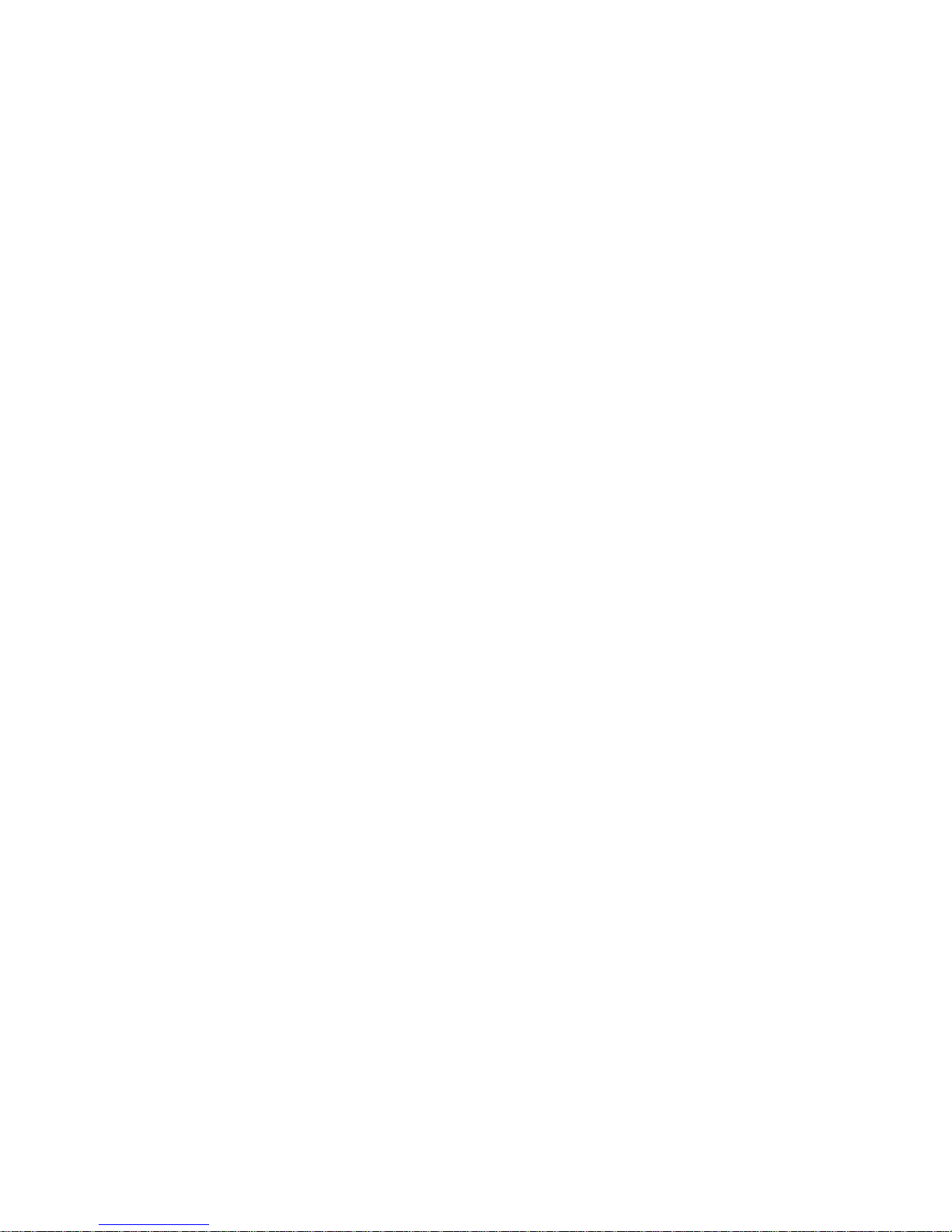
Foreword
This
manual
mobile
However,
formation
who
desires to
nance and
mechanics,
procedures
out
maintenance
ever the
doubts
maintenance, and repair
by
qualified
In
order
avoid
the
costly mistakes,
text, thoroughly
procedures before
work
carefully
tools
or
equipment
ments
are used, and
adversely
Whenever
their
instructions!
and
maintenance
is designed
mechanics
it
contains
to make
repair
the
must
owner
his
ability
mechanics.
to
perform
equ
ipment
should
can on
Iy
affect
you see
in a
enough
it
useful
perform
work
proper
be understood
and repair
has
to
do
the
familiarize
starting
in a clean area .
is specified,
not
be used. Precision
be made
the
use
safe operation
the
Always
practices.
IWARNING'
primarily
properly
for
use by
equipped shop.
detail and basic
to
the
snowmobile
his
own
basic
. A basic knowledge
use
of
tools, and
in
workshop
order
satisfactorily. WhenÂinsufficient
the
work,
should
work
the
mechanic
work,
experience
the
adjustments,
be carried
efficiently
should read
himself
and
then
with
Whenever
makeshift
measure-
if
the
of
substitute
symbols
follow
proper
of
shown
instruments
the
snowmobile
below,
safe
tools
operating
snow
user
mainte-
to
carry
out
only
and to
the
do
the
special
tools
may
heed
in-
of
or
or
This
manual
is divided
into
the
following
four
sections:
-
(1) Specifications
This section
cations, a
formance
(2)
Maintenance
contains
complete
curves.
The procedures
minor
explanation
of
the
repair are described
on
the
major
components
mechanic
general
torque
and Theory
for
inspection,
the
structure
to
better
and
technical
chart
and
of
Operation
adjustments
in
this
and
function
and
assembly
understand
specifi-
engine
per-
and
section. An
of
each
enables
what
he
is
doing.
(3) Repair
.
This section
disassembly,
which
repair.
vided to
shows
the
best
inspection, assembly, and
are necessary
Assembly
for
and
proper
installation
explain special points.
method
maintenance
notes are pro-
for
removal,
installation
and
This
structions
rectly
injury, or
This
structions
strictly
or
NOTE:
more
warning
or
followed,
loss
caution
observed,
destruction
Indicates
efficient
symbol
procedures
could
of
life.
symbol
or
procedures
could
of
equipment
points
and
convenient
identifies
which
result
identifies
which
result
.
of
particular
operation.
special
if
in
special
in
damage
in-
not
cor-
personal
in-
if
not
to,
interest
for
Appendix
(4)
The appendix
miscellaneous
ence and
in
the back
information,
conversion
charts, special tools,
diagram, and an index.
This shop
mechanic
mobiles.
followed
manual
in
All
procedures contained
closely.
has been prepared
servicing
of
the
including
the
KAWASAKI
manual
metric
to
within
contains
refer-
wiring
assist
snow-
should
the
be
FOREWORD
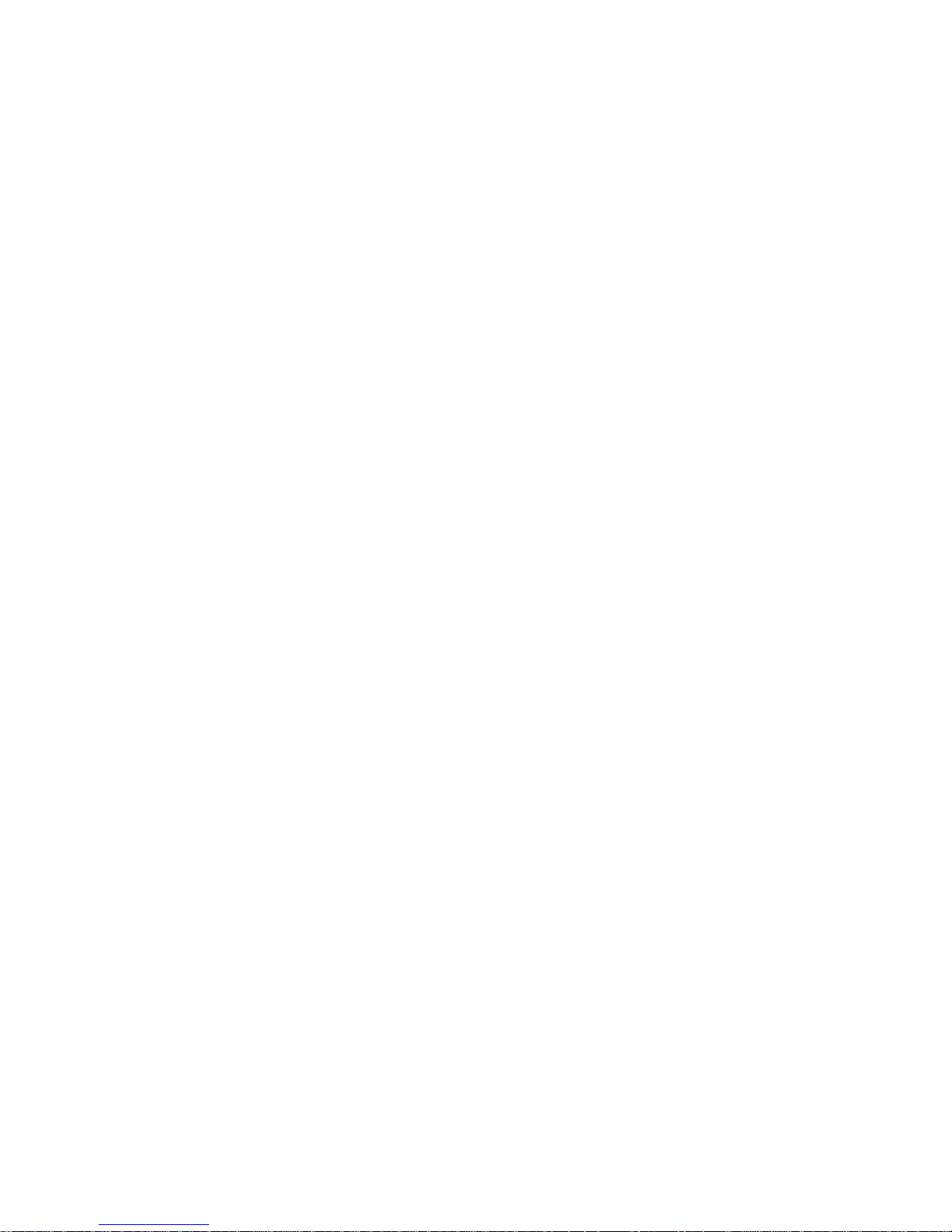
Model Identification
ST440-A4
ii
MODEL
IDENTIFICATION
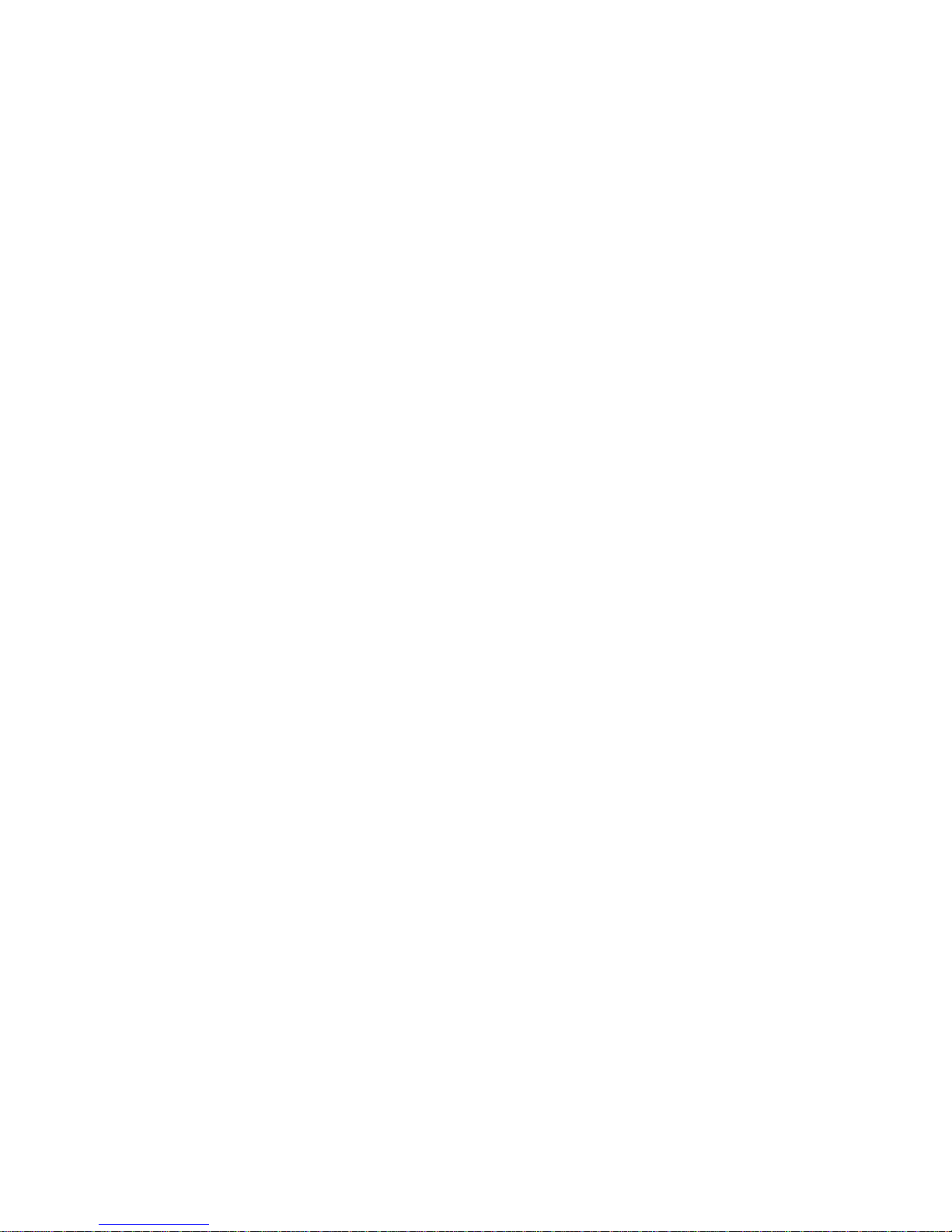
Quick Reference Guide
SECTION
"f"
peci Icatlons ............................................................................................... .
S
Maintenance and Theory ....................................................... ..
"
..
................ .
Repair ............................................................................................................ .
Appendix ....................................................................................................
...
.
Using
locating a desired topic
shop
manual.
sired section above
of
the
contents for the exact page(s)
procedure required .
the
quick reference
Bend
table
of
contents
the
with
for
guide
or
procedure
pages back
the
black tab on
that
section . Refer
to
locate
will
until
assist
contained
you
the
the
you in
match
right
to
specific
quickly
within
the
this
the
de -
hand
side
table
of
topic
or
QUICK REFERENCE GUIDE
iii
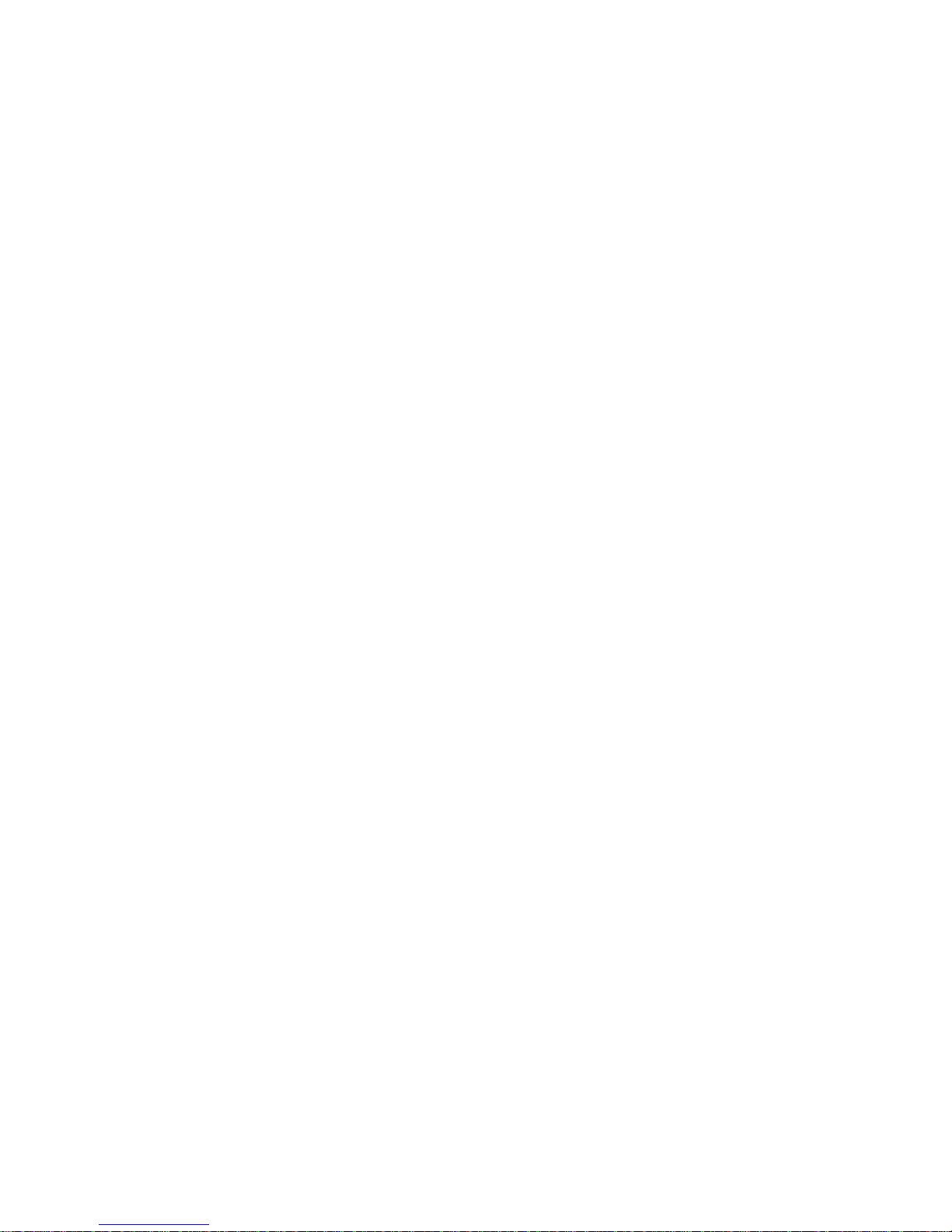
Specifications
General
Se rvice
Torque
Ratio
Gear
Engine
Table
Spec
ifications
Specifications
Chart
. . . . . . . . . . . . . . . . . . . . . . . . . . . . 1-9
Chart ............
Performance Curves/Port
of
Contents
. . . . . . . . . . . . . . . . . . . . . . 1-2
........
Dim
..
.........
. ....
ensions
...
......
. . . 1-7
. .
..
Page
1-13
1-14
SPECIFICATIONS
1-1
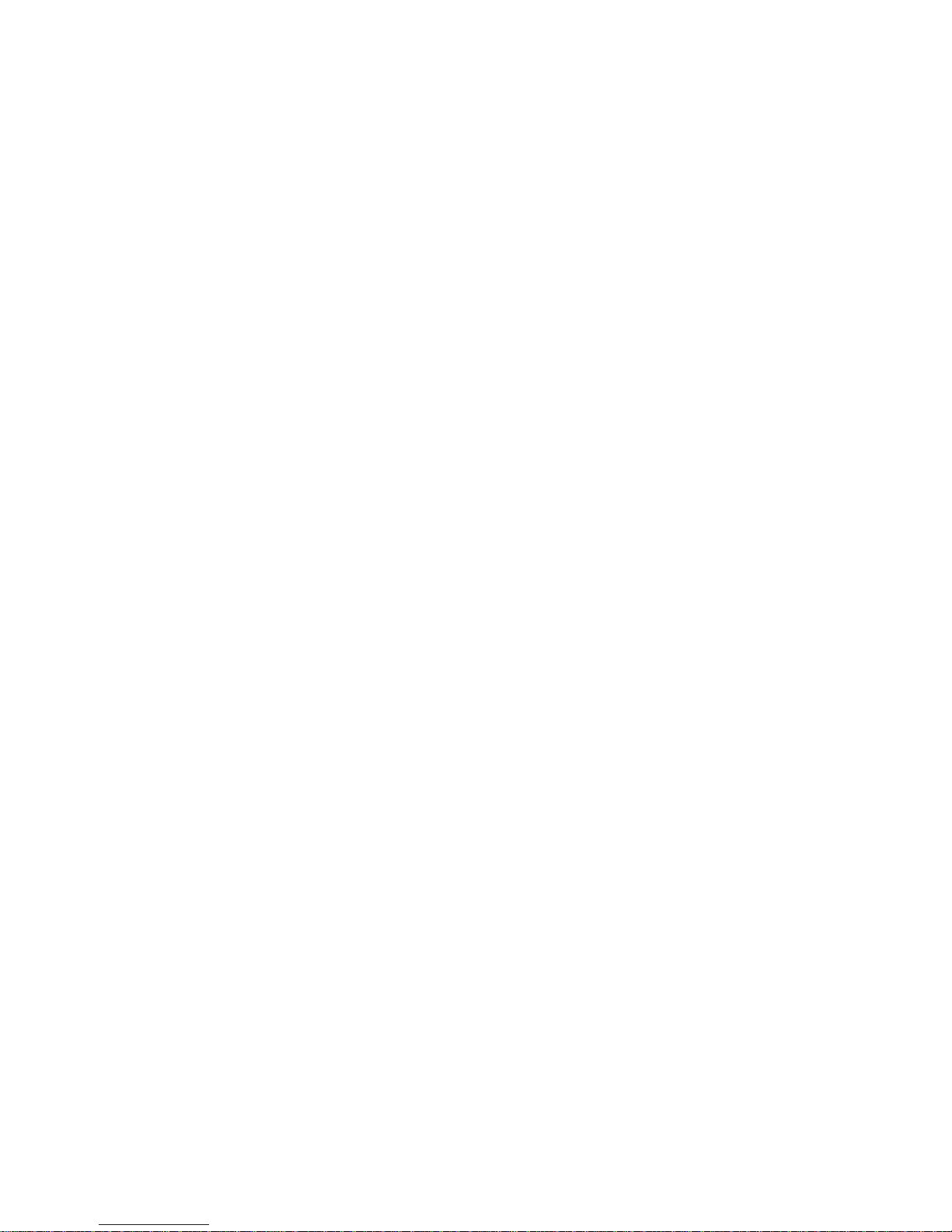
GENERAL
General Specifications
Overall Length .
