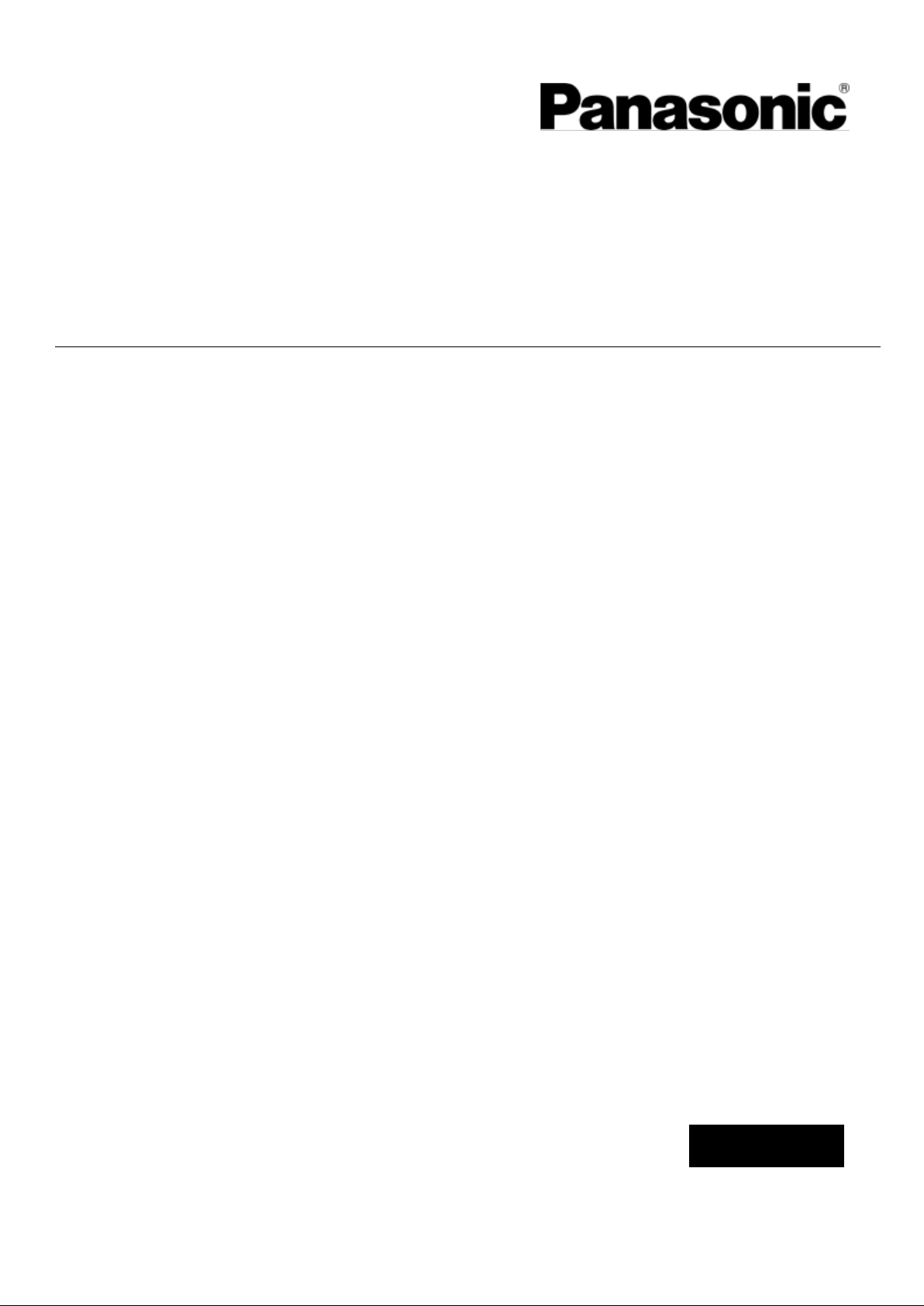
Ultra-Low Temperature Freezer
Panasonic Healthcare Co., Ltd.
Biomedical Div.
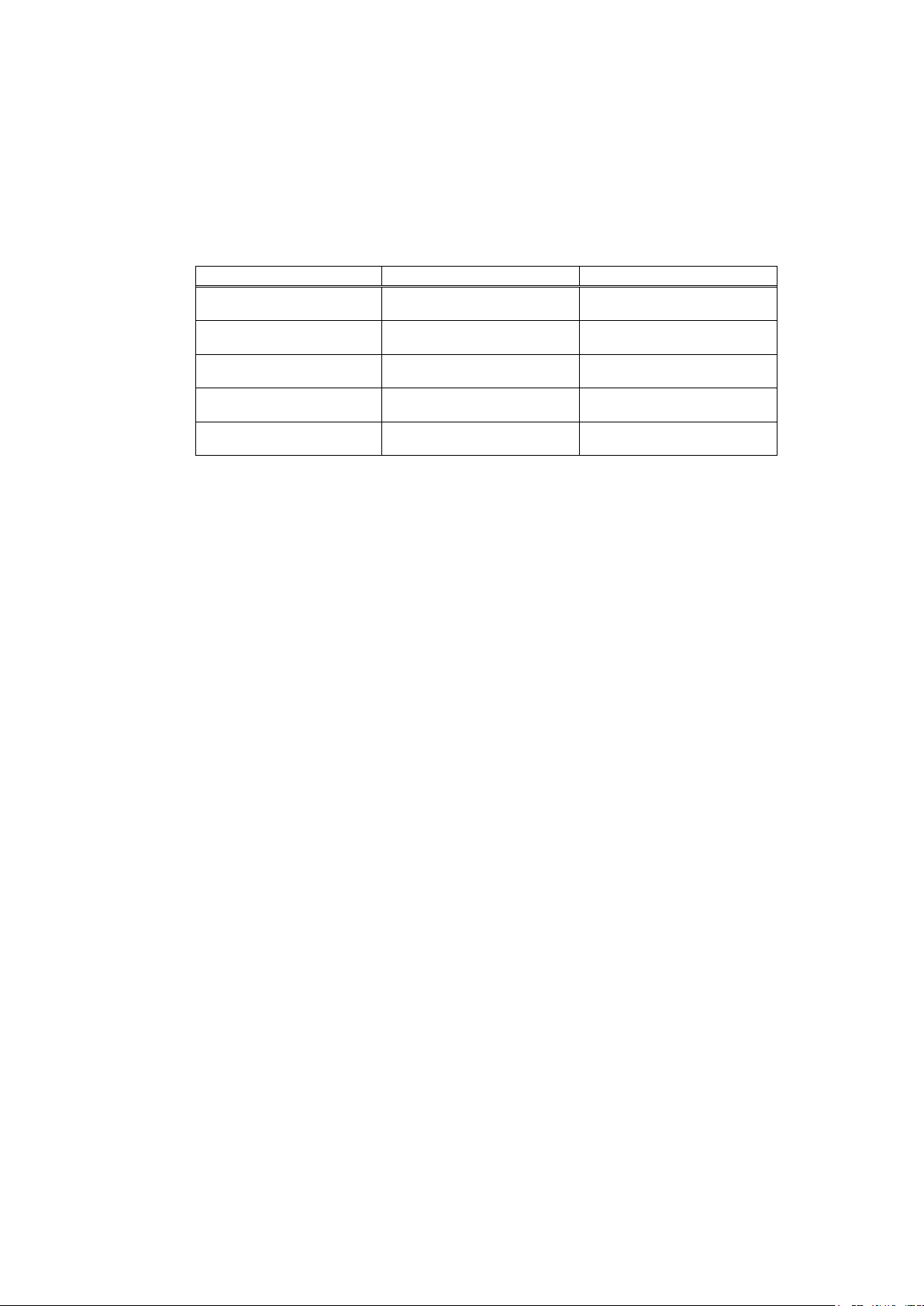
Effective model
This service manual is effective for following models.

