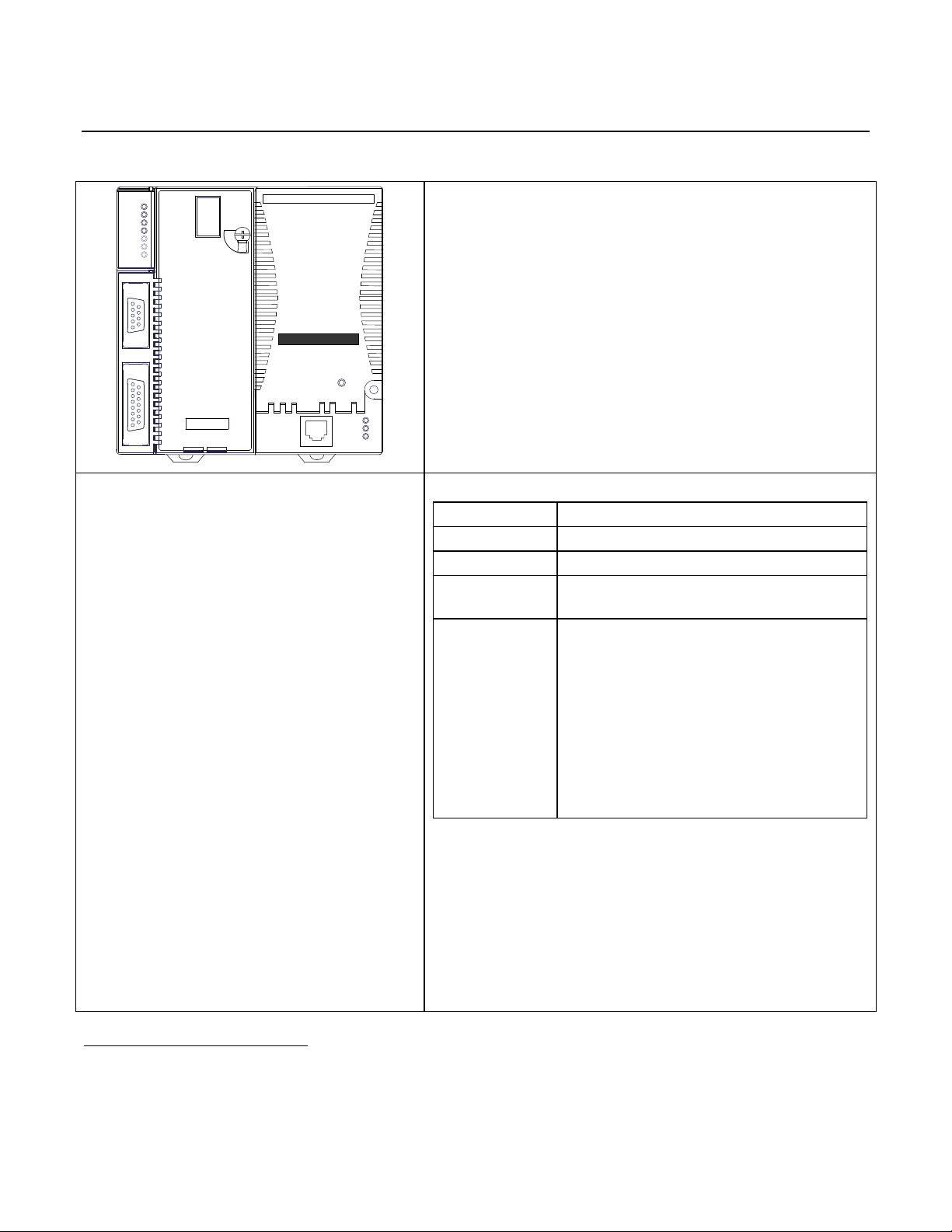
Important Product Information VersaMax*
IC200CPUE05 shares the basic features of the other VersaMax*
PLC CPUs. It provides powerful PLC functionality in a small,
versatile system. CPUE05 can serve as the system controller for up
to 64 modules with up to 2048 I/O points. Two serial ports provide
RS-232 and RS-485 interfaces for serial communications. CPUE05
also provides a built-in Ethernet Interface. The RS-232 serial port
can be configured for Local Station manager operation to provide
access to diagnostic information about the Ethernet interface.
