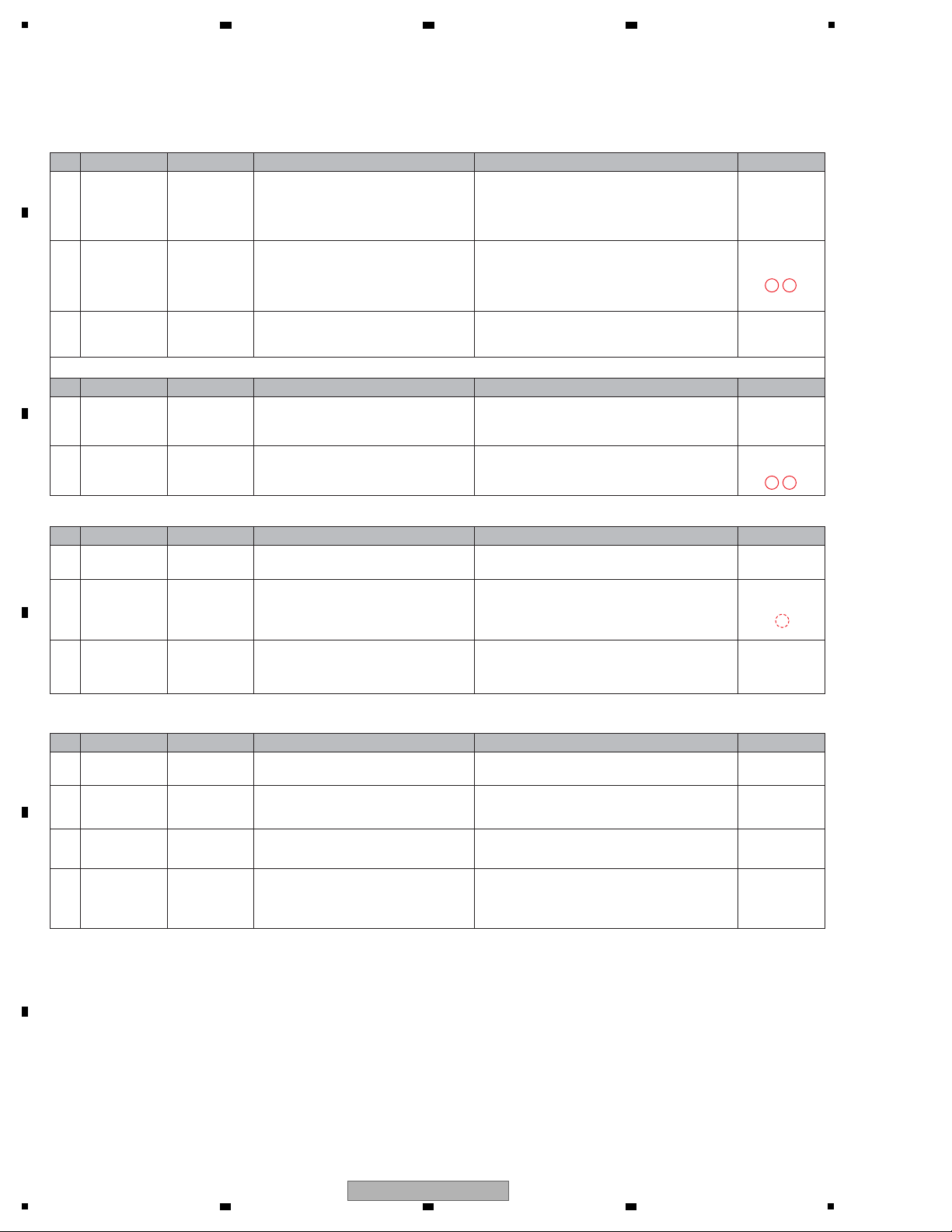
1
[7] DRIVE ASSY
[7-1] Improper operation of the loading mechanism
1
Loose
connections
Cables
MAIN Assy
JINT Assy
SLMB Assy
Check the connection of the motor-drive signal
line LO±. Check that the wires between the
loading motor (DC motor) and the SLMB Assy
are securely soldered. Check also the wires
are not broken.
