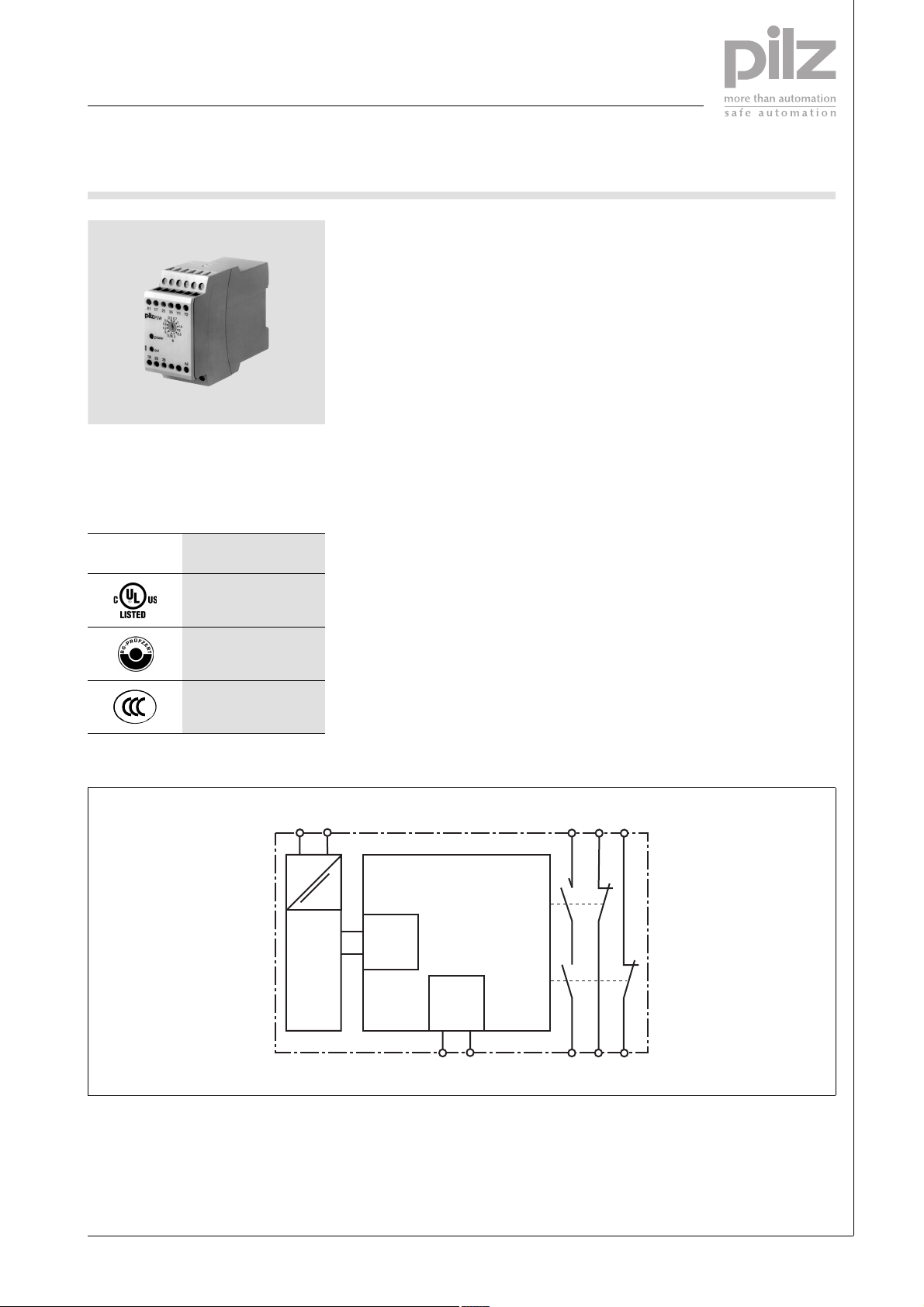
Safe timer relays
Pulsing
PZW
Pulse-on timer relay for step-by-step
control of movement sequences
Approvals
PZW
Unit features
` Positive-guided relay outputs:
– 1 safety contact, pulsing
– 2 auxiliary contacts, pulsing
` LED indicator for:
– Supply voltage
–Pulse time
` Redundant output circuit
` 12 pulse times, set via rotary switch
` Feedback loop for monitoring ex-
ternal contacts
Unit description
The unit operates as a pulse relay
` in accordance with EN 292 Part 2,
clause 3.7.10 and 4.1.4 and EN 292
Part 1, clause 3.23.8 (inching circuit
for limit movement of hazardous
machine components during installation, set up and positioning)
` in safety circuits in accordance with
VDE 0113 and EN 60204-1 (e.g. on
movable guards)
The unit is designed for use with
` A safety relay from the PNOZ series
` Safety gate monitors from the PST
series
` Two-hand relays from the P2HZ se-
ries
The category that can be achieved in
accordance with EN 954-1 depends
on the category of the base unit. The
PZW may not exceed this.
