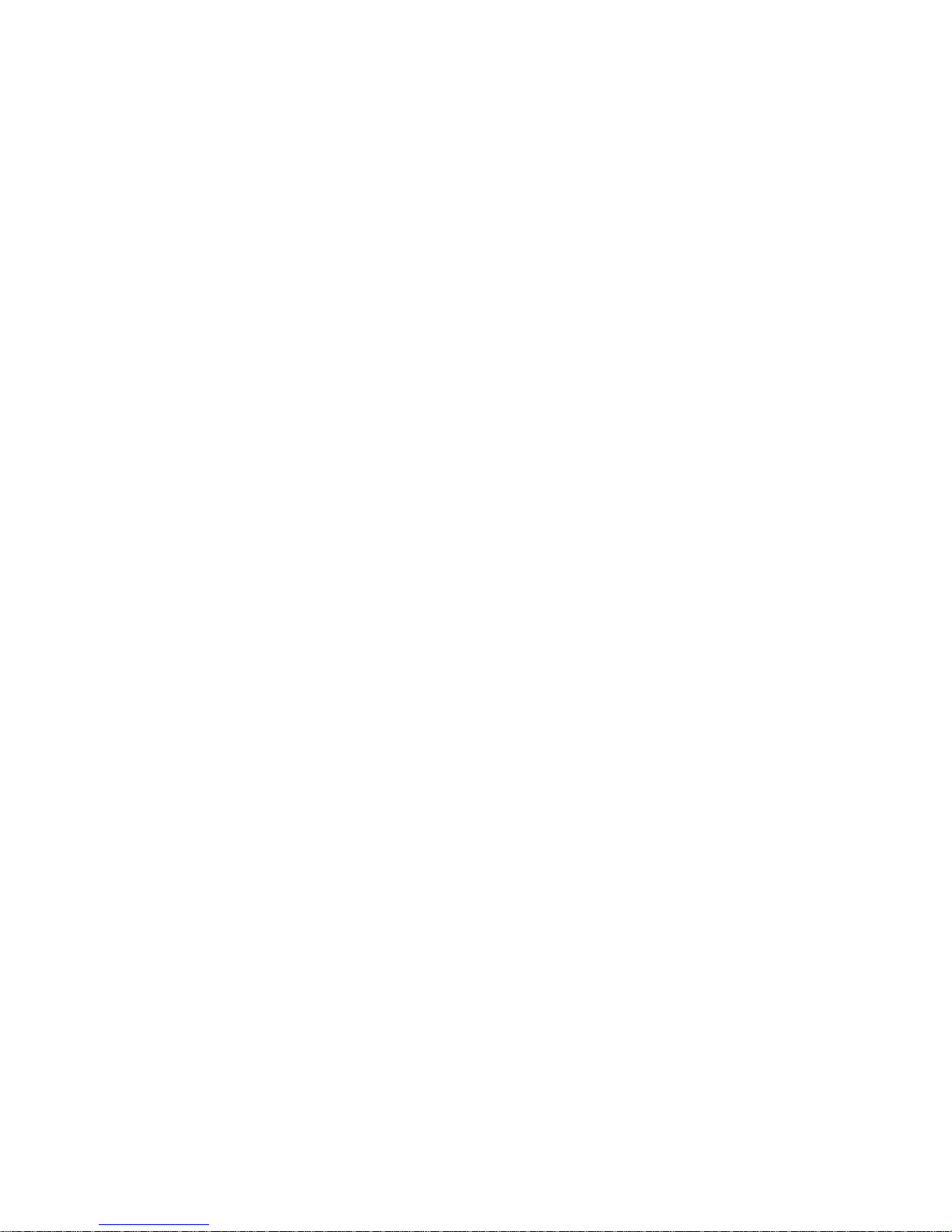
Electrical Alignment Instructions
Page
- Technical data ................................................................................ 3
- Playback ......................................................................................... 4
1. Azimuth Adjustment
2. Tape Speed Adjustment
3. Output Level Adjustment
4. DNL Adjustment
- Recording ...................................................................................... 4
1. OSC Frequency Adjustment
2. Bias Trap Adjustment
3. Bias Current Adjustment
4. Dolby Nr. Bias Trap Adjustment
5. Input Sensitivity Adjustment
6. Level Meter Adjustment
7. Record Current Adjustment
8. Peak Indicator Level Adjustment
9. ALC Balance Adjustment
- Electrical Adjustment Procedure .......................................... 5+6
1. DC F.G. Servo Motor
2. RIP Head (Azimuth)
3. Dolby P.C.B.
4. DNL P.C.B.
5. Power P.C.B.
6. Pre Amp. P.C.B.
Mechanical Alignment Instructions
Page
- Tape Speed................................. 7
- Wow and Flutter ............................................................................... 7
- Mechanical Adjustment ........................................................ 8 + 9
1. Pinch Roller Pressure Measurement
2. Azimuth, Head Location Adjustment
3. Tape Speed Adjustment Location
Mechanical Parts List ........................................... 10-14
- Take-up Torque ............................................................................... 7
- Fast Forward and Rewind Torque ................................................... 7
- Pinch Roller Pressure ...................................................................... 7
- Tape Speed / Wow and Flutter ........................................................ 7
- Azimuth Head, Alignment ................................................................ 7
Electrical Parts List
............................................ 15-21
Drawings
- Muting SW P.C.B. .................... ..................................................... 22
- Reed SW P.C.B. ...................... ..................................................... 22
- Mic Jack P.C.B. ........................ ..................................................... 23
- Auto Stop P.C.B. ...................... ..................................................... 24
- DIN/RCA Jack P.C.B. ............... ..................................................... 25
- Power Supply P.C.B. (Bottom View) .............................. 26
- Power Supply P.C.B. (Top View) ................................... 27
- LED P.C.B. ............................... ..................................................... 28
- Peak Level LED P.C.B. ............ ..................................................... 28
- PRE P.C.B. (Bottom View) .............................. 29
- PRE P.C.B. (Top View) ................................... 30
- Dolby P.C.B. (Bottom View) ............................. 31
- Dolby P.C.B. (Top View) ................................... 32
- Push SW P.C.B. (Bottom View) .............................. 33
- Push SW P.C.B. (Top View) ................................... 34
- DNL P.C.B. ............................... ..................................................... 35
- Exploded drawings ................... ............................................... 36+37
- Exploded and Lubrication drawings ......................................... 38+39
Wiring Diagram.......................... 40
Electrical Circuit Diagram ................................ ......... 40

Technical data
Mains voltage:
220 V, can be resoldered for 110 V (Europe)
240 V (UK)
117 V (USA, ANP, Canada)
Mains frequency:
50 - 60 Hz
Power requirement:
0 W
Motors:
1 DC-motor with servo control
Cassettes:
Compact cassette:
Chrome dioxide BASF CrO
2
C 60 C 401 R
Standard TEAC MTT-502
Tape speed:
4.76 cm/s
Fast forward and rewind:
<75 s with C 60 cassette
Erase and bias frequency:
105 kHz
Level meter:
2 VU-meter
1 Peak Level Indicator
Dolby Level at
± 3 dB
Inputs: (for Dolby level)
1. Microphone input with DIN plug for low-impedance
microphones
Sensitivity: 330 µV imped. about 5.6 kOhms
Max. input voltage: 33 mV
Electret microphones: + 5 V max. 0.5 mA
2. Input DIN plug connections 1 + 4
