
0108.USA
Foreword
Safe operation of the industrial truck requires specialist knowledge, which is acquired
from this Operating Manual, from the training required by OSHA under 29 CFR
1910.178, and by training operators in factory installations and their functions. Safe
operation of the industrial truck requires knowledge that can be acquired from this
ORIGINAL OPERATING MANUAL. The information is set out concisely and in a clear
format. The chapters are organized alphabetically, each starting at page 1. The page
identifier consists of the chapter letter and page number.
For example: Page B2 is the second page of Chapter B.
Various types of industrial trucks are described in this Operating Manual. When
operating the truck and carrying out maintenance work, make certain you use the
description corresponding to your vehicle type.
Safety instructions and important information, and their relative importance, are
indicated by the following safety warning symbols and indicator words:
QwD This message indicates a hazardous situation that, if not avoided, will result
in death or serious injury. The instructions, safety precautions, actions, or
procedures relating to this message must be observed to avoid the risk of
death or serious injury.
QwW This message indicates a hazardous situation that, if not avoided, could
result in death or serious injury. The instructions, safety precautions, actions,
or procedures relating to this message must be observed to avoid the
potential risk of death or serious injury.
QwK This message indicates a situation that may lead to minor or moderate injury
if disregarded. The instructions, safety precautions, actions, or procedures
relating to this message must be observed to avoid the risk of minor or
moderate injury.
IMPORTANT This message appears if special precautionary measures are needed to
ensure that the correct action is taken or to prevent damage to or malfunction
of the industrial truck or a component.
NOTICE This message appears if special information, instructions, or indications are
needed with regard to procedures, equipment, tools, pressures, loads, and
other special data.
t Indicates component fitted as standard.
o Indicates optional extra.
0108.USA
Foreword
Safe operation of the industrial truck requires specialist knowledge, which is acquired
from this Operating Manual, from the training required by OSHA under 29 CFR
1910.178, and by training operators in factory installations and their functions. Safe
operation of the industrial truck requires knowledge that can be acquired from this
ORIGINAL OPERATING MANUAL. The information is set out concisely and in a clear
format. The chapters are organized alphabetically, each starting at page 1. The page
identifier consists of the chapter letter and page number.
For example: Page B2 is the second page of Chapter B.
Various types of industrial trucks are described in this Operating Manual. When
operating the truck and carrying out maintenance work, make certain you use the
description corresponding to your vehicle type.
Safety instructions and important information, and their relative importance, are
indicated by the following safety warning symbols and indicator words:
QwD This message indicates a hazardous situation that, if not avoided, will result
in death or serious injury. The instructions, safety precautions, actions, or
procedures relating to this message must be observed to avoid the risk of
death or serious injury.
QwW This message indicates a hazardous situation that, if not avoided, could
result in death or serious injury. The instructions, safety precautions, actions,
or procedures relating to this message must be observed to avoid the
potential risk of death or serious injury.
QwK This message indicates a situation that may lead to minor or moderate injury
if disregarded. The instructions, safety precautions, actions, or procedures
relating to this message must be observed to avoid the risk of minor or
moderate injury.
IMPORTANT This message appears if special precautionary measures are needed to
ensure that the correct action is taken or to prevent damage to or malfunction
of the industrial truck or a component.
NOTICE This message appears if special information, instructions, or indications are
needed with regard to procedures, equipment, tools, pressures, loads, and
other special data.
t Indicates component fitted as standard.
o Indicates optional extra.

