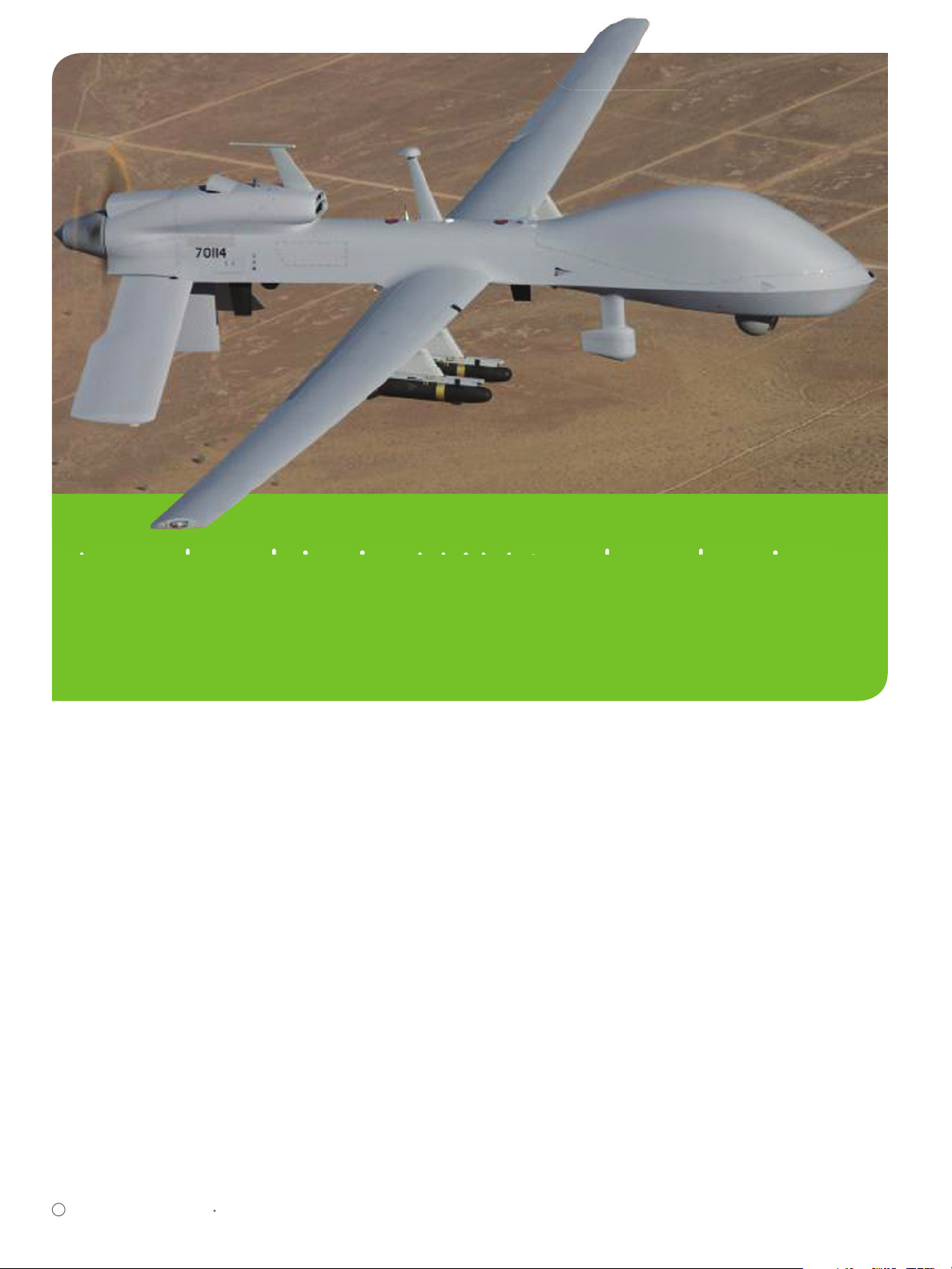
Leadership in UAV technologies
since the very beginning
The concept of the unmanned aerial system (UAS), which consists
of an unmanned aerial vehicle (UAV) as well as the ground control
ecosystem that supports it, is revolutionizing the way military
information is gathered and even how adversaries are engaged.
2
unmanned aerial systems defense.ge-ip.com/uas
GE Intelligent Platforms has been there
every step of the way, with a wide range of
embedded computing products specifically
tailored to meet the size, weight, and power
(SWaP) constraints of UAV designs.
The use of UASs is expected to grow
dramatically as unmanned platforms weigh
heavily into the announced plans of the
U.S. Department of Defense and defense
departments in other nations as well as non-
military entities such as police and border
patrol agencies. Military, security agency
and emergency response leaders recognize
that UASs provide a means of reducing risk
to personnel, conducting missions under
conditions that would preclude the use of
manned flight platforms. UASs also lower
capital and operating expenditures for
battlefield deployments as well as security,
emergency and police patrols.
