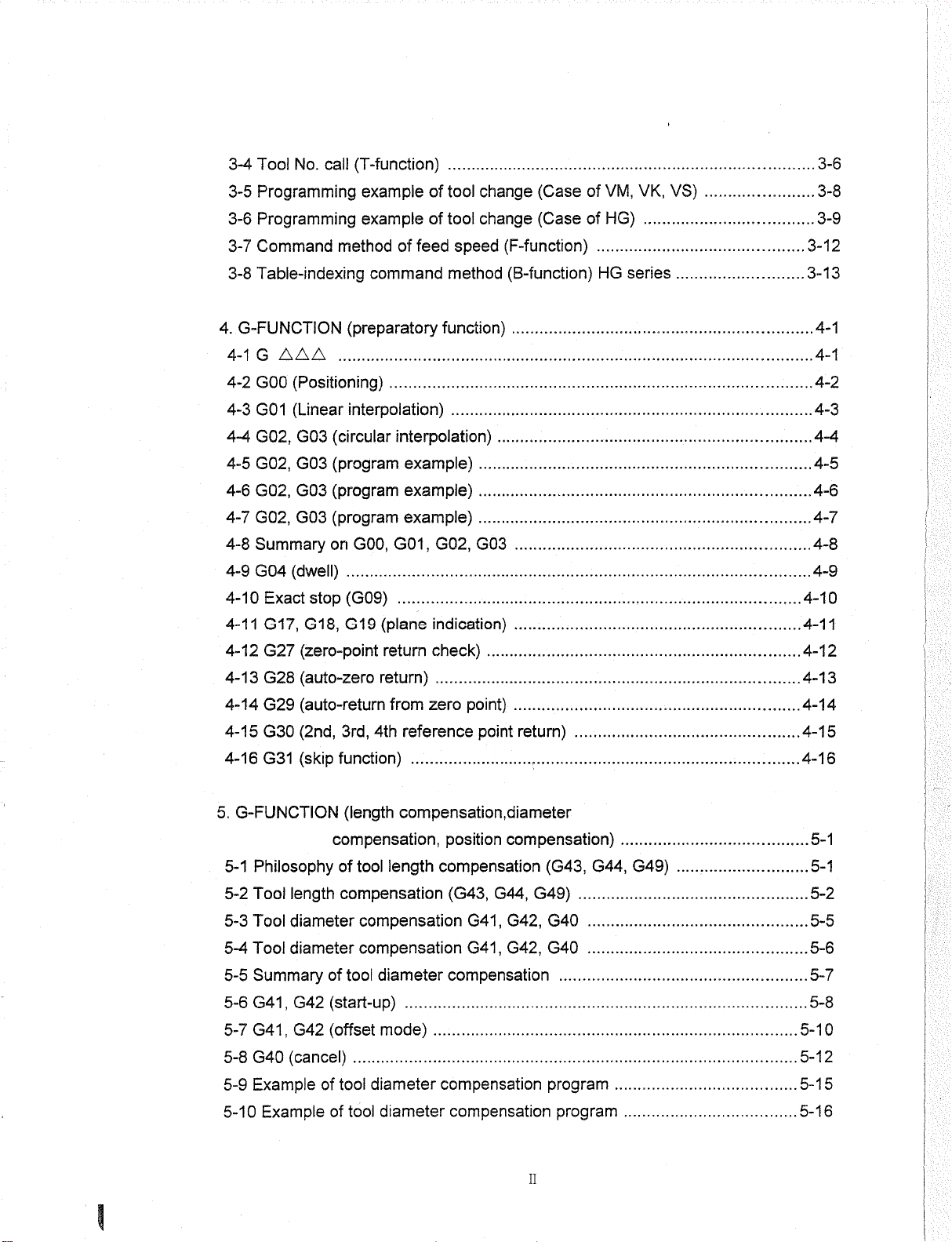
3-4
Tool
Programming
3-5
Programming
3-6
No.
call
(T-function)
example
example
of
of
tool
tool
change
change
of
(Case
(CaseofHG)
VM,
VK,
VS)
3-6
3-8
3-9
Command
3-7
Table-indexing
3-8
G-FUNCTION
4.