Sensitivity: 0.33 mV impedance: 5.6 kOhms
(0.06 mVikOhm)
Max. input voltage: 33 mV
3. Line input PHONO plug
Sensitivity: 33 mV impedance: 560 kOhms
Max. input voltage: 3.3 V
4. Phono Input (DIN) DIN Plug connection 3+5
Sensitivity: 200 mV impedance: 3.3 mOhms
Outputs: (for Dolby level)
1. DIN plug, pin 3+5: 1000 mV impedance: 15 kOhms
2. LINE output (PHONO): 1000 mV impedance: 15 kOhms
3. Headphone output: 200 mV impedance: 8 kOhms
Harmonic distortion (333 Hz): (for 0 dB VU)
Standard cassette:
< 2.0 %
Ferri chrome cassette: < 2.0 %
Frequency response with: 20 dB VU
Standard cassette: 30-15000 Hz ± 3 dB
Ferri chrome cassette: 30-16000 Hz ± 3 dB
Wow + Flutter:
to WRMS < 0.06 % to DIN 45507 weighted
< ± 0.14 %
Signal/noise ratio: (DIN 45500)
(Reference 3 % third harmonic distortion)
Standard cassette: 53 dB 58 dB
Ferri chrome cassette: 54 dB 60 dB
without Dolby with Dolby
Cross talk: (1000 Hz)
with two track recording in opposite directions: > 60 dB with
stereo recording:
> 35 dB
Erase attenuation: (1000 Hz, full modulation Cr02 tape) >
62dB
Dimensions:
268 x 424 x 107 mm
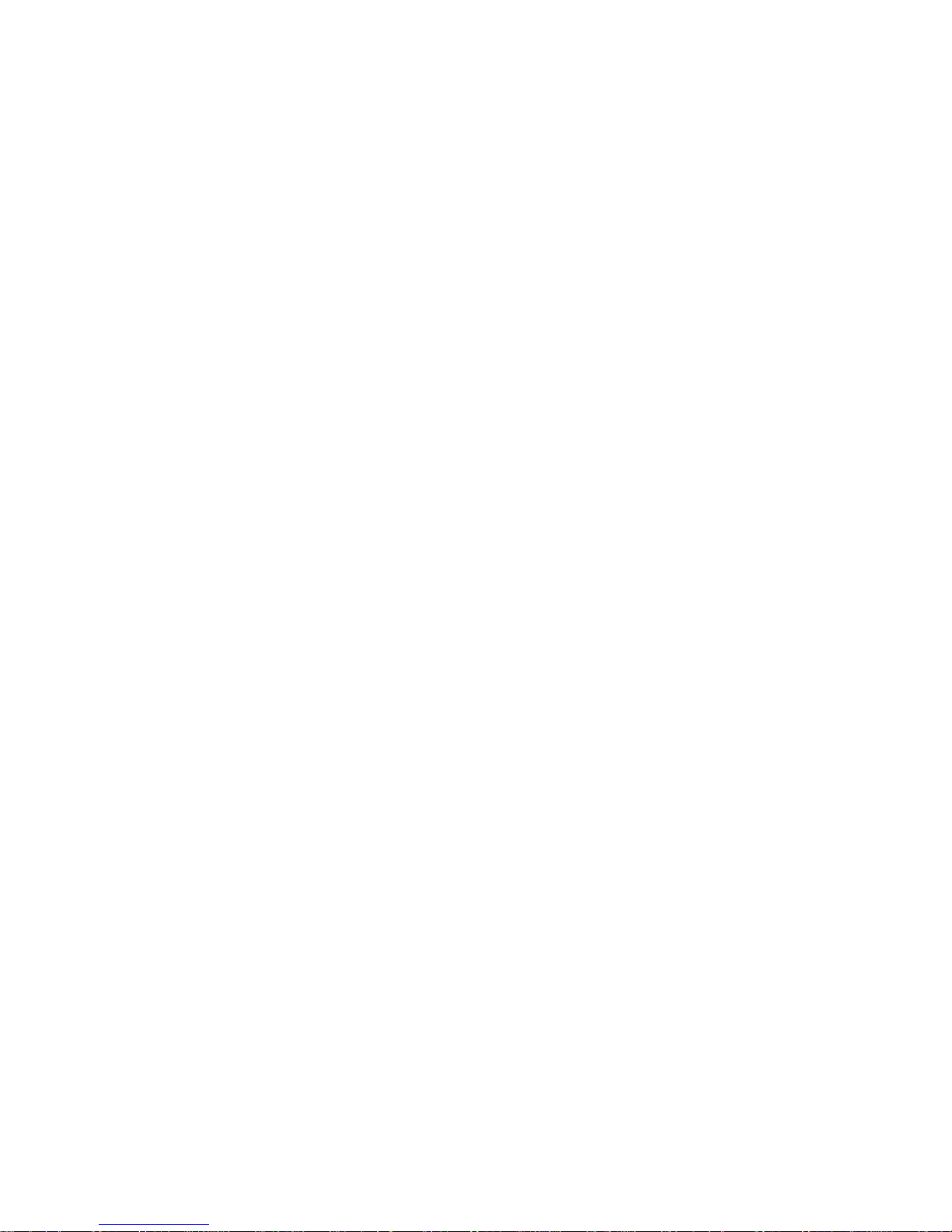
1. Azimuth Adjustment
Connect a scope or VTVM to the right channel PRE-AMP OUTPUT
jack. Insert a test tape (TEAC MTT-114, 115) into the unit. Adjust the
Azimuth adjusting screw for maximum output into the right channel.
(See figure 1 R/P HEAD.)
2. Tape Speed Adjustment
Connect scope, VTVM and FREQUENCY COUNTER to the right
channel PRE-AMP OUTPUT jack. Insert a Test Tape (MTT-111 3
kHz) into the unit. Adjust the tape speed adjusting screw for a 3 kHz
value in the frequency counter. (See fig. 1 DC F.G. Servo Motor.)
3. Output Level Adjustment
Connect scope and VTVM to the TP-2 and Ground (L-ch and R-ch).
Insert a test tape MTT-150 (Dolby level calibration tape 200 nwb/m)
into the unit. Adjust the P 104 (left) and P 204 (right) for a 580 mV
reading.
4. DNL adjustment
Connect a scope to the PRE-AMP OUTPUT jack. Set the unit for a
PLAY function, then depress the PAUSE button, DNL switch, ON.
Adjust the VR 501 (L-ch), VR 601 (R-ch) so that the level of high
frequency noise is at a minimum on the scope. (See fig. 1, DNL
P.C.B.)
1. OSC Frequency Adjustment
Connect the scope and frequency counter to the terminals of the
erase head. Set the unit for recording. Adjust L 1 so that there is an
OSC frequency value of 105 kHz on the frequency counter. (See fig.
1 Power P.C.B.)
2. Bias Trap Adjustment
Connect the scope and VTVM to the TP-3 and Ground. (See fig. 2.)
Set the unit for recording. Adjust the L 104 (L-ch) and L 204 (R-ch) so
that the level on the VTVT is at a minimum. (See fig. 2.)
3. Bias Current Adjustment AF
Generator
333 Hz
1 kHz
0 dB - 1 V
Attenuator 95 dB Unit
Mic. Input L
R
V.T.V.M.
Scope
Connection should be made as above. Set the unit for recording. For
Fe 203, adjust C 133 (L-ch), C 233 (R-ch) to flat level at between 333
Hz and 10 kHz. For Cr02, adjust C 134 (L-ch), C 234 (R-ch) to flat
level at between 333 Hz and 12,5 kHz. (See figure 2.)
4. Dolby NR Bias Trap Adjustment
Connect the VTVM and scope to the test point pin on the Dolby
P.C.B. (See figure 1).
Set the unit for recording. Dolby NR switch "ON" position. Adjust L
303 (L-ch), L 403 (R-ch) for the minimum indication on the VTVM.
5. Input Sensitivity Adjustment AF
Generator
333 Hz
0 dB - 1 V
Attenuator
-70 dB Unit
DIN Input
L
R
TP-2
V.T.V.M.
Scope
Connection should be made as above. Set the unit for recording.
Record level controls (P 103, P 203) set at maximum. Adjust P 102
(L-ch), P 202 (R-ch) for 580 mV reading at TP 2 (L-ch, R-ch). (See
figure 2.)
6. Level Meter Adjustment
Connection should be made as for ADJUSTMENT 5. When
ADJUSTMENT 5 has been completed (580 mV rading at TP a),
adjust P 107 (L-ch), P 207 (R-ch) for +3 VU reading on level meters
(L-ch, R-ch). (See figure 2.)
7. Record Current Adjustment
Connection should be made as in ADJUSTMENT 5. Feed -70 dB
(333 Hz) into the DIN input. Set the record level controls (103/203) to
maximum.
Make a recording (use blank tape) then playback what has been
recorded and adjust P 105 (L-ch), P 205 (R-ch) for Fe 203 Tape, P
106 (L-ch), P 206 (R-ch) for Cr02 Tape so that the output at TP 2 has
a value of 580 mV. (See figure 2.)