If soldering is improper, resolder it.
If the wires are broken, replace them.
2 Signal errors
MAIN Assy
JINT Assy
SLMB Assy
Check the connections and waveforms of the
LPS1 and LPS2 signal lines. In the normal state,
the LPS1 and LPS2 signals becomes "L" when
the loading detection SWs(S1701 and S1702)
are set to ON.
If the signal waveform is not proper, loose connection
and the loading detection SWs (S1701 and S1702)
may be improperly soldered or defective.
4.3 POWER SUPPLY
BLOCK DIAGRAM
3 Power failure MAIN Assy
Check the power voltages.
V+7R6_M, V+5R6_M, VREF1R65,
V+3R3_B, V+3R3, V+1R2A
For any power-supply section that does not output
the voltage, check the mounting statuses of the
regulator IC and its peripheral parts.
—
No loading (There is an abnormal noise.)
1
Improper
assembling
Slotin Mecha
Assy
SLMB Assy
Check if the SW lever has shifted on the
loading detection SWs (S1701 and S1702)
on the SLMB Assy.
If assembling is improper, resolder it.
2
Loose
connections
Signal errors
MAIN Assy
JINT Assy
SLMB Assy
Check the waveforms on the LPS1 and
LPS2 signal lines.
If the signal waveform is not proper, loose connection
and the loading detection SWs (S1701 and S1702)
may be improperly soldered or defective.
[7-2] The stepper does not work.
3 Power failure MAIN Assy
Check the power voltages.
V+7R6_M, V+5R6_M, VREF1R65,
V+3R3_B, V+3R3, V+1R2A
For any power-supply section that does not output
the voltage, check the mounting statuses of the
regulator IC and its peripheral parts. Replace it.
4.3 POWER SUPPLY
BLOCK DIAGRAM
2 Signal errors MAIN Assy
Check the waveform of INSW (INSIDE)
signal.
In the normal state,
The INSIDE SW of
TM Assy-S (Traverse mecha) becomes "L"
when the INSIDE SW is set to ON.
If the signal is not proper, check the connections.
If connections are properly made, replace the
TM Assy-S (traverse mecha).
[7-3] No CD playback
2
Any foreign
matter attached
TM Assy-S
(Traverse mecha)
Check if any foreign matter, such as
shavings, dirt, or dust, is attached to the
lens of the Pickup Assy.
Clean a lens.
3 Defective pickup MAIN Assy
Check the LD current value.
Measure the actuator resistance value.
Refer to the “5.3 Diagnosis of the Pickup Assy.”
5.3 Diagnosis of
the Pickup Assy
4 — Service mode
If the symptom persists after the above
corrections, check operations of the CD
drive in Service mode.
Check operations of the CD drive, referring to the
procedures described in “6. SERVICE MODE.”
If the CD drive functions improperly,
see “[8] SERVICE MODE” in this section.
6. Service mode
—
1
Loose
connections
MAIN Assy
JINT Assy
Check the connection of the stepping-motor
drive signal line ST1± and ST2±.
If connection is improper, resolder it.
—
—
1 Shor t switch CNCT Assy
Short switch S2501 is in the off (open)
state.
In the normal operation, turn the short switch to
off (open).
