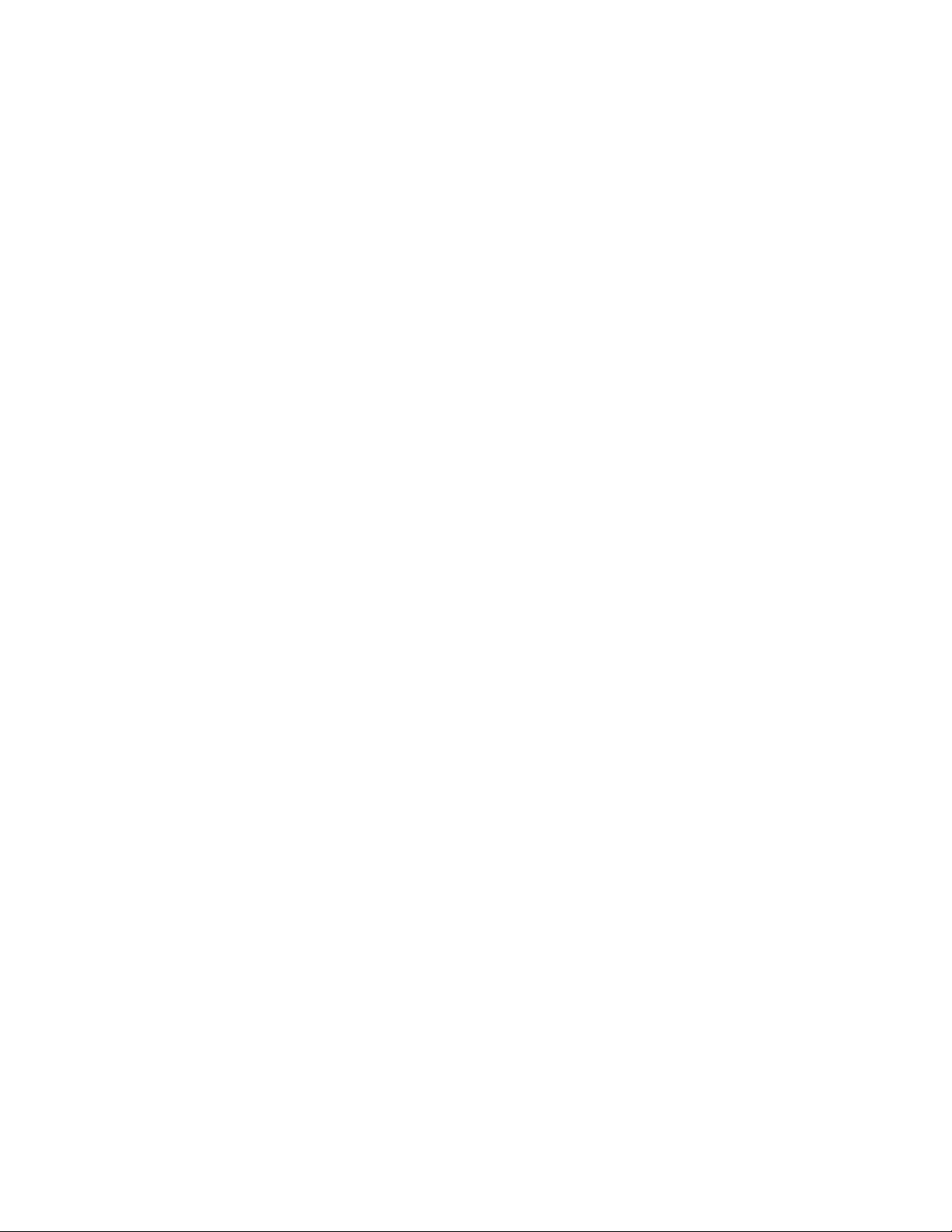
Conventional Powder Metal
Is Still A Technology Leader
Timothy R. Weilbaker, BorgWarner, Inc.
Earl R. Lumpkins, Hoeganaes Corporation
ABSTRACT
Recent advancements in powder metal technology have made it possible to achieve
physical properties rivaling many competitive technologies. Improvements in raw
materials have made powder metal a viable replacement for several malleable and
ductile cast irons. The combination of raw material and processing improvements
continues to push powder metal technology performance into the wrought steel arena.
