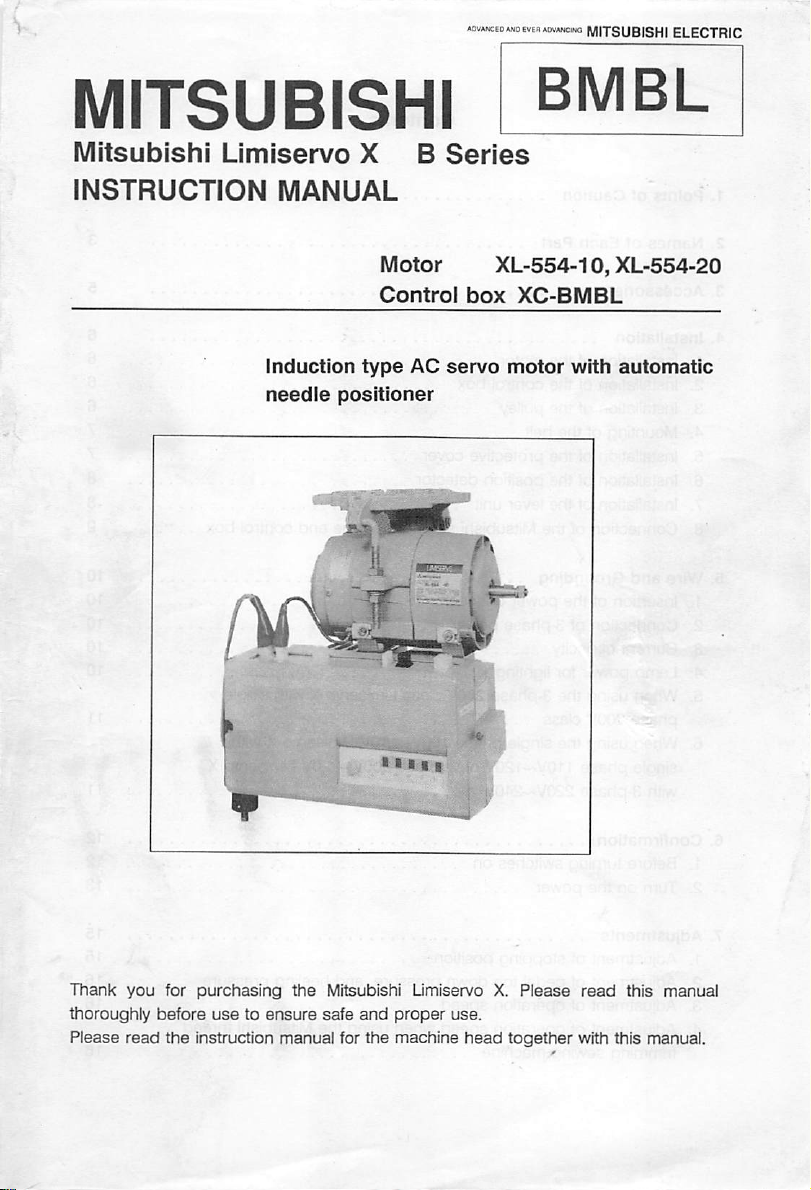
«v.«E0«0Evefl.0VA«:«0
MITSUBISHI
ELECTRIC
MITSUBISHI
Mitsubishi
INSTRUCTION
Limiservo
MANUAL
Induction
needle
X B
Motor
Control
type
positioner
AC
Series
box
servo
BMBL
XL-554-10,
XC-BMBL
motor
with
XL-554-20
automatic
Thank you for
thoroughly
Please
read
before
the
purchasing
usetoensure
instruction
the Mitsubishi Limiservo X.
safe
and
proper
use.
manual
for
the
machine
head
Please
together
read
this manual
with this manual.
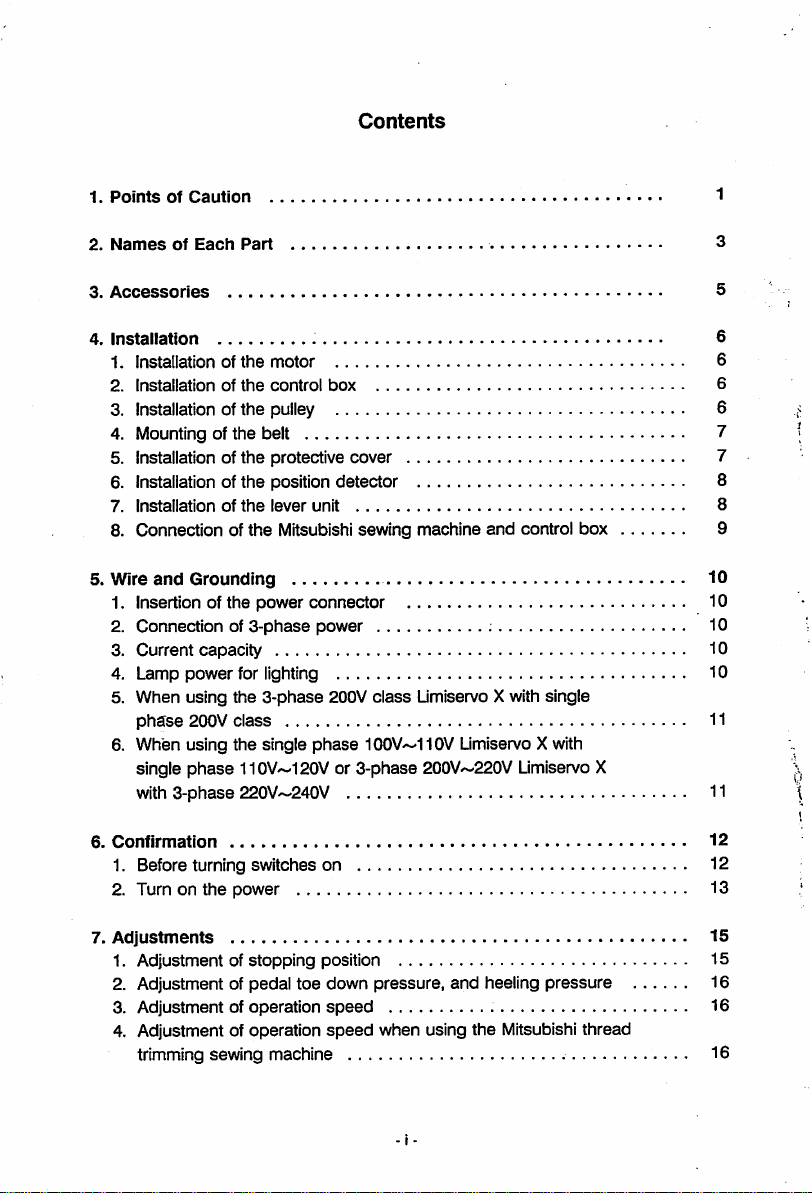
Contents
1.
PointsofCaution
2.
NamesofEach
3.
Accessories
4.
Installation
1.
installationofthe
2.
Installationofthe
Part
motor
control
box
3. Installationof the pulley 6
4. Mounting of the belt 7
5. Installation of
the
protective cover 7
6. Installation of the position detector 8
7.
Installationofthe
8. Connection of the Mitsubishi sewing machine
lever
unit
and
control box 9
1
3
5
6
6
6
8
5. Wire
and
Grounding
1. Insertion of the power connector 10
2. Connection of
3-phase
power 10
3. Current capacity 10
4. Lamp power for lighting 10
5. When using the
phase
200V
6. When using the single
single
phase
with
3-phase
6.
Confirmation
3-phase
200V
class
Limiservo X with single
class
phase
100V~110V Limiservo Xwith
110V~120V or 3-phase 200V'-220V Limiservo X
220V~240V 11
1. Before turning switches on 12
2. Turn on the power 13
7.
Adjustments
1. Adjustment of
2. Adjustment of pedal
3. Adjustment of operation
4. Adjustment of operation
stopping
toe
position 15
down pressure,
and
heeling
pressure
speed
speed
when using the Mitsubishi thread
trimming sewing machine 16
10
11
12
15
16
16
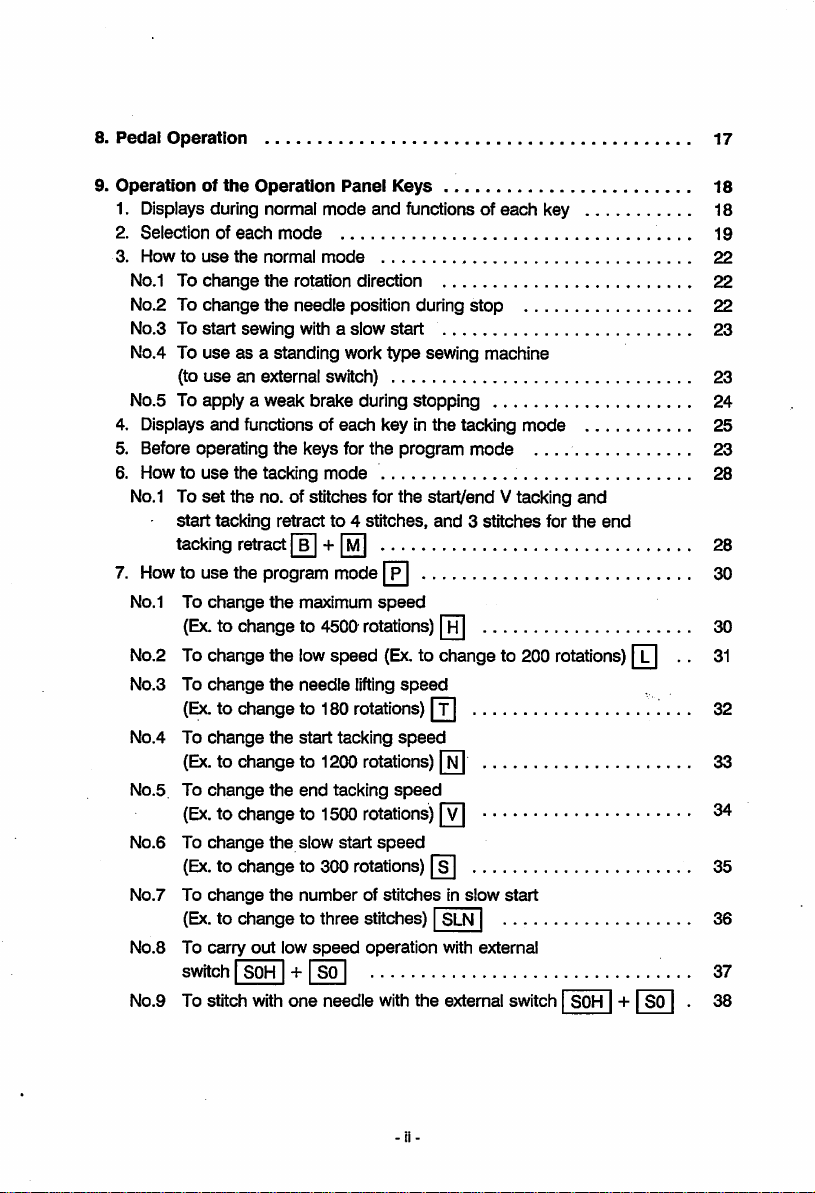
8.
Pedal
Operation
9.
Operationofthe
Operation
1. Displays during normal
2.
Selectionofeach
3.
Howtouse
No.1 To
No.2 To
No.3 To
No.4 To
the
change
change
start
sewing with a siow start 23
useasa
(to
use
an external switch) 23
No.5 To apply a
4. Displays
and
functions of
5. Before operating
6. How to
No.1 To
7. How to
No.1 To
use
the
set
the no. of stitches for the start/end V tacking
start
tacking
tacking
retract
use
the
change
(Ex. to
changeto4500 rotations) 30
No.2Tochange
No.3 To
No.4 To
No.5
change
(Ex. to
change
change
(Ex.tochangeto1200
To
change
(Ex.tochangeto1500
No.6
To
change
(Ex.tochangeto300
No.7 To
No.8
No.9
change
(Ex.tochangetothree
To
carry
out
switch
To
stitch
SOH
with
Panel
Keys
mode
and
functions of
mode
normal
mode
the
rotation direction 22
the
needle position during
standing
weak
the
tacking
work
type
sewing machine
brake during stopping 24
each
key in
the
keys for the program
mode
each
stop
tacking
mode
key 18
mode
and
retractto4
program
the
maximum
the
low
the
needle
stitches,
mode
speed
speed
(Ex.tochangeto200
lifting
speed
and3stitches
for
the
end
rotations)[p..
to 180 rotations) 32
the
start
tacking
speed
rotations) 33
the
end
tacking
the
slow
the
numberofstitchesinslow
low
speed
+
SO
one
needle
speed
rotations)
start
speed
rotations) S
stitches) SLN
operation
with
the
[v]
with
external
start
external
switch
SOH
+ SO .
17
18
19
22
22
25
23
28
28
30
31
34
35
36
37
38
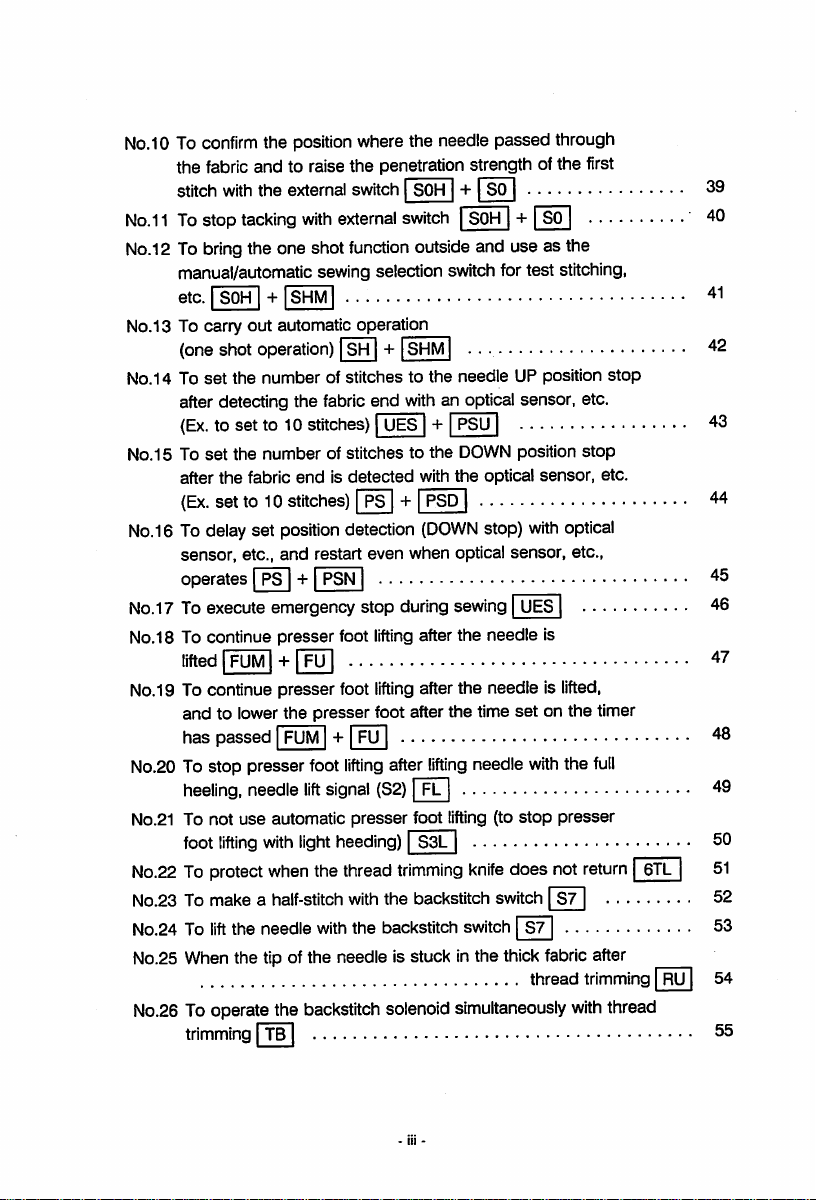
No.10Toconfirm
the position where the needle passed through
the fabric and to raise the penetration strength of the first
+
stitch
with
the
external
switch
SOH
No.11 To stop tacking withexternal switch
SO
SOH
+ SO
No.12 To bring the one shot function outside and use as the
manual/automatic sewing selection switch for test stitching,
etc.