Overall Width
Overall Height (With Windshield)
Dry
Weight (Approximate) . .
ENGINE
Model
Displacement
Bore x
Number
Engine
Engine
Starter
IGNITION
Ignition
Spark Plug .
..
Stroke
of
RPM
RPM
.....
System
.. .......................................
........................
. . .
.....
.
...
. . . . . .
...
Cylinders
at Full
at Idle
..
.......
..............................
...... _ ...
................................
Throttle
Speed
...........
. . ....
......
...
......
.......
. .
.......
.............................................
...
..........
...
................
.. ..
. .
...............................................
.........
...... ...
... _ ...................
. .
.....................
...........
. .
........
....
......
........
. . .
.
.....
...
........
.
......
.....
.
.....
...
.
......................
_ .
........
.
...........
.
.
...
.........
..
........................
.
... ...
.....
....
..
...............
.....
.
....
...
...
.
......
...
.......
.............
.
........
103 in. (2616 mm)
...
.....
. . .
....
2.677 x 2.362 in. (68 x 60 mm)
..................
.
......
40.5 in. (1029 mm)
40.5
in.
(1029 mm)
.. ..
..
425 Ib (193 kg)
.......
. . Electric and Manual
Capacitor Discharge
7,100
....
26.6
..
TA440C-D201
C.1.
to
7,300
2,500
NGK
(436cc)
RPM
RPM
(C.
D.)
BZ-9EV
2
CARBURETOR
Make
Carburetor
Carburetor Model .
Identification Marking . .
of
Type
Main Jet
Air
Jet
Needle Jet
Throttle
Pilot Jet
By
Pilot Outlet . . . . .
Air
Fl
Starter Jet
Type
Starter
Econo (Power) Jet
Carburetor ... .
...............
Jet .........
Needle .........
Slide (Cut Away) .
...........................................
Pass
.................
Screw .....
oat
Valve
of
Float Chamber ....
SYstem
....
......
.. ..
. .
...
.....................................
Seat
...
..........................
....
...............
.....
..
.............
.......
....
. .
.....
.
........
............................
.. ..........................
.......
...
...................
....... .......................
......
.....
..
. .
......
..................
.
.....
..
.. ..
......
....
..........
.
.....
....
........
..........
...
......
...............
. . .
.....
......
..
................
.........
..
......
.
................
.....
.
....... ..
...
..
..........
.
...........
.....
.
...........
.
.........
..........
.
......
....
........
..
. .
.....
.
....
..... ..
.
..
.
..
LEFT
SIDE
.
Mikuni
. VM
.
. Open
.
. None None
.
.
.
.
.
.
.
. .
.
.
. .
. .
32
Econo Jet
L32 / 185
Vent
155
6DH7 -3
0-4
0.098 in. (2.5 mm) 0.098 in. (2.5 mm)
25
0.055 in. (1.4 mm)
0.031 in. (0.8 mm) 0.
1.5 Turns 1.5 Turns
0.059 in (1.5 mm)
0.059 in. (1.5 mm)
Special
Dual Position Cable
140 RoundÂReverse
Type
Mikuni
VM 32 Econo Jet
R32/189
Open
155
6DH7-3
0-4
25
0.055 in. (1.4 mm)
031
0.059 in. (1.5 mm)
0.059 in . (1.5 mm)
Special
Dual Position Cable
120 Round ÂReverse
RIGHT
SIDE
Vent
in. (0.8 mm)
Type
1-2
GENERAL
SPECIFICATIONS

FUEL/OIL
Gasoline
Oil
........
.........
.
.....
. .... .
.....
.
...
...... ...
...
.......
..
Premium
....
. . . . .
or
regular leaded (minimum pump posted octane number 89)
....
Kawasaki Snowmobile Oil
(B.I.A. certified
Gasoline/Oil Ratio . . . . . . . . . . . . . . . . . . . . . . . . . . . . . . . . . . . . . . . . . . . . . . . . . . . . . . . . .
Oil
Tank Capacity
Fuel
Tank Capacity ..........
DRIVE
CONVERTER
Engagement
Drive Converter
Part Number and Col
Spring
Spri
ng
Part Number and Col
Spring Length - New
..................................
Speed
(approximate RPM) ...
RPM
. .
.........
or
or
with
no load ± 0.25 in. (6.3 mm)
..
.....
....
.....
. .
...
...
(Standard) .......
(Optional)
.......
.
...........
......
.
........................
........ .
....
.
.....
......
..
....
....
....
.
... ...
. . .
.......
. . .
..
. . . . . . . . .
. .
.......
.. ..
.........
.
....
. .
.. ......
. . . 8.0 Gallons (30.2 liter
..
.......
................
...
. . . .
...
. .
.. ..
...
.....
3.96 in. (Yellow
. . 2.5 Quarts (2.37 liters)
. . . 92081-3004 (Pink)
3.54 in.
3.74 in. (Red) (94.9 mm)
4.14 in.
4.33 in. (Black) (110.0 mm)
4.74 in.
Number
Spring Wire Diameter
Spring Rate
Spring Compression ± 5.5 Ib (2.5 kg)
of
Spring Coils
±2.8Ib
(All
Colors)
±0.01
in. (0.2 mm)
in. (0.05 kg-mm)
.. .......
All
Colors ... ........
All
Colors ....
.............
. . . .... ......... ..
...
.....
. .
.......
.
.....
.
...
77.2 Ib @ 2.54 in. (35.6
........
. .... .
.....
.....
...
. .
. . .
...
.....
.....
. .
..
. 56 1b in. (1.0 kg-mm)
kg
55.1 Ib @ 2.54 i
66.1
Ib @ 2.54 i
Ib @ 2.54 in. (40.7 kg @ 64.5 mm) (Blue)
88.2
n.
(25.4 kg @ 64.5 mm) (Pink)
n.
(30.4 kg @ 64.5 mm) (Red)
99.2 Ib @ 2.54 in. (45.6 kg @ 64.5 mm) (Black)
123.2 Ib @ 2.54 in. (55.9 kg @ 64.5 mm) (White)
Spring Outside Diameter ± 0.025 in. (0.63 mm)
Weight Part Numbers (Standard)
........
Ramp Part Number and Identification (Standard)
Weight - Total gram weight (Standard)
................
All
.
.........
....................
Colors
...
.
.....
..
. . .
....
.......
. . . .
.....
.
...
. . . . .
....
.
.........
. . . . . . . .
....... .......
. . .
.....
...
....
T.C.
W.)
..
Oil Inject ion
s)
.
.......
3600
. . . 7,100-7,300
92081-3001 (Yell ow)
92081-3005 (Red)
92081 -3006 (Blue)
92081-3002 (Black)
92081-3011
(P
ink) (89.9 mm)
(Blue) (105.2
(Wh
ite) (120.4 mm)
. .
.. .......
(White)
).
(100.5 mm)
mm)
. 6
0.197 in. (5.0 mm)
@ 64.5 mm) (Yel low)
. 2.28 in. (57.9 mm)
.....
..
110G0628
13042-3002
92019 -008
..
39152 -3005
.....
..
63.1
"E"
grams
Part Number
13042-3001
13042 -3002
92019-008
92001-3009
92001-3003
92001-3015
110G0620
110G0628
39152-3005
DRIVE
CONVERTER COMPONENT
Component
Weight,0.031 in. (0.8 mm)
Weight, 0.062 in. (1.6 mm)
Nut,
special 6 mm
Bolt,
aluminum, 6 x 15 mm
Bolt,
aluminum, 6 x 20 mm
Bolt,
steel, 6 x 16 mm
Bolt
, steel, 6 x
Bolt,
steel, 6 x 28 mm
Weight
Assembly E
20
mm
WEIGHT
thick
thick
CHART
GENERAL
Gram Weight
0.5
1.0
2.3
1.8
2.1
5.3
6.0
7.3
47.5
SPECIFICATIONS 1-3
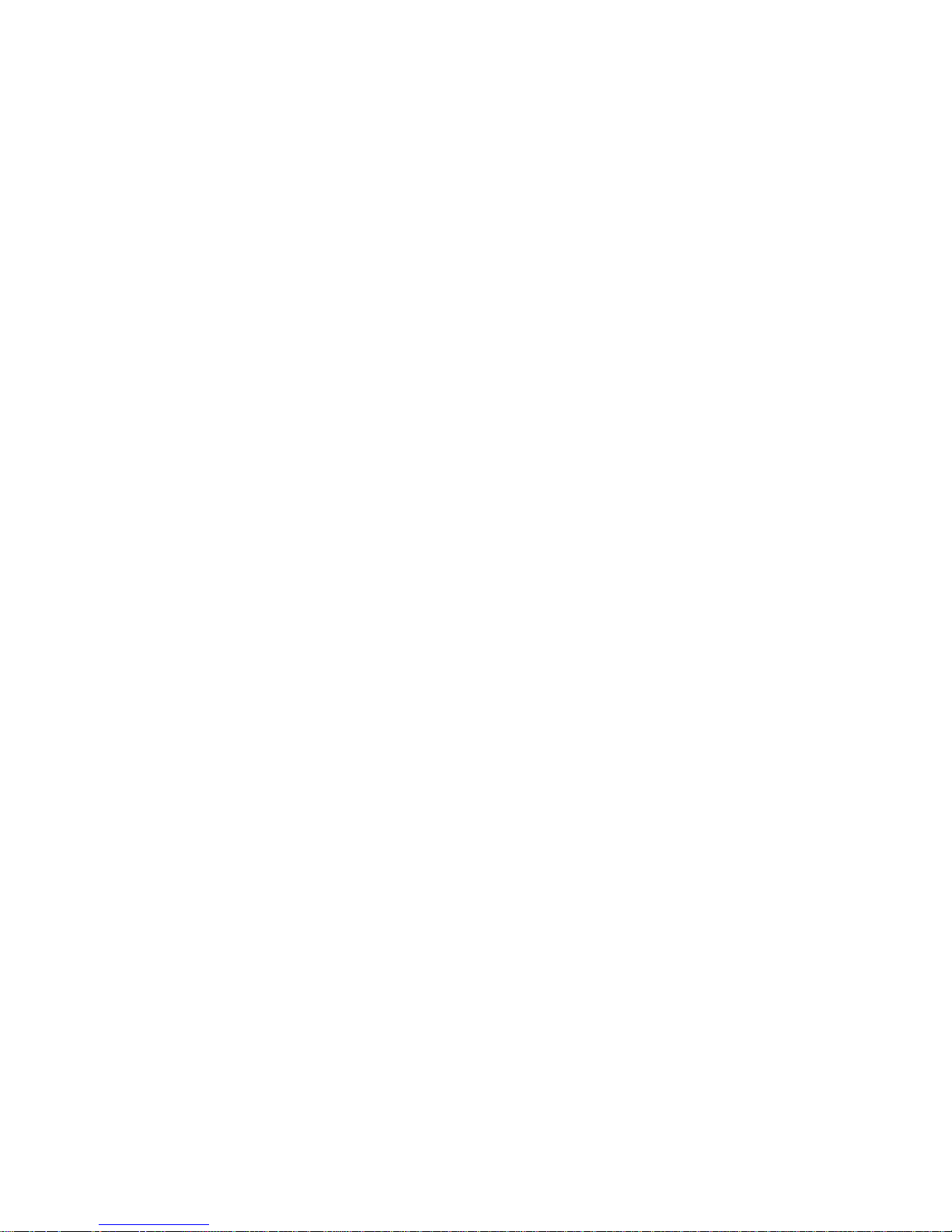
DRIVE
CONVERTER
Total Ramp
Weight-Grams
55 .1 grams
55.6
grams
56.1 grams
RAMP
Number
Weights
WEIGHT
of
Install
0
1
2
COMBINATIONS
Weight (0.5 gram each)
0.031 in. (0.8
ed
mm)
Part
Number
13042-3001
0
0.5 gram
1.0 gram
USING
thick
BOLT
PART
NUMBER
Bolt
6 x 16
Part Number Part
92001-
3015
5.3 grams
5.3 grams
5.3 grams
mm
92001-3015 (6 x
Nut
Special
Number
92019-008
2.3 grams
2.3 grams
2.3 grams
16
mm
STEEL)
Ramp Weight
Part
Number
39152-3005
47.5 grams
47.5 grams
47.5 grams
To
permit
weights
NOTE
ramp
r-
------
proper
Part
Installed
:
as
shown in
installation
Number
weight
illustration
~~
c--
------
INCORRECT
and
[:~~~!!~~J
security
13042-3001 (0.031 in., 0.8
positioning
.
RAMP
~~
------
of
must
not
WEIGHT
~
nut,
exceed 0.5 gram difference on
do
not
exceed a
mm
thick)
POSITIONING
r
----------------------------
maximum
on 6 x 16
mm
a
, t
~
NUT
~
NUT
~~
~
~
~WE
t
D
~
~
IGH~:MP
CORRECT
~
WEIGHTS
of 2 installed
bolts.
each
side
of
-,
(f.}~
\
~
~
'"
BOLT
~
WEIGHTS
~
~
~
~
~
RAMP
BOLT
""
WEIGHT
DRIVE
Weight-Grams
1-4
CONVERTER
Total Ramp
55 .8
56.3
56.8
57.3
57.8
58.3
58.8
59.3
GENERAL
RAMP
Number
Weights
To
permit
weights
NOTE
for
two
weight
illustration.
SPECIFICATIONS
Installed
0
1
2
3
4
5
6
7 3.5 grams
proper
Part
Number
: One weight Part
weights Part
positioning
WEIGHT
of
installation
COMBINATIONS
Weight
0.031 in. (0.8 mm)
and
13042-3001 (0.031 in.,
Number
Number
does
13042-3001 (0.031 in ., 0.8
not
exceed 0.5 gram difference on
USING
(0.5 gram each)
Part
Number
13042-3001
0 6.0
0.5 gram
1.0 gram
1.5 grams
2.0 grams
2.5 grams
3.0 grams
thick
BOLT
PART
NUMBER
Bolt
6 x 20 mm
Part Number
110G0620
grams
6.0 grams
6.0 grams
6.0 grams
6.0 grams
6.0 grams
6.0 grams 2.3 grams
6.0 grams 2.3 grams
110G0620
Nut
Special
Part
Number
92019-008
2.3 grams
2.3 grams
2.3 grams
2.3 grams
2.3 grams
2.3 grams
(6 x 20
[::~~~~~~:]
security
13042-
of
nut,
0.8
3002
(0.062 in., 1.6
do
mm
not
thick)
exceed a
on
6 x
mm
mm
thick)
each
side
maximum
20
mm
thick)
may
providing
of
ramp
of 7 installed
bolts
.
be
substituted
that
installed
as
shown in
mm
STEEL)
Ramp Weight
Part
Number
39152-3005
47.5 grams
47.5 grams
47.5 grams
47.5 grams
47.5 grams
47.5 grams
47.5 grams
47.5 grams
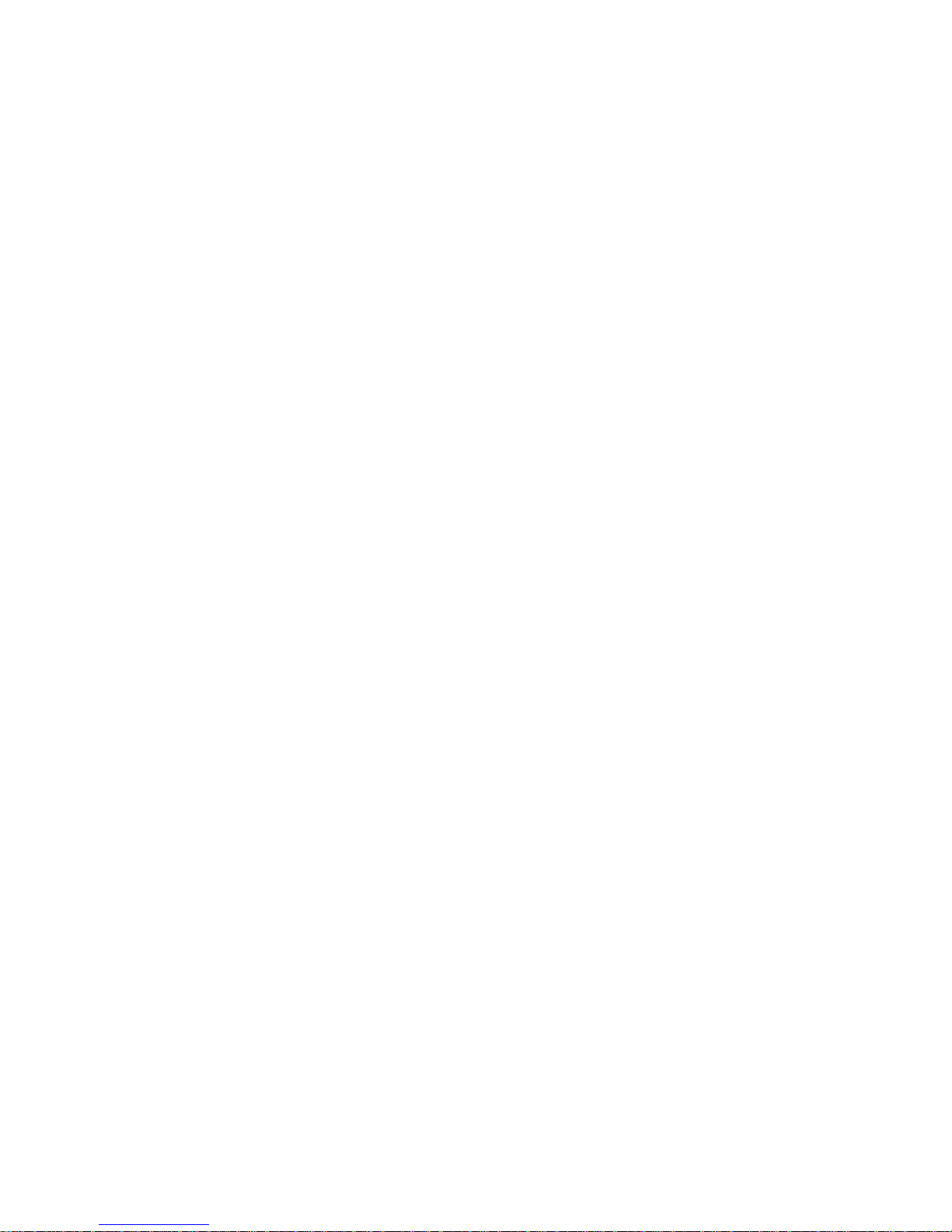
Total Ramp
We
ight
-Grams
Numb
Weights
USING
er
of
Installed
DRIVE
BOLT
CONVERTER
PART
NUMBER
Weight (0.5 gram each)
0.031 in. (0.8 mm)
Part
13042-3001
RAMP
92001-3003 (6 x 20
Numb
er
WEIGHT
thick
COMBINATIONS
mm
ALUMINUM)
Bolt
6 x
20
mm
Part
Number
92001-3003
Nut Special
Part Number
92019-008
Ramp
Weight
Part Number
39152-3005
51.9 grams
52.4 grams
52.9 grams
53.4 grams
53.9 grams
54.4 grams
54
.9 grams
55.4 grams
To
permit
weights
NOTE:
for
we
illustration
DRIVE
Weight-Grams
CONVERTER
Total Ramp
57.1 grams
57.6 grams 1
58.1 grams
58.6 grams
59.1 grams 4
59.6 grams
60.1 grams 6
60.6 grams 7
61.1 grams
61
.6 grams
62.1 grams
62.6 grams
63.1 grams
63.6 grams 13
64.1 grams 14
64.6 grams
65.1 grams
65.6 grams
Part
two
weights Part
ight
pos
Number
Weights
0
1
2
3 1.5 grams 2.1 grams 2.3 grams
4
5 2.5 grams
6
7 3.5 grams
0
0.5 gram
1.0 gram 2.1 grams 2.3 grams
2.0 grams
3.0 grams 2.1 gra
2.1
grams 2.3 grams
2.1 grams
2.1
grams
2.1
grams 2.3 grams
ms
2.1 grams 2.3 grams
2.3 grams
2.3 grams
2.3 grams
47.5 grams
47.5 grams
47.5 grams
47.5 grams
47.5 grams
47.5
47.5 grams
47.5 grams
[:~~~!!~~::]
proper
installation
Number
On
e weight Part
itioning
.