—
10.14
WAVEFORMS
10.14
WAVEFORMS
10.15 EACH
SIGNAL LEVEL
No. Cause
Diagnostics Point
Item to be Checked Corrective Action Reference
No. Cause
Diagnostics Point
Item to be Checked Corrective Action Reference
No. Cause
Diagnostics Point
Item to be Checked Corrective Action Reference
No. Cause
Diagnostics Point
Item to be Checked Corrective Action Reference
O
11 12
11 12
A
2 3 4
B
C
D
E
F
28
1
2 3 4
CDJ-850
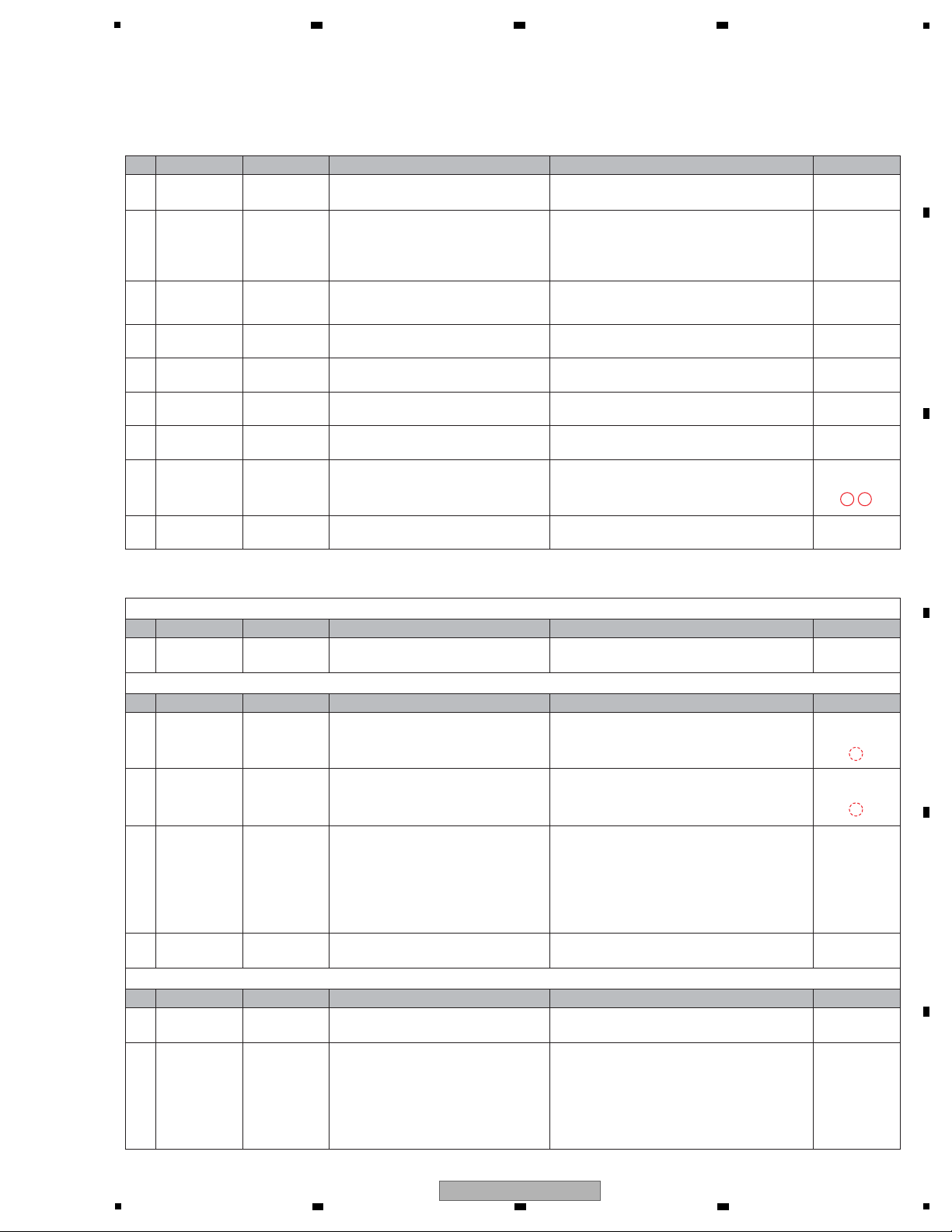
5
[8] SERVICE MODE
[8-1] The measured error rate is outside the specified range in Player Operation mode.