SOH
SHM
No.13 To carry out automatic operation
(one shot operation) SH + SHM
No.14Toset
No.15 To
No.
16 To delayset
No.17 To execute emergency
No.18 To continue presser foot
No.19 To continue presser foot
No.20
No.21 To not
No.22Toprotect
No.23
No.24 To
No.25
No.26
the
numberofstitchestothe
after detecting the fabric
(Ex. to
set
to 10 stitches) UES + PSU
set
the
numberofstitchestothe
after
the
fabric
endisdetected
(Ex.
set
to 10 stitches) PS + PSD
position
sensor,
operates
etc.,
PS
and
+
detection
restart
PSN
end
even
stop
lifting
lifted
FUM
lifting
and to lowerthe presser foot after the time
has passed
To stop presser foot
heeling,
foot
lifting
To make a
lift
FUM|
+ |FU| 48
lifting
needle
lift
signal
use
automatic
with light heeding) S3L
when
half-stitch
the
needle
the
with
presser
thread
with
the
after
(S2)|FL
trimming
the backstitchswitch| S7 | 52
backstitch switch
needleUPposition
with an optical sensor, etc.
DOWN position
with
the
optical
sensor,
(DOWN
when optical
stop)
with
sensor,
optical
etc.,
during sewing UES
after the needle is
after the needle is
lifting
needle
lifted,
set
on the timer
with
the
[
foot
lifting
(to
stop
presser
knife
does not
S7
When the tip of the needle is stuck in the thick fabric after
thread
Tooperate the backstitch solenoidsimultaneously
trimming
ITBI 55
with
39
40
41
42
stop
43
stop
etc.
44
45
46
47
full
49
return|6TL|51
trimming
RU
thread
50
53
54
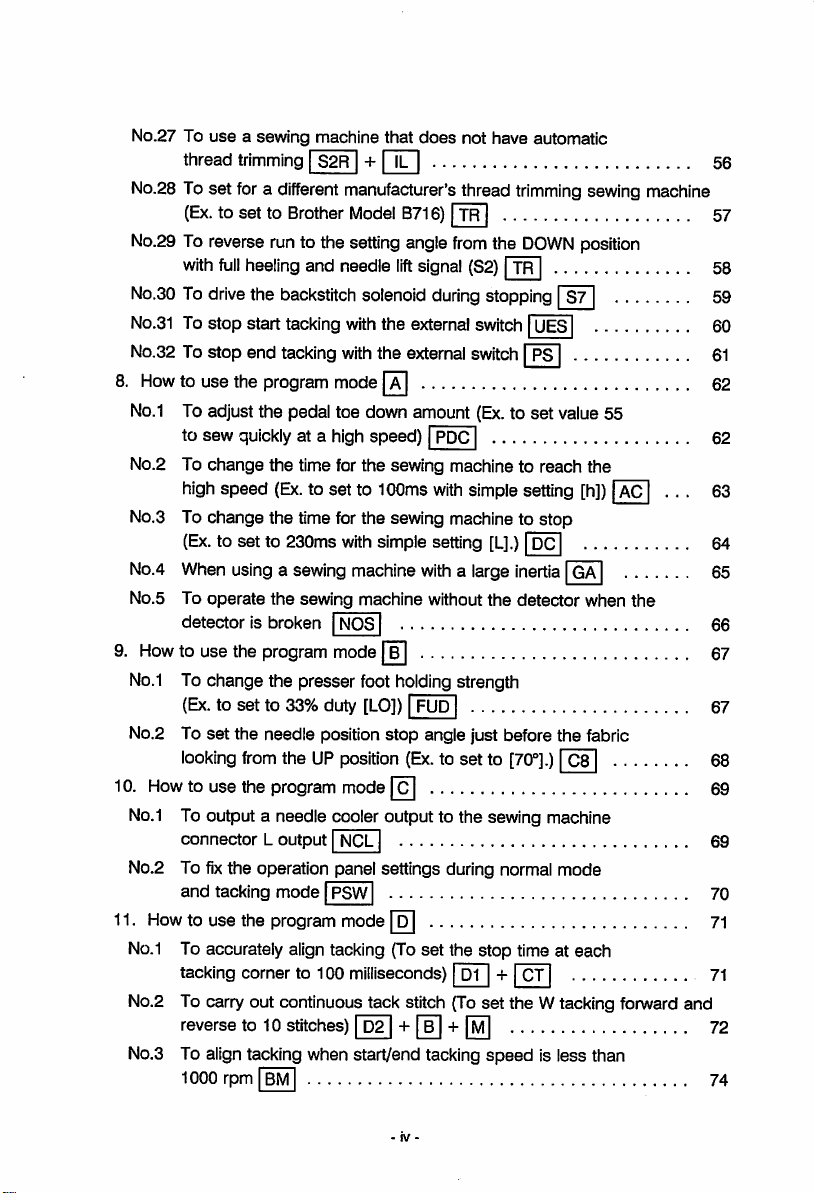
No.27 To
No.28 To set for a different manufacturer's thread
No.29
No.30
No.31 To
No.32 To
8. How to
No.1
No.2 To
use
a sewing machine that
thread trimming S2R
(Ex.
to set to
Brother
Model
To reverse runto the settingangle
with
full
heeling
and needle
-i-nn
does
8716)|TR
from
lift
signal
not have automatic
trimming
sewing machine
| 57
the
DOWN
position
(S2)|TR
| 58
To drivethe backstitchsolenoid duringstopping IS7 59
stop
start
tacking with the external switch
stop
end
tacking with the external switch PS 61
use
the program mode 62
To adjust the pedal toe down amount
to
sew
high
change
speed
quickly at a high
the time for the sewing machine to reach the
(Ex.
to set to
speed)
100ms
ROC 62
with
simple
LIES
(Ex.
to set value 55
setting
[h])
No.3 To change the timefor the sewing machineto stop
(Ex.to
set
to 230ms withsimple setting
No.4 When using a sewing machine
with
[L].)
a large
DC
inertia
GA 65
No.5 To operate the sewing machine withoutthe detector when the
detectorisbroken
9. How to
No.1
No.2 To
use
the program mode 67
To change the presser foot holdingstrength
(Ex. to
set
to 33% duty [LO]) FUD
set
the needle position stop angle just before the fabric
looking from the UP position (Ex.to
10. How to
No.1
No.2 To
11. How to
No.1
use
the
program
To output a needle cooler output to the sewing machine
connectorLoutput
fix
the operation panel settings during normal mode
and
tacking
use
the
mode
program
To accurately align tacking (To
tacking
corner
No.2 To carry out continuous tack stitch (To
reverse
to 10
No.3 To aligntacking when start/end tacking
1000
rpm BM
NOS
setto[70°].)
mode
0
NCL 69
PSW
mode
set
the stop time at each
to 100
milliseconds)[D1
| + jCT|
set
stitches)
D2
B
M
speed
08
the W tacking forward and
is less than
[AC
56
60
63
64
66
67
68
69
70
71
71
72
74
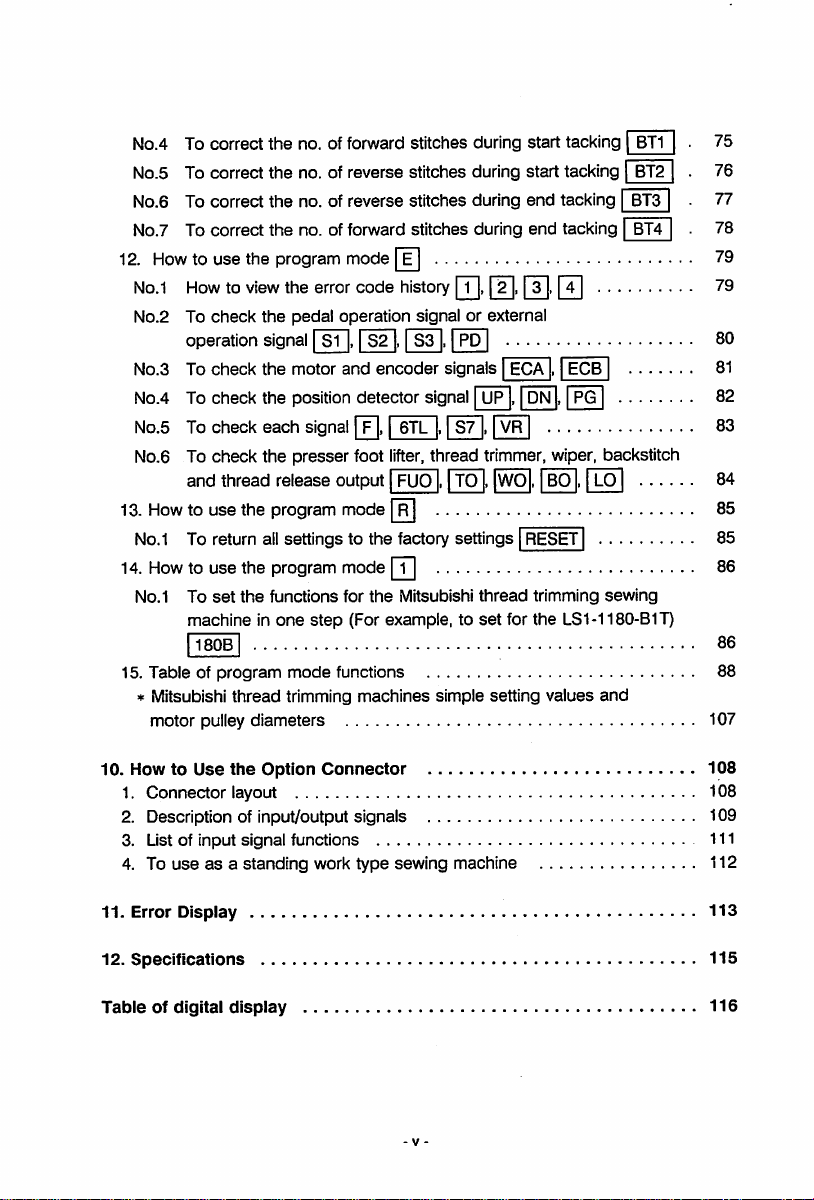
No.4
Tocorrectthe no. of
No.5
To correctthe no. of reversestitches duringstart tacking|
No.6
To correct the no. of reverse stitches during end tacking|
No.7
To correct the no. of
12. How to
No.1
Howtoview
No.2 To
operation
No.3 To
use
check
check
the
program
the
the
signal
the
forward
forward
mode
error
code
pedal
operation
| Si |,| S2 |,| S3 |,|
motor
and
encoder
stitches
during
stitches during end tacking |
history
pT],
signal or external
PD
signals
No.4 To check the positiondetector signal| UP|, |
No.5
Tocheck each
No.6 To check the presser foot
and
thread
13. How to
No.1 To return ail
14.
Howtouse
No.1 To
15.
Tableofprogram
* Mitsubishi
motor
use
the
the
set
the
machine in
180B
thread
pulley
signal
release
program
settingstothe
program
functions for
one
mode
trimming
diameters
output
mode
mode
the
step
(For example, to
functions
machines
|
6TL
1.1S71.1VR
lifter,
thread trimmer,wiper, backstitch
FUO
TO,WO.
R
factory
settings
[T]
Mitsubishi
simple setting values
start
tacking|BT1
[2],
EGA
Ieca
M.1DN
DN
[T]
.
.
EGB
PG
|
BO
. LO
RESET
thread
trimming
set
for the LSI-1180-BIT)
and
BT2
BT3
BT4
sewing
75
76
77
|
78
79
79
80
81
82
83
84
85
85
86
86
88
107
10. HowtoUse
1. Connector layout 108
2. Description of input/output signals 109
3. List of input signal functions
4. To
11. Error Display
12.
Specifications
Table
of digital
the
Option
Connector
useasa standing work type sewing machine 112
display
108
Ill
113
115
116

1.
Points
1.
Please
when
of
remove
turning
Caution
your
the
power
foot from
ON.
the
1.
Points
pedal
of
Caution
2. Alwaysturn
the
machine.
the
power OFF
when
leaving
3. Do not
5. Always
7. A high
inspect
the
tester.
The
semiconductor
when
the
tester's
ground
The
S-phase
(green). Always
control circuit with a
parts
voltageIsapplied.
tfie machine.
motor
hasagrounding
ground
voltageIsapplied
machine,sowait10minutes
the
power switch OFF before
cover.
Control
etfcuit
maybedamaged
this.
inside
tfte
after
turning
opening
wire
the
4. Alwaystum
tilting
the
the
needle,orthreading
I]
6. Do not
8. Use
the
single-phase
the
strong
welder.
use
noise
machine away from
the
power switch OFF before
sewing machine
the
Sewing
machine
branched
wiring
motor.
suchasa high
head,
needie.
when
sources
frequency
replacing
using
of
High
voltage
Notso
danger
1 -
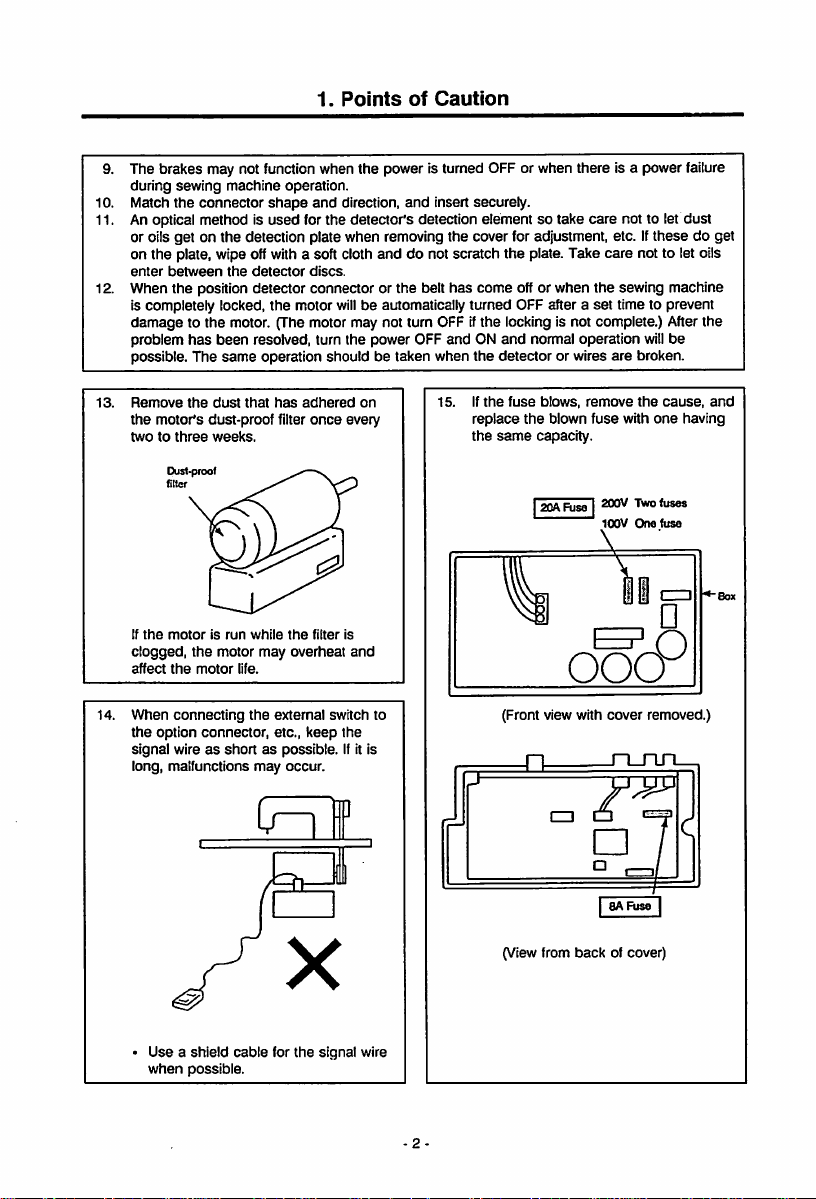
1.