----------------------------------------------------------
S p e c i f i c a t i o n s
----------------------------------------------------------
-Structural s p e c ifications
-Control spec if i c ations
-Performance s p ecificat i ons
----------------------------------------------------------
----------------------------------------------------------
R e f i r i g e r a t i o n c i r c u i t s
--------------------------------------------------
C o m p o n e n t s o n P C B
--------------------------------------------------
C o n n e c t i o n s o n P C B
--------------------------------------------------
E l e c t r i c p a r t s
-------------------------------------------------------
Sp e c i f i c a t i o n of s en s or
--------------------------------------------------
W i r i n g d i a g r a m
-------------------------------------------------------
C i r c u i t d i a g r a m
-------------------------------------------------------
------------------------------------------------------- - - ----------
C o n tr o l s p e c if i c a t i o n s
---------------------------------------------------
I n v e t e r s i g n a l
----------------------------------------------------------
----------------------------------------------------------
R e p a i r i n g u n i t / G a s c h a r g e
------------------------------------------
----------------------------------------------------------
MDF-DU502VH, MDF-DU702V H
-Pull-down & P ull-up tem p e r ature
-Pull-down t e m perature
-Pull-down c urrent-inp u t
-Temperature u n iformit y ( 1 7points meas u r e d)
-Amount of po w e r consumpti o n
Bac kup cooli n g kit instal la t ion and sett i n g procedure
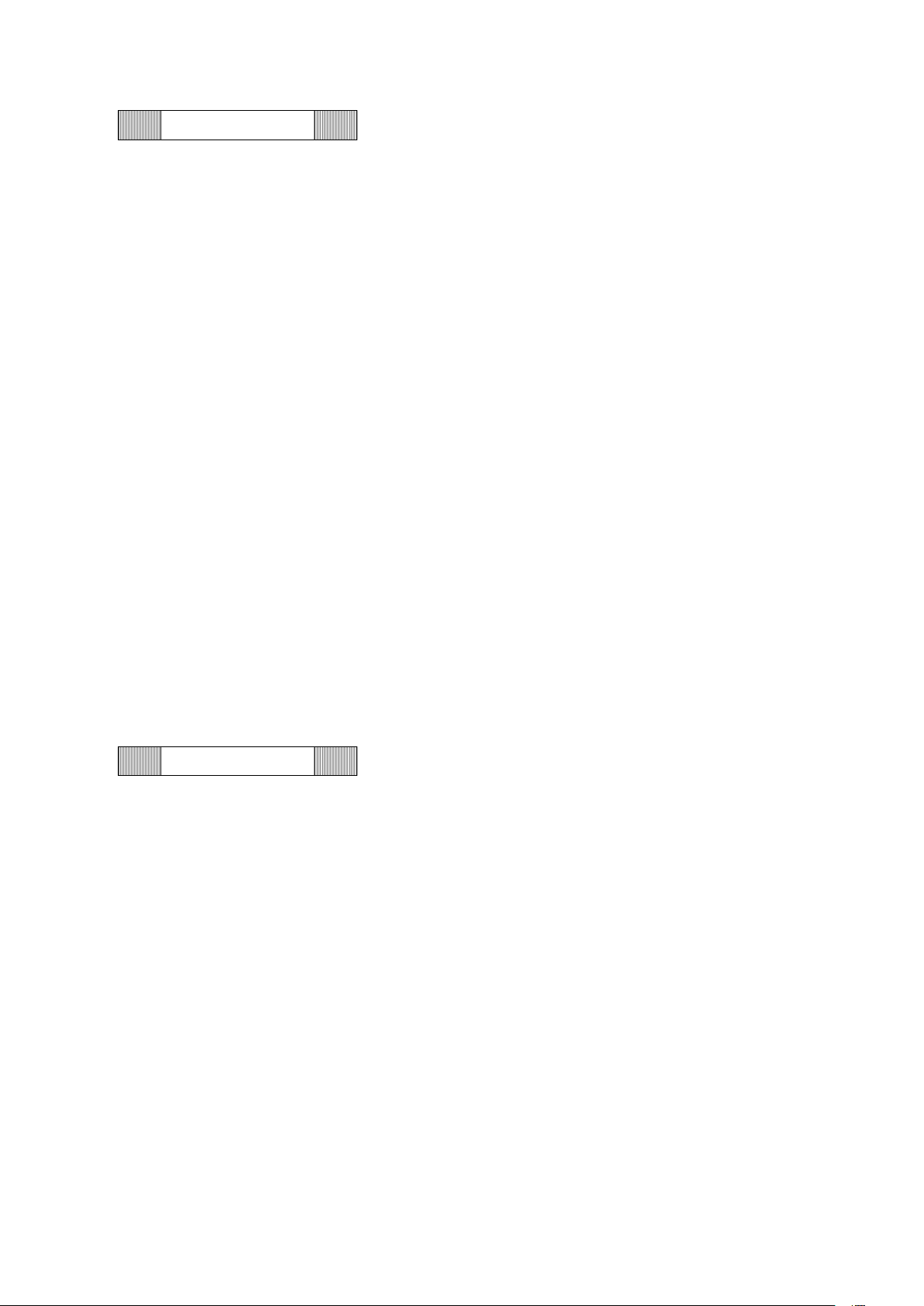
Energy saving
Inverter control of compressor
Improvement of storage efficiency
Auto air intake port
Enhancement of safety functions
New control panel with LCD touch panel
*Parts replacement and option unit installation must be done by trained service engineer.
*Service engineer must refer to the section “Electric parts” and “Cooling unit parts”
about the parts for those operations.
-1-
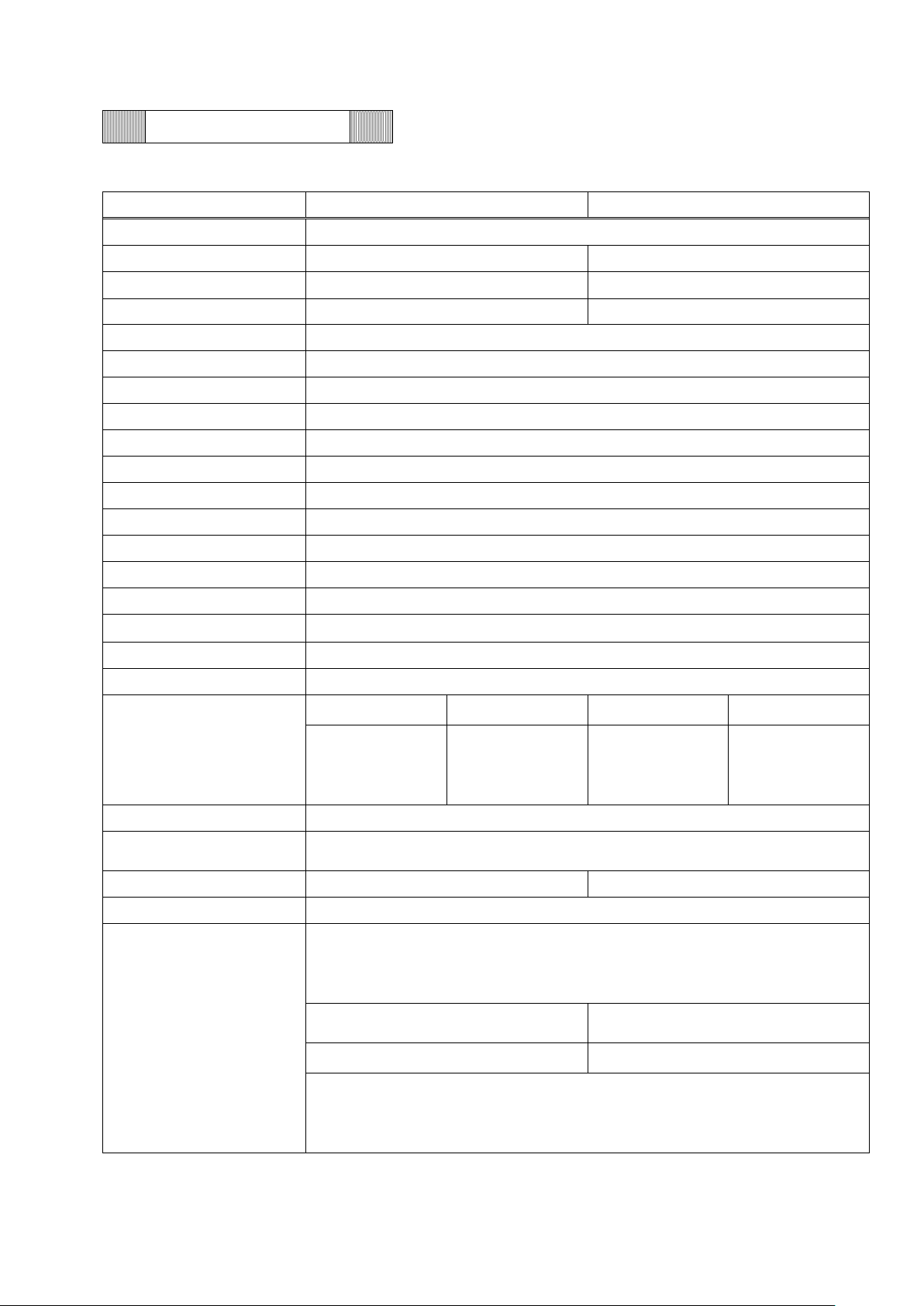
Structural specifications
Ultra-Low Temperature Freezer
W 790 × D 882 × H 1993 mm
W 1030 × D 882 × H 1993 mm
W 630 × D 600 × H 1400 mm
W 870 × D 600 × H 1400 mm
Rigid polyurethane foam+VIP PLUS
Inside of control panel (built-in anti freezing heater)
Product left side lower part
VNEU213U (single-phase 220-240V 50/60Hz)x 2
High: Cascade, Low: Tube on sheet
High: Fin and tube, Low: Cascade
R170 70 g ±3 g
n-pentane 10 g
(16cc) 0+3 g
(12.5%wt)
R170 85 g ±3 g
n-pentane 12 g
(19cc) 0+3 g
(12.5%wt)
For power failure alarm, Lead storage battery, DC6 V 7200 mAh,
Auto-recharge
1 key, 1 scraper, 1 stick for air intake port cleaning
Temperature recorder: (MTR-85H MTR-G85C),
Recorder fixing (MDF-S3085, MTR-85H)
Recorder sensor Cover:(MTR-DU700SF)
Backup cooling kit:(MDF-UB7);For Liquid CO2
Small inner door
(MDF-5ID4, MDF-5ID5)
Small inner door
(MDF-7ID4, MDF-7ID5)
Storage rack (MDF-70SC)
Inventory rack (IR-224U, IR-316U)
Interface board (MTR-L03)*; For LAN
Interface board (MTR-480)*; For RS-232C/RS-485
* For the data acquisition system MTR-5000 user only.
