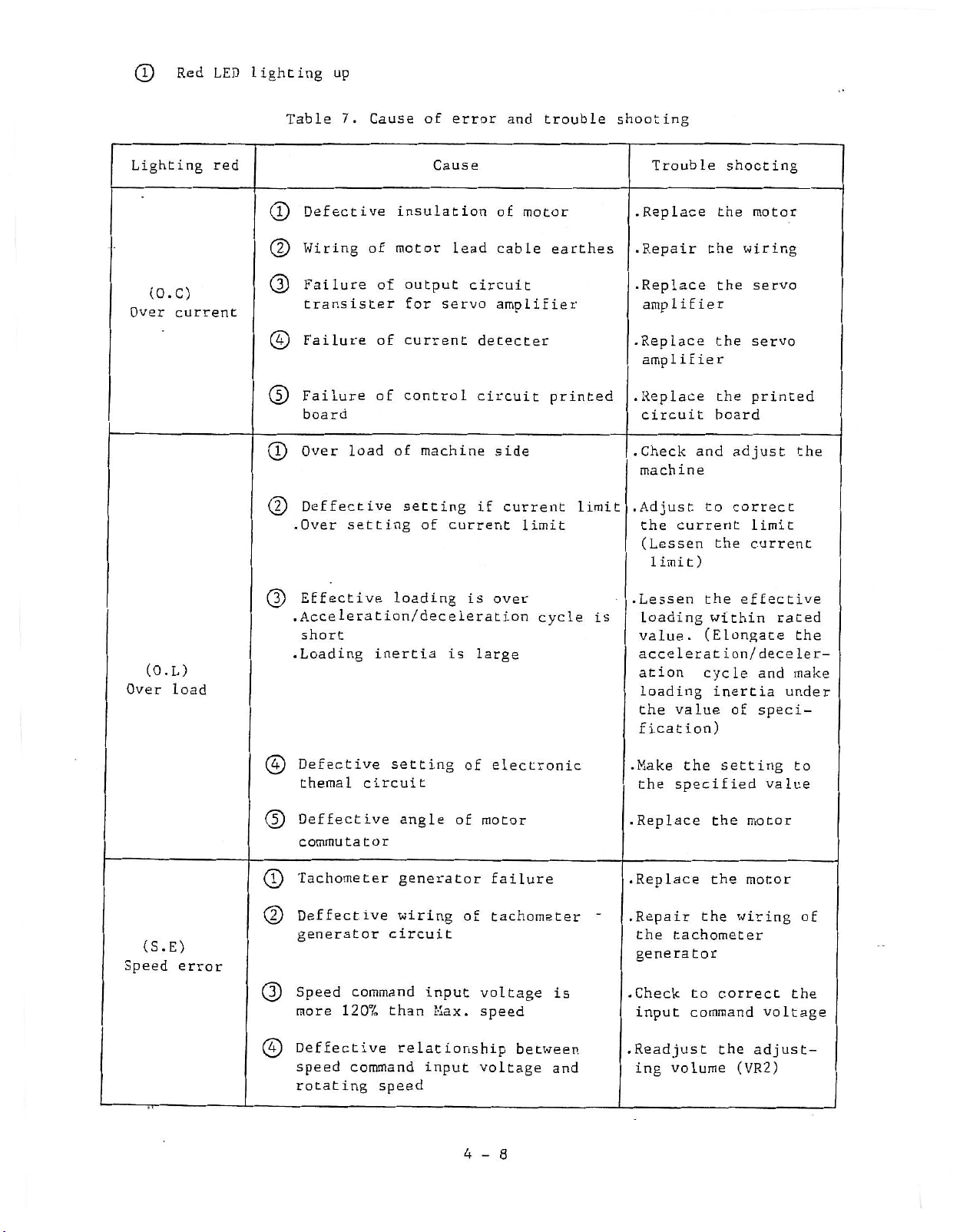
(T)
Red
LED
lighting
up
Lighting
(O.C)
Over
current
red
(T)
(2)
(3)
(4)
(J)
(T)
(2)
Table
Defective
Wiring
Failure
transister
Failure
Failure
board
Over
Deffective
•Over
7.
load
setting
Cause
of
of
of
of
of
Cause
insulation
motor
output
for
current
control
of
machine
setting
of
error
lead
servo
current
of
cable
circuit
amplifier
detecter
circuit
side
if
and
motor
current
limit
trouble
earthes
printed
limit
shooting
Trouble
.Replace
.Repair
.Replace
amplifier
•Replace
amplifier
•Replace
circuit
.Check
machine
.Adjust
the
(Lessen
1
imi
and
current
)
t
the
the
the
the
the
board
to
the
shooting
motor
wiring
servo
servo
printed
adjust
correct
limit
current
the
(O.L)
Over
(S.E)
Speed
load
error
(3)
Effective
loading
.Acceleration/deceleration
short
inertia
circuit
command
120%
setting
angle
generator
wiring
circuit
than
(4)
(5)
(T)
(2)
(3)
•Loading
Defective
themal
Deffective
commutator
Tachometer
Deffective
generator
Speed
more
input
Max.
is
of
of
is
over
large
of
electronic
motor
failure
tachometer
voltage
speed
cycle
is
.Lessen
is
.Make
.Replace
.Replace
.Repair
.Check
the
loading
value.
within
(Elongate
acceleration/
ation
loading
the
fication)
the
the
genera
input
cycle
inertia
value
the
specified
the
the
the
tachometer
tor
to
command
effective
of
setting
motor
motor
wiring
correct
rated
the
deceler¬
and
make
under
speci¬
to
value
the
voltage
of
(4)
Deffective
speed
rotating
command
relationship
speed
input
voltage
4-8
between
and
.Readjust
volume
ing
the
adjust¬
(VR2)