RAMP
Installed 13042-3001
0 0 7.3 grams 2.3 grams 47.5 grams
2
3 1.5 gram
5 2.5 grams
8
9
13042-3001 (0.031 in., 0.8
Numb
does
WEIGHT
of
10 5.0 grams
11
12
15
16
17
and
security
Number
not
COMBINATIONS
Weight (0.5 gram each)
0.031 in. (0.8 mm)
13042-3002 (0.062 in., 1.6 mm
er 13042-3001 (0.031 in
exce
ed
Part Number Part
0.5 gram 7.3 grams 2.3 grams 47.5 grams
1.0 gram
2.0 grams
3.0 grams 7.3 grams
3.5 grams
4.0 grams
4.5
5.5 grams
6.0 grams
6.5 grams
7.0 grams
7.5 grams
8.0 grams
8.5 grams
of
0.5 gram
USING
thick
grams
nut
, do
mm
.,
differenc
BOLT
not
exceed a
thick)
0.8
mm
e on e
PART
Bolt
110G0628
7.3 grams 2.3 grams
7.3 grams 2.3 grams 47.5 grams
7.3 grams 2.3 grams 47.5 grams
7.3 grams 2.3 grams
7.3 grams 2.3 grams
7.3 grams
7.3 grams 2.3 grams
7.3 grams 2.3 grams
7.3 grams 2.3 gr
7.3 grams 2.3 grams
7.3 grams 2.3 grams
7.3 grams 2.3 grams
7.3 grams 2.3 grams 47.5 grams
7.3 grams 2.3 grams 47.5 grams
7.3 grams 2.3 grams
on 6 x
thick)
ach
side
6 x
28mm
Number
maximum
20
mm
thick)
may be subs
providing
of
ramp as shown in
NUMBER
of
7 installed
bolts
.
titut
ed
that
in stall ed
110G0628
Nut
Part
92019-008
2.3 grams 47.5 grams
2.3 grams
(6 x
28
Special Ramp Weight
Numb
er
am
s
mm
Part
39152-3005
47.5 grams
47.5 grams
47.5 grams
47.5 grams
47.5 grams
47.5 grams
47.5 grams
47.5 grams
47.5 grams
47.5 grams
47.5 grams
grams
STEEL)
Number
To
permit
proper
installation
weights
NOTE:
for
weight
illustration.
Part
Number
One weight Part
two
weights Part
positioning
[:~~~~=1
and
security
13042-3001 (0 .031 in., 0.8
Number
does
not
Number
13042-3002 (0.
13042-3001 (0.031 in ., 0.8
exceed 0.5 gram difference on
of
nut,
do
not
mm
thick)
062
in., 1.6 mm
exceed a
on 6 x
mm
thick)
each
side
maximum
28
mm
thick)
may be s
providing
of
ramp
GENERAL
of
bolts.
that
as
17
installed
ubstituted
install ed
shown in
SPECIFICATIONS
1-5
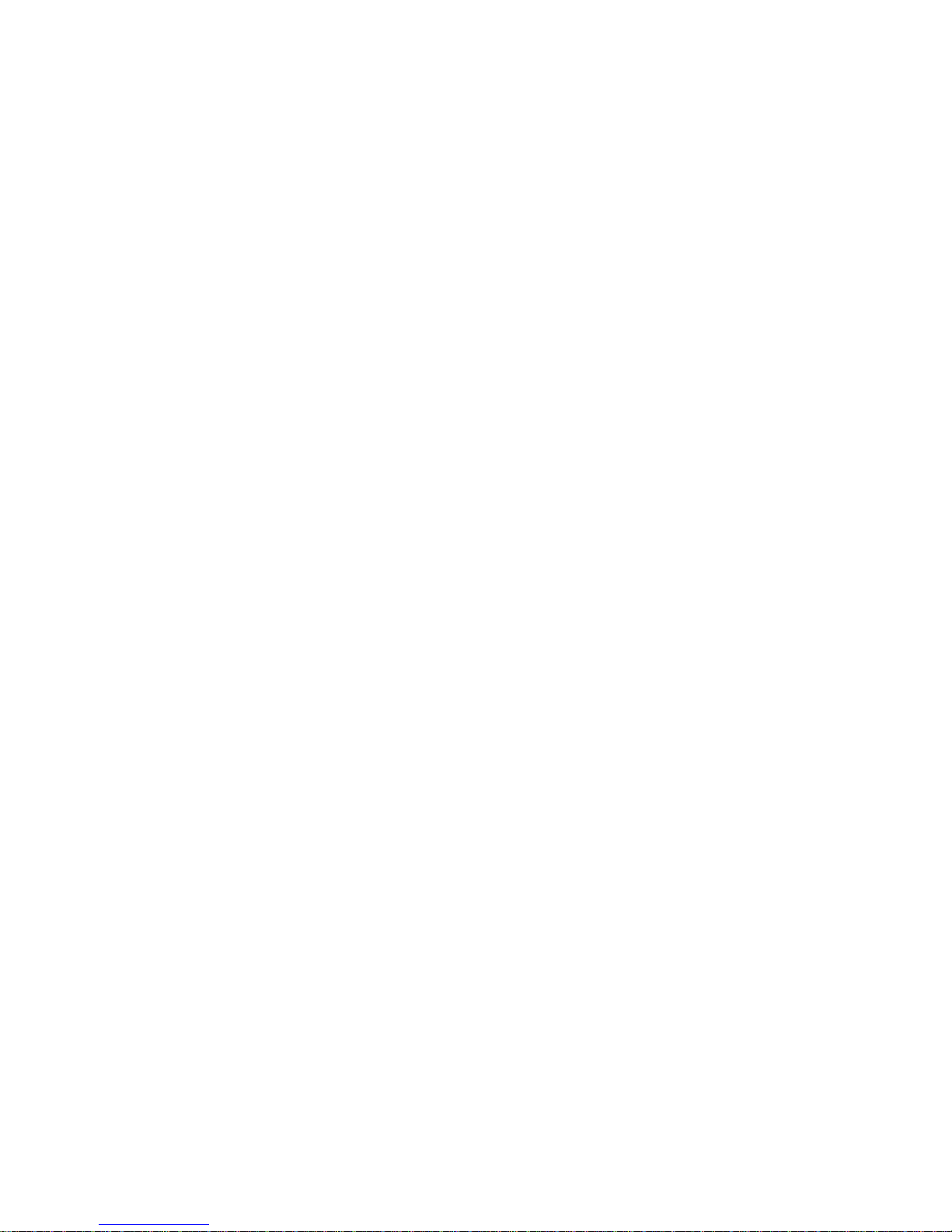
DRIVEN
CONVERTER
Cam Angle (Standard) . . . . . . . . . . . . . . . . . . . . . . . . . . . . . . . . . . . . . . . . . . . . . . . . . . . . . . . . . . . . .
Cam Angle (Optional) . . . . . . . . . . . . . . . . . . . . . . . . . . . . . . . . . . . . . . . . . . . . . . . . . . . . . . . . . . . . .
Spring Part
Spring Color . ....
Spri
ng
Spring Wire Diamteer ...........
Number
Spring
Number
Length - New
of
Spring Coils .
. . .
...
....
...........
......
with
...
......
no load .............
. . .
...........
. . . . .
....
. . .
..............
......
.....
...
. . ......
.... ...............
. .... .
.....
....
..................
. . . .
.......
. .
...
...
. .
...
. ...... ... ...
.....
.
........
........
..
.....
. .
....
..
......
..
. . 6.3 in. (160.0 mm)
. .
. . 0.177 in . (4.5
. .
...
.. ......
Preload - Counterclockwise . . . . . . . . . . . . . . . . . . . . . . . . . . . . . . . . . . . . . . . . . . . . . . . . 1500 B2
BELT
Part Number .... ....
Outside
Width
Thickness -
Circumference . .
of
Top
Surfaces .......
Top
of
Belt Taper Angle ....
belt
......
to
. . . .
....
bottom
....
...
..
. . . . .
.........
...
........
.. ..
. . . ........... . ....... .
of
lug .
...........
. . .
......
....
.
. . ........
..
. . . . . . . . . . . . . . . . . . . . . . . . . . . . . . . . . . . . . . . 30
.....
....
...
.
...
..
.....
..
...
..
....
..
....
. .
...
......
.....
....
......
46.62 ± 0.19 in. (1.184 ± 4.8 mm)
1.25 ±
0.03
....... 0.53 ± 0.03
..
in. (31.7 ± 0.8
in. (13.5 ± 0.8 mm)
..
35
..
30°
92081-3003
....
Black
mm)
7 ± 1/8
or
Cl
59011 -3502
mm)
0
0
BRAKE
Replace brake
tab
to
brake di
pads
as
sc meas
a set when the distance
ures le
ss
than
...
. . . .
from
....
outer
..
surface
....
of
brake pad
....
. . . . . . .... . .
...
......
....
GEARING
Top
Sprocket ....
Lower Spr
ocket
Sprocket Overall Ratio ....
Chain
(Silent
Type) . ........
Cha
in Tensioner Spri
Dri
ve
Chain Tension . . . . . . . . . . . . . . . . . . . . . . . . . . . . . . . . . . . . . . . . . . . . . . . . . . . . . . .
TRACK
AND
Track
Type ........
Track Width
Track
Length .
SUSPENSION
..
...
...
.....
ng
....
....
. .........
..........
..
. . . . . . ......
...
. .
..................
....
..
......
..
...........
.
......
...
.......
. .
....
. . .... .
.....
.
..... ..
. . . ....
.................
.......
.....
......
. . .
...
.
........
.......
....
.
. . . .
..
.
..
....
...
..........
.
................
......
.
.....
...........
.
....
. .......
...
Rubber (Internal Dri
..
...
...
. ....
. . ....
....
.......
..
.......... ..
..
. .
...
..... . ....
..
...
.. .......
ve
Lug)
......
...........
...
..........
.
Molded
.
......
........
..... .
121
Suspension . . . . . . . . . . . . . . . . . . . . . . . . . . . . . . . . . . . . . . . . . . . . . . . . . . . . . . . . . . . . . . . .
1/4 in. (6.4 mm)
21
39 Teeth
. .
...
..
1.86
....
66 Pitch
...
..
Self
Adjusting
in Fiberglass Bar
15 in. (381
in. (3,073.4 mm)
.. Slide Rail
Teeth
to
Green
mm)
1
1-6
GENERAL
SPECIFICATIONS
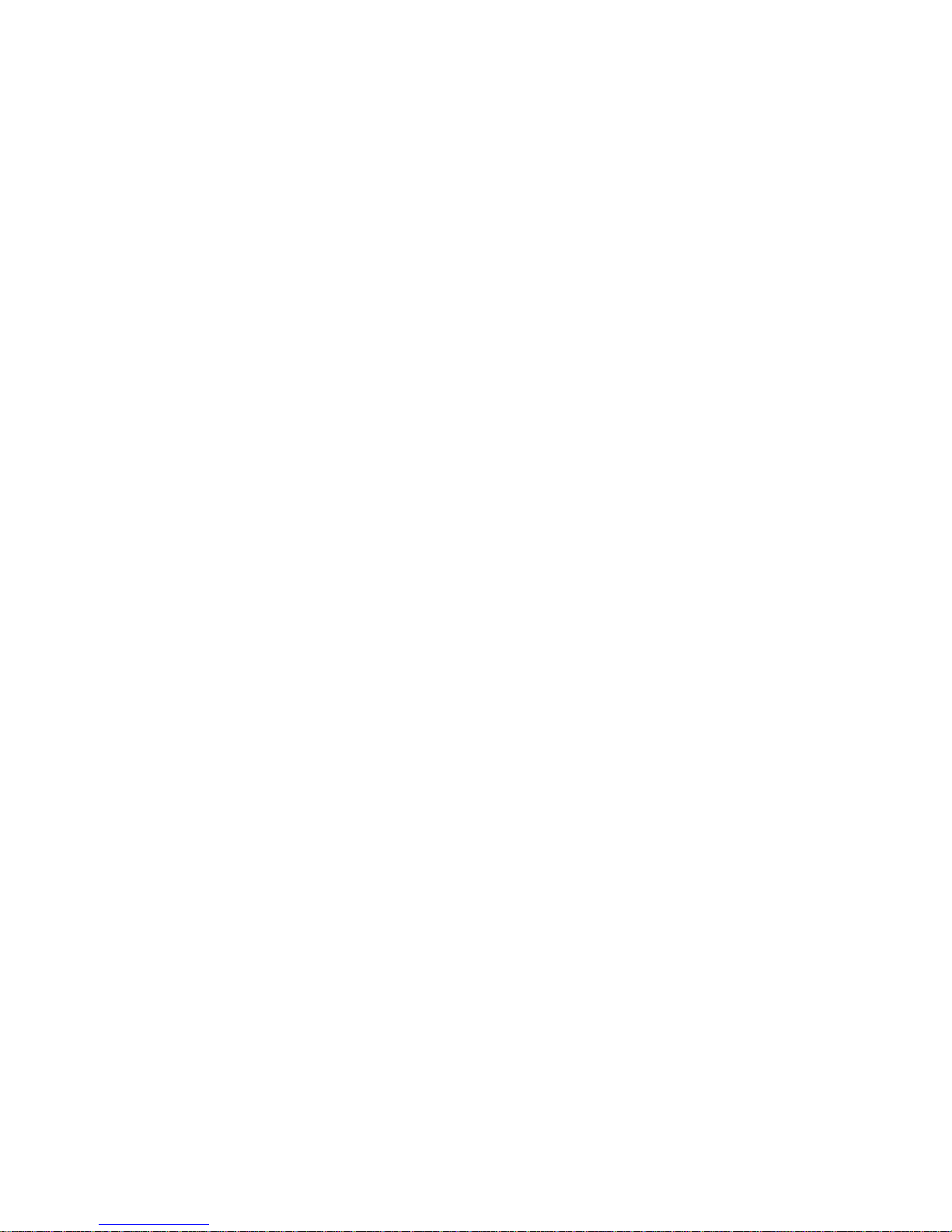
ELECTRICAL
COMPONENTS
Type . . .
Headli
Ta
il/Brake
Instrument
Battery .
Electrolyte
FRAME
Frame . .
.. .. ..
ght
Bulb Part Number . . .... . .... . .
Light ....... .....
Light
..............
Volume
...
. . .
............
. .........
.........
...
.......
. . . ......
. .
...
. ...... ...
.... . .
. . ..............
.......
. . . . . .....
...
...
. . ........
..
. ........
..
...
. . .
.. ..
. . . .... .... . . . . . . .
. .
...
. . . . . . . . . .
.. ..
. .
........
...
..
...
12 Volt
.....
...
22 amper e
. .
.....
. . . . . . . .
....
.
...
. . . . .
.........
......
Aluminum all
...
........ .
.....
. . .... . . . . .
/ho
. . . . . . . .... . .
...
urs capacity @ 10 h
. .
...
....
oy and
12
12
......
. . . .... G.
our discha
1.5 quarts (1.4 lit
HSLA
ste
el
VDC,
120 W
92069
-3501
V,
60/60 W
G.E.# 1157
E.#1816
rge rate
ers)
construct ion
ENGINE
Effective Compression Ratio .....
Piston Ri
Pisto
Piston Skirt Clearance . . .........
Connecting Rod
Connecting Rod
Connect i
Crankshaft End
Crankshaft Run
Cylinder
*Measured
ng
End
Gap
(Top)
n Ring End Gap
ng
Rod Small End Diameter . . . .
Head
with
(Bottom) ...... . . . . . . . . . . ......
Radial Play . . . ..........
Side Clearance
Play (ma
Out
Capacity* . . .
sta
ndard spark plug installed.
ximum)
(maximum) .
...
.. .. .............
Service Specifications
.....
...
. .
........
...
...
..........
..... .
. ...............
..
. . . . . . .
. . ......
..........
.....
......
.. ..
. . .............
......
. .......
....
...
......
. .
......
. . ....
..........
....
....
..
.........
.. .. ..
. .........
....
...
. . . . . . . ....
.. ..... ..
.
...... ...
... ...
...
..... .
...
. . . . . . . . . 0.016-0.
.. ..
...
. . . .
..
. . . .
.....
.....
. .....
...
....
........
..
0.008-0.
. . . 0.008-0.016 in .. (0.2-0.4 mm)
.. 0.002
..
0.0008-0.
. . 0.787-0.
. . .... . 0.015 in. (0.38 mm)
...
. . . 0.002 in. (
. . . . . . . ....
. .
......
016
in. (0.2-0.4 mm)
-0.004 in. (0.05-0. 10 mm)
001
in. (0.02-0.03 mm)
020
in. (0.4-0.5 mm)
789
in. (20.0-20.5 mm)
T.I.R.)
.. .. 18.3 + .4 cc
(0.05 mm)
. 7.3 to 1
SERVICE SPECIFICATIONS 1-7
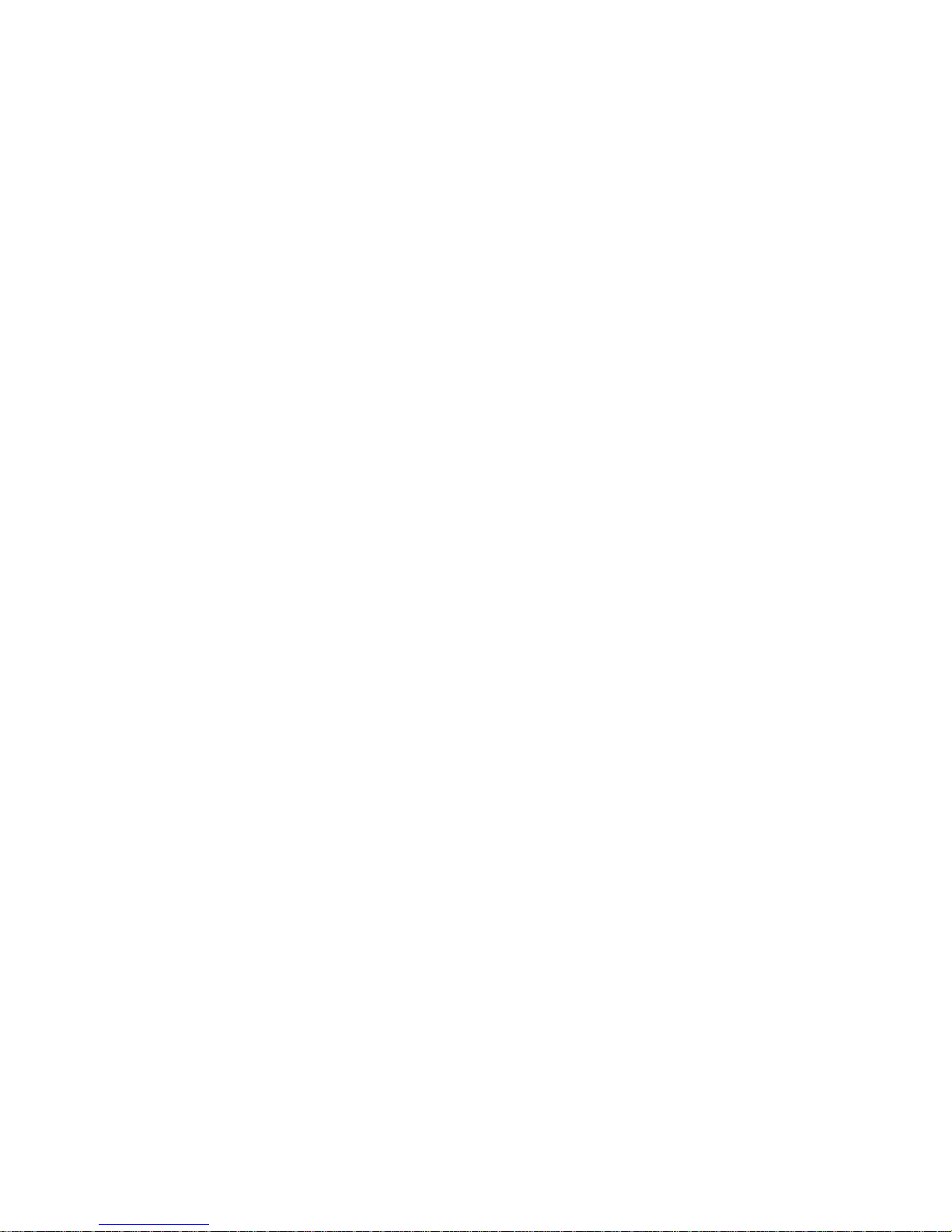
IGNITION
Spark Plug Gap
Ignition
Igni
tNOTE:
ditions
CARBURETOR
A
Idle Screw Setting
(Final)
Float
Timing
tion
Timing (B.T.D.C .) ..............
Item
Lighting
Exciter Coil
Pulser Coil
Item
tSecondary
Defective coils cannot always
is
the
recommended test method.
ir
Screw Setting
.....
Arm
Adjustment
.......
(Dynamic) . .........
Coil
winding
(Initial)
(Initial)
. . . ........
. .
...
... ...
......
..........
.........
. . . . . ........
.......
. .
. ................
......
........
MAGNETO
Ohmmeter
CDI
IGNITER
Ohmmeter
Hi
gh
be
detected using this test alone.
...
.........
....
. . . .... . .
..........
RESISTANCE TESTS
Leads
Yellow·Yellow
Red
·Ground
Red
·White
Leads
Tension-High Tension
. . .
............
..
......