0108.USA
It is impossible for the manufacturer to foresee every possible operational
circumstance that could involve a potential danger. For that reason, the warnings in
this manual and on the equipment itself do not encompass all possible
circumstances. If you use a tool, procedure, working method, or operating technique
not expressly recommended by the manufacturer, you must make sure yourself that
it does not present a safety risk to you or to anyone else. You must also ensure that
the product will not be damaged or made unsafe through operation, lubrication,
maintenance, or the chosen repair measures.
The information, technical data, and illustrations contained in this document are
based on the information available at the time of publication. Specifications, torques,
pressures, measurements, settings, illustrations, and all other data are subject to
change at any time. These changes relate to the performance of the product. Before
executing a task, you should request the most up-to-date and comprehensive
information from the manufacturer / dealer. You can also obtain additional copies of
the manual from your dealer.
In the interests of technical advancement, the manufacturer reserves the right to
make changes, while retaining the essential features of the type of vehicle described,
without correcting this Operating Manual at the same time.
Copyright
Copyright of this operating manual remains with JUNGHEINRICH AG.
Jungheinrich Aktiengesellschaft
Am Stadtrand 35
22047 Hamburg - GERMANY
Phone: +49 (0) 40/6948-0
www.jungheinrich.com
0108.USA
It is impossible for the manufacturer to foresee every possible operational
circumstance that could involve a potential danger. For that reason, the warnings in
this manual and on the equipment itself do not encompass all possible
circumstances. If you use a tool, procedure, working method, or operating technique
not expressly recommended by the manufacturer, you must make sure yourself that
it does not present a safety risk to you or to anyone else. You must also ensure that
the product will not be damaged or made unsafe through operation, lubrication,
maintenance, or the chosen repair measures.
The information, technical data, and illustrations contained in this document are
based on the information available at the time of publication. Specifications, torques,
pressures, measurements, settings, illustrations, and all other data are subject to
change at any time. These changes relate to the performance of the product. Before
executing a task, you should request the most up-to-date and comprehensive
information from the manufacturer / dealer. You can also obtain additional copies of
the manual from your dealer.
In the interests of technical advancement, the manufacturer reserves the right to
make changes, while retaining the essential features of the type of vehicle described,
without correcting this Operating Manual at the same time.
Copyright
Copyright of this operating manual remains with JUNGHEINRICH AG.
Jungheinrich Aktiengesellschaft
Am Stadtrand 35
22047 Hamburg - GERMANY
Phone: +49 (0) 40/6948-0
www.jungheinrich.com
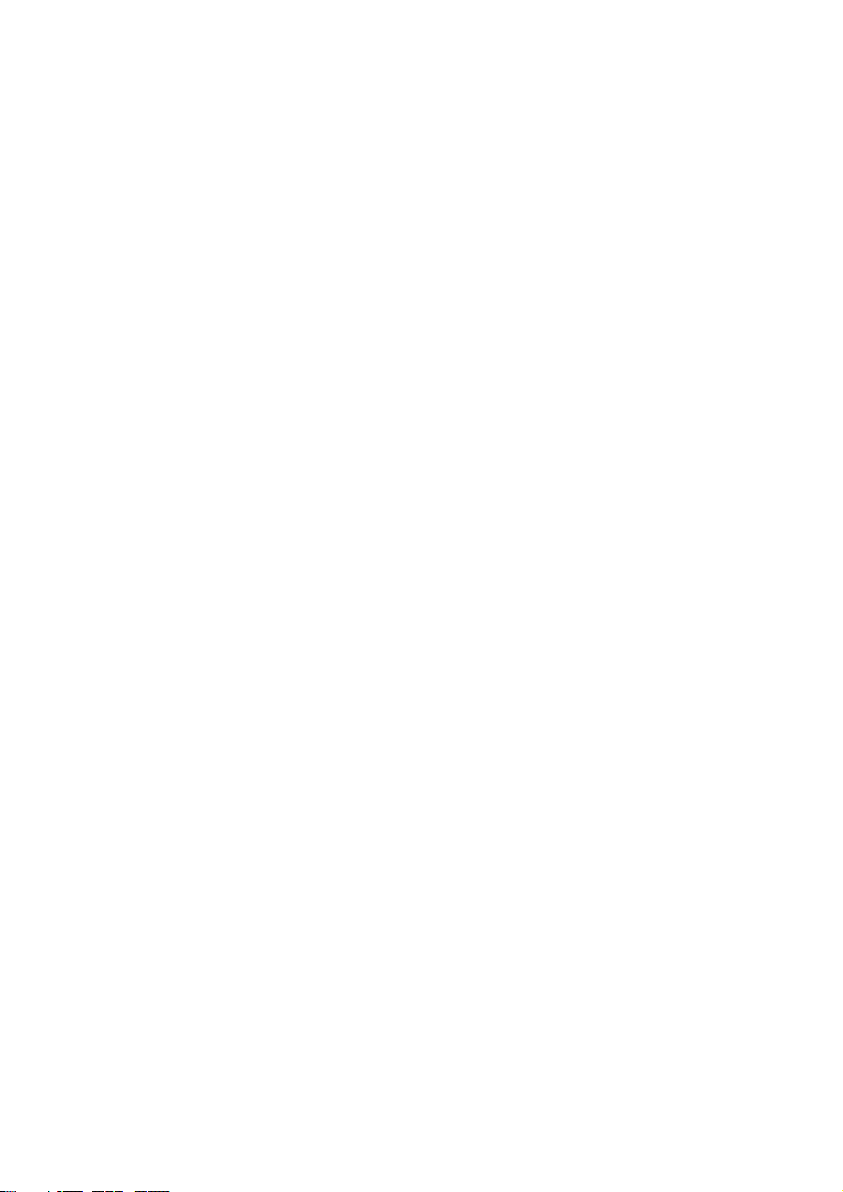
I 1
0708.USA
Table of Contents
A Following the rules- common sense and the law
B Recognize and avoid the hazards
C Correct use and application of the truck
D Truck Description
1 Application ........................................................................................... D 1
2 Assemblies and Functional Description ..............................................D 3
2.1 Truck ................................................................................................... D 4
3 Standard Version Specifications ......................................................... D 5
3.1 Performance data ................................................................................ D 5
3.2 Dimensions (as per data plate) ........................................................... D 7
3.3 Mast version ........................................................................................ D 8
3.4 US Standards ...................................................................................... D 8
3.5 Conditions for application .................................................................... D 9
4 Identification points, warning labels and data plates ........................... D 10
4.1 Truck data plate .................................................................................. D 12
4.2 Capacity .............................................................................................. D 12
I 1
0708.USA
Table of Contents
A Following the rules- common sense and the law
B Recognize and avoid the hazards
C Correct use and application of the truck
D Truck Description
1 Application ........................................................................................... D 1
2 Assemblies and Functional Description ..............................................D 3
2.1 Truck ................................................................................................... D 4
3 Standard Version Specifications ......................................................... D 5
3.1 Performance data ................................................................................ D 5
3.2 Dimensions (as per data plate) ........................................................... D 7
3.3 Mast version ........................................................................................ D 8
3.4 US Standards ...................................................................................... D 8
3.5 Conditions for application .................................................................... D 9
4 Identification points, warning labels and data plates ........................... D 10
4.1 Truck data plate .................................................................................. D 12
4.2 Capacity .............................................................................................. D 12
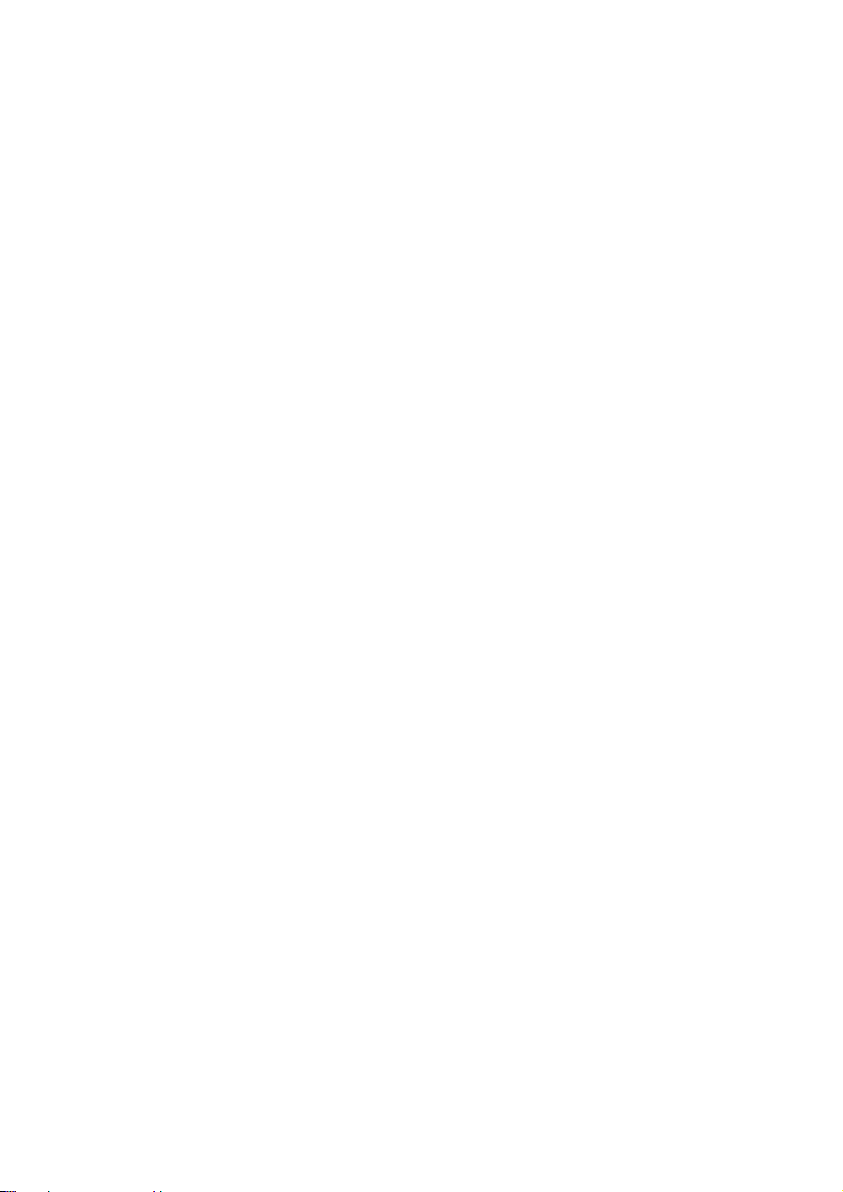
0708.USA
I 2
E Operation
1 Controls and Displays ......................................................................... E 1
1.1 Operating and display equipment on control panel ............................. E 1
1.2 Display unit controls and displays ....................................................... E 2
1.3 Truck operational status symbols ........................................................ E 6
2 Starting up the truck ............................................................................ E 7
2.1 Attaching the safety restraint belt ........................................................ E 8
2.2 t To prepare the truck for operation .................................................. E 9
2.3 o Preparing the truck for operation with an additional access code ... E 10
2.4 Setting the time ................................................................................... E 11
2.5 Operator specific settings .................................................................... E 12
3 Travelling, Steering, Braking ............................................................... E 13
3.1 Travelling ............................................................................................. E 13
3.2 Steering ............................................................................................... E 14
3.3 Braking ................................................................................................ E 14
3.4 Negotiating narrow aisles .................................................................... E 15
3.5 Lifting – Lowering – outside and inside the rack lanes ........................ E 19
3.6 Diagonal travel .................................................................................... E 19
3.7 Order picking and stacking .................................................................. E 20
3.8 Park the truck securely ........................................................................ E 22
4 Important general issues affecting safe operation
and use of the industrial truck ............................................................. E 23
4.1 Training, certification and permission to operate the truck .................. E 23
4.2 Truck damage and repair .................................................................... E 25
4.3 Load Issues ......................................................................................... E 26
4.4 Work environment ............................................................................... E 27
4.5 Safety devices and warning labels ...................................................... E 29
4.6 Lifting of persons ................................................................................. E 30
4.7 Emergency stop device ....................................................................... E 32
4.8 Driver's cab emergency lowering ........................................................ E 32
5 Operation of the truck .......................................................................... E 33
5.1 Safety regulations for the truck operator ............................................. E 33
5.2 General operation of the truck ............................................................. E 33
5.3 Make sure your truck is properly equipped ......................................... E 36
5.4 Load and transport safety ................................................................... E 37
5.5 Avoid overturn and tipover .................................................................. E 38
5.6 Attend and secure your truck .............................................................. E 39
5.7 Lifting of persons ................................................................................. E 39
5.8 Slack chain safety device override ...................................................... E 41
5.9 Travel cutout override (o) ................................................................... E 41
5.10 Lift limit override (o) ......................................................................... E 41
5.11 Aisle end safety device (o) ................................................................. E 42
5.12 Wire Guidance emergency operation (Error 144) ............................... E 43
5.13 Recovering the truck from a narrow aisle / Moving the truck
without a battery .................................................................................. E 44
0708.USA
I 2
E Operation
1 Controls and Displays ......................................................................... E 1
1.1 Operating and display equipment on control panel ............................. E 1
1.2 Display unit controls and displays ....................................................... E 2
1.3 Truck operational status symbols ........................................................ E 6
2 Starting up the truck ............................................................................ E 7
2.1 Attaching the safety restraint belt ........................................................ E 8
2.2 t To prepare the truck for operation .................................................. E 9
2.3 o Preparing the truck for operation with an additional access code ... E 10
2.4 Setting the time ................................................................................... E 11
2.5 Operator specific settings .................................................................... E 12
3 Travelling, Steering, Braking ............................................................... E 13
3.1 Travelling ............................................................................................. E 13
3.2 Steering ............................................................................................... E 14
3.3 Braking ................................................................................................ E 14
3.4 Negotiating narrow aisles .................................................................... E 15
3.5 Lifting – Lowering – outside and inside the rack lanes ........................ E 19
3.6 Diagonal travel .................................................................................... E 19
3.7 Order picking and stacking .................................................................. E 20
3.8 Park the truck securely ........................................................................ E 22
4 Important general issues affecting safe operation
and use of the industrial truck ............................................................. E 23
4.1 Training, certification and permission to operate the truck .................. E 23
4.2 Truck damage and repair .................................................................... E 25
4.3 Load Issues ......................................................................................... E 26
4.4 Work environment ............................................................................... E 27
4.5 Safety devices and warning labels ...................................................... E 29
4.6 Lifting of persons ................................................................................. E 30
4.7 Emergency stop device ....................................................................... E 32
4.8 Driver's cab emergency lowering ........................................................ E 32
5 Operation of the truck .......................................................................... E 33
5.1 Safety regulations for the truck operator ............................................. E 33
5.2 General operation of the truck ............................................................. E 33
5.3 Make sure your truck is properly equipped ......................................... E 36
5.4 Load and transport safety ................................................................... E 37
5.5 Avoid overturn and tipover .................................................................. E 38
5.6 Attend and secure your truck .............................................................. E 39
5.7 Lifting of persons ................................................................................. E 39
5.8 Slack chain safety device override ...................................................... E 41
5.9 Travel cutout override (o) ................................................................... E 41
5.10 Lift limit override (o) ......................................................................... E 41
5.11 Aisle end safety device (o) ................................................................. E 42
5.12 Wire Guidance emergency operation (Error 144) ............................... E 43
5.13 Recovering the truck from a narrow aisle / Moving the truck
without a battery .................................................................................. E 44
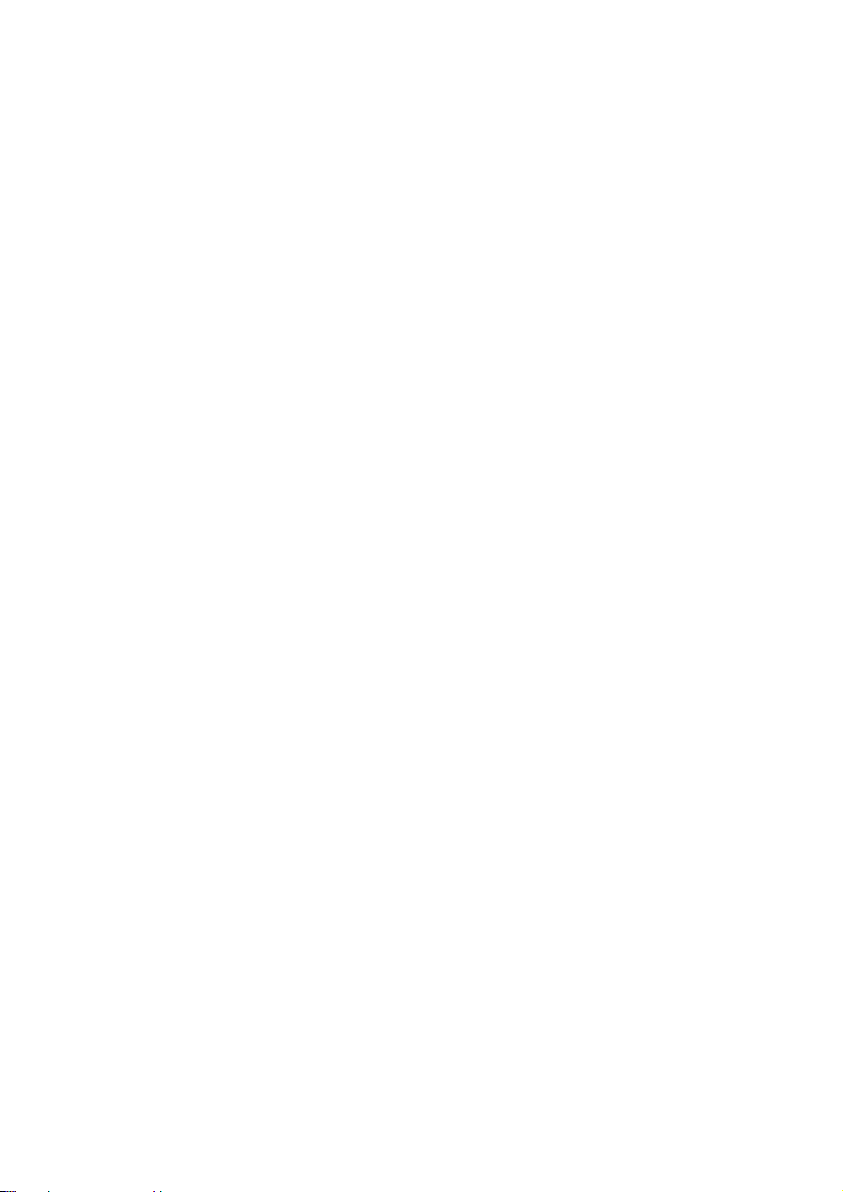
I 3
0708.USA
F Battery - Servicing, recharging, replacement
1 Safety regulations governing the handling of lead-acid batteries ........ F 1
2 Battery type ......................................................................................... F 2
3 Charge the battery .............................................................................. F 3
4 Battery removal and installation .......................................................... F 4
5 Check the battery condition, the acid level and acid density ............... F 6
6 Battery discharge indicator .................................................................. F 6
G Truck Maintenance + Troubleshooting
1 Operational safety and environmental protection ................................ G 1
2 Safety regulations applicable to truck maintenance ............................ G 1
3 Servicing and inspection ..................................................................... G 6
4 EKS 314 maintenance checklist .......................................................... G 7
5 Lubrication schedule ........................................................................... G 10
5.1 Fuels, coolants and lubricants ............................................................. G 11
6 Maintenance and Repairs ................................................................... G 12
6.1 Preparing the truck for maintenance and repairs ................................ G 12
6.2 Securing the driver’s position carriage and mast ................................ G 13
6.3 Lift Chain Servicing ............................................................................. G 13
6.4 Inspecting the lift chains ...................................................................... G 13
6.5 Hydraulic oil ......................................................................................... G 14
6.6 Hydraulic hoses ................................................................................... G 14
6.7 Checking electrical fuses .................................................................... G 15
6.8 Recommissioning the truck after cleaning or maintenance work ........ G 16
7 Decommissioning the industrial truck .................................................. G 16
7.1 Operations to be performed prior to decommissioning ....................... G 16
7.2 Measures to be taken during decommissioning .................................. G 17
7.3 Recommissioning the truck after decommissioning ............................ G 17
8 Safety inspections at regular intervals and after exceptional events .. G 18
9 Final de-commissioning, disposal ....................................................... G 18
10 Troubleshooting .................................................................................. G 19
I 3
0708.USA
F Battery - Servicing, recharging, replacement
1 Safety regulations governing the handling of lead-acid batteries ........ F 1
2 Battery type ......................................................................................... F 2
3 Charge the battery .............................................................................. F 3
4 Battery removal and installation .......................................................... F 4
5 Check the battery condition, the acid level and acid density ............... F 6
6 Battery discharge indicator .................................................................. F 6
G Truck Maintenance + Troubleshooting
1 Operational safety and environmental protection ................................ G 1
2 Safety regulations applicable to truck maintenance ............................ G 1
3 Servicing and inspection ..................................................................... G 6
4 EKS 314 maintenance checklist .......................................................... G 7
5 Lubrication schedule ........................................................................... G 10
5.1 Fuels, coolants and lubricants ............................................................. G 11
6 Maintenance and Repairs ................................................................... G 12
6.1 Preparing the truck for maintenance and repairs ................................ G 12
6.2 Securing the driver’s position carriage and mast ................................ G 13
6.3 Lift Chain Servicing ............................................................................. G 13
6.4 Inspecting the lift chains ...................................................................... G 13
6.5 Hydraulic oil ......................................................................................... G 14
6.6 Hydraulic hoses ................................................................................... G 14
6.7 Checking electrical fuses .................................................................... G 15
6.8 Recommissioning the truck after cleaning or maintenance work ........ G 16
7 Decommissioning the industrial truck .................................................. G 16
7.1 Operations to be performed prior to decommissioning ....................... G 16
7.2 Measures to be taken during decommissioning .................................. G 17
7.3 Recommissioning the truck after decommissioning ............................ G 17
8 Safety inspections at regular intervals and after exceptional events .. G 18
9 Final de-commissioning, disposal ....................................................... G 18
10 Troubleshooting .................................................................................. G 19

