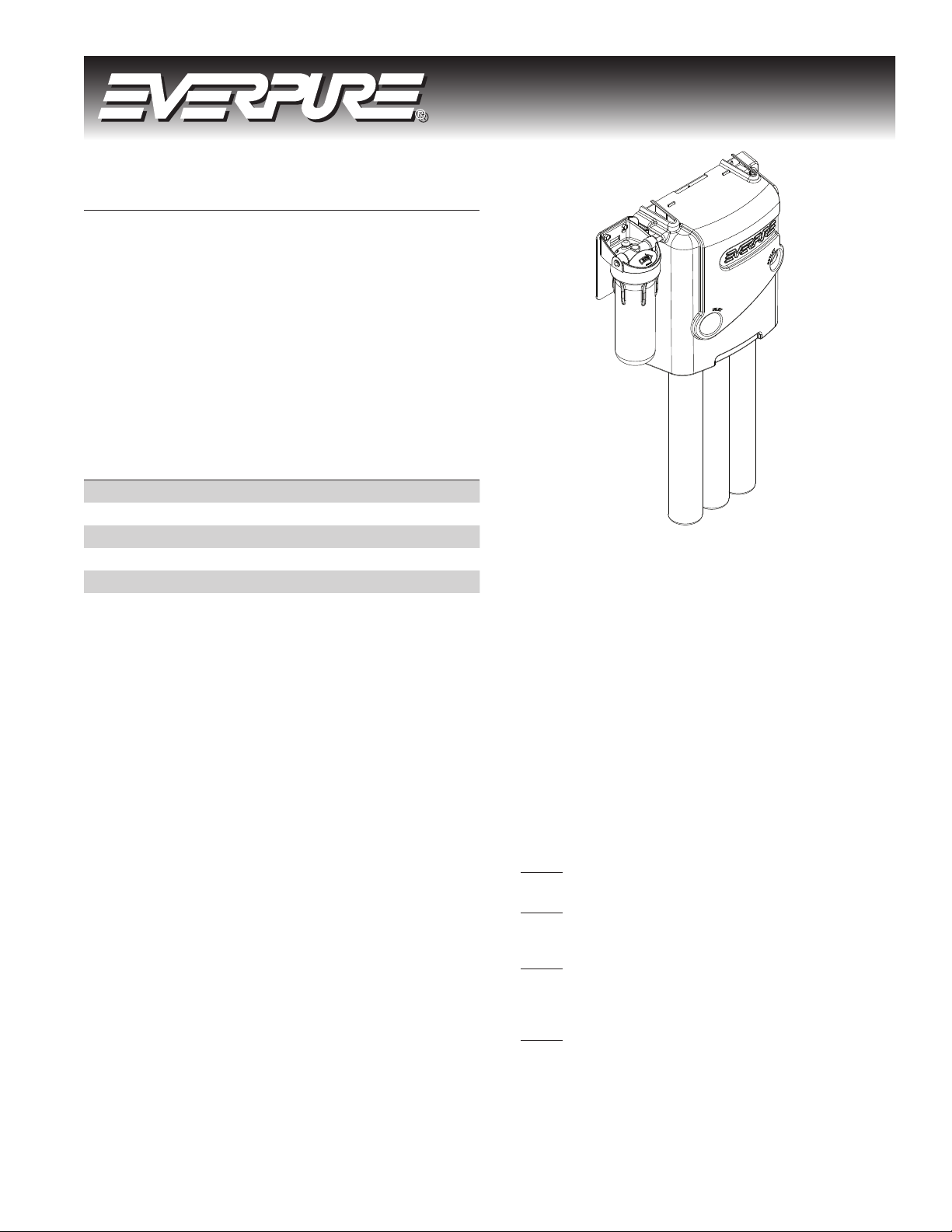
Installation and Operation Guide
MRS-100, MRS-225, MRS-100CC, MRS225CC
Reverse Osmosis Mineral Reduction System For Foodservice Applications
INTRODUCTION
The Everpure MRS (Mineral Reduction System) is a pre-engineered,
pre-assembled Reverse Osmosis (RO) system designed to provide
high purity water for many applications, such as premium espresso,
coffee and blended beverages, to name a few. It combines a
number of water treatment technologies into one easy to install
package. The system provides superior protection against taste and
odor causing contaminants while removing dirt, particulates and
dissolved solids that can foul or scale equipment.
Initial System Production
Water production depends on supply water pressure and temperature.
