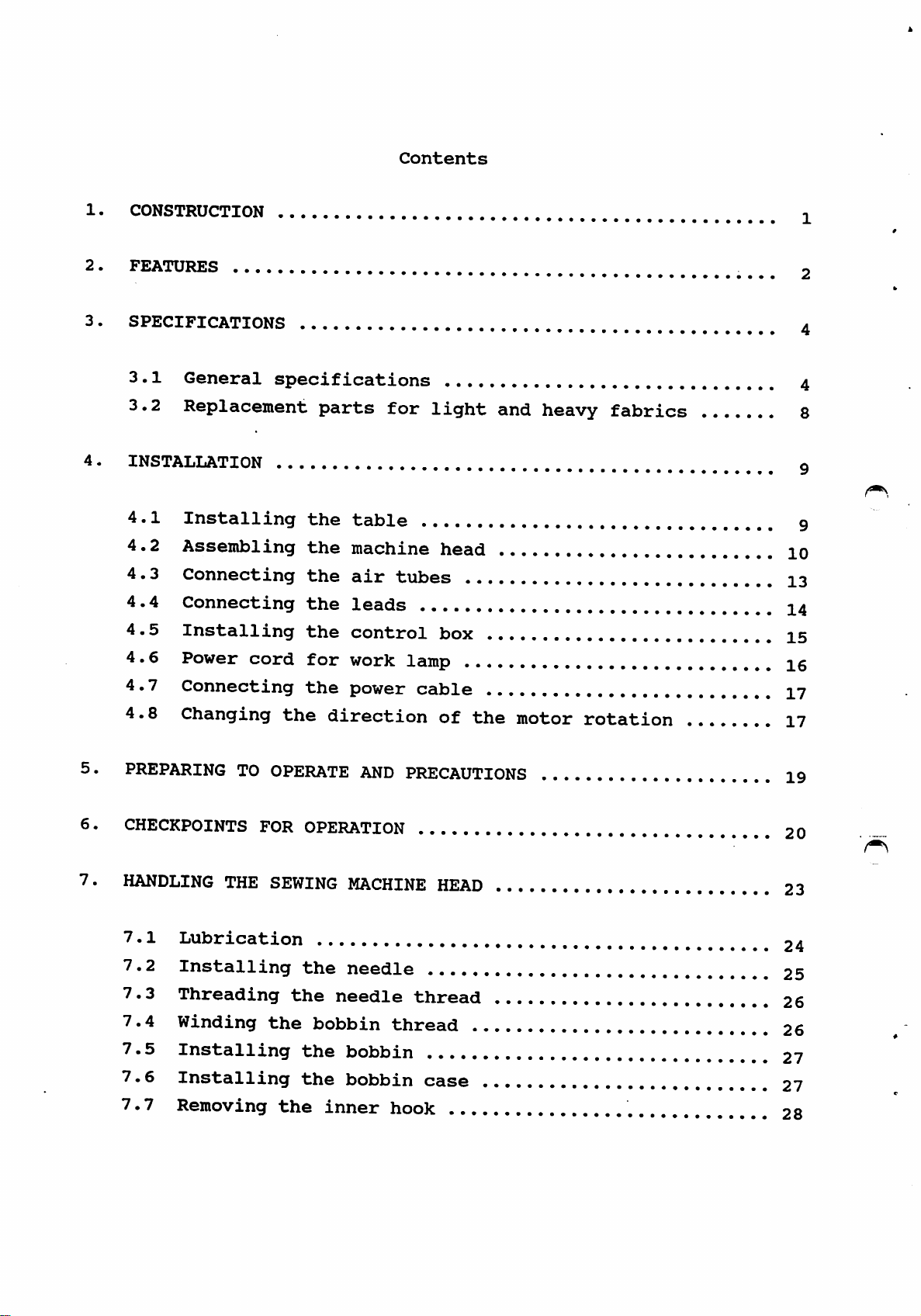
Contents
1.
CONSTRUCTION
2.
FEATURES
3.
SPECIFICATIONS 4
3^
^^ 2
3.1
3.2
4.
INSTALLATION
4.1
4.2
4.3
4.4
4.5
4.6
4.7
4.8
5.
6.
