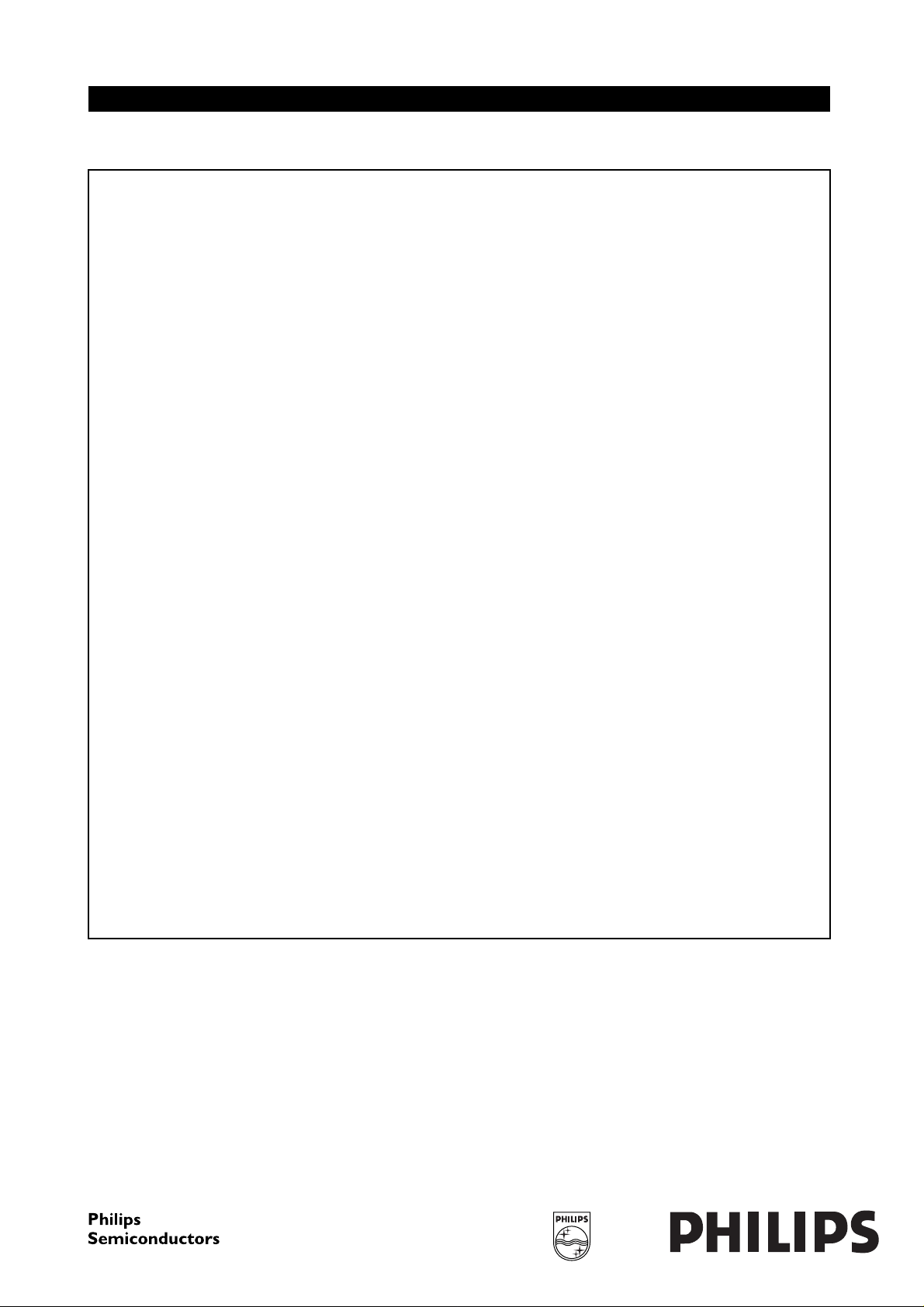
INTEGRATED CIRCUITS
DATA SH EET
TDA8357J
Fullbridgeverticaldeflectionoutput
circuit in LVDMOS
Preliminary specification
File under Integrated Circuits, IC02
1999 Nov 10
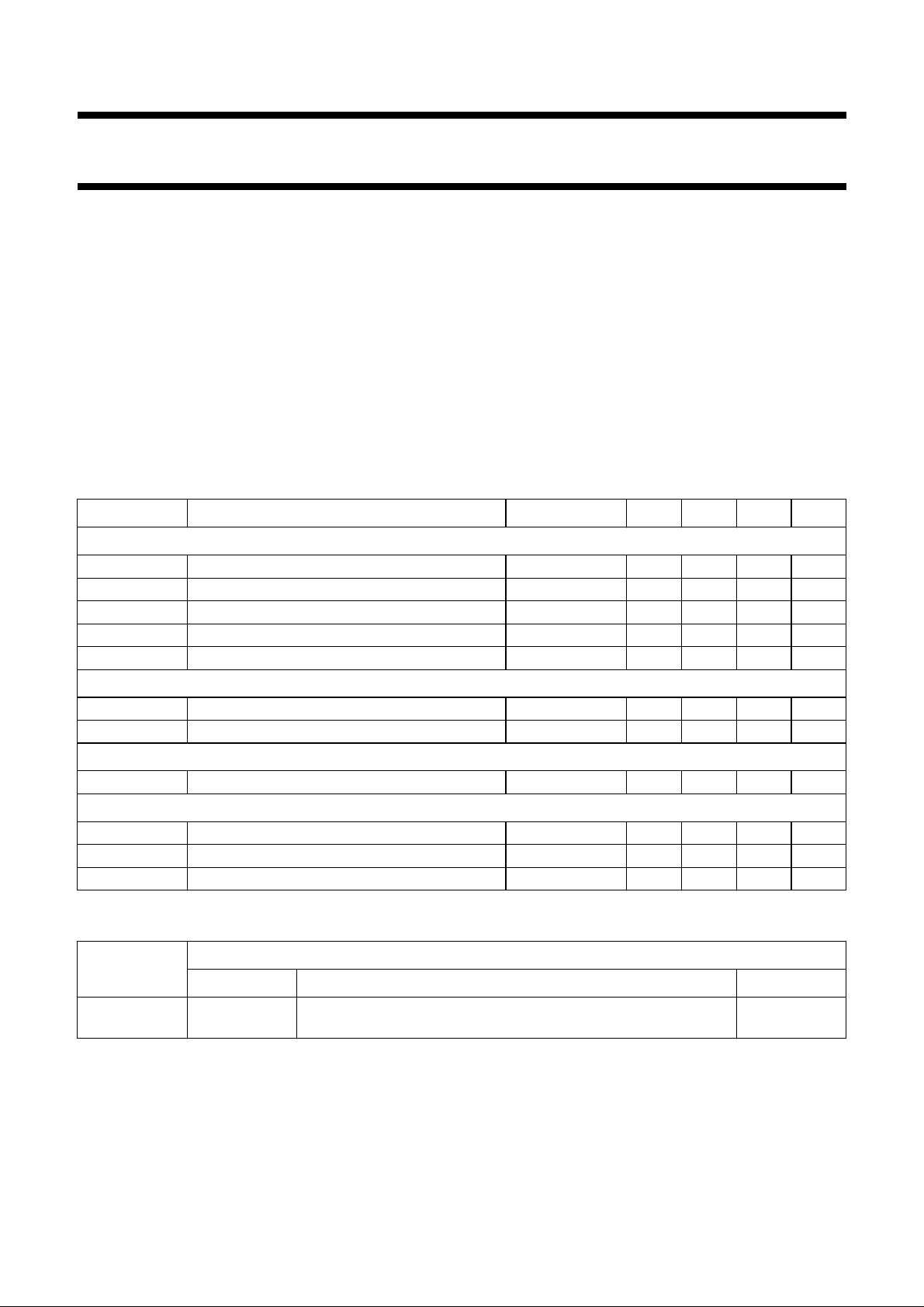
Philips Semiconductors Preliminary specification
Full bridge vertical deflection outputcircuit
TDA8357J
in LVDMOS
FEATURES
• Few external components required
• High efficiency fully DC coupled vertical bridge output
circuit
• Vertical flyback switch with short rise and fall times
• Built-in guard circuit
• Thermal protection circuit
• Improved EMC performance due to differential inputs.