See PERFORMANCE section (page 5) for normalized production.
Influent Water Characteristics
The following table lists the allowable operating range of various
water properties within which the MRS will function properly.
Total Dissolved Solids (TDS) 0-150 0 PPM (0-150 0 mg/L)
pH 5-10
Chlorine
Chloramines 0-3 PPM (0-3 mg/L)
Turbidity 0-1 NTU
Iron 0-1 PPM (0-1 mg/L)
1
Reverse osmosis membrane lter used in this system will be damaged by chlorine. An
activated carbon lter has been provided with this system to protect the reverse osmosis
membrane from chlorine attack. Inuent chlorine should not exceed 3 mg/L.
The complete MRS consists of 5 major components:
The optional 5-micron pre-filter removes suspended particles, which
can lead to pre-mature plugging of the TO and/or RO membrane
cartridge. The TO cartridge removes most oxidizers, but mainly
reduces chlorine, preventing damage to the RO cartridge. The RO
cartridge contains a semi-permeable reverse osmosis membrane.
Here, most dissolved impurities are separated from the water and
flushed down the drain. The water that is able to pass through the
membrane, which is very low in dissolved impurities, is referred to
as permeate, RO water, or product water. Depending on the model,
the permeate will do one of the following:
• Systems without calcium carbonate (CC) cartridge - The permeate
will pass through the cartridge head with by-pass plug, exiting to
service and/or enters the optional storage tank.
• Systems with calcium carbonate (CC) cartridge - The permeate will
pass through calcium carbonate cartridge, where re-mineralization
occurs. This cartridge reintroduces a metered amount of TDS level
of the RO permeate. After remineralization, the treated water exits
to service and/or enters the optional storage tank.
The optional storage tank stores water that has been produced by
the RO System. This provides a water supply "buf fer ", enabling the
system to provide reasonable volumes of product water during high
demand periods.
Printed in U.S.A. EV3123-42 Rev A AU07
1
0-3 PPM (0-3 mg/L)
A unique car tridge monitor/alarm module is available. This device
can be set to provide simultaneous water throughput and operating
time indications over easily selectable ranges. This monitor helps in
determining cartridge change-out schedules.
OPERATING SPECIFICATIONS
Dynamic Operating Pressure: 25 –80 psi (1.7–5.5 bar)•
Static Operating Pressure: 100 psi (6.9 bar)•
Operating Temperature 40–100°F (4.4 –37.8°C)•
Inlet booster pump.1.
5-Micron Pre-filter (optional).2.
Granular Activated Carbon Taste & Odor (TO) cartridge.3.
Reverse Osmosis (RO) membrane cartridge.4.
Calcium carbonate (CC) re-mineralization cartridge (optional).5.
Connections•
Inlet /Outlet: 3/8-inch tube
Concentrate: 1/4-inch tube
Electrical•
Voltage: 115 volt AC
Hertz: 6 0
Phase: 1
Ampere: 1.5
Branch Circuit Protection: 15 or 20 AMP Ground Fault Protected
Pre-Installation Checklist
1. Can the unit be mounted within a reasonable distance of
the water supply and drain facilities?
2. Is there an un-switched 115 VAC GFIC (ground fault
interrupter circuit) protected receptacle available for powering
the system?
3. Is there adequate clearance and support to install
the unit and permit access for maintenance? The total system
weight will vary based on model and storage tank selected. See
specification table for approximate operating weights.
4. Does the inlet water supply meet the requirements listed
below?
A minimum of 25 PSI pressure on a consistent basisa.
Less than 1,5 00 ppm of Total Dissolved Solids (TDS)b.
Less than 10 GPG of water hardnessc.
pH level between 7.0-9.0d.
Turbidit y less than 1 NTUe.
