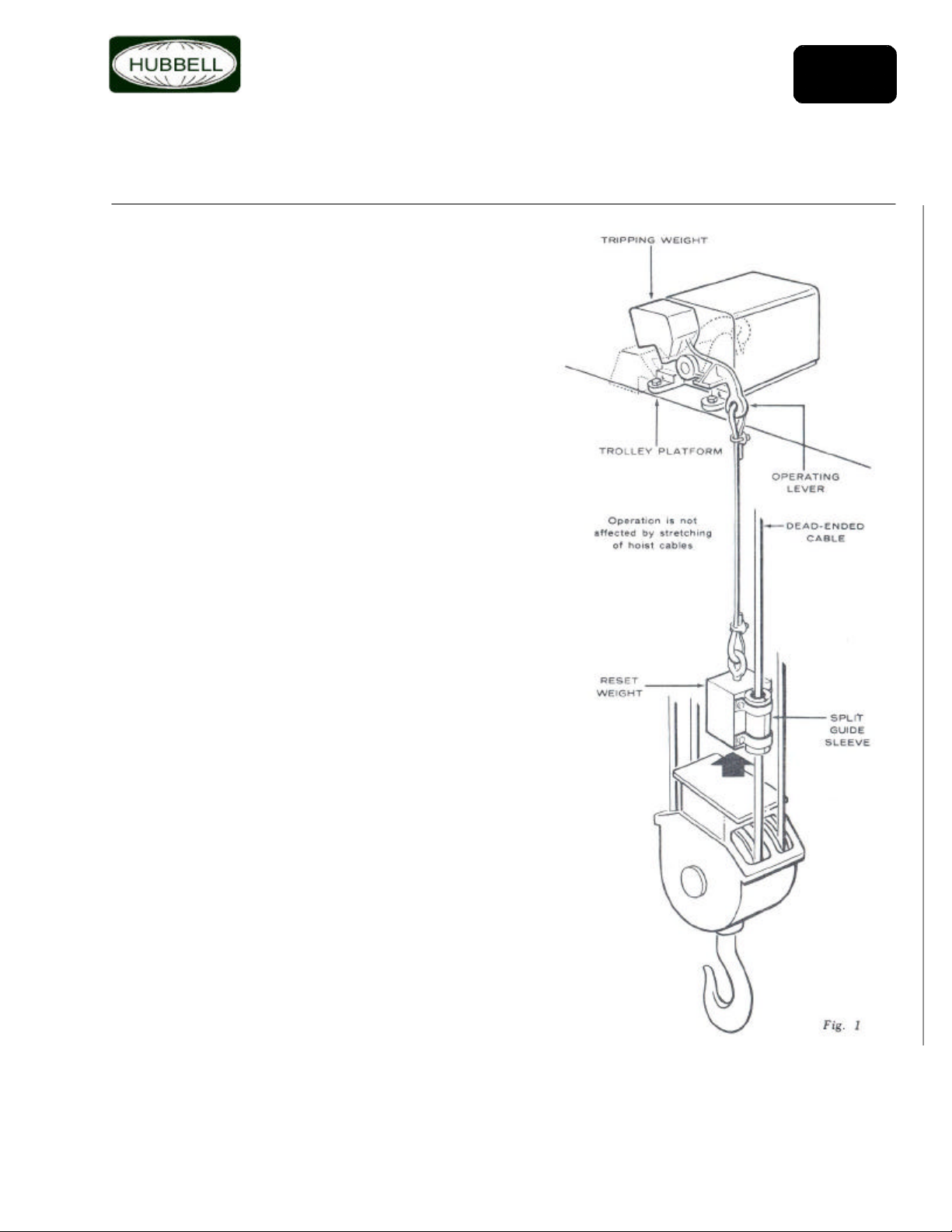
Hubbell Industrial Controls, Inc.