-2-
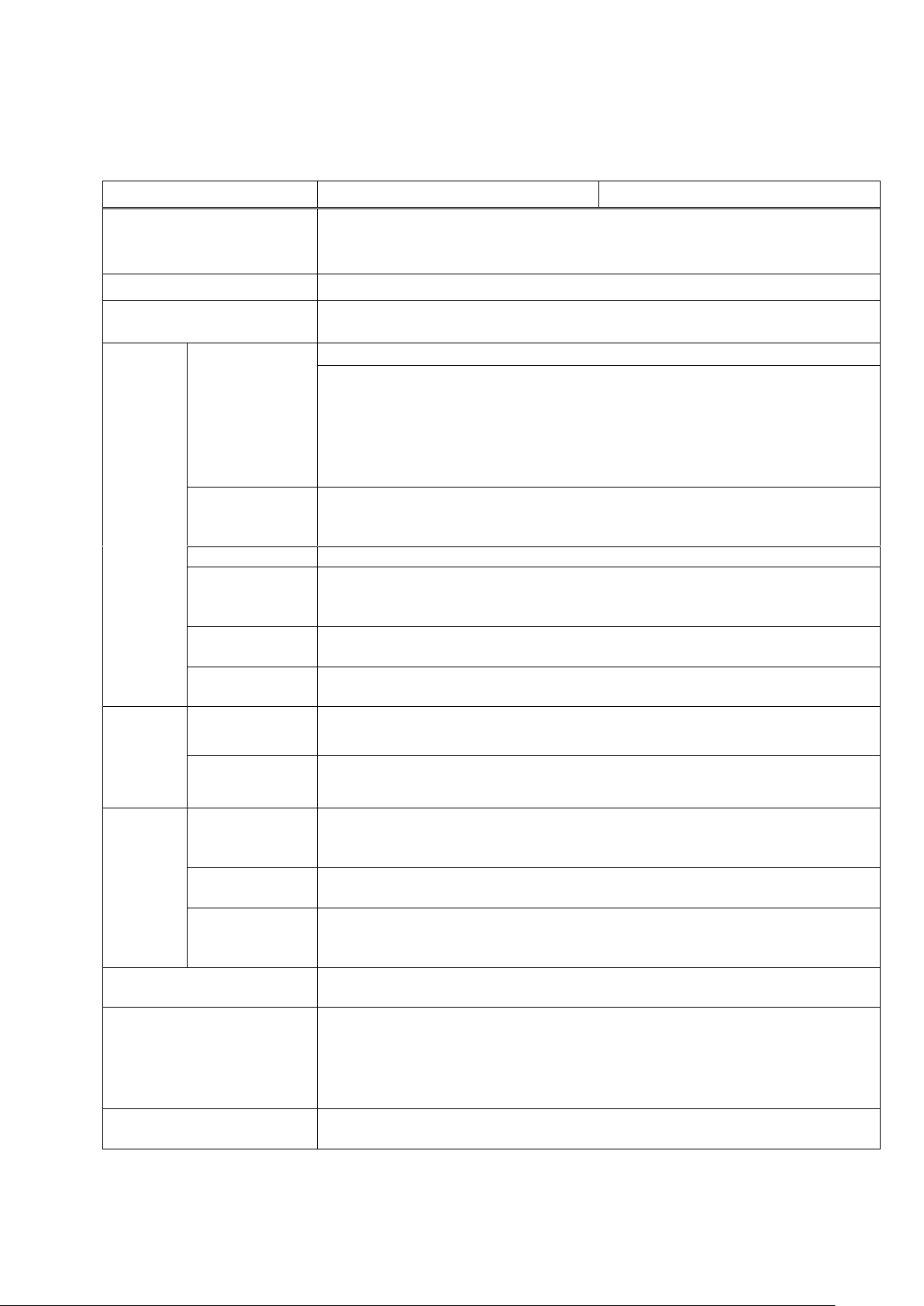
Microprocessor control system: LCD touch panel input
Settable range : -90 ℃~-50 ℃ (unit:1 ℃)
Memorized by Non-volatile memory
Platinum resistance (Type: PT 1000 Ω)
WVGA full color LCD
Digital display (Unit: 1 ℃)
SV±5 ℃~±40 ℃, changeable (default:±10 ℃)
When the chamber temperature exceeds the alarm set temperature,
"Alarm" is displayed alternately in normal characters and reverse video
in the alarm display field and chamber temperature blinks. After 15 min.
(0-15 min. changeable, default: 15℃), "Warning" is displayed in the
message display field, buzzer beeps and remote alarm activates and
chamber temperature blinks.
When the door opens, "Open" is displayed alternately in normal
characters and reverse video in the alarm display field. After 2 min.
(0-15 min. changeable), buzzer beeps, no remote alarm activates.
"Warning" is displayed alternately in normal characters and reverse
video in the alarm display field. And the notification is displayed in the
message display field. Buzzer beeps and the remote alarm activates.
Filter alarm indicator is lit when the excessive dust is accumulated on
the condenser filter. When this indicator is lit, clean the condenser filter.
Remote alarm terminal 3P; contact capacity DC 30 V, 2 A (Max)
Remote alarm activates when temp. alarm or power failure occur.
Parts
replacement
notification
Two type of battery accumulation time display in service mode. At
replacement time, it is informed in the message display field.
Fan motor accumulation time display in service mode. Replacement
notification is not performed.
When the sensor is out of the range of 35 ℃ from 0 ℃ , the
notification display in the message display field.
High-load
operation
display
When low side compressor operation rate is over 95 %, the notification
display in the message display field.
When a sensor is failed, the notification display in the message display
field. Buzzer beeps and remote alarm activates.
Overload relay (internal)
Detected value of filter sensor is 50 ℃ or more.
"Warning" is displayed alternately in normal characters and reverse
video in the alarm display field and the notification is displayed in the
message display field. Buzzer beeps and remote alarm activates.
Selection of ON or OFF by slide in Key Lock mode.
OFF: Unlocked ON: Locked
-3-
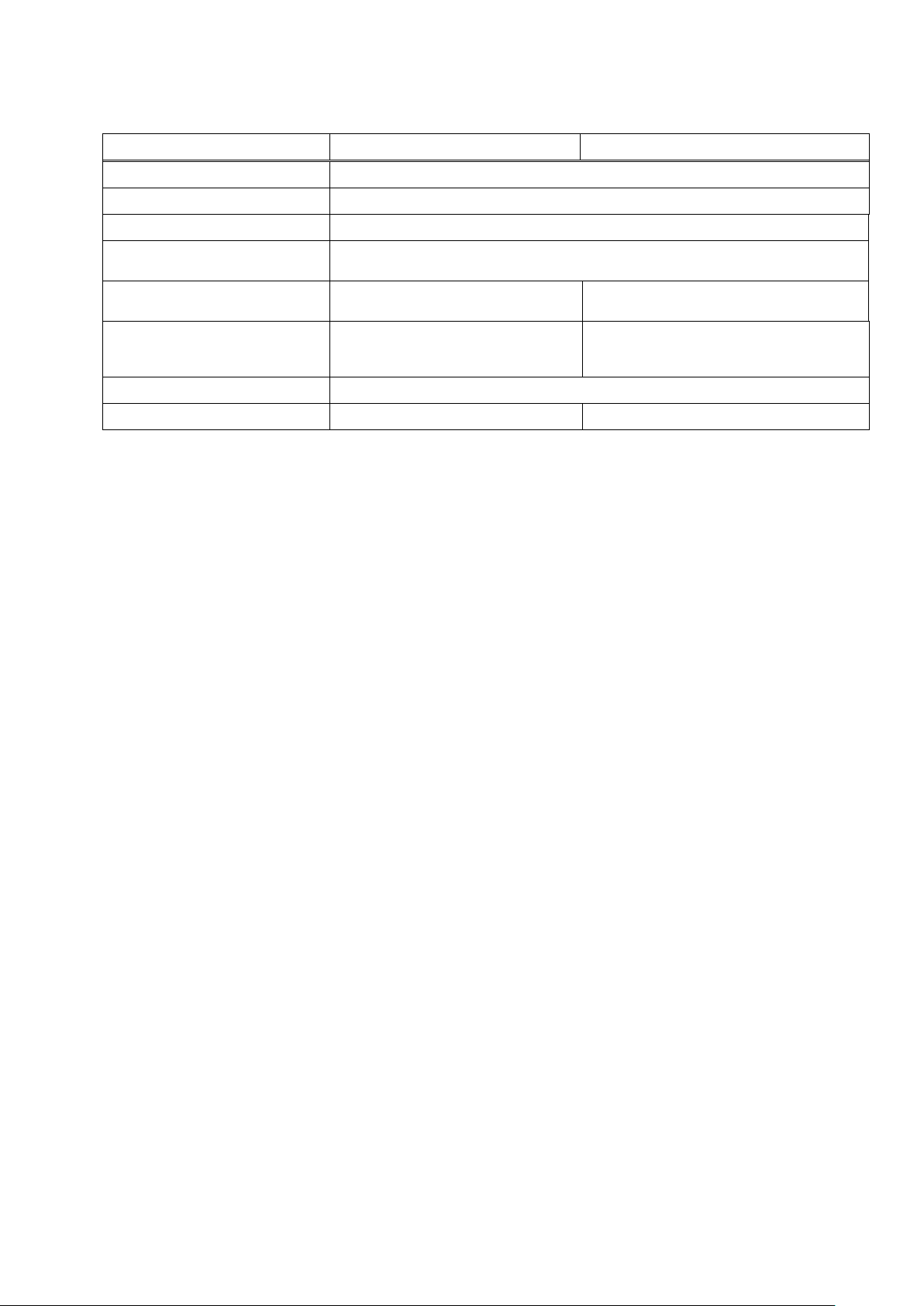
Performance specifications
Temperature control range
-86 ℃~-50 ℃ (ambient temperature; 30 ℃, no load)*
430 W (Max. 820 W)(PA)
420 W (Max. 840 W)(PE)
545 W (MAX 930W/ 945 W/ 960 W) (PE)
550 W (MAX 930 W) (PA)
1548 kJ/h (Max. 2952 kJ/h)
1512 kJ/h (Max. 3024 kJ/h)
1962 kJ/h
(Max.3348 kJ/h /3402 kJ/h /3456 kJ/h) (PE)
1980 kJ/h (Max. 3348 kJ/h))(PA)
52 dB [A] (background noise; 20 dB)
*Maximum cooling performance.