QUICK REFERENCE DATA
SYMBOL PARAMETER CONDITIONS MIN. TYP. MAX. UNIT
Supplies
V
P
V
FB
I
q(P)(av)
I
q(FB)(av)
P
tot
supply voltage 7.5 12 18 V
flyback supply voltage 2V
average quiescent supply current during scan − 10 15 mA
average quiescent flyback supply current during scan −−10 mA
total power dissipation −−8W
Inputs and outputs
V
i(dif)(p-p)
I
o(p-p)
differential input voltage (peak-to-peak value) − 1000 1500 mV
output current (peak-to-peak value) −−2.0 A
Flyback switch
I
o(peak)
maximum (peak) output current t ≤ 1.5 ms −−±1.2 A
Thermal data; in accordance with IEC 747-1
T
stg
T
amb
T
j
storage temperature −55 − +150 °C
ambient temperature −25 − +75 °C
junction temperature −−150 °C
GENERAL DESCRIPTION
The TDA8357J is a power circuit for use in 90° and 110°
colour deflection systems for 25 to 200 Hz field
frequencies, and for 4 : 3 and 16 : 9 picturetubes. The IC
contains a vertical deflection output circuit, operating as a
high efficiency class G system. The full bridge output
circuit allows DC coupling of the deflection coil in
combination with single positive supply voltages.
The IC is constructed in a Low Voltage DMOS (LVDMOS)
