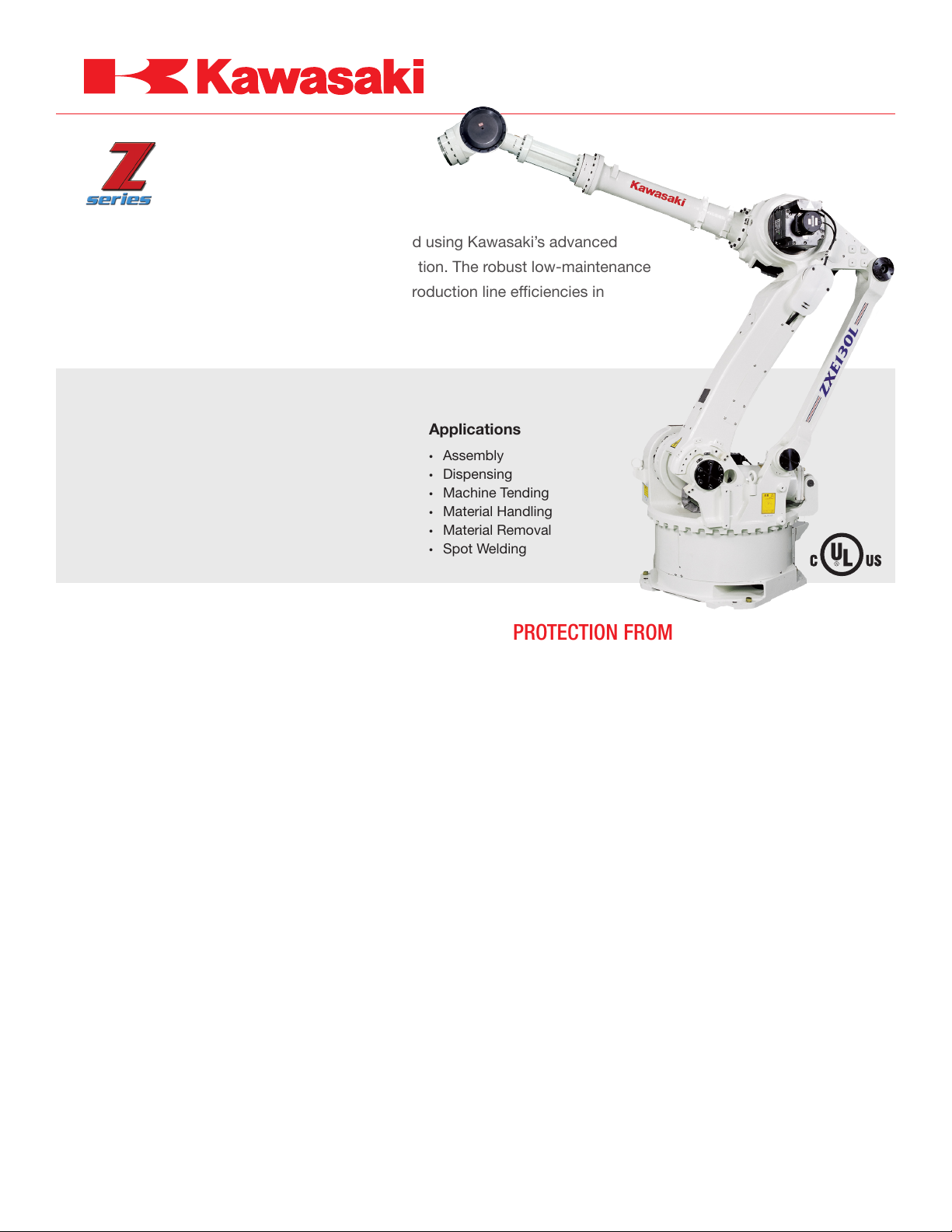
THE FLEXIBLE
HEAVY-DUTY ROBOTS
The Z-Series heavy-duty robots were developed using Kawasaki’s advanced
technology and extensive experience in automation. The robust low-maintenance
designs are directly responsible for improved production line efficiencies in
automotive and general industry applications.
ZXE130L
Payload 130 kg
Horizontal Reach 2,951 mm
Vertical Reach 4,015 mm
Repeatability ±0.3 mm
Maximum Linear Speed 2,500 mm/s
HIGH QUALITY & LOW-MAINTENANCE
The Z- Series Robots boast industry leading MTBF and
10,000 hour maintenance intervals, which translate to low
operating costs and the highest production efficiencies.