PREPARING
CHECKPOINTS
General
Replacement
Installing
Assembling
Connecting
Connecting
Installing
Power
Connecting
Changing
specifications
cord
the
TO
OPERATE
FOR
parts
the
the
the
the
the
for
the
direction
for
table
machine
air
tubes
leads
control
work
power
lamp 16
AND
PRECAUTIONS
OPERATION
light
head
box
cable
of
the
and
motor
heavy
rotation
fabrics
4
8
9
9
10
13
14
15
17
17
19
20
7.
HANDLING
7.1
7.2
7.3
7.4
Threading
Winding
7.5
7.6
7.7
Installing
Removing
THE
SEWING
Lubrication
Installing
the
Installing
the
the
the
needle
bobbin
the
the
inner
MACHINE
HEAD
needle
thread
thread
bobbin
bobbin
case
hook 28
23
24
25
26
26
27
27
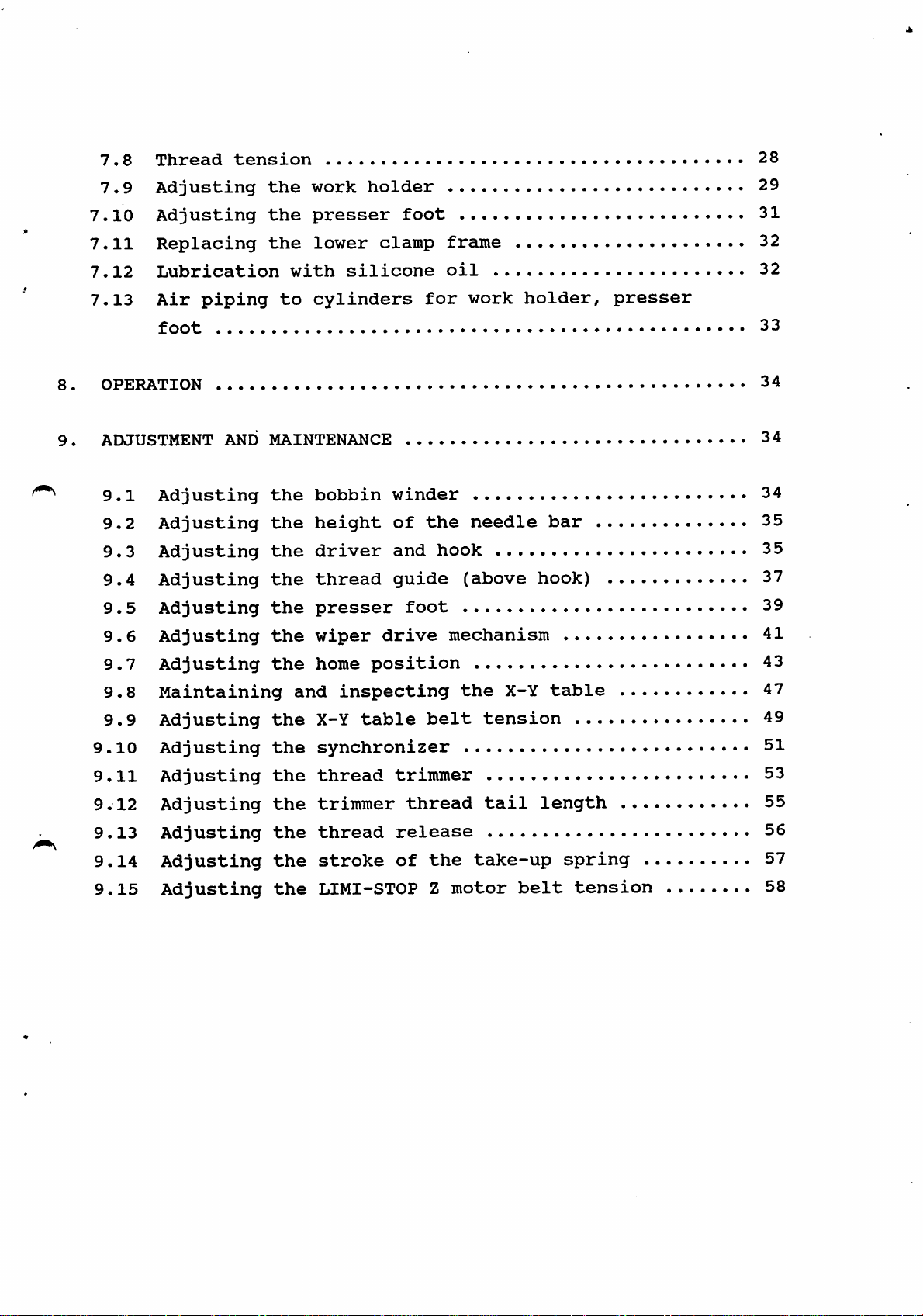
7.8
Thread
tension
28
7.9
7.10
7.11
7.12
7.13
8.