Nevertheless, in the midst of all of these technological advancements, conventional
powder metallurgy is still providing innovation in torque transfer systems. At
BorgWarner’s TorqTransfer Systems division, conventional powder metallurgy has
found application in six separate components of the newly created interactive torque
management system dubbed ITM. This patented torque transfer device provides the
all-wheel drive technology for MotorTrends SUV of the year – the Honda Acura MDX.[4]
This paper describes how conventional powder metal technology provided the perfect
solution for this highly innovative torque transfer technology.
INTRODUCTION
Technological advances are common in every industry today. Within the automotive
industry, in particular, constant innovation is the only way for a company to survive and
grow. Innovation was exactly what was required to revolutionize the traditional fourwheel drive systems used in rear-wheel drive vehicles. Once the electromechanical
design was created, the components had to be manufactured. If the components of this
technology were not equally innovative, some aspect of the new torque transfer system
would be jeopardized. To meet these critical requirements, powder metallurgy (P/M)
was researched, designed and application tested to demonstrate that indeed
conventional P/M was both an effective and economical solution for this newly
developed ITM torque transfer system.
The goals of this paper are: 1) to briefly describe the various types of torque
management systems, 2) to provide an overview of the Interactive Torque Management
1
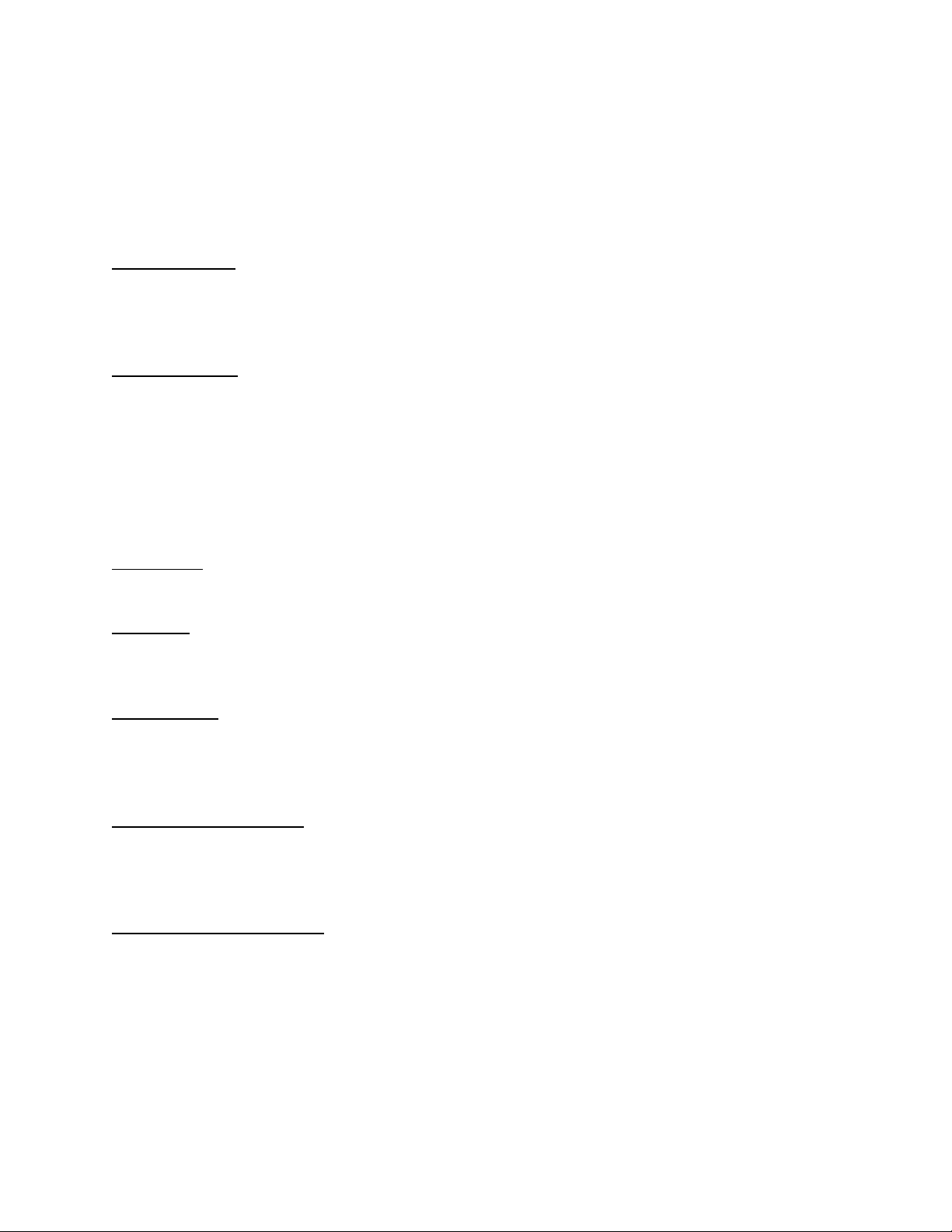
(ITM) system, 3) to describe the P/M components utilized in the ITM system, and 4) to
show how conventional P/M technology, even today, can still be used to create
innovation in automotive systems.