CYCLE TIME ADVANTAGE
The Z Robots along with the ultra high processing speed
capabilities of the Kawasaki E Controller can achieve
superior operating speeds. Add the high-speed option
package and cycle times can be reduced by up to 20% as
compared to previous models. Faster speeds translate to
shorter cycle times, resulting in maximum production.
WIDE WORK ENVELOPE
The Kawasaki Z Robot combines a long reach arm with
a minimal amount of dead space for the widest work
envelope in its class. In addition, the patented Kawasaki
Hybrid Link Configuration enables the arm to rotate back
over itself without having to rotate the base joint, thereby
improving efficiency and minimizing power consumption.
SPACE SAVING DESIGN WITH
INTEGRATED FEATURES
The small footprint of these high payload long reach robots
allows for installations in confined areas. The Z-Series
Robots are available with integrated pneumatic piping,
wiring, and fork lift pockets, limiting the amount of work
space required and minimizing potential interference.
Applications
• Assembly
• Dispensing
• Machine Tending
• Material Handling
• Material Removal
• Spot Welding
PROTECTION FROM
HARSH ENVIRONMENTS
Z-Series Robots can operate in some of the harshest
environments due to the Kawasaki sealed arm design.
The wrist portion of the robot has an Ingress Protection
classification of IP67, while the other areas of the arm are
rated at IP65. Robot maintenance due to contamination can
be eliminated.
ARM ID MEMORY
Kawasaki’s Arm ID board enables the robot arm to be
interchanged with any E Controller. The ID board stores
all of the necessary servo encoder data. In the event of
a production emergency, the controller can quickly and
easily be replaced to allow for any service and maintenance
procedures to be performed. This feature greatly limits
potential system downtime.
UPGRADEABLE
The Z-Series robot line is manufactured using modular
components and a common software platform. This flexible
design allows some models to be modified to alter reach,
payload capacities and speed. Both hardware and software
alterations can easily be performed in the field. The ability
to change the robot characteristics provide for greater
flexibility to accommodate production and system changes.
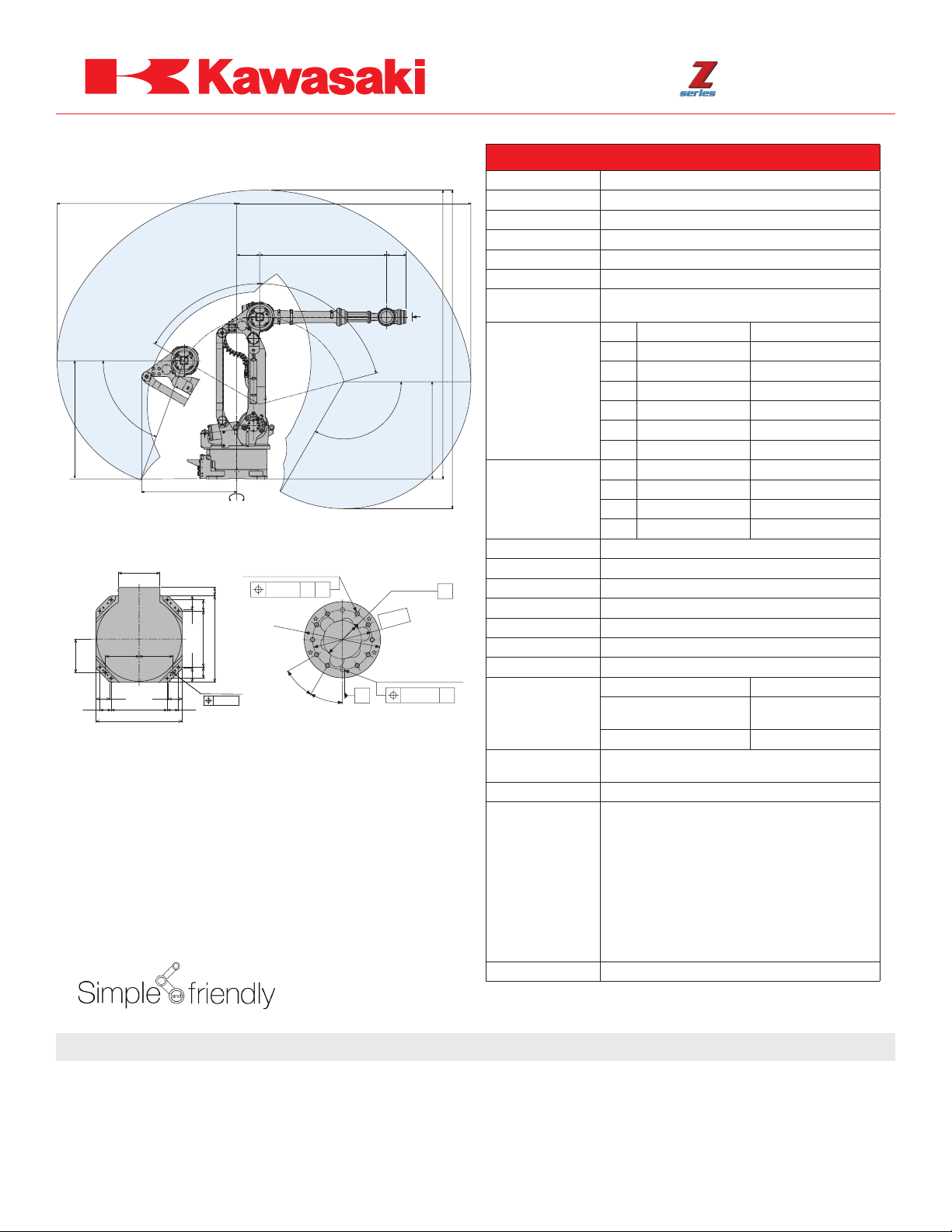
ZXE130L