OPERATION
9.
ADJUSTMENT
^
9.1
9.2
9.3
9.4
9.5
9.6
Adjusting
Adjusting
Replacing
Lubrication
Air
piping
foot
AND MAINTENANCE
Adjusting
Adjusting
Adjusting
Adjusting
Adjusting
Adjusting
the
the
the
to
the
the
the
the
the
the
work
presser
lower
with
cylinders
bobbin
height
driver
thread
presser
wiper
holder
clamp
silicone
drive
foot
for
winder
of
the
and
hook
guide
foot
frame
oil
work
holder,
needle
(above
mechanism
bar
hook)
29
31
32
32
presser
33
34
34
34
35
35
37
39
41
^
9.7
9.8
9.9
9.10
9.11
9.12
9.13
9.14
9.15
Adjusting
Maintaining
Adjusting
Adjusting
Adjusting
Adjusting
the
the
the
the
the
home
and
X-Y
position
inspecting
table
synchronizer
thread
trimmer
trimmer
thread
belt
Adjusting the thread release
Adjusting
Adjusting
the
stroke
the
LIMI-STOP Z
of
the
motor
the
tension
tail
take-up
X-Y
belt
table
length
spring
tension
43
47
49
51
53
55
56
57
58
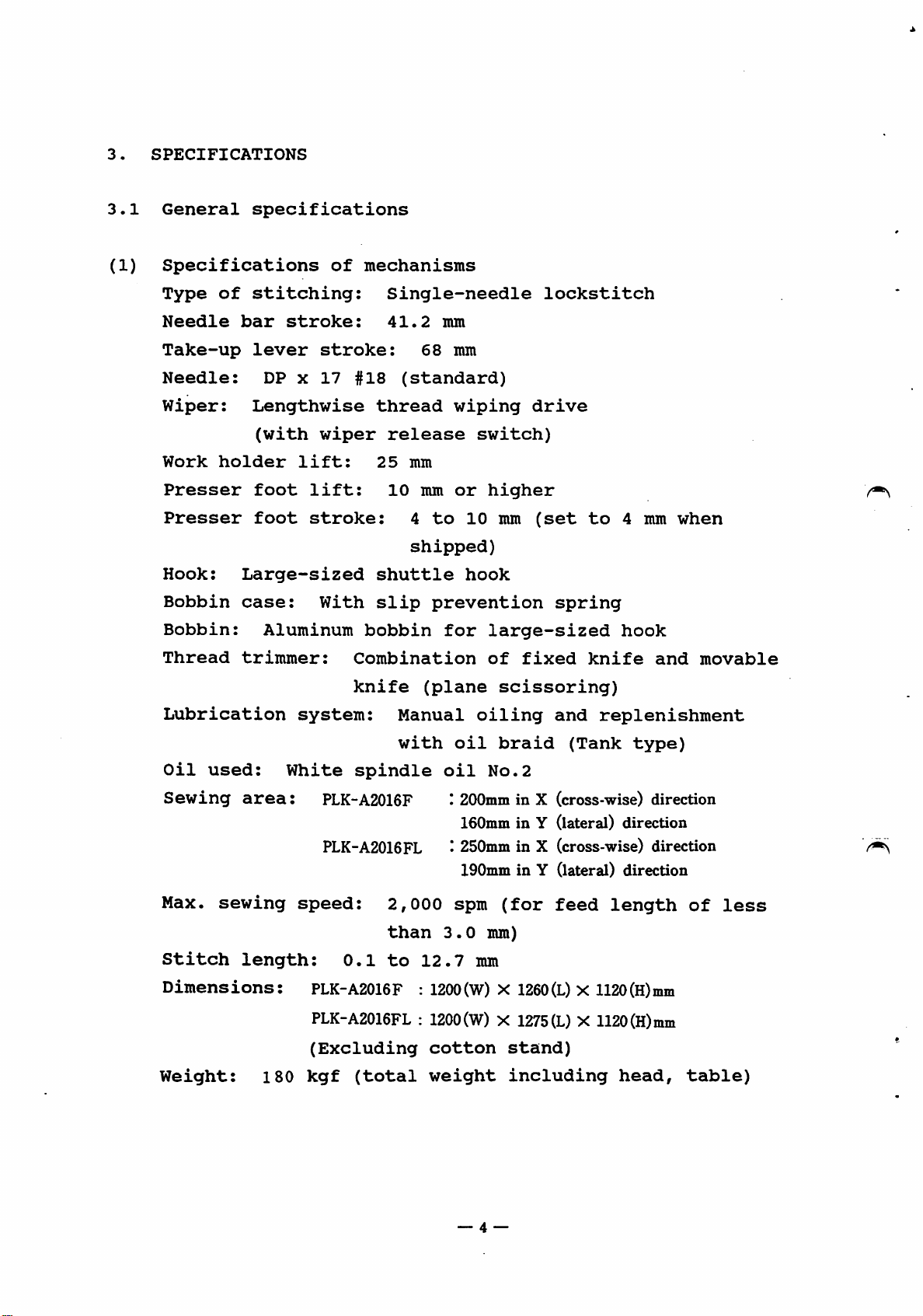
3.
