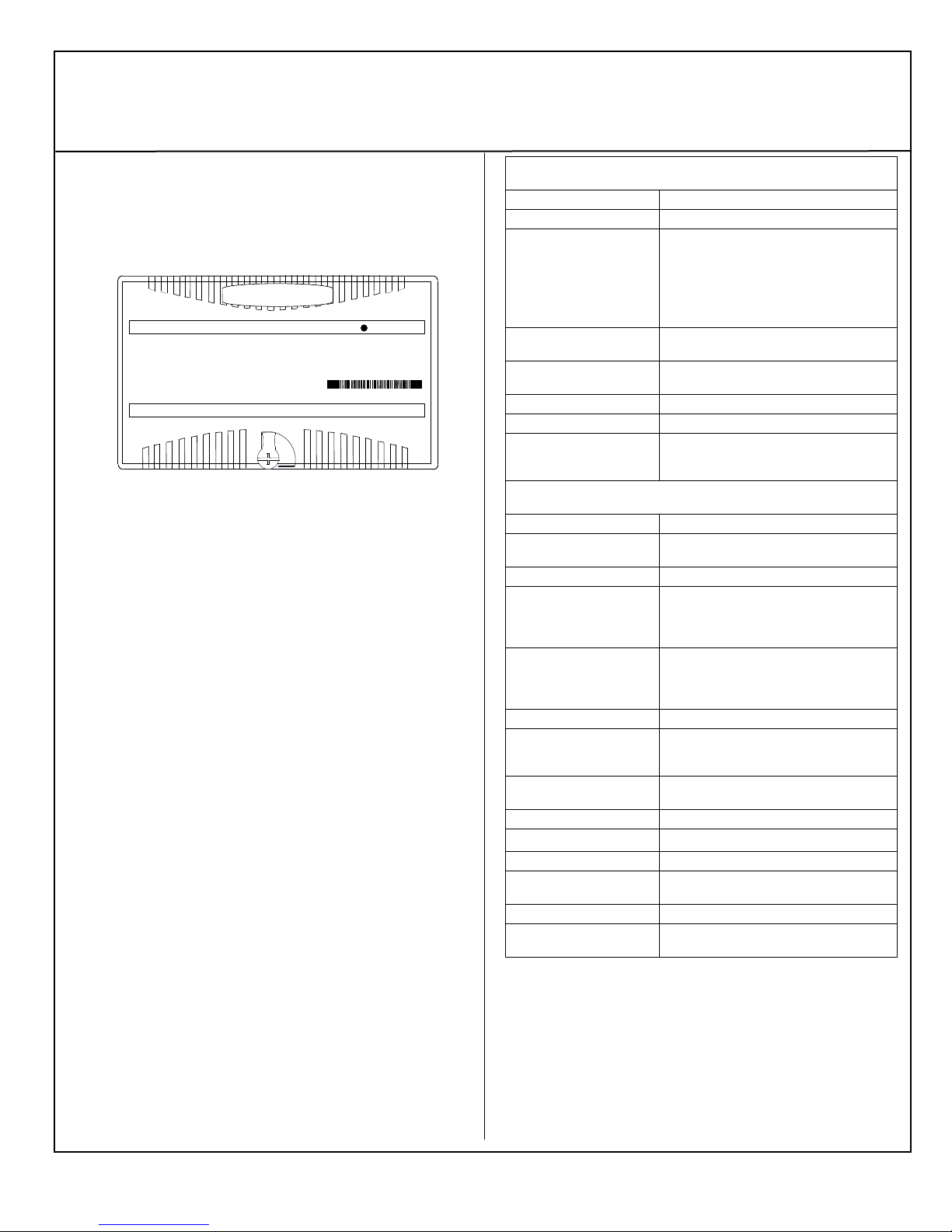
VersaMax* Analog Input, 16-Bit Thermocouple Module
ANALOG INPUT 16BIT
THERMOCOUPLE 7CH
Seven thermocouple or millivolt inputs
Isolation:
User input to logic
(optical) and to frame
ground
Group to group
Channel to channel
250VAC continuous; 1500VAC for 1 minute
Not applicable
None
OK LED: Green indicates backplane power is
present. Amber indicates module fault.
Backplane current consumption
5V output: 125mA maximum. 3.3V output: 125mA
maximum.
Open Thermocouple, over/under range, and
high/low alarm, thermistor fault (reported as
internal fault).
J, K, T, S, R, none (used for mV inputs)
19.5mV, 39mV, 78.125mV, 156.25mV, 312.5mV,
625mV
Cold junction compensation
If used, reference junction temperature is
measured at thermocouple termination using a
precision thermistor, or supplied by system, or by
fixed configuration value.