process that combines bipolar, CMOS and DMOS
devices. DMOS transistors are used in the output stage
because of absence of second breakdown.
45 66 V
P
ORDERING INFORMATION
TYPE
NUMBER
NAME DESCRIPTION VERSION
PACKAGE
TDA8357J DBS9P plastic DIL-bent-SIL power package; 9 leads (lead length
12/11 mm); exposed die pad
1999 Nov 10 2
SOT523-1
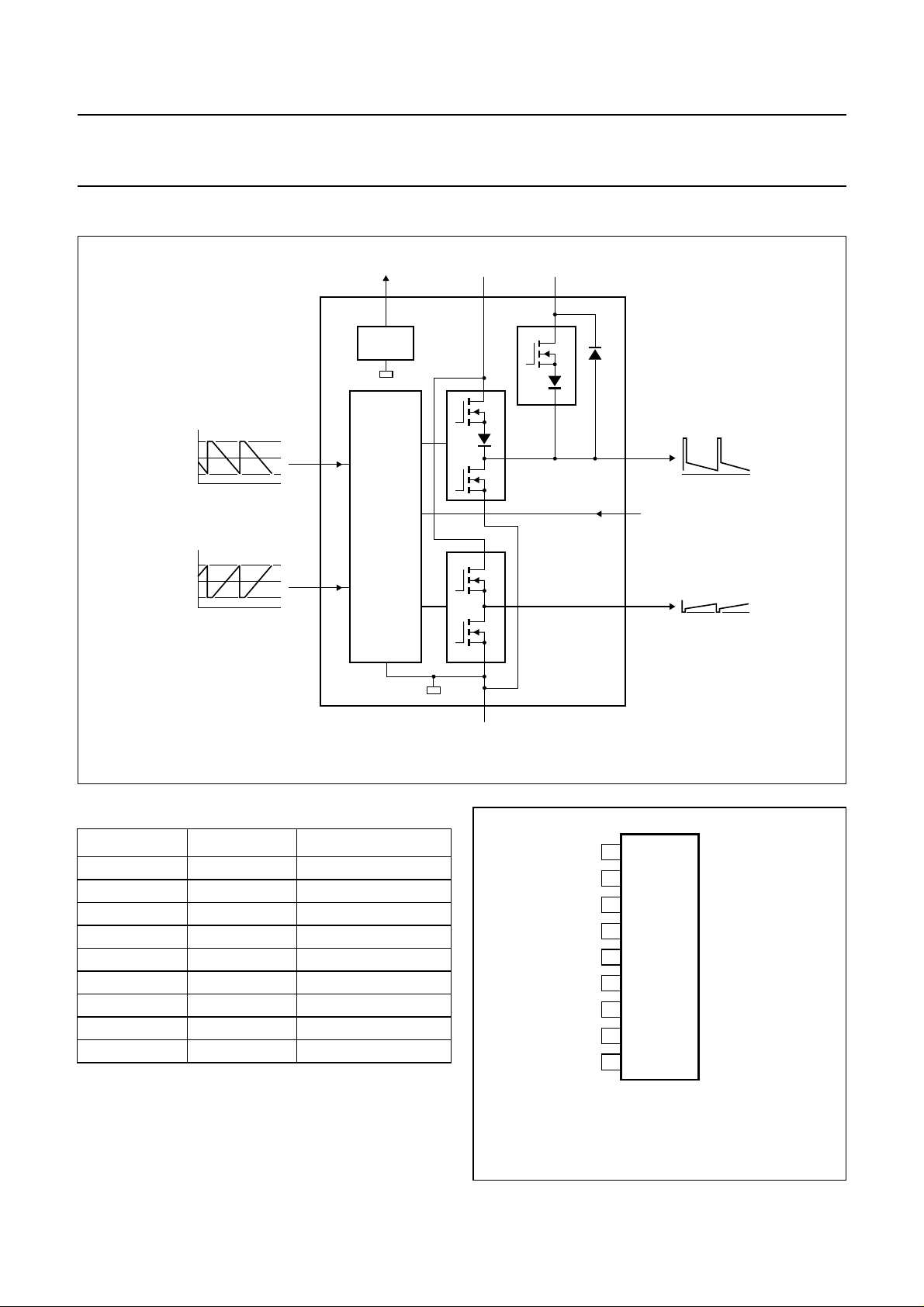
Philips Semiconductors Preliminary specification
Full bridge vertical deflection output circuit
in LVDMOS
BLOCK DIAGRAM
handbook, full pagewidth
V
I(bias)
V
I(bias)
V
i(p-p)
1
INA
0
V
i(p-p)
INB
2
0
GUARD
863
GUARD
CIRCUIT
D1
INPUT
AND
FEEDBACK
CIRCUIT
TDA8357J
V
P
M2
M4
M1
M3
D3
V
FB
M5
D2
OUTA
7
9
FEEDB
4
OUTB
PINNING
SYMBOL PIN DESCRIPTION
INA 1 input A
INB 2 input B
V
P
3 supply voltage
OUTB 4 output B
GND 5 ground
V
FB
6 flyback supply voltage
OUTA 7 output A
GUARD 8 guard output
FEEDB 9 feedback input
5
GND
Fig.1 Block diagram.
handbook, halfpage
TDA8357J
INA
INB
V
OUTB
GND
V
FB
OUTA
GUARD
FEEDB
MGS803
P
1
2
3
4
5
TDA8357J
6
7
8
9
MGS804
1999 Nov 10 3
The exposed die pad is connected to pin GND.
Fig.2 Pin configuration.