AAA
G
4-1
GOO
4-2
4-3
4-4
4-5
4-6
4-7
4-8
4-9
4-10
4-11
4-12
4-13
4-14
4-15
4-16
(Positioning)
(Linear
G01
G02,
G02,
G02,
G02,
Summary
(dwell)
G04
Exact
G17,
G27
G28
G29
G30
G31
method
(preparatory
interpolation)
(circular
G03
G03
(program
(program
G03
(program
G03
GOO,
on
(G09)
stop
G19
G18,
(zero-point
(auto-zero
(auto-return
(2nd,
3rd,
function)
(skip
of
feed
command
interpolation)
example)
example)
example)
G01,
(plane
return
return)
4th
indication)
check)
zero
from
reference
.....
speed
method
function)
G02,
(F-function)
(B-function)
G03
.
point)
return)
point
. .
3-12
HG
series
3-13
4-1
4-1
4-2
4-3
4-4
4-5
4-6
4-7
4-8
4-9
.
4-10
4-11
4-12
4-13
4-14
4-15
4-16
5.
G-FUNCTION
Philosophy
5-1
length
Tool
5-2
5-3
Tool
diameter
Tool
5-4
5-5
5-6
5-7
5-8
5-9
5-10
diameter
Summary
G41,G42
G42
G41,
(cancel)
G40
Example
Example
(length
compensation,
compensation,
length
tool
of
compensation
compensation
compensation
tool
tool
tool
diameter
mode)
diameter
diameter
of
(start-up)
(offset
of
of
diameter
position
compensation
(G43,
compensation
compensation
compensation
compensation)
G44,
G41,
G42,
G41,
G42,
II
(G43,
G49)
G40
G40
program
program
G44,
.
G49)
5-1
5-1
5-2
5-5
5-6
5-7
5-8
5-10
5-12
5-15
5-16