Cold junction temperature error
+/–0.25 degree Celsius (local measurement). To
reduce temperature transients, thermocouple
terminations should not be installed in the same
cabinet as heat dissipation assemblies.
+/–0.3 degree Celsius, +/–0.5 degree Fahrenheit.
Accuracy, at 25° C
on voltage measurement:
on temp. measurement:
+/–0.2%
+/- 3 degrees Celsius.
Temperature sensitivity
(0° to 60°C)
+/–0.004% of reading, +/–1.5µV per ° Celsius
referred to input
60dB, at 50/60 Hz, 100% span
120 dB at 50/60Hz, 100 ohm imbalance
Maximum voltage between
channels
60 Hz: approximately 60 milliseconds per point
50 Hz: approximately 70 milliseconds per point.
IC200ALG630
October 2016 GFK-1700L
Product Description
The IC200ALG630 Analog Input Thermocouple Module is an intelligent
module that accepts seven independent thermocouple or millivolt inputs.
The module receives power from the backplane power supply. No
external power source is required.
Each input channel can be configured to report millivolts ranges as
1/100 of millivolts, or thermocouple inputs as linearized temperature in
tenths of degrees Celsius or Fahrenheit, with or without cold junction
compensation.
The module automatically performs A/D calibration at powerup.
Automatic calibration is then repeated periodically to compensate for
changes in the ambient temperature. New calibration values are filtered
into the current calibration values.
Host Interface
The Analog Input Thermocouple Module uses the following data types:
7 words of analog input data.
7 optional words of analog output data.
The module exchanges data in the same manner as other types of I/O
modules: it provides all its input data when requested.
Diagnostics
The Analog Input Thermocouple Module performs diagnostics and
provides the following information.
Alarm faults are reported if the processed value for a channel
exceeds its configured alarm limit.
Over/underrange faults are reported if the millivolt value for an
input exceeds the limits of its span.
Open circuit is checked every time a thermocouple input is read
(unless Open TC checking is disabled). If the circuit is open, a fault
is reported and the input defaults to the configured channel default.
Thermistor fault will be reported as Internal fault in the I/O Fault
table.
A thermistor fault occurs if the calculated temperature value from the
thermistor is less than -10 °C or greater than +75 °C.
LED Indicators
The green OK LED is on when backplane power is present to the
module. If this LED is amber, it indicates a module fault.
Preinstallation Check
Carefully inspect all shipping containers for damage. If any equipment
is damaged, notify the delivery service immediately. Save the