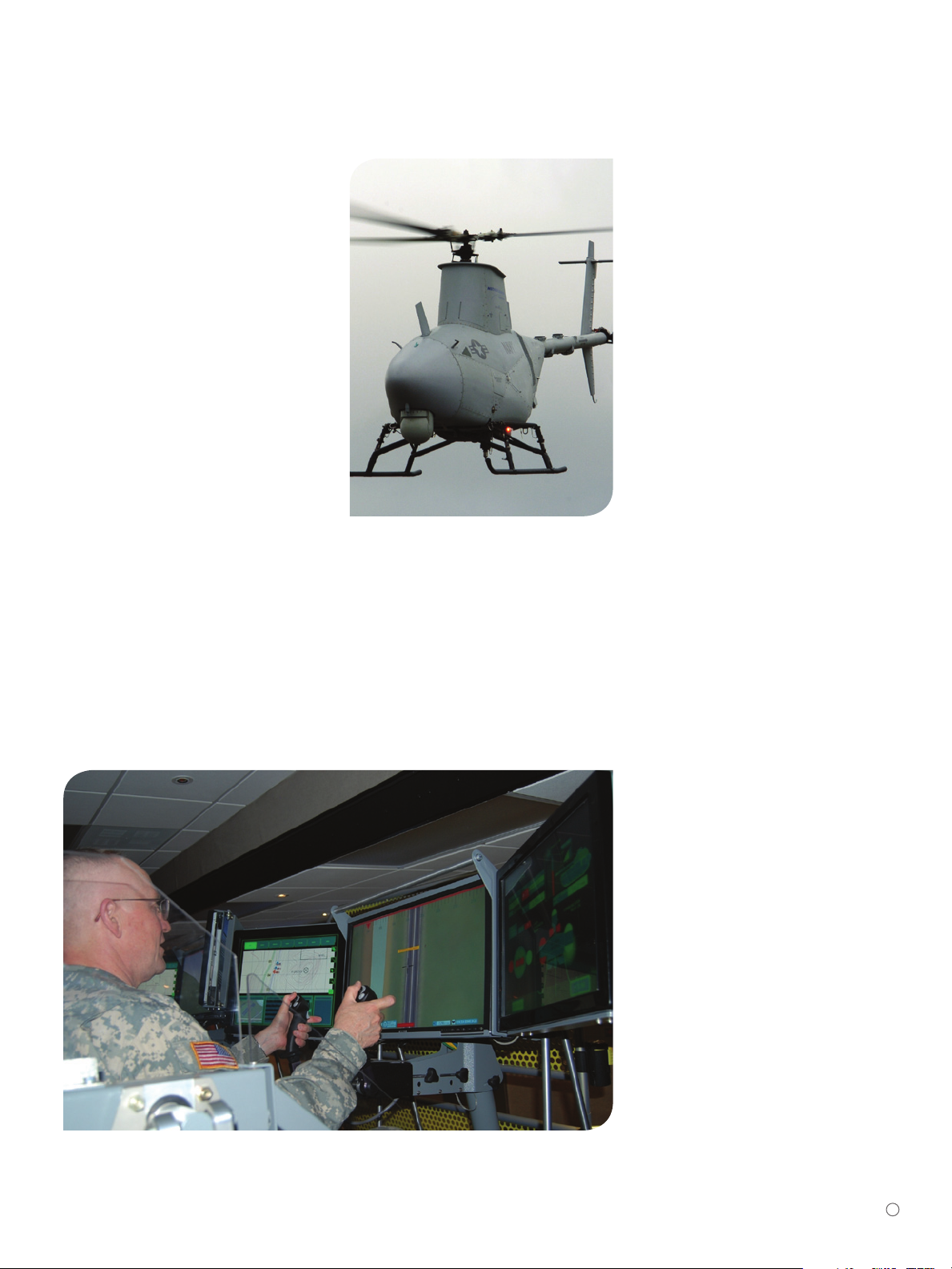
GE products helped to launch early UAV
platforms, and we continue to develop
products that will help advance UAS
future operations. Our video capture and
image processing technologies and single
board computers (SBCs) are used on UAS
programs such as the U.S. Navy Fire Scout.
Subsequent deployments have included
our PPCM2 6U VME Dual PowerPC SBC in
the Watchkeeper ground station, PPC4A
6U VME SBC in the Predator ground station,
IMP2A 3U CompactPCI and SBC340 3U VPX
®
Intel
Core™ Duo SBCs in the Herti vehicle,
and SBC310 3U VPX SBC on the South
Korean MUAV vehicle and PPC9A 6U VME
SBC in its ground station. Most recently,
our target tracking technology was used
in a successful DARPA-funded project to
demonstrate the feasibility of autonomous
UAV-to-UAV in-flight refueling.