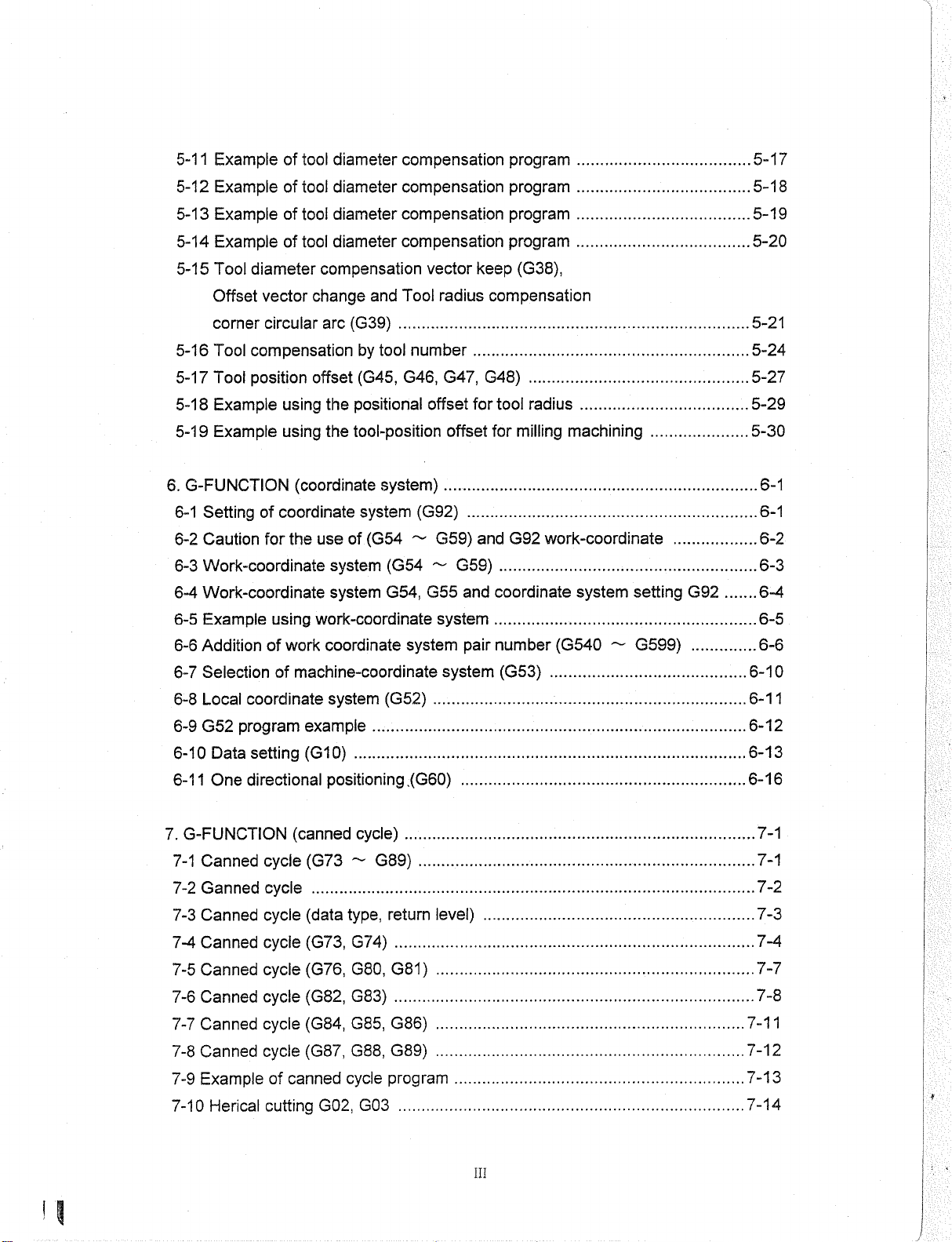
5-1
1
Example
of
tool
diameter
compensation
program
5-17
5-12
Example
3
Example
5-1
5-14
Example
5-15
Tool
Offset
corner
Tool
5-16
Tool
5-17
Example
8
5-1
Example
5-1
9
G-FUNCTION
6.
6-1
Setting
Caution
6-2
6-3
Work-coordinate
Work-coordinate
6-4
Example
6-5
Additionofwork
6-6
6-7
Selection
6-8
Local
G52
Data
One
program
6-9
6-10
6-11
tool
of
of
of
diameter
vector
circular
diameter
diameter
tool
tool
diameter
compensation
change
arc
compensation
position
of
offset
using
using
(coordinate
coordinate
use
the
for
using
work-coordinate
the
the
system
system
coordinate
machine-coordinate
of
coordinate
setting
directional
system
example
(G10)
positioning
compensation
compensation
compensation
Tool
and
(G39)
tool
number
G46,
by
(G45,
positional
tool-position
system)
system
(G54
of
(G92)
~
(G54
G54,
system
(G52)
.(G60)
vector
radius
G47,
offset
offset
G59)
G59)
~
G55
system
system
program
program
program
(G38),
keep
compensation
G48)
tool
for
and
and
pair
radius
milling
for
G92
coordinate
number
(G53)
..
machining
work-coordinate
system
setting
.
(G540
~
G599)
G92
5-18
5-19
5-20
5-21
5-24
5-27
5-29
5-30
6-1
6-1
6-2
6-3
6-4
6-5
6-6
6-10
6-11
6-12
6-13
6-16
'
G-FUNCTION
7.