TYPES OF TORQUE MANAGEMENT SYSTEMS
In all types of torque management systems the primary axle is driven by a direct
connection. The secondary axle is driven by a number of different methods including [1]:
Viscous Clutch - A viscous clutch is a conceptually simple viscous device which resists
relative motions. This device does not deliver torque to the secondary axle until a
relative speed exists between the propshafts. The amount of torque delivered is a
function of the relative speed until a hump event occurs.
Gerotor Pumps - There are two types of gerotor pump systems. A single gerotor pump
system pressurizes a hydraulic piston and applies a clutch pack when a relative speed
occurs. This type of system has the two pump elements driven by the two output
shafts. A twin gerotor pump develops a differential pressure when there is a speed
difference between the shafts where the differential pressure applies a clutch pack.
This type of system has one pump driven by the input member of the secondary
driveline and the second pump driven by the output member. The clutch pack is applied
by the difference in pressure between the two pumps.
Visco-Lock - A viscous pump using silicon fluid develops pressure on a clutch pack
when a difference in speed exists between the two output shafts.
Hydraulic - An externally controlled hydraulic system can be used to apply a clutch pack
using a piston. A control valve modulates the pressure delivered to a clutch pack. A
hydraulic circuit or an electronic controller modulates the control valve.
Roller Clutch - A roller clutch activated system allows the secondary shaft to rotate
faster than the primary but will not allow the primary to rotate faster than the secondary.
These devices are maintained in proper orientation by a friction plate to ground or an
electromagnetic clutch.
Electromagnetic Clutch - An electrically actuated clutch and an electronic controller
causes a magnetic field to be developed resulting in friction in proportion to the field
strength. This type of clutch may use a mechanical amplification device creating a
clamp load on a secondary clutch pack.
Mechanically Clutch Pack - A clutch pack applied by a cam mechanism. The cam is
actuated by an electric or hydraulic mechanism.
INTERACTIVE TORQUE MANAGEMENT
An Interactive Torque Management device is an active torque management device that
does not deliver torque to a secondary axle until acted upon by some outside force.
