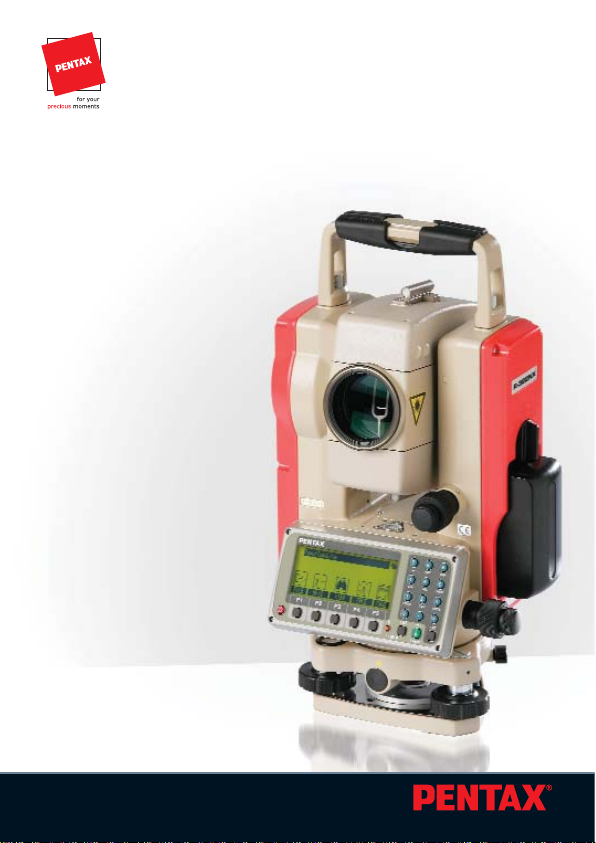
Ahead of Vision
PENTAX Industrial Instruments Co., Ltd.
2-5-2 Higashi-Oizumi
Nerima-Ku, Tokyo 178-8555, Japan
Tel. +81 3 5905 1222
Fax +81 3 5905 1225
E-mail: international@piic.pentax.co.jp
Website:www.pentax.co.jp/piic/survey
www.pentaxsurveying.com
TOTAL STATION
QUICK
REFERENCE
GUIDE
POWERTOPOLITE
FOR R-300X SERIES
R-322NX R-322EX
R-323NX R-323EX
R-325NX R-325EX
R-335NX R-335EX
R-315NX R-315NX
R-326EX
SERIES
R-300X
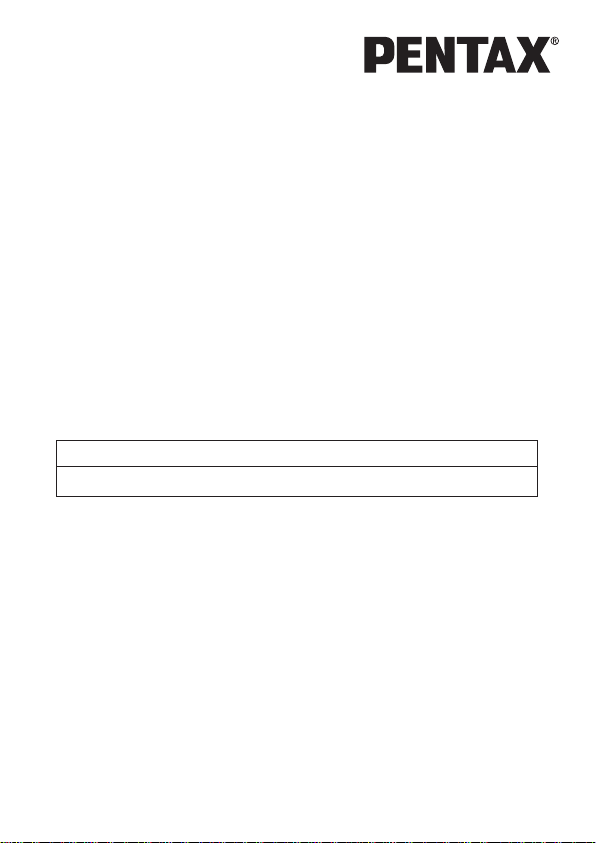
Electronic Total Station
Quick Reference Guide
PowerTopoLite For R-300X
series Operating Procedure
R-322NX, R-323NX,R-325NX, R-335NX, R-315NX,
R-322EX, R-323EX,R-325EX, R-335EX, R-315EX, R-326EX
Total Surveying Solutions
PENTAX Industrial Instruments Co., Ltd.