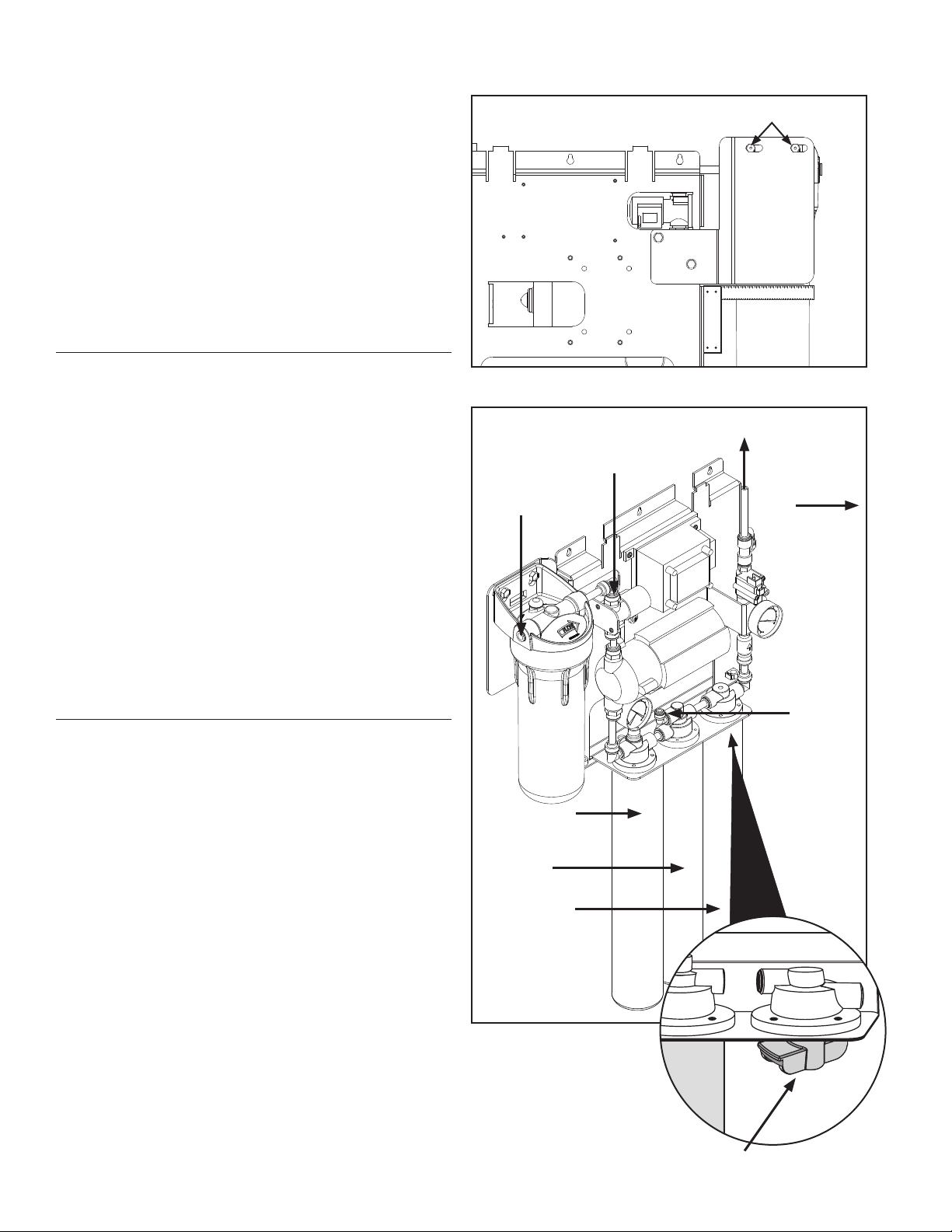
NOTES:
Please read this manual prior to installing and operating the •
system.
Incoming water supplies that do not meet these requirements •
may need additional pre-treatment prior to the system. System
performance may be affected if requirements are not met,
including system output production and cartridge change-out
frequency.
If the supply pressure exceeds 80 PSI, install a pressure reducing •
valve. Adjust the pressure reducing valve to the required
operating pressure, not to exceed 80 PSI.
Consult with your local building inspector for approval and •
required permits to install this system. Additional equipment, such
as back-flow prevention devices, seismic restraint equipment, air
gaps, etc., may be required. Completed installation must meet all
local and national codes.
Do not connect the MRS system after any water filtration system,
unless specifically provided for use with the MRS.
UNPACKING AND INSPECTION
The MRS includes all the necessary fittings for installation. Lengths
of 1/4” tubing have been provided for connecting to the wastewater/
drain connection. Supply lines and distribution piping/tubing are not
included.
The MRS system is packaged as a complete unit in two cartons. At a
minimum, you should have the following:
Carton 1
Plate mounted processor assembly (Including the following)1.
pump A.
cartridge heads B.
transformerC.
Carton 2
TO cartridge1.
RO cartridge 2.
Calcium carbonate (CC) cartridge (optional)3.