0708.USA
I 4
H Transport and Commissioning
1 Transport ............................................................................................. H 1
2 Lifting by crane .................................................................................... H 1
2.1 Crane points ........................................................................................H 3
2.2 Lifting the battery by crane .................................................................. H 3
2.3 Securing the truck during transport ..................................................... H 3
2.4 Basic truck transport safety ................................................................. H 4
2.5 Mast transport safety ........................................................................... H 5
2.6 Mast assembled .................................................................................. H 5
3 Commissioning .................................................................................... H 7
3.1 Moving the truck without a battery ...................................................... H 7
3.2 Installing/removing or erecting/folding the mast .................................. H 7
4 Commissioning .................................................................................... H 7
0708.USA
I 4
H Transport and Commissioning
1 Transport ............................................................................................. H 1
2 Lifting by crane .................................................................................... H 1
2.1 Crane points ........................................................................................H 3
2.2 Lifting the battery by crane .................................................................. H 3
2.3 Securing the truck during transport ..................................................... H 3
2.4 Basic truck transport safety ................................................................. H 4
2.5 Mast transport safety ........................................................................... H 5
2.6 Mast assembled .................................................................................. H 5
3 Commissioning .................................................................................... H 7
3.1 Moving the truck without a battery ...................................................... H 7
3.2 Installing/removing or erecting/folding the mast .................................. H 7
4 Commissioning .................................................................................... H 7

A 1
0505.USA
A Following the rules- common sense and
the law
In 1998, OSHA reported on its thorough study of industrial truck use. This report may
be found at Federal Register/ Vol. 63, No. 230. In its report, OSHA explained its
many reasons for carefully defining the duties of employers to train their employees
in the use of industrial trucks, and the duty of untrained persons not to operate industrial trucks except in controlled, training circumstances. The report addresses how
critically important the training required by the OSHA regulations is for the safety of
people and things wherever industrial trucks are operated. 29 CFR sec. 1910.178. In
simple terms, careful training before operation of an industrial truck is critical and
must occur before truck operation because accidents resulting in injury, death or
property damage almost always result from disregard of the basic risks inherent in
truck use or disregard of safety rules and procedures created to reduce or eliminate
those risks. The training required by OSHA is designed to address those risks. The
evidence provided by OSHA in its report reveals that the law’s operator training requirements for employers and operators are grounded in experience and goog judgment.
Jungheinrich has provided an industrial truck which complies with 29 CFR 1910.178,
and ASME B56.1. Jungheinrich representatives are available to assist and answer
any questions which may arise concerning the capacities, operation, use and maintenance of the truck.
According to OSHA, people do not start out with the knowledge and skills they need
to safely operate a powered industrial truck, and therefore, they need formal training
and practice to gain the knowledge and to master the skills they need to safely operate an industrial truck. Consequently, having an industrial truck which complies with
the law and standards fulfills only one half of the safety equation. It is, therefore, up
to you, the operator, and your employer, to fulfill your responsibilities by obeying all
national, state and local laws and regulations concerning training and the safe operation of industrial trucks - not just because it is the law, but because it also makes
common safety sense.
Only trained and certified persons may operate an industrial truck.
Training programs must comply with OSHA requirements and address, at least,
all of the topics listed there.
The user portion of ASME B56.1 is recommended to employers and operators
for careful review and observance.
“Safe operation is the responsibility of the operator“ ASME B56.1-2003, Part II
sec. 5.1.1.
A 1
0505.USA
A Following the rules- common sense and
the law
In 1998, OSHA reported on its thorough study of industrial truck use. This report may
be found at Federal Register/ Vol. 63, No. 230. In its report, OSHA explained its
many reasons for carefully defining the duties of employers to train their employees
in the use of industrial trucks, and the duty of untrained persons not to operate indus-
trial trucks except in controlled, training circumstances. The report addresses how
critically important the training required by the OSHA regulations is for the safety of
people and things wherever industrial trucks are operated. 29 CFR sec. 1910.178. In
simple terms, careful training before operation of an industrial truck is critical and
must occur before truck operation because accidents resulting in injury, death or
property damage almost always result from disregard of the basic risks inherent in
truck use or disregard of safety rules and procedures created to reduce or eliminate
those risks. The training required by OSHA is designed to address those risks. The
evidence provided by OSHA in its report reveals that the law’s operator training re-
quirements for employers and operators are grounded in experience and goog judg-
ment.
Jungheinrich has provided an industrial truck which complies with 29 CFR 1910.178,
and ASME B56.1. Jungheinrich representatives are available to assist and answer
any questions which may arise concerning the capacities, operation, use and main-
tenance of the truck.
According to OSHA, people do not start out with the knowledge and skills they need
to safely operate a powered industrial truck, and therefore, they need formal training
and practice to gain the knowledge and to master the skills they need to safely oper-
ate an industrial truck. Consequently, having an industrial truck which complies with
the law and standards fulfills only one half of the safety equation. It is, therefore, up
to you, the operator, and your employer, to fulfill your responsibilities by obeying all
national, state and local laws and regulations concerning training and the safe oper-
ation of industrial trucks - not just because it is the law, but because it also makes
common safety sense.
Only trained and certified persons may operate an industrial truck.
Training programs must comply with OSHA requirements and address, at least,
all of the topics listed there.
The user portion of ASME B56.1 is recommended to employers and operators
for careful review and observance.
“Safe operation is the responsibility of the operator“ ASME B56.1-2003, Part II
sec. 5.1.1.
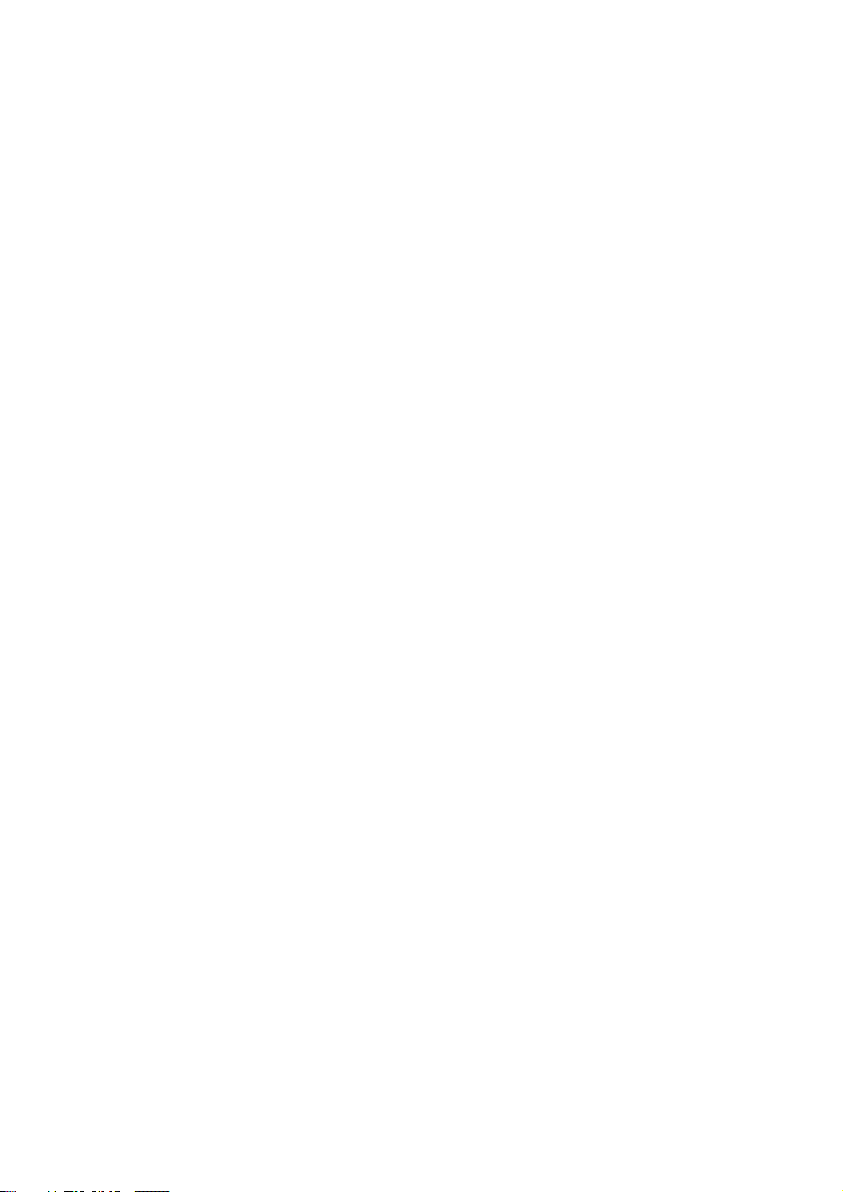
B 1
0505.USA
B Recognize and avoid the hazards
In its 1998 study of industrial truck use, OSHA identified a nummber of ways accidents regularly occur and described why they occur. OSHA concluded that untrained
and poorly trained operators pose significant risks to themselves and those working
in their vicinity. According to OSHA, the major cause of accidents with industrial
trucks and their resulting injuries and deaths is improper or unsafe operation. It is no
surprise, therefore, that when OSHA reviewed its files, it discovered that accidents
almost always occur as a result of situations or actions the operator, or the employer
and the operator, were in a position to influence or control for the better. A simple review of the accident causes identified by OSHA proves this observation. Out of 208
industrial truck accidents studied, which involved 184 deaths or serious injuries, fully
50% were caused by a load problem, including overload, instability, falling load or improper lifting of load. Similarly, 25% involved overturn/tipover of the truck. Falls of the
truck from a platform or trailer, or of lifted persons from the truck, accounted for another 20% of accidents. Although ’no training’ accounted for about 4% of the accidents,
OSHA properly noted that many of the accidents could have been equally caused by
improper training - for example, an overturn accident may also have been the result
of no, or poor, training of the operator about load balance. Other less frequent, but
equally employer and operator - controllable accident causes include speeding and
use of improper equipent.
It is therefore critically important to:
– Complete the training and operator certification process before beginning work with
an industrial truck.
– Always be in competent physical, mental and emotional condition before operating
an industrial truck.
– Understand and observe safe loading and handling practices- know your machine
capacities and work within them.
– Avoid circumstances which can lead to overturn or tipover- this includes, for ex-
ample, understanding center of gravity and following sound loading and load movement practices, and constant area awareness of edges, curbs, dropoffs and
other surface details.
– Never carry passengers or lift people without specific training, the correct truck,
equipment and procedures.
– Always follow traffic rules and always be aware of the location of co-workers, other
trucks and your physical surroundings.
The manufacturer declines all responsibility for the consequences of dismantling the
truck or making any modification which is outside the manufacturer’s control.
The manufacturer’s responsibility is limited to the configuration of the equipment described in the conformance certificate. The manufacturer is absolved from their responsibility if there are modifications, additions or use of equipment from another supplier, in which case the user assumes the manufacturer’s responsibility.
These operating instructions become invalid if the machine is modified by a company
which is not part of our company group, even if original spare parts are used and our
company logo remains displayed on the equipment.
B 1
0505.USA
B Recognize and avoid the hazards
In its 1998 study of industrial truck use, OSHA identified a nummber of ways acci-
dents regularly occur and described why they occur. OSHA concluded that untrained
and poorly trained operators pose significant risks to themselves and those working
in their vicinity. According to OSHA, the major cause of accidents with industrial
trucks and their resulting injuries and deaths is improper or unsafe operation. It is no
surprise, therefore, that when OSHA reviewed its files, it discovered that accidents
almost always occur as a result of situations or actions the operator, or the employer
and the operator, were in a position to influence or control for the better. A simple re-
view of the accident causes identified by OSHA proves this observation. Out of 208
industrial truck accidents studied, which involved 184 deaths or serious injuries, fully
50% were caused by a load problem, including overload, instability, falling load or im-
proper lifting of load. Similarly, 25% involved overturn/tipover of the truck. Falls of the
truck from a platform or trailer, or of lifted persons from the truck, accounted for ano-
ther 20% of accidents. Although ’no training’ accounted for about 4% of the accidents,
OSHA properly noted that many of the accidents could have been equally caused by
improper training - for example, an overturn accident may also have been the result
of no, or poor, training of the operator about load balance. Other less frequent, but
equally employer and operator - controllable accident causes include speeding and
use of improper equipent.
It is therefore critically important to:
– Complete the training and operator certification process before beginning work with
an industrial truck.
– Always be in competent physical, mental and emotional condition before operating
an industrial truck.
– Understand and observe safe loading and handling practices- know your machine
capacities and work within them.
– Avoid circumstances which can lead to overturn or tipover- this includes, for ex-
ample, understanding center of gravity and following sound loading and load mo-
vement practices, and constant area awareness of edges, curbs, dropoffs and
other surface details.
– Never carry passengers or lift people without specific training, the correct truck,
equipment and procedures.
– Always follow traffic rules and always be aware of the location of co-workers, other
trucks and your physical surroundings.
The manufacturer declines all responsibility for the consequences of dismantling the
truck or making any modification which is outside the manufacturer’s control.
The manufacturer’s responsibility is limited to the configuration of the equipment de-
scribed in the conformance certificate. The manufacturer is absolved from their re-
sponsibility if there are modifications, additions or use of equipment from another sup-
plier, in which case the user assumes the manufacturer’s responsibility.
These operating instructions become invalid if the machine is modified by a company
which is not part of our company group, even if original spare parts are used and our
company logo remains displayed on the equipment.
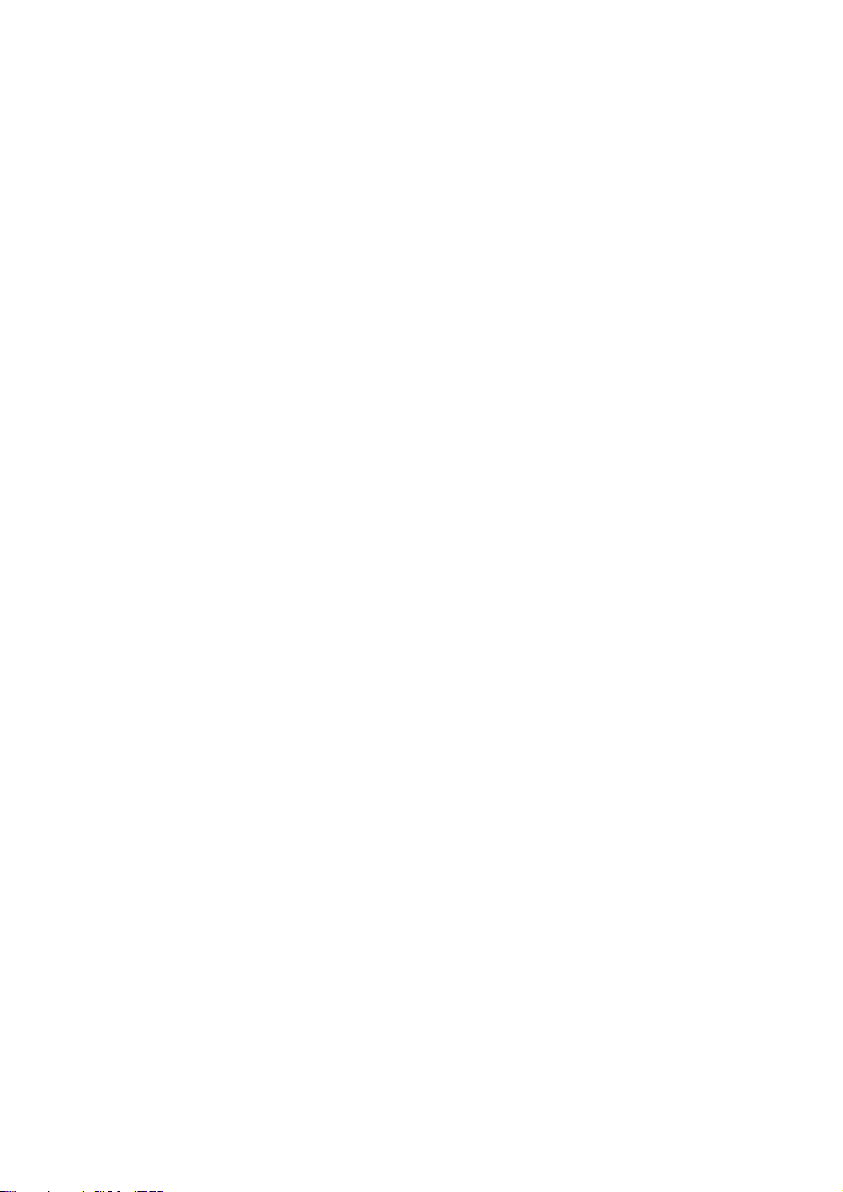
C 1
0108.USA
C Correct use and application of the truck
NOTICE These operating instructions include all the information needed for transport,
first start-up, normal use, servicing and maintenance of the described
industrial truck, in accordance with ASME B56.1-2003, UL 583 and ANSI
Z535.4-2002. Read these instructions carefully to ensure proper and safe
use of the truck.
The industrial truck described in these operating instructions is suitable for lifting and
transporting loads and must be used, operated and maintained according to the law
and the information provided in these operating instructions. Any use of the truck not
authorized by law or these instructions is a misuse of the truck and beyond the intended design of the truck. Such misuse can lead to death and/or serious injury to persons and damage to equipment and property. Overloading caused by excessively
heavy or unbalanced loads is an example of misuse of the truck which must be avoided. The maximum allowable load is indicated on the identification plate and load diagram label shown on the truck. The industrial truck must not be operated in spaces
subject to fire or explosion hazards, or in spaces where corrosive or very dusty atmospheres prevail.
These operating instructions must be kept as long as the vehicle is in use.
Duties of the user:
A user of an industrial truck may be one of several persons depending on the context
referred to in these operating instructions- it includes the truck owner, any person leasing or renting the truck and the operator, as referred to in ASME B56.1- 2003. Users
will usually be employers, and the truck operators will often be their employees for
purposes of OSHA regulations. Every user must know and follow the applicable rules
and regulations concerning industrial truck use and operation. The operator instructions are for all users, and are directed toward and should be provided to the persons
who will actually operate the industrial truck.
The user and operator must ensure that the truck is not abused and used only within
its design limits so that all danger to life and limb of the operator, and third parties, is
avoided. The user and operator must also ensure that the accident prevention regulations and other safety-related provisions, as well as the operating, servicing and
maintenance guidelines, are observed. The user must ensure that all who will operate
this truck have read and understood these operating instructions and have fulfilled all
training and certification required by law before performing any work with the truck.
The user and operator are advised that when functions on industrial trucks are automated (for example rail-guided or inductively-guided trucks), the operation of the vehicle is changed which may result in modified performance characteristics, maintenance procedures, and additional safety precautions.
The addition of any automatic function to a manned industrial vehicle requires the
evaluation of the impact of the automation on all other functions. It maybe necessary
to automate other functions to some degree.
NOTICE If these Operating Instruction are not observed the warranty becomes void.
The same applies if improper work is carried out on the device by the
customer and/or third parties.
C 1
0108.USA
C Correct use and application of the truck
NOTICE These operating instructions include all the information needed for transport,
first start-up, normal use, servicing and maintenance of the described
industrial truck, in accordance with ASME B56.1-2003, UL 583 and ANSI
Z535.4-2002. Read these instructions carefully to ensure proper and safe
use of the truck.
The industrial truck described in these operating instructions is suitable for lifting and
transporting loads and must be used, operated and maintained according to the law
and the information provided in these operating instructions. Any use of the truck not
authorized by law or these instructions is a misuse of the truck and beyond the inten-
ded design of the truck. Such misuse can lead to death and/or serious injury to per-
sons and damage to equipment and property. Overloading caused by excessively
heavy or unbalanced loads is an example of misuse of the truck which must be avo-
ided. The maximum allowable load is indicated on the identification plate and load di-
agram label shown on the truck. The industrial truck must not be operated in spaces
subject to fire or explosion hazards, or in spaces where corrosive or very dusty at-
mospheres prevail.
These operating instructions must be kept as long as the vehicle is in use.
Duties of the user:
A user of an industrial truck may be one of several persons depending on the context
referred to in these operating instructions- it includes the truck owner, any person lea-
sing or renting the truck and the operator, as referred to in ASME B56.1- 2003. Users
will usually be employers, and the truck operators will often be their employees for
purposes of OSHA regulations. Every user must know and follow the applicable rules
and regulations concerning industrial truck use and operation. The operator instruc-
tions are for all users, and are directed toward and should be provided to the persons
who will actually operate the industrial truck.
The user and operator must ensure that the truck is not abused and used only within
its design limits so that all danger to life and limb of the operator, and third parties, is
avoided. The user and operator must also ensure that the accident prevention regu-
lations and other safety-related provisions, as well as the operating, servicing and
maintenance guidelines, are observed. The user must ensure that all who will operate
this truck have read and understood these operating instructions and have fulfilled all
training and certification required by law before performing any work with the truck.
The user and operator are advised that when functions on industrial trucks are auto-
mated (for example rail-guided or inductively-guided trucks), the operation of the ve-
hicle is changed which may result in modified performance characteristics, mainte-
nance procedures, and additional safety precautions.
The addition of any automatic function to a manned industrial vehicle requires the
evaluation of the impact of the automation on all other functions. It maybe necessary
to automate other functions to some degree.
NOTICE If these Operating Instruction are not observed the warranty becomes void.
The same applies if improper work is carried out on the device by the
customer and/or third parties.