The avionics bus structure is a key element
in every UAV design. MIL-STD-1553 is a
proven technology that has now come
full-circle to include its use on the newest
commercial aircraft development at Airbus.
The 1553 standard provides EMI performance, determinism, distributed control
and a 40-year history as the standard
in military and aerospace flight controls,
weapons and communications systems.
UAS developers face unique challenges.
Due to their high capability and solid
economic benefit, UAVs are needed
urgently in the field, thus accelerating
their acquisition timeline. The developer’s
response must be rapid, and not only with
the correct solution for today but also with
a clear technology roadmap for phased
platform upgrades and modernization. Of
course, all of this must be accomplished
at a winning cost level, with open systems
architecture and within the guidelines of the
acquisition reform directives.
Of major importance are the video capture
and data streaming capabilities needed
both to control the UAV and obtain meaningful data about potential objects of
interest on the ground. Enormous volumes
of data must be captured, processed and
transmitted seamlessly and in real time
using SWaP-optimized components. In
addition, the operation of a battlefield
asset from potentially halfway around the
globe poses unique flight management,
control systems and perhaps even weapons
management systems challenges. For
these critical requirements, GE offers application-ready solutions able to accept the
developer’s unique software (or software
solutions developed by GE) that can meet
accelerated timelines and environmental
requirements. In addition, we provide
a clear, understandable upgrade path
throughout the lifecycle of the platform, all
at a winning price level.
With intelligence, surveillance and reconnaissance (ISR) a major mission of the UAS
paradigm, state-of-the-art, real-time video
tracking capability is certainly at the top
of any platform developer’s list of critical
mission requirements. GE’s advanced image
processing products such as the ADEPT5000
have been designed to achieve robust
multiple target tracking despite the presence of background clutter and obscuration.
The seamless integration of these various
technologies is essential. Our rigorous
subsystem integration and testing
programs are designed to free contractors and system integrators from the
time-consuming and capital-intensive
certification of subsystems, thus helping to
speed the time from design to deployment.
3

Products
GE specializes in the design of commercial off-the-shelf (COTS)
rugged components and custom subsystems. The use of
ruggedized commercial components and subsystems affords
state-of-the-art technologies at the lowest cost and fastest time-
to-market. In addition, such products greatly mitigate program
risks for the prime contractor.
4
unmanned aerial systems defense.ge-ip.com/uas
Our leadership in ruggedization techniques
ensures that our products will withstand the
harsh environments encountered by a UAV
throughout the full lifecycle of the platform.
Autonomous Video Tracking
for Geo-Location and Refueling
Video tracking capability is imperative on
UAVs, which may find utility both for ISR