Points
of
Caution
The brakes may not functionwhen the power is turned OFF or when there is a power failure
during
sewing
machine
10.
Match
the
An optical method is
11.
or oils
get
connector
on the detection plate when removing
operation.
shape
used
and
for the
direction,
detector's
and
insert securely.
detection element so
the
cover for adjustment, etc. If
take
care
not to let
on the plate, wipe offwitha soft cloth and do not scratch the plate. Take care not to let oils
enter
between
the
detector
When
12.
the
is completely locked,
position detector connector or
the
discs.
motor
the
belt
has
come
will
be automatically turned OFF after a
off or
when
the
sewing machine
set
time to prevent
damage to the motor. (The motor may not turn OFF ifthe locking is not complete.) Afterthe
problem
has
been
13.
possible.
Remove
the
twotothree
If
clogged,
affect
The
same
the
dust
motor's
dust-proof
weeks.
Dust-proof —N.
filler
the
motorisrun
the
motor may
the
motor
resolved, turn the power OFF
operation should be taken when
that
has
adhered
once
filter
on
every
is
and
life.
while
filter
the
overheat
andONand
the
If
the
15.
replace
the
normal operation will
detector
or wires
fuse
blows,
the
blown
same
capacity.
|20ARjse|
ooo
are
remove
fuse
200V
100V
broken.
the
with
TWofuses
One
these
be
cause,
one
fuse
dust
do get
and
having
14.
When
the
option
signal
long, malfunctions
Useashield
when
connecting
the
connector,
external
etc.,
keep
wireasshortaspossible.
may
occur.
cable
for
the
signal
possible.
switch to
the
Ifit is
wire
(Front view with
n
(View from
back
cover
n_rui
P8AFuse
of cover)
removed.)
I
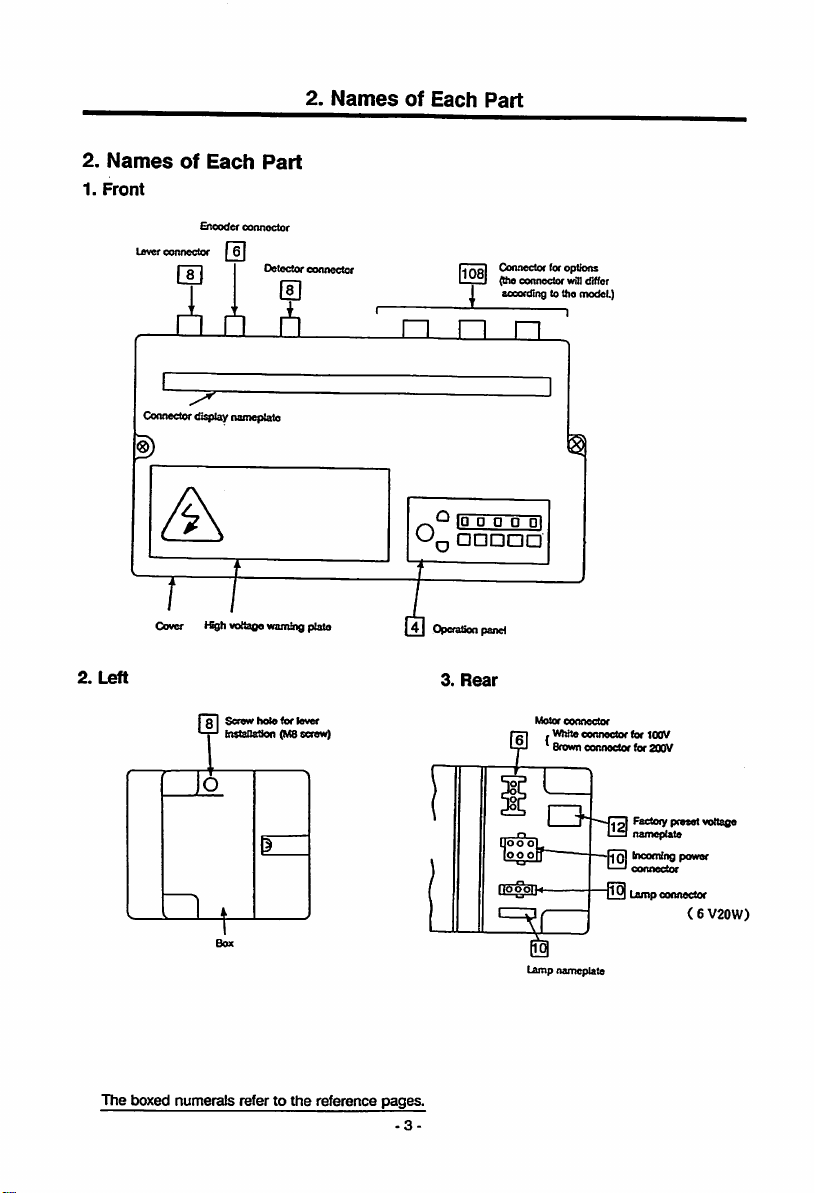
2.
1.
Names
Front
Lever
of
connector
A
Each
Encodcf
Part
connector
2.
Names
of
Each
Part
Connector tor options
(the ccnnecior willrfiffer
according to the model.)
"ID• 0 O
D
Cover Kgh voltaoe warningplate
2.
Left
I 31
Screw
holefor
l"'
installation
o
lever
(M8screw)
41
OperaSoopand
3.
Rear
t5
The
boxed
numerals
refer to
the
reference
pages.
-3-
D1
Motor
connector
WhKe
Brown
I r
»-i
Lamp namepiate
connector
connector
La
I-—'connector
t^0|
(or 100V
(or 200V
Rectory
preset
namepiate
bioocningpower
Lamp
connector
<6 V20W)
voitage
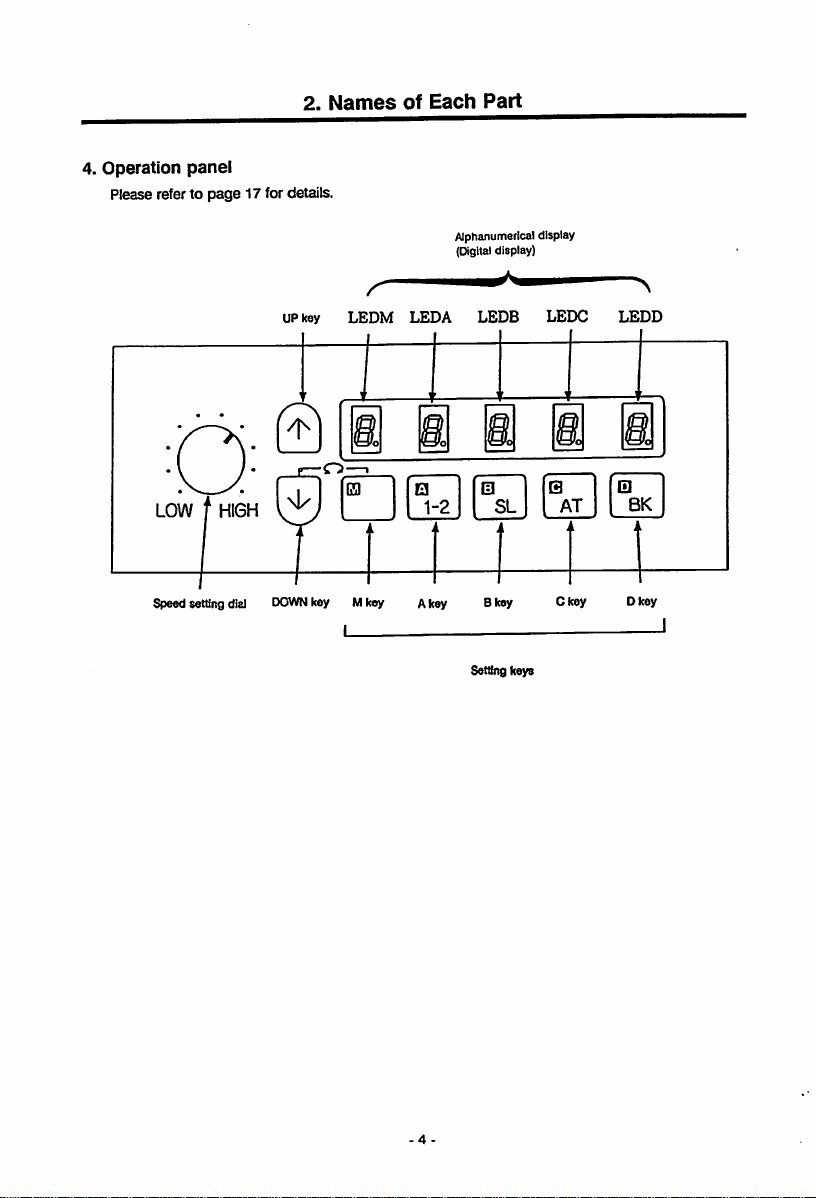
4.
Operation
Please refer to
panel
page
2.
17 for details.
Names
of
Each
Part
LOW HIGH
settSng
dial
Alphanumerical
pgltal
UP
key
LEDM
DOWN
key Mkey Akey Bkey Ckey Dkey
LEDA
•
1-2
LEDB
Setting keys
display)
m
SL
display
LEDC
Q
AT
LEDD
BK
-4
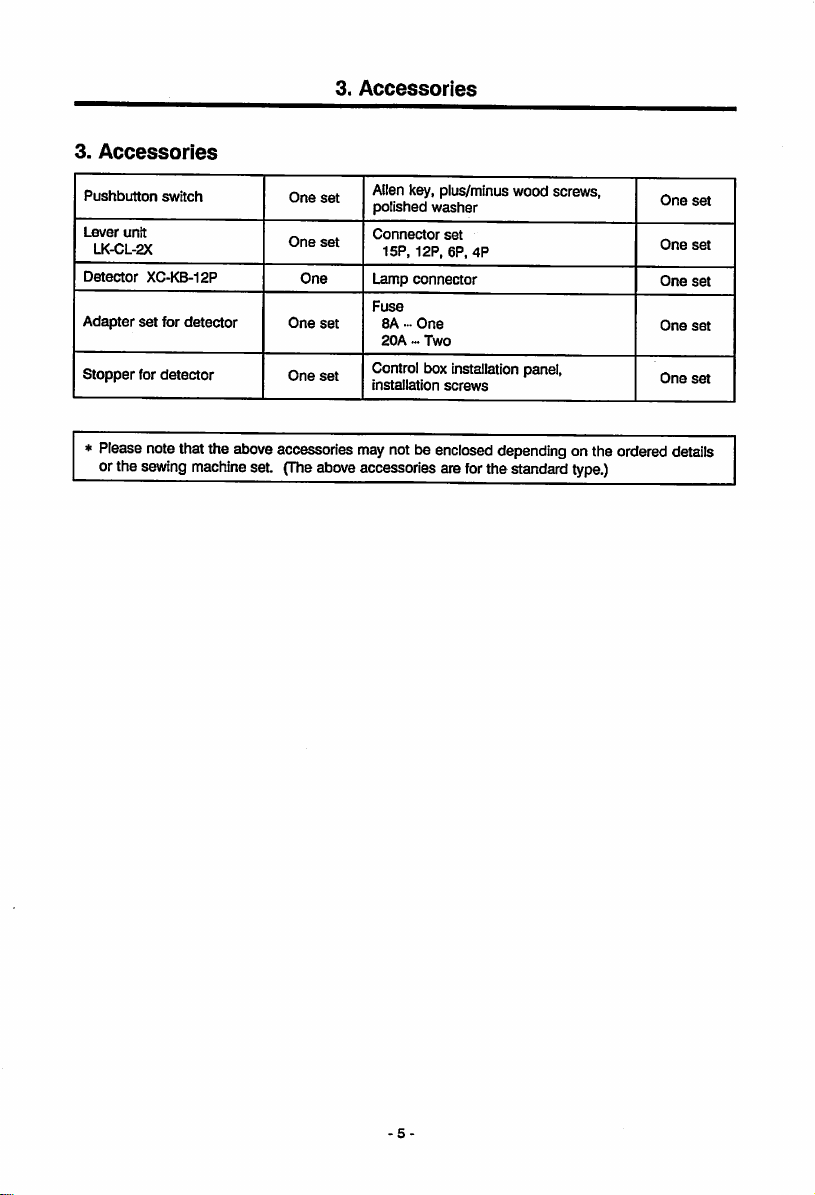
3.
Accessories
3.
Accessories
Pushbutton
Lever
unit
LK-CL-2X
Detector
Adapter
Stopper
switch
XC-KB-12P
set
for
for
detector
detector
One
One
One
One
One
Allen key, plus/minus
set
polished
washer
Connector
set
set
set
15P,
12P,
Lamp
connector
Fuse
8A-One
20A
•••
Two
Control box installation panel,
installation
set
6P,
screws
wood
screws,
4P
* Please notethat the above accessories may notbe enclosed dependingon the ordered
orthe
sewing
machine
set.
(The
aboveaccessoriesareforthestandard
type.)