The controller for this outside force is in constant communication with other vehicle
systems. These systems include braking control (ABS), traction control (TCS) and
2
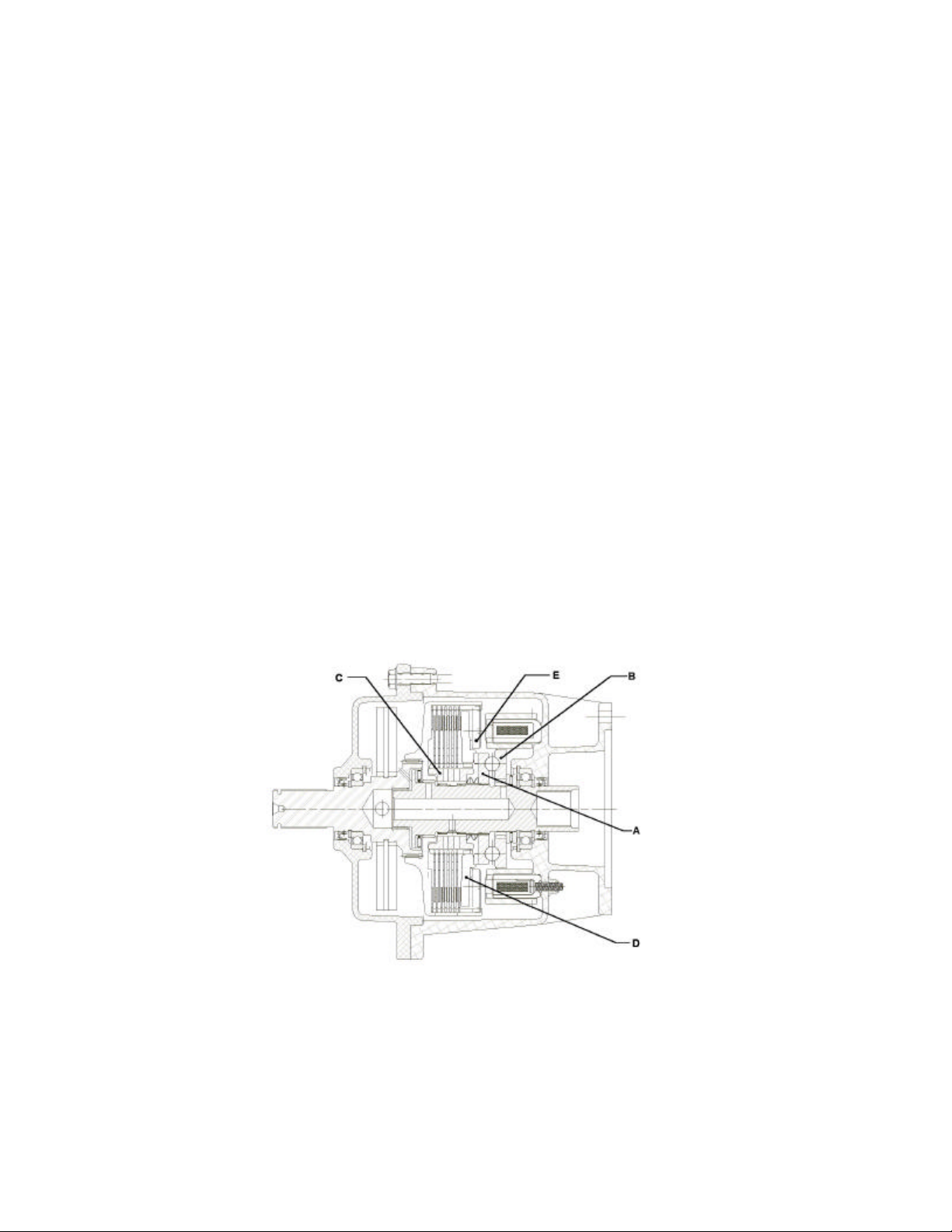
stability control (ESP). Further, only those systems that maintain communication or
Figure 1: ITM Cross Sectional View
systems that transfer torque at a variable rate qualify as ITM devices. Consequently, a
device is an active one if it delivers torque as required and can engage/disengage to
support the function of other handling systems. [1]
BorgWarner ITM I TECHNOLOGY
The device shown in Figure 1 is the latest generation of the BorgWarner ITM I
technology. This device is an electromagnetic actuated multi-plate wet friction clutch
mechanism, which is capable of maintaining constant communication with vehicle
dynamic systems as well as adapting to road conditions. The ITM I is intended to
control distribution of torque between primary and secondary axles. The ITM I utilizes
an electromagnetic primary clutch consisting of an electronic coil, a rotor, friction plates
and an armature ring. The rotor surrounds the stationary electronic coil and rotates at
the same speed as the secondary axle pinion. The primary friction plates are
alternately splined to the input housing and the base cam. The armature ring is adjacent
to the friction rings and is splined to the input housing. The armature applies pressure
to the rings when sufficient current is passed through the coil to attract the armature and
friction rings to the rotor. This attraction leads to torque transfer across the ball cam
mechanism. [1] [2]
The cam mechanism amplifies the force from the primary clutch to the secondary clutch.
The cam mechanism consists of an apply cam and base cam with corresponding ball
ramp pockets and a multiple number of balls. The apply cam is splined to the output
shaft and the base cam is acted upon by the input housing when the electronic coil is
energized. When the primary clutch is engaged, torque is applied to the base cam,
which is free to rotate about the output shaft. [1] [2]
3