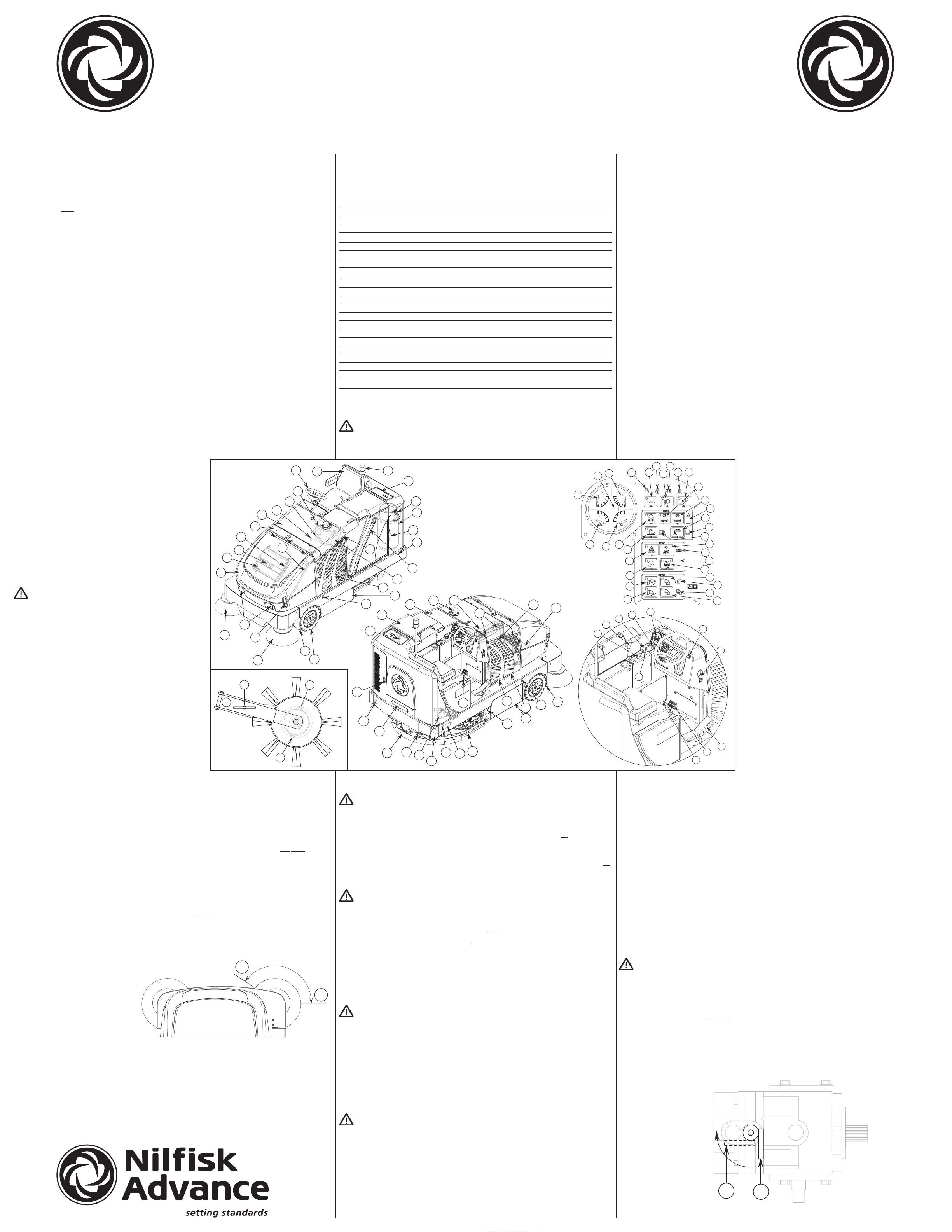
Captor
CR 1100, 1200, 1400 (LPG, Petrol & Diesel)
MAINTENANCE GUIDE
for
™
4300, 4800, 5400 (LPG, Petrol & Diesel)
AFTER USE
1 Raise the squeegee, the scrub brushes, and the brooms.
2 Shake the dust control fi lter and empty the hopper.
3 Drain and fl ush the recovery tank.
4 Flush the vacuum hose and squeegee by opening the recovery tank lid and running water down the pickup
tube on the right side of the tank. SERVICE NOTE: Tip the recovery tank out and check the squeegee hose
elbow below the tank to make sure it has fl ushed out completely.