and weapons deployment. GE is at the
forefront of rugged video tracking systems
designs that minimize SWaP parameters.
Our ADEPT5000 Multi-Target Video Tracker
incorporates advanced pre-processors that
separate targets from background clutter,
while multiple-target tracking software
provides concurrent detection, cueing and
tracking for up to five targets.
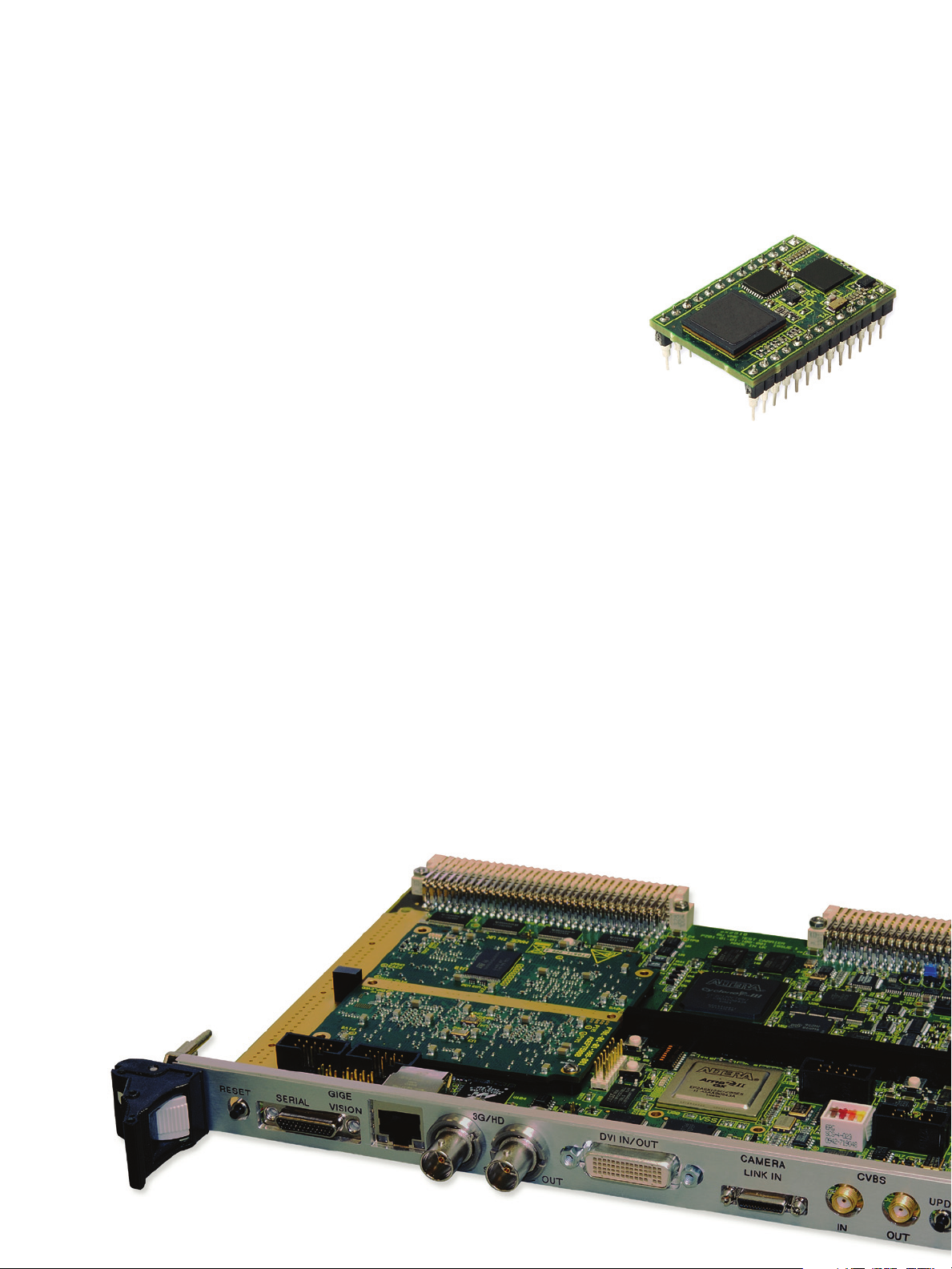
As high-definition sensors become
commonplace on UAVs, their increased
bandwidth demands places significant
processing overhead on traditional video
tracking systems. The dedicated video
architecture of the ADEPT5000 ensures
that it can process the higher pixel densities, frame rates, and multiple targets with
minimal latency. This makes the ADEPT5000
especially suited for closed-loop control
applications. A wide range of high-bandwidth digital video interfaces are available,
including high-definition video.
The ADEPT5000 has a simplified structured
approach which significantly reduces
configuration time and complexity with
a consequential cost saving. A comprehensive range of physical form factors
are available with a common functional
core, allowing a single integration process
to be used for multiple-system designs.
Careful consideration has been given to
automating operation. The enhanced
user interface, automated functions
and advanced high-resolution, full-color
symbology combine to significantly reduce
operator workload.
In keeping with GE’s leadership in the
development of COTS-based technologies to reduce SWaP, our new ADEPT3000
Video Tracker and MIP3ES Electronic Video
Stabilizer are SWaP-optimized image
processing modules designed to be placed
on small platforms such as hand-launched
UAVs or small unmanned ground vehicles.
The ADEPT3000 affords most of the functionality of larger video tracker, yet is only
slightly larger than a microprocessor chip.
The MIP3ES eliminates unwanted visible
platform motion and vibration from sensor
images using low-latency post-processing.
GE has designed both solutions to be fully
ruggedized to survive harsh military environments such as extreme temperatures,
shock, vibration, and dust.
Automatic tracking was an important development benchmark for the ADEPT3000,
because many of the platforms in which
this device will be deployed are unmanned
and potentially only minimally controlled
by human operators. These smaller platforms will also have extremely tight power
restraints, so the ADEPT3000 was held to
very low power consumption specifications.
ADEPT3000 (actual size)
With a footprint of just 24mm by 34 mm,
the ADEPT3000 is slightly smaller than a
single frame of 35mm photographic film.
Despite the SWaP-defined architecture of the
ADEPT3000, GE engineers were able to retain
a strong set of functionalities. The single
target tracker allows targets to be tracked
automatically or under operator control. The
ADEPT3000 also affords composite video
input and output, and an onboard RS232
TTL serial port. With full knowledge that the
ADEPT3000 will be deployed on platforms
that may be likely to be operated and maintained under field conditions, the tracker was
designed for ease of set-up and use with PC
control software.
ADEPT5000
5