1
Scratches or
dirt on the disc
DISC
Check if the recording surface of the disc is
dirty.
If it is clearly dirty, replace it with a disc of good
condition.
2
Scratches or
dirt on the disc
DISC
Measure the error rate, using the same disc
that produced the bad error rate but using
the addresses in a different area.
If the error rate measured in a different area is OK,
the disc is defective. Replace the disc with one in
good condition.
If no error rate measured in various areas throughout
the entire surface of the CD is OK, go to [3].
3
Any foreign
matter attached
TM Assy-S
(Traverse mecha)
TM Assy-S
(Traverse mecha)
TM Assy-S
(Traverse mecha)
TM Assy-S
(Traverse mecha)
Check if any foreign matter, such as
shavings, dirt, or dust, is attached to the
lens of the Pickup Assy.
Clean the lens.
4
Improper
assembly
Check that the TM Assy-S (traverse mecha)
has been securely installed.
If it has not, reinstall it properly.
5
Improper
assembly
Slotin Mecha
Check that the loading mechanism Assy
has been securely installed.
If it has not, reinstall it properly.
6
Any foreign
matter attached
Check for any foreign matter on the spindle
table.
Remove any foreign matter.
7
Any foreign
matter attached
Slotin Mecha
Check if any foreign matter is attached to
the magnet portion of the clamper.
Remove any foreign matter.
8 Signal errors MAIN Assy
Check that the waveforms of the RFO and
AGCRF signals form clear eye patterns.
If their waveforms are not of the same quality, check
the mounting status of the Servo IC (IC201).
If it is correctly mounted, then it may be defective.
Replace it.
10.14
WAVEFORMS
9 Defective pickup
If the symptom persists after the above
corrections,
See “5.3 Diagnosisi of the Pickup Assy” for details.
5.3 Diagnosis of
the Pickup Assy
—
—
—
—
—
—
—
3 Power failure MAIN Assy
Check the power voltages.
(V+7R6_M, V+5R6_M, VREF1R65,
V+3R3_S)
Check the mounting statuses of the regulator IC of
the power-supply section that produces that voltage
and its peripheral parts. If they are properly mounted,
then the parts may be defective.
VREF1R65 is produced at the Servo IC (IC201).
If this voltage is not output, check the mounting
status of the IC201. If it is properly mounted, then the
part may be defective.
4.3 POWER SUPPLY
BLOCK DIAGRAM
4 Defective parts
If the symptom persists after the above
corrections,
DRIVER IC(IC204) may be defective.
In-focus not possible
1 Defective pickup MAIN Assy
Check the LD current and measure the
resistance value of the actuator.
Refer to the “5.3 Diagnosis of the Pickup Assy.”
5.3 Diagnosis of
the Pickup Assy
2 Power failure MAIN Assy
Check the power voltages.
(V+7R6_M, V+5R6_M, VREF1R65,
V+3R3_S)
Check the mounting statuses of the regulator IC of
the power-supply section that produces that voltage
and its peripheral parts. If they are properly mounted,
then the parts may be defective.
VREF1R65 is produced at the Servo IC (IC201).
If this voltage is not output, check the mounting
status of the IC201. If it is properly mounted, then the
part may be defective.
4.3 POWER SUPPLY
BLOCK DIAGRAM
[8-2] The drive does not work during Test Operation mode.
The LD does not emit light.
1 Defective pickup
Check the LD current and measure the
resistance value of the actuator.
See “5.3 Diagnosis of the Pickup Assy” for details.
5.3 Diagnosis of
the Pickup Assy
The spindle motor does not rotate.
1 Signal errors MAIN Assy
Check that the DRVMUTE1 and 2 signal
becomes H after loading is completed.