Canned
7-1
Ganned
7-2
7-3
Canned
7-4
Canned
7-5
Canned
Canned
7-6
7-7
Canned
Canned
7-8
Example
7-9
Herical
7-10
(canned
cycle
cycle
cycle
cycle
cycle
cycle
cycle
cycle
canned
of
cutting
(G73
(data
(G73,
(G76,
(G82,
(G84,
(G87,
G02,
cycle)
~
type,
G74)
G80,
G83)
G85,
G88,
cycle
G03
G89)
return
G81)
G86)
G89)
program
level)
7-1
7-1
7-2
7-3
7-4
7-7
7-8
7-11
7-12
7-13
7-14
III
f
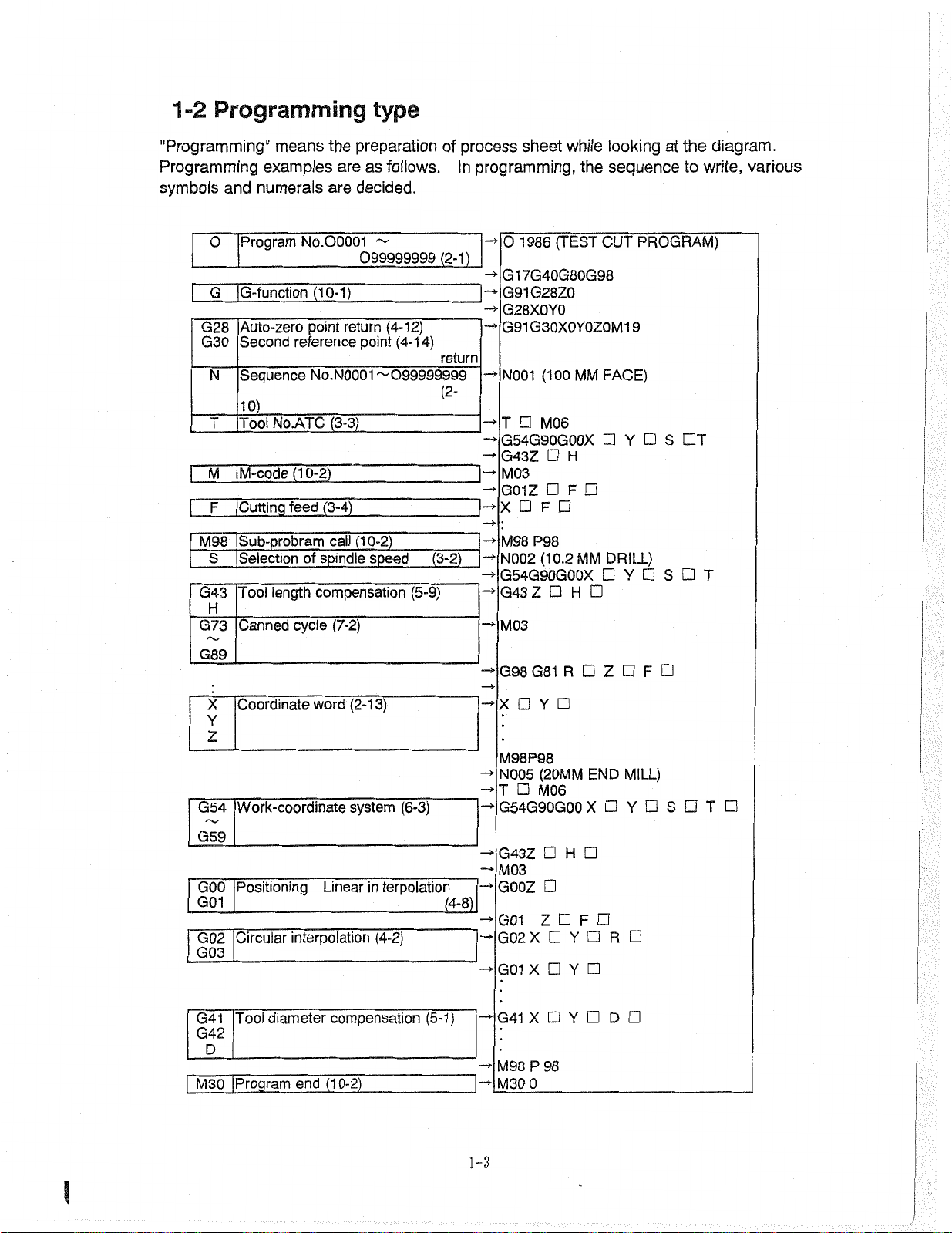
Programming
1-2
type
"Programming"
Programming
symbols
O
|
G
G28
G30
N
examples
numerals
and
Program
iG-function
Auto-zero
Second
Sequence
101
Tool
T
|
|
jM-code
M
Cutting
|
F
M98
jSub-probram
Selection
S
Tool
G43
H
G73
Canned
means
No.00001
preparation
the
as
are
are
decided.