5 Remove and clean the squeegee tool.
6 Remove and clean the scrub brushes. Rotate the scrub brushes.
7 Wipe the machine with a damp cloth.
8 Perform all required maintenance before storage.
9 Move the machine to a clean, dry storage area.
10 Store the machine with the brooms, the squeegee and the scrub brushes in the UP position, and the tank
covers open so that the tanks can air out.
REPORT ANY DEFECT OR MALFUNCTION NOTED DURING OPERATION TO AUTHORIZED SERVICE OR
MAINTENANCE PERSONNEL.
SHUTTING DOWN THE DIESEL / GASOLINE ENGINE
1 Put all controls to the OFF position.
2 Raise the squeegee, the scrub brushes, and the brooms.
3 Push the Engine Speed Switch (G) to change to “Idle” speed and let the engine idle for 30 seconds.
4 Apply the Parking Brake (GG).
5 Turn the Key Ignition Switch (MM) OFF and remove the key.
SHUTTING DOWN THE PROPANE ENGINE
1 Put all controls to the OFF position.
2 Raise the squeegee, the scrub brushes, and the brooms.
3 Turn the service valve on LP gas tank OFF.
4 Push the Engine Speed Switch (G) to change to “Idle” speed and let the engine idle until all the LP gas is
dispelled from the line.
5 Apply the Parking Brake (GG).
6 Turn the Key Ignition Switch (MM) OFF and remove the key.
24
MAIN BROOM MAINTENANCE
Since the Main Broom Motor always turns in the same direction, the bristles
on the broom eventually become curved, reducing sweeping performance.
Sweeping performance can be improved by removing the broom and turning
it around (end-for-end). This procedure, known as “rotating” the main broom,
should be done once every 30 hours of operation.
The main broom should be replaced when the bristles are worn to a length
of 2-1/2 inches (6.35 cm). The main broom stop (JJ) must be re-adjusted
when the broom is replaced. NOTE: Bristle length on a new broom is
3-1/4 inches (8.25cm).
NOTE: The machine should be stored with the Main Broom in the raised
position.
46
45
22
49
21
20
19
18
12
1
23
WARNING!
The engine must not be running when performing this
procedure.
To Rotate or Replace the Main Broom...
1 Turn the Ignition Key Switch (MM) OFF.
2 Put the Main Broom Raise / Lower (ON / OFF) Lever (II) in the
DOWN position.
3 Open the Main Broom Right Access Door (38).
4 See Figure 1. Remove the large T-Bolt (A1) from the side of
Figure 1
the broom idler arm. Pivot the idler arm assembly out of the
main broom core.
5 Pull the main broom out of the broom housing and remove any
string or wire wrapped around it. Also inspect the skirts at the
front, back and sides of the broom housing. The skirts should
be replaced or adjusted if they are torn or worn to a height of
more than 1/4 inch (6.35 mm) off the ground.
6 Turn the broom around (end-for-end) and slide it back into the
broom housing. Make sure that the Lugs (B1) on the broom
drive hub (left side of machine) engage the slots in the broom
core.
7 Swing the idler arm assembly back into the broom core and re-install the T-Bolt that holds the idler arm in
place.
8 Close and latch the Main Broom Right Access Door (38).
To Adjust the Main Broom Height...