CPUE05 has 128KB of configurable memory.
In addition, CPUE05 is compatible with the EZ Program Store
device, which can be used to write, read, update, and verify
programs, configuration, and reference table data without a
programmer or programming software.
Features
▪ Supports up to 64 modules with up to 2048 I/O
points
▪ Can be either auto-configured or configured
from a programmer using configuration software
▪ 128KB of configurable memory for the
application program, hardware configuration,
registers (%R), analog inputs (%AI), and analog
outputs (%AQ)
▪ Programming in Ladder Diagram and
Instruction List
▪ Non-volatile flash memory for program storage
▪ Battery backup for program, data, and time of
day clock
▪ Super capacitor provides power to memory for
1 hour
- Over 1 hour, backup battery protects memory
contents up to 6 months.
- Backup battery has shelf life of 5 years when
not in use.
▪ Run/Stop switch
▪ Floating point (real) data functions
▪ Embedded RS-232, RS-485, and Ethernet
communications
▪ 70mm height when mounted on DIN rail with
power supply (sold separately)
VersaPro software version 2.0 or later and
Machine Edition Logic Developer.
Expansion I/O
Compatibility
All types of I/O and communications modules can
be used in expansion racks. Some analog
modules require specific module revisions in
expansion racks, as listed below:
Module Module Revision
ALG320 B or later
ALG321 B or later
ALG322 B or later
ALG430 C or later
ALG431 C or later
ALG432 B or later
IC200CPUE05
GFK-1892TW CPU with Embedded Ethernet Interface