Safety features
The relay meets the following safety
requirements:
` The circuit is redundant in design
` The safety function remains effec-
tive in the case of a component fail-
ure.
` The correct opening and closing of
the safety function relays is tested
automatically in each on-off cycle.
Block diagram
A1 A2
~
Power
=
Input
Feed-
back
Y1 Y2
K1
K2
17
18
25 35
26
36
Pilz GmbH & Co. KG, Sichere Automation, Felix-Wankel-Straße 2, 73760 Ostfildern, Germany
Telephone: +49 711 3409-0, Telefax: +49 711 3409-133, E-Mail: pilz.gmbh@pilz.de
NSG-D-2-085-2006-10
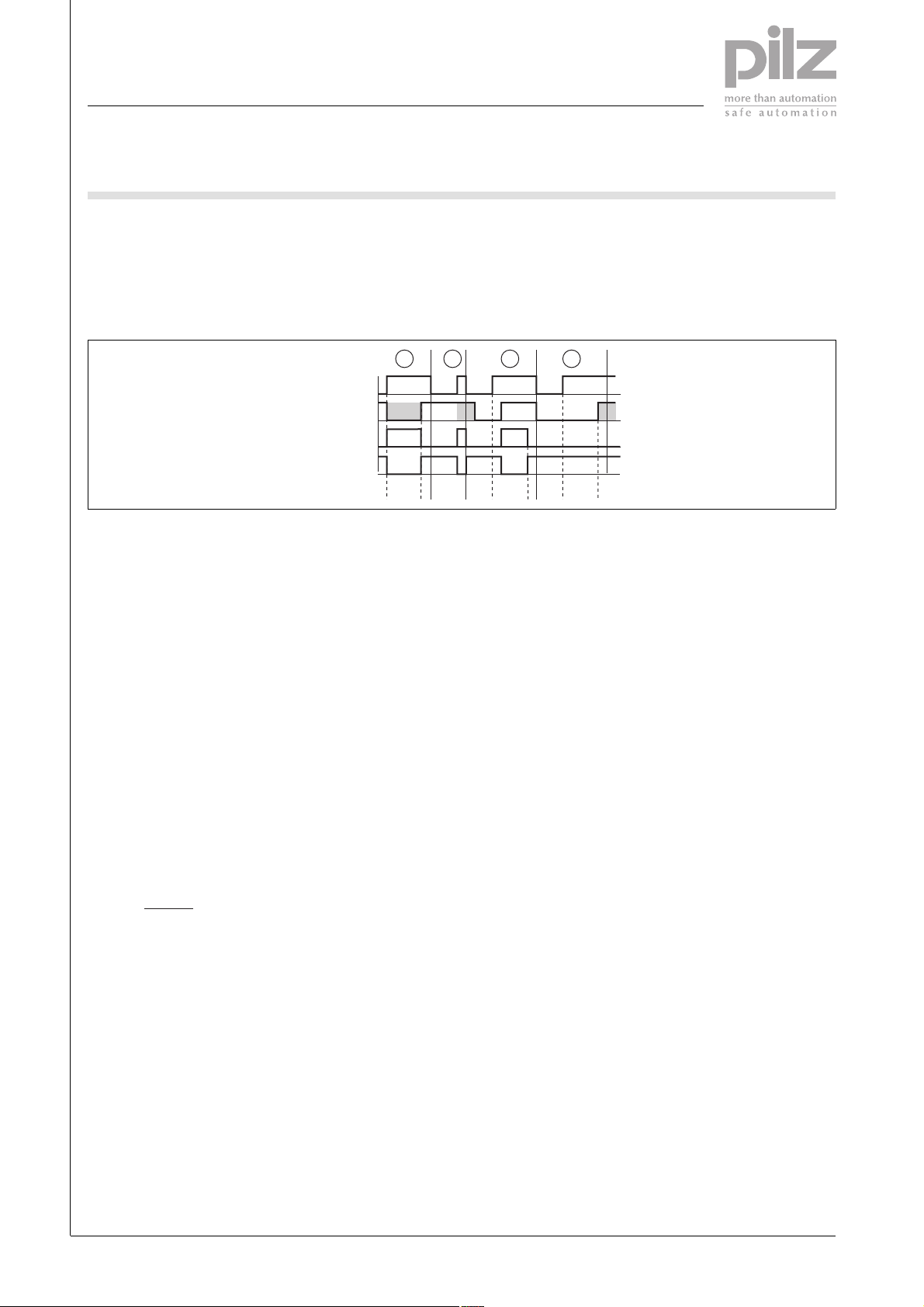
Safe timer relays
Pulsing
PZW
Function description
The time is ready to start once the
feedback loop is closed. If the supply
Timing diagram
Output safe
Output aux
Key
` Input: Input circuitA1-A2
` Feedback: Feedback loop Y1-Y2
` Output safe: Safety contact17-18
: Pulse time
` t
w
Wiring
Please note:
` Information given in the “Technical
details” must be followed.
` Output 17-18 is a safety contact,
outputs 25-26, 35-36 are auxiliary
contacts (e.g. for display)
` To prevent contact welding, a fuse
should be connected before the
output contacts (see technical details).
` Do not use the unlabelled terminals!
` Calculation of the max. cabling runs
in the input circuit:
l
max
R
lmax
=
I
max
Rl / km
= max. overall cable resist-
R
lmax
ance (see technical details)
= cable resistance/km
R
l / km
` Use copper wire that can withstand
60/75 °C.
` Supply voltage 24 VDC: Shorts be-
tween the input circuit and feedback loop or earth faults in the
feedback loop can damage the unit.
` We recommend the use of a short
circuit-proof voltage supply with
current limitation
voltage at the input circuit is interrupted, the safety contact will open. If the
input circuit is closed, i.e. supply voltage is present, the safety contact will
1 2 3
Input
Feedback
tw
w tw
t
c: Normal operating cycle
d: Fault: Input circuit opened too early
e: Fault: Feedback loop closed too
late within t
w
be closed immediately. The safety
contact will be closed again once the
set pulse time has elapsed.