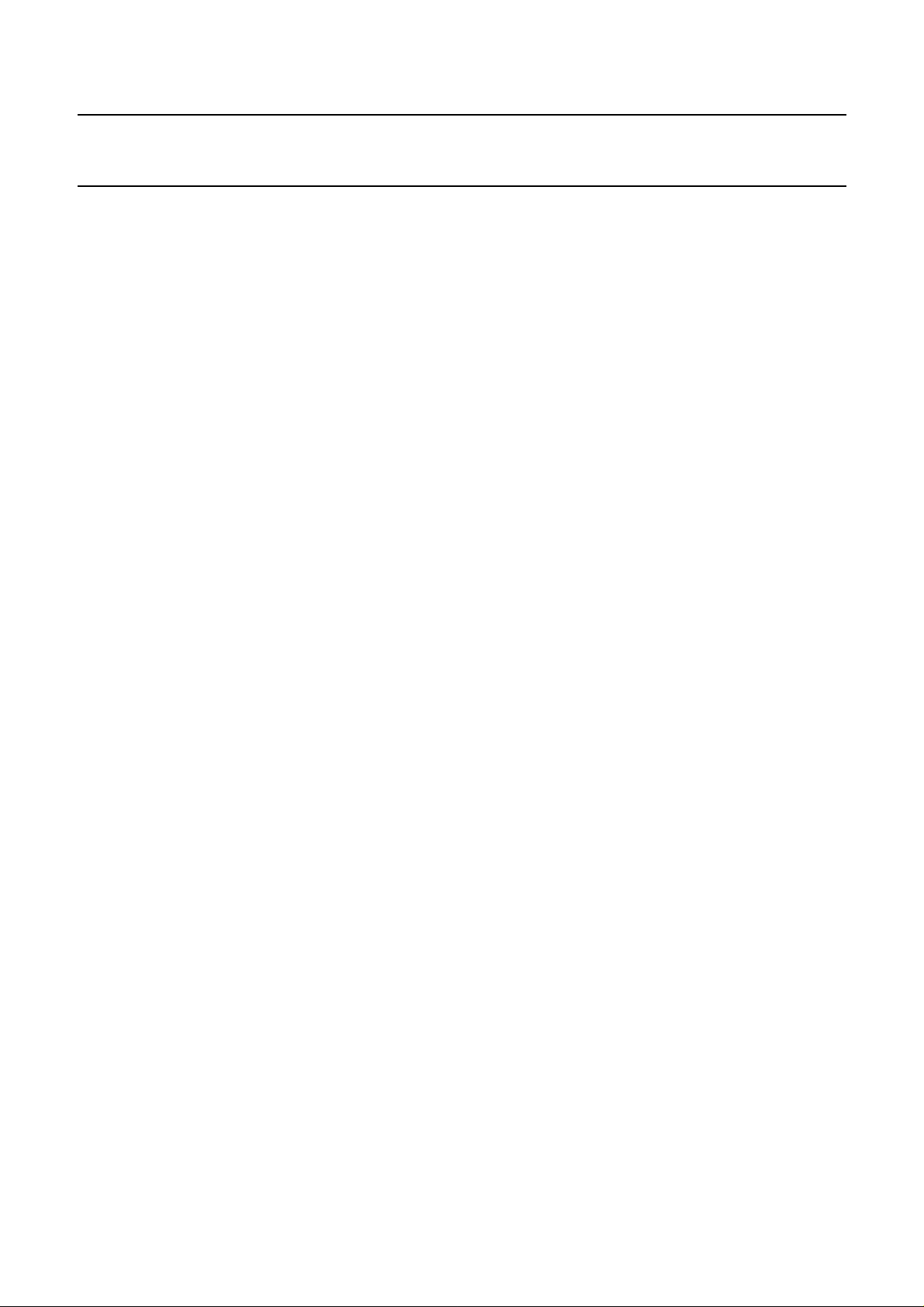
Philips Semiconductors Preliminary specification
Full bridge vertical deflection output circuit
in LVDMOS
FUNCTIONAL DESCRIPTION
Vertical output stage
The vertical driver circuit has a bridge configuration.
The deflection coil is connected between the
complimentary driven output amplifiers. The differential
input circuit is voltage driven. The input circuit is specially
designed for direct connection to driver circuits delivering
a differential signal but it is also suitable for single-ended
applications. The output currents of the driver device are
converted to voltages by the conversion resistors
R
and R
CV1
and INB. The differential input voltage is compared with
the voltage across the measuring resistor RM, providing
internal feedback information. The voltage across RM is
proportional with the output current. The relationship
between the differential input current and the output
current is defined by:
2 × I
i(dif)(p-p)
The output current should measure 0.5 to 2.0 A (p-p) and
is determined by the value of RMand RCV. The allowable
input voltage range is 100 mV to 1.6 V for each input. The
formula given does not include internal bondwire
resistances. Depending on the values of RM and the
internal bondwire resistance (typical value of 50 mΩ) the
actual value of the current in the deflection coil will be
about 5% lower than calculated.