8. Peak Indicator Level Adjustment
Set the unit for recording. Feed -68.5 dB (1 kHz) into the DIN input
Left and Right channels.
Adjust P 2 until the peak level indicator lights up. (See fig. 2).
AF Generator
1 kHz
0 dB = 1 V
Attenuator
-68.5 dB (1 kHz)
DIN Input
L
R
Unit
9. ALC Balance Adjustment
Disconnect R 1 (or cut the foil pattern) so that the Bias OSC is
stopped. Set the ALC switch to the "ON" position and keep the unit
set at recording. Feed -50 dB (1 kHz) signal into the DIN input Left
and Right channels. Adjust P 1 so that the value of the level meter on
Left and Right channel will be the same. (See figure 2 ALC
BALANCE).
AF Generator
1 kHz
0 dB = 1 V
Attenuator -50 dB
(1 kHz) Unit
DIN Input
L
R
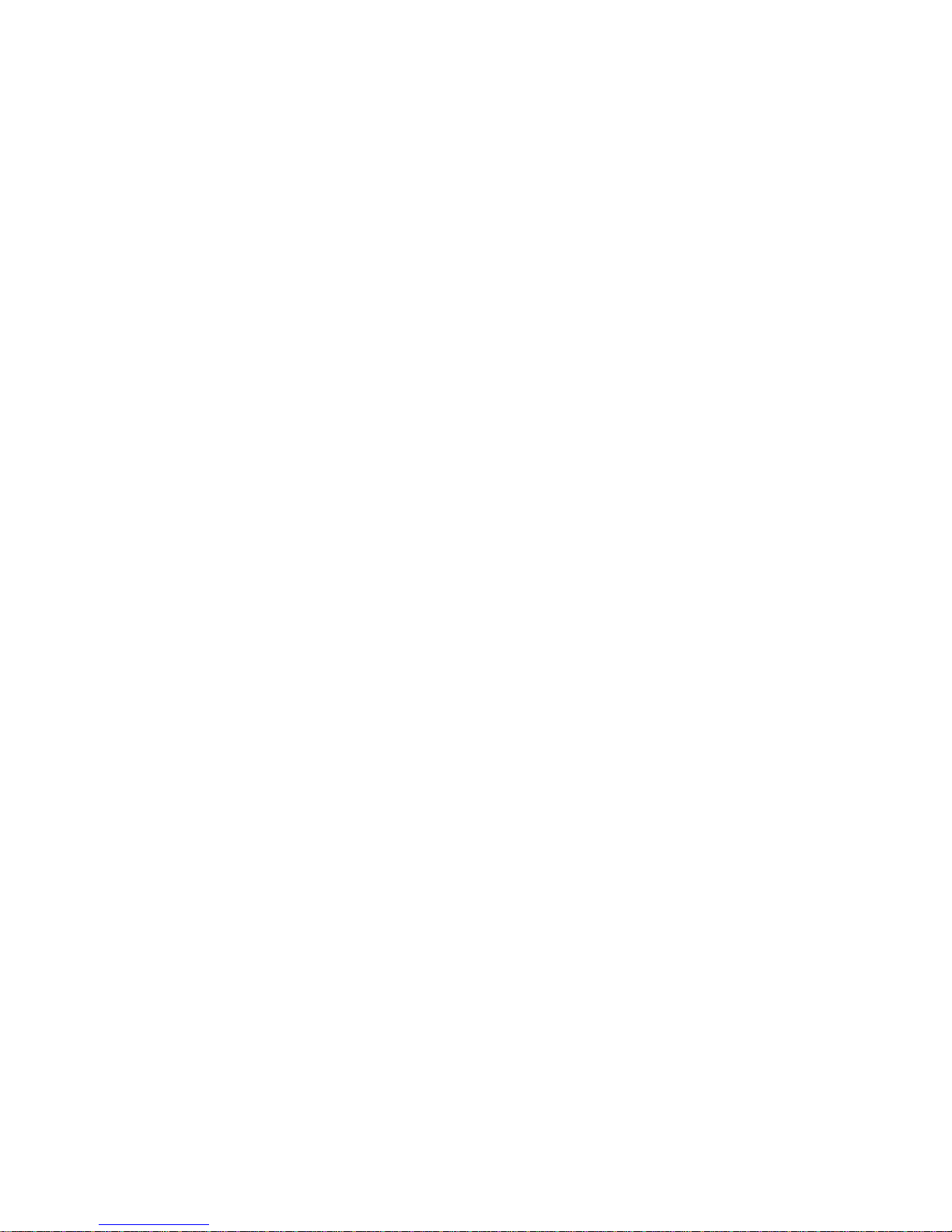
Mechanical Checks and Adjustments
Model C 1102
Note:
All the mechanical checks and alignments should be
done with the upper and bottom cabinet assembly (A-1 and A-
2) removed.
Take-up Torque
(Spec. 30-60 g/cm)
1.
Load the torque meter cassette.
2.
Set the unit in the play mode and read the value on the dial
scale. The meter should indicate a torque of 30 to 60 g/cm.
3.
If the torque range is out of the specified limit, clean the
driving surface of the take-up reel base shaft assembly (B
1-8) and tape-up pulley assembly (B 1-12) with pure
alcohol.
4.
If the above cleaning proves ineffective for a correct tor
que alignment, replace the take-up reel base shaft as
sembly.
5.
First, remove the reel table assembly (B 1-12), then pull
out the take-up reel base shaft assembly. After putting a
drop of oil on the reel shaft (B 1-17), insert the new part
and then fit the reel assembly onto it's shaft. Finally tighten
two set screws (L 1-1).
Fast-Forward and Rewind Torque
(Spec. 65-120 g/cm)
1. Load the torque meter cassette.
2. Set the unit at F.F. or REWIND mode and read the value on
the dial scale. The meter should indicate a torque of 65 to
120 g/cm.
3. If the value is outside the specified range, clean the driving
surface of the fast forward pulley A assembly (B 1-14), fast
forward pulley B (B 1-13) and C (B 1-14).
4. If the above cleaning operation is ineffective for a torque
alignment replace the fast forward pulley A assembly.
5. To replace, first remove the fast forward and rewind arm A
assembly (B 1-29).
1. Place the unit in the play mode (but without a loaded tape).
2. Attach the spring scale to the edge of the pinch roller as
sembly (B 1-18) as shown (fig. 1).
3. Gently draw the pinch roller assembly away from the capstan
shaft (in a direction parallel to a line that inter cepts the
centre of the capstan shaft and the pinch roller) until the
capstan shaft and the pinch roller are completely separated.
4. Gradually lessen the pressure until the pinch roller just begins
to rotate. The scale should then read approximately 500-650
g/cm.
5. If the scale reading is outside the above range, replace the
pinch roller spring (B 1-61) or adjust the spring arm as shown.
6. After the replacement, install the pinch roller adjusting nut (B
1-87) with 1 mm vertical clearance. Check whether the pinch
roller is vertical to the capstan.
Tape Speed / WOW and Flutter
Note:
Before commencing the following alignments, make
sure that all parts in the tape path, particularly the capstan,
pinch roller and head, are cleaned with pure alcohol.
1. Connect the AC vacuum tube voltage meter to both chan
nels of the "Line-out".
2. Use a test tape (in which 10,000 Hz signal is recorded).
3. To achieve the maximum reading on the AC VTVM adjust the
azimuth alignment screw (fig. 2).
4. After the adjustment, fix the screw with lacquer.
Tape Speed
(Spec. 3000 Hz ± 45 Hz)
1. Connect the frequency counter to both channels of the lineout.
2. Set the EQ switch to normal position, then load and play a
TEAC MTT-111 test tape in which a 3000 Hz signal is
recorded.
3. Adjust the control located at the top of the meter for a reading
of 3000 Hz ± 5 Hz on the frequency counter (fig. 3). (This
tape speed alignment should be done after approx. 30
seconds operating time).
4. Then, verify the reading on the frequency counter as being
within the specified range 3000 Hz±45 Hz at the beginning,
middle and near the end of the tape.