The chamber temperature can be reached at -86 ℃ at ambient temperature 30 ℃ with no load.
-4-
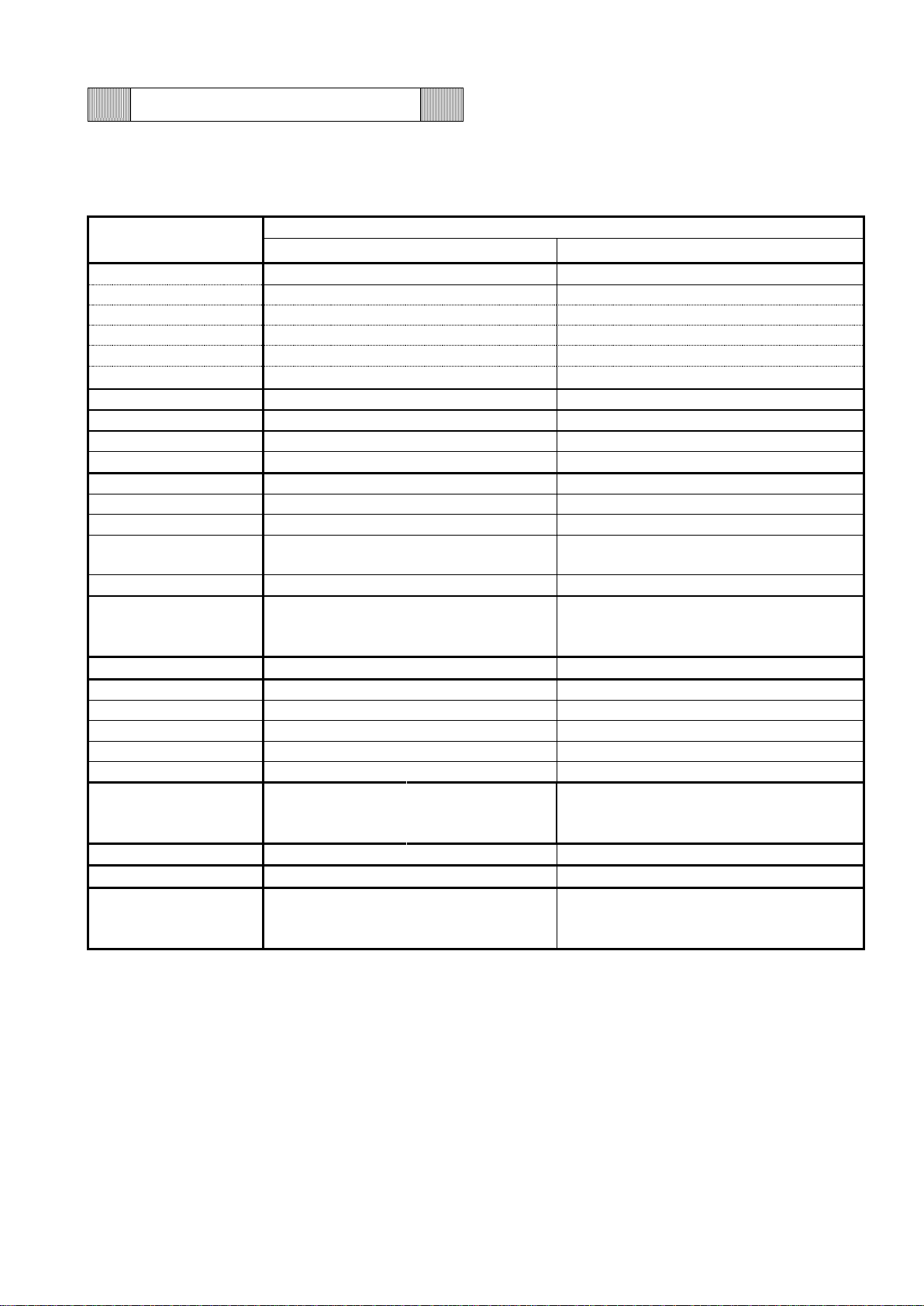
MDF-DU502VH
1Φ220-240V 50/60Hz
Circuit H(Left side at rear view)
Circuit L(Right side at rear view)
Single phase, 220-240 V, 50/60 Hz
Single phase, 220-240 V, 50/60 Hz
Forcible air circulation(partially)
Forcible air circulation(partially)
12 columns x 2 lines 5pitch Fin 50spc
W250 mm
(within 1column x6lines pre-con)
Evaporator
Type
Accumulator
Cascade condenser, Shell & Tube
Φ80 mm
Φ38 mm
Tube on sheet, Φ7.94mm
(Sharing with interior)
Amount
70g ±3 g
10g (16cc)-0+3g
Material: ABS Blade: 4 pcs. 230 mm
Material: ABS Blade: 4 pcs. Φ230 mm
Condensing fan
motor
Type
SV4-11AB5P
(440VAC,1.0μF running condenser)
SV4-11AB5P
(440VAC,1.0μF running condenser)
-7-
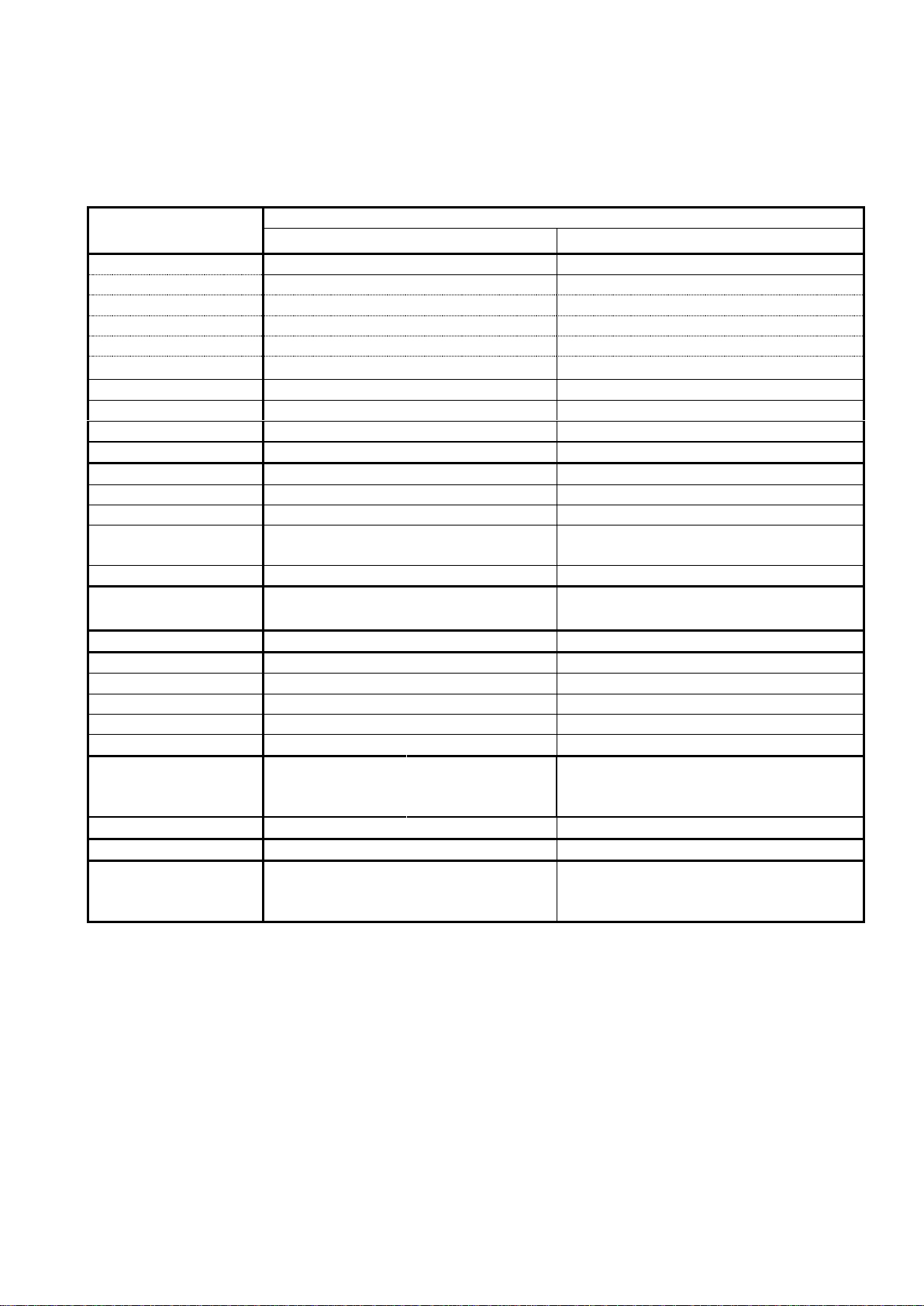
MDF-DU702VH
1Φ220-240V 50/60Hz
Circuit H(Left side at rear view)