. .... . ........
.. ..............
............
Connected Between
RESISTANCE TESTS
Connected Between
.......
...
...
Use
..............
.
.. ..
.....
. .
...
....
.....
. . .
of
a coil tester
.....
...
...................
. . .
......
. .. .
...
. .
........
. . . . . .
..... .
..
......
.. .....
. . . 0.073 in. (1.86
Re
0.18 oh m ± 20 %
160 ohms ± 20%
17
ohms ± 20%
Resistance
5,700 ohms ± 15%
which
simulates operating con-
........
....
Parallel
to
Body
0.024 in. (0.6 mm)
180@6500R
sistance
. 1.5 Turns Open
..
6 Turns
2,500 R.P.M.
Gasket Surface
Off
.P.M.
mm)
Seat
CHASSIS
Converter Offset Distance
Converter Center Distance . .
Drive Chain Tension
Brake Lever Movement
Track Tension
Steering
Tie Rod End
GENERAL
Cylinder Head Bolts .
Crankcase
Flywheel
Re
Spark Plug .......
Holder (Carb.) Bolts .......
Driven Gear
Gearcase
Alignment ... . .
Adjustment
ENGINE
Bolts and Nuts ......
Nut ...
coil
Bolt
...
Nut ...
Bolts (Socket Head) .... . . . . . . .
.......
...
...........
TORQUE
.....
..........
......
.......
.....
...
.........
..
. ..........
.................
. . .......
.......
....................
Stud Jam
. . . . . . . . . . . . . . . . . . . . . . . . . . . . . . . . . . . . . . . . . . . . . . . . . . . 50 in. Ib (0.6 kg-m)
Nut
SPECIFICATIONS
...
..
...
.....
. ......
...
. ............. ..
.....
.... . . .
. . . . . . . . .
......
.
.......
Dimension
..........
............
..........
..
....
.....
...
.....
. . .............
.... .
. .
...
. . .
. . . .... .
...
.....
...
...
............
...
......
.
........
..
. .......
. . .
.......
............
... ...
...
..........
. . . . .... . .... .
...
. . ....
......
. 3/4 in. (19 mm)
.......
. . . . .
......
......
. . . .
...
.... 0.525
.....................
...
.......
.
.................
.....
.. ..
. ......
..
......
........
.......
. .
....
.........
....
. .
...
....
...... ...
..
maximum
. .
..
....
.........
.....
. .
...
..
. ........
to
0.588 in. (13.3
. . .... .... Self Adjusting
deflection
Skis parallel
. 1-1/4
...
. . .
....
in.
......
. ....
......
...
....
. .
to
14.9 mm)
..
12 in. (305 mm)
. . 3/4 in. (19 mm)
(5
to
8 Ib pull)
or
1/8 in. toe
(32 mm) maxi
16
ft
Ib (2.2 kg-m)
16
ft
Ib (2.2 kg-m)
60
ft
Ib (8.3 kg-m)
20
ft
Ib (2.7 kg-m)
45
in. Ib (0.5 kg-m)
12
ft
Ib (1.6 kg-m)
12
ft
Ib (1.6 kg-m)
out
mum
SERVICE
1-8
SPECIFICATIONS
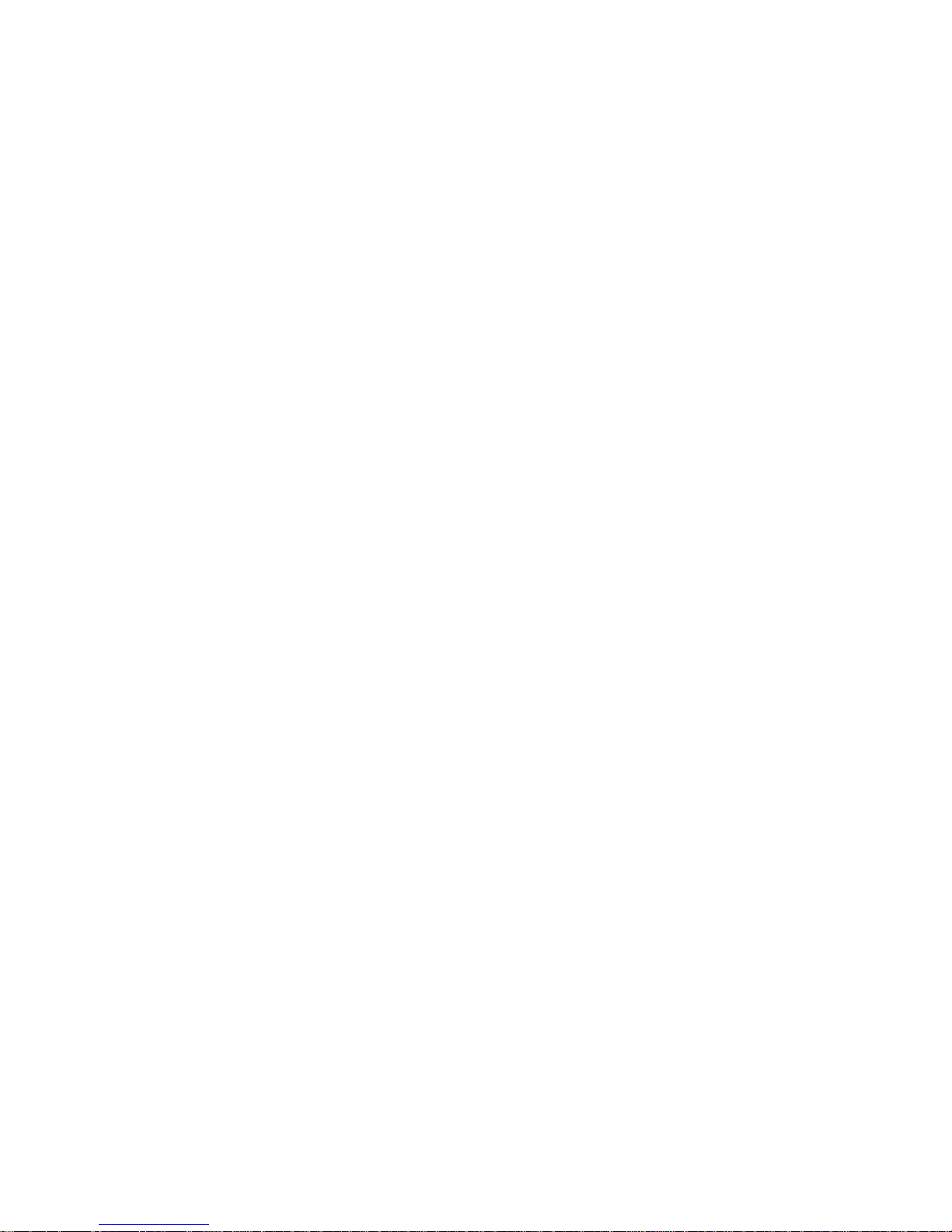
Torque Chart and Loctite Table
Description
ENGINE
Engine
Muffler
Engine
PTO
ELECTRICAL
Ign
Voltage regulator
Brake and
Ta
Tail lamp
DRIVE
Dr
Cover
Roller and pin assembly in movable
Weight ramp and pin assembly
Weight ramp -
DRIVEN
MOUNT
mount
mounting
mount
mount
to
ition
switch -
throttle
il
lamp
lens
to
door -nut
CONVERTER
ive converter
to
movable
CONVERTER
AND
EXHAUST
to
damper -nuts
- nuts
to
chassis - nuts 2
chassis - screw
SYSTEM
nut
mounting -nut
lever - lockscrew
mounting
to
nut
- screws
crankshaft -
sheave -bolt
AND
bolt
to
BRAKE
sheave -bolt
spider -
bolt
Quantity
6
4
5
1
2
1
2
2
1
6
6
6
3
Torque
105 in. Ib (1.21 kg·
60-70
in. Ib (0.69-0.81
31
ft
Ib (4.28
80-90 in. Ib (0.92-1.04
30
in . Ib (0.35 kg ·
105
in.lb
(1.21
20-25 in. Ib (0.23-0.29
50 in. Ib (0.57 kg·
32
in. Ib (0.37
65-70ftlb
8-10ft
8-10
6-
8ft
4-5
ft Ib (0.5-0.7
(9.0-
Ib (1.1 -1.4 kg·ml
ft
Ib (1.1-1.4 k
Ib
(0.8-1.1kg·ml
ml
kg·ml
ml
kg·ml
ml
kg·ml
10kg·ml
g·ml
kg·ml
Loctite
kg·ml
kg·ml
kg·ml
Driven
converter
Coupl ing
Coupling
Caliper
CHAINCASE
Chaincase
Chaincase cover
Jackshaft bearing retainer
Jackshaft bearing retainer
Top
Jackshaft - bearing retainer adjusting
Tensioner arm -
Lower
Bearing retainer cap -
NOTE: Loctite
Generally, No. 222
fastener diameter
essary
formula
lent
to
to
to
sprocket
sprocket
to
remove a fastener.
on
which may
to
jackshaft -
fixed
sheave -bolt
flange -
chaincase -
mounting
each
bolt
nut
AND
JACKSHAFT
- nuts
mounting
mounting
bolt
mounting -bolt
formulas
is
fastener requiring Loctite.
be
substituted
- screws
to
to
- screw
nut
are
is
used
on fasteners up
greater than
bolt
chassis
chassis -front
selected on the
5/16
Be
careful when applying extra force
is
Loctite
- rear
bolt
bolt
bolt -jamnut
basis
to
in. (8
mml,
Loctite
"Lock
of
the
diameter
5/ 16 in. (8
'n Seal,"
mml
No. 242
No. 222 and No. 242
is
product
1 40-50
8-10ft
6
6
8-10ft
ft
35
2
ft
18
4
70 in. Ib
6
31
1
1
1
1
2
1
2
of
the fastener, and the strength
diameter.
specified.
number 21, blue.
Loctite
as
this risks damaging the parts.
are
ft
19
ft
40-50
10-
20ft
70
in . Ib (0.
ft
35
105 in . Ib (1.21 kg
If a particularly
may significantly increase the
industrial designations. The consumer equiva-
ft
Ib (5.53-6.
Ib (1.1-1.4 kg·
Ib (1.1-1.4 kg·
Ib (4.84 kg·
Ib (2.5 kg·
(0.
Ib (4.28 kg·
Ib (2.63 kg ·ml
ft
Ib (5.53-6.92 kg·
Ib (1.38-2.
Ib (4.84 kg·
ml
ml
81
kg·ml
ml
81 kg·
ml
strong bond
92
kg·ml
ml
ml
ml
77kg·ml
ml
·ml
of
the bond required.
is
required,
Use
only
or
the
torque
nec-
the specified
TORQUE
CHART
1-9
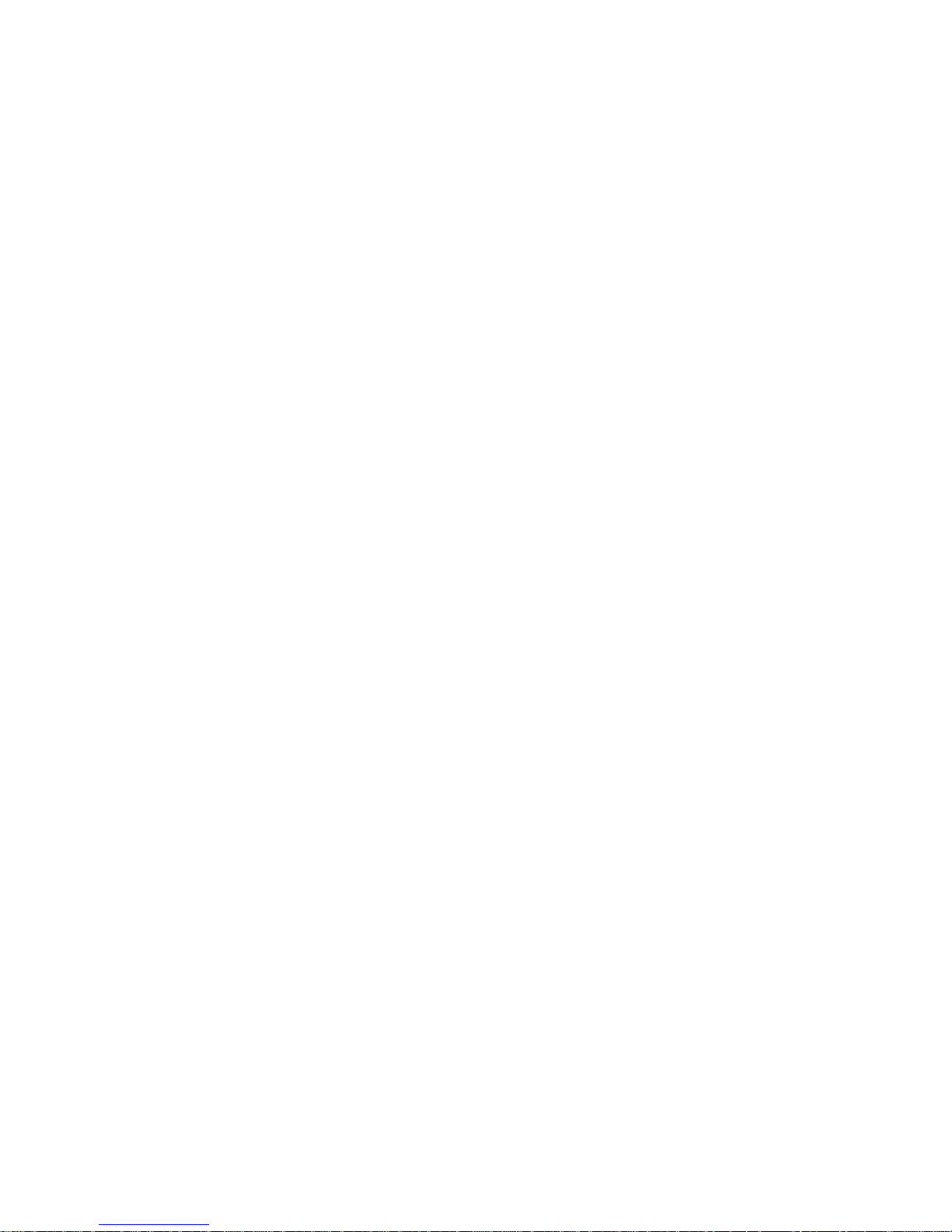
TORQUE
CHART
(CONTINUED)
Description
SUSPENSION
Rear suspension arm to track guard pi
Rear suspension arm ÂRear
axle -
bolt
Idler shaft ÂShock absorber
Swing arm - bolts
Wear strip attaching
Cross shaft
Front
Suspension brace
Limiter
DRIVE
Bearing housing - bolts
Locking
SKI
AND
bolt
mounting
pivot
shaft
strap - nuts
SHAFT
collar set screw
SPINDLE
bolt
s
s
mounting
- nuts
- bolts
to
chassis
-
front
- nuts 2
- bolts
and rear - bolts
pe
- nuts
Quantity
2
2
2
2
2
2
4
2
4
4
3
2 72 in.
Torque
11
ft.
lb
. (1.52
kg'm)
30
ft.
lb. (4.15 kg'm)
25
ft.
lb. (3.46 kg'm)
ft.
lb
25
35
25
25 i
30
25
25
45 in. lb. (0.51 kg'm)
18
. (3.46 kg'm)
ft. lb
. (4.84 kg'm)
ft
. lb. (3.46
n. lb. (0.29 kg'm)
ft.
lb . (4.15 kg'm)
ft
. lb. (3.46
ft.
lb. (3.46 kg'm)
ft
. lb. (2.5
lb. (0.83 kg'm) 222
kg
kg
kg
'm)
'm)
'm)
Loctite
Ski
skeg
attaching -
Front
spring
mount -bolt
Shock absorber
Saddle
to
spring -
Spindle
Rear spring
STEERING
Handle holder ÂSteering arm
Steering column
Steering arms
Steering post
T
Tie rod jam
R H tie rod
Handle bar
Ti
Tie rod adjusting
NOTE:
Generally,
fastener diameter
sary
formula
which may
to
ski saddle -
mount -bolt
to
to
mounting
ie
rod jam -
e r
od
to
nut
-
nut
to
steering arm -
to
steering column
adjusting - nuts (RH)
Loctite
#222
remove a fastener.
on
each
be
substituted
nut
(wear runner)
to
ski and spindle -
bolt
nut
bolt
spindle -
to
tie rods - nuts
- nuts
formulas
bolt
tie rod -
(LH)
(RH)
is
is
fastener requiring
nut
- bolts
nut
mounting
(LH)
are
selected
used
on fasteners
greater than
Be
is
Loctite
nut
- screws
on
the
basis
of
the
diameter
up
to
5/16
in. (8
mm)
diameter.
5/16
in. (8
mml,
#242
is
specified.
careful when applying extra force
Loctite.
"Lock
Loctite
'n Seal,"
#222
product
and
#242
number 21, blue.
120 in.
6
25 in.
2
31
4
46
4
46
2
31
2
1 35
2
30
1
30
30 ft. lb. (4.15 kg'm)
2
4
18
2
100-120 in. lb. (1.15-1 .
2
100-120 in. lb . (1.15-1.38 kg'm)
1
30ft
4
105 in. lb. (1.21 kg'm)
2
100-120 in. lb. (1.15-1.38 kg'm)
2
100-120 in. lb. (1.15-1.38 kg 'm)
of
the
fastener, and the strength
If
a particularly strong
Loctite
as
this risks damaging
are
may significantly increase the
industrial designations. The consumer equivalent
Ib_
(1.4 kg'm)
lb. (0.29 kg'm)
ft
. lb. (4.28
ft.
lb. (6.36 kg'm)
kg
'm)
ft. lb. (6.36 kg·m)
ft
.
lb
. (4.28 kg-m)
ft
. lb. (4.84 kg'm)
ft.
lb. (4.15 kg'm)
ft
. lb. (4.15
ft
. lb . (2.5 kg'm)
. lb. (4.15 kg'm)
the
kg
'm)
parts.
bond
38
kg'm)
of
the bond required.
is
required,
torque
Use
only
the specified
or
the
neces
-
1-10
TORQUE
CHART
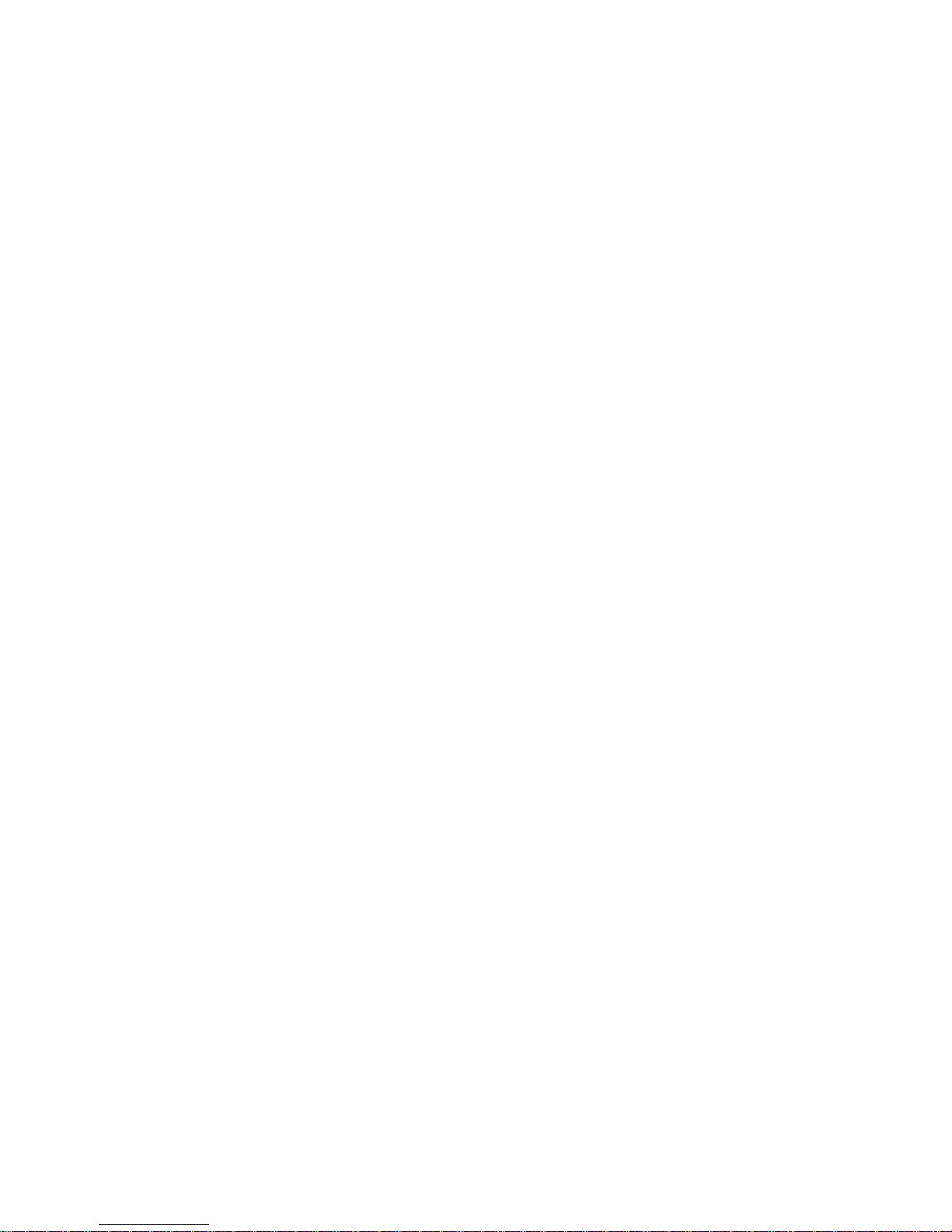
CHASSIS
Description
Quantity
Torque
Loctite
Snow
flap
to
bulkhead ÂHood guide and
Hood guide,
Passenger
Pan
brace
Rear s
tay
Trim
attaching·
Seat
attaching·
FUEL
SYSTEM
Fuel
pump
Primer
pump -nut
CABLES
Brake cable
Enrichener cable assembly· nuts
Enrichener assembly
Speedometer
Throttle
FAN
Air
Fan
cable assembly - nuts
CASE
shroud
case
trim
front
handle attaching - nuts 4
attaching·
attaching·
screws 2
bolts
assembly
jam,
cable - nuts
AND
mounting
to
crankcase
nut
mounting
bumper
nuts
AIR
and
screws
bolts 2
mounting·
pal·
nut
SHROUD
bolts
mounting
50 in. Ib (0.57
2
- screws 8
hood hinge attaching - nuts
nuts 2 35 in. Ib (0.40
nuts
18
12
20 in. Ib (0.23 kg'
70 in. Ib (0.8
10
ft
Ib (1.38
70 in. Ib (0.81 kg'
2
19
ft
Ib (2.63 kg '
20 in. Ib (0.23 kg '
35 in.