INSTALLATION & MAINTENANCE INSTRUCTIONS
POWER LIMIT SWITCHES
EUCLID™ SIZE 2, 3, 4, 5, 6, & 6A
General
The EULCID™ Power Limit Switch is a device well
suited for crane hoist overtravel protection in repetitively worked applications and under severe environmental conditions. Maintenance requirements obviously will vary with service conditions. Even though
the device has been carefully designed to minimize
maintenance due to wear and adverse environmental
conditions, a periodic inspection and maintenance
program is mandatory in the interests of insuring
maximum protection.
The following sections treat various components of
the limit switch with suggested installation and maintenance practice.
Installation
4220
EUCLID™ Power Limit Switches must always be
mounted with shaft in horizontal position with mounting feet down. Under no circumstances attempt to
mount up side down. Provide adequate support under
each of the three mounting feet.
Install the split-sleeve reset weight guide around the
dead-ended cable, see Fig. 1. A bracket or striker
plate may be attached to the hook block, if necessary,
to lift the suspended weight when hoisting. Be sure
that the reset weight is positively engaged by the hook
block during hoisting under all conditions of hook
swing. Add additional guiding means to reset weight if
necessary to insure engagement by hook block.
Provide clearance or opening in Trolley platform so
that tripping weight cannot be prevented from dropping slightly below level of mounting feet. This clearance, or opening for the trip weight insures positive
switch action by preventing dirt buildup. Avoid the use
of sheave wheels or lever systems which can introduce friction in reset weight cable assembly and retard free action of tripping weight.
Right hand operation as shown, is furnished unless
otherwise specified. Field changing from right hand to
left hand operation is accomplished by turning trip arm
around and making proper electrical connections.
Terminal markings only are involved by this change.
Refer to wiring diagram for proper connections.
Maintenance
Periodic inspection for contact wear should be performed. The size 3 and 6A contacts have a silver inlay. When the silver inlay is worn, both sets of contacts should be renewed, see Fig. 5 for allowable
wear. Size 2, 4, 5 & 6 switches have solid copper
contacts as standard. Both sets of contacts should be