0108.USA
C 2
Mounting of attachments:
The mounting or installation of any attachments and modifications and/or additions to
hardware or software which will interfere with, or supplement, rated capacity, safe operation, any emergency control or device, or any other function of the truck is only permitted with approval of the proposed modifications or additions by the manufacturer.
When such approval is granted, capacity, operation, and maintenance instruction plates, tags, or decals must be changed accordingly.
If necessary, the approval of local authorities must also be obtained.
Approval obtained from local authorities does not render manufacturer approval of
the modifications or additions unnecessary.
If the truck is equipped with attachment(s) including fork extensions, the user shall
see that the truck is marked to identify the attachment(s), show the approximate
weight of the truck and attachment combination, and show the capacity of the truck
with attachment(s) at maximum elevation with load laterally centered.
When modifications involve rebuild and repair of the basic unit, they shall be made in
accordance with the manufacturer‘s established criteria and procedures.
The basic functions of the truck are:
– steering (guidance)
– travel
– control and sensing
– lifting/load manipulation
0108.USA
C 2
Mounting of attachments:
The mounting or installation of any attachments and modifications and/or additions to
hardware or software which will interfere with, or supplement, rated capacity, safe op-
eration, any emergency control or device, or any other function of the truck is only per-
mitted with approval of the proposed modifications or additions by the manufacturer.
When such approval is granted, capacity, operation, and maintenance instruction pla-
tes, tags, or decals must be changed accordingly.
If necessary, the approval of local authorities must also be obtained.
Approval obtained from local authorities does not render manufacturer approval of
the modifications or additions unnecessary.
If the truck is equipped with attachment(s) including fork extensions, the user shall
see that the truck is marked to identify the attachment(s), show the approximate
weight of the truck and attachment combination, and show the capacity of the truck
with attachment(s) at maximum elevation with load laterally centered.
When modifications involve rebuild and repair of the basic unit, they shall be made in
accordance with the manufacturer‘s established criteria and procedures.
The basic functions of the truck are:
– steering (guidance)
– travel
– control and sensing
– lifting/load manipulation