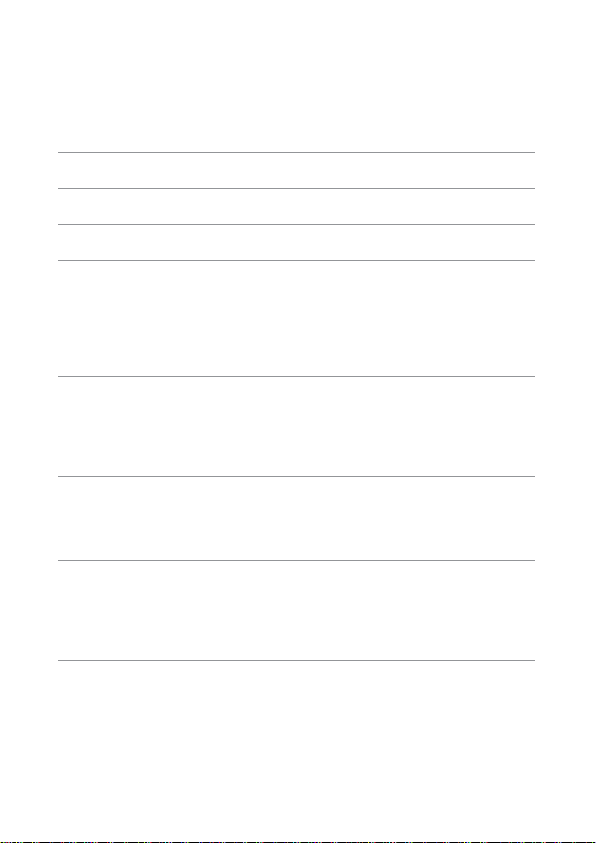
5
CONTENTS
Instruction Manuals 7
Precautions regarding safety 7
Operational Procedure 7
1 Starting Special Function 9
2 Creating / Selecting a Job File 9
3 Input a Known Point Coordinate 9
4 Rectangular Coordinate Measurement 10
4.1 Station Point Setup 10
4.2 Orientation (Station Point H. Angle Setup) 11
4.3 Measurement 12
4.4 Offset Measurement 13
4.5 Remote Measurement 13
5 Polar Coordinate Measurement 14
5.1 Station Point Setup 14
5.2 Orientation (Station Point H. Angle Setup) 15
5.3 Measurement 15
5.4 Offset Measurement 16
6 Free Stationing 17
6.1 Known Point Setup 17
6.2 Measurement 17
6.3 Calculation 17
7 Stake Out 18
7.1 Station Point Setup 18
7.2 Orientation (Station Point H. Angle Setup) 18
7.3 Stakeout Point Setup 19
7.4 Stakeout Measurement 19
8 Stake Out (Point to Line) 20
8.1 Station Point Setup 20
8.2 Orientation (Station Point H. Angle Setup) 20
8.3 Point A Setup 21
8.4 Point B Setup 21