4
1
2
2
1
1 Hand Tighten
2
4
Ib (0.40
30
in. Ib (0.35 kg'
50 in.
Ib
(0.57
15-20 in. Ib (0.17·0.23 kg '
Hand Tighten
15·20 in. Ib (0.17·0.23 kg'
60 in. Ib (0.69
1(}'12
ft
Ib (1.4-1.7
kg'ml
kg'ml
kg'ml
kg'ml
kg'ml
kg'ml
kg·ml
ml
ml
ml
ml
ml
ml
ml
222
kg·ml
HOOD
Hood hinge - nuts
Hood latch
INSTRUMENT
I nstrument panel bracket ÂGauges
I nstrument panel - screws
CRANKSHAFT
Flywheel -
CRANKCASE
Cyl inder head - nuts
Spark pl
Crankcase - bolts
band·
to
panel - nuts
nut
ug
screws
PANEL
AND
AND
CYLINDER
INSTRUMENTS
nut
6
4
3
6
6 15
1 60
16
2
8
Ib (0.29
25 in.
Compress rubber
0.06 in. (1.55
95 in.
Ib
11
in . Ib (0.13 kg'
in.lb
ft
Ib (8.30 kg'
ft
Ib (2.2 kg'
16
20
ft
Ib (2.77 kg'
16
ft
Ib (2.2
(1.09
(0.17
mml
kg'ml
kg'ml
kg'ml
kg'ml
ml
ml
ml
ml
TORQUE
CHART
1-
11
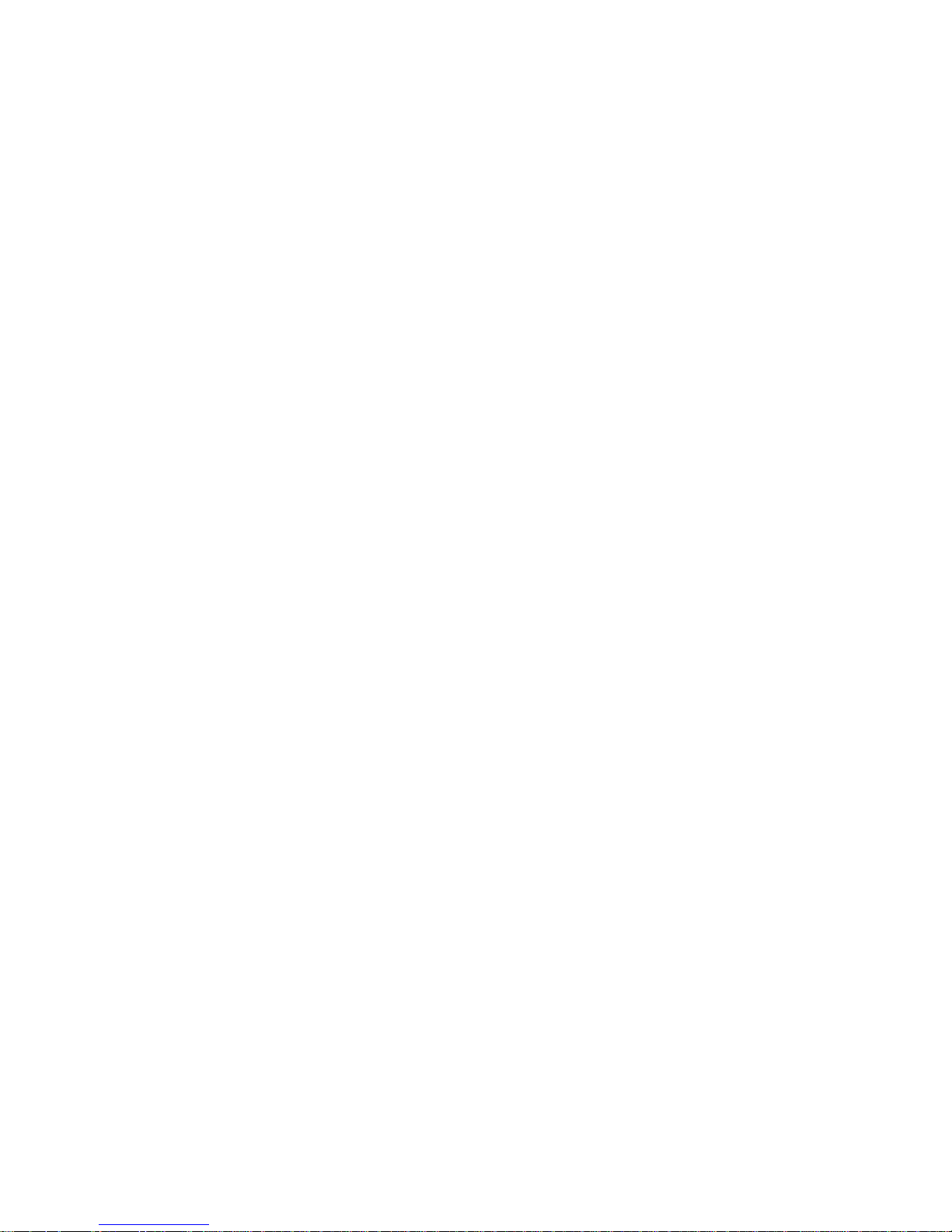
EXHAUST
Descri
ption
Quantity
Torque
Loctite
Exhaust
COl
Stator
Wire clamps
Exciter
Lighting
ELECTRICAL
COl igniter
Ignition
RECOI
Drive plate
Starter
Starter
manifold
MAGNETO
plate
mounting
to
coil and pulser coi I
coil
mounting
coil
L
STARTER
mounting -nut
pulley
mounting
- nuts 4
- screws
stator plate - screws
mounting
mounting
mounting -bolt
- screws
- screws
-screw 2
- bolts
mounting
s
- screws
8-10ft
2 5-6
Hand tighten
2
Ib (1.11-1.
ft
Ib (0.69-0.83 kg·m)
2 35 in . Ib (0.40 kg-m)
2
35 in. Ib (0.40 kg-m)
2
60 in. Ib (0.69 kg·m)
5-6
ft
Ib (0 .69-0.83 kg·m)
1
8-10ft
5-6
3
5-6
3
Ib (1.11-
ft
Ib (0.69 -
ft
Ib (0.69 -0.83 kg·m)
1.38kg
0.83
38 kg·m)
·m)
kg·m)
1-12
TOROUE
CHART
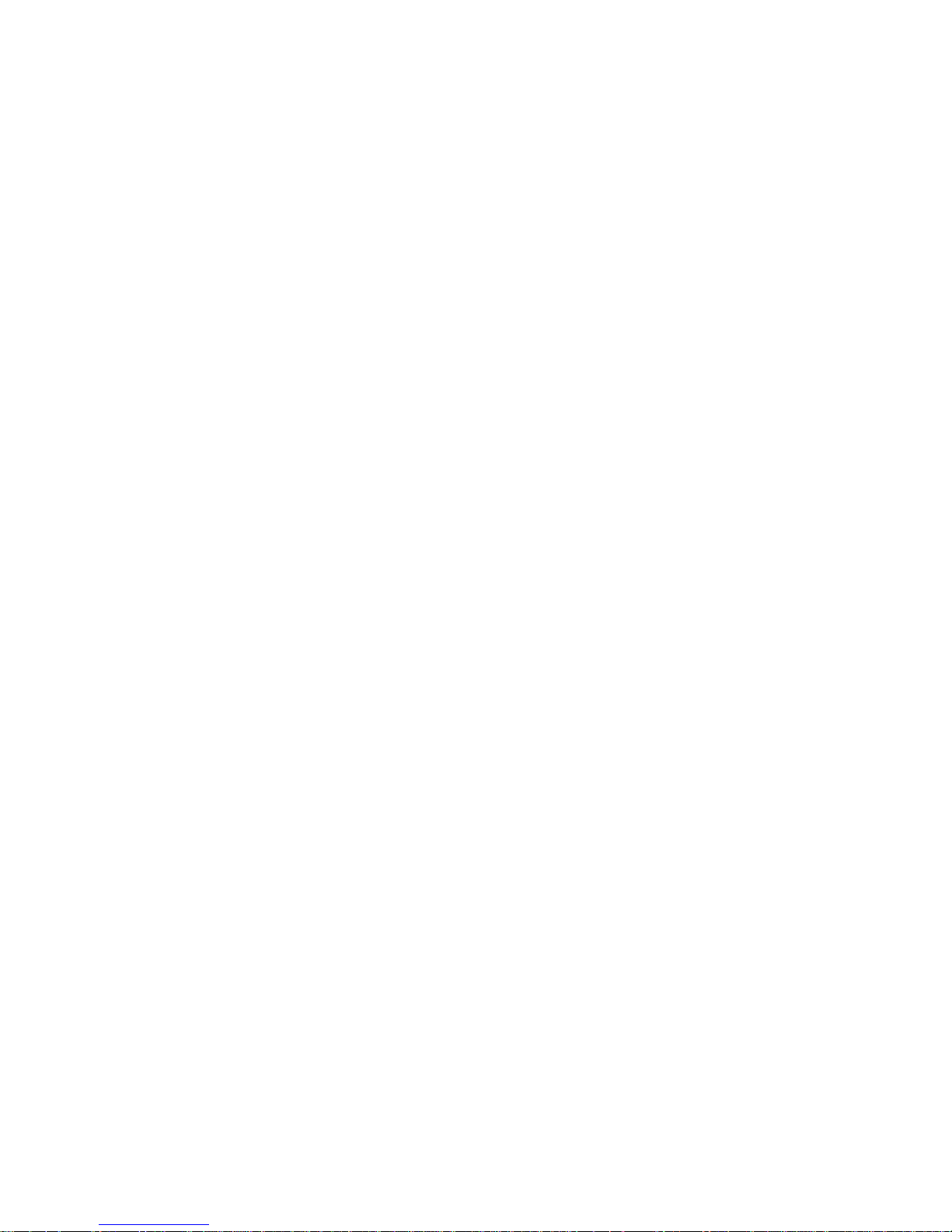
Gear Ratio
Chart
I
f-
w
w
f-
lL
0
a:
w
en
:2'
~
z
I
f-
w
~
U
0
a:
0-
til
Z
w
:::
a:
0
36
37
38
39
40
Dri ve Sproc ket · Number
17 18 19
2.18 2.06 1.95
*6
6 MPH
64
R
ed
2.24
*
64 MPH
64
Pink
2.
35
'6
1 MPH
66
P
ink
*6
9 MPH ' 73 MPH
64 64
Pink
2.
11
' 68 MPH
64
Green
2.22
' 64 MPH '
66
Pink
of
Teeth
20
L
90
' 75 MPH '
64
R
ed
Gr
een
2.
05
'
70
MPH ' 73 MPH
66
Red
2.
11
68
MPH
66
Gr
een Green Tension er Spring
1.80 Gear Ratio
80 MPH
64
Pi
nk
1.90
* 75 MPH
66 66
R
ed
1.95
66
Pink
2.
00
' 72 MPH
66
21
1.76
*
81
MPH
66 66
Re
d
1.
81
*79 MPH
Pi
nk Green
L 86
' 77 MPH
66
Green
22
1.68
*85
MPH
Pink T
1.73
' 83 MPH
66
Speed
Chain Pitch
Tension
G
ea
r Ratio
Speed
Ch
ain Pitch
ens
ioner Spring
I
Gear Ratio
Speed
Chain Pitch
Tensioner Spring
Gear Ratio
Speed
Cha
in P
Tensioner Spring
Gear Ratio
Spe
ed
Ch
ain Pitch
er
itc
Spring
h
Color
---
Black
White
Red
Orange
Pink
Yellow
Green
Blue
*Theo retical
NOTE:
All
MPH
at 7100
top
speeds based on
2.50
2.50
3.00
3.00
3.38
3.
38
3.75
3.75
RPM
0.96
overdrive
in
conv
erter
and
engine
RPM
at 7100.
Chain Tensioner Springs
Length Wire Dia.
(63.50
in.
(63.
in.
(76.
in.
(76.20
in.
(85.85 mm)
in.
(85.85
in.
(95.25 mm)
in.
(95.25 mm)
in.
50
20
mm)
mm)
mm)
mm)
mm)
0.049
0.055
0.049
0.055
in.
in.
in.
in.
0.049 in.
0.055 in.
0.
049
in.
0.055
in.
(1.245
(1.397 mm) .
(1.245
(1.397 mm)
(1.245mm)
(1.397 mm)
(1.245
(1.397 mm)
mm)
mm)
mm)
GEAR
RATIO
CHART
1-13
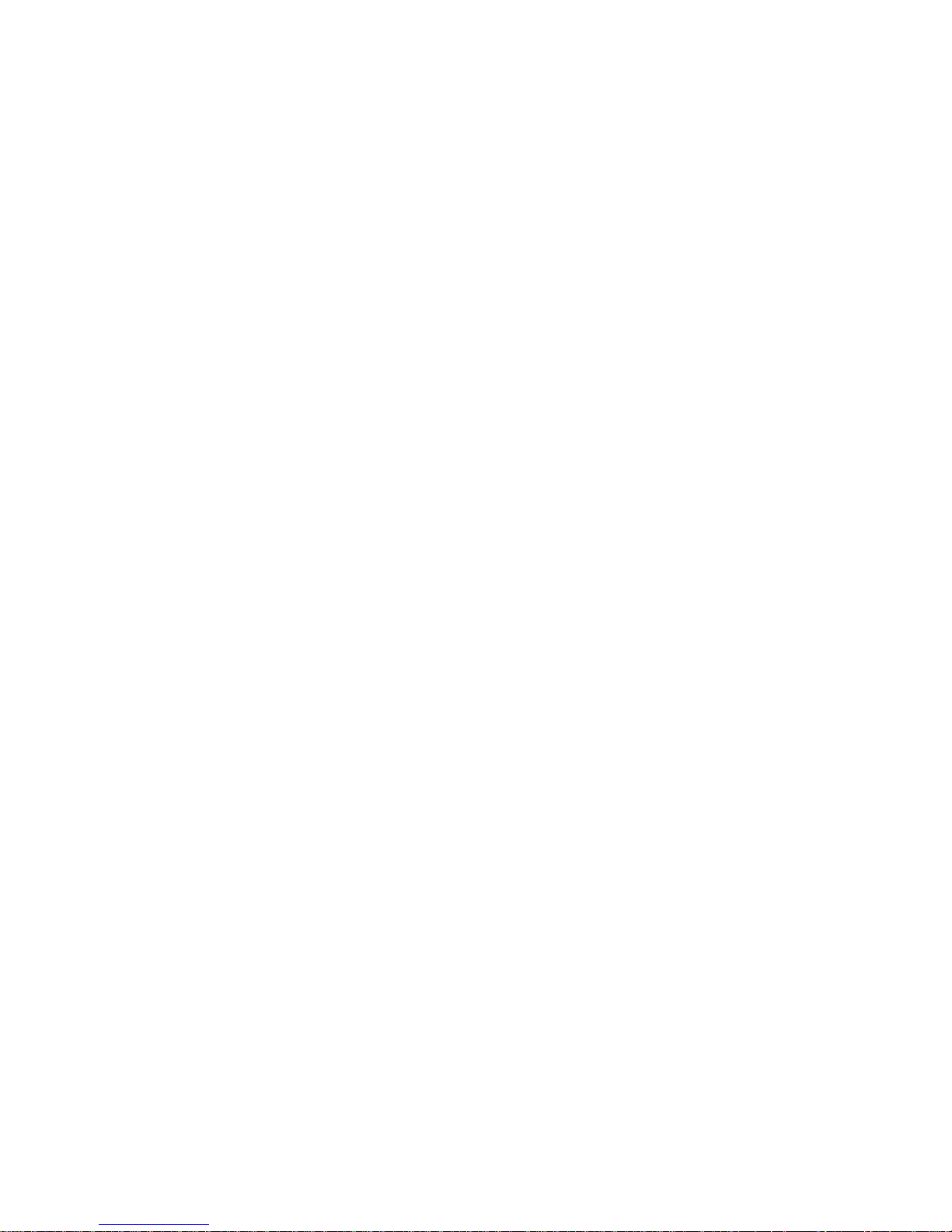
ENGINE
80
70
60
ex:
L.U
S
50
0
a..
L.U
CJ)
ex:
0
I
40
30
20
10
CJ)
CO
--1
--
f-
LL
L.U
6
ex:
0
f-
40
30
20
10
PERFO
- - - -
- -
- - - -
- - -
--
RM
--
- - - - - - -
--
--
-
ANC
- - - -
-
vEt-
[k/
~
I
~
/
~ 0 ~ a ~
~ ~ ~ ~
RPM
-
FUEL
- CONSUMPTION /
r---L2
""
/'
/
/'
o 0 0 0 0 0 0 0 0
o 0 0 0 a a
o a a a
M
~
ENGINE
ST440-A4
E
- -
HP
TORQUE-
~
00
ro
CURVES
-
0
00
-
2.2 I
2.0 I
1.
8
1.
6
1
.4
1.
2
1 . 0
0.8
0.6
0.4
ex:
a..
2:.
CJ)
~
--1
L.U
~
LL
V
~
A
EXHAUST
PORT
-.;;;
~
PORT
r
B
C
!
8
1.575 in. (40.0 mm)
A =
B
1.272 in. (32.3
=
1.189 in. (30.2
C
=
D
1.890 in . (48.0
=
E
1.
228 in. (31.2
=
F
3.807 in. (96.7 mm)
=
DIMENSIONS
TOP SURFACE OF
D
INTAKE
PORT
B
mm)
mm)
mm)
mm)
CYLINDER
F
I
E
1
0.555 in. (14
G
=
H
1.906 in. (48.4
=
I
1.906 in. (48.4
=
0.555 in . (14.1
J
=
0.795 in. (20.2
K =
0.799 in. (20.3
L =
H
t§J
r--
L---"
.1
mm)
mm)
mm)
mm)
mm)
mm)
PORT
-K-
I
~+
NOTE:
Port
width
does
not
include
the
chamfer. Port
1-14
ENGINE
PERFORMANCE
CURVES
height
AND
and
height
PORT DI
location
MEN
includes
SIONS
the
chamfer. Port
chamfer = 0.039
in. (1.0
mm)
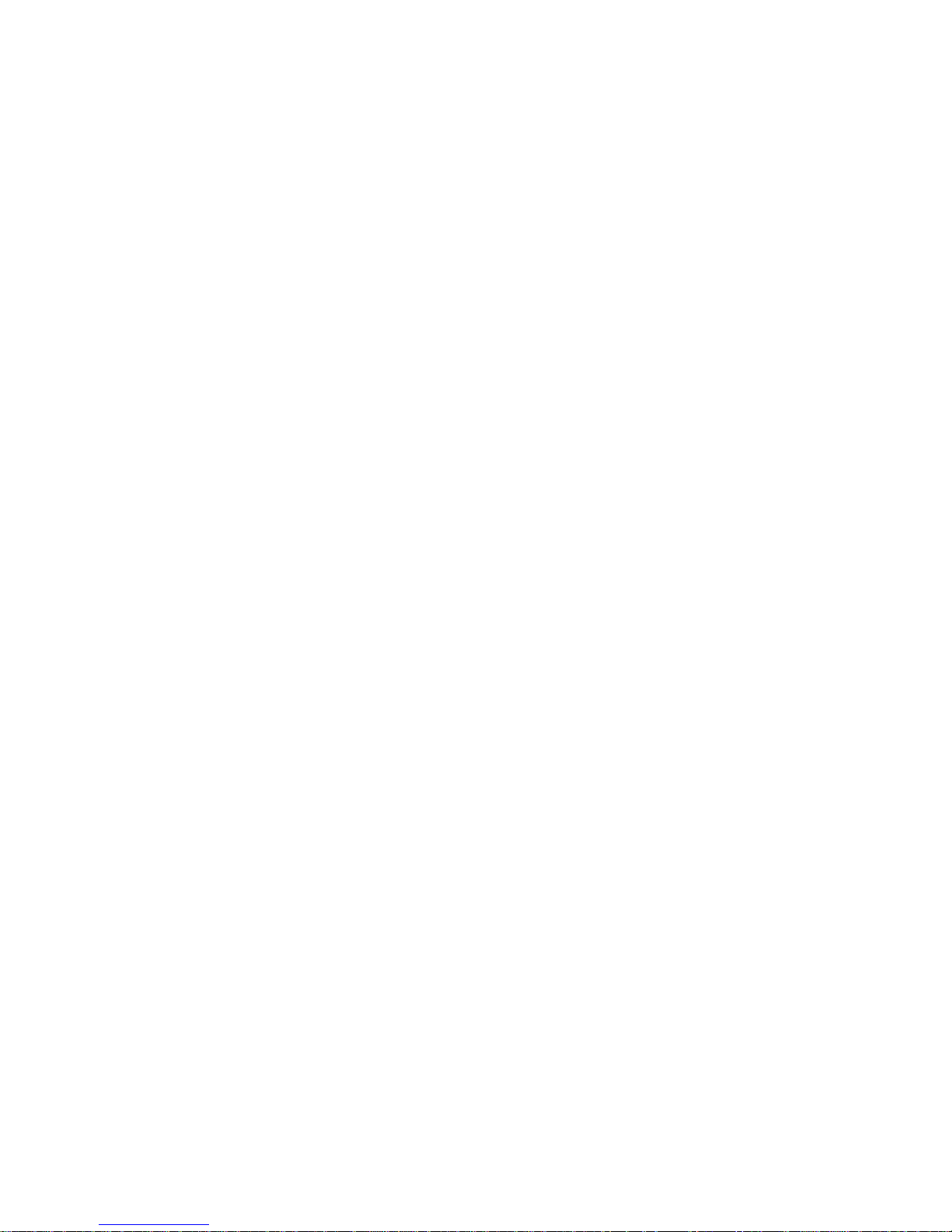
Mainten ance and Theo
ry
Table
Maintenance
Lubrication
Engine Theory
C
arburetor
Ignition
Electrical System Theory of Operati on 2ÂCharging and Ins
Co
nverter Sys
Chaincase and Gear ing Oper ation
Trac
k,
Suspension and Steering
tem
Sys
Engine Inspection . . . . . . . . . . . . . . . . . . . . .