SPECIFICATIONS
3.1
(1)
General
specifications
Specifications
Type
Needle
Take-up
Needle:
Wiper:
Work
Presser
Presser
Hook:
Bobbin
of
stitching:
bar
lever
Lengthwise
(with
holder
foot
foot
Large-sized
case:
Bobbin:
Thread
trimmer:
of
stroke:
stroke:
DP x
17
wiper
lift:
lift:
stroke:
With
Aluminum
mechanisms
Single-needle
41.2
68
#18
(standard)
thread
release
25
mm
10
mm
4
shipped)
shuttle
slip
bobbin
Combination
mm
mm
wiping
switch)
or
higher
to
10
mm
hook
prevention
for
large-sized
of
lockstitch
drive
(set
spring
fixed
to
knife
4
mm
hook
and
^
when
movable
Lubrication
Oil
used:
Sewing
Max.
Stitch
area:
sewing
length:
Dimensions:
Weight:
White
ISO
knife
system:
spindle
(plane
Manual
with
oil
oiling
oil
scissoring)
braid
No.2
and
replenishment
(Tank
type)
PLK-A2016F *200mm in X (cross-wise) direction
160mm in Y (lateral)
PLK-A2016FL 250mm in X (cross-wise) direction
speed:
0.1
2,000
than
to
12.7
190mm in Y
spm
3.0
mm)
mm
(for
(lateral)
feed
direction
direction
length
PLK-A2016F:1200(W)X1260(L)X1120(H)mm
PLK-A2016FL:1200
(Excluding
kgf
(total
(W)X1275
cotton
weight
(L)X1120(H)
stand)
including
mm
head,
of
table)
less
— 4 —
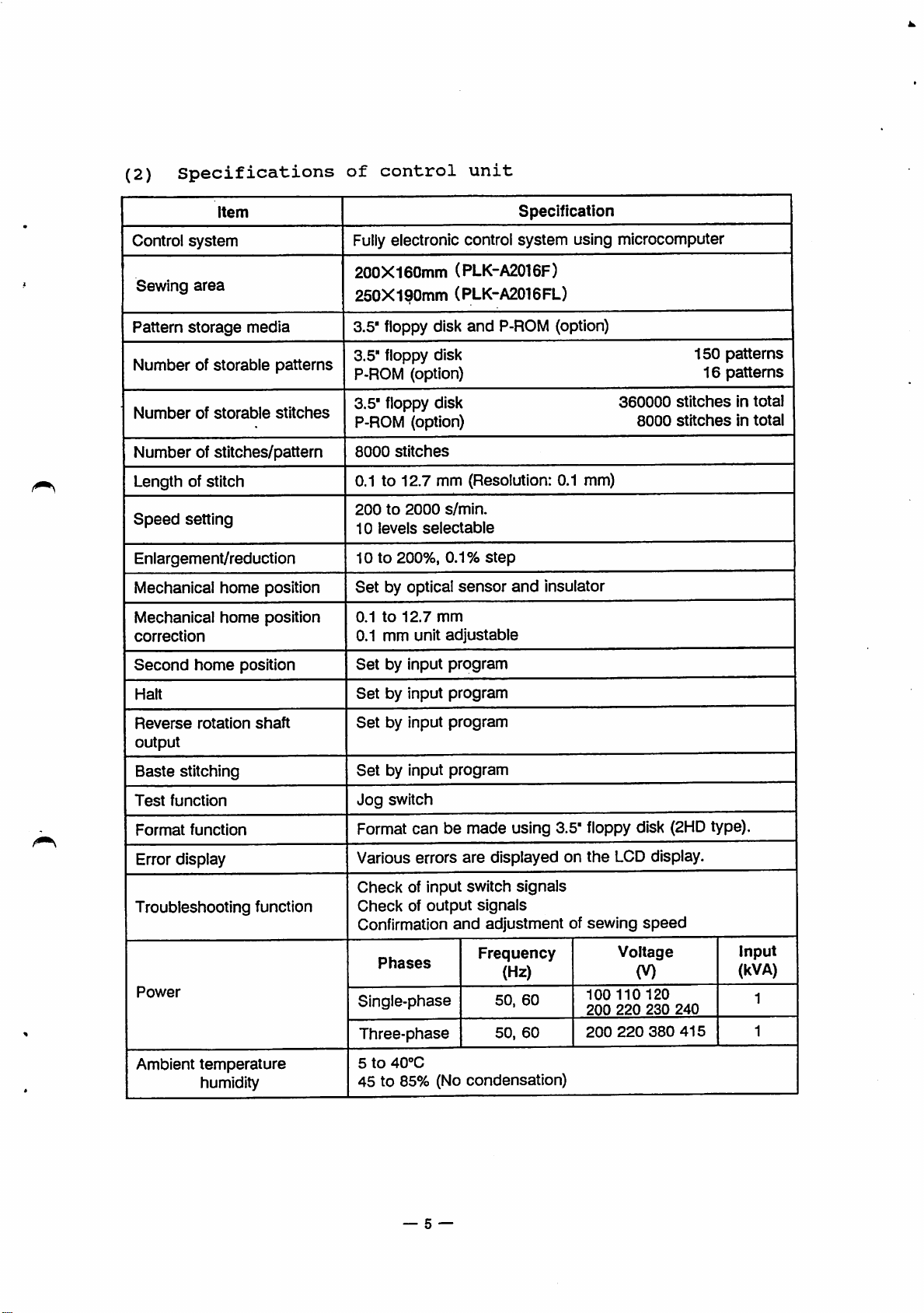
(2)
Specifications
of
control
unit
Item
Control
Sewing
Pattern
Numberofstorable
Number
system
