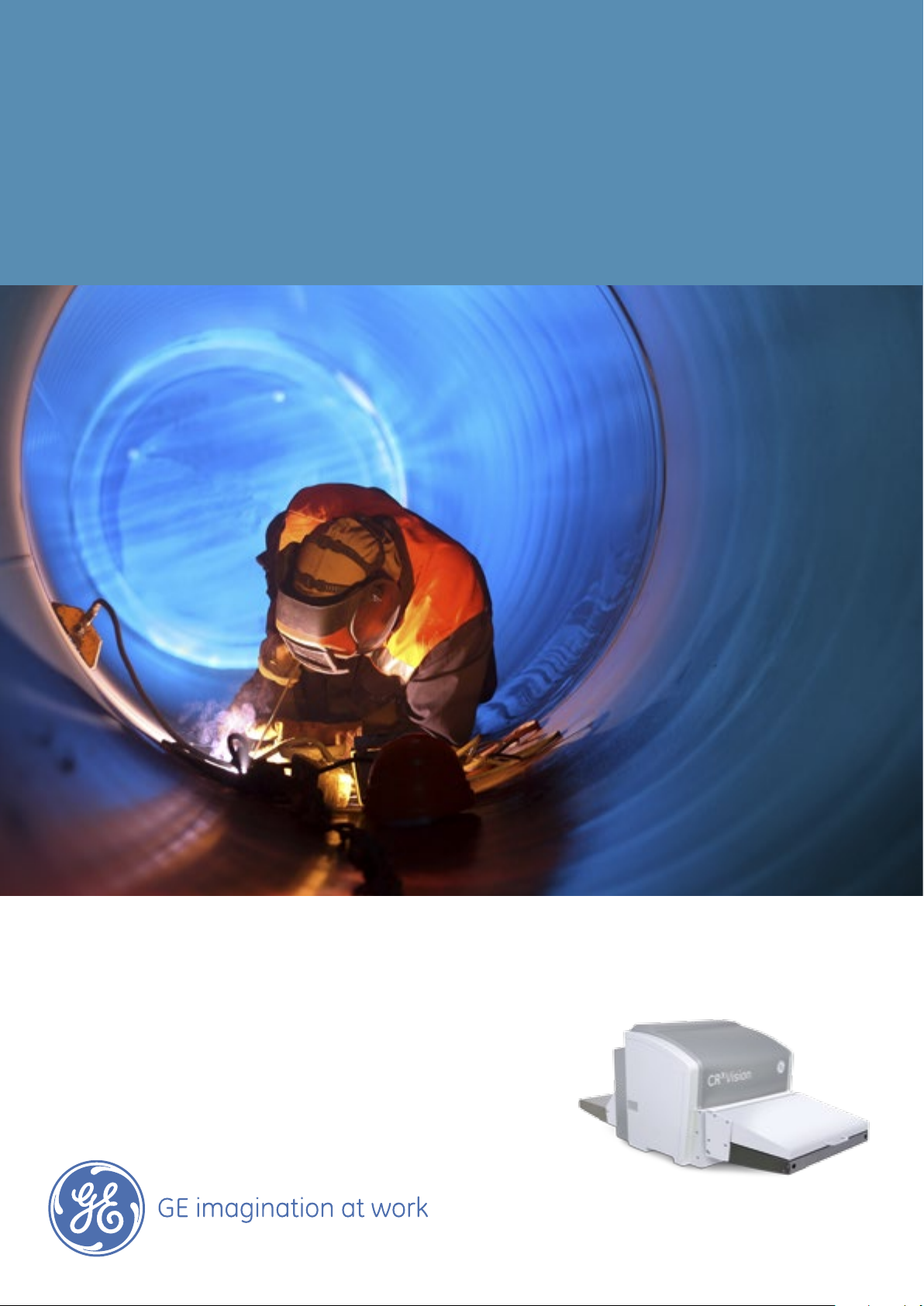
GE
Measurement & Control
High Resolution Weld Inspection and All-Purpose
Computed Radiography Scanner
Inspection Technologies:
CRxVision
Packed with innovative features to increase throughput, extend plate life
and provide excellent image quality, the CRxVision is designed specifically
for the inspection of welds. The scanner is developed to cover the stringent
ISO 17636-2 Class A and B requirements, as well as ASTM, ASME and EN
weld standards. Because of its versatility, it can also be used for many
other applications across the NDT industry.