4
f: Fault: Feedback loop closed too
late after t
elapsed
w
Telephone: +49 711 3409-0, Telefax: +49 711 3409-133, E-Mail: pilz.gmbh@pilz.de
NSG-D-2-085-2006-10Pilz GmbH & Co. KG, Sichere Automation, Felix-Wankel-Straße 2, 73760 Ostfildern, Germany
-2
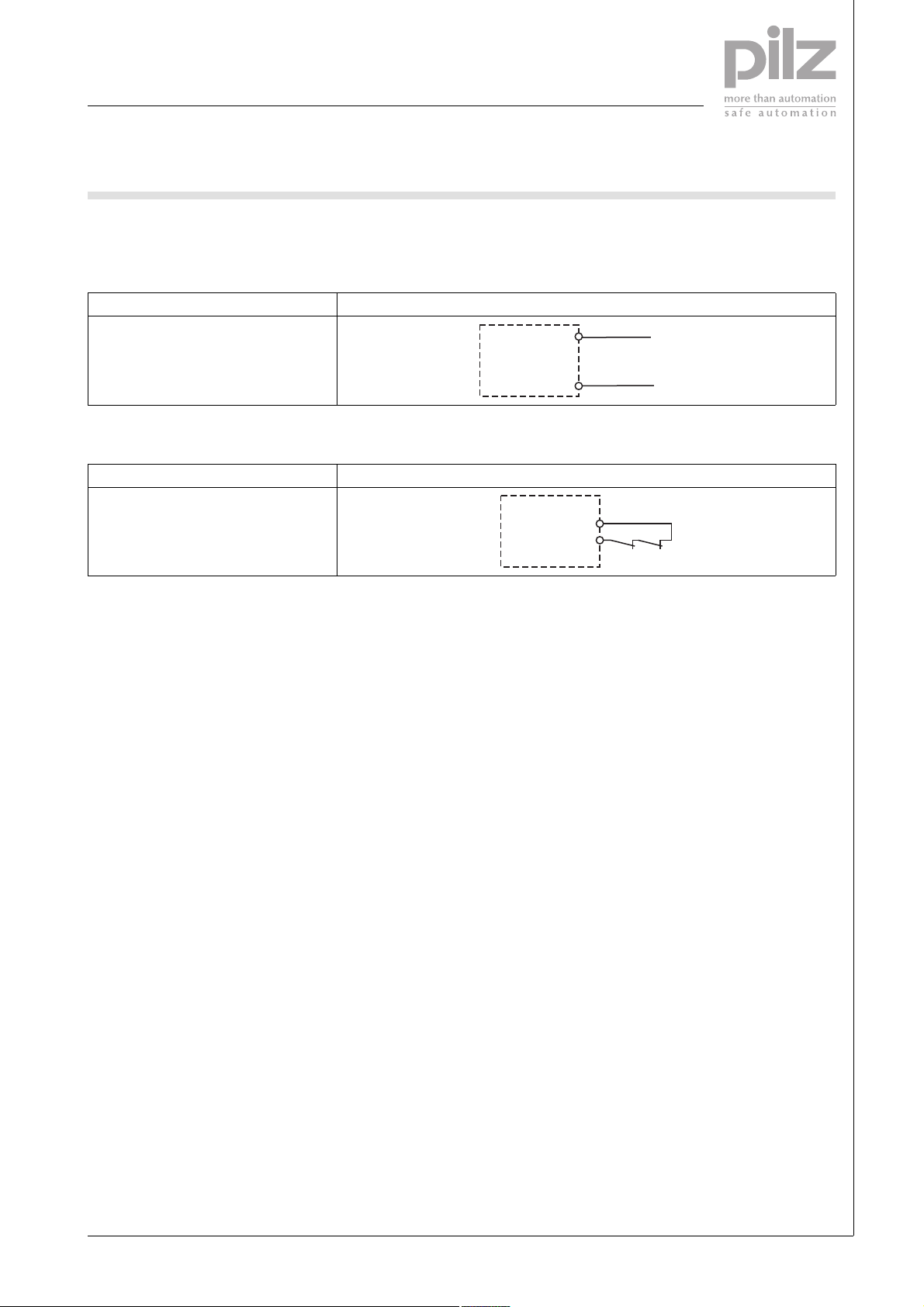
Safe timer relays
Pulsing
PZW
Preparing for Operation
` Supply voltage, input circuit
Supply voltage, input circuit
Input circuit is driven by connecting U
B
A1
L1 (L+)
` Feedback loop
Feedback loop
Contacts from external contactors
A2
Y1
Y2
K5
L2 (L-)
K6
Pilz GmbH & Co. KG, Sichere Automation, Felix-Wankel-Straße 2, 73760 Ostfildern, Germany
Telephone: +49 711 3409-0, Telefax: +49 711 3409-133, E-Mail: pilz.gmbh@pilz.de
NSG-D-2-085-2006-10