renewed when the contacts are worn, see Fig. 5 for
allowable wear. It is recommended that both the
movable and stationary contacts be renewed at the
same time.
Contact renewal steps are outlined in the following
procedure.
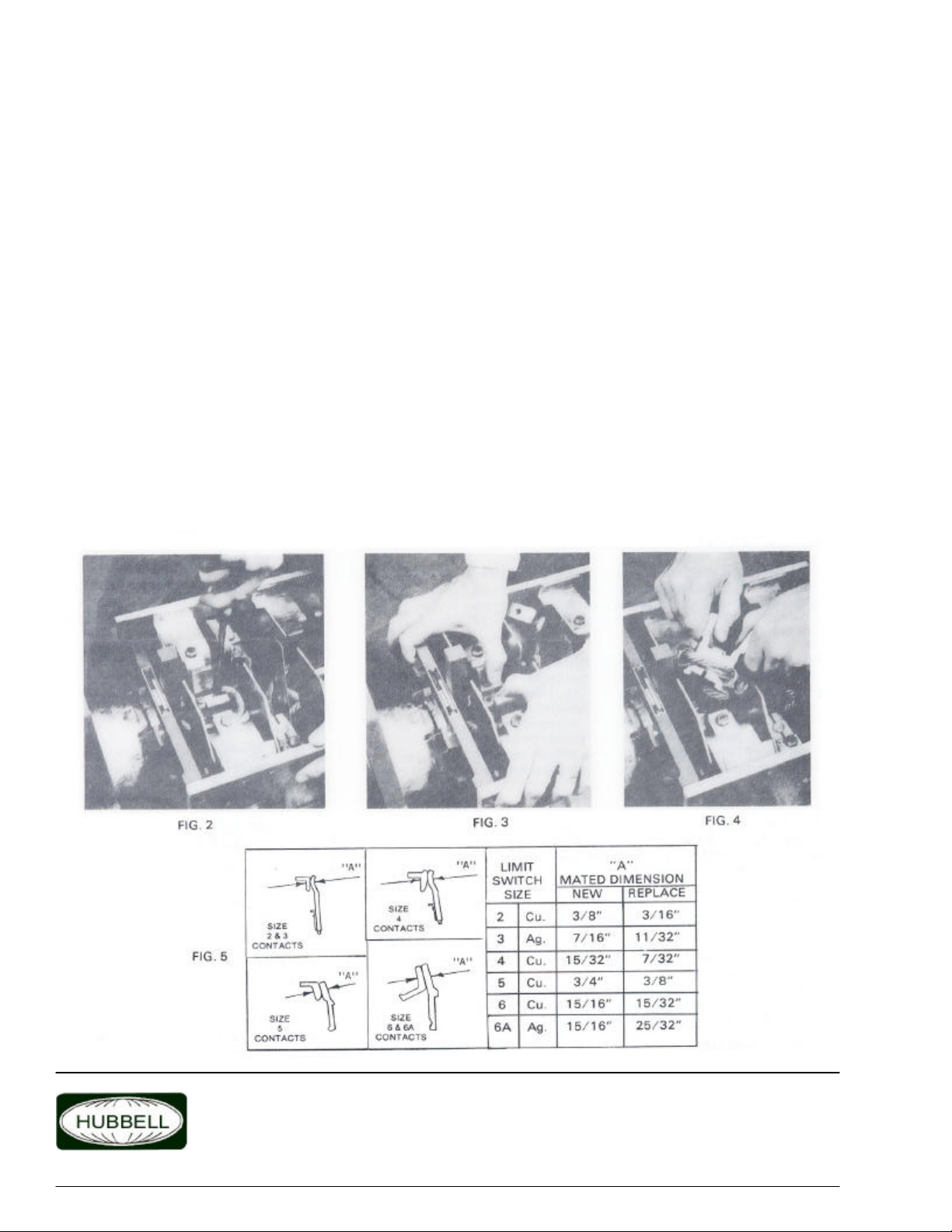
STATIONARY CONTACTS
LUBRICATION
If stationary contacts are to be changed, remove them
before attempting to change the moving contacts.
When replacing do so after moving contact assembly
has been replaced. This observance will make the
change of moving contacts easier but is not mandatory.
MOVING CONTACTS
1. Raise operating lever to mid-trip position and place
block under lever to support in this position against
hook weight.
2. Remove moving contact spring pressure by lifting
lock lever. This frees moving contact assembly for
easy removal.
3. Disconnect shunt lead from stationary terminal.
4. Remove two slotted head screws from finger holder
– figure (2). Force contacts apart and at the same
time lift up – figure (3). Remove assembly – figure
(4).
5. Change contacts making sure all contact surfaces
are thoroughly clean and connections are tightened
securely.
6. Replace assembly including contact holder and
spring, making sure shunt leads are properly
positioned to prevent chafing on adjacent parts.
1. Shaft bearings are of the permanently lubricated,
sealed type and should not require attention.
2. Torsion operation spring – Occasional
application of a Molybdenum-Disulfide grease
should suffice to minimize wear and friction
between turns.
LOCK LEVERS
These parts must work freely and should be tested
occasionally by lifting with finger. A non-gumming type
oil only should be applied to the pivot bearing once
every few months – The Nylatron roller bearing needs
no oil. A whip of lubriplate occasionally on the polished
end of the lever will reduce friction and give better
action.
FRAME AND COVER
Ample electrical clearance has been provided for
possible conductive dirt build-up in bottom of frame.
This should be cleaned out on an annual basis or
oftener if conditions warrant. Always replace cover
after inspection to minimize entrance of dirt and foreign
objects.
ER-384-2M
Hubbell Industrial Controls, Inc.
A subsidiary of Hubbell Inc.
4301 Cheyenne Dr., Archdale, NC 27263
Telephone (336) 434-2800 • FAX (336) 434-2803
http://www.hubbell-icd.com
sales@hubbell-icd.com