Wow and Flutter
(Spec. DIN weighted: within ± 0.2% at record and playback)
Note: When using these methods, obtain the maximum wow and
flutter value, by repeated play, stop or pause mode of operation.
This operation ls necessary to make sure that the wow and
flutter value between record and playback will not create a false
reading.
1. Connect the oscillator to the line-in of the unit, and the wow
and flutter meter to either channel of the line-out.
2. Set line or record controls of the unit to obtain the optimum
input level.
3. Load a test tape (BASF C 60) and set the BASF/EQ
switches to the normal position.
4. Apply and record a 3000 Hz signal.
5. Record and play the recorded section.
6. Read the value on the wow and flutter meter. The wow and
flutter value should be within ± 0.2 %, DIN max.
7. If the measured value is out of specification, check the takeup torque and pinch roller pressure, and see that the capstan
or belt is not stretched or oily.
8. If the above checks prove ineffective, repair or replace the
pinch roller assembly (B 1-6), motor and any other defective
parts.
9. When the capstan assembly must be replaced, make sure it
is weil oiled. Re-adjust the end clearance by adjusting the
thrust-screw (B 1-111) until the clearance is between 0.15-0.3
mm.
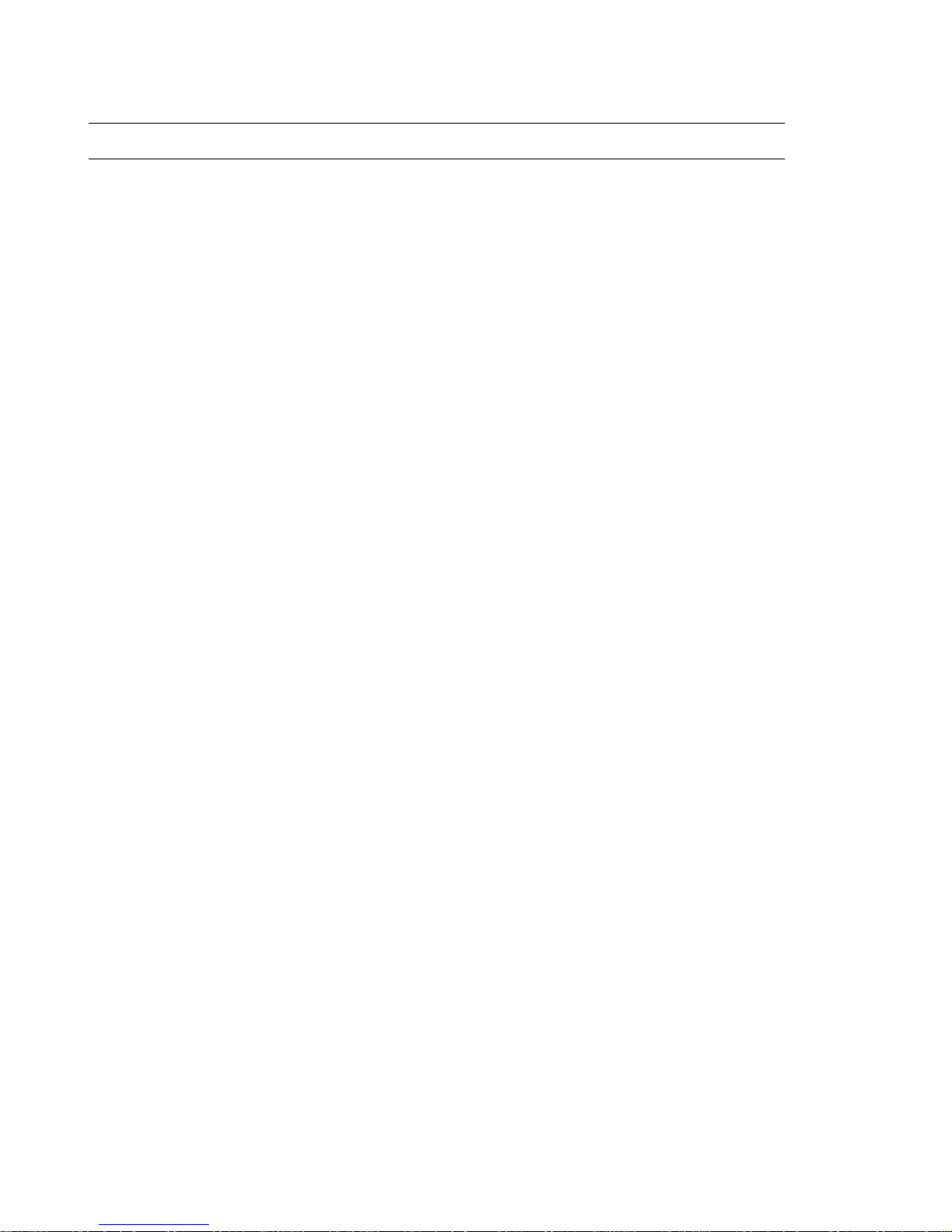
B 2-37 Cover, Volume Control
A-23 Spring, Cassette Setting
Decoration Plate, Azimuth Hole
Plate, Rating (220 V, 50 Hz)
Plate, Rating (240 V, 50 Hz)
B 1-56 Stay, Auto Stop PC Board
B 1-67 Stay, Flywheel Holder
B 1-71 Shaft, Pause Lever B
B 1-83 Shaft, Head Chassis Guide
B 1-89 Shaft, Fast Forward Arm
B 1-104 Shaft, Tape Changing Spring
Plate Assembly, Head Base
B 1-76 Stay, Pinch Roller Arm
B 1-79 Stay, Head Adjusting Spring
B 1-83 Shaft, Head Chassis Guide
Plate Assembly, Cassette Lifting
B 1-3 Plate, Cassette Lifting
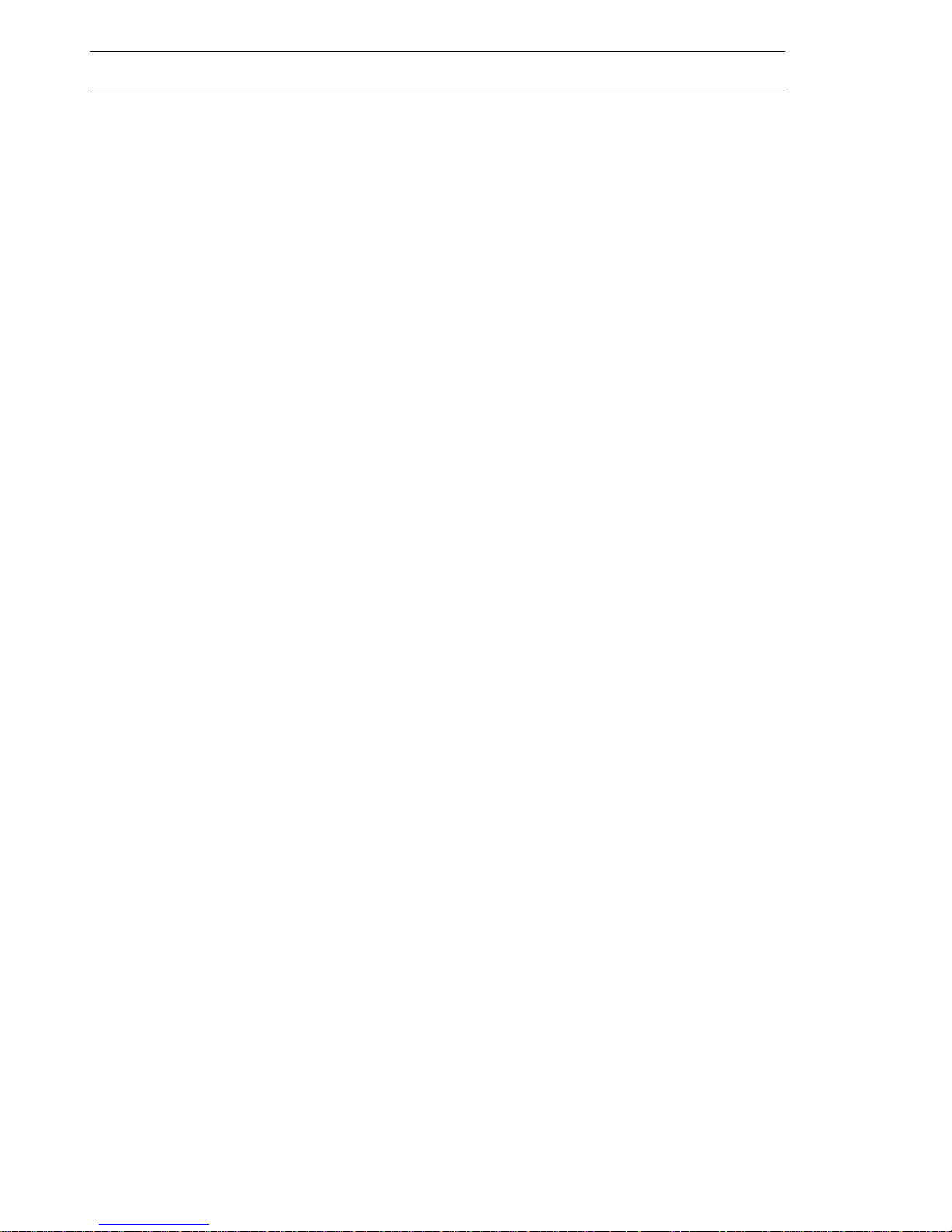
Shaft Assembly, Take-up Reel Base
Shaft Assembly, Supply Reel Base
Pulley A Assembly, Fast Forward
B 1-10 Pulley A, Fast Forward
B 1-24 Arm, Fast Forward Pulley
B 1-78 Shaft, Fast Forward Pulley
B 1-39 Arm, Take-up Pulley
B 1-68 Shaft, Take-up Pulley
B 1-66 Shaft, Pinch-Roller
Arm Assembly, Back Tension
B 1-91 Felt. Back Tension
Arm A Assembly, Fast Forward and Rewind
B 1-29 Arm A, Fast Forward and Rewind
B 1-69 Shaft, Fast Forward Pulley B