One
One
One
One
One
dptajlg
set
set
set
set
set
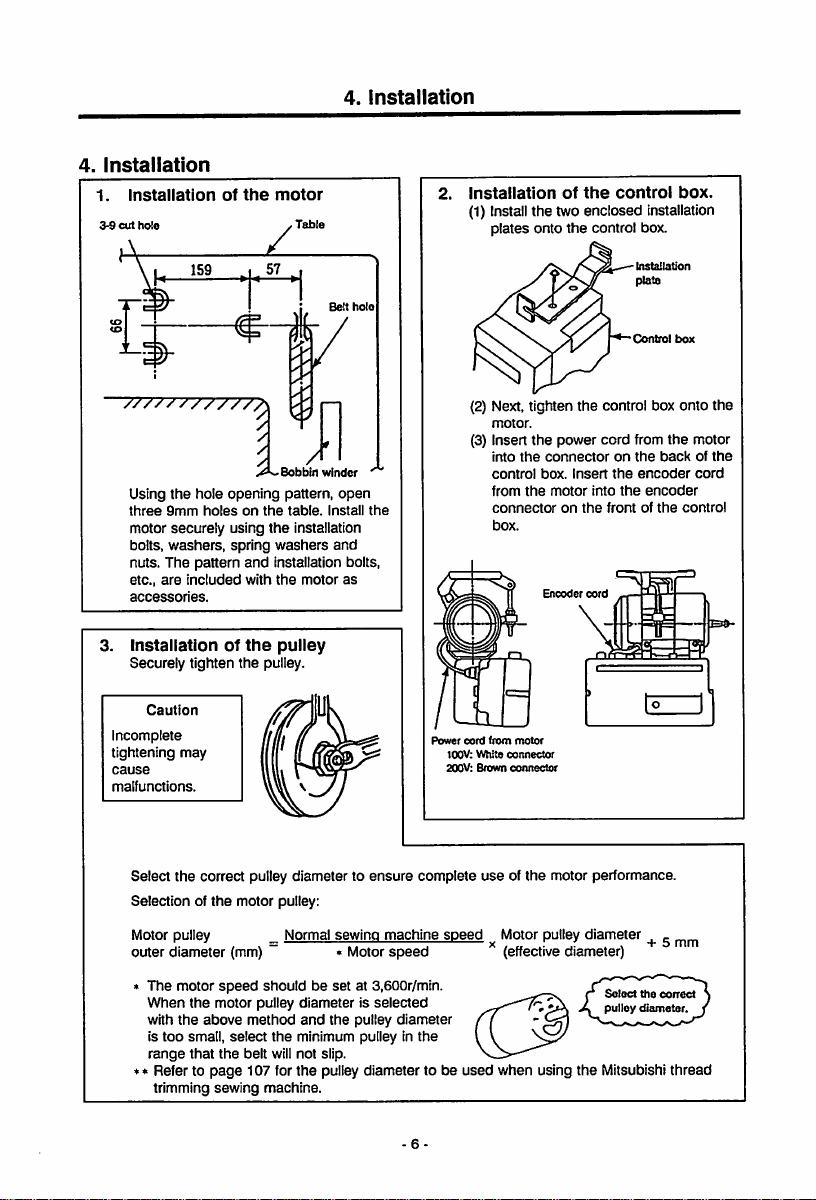
4.
Installation
1.
3-9
Installation
cut
hole
4.
Installation
of
the
motor
Table
Belt
hole
instaiiation
(1) Install the two enclosed installation
plates
onto
of
the
the
controi
control box.
Corttrol
box.
box
Bobbin
winder
Using
the
hole
opening
pattern,
three
9mm
motor securely using
bolts,
washers,
nuts.
The
etc.,
are
included
accessories.
3.
Installationofthe
Securely tighten
Caution
holesonthe
spring
pattern
and
with
the
the
washers
installation bolts,
the
puiiey
pulley.
table.
Install
installation
motor
open
and
as
Incomplete
tightening
cause
malfunctions.
may
Select
the
Selection of
correct pulley diameter to
the
motor pulley:
k/lotorpulley _ Normal sewing machine
outer diameter (mm) ~ • Motor
The
motor
speed
When
with
the
is
too
range
* Refer to
trimming
the
above
small,
that
page
sewing
shouldbeset
motor
pulley
method
select
the
the
belt will not slip.
107 for
machine.
at 3,600r/min.
diameterisselected
and
the
pulley
minimum puiiey in
the
pulley diameter to be
the
ensure
speed
Power
complete
diameter
the
(2) Next, tighten
motor.
(3) Insert
into
control
from
connector
box.
cord
from
100V:
White
Brown
connector
connector
200V:
useofthe
speed
Motor pulley diameter
(effectivediameter)
used
when
the
the
power cord from
the
connectoronthe
box.
Insert
the
motor
on
the
Encoder
motor
motor performance.
using
the
control box
the
into
the
frontofthe
cord
Select
pulley
Mitsubishi
the
backofthe
encoder
encoder
+ 5
the
correct
diameter
onto
motor
cord
control
mm
thread
the
6-
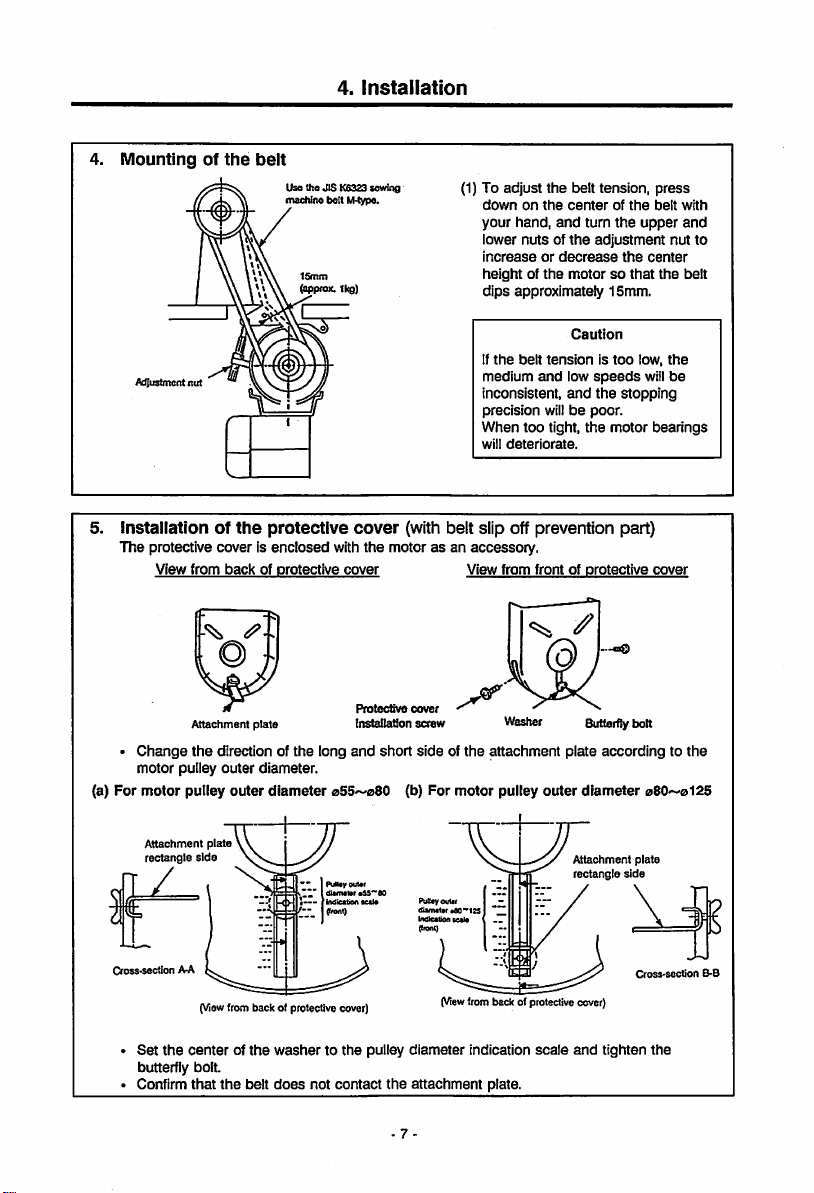
4.
Mountingofthe
Adjustment
4.
Installation
belt
Use the JIS K6323 sewing
ntacMne lielt M-type.
ISmm
^pfox.
1kg)
nut
(1) To adjust
downonthe
your
hand,
lower
nutsofthe
increaseordecrease
heightofthe
dips
approximately
If
the
belt
medium
and
inconsistent,
precision
When
too
will
deteriorate.
the
belt tension,
centerofthe
and
turn
the
adjustment
motorsothat
1Smm.
Caution
tensionistoo
low
speeds
and
the
willbepoor.
tight,
the
motor
press
belt
upper
the
center
the
low,
will
stopping
bearings
with
and
nut to
belt
the
be
5. Installation of
The protective cover is
View
from
Attachment
•
Change
the
motor
pulley
(a)
For
motor
pulley
Attachment
rectangle
Cross^section AA
Set
butterfly bolt.
Confirm
plate
side
(Viewfrom back of protective cover)
the
centerofthe
that
the
protective
enclosed
backofprotective
plate
direction of
outer
outer
the
diameter.
diameter
washertothe
the
belt
does
cover
with
the
motorasan accessory.
cover
Protective
tnstallafion
long
and
short
055~08O (b) For
PuNay
outer
diameler
•SS'^60
irrdiettioA
•e«l«
(Irertt)
pulley
not
contact
the
(with belt slip off prevention part)
View
from
frontofprotective
—caQ
cover
screw
sideofthe
PuBeyOuter
tfARMter
Indlcetioo
^ronl)
(View
diameter
attachment
motor
eflO^ISS
tcele
trom
indication
Vlfesher
attachment
pulley
outer
l>ackofprotective
scale
plate.
Butterfly bolt
plate
accordingtothe
diameter
Attachment
rectangle
cover)
and
tighten
plate
side
Cross-secUon
cover
08O~0l25
B-B
the
-7
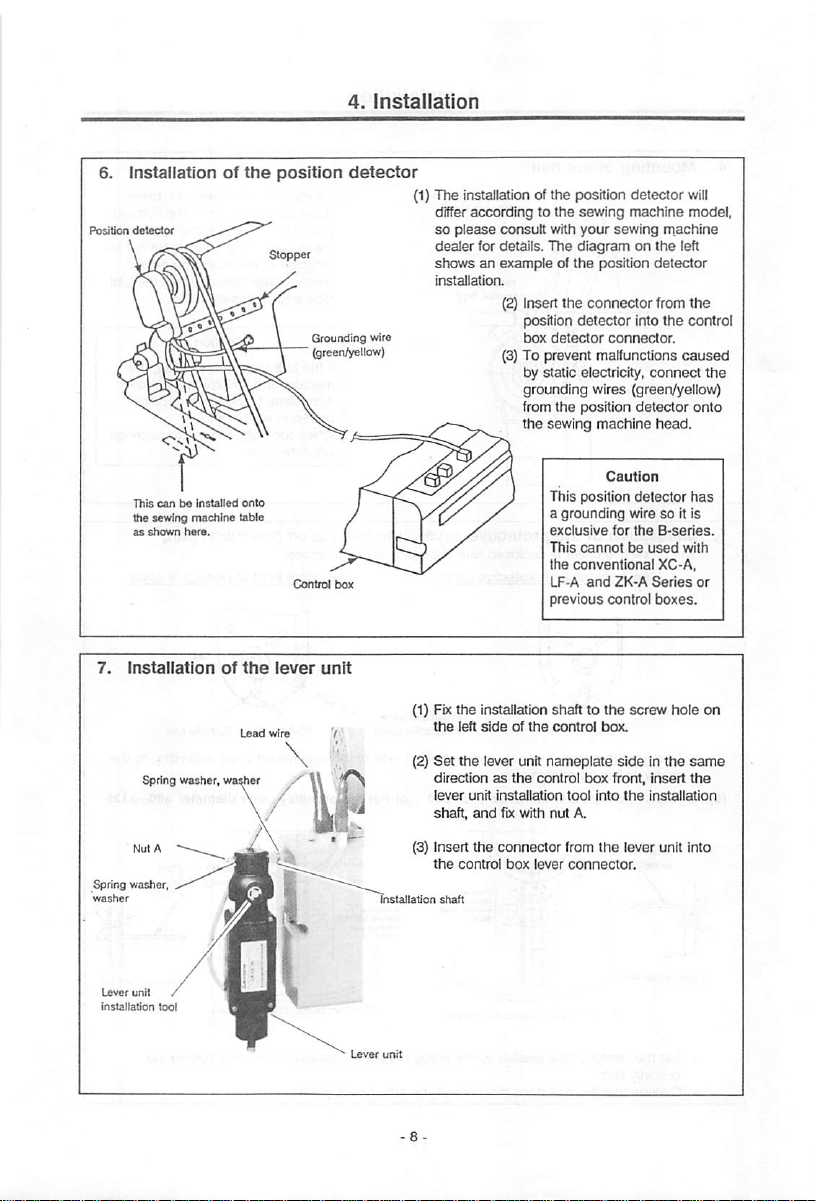
7.
Installation
spring
Spring washer,
washer
Lever
unit
Installation
tool
wssher,
/
of
washer
the
lever
unit
•
(1) Fix
the
(2)
Set
directionasthe
lever
shaft,
(3) insert the
the
7nstallation shaft
the
Installation shaft to
left
sideofthe
the
lever unit
unit
installation
and
fix
with
connector
control
box
This position
a
grounding
exclusive
This
cannotbeused
the
conventional
LF-A
and
previous control
the
control
box.
n^eplate
control
t>ox
tool
into
nut
A.
from
lever
the
connector.
Caution
detector
wiresoit is
for
the
B-series.
XC-A,
ZK-A
Series
boxes.
screw
sideInthe
front,
insert
the
installation
lever unit into
hole
has
with
or
on
same
the

8
Connectionofthe
Wire
the
unitsasshown
Table
Connector
for
hole
lever
For safety, always turn
and
for approx. 10
disconnecting
notanerror.
4.
Installation
Mitsubishi
below.
Connector
sewing
for
encoder
onnector
Caution
the
wait for the panel display
seconds)
the
before connecting or
plugs. This
machine
for
detector
and
power switch OFF
[EO]
(displayed
[EO]
display is
controi
Connector for sewing
machine
box.
-9
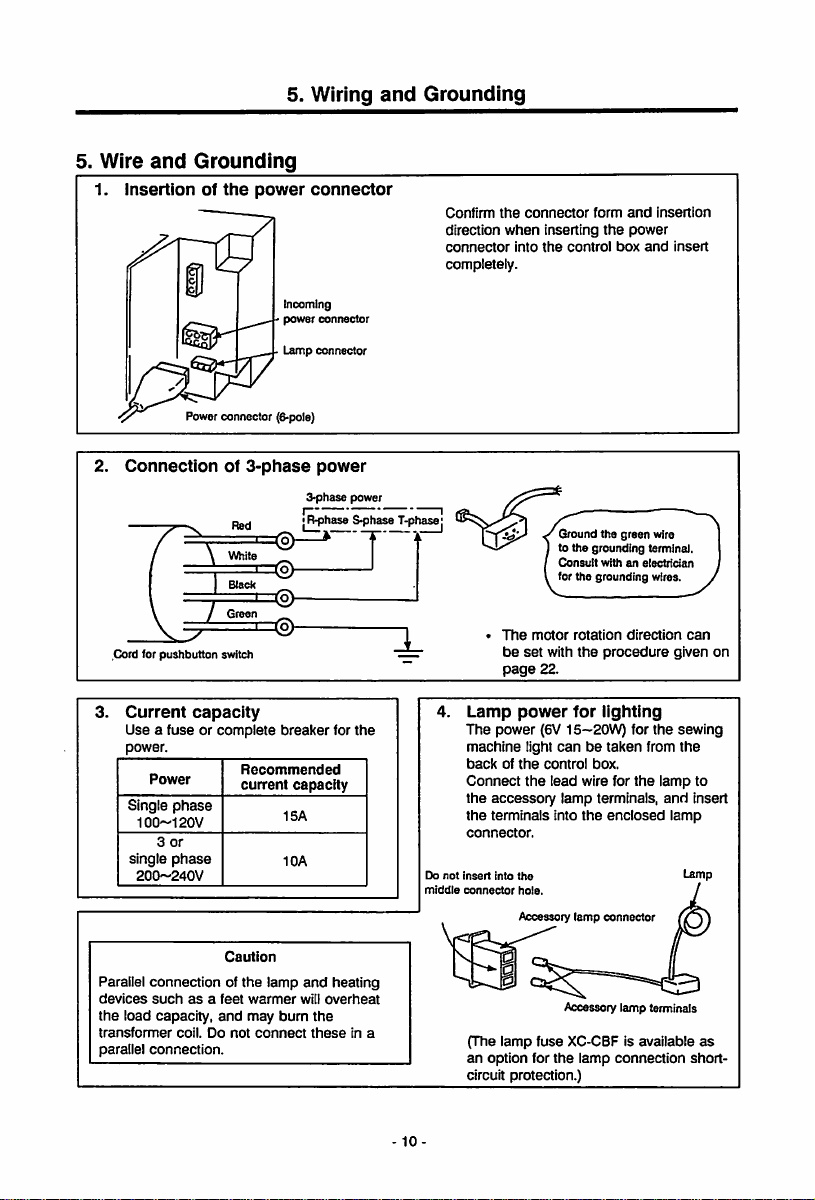
5. Wiring
and
Grounding
5. Wire
and
1.