Circuit L(Right side at rear view)
Single phase, 220-240 V, 50/60 Hz
Single phase, 220-240 V, 50/60 Hz
Forcible air circulation(partially)
Forcible air circulation(partially)
12 columns x 2 lines 5pitch Fin 50spc
W250 mm
(within 1column x6lines pre-con)
Cascade condenser, Shell & Tube
Φ80mm
Tube on sheet, Φ7.94mm
(Sharing with interior)
Amount
85g ±3 g
12g (19cc)-0+3g
Material: ABS Blade: 4 pcs. 230mm
Material: ABS Blade: 4 pcs. Φ230mm
Condensing fan
motor
Type
SV4-11AB5P
(440VAC,1.0μF running condenser)
SV4-11AB5P
(440VAC,1.0μF running condenser)
-8-
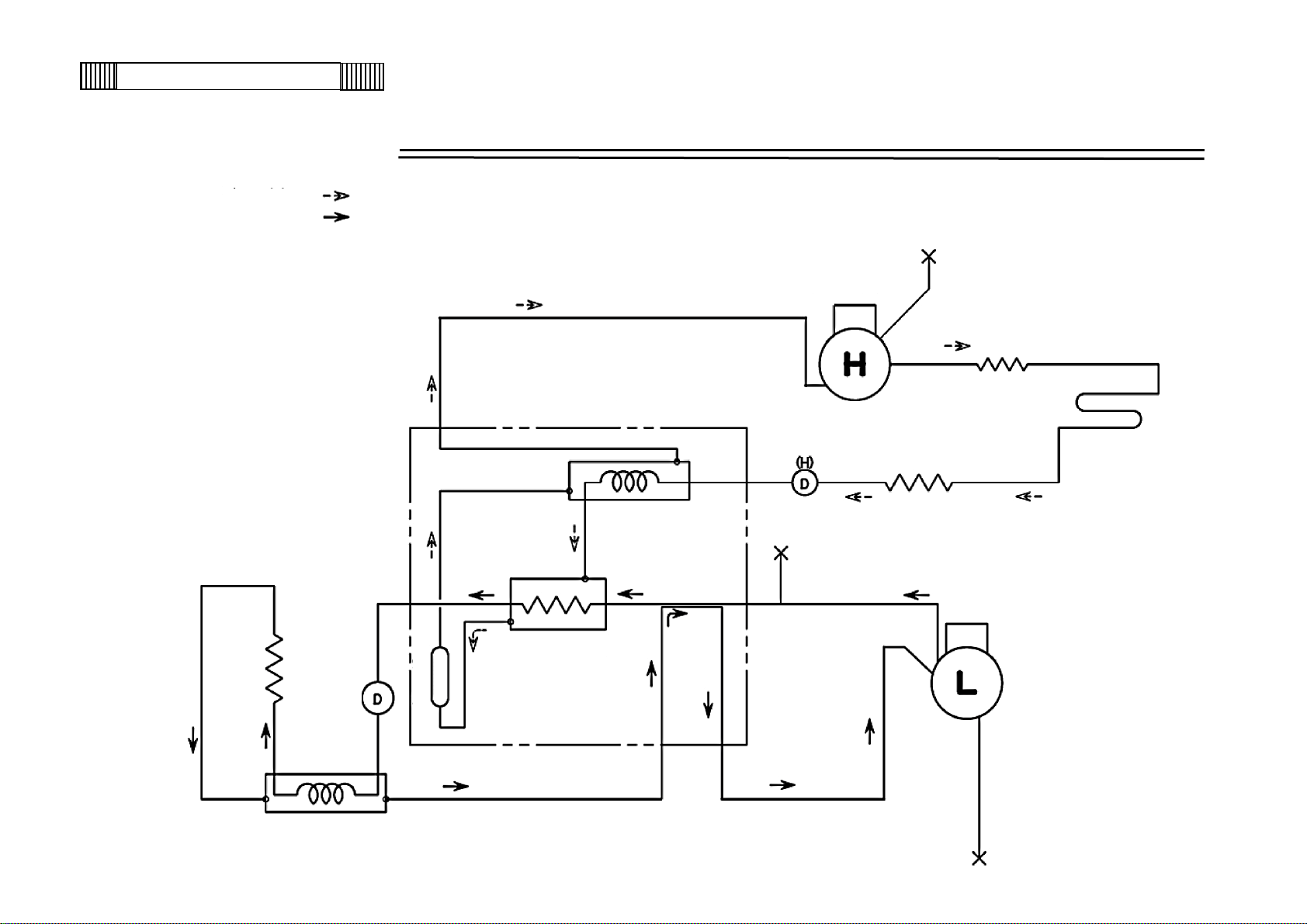
Binary refrigerating cuircuit 〈cascade system〉 〈MDF-DU502VH/DU702VH)
-9-
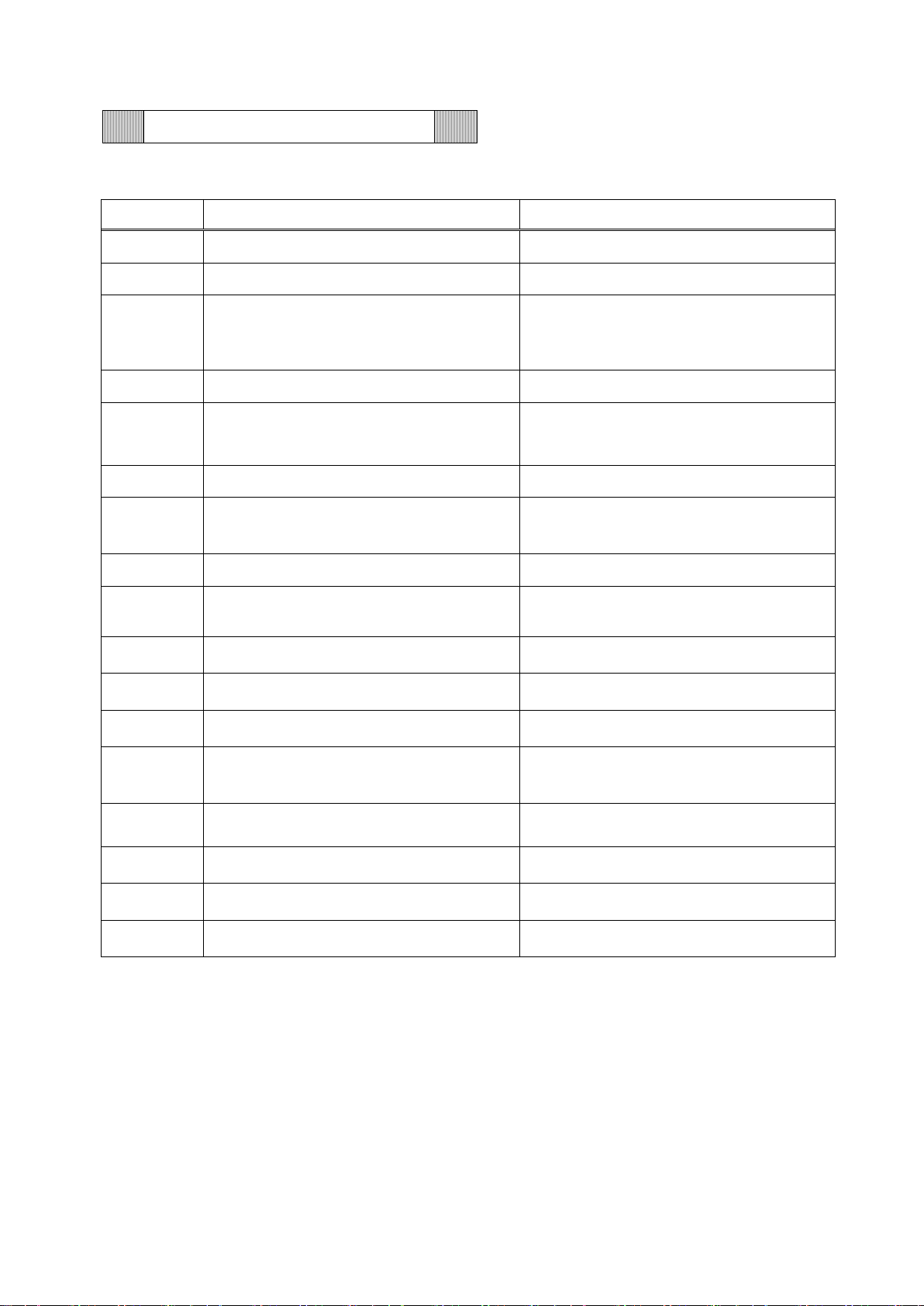
The following shows connections of connector on Main PCB.
#1~#6: MTR-480/MTR-L03 (Option)
To connect with MTR-480/MTR-L03.
Remote alarm terminal
#1: COM
#2: N.O.
#3: N.C.
Remote alarm contact outputs.