Crankc ase Press
Engine Ge
Compression Check
Fuel System . . . . . . . . . . . . . . . . . . . . . . . . . . . . 2-
Carburetor
Fuel Filters
Fuel Pump
Fuel Pump Pre ssure Test . . . .
Fuel Pump
Primer
Fuel Tank &
Throttl e Cable
Oil Pump
Synchroni
Enrichener
Ignition
Ignition
Ig
nition
Cleaning , In spe
Gapping th e Spark
Oil Inj ec
Oil Inj ection System
Bleedin g . . ................ .
Oil Pump
Elec
tric
al Syst em .......
Key S
Headlight
Bulb Replaceme
Ta
illBr
Speedo
Voltage
C
onverter
C
onverter
Without
PIN
Converter Center Distance
Without
PIN
Chart
Chart
The
System Theory
tem
Operation ....
ar
Pump .
to
Carburetor
zation . . . .
Cable
Sys
tem
Timing Check
Timing
tion
Sys
Outl
witch
Adjustment
ake Lig
meter
Reg
Alignm
Offset
Special Tool
5
7001-3503
Speci al Tool
57001 -
.............
..............
of
Operation
ory
of
trument
Theory
ur
case
Adjustments
........
........
Output
.............
Liner ...........
Adjustment .......
Adjustment
..
. . . . . .
Adjustment ....
ction
tem ..........
et Tube Purgin g . .. . . . 2-42
......
nt
ht .......
. .
...
ulation .... ........
ent
........
Alignment
3503
.
.. ..
. ....
. . .
....
. . . . 2-4
.....
......
. . .
Operation . ....... . 2-13
of
Operat ion .... 2-23
Circ
uit
s .... . . . 2-
of
Operation . .
...
....
....
..
. . . . . . . . . . . 2-32
..
e Test . . . . . . . . . . . .
......
.........
.......
....
. .
......... . . . 2-
........
.
......
. . . . . . . . . . . . . . . .
Test
..
and
Plug ... . . . .
....
.. ..
........
.....
............
.......
. .
......
. .
.......... ..
......
..
.......
. . . . . . . . . . .. .
.. .....
............. 2-
....
.. ..
. . . .
...... 2-37
. .
...
. . .
...........
.......
. .
...
. . ....
...
. . .
...
. .......
. .
.........
......
........
...
.......
. .... . . 2
....... ..
......
..
........ . 2-
..
....
. 2-
.. 2-36
. . . . . 2-
. . . . . 2-
....
2-37
...
. 2-
2-38
. ....
...
. . . . . 2-42
...
.. 2-39
. . .
....
..
. 2-43
. 2Â. . 2Â. . 2-
. 2-
2-39
2-39
2-40
2-41
2-41
2-45
2-45
of
2-3
2-5
24
27
2-30
2-
32
2-34
2-3
4
34
2-35
35
2-35
36
36
37
37
43
43
44
44
44
-44
46
Cont
Suspension
Track
Storage . . .
ents
Jackshaft
immi
Sh
Conve
Tool
Converter
Special Tool PI N 57001-3503 ... ..
Converter
Special Tool PI N 57001
Converter
Be
lt ... .
Converter
Brake
Brake
Brake Pad
Chain Tension . . . . .
Gear Ratio
Steering Sys
Ski
S
ki
Sk i Spring Preload .....
Ride
Handling
Sw
ing
Adjustments
Track Tension
Track
Preparation
Removal
Carburetor
ng . ......
rt
er
PI N 57001 -3503
............. . . . .
..
. . . . . .....
Adjustment .....
Chart
tem
Alignment
Skeg . .... . ....... ....
Adjustments .........
Adjustment
Adjustment
Arm
Al
ignment ......
.......
from
Bearing Retaine r
. . .
....
Ali
gnme
nt Using Special
........
Center Dis
Offs
et
Parallelism . . . . . . .
Lubricat
Wear
...................
Adjustment .......
for
Storage .....
Synchron
tanc
e Using
Alignment
-3503
.. .. .. .. ..
ion ... . .
. . . . . . .......... . .
.....
Inspecti on .
............
...
. . . ..
.. .....
. .... . .
. . .
Adjustment ...
.............
Storage . .
.......
........
. . . . .. . . .. . .
.....
.................
. . .
...
...
izati on . . .... .... .
..........
...
Using
....
...
. .
...
....
. . . . . . .
.. ..
. . . .....
...
. . .
...
. .
...
.. ..
. . . .
. . . . .
. ....
...
...
. . . .
...
. .
.. .....
...
....
. . .
....
. . . .
...
...
....... .
...
. . .
. .
....
. . . .
. .... . . . .
. . .
......
..
..
..
. .
. .
. .
. .
.
.
.
.
.
.
.
.
.
.
.
.
.
.
2-
47
2-47
2-
47
2-49
2-49
2-
50
2-51
2-52
2-52
2-53
2
-53
2
-54
2-
55
2-
55
2-
56
2-
56
2-
56
2-56
2-
56
2-5
7
2-57
2-58
2-
58
2-
59
2-59
2-60
2-
61
;1
TABLE
OF
CONTENTS
2-1
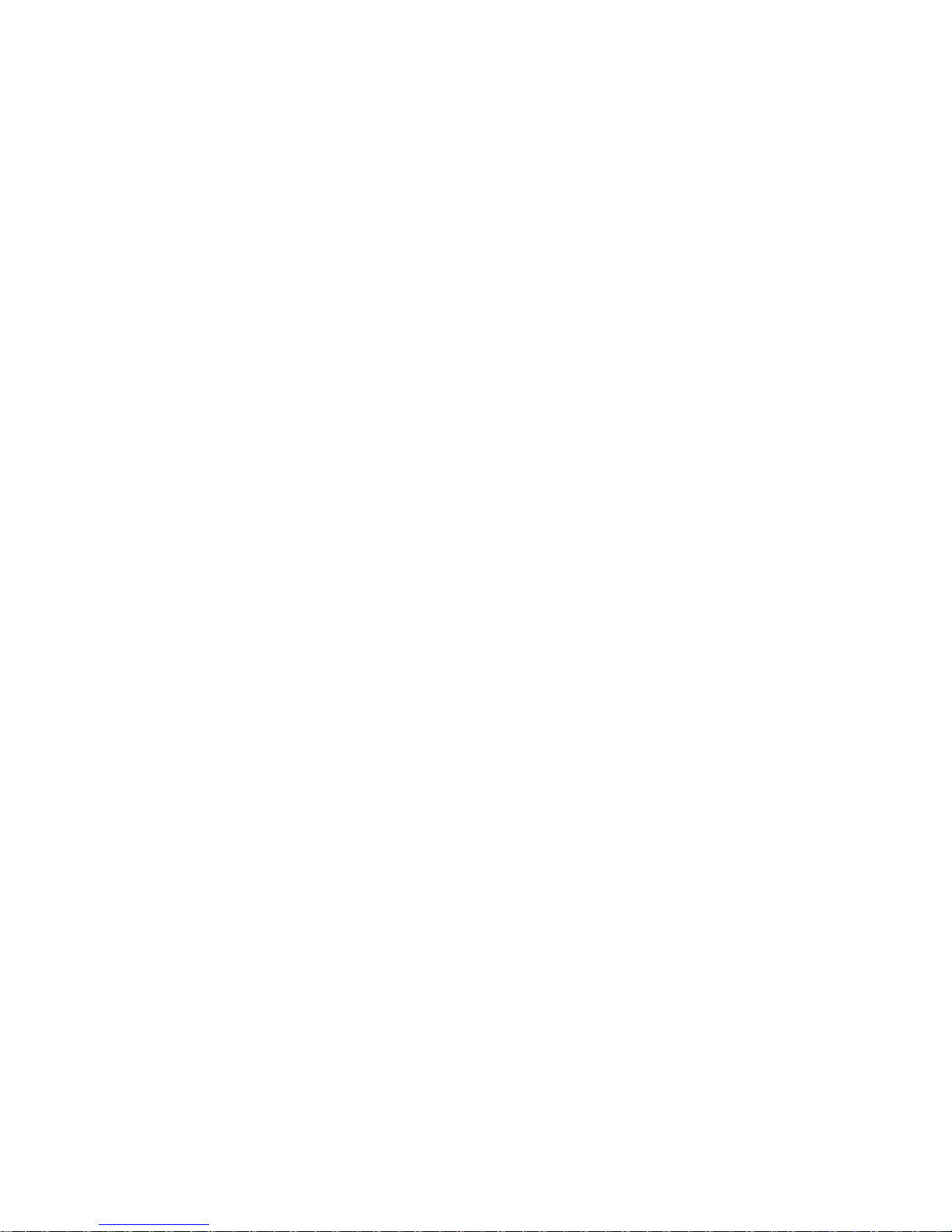
Maintenance Chart
Frequency
Operation
Install
Check
adjustment
Check
adjustment
Check
adjustment
Replace
fuel
Check
Replace drive
sure converter sheaves
are clean and dry)
Check drive
and
alignment
new
carburetor
throttle
enrichener
in-line
filter
ignition
driven
spark
converter
plugs
cable x x
cable x x
timing
belt
(be
converter
Every
480
or
Hours
km
20
Use
Every
960
or
Hours
km
40
Use
x
Beginning
of
Each
Season
x
First
80-160
or
5-10
Hours
km
Use
x x
x
x
x
x x
Every
1450
or
Hours
60
x
x
x
km
Use
End
of
Each
Season
Page
Refer-
ence
2-41
2-35
2-37
2-39
2-
36
2-39
2-50
2-45
Check drive
bushings
Clean and inspect
drive and
converters
Check drive
tensioner
Adjust
and check
Check ski
Check
Check
security
chart
as a guide)
Inspect ski skegs x
for
wear
Measure
rail
wear
Adjust
converter
for
wear
driven
chain
guides
track
tension
alignment
alignment
brake
adjustment
fasteners
(use
torque
wear
strips
headlight
of
for
slide
x
x x x
x x
x
x
x
x
x
x
x
x
x
x
3-95
3-96
3-103
2-53
2-58
2-55
2-52
1-9
2-56
3-117
2-43
Check fan
Check battery
electrolyte level
belt
tension
x
x
MAINTENANCE
x
x
CHART
3-67
2-24
2-3
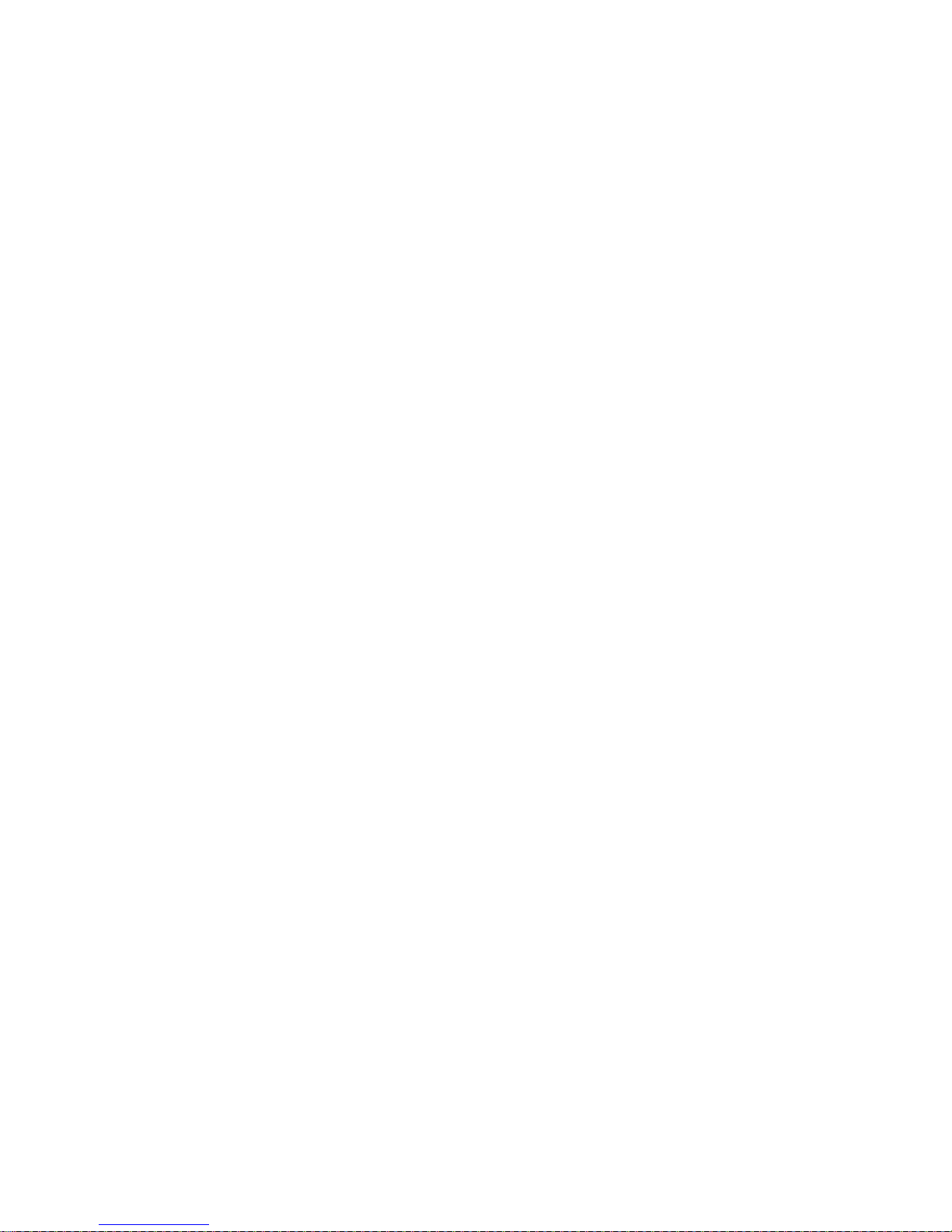
Lubrication
Lubrication
Point Lubricant
Chart
Frequency
Illustration
CONTROL CABLES
Inner
cabl~s
CHAINCASE
HOUSING
LPS, WD-40
Dri-Slide or
s
imil
ar l
temperature
ca
lubri
DEXRON
automat
transm
fluid.
Level should be
above center
si
ght
glass
higher
ow
nt.
ic
issi
than
,
II
on
of
but
the
not
top .
Once a season
and ev
of
Check level every
20
operation.
ery
20 hours
operation.
hours
of
ENGINE
CASE OIL
LEVEL
2-4
GEAR-
LUBRICATION
KAWASAKI
GEARCASE OIL
or 10W-40 motor
that
oil
or
exceeds API
service
ifications,
as
Shell
AND
ICE
Level
should
be above
center
sight
glass
but
not
higher
the
top.
CHART
meets
SE
FIRE
.
of
than
ENGINE
spec-
such
Change
100
Check every
mi
of
Drain and r
at end
each season.
les
use.
after
miles.
or
20 hours
of
ef
initial
300
ill
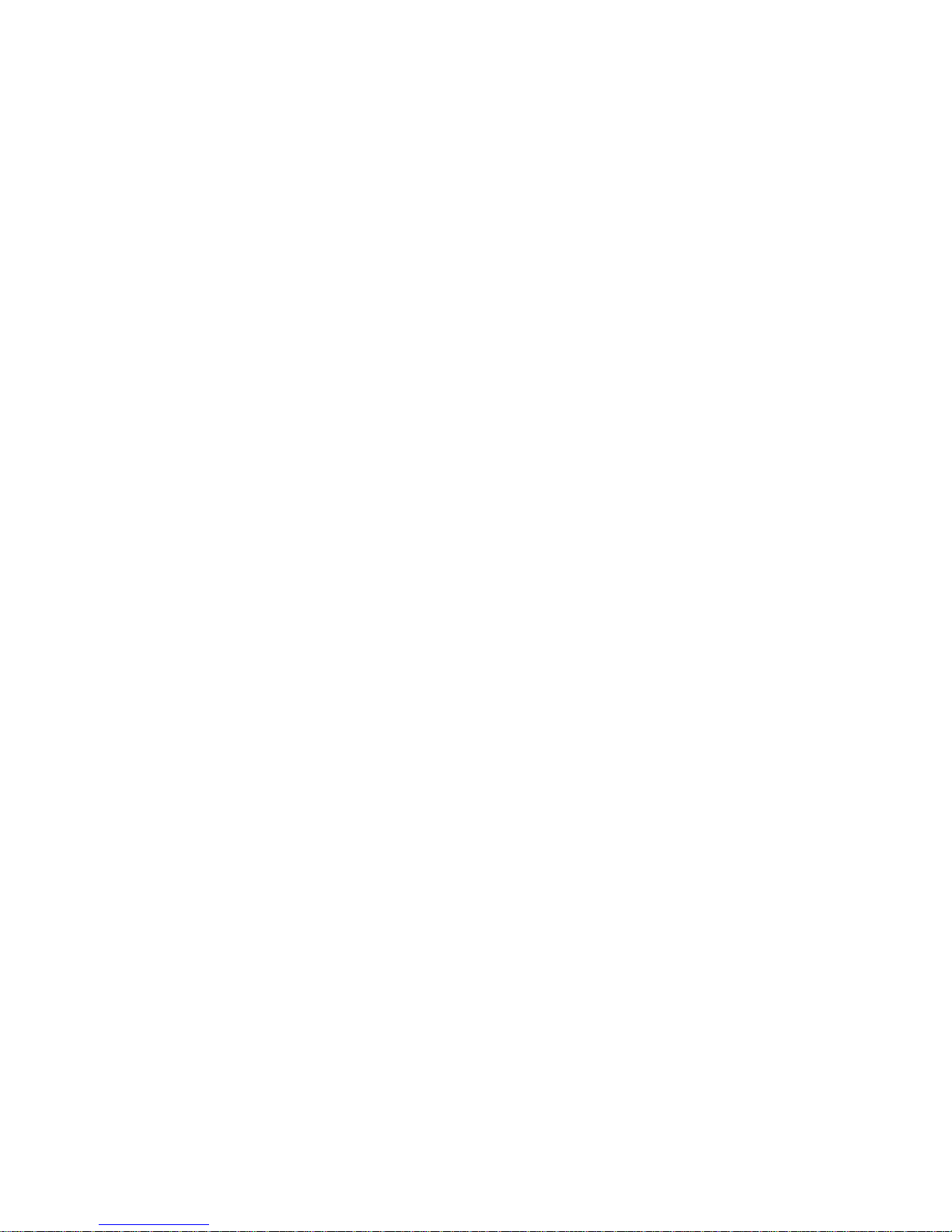
Engine Theory
Introduction
Engines
All
internal
by a four
are: 1. Intake, 2.
and
4. Exhaust.
fuel/air
A
compressed,
A
two-stroke
complish
Each
following
the
engine
1. Intake:
of
through
2.