Insertionofthe
Power connector (6*pole)
2.
Connectionof3-phase
.Cord for
pushbutton
3.
Current
Useafuseorcompiete
power.
Power
Single
phase
1G0~120V
3
or
single
phase
2G0~240V
Grounding
power
rted
White
Green
switch
capacity
Recommended
current
connector
Incoming
power
Lamp
Sybase
jR-phase
breaker
capacity
ISA
1GA
connector
connector
power
for
power
Sybase
the
T-phase;
X
Confirm
direction
connector
completeiy.
[3o
not
middle
the
when
The
be
page
Lamp
The
power
machine
backofthe
Connect
the
accessory
the
terminals
connector.
insert
Into
connector
connector
inserting
into
the
control
Ground the green wire
to the grounding terminaJ.
Consult
for the grounding wires.
motor
rotation
set
with
the
22.
power
for
(ev
15—20W) for
light
canbetaken
controi
the
lead wire for
lamp terminals,
into
the
the
hole.
Accessory
lamp
form
and
insertion
the
power
box
and
withanelectrician
direction
procedure
iighting
the
from
box.
the
iamp to
enclosed
connector
insert
given
and
iamp
can
on
sewing
the
insert
Lamp
Parailei
devices
the
load
transformer
parallel
Caution
connectionofthe
suchasa
capacity,
feet
and
coil.Donot
connection.
lamp
warmer
may
connect
burn
and
will
overheat
the
these
heating
in a
-10-
Accessory lamp terminals
(The
lamp
option
fuse
for
the
an
circuit protection.)
XC-CBF is available
iamp
connection
as
short-
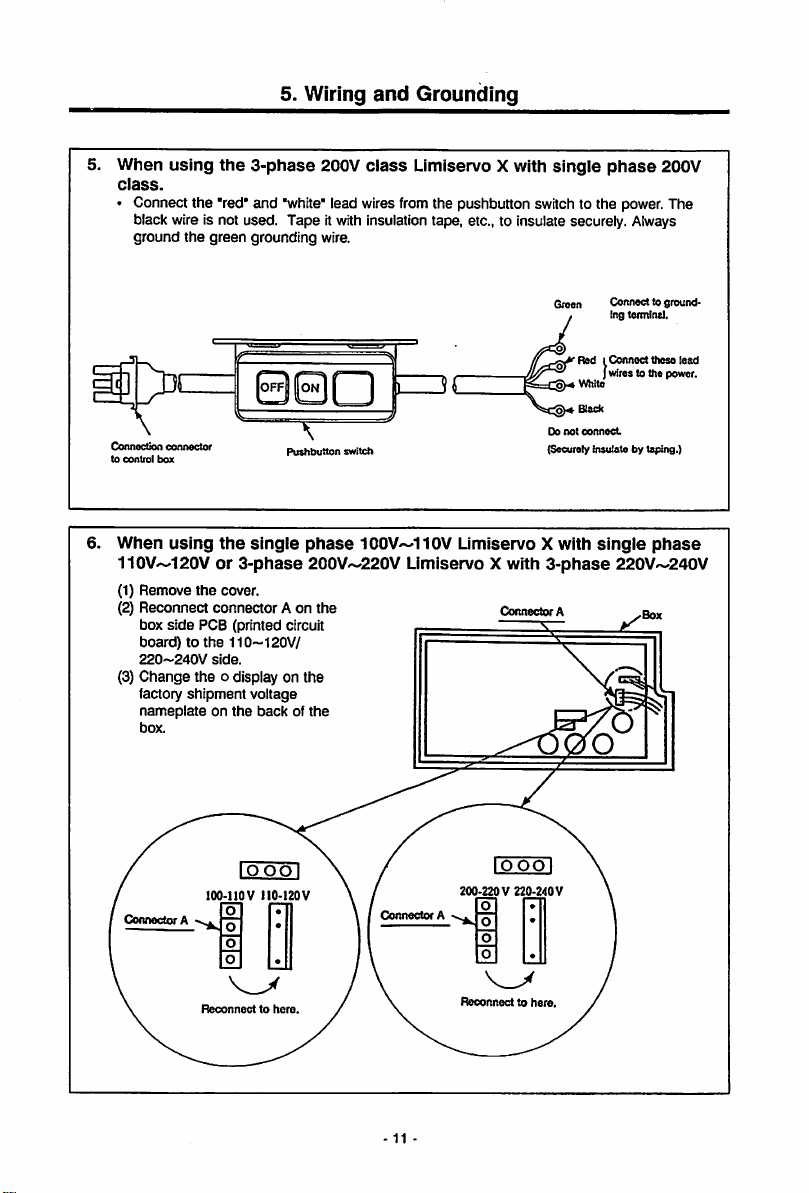
5.
When
using
class.
• Connect the "red*and
the
5. Wiring
3-phase
"white"
and
Grounding
200V
class
LImlservo X with
single
lead wires from the pushbutton switch to the power. The
black wire is not used. Tape itwith insulation tape, etc., to insulate securely. Always
ground
the
green
grounding wire.
phase
200V
Connect to ground-
Ing temtlncl.
Connection
comwctor
to
control
liox
6.
When
using
the
110V'-'120Vor3-phase
(1)
Remove
the
(2)
Reconnect
box
board)tothe
220~240V
(3) Change the o display on the
factory shipment voltage
nameplateonthe
box.
cover.
connector
side
PCB (printed circuit
110—120V/
side.
lOOOi
lOO-UOV
o
\
Pushbutton
switch
single
phase
100V~110V Limiservo X with
200V~220V Limiservo X with
A on the
backofthe
110-120
V
Connector
RedIConnect
Whte
Do
not
oonnecL
(Securely Insulate by taping.)
3-phase
these
(wirestothe
single
phase
220V~240V
lead
power.
Reconnecttohere
Reconnecttohere
11
-
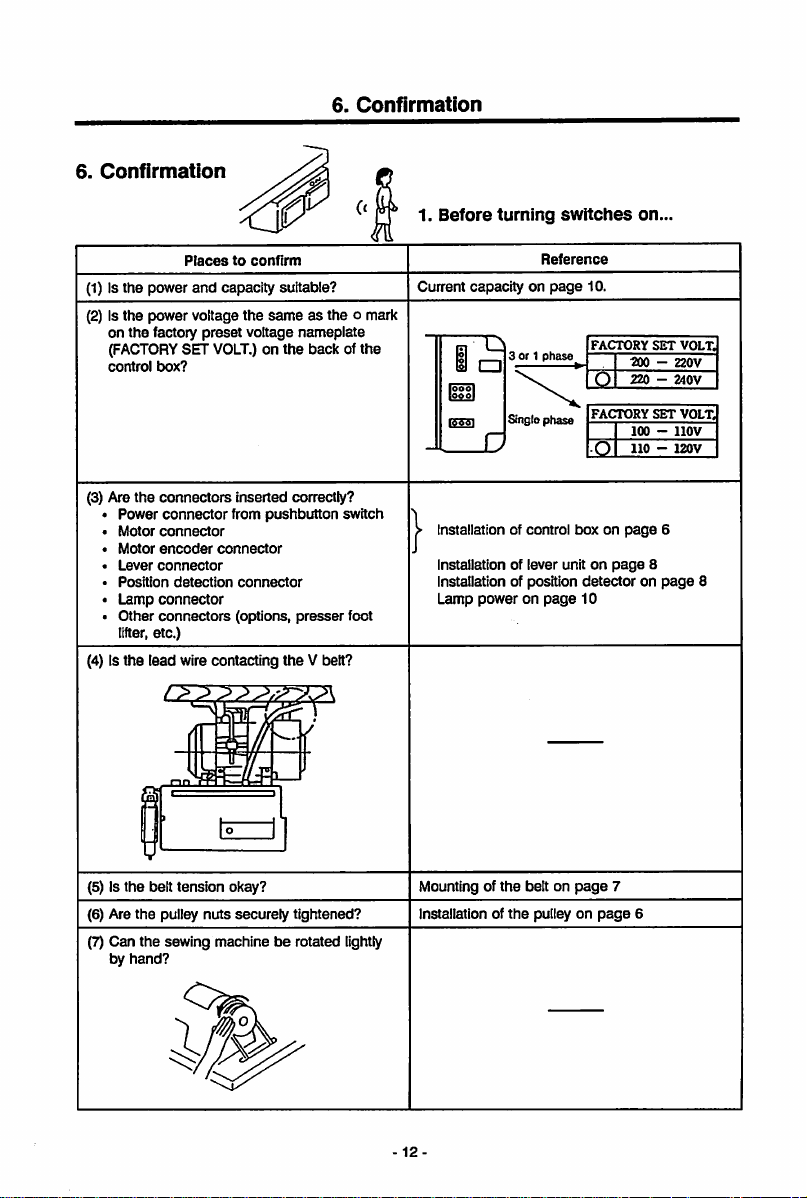
6.
Confirmation
6.
Confirmation
1.
Before
turning
switches
on.
Placestoconfirm
(1) Is the power
(2) Is the power voltage
on
the
(FACTORY
control
(3) Are
• Power
•
Motor
•
Motor
•
Lever
•
Position
•
Lamp
•
Other
lifter,
and
capacity suitable?
the
factory
preset
SET
box?
the
connectors inserted correctly?
connector
connector
encoder
connector
detection
connector
connectors
etc.)
voltage nameplate
VOLT.)onthe
from
connector
connector
(options,
(4) Is the lead wire contacting
sameasthe o mark
back of the
pushbutton
presser
the
switch
foot
V belt?
Current
capacityonpage
lOOOl
n
Installation of
}
Installation of
Installation of position
poweronpage
Lamp
Reference
3 or 1
phase
Single phase
control
lever
10.
FACTORY
700-220V
220-240V
0
FACTORY
100-llOV
110-120V
0
boxonpage
unitonpage
detectoronpage
10
SET
SET
8
VOLT.
VOLT.
6
8
(5) Is the belt tension okay?
(6) Are
the
pulley
nuts
securely
(7) Can
the
sewing machineberotated lightly
by
hand?
tightened?
Mounting of
Installation of
-12-
the
the
belt on
pulley on
page
7
page
6
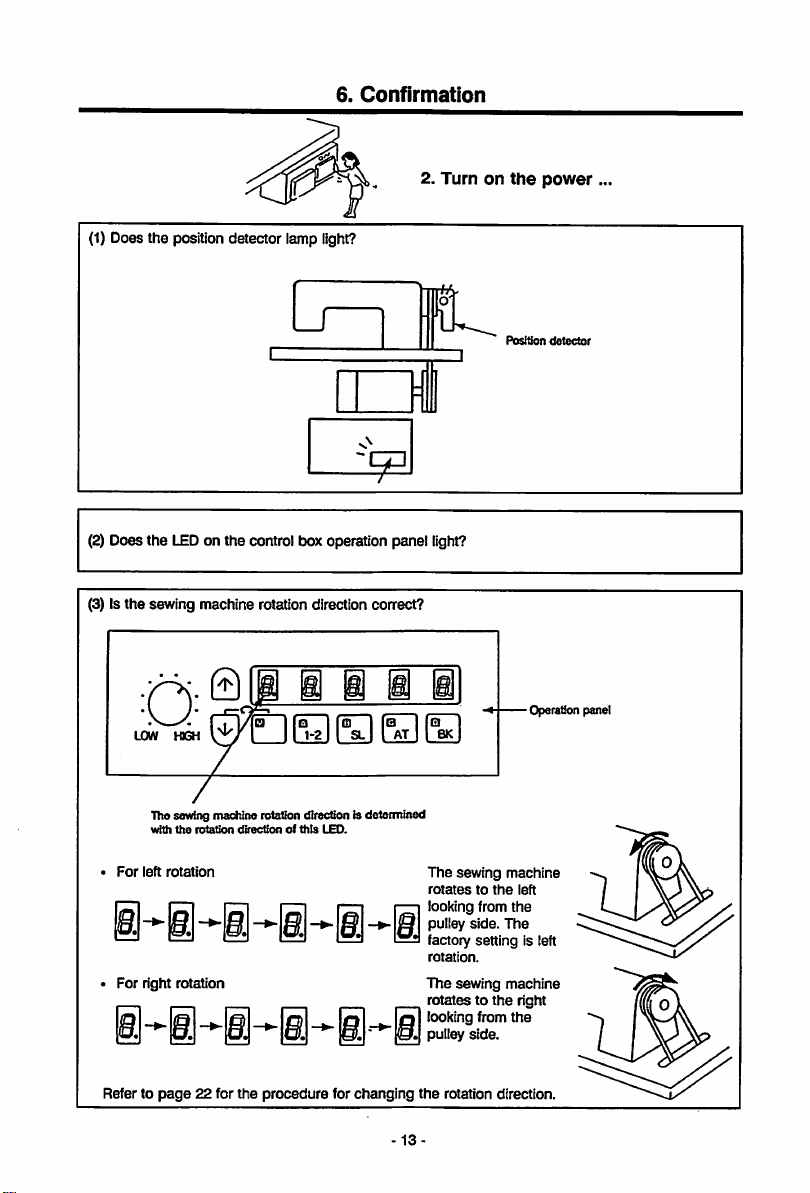
6.
(1) Does the positiondetector lamp light?
Confirmation
2.
Turnonthe
power
Lr
m
I
(2) Does the LEDon the control box operation panel light?
(3) Is the sewing machine rotation direction correct?
0
IB
@ B §
B
B
LOW H3GH
The sewing machine rotationdirecdon is determined
with
the
rotadon
For
left
rotation
For right rotation
dfrectionofthis
LEO.
Cl
SL
BK
AT
The sewing machine
rotatestothe
looking from
pulley
factory setting is left
rotation.
The
rotatestothe
looking from
pulley
Position
-Operation panel
left
the
side.
The
sewing machine
right
the
side.
detector
Refer to
page
22 for the
procedure
for
changing
the
rotation direction.