Flyback supply
The flyback voltage is determined by the flyback supply
voltage VFB.Theprincipleoftwosupplyvoltages(class G)
allows to use an optimum supply voltage VP for scan and
an optimum flyback supply voltage VFB for flyback, thus
very high efficiency is achieved. The available flyback
output voltage across the coil is almost equal to VFB, due
to the absence of a coupling capacitor which is not
required in a bridge configuration. The very short rise
and fall times of the flyback switch are determined mainly
by the slew-rate value of more than 300 V/µs.
(see Fig.3) connected to pins INA
CV2
× RCV=I
o(p-p)
× R
M
TDA8357J
Guard circuit
A guard circuit with output pin GUARD is provided.
The guard circuit generates a HIGH-level during the
flyback period. The guard circuit is also activated for one
of the following conditions:
• During thermal protection (Tj≈ 170 °C)
• During an open-loop condition.
The guard signal can be used for blanking the picture tube
and signalling fault conditions. The vertical
synchronization pulses of the guard signal can be used by
an On Screen Display (OSD) microcontroller.
Damping resistor compensation
HF loop stability is achieved by connecting a damping
resistor RD1across the deflection coil. The current values
in RD1 during scan and flyback are significantly different.
Boththeresistorcurrentandthe deflection coil current flow
intomeasuringresistor RM,resultinginatoolowdeflection
coil current at the start of the scan.
The difference in the damping resistor current values
during scan and flyback have to be externally
compensated in order to achieve a short settling time.
For that purpose a compensation resistor R
with a zener diode is connected between pins OUTA
and INA(see Fig.4). The zener diode voltage value should
be equal to VP. The value of R
VFBV
– V
R
CMP
=
-----------------------------------------------------------------------------------------------------------V
FBVloss FB()
loss FB()