area
storage
of
storable
media
patterns
stitches
Numberofstitches/pattern
Length of stitch
Speed
setting
Enlargement/reduction
Mechanical home position
Mechanical
correction
home
position
Specification
Fullyelectronic control system using microcomputer
200X160mm (PLK-A2016F)
250X190mm
3.5*
floppy disk
3.5" floppy disk
P-ROM
3.5"
floppy
P-ROM
8000
stitches
(PLK-A2016FL)
and
P-ROM
(option)
150
(option) 16 patterns
disk 360000 stitches in total
(option) 8000 stitches in total
0.1 to 12.7 mm (Resolution: 0.1 mm)
200to2000
10
levels
10to200%,
Set
by optical
0.1to12.7
0.1 mm unit
s/min.
selectable
0.1%
sensor
mm
adjustable
step
and
insulator
patterns
Second
Halt
Reverse
output
Baste
Test
Format
home
rotation
stitching
function
function
Error display
Troubleshooting
Power
Ambient
temperature
humidity
position
shaft
function
Set
by input
Setbyinput
Set
by input
Setbyinput
Jog
switch
program
program
program
program
Format can be made using 3.5"floppy disk
Various errors
Check
of input switch
Checkofoutput
Confirmation
Phases
Single-phase
Three-phase
5to40°C
are
displayed on
signals
signals
and
adjustment of sewing
Frequency
(Hz)
50.
60
50,
60
the
LCDdisplay.
Voltage
100 110
200 220
200
220
speed
(V)
120
230
45 to 85% (No condensation)
380
(2HD
240
415
type).