13
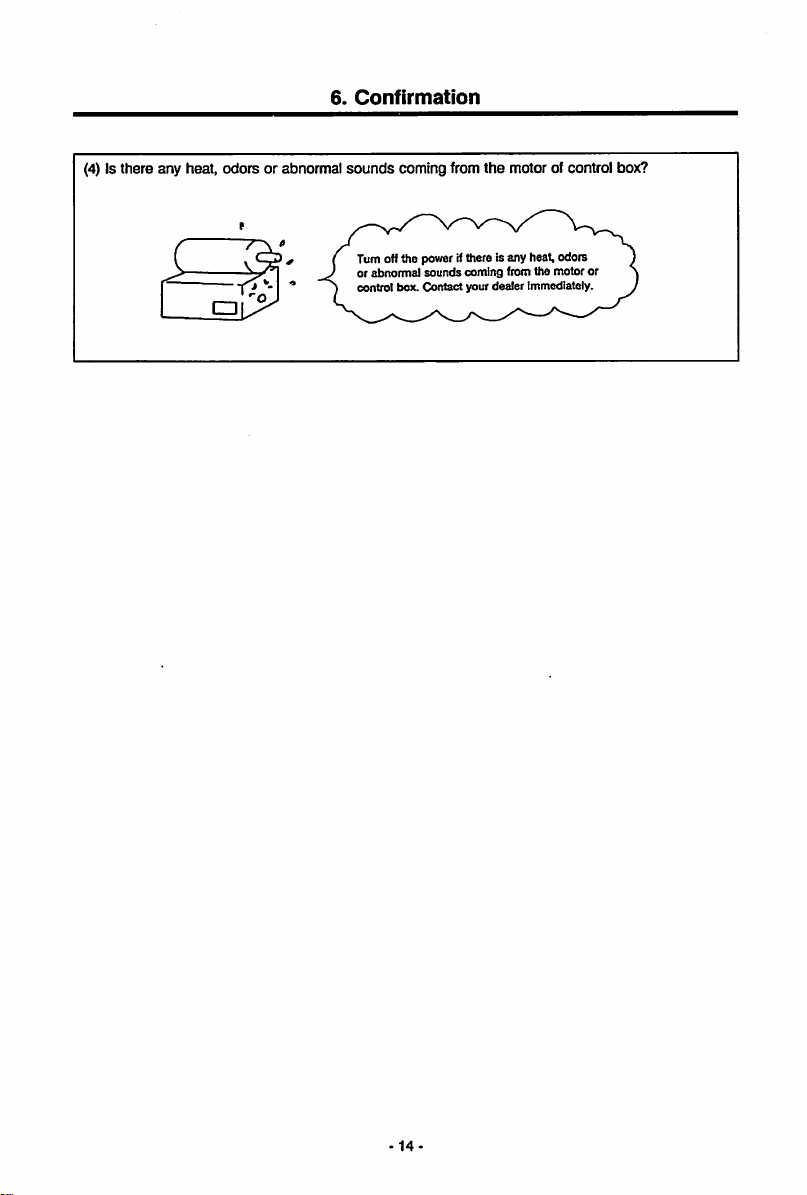
6.
Confirmation
(4) Is there any heat, odors or abnormal
sounds
coming from the motor of control box?
Turnofftfie powerifttiere is any tieat,odors
or
abnormal
sounds
coming
control box. Contact your dealer Immediately.
from the motor or
14
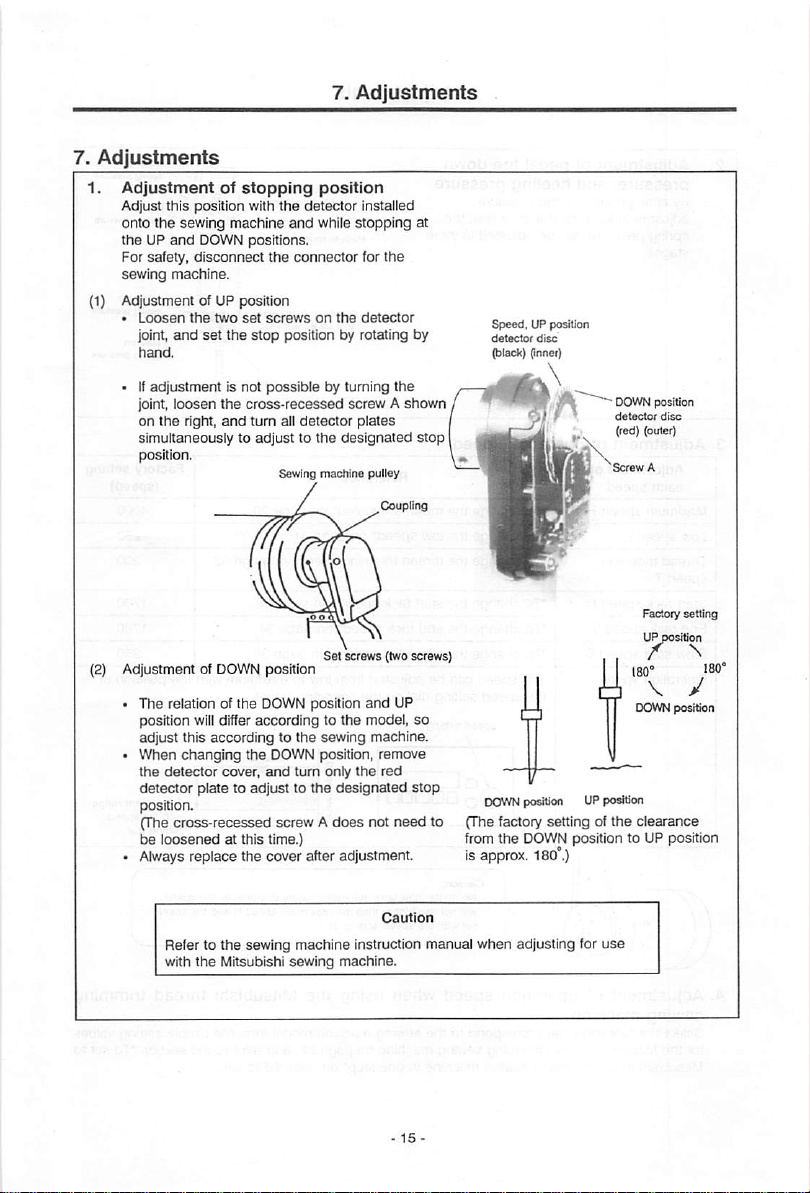
7.
Adjustments
1.
Adjustmentofstopping
Adjust this position with
onto
the
sewing
theUPand
For
safety,
machine
DOWN
disconnect
sewing machine.
(1) Adjustment of UP position
•
Loosen
the
two
right,
set
DOWN
set
the
is not
the
and
joint,
and
hand.
• If
adjustment
joint,
loosen
on
the
simultaneouslytoadjusttothe
position.
Adjustment of
•
The
relation of the DOWN position
position willdifferaccording to the model,
adjust
this
changing
detector
plate to
accordingtothe
cover,
•
When
the
detector
position.
(The
cross-recessed
loosened
be
• Always
replace
at this time.)
the
position
the
detector
and
positions.
stop
cross-recessed
turn
the
adjusttothe
while
the
connector
screwsonthe
position by rotating by
possible
by turning the
all
detector
Sewing
machine
Set
position
sewing machine.
DOWN position,
and
turn
only
screwAdoes
cover
after adjustment.
installed
stopping
for
the
detector
screwAshown
plates
designated
pulley
screws
(two
and
UP
remove
the
red
designated
not
need
at
stop
screws]
so
stop
(The factory setting of
to
from
is
approx.
Speed.
UP position
detector
disc
(black) (Inner)
• DOWN position
detector
(red) (outer)
DOWN
position UPposition
the
the
DOWN position to UP position
180°.)
disc
Factory
clearance
setting
Refer to
with
the
the
sewing
Mitsubishi
machine
sewing
instruction
machine.
manual
when
adjusting for
use
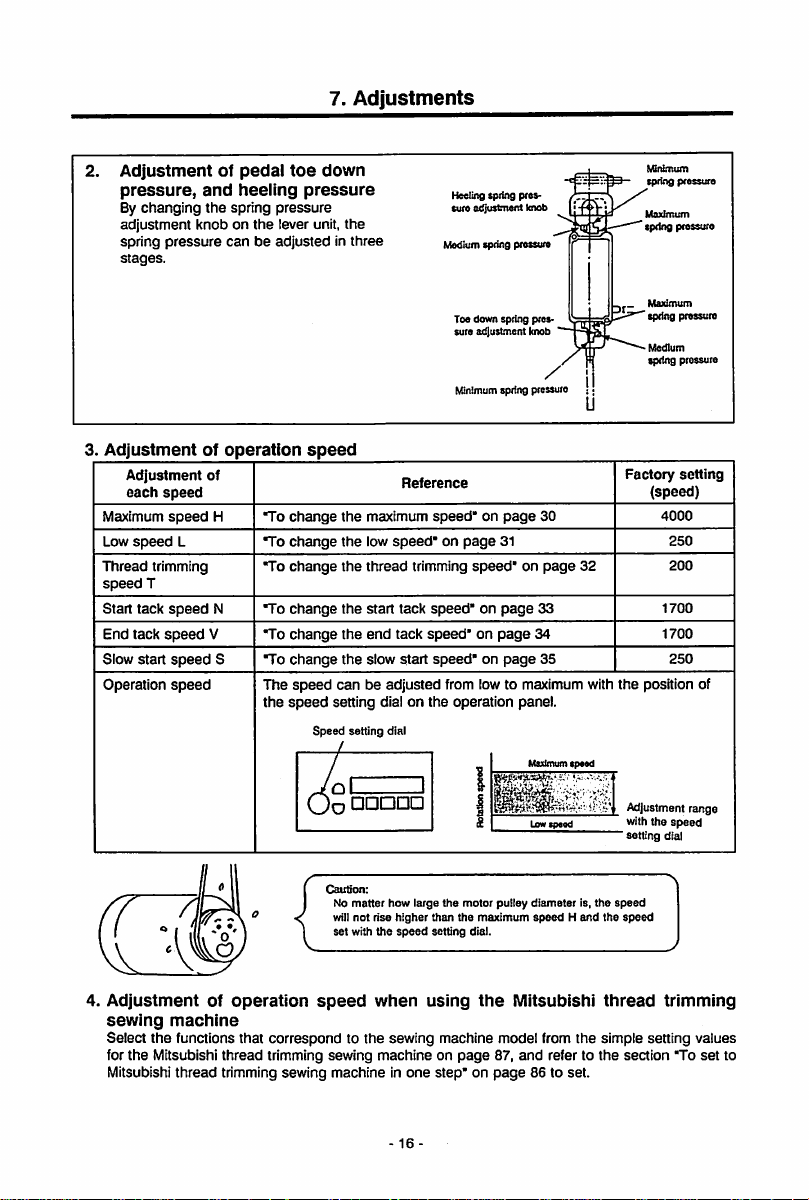
7.
Adjustments
2.
Adjustmentofpedal
pressure,
By
changing
adjustment
spring
stages.
3.
Adjustmentofoperation
Adjustment
each
Maximum
Low
speed
Thread
speed
Start
tack
End
tack
Slow start
Operation
pressure
speed
speed
L
trimming
T
speed
speed
speed
speed
and
heeling
the
spring
knobonthe
canbeadjustedinthree
of
H "To
N
V
S
toe
pressure
lever unit,
change
To
change
To
change
To
change
To
change
To
change
The
the
speed
down
pressure
speed
speed
Speed
Oo
Heeling
tpring
tura
pfes-
ttdjuxtment knob
the
Medium spring
Too down spring pressuto adjustment
Reference
the
maximum
the
low
the
thread
the
start tack
the
end
the slow start
can
be adjusted from low to maximum with the position of
setting dial on
salting dial
/
speed"onpage
speed"onpage
trimming
speed"onpage
tack
speed'onpage
speed'onpage
the
operation panel.
/
pretsjte
Imb
Minimum spring pressure
/
30
31
speed"onpage
33
34
35
Maximum
32
tpeed
I
•••••
1
£
Lowtpeod
Minimum
spring
pressuro
Maximum
tpring prossuro
Maximum
spring pressure
Medium
spring pressure
Factory
setting
(speed)
4000
250
200
1700
1700
250
Adjustmentrange
with the
speed
setting
dial
4.
Adjustmentofoperation
sewing
Select
for
Mitsubishi
machine
the
functions that correspond to the sewing machine model from the simple setting values
the
Mitsubishi thread trimming sewing machine on
thread
trimming sewing machine in
Caution;
No
will not rise
set
speed
matter
with
how large the
higher
the
speed
when
one
16
than
setting
using
step* on
motor
the
dial.
page
pulley
maximum
the
Mitsubishi
87,
page
diameter
speedHand
and
refer to
86 to set.
Is,
the
speed
the
speed
thread
the
section "To
trimming
set
to
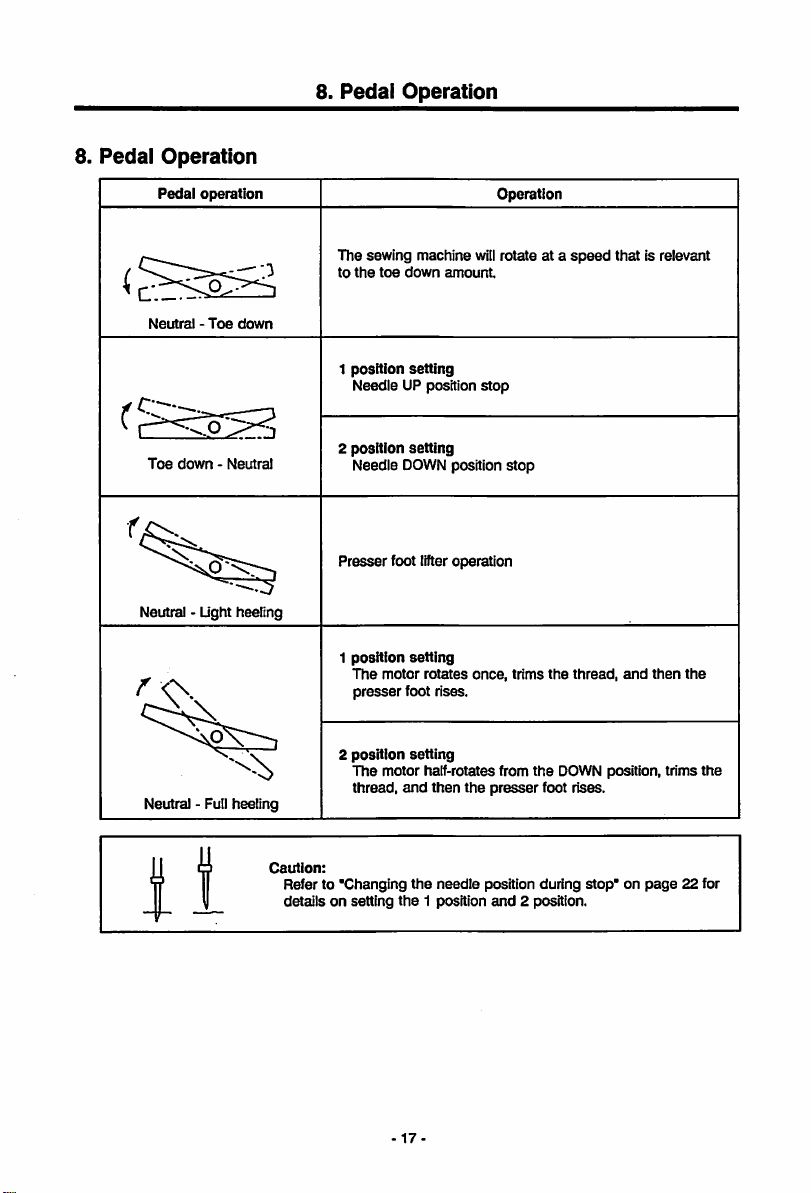
8.
Pedal
Operation
Pedal
operation
8.
Pedal
Operation
Operation
Neutral-Toe
Toe
down-Neutral
Neutral - Light heeling
down
/'O.