December 2016
*
Indicates a trademark of General Electric Company and/or its subsidiaries. All other trademarks are the property of their respective
owners.
© 2001-2016 General Electric Company. All Rights Reserved.
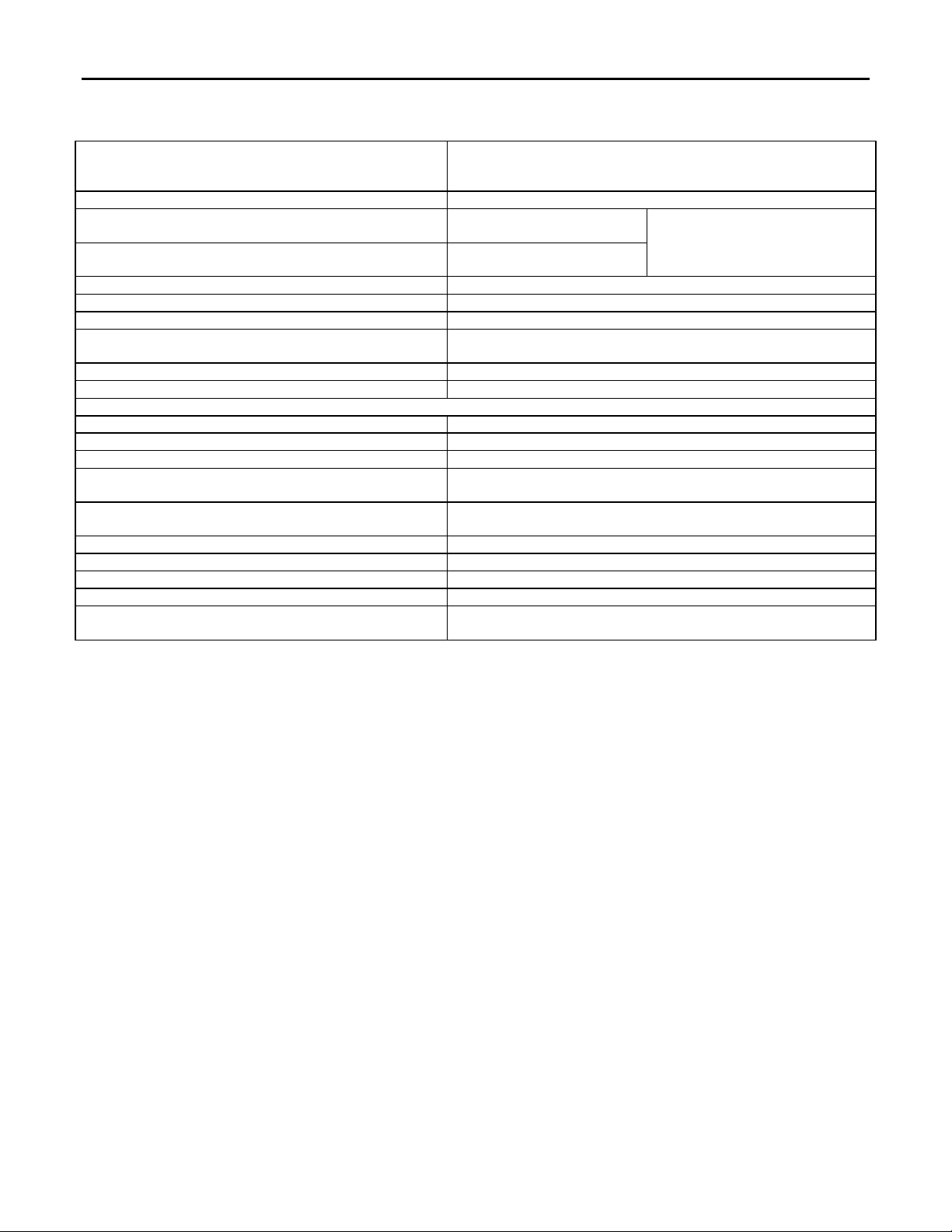
2 CPU with Embedded Ethernet Interface
Width: 4.95” (126mm) - along DIN rail
Length: 5.04” (128mm)
Depth: 2.72” (69.1mm)
System flash, battery-backed RAM
Power Supply current consumption with no serial port
converter or EZ Program Store device
Power Supply current consumption with serial port
converter or EZ Program Store device
5Vdc uses: 320mA
Floating point
Real time clock accuracy (for timer functions)
100ppm (0.01%) or ±9sec/day
Time of day clock accuracy
23ppm (0.0023%) or ±2sec/day @ 30°C.
100ppm (0.01%) or ±9sec/day @ full temperature range
Ethernet Interface Specifications
10Mbps (half- or full-duplex)
Number of SRTP server connections
Number of Ethernet Global Data (EGD) configuration-based
exchanges
100 data ranges per exchange
1400 bytes of data per exchange
EGD Selective Consumption
Load EGD configuration from PLC to programmer
Remote Station Manager over UDP
Local Station Manager
(RS-232)
GFK-1892TW IC200CPUE05
Specifications: IC200CPUE05
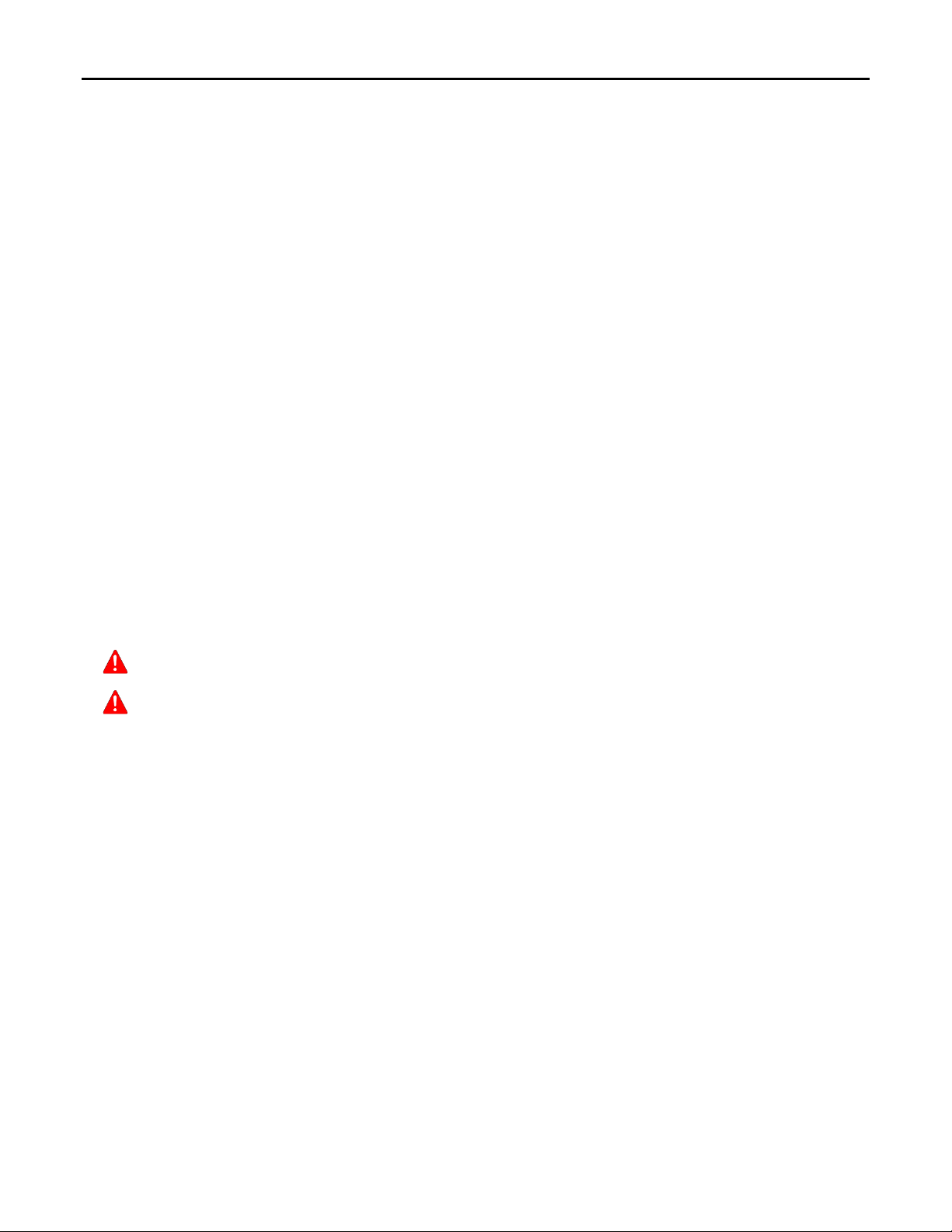
CPU with Embedded Ethernet Interface 3
IC200CPUE05 GFK-1892TW
EMC Installation Requirements
To meet EN 55011 and FCC Class A radiated emissions, the Control system in which the IC695PNC001 module is used
shall be mounted in a metal enclosure when three or more IC695PNC001 modules are used. All surfaces of the