8.5 Point to Line Measurement 21
>>
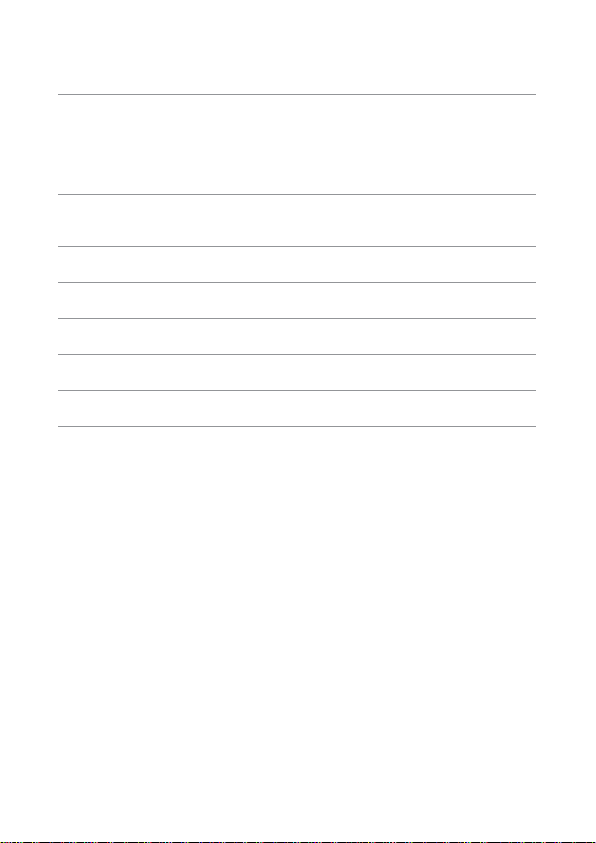
6
CONTENTS
>>
9 Traverse Measurement 22
9.1 Measurement at the Start Point 23
9.2 Measurement at a Corner Point 24
9.3 To Finish the Traverse Measurement 25
9.4 Traverse Calculation 25
10 Cogo 26
Calculation Parameters and Output 27
11 Area Calculation 28
12 3D Surface and Volume Calculation 28
13 REM (Remote Element Measurement) 29
14 RDM (Remote Distance Measurement) 30
15 VPM (Virtual Plane Measurement) 30
16 Changing Preference 31
Preference List 32
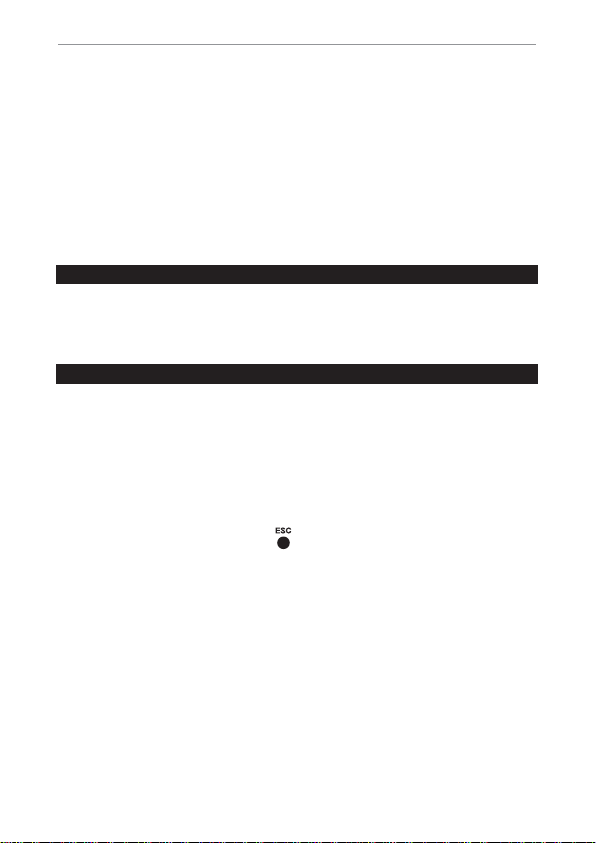
7
INSTRUCTION MANUALS
Quick Reference Guide is intended to provide a quick reference in the
field. For ease of use in the field, the following Quick Reference Guide
booklets are provided in the carrying case.
1. Basic procedure
2. PowerTopoLite for R-300X series, Operating procedure
The complete instruction manuals are contained on the CD that is
attached to each R-300X.