MOTION RANGE & DIMENSIONS
2,265
Ø0.15
Ø160
30
1,600 228
JT2
75°
XY
°
30
°
VIEW A
288
JT2
°
60
JT3
70
°
1,490
1,199
JT1±180°
370
125 125
300
300 300
125 125
100 100
INSTALLATION DIMENSIONS
500
770
500
100100
2–Ø25G8
75
770
Ø0.05
6–M10 Depth 12
Note: Detailed drawings are available upon request.
2,951
JT3
120
Y
A
3,640
°
1,225
Ø80H7
Ø0.04
X
X
Depth 8
Ø125
2-Ø10H7 Depth 12
(mm)
Type
Degrees of Freedom
Payload
Horizontal Reach
Vertical Reach
Repeatability
Maximum Linear
Speed
4,015
Work
Envelope
(degrees)
&
Maximum Speed
(degrees/s)
Wrist Load
Capacity
Motor(s)
Brakes
Hard Stop(s)
Limit Switch
Mass
Body Color
Installation
Environmental
Conditions
Protection
Classification
Built-in Utilities
Options
Controller
ZXE130L SPECIFICATIONS
Articulated
6 axes
130kg
2,951 mm
4,015 mm
±0.3 mm
2,500 mm/s at robot flange
Axis Motion Range Maximum Speed
JT1 ±180º 110°/s
JT2 +75° ~ -60° 110°/s
JT3 +250° ~ -120° 110°/s
JT4 ±360° 140°/s
JT5 ±130° 135°/s
JT6 ±360° 230°/s
Axis Maximum Torque Moment of Inertia
JT4 735.0 N·m 107.8 kg·m
JT5 735.0 N·m 107.8 kg·m
JT6 421 N·m 45.9 kg·m
Brushless AC Servomotor
All axes
Adjustable mechanical stopper JT1
End of stroke limit switch JT1
1,400 kg (excluding Options)
Kawasaki Standard
Floor (includes fork pockets)
Temperature 0 ~ 45º C
Humidity
Vibration Less than 0.5 G
Wrist: IP67 Base: IP65 * Equivalent
Pneumatic piping (ø12 x 2 lines)
Linear track options
Base plate
Adjustable mechanical stopper JT2/JT3
Limit switch JT2/JT3
Signal harness (up to 24 inputs and 8 outputs)
Double/single solenoid valves (2 units max.)
Internal wiring (37 wires inside robot arm)
Air cleaning equipment (filter, regulator, mist separator)
Piping for cooling water
Wrist flange adapter with ø92 mm mounting pattern
E32 (See E Controller data sheet for specifications)
35 ~ 85 % (no dew, nor
frost allowed)
2
2
2
Assembly • Cutting • Dispensing • Grinding • Handling
Kawasaki Robotics (USA), Inc.
United States
28140 Lakeview Drive
Wixom, Michigan 48393
Phone (248) 446-4100
Email sales@kri-us.com
Canada
Phone (905) 304-7784
Mexico
Phone (52) 33-3110-1895
•
Inspection • Packaging • Painting • Palletizing • Polishing • Tending • Welding
www.kawasakirobotics.com
ZXE130L - REV02/14
© Kawasaki Robotics (USA), Inc. All rights reserved.
Technical specifications subject to change without notice.