enclosure must be adequately grounded to adjacent surfaces to provide electrical conductivity. Wiring external to the
enclosure must be routed in metal conduit or the equivalent. The conduit must be mounted to the enclosure using
standard procedures and hardware to ensure electrical conductivity between the enclosure and conduit.
When installing, operating, or maintaining the IC695PNC001, personnel must insure any electrostatic charge is
discharged through the use of a grounded ESD strap or other means.
Installation Location
This product is intended for use with the VersaMax system. Its components are considered open equipment (having live
electrical parts that may be accessible to users) and must be installed in an ultimate enclosure that is manufactured to
provide safety. At a minimum, the enclosure shall provide a degree of protection against solid objects as small as 12mm
(fingers, for example). This equates to a NEMA/UL Type 1 enclosure or an IEC60529 IP20 rating providing at least a
pollution degree 2 environment. For details about installing VersaMax rack systems, refer to VersaMax Modules, Power
Supplies and Carriers User's Manual, GFK-1504.
Installation in Hazardous Areas
The following information is for products bearing the UL marking for Hazardous Areas or ATEX marking for explosive
atmospheres:
CLASS 1 DIVISION 2 GROUPS ABCD
This equipment is an open-type device and is meant to be installed in an enclosure suitable for the
environment that is only accessible with the use of a tool.