Input
(kVA)
1
1
— 5 —
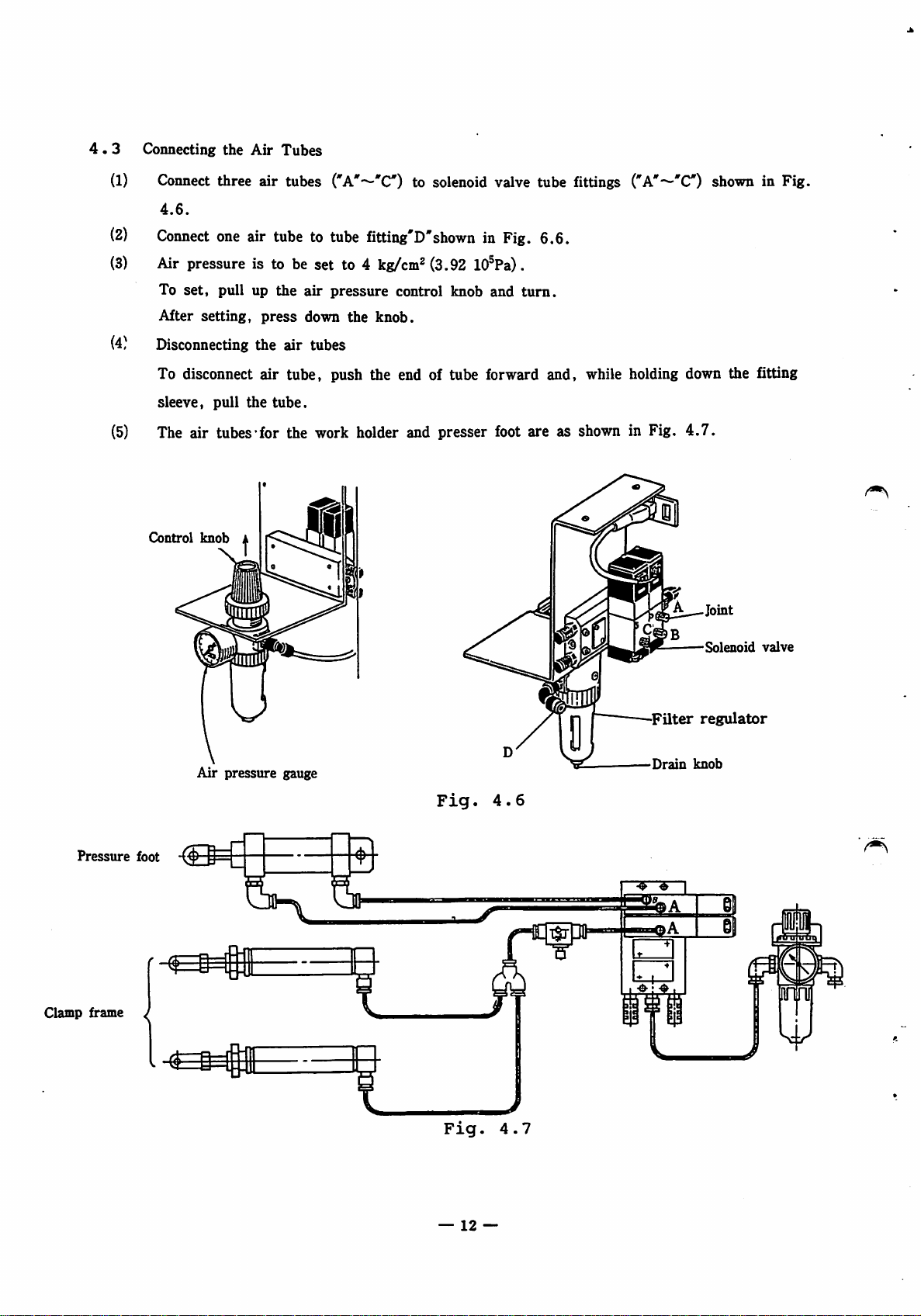
4.3
(1)
(2)
Connecting
Connect
4.6.
Connect
the
Air
Tubes
three air tubes
one
air
tubetotube
('A'—'C)
to solenoid valve tube fittings
fitting'D'shown in Fig. 6.6.
("A'-^'C)
shown in Fig.
(3)
Air pressure is to be set to 4
To
set,
pull up
After
(4)
setting,
Disconnecting
To disconnect
sleeve,
pull
press
the air tubes
air
the
the
air
down
pressure
the
kg/cm^
knob.