To upgrade firmware version
#1,#7:USB PCB
#8,#9:Door switch
To connect with LCD PCB
To detect door open and shut
To control chamber temperature
#1~#2:Cascade sensor
#3~#4:Filter sensor
To detect temperature of cascade
To detect temperature of filter
To detect ambient temperature
#1,#2:Main battery switch
To supply power during power failure
To supply power during power failure
#1~#6:Back-up battery charging PCB
To control battery charging
#1~#3:Inverter L
#3~#6:Inverter H
To control inverter L
To control inverter H
#1,#2: Auto air intake port (AIP) heater
#1,#4:Recorder, Power switch
#1、#3:Fan motor condenser
To control condensing fan motor
-11-
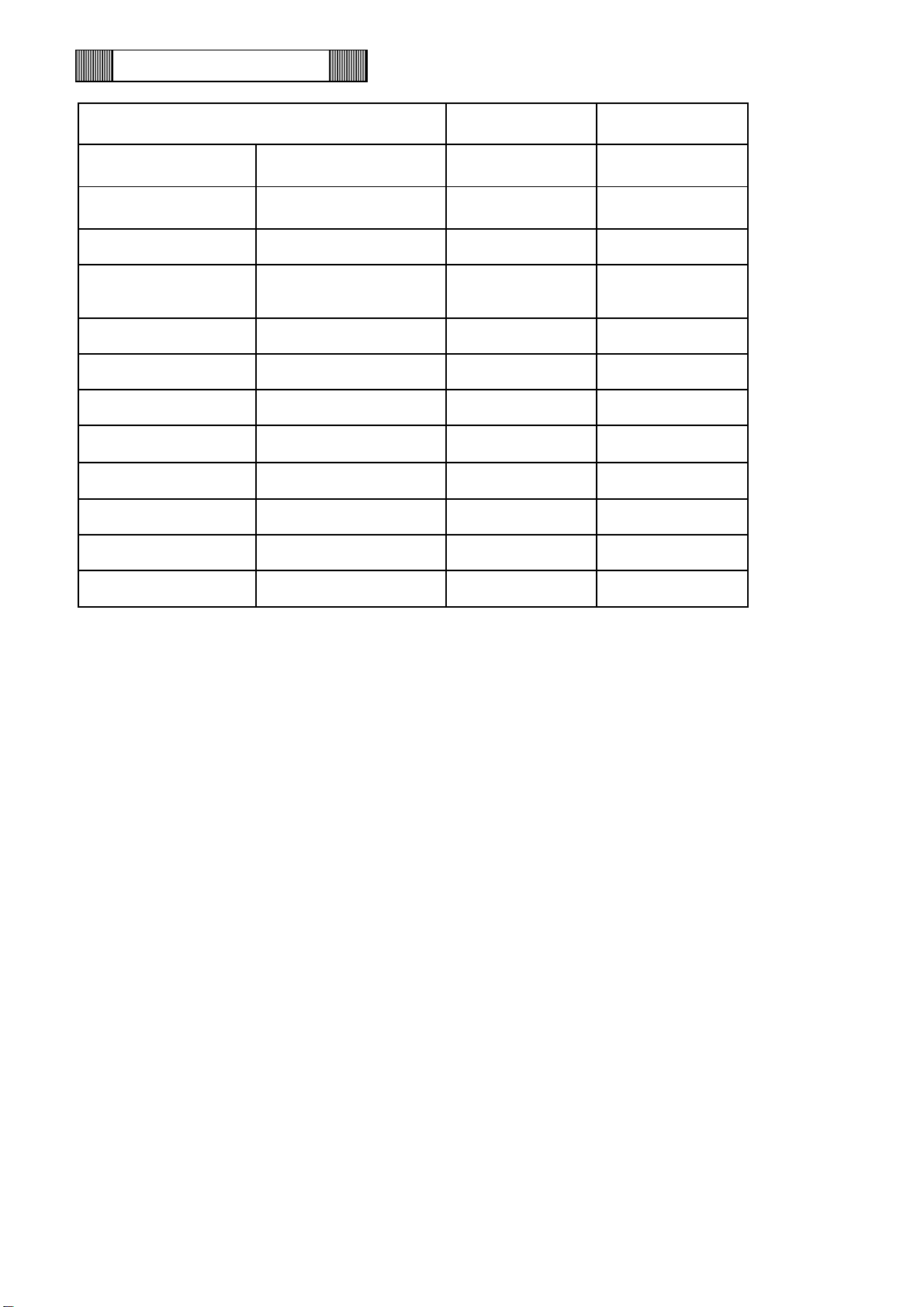
Compressor(A)(B) Type VNEU213U VNEU213U
Rating
220-240 V, 50/60 Hz 220-240 V, 50/60 Hz
Inverter Type VCCHP2456 VCCHP2456
Rating
220-240 V, 50/60 Hz 220-240 V, 50/60 Hz
Condensing fan motor Type SV4-11AB5P SV4-11AB5P
Rating 230 V,10 W 230 V,10 W
Capi. Tube Heater(A),(B) Rating 230V,12W 230V,12W
MDF-DU702VH Resistance(25℃) 4700Ω 4700Ω
Temp. sensoor Type Pt (THC-663) Pt (THC-663)
Cascade sensor Type 502AT-11 502AT-11
Rating 5 kΩ,25 ℃ 5 kΩ,25 ℃
Filter sensor Type 502AT-11 502AT-11
Rating 5 kΩ,25 ℃ 5 kΩ,25 ℃
Door Switch Type SDKNA20700 SDKNA20700
Battery Type LC-P067R2J LC-P067R2J
Rating 6 V 7.2 AH 6 V 7.2 AH
Battery Switch
Type SLE6A2-5 SLE6A2-5
Rating 4 A 250 VAC 4 A 250 VAC
Power Switch Type JW-L21RRK-P4G JW-L21RRK-P4G
Rating 16A, 250VAC 16A, 250VAC
Power Cord Plug U3 250VAC 15A K3 250VAC 16A
-12-
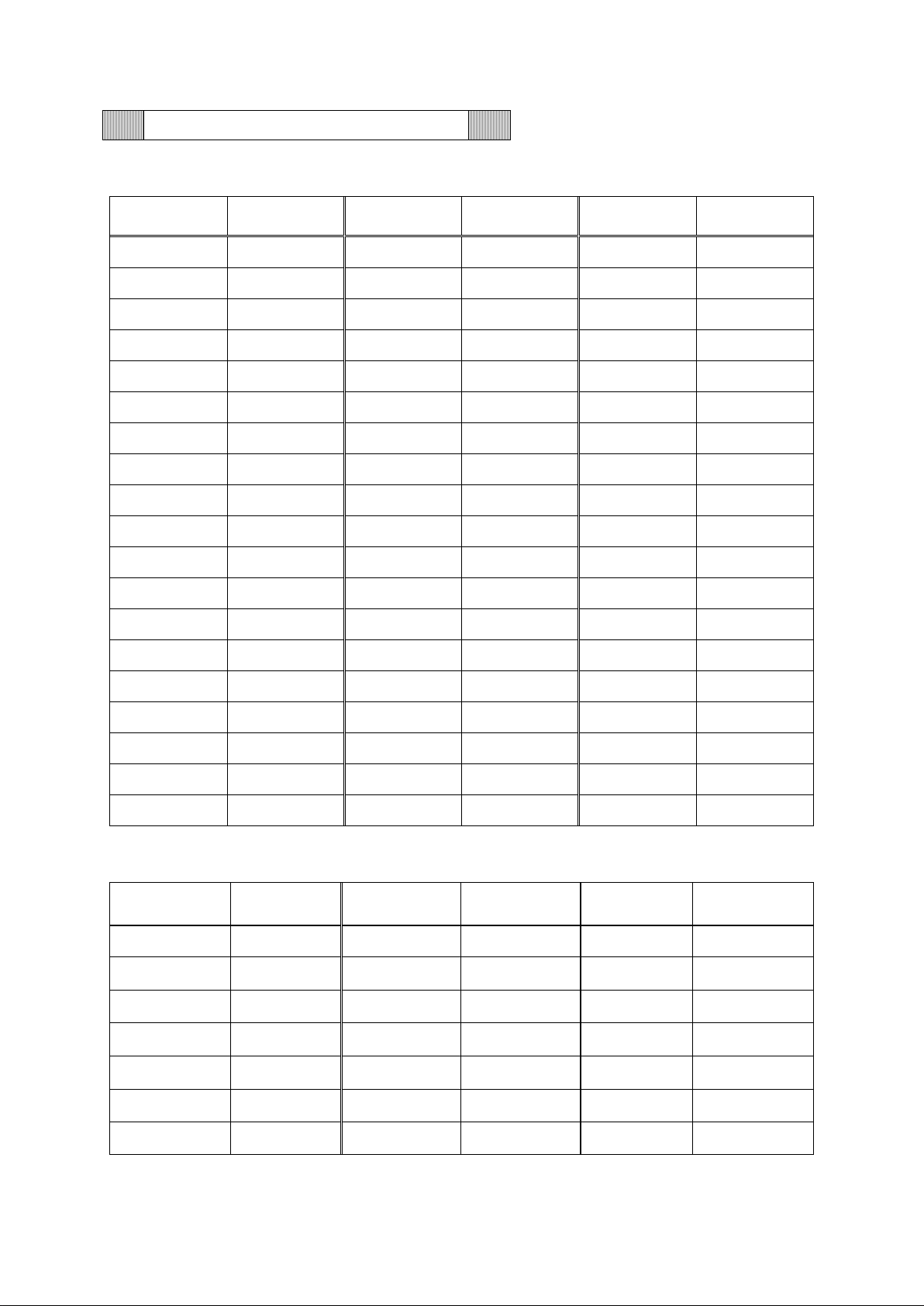
The following shows the temperature in thermal sensor (502AT-11) and its resistance value.
The following shows the temperature in thermal control sensor (PT1000Ω) and its resistance value.