PRECAUTIONS REGARDING SAFETY
Before using this product, be sure that you have thoroughly read
and understood the instruction manual that is included on the
attached CD-R to ensure proper operation.
OPERATIONAL PROCEDURE
The operational procedure in this guide is described based on
the default software parameter settings (preferences). Changing
preferences may cause a different operational procedure. For further
detail of preferences, please refer to the instruction manual of
PSF300 software.
This guide uses the symbol " xN " as an expression of repeating times
of key operation. For example," " means that [ESC] key is pressed
two times.
x2
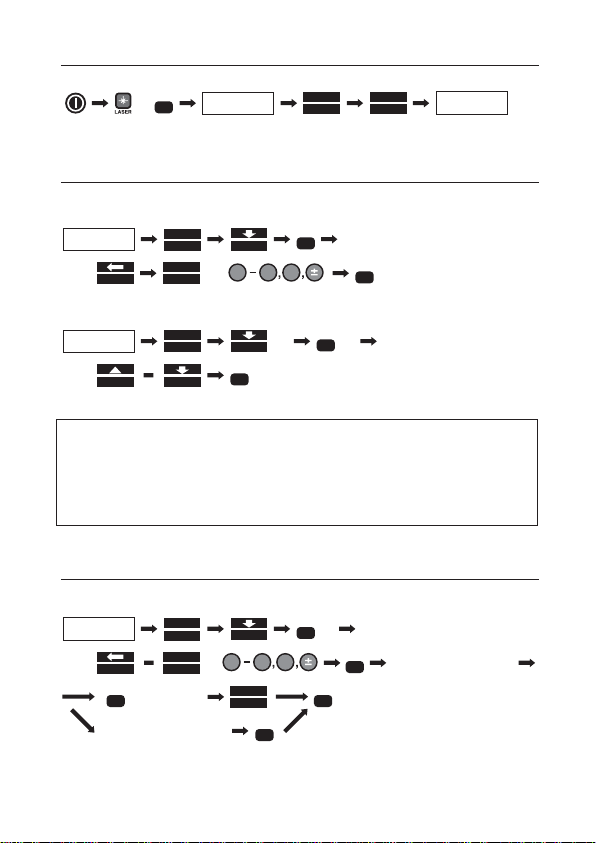
9
1. Starting Special Function
2. Creating / Selecting a Job File
To create a new job file:
Or to select a job file:
NOTE: Once a job file is created or selected, it is effective until a
new job file is created or another job file is selected.
The default job file "PENTAX" is provided permanently
so that data is stored even when no user defined
job file exists.
3. Input a Known Point Coordinate
To input and store a known point coordinate;
POWER TOPO LITE
MAIN MENU
input a new job name by using
POWER TOPO LITE
MAIN MENU
x2
x2 select a job file by
POWER TOPO LITE
MAIN MENU
input a Point Name by using
ESC
MODE A SCREEN
MODE
S. FUNC
F5
F1
POWER TOPO LITE
MAIN MENU
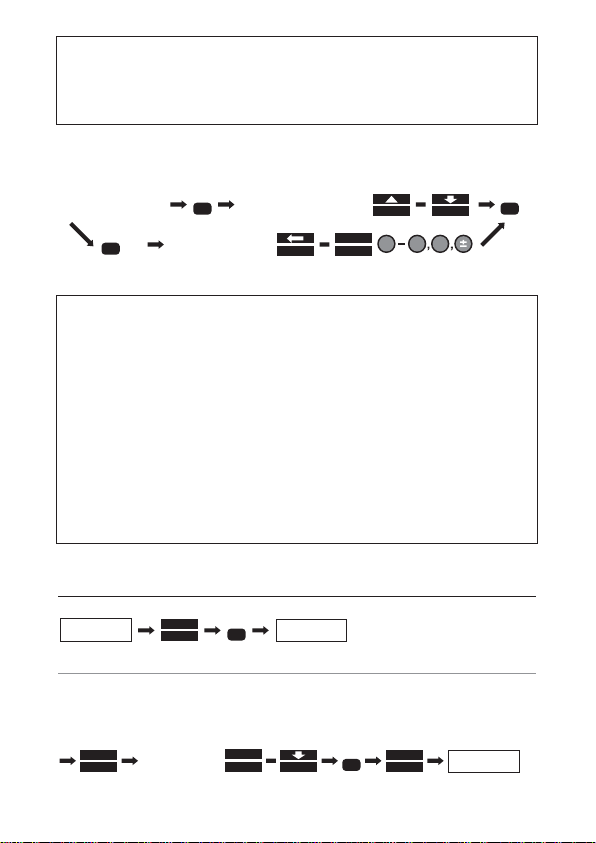
10
NOTE: There are other functions in VIEW menu; Graphical View,
Edit Rectangular Data, and Edit Polar Data. For detail of
these functions, please refer to the instruction manual of
PowerTopoLite.