Arm B Assembly, Fast Forward and Rewind
B 1-30 Arm B, Fast Forward and Rewind
B 1-103 Shaft, Fast Forward and Rewind Arm B
Arm C, Fast Forward and Rewind
Arm Assembly, Fast Forward
B 1-72 Shaft, Fast Forward and Rewind Arm C
B 1-72 Shaft, Fast Forward and Rewind Arm C
Arm A Assembly, Tape Changing
B 1-34 Arm A, Tape Changing
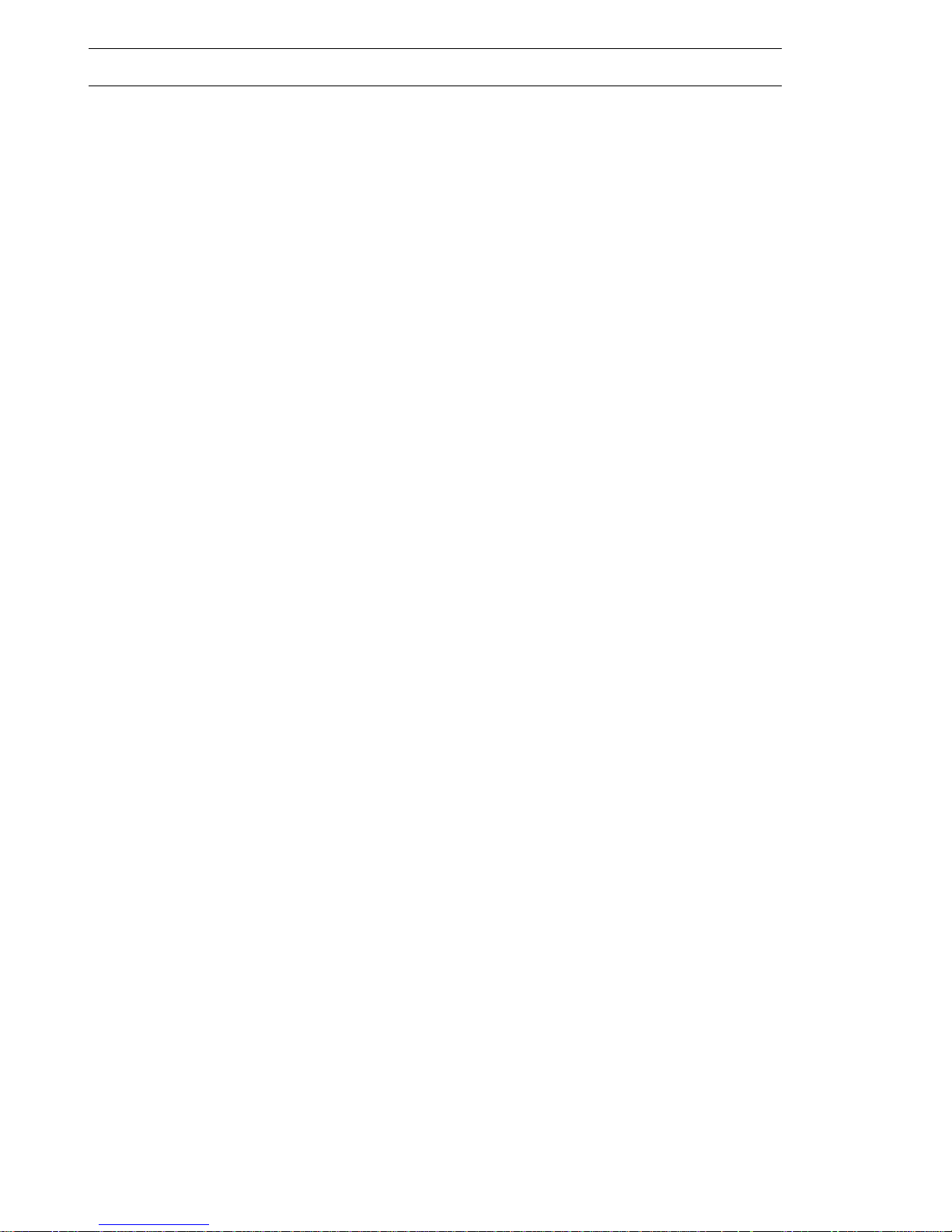
B 1-90 Shaft, Pause Lever A
Spring A, Head Chassis Holding
Spring B, Head Chassis Holding
Spring, Slide Switch Changing
Spring, Record Prevention Plate
Spring, Take-up Pulley Arm
Shaft, Record Prevention Plate
Shaft, Tape Changing Arm A
Shaft, Head Chassis Pushing
Shaft 8, Pinch Roller Arm
Nut B, Pinch Roller Adjusting
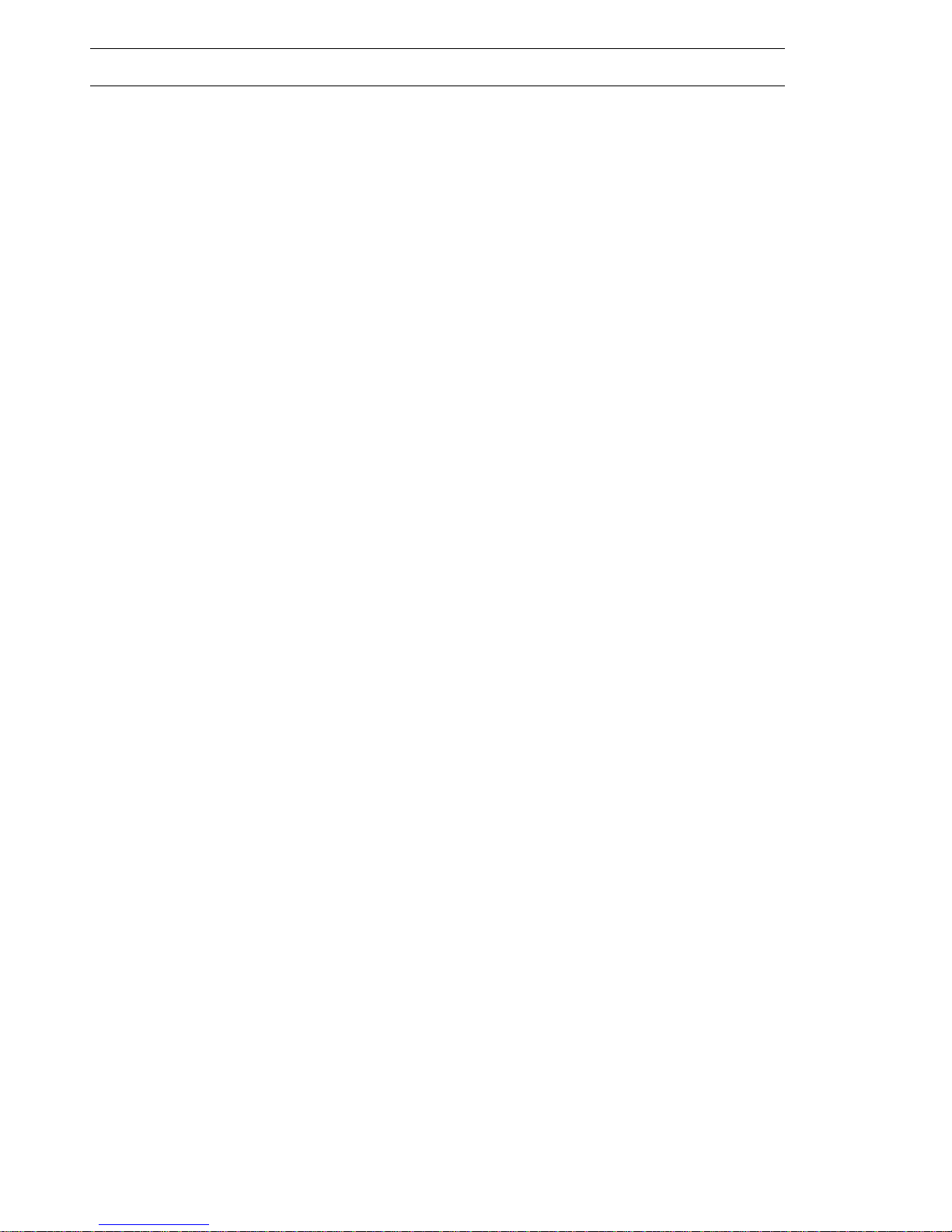
Guide, Tape Changing Arm B
Spring C, Head Chassis Holding
Spring, Eject Bar Locking
Holder Assembly, VU Meter Box
B 2-8 Holder, VU Meter Box
B 2-40 Cover, VU Meter Box
Spring, VU Meter Box Locking
Stay, Bottom Cabinet Holding
Spring, Meter Box Lifting Button
Holder, Push Switch Button
Bracket, Mechanism Chassis
Bracket B, Record/Playback PC Board
Bracket C, Record/Playback PC Board
Holder, Power Switch Button