1 Drive the machine to an area with a level fl oor and set the parking brake (GG).
2 Pull the Main Broom Raise / Lower (ON/OFF) Lever (II) back and slide to the right and up to lower the main
broom. Push lightly on the front of the Drive Pedal (OO) to start the main broom rotating. DO NOT move the
machine.
3 Let the main broom run in place for 1 minute. This allows the broom to polish a “strip” on the fl oor. After 1 minute,
raise the broom, release the parking brake and move the machine so that the polished strip is visible.
4 Inspect the polished strip on the fl oor. If the strip is less than 2 inches (5.08 cm) or more than 3 inches (7.62cm)
wide, the broom needs to be adjusted.
5 To adjust, loosen the Main Broom Adjust Knob (JJ) and slide forward or backward to lower or raise the Main
Broom. The farther the Knob (JJ) travels up in the slot, the lower the Main Broom will be. Tighten Knob (JJ)
after adjustment is complete.
6 Repeat steps 1-5 until the polished strip is 2-3 inches (5.08-7.62cm) wide.
The width of the polished strip should be the same at both ends of the broom. If the strip is tapered, move
the machine to a different area and repeat steps 1-5. If the polished strip is still tapered, contact your Nilfi sk-
Advance Dealer for service.
Figure 2
SIDE BROOM MAINTENANCE
The side broom(s) move dirt and debris away
from walls or curbs and into the path of the main
broom. Adjust the side broom so that the bristles
are contacting the fl oor from the 10 O’clock (A2)
to the 3 O’clock (B2) area shown in fi gure 5 when
the broom is down and running.
To adjust the Side Broom...
1 The side broom(s) are adjusted simply by pressing and holding the Side Broom DOWN/ON Switch (N) or the
Side Broom UP/OFF Switch (Y) until the desired amount of bristles are contacting the fl oor.
NOTE: The machine should be stored with the Side Broom(s) in the raised position. The Side Broom(s) should be replaced
when the bristles are worn to a length of 3 inches (7.62 cm) or they become ineffective.
To replace the Side Broom...
1 Raise the Side Broom(s).
2 Reach under the Side Broom and remove the large Thumb-Nut holding the side broom on and remove the
broom and plastic disc.
3 Install the new broom and plastic disc by aligning the three alignment pins and pushing on. Re-install the
Thumb-Nut and tighten.
16
17
A1
15
44
14
B1
13
B1
A2
B2
MAINTENANCE SCHEDULE
Keep the machine in top condition by following the maintenance schedule closely. Maintenance
intervals given are for average operating conditions. Machines used in severe environments
may require service more often.
MAINTENANCE ITEM PERFORM DAILY
Perform the “After Use” maintenance steps X
Check parking brake X
Check engine oil X
*Clean main and side brooms X
Check fi lter indicator and lights (hyd & air) X
Check engine coolant level X
Check hydraulic oil level X
MAINTENANCE ITEM 15 hrs. 30 hrs. 150 hrs. 300 hrs. 500 hrs. 1000 hrs.
*Rotate main broom X
Clean solution fi lter X
*Inspect/adjust brooms X
*Clean hopper fi lter X X X
*Inspect broom housing skirts X
*Inspect hopper seals X
Clean radiator and oil cooler X
Perform engine maintenance X
*Inspect and grease steering rack X
Change the hydraulic “charge” oil fi lter X
Change reservoir hydraulic oil and fi lter X
Flush the radiator X
Engine fuel fi lter(s) gas or propane X
*See the Mechanical Repair Service Manual and Operator Manual for detailed maintenance
information of systems listed. (Sweeping, Hopper, Steering, Dust Control, Squeegee)
WARNING!
Turn the key switch off, set the parking brake and disconnect the battery before servicing
the machine.
29
28
2
3
4
5
47
48
9
10
6
30
50
27
26
6
7
8
33
41
43
32
35
34
51
42
40
6
11
39
37
38
6
31
25
DD
36
44
CC
EE
PP
F
1/2
E
HOURS 1/10
OIL
PSI/BAR
100
8
50
3
1
0
BB
II
HH
HYDRAULIC OIL
WARNING!