C 3
0108.USA
Identification plate:
We highly recommend that the data from the identification plate be copied onto the
diagram below to ensure that this important data is available to the operator and that
these instructions are not inadvertently used with any other product.
The user is responsible for confirming that all identification plates and caution and instruction markings are in place and legible (refer to section “Identification points and
data plates“ in chapter D).
QwW Industrial truck use is subject to certain hazards that cannot be completely
eliminated by mechanical means. Those risks can, however, be minimized by
the exercise of intelligence, care and common sense. Operators must,
therefore, be competent, careful, physically and mentally fit, and thoroughly
trained in the safe operation of the equipment and load handling.
for type "E" industrial trucks with type "E" battery
Built in compliance with ASME B 56.1
C 3
0108.USA
Identification plate:
We highly recommend that the data from the identification plate be copied onto the
diagram below to ensure that this important data is available to the operator and that
these instructions are not inadvertently used with any other product.
The user is responsible for confirming that all identification plates and caution and in-
struction markings are in place and legible (refer to section “Identification points and
data plates“ in chapter D).
QwW Industrial truck use is subject to certain hazards that cannot be completely
eliminated by mechanical means. Those risks can, however, be minimized by
the exercise of intelligence, care and common sense. Operators must,
therefore, be competent, careful, physically and mentally fit, and thoroughly
trained in the safe operation of the equipment and load handling.
for type "E" industrial trucks with type "E" battery
Built in compliance with ASME B 56.1
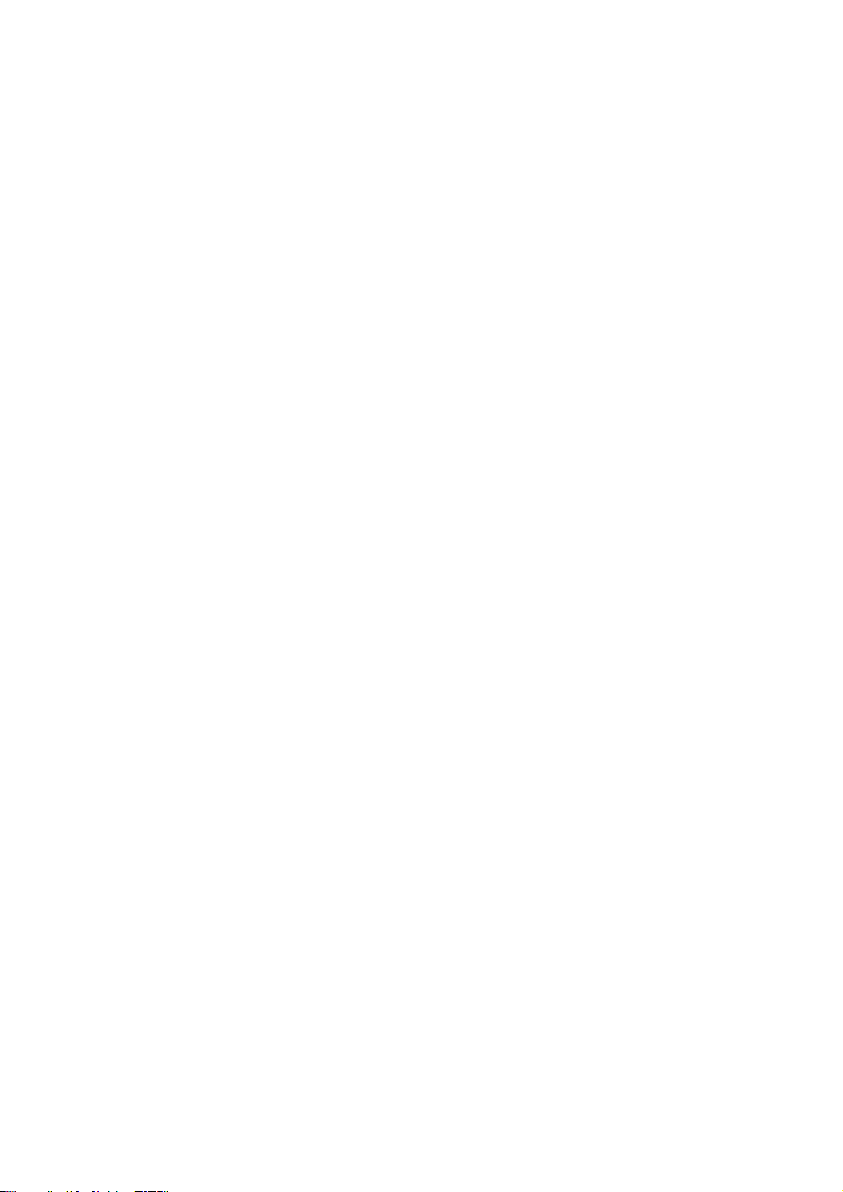
0108.USA
C 4
General instructions for Users and Operators
QwW The following are general instructions which apply to all users, including
company management, department heads, operators, transporters and
employees who work in the vicinity of industrial trucks. The user is
responsible for safe operation of this truck, and both employer and operator
must work together to enforce and follow the safety regulations which apply
to use of the truck.
1. These instructions must be read before using the truck and followed when the
truck is in use
2. The user and operator must ensure that the truck is used only for the purpose for
which it has been designed. The user and operator must NOT:
– allow abnormal use of the truck
– disable the safety devices
– overload or operate the truck outside the load graph
(refer to section “Capacity“ in chapter D)
– use the truck as a crane
– use the truck to lift or carry people
– lock a control in position
– ignore standard practices for handling and manipulating loads
– transport loads over people’s head
– push or pull loads with the truck
– engage in games or horseplay with the truck such as racing, or ’chicken’
– carry unbalanced loads
3. The user and operator must check the strength of the floors (to avoid damaging
them), the racks, and in general all the corridors and areas where the truck will or
may be used.
4. Read the instructions on the plates attached to the truck and make sure that they
remain legible
5. Keep these instructions available for all operators in an accessible location on
the truck
6. Make sure that only trained, certified and responsible persons, capable of safe
operation of the truck, are allowed to operate the truck.
7. Make sure that the truck cannot be tampered with when it is not in use
8. Never use a truck which does not appear to be in good working condition
9. Never use the truck to carry a load or apply a force which exceeds its maximum
operating load
10. Never use the truck for a purpose for which it is not intended
11. Read the truck safety regulations and apply them rigorously
0108.USA
C 4
General instructions for Users and Operators
QwW The following are general instructions which apply to all users, including
company management, department heads, operators, transporters and
employees who work in the vicinity of industrial trucks. The user is
responsible for safe operation of this truck, and both employer and operator
must work together to enforce and follow the safety regulations which apply
to use of the truck.
1. These instructions must be read before using the truck and followed when the
truck is in use
2. The user and operator must ensure that the truck is used only for the purpose for
which it has been designed. The user and operator must NOT:
– allow abnormal use of the truck
– disable the safety devices
– overload or operate the truck outside the load graph
(refer to section “Capacity“ in chapter D)
– use the truck as a crane
– use the truck to lift or carry people
– lock a control in position
– ignore standard practices for handling and manipulating loads
– transport loads over people’s head
– push or pull loads with the truck
– engage in games or horseplay with the truck such as racing, or ’chicken’
– carry unbalanced loads
3. The user and operator must check the strength of the floors (to avoid damaging
them), the racks, and in general all the corridors and areas where the truck will or
may be used.
4. Read the instructions on the plates attached to the truck and make sure that they
remain legible
5. Keep these instructions available for all operators in an accessible location on
the truck
6. Make sure that only trained, certified and responsible persons, capable of safe
operation of the truck, are allowed to operate the truck.
7. Make sure that the truck cannot be tampered with when it is not in use
8. Never use a truck which does not appear to be in good working condition
9. Never use the truck to carry a load or apply a force which exceeds its maximum
operating load
10. Never use the truck for a purpose for which it is not intended
11. Read the truck safety regulations and apply them rigorously