CRxVision: the versatile, new tabletop scanner from GE.
Flexible
accepting a wide range of sizes, shapes and classes of imaging plates
Intuitive
no gain setting or photomultiplier adjustments required when
exposing various thicknesses
Fast
multiple plate scanning option: side-by-side and back-to-back
with a flat transport path
High Resolution
new laser optics for profound reading and
higher data extraction
4
3
2
1
6
ASTM DICONDE Compliant
fully compatible with GE´s existing
Rhythm Software Platform
7
Ambient Operation
cover protects the imaging plate
from light exposure
Extended Plate Life
no mechanical handling of the imaging
plate during scanning and erasing
Your Benefits:
— Compliant to ISO 17636-2 Class A
and B, ASME, ASTM and EN weld
inspection standards.
— The CRxVision has an extremely wide
latitude eliminating the need for multiple
gain settings when exposing over a wide
range of thicknesses. This is the result of a
16 bit image processing at selectable
35 or 70 microns resolution.
— Exposure times for welds are equal or
better than existing film exposure times
(to comply with Code Standards like EN
and ASME) and can be reduced by up to
ten times for non-code type applications
like erosion/corrosion or valve placement.
5
— Designed for extremely high throughput:
90 plates/hr at 70 microns or 28 plates/hr
at 35 microns for a 10 x 40 cm (4.5 x 17”)
plate. The scanner allows multiple imaging
plates to be scanned simultaneously …
side-by-side and back-to-back as well as
various lengths to be scanned together.
This is a result of the straight and flat,
in-line scan and erase transport path.
— Ability to scan any shape or size of
imaging plate from from 20 to 1500 mm
(0.75 to 60”) in length. Imaging plates can
be exposed in any type of cassette, then
simply removed and inserted directly
into the scanner without the need of
any type of adapter, template or leader.
— A new innovative imaging plate design
now provides the GE CRxVision imaging
plates with more flexibility. This new
design allows each imaging plate the
ability to return to a flat state after being
constantly bent around pipes for the
inspection of welds. This feature also helps
improve productivity by allowing the
imaging plates to be easily extracted and
reinserted into cassettes.
— Plate transport through the scanners
is achieved by a magnetic transportation
system. This new combination of scanner
and imaging plate design allows the
imaging plate to be transported through
the scanner without any mechanical
handling of the phosphor ultimately
extending the overall life of the plate.
— The updated Rhythm RT software
simplifies inspection workflow. It now has
the ability to automatically crop the images
by detecting the physical edges of each
individual plate when they are processed.
Consequently, each individual plate can be
separately identified and saved or grouped
together and saved as one file.
— The new scanner enjoys all the
functionality offered by GE´s Rhythm
Software giving the inspector the ability
to view, enhance, measure, annotate and
comment on the images. The CRxVision
8
system is completely DICONDE compliant
and compatible with all existing modules in
GE´s Rhythm Software platform.
— The CRxVision can be used in ambient
light conditions with suitable handling as
the light cover protects the plates from light
exposure during the scan cycle. The cover
can be removed for work in darkrooms if
required.
— The scanner weighs less than 45 kg
(99 lbs) and has a footprint of 560 x 560 mm
(22 x 22 inches). It extends to 560 x 1280 mm
(22 x 50 inches) when the feed and exit
tables are attached.
Direct Laser Contact
the laser beam is in direct contact
with the imaging plate (no glass to
obscure data collection)
— The light guide can be easily cleaned
with an internal brush which is operated
by simply turning a set screw. The eraser
section of the scanner is completely sealed
from the optics section to prevent migration
of any dust particles into the machine.