To avoid hydraulic oil injection or injury, always wear appropriate clothing and eye protection
when working with or near hydraulic system.
Check the Hydraulic Oil Level. Remove the Right Engine Access Panel (37) and look at the
gauge on the side of the reservoir. If the oil level is below the minimum level, add 10W30 motor
oil until the gauge is 3/4 full. Do not fi ll above maximum. Change the oil if major contamination
from a mechanical failure occurs. SERVICE NOTE: Remove the small access panel (49)
directly above the reservoir to add oil. This panel is held on by (2) wing nuts on the underside
of the panel. Only fi ltered oil should be added.
IMPORTANT!
This machine is equipped with an indicator light which lights if the “In Tank” oil fi lter requires
changing. Remove fi lter element from the fi lter cup and replace with new fi lter. Hydraulic
fi lter is found on top of the Hydraulic Reservoir (36).
Change the Hydraulic “Charge” Oil Filter (35).
Note: Oil should be warm, cold oil is thicker and may cause the light to come on intermittently
until it warms up.
ENGINE COOLANT
Lift the Engine Cover (22) and observe the coolant level in the Coolant Recovery Tank (23). If the level is low,
add a mixture of half water and half automotive type anti-freeze.
CAUTION!
Do not remove the radiator cap when the engine is hot.
LUBRICATING THE MACHINE
Steering Rack
Once every 150 hours pump a small amount of grease onto the steering rack and pinion
components.
Also every 150 hours apply light machine oil to maintain free movement of all general pivot points.
Example the seat, and broom door hinges etc. Broom, squeegee and hopper pivots use composite
bearings lubrication is not required.
WARNING
For the protection of the environment; when servicing any of the machine’s lubrication fl uids they
must be disposed of safely in accordance with your local environmental regulations (recycling).
Examples of machine lubrication products: (Engine crankcase oil, Engine crankcase oil fi lter,
Hydraulic system oil, Hydraulic system oil fi lters).
KNOW YOUR MACHINE
1 Operator’s Seat
2 Strobe Light (optional)
3 Solution Tank Fill
4 Gasoline Tank Cap
5 Fuel Tank
6 Tie Down Locations
7 Recovery Tank Drain Hose
8 Engine Air Filter
9 Left Engine Compartment Access Panel
10 Main Broom Left Access Door
11 Battery
12 Hopper Lid Prop Rod
13 Front Wheel
14 Left Side Broom
15 Hopper Lid Latch
16 Headlights
17 Right Side Broom
18 Hopper Cover
19 Dust Control Filter
20 Dust Control Shaker Assembly
21 Shaker Assembly Latch
KNOW YOUR MACHINE (CONTINUED)
31 Recovery Tank “Tip-Out” Grip
32 Engine Air Filter Hood
33 Radiator Cap
34 Oil Cooler “Tip-Out” Latches
35 Hydraulic “Charge” Oil Filter
36 Hydraulic Reservoir / In Tank Return Oil Filter
37 Right Engine Compartment Access Panel
38 Main Broom Right Access Door
39 Access Door Latch
40 Skirt Assembly
41 Inline Solution Filter
42 Solution Tank Drain Hose
43 Rear Roller Bumper
44 Jacking Location
45 Engine Oil Dipstick
46 Air Filter Service Indicator
47 Fuel Filter (Gas Models)
48 Recovery Tank Latch
49 Hydraulic Reservoir Access Panel
50 Water Level Gauge
51 Operator Seat Adjustment Lever
22 Engine Compartment Door
23 Coolant Recovery Tank
24 Steering Wheel
25 Squeegee Handle
26 Squeegee Tool Assembly
27 Tail Light
28 Exhaust Tail Pipe
29 Fuel Tank Compartment Door
30 Recovery Tank Lid
OPERATOR’S COMPARTMENT
A Low Fuel Indicator (LP)
B Horn Switch
C Engine Service Indicator (triggered by ECU)