If the signal is not normal, check the mounting
statuses of the DRIVER IC (IC204) and MAIN CPU
(IC103) terminals. If they are properly mounted, then
the IC103 may be defective.
2 Signal errors MAIN Assy
Check a SPIN signal.
In the normal, 1.65 V at the center.
The voltage in the start-up acceleration is
around 3 V.
If the signal is not normal, check the mounting
statuses of the DRIVER IC (IC204) and Servo CPU
(IC201) terminals. If they are properly mounted, then
the IC204 and IC201 may be defective.
—
—
—
10.15 EACH
SIGNAL LEVEL
10.15 EACH
SIGNAL LEVEL
No. Cause
Diagnostics Point
Item to be Checked Corrective Action Reference
No. Cause
Diagnostics Point
Item to be Checked Corrective Action Reference
No. Cause
Diagnostics Point
Item to be Checked Corrective Action Reference
No. Cause
Diagnostics Point
Item to be Checked Corrective Action Reference
S
T
13 14
6 7 8
A
B
C
5
6 7 8
CDJ-850
D
E
F
29
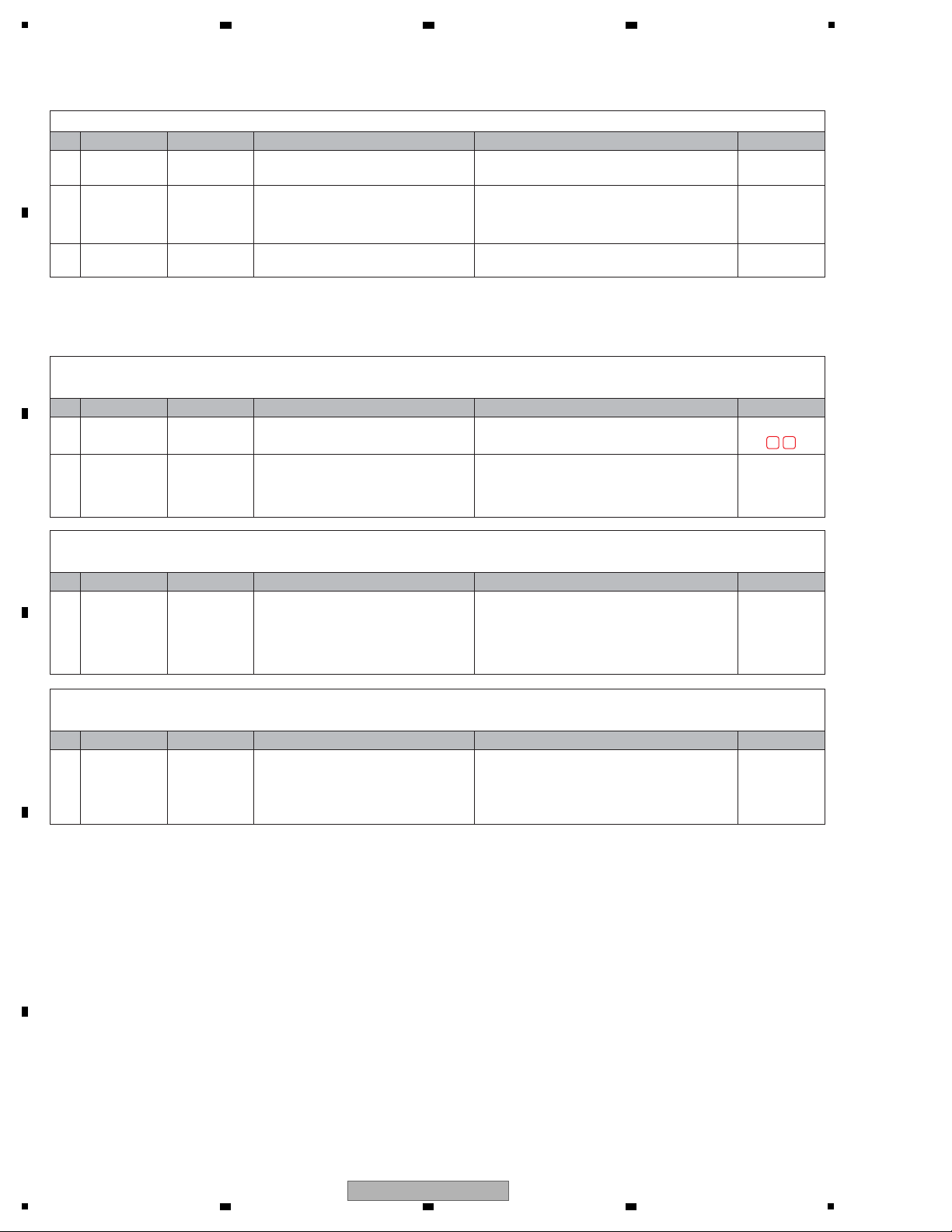
1
[10] Basic operation
check of CPU/DSP
10.13 VOLTAGES
[9] Error Codes
How to respond when an error code is displayed on the FL DISPLAY is described below.