C 5
0108.USA
12. The manufacturer declines all responsibility for the consequences of dismantling
the truck or making any modification which is outside the manufacturer’s control
13. The manufacturer’s responsibility is limited to the configuration of the equipment
described in the conformance certificate. The manufacturer is absolved from
their responsibility if there are modifications, additions or use of equipment from
another supplier, in which case the user assumes the manufacturer’s responsibility
14. These operating instructions become invalid if the machine is modified by a company which is not part of our company group, even if original spare parts are
used and our company logo remains displayed on the equipment
15. The conditions of your workplace, and other unusual operating conditions may
require additional safety precautions and special operating instructions
16. Supervision is an essential element in the safe operation of powered industrial
trucks
17. Batteries must comply with the minimum/maximum battery weight range shown
on the truck identification plate
18. Floor and wheel locks (if provided) are intended only to hold the truck in a desired position on a level surface
QwW Serious hazards are overloading, load instability, obstruction to the free
passage of the load, collision with objects or pedestrians, poor maintenance,
and use of equipment for purposes it was not intended or designed. Changes
in load(s), dimension(s), coupling types(s) and/or position(s), and floor
surface condition(s) or battery weights may affect rated capacities and safe
operation. Only stable or safely arranged loads shall be handled.
The operator is responsible for proper loading, load stability and securement. The
operator shall, as necessary, verify that the load remains stable and secure.
C 5
0108.USA
12. The manufacturer declines all responsibility for the consequences of dismantling
the truck or making any modification which is outside the manufacturer’s control
13. The manufacturer’s responsibility is limited to the configuration of the equipment
described in the conformance certificate. The manufacturer is absolved from
their responsibility if there are modifications, additions or use of equipment from
another supplier, in which case the user assumes the manufacturer’s responsibi-
lity
14. These operating instructions become invalid if the machine is modified by a com-
pany which is not part of our company group, even if original spare parts are
used and our company logo remains displayed on the equipment
15. The conditions of your workplace, and other unusual operating conditions may
require additional safety precautions and special operating instructions
16. Supervision is an essential element in the safe operation of powered industrial
trucks
17. Batteries must comply with the minimum/maximum battery weight range shown
on the truck identification plate
18. Floor and wheel locks (if provided) are intended only to hold the truck in a desi-
red position on a level surface
QwW Serious hazards are overloading, load instability, obstruction to the free
passage of the load, collision with objects or pedestrians, poor maintenance,
and use of equipment for purposes it was not intended or designed. Changes
in load(s), dimension(s), coupling types(s) and/or position(s), and floor
surface condition(s) or battery weights may affect rated capacities and safe
operation. Only stable or safely arranged loads shall be handled.
The operator is responsible for proper loading, load stability and securement. The
operator shall, as necessary, verify that the load remains stable and secure.
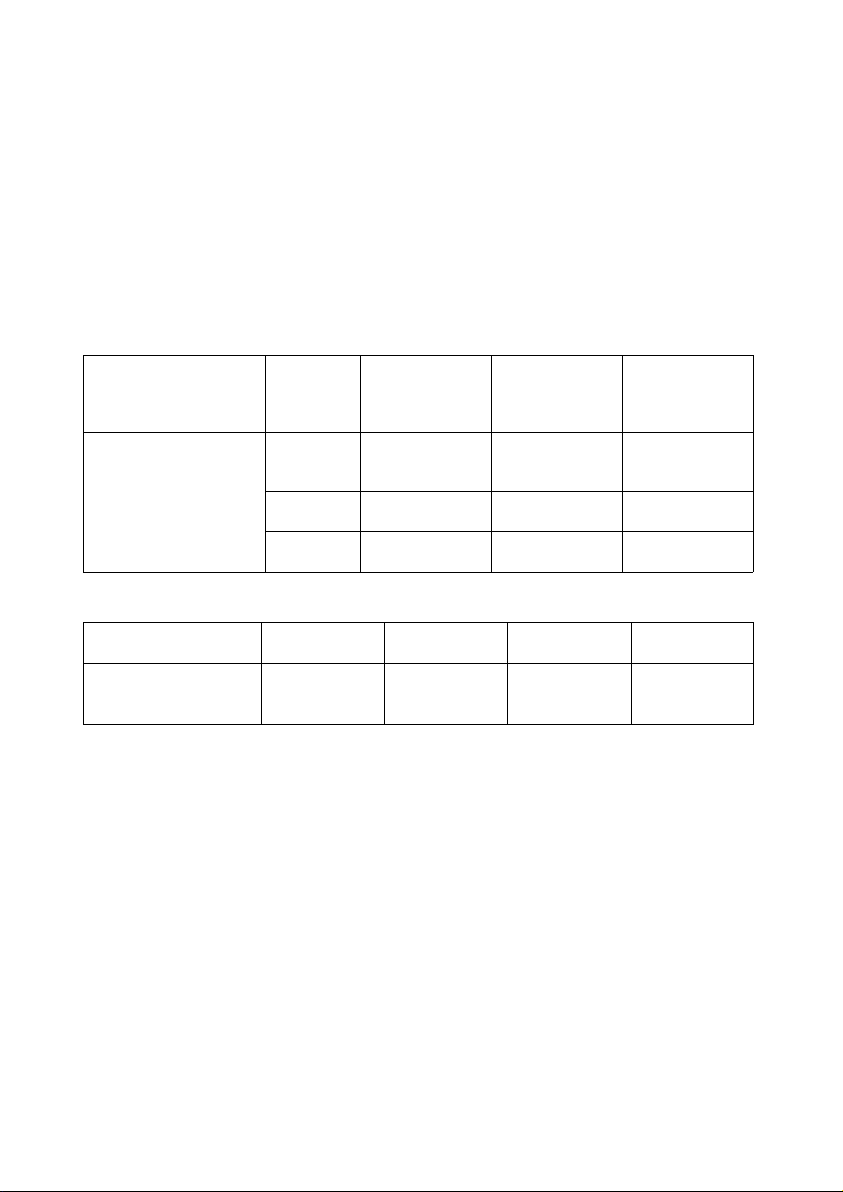
D 1
0108.USA
D Truck Description
1 Application
The EKS 314 is an electric stockpicker. It is designed to be used on level surfaces to
transport and pick goods. The floor surface must comply with the following requirements:
Floor specifications
QwW In order to prevent accidents due to operation on uneven floor surfaces the
following floor surface tolerances must not be exceeded.
Max. permitted height differences (h) across the aisle:
Floor planeness / tolerances lengthwise to the tracks for both height classes
– Floor has to be oil and grease resistant.
– Floor leakage resistance RE is not permitted to pass 10
6
Ω.
– Floor surface must be carefully finished to eliminate all short floor waves.
Axle width (S)
up to 1 m
up to 40 inch
more than 1,0 m
up to 1,5 m
more than 40 inch
up to 59 inch
more than 1,5 m
up to 2,0 m
more than 59 inch
up to 79 inch
more than 2,0 m
up to 2,5 m
more than 59 inch
up to 98 inch
Max. permitted
height difference
between outer tracks (SP)
VNA truck lift height
</= 6 m / </= 236 inch
VNA truck lift height
> 6,01 m / > 236 inch
2,0 mm
0.08 inch
2,5 mm
0.10 inch
3,0 mm
0.12 inch
3,5 mm
0.14 inch
1,5 mm
0.06 inch
2,0 mm
0.08 inch
2,5 mm
0.10 inch
3,0 mm
0.12 inch
Distance of
measuring points
1,0 m /
39.34 inch
2,0 m /
78.68 inch
3,0 m /
118.02 inch
4,0 m /
157.36 inch
Max. permitted tolerance/
planeness
Bulk sample as limit value
2,0 mm
0.08 inch
3,0 mm
0.12 inch
4,0 mm
0.16 inch
5,0 mm
0.20 inch
D 1
0108.USA
D Truck Description
1 Application
The EKS 314 is an electric stockpicker. It is designed to be used on level surfaces to
transport and pick goods. The floor surface must comply with the following require-
ments:
Floor specifications
QwW In order to prevent accidents due to operation on uneven floor surfaces the
following floor surface tolerances must not be exceeded.
Max. permitted height differences (h) across the aisle:
Floor planeness / tolerances lengthwise to the tracks for both height classes
– Floor has to be oil and grease resistant.
– Floor leakage resistance RE is not permitted to pass 10
6
Ω.
– Floor surface must be carefully finished to eliminate all short floor waves.
Axle width (S)
up to 1 m
up to 40 inch
more than 1,0 m
up to 1,5 m
more than 40 inch
up to 59 inch
more than 1,5 m
up to 2,0 m
more than 59 inch
up to 79 inch
more than 2,0 m
up to 2,5 m
more than 59 inch
up to 98 inch
Max. permitted
height difference
between outer tracks (SP)
VNA truck lift height
</= 6 m / </= 236 inch
VNA truck lift height
> 6,01 m / > 236 inch
2,0 mm
0.08 inch
2,5 mm
0.10 inch
3,0 mm
0.12 inch
3,5 mm
0.14 inch
1,5 mm
0.06 inch
2,0 mm
0.08 inch
2,5 mm
0.10 inch
3,0 mm
0.12 inch
Distance of
measuring points
1,0 m /
39.34 inch
2,0 m /
78.68 inch
3,0 m /
118.02 inch
4,0 m /
157.36 inch
Max. permitted tolerance/
planeness
Bulk sample as limit value
2,0 mm
0.08 inch
3,0 mm
0.12 inch
4,0 mm
0.16 inch
5,0 mm
0.20 inch
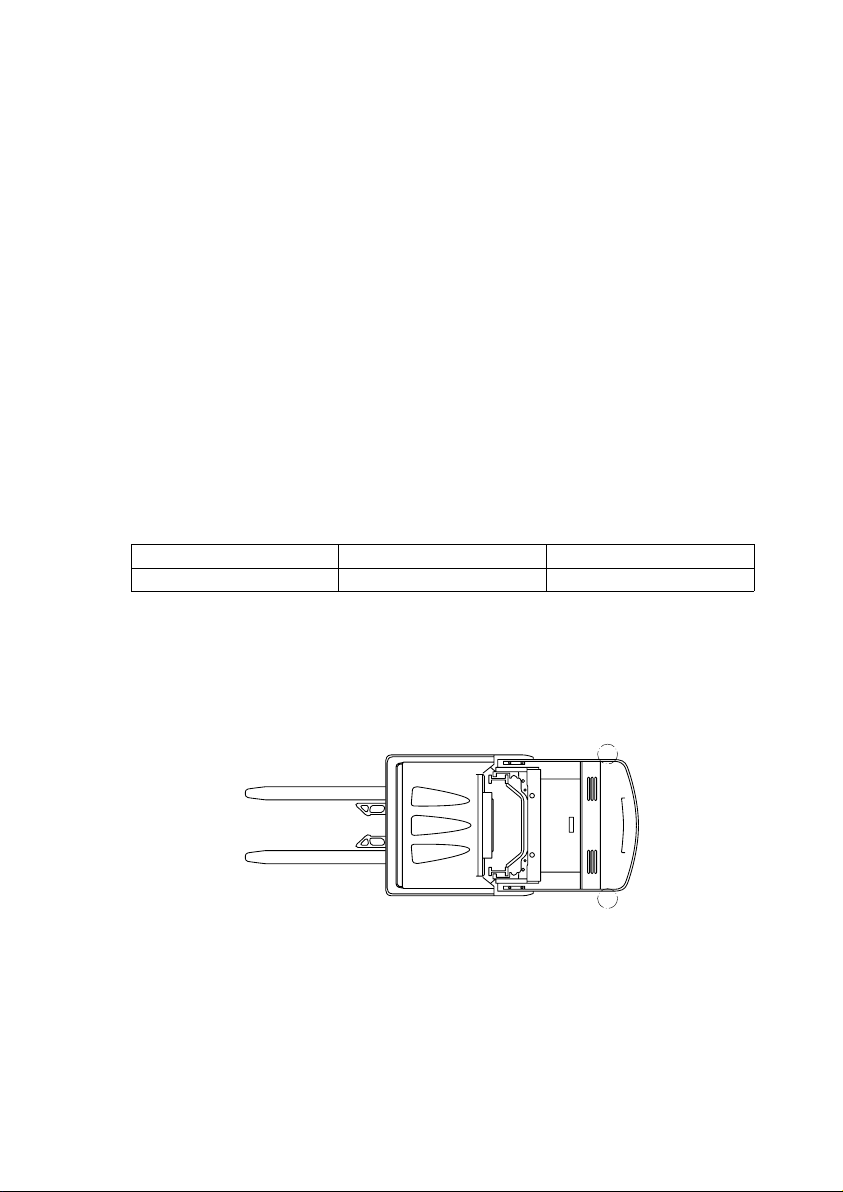
0108.USA
D 2
Open bottom pallets or pallets with transverse boards can be lifted inside or outside
the area of the load wheels or roll cage.
Loads can be stacked and unstacked and transported over long distances.
The driver's cab is raised together with the load lifting device to provide excellent visibility and easy access to the rack levels to be operated.
The racks must be suitable for the EKS 314. The following safety distances specified
by the manufacturer must be observed:
QwW In order to prevent accidents, whenever a truck is used in rack system aisles
(rail guided) a safety distance of at least 3.54 inch / 90 mm between either
side of the truck and the racks must be maintained.
In case of inductively / wire guided trucks a safety distance of at least
4.92 inch/ 125 mm is recommended.
The ground surface must comply with the floor specifications mentioned above.
Guide rails must be provided in the narrow aisles for the rail guidance system.
Vulkollan guide rollers attached to the truck chassis guide the truck between the
guide rails.
A guidance wire must be routed in the ground for the inductive / wire guidance (WG)
system. The signals from the wire are received on the chassis and processed in the
on-board computer.
The capacity is shown on the data plate, for example:
Travel direction definition:
To indicate travel directions, the following orientations will be used in this manual:
Type Capacity Load center of gravity
EKS 314 3000 lbs / 1360 kg 23.6 inch / 600 mm
Left
Right
Drive
direction
Load
direction
0108.USA
D 2
Open bottom pallets or pallets with transverse boards can be lifted inside or outside
the area of the load wheels or roll cage.
Loads can be stacked and unstacked and transported over long distances.
The driver's cab is raised together with the load lifting device to provide excellent vis-
ibility and easy access to the rack levels to be operated.
The racks must be suitable for the EKS 314. The following safety distances specified
by the manufacturer must be observed:
QwW In order to prevent accidents, whenever a truck is used in rack system aisles
(rail guided) a safety distance of at least 3.54 inch / 90 mm between either
side of the truck and the racks must be maintained.
In case of inductively / wire guided trucks a safety distance of at least
4.92 inch/ 125 mm is recommended.
The ground surface must comply with the floor specifications mentioned above.
Guide rails must be provided in the narrow aisles for the rail guidance system.
Vulkollan guide rollers attached to the truck chassis guide the truck between the
guide rails.
A guidance wire must be routed in the ground for the inductive / wire guidance (WG)
system. The signals from the wire are received on the chassis and processed in the
on-board computer.
The capacity is shown on the data plate, for example:
Travel direction definition:
To indicate travel directions, the following orientations will be used in this manual:
Type Capacity Load center of gravity
EKS 314 3000 lbs / 1360 kg 23.6 inch / 600 mm
Left
Right
Drive
direction
Load
direction

D 3
0108.USA
2 Assemblies and Functional Description
Item Description
1 t Mast
2 t Overhead guard
3 t Safety gates
4 t Safety restraint belt
5 t Control panel
6 t Height-adjustable driver’s position
7 t Chassis
8 t Foot switch/deadman switch
9 t Pallet clamp
t = Standard equipment o = Optional Equipment
1
2
4
3
6
7
5
8
9
D 3
0108.USA
2 Assemblies and Functional Description
Item Description
1 t Mast
2 t Overhead guard
3 t Safety gates
4 t Safety restraint belt
5 t Control panel
6 t Height-adjustable driver’s position
7 t Chassis
8 t Foot switch/deadman switch
9 t Pallet clamp
t = Standard equipment o = Optional Equipment
1
2
4
3
6
7
5
8
9