(3.92 lO^Pa).
control knob and
turn.
tube, push the end of tube forward and, while holding down the fitting
tube.
(5) The air tubes'for the work holder and presser foot are as shown in Fig.
Control
knob
4.7.
Joint
Solenoid
valve
Pressure
Clamp frame ^
foot
Air
pressure
gauge
Fig.
Fig.
4.6
4.7
T$T
Filter
Drain
regulator
knob
II
—
12
—
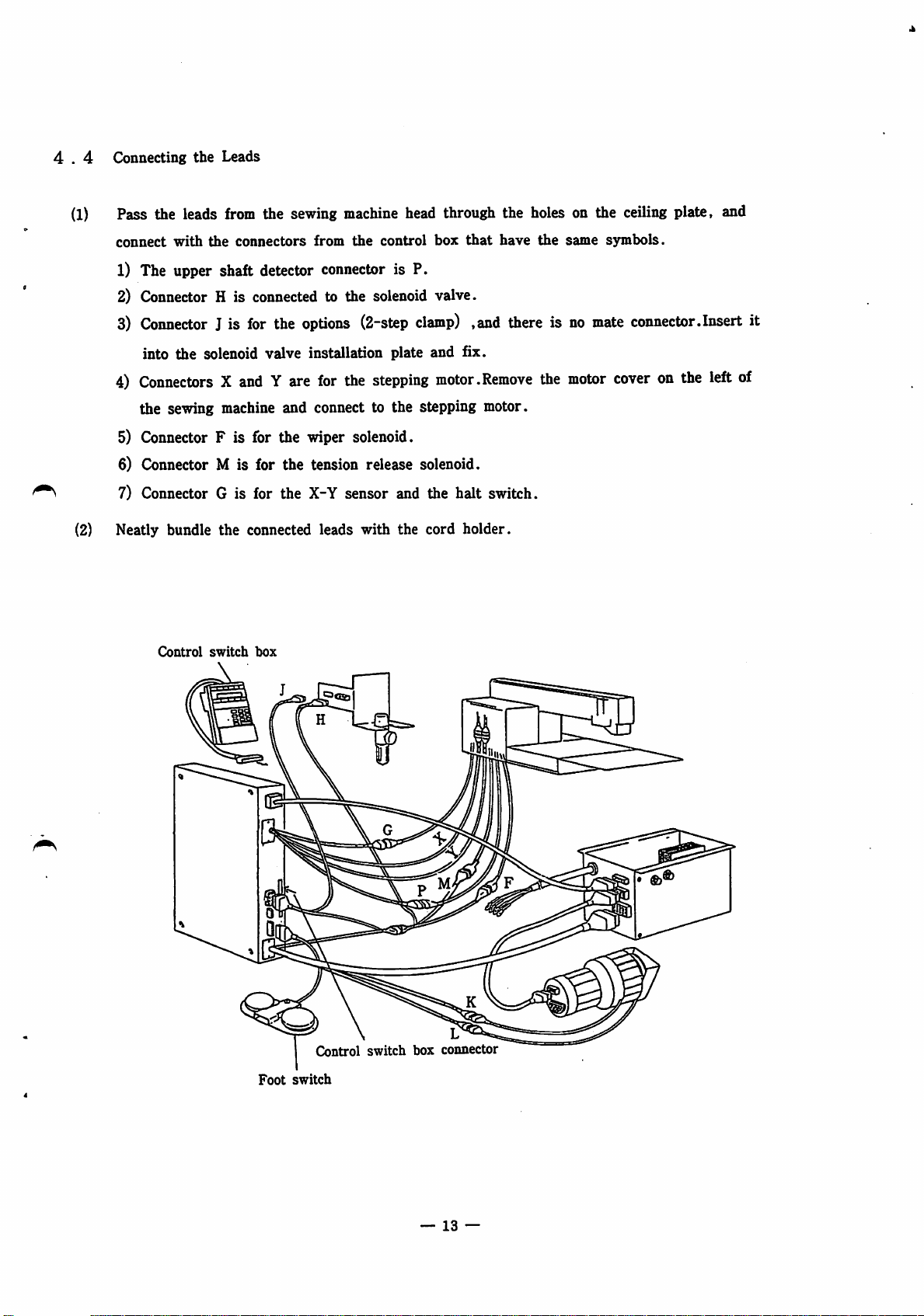
4 . 4 Connecting
(1)
Pass the leads
the
Leads
from
the sewing
machine
head through the holes on the
ceiling
plate, and
connect
with
the
connectors
from
the
control
box
that
have
1) The upper shaft detector connector is P.