The MAIN CPU cannot write in a program to the AUDIO DSP at start-up.
[9-1] E-6002: COMMUNICATION ERROR
1 Power failure MAIN Assy
Check the power voltages for Audio DSP.
(V+3R3_A, V+1R25)
If the voltage level is abnormal, IC402 or IC403
may be defective.
2 Defective part MAIN Assy
Check if the AUDIO DSP (IC301) is
operating.
If the AUDIO DSP (IC301) is not operating, AUDIO
DSP (IC301) and its peripheral parts may be defective.
If the AUDIO DSP (IC301) is operating, the MAIN
CPU (IC103) and its peripheral parts may be defective.
[8] SERVICE
MODE
[9-2] E-7201: TOC READ ERROR
TOC data cannot be read from a disc.
1
TM Assy-S
(Traverse mecha)
Measure the error rate in Player Operation
mode of Service mode in order to distinguish
whether the cause is attributable to the disc
or to the player. For measurement, play back
the reading point at which reading resulted in
an error, by listening to the sound.
See [8] SERVICE MODE for details.
1 Defective pickup MAIN Assy
Check the LD current and measure the
resistance value of the actuator.
Refer to the “5.3 Diagnosis of the Pickup Assy.”
5.3 Diagnosis of
the Pickup Assy
2 Power failure MAIN Assy
Check the power voltages.
(V+7R6_M, V+5R6_M, VREF1R65,
V+3R3_S)
For any power-supply section that does not output
the voltage, check the mounting statuses of the
regulator IC and its peripheral parts. If they are
properly mounted, then the parts may be defective.
4.3 POWER SUPPLY
BLOCK DIAGRAM
No tracking close
3—
TM Assy-S
(Traverse mecha)
Check that focusing is in. (If focusing is out,
tracking close is not possible.)
See “In-focus not possible” above.
—
—
[1-3] “E-8709” is
displayed on the
DATA FL display
after startup
[9-3] E-8709: COMMUNICATION ERROR
Communication between the PANEL CPU (IC1007) and MAIN CPU (IC103) is not possible.
1
DFLB Assy
MAIN Assy
Check the waveforms of TSCK, TSI,
PNL_BUSY, TSO, and MAIN_BUSY,
check the voltages of V+3R3 and V+1R2.
See “[1-3] “E-8709” is displayed on the DATA FL
display after startup“ for details.
—
No. Cause
Diagnostics Point
Item to be Checked Corrective Action Reference
No. Cause
Diagnostics Point
Item to be Checked Corrective Action Reference
No. Cause
Diagnostics Point
Item to be Checked Corrective Action Reference
No. Cause
Diagnostics Point
Item to be Checked Corrective Action Reference
11 12
A
2 3 4
B
C
D
E
F
30
1
2 3 4
CDJ-850