To input PC (point code):
NOTE: PC list is displayed only when point codes are stored in
the job named “PointColeList”. “PointCodeList” job can be
created by the procedure described in the section 2, and
PC can be stored by inputting PN and PC as a point
coordinate data. PC list can be also transferred from a
computer.For more detail,refer to the instruction manual
of PowerTopoLite.
A new point code can be input and memorized as a point
coordinate data, but it is not stored as the data of
“PointCodeList”. If a new PC need to be added to the list,
select “PointCodeList” job and add a PC as a new
Rect.Coord.Data.
4. Rectangular Coordinate Measurement
4.1 Station Point Setup
To select from the memory:
select a PC
from the list by
input a new PC by
move cursor to PC
POWER TOPO LITE
MAIN MENU
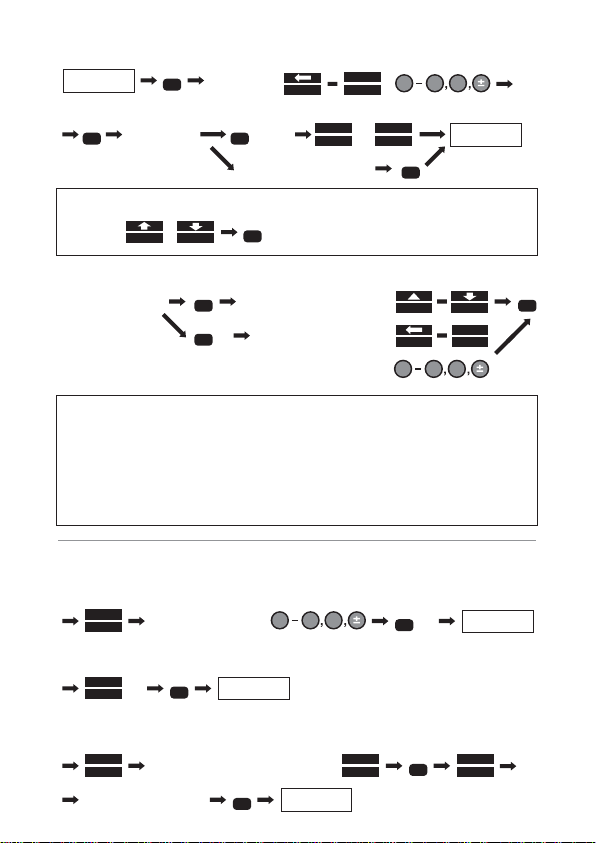
11
Or to input the station point information:
NOTE: The input item (cursor position) may be selected by
To input PC (point code):
NOTE:
Input items are PN (point name), X, Y, Z, IH (instrument
height), and PC (point code).
If the input PN already exists in the memory, then the corresponding
point information
(coordinate & point code) is displayed in the screen.
The result of Free Station, prior to stakeout, is automatically
set in each field of Station Setup.
4.2 Orientation (Station Point H.Angle Setup)
To input a given angle:
Or to set the angle 0°:
Or to calculate by the Back Sight Point:
select a PC from the list by
input a new PC by using
input value or select from the list