~
099999999
(10-Tf
point
return
reference
No.N0001~099999999
No.ATC
(10-2)
feed
of
length
cycle
point
(3-3)
(3-4)
(10-2)
call
spindle
compensation
speed
(7-2)
follows.
(4-12)
(4-14)
(5-9)
process
of
In
programming,
(2-1)
return
(2-
-»
(3-2)
-»
while
sheet
the
(TEST
1986
O
G17G40G80G98
G91G28Z0
G28X0Y0
G30X0Y0Z0M
G91
(100
N001
M06
T
G54G90G00X
G43Z
M03
G01Z
F
X
P98
M98
(10.2
N002
G54G90G00X
G43Z
M03
H
F
H
MM
MM
CUT
FACE)
looking
at
sequence
PROGRAM)
9
1
S
Y
DRILL)
Y
S
the
to
DT
write,
T
diagram.
various
|
G03
G41
G42
M30
G89
Coordinate
X
Y
Z
I
Work-coordinate
G54
G59
Positioning
GOO
G01
Circular
G02
__
[Tool
D
iProgram
word
interpolation
diameter
end
(2-13)
system
Linear
compensation
(10-2)
terpolation
in
(4-2)
(6-3)
(4-8)
(5-1)
G98
G81
X
M98P98
N005
T
G54G90GOO
G43Z
M03
G00Z
G01
G02X
G01
X
-*
G41
X
!
P
M98
M30
0
R
Y
(20MM
M06
H
Z
Y
Y
Y
98
END
X
F
Z
R
D
F
MILL)
Y
T
S
l-3
I
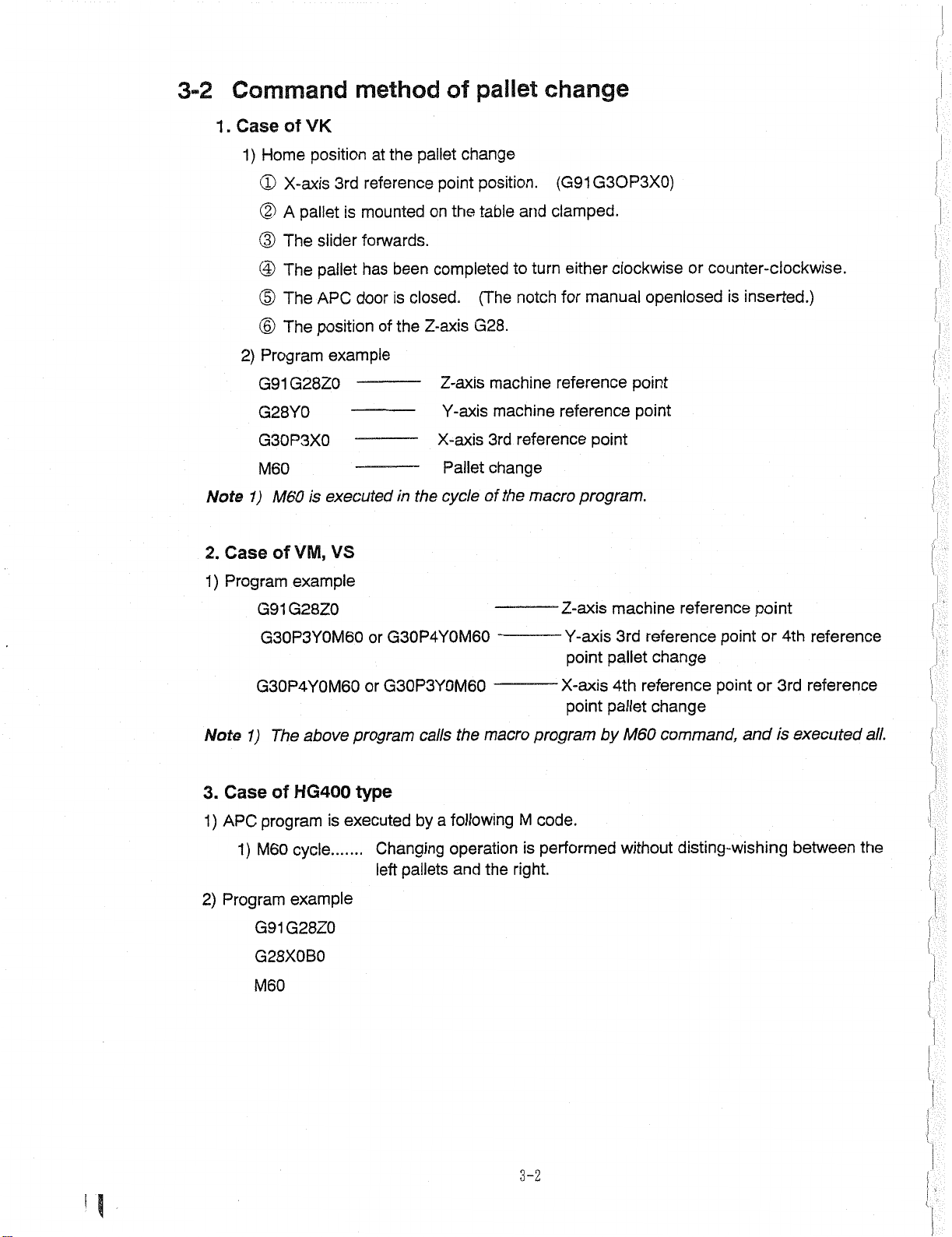
3-2
Command
method
of
pallet
change
.
1
Note
Case
2.
Case
of
1)
Home
X-axis
<2>
(D
A
(D
The
@
The
(D
The
The
©
Program
2)
G91G28Z0
G28Y0