D Headlight Switch
E Glow Plug Indicator (Diesel / Release key after indicator
turns OFF)
F Hydraulic Filter Plugged Indicator
G Engine Speed Switch
H Scrub Pressure Decrease Switch
I Scrub Pressure Increase Switch
J Scrub Pressure Display
K Solution Switch
L Solution Tank Empty Indicator
M Recovery Tank Full Indicator
N Side Broom DOWN/ON Switch
O Main Broom ON Indicator
P Light Sensor
Q Shaker Switch
* Dust Filter Plugged Indicator (right)
R Open Dump Door Switch
S Hopper Open Indicator
T Hopper Overtemp Indicator
U Close Dump Door Switch
V Lower Hopper Switch
W Raise Hopper Switch
X Dust Control Switch
Y Side Broom UP/OFF Switch
120
AA
C
E
G
B
A
+
18
13
10
VOLTSFUEL
TEMP
F/C
250
100
175
75
50
Z
Y
X
W
V
LL
KK
JJ
F
D
H
I
J
K
L
M
N
O
P
Q
R
S
T
U
MM
Z Vacuum System Switch
NN
AA Scrub System OFF Switch
BB Coolant Temperature Gauge
CC Oil Pressure Gauge
QQ
DD Fuel Gauge (Gas / Diesel)
EE Voltmeter
FF Brake Pedal
GG Parking Brake Latch
HH Solution Flow Control Lever
II Main Broom Raise/Lower (ON/OFF) Lever
JJ Main Broom Adjust Knob
KK Hopper Safety Support Lever
LL Control Panel
MM Ignition Switch
GG
OO
FF
NN Tilt Wheel Lever
OO Drive Pedal
PP Hour meter
QQ Main Broom Overload Indicator Light
ROUTINE ENGINE MAINTENANCE
• Keep the fuel tank fi lled. This helps to reduce condensation and moisture entering the fuel system (gasoline & diesel).
• Repair any oil or coolant leaks immediately.
• Check condition of battery (water level) and cables weekly.
• Observe the engine coolant temperature gauge frequently.
• Observe the engine oil pressure gauge frequently.
• Check the voltmeter and charging system.
ENGINE MAINTENANCE (150 HOURS)
At 150 hour intervals it is recommended that the following service be performed: Change oil and fi lter, clean and inspect spark
plugs, check all engine belts condition and adjustment, check battery charge and level, check cooling system hoses and clamps,
check engine air cleaner fi lter and hoses, and check general condition and performance of engine.
Note: Reference the separately supplied PSI GM Power Train Products Operation and Maintenance manual for more detailed
service data. PSI manual number is 3610000.
TOWING OR PUSHING A DISABLED MACHINE
CAUTION!
The machine’s drive propelling pump is manufactured with an adjustable tow valve. This valve prevents
damage to the hydraulic system when the machine is being towed/pushed short distances without use
of the engine.
To access the valve, open the Engine Compartment Door (22) and lift off the Right Engine Compartment Access Panel (37).
Locate the valve as shown on the underside of the hydrostatic pump by reaching under the radiator. Turn the valve 90 degrees;
this disengages the hydrostatic lock between the motor and pump.
The hydrostatic pump can be damaged if the machine is towed with the valve in the normal working position (A3). Reference
the illustration below for the normal working setting (A3) and the free wheeling towing setting (B3). Note: If the tow valve is left
in free wheeling (B3) position the hydrostatic pump can’t drive the machine FWD or REV. No damage will result, just re-set
valve to the normal working setting (A3). Tow or push machine no faster than a normal walking pace (2-3 miles per hour) and
for short distances only. If the machine is to be moved long distances the rear drive wheel needs to be raised off the fl oor and
placed on a suitable transport dolly.
Figure 3
B3
A3
8/05 Form No. 56043104© 2005, Nilfi sk-Advance, Inc.