-13-
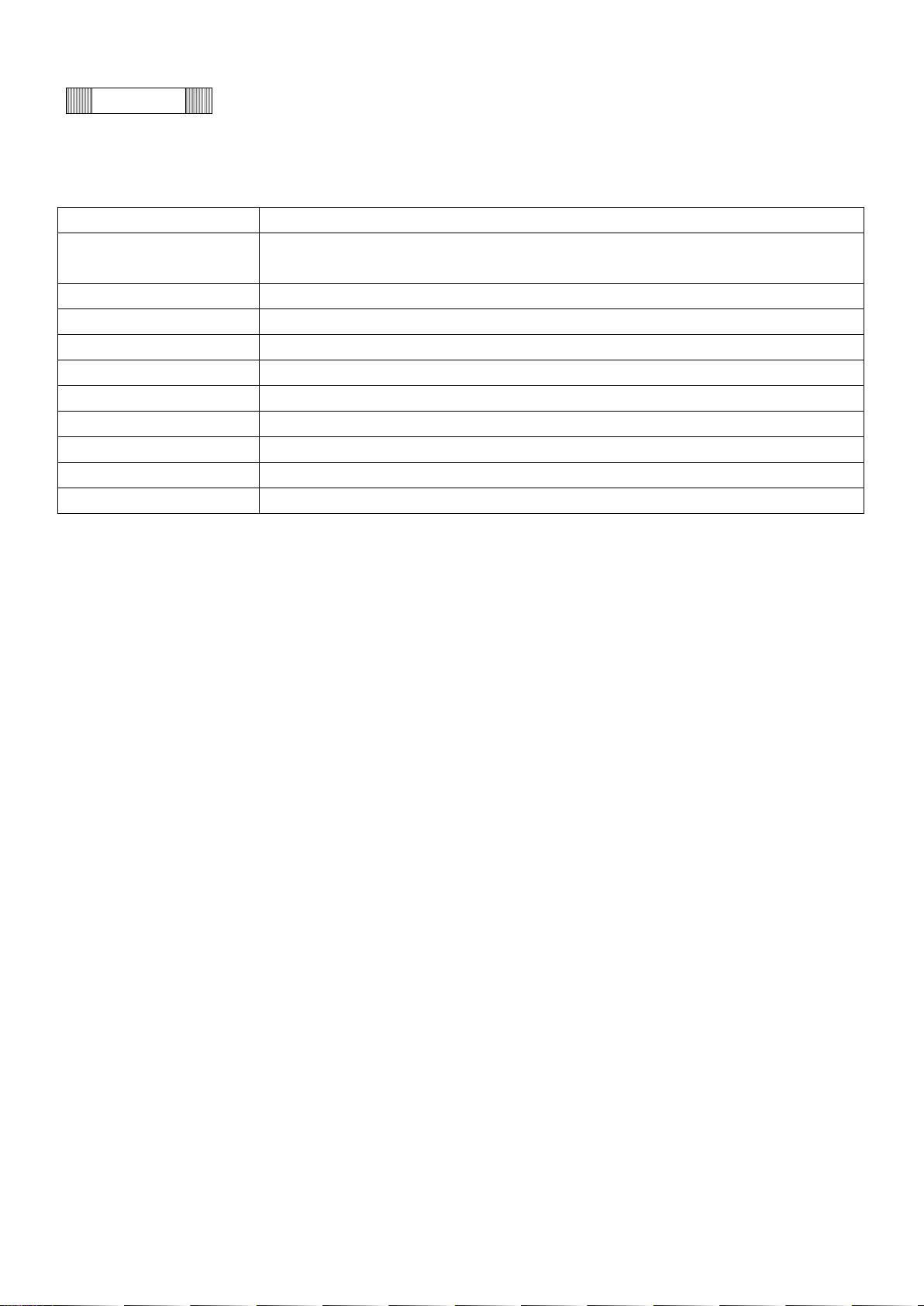
How to operate Service # 1 and Service # 2 on the service menu is described below. For other operations on the LCD, refer
to the instruction manual.
CAUTION) Firmware update, compressor, FAN, and cap heater settings affect basic performance.
Be careful when operating.
Display the accumulate time of Main battery, Backup battery FAN A and FAN B, Reset
them.
Update the firmware of main board and touch panel.
Chamber adjustment method.
Setting Capi. Heater and its timer, compressors, Fan A/B .
Monitoring of chamber temp. , ambient temp, comp. evaporator and fan.
Turning On/Off of AIP heater, and Backup. Setting overload alarm delay..
Initialization of data, and flash memory. Setting model code.
Output of error log data.
Input and output the data.
Turning On/Off Screen Capture, Demo Mode, Self-diagnosis Function and FAN Alarm.
-18-
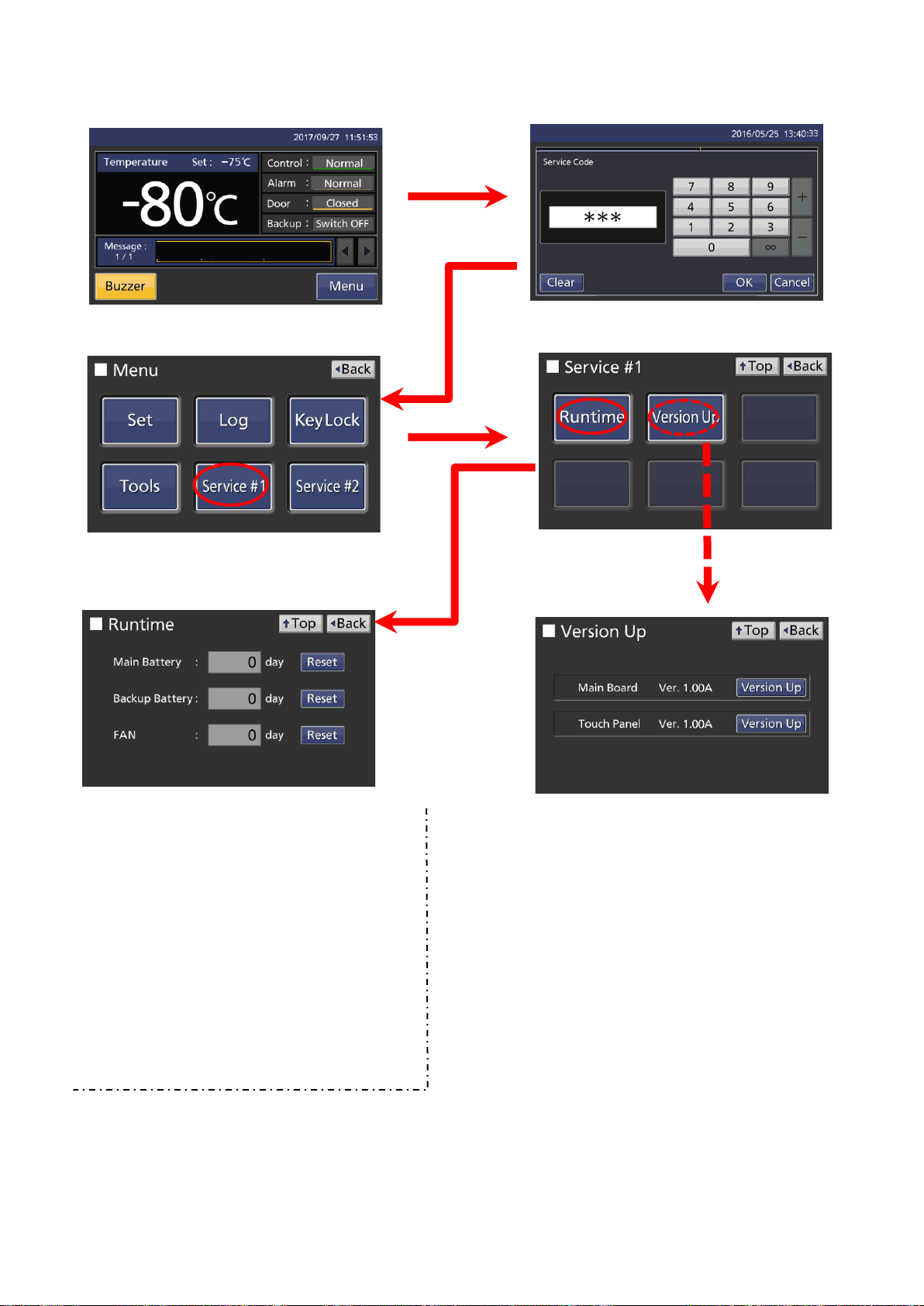
Main Battery
Main Battery accumulated time
Backup Battery
Backup Battery accumulated time
FAN
FAN accumulated time
When each part replace, reset corresponding
data.
・Confirm the existence of file in predefined folder of USB
memory.
・If file is not existence, message “File not found.” is displayed
in “Notice” screen and the process end.
・If file is a existence, if it is not compatible model, "Confirm
firmware" is displayed and the process is terminated. If it is a
compatible model, "Confirm firmware rewrite · · ·" is displayed
and when “Yes” is selected, version upgrade of the touch
panel embedded software is started, and when “No” is
selected, the process is ended.
・During version up, wheel appear in the screen.
・ When version upgrade is completed, "Firmware rewrite
complete. ..." is displayed.
・If an error (other than Verify check) occurs during version
upgrade, "Firmware rewrite failure ... ..." is displayed
・If a Verify error occurs in the Verify check, "Verify check
NG. ..." is displayed.