Compression: Near
stroke,
starts
fuel/air
volume.
part
mixture
all
of
the
the
. (See
On
fuel mixed
the
back up.
to
combustion
cycle
Compression,
must
burned,
engine
four
four
path
the
an
intake
mixture
uses
parts.
parts
of
Figure
upstroke
with
open
port
port
This
to a fraction
Two-Stroke
of
and
can
the
air
the
of
engines
operation.
be
drawn
exhausted.
only
two
be
easily
fuel/air
2-1.)
of
the
is
drawn
in
the
bottom
is closed,
upstroke
Operation
are
characterized
The
four
parts
3.
Combustion,
into
the
engine
strokes
understood
mixture
piston a charge
into
cylinder
and
compresses
of
of
the
.
the
the
its
through
engine
former
to
ac-
by
down-
piston
the
,
3.
Combustion: When
pressed,
down.
4. Exhaust:
gases
and
The
piston
power
the
crankshaft
The
most
air
have
into
the
cylinder
the
lower
effectively
drawing
piston
presses
55°-60
upper
inder
mixture
through
This
exit
the
cycle is ready
is
stroke
intake
the
of a two-stroke
complex
been
crankcase.
wall
edge
increases
in
the
blocks
the
° BBDC (before
edge
of
wall
that
in
the
these
it
is i
gnited
is
called
After
mixture
the
through
carried
to
the
.
part
of
mixed
(the
of
mixture
the
intake
the
piston
are
connected
crankcase,
transfer
the
power
the
through
next
the
in
the
As
the
intake
the
the
in
bottom
ports
mixture
and
the
power
stroke,
now
open
to
start
each
by
the
engine
cycle.
carburetor,
piston
port)
piston.
volume
. On its
port
the
crankcase. At
uncovers
to
the
under
into
the
has
been
forces
rotating
After
The risin g
of
and
dead
pressure,
the
stroke
the
exhaust
again
step
is
perhaps
the
it
rises, a
is
uncovered
the
crankcase,
return
lightly
center),
ports
in
crankcase
cylinder.
com-
piston
.
burned
port,
.
from
inertia
fuel
is
drawn
hole
piston
trip,
com-
about
the
. The
rushes
one
of
the
and
in
by
the
the
cyl-
o
Figure 2-1
o
ENGINE
THEORY
OF
OPERATION
o
2-5
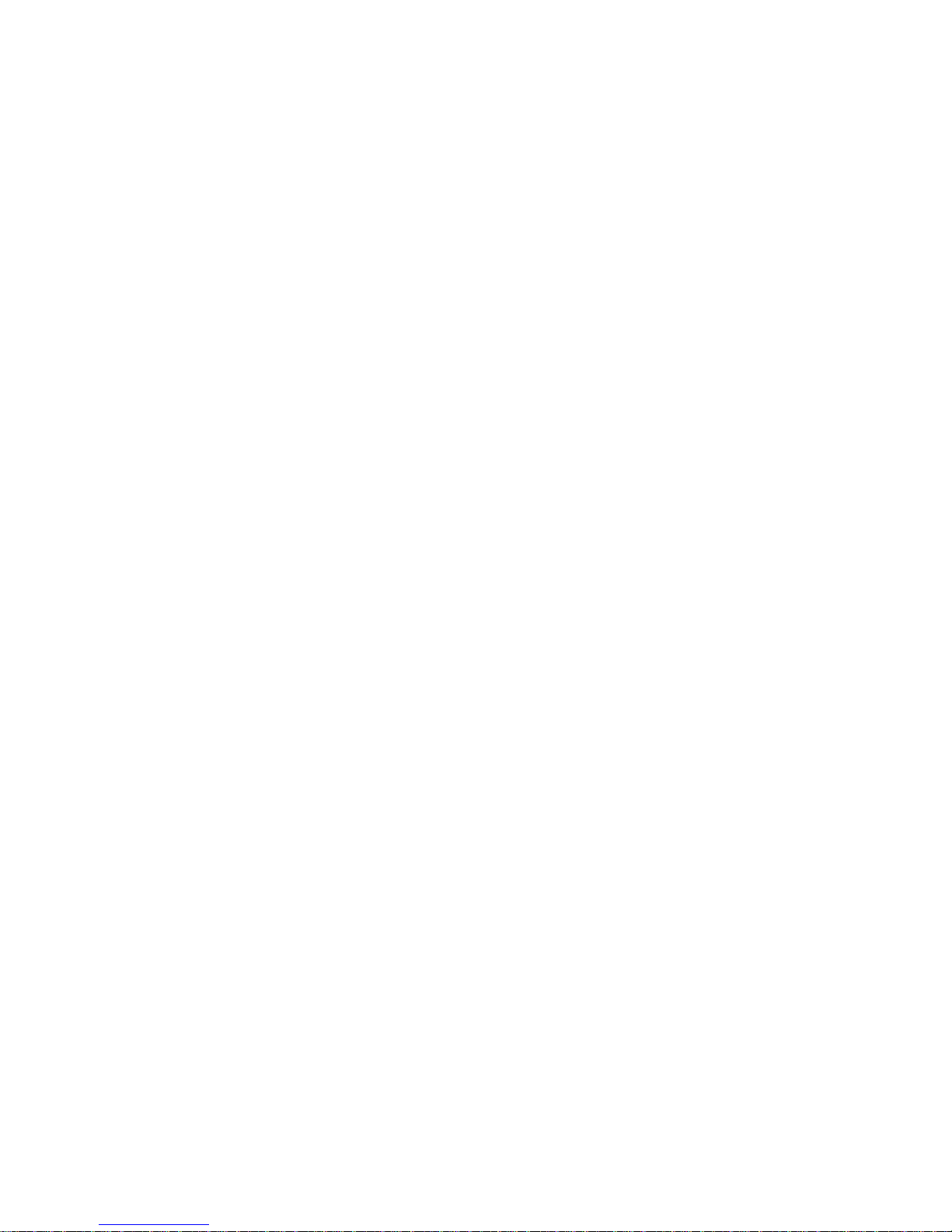
There are
the
crankcase,
two
-stroke
is called
fer
used because
inder
combustion
enging" the
After
rises, closing
opening
above
two
separate
and
terminology,
the
intake;
or scavenging
the
helps
to
chamber
exhaust.
the
piston
passes BDC (bottom dead center)
the
the
intake again. The
the
piston
the
the
flow.
new
clean
transfer
is
compressed
TDC (top dead center),
the
mixture
The
piston
until
the
edge of
through
the
piston, and one
starts
is
driven
exhaust
the
piston
all
four
burning
downward
port
. The
basic
crankshaft.
Intake
A
two-stroke
carburetor.
To
get
the
be an
etor
opening
bore . The
opens and closes
either side
fuel/air
The
and
takes a certain
engine
mixture
from
intake
of
TDC. (See
mixture
's
into
the
amount
intake
second
only
actions: the
into
the
second is called
The
word
mixture
the
. This is
flowing
exhaust
and
known
exhaust
as
the
spark
.
by
is
uncovered
two-stroke
parts
in
just
complete
intake
the
timing
same
tract
the
crankcase,
crankcase
is "
number
Figure
in
the
intake
of
time
first
the
cylinder
first
intake
the
"scavenge"
into
the
out
as
ports
mixture
the
plug
the
trapped
piston
is
fired
combustion
by
the
engine
two
strokes
rotation
starts
with
there
to
the
symmetrical,"
of
degrees
2-2.)
tract
has
to
get
into
into
. In
action
trans
is
cyl-
of
the
"scav-
, and
nears
and
upper
goes
of
of
the
the
must
carbur-
on
inertia,
the
it
it
crankcase. The
more
time
crankcase. If
-
crankcase
mospheric
direction
. The
600 ABDC,
would
BTDC,
seem ideal
just
on a piston
intake
and
the
the
to
all
the
mixture
open intake.
sooner
there
the
pressure
and
the
transfers
which
after
the
port
remain
crankcase
to
the
is
to
intake
mixture
is
the
to
open
transfer
engine
open
cylinder
the
intake
draw
the
is
opened
will
be
will
generally
same
the
intake
ports
this
until
1150 ATDe
pressure
would
is opened,
mixture
higher
flow
close
as
into
too
soon,
than
in
the
at
1200 BTDC. It
at
about
close . However,
would
require
as
meant
be
to
lost
transfer
back
the
the
the
at-
wrong
around
115
the
well
out
0
,
Transfer
Transfer
mixture
scavenge
the
exhaust
direction
exhaust
transfer
such a way
inder,
haust
The size
portant
small ,
port
of
the
scavenging. The
crankcase vol
lower
from
exhaust
. As
will
ports
pushing
port.
for
the
is
too
inertia
flow
the
ports are
the
the
exhaust
port
opens before
gases are
the
pressure
no
longer
aim
that
it
the
and
shape
efficient
transfer
large,
the
of
the
gases
after
it leaves
transfer
ume
crankcase
designed
crankcase
from
already
in
flow
the
incoming
will
sweep
exhaust
of
the
scavenging
flow
will
flow
speed
will
the
port
. The
larger
pressure
to
move
to
the
cylinder,
the
cylinder.
the
transfers
traveling
the
cylinder
of
its
own
fuel/air
throughout
gases
toward
transfer
. If
be
restricted
will
affect
port,
the
resulting
passage is
the
.
the
fuel/air
and
Because
do,
in
the
drops,
accord. The
mixture
the
the
ports
are
they
are
. If
drop
. The lack
direction
in poor
part
passage,
right
of
to
the
the
in
cyl-
ex-
im-
too
the
of
the
the
TYPICAL
0
89
ABDC
2-6
ENGINE
PISTON
TDC
BDC
Figure
THEORY
VALVE
ENGINE
2-2
OF OPERATION
76°
89°
ATDC
BBDC
Timing
of
the
transfer
ports
runs
BBDC to about 600 ABDC. The
cannot
haust
mix
less
symmetrical
transfer
open
into
open
would
the
new
power
port
too
the
crankcase .
(or
about
long,
until
after
flow
charge
none
is
important
some
the
into
the
and
the
at
all).
BDC . The
to
of
the
exhaust
crankcase. This
exhaust,
Transfer
closing
good
mixture
Compression
Compression occurs as
closes
presses
fraction
pression of
mechanically
the
the
of
its
intake and
fuel/air
original
any
sealed .
mixture
kind,
the
piston
exhaust
volume
the
in
. To
from
transfer
does
port
cylinder
will
on
ports
the
cylinder
achieve
cylinder
about
or
the
resulting
timing
point
of
filling.
flow
its
upstroke
and
must
60
ports
ex-
would
in
is
the
back
com-
to
a
com-
be
0
If

The
cylinder
from
the
tween
both compression and
gasket
standing
head gaskets are
aluminum.
asbestos sheets. The head
to
just
leaking.
The piston is a close
the
special cast iron
grooves and press
wall
bustion
withstand
without
down
Most
piston
the
the
."
the
the
final
to
on the
engines
rings. Their job is
piston and cylinder.
head,
cylinder itself. The
he'3d
This gasket
high
Others
cylinder, squeezing
right
seal is made by piston
prevent
past
high
deforming
cylinder
have one or
in
most
and
the
combustion
must
temperatures
simply a sheet
are a
amount
fit
rings which circle
outward
leakage
the
piston. The piston rings
temperatures
while
wall.
engines,
joining
cylinder
be capable
and pressures.
sandwich
must
be fastened
the
head gasket
of
force
in
the
cylinder
against
of
compression
rubbing
two
to
constantly
compression
seal
the
is
surface
is sealed
by
the
of
copper
of
copper and
to
keep
rings
. These are
the
the
and
pressures
gap
separate
be-
against
"head
of
with
Some
or
tightly
with
it
from
bore,
but
piston in
cylinder
or
comÂmust
up and
sealing
between
-
FLAT
RINGS
The compression ratio
different
from
displacement
two-stroke
SDC
second
engine in Figure
displacement
method
KEYSTONE
Figure
ways
. The
to
above
engines
can
entire
TDC
may
the
are
. As an example,
2-4 with a 60
be
figured
RINGS
2-3
may
be
cylinder
be used, or
exhaust
generally
as
"DYKES"
RING
measured in
displacement
just
port. Kawasaki
rated by
imagine
mm
stroke . Its
shown.
two
the
the
the
New
piston
rings do
the
cylinder
This
initial
The cross-section
its design. Rings having a
section are
type
of
has a wedge-shaped
3). This type
its groove has
ring and its groove are designed
outward
bustion
should
sometimes
should always
manufacturer's
A
third
This
ring
piston. It is placed
so
that
the
edge
i nder
wall
cylinder
combustion
of
the
cylinder
rings
not
conform
wall,
wear
called
ring
has
of
against
stroke for
not
be
also have a "
type
of
is
usually
one
side
slightly
duri
wall
twisting
stroke
upper leg
wall
for
must
be
"broken in." The
exactly
but
is
the
of
a ring is an
"flat"
parallel
cross-section . (See Figure 2-
ring
called a
nonparallel walls
the
cylinder
better
installed
be
installed
instructions.
ring
is
used alone on a
at
the
of
the
. The ring is forced
ng
the
the
the
of
the
a good seal.
to
they
gradually
break-in
rings
. The groove
walls. Another
"key-stone"
wall
sealing
upside
top"
carefully
the
"Dykes"
upper
"L"
shape
upstroke by
ring
outward. During
gas pressure on
"L"
forces
tiny
irregularities
wear
to fit.
period.
important
rectangular
. The shape
to
force
during
. Key-stone rings
down.
and
"bottom"
following
edge
of
protrudes
against
the
it
out
part
cross-
for
type
of
ring and
of
the
the
Flat rings
pattern
single-ring
the
piston,
above
the
drag
of
the
inside
against
com-
ring.
new
of
of
this
ring
the
ring
and
the
cyl-
the
the
the
o
Figure
2-4
BORE = 60
STROKE = 60
mm
mm
ENGINE
THEORY
OF
OPERATION
2-7
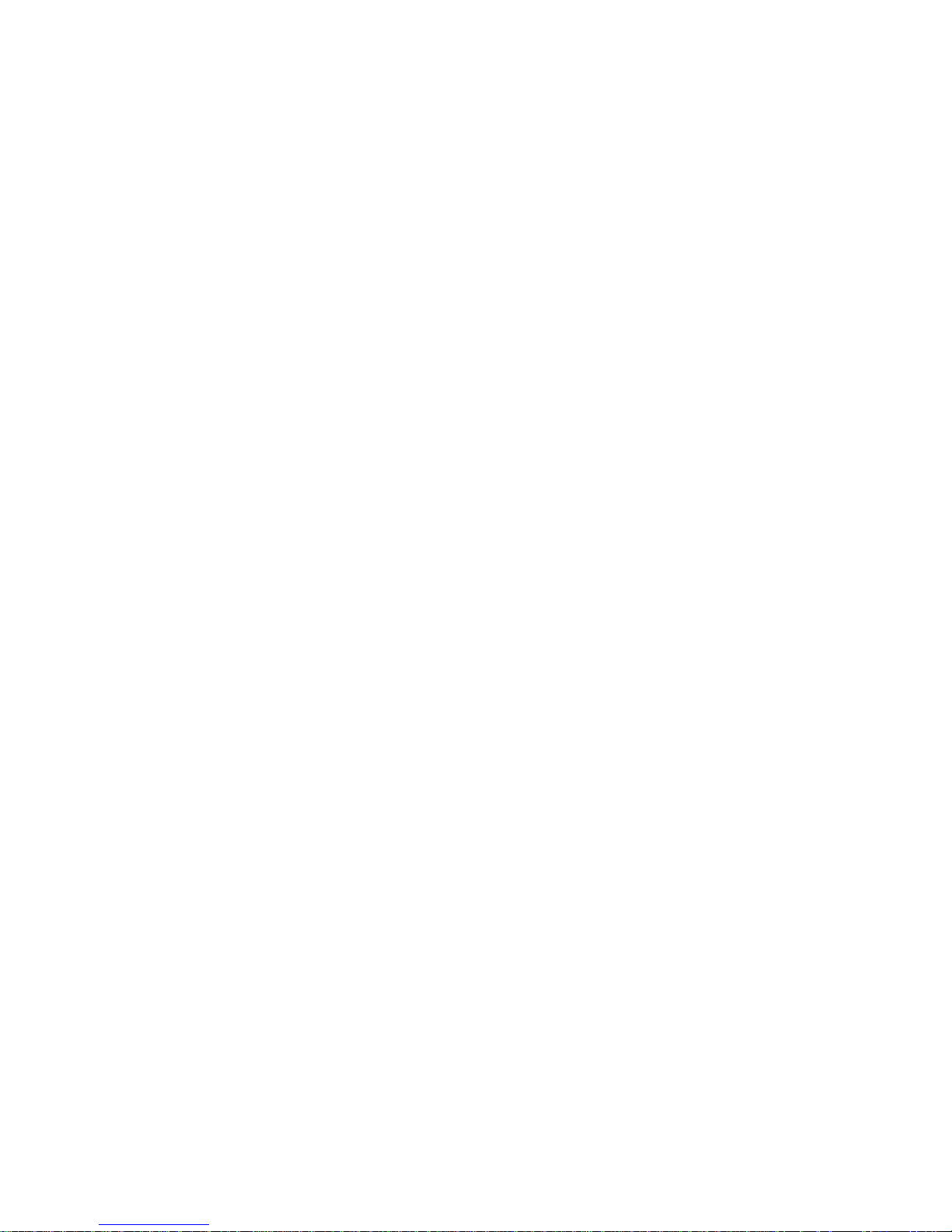
2
V=m
WHERE:
V
r = 112 bore - 30
h = stroke -
17
V = (3
V
If
ume
can
h
=
displacement
60
= 3.
1416
.1416
) (9) (6)
=
169.6
the
be
cc or approximately
engine has a total
of
20
cc
at TDC,
figured.
mm
Vl + V2
R=---
volume
mm
or 3 em
or
then
6 em
170
combustion
the
compression ratio
cc
chamber
vol-
The compression ratio
sure of the
compression ratio,
will
use its fuel, up to a
with a high
horsepower
of gas
low
er
further
The
burned,
more heat
more expansion
that
means more
fuel used and
efficiency
the
compression ratio
for its size and go
than
an
otherwise
compression ratio.
the
mixture
the
hotter
will
the
be produced.
of
the
horsepower
the
engine
Combustion
of
an
engine
of
the
engine.
more
efficiently
certain
further
identical
is compressed before
combustion
Greater
combustion
for
size.
is one
The
point.
will
put
engine
will
heat
products, and
the
higher
the
engine
An
engine
out
on a
with
be and
means
amount
mea-
the
more
gallon
a
it
is
the
of
WHERE:
R
= compression
V =
displacement
V
=
volume
170 + 20
R=---
20
at
TDC -20
-
R = 9.5
This is
However,
cylinder
of
look like these.
V
WHERE:
V
r
h = distance
17
V = (3.1416)
V
called the
if
we
at
the
closing
at BDC,
=1Tr
=
displacement
= 112 bore -
top
=
3.1416
the
2
h
from
of
exhaust port -
compression ratio
30
(3)2
= 113.1 cc or about
V1 + V2
R=--
-
113 + 20
R=----
20
R = 6.7
This is
ratio, and is
compressi on ratio.
usually
always
ratio
volume -170
cc
"th
eoretical"
measure
volume
mm
top
(4)
called the
the
of
the
above
or
of
cylinder
40
113
lower
3 cm
cc
compression ratio.
total
volume
exhaust
mm
cc
"actual
than
port instead
calculations
exhaust
to
or
port
4 cm
" compression
the
theoretical
of
the
might
Combustion
trodes
The spark
voltage
instant.
will
try
power
ignite
the
6500
revolutions
for
this
so
that
TDC
at
When
that
is
mixture
front"
flame
across
speed.
common
flame
defines
detonation.
front
burning
Normal
bustions
hard,
the
an even
related
The
standard
the
to a laboratory
ability
two
produce
adding
petroleum
makes
detonation
metallic,
front
mixture
"o
octane,
petroleum
is
of
a spark
plug
electricity
If
the
to
run
stroke
mixture
lead is
peak
cylinder
high
the
spark
between
ignites
travels
moves
the
mixture
combustion
the
combustion
There
and
is
detonation.
travels
resulting
burning
to
the
ctane"
that
set
the
Octane
to
resist
gasoline
tetra-ethyl
distillates
it
burn
.
started
ignition
backward;
will
to
speeds.
the
across
are several
all
hammering
octane
of a gasoline
gasoline's
of
procedure
detonation
by a
plug
in
receives a
to
ignite
comes
be lost. The
at
18°
per
minute
start
the
pressures
plug
fires,
its
mixture
the
across
as
is a
are
almost
in an
of
the
of
laboratory
more
resistant
ratings
distillate
to
meet
of
lead
. The
more
spark
across
the
combustion
timed
the
too
before
mixture
it
electrodes.
around
combustion
the
it
goes.
single
chamber
types
undesirable.