G30P3X0
M60
M60
1)
ofVSVS,
VK
position
3rd
pallet
slider
pallet
APC
position
example
is
executed
VS
at
reference
mounted
is
forwards.
has
door
of
the
been
closed.
is
the
the
in
change
pallet
point
the
on
completed
Z-axis
Z-axis
Y-axis
X-axis
Pallet
cycle
position.
and
table
to
notch
(The
G28.
machine
machine
reference
3rd
change
the
of
(G91
clamped.
either
turn
for
reference
reference
macro
G3OP3X0)
clockwiseorcounter-clockwise.
inserted.)
manual
point
point
program.
openlosed
point
is
!;
!
i
,
Program
1)
Note
Case
3.
APC
1)
Program
2)
example
G91G28Z0
G30P3Y0M60
G30P4Y0M60
1)
1)
M60
G91G28Z0
G28X0B0
M60
above
The
HG400
of
program
cycle
example
Z-axis
program
M
code.
performed
is
right.
-Y-axis
X-axis
point
G30P4Y0M60
or
G30P3Y0M60
or
the
following
a
operation
and
macro
the
program
type
executed
is
.......
calls
by
Changing
left
pallets
point
machine
3rd
pallet
4th
pallet
by
M60
without
reference
reference
change
reference
change
command,
disting-wishing
point
point
or
4th
3rd
or
point
andisexecuted
between
reference
reference
all.
;
the
(
3-2