0108.USA
D 4
2.1 Truck
Safety mechanisms: Side mounted safety gates (3). The driver is also secured by a
safety restraint belt (4). The overhead guard (2) protects the driver from falling objects.
The Emergency Disconnect switch immediately cuts out all truck movements in hazardous situations. Safety gates (3) on either side of the cab disable all truck movements as soon as they are opened.
Travelling, lifting and lowering can only be activated when the foot switch (8) is
pressed.
Drive:
Vertical, heavy-duty threephase motor (asynchronous), hence easy and rapid maintenance. The motor is mounted directly onto the single-wheel driving gear
Brake system:
The truck can be braked gently and wear-free by pulling back the travel control button
or steering in the opposite direction. This feeds energy into the battery (operating
brake).
The electromagnetic spring pressure brake acting on the drive motor serves as a
parking brake and handbrake.
Steering:
Particularly smooth steering with threephase drive system. The handy steering
wheel is integrated within the control panel. The position of the steered drive wheel
is shown in the display unit. The steering angle is +/- 90°, offering maximum
maneuverability in narrow aisles.
With the mechanical rail guidance (RG) system the drive wheel is set to the forward
position at the press of a button.
In wire guidance (WG) mode, steering is automatically assumed by the truck controller when it detects the guidance wire, and manual steering is deactivated.
Controls and displays:
The functions are activated via ergonomic thumb and finger movement to ensure fatigue-free operation without straining the wrists; sensitive application of travel and hydraulic movements to spare and position the goods exactly.
Integrated information display unit for all important driver information such as steering
wheel position, overall lift, truck status reports (e. g. faults), service hours, battery capacity, time and wire guidance status etc.
Hydraulic system:
All hydraulic movements are controlled by a maintenance-free AC motor with a flanged low emission gear pump. Oil is distributed via magnetic switch valves. The varying
oil requirements are controlled by the speed of the motor. During a lowering operation
the hydraulic pump drives the motor which then acts as a generator (regenerative
lowering). The energy produced is then fed back to the battery.
0108.USA
D 4
2.1 Truck
Safety mechanisms: Side mounted safety gates (3). The driver is also secured by a
safety restraint belt (4). The overhead guard (2) protects the driver from falling ob-
jects.
The Emergency Disconnect switch immediately cuts out all truck movements in haz-
ardous situations. Safety gates (3) on either side of the cab disable all truck move-
ments as soon as they are opened.
Travelling, lifting and lowering can only be activated when the foot switch (8) is
pressed.
Drive:
Vertical, heavy-duty threephase motor (asynchronous), hence easy and rapid main-
tenance. The motor is mounted directly onto the single-wheel driving gear
Brake system:
The truck can be braked gently and wear-free by pulling back the travel control button
or steering in the opposite direction. This feeds energy into the battery (operating
brake).
The electromagnetic spring pressure brake acting on the drive motor serves as a
parking brake and handbrake.
Steering:
Particularly smooth steering with threephase drive system. The handy steering
wheel is integrated within the control panel. The position of the steered drive wheel
is shown in the display unit. The steering angle is +/- 90°, offering maximum
maneuverability in narrow aisles.
With the mechanical rail guidance (RG) system the drive wheel is set to the forward
position at the press of a button.
In wire guidance (WG) mode, steering is automatically assumed by the truck control-
ler when it detects the guidance wire, and manual steering is deactivated.
Controls and displays:
The functions are activated via ergonomic thumb and finger movement to ensure fa-
tigue-free operation without straining the wrists; sensitive application of travel and hy-
draulic movements to spare and position the goods exactly.
Integrated information display unit for all important driver information such as steering
wheel position, overall lift, truck status reports (e. g. faults), service hours, battery ca-
pacity, time and wire guidance status etc.
Hydraulic system:
All hydraulic movements are controlled by a maintenance-free AC motor with a flang-
ed low emission gear pump. Oil is distributed via magnetic switch valves. The varying
oil requirements are controlled by the speed of the motor. During a lowering operation
the hydraulic pump drives the motor which then acts as a generator (regenerative
lowering). The energy produced is then fed back to the battery.

D 5
0108.USA
Electrical System:
Service laptop connection interface:
– To configure all the key truck data (limit position damping, lift cutout, retardation
and acceleration patterns, cut-outs etc.) rapidly and reliably.
– To read out the error log to analyse fault causes.
– To simulate and analyse program operations.
– Provides simple functional extension by releasing code numbers.
The controller is fitted with a CAN Bus and a continually measuring sensor system.
The controller provides smooth start-up and braking of the load in all limit positions
through limit position and intermediate cushioning.
Highly efficient threephase technology with energy retention for the drive and lift motors provides high travel and lift speeds and better use of energy.
The MOSFET threephase controller provides smooth starting for all movements.
For drive battery options see section “Battery type“ in chapter F.
3 Standard Version Specifications
NOTICE Technical data specified in accordance with the german standart „Type
sheets for industrial trucks“.
Technical modifications and additions reserved.
3.1 Performance data
RG: Rail Guidance
WG: Wire Guidance
FR: Free Range
Description EKS 314
Q Capacity (where c= 23.6 inch (600 mm)) 3000 lbs 1360 kg
c Load center of gravity distance 23.6 inch 600 mm
Travel speed without load (RG) 6.0 mph 9.6 km/h
Travel speed with load (RG) 6.0 mph 9.6 km/h
Travel speed without load (WG) 4.7 mph 7.5 km/h
Travel speed with load (WG) 4.7 mph 7.5 km/h
Travel speed without load (FR) 6.0 mph 9.6 km/h
Travel speed with load (FR) 6.0 mph 9.6 km/h
Lift speed without load 1.21 ft/s 0.37 m/s
Lift speed with load 1.21 ft/s 0.37 m/s
Lowering speed with load 1.15 ft/s 0.35 m/s
Lowering speed without load 1.12 ft/s 0.34 m/s
D 5
0108.USA
Electrical System:
Service laptop connection interface:
– To configure all the key truck data (limit position damping, lift cutout, retardation
and acceleration patterns, cut-outs etc.) rapidly and reliably.
– To read out the error log to analyse fault causes.
– To simulate and analyse program operations.
– Provides simple functional extension by releasing code numbers.
The controller is fitted with a CAN Bus and a continually measuring sensor system.
The controller provides smooth start-up and braking of the load in all limit positions
through limit position and intermediate cushioning.
Highly efficient threephase technology with energy retention for the drive and lift mo-
tors provides high travel and lift speeds and better use of energy.
The MOSFET threephase controller provides smooth starting for all movements.
For drive battery options see section “Battery type“ in chapter F.
3 Standard Version Specifications
NOTICE Technical data specified in accordance with the german standart „Type
sheets for industrial trucks“.
Technical modifications and additions reserved.
3.1 Performance data
RG: Rail Guidance
WG: Wire Guidance
FR: Free Range
Description EKS 314
Q Capacity (where c= 23.6 inch (600 mm)) 3000 lbs 1360 kg
c Load center of gravity distance 23.6 inch 600 mm
Travel speed without load (RG) 6.0 mph 9.6 km/h
Travel speed with load (RG) 6.0 mph 9.6 km/h
Travel speed without load (WG) 4.7 mph 7.5 km/h
Travel speed with load (WG) 4.7 mph 7.5 km/h
Travel speed without load (FR) 6.0 mph 9.6 km/h
Travel speed with load (FR) 6.0 mph 9.6 km/h
Lift speed without load 1.21 ft/s 0.37 m/s
Lift speed with load 1.21 ft/s 0.37 m/s
Lowering speed with load 1.15 ft/s 0.35 m/s
Lowering speed without load 1.12 ft/s 0.34 m/s

D 7
0108.USA
3.2 Dimensions (as per data plate)
1)
ZT mast performance data measured for 600 DZ.
Description EKS 314
h
1
Mast height (retracted)
1)
109.5 inch 2780 mm
h3Lift
1)
236.2 inch 6000 mm
h4Mast height (extended)
1)
327.6 inch 8320 mm
h6Height above overhead guard 91.3 inch 2320 mm
h7Height 8.3 inch 210 mm
h12Truck height raised
1)
244.5 inch 6210 mm
h15Stockpicking height
1)
307.5 inch 7810 mm
Ast Working aisle width for pallets 39.4 x
47.2 inch (1000 x 1200 mm) trans.
55.1 inch 1400 mm
b1Chassis width 39.4 inch 1000 mm
b5Distance between forks, outer 22.7 -31.3 inch 576 -794 mm
b6Width across guide rollers 51.2 inch 1300 mm
b10Width across front axle 42 inch 1067 mm
l1Overall length w.o. load 118.5 inch 3010 mm
l2Length incl. fork shank 76.4 inch 1940 mm
l Fork length 42 inch 1067 mm
WaTurning radius 66.1 inch 1680 mm
m1Ground clearance below forks 0.98 inch 25 mm
m2Ground clearance from center of
wheelbase
2.56 inch 65 mm
x Load distance 7.5 inch 190 mm
y Wheelbase 59.8 inch 1520 mm
Net weight incl. battery, w.o. load 7672.1 lb 3480 Kg
D 7
0108.USA
3.2 Dimensions (as per data plate)
1)
ZT mast performance data measured for 600 DZ.
Description EKS 314
h
1
Mast height (retracted)
1)
109.5 inch 2780 mm
h3Lift
1)
236.2 inch 6000 mm
h4Mast height (extended)
1)
327.6 inch 8320 mm
h6Height above overhead guard 91.3 inch 2320 mm
h7Height 8.3 inch 210 mm
h12Truck height raised
1)
244.5 inch 6210 mm
h15Stockpicking height
1)
307.5 inch 7810 mm
Ast Working aisle width for pallets 39.4 x
47.2 inch (1000 x 1200 mm) trans.
55.1 inch 1400 mm
b1Chassis width 39.4 inch 1000 mm
b5Distance between forks, outer 22.7 -31.3 inch 576 -794 mm
b6Width across guide rollers 51.2 inch 1300 mm
b10Width across front axle 42 inch 1067 mm
l1Overall length w.o. load 118.5 inch 3010 mm
l2Length incl. fork shank 76.4 inch 1940 mm
l Fork length 42 inch 1067 mm
WaTurning radius 66.1 inch 1680 mm
m1Ground clearance below forks 0.98 inch 25 mm
m2Ground clearance from center of
wheelbase
2.56 inch 65 mm
x Load distance 7.5 inch 190 mm
y Wheelbase 59.8 inch 1520 mm
Net weight incl. battery, w.o. load 7672.1 lb 3480 Kg

0108.USA
D 8
3.3 Mast version
3.4 US Standards
Continuous sound pressure level at ear:
58 db(A)
as per ASME B56.11.5 test procedures ASME
NOTICE The continuous sound level is a value averaged according to standard
regulations, taking the sound pressure level into account when driving, lifting
and idling. The sound pressure level is measured at the ear.
Vibration: a
w,zS
= 3.65 ft/s2 (1.11 m/s2).
NOTICE The swinging acceleration acting on the body in its operating position is the
linear integrated, weighted acceleration in the vertical plane. It is determined
by driving over bumps with a constant speed.
Description EKS 314 (TL/ZT)
h1Retracted height 91.3 - 189 inch 2320 - 4800 mm
h3Lift 118.1 - 315 inch 3000 - 8000 mm
h4Extended height 209.5 - 406.3 inch 5320 - 10320 mm
h6Height above overhead guard 91.3 inch 2320 mm
h12Truck height raised 126.4 - 323.2 inch 3210 - 8210 mm
h15Stockpicking height 189.4 - 386.2 inch 4810 - 9810 mm
Description EKS 314 (TL/DZ)
h1Retracted height 91.3 - 137 inch 2320 - 3480 mm
h3Lift 137.8 - 315.4 inch 3500 - 8010 mm
h4Extended height 229.1 - 406.7 inch 5820 - 10330 mm
h6Height above overhead guard 91.3 inch 2320 mm
h12Truck height raised 146.1 - 323.6 inch 3710 - 8220 mm
h15Stockpicking height 209.1 - 386.6 inch 5310 - 9820 mm
0108.USA
D 8
3.3 Mast version
3.4 US Standards
Continuous sound pressure level at ear:
58 db(A)
as per ASME B56.11.5 test procedures ASME
NOTICE The continuous sound level is a value averaged according to standard
regulations, taking the sound pressure level into account when driving, lifting
and idling. The sound pressure level is measured at the ear.
Vibration: a
w,zS
= 3.65 ft/s2 (1.11 m/s2).
NOTICE The swinging acceleration acting on the body in its operating position is the
linear integrated, weighted acceleration in the vertical plane. It is determined
by driving over bumps with a constant speed.
Description EKS 314 (TL/ZT)
h1Retracted height 91.3 - 189 inch 2320 - 4800 mm
h3Lift 118.1 - 315 inch 3000 - 8000 mm
h4Extended height 209.5 - 406.3 inch 5320 - 10320 mm
h6Height above overhead guard 91.3 inch 2320 mm
h12Truck height raised 126.4 - 323.2 inch 3210 - 8210 mm
h15Stockpicking height 189.4 - 386.2 inch 4810 - 9810 mm
Description EKS 314 (TL/DZ)
h1Retracted height 91.3 - 137 inch 2320 - 3480 mm
h3Lift 137.8 - 315.4 inch 3500 - 8010 mm
h4Extended height 229.1 - 406.7 inch 5820 - 10330 mm
h6Height above overhead guard 91.3 inch 2320 mm
h12Truck height raised 146.1 - 323.6 inch 3710 - 8220 mm
h15Stockpicking height 209.1 - 386.6 inch 5310 - 9820 mm