B 2-31 Shaft, Record Lever D

Spring, Meter 80x Lifting
Siotted Socket Setscrew M 2 X 3
Flat Countersunk Head Screw M 2 X 5
Siotted Socket Setscrew M 2.6 X 4
Pan Head SEMS Screw M 2 X 5
Pan Head SEMS Screw M 2 X 8
Pan Head SEMS Screw M 2 X 10
Pan Head SEMS Screw M 2 X 12
Pan Head SEMS Screw M 2.6 X 4
Pan Head SEMS Screw M 2.6 X 6
Pan Head SEMS Screw M 2.6 X 8
Pan Head SEMS Screw M 2.6 X 10
Pan Head W SEMS Screw M 2.6 X 6
Pan Head W SEMS Screw M 3 X 6
Pan Head SEMS Screw M 3 X 6
Pan Head W SEMS Screw M 3 X 12
Flat Washer M 2 (0.4 t X Ø 5)
Flat Washer M 2.6 (0.5 t X Ø 7.5)
Flat Washer M 3.5 (0.5 t X Ø 7)
Flat Washer Ø 4 X Ø 10X 0.8 t
Flat Washer M 4 (0.5 t X Ø 10)
Tapping Screw (Tap-Tite C Type) M 3 X 6
Tapping Screw (Tape-Tite C Type) M 3 X 8
Pan Head SEMS Screw M 3 X 6
Pan Head W SEMS Screw M 3 X 6
Pan Head SEMS Screw M 3 X 5
8inding Head Screw M 3 X 8
Pan Head SEMS Screw M 2.6 X 6
Pan Head Tapping Screw M 2.6 X 6
Flat Countersunk Head Screw M 2.6 X 6
Pan Head W SEMS Screw M 2.6 X 6
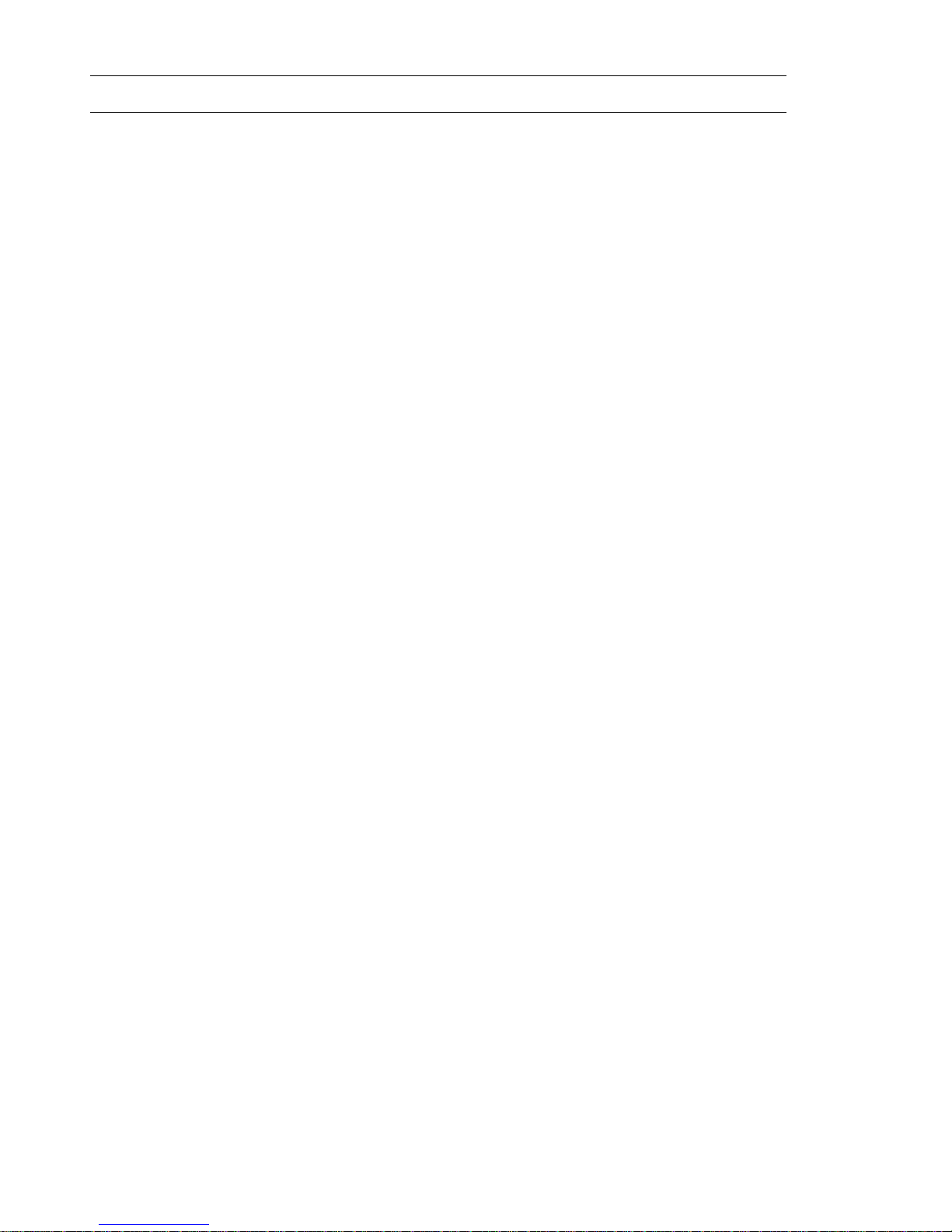
AC Cord Stopper (COMMON-type)
AC Cord Stopper (BASEC-type)
AC Cord Stopper (SAA-type)
Slide Switch (12-Circuit)
Slide Switch ( 9-Circuit)