– I
is calculated by:
CMP
–()R
× R
Z
D1
R
coil peak()
×–()R
where:
• V
is the voltage loss between pins VFBand OUTA
loss(FB)
at flyback
• R
is the deflection coil resistance
coil
• VZ is the voltage of zener diode D5.
in series
CMP
×
CV1
×
coil
M
Protection
The output circuit contains protection circuits for:
• Too high die temperature
• Overvoltage of output A.
1999 Nov 10 4
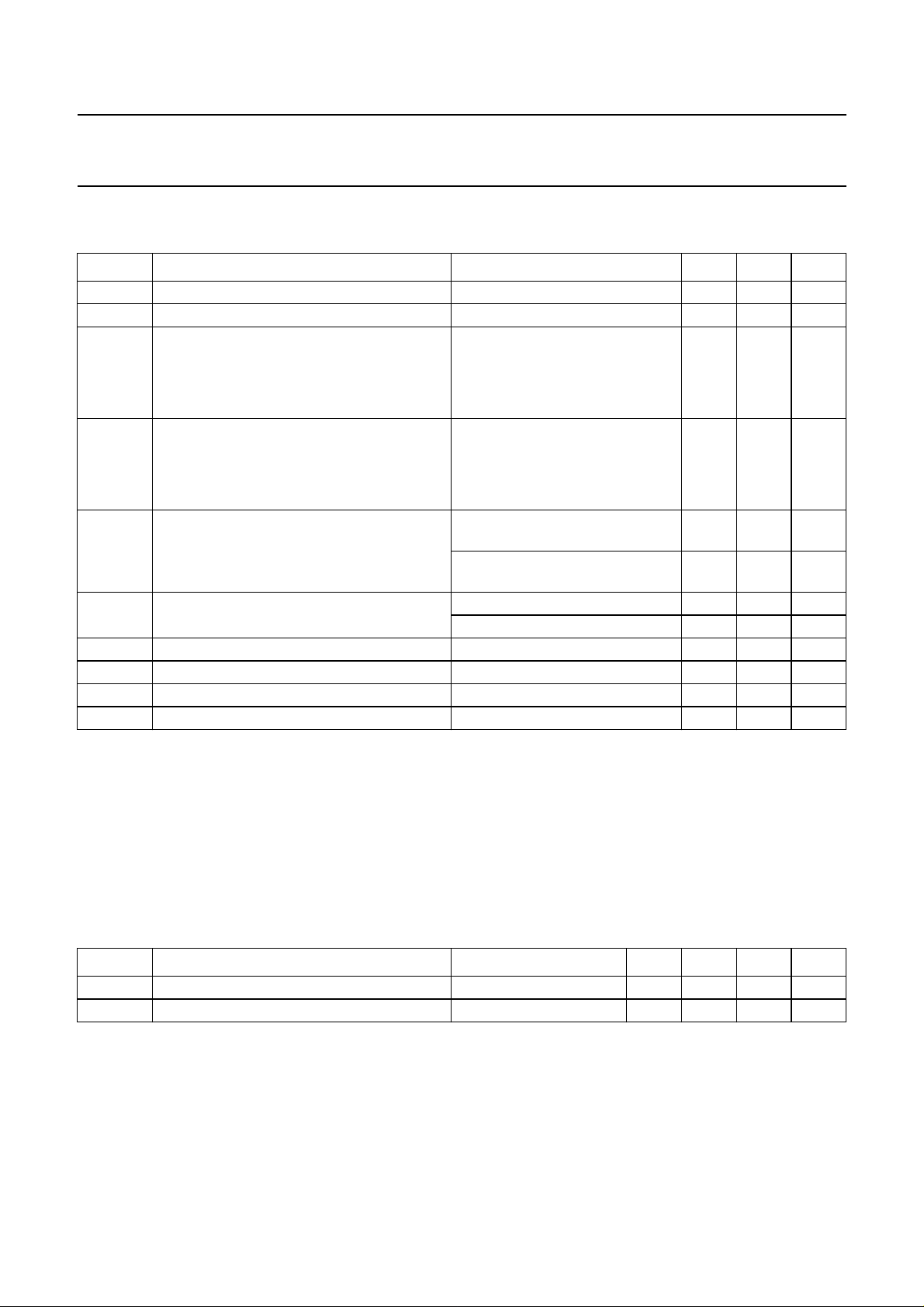
Philips Semiconductors Preliminary specification
Full bridge vertical deflection output circuit
TDA8357J
in LVDMOS
LIMITING VALUES
In accordance with the Absolute Maximum Rating System (IEC 134).
SYMBOL PARAMETER CONDITIONS MIN. MAX. UNIT
V
P
V
FB
V
n
I
n
I
lu
V
es
P
tot
T
stg
T
amb
T
j
supply voltage − 18 V
flyback supply voltage − 68 V
DC voltage
pin OUTA note 1 − 68 V
pin OUTB − V
pins INA, INB, GUARD and FEEDB −0.5 V
V
P
V
P
DC current
pins OUTA and OUTB during scan (p-p) − 2.0 A
pins OUTA and OUTB at flyback (peak); t ≤ 1.5 ms −±1.2 A
pins INA, INB, GUARD and FEEDB −20 +20 mA
latch-up current current into any pin; pin voltage
− +200 mA
is 1.5 × VP; note 2
current out of any pin; pin voltage
is −1.5 × V
; note 2
P
−200 − mA
electrostatic handling voltage machine model; note 3 −300 +300 V
human body model; note 4 −2000 +2000 V
total power dissipation − 8W
storage temperature −55 +150 °C
ambient temperature −25 +75 °C
junction temperature note 5 − 150 °C
Notes
1. When the voltage at pin OUTA supersedes 70 V the circuit will limit the voltage.
2. At T
j(max)
.
3. Equivalent to 200 pF capacitance discharge through a 0 Ω resistor.
4. Equivalent to 100 pF capacitance discharge through a 1.5 kΩ resistor.
5. Internally limited by thermal protection at Tj≈ 170 °C.
THERMAL CHARACTERISTICS
In accordance with IEC 747-1.
SYMBOL PARAMETER CONDITIONS MIN. TYP. MAX. UNIT
R
R
th(j-c)
th(j-a)
thermal resistance from junction to case −−6 K/W
thermal resistance from junction to ambient in free air −−65 K/W
1999 Nov 10 5