Neutral - Full heeling
The sewing machine willrotate at a
to
the toe
down
amount.
1
position
setting
Needle UP position
2 position
setting
Needle DOWN position
Presser
foot lifteroperation
position
1
2
setting
The
motor
presser
foot rises.
position
setting
The
motor half-rotates from
thread,
and
rotates
then
once,
the
stop
presser
stop
trims
the
foot rises.
speed
that is relevant
the
thread,
and
then
DOWN position, trims
the
the
1
1
Caution:
Refer to
'Changing
detailsonsetting
the
-17-
the
needle
1 position
position during stop* on
and
2 position.
page
22 for
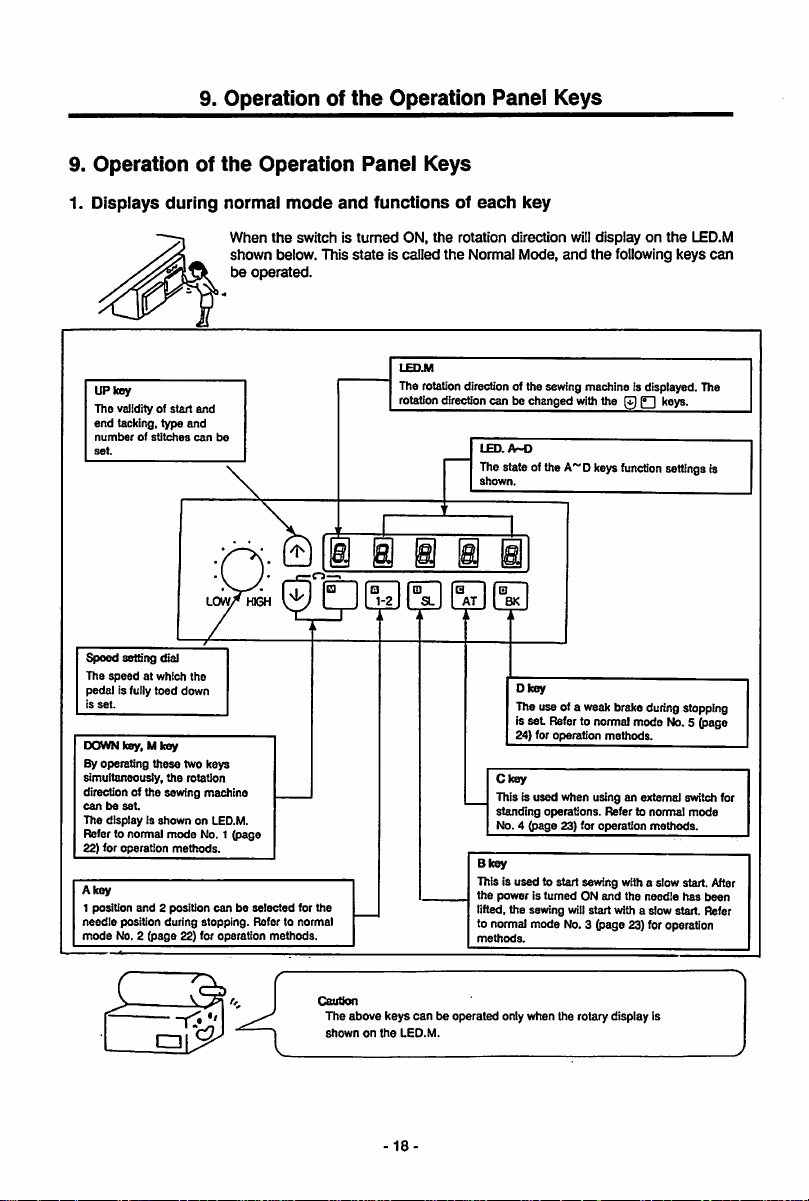
9.
9.
Operationofthe
1.
Displays
UP key
The validity of
end
numberofstitches
Speed
The
pedal
Is
set.
DOWN key, M key
By operating
simultaneously,
direction of the sewing machine
canbeset.
The
Refer to normal
22) for operation
Akey
1 position
needle
mode
during
start
tacking, type
setting dial
speed
is fully
displayisshown
and
position during
No. 2 (page 22) for operation methods.
and
at which the
toed
down
these
two keys
the
rotation
mode
methods.
2 position
and
can
LOWT* HIGH
on LED.M.
No. 1 (page
stopping.
Operationofthe
Operation
normal
be
canbeselected
When
the
shown
be
operated.
Refer to normal
mode
switch is
below. This
•
for the
and
Operation
Panel
turned
state
Keys
functionsofeach
ON,
the
is called
LED.M
The rotationdirection of the sewing machine is displayed. The
rotation
• (D Q
1-2
SL
Panel
Keys
key
rotation direction will
the
Normal Mode,
direction
canbechanged
LED.
A-O
Thestate ofthe A~D keys
shown.
R
AT
BK
Dkey
The use of a weak brake duringstopping
set
is
24) for operation methods.
Ckey
This Is
used
standing
No. 4 (page 23) for operation
Bkey
This is used to start sewing with a slow start. After
the
poweristurnedONand
lifted, the sewing willstart with a slow start. Refer
to normal mode No. 3 (page 23) foroperation
methods.
displayonthe
and
the
with
the0P~|
Referto normalmode No. 5 (page
when using an extemal switch for
operations.
Refer to
following keys
keys.
function
settingsis
normal
methods.
the
needle
has
LED.M
can
mode
been
Cautkm
The
above
shownonthe
keys
canbeoperated
LED.M.
18
only when the rotary display is
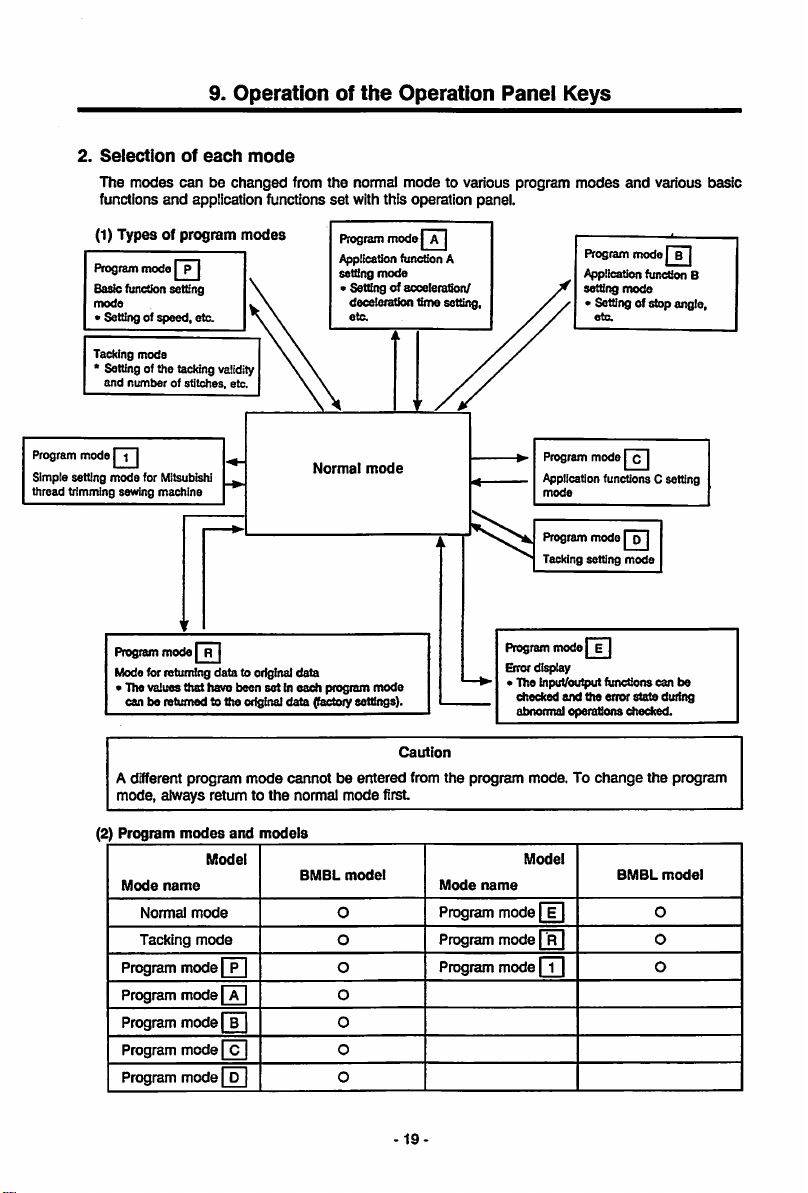
2.
Selection
The
modes
functions
(1)
Typesofprogram
Program
Basic (unction setting
mode
• Setting of
Tacking
* Settingof the tacking
and
numberofstitches,
Program
mode
| i |
Simple setting
thread trimming sewing
mode
Program
Mode for returning
• The values
can be returned to the ortginaldata (factoiysettings).
of
canbechanged
and
application functions
mode
I p |
speed,
etc.
mode
for Mitsubishi
machine
mode
that
9.
Operationofthe
each
mode
from
modes
validity
etc.
Normal
data
to original
have been set In
data
each
Operation
the
normal
set
Program
Applicationfuncfion A
setting
« Setting of acceleration/
program
mode
with this operation panel.
mode
| A|
mode
deceteration tinne setting
eta
mode
mode
Panei
to various program
Program
Appiication
mode
Program
Tacking setting
Program
mode}
Error display
• The input/output functions can tie
checked
abnormal operationschecked.
Keys
modes
and
Program
mode
Application function B
setting
mode
• Setting of stop angle,
eta
mode
[c |
functions C setting
mode
| p |
mode
E|
and
the
error
state
various
| b j
during
basic
A different program
mode, always return to
(2)
Program
Mode
modes
name
Normal
Tacking
mode
mode
Model
and
mode
the
models
Programmode| P | O
Programmode| A | O
Program
mode| B | O
Program
mode
Program
mode
cannotbeentered
normal mode first
BMBL
model
O
O
O
O
Caution
from
the
program mode. To
Model
Mode
name
Program
mode
fil
Programmode|°R| O
Program
mode
fTl
-19
change
BMBL
the
0
O
program
model
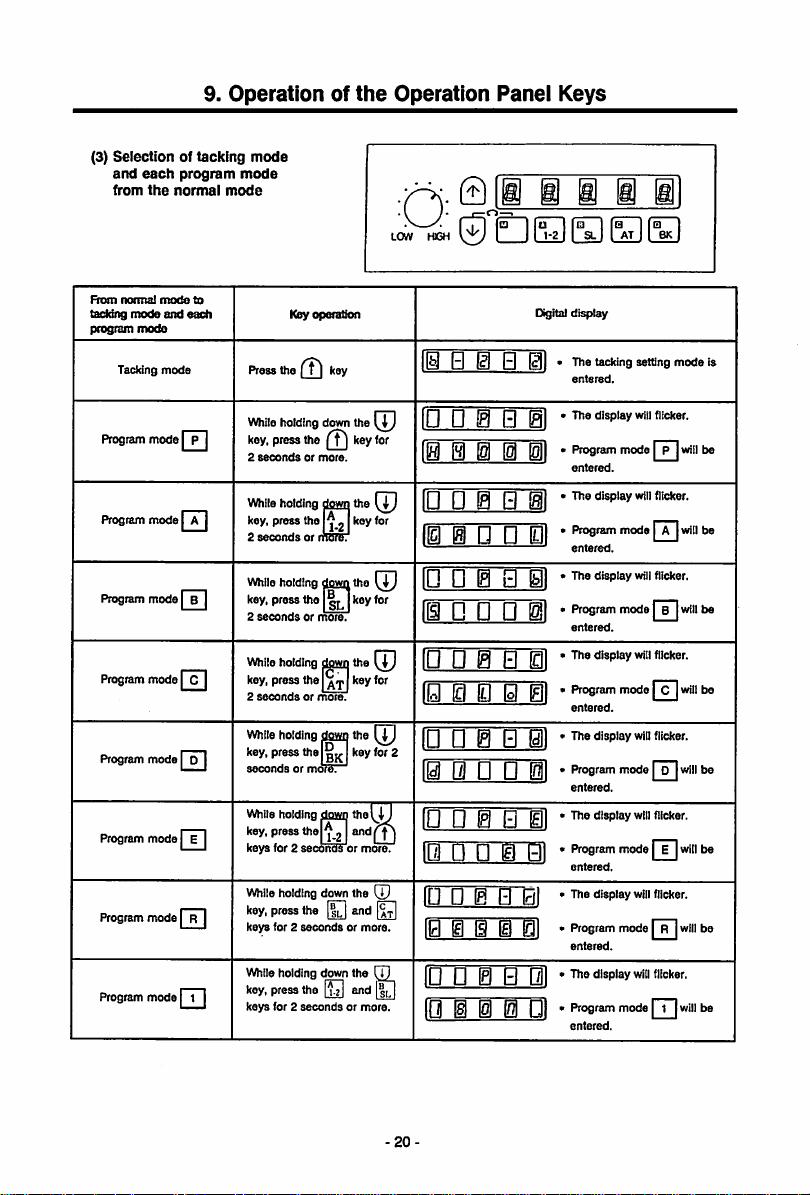
(3)
Selectionoftacking
and
each
notmal
mode
the
mode
normal
modeto
and
mode
program
from
From
taddng
program
Tacking
9.
Operationofthe
mode
mode
mode
each
Press
the key
Key
operation
Operation
011
11^
El
Panei
Q
@1•The
Keys
i
Digital
IBS
ID Q 0
SL AT BK
display
tacking
entered.
setting
mode
is
Program
Program
Program
Program
Program
Program
Program
Program
mode
mode
mode
mode
mode
mode
mode
mode
| p |
[ A|
| B |
| C |
| p [
| E |
[ R |
| i |
While holding down the
key,
press
the key for
2
secondsormore.
Whileholding dowri the
key,
press
f'lo1^j
2
secondsorrmSrST
While
holding
press
the |
holding
press
fitol
press
f>te key for 2
holding
press
the
for 2
secondiormore.
holding
press
the
secondsormore.
holding
press
the
for 2
secondsormore.
dowri
dowij
^tI
down
down
[|2
down
key,
2
secondsormore.
While
key,
2
secondsormore.
While holding dowri the
key,
secondsormof^.
While
key,
keys
While
key,
keys for 2
While
key,
keys
the
Ijrj
key
for
the
the^J
(i)
the
[p
and
[|3
the
Q]
and
l|n
fill
D ® 0
10 0
10 D 0
IIS
0 • n Bl '
' '
IE)
0 @ 0 0] *
@1*tl'spiay
IS
0 01 •
El
0l *
10 0 0 0 0l *
10 0 @ 0 0! *
10 0 0 0
@1•P'«>sram
r0 0 @ 0 0] *
10 0 0 0 01 *
rO 0 0 0 0] *
0 0 0 0
ID 0 E 0 01 *
10 E @HI01 »
0l*Program
r0 0 0 0 Ql *
[Q H 0 0 01 *
Program
mode
entered.
display
Pwgiam
mode
entered.
display
PfogtaAT
mode1B[will
entered.
mode
entered.
display
Program
mode
entered.
'"®P'®y
mode
entered.
display
Program
mode
entered.
display
Program
mode]t[will
entered.
will
will
will
will
^"1
will
will
| p
fT)
| D
| E|
Er~|
flicker.
flicker.
[will
flicker.
will
flicker.
will
flicker.