damaged shipping container for inspection by the delivery service.
After unpacking the equipment, record all serial numbers. Save the
shipping containers and packing material in case it is necessary to
transport or ship any part of the system.
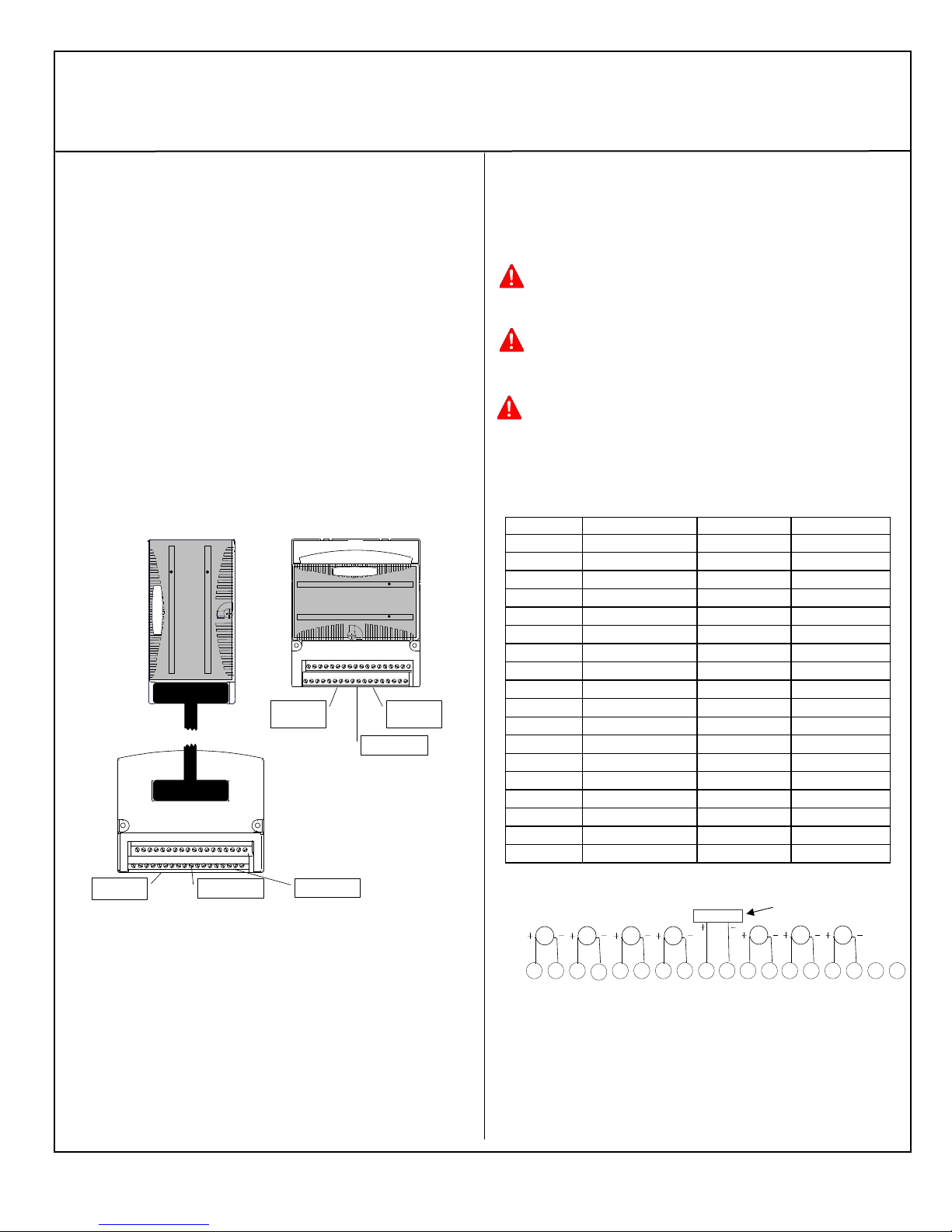
VersaMax* Analog Input, 16-Bit Thermocouple Module
Thermocouple
or Millivolt
Inputs
Thermocouple
or Millivolt
Inputs
Install Optional
Thermistors Here
Built-In Thermistors
Located Here
1234567891112131415161718
Note: only for thermocouple carrier
IC200ALG630
October 2016 GFK-1700L
Installation Instructions
The preferred installation technique is to mount the Thermocouple
Module on a Connector-style I/O Carrier and connect thermocouples to
an Interposing Thermocouple Carrier as shown below. The Interposing
Thermocouple-style I/O Carrier provides both box-style wiring terminals
and a built-in thermistor for Local Cold Junction Compensation. It
connects to the Connector-Style Carrier via a cable as shown. This
allows the thermocouple connections to be located away from the I/O
modules in the system. Each TC terminal on the Interposing
Thermocouple Carrier accommodates one solid or stranded AWG #14
(avg. 2.1mm2 cross section) to AWG #22 (avg. 0.36mm2 cross section)
wire, or two wires up to AWG #18 (avg. 0.86mm2 cross section).
However, it is also possible to mount the Thermocouple Module on one
of the terminal-style carriers (box-style, spring-style, or barrier-style) and
provide Local Cold Junction Compensation by using a kit that includes
the correct type of thermistor, as described in the I/O Modules User
Manual. Both methods are shown below. The thermistor kit must be
installed on the A9 and A10 terminals of the carrier.
If the module will only be used to measure millivolt inputs, not
thermocouple inputs, it can be mounted on any type of I/O Carrier. The
thermistor terminals A9 and A10 cannot be used as millivolt input
terminals.
Installation in Hazardous Locations
EQUIPMENT LABELED WITH REFERENCE TO CLASS I,
GROUPS A, B, C & D, DIV. 2 HAZARDOUS LOCATIONS IS
SUITABLE FOR USE IN CLASS I, DIVISION 2, GROUPS A, B, C,
D OR NON-HAZARDOUS LOCATIONS ONLY
WARNING - EXPLOSION HAZARD - SUBSTITUTION OF
COMPONENTS MAY IMPAIR SUITABILITY FOR CLASS I,
DIVISION 2;
WARNING - EXPLOSION HAZARD - WHEN IN HAZARDOUS
LOCATIONS, TURN OFF POWER BEFORE REPLACING OR
WIRING MODULES; AND
WARNING - EXPLOSION HAZARD - DO NOT DISCONNECT
EQUIPMENT UNLESS POWER HAS BEEN SWITCHED OFF OR
THE AREA IS KNOWN TO BE NONHAZARDOUS.
Field Wiring Terminals
The terminal assignments shown below are the same for all carriers.
Wiring Connections for Carriers with Two Rows of Terminals: