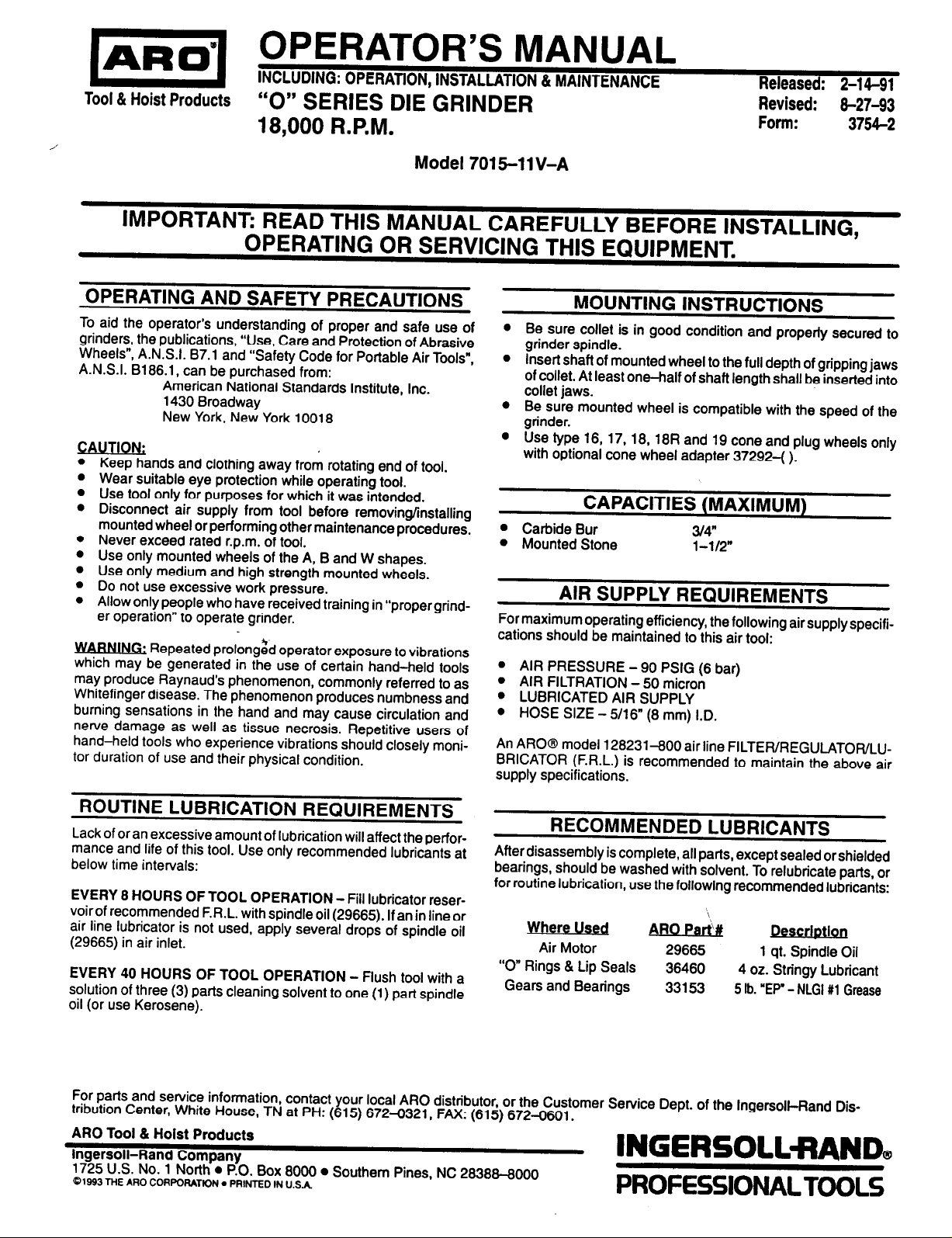
OPERATOR’S MANUAL
INCLUDING: OPERATION, INSTALLATION & MAINTENANCE
Tool & Hoist Products
“0” SERIES DIE GRINDER
18,000 R.P.M.
Model 7015-11V-A
IMPORTANT: READ THIS MANUAL CAREFULLY BEFORE INSTALLING,
OPERATING OR SERVICING THIS EQUIPMENT.
Released: 2-14-91
Revised: 9-27-93
Form:
3754-2
OPERATING AND SAFETY PRECAUTIONS
To aid the operator’s understanding of proper and safe use of
grinders, the publications, “Use, Care and Protection of Abrasive
Wheels”, A.N.S.I. 87.1 and “Safety Code for Portable Air Tools”,
A.N.S.I. B186.1, can be purchased from:
American National Standards Institute, Inc.