[will
flicker.
will
flicker.
will
be
be
be
bo
be
be
bo
be
20-
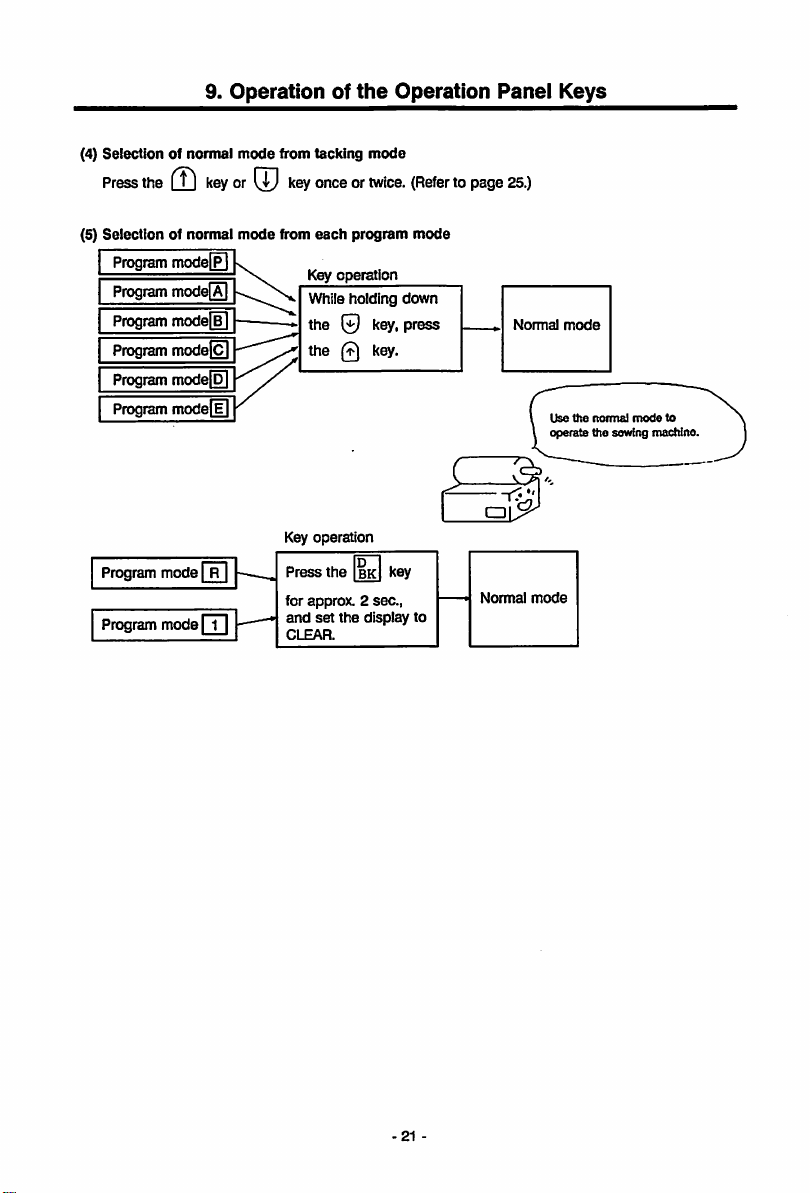
(4)
Selectionofnormal
Press
the
(Tl
(5)
Seiectionofnormal
Program
Program
modeQ
Program
mode[B]
Program model
Program
modefol
Program
Program
mode
Program
mode
9.
Operationofthe
mode
keyor[5
mode
modeE
modefll
[r^
[T]
from tacking
key
onceortwice.
from
each
Key
operation
While holding
the
0
the
Q
Key
operation
Press
the
for
approx.2sec.,
and
set
the
CLEAR.
mode
program
key,
key.
D
key
BK
display
Operation
(Refertopage
mode
down
press
to
Panel
Normal
25.)
Normal
mode
Keys
mode
Use
the
operate
normal
the
mode
sewfng
to
machine
-21
-
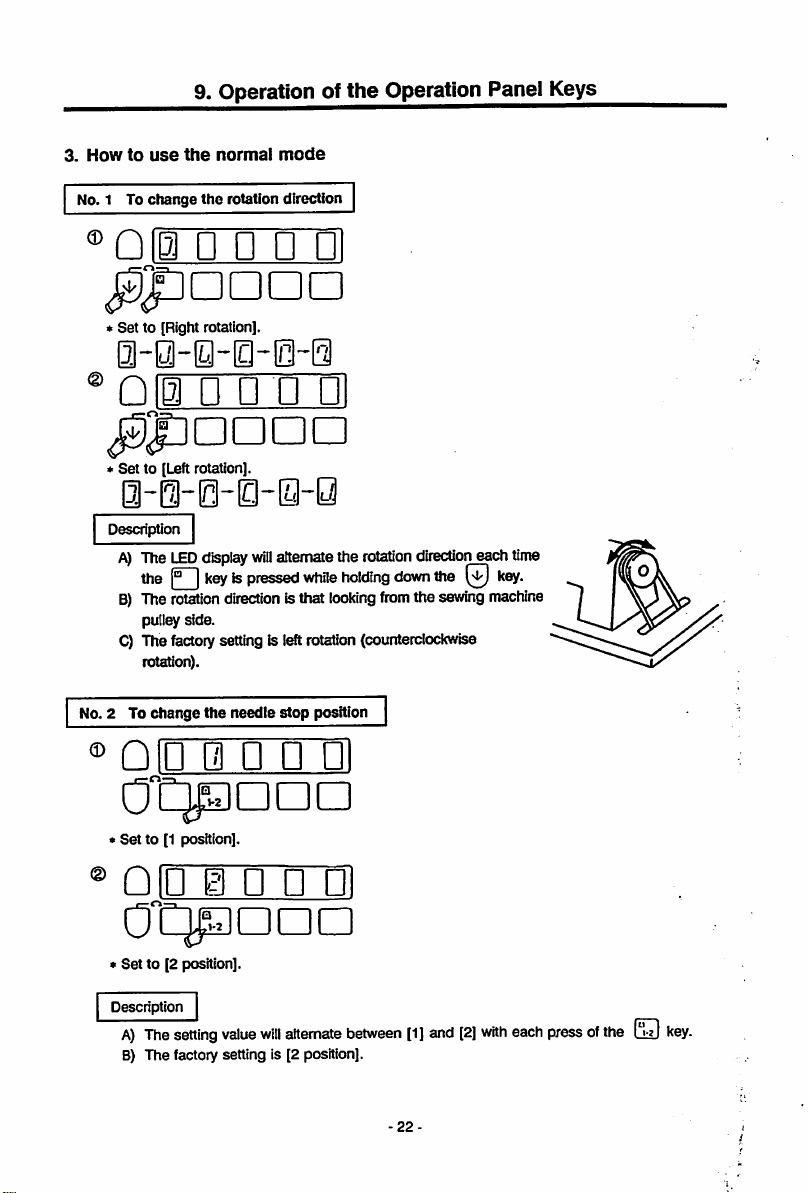
3.
Howtouse
9. Operation of
the
normal
mode
the
Operation Panel Keys
No. 1 To
change
the
OB
•
'Q
Set
0-
Set
D U U 0
to [Right rotation].
3~0~[3 lcl~0
0 • • • •!
to [Leftrotation].
rotation
direction
0-@-0-0-0-y
Description
The
LED
display
wili
alternatethe
the1°I
B)
The
pulley side.
C) Thefactorysetting is leftrotation(counterclockwise
rotation).
No. 2 To
®
Qin
keyispressed
rotation
change
the
0 • • •!
direction
needle
isthat
stop
while
looking
position
rotation
holding
down
from
direction
the
the
sewing
each time
key.
machine
*
Set
to [1 position].
®Qjg 0 • •
0
CjpZI
*
Set
to [2 position].
Description
A)
The
setting
B) The factory setting is [2 position].
Dn
value
will
ni
CD
alternate
between
22-
[1]
and
[2]
with
eachpressofthe
fin
Li±J
key.
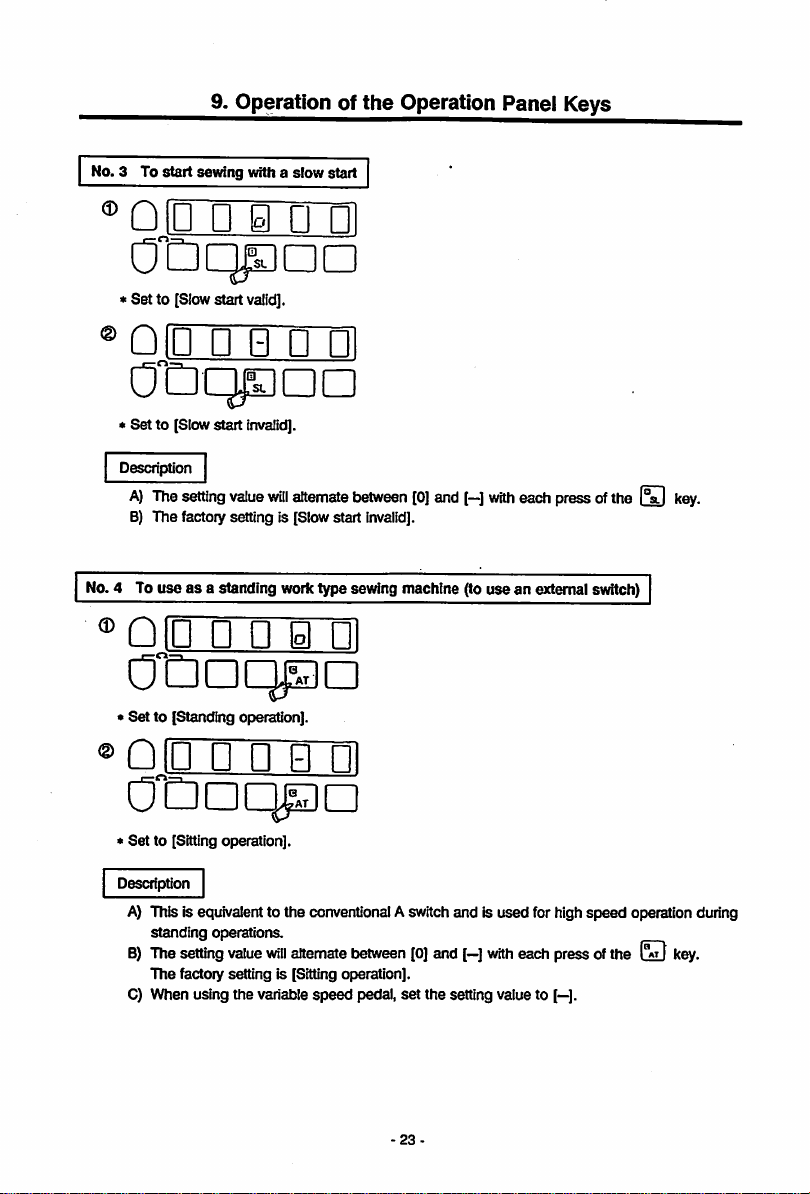
9. Operation of
the
Operation Panel Keys
No. 3 To
start
sewing with a slow start
"^QlU • H n p]
* Set to [Slow start valid].
®QIU • B • PI
OtDqpoD
• Set to [Slowstart invalid).
Description
A)
Thesettingvalue
B) The factory setting is [Slowstart
No.4 To use as a standing worktype sewing machine (to use an externalswitch)
will
alternatebetween[0]and
invalid].
[—]
with
each press ofthe
Q IP P P H PI
OtlDC^D
• Set to [Standing operation].
key.
®
Qip
p p n PI
Otiaqpn
*
Set
to [Sitting operation].
Description
A) This is equivalentto the conventionalAswitch and Is used for high
standing
8)
The
The factory setting is [Sitting operation].
C) When using the variable
operations.
setting
value
vrill
alternate
tjetween
[0]
and
speed
pedal, set the setting valueto
-23
[—]
with
speed
each
pressoftheQkey.
[—].
operation during
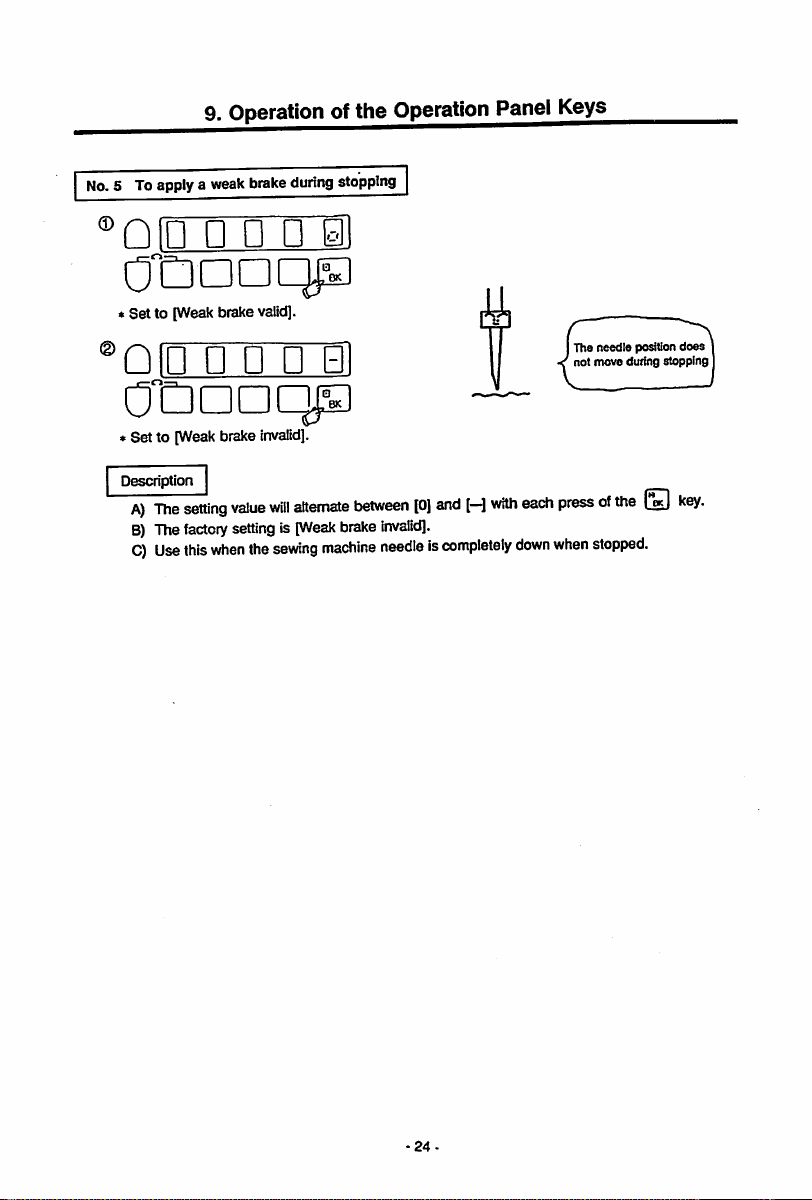
9. Operation ofthe Operation Panel Keys
No.5 To applya weakbrakeduringstopping
®nin
«Set to [Weakbrake valid].
®Qin
• Set to [Weak brake
Description
A)
B)
C)
The
The
Use
n • u
n • •
setting
value
factory
settingIs[Weak
this
when
invalid].
will
the
sewing
B1
alternate
between
brake
machine
[0]
and
[—]
with
invalid].
needleiscompletely
down
The needle position
not move during stopping
each
pressofthe
when
does
L®eJ
stopped.
24