D 9
0108.USA
Electromagnetic compatibility (EMC)
The manufacturer confirms compliance with the limit values for electromagnetic emission and interference immunity as well as testing of static electricity discharge according to the following table:
Resistance
The following thresholds apply to industrial trucks / systems:
NOTICE Very powerful electromagnetic fields may affect the performance of the truck.
Likewise, equipment that is highly sensitive to electromagnetic fields may in
turn be affected by the truck. Ensure that truck emissions will not affect the
operation of any nearby equipment.
NOTICE Electrical or electronic components and their arrangement may only be
modified after written approval by the manufacturer has been obtained.
3.5 Conditions for application
Ambient temperature:
- during operation: 41 °F (+5 °C) to 104 °F (+40 °C)
24-hour ambient temperature average:
max. 77 °F (25 °C)
max. humidity in interior rooms 70%, no condensation
NOTICE Industrial trucks must be specially equipped and approved for continuous use
in environments with temperatures below 41 °F (5 °C) or in cold stores
respectively with extreme temperatures or humidity changes.
Ambience condition Test Unit
1.1 Frequency
Electromagnetic field
Amplitude modulation
27-1000 *
10
80
MHz
V/m (unmodulated, rms)
% AM (1kHz)
1.2 Frequency
Electromagnetic field
Pulse modulation
900 ± 5
10
50
200
MHz
V/m (unmodulated, rms)
% duty cycle
Hz freq. of recurrence
1.3 Static electricity discharge 4 contact
8 air
discharge
kV (discharge voltage)
* The frequency range has been extended to include low frequencies in the
wiring.
D 9
0108.USA
Electromagnetic compatibility (EMC)
The manufacturer confirms compliance with the limit values for electromagnetic emis-
sion and interference immunity as well as testing of static electricity discharge accord-
ing to the following table:
Resistance
The following thresholds apply to industrial trucks / systems:
NOTICE Very powerful electromagnetic fields may affect the performance of the truck.
Likewise, equipment that is highly sensitive to electromagnetic fields may in
turn be affected by the truck. Ensure that truck emissions will not affect the
operation of any nearby equipment.
NOTICE Electrical or electronic components and their arrangement may only be
modified after written approval by the manufacturer has been obtained.
3.5 Conditions for application
Ambient temperature:
- during operation: 41 °F (+5 °C) to 104 °F (+40 °C)
24-hour ambient temperature average:
max. 77 °F (25 °C)
max. humidity in interior rooms 70%, no condensation
NOTICE Industrial trucks must be specially equipped and approved for continuous use
in environments with temperatures below 41 °F (5 °C) or in cold stores
respectively with extreme temperatures or humidity changes.
Ambience condition Test Unit
1.1 Frequency
Electromagnetic field
Amplitude modulation
27-1000 *
10
80
MHz
V/m (unmodulated, rms)
% AM (1kHz)
1.2 Frequency
Electromagnetic field
Pulse modulation
900 ± 5
10
50
200
MHz
V/m (unmodulated, rms)
% duty cycle
Hz freq. of recurrence
1.3 Static electricity discharge 4 contact
8 air
discharge
kV (discharge voltage)
* The frequency range has been extended to include low frequencies in the
wiring.

0108.USA
D 10
4 Identification points, warning labels and data plates
QwW Warnings and notices such as load diagrams, strap points and data plates
must at all times be legible. Replace if necessary.
Item Description
1 “Pressurized hydraulic system” warning
2 “Emergency drain” decal
3 “Electrical system” warning
4 “Electric voltage” warning
5 “Charger” warning
6 “Explosive gases” warning
7 “Min. battery size” warning
NOTICE Continued on the next page
9
7
1
3
4
2
16
13
14
D (mm)
11
15
9
16
18
8
6
8
3
9
12
8
19
5
10
17
for type "E" industrial trucks with type "E" battery
Built in compliance with ASME B 56.1
0108.USA
D 10
4 Identification points, warning labels and data plates
QwW Warnings and notices such as load diagrams, strap points and data plates
must at all times be legible. Replace if necessary.
Item Description
1 “Pressurized hydraulic system” warning
2 “Emergency drain” decal
3 “Electrical system” warning
4 “Electric voltage” warning
5 “Charger” warning
6 “Explosive gases” warning
7 “Min. battery size” warning
NOTICE Continued on the next page
9
7
1
3
4
2
16
13
14
D (mm)
11
15
9
16
18
8
6
8
3
9
12
8
19
5
10
17
for type "E" industrial trucks with type "E" battery
Built in compliance with ASME B 56.1

D 11
0108.USA
Item Description
8 “Danger of trapping” warning
9 Strapping points for lifting by crane
10 Truck data plate
11 Capacity plate
12 “Trapped / Crushed“ warning
13 “Danger of crashing” warning
14 “Only authorized specialist personnel, hazard listing” notice
15 “Danger when dismantling the pallet clamp” warning
16 Jack contact points
17 Serial number (engraved in chassis underneath the battery cover)
18 “Emergency drain key” decal
19 “Add hydraulic oil” notice
9
7
1
3
4
2
16
13
14
D (mm)
h3 (mm) Q (kg)
11
15
9
16
18
8
6
8
3
9
12
8
19
5
10
17
for type "E" industrial trucks with type "E" battery
Built in compliance with ASME B 56.1
D 11
0108.USA
Item Description
8 “Danger of trapping” warning
9 Strapping points for lifting by crane
10 Truck data plate
11 Capacity plate
12 “Trapped / Crushed“ warning
13 “Danger of crashing” warning
14 “Only authorized specialist personnel, hazard listing” notice
15 “Danger when dismantling the pallet clamp” warning
16 Jack contact points
17 Serial number (engraved in chassis underneath the battery cover)
18 “Emergency drain key” decal
19 “Add hydraulic oil” notice
9
7
1
3
4
2
16
13
14
D (mm)
h3 (mm) Q (kg)
11
15
9
16
18
8
6
8
3
9
12
8
19
5
10
17
for type "E" industrial trucks with type "E" battery
Built in compliance with ASME B 56.1

0108.USA
D 12
4.1 Truck data plate
NOTICE For queries relating to the truck or spare parts orders, please state the truck
serial number (21).
4.2 Capacity
The capacity plate (11) gives the capacity (Q in lbs / kg) of the truck as a function of
the load center of gravity distance (D in inch / mm) and lift height (h3 in inch / mm) in
tabular form.
Item Description Item Description
20 Option 29 Manufacturer's logo
21 Serial number 30 Max. lift height
22 Load center distance 31 Residual lift capacity
23 Year of manufacture 32 Battery weight min.
24 Battery ID 33 Max. Battery capacity
25 Hour Rate 34 System voltage
26 Battery weight max. 35
Weight of truck without battery
+/- 5%
27 Nominal power 36 Rated capacity
28 Manufacturer 37 Model
for type "E" industrial trucks with type "E" battery
Built in compliance with ASME B 56.1
20
21
22
23
24
25
26
27
28
29
37
36
35
34
33
32
31
30
D (mm)
h3 (mm) Q (kg)
D (inch)
h3 (inch) Q (lbs)
11
0108.USA
D 12
4.1 Truck data plate
NOTICE For queries relating to the truck or spare parts orders, please state the truck
serial number (21).
4.2 Capacity
The capacity plate (11) gives the capacity (Q in lbs / kg) of the truck as a function of
the load center of gravity distance (D in inch / mm) and lift height (h3 in inch / mm) in
tabular form.
Item Description Item Description
20 Option 29 Manufacturer's logo
21 Serial number 30 Max. lift height
22 Load center distance 31 Residual lift capacity
23 Year of manufacture 32 Battery weight min.
24 Battery ID 33 Max. Battery capacity
25 Hour Rate 34 System voltage
26 Battery weight max. 35
Weight of truck without battery
+/- 5%
27 Nominal power 36 Rated capacity
28 Manufacturer 37 Model
for type "E" industrial trucks with type "E" battery
Built in compliance with ASME B 56.1
20
21
22
23
24
25
26
27
28
29
37
36
35
34
33
32
31
30
D (mm)
h3 (mm) Q (kg)
D (inch)
h3 (inch) Q (lbs)
11
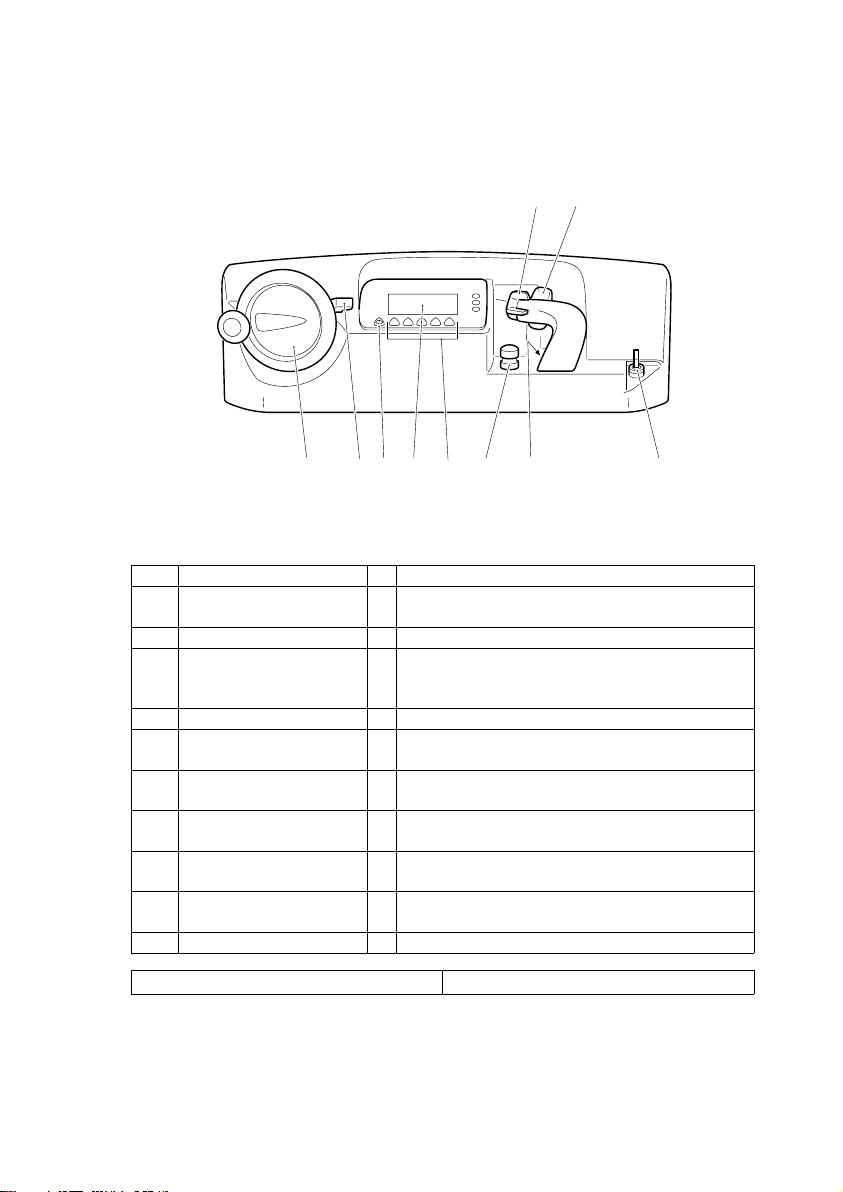
E 1
1005.USA
E Operation
1 Controls and Displays
1.1 Operating and display equipment on control panel
Item Control / Display Function
1 Travel control button t Controls the travel direction and speed of the
truck
2 Hydraulic control switch t Lifting and lowering of main lift
3 Key switch t Switches control current on and off. Removing
the key prevents the truck from being switched
on by unauthorized personnel
4 “Warning” (Horn) button t Sounds Horn, Activates a warning
5 EMERGENCY DISCON-
NECT switch
t Interrupts the main supply, all truck movements
are disabled
6 Buttons (F1 - F5) t Activate or confirm the function related to the
symbol displayed above it
7 Display unit t Operating information and warning message
display
8 “Cancel sub-menu”
switch (F0)
t Sets the menu to the basic display
9 Switch for
“palletclamp”
t Fixes (clamps) and loosens the pallet.
10 Steering wheel t Steers the truck in the required direction
t = Standard equipment o = Optional Equipment
5
1
7910 4 38
6
2
E 1
1005.USA
E Operation
1 Controls and Displays
1.1 Operating and display equipment on control panel
Item Control / Display Function
1 Travel control button t Controls the travel direction and speed of the
truck
2 Hydraulic control switch t Lifting and lowering of main lift
3 Key switch t Switches control current on and off. Removing
the key prevents the truck from being switched
on by unauthorized personnel
4 “Warning” (Horn) button t Sounds Horn, Activates a warning
5 EMERGENCY DISCON-
NECT switch
t Interrupts the main supply, all truck movements
are disabled
6 Buttons (F1 - F5) t Activate or confirm the function related to the
symbol displayed above it
7 Display unit t Operating information and warning message
display
8 “Cancel sub-menu”
switch (F0)
t Sets the menu to the basic display
9 Switch for
“palletclamp”
t Fixes (clamps) and loosens the pallet.
10 Steering wheel t Steers the truck in the required direction
t = Standard equipment o = Optional Equipment
5
1
7910 4 38
6
2