1430 Broadway
New York, New York 10016
CAUTION,
l
l
l
l
l
l
l
l
l
WARNING: Repeated prolonged operator exposure to vibrations
which may be generated in the use of certain hand-held tools
may produce Raynaud’s phenomenon, commonly referred to as
Whitefinger disease. The phenomenon produces numbness and
burning sensations in the hand and may cause circulation and
nerve damage as well as tissue necrosis. Repetitive users of
hand-held tools who experience vibrations should closely moni-
tor duration of use and their physical condition.
.
Keep hands and clothing away from rotating end of tool.
Wear suitable eye protection while operating tool.
Use tool only for purposes for which it was intended.
Disconnect air supply from tool before removing/installing
mounted wheel or performing other maintenance procedures.
Never exceed rated r.p.m. of tool.
Use only mounted wheels of the A, B and W shapes.
Use only medium and high strength mounted wheels.
Do not use excessive work pressure.
Allow only people who have received training in “proper grinder operation” to operate grinder.
MOUNTING INSTRUCTIONS
Be sure collet is in good condition and property secured to
grinder spindle.
Insert shaft of mounted wheel to the full depth of gripping jaws
of collet. At least one-half of shaft length shall be inserted into
collet jaws.
Be sure mounted wheel is compatible with the speed of the
grinder.
Use type 16, 17, 18, 18R and 19 cone and plug wheels only
with optional cone wheel adapter 37292-( ).
CAPACITIES (MAXIMUM)
l
Carbide Bur
l
Mounted Stone
3/4”
1-1/2”
AIR SUPPLY REQUIREMENTS
For maximum operating efficiency, the following air supply specifi-
cations should be maintained to this air tool:
l
AIR PRESSURE - 90 PSIG (6 bar)
l
AIR FILTRATION - 50 micron
l
LUBRICATED AIR SUPPLY
l
HOSE SIZE - 5/16” (8 mm) I.D.
An ARO® model 128231-800 air line FILTER/REGULATOR/LUBRICATOR (F.R.L.) is recommended to maintain the above air
supply specifications.
ROUTINE LUBRICATION REQUIREMENTS
Lack of or an excessive amount of lubrication will affect the performance and life of this tool. Use only recommended lubricants at
below time intervals:
EVERY 8 HOURS OF TOOL OPERATION -Fill lubricator reser-
voir of recommended F.R.L. with spindle oil (29665). If an in line or
air line lubricator is not used, apply several drops of spindle oil
(29665) in air inlet.
EVERY 40 HOURS OF TOOL OPERATION - Flush tool with a
solution of three (3) parts cleaning solvent to one (1) part spindle
oil (or use Kerosene).
For parts and service information, contact your local ARO distributor, or the Customer Service Dept. of the Ingersoll-Rand Distribution Center, White House, TN at PH: (615) 672-0321, FAX: (615) 672-0601.
ARO Tool & Hoist Products
Ingersoll-Rand Company
1725 U.S. No. 1 North l P.O. Box 8000 l Southern Pines.
©1993 THE ARO CORPORATlON PRINTED IN U.S.A.
NC 28388-8000
After disassembly is complete, all parts, except sealed or shielded
bearings, should be washed with solvent. To relubricate parts, or
for routine lubrication, use the following recommended lubricants:
“0” Rings & Lip Seals
RECOMMENDED LUBRICANTS
Where Used
Air Motor
Gears and Bearings
ARO Part #
29665
36460
33153
.