Inspect the cartons for damage. Report any damage to freight
carrier immediately. Carefully unpack each item. Save the packaging
material temporarily, as it may be used to protect painted sur faces
during assembly.
SYSTEM ASSEMBLY
The MRS is configured as a two piece unit; with the processor
mounted on a vertical surface and the storage tank located nearby.
Locate the system in an area that is convenient to the inlet water
supply and drain facilities, with access for routing the product water
tubing/piping to the equipment. Install in a dry location, away from
all forms of corrosive and/or flammable materials. Consider ease of
access for servicing when selecting a location.
Processor Assembly Mounting
If the optional Pre-filter has been supplied, go to step to 2. If not 1.
supplied, go to step 5.
Position the MRS processor assembly so the rear of the 2.
mounting plate is accessible. Secure the wing bracket to the rear
of the mounting plate as shown Figure 1. Use the 5/16” hex bolts
and washers provided. Align the wing bracket so it is inward
and upward as far as possible – use a combination square to
maintain alignment. Tighten both bolts securely.
Attach Pre-filter head to Pre-filter bracket with 5/16” hex bolts, 3.
nuts and washers provided.
Insert elbow fitting into solenoid valve inlet. Connect 1/4” OD 4.
tubing between pre-filter outlet and elbow fit ting on solenoid
valve.
5. The processor framework has 6 mounting holes (3 keyhole
slots, 3 standard) on 4.5” centers for securing to a stationary
vertical surface. Evaluate the mounting surface for its abilit y
to properly support the weight of the processor when in
operation (Approximately 40 pounds).
continued on the next page . . .
2
Figure 1. Back view of Prefilter bracket.
Figure 2. MRS Assembly.
Inlet
(without optional Pre-filter)
Inlet
(with Pre- filter)
MRS
Processor
Pre-filter
(optional)
6TO-BW
Carbon
Cartridge
MRRO Car tridge
7CC-BW
Cartridge
(optional)
By-pass Plug
(Keep inserted if optional
7CC-BW car tridge is not used)
Prefilter bolts
Wing
bracket
Outlet
Storage
Tan k
(not shown,
not
included)
RO Reject
(1/4" John
Guest) route
to drain
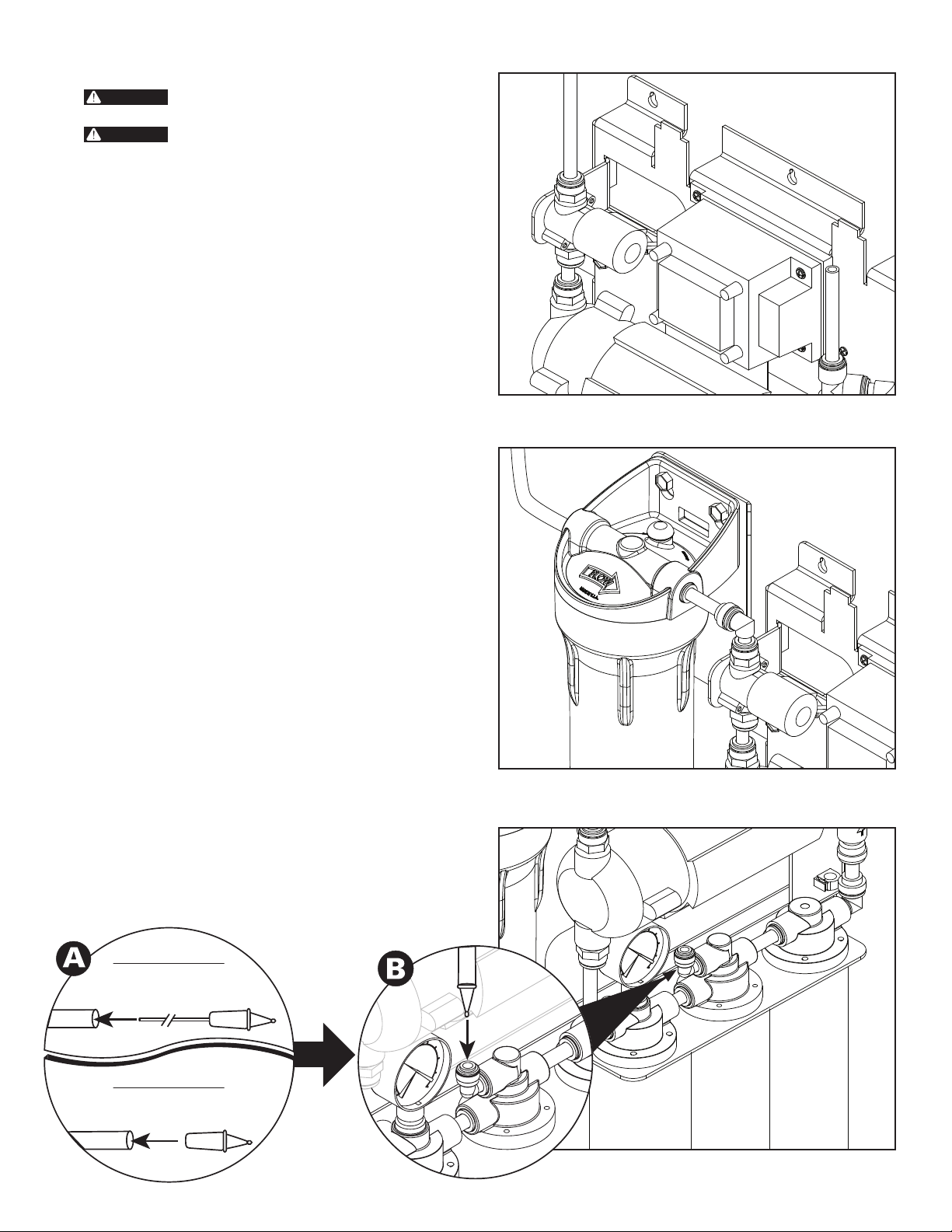
6. Attach processor to the vertical surface with screws and
TUBE
FLOW
CONTROL
Model MRS-100
TUBE
FLOW
CONTROL
Model MRS-225
anchors designed for the mounting surface material.
Do not use screws smaller than #12 for mounting the
processor.
suppor t processor safely. Hollow walls, dry wall and other nonstructural surfaces are not suitable unless reinforced.
Mounting surface may require reinforcement to
Piping/Tubing Connections
Refer to Figure 2 for views of the piping, with a description of major 1.