Detonation
from
instantaneously
explosion
mixture.
the
burning
conditions.
are
which
to
fuels
octane
or
"lead"
slowly,
surge
mixture
too
soon
late and
ignition
top
and
up). The reason
burning
will
occur
ignites
it,
combustion
flame
at
of
abnormal
the
gasoline
is a
speed
the
assigned
compares a fuel's
that
of a mixture
. Oil
requirements
certain
in
the
chamber.
of
at
the
the
engine
part
of
is
timed
dead
center
in
just
the
mixture
That
front
sounds
Detonation
number
gasoline
thus
burning
and a "flame
chamber.
chamber,
traveling
just
the
The
like a
engine
used.
the
. The
through
rather
which
under
The
high
according
companies
high-octane
gasoline
avoiding
elec -
high-
right
the
(at
time
after
The
right
com
most
than
er
is
by
to
-
is
a
to
of
2-8
ENGINE
THEORY
OF
OPERATION
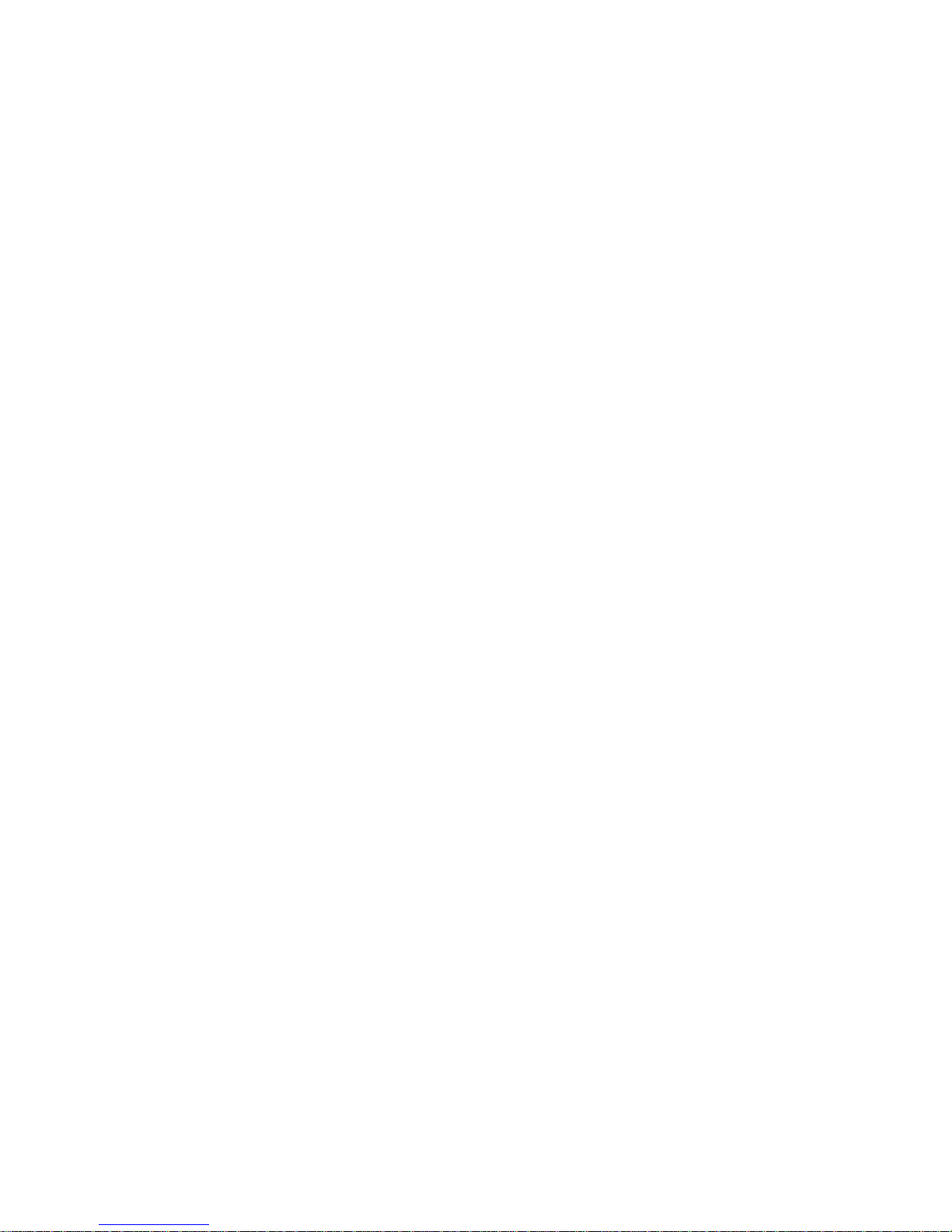
When
place. The
molecules
carbon-diox
the mixture
molecules
of
!he
ide,
water,
burns, a
of
air
to
traces
chemical reaction
fuel
comb ine
produce
carbon-monoxide,
of
other
pounds, and heat. Heat is absorbed by
and
combustion
engine
bustion
them
th
The shape
a
chamber
more
is wasted,
products increases
to expand. This expansion is what
e actual
power
of
factor
in its
with
res
istant
induce mixture
tion
resistant;
per
unit
of
Smoot
hly
surfaced
designed.
having a
bustion
top of
squirt
chamber
Mixture
squish
chamber roof
the
piston (at
out
roof as
with the lowest
the
sphere.
be a smoothly
with
a squis h area
allows
a
smooth
chamber, especially
products
but
heat
in
the
the
engine's combustion
ability
few
projections
to
resist
to detonation. Ch
turbulenc
and
volume
e are more
chamb
detonate less than
combustion
turbulence
area :
that
that
TDC), causing
from
the
surface
An
ideal
finished,
between
piston
area
combustion
almost
around
scavenging
when
. Heat absorbed by
that
goes
their
pressure,
engine.
detonation. A smooth
and
irregularities
highly
ers
with
less surface area
chambers
can be induced by
is a
part
comes very close
the
the
piston and
nears TDC. The shape
per
unit
chamber
sphe rical
the
edge. This design
flow
scavenging
lowest.
takes
with
oxygen
various com-
the
engine
the
into
the
com-
forcing
produces
chamber
is
is
ambers that
detona-
others
.
are
easily
of
the
com-
to
the
mixture
to
the
of
volume
is
would
chamber,
across
flow
the
is
Another
design
should
so
the
to
travel
plug
front
center,
far
.
Part
mined
bottom
piston
st
rengthen its
center
and
As
the
consideration
is
spark
be
placed
flame
to reach
is on
of
has
the
by
one
to
flame
the
combustion
the
of the
is
generally shaped
to
take
rai se
the
piston
the connecting
around
cylinder
piston's
inder
during
off-set.
crankp
of
inder
the
of
its
circle,
and
being
wall
during
compression. The
in
the
in travel
the
piston's
wall.
The
crankpin
does, and
combustion
plug
placement.
near the
front
will
all
po in
edge
of the
travel
all
front only
top
of
the
chamber
center.
up
Some
space
compression
is
forced
rod
downward,
increases.
away
then
back again.
thrust
against one side
combustion,
direction
near
TDC.
sideways
piston
reach es TDC
piston "sla
is
minimized
--~
..
~
.
in
combustion
The
have
ts
center
of the
of
the
the shortest distance
chamber.
chamber,
the
way
across. From
has
to
travel
chamber
pi s
at
in
the
shape
ton.
It beco
TDC. The
in a
gentle
pistons
have a raised
combustion
ratio.
the
The
crankpin
from the
centerline
This
results
and the
piston
opposite
pin
bore
the
This lessens
motion
again
slightly
p"
at
1""
.....
. (See F
----
igure
OFFSET
chambe
spark
plug
chamber
If the
the
flame
half
is
deter
mes
top
of
arc
chamber
angularity
move
of
in
of
the
other
is s
lightly
direction
the
impa
st
the
before
the
instant
2-5.)
the
as
the
the
to
of
the
the
cyl
side
of
ct
cyl-
r
-
s
-
Compression
high
compression
to
avoid
use a
lower
ratio
ratio
deto
nat ion. A l
octane gasoline.
is
imp
ortant
requires a high
ow
compression
to
combustion
octane
engine
. A
fuel
can
The compression pressure produced by an engine
is a more accurate
detonation than i
pression pressure is
bustion
risi
Another
i
gnition
hot,
on
may
flame
the plug
flame
ignition
will
lead
chamber,
ng
piston.
type of
. If
the
or a fleck
the
head of
be
front
of
ignited before
traveling
fires, its
front
with
creates advanced
soon overheat.
to
ser ious
measure
ts
compression
the
before
of
pressure
ignition,
abnormal combustion
combustion
carbon
the
piston
flame
a small,
chamber
on
the
chamber
heats
the
plug fires. This starts a
across
front
the
meets
sharp
timing
Detonation
engine
damage .
and
its resistance
ratio
. Com-
in
the
com-
produced by
is
pre-
becomes
very
surface
up,
the
mixture
chamber. When
the
preignition
sound
. The pre-
, and
the
engine
preignition
to
the
or
can
Figure
2-5
ENGINE
THEORY
OF
OPERATION
2-9
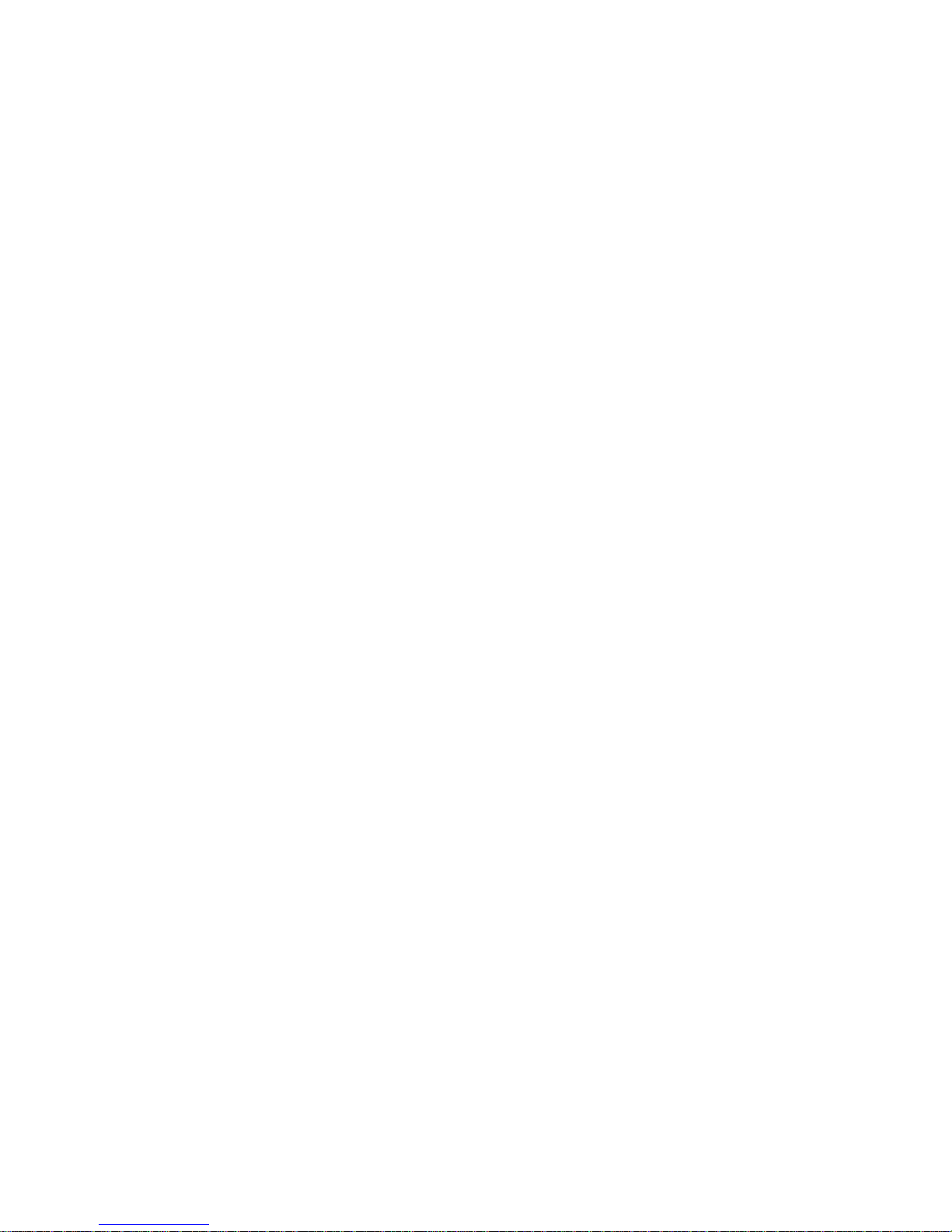
The
piston
drical
only
when
when
pand
evenly
through
and
for
extra
(See Figure
expand
The
wall
greater
motion
across
an elliptical shape.
p
ands
cannot
shape
the
of
the piston
into a cylindrical
the
engine
as
the
strength;
2-6
more
thickness
to
hand
the
or
the
engine
it
head,
.) The
than
le
piston.
pin
be
made
piston
was
was
hot. A
heats up.
the
the
skirt
upper
the
skirt, and
near
the
stresses
The
bores and
As
the
shape and
in a perfectly
would
cold, and
Near
piston
is
part
the
piston will expand
piston
fit
piston
the
walls
thin
to
of
must
piston
of
the
must
heats up,
fits
the
cylinder
not
does
ring
grooves
are
save
weight.
the
piston
be
smaller.
pin
bores is
reciprocating
be
made
the
cylinder
cylin-
fit
well
not
ex-
thicker
will
more
with
it
ex-
The last
into
exhaust port. This forces the gases
right
piston forces the rest
through
The exhaust system consists
exhaust port
haust
exhaust gases quickly and
excessive noise.
.
Engine Crankcase Design
bit
of pressure
the
exhaust system
direction.
the exhaust
manifold, and a
After
through
in
bottom dead center, the rising
of
port
the
the
cylinder
with
the opening
the
.
of
cylinder
muffler.
easily
is released
to
move in
burned
a passage
head,
It removes
while
of
gases
from
an
reducing
the
the
out
the
ex-
the
The
rather
makes
when
Usually
across
about
The
diameter.
(if available)
directions
sured
taper
it
checking
the
the
0.1875
other
not
.
important
This
odd
piston
skirt
half
at
at
each
only
Figure
shape
piston
at
in. (5
of
piston
is
measured
four
for
of
to
know
is
measured
900 to
mm)
different
position
size,
PISTON SHAPE
(EXAGGERATED)
2-6
the
piston
where
to
cylinder
with a micrometer
the
piston
up
from
the
bottom
clearance
with a dial-bore
positions,
. The
but
is
cylinder
for
roundness
when
to
measure
clearances
pin
bores,
edge.
the
cylinder
gauge
and
in
is
mea-
cold
two
and
Theory,
of
the
understood.
The
supports
use ball bearings
These
two
of
race, and
the
which
balls
2-7
The crankcase is designed to
crankshaft. In order
crankshaft, the crankcase is
The crankcase
mating
.
match perfectly. A sealing
rather
Kawasaki
seals
function,
the
engine are important,
lower
crankcase
the
ball beari ngs are very
hardened steel races separated by a caged set
steel balls. The
the
crank turns,
roll on the
from
rubbing
.)
surfaces
than
two-stroke
and cylinder base baskets have to
and design
end
(crankcase)
contains
main
for
crankshaft
crankcase carries
the
outer
against
must
of
a gasket, to
of
the
but
not
functions
the
crankshaft,
bearings.
the
inner
to
be
the
engines
Snowmobile
main
bearings.
strong
is
fitted
the
race rolls on
race. The cage keeps
each other. (See Figure
totally
install
airtight
crankcase halves
and remove
split
and
compound
insure
. The
horizontally.
upper portion
complete
engines
and consist
to
the
outer
race.
the
enclose
oiltight.
is used,
airtightness
crankshaft
be
airtight
until
are
and
of
inner
As
balls
the
the
the
The
must
on
oil
.
Exhaust
Th-e
design
major
The speed
height
useful
exhaust
BBDC. The
The
higher
angle
.
2-10
of
effect
range
of
the
power
port
height
the
ENGINE
the
on
the
of
exhaust
range
opens
exhaust
exhaust
and
of
THEORY
system
characteristics
the
engine
port. Proportionately,
of
the
engine
closes
the
port
port,
OF
and
increases
at
about
determines
the
wider
OPERATION
timing
of
the
decreases. The
the
engine
with
800 to
its
timing.
exhaust
has
the
the
90
a
.
0
Figure
2-7
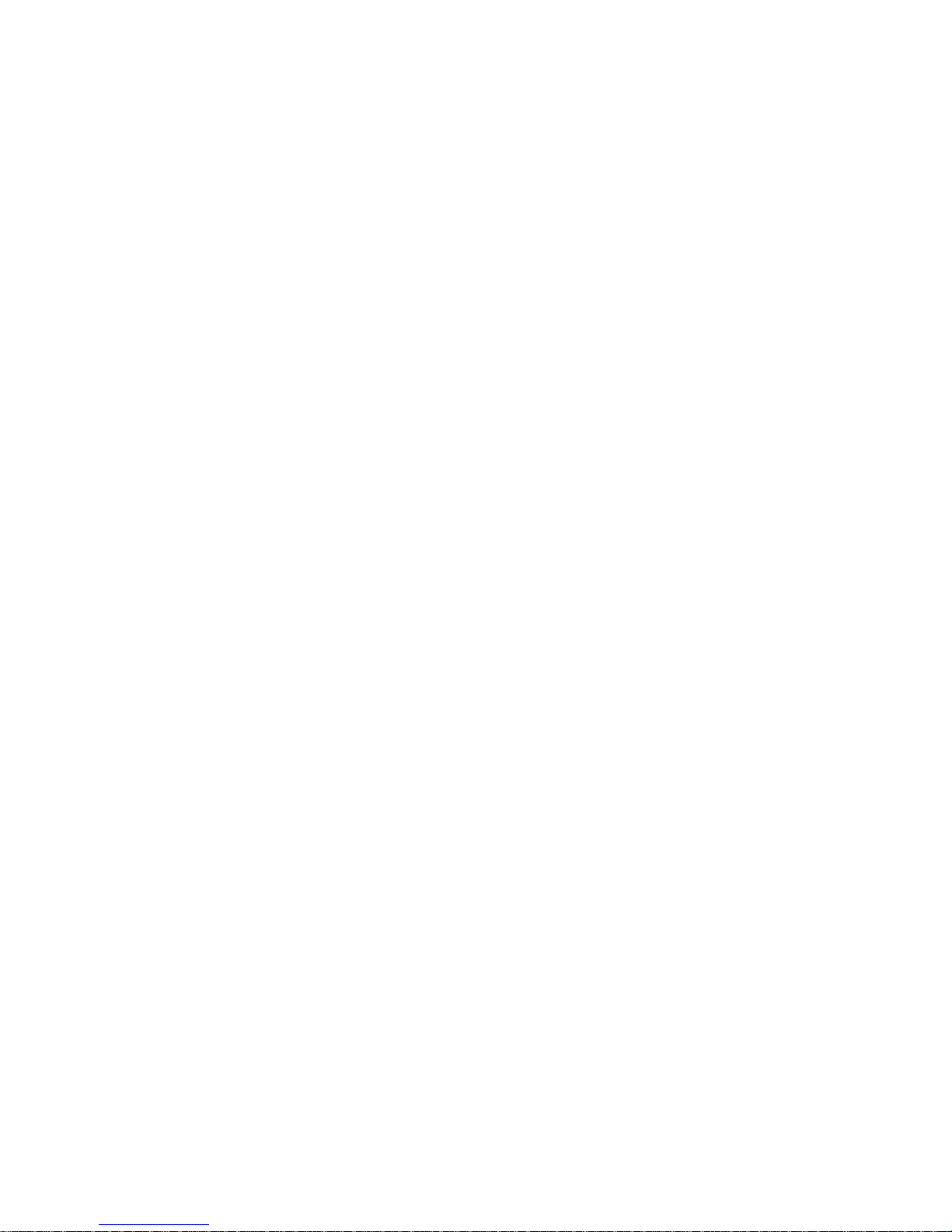
To
achieve
wheels
pletely
the
connecting
space
good
are
designed
as possible.
inside
the
crankcase
rod . There is
crankcase
compression, the
to
fill
the
Between
.
crankcase
the
crankwheels
very
little
crank-
as
com-
wasted
is
CONNECTING ROD
END)
(BIG
CRANKP
IN
crankshaft
The
parts
. A caged
crankpin
the
the
sideways, and
each side
The
misaligned
pressed
perfectly
There
the
Figure
. The
needles
connecting
of
crankshaft
because
together.
aligned
is a
specified
big
end
2-9
.)
@)
RIGHT
WRONG
is pressed
needle
crankpin
roll
on
rod. The
held
the
big end.
can
on
bearing
Figure 2-8
together
bearing
rolls on
the
inside
connecting
by
two
thrust
twist
or
loosen
it
consists
The
crankwheels
the
crankpin.
side and radial
of
the
connecting
from
separate
is used
the
needles,
of
the
large
rod is located
washers,
and
of
separate pieces
must
(See Figure
clearance
rod. (See
on
end
one
become
2-8.)
RIGHTW
WRONG
the
and
of
on
be
for
THRUST
WASHERS
A+B+C+D
= SIDE
E =
RADIAL
Figure
Engine Lubrication
This
snowmobile
cated by a variable
mixture
depending on
When
gets less oil.
Under
Automatic
engine
down
from
the
engine
full
throttle,
oiling
only
as
on visible
engine
pump
about
engine
110
speed and
needs less oil, as at an idle,
the
engine
is economical because
much
oil as
exhaust
E
CLEARANCE
CLEARANCE
2-9
is
automatically
which
to 1 to
it
emissions
may change
about
throttle
will be fed more oil.
it
needs. This also cuts
.
lubri-
the
25
to
opening.
gives
the
1,
it
Figure
2-10
ENGINE
THEORY
OF OPERATION
2-11