Description
1 qt. Spindle Oil
4 oz. Stringy Lubricant
5 lb. “EP” - NLGI #1 Grease
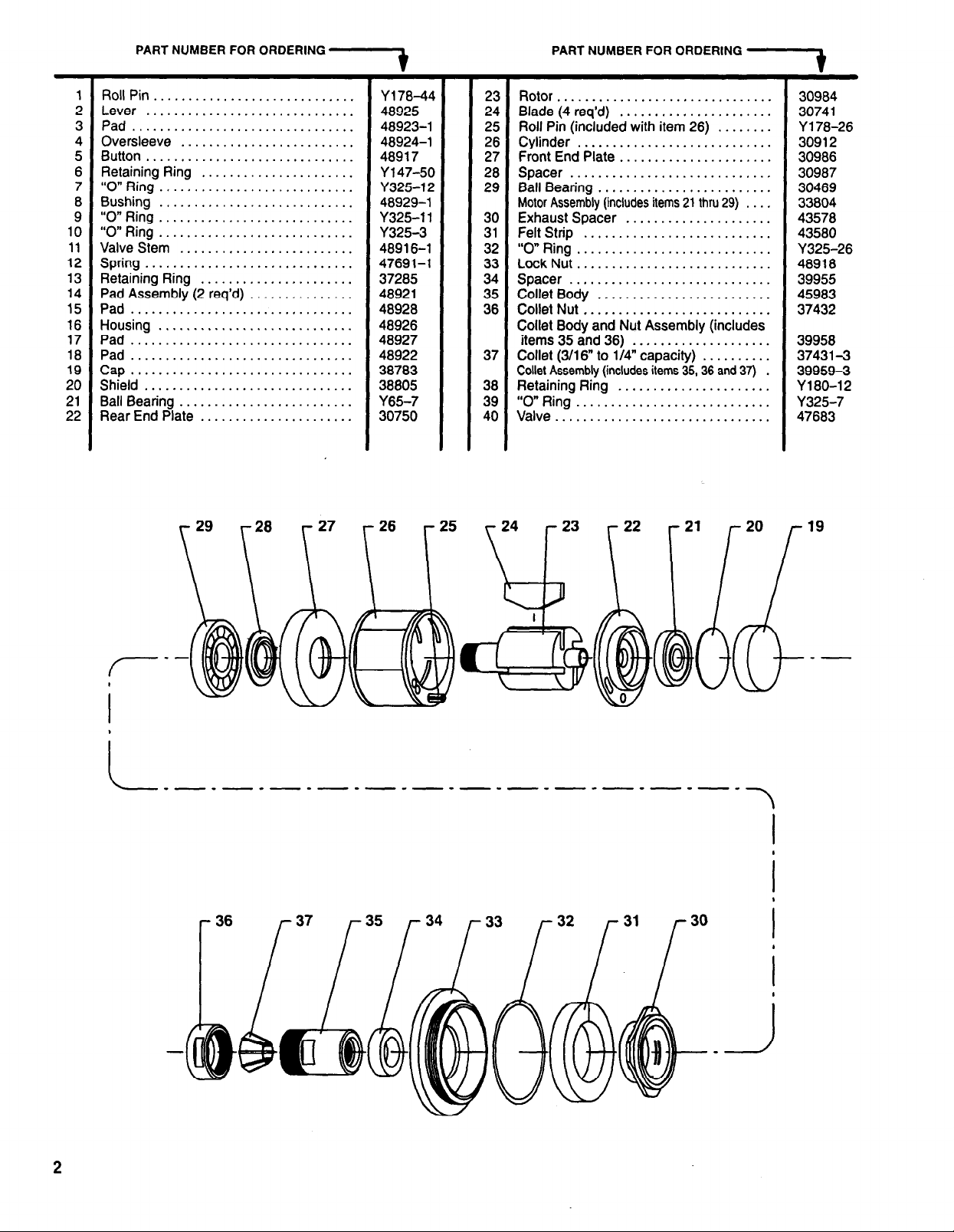
PART NUMBER FOR ORDERING
1
Roll Pin .............................
2
Lever
3
4
5
6
7
..............................
Pad.. ..............................
Oversleeve .........................
Button ..............................
Retaining Ring ......................
“0” Ring ............................
Bushing ............................
9
“0” Ring.. ..........................
10
“0” Ring.. ..........................
11
Valve Stem .........................
12
Spring ..............................
13
Retaining Ring ......................
14
Pad Assembly (2 req’d) ...............
Pad.. ..............................
15
Housing ............................
16
17
Pad.. ..............................
18
Pad.. ..............................
Cap ................................
20
Shield ..............................
21
Ball Bearing .........................
22
Rear End Plate ......................
t
Y178-44
48925
46923-1
48924-1
48917
Y147-50
Y325-12
48929-1
Y325-11
Y325-3
48916-1
47691-1
37285
48921
48928
48926
48927
48922
38783
38805
Y65-7
30750
I -
PART NUMBER FOR ORDERING
Rotor ...............................
23
24
Blade (4 req’d) ......................
Roll Pin (included with item 26) ........
25
Cylinder ............................
28
27
Front End Plate ......................
Spacer .............................
28
Ball Bearing .........................
Motor Assembly (includes items 21 thru 29) ....
Exhaust Spacer .....................
30
31
Felt Strip ...........................
32
“0” Ring.. ..........................
Lock Nut ............................
34
Spacer .............................
35
Collet Body .........................
Collet Nut ...........................
36
Collet Body and Nut Assembly (includes
items 35 and 36) ....................
37
Collet (3/16” to 1/4” capacity) ..........
Collet Assembly (includes items 35, 36 and 37) .
38
Retaining Ring ......................
39
“0” Ring.. ..........................
40
Valve ...............................
t
30984
30741
Y178-26
30912
30966
30987
30469
33804
43578
43580
Y325-26
48918
39955
45983
37432
39958
37431-3
39959-3
Y180-12
Y325-7
47683
21 20
3
19
--