Slide Switch ( 4-Circuit)
Push Switch (5-function- common)
Connector (5 P-2.5 mm) L-type
Connector Socket (5 P-3.5 mm)
Connector Socket (3 P-3.5 mm)
Connector Socket (5 P-2.5 mm)
LED P.C.B. (4-function-common)
Semi-fixed Inductance 6.8 mH
Semi-fixed Inductance 4.7 mH (J)
Semi-fixed Inductance 15 mH
Semi-fixed Inductance 200 µH
Semi-fixed Resistor (8 mm) 1 K
Semi-fixed Resistor (8 mm) 10 K
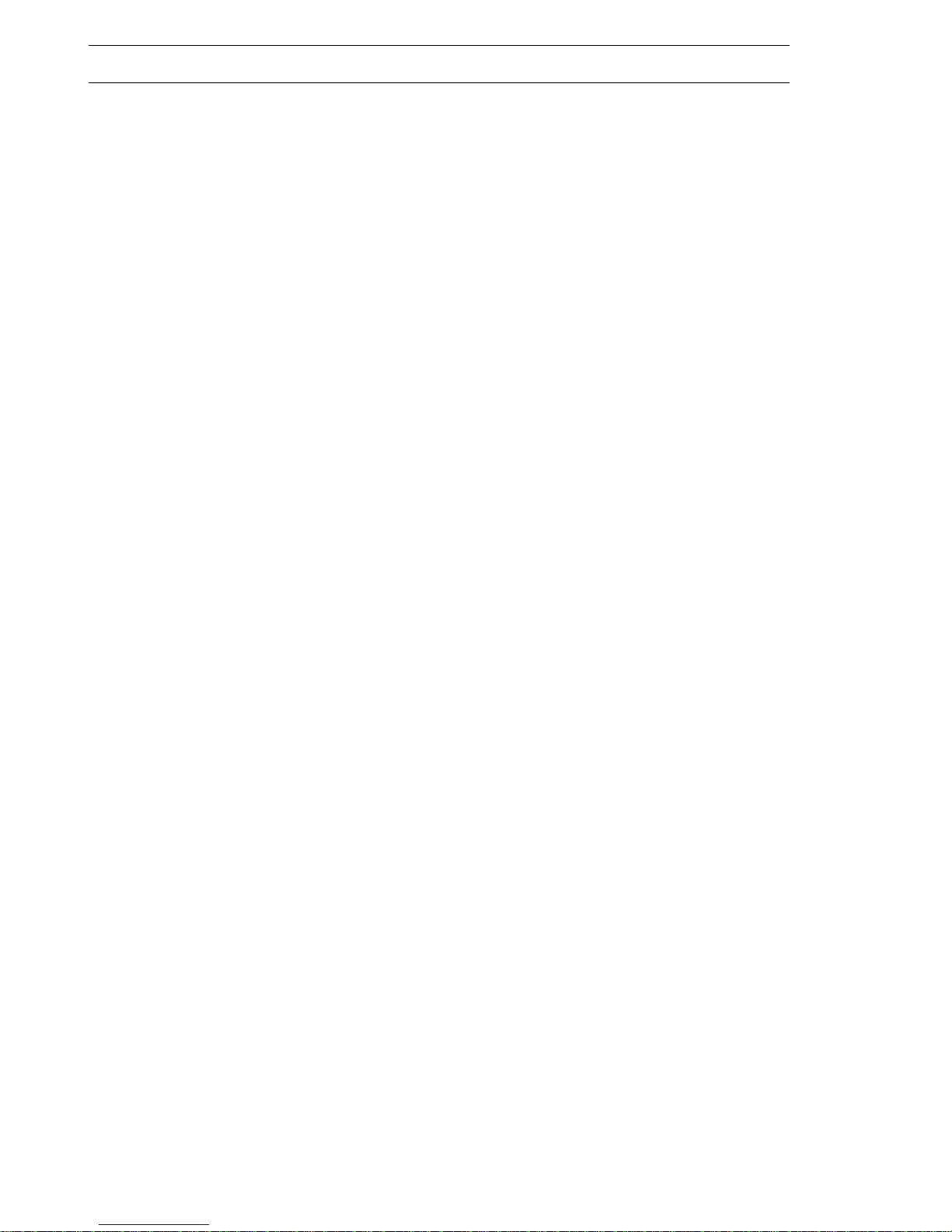
Semi-fixed Resistor (8 mm) 20 K
Semi-fixed Resistor (8 mm) 100 K
DIN/RCA Jack P.C.B. Assembly
Peak Level P.C.B. Assembly
Pre-Amplifier P.C.B. Assembly
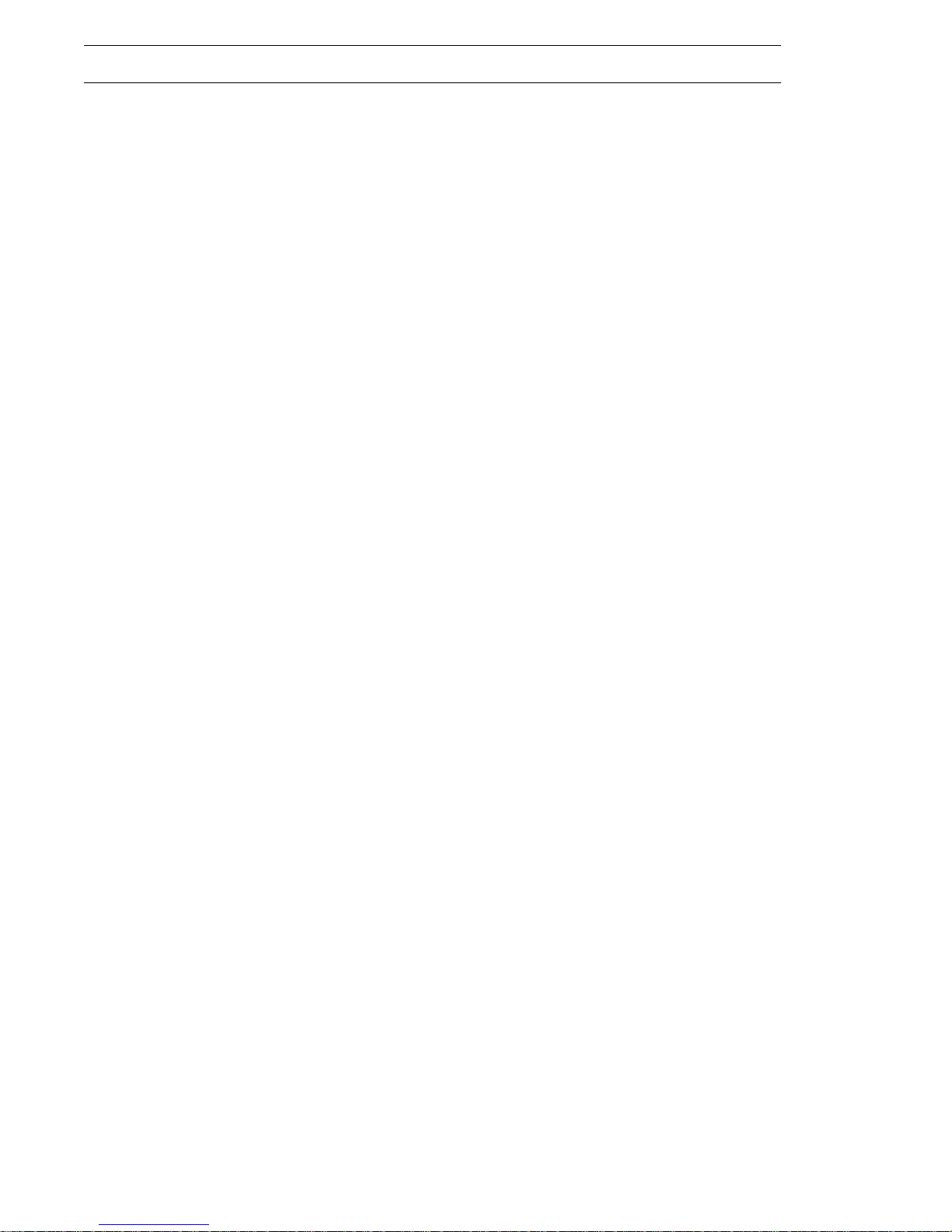
Tantal Electrolytic Capacitor
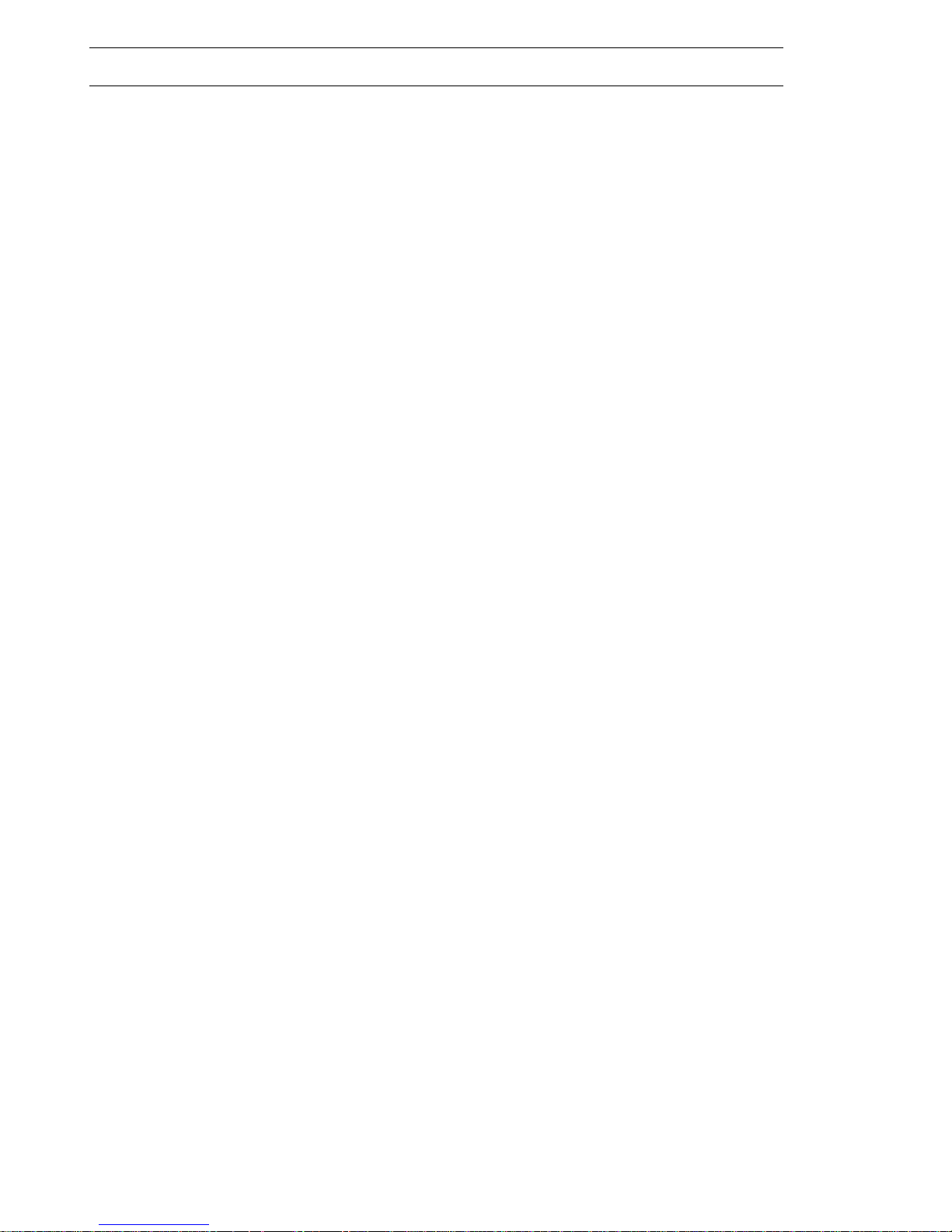
Tantal Electrolytic Capacitor
Tantal Electrolytic Capacitor
Tantal Electrolytic Capacitor
Tantal Electrolytic Capacitor
Aluminium Solid Element Capacitor 0.47 µ/10
Carbon Resistor (Precision)
Carbon Resistor (Precision)
Carbon Resistor (Precision)

Carbon Resistor (Precision)
Alminium Solid Element Capacitor
Auto Stop P.C.B. Assembly
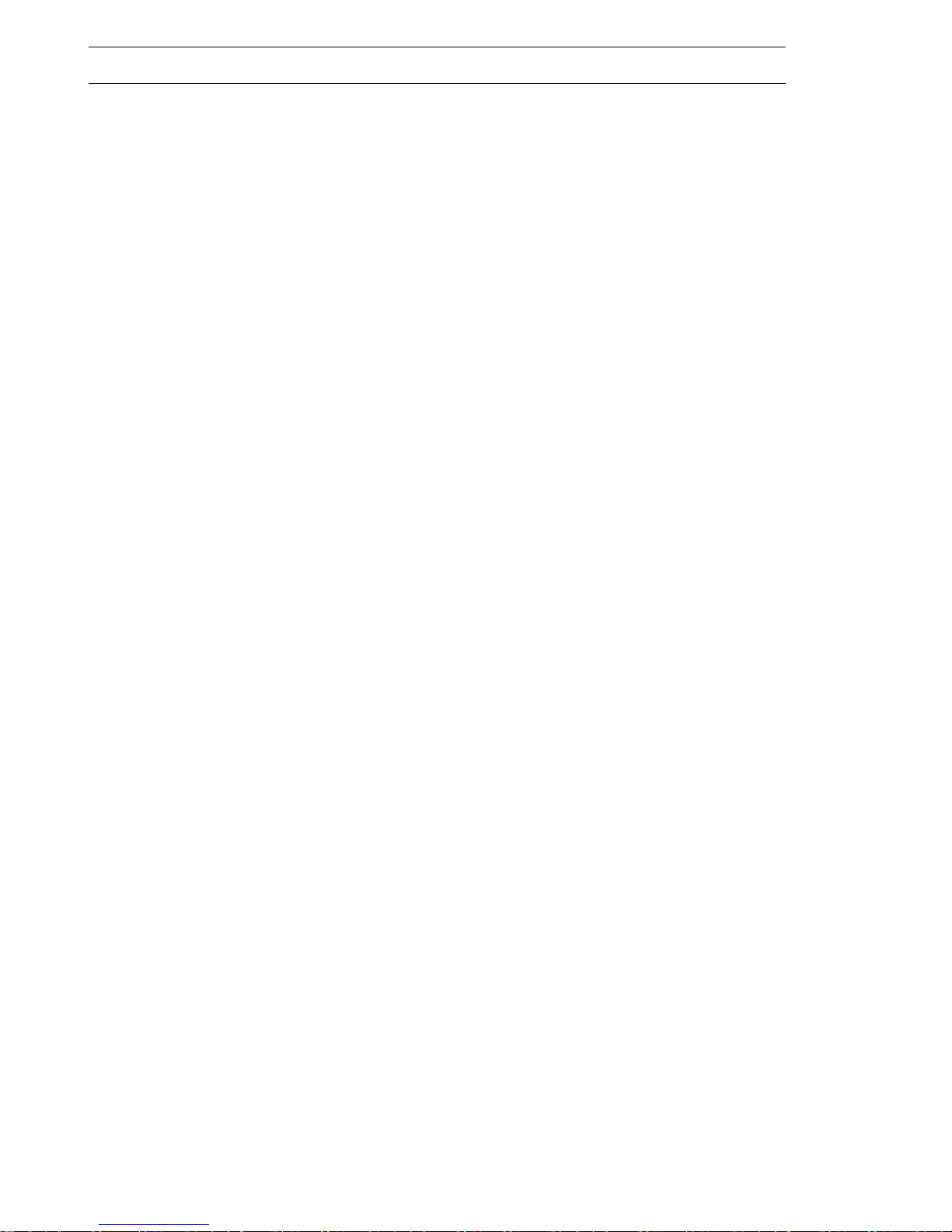
Reed Switch P.C.B. Assembly
LED P.C.B. (4-function) Assembly
Push Switch P.C.B. Assembly