※When some version up files are plurality, the first found file is used for version up
※During appearance “wheel”, all operations are not able to receive.
※“OK” button in “Result” screen is disable, and all operations are not able to receive.(unless user turn off power)
※“OK” button in “Error” screen is disable, and all operations are not able to received. (unless user turn off power)
※During version up , no communication is not carried out and no log.is not output.
※If you cancel after or during upgrade, restart the main power supply.
Keep touching MENU KEY (5 sec)
Move to Service Code input display, so
input “384” or “335232”
Move to Menu display, touch service #1
key.
Move to Service #1
display, touch Runtime
or Version Up key
Input “384”,
only can check
the firmware
version.
-19-
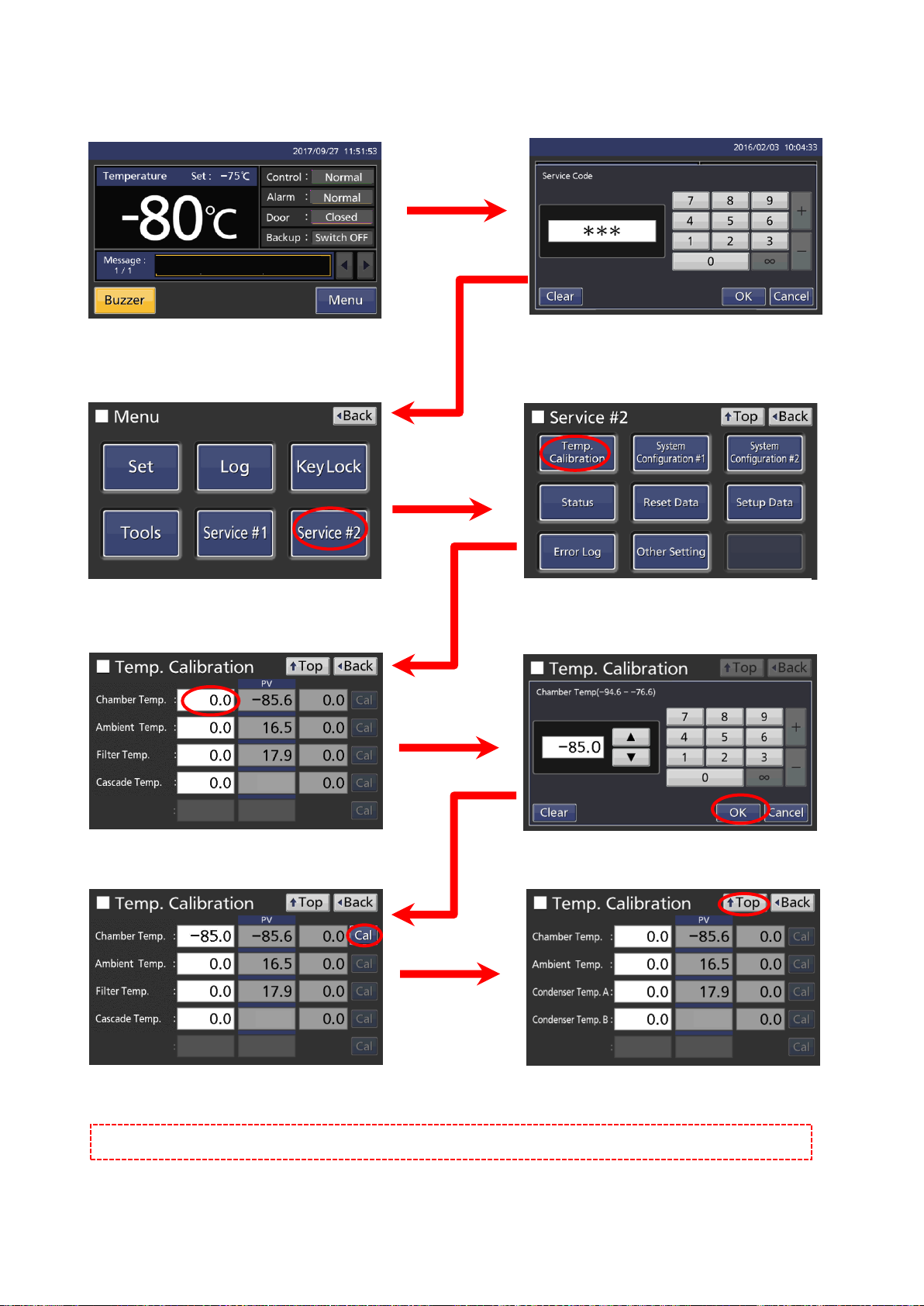
(Temperature calibration procedure:chamber sensor)
Cal key is vialed within setting range, touch
Cal key.
Move to Menu display, touch Service #2
key.
Move to Service display, touch Temp.
Calibration key
Move to input value display.
Input measured value by thermometer
Touch TOP key, so return to Menu display.
Input value area return to zero.
NOTE:: Ambient Temp. sensor and condenser A&B sensor can calibrate in the same procedure.
Keep touching MENU KEY (5 sec)
Move to Service Code input display,
so input “335232”
-20-
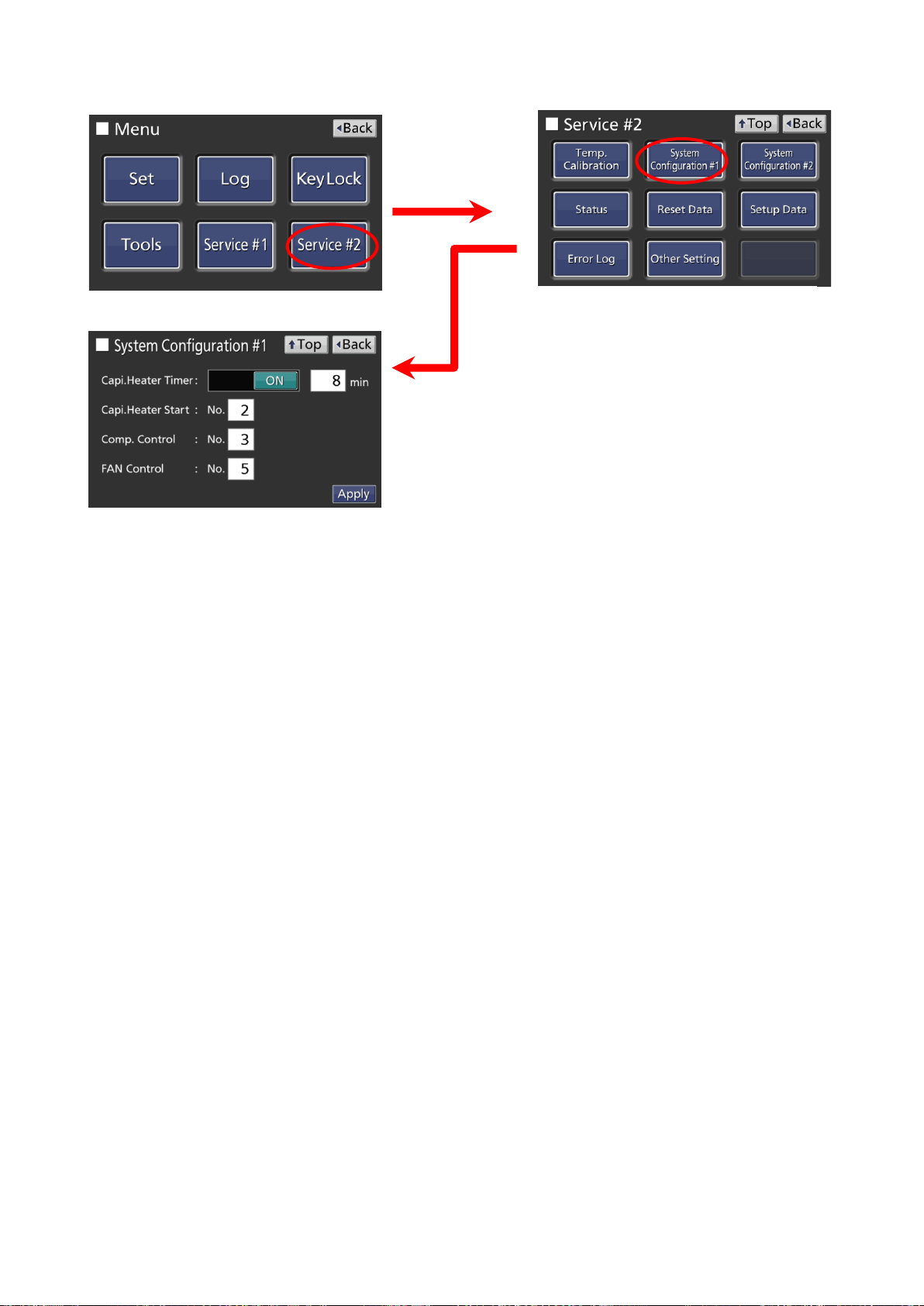
(Operation System Configuration #1)
■
Capi. Heater Timer
Slide key ON(enable),
setting time(Default 8 min).
Capi. Heater Start
Capi. heater control setting
(0) Heater on once in 18 hours
(1) Force on now
(2) Force off now(default)
Comp. Control
Compressor control setting
(0)Off
(1)On
(2)Auto(default)
(3)Manual
FAN control setting
(0) Off
(1) On
(2) Auto(default)
Refer to Control Specification for Capi. Heater Start,
Comp. Control, FAN Control.
Move to Menu display, touch Service #2 key.
Move to Service display, touch System
Configuration #1 key
-21-