components and connection points. These major components and
connections will be referred to in the following steps.
Prepare the plumbing to accept the RO system. It is recommended2.
that a three valve by-pass is installed to provide an uninterrupted
supply of water when the RO system requires service.
Note: The product water tubing/piping and associated fittings
connecting the RO product outlet to the equipment being serviced
should be food grade material that meets NSF Standard 51 or 61
with a minimum pressure rating of 75-PSI. The product water
will react with most metal piping, creating a corrosive condition,
in addition to imparting an objectionable taste. Plastic pipe or
reinforced tubing are generally very good choices for RO water
distribution materials. The size of the product water tubing/piping
should be 3/8" ID minimum. Distances of 25 feet or greater
the RO to the equipment being serviced should be 1/2" ID minimum.
Connect the inlet supply.3.
MODELS WITHOUT PRE-FILTER – See Figure 3. Connect to A.
the Inlet open por t (3/8 " JG) on the solenoid valve.
MODELS WITH PRE-FILTER – See Figure 4. Connect to the B.
Inlet open port (3/ 8" JG) on the pre-filter head.
Connect the appropriate size and t ype of tubing/piping and 4.
associated fit tings to the Outlet tee connection. Route the line(s)
to the equipment being serviced (i.e.; espresso, coffee, etc.).
Locate the storage tank directly below or adjacent to the 5.
processor assembly. Be sure the mounting surface is capable
of supporting the weight of the tank when full (see specification
table for operating weights). Connect a suitable length of 3/8"
inch OD tubing to the tank connection. Route this section of
tubing to the main processor assembly. Connect the tubing to the
elbow fitting at tached to the side of the outlet tee connection.
Note: The storage tank pre-charge pressure should be
checked and adjusted when the storage tank is empty. For
most applications, a low (5-10 psi) pre-charge pressure is
recommended, to attain maximum storage tank volume.
Close the inlet, outlet and by-pass ball valves.6.
Locate the correct reject flow control assembly based on the 7.
illustration below (A). Insert the reject flow control assembly
into the 1/4" OD tube (See A Below). Insert the 1/4" OD tube
with reject flow control assembly into the elbow fitting on RO
head (See B below). Route the other end of the tubing to a drain
nearby, securing it temporarily. Allow an air gap at the drain,
following any applicable local codes. See Figure 5.
continued on the next page . . .
from
Figure 3. No Prefilter
Figure 4. Pre-filter
Figure 5. RO Reject Flow Control Assembly
3