Suitable for use in Class I, Division 2, Groups A, B, C and D Hazardous Locations, or nonhazardous locations
only.
Warning – EXPLOSION HAZARD - SUBSTITUTION OF COMPONENTS MAY IMPAIR SUITABILITY FOR CLASS I,
DIVISION 2.
Warning – EXPLOSION HAZARD – DO NOT CONNECT OR DISCONNECT EQUIPMENT UNLESS POWER HAS BEEN
SWITCHED OFF OR THE AREA IS KNOWN TO BE NON-HAZARDOUS.
ATEX Zone 2
This module must be mounted in an enclosure certified in accordance with EN60079-15 for use in Zone 2, Group IIC and
rated IP54. The enclosure shall only be able to be opened with the use of a tool.

4 CPU with Embedded Ethernet Interface
GFK-1892TW IC200CPUE05
Quick Start
Installation and initial startup procedures for the CPUE05 include the following steps. Before installing and operating the
CPUE05, refer to VersaMax PLC User's Manual, GFK-1503 for detailed information.
Pre-Installation check
Carefully inspect all shipping containers for damage. If any equipment is damaged, notify the delivery service
immediately. Save the damaged shipping container for inspection by the delivery service. After unpacking the
equipment, record all serial numbers. Save the shipping containers and packing material in case it is necessary to
transport or ship any part of the system.
Module Installation
This equipment may be mounted on a horizontal or vertical DIN rail. If mounted on a vertical DIN rail, the CPU module
must be located at the bottom. The CPU and connecting carriers must be installed on the same section of 35mm (1.38in)
x 7.5mm (.3in) DIN rail, 1mm (.04in) thick. Steel DIN rail is recommended. The DIN rail must be electrically grounded to
provide EMC protection. The rail must have a conductive (unpainted) corrosion-resistant finish. DIN rails compliant with
DIN EN50022 are preferred. For vibration resistance, the DIN rail should be installed on a panel using screws spaced
approximately 15.24cm (6in) apart.
Rated thermal specifications for the CPU module are based on a clearance of 50.8mm (2in) above and below the
equipment and 25.4 mm (1 inch) to the left of the CPU module.
1. Allow sufficient finger clearance for opening CPU door.
2. Allow adequate clearance for serial port and Ethernet cables.
3. Allow adequate space for power wiring.
The CPU with power supply attached fits into a 70mm (2.76in) deep enclosure.
Installing the CPU on the DIN Rail
The CPU snaps easily onto the DIN rail. No tools are required for mounting or grounding to the DIN rail.
Before joining module carriers to the CPU, remove the connector cover on the right-hand side of the CPU. Do not
discard this cover: you will need to install it on the last carrier, to protect the connector pins from contamination and
damage during use.

CPU with Embedded Ethernet Interface 5
Caution
Battery may explode if mistreated.
Do not recharge, disassemble, heat above 100°C (212°F), or incinerate.
IC200CPUE05 GFK-1892TW
Panel-Mounting
If excessive vibration is a factor, the CPU should also be screwed down to the mounting panel.
Note 1. Tolerances are ±0.13mm (0.005in) non-cumulative.
Note 2. 1.1-1.4Nm (10-12 in/lbs) of torque should be applied to M3.5 (#6-32) steel screw threaded into material
containing internal threads and having a minimum thickness of 2.4mm (0.093in).
Removing the CPU from the DIN Rail
1. Turn off power to the power supply.
2. (If the CPU is attached to the panel with a screw) remove the power supply module. Remove the panel-mount
screw.
3. Slide the CPU away from the other modules until the connector on the right side disengages from the next carrier.
4. With a small flathead screwdriver, pull the DIN rail latch outward while tilting the other end of the module down to
disengage it from the DIN rail.
Activating or Replacing the Backup Battery
The CPU is shipped with a battery already installed. The battery holder is located in the top side of the CPU module.
Before the first use, activate the battery by pulling and removing the insulator tab.
To replace the battery, use a small screwdriver to gently pry open the battery holder. Replace battery only withACC001
from your PLC supplier, or with Panasonic battery: BR2032. Use of another battery may present a risk of fire or
explosion.