2) Connector H is connected to the solenoid valve.
3)
Connector
into
4)
ConnectorsXand
the sewing machine and connect to the stepping motor.
5) Connector F is for the wiper solenoid.
6) Connector M is for the tension release solenoid.
^ 7) Connector G is for the X-Y sensor and the halt switch.
(2) Neatly bundle
Control
J is
for
the
options
the
solenoid valve installation plate and fix.
Y are
the
connected leads with the
switch
box
for
(2-step
the
clamp)
stepping
,and there isnomate
motor.Remove
cord
holder.
the
the
same
motor
symbols.
connector.Insert it
cover
on the
left
of
Foot
Control
switch
switch
box
—
connector
13
—

7.10
(1)
Adjusting
Check
that
the
the
presser
needle
foot
passes
(2)
(3)
through
presser
Rotate
ually
foot
presser
9.11)
of
the
the
lower
foot
above
presser
position.
The
vertical
presser
adjusted
crease
the
bolt
and
set
and
is
the
the
foot
the
loosen
screw
bar
adjust
presser
end
between
fabric
bar
foot
to
the
in
center
hole.
balance
set
of
is
stroke
is
4 mm.
stroke,
Fig.
the
(Fig.
screw
the
foot
the
0
and
when
at
its
factory-
7.16
of
wheel
presser
7.15)
height
so
presser
of
To
loosen
the
man
(Fig.
that
0.5
the
lowest
the
in
and
or
mm
move
Bolt
Presser
adjusting
Fabric
Fig.
foot
Approx.
30
screw
mm
Presser
foot
Presser
O^O-Omm
7.15
set
foot
screw
Auxiliary
adjusting
screw
Approx.
20
Thumb
mm
nut
it
up.
can
be
(4)
To
adjust
presser
nut
presser
The
screw
counterclockwise.
Normally,
to
be
Note:
The
thickness
The
increased
foot,
in
Fig.
foot
pressure
is
touched.
height
the
turned
there
of
of
vertical
pressure
loosen
7.16
adjusting
increases
the
the
up
to
and
clockwise
The
is
no
presser
fabric
stroke
10
of
the
turn
screw.
when
figure
need
mm.
the
thumb
the
and
foot
is
the
reduced
shows
for
the
must
changed.
when
the
auxiliary
also
Fig.
it
standard
be
changed
7.16
is
turned
adjustment.
adjusting
when
screw
the
—
30
—

9.13
(1)
Adjusting
If
the
thread
the
thread
release
release
is
not
adjusted
properly,
the
trimmed
(2)
(3)
thread
or
the
If
the
lowered,
thread
When
to
1.0
9.30.
tail
tension
the
mm
needle
the
tension
thread
develops
length
thread
discs
needle
develops
will
thread
release
when
iiiiiiH
O.onim-^l.Dinm
may
do
be
reduced
leave
not
tension
an
imbalance.
is
adjusted
the
SlSfcjg
Fig.
close
tension
=E!=
=
Es
the
9.30
and
needle
when
is
properly,
discs
stitches
the
reduced
to
when
presser
open,
will
sewing
and
a
clearance
as
be
foot
the
shown
skipped
commences.
is
overall
of
0.8
in
Fig.
(4)
Thread
holder
the
trimmed.
release
is
fabric
(5) Adjusting
• To adjust,remove the top cover,loosen nut
The opening of the discs will increase when Turned to the
If opening of
sion to the needle
If opening cannot be adjusted by
to
adjust.
at
is
the
the
occurs
the
fed
amount
tension
thread.
when
home
position
without
of thread
discs
is too
Too loose tension discs,however,may cause loose
moving
the
presser
when
stitching)
release
(C)
shownis Fig. 9.31and
Note
small,the
needle
the wire tube,loosen the screw (A) and pull the wire
foot
the
and
rises
power
when
during thread trimming ^
move
arrow.
thread
may
break
(the
is
switched
threads
the wire tube.
due
to excessive
stitch.
work
are
ON
ten
or
—
54
—